Организация единого технологического процесса функционирования баз и складов (на примере инженерно-технического имущества Вооруженных Сил Республики Белару
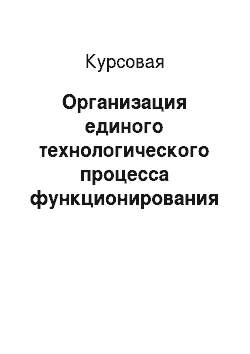
Есть еще один способ определения мест хранения — составление карты размещения свободных мест на складе. Этот способ может показаться весьма примитивным, но позволяет существенно оптимизировать процесс поиска свободных мест на складе средней площади — 2000…5000 м2. Сущность метода сводится к тому, что приобретается большая маркерная (пластиковая) доска, на которой несмываемой краской наносят все… Читать ещё >
Организация единого технологического процесса функционирования баз и складов (на примере инженерно-технического имущества Вооруженных Сил Республики Белару (реферат, курсовая, диплом, контрольная)
МИНИСТЕРСТВО ОБРАЗОВАНИЯ РЕСПУБЛИКИ БЕЛАРУСЬ УО «Белорусский государственный экономический университет»
Кафедра логистики и ценовой политики КУРСОВАЯ РАБОТА по дисциплине: Логистика складирования на тему: Организация единого технологического процесса функционирования баз и складов (на примере инженерно-технического имущества Вооруженных Сил Республики Беларусь) Исполнил студент ВШУБ, 5 курс, ВВЛ-2
М.К. Дубицкий Руководитель Кандидат экономических наук доцент О. Л. Ковалева МИНСК — 2014
РЕФЕРАТ Курсовая работа: 62с., 8 рис., 13 источников, 4 табл.
СКЛАД, ТЕХНОЛОГИЧЕСКИЙ ПРОЦЕСС, НОРМАТИВНО-ПРАВОВЫЕ ДОКУМЕНТЫ, ЗАКАЗЧИК, ПОСТАВЩИК, ПРИЕМКА, ОТГРУЗКА, ХРАНЕНИЕ.
Объектом исследования является технологический процесс функционирования баз и складов.
Предметом исследования является организация единого технологического процесса функционирования баз и складов.
Цель работы: оценка и изучение эффективности организации единого технологического процесса функционирования баз и складов.
Метод исследования: сравнительный анализ.
В процессе работы раскрывается сущность и необходимость организации единого технологического процесса функционирования баз и складов, указаны пути и методы повышения эффективности его использования.
На основе проведенного анализа организации технологического процесса, сделан вывод о том, что механизация и автоматизация складского технологического процесса имеют большое значение, так как применение средств механизации и автоматизации при приемке, хранении и отгрузке товаров способствует росту производительности труда складских работников, повышению эффективности использования площади и емкости складов, ускорению погрузочно-разгрузочных работ, сокращению простоев транспортных средств.
Подтверждаю, что приведённый в курсовой работе аналитический материал правильно и объективно подтверждает состояние исследуемого процесса, а все заимствованные из литературных и других источников теоретические, методологические и методические положения и концепции сопровождаются ссылками на их авторов.
СОДЕРЖАНИЕ Введение
1. Содержание и принципы организации единого технологического процесса функционирования баз и складов
1.1 Основные функции и задачи баз и складов
1.2Содержание и принципы организации складского технологического процесса
2. Анализ организации технологического процесса на складах Вооруженных Сил Республики Беларусь (на примере склада связи)
2.1 Организационно-техническая характеристика склада связи
2.2 Организация технологического процесса склада связи
3. Оптимизация технологического процесса на складе
Заключение
Список использованных источников
Приложение
ВВЕДЕНИЕ
Склады являются одним из основных элементов логистических систем (далее — ЛС). Глубокая переработка предметов труда, осуществляемая в процессе производства материальных благ в соответствии с требованиями конечного потребителя продукта труда, здесь не выполняется. Однако здесь осуществляется преобразование предмета труда, в соответствии с логистическими потребностями других элементов товаропроводящих систем: транспорта, других складов, потребителей материалов, в том числе и конечных потребителей. На складах грузы временно накапливаются, маркируются, переупаковываются и т. п. Если от качества работы производственного участка зависит качество работы конечного изделия у конечного потребителя, то от качества работы склада зависит качество работы последующих элементов логистической цепи.
Практика организации складской деятельности до начала 90-х годов опиралась на использование нормативов, типовых решений, рекомендаций, которые разрабатывались различными НИИ в целях рационального потребления ресурсов единого собственника — государства. Функция эта централизованно более не реализуется, в результате отсутствует методологическая поддержка решений в области складского менеджмента.
Складская сеть, оставшаяся в наследство от прежней экономической системы, создавалась в условиях единого собственника и не соответствует задачам оптимальной организации товародвижения в условиях рыночной экономики.
Основные направления оптимальной организации работы складов:
— оптимизация дислокации складов, то есть пересмотр расположения складов с учетом перспектив роста и требований к пропускной способности складов. Данные меры, как правило, позволяют снизить транспортные издержки, оптимизировать запасы в цепях поставок, а также повысить уровень сервиса клиентов склада;
— оптимизация складских технологических процессов, что позволяет повысить производительность и качество работы склада;
— достижение высоких показателей использования складской площади и объема за счет применения рациональных технологических решений и рациональных схем механизации погрузочно-разгрузочных и транспортно-складских работ, что позволяет снизить складские затраты на единицу перерабатываемого потока, повысить мощность склада без соответствующего увеличения складской площади;
— стандартизация складских технологических процессов, то есть описание и закрепление порядка выполнения отдельных операций и процессов. Стандартизации в первую очередь подлежат значимые процессы и операции, то есть те, которые сопряжены с высокими издержками, от которых зависит уровень сервиса, а также сохранность материальных ценностей. Стандартизация технологических процессов позволяет поднять уровень технологической дисциплины, повысить качество отдельных операций и процесса в целом, позволяет сократить затраты на обучение персонала;
— разработка норм по установленным видам работ, в первую очередь по наиболее важным, создает возможности точного планирования, а также точного учета и контроля качества и количества труда, позволяет эффективно решать вопросы мотивации персонала;
— оптимизация парка подъемно-транспортного оборудования, применяемого на складе, что позволяет поднять производительность труда, повысить скорость и качество технологического процесса;
— внедрение рациональных схем механизации погрузочно-разгручных и транспортно-складских работ, что также положительно сказывается на производительности, скорости и качестве технологического процесса;
— оптимизация размещения товаров на складе, что позволяет минимизировать перемещения на складе, то есть выполнять заказы быстрее и с наименьшими затратами трудовых и технических ресурсов.
В данной курсовой работе предпринята попытка рассмотреть механизм организации единого технологического процесса функционирования баз и складов в целом по Республике Беларусь и в отдельно взятой организации. На основании анализа предложены пути совершенствования функционирования технологического процесса.
Целью работы является оценка и изучение организации технологического процесса функционирования баз и складов.
Объектом исследования является технологический процесс функционирования баз и складов.
Предметом исследования является организация технологического процесса склада связи.
Задачами данной курсовой работы являются:
— рассмотреть теоретические основы организации технологического процесса функционирования баз и складов;
— изучить организацию технологического процесса склада связи;
— найти пути совершенствования технологического процесса склада связи.
1. СОДЕРЖАНИЕ И ПРИНЦИПЫ ОРГАНИЗАЦИИ ЕДИНОГО ТЕХНОЛОГИЧЕСКОГО ПРОЦЕССА ФУНКЦИОНИРОВАНИЯ БАЗ И СКЛАДОВ
1.1 Основные функции и задачи баз и складов Склады — это здания, сооружения и разнообразные устройства, предназначенные для приемки, размещения и хранения поступающих на них товаров, подготовки их к потреблению и отпуску потребителю.
Склады являются одним из наиважнейших элементов ЛС. Объективная необходимость в специально обустроенных для содержания запасов существует на всех стадиях движения материального потока, начиная от первичного источника сырья и кончая конечным потребителем. Этим объясняется наличие большого количества разнообразных видов складов.
В логистике склад — это место преобразования материальных потоков, направленных на удовлетворение потребностей клиентской базы. Логистика занимается не управлением складом, а управлением товарными потоками, проходящими через склад и складскую сеть.
Основными причинами использования складов в ЛС можно считать следующие:
— координация и выравнивание спроса и предложения в снабжении и распределении;
— уменьшение логистических издержек при транспортировке (экономичные партии доставки);
— обеспечение максимального удовлетворения потребительского спроса (максимальный уровень сервисного обслуживания);
— создание условий для поддержания активной стратегии сбыта;
— увеличение географического охвата рынка сбыта (увеличение территориального охвата рынка);
— бесперебойное снабжение конечных потребителей и возможность организации у них товарных запасов;
— обеспечение гибкой политики обслуживания, особенно в системах с независимым спросом.
Склад, как любой элемент ЛС, должен осуществлять свою деятельность с позиции эффективности всей системы. Из этого следует, что склады в рамках ЛС должны выполнять следующие функции:
— выравнивание интенсивности материальных потоков в соответствии со спросом потребителей;
— преобразование ассортимента внутри материального потока в соответствии с заказом клиента;
— обеспечение концентрации и хранения запасов;
— сглаживание асинхронности производственного процесса;
— унитизации партии отгрузки;
— предоставление услуг.
В рамках системы логистики склад решает задачи:
— своевременное предоставление товаров и услуг потребителям, обеспечивая максимальный уровень обслуживания клиентов;
— концентрация и пополнение запасов при оптимальных затратах на основе учета запасов в натуральном и стоимостном выражениях;
— защита производства и потребителей от непредвиденных обстоятельств (отсутствие товаров у поставщика, забастовка, катастрофа и т. д.);
— сбалансирование увеличения темпов производства и объемов производимой продукции при росте спроса потребителями.
Склад решает и чисто традиционные задачи, связанные с осуществлением технологического процесса переработки грузов:
— максимальное использование складских мощностей;
— рациональное ведение погрузочно-разгрузочных и складских работ;
— эффективное использование складского оборудования;
— устранение потерь товаров при их складской обработки и хранении;
— подготовка товара к продаже: маркировка, специальная упаковка и т. д.
На политику складирования и деятельность склада организации оказывают влияние:
— место склада в ЛС;
— особенности отрасли;
— цель и задачи деятельности, реализуемые организацией;
— доступность капитала;
— характеристики и особенности товара, такие, как вес и размер товара и упаковки, условия хранения, разнообразие товарных позиций, возможность замены одного товара другим;
— сроки хранения товара;
— экономические условия функционирования организации;
— конкурентная среда деятельности;
— сезонность спроса на товар;
— применяемые логистические технологии;
— использование электронной коммерции.
Разнообразие видов складов в ЛС, выполняемые ими функции и задачи, особенности перерабатываемых грузов и т. д. требуют их обязательной систематизации. Цель классификации складов в логистике состоит в выявлении тех или иных признаков систематизации складского объекта как элемента ЛС, влияющего на особенности продвижения материального потока.
Общепринятая еще во времена СССР классификация складов предполагает систематизацию складов по следующим основным признакам:
— отношению к базисным функциональным областям;
— виду продукции;
— форме собственности;
— функциональному назначению;
— отношению к участникам ЛС;
— товарной спецификации;
— технической оснащенности;
— виду складских зданий;
— наличию внешних транспортных связей.
Более подробно рассмотрим склады по функциональному назначению и технической оснащенности (рисунок 1).
Рисунок 1 — Классификация складов по функциональному назначению Примечание — Источник:[3,с.10]
По этому признаку склады можно разделить на две основные группы:
— склады на участке движения продукции производственно-технического назначения.
— склады на участке движения товаров народного потребления.
По технической оснащенности склады можно разделить на 6 классов (по классификации риэлторов):
Склад класса А+.
Современное одноэтажное складское здание, построенное по современным технологиям с использованием высококачественных материалов. Высота потолка от 10 метров, позволяющая установку многоуровневого стеллажного оборудования. Ровный пол с антипылевым покрытием. Система пожарной сигнализации и автоматическая система пожаротушения (спринклерная или порошковая). Регулируемый температурный режим. Тепловые завесы на воротах. Автоматические ворота докового типа с гидравлическим пандусом, регулируемые по высоте. Центральное кондиционирование или принудительная вентиляция. Система охранной сигнализации и видео наблюдения. Офисные площади при складе. Оптико-волоконные телефонные линии. Достаточная территория для отстоя и маневрирования большегрузных автопоездов. Расположение на основных магистралях, обеспечивающих хороший подъезд.
Склад класса А-.
По функциональности приближается к складам класса А+, но уступает им по качеству используемого оборудования, по менее выгодному расположению, или же помещения такого уровня не предоставляют полный спектр услуг, или не полностью соответствуют всем требованиям помещений класса А+.
Склад класса В+.
Одноэтажное складское здание, предпочтительно прямоугольной формы, вновь построенное или реконструированное. Высота потолка от 8 метров. Ровный бетонный пол с антипылевым покрытием. Система пожарной сигнализации и автоматическая система пожаротушения. Регулируемый температурный режим. Тепловые завесы на воротах. Автоматические ворота докового типа с гидравлическим пандусом, регулируемые по высоте. Центральное кондиционирование или принудительная вентиляция. Система охранной сигнализации и видео наблюдения. Офисные площади при складе. Оптико-волоконные телефонные линии. Достаточная территория для отстоя и маневрирования большегрузных автопоездов.
Склад класса В-.
Капитальное здание одноили многоэтажное (реконструированные бывшие производственные помещения, с необходимыми коммуникациями и оборудованием). Высота потолка от 4,5 до 8 метров. Пол асфальт или бетон без покрытия. Пожарная сигнализация и гидрантная система пожаротушения. Пандус для разгрузки автотранспорта. Офисные помещения при складе. Телефонные линии. Охрана по периметру территории.
Склад класса С.
Капитальное производственное помещение или утепленные ангары. Высота потолка от 3,5 до 18 метров. Пол асфальт или бетонные плиты. Ворота на нулевой отметке, автомашина заходит внутрь помещения.
Склад класса D.
Подвальные помещения или объекты гражданской обороны, неотапливаемые производственные помещения или ангары.
Совокупность работ, выполняемых на различных складах примерно одинакова. Это объясняется тем, что в различных логистических процессах склады выполняют следующие схожие функции:
— временное размещение и хранение материальных запасов;
— преобразование материальных потоков;
— обеспечение логистического сервиса в системе обслуживания.
Любой склад обрабатывает, по меньшей мере, три вида материальных потоков: входной, выходной и внутренний.
Наличие входного потока означает необходимость разгрузки транспорта, проверки количества и качества прибывшего груза. Выходной поток обусловливает необходимость погрузки транспорта, внутренний — необходимость перемещения груза внутри склада. Реализация функции временного хранения материальных запасов означает необходимость проведения работ по размещению грузов на хранение, обеспечению необходимых условий хранения, изъятию грузов из мест хранения.
Преобразование материальных потоков происходит путем расформирования одних грузовых партий или грузовых единиц и формирования других. Это означает необходимость распаковки грузов, комплектования новых грузовых единиц, их упаковку, затаривание.
Однако это лишь самое общее представление о складах. Любая из вышеперечисленных функций может изменяться в широких пределах, что сопровождается соответствующим изменением характера и интенсивности протекания отдельных логистических операций. Это в свою очередь, меняет картину протекания технологического процесса на складе.
1.2 Содержание и принципы организации складского технологического процесса Любой склад является достаточно самостоятельной системой с четко определенными задачами. Эффективность решения этих задач определяется рациональностью организации внутрискладского процесса.
Технологический процесс на складах, основу которого составляют материальные потоки, должен отвечать оптимальным параметрам по скорости процесса, обеспечивать сохранность товаров и экономичность затрат. Условием выполнения указанных требований является соблюдение следующих принципов организации материальных потоков на складе: пропорциональности, параллельности, непрерывности, ритмичности, прямоточности, поточности.
Пропорциональность процесса означает, что все его части операции, связанные между собой должны быть пропорциональными, т. е. соответствовать друг другу по производительности, пропускной способности или скорости. В соответствии с этим принципом планируются пропорциональные затраты труда в единицу времени на различных участках.
Параллельность — одновременное выполнение различных операций на всех стадиях процесса. Параллельное выполнение работ способствует сокращению цикла работ, повышению уровня загрузки рабочих и эффективности их труда на основе его специализации, выработки профессиональных навыков, достижению определенной степени автоматизма движений.
Ритмичность выражается в повторяемости всего цикла и отдельных операций в равные отрезки времени.
Непрерывность — устранение или сокращение всякого рода перерывов в технологическом процессе.
Прямоточность — обеспечивает сокращение трудовых затрат при одинаковой мощности складов.
