Математическое моделирование процессов горячего деформирования при штамповке башенных поковок
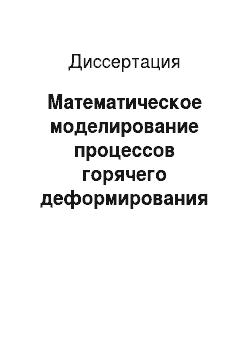
В условиях рыночной экономики для выживания предприятий большое значение имеет снижение себестоимости продукции и уменьшение сроков разработки новых изделий, что достигается, прежде всего, автоматизацией деятельности предприятия на основе современных компьютерных технологий. И хотя наибольший эффект может быть получен лишь внедрением комплексной автоматизации, локальная автоматизация отдельных… Читать ещё >
Содержание
- 1. Вычислительные системы, моделирующие процессы обработки металлов давлением, и перспективы их дальнейшего развития
- 2. Моделирование температурных полей в сложнопрофильных локальнооднородных конструкциях
- 2. 1. Конечноэлементная аппроксимация температурной задачи
- 2. 1. 1. Моделирование плоских температурных полей
- 2. 1. 2. Моделирование осесимметричных температурных полей
- 2. 1. 3. Реализуемые типы граничных условий
- 2. 2. Тестовые задачи и примеры расчета температурных полей
- 2. 2. 1. Расчет плоского температурного поля пластины МКЭ и его сравнение с аналитическим решением Исаченко В. П
- 2. 2. 2. Расчет осесимметричного температурного поля цилиндра МКЭ и его сравнение с аналитическим решением
- 2. 1. Конечноэлементная аппроксимация температурной задачи
- 2. 2. 3. Расчет температурных полей промышленных изделий
- 3. 1. Постановка краевой задачи
- 3. 2. Конечноэлементная аппроксимация задачи термоупругости
- 3. 2. 1. Соотношения МКЭ для щфокодеформированного и плосконапряженного состояний"
- 3. 2. 2. Соотношения МКЭ для осесимметричного состояния
- 3. 2. 3. Автоматизация расчетов. Пакет БРЬЕМ-КТ
- 3. 3. Проверка точности и сходимости, получаемых в системе 8РЬЕ1чГ-КТ, результатов расчетов
3.3.1. Аналитическое решение задачи о толстостенной трубе под давлением и с неоднородным распределением температуры
3.3.2. Численный эксперимент. Основные результаты
3.3.3. Анализ результатов моделирования ТНДС в окрестности электрического ввода в конструкции кольцевого лазера типа ЗЛК-16 при его изготовлении и эксплуатации
4. Моделирование процессов горячего деформирования при штамповке башенных поковок на КГШП
4.1. Математическая модель процесса горячей штамповки осесимметричных изделий. Последовательность действий при построении решения
4.2. Получение конечноэлементных соотношений для математической модели горячего пластического течения
4.3. Моделирование получения башенных поковок 7510А1 и 7207А на линии Л-309 в условиях Волжского подшипникового завода 113 4.3.1. Расчет течения металла при многопереходной штамповке серийных колец 7510А1. Сравнение с экспериментальными данными, полученными в промышленных условиях
4.3.2. Расчет течения металла и термонапряженного состояния штамповой оснастки при получении башенной поковки 7207А
4.3.3. Предложение по усовершенствованию технологического процесса получения башенной поковки 7207А на линии Л
Математическое моделирование процессов горячего деформирования при штамповке башенных поковок (реферат, курсовая, диплом, контрольная)
В условиях рыночной экономики для выживания предприятий большое значение имеет снижение себестоимости продукции и уменьшение сроков разработки новых изделий, что достигается, прежде всего, автоматизацией деятельности предприятия на основе современных компьютерных технологий. И хотя наибольший эффект может быть получен лишь внедрением комплексной автоматизации, локальная автоматизация отдельных участков технологического процесса также может принести существенную экономию материальных и временных затрат. Одним из таких участков является проектирование элементов технологии кузнечного производства.
