Эпоксидные смолы: получение и применение
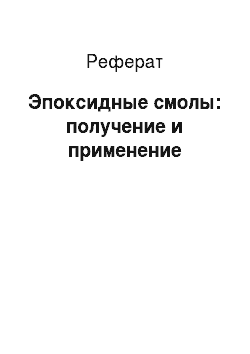
После смешения эпоксидной смолы с пластификатором в неё добавляют отвердитель. Иногда имеет смысл немного охладить эпоксидную смолу (до 30°С), чтобы уменьшить риск «закипания» смолы. Стандартное соотношение эпоксидная смола/отвердитель — 1:10. В некоторых специфических технологических процессах соотношение может сильно отличаться от общепринятого — быть от 1:5 до 1:20, но в подавляющем… Читать ещё >
Эпоксидные смолы: получение и применение (реферат, курсовая, диплом, контрольная)
Министерство Образования и Науки РТ Казанский Государственный Технологический Университет Кафедра химической технологии переработки нефти и газа.
Реферат
на тему:
Эпоксидные смолы: получение и применение
Выполнил: студент группы 419 142.
Хисмиев Ришат Ринатович Проверил:
ассистент Терентьева Наталья Александровна Казань 2011 г.
I.
Введение
.
II. Получение.
III. Применение.
IV.
Заключение
.
V.
Литература
.
I.
Введение
Эпоксидные смолы: вчера, сегодня, завтра.
к.т.н. А. Д. Еселев, ООО «Фирма ФЕАС»;
к.х.н. В. А. Бобылев, ЗАО «ХИМЭКС Лимитед».
«Лакокрасочная промышленность» № 9 2009 год.
Слово «эпоксид» образовано от двух греческих корней: «epi» — «над» и «оху» — «кислый». История возникновения и широкого развития эпоксидных соединений восходит к началу прошлого столетия, когда в 1908 г. известным русским химиком Н. А. Прилежаевым была открыта реакция окисления алкенов надкислотами с образованием эпоксидных соединений, получившая его имя. В середине 1930х гг. немецкий химик П. Шлак запатентовал способ получения высокомолекулярных полиаминов, образующихся при взаимодействии аминов с эпоксидными соединениями, содержащими в молекуле более одной эпоксидной группы. В 1936 г. швейцарский учёный П. Кастан путем взаимодействия бисфенола, А с эпихлоргидрином синтезировал низковязкую смолу янтарного цвета, которая при взаимодействии с фталевым ангидридом переходила в неплавкое и нерастворимое состояние. Он предложил применять такие смолы в производстве зубных протезов и некоторых литых изделий. Сделанное открытие позднее было запатентовано известной фирмой Ciba.
В 1939 г. американский химик С. Гринли, сотрудничая с фирмой DevoeReynolds, синтезировал ряд аналогичных смол, рекомендованных для получения защитных покрытий. Это направление оказалось весьма перспективным. Однако первый успешный промышленный выпуск таких смол состоялся лишь в 1947 г. В дальнейшем в течение 10 лет объём их производства составил более 13,6 тыс. т, а в последующие шесть лет увеличился ещё в 3 раза.
В конце 1950х гг. были синтезированы новые эпоксидные смолы (ЭС), отличающиеся от вышеописанных и получившие название эпоксиднодиановых (или диановых ЭС). В конце 1960х гг. промышленностью было освоено производство не менее 25 типов этих смол. В то время термин «эпоксидные смолы» стал общим, и сейчас он относится к целому классу материалов: в первую очередь — к глицидиловым эфирам различных соединений, содержащих в молекуле активный атом водорода (фенолы, спирты, амины, фенольные и другие смолы), а также к продуктам непосредственного бэпоксидирования ненасыщенных соединений (растительные масла, циклоалифатические соединения, содержащие двойные связи) надкислотами.
Следующие 30 лет характеризовались бурным ростом производства ЭС. К началу 1990х гг. их потребление в странах Западной Европы составляло около 200 тыс. т/год, в США—примерно 180 тыс. т, в Японии — около 150 тыс. т, причем 2/3 мирового производства приходилось на два крупнейших международных концерна — Dow Chemical (США) и Shell (Великобритания).
Благодаря комплексу ценных свойств эпоксидных покрытий? превосходной адгезии к большинству конструкционных материалов (металлам, бетону, стеклу, камню и др.) в сочетании с хорошими физикомеханическими свойствами, минимальной усадке в процессе отверждения, отсутствию в их составе легко омыляемых групп, что обеспечивает низкий уровень внутренних напряжений, основной областью применения ЭС являются защитные покрытия (см. рисунок).
В нашей стране первые промышленные эпоксиднодиановые смолы марок ЭД5 и ЭД6 были разработаны в середине 1950х гг. Л. Н. Смирновой и Е. С. Потехиной в НИИПМ и внедрены в производство на Ленинградском Охтинском химкомбинате. Параллельно в те же годы в ГИПИ ЛКП под руководством Н. А. Суворовской был создан ассортимент смол для лакокрасочной промышленности: базовая низкомолекулярная смола Э40 и на её основе? твёрдые смолы марок Э41, Э44 и Э49, производство которых было освоено на ярославском заводе «Свободный труд». В этом же институте под руководством А. А. Благонравовой впервые в мировой практике была разработана одностадийная технология получения среднемолекулярных ЭС воднодисперсионным способом.