Поточность — представляет ведущий принцип современной организации микрологистических систем, в соответствии с которым все операции технологического цикла взаимосвязаны и подчинены единому расчетному ритму.
Правильно организованный технологический процесс работы склада должен обеспечивать:
— четкое и своевременное проведение количественной и качественной приемки товаров;
— эффективное использование средств механизации;
— правильный выбор оборудования и методов укладки товаров, обеспечивающее максимальное использование площади и емкости складов, а также полную сохранность товарно-материальных ценностей;
— рациональную организацию работ по отборке, комплектованию и подготовке к отпуску товаров, включая работу залов товарных образцов;
— последовательное и планомерное выполнение складских операций, способствующих ритмичной и эффективной организации труда складских работников;
— четкую работу экспедиции и организацию централизованной доставки товаров;
— внедрение современных форм организации труда, создание нормальных условий труда и техники безопасности;
— снижение общего уровня складских расходов на основе использования передовых методов работы.
Принципиальная схема технологического процесса (рисунок 2), разрабатываемая на основе сформулированных ранее требований, представляет собой взаимосвязанную последовательность крупных блоков операций, которые предусмотрено выполнять на складе.
Рисунок 2 — Принципиальная схема технологического процесса на складе предприятия Примечание — Источник:[3,с.44−45]
Операции по поступлению товаров составляют начальную стадию складского технологического процесса. Количество операций и последовательность их выполнения зависят от размеров партий товаров и видов транспортных средств, которыми они доставляются на склад.
В организации приемки большое значение имеет предварительное установление времени прибытия и количества, поступающих на склад товаров, что позволяет заблаговременно спланировать необходимые мероприятия по приемке товаров.
К подготовительным мероприятиям по приемке товаров на складе относится:
— установление места разгрузки транспортных средств, максимально приближенного к помещению для хранения;
— определение необходимого количества работников для разгрузки и распределение работ между ними;
— определение необходимого количества и видов подъемно-транспортного оборудования и подготовка его к прибытию товаров;
— заблаговременное определение мест хранения;
— подготовка документации, связанной с оформлением приемки-сдачи товаров.
Разгрузка
Прежде чем приступить к непосредственной приемке товара, необходимо его разгрузить. При разгрузке осуществляется передвижение товаров с транспорта на товарную платформу. Разгрузку осуществляют работники того предприятия, чьим транспортом был доставлен товар на склад, то есть это могут быть работники фирмы поставщика, транспортной организации, фирмы покупателя. Если товар доставлен собственным транспортом фирмы покупателя или железной дорогой, разгрузку осуществляют работники склада.
Содержание операций по разгрузке товаров зависит от того, каким транспортом они были доставлены.
Если товары поступили в железнодорожных вагонах, то выполняются следующие основные операции:
— проверка целостности пломб и вскрытие вагона;
— осмотр состояния поступившего груза (состояние укладки, тары и т. д.);
— разгрузка вагонов с укладкой товаров на поддоны или тележки;
— первичная приемка товаров по количеству (проверка соответствия числа тарных мест сопроводительным документам);
— доставка сформированных партий товаров на участок приемки, экспедиционный склад или в зону хранения.
При поступлении товаров в железнодорожных контейнерах операции выполняются по следующей схеме:
— проверка целостности пломб и состояния контейнера (отсутствие повреждений и поломок);
— перемещение контейнера на разгрузочную рампу;
— перемещение контейнера в зону приемки товаров.
По следующей схеме будут выполняться операции, если товары доставлены на склад автомобильным транспортом:
— проверка целостности упаковки, первичная приемка товаров по количеству;
— укладка товаров на поддоны или тележки;
— перемещение сформированных транспортных единиц в зону приемки или хранения.
Штучные, тарно-упаковочные и навальные грузы транспортируются в вагонах. Длинномерные и крупногабаритные грузы (лесоматериалы и др.) доставляются в полувагонах и на платформах. Для транспортировки жидких грузов (масло растительное, керосин и др.) используют цистерны. Универсальные контейнеры могут доставляться на склады на железнодорожных платформах или автомобилях.
Если склад имеет подъездные железнодорожные пути, то вагоны, полувагоны, платформы и цистерны адресуются на близлежащую железнодорожную станцию, а затем подаются на ветку базы.
Контейнеры поступают или непосредственно на склад, или на контейнерную площадку железнодорожной станции, а затем доставляются на склад автомобильным транспортом.
При поступлении груза в неисправном вагоне или контейнере или с нарушенной пломбой необходимо произвести сплошную проверку количества и качества товаров и обязательно составить коммерческий акт, который является основанием для предъявления претензии транспортным органам или поставщику. Он должен быть составлен на специальных бланках до получения груза от органов транспорта. Если вагон имеет течь или обнаружено, что груз испорчен вследствие неисправности вагона, то дополнительно к коммерческому акту составляется технический акт.
Разгрузка товаров может потребовать применение физической силы, однако, во всех случаях, когда возможно, следует использовать оборудование для перемещения грузов.
Для выгрузки товаров применяют различные типы подъемно-транспортного оборудования:
— конвейеры;
— электропогрузчики;
— транспортеры;
— средства малой механизации.
При этом непакетированные штучные грузы предварительно формируют в пакеты, используя поддоны, которые после их загрузки перемещают в зону приемки товаров.
Товары в разной таре (мешках, кипах, ящиках) по транспортеру перемещают из машины и укладывают на освобожденном от разгрузки пространстве.
Для выгрузки и перемещения автомобильных контейнеров используют электротележки с подъемной платформой или вилами. Все более широкое применение находит и доставка контейнеров в автомобилях, оборудованных подъемным устройством заднего борта, что упрощает процесс разгрузки при поступлении товаров в контейнерах.
Железнодорожные контейнеры снимают с транспортных средств при помощи мостовых кранов или автопогрузчиков. Причем, процесс разгрузки товаров должен быть организован таким образом, чтобы исключались встречные перевозки, поэтому разгрузку поступивших товаров и их погрузку при отпуске желательно производить на рампах, расположенных с разных сторон склада.
Разгрузка транспортных средств должна осуществляться при строгом соблюдении установленных правил выполнения погрузочно-разгрузочных работ.
Организация и технология приемки товаров по количеству и качеству на складе Доставленные в зону приемки товары принимаются по количеству и качеству в соответствии с постановлением Совета Министров Республики Беларусь от 3 сентября 2008 года № 1290 «Об утверждении Положения о приемке товаров по количеству и качеству».
Следует отметить, что приемка товаров по количеству и качеству является одной их важных составных частей складского технологического процесса. Она предусматривает проверку выполнения поставщиками договорных обязательств по количеству, ассортименту, качеству и комплектности товаров.
Приемка товаров производится материально ответственными работниками склада (обычно — заведующим складом совместно с товароведом), уполномоченными на то руководителем или заместителем руководителя предприятия-получателя.
Она включает следующие операции:
— проверку количества и качества поступивших товаров;
— оформление приемки соответствующими документами;
— принятие товаров на учет.
Порядок проведения приемки товаров определяется сторонами договора поставки. Груз, поступивший на склад каким-либо видом транспорта, первоначально принимают, руководствуясь действующими на транспорте правилами, установленными соответствующими уставами, кодексами.
Приемка товаров по количеству.
Приемка товаров по количеству проводится с целью проверки соответствия фактически поставленного количества товаров количеству, указанному в транспортных и сопроводительных (счете-фактуре, спецификации, описи, упаковочных ярлыках и др.) документах производителя (изготовителя). Если товары поступили без сопроводительных документов, то их отсутствие не приостанавливает приемку. В этом случае составляется акт о фактическом наличии товаров и в нем указывается, какие документы отсутствуют.
Место проведения приемки товаров зависит от способа их доставки. Приемка может производиться:
— на складе получателя;
— на складе поставщика;
— в месте вскрытия опломбированных или в месте разгрузки неопломбированных транспортных средств и контейнеров или на складе органа транспорта.
На складе получателя приемку товаров производят, если они доставлены поставщиком. В этом случае кроме проверки массы брутто и количества мест получатель может потребовать от поставщика вскрытия тары и проверки массы нетто и количества товарных единиц в каждом месте. Если же товары поступили в поврежденной таре, то получатель обязан провести такую приемку (по массе нетто и количеству товарных единиц) в момент доставки их на склад.
На складе поставщика приемка производится в том случае, если товары вывозятся с этого склада получателем. При этом товары, находящиеся в исправной таре, принимают по массе брутто и количеству тарных мест, а окончательную их приемку производят на складе получателя. Товары, поставляемые без тары, в открытой или поврежденной таре, окончательно принимаются на складе поставщика.
Если товары доставляются и выдаются органом железнодорожного, водного, воздушного или автомобильного транспорта, то приемка осуществляется с их участием вместе вскрытия опломбированных или в месте разгрузки неопломбированных транспортных средств и контейнеров или на складе соответствующего органа транспорта.
Следует иметь в виду, что приемка товаров, поступивших в исправной таре, по массе нетто и количеству товарных единиц в каждом месте производится, как правило, на складе конечного получателя. Приемка товаров по количеству производится в установленные сроки.
Своевременно произведенной приемка считается в том случае, когда проверка количества товаров окончена в условленные сроки.
Руководство склада обязано создать такие условия для правильной и своевременной приемки товаров, при которых обеспечивалась бы их сохранность и предотвращалась возможность образования недостач и хищений. Лица, осуществляющие приемку, должны хорошо знать правила приемки товаров, установленные соответствующими нормативными документами и договором поставки. С целью предупреждения нарушений правил приемки товаров руководству необходимо систематически контролировать работу лиц, производящих ее.
Работникам склада следует обеспечить точное определение количества поступивших товаров, то есть их массы, количества мест (ящиков, мешков, связок, кип, пачек и т. п.). Оно определяется в тех же единицах измерения, которые указаны в сопроводительных документах. Причем, если в документах отправитель указал массу товаров и количество мест, то получатель при приемке должен проверить и то, и другое.
В случае обнаружения недостачи дальнейшая приемка приостанавливается, обеспечивается сохранность товаров, и принимаются меры по предотвращению их смешения с другими однородными товарами. О выявленной недостаче товаров составляется акт за подписями лиц, производивших приемку.
Если при приемке товаров будет выявлено несоответствие массы брутто отдельных мест массе, указанной в транспортных или сопроводительных документах либо на трафарете, то вскрытие тары и упаковки в таких случаях производиться не должно. Одновременно с приостановлением приемки получатель обязан вызвать для участия в ее продолжении и составлении двустороннего акта представителя отправителя или изготовителя (если товары поступили в ненарушенной таре изготовителя, не являющегося отправителем).
Представитель отправителя (изготовителя) может принимать участие в приемке только при наличии у него удостоверения, дающего на это право.
Отправитель (изготовитель) может уполномочить на участие в приемке товаров предприятие, находящееся в месте их получения. В этом случае удостоверение представителю выдается предприятием, выделившим его. В удостоверении должна быть ссылка на документ, которым отправитель уполномочил данное предприятие участвовать в приемке товаров.
С согласия отправителя (изготовителя) предприятие — получатель может произвести одностороннюю приемку товаров.
Если при приемке с участием представителя отправителя (изготовителя) будет выявлена недостача товаров против данных, указанных в транспортных или сопроводительных документах, то результаты приемки товаров оформляются актом. Он составляется в тот же день, когда недостача выявлена. В случае, когда работа по приемке прерывалась, в акте делается соответствующая запись с указанием вызвавших это причин и условий хранения товаров во время перерыва.
Если при приемке одновременно будут выявлены не только недостача, но и излишки товаров, то в акте указываются точные данные об этих излишках.
Акт должен быть подписан всеми лицами, участвовавшими в приемке. При этом они вправе удостоверять своей подписью только те факты, которые были установлены с их помощью. Лицо, не согласное с содержанием акта, обязано его подписать с оговоркой о несогласии и изложить свое мнение. За подписание акта, содержащего не соответствующие действительности данные, лица, принимавшие участие в приемке товаров, несут установленную законом ответственность. Запись о предупреждении об этом, участвующих в приемке лиц должна быть сделана перед их подписями.
Не позднее, чем на следующий день после составления акта он утверждается руководителем или заместителем руководителя предприятия-получателя.
В случаях выявления в результате приемки фактов злоупотреблений или хищений товаров руководитель или заместитель руководителя предприятия-получателя обязан немедленно сообщить об этом органам МВД или прокуратуры и направить им соответствующие документы.
После проверки по количеству товары помещаются в помещение для распаковки и проверки их по качеству.
Распаковка и приемка товаров по качеству.
Операцию распаковки осуществляют для проверки качества полученного товара. Иногда в таре находятся по-разному упакованные товары, в этом случае также требуется распаковка.
Качественная проверка товаров способствует лучшей организации хранения, учета и последующего отпуска товара со склада.
Распаковка позволяет организовать упорядоченное складирование товаров на складе и сокращает время выполнения заказов потребителей.
Приемка товаров по качеству проводится для выявления соответствия качества поступивших на склад товаров требованиям стандартов, технических условий, условиям договора, а для некоторых товаров — образцам-эталонам и т. д. Одновременно с приемкой товаров по качеству производится проверка их комплектности, а также тары, упаковки и маркировки.
Товары, поступившие в исправной таре, принимаются по качеству и комплектности, как правило, на складе конечного получателя. Поэтому на складе оптового предприятия такие товары могут не приниматься по качеству, если они переотправляются покупателям в таре или упаковке изготовителя или первоначального отправителя. Однако проведение приемки является обязательным, если это предусмотрено договором, а также при получении товаров в поврежденной, открытой или немаркированной таре, в таре с поврежденной пломбой или при наличии признаков порчи (течь, бой и т. д.).
Приемка товаров по качеству и комплектности может производиться и на складе поставщика, но лишь в случаях, предусмотренных в договоре.
Сроки приемки товаров по качеству могут быть предусмотрены договором поставки либо установлены стандартами или техническими условиями для отдельных видов товаров. Приемка считается произведенной своевременно, если проверка качества и комплектности товаров окончена в установленные сроки.
На складе необходимо создать такие условия для правильной и своевременной приемки товаров по качеству, при которых обеспечивалась бы сохранность товаров и предотвращалась их порча. Следует своевременно проверять средства испытания и измерения, которыми определяется качество товаров, и следить за их исправностью.
Проведение приемки товаров возлагается на компетентных лиц в точном соответствии со стандартами, техническими условиями, другими обязательными для сторон правилами, а также по сопроводительным документам, удостоверяющим качество и комплектность поставленных товаров (технический паспорт, сертификат, счет-фактура, спецификация и т. п.). Как правило, при приемке товаров производится сплошная проверка их качества и комплектности. Выборочная проверка с распространением результатов проверки качества какой-либо части товаров на всю партию допускается в случаях, предусмотренных стандартами, техническими условиями или договором.
В целом же, процедура проверки товаров по качеству аналогична описанной выше приемки по количеству.
Составленные по результатам приемки товаров акты являются документами, подтверждающими невыполнение поставщиком (отправителем, изготовителем) условий договора. Поэтому они служат основанием для предъявления ему претензий.
Технология хранения товаров на складе.
Товары, принятые по количеству и качеству, из зоны приемки поступают в зону хранения.
Для перемещения товаров на хранение требуется:
— решить вопрос о том, какое количество товара разместить в активной складской зоне и какое — в резервной;
— определить необходимые для размещения товара размеры активного и резервного складского пространства;
— распределить товары по маркировке;
— определить место хранения товара;
— переместить товар к отведенному на складе месту.
Правильная технология хранения товаров на складе предусматривает:
— рациональное их размещение и укладку;
— создание и поддержание оптимальных условий хранения.
Передвижение и укладку товаров в пределах выбранной зоны осуществляют работники отдела приема склада. При выборе места хранения товара учитывается количество и частота поступления товаров. Решения о размещении определенного количества товара в активной или резервной зоне принимается отдельно по каждому товарному наименованию.
В практике складов принято бункеры активной зоны хранения пополнять запасами из резервных зон, а резервные зоны наполнять новыми товарами по мере их поступления. При таком порядке осуществляется расходование запасов в порядке их прихода на склад.
Для каждого наименования товара устанавливается определенная зона хранения. Товар перемещается в выделенную зону и укладывается.
Размещение и укладка товаров зависят от принятого на складе способа хранения. Наливные товары (олифа, бензин, растительное масло и др.) хранят в баках, бочках, цистернах. Для хранения многих продовольственных и некоторых непродовольственных товаров применяются контейнеры. В них товары могут доставляться непосредственно в магазины.