Компьютерное моделирование позволяет отработать технологию кузнечных процессов на стадии проектирования без дорогостоящих натурных экспериментов, а также оптимизировать уже имеющуюся — конфигурацию штамповой оснастки, размер и температуру заготовки и т. д. Оптимизация технологии подразумевает как получение качественной поковки, так и вопросы связанные с износом оборудования, уменьшением энергоемкости производства.
Часто бывает трудно или невозможно получить экспериментальные данные об интересующих параметрах процесса. Это связано с экстремальными рабочими условиями кузнечных машин горячей штамповки: большая скорость, высокое давление и температура.
Поэтому, с развитием персональной вычислительной техники появилось множество математических моделей и реализующих их программных комплексов, призванных помочь проектировщикам-технологам.
Наибольшее распространение среди таких программных комплексов получили системы, основанные на методе конечных элементов (МКЭ). Поскольку он является наиболее универсальным методом, практически не накладывает ограничений на геометрию детали, свойства материала и граничные условия.
В данной работе на основе МКЭ построена модель неизотермического течения металла при многопереходной штамповке, а также термоупруго-пластическая модель для расчета штамповой оснастки. Последняя применима также к элементам конструкций и деталям машин. Модели реализованы в рамках вычислительной системы ЭРЬЕК, предъявляющей умеренные требования к мощности вычислительной системы и компьютерным навыкам пользователя.
В первой главе приведен обзор существующих МКЭ-систем, моделирующих обработку металлов давлением. Определена цель работы. Это дальнейшее развитие актуального и перспективного направления в создании проблемно-ориентированных пакетов состоящих из универсальных блоков и модулей. А именно разработка новых математических моделей процессов, поддерживаемых программным комплексом 8РЬЕЫ, а также методик его использования для комплексного проектирования новых и усовершенствования существующих технологий основанных на эффективном применении теории механики деформируемого твердого тела.
Во второй главе построены модели температурных полей в сложно-профильных локальнооднородных плоских и осесимметричных конструкциях. Выведены соответствующие соотношения МКЭ и рекурсивная по времени система линейных уравнений относительно вектора температур.
Рассмотрены тестовые задачи, имеющие аналитическое решение в виде рядов. Сравнение аналитического решения с решением, полученным МКЭ, показало хорошее совпадение. Отклонения составили десятые доли процента.
Приведены примеры расчета температурных полей промышленных изделий и результаты сравнения расчетных полей с экспериментальными данными. Разница в контрольных точках находится в пределах 3−5%.
В третьей главе построена математическая модель термо-упруго-пластического формоизменения изделий при термомеханическом воздействии, выведены соотношения МКЭ для плоскодеформированного, плосконапряженного и осесимметричного состояний.
Описан пакет БРЬЕМ-КТ, в котором реализован алгоритм расчета температурных полей и термонапряженного состояния.
На примере задачи о толстостенной трубе под давлением и с неоднородным распределением температуры проверена точность и сходимость получаемых в пакете БРЬЕТЧ-КТ результатов. Погрешность составляет доли процента.
Проведено моделирование термо-напряженно-деформированного состояния (ТНДС) в окрестности электрического ввода в конструкции кольцевого лазера типа ЗЛК-16 при его изготовлении и эксплуатации. Изучена зависимость нежелательных деформаций в конструкции при изменении температуры и найдены пути их уменьшения.
Проведенные в НПК-470 НИИ «Полюс» эксперименты по измерению кривизны поверхности оптического контакта в широком температурном диапазоне с помощью лазерного интерферометра подтвердили эффективность предложенных рекомендаций и высокую степень достоверности полученных в пакете БРЬЕИ-КТ результатов. Среднее статистическое отклонение экспериментальных данных от рассчитанных прогнозов не превышает 25%, при погрешности измерений кривизны — 15%.
