Оптимизация конструкции подрельсового основания на высокоскоростных линиях ГАЖК «Узбекистон Темир Йуллари»
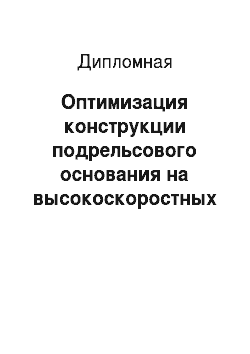
В составе железнодорожного пути железобетонные шпалы предназначены для применения на всех железнодорожных линиях и путях, по которым обращается типовой подвижной состав с нагрузками и скоростями, установленными для общей сети железных дорог, без ограничения по грузонапряженности. При этом в странах СНГ, в том числе и на ГАЖК «Узбекистонтемирйуллари», типовые железобетонные шпалы предназначены для… Читать ещё >
Оптимизация конструкции подрельсового основания на высокоскоростных линиях ГАЖК «Узбекистон Темир Йуллари» (реферат, курсовая, диплом, контрольная)
Оптимизация конструкции подрельсового основания на высокоскоростных линиях ГАЖК «Узбекистон Темир Йуллари»
Диссертация на соискание степени магистра
подрельсовый шпала железнодорожный Шпалы — традиционный и наиболее распространенный тип подрельсового основания. Основные материалы для них — дерево, железобетон и металл. В железнодорожном пути шпалы обычно укладываются на балластный слой верхнего строения пути и обеспечивают неизменность взаимного расположения рельсовых нитей, воспринимают давление непосредственно от рельсов или от промежуточных скреплений и передают его на подшпальное основание (рис. 1).
Рис. 1. Элементы верхнего строения пути: 1 — рельс; 2 — шпала; 3 — промежуточное рельсовое скрепление; 4 — песчаная подушка; 5 — щебеночный балласт; 6 — земляное полотно В целом шпалы служат для восприятия давления от рельсов и передачи его балластному слою; упругой переработки динамических воздействий на путь; обеспечения постоянства ширины колеи и совместно с балластом устойчивости рельсошпальной решетки в горизонтальной и вертикальной плоскостях. [13−18]
Первоначально шпалы были деревянными. Однако на основании многочисленных расчетов, опытно-конструкторских работ, экспериментальных и эксплуатационных исследований в настоящее время наиболее перспективным видом подрельсового основания в большинстве стран мира принята железобетонная шпала. [1−2-18]
Железобетонные шпалы имеют следующие достоинства [1]: сравнительно большой срок службы (40−50 лет), однородная упругость пути по длине, хорошая устойчивость в балласте против сдвига, возможность придания им целесообразной формы. Жесткие динамические нагрузки, ощутимые температурные перепады, увлажнение и высушивание, замораживание и оттаивание, воздействие органо-нефтяной среды и другие агрессивные факторы предъявляют исключительно высокие требования к надежности и долговечности этих изделий. В соответствии с этим шпалы должны обладать достаточной прочностью, упругостью, хорошо сопротивляться механическому износу и перемещениям, быть простыми по форме, иметь наибольший срок службы и наименьшую стоимость при изготовлении и содержании.
В составе железнодорожного пути железобетонные шпалы предназначены для применения на всех железнодорожных линиях и путях, по которым обращается типовой подвижной состав с нагрузками и скоростями, установленными для общей сети железных дорог, без ограничения по грузонапряженности. При этом в странах СНГ, в том числе и на ГАЖК «Узбекистонтемирйуллари», типовые железобетонные шпалы предназначены для применения с рельсами типов Р75, Р65 и Р50 на прямых участках пути и в кривых радиусом не менее 350 м. Число шпал на 1 км (эпюра) зависит от величины нагрузок на рельсы, грузонапряженности, скоростей движения поездов, типа рельсов, рода балластного слоя, плана и профиля пути. В странах СНГ приняты 3 эпюры: 1600 шт./км (на второстепенных путях), 1840 и 2000 (в зависимости от плана линии и скорости движения). [7−8-9]
Современная железобетонная шпала — цельнобрусковая из предварительно напряженного железобетона, армированная высокопрочной проволокой [1−5]. Она представляет собой железобетонную балку переменного сечения. На таких балках имеются площадки для установки рельсов, а также отверстия под болты рельсошпального скрепления (при забивании в отверстия деревянных пробок используются также костыльные и шурупные соединения). Современные типы шпал имеют анкеры. Железобетонные шпалы изготавливаются с предварительным натяжением арматуры. Технология изготовления железобетонных шпал следующая: в специальную форму помещаются струны арматуры, которым сообщаются растягивающие усилия. Затем под действием вибратора форма заполняется бетоном. Когда бетон затвердевает, напряжения передаются на бетон. Такой способ изготовления шпал придаёт им трещиностойкость и предохраняет шпалу от раскола под подвижным составом.
Массовая укладка железобетонных шпал началась только в 60-х — 70-х годах прошлого столетия.
В Республике Узбекистан железобетонные шпалы (С-56−2, ШС-1, Ш1−1) в массовом порядке стали применяться также со второй половины прошлого века. Многолетняя эксплуатация предварительно напряженных железобетонных шпал на железных дорогах мира доказала их надежность. Существуют участки железных дорог, на которых преднапряженные железобетонные шпалы прослужили более 40−50 лет и не имели каких-либо существенных повреждений. В мире в настоящее время уложено более одного миллиарда шпал.
Однако, в настоящее время шпалы С-56−2, ШС-1, Ш1−1 с жестким клеммно-болтовым рельсовым скреплением типа КБ морально устарели и на смену им приходят новые типы шпал с упругими (эластичными) типами рельсовых скреплений.
В связи с отмеченным настоящая диссертация посвящена исследованию и оптимизации работы современного типа шпал с упругими типами скреплений на ГАЖК «Узбекистон темир йуллари». Это положение определяет актуальность выполненного исследования.
1. Обзор литературы, постановка вопроса, задачи и цели исследований
1.1 Общие сведения
Первые железобетонные железнодорожные шпалы были изготовлены в России в 1903 г. и испытаны в лаборатории Петербургского института инженеров путей сообщения, а затем уложены на одной из станций Финляндской железной дороги. С 1903 по 1927 гг. попытки применения железобетонных шпал в России неоднократно повторялись — к числу наиболее крупных опытов относится укладка 4-х тыс. шпал в 1922 г. на Южной дороге.
На первом этапе отработки конструкции шпалы железобетонной были проведены широкие эксплуатационные испытания двухшарнирных трёхблочных шпал, двухблочных с металлической соединительной поперечиной (таврового или трубчатого сечения) и цельнобрусковых шпал из предварительно напряжённого железобетона. Конструкционные особенности этих типов шпал:
— цельнобрусковые, представляющиеиз себя один монолитный брус для опирания двух рельсовых нитей (рис 2а);
— двухшарнирные, представляющие свободную шарнирную конструкцию из трех блоков, соединенных друг с другом, напряженной арматурой (рис 2б);
— двухблочные, состоящие из двух подрельсовых блоков из напряженного железобетона, жестко соединенных металлическим элементом (рис 2в);
— полушпалы, представляющие собой несвязанные друг с другом подрельсовые блоки, укладываемые отдельно под каждую рельсовую нить.
При этом наибольший вклад в разработку вопросов конструкции и рациональной системы эксплуатации железобетонных шпал внесли следующие ученые: Г. М. Шахунянц, И. Ф. Вериго, В. Я. Шульга, М. А. Фришман, С. П. Першин, Золотарский А. Ф., Андреев Г. Е., Ю. Д. Волошко, В. И. Ангелейко, Евдокимов Б. А., Исаев Н. М., Крысанов Л. Г., Серебренников В. В., Федулов В. Ф., Клинов С. И. Среди ученых Республики Узбекистан можно назвать имена, таких ученых как Тарсин В. П., Иргашев Ш. А., Виноградов В. А., Овчинников А. Н. и др.
Многолетний опыт применения железобетонных шпал на различных железных дорогах с различными эксплуатационными параметрами определил цельнобрусковые железобетонные шпалы как наиболее оптимальную конструкцию. Это положение принимается в настоящее время большинством стран мира.
При этом в большинстве стран мира подавляющее предпочтение также отдается моноблочным железобетонным шпалам [1,4,5] с предварительно напрягаемой арматуро, хотя в ряде стран применяются и другие конструкции шпал.
Рис. 2. Моноблочные железобетонные шпалы зарубежных стран
Рис. 3. Двухблочная шпала типа RS (Франция) Массовое применение железобетонных шпал на железных дорогах мира объясняется рядом присущих им ценных качеств, к которым относятся:
— высокая долговечность шпал при небольшой одиночной смене в процессе эксплуатации (расчетный срок их службы составляет не менее 50 лет по сравнению с 15 — 20 годами для пропитанных деревянных шпал);
— обеспечение повышенной устойчивости рельсовой колеи от боковых сдвигов и выброса вверх, т. е. увеличение стабильности пути, что способствует применению бесстыкового пути и расширению сферы его укладки;
— однородность физического состояния шпал на протяжении всего срока службы, положительно влияющая на обеспечение одинаковых характеристик упругости рельсового основания;
— возможность придания шпалам целесообразных геометрических форм с учетом действующих на шпалу сил.
Недостатком железобетонных шпал является большая масса, наличие электропроводности, высокая жесткость и сложность крепления рельсов к ним. Для повышения упругости под рельсы укладывают амортизирующие прокладки. Во избежание утечки электрического тока применяют рельсовые скрепления специальной конструкции с электроизоляционными деталями. [1−2-17−18]
Основные конструкционные особенности железобетонных шпал, основные характеристики материалов, применяемых при изготовлении железобетонных шпал и основные технологические характеристики их производства в различных странах мира приведеныв табл. 1−3.
Первые типовые цельнобрусковые шпалы С-55−1 и С-55−2 изготавливались в 1955;1956 гг. и были уложены на протяжении нескольких десятков километров. Основными недостатками этих шпал были: недостаточная толщина защитного слоя бетона, излишнее количество ненапряженной арматуры, большое ослабление подрельсовых частей шпалы деревянными дюбелями, расположенными попарно в одном поперечном сечении. Кроме того, в этих шпалах часто применялась гладкая арматура вместо арматуры периодического профиля 3 мм. Шпала рассчитана на применение раздельного скрепления типа К2 с клинчатыми подкладками, поскольку подрельсовые площадки шпалы подуклонки не имеют.
В 1956 г. с учетом всего накопленного опыта применения струнобетонных шпал была разработана струнобетонная шпала С-56, которая была затем утверждена как основной тип железобетонных шпал на перспективу (ГОСТ 10 629 — 88).
На ГАЖК «Узбекистон темир йуллари» в настоящее время применяется два типа железобетонных шпал: Ш1−1-1 со скреплением КБ и шпалы типа BF70 со скреплением «Pandrol Fastclip» (рис. 5).