Чаще всего на складах применяют два способа хранения товаров — стеллажный и штабельный, выбор которых зависит от формы товара и тары, массы каждого тарного места, физических свойств товаров и других факторов. Предпочтение отдается такому способу укладки, при котором не допускается повреждение товара и тары, более рационально используются складские помещения и оборудование, создаются удобства для контроля за состоянием товарных запасов.
Штабельную укладку применяют при хранении различных продовольственных и непродовольственных товаров, затаренных в мешки, кипы, кули, ящики, бочки. При формировании штабеля необходимо следить за тем, чтобы он был устойчивым, соответствовал определенным нормам по высоте и обеспечивал свободный доступ к товарам. Высота штабеля зависит от свойств товара и его упаковки, применяемых средств механизации, предельной нагрузки на 1 кв. м пола, высоты складских помещений.
Различают три способа штабельной укладки товаров: прямой, в перекрестную клетку, в обратную клетку.
При прямой укладке расположение каждого верхнего затаренного места совпадает с расположением каждого места в нижнем ряду. Такой способ применяется при штабелировании товаров, затаренных в ящики. Для повышения устойчивости штабеля может применяться прямая пирамидальная кладка, при которой в каждом верхнем ряду число затаренных мест сокращается на единицу и каждое место, расположенное в верхнем ряду, опирается на два нижних, этот способ укладки удобен при штабелировании бочек.
В перекрестную клетку осуществляется кладка товаров, затаренных в ящики различных размеров. При этом ящики верхнего ряда укладываются поперек ящиков нижнего ряда.
Товары, затаренные в мешки, укладывают, как правило, в обратную клетку, т. е. каждый следующий ряд мешков размещают на предыдущий в обратном порядке.
При укладке товаров в штабеля необходимо следить за тем, чтобы в складском помещении обеспечивалась нормальная циркуляция воздуха и выполнялись санитарные требования. С этой целью штабеля должны размещаться не ближе чем 0,5 м. от внешней стены и 1,5 м. от отопительных приборов. Между штабелями должны быть проходы шириной около 1,5 м.
Товары, доставленные в места хранения не на поддонах, укладывают в штабеля на подтоварники, что обеспечивает нормальную циркуляцию воздуха. Более эффективным является штабельное хранение товаров, уложенных на различные виды поддонов, что позволяет не только рациональнее использовать складские помещения, но и широко применять для внутрискладской переработки грузов средства механизации погрузочно-разгрузочных работ.
Широкое распространение получил стеллажный способ укладки товаров на хранение. При этом способе распакованные товары, а также товары во внешней таре различными способами (рядами, десятками и т. д.) укладывают на стеллажи. Наиболее эффективно стеллажное хранение товаров, уложенных на поддоны. Оно обеспечивает широкое применение подъемно-транспортных механизмов, создает хорошие условия для повседневного оперативного учета товаров. Стеллажное хранение товаров позволяет более рационально использовать емкость склада, так как при помощи вилочных погрузчиков или кранов-штабелеров товары можно укладывать на полках, расположенных на максимальной высоте. Так, применение высокостеллажных электроштабелеров с вилочным захватом, которые способны выполнять работу по складированию на высоте 10−12 м. и более, позволяет максимально использовать емкость складских помещений.
Укладка товаров на стеллажи осуществляется по вертикали, что позволяет рационализировать процесс их отборки. На нижних полках размещают товары, отпускаемые небольшими партиями, отборка которых осуществляется вручную, на верхних — товары, отпускаемые партиями не менее одного поддона.
При укладке товаров на хранение необходимо придерживаться следующих основных требований:
— однородные товары должны быть уложены в стеллажи по обе стороны одного прохода;
— при укладке товаров вручную их следует размещать в ячейках стеллажей по вертикали, с тем, чтобы они находились в одной или в нескольких рядом расположенных секциях;
— на верхних ярусах стеллажей должны размещаться товары длительного хранения, а также товары, отпускаемые со склада крупными партиями;
— тарные места должны укладываться (при любом способе хранения) маркировкой наружу.
Рациональная организация хранения товаров достигается не только правильным выбором способа хранения, но и системой размещения товаров на складе.
Такая система предусматривает закрепление за каждой товарной группой или отдельным видом товара постоянных мест хранения (площадок, стеллажей, секций, ячеек и т. д.). При этом важно учитывать частоту и очередность поступления и отпуска товаров, сроки и условия их хранения, габариты и массу тарных мест, соблюдать правила товарного соседства.
Товары с высокой оборачиваемостью, а также крупногабаритные и тяжелые товары следует располагать ближе к выходу и участку комплектования заказов. И наоборот — товары, редко поступающие на склад, должны храниться вдали от входа и выхода зоны хранения. То же самое относится и к товарам сезонного хранения, длительное время хранящимся на складе.
Товары с сильным запахом нельзя хранить рядом с товарами, воспринимающими посторонние запахи, а гигроскопичные (легко поглощающие влагу) — с товарами, имеющими большой процент влаги.
Изолированно хранят на складе горючие и легковоспламеняющиеся товары.
Для ускорения работ по размещению товаров на местах хранения при их поступлении на склад и облегчения их поиска при последующей отборке каждому месту хранения присваивается собственный код. Цифровое или буквенно-цифровое обозначение наносится краской на ячейки стеллажей. Кроме того, на каждом стеллаже крепится табличка с его номером и символом хранящихся товаров.
Схемы размещения стеллажей с указанием кодов вывешиваются в зоне хранения на видном месте. Независимо от способа хранения товаров они укладываются маркировкой наружу, что также упрощает процесс отборки товаров.
Как уже отмечалось, помимо рационального размещения товаров на складе необходимо создать оптимальные условия для их хранения. С этой целью следует постоянно следить за температурой и влажностью воздуха внутри помещений склада и поддерживать их на уровне, установленном стандартами и санитарными правилами для отдельных групп товаров. Причем, нельзя допускать их резких перепадов. Контроль за температурой воздуха осуществляют при помощи термометров или универсальных блочных систем дистанционного контроля, представляющих переносные приборы, при помощи которых в течение 3−4 мин. можно определить температуру в 12 точках хранилища.
Для измерения влажности воздуха на складах применяется психрометрический метод, с помощью которого определяется относительная влажность воздуха. Она рассчитывается как процентное отношение абсолютной влажности к максимальной. При этом под абсолютной влажностью следует понимать количество граммов водяных паров, содержащихся в 1 куб. м. воздуха, а под максимальной — количество граммов водяных паров, которые могут насытить 1 куб. м. воздуха при данной температуре.
Регулирование температуры и относительной влажности воздуха проводится при помощи отопления и вентиляции. Для понижения относительной влажности можно также использовать влагопоглощающие вещества.
За товарами, хранящимися на складах, должны быть обеспечены постоянное наблюдение и уход. Необходимо регулярно проверять состояние товаров, обращая при этом внимание на появление признаков порчи, следов грызунов и насекомых. Товары, уложенные в штабеля, должны периодически перекладываться: верхние — вниз, нижние — вверх. Сыпучие товары следует перелопачивать. Изделия из шерсти, меха необходимо предохранять от повреждения молью, отсыревшие товары следует просушивать и проветривать.
Соблюдение оптимальных режимов хранения товаров, регулярный осмотр и аккуратное обращение с ними позволяют не только снизить потери товаров из-за их порчи, боя, лома, но и уменьшить естественную убыль в результате усушки, выветривания, утечки.
Для поддержания необходимых санитарно-гигиенических условий на складе должны регулярно проводиться уборки и мероприятия по уничтожению микробов (дезинфекция), насекомых (дезинсекция), грызунов (дератизация) и стойких запахов (дезодорация).
Организация и технология отпуска товаров со склада.
Операции по отпуску товаров составляют заключительную часть складского технологического процесса. От правильности их организации зависит рациональное и своевременное снабжение розничной торговой сети товарами в необходимом количестве и ассортименте.
Эти операции включают в себя:
— отборку товаров с мест хранения;
— комплектование и упаковку отобранных товаров;
— оформление документов и передачу подготовленных товаров в экспедицию;
— погрузку товаров и их отправку в розничную торговую сеть.
Перечисленным операциям предшествует работа по организации продажи товаров оптовым покупателям (магазинам и др.). При этом могут быть использованы различные методы оптовой продажи товаров, например, — посредством передвижных складов и разъездных товароведов, мелкооптовая посылочная торговля и некоторые другие.
При реализации сложного ассортимента товаров или товаров, ранее неизвестных покупателям, целесообразно организовать их продажу с личной отборкой представителем розничного торгового предприятия. При этом методе продажи покупатели прибывают на склад по заранее согласованному графику и самостоятельно выбирают товары, выставленные в зале товарных образцов.
Зал товарных образцов представляет собой обособленное помещение склада, оснащенное специализированной торговой мебелью (стеллажами, горками, подиумами и др.), средствами рекламы и информации. Площадь зала разделена оборудованием на отдельные участки, на каждом из которых представлены образцы товаров одной или нескольких товарных групп. При этом каждой товарной группе отводится определенное место, что позволяет постоянным покупателям быстро находить нужные товары. Здесь же находятся рабочие места товароведов-коммерсантов.
Данные обо всех товарах, поступающих на склад, заносятся в карточки количественно-стоимостного учета.
Находящиеся в зале товарных образцов передвижные картотеки с такими карточками позволяют товароведам иметь постоянную и полную информацию о наличии на складе товаров. Это, в свою очередь, способствует своевременной информации покупателей посредством списков о имеющихся в наличии товаров, которые регулярно рассылаются розничным торговым предприятиям.
Следует отметить, что товары простого ассортимента, как правило, не требуют их личной отборки покупателем, а заказы на них могут передаваться, например, по телефону. На основании полученных заказов покупателей выписываются отборочные листы и счета-фактуры, в соответствии с которыми происходит отборка товаров с мест их хранения и заполнение товарно-транспортных накладных. Причем, отборочные листы и счета-фактуры, оформленные таким образом, при котором последовательность записи в них товаров соответствует порядку размещения их в секциях стеллажей, в штабелях значительно облегчают отборку товаров работниками склада.
Различают механизированную и ручную отборку товаров с мест хранения.
Механизированная отборка применяется в основном на крупных складах. При этом груз, спакетированный на поддоне, снимается с помощью механизма с места укладки и в виде целой транспортной единицы перемещается в зону комплектования заказов.
Ручная отборка осуществляется при отпуске небольшого количества товаров, мелкоштучных товаров сложного ассортимента, хранимых на стеллажах.
На складах применяют два метода отборки товаров — индивидуальный и комплексный.
Индивидуальная отборка ведется по отборочному листу, выписанному для одного покупателя. При этом отборщик, обходя секции стеллажей, отбирает требуемое количество товаров и укладывает их на поддон, тележку или контейнер, которые затем перемещаются на участок комплектования. Как правило, индивидуальная отборка производится вручную.
Комплексная отборка позволяет отбирать товары одновременно для нескольких покупателей. Товары при таком методе изымаются с мест хранения последовательно для всей партии заказов согласно сводному отборочному листу, заранее составленному в зале товарных образцов. Рассортировка отобранных таким образом товаров по отдельным заказам производится в дальнейшем на участке комплектования. Применение комплексной отборки позволяет повысить производительность труда работников склада за счет использования средств механизации, так как товары отбираются, как правило, целыми поддонами, контейнерами.
Отобранные товары доставляются в зону комплектования заказов покупателей, где проверяется правильность отборки товаров в соответствии с заказами покупателей. Затем товары укладывают в инвентарную тару отдельно для каждого магазина. В качестве инвентарной тары используются специальные разборные ящики, брезентовые мешки и т. д. В последнее время широкое распространение получили контейнеры на роликах грузовместимостью 0,5 и 1,25 т. Контейнеры приспособлены для захвата их вилочными погрузчиками. Их погрузка и выгрузка может производиться бортподъемником грузовой автомашины.
Перед пломбированием тарных мест в них вкладывается один экземпляр заполненного упаковочного ярлыка. Он выписывается работником склада на каждое отдельное место, подписывается материально ответственными лицами и упаковщиком. Второй экземпляр ярлыка (с указанием массы каждого места) прилагается к счету-фактуре, а третий — остается на складе.
Опломбированную инвентарную тару перемещают в экспедицию, где происходит помаршрутное комплектование партий товаров в соответствии с расположением розничных торговых предприятий на маршруте. Формирование помаршрутных отправок должно происходить с учетом максимального использования грузоподъемности автотранспорта и минимального его пробега.
Учет принимаемых в экспедицию со склада и отправляемых покупателям товаров ведется в специальном журнале. В нем указывается наименование покупателя, номер, дата оформления и сумма счета-фактуры, количество мест, подлежащих отправке, номера тары. После возврата счета-фактуры с распиской получателя товаров в журнале делается соответствующая отметка.
Из экспедиции товары с помощью вилочных погрузчиков, электротележек и других средств механизации перемещают в зону погрузки транспорта, откуда происходит их доставка к месту назначения.
Таким образом, рассмотрев теоретические аспекты организации технологического процесса, проследим его организацию на примере склада связи. А именно рассмотрим приемку, хранение и отпуск техники связи и комплексов средств автоматизации (далее — КСА).
2. АНАЛИЗ ОРГАНИЗАЦИИ ТЕХНОЛОГИЧЕСКОГО ПРОЦЕССА НА СКЛАДАХ ВООРУЖЕННЫХ СИЛ РЕСПУБЛИКИ БЕЛАРУСЬ (НА ПРИМЕРЕ СКЛАДА ИНЖЕНЕРН-ТЕХНИЧЕСКОГО ИМУЩЕСТВА)
2.1 Организационно — техническая характеристика склада инженерно-технического имущества Склады ИТИ предназначаются для приема, хранения, отправки, размещения запасов, технического обслуживания, ремонта, контроля качественного состояния, учета и охраны инженерной техники и средств инженерного вооружения (далее — ВВТ).
По предназначению они подразделяются на центральные склады, склады видов Вооруженных Сил, оперативных (оперативно-тактических) командований и войсковые склады.
По месту дислокации склады подразделяются на стационарные и полевые (подвижные). Стационарные склады создаются в районах постоянной дислокации войск, полевые развертываются в военное время, а также при проведении учений, маневров.
Склады представляют собой воинские части (подразделения) с определенной организационно-штатной структурой, с размещенными на их территории хранилищами для техники и имущества, ремонтными цехами, зданиями и сооружениями охраны, обслуживания и вспомогательных служб.
Движение материальных средств на складах проводится только по указанию (разнарядкам, нарядам) непосредственных начальников в соответствии со схемой обеспечения воинских частей и формирований Склады содержатся по различным штатам в зависимости от разрядности, назначения, объема производственной и операционной деятельности.
В состав складов могут входить следующие основные подразделения (рисунок 3):
Рисунок 3 — Структура склада Примечание — Источник: собственная разработка Основные задачи складов (рисунок 4):
Рисунок 4 — Задачи склада Примечание — Источник: собственная разработка Склад занимает территорию, на которой расположены места хранения, комплекс оборудования и вспомогательные помещения, обеспечивающие прием, хранение, техническое обслуживание, ремонт и выдачу материальных средств.
Территория склада делится на техническую и административно-хозяйственную. Техническая территория делится на зону хранения и технологическую зону по обслуживанию и ремонту техники. В зоне хранения располагаются места хранения, погрузочные и разгрузочные платформы. В технологической зоне по обслуживанию и ремонту техники располагаются мастерская, пункты технического обслуживания и консервации техники, зарядная база, технологическая линия.
На административно-хозяйственной территории размещаются здание управления склада, караульное помещение, пожарное депо, хозяйственные мастерские, хозяйственные склады, гаражи, столовая и клуб, санитарная часть и жилые постройки.
В зависимости от требований по обеспечению условий хранения материальных средств на технической территории склада оборудуются места хранения (рисунок 5).
Хранилища должны соответствовать виду и габаритным размерам изделий, обеспечивать поддержание условий хранения, заданных для данного типа хранилищ и изделий, удобство размещения и наблюдения за изделиями, проведение работ по поддержанию их в исправном состоянии, быстроту приема и выдачи.
Хранилища классифицируются:
а) по степени соответствия условиям хранения:
закрытые отапливаемые;
закрытые неотапливаемые, позволяющие обеспечивать укрытие материальных средств от непосредственного воздействия природных факторов (солнца, осадков). Кроме того, местами хранения являются навесы открытые и закрытые с одной-трех сторон, позволяющие укрывать материальные средства от непосредственного воздействия природных факторов, а также открытые площадки.
б) по расположению:
наземные (стационарные и сборно-разборные);
полуподземные;
подземные.
в) по степени огнестойкости и долговечности основных конструктивных элементов:
капитальные (имеющие кирпичные, каменные, бетонные, железобетонные, шлакобетонные, металлические, шиферные и металлошиферные конструкции основных несущих элементов (фундаменты, стены, опоры, перекрытия, крыши);
некапитальные (имеющие деревянные сборно-щитовые, каркасно-засыпные конструкции основных несущих элементов).