Период с начала 1960х гг. до 1985 г. был временем расцвета научно-исследовательских и производственных работ в области ЭС и материалов на их основе, что в значительной степени явилось составной частью и результатом программы ускоренной химизации народного хозяйства в СССР. Благоприятная ситуация для развития производства эпоксидных ЛКМ была продиктована в первую очередь необходимостью их использования в изделиях так называемого «спецназначения». В те годы были построены и введены в эксплуатацию крупные по тем временам мощности по производству ЭС в Дзержинске, Сумгаите, Котовске, Уфе и Ленинграде, а также цеха по производству сырьёвых компонентов для ЭС — бисфенола, А (в Уфе) и эпихлоргидрина (в УсольеСибирском). В результате в 1985 г. отечественная промышленность выпускала около 55 тыс. т ЭС, что составляло примерно 10—12% их мирового выпуска. В середине 1970х гг. решением правительства разработки в области ЭС и материалов на их основе, а также координация всех исследовательских работ в данном направлении в стране были поручены УкрНИИПМ (Донецк).
Структура общего объёма потребления эпоксидных смол, %: 1 — автомобильная промышленность, судостроение, окраска консервной тары и аэрозольных упаковок, порошковые краски, химическая и нефтехимическая промышленность — 45; 2 — промышленное и гражданское строительство — 20; 3 — электротехническая промышленность — 12; 4 — электроника и композитные материалы — 15; 5 — другие отрасли — 8.
эпоксидная смола полимеризация отверждение Работы в области эпоксидных ЛКМ, оставшиеся в компетенции ГИПИ ЛКП как головного института лакокрасочной отрасли, проводились в двух основных направлениях. Первое из них предусматривало создание современной технологии производства лаковых ЭС, позволяющей обеспечить их изготовление в крупных промышленных масштабах и улучшить качество выпускаемой продукции, которая бы удовлетворяла потребности важнейших отраслей промышленности. Основное внимание уделялось разработке одностадийной технологии синтеза лаковых средне и высокомолекулярных ЭС методом гетерофазной поликонденсации в водноорганической среде. Этот способ производства осваивался на Котовском лакокрасочном заводе (ЛКЗ). Разработанная технология позволила осуществить синтез некоторых марок лаковых ЭС в ЛНПО «Пигмент» в аппаратах крупной единичной мощности (32 м3).
Другим важнейшим направлением научно-исследовательских работ явилось создание рецептур ЛКМ для таких отраслей, как пищевая (консервные лаки), газовая и нефтяная (порошковые краски), автомобильная промышленность (электрофорезные и эпоксиэфирные грунтовки), покрытия специального назначения и др. Из перечисленных выше материалов стоит выделить эпоксиднофенольные лаки и эмали для защиты консервной тары и аэрозольных упаковок, важное народнохозяйственное значение которых сохраняется и в наши дни. С начала 1970х гг. особое внимание уделялось развитию таких прогрессивных направлений, как порошковые краски (эпоксидные и эпоксиднополиэфирные), эпоксидные ЛКМ с высоким сухим остатком, водоразбавляемые грунтовки и краски.
История возникновения и развития ЭС будет неполной, если не коснуться другого важнейшего компонента эпоксидных композиций — отвердителей. Общеизвестно, что большинство материалов на основе ЭС выпускается и находит применение в виде двухупаковочных композиций с отвердителями, чаще всего аминного типа.
Отвердители в нашей стране создавались одновременно с разработкой ЭС. Так, в НИИПМ в конце 1950х гг. были предложены в качестве отвердителей полиэтиленполиамины, производство которых появилось на Нижне-Тагильском заводе пластмасс. В ГИПИ ЛКП предложили использовать для этой цели 50%ный раствор гексаметилендиамина (ГМДА) в этиловом спирте, названный «отвердитель № 1». Производство этого продукта было обеспечено сырьём, так как ГМДА — компонент производства полиамидных волокон. Отвердитель № 1 придаёт покрытиям в отличие от полиэтиленполиамина более высокие блеск и эластичность. В начале 1960х гг. был разработан первый аминоаддукт на основе смолы Э40 и ГМДА, выпускаемый под маркой АЭ4.
Несколько позже, практически одновременно в НИИПМ и ГИПИ ЛКП, начались разработки низкомолекулярных полиамидов (впоследствии их стали называть олигоаминоамидами, а на западе — версамидами). В середине 1960х гг. было организовано небольшое промышленное производство этих продуктов в Северодонецке (марки Л18, Л19, Л20) и в Ленинграде на Объединении «Лакокраска» (марки ПО200, ПО300 и имидазолиновые производные И5М, И6М). В те же годы в ЦЗЛ Охтинского завода были разработаны и выпускались в малотоннажном производстве аминофенольный отвердитель АФ2 и аминоакриловый ДТБ2.
В начале 1970х гг. в УкрНИИПМ была организована специальная лаборатория отвердителей под руководством Л. Я. Мошинского, где была разработана серия отвердителей типа модифицированных алифатических аминов, ароматических аминов, ангидридов кислот, ускорителей отверждения и др. Производство этих продуктов было освоено на Киевском заводе реактивов «РИАП» и ПО «Каустик».
На стерлитамакском химзаводе (позднее ПО «Каустик») было создано производство отдельных фракций ди и полиаминов (ЭДА, ДЭТА, ТЭТА) и их смесей, используемых в качестве сырья для производства модифицированных отвердителей. Т. о., в 1950—1990е гг. в СССР были разработаны и освоены в производстве важнейшие типы ЭС и материалов на их основе, причем СССР занимал достойное место как по объёму выпуска этих продуктов, так и по уровню научно-исследовательских работ в данной области.