Рис. 4. Путь со скреплениями Pandrol Fastclip (слева) и КБ-65 (справа) Таблица 1. Основные конструкционные особенности железобетонных шпал
Страна | Основной тип шпал. | Условное обозначение | Тип напрягаемой арматуры | Число проволок и диаметр арматуры | Масса шпалы, кг | Срок службы, лет | Общее кол-во уложенных шпал, тыс. штук | |
СНГ | цельнобрусковые | Ш1 44х3 | проволочная | 44×3 мм | 280 000 | |||
Узбекистан | цельнобрусковые | BF70 | проволочная | 16×5 мм | ||||
Венгрия | цельнобрусковые | LX | проволочная | 60×2,5 мм | ; | |||
Польша | цельнобрусковые | JNBK-7 | пряди | 8х7×2,5 мм | 210−245 | ; | ; | |
Германия | цельнобрусковые | B50, B58, B70 | стержневаязакаленная | 8х6,9 мм 4х9,7 м 4х10 мм | 236−295 | ; | ||
Англия | цельнобрусковые | F23 | стержневая | ; | ||||
Япония | цельнобрусковые | RT | проволочная и стержневая | 32×2,6 мм 4х12 мм | ; | |||
США | цельнобрусковые | E, MR-2, RT7 | стержневая, проволочная | 4х11 м | 280−408 | |||
Франция | двухблочные | RS | проволочная | 6−7 мм | ; | ; | ||
Швеция | цельнобрусковые | стержневая, проволочная | 19 мм 44×3 мм | |||||
Австралия | цельнобрусковые | ; | ; | ; | ; | |||
Бельгия | цельнобрусковые | ; | ; | ; | ; | |||
Чехия | цельнобрусковые | ; | ; | ; | ; | |||
Греция | цельнобрусковые | ; | ; | ; | ; | |||
Нидерланды | цельнобрусковые | ; | ; | ; | ; | ; | ||
Норвегия | цельнобрусковые | ; | ; | ; | ; | |||
Швейцария | цельнобрусковые | ; | ; | ; | ; | |||
Словакия | цельнобрусковые | ; | ; | ; | ; | ; | ||
Таблица 2. Основные характеристики материалов для изготовления шпал
Страна | средний расход цемента, кг/м3 бетона | Максимальная крупность щебня, мм | Водоцементное отношение | Отпускная прочность, МПа | Марка бетона по прочности на сжатие, МПа | |
СНГ | 440−460 | 0.36 | ||||
Узбенистан | 0.30 | 60−70 | ||||
Венгрия | 450−550 | ; | ; | 37.5 | ||
Польша | 470−490 | ; | ; | |||
Германия | 380−390 | 0.38 | 40−45 | |||
Англия | 380−390 | 0.38−0.42 | 28−35 | |||
Япония | 450−470 | 25.4 | 0.35 | |||
США | 375−450 | 0.3 | 35,5−57 | 65−73 | ||
Франция | 350−360 | 0,36−0.39 | ; | |||
Швеция | 390−400 | 0.35 | ; | |||
Таблица 3. Основные технологические характеристики производства шпал
Страны | Технологическая схема | Время ТВО, час | Режим ТВО/ tmax, 0С | Продолжительность оборачиваемости форм, час. | Сила предварительного натяжения, кН | |
СНГ | поточно-агрегатная | 2+3+4+2/80 | ||||
Узбекистан | стендовая | 2+3+4+2/60 | ||||
Венгрия | поточно-конвейерная | /80 | 7.5−12 | |||
Польша | стендовая, поточно-конвейерная | 3+2+4+5/85 | 12−16,5 | |||
Германия | поточно-агрегатная | /70 | 8−12 | |||
Англия | стендовая | ; | без ТВО ; | |||
США | стендовая, конвейерная | /66 | ||||
Франция | поточно-агрегатная | ; | без ТВО | ; | ||
Швеция | стендовая | без ТВО | без ТВО | 16−24 | ||
1.2 Железобетонные шпалы Ш-1-1, изготавливаемые по ГОСТ 10 629 — 88/4/
Конструкция железобетонных шпал, эксплуатируемых в большинстве стран бывшего Советского Союза со второй половины ХХ века, постоянно совершенствовалась. В настоящее время она установлена в соответствии с ГОСТ 10 629–88 (взамен ГОСТ 10 629–78), вступившем в действие с 01.01.1990 г. (рис. 6).
Железобетонные шпалы по ГОСТ 10 629– — 88 В зависимости от типа рельсового скрепления подразделяются на:
Ш1 — для скрепления КБ (Ш1−1 — с первым вариантом исполнения подрельсовой площадки; Ш1−2 — со вторым вариантом исполнения подрельсовой площадки);
Ш2 — для нераздельного клеммно — болтового скрепления типа БПУ (этот тип скрепления на ГАЖК «Узбекистон темир йуллари» не эксплуатируется).
Шпалы армированы проволокой периодического профиля диаметром 3 мм (44 шт.); сила натяжения одной проволоки 8,1 кН. Глубина подрельсовых выемок у этих шпал 25 мм. Для изготовления шпал применяют бетон марки не ниже 500. Масса шпалы около 265 кг.
Конструкция шпалы позволяет использовать ее при рельсах Р50, Р65 и Р75.
Особенность шпалы С-56−2 состоит в том, что ширина ее увеличивается к торцам. Это создает большую опорную площадь там, где давление на балласт у железобетонных шпал наибольшее. Кроме того, с уширением подошвы увеличивается площадь торца шпалы, что увеличивает устойчивость пути в поперечном направлении. Опорные подрельсовые площадки запроектированы с подуклонкой, что позволяет применять скрепления с плоской металлической подкладкой или совсем без подкладок. [3−5]
Рис. 5. Железобетонная шпала Ш1 — 1.
Следует отметить, что в процессе эксплуатации пути с железобетонными шпалами Ш1 — 1 достаточно интенсивно изнашиваются рельсовые скрепления. Это побуждает заменять рельсошпальную решетку, укладывая старогодную на менее деятельные линии, а затем — на станционные и подъездные пути. Такая система многократной перекладки путевой решетки с железобетонными шпалами позволит обеспечить срок их службы больше 50 лет.
1.3 Железобетонные шпалы, изготавливаемые по Евростандарту ЕN 13 230 — 1,2 /2,5/
Начиная с 2004 года на магистральных линиях ГАЖК «Узбекистон темир йуллари» в массовом порядке стали укладываться и эксплуатироваться железобетонные шпалы современного типа BF70 (рис. 77) с упругим (эластичным) промежуточным рельсовым скреплением типа «Pandrol Fastclip» (Англия). Шпалы изготавливаются местным производителем в соответствии с Евростандартом EN 13 230 — 1,2, гармонизированном на территории Республики Узбекистан (O'zDStEN 13 230 — 1,2).
В шпалах BF70 используется высокопрочная проволока Вр класса 1400 диаметром 5 мм, что позволило уменьшить количество проволок в шпале в 3 раза по сравнению со шпалами типа ШС1. Шпалы BF 70 имеют прочностные параметры шпал в среднем на 25−30% выше, чем у шпалы типа Ш-1. Это позволяет укладывать и эксплуатировать их на магистральных линиях любых классов, включая скоростные и высокоскоростные линии, а также участки с повышенных осевых нагрузках. При сборке, укладке и эксплуатации шпал BF70 применяется меньшая эпюра: [5]
1720 шпал/км — в прямых участках пути;
1840 шпал/км — в кривых радиуса менее 2000 м.
Только за счет этого экономится значительные средства (около 14 000 $/км). Основные характеристики шпалы типа BF 70 приведены в табл. 4
Рис. 6. Железобетонная шпала BF70 со скреплением «PandrolFastclip»
Кроме того, существенно сокращаются затраты труда на сборку путевой решетки с эластичными типами скреплений на путевых производственных базах, т.к. шпалы выходят с завода по их производству в комплекте со скреплениями (рис8б). На путевых производственных базах шпалы раскладываются по эпюре и после установки рельсов клеммы переводятся в рабочее положение (рис. 8в), после чего рельсошпальная решетка транспортируется к месту укладки. [15]
Таблица 4 — Основные характеристики шпалы типа BF 70
Количество шпал на 1 км на прямых участках | 1720 шт. | |
Ширина рельсовой колеи | 1520 мм* | |
Тип рельса (с шириной подошвы 150 мм) | Р65, Р75, UIC60 | |
Уклон подрельсовых площадок | 1/20 | |
Длина шпалы | 2700 мм | |
Площадь опирания (площадь нижней постели шпалы) | 0,72 м2 | |
Скорости движения пассажирских поездов | до 250 км/ч** | |
Скорости движения грузовых поездов | до 100 км/ч** | |
Максимальная осевая нагрузка от колес подвижного состава | 25 т/ось** | |
Класс бетона / марка бетона | не ниже В45/М600 | |
Передаточная прочность бетона | не ниже 40 МПа | |
Марка бетона по морозостойкости | F200 | |
Вид промежуточного рельсового скрепления скрепления | PandrolFastclip, Vossloh W14, КБ65*** | |
Расчетный срок службы шпал BF 70 | не менее 50 лет | |
*Ширина колеи 1520 мм является универсальной для стран СНГ. Технология изготовления шпал BF 70 предусматривает возможность изменения этого параметра в любую сторон.
**По желанию заказчика скорости движения и осевые нагрузки могут быть увеличены (за счет увеличения величины предварительного напряжения проволок)
***Технология изготовления позволяет в кратчайшие сроки модифицировать производственную линию для выпуска шпал с любым типом скреплений.
а) нерабочее положение б) положение «парковки» в) рабочее положение Рис. 7. Схема монтажа скрепления «Pandrol Fastclip»
Следует также отметить, что при эксплуатации указанной конструкции железнодорожного пути расходы на его текущее содержание являются существенно более низкими, чем при применении традиционных скреплений типа КБ. Это связано с тем, что расходы на содержание скреплений «Pandrol Fastclip» в процессе эксплуатации практически отсутствуют, так как в конструкциях скреплений использован принцип «установить и забыть».
Ниже приведены основные преимущества использования шпал BF70 относительно шпал Ш1-1:
v спроектированы и производятся по Евростандарту EN 13 230 — 1,2 с использованием системы менеджмента качества согласно международному стандарту ISO 9001, что обеспечивает высочайшее качество шпал и их соответствие аналогичной продукции ведущих мировых производителей;
v по параметрам прочности и трещиностойкости шпалы BF70 на 25−30% превосходят шпалы Ш1−1, что позволяет использовать их на магистральных линиях любых классов, включая скоростные и высокоскоростные участки (200−250 км/ч) и линии с повышенными осевыми нагрузками (30 т/ось);
v укладываются и эксплуатируются в пути с меньшим количеством шпал на километр, за счет чего экономия составляет до $ 17 000 на каждом километре;
v монтаж всех элементов эластичных скреплений выполняется на заводе, что в 8−10 раз сокращает затраты труда при сборке путевой решетки, а также исключает возможность утери элементов скреплений или их некомплектной поставки;
v применение скрепления «Fastclip» позволяет выполнять быстрый монтаж / демонтаж подрельсового узла при помощи специального инструмента (входит в комплект поставки), обеспечивая защищенность от несанкционированного демонтажа; при этом отсутствие в шпале и в скреплениях болтовых и шурупных соединений делает шпалу BF70 незаменимой, особенно в условиях пустынь, засоленных почв, а также на участках с повышенным снегозаносом и низкими температурами;
v минимизация расходов на текущее содержание пути, так как при эксплуатации практически отсутствуют затраты на обслуживание шпал BF70 и скреплений;
v технологические преимущества изготовления шпал BF70: высокоточное дозирование компонентов бетона; индивидуальное и контролируемое натяжение каждой из проволок; использование специальных добавок, обеспечивающих марку бетона не ниже В45; высокая передаточная прочность (40 МПа); плавная передача преднапряжения на бетон и др.
1.4 Требования нормативных документов к железобетонным шпалам на скоростных и высокоскоростных участках ГАЖК «УТЙ»
1. ВСН 450-Н «Ведомственными техническими указаниями по проектированию и строительству. Железные дороги колеи 1520 мм» [7]
В настоящее время в соответствии с действующими на ГАЖК «Узбекистонтемирйуллари» ВСН 450-Нимеются приведенные ниже нормативы по укладке железобетонных шпал:
Пункт 5.10: Род и число шпал на главных путях в пределах станций, разъездов и обгонных пунктов должны соответствовать нормам, установленным для перегонов (табл. 5), на приемоотправочных путях, сортировочных горках и в сортировочных парках — по нормам не ниже IV категории. На горках с перерабатывающей способностью более 1500 вагонов в сутки род и число шпал следует принимать по нормам II категории. На прочих станционных путях следует укладывать деревянные шпалы II типа или старогодние железобетонные с числом не менее 1600 шт./км. В пределах закрестовинных кривых число шпал должно назначаться из расчета не менее 1840 шт./км, а на главных путях — 2000 шт./км.