г) по назначению:
специальные;
универсальные;
приспособленные помещения различного назначения.
д) по оборудованию:
оборудованные рампами, разгрузочными платформами и площадками;
имеющие подъездные пути (железнодорожные, автомобильные с искусственным или грунтовым покрытием);
оснащенные стационарными средствами механизации;
без стационарных средств механизации.
Оптимальными условиями хранения являются:
— температура окружающей среды от +5 до +15?С перепад температуры допускается не более 5? С в сутки;
— относительная влажность воздуха в пределах 40−55%;
— отсутствие осадков, ветра и конденсации влаги, пыли, песка, коррозийно-активных реагентов, воздействия прямого солнечного излучения и биологических факторов.
Для отдельных видов изделий в зависимости от особенностей их конструкции оптимальные значения температуры и влажности могут отличаться от указанных. Хранилища с регулируемыми параметрами атмосферы (с кондиционированием воздуха) проектируются и строятся с учетом поддержания в них оптимальных условий хранения. В отапливаемых хранилищах поддерживаются допустимые условия, приближающиеся к оптимальным, с учетом использования всех возможностей данного хранилища и местного климата.
В зависимости вида изделий хранилища подразделяются на универсальные и специализированные. Универсальные хранилища предназначены для любых видов изделий, которые разрешается хранить совместно, специализированные — для хранения определенных видов изделий. Здания хранилищ рекомендуется строить из огнеупорных материалов. Деревянные конструкции хранилищ должны быть обработаны огнестойким составом, а места их соприкосновения с грунтом — антисептиком.
В хранилищах (или на группу хранилищ) должны быть предусмотрены:
участок для ввоза, распаковки и упаковки изделий с подъездными путями для транспорта;
тамбур для выдерживания изделий, поступающих на хранение в холодное время года (для отапливаемых хранилищ и хранилищ с регулируемыми влажностью и температурой);
участок для проведения технического обслуживания;
рабочие места для личного состава и начальника хранилища;
кладовые для хранения инвентаря, инструмента, специальной и верхней одежды.
Емкость складов определяется размерами всех хранилищ и исчисляется в кубических метрах объема хранилищ, квадратных метрах площади пола хранилищ и количеством техники, которая может быть размещена на складе.
Количество материальных средств в хранилищах исчисляется в условных 20-тонных железнодорожных вагонах. При определении емкости склада учитывается только полезная площадь или объем хранилищ, то есть только помещения, где должны храниться материальные средства, и не учитывается площадь (объем) вспомогательных помещений.
Ворота (двери) хранилищ должны открываться наружу или быть раздвижными и по конструкциям и габаритам обеспечивать возможность использования средств механизации складских работ. Количество ворот зависит от вида изделий, емкости хранилищ, требований пожарной безопасности склада. Кроме наружных ворот рекомендуется иметь вторые (внутренние решетчатые) ворота или люки в нижней части наружных ворот для обеспечения искусственной вентиляции.
Полы хранилищ должны иметь:
поверхность, стойкую к образованию крошки, песка;
выдерживать нагрузку, создаваемую изделиями, устанавливаемыми на хранение, и средствами механизации складских работ, быть удобными для уборки.
Неровности, выбоины, трещины и другие повреждения полов должны своевременно устраняться. Крупногабаритную технику допускается размещать в хранилищах, имеющих грунтовые полы, на подставках или лежнях. Пороги наружных ворот хранилищ для предохранения от затекания поверхностных вод должны быть выше уровня отмостков и иметь защитные легкосъемные козырьки от проникновения грызунов. Окна хранилищ должны быть застеклены, иметь форточки и защитные механические решетки или сетки. Стекла окон в зависимости от требуемых условий хранения должны быть окрашены в белый цвет или закрыты шторами (ставнями) для защиты изделий от солнечной радиации. Для регулирования температуры и влажности внутри хранилищ должна быть предусмотрена искусственная или естественная вентиляция. Необходимость вентиляции и ее схема должны определяться в зависимости от характера изделий, размещенных на хранение, емкости и планировки хранилищ, а также режима хранения. Полуподземные и подземные хранилища, не имеющие устройства для сквозного проветривания, должны быть оборудованы искусственной вентиляцией, имеющей вытяжные вентиляционные трубы с дверцами, снабженными запорными устройствами и клапанами, позволяющими их открывать и закрывать в нужных случаях.
Отопление хранилищ должно быть центральным. В исключительных случаях по согласованию с представителем службы противопожарной защиты допускается печное отопление.
Освещение в хранилищах может быть естественным или искусственным (электрическим). При электрическом освещении электропроводка должна быть безопасна в пожарном отношении. Освещение в хранилищах, предназначенных для легковоспламеняющегося имущества и всех видов смазочных материалов, как правило, должно быть естественным. Применение электрического освещения допускается только с использованием взрыво-пожаробезопасной проводки и арматуры.
Для размещения переносной техники хранилища должны оборудоваться стеллажами, шкафами, поддонами, подставками, подкладками и тому подобными, конструктивно обеспечивающими нормальное ее хранение. Стеллажное оборудование должно устанавливаться с расчетом наиболее эффективного использования внутреннего объема мест хранения, обеспечения естественного освещения и наибольших удобств для наблюдения за хранящимися материальными средствами и выполнения необходимых операций.
Стеллажи делятся на универсальные, пригодные для хранения различных типов техники, и специализированные, предназначенные для хранения только определенных видов техники. По конструкции стеллажи могут быть полочные, клеточные и ящичные, поддоны — плоские, ящичные и стоечные. Стеллажи, шкафы для укладки материальных средств нумеруются римскими цифрами, полки сверху вниз обозначаются прописными буквами, клетки слева направо нумеруются арабскими цифрами. Высота и длина стеллажей и шкафов определяются габаритами помещения, в котором они устанавливаются, ширина стеллажей может быть от 1 до 1,5 м в зависимости от габаритов материальных средств, предназначенных для укладки на них. При широких стеллажах материальные средства укладываются с обеих сторон. Стеллажи и поддоны устанавливаются на расстоянии не менее 0,6 м от стен. Проход между стеллажами должен быть 0,8 — 1,5 м в зависимости от хранящихся материальных средств. Посередине хранилища (как правило, вдоль осевой линии) оставляется главный проход шириной 1,5 — 2 м. В тех случаях, когда двери (ворота) расположены в продольных стенах, необходимо оставлять проход между ними во всю ширину дверей (ворот) поперек хранилища. Для хранения мелких изделий в стеллажах или шкафах делаются выдвижные ящики, на наружной стороне которых закрепляются ярлыки с наименованиями хранящихся изделий и прикрепляются образцы мелких хранящихся изделий. Ящики нумеруются арабскими цифрами слева направо и сверху вниз по рядам. В отдельных случаях разрешается при большом количестве разнообразных деталей, уложенных в пачках, не вывешивать ярлыки и образцы на ящиках, а иметь в каждом ящике опись изделий. На пакетах должна быть маркировка, содержащая данные о массе пакета и груза в нем, числе грузовых мест в пакете. В первой строке маркировки наносится надпись: «Маркировка пакета». На наиболее видных местах стеллажей, полок, штабелей на каждый вид и категорию хранящихся материальных средств должны быть вывешены ярлыки. Материальные средства, имеющие ограниченный срок годности, снабжаются стеллажными ярлыками на каждую поступившую на хранение партию. На аппаратуру (партию), имеющую гарантию завода-изготовителя, вывешивается бирка с указанием даты окончания гарантийного срока.
Для хранения материальных средств могут использоваться навесы. Навесы располагаются на местности с ориентированием короткой или закрытой стороны в направлении преобладающих ветров. Полы навесов должны иметь уклон от середины к краям от 1 до 2?. При возвышении пола над поверхностью земли менее 0,2 м вокруг навесов должны быть устроены водоотводные канавы (кюветы). При отсутствии пола изделия должны располагаться только на подкладках, подставках и тому подобных. Деревянные конструкции хранилищ, стеллажей, навесов должны быть обработаны огнестойким составом, а места их соприкосновения с грунтом — антисептиком. Материальные средства могут храниться на специально оборудованных и необорудованных открытых площадках. Оборудованные площадки должны иметь твердое покрытие из бетона или асфальтобетона по всей территории или на участках хранения. Необорудованные площадки могут иметь улучшенное покрытие в виде уплотненного слоя гравийно-песчаной смеси на участке хранения и подъездах к нему. При удовлетворительном состоянии грунта, обеспечивающего проходимость машин, улучшенное покрытие может отсутствовать. При размещении открытых площадок на местности должны быть выполнены следующие требования:
— площадка должна располагаться на участке местности с незначительным уклоном (от 2 до 3?) естественного рельефа;
— уровень поверхности площадки должен быть выше уровня грунтовых вод не менее чем на 0,5 м. Грунт на площадке должен выдерживать давление не менее 5 кгс/см;
— площадка должна быть прямоугольной и, по возможности ориентирована короткой стороной в направлении преобладающих ветров;
— вокруг площадки должны быть устроены водоотводные канавы (кюветы);
— должна быть обеспечена возможность выезда техники без разворота.
Склад оборудуется подъездными железнодорожными путями нормальной колеи, которые, как правило, должны обеспечивать подъезды к нему с двух сторон. Техническая территория склада оборудуется кольцевыми дорогами для перевозки грузов, а также подъездными путями, обеспечивающими возможность свободного проезда машин к хранилищам. На местах пересечения дорог рельсовыми путями или осушительными канавами устраиваются надежные и удобные проезды. Дороги, переезды и подъезды к складам, хранилищам (навесам, открытым площадкам) должны содержаться в постоянной исправности, а зимой расчищаться от снега.
Для погрузочно-разгрузочных работ склад оборудуется погрузочно-разгрузочными платформами, навесами и обеспечивается подъемно-транспортным оборудованием, другими средствами механизации. Постоянные погрузочно-выгрузочные платформы и рампы строятся по типовым проектам, согласованным в органах военных сообщений. В зависимости от расположения относительно железнодорожных путей постоянные платформы могут быть боковые, торцовые, комбинированные и островные.
Вся территория склада должна быть ограждена двумя рядами проволочной изгороди высотой не менее 2 м, при этом первый ряд проволочной изгороди (внутренний) располагается не менее чем в 10 м от построек склада, второй ряд (внешний) — на расстоянии 20 — 30 м от первого ряда в зависимости от рельефа местности. При размещении склада в ненаселенной местности зона, расположенная на расстоянии 50 м перед внешней изгородью и между рядами изгороди, должна быть расчищена, при размещении склада в населенных пунктах его территории должна быть обнесена сплошным забором. Техническая территория склада обязательно огораживается забором высотой не менее 2 м. Территория разбивается на участки, ответственность за содержание, безопасность, исправность, противопожарное состояние и чистоту которых несут начальники отделов хранения, пунктов технического обслуживания, начальники (заведующие) хранилищ и другие должностные лица. Границы участков устанавливает начальник склада.
Вся территория склада должна содержаться в чистоте, обеспечивать необходимые условия для хранения и содержания материальных средств, боеготовность и пожарную безопасность склада, что достигается:
— систематическим наблюдением за состоянием помещения и устранением неисправностей;
— проведением ежегодных осмотров в целях определения необходимых ремонтов;
— своевременным проведением текущих и капитальных ремонтов.
Таким образом, склад связи представляет собой воинскую часть (подразделение) с определенной организационно-штатной структурой и размещенными на своей территории хранилищами для техники и имущества, ремонтными цехами, зданиями и сооружениями охраны, обслуживания, вспомогательных служб и предназначен для обеспечения других воинских частей (формирований) материальными средствами, в целях своевременного удовлетворения их потребностей в мирное и военное время.
2.2 Организация технологического процесса склада инженерно технического имущества
Прием ВВТ, доставленных силами транспортных органов Порядок приема ВВТ, как и других материальных средств, доставленных силами транспортных органов, определяется уставами соответствующих транспортных организаций и другими правовыми актами, действующими в народном хозяйстве и в Вооруженных Силах.
Уполномоченное должностное лицо железной дороги (пристани, аэропорта) обязано уведомить начальника склада о прибывшем в его адрес грузе не позднее 12 ч следующего дня. При несвоевременном уведомлении начальника склада он не несет ответственность за простой транспортных средств и склад освобождается от уплаты сбора за хранение груза до посылки уведомления. Начальник склада обязан организовать прием и вывоз со станции груза, прибывшего в адрес склада. Грузы могут храниться на станции назначения бесплатно в течение 24 ч. Срок хранения исчисляется с ноля часов суток, следующих за днем выгрузки груза с применением средств железной дороги или подачи вагонов под выгрузку с применением средств склада. За хранение груза сверх указанного срока взыскивается сбор в размере, предусмотренном тарифом.
При прибытии на склад ВВТ повагонно должностное лицо железной дороги должно уведомить об этом начальника склада за час до подачи вагонов при разгрузке их в пределах станции и за 2 часа при разгрузке на подъездных путях не общего пользования, в том числе на ветке склада. Прием ВВТ осуществляют члены комиссии склада в присутствии представителя транспортного органа. В состав комиссии, назначаемой приказом начальника склада, обязательно включаются начальник соответствующего отдела хранения и приемщик, имеющий доверенность на получение ВВТ.
ВВТ принимаются от представителя транспортного органа на основании сопроводительных документов. При их отсутствии члены комиссии склада принимают прибывшие ВВТ по транспортным документам, обращая особое внимание на соответствие количества мест прибывшего груза указанному в транспортной накладной количеству. При обнаружении неисправностей вагонов (контейнеров, люков трюмов судна) и нарушения пломб, а также при наличии дефектов в упаковке (таре) и признаков утраты или повреждения груза члены комиссии склада с участием представителя транспортного органа составляют коммерческий акт. Коммерческий акт также составляется при: прибытии груза без документов или документов без груза; обнаружении недостачи, превышающей нормы естественной убыли, и разницы в показаниях весоизмерительных приборов; несоответствии фактического количества и качества материальных средств данным сопроводительных документов; подаче груза на подъездной путь склада (к месту выгрузки) по истечении 24 часов после оформления в товарной конторе документов на получение ВВТ.
Порядок составления коммерческих актов и предъявления претензий в транспортные органы определяется соответствующими правовыми актами, а также правилами перевозки грузов. В коммерческом акте должно быть точное описание состояния груза и изложены обстоятельства, вызвавшие необходимость составления акта. В случае несоставления коммерческого акта и несвоевременного предъявления иска в транспортные органы за порчу или утрату груза ответственность несут члены комиссии склада, принявшие груз. В случае отказа представителя транспортного органа от составления коммерческого акта недостача или повреждение груза должны быть зафиксированы в акте комиссии склада в день принятия груза. Кроме членов комиссии акт подписывает представитель незаинтересованной организации или транспортной милиции.
При отсутствии расхождения между фактическим количеством и качеством поступивших ВВТ и данными сопроводительных документов, а также при поступлении груза в исправном вагоне с неповрежденными пломбами станции отправления или отправителя, без следов утраты или хищения председатель комиссии склада может потребовать от представителя транспортного органа проверки груза в пределах, предусмотренных правилами.
В случае получения ВВТ, прибывших повагонно, без проверки председатель комиссии склада обязан потребовать от представителя транспортного органа отметки на железнодорожной накладной за подписью начальника станции следующего содержания:
— для грузов, прибывших в крытом вагоне, — «Груз прибыл по настоящей накладной в исправном вагоне №____ за исправными пломбами станции отправления (отправителя) и выдан согласно Уставу железных дорог без проверки»;
— для грузов, прибывших в полувагонах и на платформах, — «Груз прибыл по настоящей накладной в исправном полувагоне (на платформе) №____ без следов утраты и хищений и выдан согласно Уставу железных дорог без проверки».
При приеме ВВТ, прибывших с караулом (сопровождающими), члены комиссии склада в присутствии начальника караула проводят осмотр прибывшего груза, обращая особое внимание на: соответствие количества мест данным, указанным в сопроводительных документах; наличие и целостность пломб. В случае обнаружения утрат, недостач (излишков), порчи, повреждения тары, неисправных пломб председатель комиссии склада обязан составить приемный акт с участием начальника караула. Один экземпляр акта вручается начальнику караула для передачи его в организацию, выделявшую караул, для возмещения ущерба, второй подшивается в дело склада. О составлении и вручении акта делается отметка в командировочном предписании начальника караула.
Прием ВВТ при их получении на другом складе и на предприятии промышленности склад товар приемка военный Получение ВВТ на складе объединения (центра) или на складе (базе) поставщика, а также на предприятии промышленности проводит приемщик склада получателя по предъявлении доверенности.