В четвертой главе построена математическая модель процесса горячей штамповки осесимметричных изделий, описывающая поле скоростей течения металла при штамповке и эволюцию поля температур заготовки при прохождении технологической цепи. Получены МКЭ соотношения для математической модели неизотермического пластического течения, изложен алгоритм решения задачи.
Приведены результаты моделирования штамповки башенных поковок 7510А1 и 7207А на линии Л-309 в условиях Волжского подшипникового завода.
Проведено сравнение расчетной конфигурации поковки 7510А1 с экспериментальными данными, полученными в промышленных условиях. А также сравнение изотермической и не изотермической моделей штамповки. Для всех трех переходов отклонение формы поковки от опытного образца находится в пределах 1 мм., что соответствует заводским допускам и точности измерений. По отношению к радиусу поковки последнего перехода (45 мм.) наибольшее отклонение предсказанной формы от формы опытных образцов составляет 2%.
Моделирование показало, что не изотермическое течение металла в угловых точках и вблизи границы заметно отличается от изотермического. А эти участки имеют практическое значение при проектировании процессов, поскольку тенденции течения металла в поковке определяют не только развиваемые механические усилия, но и конечную износостойкость, и коррозию изделий во время эксплуатации. Таким образом, неизотермическая модель более точно отражает действительную ситуацию и является предпочтительной в тех случаях, когда требования к точности прогноза достаточно высоки.
По результатам моделирования башенной поковки 7207А, предложено усовершенствование профиля штамповой оснастки, которое должно привести к выравниванию усилия штампа на втором и третьем переходах за счет снижения усилия на третьем переходе, к синхронизации срока службы штампов второго и третьего переходов. То есть, в конечном счете, к уменьшению времени простоя линии.
На основании расчетов штамповой оснастки принят ряд решений конструкторского характера. Определено наилучшее расположение выталкивателя в штампе. Цилиндрическая поверхность выталкивателя должна пересекать рабочую поверхность штампа в зоне средних напряжений близких к нулю. Если она находится в зоне сжимающих напряжений, возможно заклинивание выталкивателя, а если в зоне растягивающих напряжений, то возможно раскрытие щели в рабочей поверхности штампа, которое может привести к непоправимой порче изделия и штампового инструмента.
Достоверность основных результатов работы обеспечена применением хорошо изученных вычислительных методов и подтверждена сравнением результатов расчета с экспериментальными и промышленными данными, с аналитическими решениями модельных задач. А также практическим применением системы в промышленности.
На защиту выносится:
1. Математическая модель процессов горячего деформирования при штамповке башенных поковок, описывающая неизотермическое течение металла и термо-напряженно-деформированное состояние (ТНДС) штамповой оснастки.
2. Алгоритм решения конструкционных задач с учетом ТНДС, построенный с использованием базовых вычислительных систем программного комплекса БРЬЕЫ.
3. Результаты расчетно-экспериментальных исследований течения металла в рамках технологического процесса получения башенных поковок на кривошипных горячештамповочных прессах и предложение по их усовершенствованию.
В заключении автор считает необходимым выразить свою глубокую признательность профессору, доктору технических наук Е. Н. Чумаченко за научное руководство и моральную поддержку при написании работы и И. В. Логашиной за оказанную помощь.
Заключение
и выводы.
1. Разработана математическая модель термо-упруго-пластического формоизменения изделий при термомеханическом воздействии. На основе МКЭ построен алгоритм расчета термо-напряженно-деформированного состояния. Создана новая версия пакета БРЬЕИ-КТ позволяющая, с учетом разработанных алгоритмов, рассчитывать температурные поля и термо-упруго-пластическое формоизменение разнообразных конструкций. В частности термонапряженное состояние штам-повой оснастки.