Таблица 5. Нормы по эпюре железобетонных шпал
Показатель | Мощность верхнего строения пути на железнодорожных линиях категорий | |||||||
Высоко-скоростные | Скоростные | Особо-грузонапряженные | I | II | III | IV | ||
Тип рельсов | Р75-Р65 | Р75-Р65 | Р75-Р65 | Р75-Р65 | Р65 | СтарогодниеР75-Р65, новые Р65 | ||
Род шпал | ДеревянныеI типа или железобетонные | Дер. или жел. бет. | ||||||
Число шпал на 1 km пути, шт. | ||||||||
на прямых и кривых радиусом 1200 и более | ||||||||
радиусом менее 1200 m | ||||||||
При этом в действующих нормах (табл. 5) для скоростных и высокоскоростных участков не учтено, что шпалы BF70 имеют значительные преимущества перед стандартными шпалами Ш1−1, что, возможно, позволяет их применять с меньшей эпюрой шпал. Это надо подтвердить, как теоретическими расчетами, так и экспериментальными и эксплуатационными исследованиями. [7]
2. ВСН 448-Н «Инфраструктура высокоскоростной железнодорожной линии Ташкент — Самарканд. Общие технические требования» /8/.
Пункт 6.4.4:В пути должны быть уложены железобетонные шпалы с эпюрой 1840 штук на 1 km. [8]
Пункт 6.4.5: Железобетонные шпалы должны укладываться на слой щебня фракции от 25 до 60 mm марки не ниже И20 и У75 по ГОСТ 7392.
3. Ведомственные технические указания по проектированию
Железные дороги колеи 1520 мм[9]
Пункт 6.1: Мощность верхнего строения главных путей при проектировании новых железнодорожных линий и дополнительных главных путей надлежит устанавливать по нормам (таблица 6).
Таблица 6. Конструкция верхнего строения пути
Показатель | Мощность верхнего строения пути на железнодорожных линиях категорий | |||||||
Высоко-скоростные | Скоростные | Особо-грузонапряженные | I | II | III | IV | ||
Тип рельсов | Р75-Р65 | Р75-Р65 | Р75-Р65 | Р75-Р65 | Р65 | Старогодние Р75-Р65 Новые Р65 | ||
Род шпал | Деревянные I типа или железобетонные | Дер. или ж. бетонные | ||||||
Число шпал на 1 км пути, шт.: | ||||||||
на прямых и кривых радиусом 1200 м и более | ||||||||
на кривых радиусом менее 1200 м | ||||||||
4. N ЦРБ-393. Инструкция по техническому обслуживанию и эксплуатации сооружений, устройств, подвижного состава и организации движения на участках обращения скоростных пассажирских поездов [10].
Пункт 12, параграф 2:
На участках пути, где осуществляется скоростное движение пассажирских поездов, должны применяться железобетонные шпалы. Эпюра шпал 1840 штук на 1 км в прямых и кривых с радиусом более 1200 м и 2000 штук на 1 км в кривых меньших радиусов. Допускается до усиления пути сохранение эпюры шпал 1840 штук на 1 км во всех случаях.
Промежуточные рельсовые скрепления должны быть с упругими клеммами. Допускается до организации их серийного производства применение скреплений типа КБ с жесткими клеммами.
5. Специальные технические условия на проектирование железнодорожной линии Ташкент — Самарканд
Таблица 7. Параметры проектирования для скоростей 160 км/час и 250 км/час
№ п/п | Наименование показателей | Ед. изм. | Характеристики показателя | ||
V= 160 км/час | V= 250 км/час | ||||
величина | величина | ||||
1. | Расчетная рузонапряженность нетто в грузовом направлении | млн. ткм/км | свыше 12−20 | свыше 15 — 30 | |
2. | Категория линий | I | высокоскоростная | ||
3. | Максимальные скорости пассажирских поездов | км/час | |||
4. | Число шпал на км | шт. | 1840 / 2000 | ||
Таким образом, в действующих в Республике Узбекистан нормативных документах нет единого подхода к выбору конструкции и типа подрельсового основания на ГАЖК «Узбекистонтемирйуллари». Также не учитываются особенности и значительные преимущества шпал BF70, изготавливаемых по Евростандарту, относительно традиционных шпал Ш1−1 (ГОСТ 10 629−88), эксплуатируемых с жесткими скреплениями типа КБ.
В связи с отмеченным, приведенные в диссертационной работе разработки направлены на анализ, испытания и оптимизацию конструкции и системы использования железобетонных шпал типа BF70 с упругим (эластичным) промежуточным рельсовым скреплением типа «Pandrol Fastclip». [8]
Приведенные в диссертационной работе исследования включают в себя следующие цели:
1. Анализ конструкции железобетонных шпал BF70 и возможность их надежной и долгосрочной эксплуатации на скоростных и высокоскоростных линиях.
2. Оценка напряженного и деформированного состояния верхнего строения пути со шпалами типа BF70 и скреплениями «Pandrol Fastclip» на скоростных и высокоскоростных линиях ГАЖК «Узбекистон темир йуллари» при воздействии электропоездов с электровозом «Узбекистан» и электропоезда «Афрасиаб».
3. Выбор оптимальных параметров укладки и эксплуатации шпал BF70 со скреплениями «Pandrol Fastclip» на скоростных и высокоскоростных линиях ГАЖК «Узбекистон темир йуллари».
Приведенные в диссертационной работе исследования включают в себя следующие задачи:
1. Расчет прочностных параметров шпал BF70 (прочность, выносливость, трещиностойкость).
2. Экспериментальные испытания железобетонных шпал по прочностным показателям и параметрам трещиностойкости.
3. Сравнительный анализ шпал Ш1−1 и BF70.
4. Расчеты пути на прочность и устойчивость (с электровозом «Узбекистан» выполнены самостоятельно, а данные расчетов с электропоездом «Афрасиаб» взяты из статьи магистранта Аликперова С.).
Основное содержание диссертации изложено в следующих трудах:
1. ТашИИТ Научные труды республиканской научно-технической конференции с участием зарубежных ученых.
2.ТАДИ Cборник научных трудов конференции молодых ученых.
2. Анализ конструкции железобетонной шпалы BF70 и расчет ее прочностных параметров
Как видно из рис. 6 и 7 шпала BF70 при практически одинаковой длине и ширине имеет значительно большую высоту, чем шпала Ш1−1 и, соответственно, лучшую сопротивляемость вертикальным нагрузкам от подвижного состава. Для сравнительного анализа прочностных параметров этих шпал ниже выполнен расчет основных параметров железобетонных шпал BF70 и Ш1−1 [4,5], характеризующих их прочность, выносливость и трещиностойкость. Расчет включает в себя определение:
1. Предельных изгибающих моментов по условию:
— выносливости бетона в сжатых зонах шпалы;
— выносливости наиболее растянутой арматуры;
— трещиностойкости бетона в растянутых зонах шпалы;
2. Предельных поперечных сил по условию трещиностойкости на нейтральной оси приведенного сечения шпалы BF70.
Расчет выполнен по методике и рабочим чертежам шпалы BF70.
2.1 Геометрические характеристики сечений шпалы
При расчетах определены следующие основные характеристики поперечных сечений железобетонной шпалы типа BF70 (рис. 9,10), предназначенной для эксплуатации на ГАЖК «Узбекистонтемирйуллари»:
Площадь поперечного сечения напряженной арматуры, мм2,
Fн = У nifa,
где У ni — общее число стержней (под термином стержень здесь и ниже понимается также проволока, канат или другой любой одиночной элемент арматуры);
fa — площадь поперечного сечения одного стержня (ВрII диаметром 5 мм), мм2.
Общая площадь Fн и вес Рн высокопрочных проволокВр класса 1400 диаметром 5 мм в шпале BF70 составляют:
Для подрельсового сечения и сечения посередине шпалы:
Fн = 314,2 мм2;
Расстояние от низа поперечного сечения шпалы до центра тяжести преднапрягаемых проволок:
aн= ,
где ni — число стержней в данном горизонтальном ряду арматуры;
yi — расстояние данного горизонтального ряда арматуры от низа сечения, мм.
Для подрельсового сечения и сечения посередине шпалы:
aн= 90 мм.
Площадь поперечного сечения бетона шпалы F, мм2, определяется по наружным размерам шпалы за вычетом внутренних пустот, каналов и вкладышей из материалов с резко отличными от бетона свойствами из материалов с резко отличными от бетона свойствами (например, деревянные или пластмассовые дюбели, попадающие в сечение.
Подрельсовое сечение: F = 520×102 мм2;
Середина шпалы: F = 382×102 мм2;
Площадь приведенного поперечного сечения шпалы, мм2,
Fп = F + nFн,
Подрельсовое сечение: Fп = 520×102 + 6,15×314,2 = 53 932 мм2;
При n/ = 10 получено Fп = 520×102 + 10×314,2 = 55 142 мм2;
Середина шпалы: Fп= 382×102 + 6,15×314,2 = 40 132 мм2;
При n/ = 10 получено 382×102 + 10×314,2 = 41 342 мм2;
где. Величины Еа и Еб определяют в соответствии с модулями упругости соответственно арматуры и бетона.
n = 200 000/32 500 = 6,15
При расчете на выносливость вместо n принята величина n/ в зависимости от проектной марки бетона (n/ = 10).
Статический момент приведенной площади поперечного сечения шпалы относительно низа сечения определяют по формуле
Sп = S + nFн ан,
где S — статический момент площади поперечного сечения бетона шпалы относительно низа сечения, мм3; S = (2 а + b) х h2/6;
Рис. 8. Расположение арматуры в среднем сечении шпалы типа BF70
Рис. 9. Расположение арматуры в подрельсовом сечении шпалы типа BF70
Подрельсовое сечение: S = (2×185 + 277) х 2252/6 = 5459×103 мм3;
Sп = 5459×103 + 6,15×314,2×90 = 5633×103 мм3;
При n/ = 10 получено: Sп = 5459×103 + 10×314,2×90 = 5742×103 мм3;
Среднее сечение шпалы:
S= (2×178 + 235) х 1852/6 = 3371×103 мм3;
Sп = 3371×103 + 314,2×6,15×90 = 3545×103 мм3;
При n/ = 10 получено: Sп = 3371×103 + 314,2×10×90 = 3654×103 мм3;
Расстояние от низа поперечного сечения шпалы до центра тяжести площади приведенного поперечного сечения шпалы, мм, определяют по формуле
.
Подрельсовое сечение: уп = 5633×103 / 53 932 = 104 мм;
при n/ = 10 получено: уп = 5742×103 /55 142 = 104 мм, Среднее сечение шпалы: уп = (3545×103) / (40 132) = 88 мм;
при n/ = 10 получено: уп = 3654×103 /41 342 = 88 мм.
Эксцентриситет усилия предварительного обжатия относительно центра тяжести приведенного поперечного сечения шпалы, мм, еон= yп — ан.
Подрельсовое сечение: еон = 90 — 88= 2 мм;
при n/ = 10 получено: еон = 90 — 88= 2 мм;
Среднее сечение: еон = 104 — 90 = 14 мм;
при n/ = 10 получено: еон =104 — 90 = 14 мм.
Момент инерции приведенного поперечного сечения шпалы относительно горизонтальной оси, проходящей через центр тяжести приведенного сечения, мм4,
Iп = I + n У nifa(yп — yi)2,
где I — момент инерции площади поперечного сечения бетона шпалы относительно центра тяжести поперечного сечения. Разница в положении центра тяжести поперечного сечения бетона шпалы и центра тяжести приведенного поперечного сечения шпалы не учитывается.