Прием ВВТ осуществляется по нарядам, выдаваемым в вышестоящем органе управления, или по нарядам, выписанным на складе (базе) поставщика (предприятии промышленности) по разнарядке указанного органа. Порядок ВВТ при их получении на складе поставщика и на предприятии промышленности определяется основными условиями поставки продукции для военных организаций, другими правилами, действующими в народном хозяйстве и в Вооруженных Силах.
На принятые ВВТ приемщику склада получателя представитель склада поставщика (предприятия промышленности) вручает второй экземпляр исполненного наряда, а на ВВТ, учитываемые по номерам и техническому состоянию, кроме того, и техническую документацию.
При получении техники связи и КСА приемщик склада получателя обязан:
— принимать ВВТ, упакованные на предприятии и имеющие пломбы военного представителя, по числу мест, проверяя при этом исправность упаковки, пломб и соответствие маркировки записям в накладной, выписываемой на предприятии;
— подвергать наружному осмотру неупакованные технику связи и КСА, которые принял военный представитель, и проверять их комплектность;
— принимать с полной проверкой комплектности, а в отдельных случаях выборочно на соответствие нормам технических условий, технику связи и КСА, не имеющих пломб военного представителя.
При получении техники связи и КСА на предприятии промышленности, где военный представитель отсутствует, приемщик склада получателя обязан проверить комплектность и соответствие их нормам технических условий. Выявленные недостатки приемщик склада получателя доводит до представителя предприятия поставщика для их устранения в установленный законодательством срок или полной замены изделия. При перевозке техники связи и КСА, полученных на предприятии, приемщик склада получателя отвечает за их количество, комплектность, целостность пломб и упаковки, сохранность.
Прием ВВТ непосредственно на складе от сдатчика грузоотправителя Прием ВВТ, доставленных на склад в сопровождении сдатчика грузоотправителя, проводится силами комиссии склада на основании нарядов по их фактическому количеству и качеству. При соответствии фактического количества и качества ВВТ данным наряда приемщик склада в нем указывает: «Груз принят». Роспись приемщика заверяется мастичной печатью склада с изображением Государственного герба Республики Беларусь.
В случаях обнаружения несоответствия количества или качества принимаемых ВВТ данным нарядов члены комиссии с обязательным участием сдатчика грузоотправителя составляют акт.
При отказе сдатчика грузоотправителя от участия в составлении и подписании акта в нем делается соответствующая запись с указанием его воинского звания, фамилии, имени и отчества и мотивов отказа.
Прием ВВТ от сдатчиков воинских частей (соединений) проводится по указанию руководителя (на основании наряда) органа управления, которому подчинен склад. ВВТ принимаются только с заполненными и оформленными формулярами (паспортами), а учитываемые по номерам и техническому состоянию, кроме того, и с актами. По прибытии на склад сдатчик грузоотправителя представляет в учетно-операционный отдел сопроводительные документы на сдаваемый груз для регистрации их в книге. В учетно-операционном отделе выписывается пропуск для ввоза груза на территорию склада.
Хранение ВВТ Хранение заключается в содержании ВВТ в установленных местах в исправном состоянии с применением средств и методов защиты от воздействия окружающей среды и проведением технического обслуживания. В зависимости от продолжительности хранение может быть кратковременным (продолжительностью до одного года) и длительным (продолжительностью год и более).
Поддержание постоянной готовности к применению и сбережение ВВТ при хранении обеспечиваются:
— созданием оптимальных условий хранения;
— правильным устройством, оборудованием, содержанием и использованием складских помещений (хранилищ);
— качественным приемом поступающих на хранение ВВТ, устранением выявленных в ходе приема недостатков;
— применением установленных средств и методов консервации;
— своевременным и качественным проведением технического обслуживания;
— проверкой должностными лицами состояния хранящихся ВВТ, качества консервации, а также состояния мест хранения;
— своевременным устранением выявленных в процессе проверки недостатков;
— правильным подбором материально ответственных лиц;
— надлежащей организацией общей и противопожарной охраны складов и соблюдением требований пожарной безопасности.
Распределение ВВТ по местам хранения проводит командир воинской части на основании:
— требований правовых актов о порядке хранения ВВТ;
— требований эксплуатационных документов по условиям хранения конкретных типов ВВТ;
— данных о защитных свойствах консервационных материалов, методах и способах консервации;
— конструктивных особенностей и габаритных размеров;
— возможности совместного хранения различных типов техники и материалов с учетом нейтральности и выполнения противопожарных требований;
— типа тары, ее прочности и устойчивости при многоярусной укладке в штабеля;
— фактического наличия складских помещений.
В отапливаемых хранилищах должны храниться ВВТ, имеющие в своем составе изделия электронной техники и электротехники, запасные части, инструмент и принадлежности (далее — ЗИП) к ним, радиотехническая аппаратура, средства измерений, электровакуумные и СВЧ-приборы, системы единого времени и эталонных частот, залитые электролитом и заряженные аккумуляторы. В исключительных случаях при недостатке отапливаемых хранилищ допускается хранение ВВТ в неотапливаемых хранилищах и под навесами.
В неотапливаемых хранилищах могут храниться антенные машины, средства механизации для прокладки линий связи, полевые кабели связи, силовые и высокочастотные кабели, различные виды проводов, источники питания электроэнергией (электростанции, электроагрегаты, генераторы), электротехнические изделия, двигатели внутреннего сгорания, изоляционные материалы, кислотные и щелочные аккумуляторы (сухие и сухозаряженные), лакокрасочные материалы и их растворители, кислоты, щелочи и химикаты.
Под навесами и на открытых площадках могут храниться антенно-мачтовые устройства, стационарные кабели для подземных и подводных линий связи, линейное имущество для строительства постоянных воздушных и подземных линий связи, прокат черных металлов.
ВВТ учитываются и хранятся комплектно. Отдельно разрешается хранить только те комплектующие изделия, которые требуют иных условий хранения (приведенные в рабочее состояние аккумуляторные батареи, средства измерений). Запрещается хранение совместно с ВВТ приведенных в рабочее состояние аккумуляторных батарей и агрессивных материалов.
ВВТ, имеющие гриф секретности, должны быть размещены в отдельном специально оборудованном помещении и храниться в порядке, установленном соответствующими правовыми актами.
Возимое имущество подвижных объектов ВВТ должно храниться в одном боксе (хранилище) с ними. Прицепы размещаются вместе с буксирующими их машинами.
Учебные ВВТ размещаются на отдельных стеллажах, в шкафах или штабелях, на которых должна быть надпись «Учебная».
Переносные ВВТ, имеющие укладочные ящики, хранятся в кладовых подразделений в штабелях, а без укладочных ящиков — на специальных стеллажах или в шкафах.
Постановка ВВТ на длительное хранение и их освежение оформляются актом закладки (освежения). Длительное хранение ВВТ организуется отдельно от ВВТ текущего обеспечения. При этом должен быть исключен доступ к ним посторонних лиц, а также лиц суточного наряда. Входы в хранилища (площадки) пломбируют или опечатывают печатями или пломбами, предназначенными только для хранилищ ВВТ длительного хранения, начальники (заведующие) складов (хранилищами, площадками) или начальники соответствующих служб. Указанные печати или пломбы хранятся у лиц, ответственных за хранение техники связи и КСА.
ВВТ, хранящиеся на складах, должны размещаться пономенклатурно с учетом специализации отделов хранения, количества и состояния имеющихся складских помещений.
ВВТ, заложенные на длительное хранение в воинских частях, должны размещаться по командам (воинским частям, формированиям) и литерам (подразделениям).
Все ВВТ, находящиеся на длительном хранении, должны быть законсервированы.
В зависимости от типа ВВТ, условий и мест хранения их консервация осуществляется одним из следующих методов:
— герметизацией с применением влагопоглотителя-силикагеля;
— герметизацией с применением ингибиторов коррозии и силикагеля или только ингибиторов коррозии;
— нанесением защитных покрытий;
— комбинированными методами, заключающимися в сочетании вышеуказанных методов и других современных методов консервации.
На каждый законсервированный комплект ВВТ составляются карточка консервации и технологическая карта расконсервации и подготовки к использованию, которые хранятся в полиэтиленовом конверте, закрепленном вне герметизированного объема. На однотипные переносные ВВТ, имеющие общую дату консервации, составляется одна карточка консервации.
Хранение ВВТ, размещенных на средствах подвижности ВВТ, размещенные на средствах подвижности, устанавливаются на хранение с учетом максимального использования площади хранилища в один или два ряда друг за другом в направлении ворот. При этом должны соблюдаться следующие минимальные расстояния:
— от стены до кормы гусеничной базовой машины (задней части транспортного средства) — 1 м;
— между боковыми бортами гусеничных базовых машин и стеной или колонной — 1 м;
— между боковыми бортами колесных базовых машин и стеной или колонной — 0,8 м;
— между передней частью гусеничной (колесной) базовой машины и воротами — 0,7 м;
— между гусеничными (колесными) базовыми машинами в ряду — 1,5 м;
— между рядами гусеничных (колесных) базовых машин — 1 м.
Высота помещений для хранения техники ракетно-артиллерийского вооружения, бронетанковых вооружения и техники от пола до выступающих элементов покрытий должна быть на 1 м больше высоты наиболее высокого образца техники, но не менее 3,6 м.
Высота помещений для хранения колесных базовых машин от пола до выступающих элементов покрытий должна быть на 0,2 м больше высоты наиболее высокого колесного автомобиля, но во всех случаях не менее 2 м.
При двустороннем расположении ворот хранилищ разрешается устанавливать машины в четыре ряда: два — в направлении одних ворот и два — в противоположном направлении.
Под навесами машины хранятся в таком же порядке, что и в хранилище.
Машины на открытых площадках размещаются группами не более чем по 80 единиц. Расстояние между группами машин и от крайней машины до зданий устанавливается не менее 20 м. Расстояние между рядами в группе, ориентированными в одном направлении, должно быть не менее 10 м. с интервалом в ряде 1,5 — 2 м. Автомобили, артиллерийские тягачи, прицепы в составе поезда (тягач-прицеп) располагаются только в два ряда (тягачами в противоположные стороны). При этом расстояние между рядами сокращается до 3 м., а емкость площадок должна составлять не более 30 единиц техники.
При размещении ВВТ, установленных на средствах подвижности, в хранилищах и под навесами в два ряда и более машины второго ряда сцепляются буксирными тросами с машинами первого ряда. Буксирные тросы надеваются на буксирные крюки машин первого ряда и укладываются впереди машин (выводятся и крепятся на лицевой стороне ворот хранилищ).
Специальные автомобили и бронетанковые базовые машины, находящиеся на длительном хранении, должны быть установлены на металлических или деревянных подставках (козлах) так, чтобы колеса были подняты от уровня пола (грунта) на 8 — 10 см. На мягком грунте под подставки подкладываются для устойчивости отрезки досок. Рессоры разгружаются путем установки между рамой и осями устройств для разгрузки рессор или деревянных брусков. Разрешается проводить разгрузку задних рессор путем установки брусков между рамой и полом, передних — между буфером и полом. Установка автомобилей на подставки и разгрузка рессор должны проводиться не позднее одного месяца со дня их приема. Гусеничные бронетанковые машины устанавливаются на деревянных или бетонных лежнях. Лежни должны быть на 1 м длиннее опорной поверхности гусениц. Если машины хранятся в парках с бетонным полом, то лежни можно не укладывать. Гусеничные машины с гидропневматической подвеской и изменяемым клиренсом хранятся на минимальном клиренсе с вывешенным на брусьях корпусом, разгруженной подвеской и ослабленными гусеницами. Колесные бронетанковые машины хранятся с вывешенным на подставках корпусом.
Хранение переносных и стационарных ВВТ Переносные и стационарные ВВТ хранятся в шкафах, контейнерах, пакетах, штабелях, на стеллажах и поддонах, в укладочных или тарных ящиках комплектно. Приведенные в рабочее состояние аккумуляторы хранятся отдельно. При размещении ВВТ должны выполняться все требования Межотраслевой типовой инструкции по охране труда для работников, выполняющих погрузочно-разгрузочные и складские работы, и эксплуатационной документации.
Размещать и складировать ВВТ следует в специально оборудованных помещениях (на площадках) в соответствии с планом размещения, учетом их агрегатного состояния, совместимости и однородности, характерных свойств (взрывопожароопасные, токсичные, химически активные и тому подобные) и выбора средств пожаротушения.
Места складирования ВВТ должны быть оснащены специальными устройствами и приспособлениями, исключающими произвольное смещение и падение груза при хранении (боковые стойки, прокладки, подпорки и тому подобное), средствами механизации погрузочно-разгрузочных работ.
Укладка грузов в проходах, проездах, возле электроустановок, рубильников, пожарных щитов и токопроводящей арматуры не допускается.
Укладка ВВТ должна проводиться с соблюдением следующих условий:
— должен обеспечиваться свободный доступ для контроля их состояния и возможности количественного счета (при этом должны соблюдаться проходы: против ворот — не менее ширины ворот; против дверных проемов — шириной, равной ширине дверей, но не менее 1,0 м.; между стеной и стеллажом, а также между стеллажами (штабелями) — не менее 0,8 м.);
— необходимо наиболее выгодно и экономно использовать площади и объем помещения, а также стеллажное оборудование с учетом объема и массы ВВТ (более громоздкие и тяжелые ВВТ укладываются на нижние полки и ближе к выходу для обеспечения возможности их быстрой выдачи);
— при укладке штабелей необходимо располагать их таким образом, чтобы расстояние между штабелями превышало ширину транспортных средств (погрузчиков, тележек и тому подобных) не менее чем на 0,8 м, а при необходимости обеспечения встречного движения — двойную ширину транспортного средства плюс 1,2 м;
— размещать ВВТ на стеллажах следует с учетом предельно допустимой нагрузки на каждую полку, обеспечения устойчивого положения складируемых средств и имущества связи, исключения их выпадения при хранении;
— каждый стеллаж должен быть надежно закреплен, иметь инвентарный номер и надписи о предельно допустимой нагрузке на каждой полке;
— полки стеллажей должны иметь бортики;
— деревянные стеллажи в складских помещениях должны обрабатываться огнезащитными составами;
— перед укладкой ВВТ в стеллажи их ячейки необходимо очистить от грязи, остатков упаковки и консервации;
— укладывать грузы на неисправные стеллажи и перегружать стеллажи не допускается;
— необходимо разделять ВВТ по номенклатуре;
— соблюдать требования безопасности, в том числе пожарной;
— соблюдать давление, допустимое на единицу площади пола, стеллажа, полки.
На стеллажи должны укладываться в первую очередь ВВТ:
— имеющие интенсивное движение;
— разных наименований, поступающие на склады в малых количествах, в общей таре и имеющие интенсивное движение;
— которые в процессе хранения подлежат частым осмотрам, просушке, переукладке.
ВВТ с высокой интенсивностью движения, масса которых с упаковкой составляет до 20 кг, малогабаритные по размерам должны укладываться на средние полки стеллажей.
ВВТ, имеющие массу свыше 20 кг, должны укладываться на нижних полках стеллажей, в местах более близких к проходам и выходам. На верхние полки стеллажей должно укладываться легкое, редко выдаваемое имущество.
При складировании ВВТ с низкой интенсивностью движения следует применять штабельное хранение. Складирование грузов в штабеля следует проводить на полу склада или на открытой площадке в один или несколько рядов в ящиках и другой транспортной таре. Во избежание просадок и нарушения вертикального положения штабеля открытые площадки предварительно очищаются от мусора и посторонних предметов, а в зимнее время — от льда и снега.
В многорядные штабеля не допускается складировать ВВТ, имеющие слабую упаковку, которая не может выдержать давление верхних рядов, упаковку и конфигурацию неправильной формы, не позволяющую обеспечить устойчивость штабеля.
Максимально допустимая высота штабелей определяется в зависимости от вида упаковки ВВТ, их веса и условий механизации погрузочно-разгрузочных работ с учетом требований манипуляционных знаков. Высота однорядного штабеля при ширине менее 1 м. не должна превышать 1,5 м.
Однотипные малорасходуемые ВВТ разных наименований могут упаковываться в общую укладочную или транспортную тару и также храниться в штабелях. В данном случае на них должна быть составлена укладочная опись, один экземпляр которой должен находиться внутри упаковки, а второй — укреплен на ее наружной стороне.
Укладка ВВТ в штабеля проводится с соблюдением следующих правил:
— давление, которому подвергается нижний ряд средств связи, сложенных в штабель, не должно вызывать их повреждения;
— высота штабеля должна быть такой, чтобы не нарушать его устойчивость;
— размер штабелей должен давать возможность просчитывать уложенные ВВТ.