2. Анализ результатов моделирования ТНДС в окрестности электрического ввода в конструкции кольцевого лазера типа ЗЛК-16 позволил выявить температурные зависимости нежелательных деформаций, возникающих при высокотемпературном соединении оптических деталей и деталей из металлов с низким пределом текучести, а также при эксплуатации сварного ввода газового лазера.
3. В результате проведенных исследований предложена новая технологическая операция охлаждения части конструкции лазера, находящейся в состоянии активного температурного пластического нагруже-ния, до уровня ниже требуемой температуры с последующим нагревом до номинальной температуры оптического контакта, что позволило обеспечить его высокую надежность. Кроме этого, предложен способ локализации деформаций путем выполнения проточки вокруг зоны приварки алюминиевого электрода. Даны конкретные рекомендации по размерам проточки для различных вариантов сварной конструкции.
4. Проведенные в НПК-470 НИИ «Полюс» эксперименты по измерению кривизны поверхности оптического контакта в широком температурном диапазоне с помощью лазерного интерферометра подтвердили эффективность предложенных рекомендаций и высокую степень достоверности полученных в пакете 8РЬЕЫ-КТ результатов. Среднее статистическое отклонение экспериментальных данных от рассчитанных прогнозов не превышает 25%, при погрешности измерений кривизны — 15%. Пакет БРЬЕМ-КТ рекомендован НПК-470 НИИ «Полюс» для использования при моделировании напряженно-деформированного состояния оптических приборов, работающих в широком интервале температур.
5. Вычислительная система 8РЬЕ? ч[-КТ в настоящее время установлена и используется в учебном процессе и научных исследованиях Московского государственного института стали и сплавов для подготовки специалистов и расчетов термонапряженнодеформированного локально-однородного упругопластического состояния тяжело нагруженных деталей металлургических машин.
6. Разработана математическая модель процесса горячей штамповки осесимметричных изделий. На основе МКЭ построен алгоритм расчета неизотермического течения металла при штамповке с учетом трения.
Компьютерная реализация алгоритмов осуществлена в вычислительной системе.
SPLEN-ST.
7. При помощи пакета SPLEN-ST проведено моделирование получения башенных поковок 7510А1 и 7207А на линии JI-309 в условиях Волжского подшипникового завода. Проведено сравнение формы опытных образцов поковки 7510А1 с расчетной формой. Установлено, что для всех трех переходов отклонение формы поковки от опытного образца находится в пределах 1 мм., что соответствует заводским допускам и точности измерений. По отношению к радиусу поковки последнего перехода (45 мм.) наибольшее отклонение предсказанной формы от формы опытных образцов составляет 2%.
8. Сопоставление изотермической и неизотермической моделей штамповки башенной поковки 7510Al показало, что не изотермическая модель дает прирост максимального усилия штампа по переходам относительно изотермической модели соответственно на 7,36%, 16,55% и 4,01% вследствие захолаживания металла, ведущего к увеличению сопротивления деформированию.
9. На примере получения башенной поковки 7207А показана методика разработки профиля штамповой оснастки. Проведен расчет течения металла и термонапряженного состояния штамповой оснастки. Предложено усовершенствование профиля штамповой оснастки, которое должно привести к выравниванию усилия штампа на втором и третьем переходах за счет снижения усилия на третьем переходе, к синхронизации срока службы штампов второго и третьего переходов. То есть, в конечном счете, к уменьшению времени простоя линии.
10. Вычислительный комплекс SPLEN-ST успешно прошел опытно-промышленное опробование на Волжском подшипниковом заводе и в настоящее время используется, как основной элемент САПР ТП, при проектировании новых технологических процессов и усовершенствовании существующих элементов промышленных технологий.
Список литературы
- Zienkiewicz О. С., Jain Р. С., Onate Е. Flow of Solids During Forming and Extrusion: Some Aspects of Numerical Solutions/Ant. J. Solids Struct. -1978.-Vol. 14. -p.15−38.