В результате существенного перераспределения рынка потребления ЭС, значительное место на котором стали занимать Китай и страны Юго-Восточной Азии, резко возрос выпуск смол в азиатских странах. Фирмы Nan Ya (Тайвань) и KUKDO (Южная Корея), значительно увеличив выпуск ЭС и отвердителей, заняли твёрдые позиции в ряду крупнейших мировых производителей этих материалов. Производство ЭС мощностью 80 тыс. т/год имеется в Таиланде. Значительный интерес к изготовлению и потреблению ЭС проявляет КНР, заявившая о своем желании довести потребление ЭС к 2010 г. до 1 млн. т. Появляются сведения о новых производствах ЭС в восточноевропейских странах. Так, фирма Spolchemie (Чешская Республика) объявила недавно об удвоении мощности по их производству на заводе в Устинад-Лабой и доведении её до 60 тыс. т/год. Все эти факты свидетельствуют о возрастающем интересе к этому классу полимерных связующих.
В нашей стране производство и потребление эпоксидных связующих также претерпело определённые изменения. С сожалением приходится констатировать, что в настоящее время Россия полностью утратила ранее завоёванные позиции на рынке этих материалов. Достаточно сказать, что за все годы, прошедшие с распада СССР, в стране не появилось ни одной (!) выпускаемой в крупном промышленном масштабе новой марки ЭС. Не выдержав конкуренции с зарубежными изготовителями и в силу ряда других причин прекратили свою работу крупные производства ЭС в С. Петербурге на НПО «Пластполимер», в Уфе на предприятии «Химпром», в Ярославле на ЯПО «Лакокраска». В период кризиса максимально сокращён объём выпуска лаковых ЭС на Котовском ЛКЗ. В отдельных случаях смолы марок ЭД20, ЭД16 и Э40 производятся на ОАО «Пигмент» (С.Петербург) и на предприятии «Усольехимпром», входящем в ООО «Группа НИТОЛ». Лишь Дзержинский завод им. Я. М. Свердлова за последние годы сохранил свои позиции на рынке ЭС, однако масштаб производства и ассортимент продукции совершенно недостаточны для обеспечения потребности многих отраслей.
Вопрос об организации в России нового производства ЭС на современном научно-техническом уровне крайне актуален, так как многочисленные потребители вынуждены применять зарубежные аналоги отечественных смол, благо в предложениях нет недостатка. Однако новое производство будет эффективным и конкурентоспособным только при годовой мощности предприятия не менее 30 тыс. т. Таких условий в настоящее время нет, как нет и научно-технической базы для его создания. Многие крупные российские фирмы — потребители ЭС предпочитают закупать сырьё непосредственно у производителя, что затрудняет определение объёмов импорта ЭС. По ориентировочным данным, Россия ежегодно приобретает по импорту 25—30 тыс. т ЭС, преимущественно у наиболее известных производителей.
Используемые в лакокрасочной промышленности ЭС по физико-химическим показателям и областям применения могут быть разделены на несколько групп. При этом надо иметь в виду, что наиболее популярные отечественные смолы (ЭД20, Э40 и др.) практически не имеют точных зарубежных аналогов, поэтому при их эквивалентной замене в составе ЛКМ в большинстве случаев требуются проведение сравнительных испытаний и корректировка рецептур.
Основные современные тенденции производства ЭС рассмотрим на примере корейской фирмы KUKDO. Главная тенденция — приведение в соответствие показателей качества отдельных марок требованиям индивидуальных потребителей и отраслей. В ассортименте KUKDO насчитывается более 310 марок продукции. Так, жидких низкомолекулярных эпоксиднодиановых смол (с молекулярной массой 340—670), различающихся значениями эпоксиэквивалентной массы, вязкости, содержанием омыляемого хлора и цветовыми характеристиками, выпускается 27 марок. Специально для порошковых ЛКМ в каталоге фирмы значатся 18 марок ЭС, отличающихся показателями качества и способом производства. Другой тенденцией является использование для синтеза ЭС не только бисфенола А, но и его производных, в частности, бисфенола F, бисфенола Н, бромированного бисфенола А, а также фенолформальдегидных смол. Это позволяет придавать получаемым полимерам определённые специфические свойства. Наконец, в качестве третьей тенденции можно отметить выпуск модифицированных ЭС: с активными разбавителями, три и тетрафункциональных эластифицированных димерной кислотой или каучуками, специальных? для отверждения УФизлучением, изоцианатами, при низких температурах, водоразбавляемых и др. Фирма «ХИМЭКС Лимитед», являющаяся дистрибьютором фирмы KUKDO, может не только предоставить потребителям образцы для испытаний, но и разработать состав связующего, позволяющий решать сложные технические задачи конкретных заказчиков.
В заключение хотелось бы кратко остановиться на проблеме дальнейшего развития производства и потребления ЭС в нашей стране. Прежде всего, следует отметить, что причины столь резкого снижения объёмов их производства, особенно в последние годы, вполне типичны для многих промышленных производств. После распада СССР ряд цехов, выпускающих ЭС в Азербайджане, Украине, Эстонии, оказался за пределами РФ. Значительно снизилась потребность в ЭС в оборонной и машиностроительной отраслях.