Рис. 10. Эксцентриситет усилия и эпюра напряжений предварительного обжатия в средней части шпалы типа BF70
Рис. 11. Эксцентриситет усилия и эпюра напряжений предварительного обжатия в подрельсовом сечении шпалы типа BF70
I = h3х (а2 + 4 х a х b + b2) / 36 х (a + b);
Подрельсовое сечение:
I = 2253 х (1852 + 4×185×277 + 2772) / 36х (185 + 277) = 21 638×104 мм4;
IП = 22 050×104мм4;
При n/ = 10 получено: Iп = 22 308×104 мм4;
Среднее сечение шпалы:
I = 1853 х (1782 + 4×178×235 + 2352) / 36х (178 + 235) = 10 826×104 мм4;
IП = 11 201×104мм4;
При n/ = 10 получено: Iп/ = 11 436×104 мм4.
2.2 Напряжения в бетоне и арматуре
В расчете принято, что предварительно напряженные шпалы в эксплуатации работают только в стадии упругих деформаций. Поэтому напряжения в шпале рассчитывают по известным правилам расчета упругих материалов.
При первоначальном натяжении арматуры на упоры в ней создается предварительное напряжение уо, МПа. При механическом способе натяжения арматуры оно должно быть в пределах:
для проволочной арматуры 0,76 RaII? уо? 0,21 RaII;
для стержневой арматуры 0,95 RaII? уо? 0,32 RaII.
Принято для принятой проволочной арматуры типа ВрIIуо= 1170 Мпа, т. е. 1170/1670 = 0,70 0,76 (условие выполняется) Общее начальное усилие предварительного натяжения арматуры, Н:
No= Fн уо = 314,2×1170 = 367 614 Н = 367, 6 кН.
Начальное предварительное напряжение фактически существует только в самый первый момент после натяжения арматуры, так как сразу же возникают потери этого напряжения в МПа от ряда факторов.
Потери от релаксации напряжений арматуры, которые при механическом способе ее натяжения определяют по формулам:
— для проволочной арматуры:
;
n1 = (0,27×1170/1670 — 0,1) х 1170 = 104 Мпа,
— для стержневой арматуры: уп1 = 0,1 уп о — 20.
Потери от температурного перепада (от разности температур Дt натянутой арматуры и упоров, воспринимающих усилие натяжения) при пропаривании или прогреве бетона уп2= 1,2 Дt. Потери от температурного перепада следует учитывать при стендовом способе производства железобетонных шпал. В этом случае арматура, находящаяся в свежеуложенном бетоне, при его пропаривании тоже нагревается и удлиняется, напряжения в ней падают, а положение упоров стенда, не подвергающихся нагреву, остается неизменным. В результате этого схватывание арматуры с бетоном происходит при пониженном ее напряжении. При технологии, прелагаемой производства шпал SICI металлическая форма, воспринимающая натяжение арматуры, нагревается в камере вместе с бетоном, имеет ту же температуру, что и арматура, и поэтому потери напряжения уп2 в этом случае отсутствуют. При Дt = 400C получено:
уп2=1,2×40 = 48 МПа;
Потери от деформации анкеров или смещения стержней в инвентарных зажимах уп3= Еа,
где л = 1,25 + 0,15d;
d — диаметр стержня, мм;
l — длина натягиваемого стержня (расстояние между наружными гранями формы или упоров стенда), мм.
уп3 = (1,25 + 0,15×5) х 200 000 / 110 000 = 3,6 МПа;
Потери от трения арматуры, о поверхность бетона или огибающие приспособления. Потери уп 4 от этих факторов следует учитывать при последующем натяжении арматуры на затвердевший бетон. При существующей технологии эти потери отсутствуют.
Потери от деформации стальной формы при натяжении на нее арматуры. Величину потерь напряжения уп 5 от этого фактора при отсутствии точных данных о конструкции формы принимают равной 30 МПа (300 кгс/см2). При существующей технологии эти потери отсутствуют. [1]
В результате потерь начальное предварительное напряжение арматуры к моменту передачи напряжения на бетон снижается до величины уап= уо — (уп1+ уп2 + уп3 +уп4 + уп5),
уап= 1170 — (104 +48+ 3,6) = 1014 МПа;
а общая сила предварительного натяжения арматуры — до величины
Nон = Fн уан.
Nон = 314,2×1014 = 318 724 кг? 319 тн При передаче этой силы на бетон в нем тоже возникают предварительные напряжения, величина которых на уровне центра тяжести напряжений арматуры составляет убн= .
убн= 318 724/55 142 + 299 872×142/22 050×104 = 5,6 МПа Сразу же от этих напряжений в бетоне возникнут явления быстропротекающей ползучести. Потери предварительного напряжения арматуры вследствие этой ползучести бетона к моменту окончания процесса его обжатия составят уп6= 42,5
уп6= 42,5×5,6/40 = 6 МПа при условии, что? 0,6, (5,6/38 = 0,15 0,6)
Таким образом, общие потери предварительного напряжения арматуры к моменту окончания процесса обжатия бетона, называемые «первыми», будут уп1= уп1 + уп2 + уп3 + уп4 +уп5 + уп6.
у01 = 1170 — (104 +48+ 3,6) — 6 = 1008,4 Мпа Натяжение арматуры на уровне ее центра тяжести после окончания процесса обжатия бетона будет равно N01 = Fн (у0 — уп1) = Fн у01.
N01 = 314,2×1008,4 = 316,84 кН.
В дальнейшем процесс усадки и ползучести бетона продолжается, а следовательно, растут и потери предварительного напряжения арматуры от этих факторов, называемые «вторыми» потерями. Потери уп8 от усадки тяжелого бетона, подвергавшегося тепловой обработке при атмосферном давлении, в зависимости от проектной марки бетона будут равны 40 МПа.
Потери уп9от ползучести тяжелого бетона при указанной выше тепловой обработке определяют по формуле уп9 = 170 .
уп9 = 170×5,6/40 = 24 МПа В этом случае тоже должно выполняться условие? 0,6, т. е. (5,6/40 = 0,14)
После всех потерь напряжения в арматуре на уровне ее центра тяжести будут у02 = у01 — (уп 8 + уп 9),
у02 = 1008,4 — 40 — 24 = 944,4 МПа, а общая сила предварительного обжатия бетона
N02 = Fн у02.
N02 = 314,2×944,4 = 296 730 МПа
Установившиеся предварительные напряжения в бетоне:
уб2= ,
Подрельсовое сечение: уб2 = 296 730/(55 142) + 296 730×14/ (22 308×104) х у = 5,4 + 0,019 х у;
Для верха сечения: уб2 = 5,4 — 0, 019×121 = 3,1 Мпа Для низа сечения: уб2 = 5,4 + 0,019×104 = 7,4 Мпа.
Среднее сечение шпалы: уб2= 296 730/41342 + 296 730×2,0 / 11 436×104 х у = 7,2 + 0,005 х у.
Для верха сечения: уб2 =7,2 + 0,005×97 = 7,7 Мпа;
Для низа сечения: уб2 = 7,2 — 0,005×88 = 6,7 МПа где y — расстояние от центра тяжести приведенного поперечного сечения шпалы до рассматриваемого слоя бетона.
Установившиеся предварительные напряжения в арматуре, находящейся в этом слое бетона уа2= у02 — n уб2.
Подрельсовое сечение: уа2= 944,4 — 10×7,4= 870,4 МПа;
Среднее сечение: верх сечения уа2= 944,4 — 10×7,7= 867 МПа;
низ сечения: уа2 = 944,4 — 10×6,7= 877 МПа;
2.3 Расчет железобетонных шпал BF70 на выносливость
Выносливость железобетонных шпал определяют исходя из следующих условий:
- для сжатого бетона убmax? mб2Rпр;
- для растянутой арматурыуаmax? mа1 Ra,
где убmaxиуаmax — максимальные напряжения от эксплуатационной нагрузки соответственно в сжатом бетоне и в растянутой арматуре.
При определении этих напряжений геометрические характеристики приведенного сечения шпалы принимают с коэффициентом n/.
Если в указанных выше условиях принять убmax= mб2 Rпри уаmax= mа1 Ra, то можно получить предельные значения изгибающих моментов Мсж и Ма по выносливости шпалы в данном сечении.
Для сжатой зоны сечения ууmax= yсж,
где yсж — расстояние от центра тяжести приведенного поперечного сечения шпалы до наиболее удаленного слоя бетона сжатой зоны (см. рис. 11,12).
В рассматриваемом слое бетона уже имеется установившееся предварительное напряжение уб2, а наибольшее напряжение, которое может быть допущено в этом слое, согласно условию равно mб2Rпр. Следовательно, допустимая амплитуда изменения напряжения в данном слое бетона — от уб2 до mб2Rпр. Таким образом, предельное значение Мсж =).
Подрельсовое сечение: уб2= 3,0 МПа; Rпр = 24,5 МПа;
Мсж = 22 308×104 / 121 х (0,79×24,5 — 3,0) = 3021×104Нмм = 30 кНм;
Среднее сечение шпалы: уб2= 6,7 МПа; Rпр = 24,5 МПа;
Мсж = 11 436×104 /88 х (0,85×24,5 — 6,7) = 18 356 179 Нмм =18,4 кНм Величина с в этом случае составляет ,
В рассматриваемом случае она равна соответственно сб= 0,18 и 0,3.
Поскольку в приведенном неизвестны и сб, и mу2, то величину mу2 определяют подбором и интерполяцией до тех пор, пока значение сб, соответствующее по этой таблице величине mу2, не совпадает со значением сб. Для растянутой арматуры
уаmax= n/ ,
где ya — расстояние от центра тяжести приведенного поперечного сечения шпалы до наиболее удаленного ряда или стержня арматуры (см. рис 11,12).
В рассматриваемом стержне уже имеется установившееся предварительное напряжение уа2, а наибольшее напряжение, которое может быть допущено в этом стержне, согласно условию равно ma1Ra. Следовательно, допустимая амплитуда изменения напряжения в данном стержне — от уа2до ma1Ra. Таким образом, предельное значение Ма =).
Подрельсовое сечение: Ма = 1/10×22 308×104/69 х (0,91×1110 — 870) = 45,0 кНм;
са= 87/(0,91×1110) = 0,86
Среднее сечение шпалы: Ма = 1/10×11 436×104 /72х (0,91×1110 — 867) = 22,7 кНм;
са=867/0,91/1100 = 0,86
Величинаса в этом случае составляет са = .
Как и в предыдущем случае, величину ma1 определяют подбором и интерполяцией.
2.4 Расчет железобетонных шпал на трещиностойкость
Железобетонные шпалы относятся к конструкциям 1-й категории трещиностойкости, в которых не допускается образование трещин при расчетных нагрузках. По этому шпалы рассчитывают из условия убmax? mб2 RpII,
где убmax — максимальное напряжение от расчетной эксплуатационной нагрузки в растянутой зоне бетона;
mб2 = 0,75, так как в этом случае всегда сб< 0,1.
Если принять убmax= 0,75 RpII, то предельное значение изгибающего момента Мтр по условию стойкости бетона против образования трещин, нормальных к продольной оси шпалы, при многократно повторяющейся нагрузке определяется выражением Мтр= ,
где yp — расстояние от центра тяжести приведенного поперечного сечения шпалы до наиболее удаленного растянутого слоя бетона. Геометрические характеристики приведенного сечения в этом случае также определяют с коэффициентом n/;
— установившееся предварительное напряжением в рассматриваемом слое бетона.