- Rebelo N., Kobayashi S., A Coupled Analysis of Viscoplastic Deformation and Heat Transfer II. Applications//Int. J. Mech. Sci. — 1980. — Vol. 22. -p.707−718.
- Coupez Т., Soyris N., Chonot J. L. 3-D Finite Element Modelling of the Forging Process with Automatic Remeshing//J. Meterias Process. Tech. -1991.-Vol. 27.-p.l 19−133.
- Cho J. R., Park C. Y., Yang D. Y. Investigatation of the Cogging Processes by Three-Dimensional Thermo-Viscoplastic Finite Element Analysis//Proc. Instn. Mech. Engrs. 1992. — Vol. 206. — p.277−286.
- Joun M. S., Moon H. K., Hwang S. M. Automatic Computer Simulation of Multi-Stage Hot Forging Process Flow Analysis, Temperature Analysis, Temperature Analysis and Die Stress Analysis//95 KSME Spring Meeting (in Korean). — 1995. — Vol. 1. -p.337−340.
- Shen G., Semiatin S. L., Shivpuri R. Modeling Microstructural Development during the Forging of Waspaloy//Metall. Trans. A. 1995. — Vol. 26A. -p.1795−1803.
- Гун Г. Я. Теоретические основы обработки металлов давлением (теория пластичности). -М.: Металлургия, 1980. 688с.
- Гун Г. Я. Математическое моделирование процессов обработки металлов давлением. М.: Металлургия, 1983. — 351с.
- Оптимизация прокатного производства/А.Н. Скороходов, П. И. Полухин, Б. М. Илюкович и др. -М.: Металлургия, 1983. 431с.
- Тарновский И.Я., Скороходов А. Н., Илюкович Б. М. Элементы теории прокатки сложных профилей. -М.: Металлургия, 1972. 350с.
- Малинин Н.Н. Прикладная теория пластичности и ползучести. -М.: Машиностроение, 1975.-399с.
- Романов К.И. Механика горячего формоизменения металлов. М.: Машиностроение, 1993.-240с.
- Бровман М.Я. Применение теори пластичности в прокатке. М.: Металлургия, 1991.-254с.
- Богатов А.А., Мижирицкий О. И., Смирнов С. В. Ресурс пластичности металлов при обработке давлением. М.: Металлургия, 1984. — 144с.
- Поздеев А.А., Няшин Ю. И., Трусов П. В. Остаточные напряжения, теория и приложения. М.: Наука, 1982. — 112с.
- Математическое моделирование технологических процессов обработки металлов давлением: Тез докл. всерос. науч.-техн. конф. (19−21 июня 1990 г.)/АН СССР, Институт механики сплошных сред УНЦ/Редкол.: Ю. И. Няшин и др. Пермь: Б. и., 1990. — 207с.
- Большие упруго-пластические деформации: теория, алгоритмы, прило-жения/А.А. Поздеев, П. В. Трусов, Ю.И. Няшин- отв. ред. В. В. Мошев. -М.: Наука, 1986.-20с.
- Разрушение металлов при пластическом деформировании/ С. М. Красневский, Е. М. Макушок, В.Я. Щукин- под ред. A.B. Степаненко. Минск: Наука и техника, 1983. — 173с.
- Теоретические основы процессов поверхностного пластического деформирования/АН БССР, Физ.-Техн. ин-т/Е.М. Макушок, Т.В. Калинов-ская, С. М. Красневский и др.- под ред. В. И. Беляева. Минск: Наука и техника, 1988. — 182с.
- Обработка металлов давлением: Межвуз. сб. науч. тр./Урал. политех, ин-т им. С.М. Кирова/Отв. ред. B.JI. Колмогоров. Свердловск: УПИ, 1989.- 135с.
- Колмогоров В. Л. Механика обработки металлов давлением. М.: Металлургия, 1986. — 688с.
- Колмогоров B.JI. Краевые задачи обработки металлов давлением, их решение вариационными методами и некоторые математические модели. Изд. УрО АН СССР, 1990. — 145с.