Прекратили работу лаборатории в УкрНИИПМ и НПО «Спектр ЛК» (бывший ГИПИ ЛКП), занимающиеся синтезом ЭС. Кроме того, в стране отсутствует техническая политика в данной области. Поэтому большая часть используемых смол приобретается по импорту. Нельзя не отметить, что закупаемая продукция в основном представляет собой традиционные базовые смолы, а не новые продукты современного качества. Как отмечалось выше, большинство отечественных специалистов не представляют или не учитывают реальное состояние промышленности в данной области. Ничем иным нельзя объяснить доминирующее положение смолы ЭД20 в большинстве научно-исследовательских разработок.
В то же время складывающаяся сейчас экономическая и политическая ситуация диктует решительное изменение подхода к деятельности российских производителей ЭС. Нельзя допустить практически полного прекращения выпуска продукции немногими оставшимися заводами, в частности Котовским ЛКЗ. В противном случае отечественная промышленность рискует оказаться в кабальной зависимости от зарубежных компаний.
II. Получение.
1. Эта стадия по праву относится к типу реакций ступенчатой полимеризации. Сначала делают форполимер с использованием бисфенола, А и эпихлоргидрина. Реакция примерно такова:
И как же протекает эта реакция? Первое, что происходит это то, что NaOH обменивается с бисфенолом А, при этом получается натриевая соль бисфенола:
Соль, как вы заметили, содержит кислород с тремя парами электронов, которые он ни с кем не делит. Этот конкретный атом кислорода очень щедр и готов поделиться этими электронами с атомом, которому повезло меньше. Поэтому он находит атом углерода на соседнем эпихлоргидрине, которому могли бы пригодиться электроны. Этот атом углерода тот, что находится рядом с атомом хлора. Предполагается, что атом хлора должен делить пару электронов с этим атомом углерода, но поскольку хлор является сильно электроотрицательным, он склонен к сохранению этой пары.
Поэтому кислород, будучи атомом добрым, дарит пару своих электронов углероду. Конечно, углерод может одновременно делить только четыре пары электронов, поэтому одна пара должна уйти от него, если он хочет взять ту пару у кислорода. Поэтому он отпускает те электроны, которые он делил с хлором, и посылает атом хлора идти своей дорогой, выталкивая его из молекулы.
В результате мы получаем молекулу, похожую на бисфенол А, только с присоединённой к ней эпоксидной группой. К тому же мы получаем NaCl. И что же происходит дальше? Могут происходить разные вещи. Как вы помните, эти форполимеры могут обладать разной молекулярной массой. Иногда степень полимеризации достигает 25. Иногда молекулы форполимера могут быть и маленькими, например, вот такими:
Будет молекула форполимера большой или маленькой, зависит от соотношения количества эпихлоргидрина и бисфенола в реагирующей смеси. Предположим, что cоотношение их таково, что на одну молекулу бисфенола, А приходится две молекулы эпихлоргидрина. Давайте посмотрим, что произойдёт с молекулой, которую мы только что сделали при этом соотношении:
А произойдёт то, что мы получим присоединённую эпоксидную группу также и с другой стороны. Тогда реакция останавливается, поскольку не осталось групп соли бисфенола А, которые могли бы провзаимодействовать.
А что, если на каждую молекулу бисфенола, А приходится менее двух молекул эпихлоргидрина? Тогда не все молекулы соли бисфенола, А могут провзаимодействовать с эпихлоргидрином. Предположим, что соотношение теперь таково, что на каждые три молекулы эпихлоргидрина приходится две молекулы бисфенола А. Когда все молекулы эпихлоргидрина провзаимодействуют, у нас останется смесь с отношением вот таких двух молекул 50 :50.
Эти две молекулы могут прореагировать и вместе образовать такую молукулу:
А теперь у нас остался димер, который? так уж получилось? является натриевой солью. Обратите особое внимание на отрицательный заряд на атоме кислорода. Когда рядом оказывается молекула воды (а как вы помните, когда мы делали натриевую соль бисфенола А, у нас получилась заодно целая куча молекул воды) пара электронов атома кислорода атакует один из атомов водорода в молекуле воды и украдёт его у воды.
Теперь кислород образует спиртовую группу, и мы получаем обратно наш NaOH. Чем больше у вас эпихлоргидрина по сравнению с количеством соли бисфенола А, тем большего размера олигомер вы получаете.
2. Отверждение диэпоксида при помощи диамина Когда вы получили диэпоксидные форполимеры, вы должны все их связать вместе. Мы можем это сделать, добавив диамин. Диамин делает нечто интересное, когда он видит все эти эпоксидные группы на концах форполимера. Одинокие пары электронов в группе амина будут смотреть на эти эпоксидные группы и увидят, что эпоксидный атом кислорода, будучи электроотрицательным, утягивает все электроны у соседнего с ним атома углерода. Итак, аминные группы смотрят на эти атомы углерода и видят, что они могут легко отдать свои электроны атому углерода на конце молекулы.
Когда они сделали это, углерод отдаёт те две пары, которые он неравноправно делил с кислородом. Связь между атомами углерода и кислорода разрывается и образуется новая связь между атомом углерода и азотом в аминной группе. У нас остаётся отрицательный заряд на атоме кислорода и положительный на атоме азота.
А теперь давайте посмотрим на этот атом кислорода. У него уже есть три пары электронов, которые он не делит ни с каким другим атомом. Поэтому один из этих электронов, не задействованных в связях, смотрит, нет ли кругом чегонибудь, с чем можно было бы связаться, и он обнаруживает атом водорода, присоединённый к положительному атому азота. Поэтому те электроны и атакуют этот атом водорода.