Для подрельсового сечения:
Низ сечения: Мтр = 22 308×104/104 х (7,4 + 0,75×2,2) = 19,4 кНм;
Верх сечения: Мтр = 22 308×104/121 х (3,1 + 0,75×2,2) = 8,8 кНм.
Для среднего сечения шпалы:
Верх сечения: Мтр = 11 436×104 / 97 х [7,7 + 0,75×2,2] = 11,0 кНм;
Низ сечения: Мтр = 11 436×104 / 88 х [6,7 + 0,75×2,2] = 10,8 кНм.
2.5 Расчет предельных поперечных сил по условию трещиностойкости бетона против образования трещин, наклонных к продольной оси шпалы
Предельную поперечную силу Qтр, которая может быть допущена по условию трещиностойкости бетона против образования трещин, наклонных к продольной оси шпалы, при многократно повторяющейся нагрузке, определяют из условия уг. р.? mу2RpII,
где уг. р. — главные растягивающие напряжения на нейтральной оси приведенного сечения шпалы, определяемые по формуле уг. р. = - ,
— установившиеся предварительные сжимающие напряжения в бетоне на нейтральной оси приведенного сечения, МПа;
— касательные напряжения в бетоне на нейтральной оси приведенного сечения, МПа;
Sпн — статический момент части приведенного сечения, расположенной выше нейтральной оси этого сечения, относительно нейтральной оси, мм3;
bн — ширина сечения шпалы на уровне нейтральной оси, мм.
Все геометрические характеристики приведенного поперечного сечения шпалы определяют с коэффициентом n/.
После подстановки указанных величин получена формула для определения предельного значения поперечной силы:
Qтр= .
Подрельсовое сечение: bн = 185 + (277 — 185) х (225 — 104)/225 = 208 мм;
S = (2×185 + 208) х 1212/6 = 1410×103 мм3;
При n/ = 10 получено: Sпн= = 1452×103 мм3;
Qтр =22 308×104 х 208/1452×103хV (0,75×2,2)2 + 0,75×2,2×5,4= 108 971 Н = 10,9 тн Среднее сечение шпалы: bн = 185 + (277 — 185) х (225 — 104)/225 = 208 мм;
S= (2×178 + 208) х 972/6 = 884×103 мм3;
Sп = 884×103 + 10×19,63×4 [0.5х (100−88)+ (130−88)+0,5 (160−88)] = 950×103 мм3;
Qтр =11 436×104х208/950×103 х V (0,75×2,2)2+0,75×2,2×7,2= 95,6 Н = 9,56 тн Полученные расчетами величины предельных изгибающих моментов и поперечных сил приведены ниже в табл. 6.
Таблица 6 — Сравнительные параметры по выносливости, трещиностойкости и предельным поперечным силам шпал Ш1 и BF70
№№ | Наименование показателя | ШПАЛА Ш1* | ШПАЛА BF70 | |||
Посередине подрельсовой площадки | По середине шпалы | Посередине подрельсовой площадки | По середине шпалы | |||
Предельный изгибающий момент, кН х м по условию: | ||||||
— выносливости бетона в сжатой зоне | 16,6 | - 9,0 | 30,2 | - 18,4 | ||
— выносливости наиболее растянутой арматуры | 43,9 | -18,8 | 45,0 | - 22,7 | ||
— трещиностойости бетона в растянутой зоне | 13,5 | -9,2 | 19,4 | -11,0 | ||
Предельная поперечная сила, кН (тс) по условию трещиностойкости на нейтральнойоси | 94,0 | 60,0 | ||||
* Данные соответствуют результатам расчетов, приведенных в книге Золотарского А. Ф., Евдокимова Б. А., Исаева Н. М. и др «Железобетонные шпалы для рельсового пути», М., Транспорт, 1980 г.
Вывод по результатам расчетов Установлены следующие преимущества шпал BF70 относительно шпал типа Ш1 (ГОСТ 10 629−88):
1. По критерию выносливости бетона в сжатых зонах показатели шпалы BF70 превышают аналогичные показатели шпалы Ш1:
— в подрельсовом сечении — на 82%;
— в средней части шпалы — на 104%.
2. По критерию выносливости наиболее растянутой арматуры показатели шпалы BF70 превышают аналогичные показатели шпалы Ш1:
— в подрельсовом сечении — на 3%;
— в средней части шпалы — на 21%.
3. По критерию трещиностойкости бетона в растянутых зонах показатели шпалы BF70 превышают аналогичные показатели шпалы Ш1:
— в подрельсовом сечении — на 44%;
— в средней части шпалы — на 20%.
4. Предельная поперечная сила, кН (тс) по условию трещиностойкости на нейтральной оси приведенного сечения шпалы BF70 превышают аналогичные показатели шпалы Ш1: — в подрельсовом сечении — на 16%;
— в средней части шпалы — на 60%.
В целом, по критериям выносливости и трещиностойкости шпалы BF70 существенно превышают аналогичные показатели шпалы Ш1, что определяет их более высокую надежность, а также возможность укладки и эксплуатации на скоростных и высокоскоростных линиях и на участках с повышенными осевыми нагрузками.
Выполненные расчеты подтверждаются испытаниями шпал на прочность и трещиностойкость (раздел 2.6).
2.6 Испытания шпал BF70 на трещиностойкость и прочность
Важнейшим параметром, определяющим возможность применения шпал BF70 на высокоскоростных участках является их сопротивляемость к возникновению трещин. В связи с этим для оценки трещиностойкости железобетонных шпал типа BF70 были выполнены их испытания в средней части и подрельсовом сечении (рис. 13). Методика исследований соответствовала требованиям стандартовО’zDSt EN 13 230 — 1,2:2003. При этом нагружение шпал выполнялось до первой трещины (табл. 13).
Таблица 7/ Результаты испытаний шпал на трещиностойкость
Параметры | Номера шпал | |||||||
Fcon, кН | Норма | |||||||
Факт | 52,3 | 54,4 | 53,8 | ; | ; | ; | ||
Frr, кН | Норма | |||||||
Факт | ; | ; | ; | |||||
Примечание. Frr — испытательная нагрузка при которой появляется первая трещина в подрельсовом сечении;
Fсrn — испытательная нагрузка при которой появляется первая трещина в среднем сечении шпалы.
Рис. 12. Испытания железобетонных шпал BF70 на заводе-производителе
Выводы по результатам испытаний:
1. В результате испытаний выявлен значительный запас прочности шпал BF70 по критерию трещиностойкости, что позволяет укладывать эти шпалы на участках с повышенным динамическим воздействием.
2. Коэффициент запаса по трещиностойкости в средней части шпалы составляет Кс = 1,94 — 1,97, в подрельсовом сечении — Кr = 2,2 — 2,5.
3. Результаты контроля качества работы шпал BF70, выполняемые как в аккредитованном испытательном подразделении ДП «RWS Optimum», так и непосредственно на эксплуатируемых участках, подтверждают высокую надежность, экономичность и перспективность их применения на магистральных линиях, включая скоростные и высокоскоростные участки (200−250 км/ч).
4. Испытания бетона шпал на прочность выполнялись на кубах бетона, подвергнутых тепловлажностной обработке на технологических линиях завода-производителя железобетонных шпал — ДП «RWS Optimum». Были испытаны 4 пары кубов бетона в возрасте 28 суток (рис. 13). В результате испытаний установлено, что прочность бетона шпал значительно превышает требуемые значения (53 МПа) и составляет в среднем 72,7 МПа. Коэффициент запаса составляет 1,37.
5. Испытания шпал на прочность и трещиностойкость подтвердили высокие показания по указанным критериям и возможность их применения на скоростных и высокоскоростных линиях ГАЖК «Узбекистонтемирйуллари».
6. Расчетами бесстыкового пути на прочность и устойчивость также следует подтвердить возможность уменьшения эпюры укладки шпал BF70 на участках скоростного и высокоскоростного движения электропоездов «Афрасиаб» и «Узбекистан». Эти расчеты выполнены ниже в разделе 3.
Рис. 12. Схема испытания шпал на трещиностойкость а) подрельсовое сечение б) среднее сечение
1 — жёсткая опора; 2 — шарнирная опора; 3 — упругая прокладка;
4 — шпала BF 70; 5 — прокладка под рельс; 6 — клин; 7 — анкер.
Fr — испытательная нагрузка на подрельсовое сечение шпалы
Fсn — испытательная нагрузка в среднем сечении шпалы;
Lr = 60 мм расчётное расстояние между опорами при испытаниях подрельсовыхподрельсовых площадок.
Lс = 1600 мм расчётное расстояние между опорами при испытаниях средней части шпал.
3. Расчет пути со шпалами BF70 и скреплениями «Pandrolfastclip» на прочность и устойчивость при воздействии поезда «Узбекистан»
3.1 Общие положения
Расчет выполнен с целью определения оптимальных параметров укладки и эксплуатации бесстыкового пути со шпалами типа BF70 и рельсовым скреплением типа «Pandrol Fastclip» на ГАЖК «Узбекистон темир йуллари», включая скоростные и высокоскоростные линии. В данном разделе устанавливаются оптимальные эпюры укладки шпал BF70 на участках скоростного и высокоскоростного движения поездов.
Расчеты пути на прочность выполняются для летних и зимних условий эксплуатации при радиусах 500, 600, 700, 800, 100, 1200, 2000 и в прямой для скоростей движения скоростного электропоезда «Узбекистан» — 120, 140 и 160 км/ч.
Результаты выполненных расчетов на скоростном участке от воздействия электропоезда «Узбекистан» сравнены с аналогичными расчетами для электропоезда «Афрасиаб» на высокоскоростных участках со скоростями движения 160, 200 и 250 км/ч (расчеты магистранта Аликперова С).
3.2 Расчетные усилия, передаваемые на рельс
Расчетная величина силы взаимодействия колеса и рельса в сечении под колесом определяется с вероятностью непревышения ее Ф = 0,99 379 и составляет: [15]
РРАСЧ = РСР + 2,5 S (1)
С учетом вероятностного сочетания составляющих общего давления колеса на рельс, реализуемых при движении современных единиц подвижного состава, имеем:
для силы среднего давления колеса на рельс
РСР = РСТ + (2)
и для среднеквадратического отклонения совокупности действующих на рельс сил
(3)
Из формул (1 — 3) видно, что величина расчетного давления колеса на рельс определяется с учетом: статического давления от подвижного состава, отнесенного к одному колесу, (РСТ); дополнительного динамического давления, вызванного колебаниями кузова на рессорах, (); дополнительных динамических давлений, вызванных наличием изолированной неровности на пути, (SНП), неровностей на колесе — изолированной (SИНК) и непрерывной (SННК) с учетом доли колес, обращающихся на участке, с изолированными неровностями, (q1).
