Совершенствование технологического процесса и технических средств для измельчения пористых строительных материалов: На примере керамзита
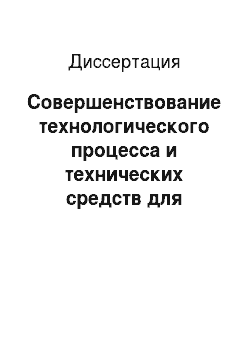
Обзор современного состояния производства пористых заполнителей способом дробления показывает, что существующие технологии и устройства не позволяют получать качественного продукта в соответствии с требованиями, а также обладают высокой энергозатратностью процесса и загрязняют окружающую среду вредной пылью. Анализ литературных источников показывает, что процессы, связанные с получением пористых… Читать ещё >
Содержание
- 1. СОСТОЯНИЕ ВОПРОСА И ВЫБОР НАПРАВЛЕНИЯ ИССЛЕДОВАНИЙ
- 1. 1. Применение и получение пористых заполнителей для различных бетонов
- 1. 2. Анализ существующих конструкций устройств для измельчения пористых строительных материалов
- 1. 3. Состояние исследований процесса измельчения пористых строительных материалов
- 2. ТЕОРЕТИЧЕСКИЕ ИССЛЕДОВАНИЯ ПРОЦЕССА ИЗМЕЛЬЧЕНИЯ ХРУПКИХ ПОРИСТЫХ МАТЕРИАЛОВ И РАБОЧЕГО ПРОЦЕССА ИЗМЕЛЬЧАЮЩЕГО УСТРОЙСТВА
- 2. 1. Влияние технологических факторов на эффективность процесса получения керамзита мелких фракций
- 2. 2. Конструктивно-технологическая схема устройства для измельчения пористых материалов
- 2. 3. Параметрическая модель функционирования устройства для измельчения
- 2. 4. Теоретическое обоснование основных параметров устройства
- 2. 4. 1. Определение минимальной частоты колебаний подвижной плиты
- 2. 4. 2. Влияние параметров рабочего органа на энергозатраты процесса измельчения
- 2. 4. 3. Определение оптимальной формы рабочего органа
- 2. 4. 4. Обоснование основных технологических параметров устройства
- 2. 4. 5. Определение энергии затрачиваемой на процесс измельчения
- 2. 4. 6. Оценка качества функционирования устройства
- 3. 1. Программа экспериментальных исследований
- 3. 2. Общая методика экспериментальных исследований
- 3. 3. Описание экспериментальных установок 77 3.4 Методика проведения опытов
- 3. 4. 1. Определение физико — механических характеристик керамзитового сырья
- 3. 4. 2. Методика определения влияния угла заточки рабочего органа на величину разрушающих нагрузок
- 3. 4. 3. Методика определения коэффициента трения материала различных фракций по лотку
- 3. 4. 4. Определение влияния интервала между элементами рабочего органа на процесс измельчения
- 3. 4. 5. Обоснование режимных параметров работы устройства
- 4. 1. Характеристика керамзита
- 4. 2. Основные физико-механические свойства пористых материалов
- 4. 2. 1. Прочностные свойства материала при сжатии
- 4. 2. 2. Результаты исследования трения керамзита различных фракций по поверхности лотка
- 4. 3. Влияние угла заточки рабочего органа на величину разрушающих нагрузок
- 4. 4. Влияния интервала между рабочими органами на процесс измельчения
- 4. 5. Режимные параметры работы измельчающего устройства с предлагаемым рабочим органом
- 4. 5. 1. Влияние угла наклона камеры дробления и частоты на выходные показатели процесса измельчения Ю
- 4. 5. 2. Влияние зазора в камере дробления и рабочего хода на выходные показатели процесса измельчени
- 5. 1. Производственные испытания технологической линии переработки пористых заполнителей для бетона с использованием предлагаемого устройства
- 5. 2. Испытания полученного керамзитового песка и щебня в бетоне
- 5. 3. Оценка экономической эффективности применения измельчителя
Совершенствование технологического процесса и технических средств для измельчения пористых строительных материалов: На примере керамзита (реферат, курсовая, диплом, контрольная)
В настоящее время в производстве керамзита сложилась диспропорция в выпуске мелких и крупных фракций. При потребности для производства различных бетонных и железобетонных конструкций в керамзитовом песке фракции 0.5 мм и мелком керамзите фракции 5.10 мм в количестве соответственно 20.30 и 30.40% от объема выпускаемого керамзита их общий выпуск не превышает 10%. В практике используются два способа получения керамзитового песка и мелкого керамзитового гравия, за счет обжига соответствующего полуфабриката в печах «кипящего слоя» и измельчения крупных фракций керамзита (свыше 20.40 мм.) и брака его производства (спеки, свары и т. п.).