Когда они нападают, они образуют связь с атомом водорода, и атом водорода отделяется от атома азота, оставляя при этом за собой электроны. Это нейтрализует положительный заряд, оставляя азот нейтральным. И, конечно же, атом кислорода теперь тоже нейтрален, поскольку он присоединил протон, и теперь он образует спиртовую группу.
На аминной группе еще остался один атом водорода, и он может провзаимодействовать с ещё одной эпоксидной группой точно таким же образом. Сколько атомов водорода есть у аминной группы, с таким количеством эпоксидных групп она и может прореагировать. Вот что мы, в конце концов, получаем:
Как вы помните, мы используем диамин, поэтому аминная группа на другом конце молекулы диамина также может провзаимодействовать ещё с двумя эпоксидными группами. Поэтому, в конце концов, мы получаем четыре эпоксидных форполимера, связанных с одной молекулой диамина.
Как вы помните, другие концы диэпоксидных форполимеров присоединены к другим молекулам диамина. Таким образом, все молекулы диамина и все диэпоксидные молекулы связываются между собой в одну большую молекулу с сетчатой структурой. Эта структура выглядит примерно так:
III. Применение.
1. Наиболее часто эпоксидные смолы применяются в качестве эпоксидного клея, пропиточного материала вместе со стеклотканью для изготовления и ремонта различных корпусов (лодки, элементы кузова автомобиля и др.) или выполнения гидроизоляции помещений (пол и стены подвальных помещений, бассейны), а также как самый доступный способ в домашних условиях изготовить изделие из стеклопластика, как сразу готовое после отливки в форму, так и с возможностью последующей обработки резанием и шлифовки.
Использование эпоксидной смолы в качестве эпоксидного клея наиболее простое. Смешение эпоксидной смолы с отвердителем в этом случае как правило выполняется в крайне небольших объёмах (несколько граммов), поэтому перемешивание производится при комнатной температуре и не вызывает затруднений, а точность пропорции эпоксидная смола/отвердитель не столь важна (стандартная пропорция — 1:10, допустима приличная передозировка отвердителя, вплоть до 1:5).
Совсем другое дело, когда необходимо приготовить для работы большой объём эпоксидной смолы с отвердителем, хотя бы несколько килограммов. Эта операция сильно отличается от приготовления нескольких граммов эпоксидного клея. Ещё более сложным делом является изготовление достаточно массивного изделия из эпоксидной смолы (т.е. фактически изготовление стеклопластика), которое должно быть, например, достаточно прозрачным, чистым, не содержать пузырей воздуха, равномерно отвердеть в толще и по поверхности.
Реакция эпоксидной смолы с отвердителем необратима. Для успешного перемешивания смолы с пластификатором и отвердителем, эпоксидную смолу желательно нагреть до температуры выше комнатной, чтобы она стала менее вязкой. Для эпоксидной смолы, которая может кристаллизоваться при хранении, необходимо убедиться, что она прозрачная, не мутная, в противном случае нагреванием до 4050 °C и интенсивным перемешиванием вернуть её в прозрачное состояние.
Для нагревания эпоксидной смолы удобно использовать «водяную баню» — опустить ёмкость с эпоксидной смолой в воду температурой 5060 °C, помешивать для равномерного нагревания. Внимание! Избегайте попадания воды в эпоксидную смолу, и нагрева эпоксидной смолы до температуры выше 60 °C. В случае перегрева возможно «закипание» эпоксидной смолы смола станет матовобелой, покроется пеной — такая эпоксидная смола непригодна к использованию.
Сначала в эпоксидную смолу добавляют пластификатор, смолу с ДБФ необходимо «варить» (медленно нагревать), при использовании ДЭГ1? просто тщательно перемешать. Для перемешивания удобно использовать строительный миксернасадку на дрель. Соотношение эпоксидная смола/пластификатор может быть различным в зависимости от требуемого пластического эффекта, но обычно добавляется 510% пластификатора.
После смешения эпоксидной смолы с пластификатором в неё добавляют отвердитель. Иногда имеет смысл немного охладить эпоксидную смолу (до 30°С), чтобы уменьшить риск «закипания» смолы. Стандартное соотношение эпоксидная смола/отвердитель — 1:10. В некоторых специфических технологических процессах соотношение может сильно отличаться от общепринятого — быть от 1:5 до 1:20, но в подавляющем большинстве случаев используется соотношение, близкое к стандартному. Отвердитель необходимо лить в эпоксидную смолу, очень медленно, постоянно перемешивая. Сильная передозировка отвердителя даже временно в части ёмкости может привести к «закипанию» эпоксидной смолы (смола станет матово-белой, покроется пеной), в этом случае вся эпоксидная смола будет испорчена. Необходимо иметь в виду, что процесс смешивания эпоксидной смолы с отвердителем экзотермический (выделяется тепло), смола будет нагреваться. Иногда в процессе добавления отвердителя или сразу по окончании смешивания возникает лавинообразный процесс — эпоксидная смола очень быстро нагревается, практически моментально «встаёт» (затвердевает). Точная причина этого неизвестна, вероятно, это связано с передозировкой отвердителя и слишком высокой исходной температурой смолы. Жизнеспособность смеси эпоксидной смолы с отвердителем обычно 30 минут — 1 час (это сильно зависит от температуры смолы, типа отвердителя, его количества; можно добиться большего времени).