Отдельные составляющие расчетного давления колеса на рельс учитываются следующим образом:
статическое давление колеса на рельс (РСТ) принимается в расчете по паспортным данным подвижного состава;
сила дополнительного давления от колебания кузова на рессорах учитывается средним давлением и среднеквадратическим отклонением:
(4)
сила дополнительного давления, вызванного наличием изолированной неровности на пути, учитывается среднеквадратическим отклонением:
(5)
сила дополнительного давления, вызванного наличием изолированной неровности на колесе, учитывается среднеквадратическим отклонением;
(6)
сила дополнительного давления, вызванного наличием непрерывной, неровности на колесе, учитывается среднеквадратическим отклонением:
(7)
В формулах (4 — 7) введены следующие расчетные величины:
0 — коэффициент, учитывающий влияние приведенной массы пути не дополнительные давления, вызванные наличием неровностей на колесе (табл. 8);
1 — коэффициент, учитывающий влияние приведенной массы пути на дополнительное давление, вызванное наличием изолированной неровности на пути (табл. 8);
— коэффициент, учитывающий влияние жесткости подрельсового основания на крутизну дополнительной динамической неровности на пути (табл. 8);
— коэффициент, учитывающий род балластного слоя (табл. 8);
l — среднее расстояние между осями шпал (табл. 9);
U — модуль упругости подрельсовго основания;
v — скорость движения экипажа;
qK — вес необрессоренных частей экипажа, отнесенный к одному колесу;
Таблица 8/ Расчетные коэффициенты, учитывающие состояние подрельсового основания
Обозначение расчетного коэффициента | Величина расчетного коэффициента для пути на балласте | ||||||
Песчаном | Гравий-ном | асбестовом при шпалах | щебеночном при шпалах | ||||
Железо-бетонных | Дере-вянных | Железо-бетонных | Дере-вянных | ||||
0,433 | 0,433 | 0,402 | 0,433 | 0,402 | 0,433 | ||
1,0 | 1,0 | 0,931 | 1,0 | 0,931 | 1,0 | ||
1,0 | 1,0 | 0,322 | 1,0 | 0,322 | 1,0 | ||
1,5 | 1,1 | 1,5 | 1,5 | 1,0 | 1,0 | ||
Таблица 9/ Величина среднего расстояния между осями шпал
Обозначение расчетной величины | Среднее расстояние между осями шпал в см при фактической эпюре шпал на участке, шт./км | ||||
l | |||||
d — диаметр среднего круга катания колеса;
е0 — величина наибольшей расчетной глубины изолированной неровности (табл. 2.4.);
Таблица 10 — Наибольшая расчетная глубина изолированной неровности
Обозначение расчетной величины | Расчетная глубина изолированной неровности в см для колес | ||||
локомотивных или моторвагонного состава при подшипниках | вагонных при подшипниках | ||||
скольжения | качения | скольжения | качения | ||
е0 | 0,067 | 0,047 | 0,133 | 0,067 | |
— коэффициент, учитывающий влияние мощности рельса на образование неровности на пути:
;
J — момент инерции рельса с учетом величины износа;
К — коэффициент относительной жесткости рельса и основания:
;
Е — модуль упругости материала рельсовой стали, Е=2,1106 кг/см2;
— максимальный дополнительный прогиб рельса при проходке колесом косинусоидальной неровности, отнесенный к единице глубины неровности; принимается = 1,47, если соблюдается неравенство:
vvКР,
где
g — ускорение свободного падения, g = 981 см/с2.
При расчетах бесстыкового пути, а также для единиц подвижного состава, не прошедших экспериментальную проверку,
где fСТ — статический прогиб рессорного комплекта.
3.3 Расчетные напряжения и деформации в элементах верхнего строения пути
Величина напряжений в элементах верхнего строения пути и прогиб рельса определяются с учетом воздействия на расчетное сечение системы (сосредоточенных нагрузок, в зону воздействия которых входит рассматриваемое расчетное сечение. Для верхнего строения пути современных типов влияние от отдельных сосредоточенных нагрузок (давлений осей подвижного состава) практически ощущается при расстоянии от оси до расчетного сечения не более 350 см. Притом следует выбирать наиболее неблагоприятные сочетания системы сосредоточенных нагрузок от осей подвижного состава, а именно; в расчетном сечении устанавливается ось подвижного состава, оказывающая максимально-вероятностное давление на рельс (РРАСЧ); воздействие от соседних осей учитывается коэффициентами линий влияния при величине давления этих осей на рельс, равной РСР. Коэффициенты линий влияния принимаются с учетом относительной жесткости рельса и основания (К) и расстояния от расчетного сечения до учитываемой нагрузки от соседней оси (Х=Li) в соответствии с расчетными формулами: для изгибающих моментов
=е-КХ(cos KX — sin KX),
для прогибов, перерезыващих сил и давления рельса на шпалу
=е-КХ(cos KX + sin KX).
Наиболее неблагоприятное сочетание нагрузок следует принимать следующим образом:
— для экипажей с двухосной жесткой базой — одна из осей принимается за расчетную и учитывается влияние второй оси; для экипажей с трехосной жесткой базой предварительно определяется знак коэффициента линии влияния ближайших осей тележки: при положительном значении коэффициента линии влияния за расчетную ось принимается средняя ось тележки и учитывается влияние крайних осей, при отрицательном значении коэффициента линии влияния за расчетную ось принимается крайняя ось тележки и учитывается влияние средней оси.
Считая схему работы рельса под действием расчетной системы грузов статической, получаем:
величину изгибающего момента в расчетном сечении рельса
(8)
величину давления рельса на шпалу в расчетном сечении
(9)
величину прогиба рельса в расчетном сечении
(10)
По величине изгибающего момента и давления рельса на шпалу определяется напряжения в элементах верхнего строения пути:
в рельсах:
по оси подошвы
(11)
кромочные по подшве
(12)
кромочные в головке
(13)
по верхней постели шпалы под подкладкой
(14)
в балластном слое по нижней части шпалы
. (15)
В приведенных выше формулах приняты следующие обозначения:
W — момент сопротивления рельса;
f — коэффициент учета горизонтального изгиба и кручения рельса;
mГ-К — коэффициент перехода от осевых напряжений в подошве рельса к кромочным напряжениям в подошве рельса:
ZГ, ZП — расстояние от горизонтальной оси рельса, проходящей через центр тяжести рельса, до крайних волокон соответственно головки и подошвы рельса;
bП, bГ — ширина соответственно подошвы и головки рельса в расчетном уровне;
— площадь подрельсовой подкладки;
— опорная площадь полушпалы с учетом изгиба.
3.4 Допускаемые напряжения
В соответствии с критерии прочности пути определены из условия обеспечения его надежности по следующим критериям:
* [ук] - из условия непревышения допускаемого количества отказов рельсов за период нормативной наработки;
* [уш] - из условия непрснышеиия допускаемого износа шпал и прокладок под подкладками за период нормативной наработки;
* [уб] и [уз] - из условия непревышения допускаемой интенсивности накопления остаточных деформации соответственно в балласте и па основной площадке земляного полотна.
Численные значения оценочных критериев приведены в табл. 11.
Таблица 11/ Оценочные критерии прочности
Критерии | Вид подвижного состава | Значения оценочных критериев прочности, кг/см2, при грузонапряженности, млн. ткм брутто на км в год* | ||||
>50 | 50−25 | 24−10 | <10 | |||
[ук] | Локомотив «Узбекистон» | |||||
Вагоны | ||||||
[уш] | Локомотив «Узбекистон» | |||||
Вагоны | ||||||
[уб] | Локомотив «Узбекистон» | 4.0 | 4.2 | 4.5 | 5.0 | |
Вагоны | 2.6 | 3.0 | 3.5 | 4.0 | ||
[уз] | Локомотив «Узбекистон» | 1.0 | 1.0 | 1.1 | 1.2 | |
Вагоны | 0.8 | 0.8 | 0.9 | 1.0 | ||
Примечание. *Для новостроек па 10-й год эксплуатации.
Данные таблицы применимы: [ук] — для типовых нетермообработанных рельсов в прямых и кривых радиусом более 1000 м. Для термоупрочненных рельсов значения [ук] увеличиваются на 14%, В кривых с R?1000 м [ук] —2400 кг/см2, так как нормативными документами предусмотрена сплошная смена рельсов между капитальными ремонтами пути в кривых с R=1000ч651 м — один paз, R=650ч351 м — два раза; R?350 м — три раза; [уш] — для сосновых стандартных шпал; [ук]=40 кг/см2 допускаемое напряжение в прокладке (при железобетонных шпалах); [уб] — для щебеночного и асбестового балласта. Для песчаного балласта приведенные значения [уб] необходимо уменьшить в 1,6 раза, при карьерном гравии и ракушкe в 1,4 раза; [уз] для земляного полотна из суглинистых грунтов.
3.5 Напряженное состояние основной площадки земляного полотна
Расчет напряжений на основной площадке земляного полотна, как правило, принято вести на основе вероятностного совокупного воздействия всех осей расчетного поезда. Учитывая, что по пути проследуют поезда с различным сочетанием нагрузки на ось (порожние и груженые), имеющие в составе вагоны различных типов (четырех-, шестии восьми-осные), выбор состава расчетного поезда является затруднительным. Поэтому целесообразно определять напряжение на основной площадке земляного полотна от воздействия типовой единицы подвижного состава, преобладающей в поезде. Для средних условий за такую единицу подвижного состава можно принимать четырехосный грузовой вагон. При преобладающем движении по участку шестиили восьми-осных полувагонов за расчетную единицу подвижного состава принимать шестиили восьмиосный полувагон для определения воздействий на основную площадку земляного полотна.
Метод расчета напряжений на основной площадке земляного полотна заключается в суммировании напряжений, передаваемых в расчетную точку от трех соседних шпал, средняя из которых расположена в сечении над расчетной точкой.
где — напряжение на основной площадке земляного полотна, вызванное давлением основной расчетной шпалы в расчетном сечении:
б — напряжение в балласте по нижней постели расчетной шпалы;
r1 — поправочный коэффициент, учитывающий род шпал: для железобетонных — r1 = 0,7, для деревянных — r1 = 0,8;
m — коэффициент, учитывающий характер распределения напряжений в балластном слое по нижней поверхности шпалы в поперечном направлении:
Принимаемая в расчетах величина m должна соответствовать условию: 1 m 2;
С1, С2 — параметры, учитывающие характер распределения напряжений в балластном слое под шпалой:
,
b — средняя ширина нижней постели шпалы,
h — толщина балласта под шпалой Величины параметров С1 и С2 можно принимать для типовых конструкций верхнего строения пути;
— напряжение в расчетной точке основной площадки земляного полотна, передаваемое от соседних шпал:
А — параметр, определяющий характер передачи давлений в балластном слое от соседних шпал на расчетную точку:
А=1-2+0,5 (sin 21 — sin 22),
— соответственно напряжения в балластном слое под первой и второй соседними шпалами от поездной нагрузки:
; ;
— давления от расчетной нагрузки и соседних осей подвижного состава соответственно на первую и вторую соседние шпалы:
;
Полученное в процессе расчета напряжение h сравнивается с допускаемым напряжением для грунта основной площадки земляного полотна (табл. 11).
3.6 Выводы по результатам расчетов на прочность
Самостоятельные расчеты были выполнены для пассажирского электровоза «Узбекистан» для скоростей движения 100 — 120 — 160 км/ч (приложение 1).
Расчеты для электропоезда «Афрасиаб» расчеты были взяты из диссертации АликпероваС.
При этом были приняты следующие начальные условия, соответствующие эксплуатационным параметрам ГАЖК «Узбекистонтемирйуллари»:
1. Локомотив: Узбекистан
2. Район: Ташкентский вилоят
3. Рельсы: P65, шпалы BF70 с эпюрой1680/1720/1840/2000 шт./км
4. Температура рельса: минимальная: -30
максимальная: 64
годовая амплитуда: 94
5. Модуль упругости подрельсового основания, кг/см2 (I вариант):
в прямой: — летом: 2000
— зимой: 3000
в кривой: — летом: 2200
— зимой: 3300
6. Модуль упругости подрельсового основания, кг/см2 (II вариант):
в прямой: — летом: 3000
— зимой: 4500
в кривой: — летом: 3400
— зимой: 5100
7. Балласт щебеночный на песчаной подушке толщиной, см
Iвариант — 35/20 см
IIвариант — 20/20 см
8. Путь и подвижной состав находятся в исправном состоянии, отвечающем требованиям ПТЭ; колеса подвижного состава при движении не отрываются от поверхности катания рельсов (рассматривается безударное движение).
3.7 Расчеты бесстыкового пути
Практические расчеты бесстыкового пути выполняются с целью определения условий укладки и закрепления плетей бесстыкового пути и установления режимов эксплуатации. Для этого на основе рассмотрения условий прочности и устойчивости плетей бесстыкового пути определяются возможные запасы изменения температуры плети по сравнению с температурой закрепления ее для работы в выбранном режиме эксплуатации[15].