Известно, что производство обжигового керамзитового песка требует специального дорогостоящего оборудования, имеет низкую производительность печей для его обжига и высокие энергозатраты. Также при дроблении утилизируется крупный гравий, который непригоден для изготовления легкобетонных конструкций. В связи с этим второй способ получения легких заполнителей более эффективен. Как правило, эта операция осуществляется на вальцевых дробилках и сопровождается значительными выбросами пыли и создает неблагоприятную экологическую обстановку вокруг производства. Основным недостатком производства керамзита способом дробления является низкий коэффициент выхода готовой продукции, вследствие переизмельчения части материала до пылевидной фракции. Кроме того, применение в бетоне пористого песка с повышенным содержанием пыли (фракции менее 0,16 мм) существенно ухудшает его свойства.
Обзор современного состояния производства пористых заполнителей способом дробления показывает, что существующие технологии и устройства не позволяют получать качественного продукта в соответствии с требованиями, а также обладают высокой энергозатратностью процесса и загрязняют окружающую среду вредной пылью. Анализ литературных источников показывает, что процессы, связанные с получением пористых заполнителей мелких фракций изучены не полно. Неполно изучены взаимосвязи этих процессов с физико-механическими свойствами материалов и конструктивно-технологическими параметрами устройств.
Исследованию процесса получения пористых материалов (керамзита) посвящены труды Ахундова А. А, Полинковской А. И., Комиссаренко Б. С., Петрова В. П., Чикноворяна А. Г. Эльконюка А.А., Хохрина Н. К., H.JI. Антоненко и др.
Теоретическая основа, посвященная измельчению хрупких строительных материалов сформулирована в работах Ребиндера ПА., Кирпичева В. Л., Еремина Н. Ф., Демидова А. Р., Чиркова С. Е., Доценко А. И., Волкова Д. П., Моргулиса M. JL, Левенсона Л. Б., Андреева С. Е., С. В. Мельникова и др.
Проведенный анализ устройств для дробления пористых заполнителей показал, что для этих целей применяются различные измельчающие устройства. Однако существующие устройства не в полной мере обеспечивают эффективное производство пористых заполнителей мелких фракций.
В связи с этим, создание устройств, обеспечивающих получение дробленых пористых заполнителей для бетона, в рамках требований производства бетонов и обладающих существенным ресурсосбережением, является актуальным.
Цель работы. Повышение эффективности процесса измельчения, обеспечение ресурсосбережения и повышение качества пористых материалов (заполнителя мелких фракций для бетонов).
Объект исследований. Процесс измельчения пористых хрупких строительных материалов и устройство для его осуществления.
Задачами исследования являются:
— проведение анализа устройств для измельчения пористых строительных материалов и обоснование конструкционно-технологической схемы измельчающего устройства;
— определение физико-механических свойств исследуемых легких заполнителей;
— выполнение теоретических исследований процесса работы устройства для измельчения пористых строительных материалов с целью определения его конструктивно-режимных параметров;
— проведение экспериментальных исследований устройства для выявления влияния его параметров на гранулометрические характеристики легких заполнителей;
— проведение производственных испытаний промышленного образца названного устройства и оценивание экономической эффективности его использования.
Методика исследований. Решение поставленных задач осуществлялось с помощью методов параметрического и математического моделирования, теории измельчения, математической статистики. Теоретические исследования заключались в получении зависимостей, позволяющих установить оптимальные конструктивно-кинематические и технологические параметры измельчающего устройства.
Экспериментальные исследования выполнены на специально изготовленных установках с использованием существующих и предложенных методик в соответствии с действующими стандартами.
Научную новизну составляют:
— параметрическая модель функционирования устройства для измельчения хрупких пористых строительных материалов;
— методика расчета производительности камеры основного измельчения и камеры предварительного измельчения в зависимости от поступающего потока гранул и кусков материала;
— выражения для определения геометрических параметров устройства и затрачиваемой мощности.
Практическая значимость. Разработано устройство для измельчения гранул и кусков керамзита обеспечивающее получение пористого заполнителя с минимальным выходом пылевидной фракции и минимальными затратами энергии. Опытный образец измельчающего устройства испытан в условиях производства керамзита на Безымянском керамзитовом заводе (ОАО «Легкий керамзит») и принят в эксплуатацию.
Апробация. Основные положения диссертации доложены, обсуждены и одобрены: на 3-й Международной научно-практической конференции.
Безопасность транспортных систем" (МАНЭБ, г. Самара) 2002 г.- на 59, 60 и 61-й научно-практических конференциях «Актуальные проблемы в строительстве и архитектуре. Образование, наука, практика» (СамГАСА, г. Самара) в 2002, 2003 и 2004 гна региональной научно-практической конференции «Вузы Сибири и Дальнего Востока ТРАНССИБу» (СГУПС, г. Новосибирск) в 2002 гна межвузовской научно-практической конференции «Вклад ученых вузов в научно-технический прогресс на железнодорожном транспорте» (СамГАПС, г. Самара) 2003 г.- на научно-методической конференции «Проблемы строительства, реконструкции и капитального ремонта зданий и сооружений на железнодорожном транспорте» (ПГУПС, г. Санкт-Петербург) 2003 г.- на 57-й международной научно-технической конференции молодых ученых (аспирантов, докторантов) и студентов «Актуальные проблемы современного строительства» (СПбГАСУ, г. Санкт-Петербург).