По окончании работ изделие рекомендуется сначала отверждать при температуре, немного превышающей комнатную. В течение 23 часов происходит т.н. отверждение «до отлипания» (первичная полимеризация), после чего изделие можно сильно нагреть, что позволит закончить процесс отверждения за 56 часов. При комнатной же температуре полная полимеризация может продлиться несколько суток (до 7 дней, согласно литературе), а при использовании ТЭТА поверхность может остаться липкой.
Заметим, что несколько граммов клея ЭДП прекрасно смешиваются и отверждаются при комнатной температуре, но когда в работе используется большое количество смолы, технология должна быть другая.
Если необходима большая толщина (больше 2 мм), то материал обычно накладывают слоями, дожидаясь первичной полимеризации предыдущего слоя перед нанесением следующего. Процесс несколько усложняется, если необходимо изготовить объёмное изделие из смолы (стеклопластик).
Эпоксидную смолу можно отливать в форму. Для обеспечения возможности отделения готового изделия от формы она смазывается жиром (например, техническим вазелином). Добавляя в смолу порошковый краситель, можно придать изделию любой цвет. Отлитое из эпоксидной смолы изделие можно в дальнейшем подвергать механической обработке (резать, шлифовать).
Для отливки объёмного изделия отечественная эпоксидная смола малопригодна, т.к. из-за неравномерности свойств изделие может неравномерно отвердиться в толще.
2. Достаточно часто эпоксидные смолы применяют для ремонта бетона, железобетонных конструкций, фундаментов, а также для их усиления. Например, с помощью эпоксидного полимерраствора произведён ремонт бетонных бордюров на существующих мостах, а также увеличение их высоты.
2.1 Известно, что от высоты бордюров в значительной мере зависит безопасность движения по мосту, так как они препятствуют выезду автомобилей с проезжей части на тротуары. Обследование показало, что высота бордюров на многих существующих мостах не превышает 15 см, и в случае скопления мусора и грязи, а зимой наледи вдоль бордюра автомобили беспрепятственно выезжают за пределы проезжей части. Имели место и обрушения автомобилей с мостов.
Выполнено увеличение высоты бетонных бордюров до 40 см. Проектом производства работ предусматривалось наращивание их на 25 см монолитным бетоном, для чего требовалось обнажить арматуру плиты проезжей части, установить арматурный каркас, опалубку и т. д. Технологически сложный, многодельный и трудоёмкий метод производства работ был заменён клеевым способом прикрепления готовых бордюрных блоков. Бетонные блоки ограждения длиной 1,5 м были изготовлены из бетона класса В 22,5 (марки М300). Основание блока ограждения тщательно очищалось с помощью металлических щеток от цементной корки и прогрунтовывалось. Затем раскладывался полимерраствор и на него устанавливался блок ограждения. Все работы были выполнены за 5 рабочих смен без ограничения движения транспорта по мосту. Было приклеено 225 м блоков. Несмотря на наличие следов наезда автомобилей на бордюр, за 5 лет эксплуатации моста нарушений в клеевых швах не зафиксировано.
2.2 Полимербетоны и полимеррастворы использованы также для ремонта бетонных опор моста через Свиягу на автотрассе Казань—Ульяновск. Опоры моста имели значительные повреждения: раковины, сколы бетона с обнажением защитной металлической сетки, вызванные ледоходом.
В неглубокие раковины полимерраствор укладывался без опалубки, во всех остальных случаях использована инвентарная металлическая опалубка с резиновыми уплотнителями по краям. Смесь укладывалась через загрузочные воронки. Через 1,5—2 ч после укладки полимерраствора опалубка перемещалась на следующий участок. Ввиду довольно низкой температуры окружающего воздуха (810°С) опалубка предварительно прогревалась. Дефекты большого объёма заделывались обычным цементным мелкозернистым бетоном с промазкой контактной зоны старый — новый бетон эпоксидным составом. Увеличение адгезии нового бетона к старому было необходимо ввиду сложных условий эксплуатации (воздействие воды, мороза) опор.
Восстановление опор с помощью полимерраствора позволило значительно сэкономить опалубочный материал, снизить трудоёмкость, упростить технологию и сократить сроки производства работ. Надёжность защиты опор от повреждений подтвердилась пропуском льда в течение 5 лет.
2.3 Широкое применение сборных железобетонных конструкций в промышленном и жилищно-гражданском строительстве вызвало необходимость выполнения большого количества стыков сборных элементов. Клеевые стыки, как показали многочисленные исследования, характеризуются значительными технико-экономическими достоинствами. Известны также попытки стыкования железобетонных свай, которые по производственным причинам не могли быть изготовлены или погружены в грунт целиком. Модифицированные эпоксидные составы применены для ремонта свай, получивших повреждения при погрузочно-разгрузочных и транспортных работах, а также при забивке (разрушении головы сваи); стыковании обрубков свай для их последующего использования по прямому назначению и наращивания железобетонных свай в процессе забивки. Склеивание свай представляет интерес и как наглядный, жёсткий метод испытания эпоксидного клея в натурных условиях, так как в процессе забивки в грунт клееный стык испытывает значительные динамические нагрузки. Железобетонные сваи имели следующие типы стыков (рис.1): 1, 2 — арматурные; 3, 4 — безарматурные; 5 — со сваркой стыковыми накладками и последующим омоноличиванием эпоксидным составом.