- Колмогоров B.JI., Мигачев Б. А. Прогнозирование разрушения металлов в процессе горячей пластической деформации//Известия академии наук. Металлы. 1991.- № 3. — с.124−128.
- Колмогоров В.Л., Унксов Е. П., Джонсон У., Овчинников А. Г., и др. Теория ковки и штамповки. 2-е изд. — М.: Машиностроение, 1992. -719с.
- Jon M.S., Moon Н.К., Rajiv Shivpuri Automatic Simulation of a Sequence of Hot-Former Forging Process by a Rigid-Thermoviscoplastic Finite Element Method//Journal of Engineering Materials and Tehnology. 1998. -october. — Vol. 120. — p.291−296.
- Сегерлинд Л. Применение метода конечных элементов.: Пер. с англ. -М.: Мир, 1979.-392с.
- Зенкевич О. Метод конечных элементов в технике.: Пер. с англ. М.: Мир, 1975.-542с.
- Оден Дж. Конечные элементы в нелинейной механике сплошных сред: Пер. с англ. М.: Мир, 1979. — 392с.
- Коннор Дж., Бреббиа К. Метод конечных элементов в механике жидкостей. Л.: Судостроение, 1979. — 263с.
- Печенкин Д.В. Автоматизация расчета температурных полей для плоских и осесимметричных тел произвольной формы//Тезисы докладов НТК студентов, аспирантов и молодых специалистов/МГИЭМ. М.: МГИЭМ, 1998.-c.53.
- Чумаченко E.H., Печенкин Д. В., Рогалевич Л. Э. Моделирование температурных полей в элементах конструкций и изделиях металлургического и кузнечного производств (Сообщение 1)//Металлург. 2000. — № 3. -с.45−46.
- Donea J. On the Accuracy of Finite Element Solutions to the Transient Heat Conduction Education//Intern. J. For Numerical Methods in Engineering. -1974.-Vol. 8.-p. 103−110.
- Чумаченко E.H., Печенкин Д. В., Рогалевич Л. Э. Моделирование температурных полей в элементах конструкций и изделиях металлургического и кузнечного производств (Сообщение 2)//Металлург. 2000. — № 4. -с.42−43.
- Исаченко В.П., Осипов В. А., Сукомел A.C. Теплопередача. М.: Энергия, 1969.-438с.
- Подгорный А.Н., Гонтаровский П. П., Марченко Г. А., Печерская О. П. Метод конечных элементов в стационарной задаче термоупругости. -Харьков: Изд-во АН УССР, 1980. с. 19, 20.
- Скороходов А.Н., Зудов Е. Г., Киричков A.A., Петренко Ю. П. Остаточные напряжения в профилях и способы их снижения. М.: Металлургия, 1985.- 184с.
- Термопрочность деталей машин/Под ред. И. А. Биргера и Б. Ф. Шорра.- М.: Машиностроение, 1975. 455с.
- Чумаченко E.H., Печенкин Д. В. Моделирование и расчет термоупруго-пластических деформаций при анализе локально изотропных конструкций. Учебное пособие. М.: Московский государственный институт электроники и математики, 2000. — 183с.
- Смирнов О.М., Чумаченко E.H., Чумаченко С. Е. Оптимизация проектирования штамповой оснастки и ответственных узлов металлургических машин//Теория и технология процессов пластической деформации.- М.: МИСиС. 1997. — с.377−380.
- Метелкин И.И., Павлова М. А., Поздеева Н. В. Сварка керамики с металлами. -М.: Металлургия, 1977. 160с.
- Виноградов А.Н., Ершов B.C., Печенкин Д. В., Мельников A.B. Упругие и пластические деформации в оптических датчиках//Сб. материалов XII
- НТК с участием зарубежных специалистов «Датчик-2000"/Под ред. проф. В. Н. Азарова. М.: МГИЭМ, 2000. — с.38−39.