Порядок отпуска (выдачи) ВВТ Отпуск (выдача) ВВТ, других материальных средств со склада проводится в дни выдачи, определенные по решению руководителя довольствующего органа, на основании нарядов или разнарядок, выданных в органе управления, руководителю которого подчинен склад. Как исключение отпуск материальных средств может проводиться на основании распоряжений руководителя органа управления, переданных по телеграфу (телефону). Достоверность таких распоряжений начальник склада обязан установить путем обратной проверки. Распоряжение в последующем подтверждается нарядом, номер которого может быть передан одновременно с распоряжением. На лицевой стороне наряда в данном случае должно быть указано: «В подтверждение распоряжения от „___“ __________ 20___ г. № _____».
Для отпуска (выдачи) ВВТ из органа управления, руководителю которого подчинен склад, направляется наряд в трех-четырех экземплярах (разнарядка — в двух экземплярах). На основании наряда (разнарядки) или распоряжения руководителя органа управления в учетно-операционном отделе склада на каждого грузополучателя выписывается наряд в трех-четырех экземплярах. Во всех случаях наряды передаются в подразделения склада на исполнение.
Отпуск (выдача) ВВТ со склада проводится в строгом соответствии с данными, указанными в наряде. Все исправления в наряде должны быть заверены подписями лиц, подписывающих наряд.
Наряд на отпуск (выдачу) ВВТ со склада действителен только на срок, указанный в нем. Если срок действия не указан, то наряд действителен в течение трех месяцев для центральных и 30 суток для остальных складов со дня выдачи.
Порядок отгрузки (отправки) ВВТ В отделе хранения склада на основании наряда проводится подготовка ВВТ к отгрузке, включающая в себя:
— отбор с учетом требований по освежению запасов;
— оформление эксплуатационной документации (для техники) ;
— проверку технического состояния;
— подготовку тары в соответствии с требованиями перевозки;
— укладку материальных средств в тару;
— оформление упаковочных листов, один экземпляр которых вкладывается в тару вместе с материальными средствами, другой прилагается к первому экземпляру наряда: при упаковке техники в упаковочных листах указываются ее номера;
— составляется весовая ведомость на материальные средства, подлежащие взвешиванию, в двух экземплярах.
По окончании отбора ВВТ в наряде заполняется графа «Выдано (отгружено)».
Подготовленные к отгрузке ВВТ вместе со вторым экземпляром весовой ведомости передаются в транспортный отдел склада под расписку на первом экземпляре наряда о количестве принятых мест. Первые экземпляры наряда и весовой ведомости с приложенными вторыми экземплярами упаковочных листов передаются в учетно-операционный отдел.
При наличии на складе подъездных железнодорожных путей (причалов, посадочных площадок) и при отгрузке однородных грузов из одного отдела хранения отправка проводится силами данного отдела без передачи грузов в транспортный отдел. В указанном случае весовая ведомость составляется в одном экземпляре.
Подача заявок на планирование железнодорожного транспорта в вышестоящий орган осуществляется из учетно-операционного отдела на основании имеющихся нарядов за 45 суток до планируемого месяца.
Заказ железнодорожных транспортов для отправки ВВТ со склада проводит подекадно начальником учетно-операционного отдела на основании выписки из плана отправок, высылаемой из органа управления не позднее 15-го числа текущего месяца. Заявки на подвижной железнодорожный состав с разбивкой по дням погрузки и указанием номеров транспортов не позднее чем за 3 суток до срока отгрузки представляются военному коменданту железнодорожного участка, а их копии — начальнику станции погрузки. В случае отсутствия возможности загрузки запланированных транспортов начальник склада должен своевременно поставить в известность об этом начальника, подписавшего план перевозок.
Прием железнодорожных вагонов проводит представитель транспортного отдела. При этом проверяются целостность вагонов и их пригодность для перевозки данных ВВТ. В транспортном отделе после получения из отдела хранения затаренных ВВТ составляется на каждый вагон (контейнер) повагонная ведомость в двух экземплярах, которую подписывают ответственные за погрузку лица. Первый экземпляр ведомости остается в транспортном отделе, второй прикрепляется к внутренней стенке вагона (контейнера) с правой стороны двери.
Погрузка и крепление ВВТ в железнодорожном подвижном составе проводятся по правилам, установленным правовыми актами Белорусской железной дороги. При этом должно обеспечиваться полное использование вместимости вагонов, но не более их грузоподъемности. Укладка ВВТ должна обеспечить их полную сохранность при транспортировании. Мелкие места следует объединять в более крупные путем контейнеризации или пакетирования. Необходимые для погрузки и перевозки приспособления и материалы заготовляет грузоотправитель. Нормы расхода крепежного материала определяются в соответствии с Наставлением по перевозкам войск.
По окончании загрузки вагона представитель склада пломбирует двери вагона (контейнера) и выписывает железнодорожную накладную. Накладная составляется на имя грузополучателя, подписывает ее грузоотправитель, она находится с грузом на всем пути его следования и на станции назначения выдается грузополучателю вместе с грузом.
Грузоотправитель несет ответственность за все последствия неправильности, неточности или неполноты сведений, указанных в накладной.
Время приема груза к перевозке удостоверяется путем проставления календарного штемпеля станции отправления на железнодорожной накладной.
Соответствующие транспортные документы оформляются и при отправке имущества другим видом транспорта.
Отправка ВВТ со склада авиа-, автомобильным и пассажирским транспортом проводится по письменному распоряжению руководителя органа управления. В данном случае начальник учетно-операционного отдела подает заявку в адрес начальника аэропорта (вокзала), в которой указывает наименование груза, количество мест, массу, наименование аэропорта (станции) назначения.
По окончании отгрузки ВВТ на третьем экземпляре наряда в транспортном отделе делаются записи о количестве отправленных мест, характере упаковки, массе груза, номерах транспортных документов и дате отгрузки, после чего наряд передается в учетно-операционный отдел, где указанные данные вносятся в первый и второй экземпляры наряда.
Первый экземпляр исполненного наряда с приложениями остается в делах склада. Второй его экземпляр с сопроводительными документами прилагается к транспортному документу, выдается начальнику караула, сопровождающему транспорт, или не позднее следующего дня после отгрузки высылается по почте грузополучателю. Третий экземпляр с отметкой об отгрузке высылается в орган управления, в котором был выдан наряд. В те же адреса направляются экземпляры нарядов, выписанных на складе в счет разнарядки органа управления. При этом первый экземпляр разнарядки остается в делах склада, второй экземпляр высылается в орган управления после полного выполнения разнарядки или истечения срока ее действия. Грузополучатель уведомляется об отправке ВВТ извещением, составляемым в учетно-материальном отделе. При отправке имущества почтовыми посылками в учетно-операционном отделе выписывается реестр в двух экземплярах, в котором указываются количество посылок и почтовый адрес пункта назначения. Один экземпляр реестра посылается получателю.
Второй экземпляр реестра после отметки, сделанной в почтовом отделении о принятии посылок возвращается в учетно-операционный отдел и подшивается в дело вместе с нарядом.
По специальному распоряжению начальника, которому подчинен склад, ВВТ могут доставляться непосредственно получателю на транспортных средствах склада. В данном случае доставка возлагается на транспортный отдел.
При этом лица, которым поручена доставка, обязаны:
— убедиться в соответствии получаемых для доставки ВВТ данным сопроводительных документов;
— принять меры по укладке ВВТ на транспортные средства так, чтобы предохранить их от порчи или утраты в пути.
Сдатчику склада выдаются первый и второй экземпляры наряда на каждого грузополучателя. Сдатчик своей подписью в третьем экземпляре наряда, который остается в отделе хранения, подтверждает получение ВВТ, а также первого и второго экземпляров наряда. Сдача ВВТ грузополучателю проводится под расписку его приемщика на первом экземпляре наряда. Ему вручается второй экземпляр наряда, оформленного на складе. Сдатчик по возвращении на склад первый экземпляр выполненного наряда вместе с доверенностью грузополучателя сдает в учетно-операционный отдел. При этом в присутствии сдатчика проверяется по выполненному наряду полнота доставки ВВТ грузополучателю. При отсутствии расхождений между полученными и доставленными ВВТ на третьем экземпляре наряда погашается роспись сдатчика.
При отпуске ВВТ со склада непосредственно приемщику грузополучателя в учетно-операционном отделе проверяются документы, удостоверяющие его личность, и доверенность.
Оба экземпляра наряда вручаются приемщику, который передает их на исполнение в отдел хранения. Начальник отдела хранения делает в обоих экземплярах отметки о количестве и качестве отпускаемых ВВТ, заверяет их своей подписью, после чего первый экземпляр вручается приемщику для передачи в учетно-операционный отдел. За принятые средства приемщик расписывается во всех экземплярах наряда. Доверенность приемщика прилагается к первому экземпляру наряда и хранится вместе с ним в учетно-операционном отделе. При отпуске ВВТ приемщику по одному наряду из нескольких отделов хранения на каждый отдел в учетно-операционном отделе выписывается накладная в двух экземплярах. Отпуск имущества из отделов хранения проводится под роспись приемщика в накладных. Указанные накладные прилагаются к первому экземпляру наряда, о чем на нем делается отметка.
По окончании отпуска ВВТ в учетно-операционном отделе оформляются второй экземпляр наряда и пропуск, которые вручаются приемщику грузополучателя. При наличии четвертого экземпляра наряда он оформляется аналогично второму и в дальнейшем грузополучатель направляет его в свой орган управления в качестве донесения о получении ВВТ.
После выдачи (отгрузки) ВВТ и оформления всех документов они списываются с книг и карточек учета в соответствующих отделах склада.
Механизация погрузочно-разгрузочных и внутрискладских работ Механизация погрузочно-разгрузочных и внутрискладских работ должна быть направлена на облегчение условий и повышение производительности труда, снижение себестоимости складских операций, ускорение операционной деятельности. Средства механизации определяются табелем склада. Средства малой механизации могут изготовляться собственными силами.
На складах должны применяться стационарные и подвижные средства механизации. К стационарным средствам механизации относятся мостовые электрические краны, козловые электрические краны, кран-балки с электроталью, монорельсы с электроталью, грузовые лифты и подъемники, транспортеры конвейерного типа.
К основным типам подвижных средств механизации относятся автомобильные подъемные краны, крановые самопогрузчики, автопогрузчики, электропогрузчики и другие.
На складах должны применяться средства малой механизации: тележки грузовые, тележки с подъемными вилами, тележки-медведки, тележки-краны, электрокары, ручные лебедки, катки, роликовые ломы, стропы, захваты.
При наличии на складе железнодорожной ветки применяются мотовозы (тепловозы) для перевозки грузов на вагонетках и для маневровых работ. При наличии на мотовозе (тепловозе) крана он может быть использован и для выполнения работ по погрузке и выгрузке различных грузов. Здания, имеющие два и более этажей, должны быть оборудованы лифтами для подъема грузов. Масса перемещаемого груза не должна превышать предельной нагрузки лифта. Для склада и каждого хранилища должны быть отработаны и внедрены конкретные схемы комплексной механизации погрузочно-разгрузочных работ с применением штатно-табельных средств и средств малой механизации.
Технические характеристики средств механизации приведены в таблицах 1, 2:
Таблица 1 — Технические характеристики автомобильных кранов, используемых на складах
Характеристика | КС-156А | КС-2561Е | КС; | КС; | КС-4561А | КС; | КС-3562А | КС; | |
Базовый автомобиль Максимальная грузоподъемность, кг (в числителе) при вылете стрелы, м (в знаменателе) Грузоподъемность, кг (в числителе) при вылете стрелы, м (в знаменателе) Рабочая скорость подъема груза, м/мин Рабочая частота вращения стрелы, об/мин Габариты в транспортном положении, мм Собственная масса, кг Максимальная скорость, км/ч Тип привода крановых механизмов | ГАЗ-53А 3,2 0,3 — 12,6 0,39 — 2,74 Механический | ЗИЛ-131 3,3 2,2 — 13,1 0,39 — 2,74 Механический | МАЗ-500 0,5 — 12,5 0,15 — 2,5 Механический | МАЗ-500А 3,5 7,5 0,5 — 6,5 0,6 — 1,6 Электри-ческий. | КрАЗ-257 3,8 2,7 — 7,2 0,3 — 1,5 Электрический. | Самоходное шасси 4,5 13,8 0,1 — 1,2 Электричес-кий. | МАЗ-500А 0,5 — 12,5 0,2 — 2,5 Гидравли-ческий | КрАЗ-257 3,8 8,5 0,2 — 8,4 0,1 — 1,6 Гидравли-ческий | |
Примечание — Источник: [10, с. 45, таблица 3]
Таблица 2 — Технические характеристики электропогрузчиков и автопогрузчиков
Характеристики электропогрузчиков | ЭП-106−28 | ЕВ-641−2 | ЕВ-661 | ЭПК-0805 | ЭПК-1205 | |
Грузоподъемность, кг Расстояние центра тяжести груза на вилах, мм Наибольшая высота подъема, мм Свободный подъем грузовой каретки, мм Длина с вилами, мм Ширина, мм Строительная высота, мм Высота при наибольшем подъеме вил, мм Внешний радиус поворота, мм Скорость передвижения, км/ч: с грузом без груза Собственная масса, кг | ; | |||||
Характеристики автопогрузчиков | |||||||||
Грузоподъемность на вилах, кг Максимальная высота подъема вил, мм Угол наклона рамы, град: вперед назад База, мм Колея, мм: передних колес задних колес Габаритный радиус, мм Базовые агрегаты автомобиля Модель двигателя Максимальная скорость без груза, км/ч Габариты, мм Собственная масса, кг | Спец. шасси МеМЗ-968 | ; МЗМА-408 | ГАЗ-53А ГАЗ; 51А | ЗИЛ-130 ГАЗ; 51А | ЗИЛ-130 ГАЗ; 51А | ЗИЛ-130 ГАЗ; 51А | МАЗ-500А ЗИЛ; | ; ; МАЗ-500А ЗИЛ; | |
Примечание — Источник: [10, с. 47, таблица 4−5] | |||||||||
По мере поступления более совершенных механизмов, внедрения рационализаторских предложений и накопления опыта комплексное использование механизмов должно постоянно совершенствоваться.
При выборе средств механизации и автоматизации процессов перемещения грузов следует учитывать следующие факторы:
— габаритные размеры, форму, массу, количество перемещаемых грузов;
— строительные характеристики зданий и сооружений;
— номенклатуру хранимых грузов, запас их хранения и оборачиваемость;
— периодичность поступления и выдачи грузов со склада;
— характер операций по комплектованию заказов;
— вид транспорта для доставки грузов на склад и их отправления со склада.
На складах должна внедряться переработка грузов в пакетах и контейнерах, что обеспечивает:
— возможность механизированной погрузки (выгрузки);
— сохранность пакетов (контейнеров) и грузов в них без деформации при транспортировании и перегрузках;
— повышение плотности укладки и устойчивости грузов;
— оптимальное использование грузоподъемности транспортных средств);
— сокращение времени на переработку грузов.
Под пакетом понимается укрупненная грузовая единица, сформированная из более мелких грузовых мест (не менее двух) в транспортной таре (ящиках, барабанах и других), скрепленных между собой на подкладках или поддонах.
Основные положения по организации и осуществлению пакетного способа перевозок и хранения грузов изложены в Инструкции по пакетному способу транспортировки и хранения воинских грузов в Вооруженных Силах Республики Беларусь.
Для пакетирования грузов могут использоваться плоские, стоечные и ящичные поддоны. Типы, основные параметры и размеры плоских поддонов приведены таблице 3:
Таблица 3 — Типы, наименования и основной размер плоских поддонов
Тип поддона | В | L | h1, не менее | h2, не менее | В, не менее | В1, не более | l, не более | Масса брутто, т не более | ||
не менее | ||||||||||
П2 П4 2П4 2ПВ2 2ПВ2 | 3,2 | |||||||||
Типы поддонов ГОСТ 9073– — 84 | Наименования поддонов | Основной размер ВL, мм | |
П2 П4 2П2 2П04 2ПВ2 2ПВ2 | Однонастильный двухзаходный Однонастильный четырехзаходный Двухнастильный четырехзаходный Двухнастильный четырехзаходный с окнами в нижнем настиле Двухнастильный двухзаходный с выступами Двухнастильный двухзаходный с выступами | 800×1200 800×1200 1000×1200 1000×1200 1200×1600 1200×1800 | |
Примечание — Источник: [10, с. 49, таблица 6−7]
Для транспортирования, хранения и отправки штучных грузов как в пакетах, так и россыпью могут применяться грузовые контейнеры. По назначению контейнеры делятся на две основные группы: общего назначения (универсальные) и специального назначения (специализированные).