Рисунок 1. Типы клеевых стыков с применением модифицированных эпоксидных полимербетонов и полимеррастворов: 1? основная арматура; 2 — полимерраствор Общая длина клееных свай сечением 0,3×0,3 м, состыкованных из обрубков, составляла 6—7 м, а количество стыков на одной свае — 13. Подготовка обрубков свай к склеиванию заключалась в оголении арматуры на необходимую длину; выравнивании торца (с помощью отбойного молотка) и очистке поверхности от снега, грязи и слабых трещиноватых мест. Подготовленные обрубки подбирались по длине и раскладывались с помощью крана на стеллажах. Арматура соединялась (связывалась или сваривалась), на стык устанавливалась несложная металлическая опалубка. Разделительным слоем служила суспензия воска в бензине. Использованы полимербетоны и эпоксидные составы, частей (по массе): I — эпоксидная смола Э40? 70; фенольная смесь — 30; полиэтиленполиамин — 1020; цемент? 200—400; щебень? 100 200; II? эпоксидная смола ЭД20? 23; фенольная смесь? 23; полиэтиленполиамин? 6; цемент или молотый кварцевый песок — 48. Наибольшая крупность зерен щебня составляла 15 мм. Эпоксидная полимерная смесь готовилась вручную в полиэтиленовой емкости. Сваи склеивались и омоноличивались в горизонтальном положении (за исключением типа II, который был выполнен в вертикальном проектном положении). Отверждение эпоксидной смеси осуществлялось в естественных условиях при температуре наружного воздуха + 1020 °C в состав вводился ускоритель (хлорное железо) в количестве 1—3 ч. по массе на 100 ч. по массе связующего. Такие смеси при температуре наружного воздуха 15 °C набирают прочность 40 МПа. Количество отвердителя варьировалось в зависимости от температуры окружающей среды, а количество наполнителя лимитировалось необходимой удобоукладываемостью смеси.
Клееные сваи погружались в грунт сваебойным копром. Все типы стыков выдержали испытания, связанные с транспортированием и погружением в грунт. Нарушений в клеевых швах не обнаружено. Установлено, что наилучшими техникоэкономическими показателями обладают стыки с ванной сваркой арматуры.
Использование эпоксиднофенольных клеящих составов взамен сварки при наращивании свай в процессе погружения позволило снизить стоимость, трудоёмкость и материалоёмкость. Внедрение клеевого способа наращивания железобетонных свай было проведено на объектах треста «Татгражданстрой». Шестнадцатиметровые сваи состояли из нижней (l = 12 м) и верхней (l = 4 м) частей. На торец нижней части сваи, погружённой в грунт на глубину 11 м, разливалась полимеррастворная смесь, которая заполняла анкерные отверстия и покрывала торец (рис. 2).
Рисунок 2. Полимеррастворы при наращивании железобетонных свай: 1? верхняя часть сваи; 2 — выпуски арматуры диаметром 16 мм; 3? нижняя часть сваи; 4 анкерные отверстия диаметром 35 мм; 5? основная арматура диаметром 16 мм; 6? полимерраствор После установки верхней части и дальнейшем погружении торцы свай соприкасаются и склеиваются. Эпоксидный состав надёжно соединяет бетон и арматуру. Положение верхней сваи фиксировалось на период отверждения смеси с помощью кондуктора. Дальнейшее погружение свай проводилось через сутки после стыкования. Вес ударной части сваебойного копра составлял 3,2 т, высота подъема — 1 м. Осмотр погруженных свай путем откапывания до клеевого стыка показал отсутствие повреждений клеевого шва.
Эпоксидные композиции применяют для соединения железобетонных колонн, элементов сборных куполов, балок и др. При этом для круглогодичного производства строительных работ созданы композиции, отверждающиеся при отрицательных температурах до 20 °C и ниже. С этой целью в эпоксидное связующее вводят ускоритель: хлорное железо или солянокислый анилин в сочетании с фуриловым спиртом или изготавливают клеи в виде плёнокпрокладок, способных склеивать и отверждаться при прогреве.
2.4 Ремонт фундамента включает в себя замоноличивание пустот, каверн и трещин. Для ремонта бетонных фундаментов под технологическим оборудованием на участке ёмкостного парка производства фенола и ацетона в Казанском производственном объединении «Органический синтез» был применён эпоксиднофенольный пенопласт с повышенной плотностью, обеспечивающий высокую прочность и малое водопоглощение.
Возможность регулирования в широких пределах прочностных показателей, простота получения эпоксиднофенольных пенопластов (ЭФП) создали предпосылки для их применения в качестве эффективных расширяющихся композиций для замоноличивания трещин, заполнения пустот в бетонных и железобетонных конструкциях. Вспенивание композиции заливочного эпоксиднофенольного пеннопласта позволяет при сохранении требуемых свойств (достаточная прочность и небольшое водопоглощение) повысить качество выполнения работ, поскольку вспенивание композиции пенопласта непосредственно в трещинах и пустотах обеспечивает их наилучшее заполнение и наименьшую проницаемость конструкции.
Для заливки была использована композиция эпоксиднофенольного пенопласта следующего состава, частей по массе:
Эпоксидная смола ЭД16 100.
Фенольная смесь (смола) 50.
Поверхностноактивное вещество ОП10 3.
Кремнийорганическая жидкость ГКЖ94 1.
Полиэтиленполиамин 15.
Заливочный эпоксиднофенольный пенопласт вышеуказанного состава в отверждённом состоянии имеет следующие показатели:
Плотность пенопласта, кг/м3 630 650.
Прочность при сжатии, МПа 29,530.
Водопоглощение за 24 ч, % по объёму 0,3 0,35.