Допускаемые интервалы изменения температуры плети бесстыкового пути по условиям прочности рельса
Для бесстыкового пути из-за наличия погонных и стыковых сопротивлений температурному изменению длины плети характерно развитие значительных продольных сил, вызывающих осевое напряженное состояние рельса даже при отсутствии поездной нагрузки. Поэтому общее условие прочности для рельсов бесстыкового пути, принятое до настоящего времени в практических расчетах, имеет вид:
KПК+t[]
где КП — коэффициент запаса прочности, КП= 1,3;
К — кромочные напряжения в наиболее загруженных волокнах рельса, реализуемые при воздействии поездной нагрузки. Устанавливаются предварительным расчетом элементов верхнего строения пути на прочность;
t — нормальные напряжения в рельсах, возникающие в связи с изменением температуры плети по сравнению с температурой ее зацепления;
[] - допускаемое напряжение для рельса плети бесстыкового пути, принимаемое равным условному нормальному пределу текучести рельсовой стали, []= 3500 кг/см2.
Плеть бесстыкового пути работает при температурах как выше, так и ниже температуры закрепления. То есть нормальные температурные напряжения могут быть и растягивающими (при пониженных температурах), и сжимающими (при повышенных температурах). Учитывая характер распределения нормальных напряжений от изгиба по поперечному сечению рельса, следует общее условие прочности преобразовать:
для температур работы бесстыковой плети ниже температуры закрепления
KПП-К+tp[];
для температур работы бесстыковой плети выше температуры закрепления
KПГ-К+tс[];
где tp; tс — соответственно нормальные напряжения растяжения и сжатия по поперечному сечению рельса бесстыковой плети, вызванные изменением температуры рельса по сравнению с температурой закрепления;
П-К — растягивающие напряжения в кромочных волокнах подошвы рельса от изгиба под поездной нагрузкой. Для районов с минимальными температурами не ниже — 20ОС расчетные параметры состояния железнодорожного пути принимаются для подсчета П-Кпо летним условиям работы, а для районов с минимальными температурами рельса ниже — 20 °C — по зимним условиям работы;
Г-К — сжимающие напряжения в кромочных волокнах головки рельсе от изгиба под поездной нагрузкой. Подсчитываются по формуле (2.13) для летних условий работы пути.
При полном отсутствии температурного изменения длины рельса температурные напряжения незагруженной поездной нагрузкой плети составляют
t = Еt25t,
где — коэффициент линейного расширения рельсовой стали,
=1,1810-5 1/град;
t — интервал изменения температуры рельса по сравнению с температурой закрепления.
Следовательно, на основе условий прочности можно определить допускаемые интервалы безопасного изменения температуры:
— понижение температуры рельса по условиям прочности кромочных волокон подошвы рельса
— повышение температуры рельса по условиям прочности кромочных волокон головки рельса
Допускаемые интервалы изменения температуры плети бесстыкового пути по условиям устойчивости
В летних условиях при повышенных по сравнению с закреплением плети температурах продольные сжимающие температурные силы могут привести к нарушению устойчивости первоначального положения плети, т. е. к выбросу пути. Допускаемое повышение температуры по условиям сохранения устойчивости положения рельсо-шпальной решетки составляет:
где F — площадь поперечного сечения рельса;
[NK] - допускаемая продольная сила, не вызывающая потери устойчивости положения рельсошпальной решетки.
Условия укладки и эксплуатации бесстыкового пути
Для железных дорог Узбекистана характерно применение температурно-напряженного бесстыкового пути без сезонных разрядок напряжений. Укладка и эксплуатация бесстыкового пути в этом случае возможны при соблюдении условия
ТА[ТА], (16)
где ТА — фактическая максимальная годовая амплитуда колебания температуры рельса для района эксплуатации бесстыкового пути;
[ТА] - допускаемая по условиям прочности и устойчивости амплитуда изменения температуры рельса:
[ТА]=tP+tC — [t3],
tP — допускаемый интервал понижения температуры рельса по сравнению с температурой закрепления, когда в рельсах возникают растягивающие температурные силы, принимается tP=tПП;
tC — допускаемый интервал повышения температуры рельса по сравнению с температурой закрепления, когда в рельсах возникают сжимающие температурные силы, принимается равным наименьшей из величин tПГ и ty;
[t3] - интервал температур, на котором можно произвести окончательное закрепление плетей, устанавливаемый по условиям производства работ; минимальный интервал [t3] рекомендуется принимать при закреплении в весенний период 15ОС, а в осенний период — 10ОС;
При соблюдении условия (16) возможна укладка и эксплуатация бесстыкового пути температурно-напряженного типа без сезонных разрядок. Фактический возможный интервал закрепления плети составит:
t3=tР+tС-ТА
При этом возможные крайние температуры закрепления плети могут быть приняты:
минимальная температура закрепления
mint3 = tmaxmax — tС
максимальная температура закрепления
maxt3 = tР + tminmin.
В этих формулах включены температуры:
tmaxmax — максимальная летняя температура рельса;
tminmin — минимальная зимняя температура рельса.
В случае несоблюдения условия (16) необходимо решить вопрос о переходе к более мощному типу верхнего строения пути.
3.8 Результаты расчетов на прочность и устойчивость
Расчет выполнен с целью определения оптимальных параметров укладки и эксплуатации бесстыкового пути со шпалами типа BF70 и скреплениями типа «PandrolFastclip» на ГАЖК «Узбекистонтемирйуллари» при максимальных скоростях движения пассажирского электровоза «УЗБЕКИСТАН» 160 км/час.
Таблица 12. Исходные данные для расчета
Тип локомотива | «УЗБЕКИСТАН» | |
Расчетная скорость движения, v, км/ч | 100,120,160 | |
Тип рельса / износ, мм | Р65 / 9 | |
Тип шпал | BF70 | |
Эпюра шпал, Эш, шт./км: (прямая / кривая) 1680/1720; 1720/1840; 1840/2000 | ||
Тип скреплений | PandrolFastclip | |
Толщина балласта (щебень / песок), см | 20/20; 20/35 | |
Нагрузка от колеса на рельс, РСТ, кг | ||
Диаметр колес, см | 125,0 | |
Неподрессоренный вес на одно колесо, qК, кг | ||
Статический прогиб рессорной системы, fСТ, мм | 38,9/136,7 | |
Модуль упругости подрельсового основания, кг/см2 | ||
в прямом участке пути летом Uпр-л | 2000 — 3000 | |
в прямом участке пути зимой Uпр-з | 3000 — 4500 | |
в кривом участке пути летом Uкр-л | 2200 — 3400 | |
в кривом участке пути зимой Uкр-з | 3300 — 5100 | |
Наибольшая расчетная глубина изолированной неровности на колесе, e0, см | 0,047 | |
Расстояние между осями шпал, l, см | ||
на прямой | ||
на кривой | ||
Характеристика рельса: | ||
Площадь поперечного сечения, F, см2 | 76,08 | |
Момент инерции рельса, IВ, см4 | ||
Момент сопротивления, WП, см3 | ||
zП, см | 7,42 | |
zГ, см | 9,68 | |
Площадь полушпалы,, см2 | ||
Опорная площадь подрельсовой прокладки,, см2 | ||
Коэффициент учета боковых сил, f | ||
— на прямом участке | 1,13 | |
— в кривых | 1,21−1,69 | |
Расчетная минимальная температура рельса, tmin | — 30OC | |
Расчетная максимальная температура рельса, tmax | +64OС | |
Расчеты пути на прочность выполнены на ЭВМ для летних и зимних условий эксплуатации в прямых и кривых участках пути при скоростях движения пассажирских поездов 100; 120 и 160 км/ч.
В результате расчетов были получены следующие параметры: сила воздействия от колеса на рельс (Pрасч); осевые и кромочные напряжения в подошве и головке рельса (уп-о;уп-к; уг-к); напряжения в прокладке (уш); напряжения в балластном слое и на основной площадке земляного полотна (уб и уопзп); допускаемые интервалы изменения температуры плети бесстыкового пути по условию прочности рельса Дtp и Дtс; температурный интервал закрепления плетей (mintз — maxtз); температурные силы в плетях Рt. Для примера ниже приведены полученные величины Pрасч и напряжений (табл. 13) при: Эш=1720/1840 шпал/км; Uпр-л=2000 кг/см2; Uпр-з=3000 кг/см2; Uкр-л=2200 кг/см2; Uкр-з=3300 кг/см2; толщина балласта аб=35/20 см, минимальный радиус: 500 м (для v=100 км/ч), 700 м (для v=120 км/ч), 1200 м (для v=160 км/ч).
Полученные данные были сравнены с их допускаемыми величинами (табл. 4), в результате чего были сделаны следующие выводы:
1. Для Эш = 1680/1720 и 1720/1840 шпал/км при толщине балласта аб=35/20 см и Uпр-л=2000 кг/см2; Uпр-з=3000 кг/см2:
— напряжения в рельсах значительно ниже допускаемых величин;
— напряжения в подрельсовых прокладках критичны, так как они практически равны допустимым напряжениям (Д=1−3%);
— напряжения на основной площадке земляного полотна критичны, так как они практически равны допустимым напряжениям;
— напряжения в балластном слое не являются критичными, т.к. они меньше допустимых (Д=7−14%)
2. При толщине балласта аб=20/20 см для Эш = 1680/1720 и 1720/1840 шпал/км и Эш = 1840/2000 шпал/км:
— напряжения в рельсах ниже допускаемых величин;
— напряжения в подрельсовых прокладках и на основной площадке земляного полотна значительно превышают допустимые напряжения;
— напряжения в балластном слое не являются критичными, т.к. они меньше допустимых напряжений.
3. Возможность применения эпюры Эш = 1680/1720 шт./км может быть установлена после определения фактической величины Ui.
В результате расчетов также установлено, что при обращении электровоза «Узбекистан» со скоростями до 160 км/ч:
- толщина балласта должна быть не менее аб=35/20 см. Данные ГАЖК «Узбекистонтемирйуллари» свидетельствуют о наличии большого количества участков с фактической толщиной балласта менее 35/20 см (например, 20/20 см) (табл.); такие участки подлежат реконструкции с увеличением толщины балласта;
- напряжения в элементах пути существенно зависят от величины модуля упругости подрельсового основания, фактическая величина которого должна устанавливаться в каждом конкретном случае при проведении соответствующих экспериментальных исследований.
Толщина балласта на направлении Ташкент — Самарканд
Общие выводы по диссертации
1. Настоящая диссертация посвящена исследованию и оптимизации работы современного типа шпал BF70 с упругими типами скреплений «Pandrol Fastclip» на скоростных и высокоскоростных участках ГАЖК «Узбекистон темир йуллари». Это положение определяет актуальность выполненного исследования.
2. Установлено, что в действующих нормативных документах для скоростных и высокоскоростных участков нет единого подхода к параметрам укладки и эксплуатации железобетонных шпал. Также в нормативах не учтено, что шпалы BF70 имеют значительные преимущества перед традиционными шпалами Ш1−1.
3. Был выполнен анализ конструкции железобетонной шпалы BF70 и расчет ее прочностных параметров (прочность, выносливость, трещиностойкость) и произведен сравнительный анализ шпал Ш1−1 и BF70 по следующим критериям:
3.1 Предельные изгибающие моменты по условию:
- выносливости бетона в сжатых зонах шпалы;
- выносливости наиболее растянутой арматуры;
- трещиностойкости бетона в растянутых зонах шпалы;
3.2 Предельных поперечных сил по условию трещиностойкости на нейтральной оси приведенного сечения шпалы BF70.