Универсальные контейнеры делятся на три типа: крупнотоннажные, среднетоннажные и малотоннажные контейнеры, параметры которых указаны таблице 4:
Таблица 4 — Типы, основные параметры и размеры универсальных контейнеров
Типы | Номинальная масса брутто, кг | Собственная масса, кг | Внутренний объем, м3 | Площадь пола, м2 | Габаритные размеры, мм | Дверной проем (в свету), мм, не менее | ||||
длина | ширина | высота | ширина | высота | ||||||
Малотоннажные контейнеры | ||||||||||
АУК — 0,625 АУК — 1,25 МК — 1 МК — 1,25 | 1,6 3,1 1,66 | 1,045 1,64 ; ; | ; ; | ; ; | ||||||
Среднетоннажные контейнеры | ||||||||||
УУК — 3 УУК — 5 УУК — 2,5 — 3 УУК — 5 — 2 УУК — 5 — 1 УУК — 5У УУКФ — 5 | (3000) | 600 — 650 | 6,2 10,1 5,1 — 5,3 10.3 5,1 — 5,3 11,7 | ; ; 2,4 4,9 2,4 ; | ||||||
Крупнотоннажные контейнеры | ||||||||||
1ДХ 1СХ 1А 1АА | 14,7 30,6 64,8 66,7 | 6,6 13,7 ; | ||||||||
Примечание — Источник: [10, с. 65, таблица 9]
Все средства механизации, выделяемые в отделы (отделения) хранения склада и в хранилища, должны быть закреплены приказом начальника за специально подготовленным личным составом отдела.
Контроль за техническим состоянием и эксплуатацией средств механизации возлагается на помощника начальника склада по хранению.
Подводя итоги данной главы можно утверждать, что организация технологического процесса на складе связи содержит те же операции, что и на других складах. Однако существенные трудности возникают из-за отсутствия автоматизации технологического процесса, так как учет ведется в основном вручную, приемка и выдача ВВТ осуществляется строго по определенным дням, а не круглосуточно, операции грузопереработки, в основном, ведутся без применения средств механизации.
3. ОПТИМИЗАЦИЯ ТЕХНОЛОГИЧЕСКОГО ПРОЦЕССА НА СКЛАДЕ
Основу внутрискладской логистики составляет технологический процесс, т. е. система операций по подготовке склада к приемке продукции, разгрузке транспортных средств, приемке продукции, размещению ее на хранение, организации хранения, комплектации заказов, подготовке к отпуску и отгрузке со склада. От того, насколько эффективно будут выполнены эти операции, зависит работа других отделов компании, уровень логистического сервиса, предоставляемого клиентам, следовательно, и уровень конкурентоспособности компании на рынке. В связи с этим перед руководством склада каждого предприятия стоит задача максимально оптимизировать технологический процесс.
Первичной операцией этого процесса является приемка продукции и связанные с ней операции по подготовке склада к приемке.
Результаты статистического анализа приемки продукции на различных складах свидетельствуют, что:
— на 60% исследуемых складов допускались ошибки в приемке продукции по количеству (массе), которые приводили к отсутствию более 8% товаров, на 25% складов допускались ошибки, приводившие к 5%-ной недостаче, и на 15% складов были допущены ошибки, приводившие менее чем к 2%-ной недостаче.
— на 70% складов качество приемки становилось причиной того, что предприятия, сами того не ведая, принимали на хранение и реализацию более 12% товарных позиций, которые не соответствовали товарной номенклатуре, определенной в договоре поставки, а это в дальнейшем, естественно, приводило к пересортице.
— на большинстве складов (более 60%) осуществлялась приемка бракованной продукции (как с несоответствующими потребительскими свойствами, так и с нарушенной оригинальной упаковкой производителя), составляющая от 3 до 8% общего объема единовременной поставки.
В совокупности эти ошибки приводили к серьезным финансовым потерям и ухудшению отношений с клиентами, так как из-за возникающей пересортицы клиентам данных компаний также частично поставлялась продукция, не соответствующая условиям договора. С целью исключить возможность возникновения подобной ситуации был разработан универсальный алгоритм осуществления процедуры приемки продукции и смежных операций (рисунок 6), который позволяет существенно оптимизировать процесс приемки продукции и связанных с ней операций.
Подготовка склада к приёмке продукции.
На большинстве складов какие-либо операции по подготовке к приемке продукции не проводят вообще. Как следствие, поступление партий товара является полной неожиданностью для складского персонала, что в дальнейшем приводит также к негативным последствиям: незапланированный перевод сотрудников с одних операций на другие, например разгрузку транспорта, перемещение товаров и т. п., затоваренность проходов, проездов и др. Чтобы этого избежать, рекомендуется принимать ряд мер:
а) своевременно получать информацию об ожидаемой поставке товара из отдела снабжения, а именно:
— перечень товарных позиций;
— количество поступающего товара (в том числе по каждой товарной позиции);
— сроки поступления товара;
— наименования поставщика (-ов);
— тип тары (короба, паллеты);
— информацию о дополнительной сопроводительной документации (сертификаты соответствия и т. д.).
Рисунок 6 — Алгоритм осуществления приемки и смежных операций Примечание — Источник:[13,с.1]
Наиболее удобно создать форму документа (карточка сведений поставки), в которую эта информация экспортировалась бы из информационной системы или которую заполняют «вручную», в зависимости от возможностей склада.
б) определить число служащих (с использованием технологических карт), участвующих в разгрузке и приемке продукции; определить состав техники, необходимой для разгрузки транспорта.
в) определить потенциальные места хранения поступившей продукции.
В складской логистике существует философский принцип «всё имеет свое место и на этом месте должно храниться», т. е. предпочтительно, чтобы за каждой товарной группой (товарной позицией) от поставки к поставке была закреплена определенная зона хранения, что позволит в дальнейшем упростить поиск и подбор товара с мест хранения, а также соблюдать принципы товарного соседства. Определить число мест и их конкретное месторасположение можно несколькими способами.
Первый — это использование данных информационной системы. В настоящее время практически любая ERPили WMS-система позволяет достаточно быстро получить данную информацию, однако число складов, которые располагают такими программами, составляет приблизительно от 5 до 10% общего числа складов на территории Республики Беларусь.
На складах площадью до 1500…2000 м2 число и месторасположение свободных мест на складе обычно определяют исключительно визуально, что занимает значительное количество времени. Кроме того, такая информация быстро теряет актуальность, поскольку за время, которое тратит служащий, производящий осмотр, на перемещение из одной зоны в другую, свободные места уже, как правило, затовариваются. На складах большей площади применение такого метода невозможно в принципе.
Есть еще один способ определения мест хранения — составление карты размещения свободных мест на складе. Этот способ может показаться весьма примитивным, но позволяет существенно оптимизировать процесс поиска свободных мест на складе средней площади — 2000…5000 м2. Сущность метода сводится к тому, что приобретается большая маркерная (пластиковая) доска, на которой несмываемой краской наносят все зоны склада, стеллажи, ячейки с указанием адреса каждого стеллажа и ячейки. Когда производится комплектация заказов, комплектовщик в листе отборки или в другом документе отмечает напротив каждой товарной позиции степень заполненности той ячейки, из которой осуществляется отбор. После комплектации заказа или его части комплектовщик пишет эту же величину маркером на доске (карте) размещения свободных мест на складе. При этом определяется перечень цветов, которыми производят заполнение. Например, красный — полностью заполненная ячейка, синий — ячейка заполнена наполовину, белый/пустой — отсутствие товара в ячейке. Число цветов увеличивать не рекомендуется — это может привести к путанице. В ходе процесса размещения товаров на хранение выполняют аналогичную операцию. Таким образом, получить информацию о наличии и расположении свободных мест на складе возможно при визуальном осмотре такой карты.
Безусловно, у этого метода есть ряд недостатков и ограничений:
— наличие информации не в режиме online;
— трудовые и временные затраты складских служащих на процедуры отметки в листе комплектации и карте размещения свободных мест хранения;
— риск человеческого фактора при заполнении карты (особенно на начальном этапе внедрения метода);
— практическая невозможность создать карту при глубинном хранении (технически «прорисовать» данную карту практически не представляется возможным);
— отсутствие возможности автоматической распечатки данных карты и передачи их непосредственным исполнителям (возможен только визуальный осмотр и фиксация «вручную» в ином документе).
Несмотря на эти недостатки, данный метод успешно реализован на складах ряда компаний. С течением времени число ошибок при заполнении карты существенно сокращалось, а экономическая привлекательность данного метода вполне удовлетворила руководство складов, не имеющих должного финансового обеспечения.
Скрытые недостатки продукции.
Среди большинства сотрудников складов и отделов снабжения бытует мнение, что претензии по качеству поступившей продукции можно предъявлять только в процессе приемки продукции либо непосредственно по ее окончании, но это далеко не так. Законодательство Республики Беларусь позволяет предъявить претензии к предприятию-поставщику и в случае обнаружения скрытых недостатков продукции. Скрытыми признаются такие недостатки, которые не могли быть обнаружены при обычной для данного вида продукции проверке и которые выявлены лишь в процессе обработки, подготовки к монтажу, в процессе монтажа, испытания, использования и хранения продукции на складе. В связи с этим склады предприятий имеют право независимо от проверки качества товаров, проведенной ими в сроки, указанные в договоре или ином документе, актировать скрытые недостатки продукции. Акт о скрытых недостатках продукции должен быть составлен в течение 24 часов с момента их обнаружения. После завершения всех операций, связанных непосредственно с приемкой продукции, оформляют товар на хранение с занесением всей необходимой информации в информационную систему. Далее проводят операции по идентификации продукции и размещению продукции на хранение.
Идентификация.
Безусловно, нет необходимости объяснять значимость такой операции, как идентификация поступающей продукции, ведь если ее не проводить, любой склад просто «задохнется», так как в дальнейшем невозможно будет осуществлять учет и контроль за движением, состоянием продукции на складе, его поиск при комплектации и инвентаризации. Однако к выбору метода идентификации следует подходить, тщательно взвесив задачи, стоящие перед складом, его технико-технологические и финансовые возможности, природу товарного ассортимента и многое другое. В своей практике мы встречали объекты, где идентификация практически не проводилась вообще, а точнее, к периодически присутствующим ярлыкам производителя на коробах и паллетах грузчики подручными средствами «дорисовывали» им одним понятные символы и обозначения, что, естественно, в дальнейшем приводило к путанице. Как правило, проблему пытались разрешить резким, необдуманным введением штрихового кодирования, что в 80% случаев приводило к неэффективным затратам, так как склады изначально не были подготовлены к внедрению этого метода — не было технико-технологических возможностей для выполнения данных операций. Отсутствовало и должное программное обеспечение. Таким образом, эффективность операций по идентификации продукции на складах сводилась к нулю. В связи с этим мы рассмотрим три основных метода идентификации в складском технологическом процессе, каждый из которых может быть эффективен в зависимости от возможностей конкретного склада, целей и задач, стоящих перед ним.
Индивидуальное кодирование.
Это наиболее простой метод идентификации, предполагающий минимальные затраты на его внедрение и использование. Сущность индивидуального кодирования заключается в следующем: каждой товарной позиции присваивается индивидуальный код, который может содержать в себе информацию («смысловой» код), а может не нести никакой информации («не смысловое» кодирование). При разработке «смыслового» кода необходимо определить, какая информация является важнейшей и требует сохранения в коде. Например, создается девятизначный код, содержащий информацию о поставщике (первые три цифры), информацию о товарной группе (две цифры) и товарной позиции (три цифры), о статусе данного товара (например, о его ценности, порядке хранения и прочее).
Абсолютно не обязательно знать структуру кода оперативным работникам — грузчикам, комплектовщикам. Важно, чтобы структура кода и значение каждой цифры были зафиксированы в нормативном документе предприятия и руководитель склада, его заместители и лица при необходимости всегда могли расшифровать информацию по конкретной грузовой единице. Основной целью данного вида идентификации является возможность учета продукции на складе, ее индивидуализации при комплектации заказов. Аналогичную функцию носит и «не смысловое» кодирование, когда каждой товарной позиции присваивается свой номер, что позволяет индивидуализировать ее среди другой продукции при однородном внешнем виде. Стоимость внедрения и использования этого метода не высока. Как правило, в затраты на введение индивидуального кодирования включается только закупка этикеточной ленты и печать на ней кода товаров, а также закупка нескольких этикет-пистолетов. Ярлык (этикетку) с напечатанным на ней кодом товарной позиции наклеивают с помощью этикет-пистолета на каждую грузовую единицу по завершении операций приемки продукции и ее сортировки.
Штриховое кодирование (далее — ШК).
Внедрение ШК на складе позволяет существенно ускорить процесс приемки продукции (в случае, если на поступающих грузовых единицах уже имеется штрих-код), значительно снизить влияние человеческого фактора в процессе выполнения технологических операций и при инвентаризации, упростить поиск (определение) нужного товара на стеллаже или в стеллажной ячейке. Внедрение ШК обосновывается и тем, что все чаще крупные клиенты торговых и производственных компаний ставят его наличие обязательным условием при закупках продукции. Однако внедрение системы ШК влечет за собой серьезные основные и дополнительные затраты. К основным затратам относится закупка оборудования (терминалы сбора данных, сканеры, сервер, принтер для печати этикеток), программного обеспечения, совместимого с системой ШК, оплата услуг и взносов в Ассоциацию Юнискан/EAN. К дополнительным затратам можно отнести обучение персонала, услуги консультантов по подготовке склада к внедрению ШК и прочее.
Радиочастотная идентификация (далее — RFID).
Система RFID появилась сравнительно недавно и в настоящее время на российских складах практически не используется, однако успешный опыт внедрения этой системы рядом крупных компаний в Европе (в частности, в Италии и Германии) позволяет сделать вывод, что в среднесрочной перспективе широкое применение системы RFID начнется и в Беларуси.
Система RFID состоит из трех элементов — метка (tag), антенна (reader) и компьютер (рисунок 7).
Рисунок 7 — Система RFID
Примечание — Источник:[5,с.472]
В метку заносятся необходимые данные о грузовой единице, после чего данные метки могут передаваться в компьютер с помощью антенны.
Преимущества RFID:
— данные идентификационной метки можно менять и дополнять;
— на метку можно записать гораздо больше данных по сравнению со штрих-кодом;
— данные на метке могут быть засекречены;
— радиочастотные метки более долговечны;
— расположение метки не имеет значения для считывания (метка может находиться внутри короба или паллеты);
— метка лучше защищена от воздействия окружающей среды;
— метки могут быть многоразового использования;
— при использовании RFID появляется возможность контролировать перемещения груза.
Недостатки RFID:
— относительно высокая стоимость;
— невозможность размещения под металлическими и электропроводными поверхностями;
— подверженность помехам в виде электромагнитных полей;
— возможность только локального использования.
Характеристики технологии | RFID | Штрих-код | QR-код | |
Необходимость в прямой видимости метки | Чтение даже скрытых меток | Чтение без прямой видимости невозможно | Чтение без прямой видимости невозможно | |
Объём памяти | От 10 до 512 000 байт | До 100 байт | До 3 072 байт | |
Возможность перезаписи данных и многократного использования метки | Есть | Нет | Нет | |
Дальность регистрации | До 100 м | До 4 м | До 1 м | |
Одновременная идентификация нескольких объектов | До 200 меток в секунду | Невозможна | Зависит от считывателя | |
Устойчивость к воздействиям окружающей среды: механическому, температурному химическому, влаге | Повышенная прочность и сопротивляемость | Зависит от материала, на который наносится | Зависит от материала, на который наносится | |
Срок жизни метки | Более 10 лет | Зависит от способа печати и материала, из которого состоит отмечаемый объект | Зависит от способа печати и материала, из которого состоит отмечаемый объект | |
Безопасность и защита от подделки | Подделка практически невозможна | Подделать легко | Подделать возможно | |
Работа при повреждении метки | Невозможна | Затруднена | Затруднена | |
Идентификация движущихся объектов | Да | Затруднена | Затруднена | |
Подверженность помехам в виде электромагнитных полей | Есть | Нет | Нет | |
Идентификация металлических объектов | Возможна | Возможна | Возможна | |
Использование как стационарных, так и ручных терминалов для идентификации | Да | Да | Да | |
Возможность введения в тело человека или животного | Возможна | Затруднена | Затруднена | |
Габаритные характеристики | Средние и малые | Малые | Малые | |
Стоимость | Средняя и высокая | Низкая | Низкая | |
Составлена по материалам книги Сандип Лахири «RFID. Руководство по внедрению»
Размещение товаров на хранение Размещение товаров на хранение необходимо выполнять таким образом, чтобы при последующих технологических операциях число перемещений складских служащих было минимальным. С этой целью делят все товарные позиции на три группы, после чего для их хранения выделяют «горячие» и «холодные» складские зоны. Чтобы оптимально разделить всю номенклатуру, необходимо воспользоваться методиками АВСи XYZ-анализа. В данном случае, т. е. применительно к технологическому процессу, основным критерием деления товарных позиций на группы станет выступать число подходов/ перемещений складского персонала при выполнении технологический операций, в частности при процедуре комплектации заказов в производство или клиентам.