Публикации. По теме диссертационной работы опубликовано 13 печатных работ. Новизна конструкции устройства для измельчения гранулированных пористых материалов подтверждена патентом Российской федерации № 2 196 490.
Структура и объем диссертации
Диссертация состоит из введения, 5 глав, общих выводов, заключения, списка использованной литературы и 2 приложений. Она содержит 149 страниц машинописного текста и 56 иллюстрации.
ОБЩИЕ ВЫВОДЫ.
Результаты анализа существующих технических средств показали, что они не отвечают требованиям поставленной задачи — измельчению пористых строительных материалов, используемых в качестве заполнителя для бетона. Основным недостатком в технологии получения керамзита мелких фракций является низкий коэффициент выхода готовой продукции, вследствии повышенного содержания в ней пылевидной фракции, возникающей в процессе дробления. Это существенно снижает эффективность всего процесса производства заполнителя. Также основными недостатками рассмотренных устройств являются дополнительное пылеобразование, высокая энергоемкость, большая материалоемкость. Наиболее перспективным является избирательное дробление хрупких пористых материалов, при котором рабочие органы измельчителя воздействуют концентрированными нагрузками только на частицы недоизмельченного материала, при этом, не измельчая готовой фракции продукта.
На основании теоретических исследований была разработана параметрическая модель функционирования предлагаемого устройства, обоснованы выражения для определения минимальной частоты колебаний подвижной плиты, затрат энергии, расходуемой на процесс измельчения, затрачиваемой мощности. Разработана методика расчета производительности камер предварительного и основного измельчения предлагаемого устройства.
Экспериментально установлено, что дробление гранул и кусков исследованных видов керамзита лучше осуществлять клиновидным рабочим органом с углом заточки 40.50°, угол наклона лотка должен составлять 30.40°, частота колебаний подвижной плиты 150.270 об/мин, амплитуда колебаний подвижной плиты 10. 14 мм, зазор между лотком и клиновидным рабочим органом 3.4 мм, расстояние между клиновидными пластинами 5.9 мм. При таком режиме работы удельная энергоемкость процесса составляет 0,2. 0,3 Вт* с/кг, выход готовой продукции увеличился на 5. 7%.
Производственными испытаниями установлено, что в сравнении с агрегатом СМ-5 (существующий вариант) предлагаемое устройство позволяет в процессе производства получать качественный керамзитовый песок и щебень, обеспечить снижение энергоемкости в 2,4 раза, повысить качество измельчения (у существующего варианта содержание пылевидной фракции составляет 8.15%, у предлагаемого не более 3%). Использование предлагаемого устройства позволит обеспечить экологическую безопасность процесса переработки керамзита за счет сокращения пылевидной фракции в готовом продукте. Экономия за счет повышения коэффициента выхода готовой продукции составит около 370 тыс. руб. Экономический эффект от внедрения одного измельчающего устройства составит около 385 тыс. руб. в ценах II квартала 2004 г.
Список литературы
- Адлер Ю.П. и др. Планирование эксперимента при поиске оптимальных условий. М.: Наука, 1978. — 210 с.
- Андреев С.Е., Петров В. А., Зверевич В. В. Дробление, измельчение и грохочение полезных ископаемых. 3-е изд., перераб. и доп. М.: Недра, 1980. -415 с.
- Анисимов В.П., Романенко И. И., Каледа В. Н. Оборудование для производства строительных материалов. Ч. 1., Пенза, ПГАСА, 2001. 95 с.
- Ахвердов И.Н. О научных проблемах в области легких бетонов. В кн.: Аглопорит и аглопоритбетон, Минск, 1965. — с. 14.
- Балантьев П.К., Движик В. Г. Состояние и перспективы развития технологии производства конструкций из легких бетонов. Материалы всесоюз. конф. по легким бетонам. — Минск: Стройиздат, 1970. — с. 5−37.
- Барабашкин В.П. Молотковые и роторные дробилки. М.: Недра, 1988. -112 с.
- Бауман В.А., Быховский И. И. Вибрационные машины и процессы в строительстве. М.: Высшая школа, 1977. -354 с.
- Бауман В.А., Клушанцев Б. В., Мартынов В. Д. Механическое оборудование предприятий строительных материалов, изделий и конструкций. М.: Машиностроение, 1981. -325 с.
- Беренс Б. Ударное измельчение единичных зерен хрупких материалов (сообщение о технике измельчения в Карлсруэ ФРГ в 1964 г.). № 36, 1964.
- Берзиня Н.Э., Калинин В. П. Экономика машиностроительного производства. Учебник для вузов. М.: Высшая школа, 1988. 304 с.
- Бирюков А.В., Ташкинов А. С., Шелепов В. В. Гранулометрия и процессы дробления. Кемерово, 1999. 54 с.
- Боровиков В.П., Боровиков И.П. STATISTIKA: статистический анализ и обработка данных в среде WINDOWS. М.: ИИД Филинъ, 1997. — 608 с.
- Борщевский А.А., Ильин А. С. Механическое оборудование для производства строительных материалов и изделий. М.: Высшая школа, 1987. — 242 с.14