- Тихонов Л.В., Кононенко В. А. и др. Структура и свойства металлов и сплавов. Справочник. Киев: Наукова Думка, 1986. — 568с.
- Чумаченко E.H. Математическое моделирование пластического формоизменения материалов при обработке давлением, Учебное пособие. -М: МГИЭМ, 1998.- 157с.
- Печенкин Д.В. Компьютерное моделирование процесса горячей штамповки осесимметричных деталей//Тезисы докладов НТК студентов, аспирантов и молодых специалистов МГИЭМ. М.: МГИЭМ, 2000. -с.4−5.
- Чумаченко E.H., Скороходов А. Н., Александрович А. И. К вопросу о применении МКЭ в задачах о деформировании несжимаемых сред //Изв. вузов. Черная металлургия. 1985. — № 9. — с.89−92.
- Крупенко Е.А., Чумаченко E.H. Моделирование технологических процессов штамповки в условиях сверхпластичности//Малоотходные процессы холодного и горячего деформирования металлов и оборудование для их реализации/ЭНИКМАШ. Воронеж, 1985. — с.108−125.
- Расчет формоизменения оболочек вращения при газостатической формовке в состоянии сверхпластичности/Е.Н. Чумаченко, JI.T. Макарова, А. Н. Скороходов и др.//Изв. вузов. Черная металлургия. 1985. — № 3. -с.71−75.
- Контактное трение в процессах ОМД//А.Н. Леванов, А. Л. Колмогоров, С. П. Буркин и др. М.: Металлургия, 1976. — 416с.
- Агапов H.A., Бойцов В. В. Влияние параметров изотермического деформирования на эффективность стеклянных смазок/Авиационная промышленность. Приложение к журналу. М.: Машиностроение — 1984. -№ 4. — с.25−29 (ДСП).
- Охрименко Я.М. Технология кузнечно-штамповочного производства. -М.: Машиностроение, 1976. 560с.
- Чумаченко E.H. Моделирование контактного взаимодействия в процессах обработки давлением//КШП. 1996. — № 5. — с. 2−6.
- Ефимов А.Б., Романюк С. Н., Чумаченко E.H. Об определении закономерностей трения в процессах ОМД//Механика твердого деформируемого тела. 1995. — № 6. — с.82−98.
- Крагельский И.В., Добычин М. Н., Комбалов B.C. Основы расчетов на трение и износ. М.: Машиностроение, 1977. — 525с.
- Боуден Ф., Тейбор Д. Трение и смазка твердых тел. М.: Машиностроение, 1968. — 543с.
- Грудев А.П., Зильберг Ю. В., Тилик В. Т. Трение и смазки при ОМД. Справочник. М.: Металлургия, 1982. — 312с.
- Чертавских А.К., Белосевич В. К. Трение и технологическая смазка при ОМД. М.: Металлургия, 1968. — 362с.
- Исаченков Е.И. Контактное трение и смазки при ОМД. М.: Машиностроение, 1978. — 208с.
- Макушок Е.М. Механика трения. Минск: Наука и техника, 1974. -254с.
- Мур Д. Основы и применение трибоники.: Пер. с англ. М.: Мир, 1978. — 520с.
- Губкин С.И. Пластическая деформация металлов. т. 2. — М.: Гостех-издат, 1961. — 416с.
- Колмогоров B.JI. Механика ОМД. М.: Металлургия. — 1986. — 687с.
- Томсен Э., Янг Ч., Кобаяши Ш. Механика пластических деформаций при обработке металлов. М.: Машиностроение, 1969. — 503с.
- Бэкофен В. Процессы деформации. М.: Металлургия, 1977. — 288с.
- Обработка металлов давлением в машиностроении/П.И. Полухин, В. А. Тюрин, П. И. Давидков, Д. Н. Витанов. М.: Машиностроение- София: Техника, 1983. — 279с.