В результате расчетов было установлено, что по всем перечисленным в пункте 3 параметрам шпалы BF70 значительно превосходят шпалы Ш 1−1 (в среднем на 30−40%).
4. В результате испытаний шпал на трещиностойкость в аккредитованной лаборатории был выявлен значительный запас шпал BF70 по критерию трещиностойкости. Коэффициент запаса по трещиностойкости в средней части шпалы составляет К ср = 1,94 — 1,97, в подрельсовом сечении — К подр= 2,2 — 2,5.
5. В результате испытаний бетона шпал на прочность установлено, что прочность бетона шпал значительно превышает требуемые значения (53 МПа) и составляет в среднем 72,7 МПа. Коэффициент запаса составляет от 1,32 до 1,54.
6. Выполненные расчеты и экспериментальные исследования подтвердили значительные преимущества шпалы BF70 относительно шпал Ш1−1 и определили возможность исследования уменьшения эпюры их укладки на участках скоростного и высокоскоростного движения поездов. Для этого были выполнены комплексные расчеты пути со шпалами BF70.
7. В диссертации впервые выполнен расчет бесстыкового пути со шпалами BF70 и скреплениями «Pandrol Fastclip» на прочность и устойчивость при воздействии поезда «Узбекистан» на скоростных участках. Расчет был сравнен с результатами аналогичных расчетов под воздействием электропоезда «Афрасиаб» на высокоскоростных участках (магистрант Аликперов С), (скорости — до 160 км/ч). Расчеты выполнены с целью определения оптимальных параметров укладки и эксплуатации бесстыкового пути со шпалами BF70 на ГАЖК «Узбекистон темир йуллари», включая скоростные и высокоскоростные линии.
8. В результате расчетов установлено, что воздействие электропоезда «Узбекистан» на скоростных участках при скоростях 160 км/ч достаточно близко к аналогичным показателям от воздействия электропоезда «Афрасиаб» на высокоскоростных участках при скоростях до 250 км/ч. И в том и другом случае динамическая сила воздействия от колеса на рельс находится в пределах 21 — 23 т.
9. Данные ГАЖК «Узбекистон темир йуллари» свидетельствуют о наличии большого количества участков со шпалами BF70, где фактическая толщина балласта менее 35/20 см (например, 20/20 см), табл. 13.
10. В результате расчетов установлено, что при такой толщине балласта (аб=20/20 см) и для Эш = 1680/1720 и 1720/1840 шпал/км и Эш = 1840/2000 шпал/км:
— напряжения в рельсах ниже допускаемых величин;
— напряжения в балластном слое не являются критичными, т.к. они меньше допустимых напряжений.
- напряжения в подрельсовых прокладках и на основной площадке земляного полотна значительно превышают допустимые напряжения. Такие участки требуют немедленной реконструкции с увеличением толщины балластного слоя независимо от эпюры шпал.
11. При толщине балласта аб=35/20 см и эпюре шпал Эш = 1680/1720 и 1720/1840 шпал/км и при Uпр-л=2000 кг/см2; Uпр-з=3000 кг/см2:
— напряжения в рельсах значительно ниже допускаемых величин;
— напряжения в подрельсовых прокладках критичны, так как они практически равны допустимым напряжениям (Д=1−3%);
— напряжения на основной площадке земляного полотна критичны, так как они практически равны допустимым напряжениям;
— напряжения в балластном слое не являются критичными, т.к. они меньше допустимых (Д=7−14%).
Такие участки возможно эксплуатировать при Эш = 1680/1720 и 1720/1840 шпал/км при постоянном контроле всех параметров рельсовой колеи и земляного полотна.
12. Притолщине балласта аб=35/20 см и Uпр-л=3000 кг/см2; Uпр-з=4500 кг/см2, для Эш = 1680/1720 и 1720/1840 шпал/км, Эш = 1840/2000 шпал/км и Эш = 2000/2000 шпал/км:
— напряжения в рельсах ниже допускаемых величин;
— напряжения в балластном слое не являются критичными, т.к. они меньше допустимых напряжений.
- напряжения в подрельсовых прокладках и на основной площадке земляного полотна значительно превышают допустимые напряжения;
Такие участки требуют реконструкции с увеличением толщины балластного слоя независимо от эпюры шпал.
13. В результате выполненного исследования установлена значительная зависимость напряжений в элементах верхнего строения пути от модуля упругости подрельсового основания. Поэтому важно установить фактическую величину этого показателя на конкретных участках ГАЖК «УТЙ» со шпалами BF70 и скреплениями.
14. При Uпр-л=2000 кг/см2; Uпр-з=3000 кг/см2; Uкр-л=2200 кг/см2; Uкр-з=3300 кг/см2 на скоростных участках при воздействии электропоездов «Узбекистан» и «Афрасиаб» возможен переход с эпюры шпал Эш = 2000/2000 шпал/км на эпюру шпал Эш = 1720/1840 шпал/км (или Эш = 1840/2000 шпал/км). При этом экономия составит от 160 до 280 шпал на каждый километр (от 17 000 до 30 000 тыс. долларов США на км).
15. При Uпр-л=2000 кг/см2; Uпр-з=3000 кг/см2; Uкр-л=2200 кг/см2; Uкр-з=3300 кг/см2 на высокоскоростных участкахпри воздействии электропоезда «Афрасиаб» также возможен переход с эпюры шпал Эш = 2000/2000 шпал/км на эпюру шпал Эш = 1720/1840 шпал/км (или при контроле состояния рельсовой колеи и земляного полотна на эпюру Эш = 1840/2000 шпал/км). При этом экономия также составит от 160 до 280 шпал на каждый километр (от 17 000 до 30 000 тыс. долларов США на км).
Приведенные выше выводы определяют систему рационального использования шпал BF70 с упругими типами скреплений «Pandrol Fastclip» на скоростных и высокоскоростных участках ГАЖК «Узбекистон темир йуллари» и рекомендуются к внедрению.
Список использованных источников
1. Золотарский А. Ф., Евдокимов Б. А., Исаев Н. М. и др, 1980 г. Железобетонные шпалы для рельсового пути. М., Транспорт, 1980.
2. Технологическая инструкция по производству предварительно напряженных железобетонных моноблочных шпал ТИ 64−21 468 397−01:2007. Рабочие чертежи шпалы BF70. Ташкент, ДП «RWS Optimum», 2007.
3. Овчинников А. Н. Экспериментальные испытания железобетонных шпал типа BF70 на трещиностойкость. Ташкент, ТАСИ, 2007 г.
4. ГОСТ 10 629–88 «Шпалы железобетонные предварительно напряженные для железных дорог колеи 1520 мм.» Технические условия. Москва, 1988.
5. O’zDSt EN 13 230−1,2:2003. Шпалы и брусья бетонные для применения на железнодорожных путях. Ташкент, Государственный комитет РУз по архитектуре и строительству, 2003.
6. Методика оценки воздействия подвижного состава на пути по условиям обеспечения его надежности. №ЦПТ-52/14. Утв. 16.06.2000 г.
7. ВСН 450-Н «Ведомственными техническими указаниями по проектированию и строительству. Железные дороги колеи 1520 мм». Ташкент, ГАЖК «УТЙ», 2012.
8. ВСН 448-Н «Инфраструктура высокоскоростной железнодорожной линии Ташкент — Самарканд. Общие технические требования». Ташкент, ГАЖК «УТЙ», 2012.
9. ВСН «Ведомственные технические указания по проектированию. Железные дороги колеи 1520 мм». Ташкент, ГАЖК «УТЙ»
10. NЦРБ-393. Инструкция по техническому обслуживанию и эксплуатации сооружений, устройств, подвижного состава и организации движения на участках обращения скоростных пассажирских поездов. МПС, 1996.
11. Лехно И. Б. и др. Путевое хозяйство: Учебник для вузов ж.-д. трансп./ И. Б. Лехно, С. М. Бельфер, Э. В. Воробьев и др.; Под ред. И. Б. Лехно. — М.: Транспорт, 1990. — 472 с.
12. Технологические процессы ремонта бесстыкового пути на железобетонных шпалах. М., Транспорт, 1973. — 320 с.
13. Крейнис З. Л., Коршикова Н. П. Техническое обслуживание и ремонт железнодорожного пути: Учебник для техникумов и колледжей железнодорожного транспорта. М.: УМК МПС России, 2001. — 768 с.
14. Тихомиров В. И. Содержание и ремонт железнодорожного пути / Учебник для техникумов. — М.: Транспорт, 1987. — 336 с.
15. Овчинников А. Н. Шпалы BF70 с упругими скреплениями на дорогах Узбекистана / А. Овчинников, А. Расулев, З. Фазилова // Путь и путевое хозяйство. — 2008. — № 7. — с. 35−36.
16. Гасанов А. И. Несущая способность подрельсового основания в сложных условиях / Путь и путевое хозяйство. — 2008. — № 7. — с. 37−38.
17. Щахунянц Г. М. Железнодорожный путь. Изд. 3, перераб. и доп. — М.: Транспорт, 1987.
18. Крейнис З. Л., Селезнева Н. Е. Бесстыковый путь. Как ремонтировать Бесстыковый путь: Учеб. пособие / под ред. З. Л. Крейниса — М.: Маршрут, 2005. — 123 с.
19. Каменский В. П., Шац Э. Я. Содержание железнодорожного пути в кривых. — М.: Транспорт, 1987. — 189 с.
20. Нишанбаев Ш. Применение упругих скреплений на железобетонных шпалах: Дис. магистра. — Т., 2002.
21. Блохин К. А., Пашинин С. Л. Ремонт железнодорожного пути. М.: Транспорт, 1987. — 360 с.
22. Устройство, ремонт и текущее содержание железнодорожного пути: /Учебник для ПТУ/ С. В. Амелин, М. П. Смирнов. В. И. Рязанцев, В.И. Ярохно/; под ред. С. В. Амелина. — 2-е изд., перераб. и доп. — М.: Транспорт, 1991. — 272 с.
23. Путевое хозяйство: Учебник для вузов ж.-д. транспорта/ Альбрехт В. Г., Лидерс Г. В. и др.; Под ред. М. А. Чернышева. — М.: Трансжелдориздат, 1959. — 435 с.
24. Устройство, содержание и ремонт железнодорожного пути: Учебник для техн. школ ж. — д. транспорта/ 4-е перераб. изд. — М.: Транспорт, 1974.
25. Фришман М. А. и др. Конструкция железнодорожного пути и его содержание/ М. А. Фришман. Н. А. Понамаренко. С. И. Финицкий. -2-е изд., перераб. и доп. — М.: Транспорт, 1987. — 351 с.
26. Рельсы железнодорожные новые сварные. Технические условия ТУ 0921−057−1 124 328−98 (взамен ТУ 32 ЦП-560−93). Рельсы железнодорожные старогодные отремонтированные сварные. Технические условия ТУ 0921−077−1 124 328−99 (взамен ТУ 32 ЦП-561−93) / МПС России. М.:Транспорт, 1999. 55 с.
27. Технические указания по устройству, укладке, содержанию и ремонту бесстыкового пути / МПС России. М.:Транспорт, 2000. 96 с.
28. Технические условия на работы по ремонту и планово-предупредительной выправке пути / МПС России. М.:Транспорт, 1998. 188 с.
29. Руководство по установке рельсовых скреплений
30. Современные рельсовые скрепления./ЖДМ — online / Информационная служба журнала <�Железные дороги мира>. — 1998. — № 5. / Kramer. Railway Track & Structures, 1998, № 6, p 41 — 47.
31. Рельсовые скрепления для современных условий эксплуатации /ЖДМ — online / Информационная служба журнала <�Железные дороги мира>. — 2002. — № 11. / T. Judge. RailwayTrack&Structures, 2000, № 6, p. 49 — 53