Для проведения АВСили XYZ-анализа необходимо собрать статистические данные, предпочтительно не менее чем за предыдущий год. Информация должна содержать: наименование по каждой товарной позиции, число заказов и число отгруженных универсальных грузовых единиц помесячно по каждой товарной позиции. После составления статистической базы весь товарный ассортимент по АВС-анализу делят на три группы. Как правило, деление проводится в классических пропорциях: группа, А — 20%, группа В — 30%, группа С — 50%. Критерием деления является число заказов по каждой товарной позиции.
Рассмотрим методику проведения XYZ-анализа, критерием деления в котором будет число отгруженных универсальных единиц. Пропорциональное деление аналогично соотношению при проведении АВС-анализа, т. е. 20/ 30/ 50. Чтобы решить конечную задачу о размещении товаров в «горячую» и «холодные» зоны, необходимо составить матрицу результатов АВС-, XYZ-анализа. Обычно сопоставление результатов проведенного анализа производится в MS Excel с помощью функции сортировки и занимает минимальное количество времени.
При проведении АВС-, XYZ-анализа следует придерживаться по крайней мере двух правил. Первое — статистические данные должны быть взяты не позднее чем за предыдущий год, с разделением по кварталам и месяцам, так как именно в течение всего годового цикла можно выделить сезоны спроса по каждой товарной позиции, и размещать продукцию по зонам хранения не статично весь год, а перемещать ее между зонами в соответствии с сезонностью спроса. Второе — единицы измерения должны быть унифицированы: если на склад продукция приходит и хранится, допустим, в коробах 15 различных видов, следует измерить геометрические параметры каждого из них и выбрать размеры унифицированного короба, в котором и будет измеряться количество отгружаемой продукции.
После проведения АВС-, XYZ-анализа по каждой товарной позиции вычисляют норму запаса, находящуюся на складе единовременно. Далее определяют число мест хранения для каждой товарной позиции и производят размещение на основе результатов анализа. «Горячая» зона, как правило, располагается ближе к зоне отгрузки, на стеллажах, находящихся в центральном проезде, в нижних ярусах стеллажей, что позволяет существенно сократить время на выполнение технологических операций. Следует отметить, что в настоящее время большинство информационных систем класса ERP или WMS имеют функцию проведения АВС, XYZ-анализа по различным задаваемым критериям.
Второй задачей при размещении продукции на хранение является оптимальное разделение складских запасов. Безусловно, оптимальным является такой вариант, когда весь товарный запас хранится на стеллажах (исключая наливные, насыпные и «негабаритные» грузы), при котором отбираемый запас находится в нижних ярусах стеллажей, а резервный — в верхних. Однако склады с недостаточным финансированием зачастую не имеют возможности приобрести стеллажное оборудование для хранения всего товарного запаса. Для них возможно применение варианта с разделением товарного запаса на две категории и хранением их в двух зонах. В зоне отбираемого запаса на стеллажах хранят только минимальный одно-, двухдневный запас по каждой товарной позиции. В резервной зоне хранения весь оставшийся запас хранится штабельным способом. Пополнение запаса отбираемой зоны хранения производится, как правило, в третью смену, чтобы исключить пересечение потоков. Данный способ позволяет в несколько раз сократить количество стеллажного оборудования и площадь комплектации, следовательно, и число перемещений между местами отборки.
Комплектация заказов.
На большинстве складов оптовых торговых и производственных предприятий, а также на складах логистических центров данная операция является ключевой, так как именно от нее зависит уровень логистического обслуживания (скорость выполнения заказа, отсутствие ошибок при сборке и т. д.). При всем том эта операция является одной из самых трудоемких в складском технологическом процессе.
Существует две системы выполнения технологических операций по комплектации — «человек к товару» и «товар к человеку».
Система «товар к человеку» является полностью автоматизированной. Управление передвижением товара осуществляется при помощи пульта управления, при этом сам оператор не производит никаких перемещений, и товар поступает к окну выдачи автоматически. К настоящему времени такие системы в Беларуси пока не нашли широкого применения, однако интерес к ним очень высок и число реализованных проектов постоянно растет.
В отношении системы «человек к товару» по результатам хронометража работы комплектовщика, проводимого на различных складах предприятий, были получены следующие усредненные результаты: 50% времени комплектовщика расходуется на перемещение между местами отборки, 20% времени — это вынужденный простой (ожидание), 20% - работа с документами, 10% - изъятие с места отборки. Однако существуют методы оптимизации процедуры комплектации, применение которых сокращает общее время сборки заказа за счет полного упразднения простоя и сокращения времени на перемещения между местами отборки.
Рассмотрим типовую схему процесса комплектации заказов (рисунок 8):
Рисунок 8 — Типовая схема комплектации заказов Примечание — Источник:[8,с.216]
Процедура комплектации.
Процедура комплектации начинается с получения накладной на отпуск товара (заявка, лист комплектации и т. д.). Обязательным условием является расположение в документе товарных позиций в соответствии с размещением продукции на складе, иначе создается ситуация, когда накладная составляется в том порядке, как она существует в информационной системе, и комплектовщик вынужден проходить неэффективный путь, т. е. неоднократно возвращаться к ранее пройденным местам и т. д.
Составление маршрутной карты.
В работе большинства складов эта процедура не используется вовсе, однако оптимально продуманный путь движения комплектовщика позволяет существенно сократить время на сборку заказа. Критерием составления маршрутной карты будет являться не только размещение адресов нахождения товара в соответствии с их расположением на складе, но и, что более важно, учет принципа «товарного соседства».
Комплектация собранного заказа, его упаковка и маркировка.
Дифференциация в выполнении последних двух операций будет зависеть от вида комплектации — индивидуальной или комплексной. Индивидуальная комплектация заказа заключается в последовательной отборке одного заказа одним сборщиком. Комплексная комплектация — это сборка одного заказа по частям разными комплектовщиками в отдельных секторах склада. При индивидуальной сборке комплектовщик вынужден проходить значительные расстояния, следовательно, затрачивать большое количество времени при перемещениях между местами отборки. Более того, возрастает вероятность пересечения потоков, т. е. возникновения ситуаций ожидания освобождения технологической зоны другими служащими. Комплексный способ сборки заказов более эффективен. При таком способе склад разделяется на несколько зон, в каждой из которых работает один комплектовщик. При этом геометрические размеры зон могут быть разными, и важно рассчитать одинаковое число операций, приходящееся на каждую зону, а точнее — время для их выполнения.
Поступивший заказ разделяют на части, соответствующие зонам склада. После сборки в каждом участке собранную часть передают на участок приемки в квадрат, номер которого обозначен в листе комплектации у каждого комплектовщика, собирающего единый заказ. После сборки всего заказа кладовщик проверяет правильность собранного заказа, а далее производятся предотгрузочные операции.
Преимущества такого метода очевидны. Во-первых, время выполнения заказа сокращается в несколько раз за счет сокращения числа перемещений между местами отборки и упразднения вынужденного простоя. Во-вторых, каждый комплектовщик, «прикрепленный» к конкретной зоне, гораздо быстрее узнает номенклатуру, хранящуюся в ней, и фактически имеет возможность работать без маршрутного листа. В-третьих, появляется возможность закрепить индивидуальную ответственность за состоянием каждой складской зоны. «Минусом» этой системы некоторые руководители складов называют возможность внезапного невыхода на работу части складского персонала и отсутствия в зоне комплектовщика. Однако это уже вопрос административно-организационный, и большинство руководителей крупных складов, вводящие данную систему, сумели справиться с данным негативным фактором методами мотивации и административных взысканий. Во всяком случае, остается возможность «аварийной» переброски персонала из другой зоны.
Применение на практике указанных выше способов совершенствования организации технологического процесса позволит:
— снять проблему очередей транспортных средств;
— повысить экономичность и надежность работы склада;
— снизить риск остановки технологического процесса;
— рационально использовать складские площади;
— выявлять излишки и недостачи сразу после реализации товара, а не после инвентаризации;
— минимизировать трудовые затраты.
ЗАКЛЮЧЕНИЕ
Организация технологических процессов на складе предусматривает использование складских мощностей, всех необходимых технических средств и складского персонала с целью выполнения задач, стоящих перед складом. Оптимальное использование складских ресурсов при минимизации затрат на грузопереработку и удовлетворении потребностей клиентов по уровню обслуживания свидетельствует о рациональной организации технологических процессов на складе. Совершенствование применяемых решений с целью их рационализации, требует проведения анализа технологических решений на складе с определенной периодичностью или в зависимости от изменений внешней и внутренней среды, влияющей на деятельность склада или отражающуюся на политике обслуживания клиентов. Рациональная организация технологического процесса зависит от многих факторов:
функционального назначения склада;
компоновочных решений складских помещений и зонирования зон основного производственного назначения;
параметров склада;
применяемой системы складирования;
организационной структуры управления складом и распределения полномочий;
номенклатуры перерабатываемого груза и специфики его хранения;
внешних транспортных средств, осуществляющих доставку;
особенностей погрузочно-разгрузочного фронта и его технического оснащения;
интенсивности входящих и выходящих потоков;
внешних товароносителей;
имеющегося складского оборудования;
принятого документооборота;
количества обрабатываемых заказов в сутки и их ассортиментного разноообразия и т. д.
Каждый из перечисленных факторов оказывает существенное влияние на выполнение той или иной операции технологического процесса, однако общая последовательность проведения основных этапов грузопереработки на складе традиционно одинакова: разгрузка — приемка — складирование (хранение) — отгрузка.
Успех рациональной организации технологического процесса на складе тесно связан с оптимальным выбором и реализацией системы складирования, которая является основой применяемых объемно-планировочных решений на складе, определяет, какими техническими средствами будет осуществляться каждая операция процесса. А также с рациональной организационной структурой управления складом, включая функциональное распределение полномочий между персоналом склада и его численностью, механизацией и автоматизацией работ там, где это технологически возможно и экономически выгодно. Рациональное осуществление технологического процесса на складе является залогом рентабельности склада.
СПИСОК ИСПОЛЬЗОВАННЫХ ИСТОЧНИКОВ
1. Волгин, В. В. Кладовщик. Устройство складов. Складские операции. Управление складом. Нормативные документы. — 5-е изд., стер. — М: Ось — 89, 2008. — 544с.
2. Гаджинский, А.М., Логистика: Учебник — 18 изд., перераб. и доп.- М.: Издательско-торговая корпорация «Дашков и К», 2010. — 484с.
3. Гаджинский, А. М. Современный склад. Организация, технологии, управление и логистика: учеб.- практическое пособие. — М.: ТК Велби, Издательство Проспект, 2005. — 176с.
4. Дыбская В. В., Зайцев Е. И., Сергеев В. И., Стерлигова А. Н., под редакцией Сергеева В. И.; Логистика: Учебник — М.: Эксмо, 2008. — 944с. — (Полный курс MBA).
5. Дыбская, В. В. Управление складированием в цепях поставок. — М.: Издательство «Альфа-Пресс», 2009. — 720с.
6. Манжосов, Г. П. Технологический процесс на складе // Современный склад. — 2003 — № 1.
7. Николайчук, В.Е. Транспортно-складская логистика: Учебное пособие — 4-е изд. — М.: Издательско-торговая корпорация «Дашков и К», 2010. — 452с.
8. Таран, С. А. Как организовать склад. Практические рекомендации профессионала. Изд. 2-е. — М.: Издательство «Альфа-Пресс», 2008. — 240с.
9. Об утверждении Инструкции о порядке хранения материальных средств вещевой службы в Вооруженных Силах Республики Беларусь: Приказ Министерства обороны от 25 апреля 2006 г., № 15// Национальный реестр правовых актов РБ. -2006г -№ 93. — 9/25 362.
10. Об утверждении Руководства по хранению техники связи и комплексов средств автоматизации в Вооруженных Силах Республики Беларусь: Приказ начальника Генерального штаба Вооруженных Сил — первого заместителя Министра обороны Республики Беларусь от 30 ноября 2007 года № 683
11. Сербул, И. Т. Логистика складирования: учеб.-метод. пособие, — Минск: БГЭУ, 2009. — 63с.
12. Об утверждении Инструкции о порядке организации хозяйственной деятельности в органах военного управления, соединениях, воинских частях, военных учебных заведениях и организациях Министерства обороны Республики Беларусь: Постановление Министерства обороны Республики Беларусь от 8 апреля 2008 г. № 41// Национальный реестр правовых актов РБ — № 8/18 661 от 23.04.2008 г.
13. Демин, В. Б. Оптимизация технологического процесса на складе «Склад и техника», № 9/2005. — 15с.
ПРИЛОЖЕНИЕ Перечень вооружения и военной техники, поступивших на склад инженерно-технического имущества 1 квартале 2014 года на хранение
№ п/п | Наименование ПРМ | Общее кол-во (к-тов) | По категориям | год изготовле-ния | Срок службы | ||||
II | III | IV | V | ||||||
Миноискатель МН-8 | 1983;89 | 18 лет | |||||||
Тент урывочный | 18 лет | ||||||||
Мотопомпа — МП-800 | 1983 — 91 | 18 лет | |||||||
Автомобильный кран КС-4561 | 290 тыс. км (24 года) | ||||||||
Лопата саперная | 1983 — 88 | 8 лет | |||||||
Лопата мала саперная | 18 лет | ||||||||
Пила поперечная | 18 лет | ||||||||
Кирко-матыга тяжолая | 1985 — 88 | 18 лет | |||||||
Лом | 1987 — 89 | 18 лет | |||||||
Экскаватор ЭОВ-4421 | 18 лет | ||||||||
Экскаватор ЭО-4121 | 1984 — 89 | 18 лет | |||||||
Экскаватор ЭОВ-2621 | 1987 — 88 | 18 лет | |||||||
Экскаватор ЭОВ-4221 | 18 лет | ||||||||
Магнето | 1988 — 91 | 18 лет | |||||||
Генератор | 18 лет | ||||||||
Электростанция ЭСД-10-ВС-230М | 1983; 88 | 25 лет | |||||||
Электростанция ЭСД-30-ВА (ВА-1) | 1962 — 72 | 25 лет | |||||||
Электростанция ЭСД-30-ВАМ-2 | 1980 -84 | 25 лет | |||||||
Электростанция ЭСД-30-ВАМ-4 | 1988 — 91 | 25 лет | |||||||
Изделие Н-3 | 1984 — 89 | 18 лет | |||||||
ПБШ2-П-8 | 246,5 тыс.км. (24 года) | ||||||||
Изделие КЛ-5 | 18 лет | ||||||||
Изделие КЛП-4М | 1988 — 89 | 18 лет | |||||||
Прицеп 2ПН-2М | 1982 — 85 | 246,5 тыс.км. (24 года) | |||||||
Изделие МРС-ОР | 1983 — 88 | 18 лет | |||||||
Прицеп 1П-1,5 | 1975 — 79 | 246,5 тыс.км. (24 года) | |||||||
Изделие ЭСД-20 ВЛ/230−4/400 М2 | 1978 — 81 | 25 лет | |||||||
Изделие СПМ-1А | 18 лет | ||||||||
Изделие ЭСД-30/ВС/400-М-4 | 25 лет | ||||||||
Мастерская ОЭ | 1981 — 83 | 18 лет | |||||||
Изделие 9Ф660 | 1987;89 | 18 лет | |||||||
Изделие ЭСБ-4-ВЗ-М1 | 1979 — 88 | 25 лет | |||||||
Изделие Э2 | 1984;91 | 18 лет | |||||||
Изделие «Плазма-2» (адб 12У1.302) | 1986 — 90 | 18 лет | |||||||
Изделие ТП-12М | 18 лет | ||||||||
Изделие ТП-11М | 1988 — 89 | 18 лет | |||||||
Изделие ПМ-2−70 | 1974 — 84 | 18 лет | |||||||
Изделие ПМ-2−70М | 1985;87 | 18 лет | |||||||
Изделие МРС-АР | 1979 — 88 | 18 лет | |||||||
Всего | 1979 — 88 | 18 лет | |||||||
Примечание — Источник: собственная разработка