- Колмогоров Г. Л. Гидродинамическая смазка при ОМД. М.: Металлургия, 1986. — 166с.
- Томленов А.Д. Теория пластического деформирования металлов. М.: Металлургия, 1972. — 408с.
- Норри Д., Де Фриз Ж. Введение в метод конечных элементов. М.: Мир, 1981.-304с.
- Al-Khattat Ibrahim М. Finite element upsetting analysis of a ring: an incremental solution to the contact problem//Eng. Software III. Proc. 3rd Int. Conf. London Berlin. — 1983. — p.952−964.
- Bathe K.J., Chaudhary A. On finiteelement analysis of large deformation frictional contact problems//Unific. Finite Element Method. Amsterdam, 1984. -p.123−147.
- Калмыков B.B., Чумаченко E.H., Ананьев И. Н. Способ задания граничных условий при решении задач обработки давлением//Изв. вузов. Машиностроение. 1985. — № 12. — с. 122−125.
- Ильюшин A.A. Пластичность. Москва.: Гостехиздат, 1948. — 376с.
- Ленский B.C. Введение в теорию пластичности. М.: МГУ, 1969. -92с.
- Чумаченко E.H., Скрылев И. В., Логашина И. В. Модельное исследование изотермической штамповки кольцевых заготовок//КШП. 1991. -№ 10. — с.7−10.
- Чумаченко E.H., Ефимов В. Н., Соколов JI.H. и др. Моделирование и экспериментальная проверка изотермической осесимметричной штамповки легких сплавов//Сообщение АН Груз. ССР. 1987. — № 3. — с.609−612.
- Чумаченко E.H., Ефимов В. Н., Соколов JI.H. и др. Исследование осадки цилиндра из сплава АМгб с применением МКЭ//Изв. вузов. Черная металлургия. 1987. — № 3. — с.78−82.
- Корноухов А.К. Исследование реологических моделей применяемых при моделировании ОМД на примере осадки цилиндра. М. — 1993. -11с. — Деп. в ВИНИТИ, N3059-B93.
- Белянинов В.К., Ананьев И. Н., Чумаченко E.H. Объемные задачи теории и технологии обработки металлов давлением//Тезисы ВС «Вопросы пластичности в современной технологии». М.: МГУ. — 1985. — с.25−26.
- Скрылев В.И., Чумаченко E.H., Графов Б. Г. Разработка технологического процесса штамповки крупногабаритной детали «фланец» //КШП. -1992. -№ 1.-С.6−9.
- Чумаченко E.H., Семянистый A.B., Грунин H.H. Автоматизированное проектирование технологических процессов изотермической штамповки на базе программного комплекса SPLEN//KIIin 1993. — № 2. — с.13−15.
- Чумаченко E.H., Плохих Г. П., Бирюлин С. И. Автоматизированные системы разработки технологий штамповки подшипниковых колец и «башенных» поковок//КШП. 1998. — № 3. — с.10−12.
- Чумаченко E.H., Рогалевич Л. Э., Свешников М. В., Чумаченко С. Е. Моделирование и расчет течения металла при штамповке на КГШП с использованием вычислительного комплекса SPLEN-S//KIlin. 2000. -№ 4. — с.37−42.
- Сопротивление пластической деформации металлов и сплавов. Справочник. 2-е изд., перераб. и доп./П.И. Полухин, Г. Я. Гун, A.M. Галкин.- М.: Металлургия, 1983. З52.с.
- Марочник сталей и сплавов/В.Г. Сорокин, A.B. Волосникова, С.А. Вят-кин и др.- Под ред. В. Г. Сорокина. М.: Машиностроение, 1989. — 639с.
- Изсшшй FSTBTjft 1МТ|№Ш№Гв -?^--.0G7p0im32. P 8- ?№&t.1. Вколвшьй ?1 .1. Дело .од m is'1. Л**-,