Заливка композиций пенопласта осуществлялась шприцеванием. Подготовка поверхности бетона ремонтируемых участков под заливку состояла в удалении слабых трещиноватых мест и обезжиривании их ацетоном. Для предотвращения вытекания заливочной смеси на вертикальных поверхностях устраивалась несложная опалубка.
Как показал опыт, заливочная композиция эпоксиднофенольного пенопласта после отверждения обеспечивает восстановление монолитности конструкции и полное заполнение всех пустот и трещин фундамента. Ремонт фундамента проходил без прекращения эксплуатации ёмкостей.
2.5 В настоящее время железобетонные конструкции очень широко применяются в гражданском и промышленном строительстве. С течением времени возникает вопрос о ремонте и усилении железобетонных конструкций. Оздоровление и ремонт мостов играет важную роль для обеспечения бесперебойного движения автотранспорта без ограничения скорости и массы. Эксплуатационным службам приходится выполнять большой объём работ: ремонт и смену гидроизоляции, заделку сколов и раковин, затирку трещин, инъекцию цементного раствора и т. д., а в некоторых случаях (при недостаточной несущей способности) и усиление железобетонных конструкций. Так, ряд мостов, построенных в 19 001 912 гг., не имеет гидроизоляции и водоотводных устройств, в результате чего вода с проезжей части стекает по фасадным поверхностям главных балок, смачивая их. При обследовании железобетонного моста на дороге Казань — Пермь, построенного в 1912 г., было установлено, что толщина слоя коррозии арматуры главных балок достигала 45 мм и вызвала ослабление площади сечения рабочей арматуры до 2025%. Коррозия сопровождалась разрушением бетона по нижним поясам балок и образованием продольных трещин раскрытием до 2 мм. Поверочный расчёт с целью определения грузоподъёмности моста выявил, что несущая способность главных балок недостаточна для восприятия современных нормативных нагрузок и мост нуждается в усилении.
Традиционные методы усиления железобетонных конструкций предполагают увеличение площади рабочей арматуры путём установки дополнительной арматуры и омоноличивания её бетоном. Такая технология требует длительного времени твердения (1014 сут.), что вызывает закрытие движения по мосту, устройство временных объездов. Кроме того, не всегда удаётся получить надёжное сцепление нового бетона со старым, вследствие чего приходится отказываться от усиления и заменять дефектные балки.
Этих недостатков лишён способ усиления железобетонных конструкций, при котором дополнительная арматура объединяется с существующей арматурой и бетоном балок с помощью полимеррастворов на основе эпоксидных и модифицированных эпоксидных связующих. Обладая высокой плотностью и клеящей способностью к стали и бетону, полимеррастворы обеспечивают необходимую стойкость и долговечность конструкций, а значительная прочность в раннем возрасте позволяет быстро вводить в эксплуатацию ремонтируемое сооружение.
В соответствие с проверочным расчётом определена площадь необходимой дополнительной арматуры (листовая сталь толщиной 1015 мм), которая устанавливалась в сечении главной балки в соответствии с эпюрой изгибающих моментов.
Работы по приклеиванию дополнительной арматуры с помощью полимеррастворов проводили в два этапа: сначала? в надопорных сечениях ригелей, а затем? и пролёте по низу. В надопорных сечениях прикрывали проезжую часть до верха плиты. Поверхность бетона тщательно очищали механическим способом, промывали водой и просушивали. Затем на поверхность бетона наносилась грунтовка и сразу же по ней? полимерраствор. На последний накладывался металлический лист, очищенный и огрунтованный эпоксидным составом. Для обеспечения плотного контакта металлического листа и поверхности бетона лист пригружали сверху песчаногравийной смесью толщиной 0,4 м, которая одновременно выполняла функции основания для асфальтобетонного покрытия.
Рисунок 1. Схема усиления ригеля: 1? главная балка; 2? полимерраствор; 3? металлический лист В пролёте по низу ригелей удалялся слабый, разрушенный бетон, а оголённая арматура тщательно очищалась от ржавчины металлическими щётками и раствором соляной кислоты (рис. 1). К рабочей арматуре балок через 0,40,5 м по длине приваривали металлические коротыши с резьбой и гайками на концах, куда подвешивались металлические листы с бортиками высотой 50 мм для предотвращения вытекания полимеррастворной смеси. На металлический лист через загрузочные воронки подавали полимеррастворную смесь. После окончания укладки последней металлический лист плотно прижимался к нижнему поясу балки посредством двух 5тонных гидравлических домкратов, и его положение фиксировалось с помощью гаек. Для заделки сколов бетона и клеевого шва использован жёсткий состав полимербетона.
Жизнеспособность модифицированных составов при температуре производства работ 2025 °C составляла 1,6 ч. Все работы были проведены за 7 рабочих смен, при этом движение автотранспорта по мосту не прекращалось, а регулировалось путём переноса на одну из половин проезжей части моста. Эффективность усиления железобетонных конструкций моста была проверена статической нагрузкой через 2 недели и 1 год после окончания работ. Максимальный прогиб от испытательной нагрузки составил 0,8 мм, что на 0,16 мм меньше прогиба до усиления. Трещин и нарушений в клеевом шве не обнаружено. После усиления железобетонных конструкций жёсткость и несущая способность главных балок выросла за счёт включения в работу дополнительной арматуры усиления. Наблюдение за мостом в течение 6 лет показало, что нарушения сцепления полимерраствора с металлом и бетоном не имеют места.
V.
Заключение
Эпоксидные смолы являются важным и широко распространённым материалом в современном мире. Благодаря комплексу ценных свойств эпоксидных покрытий? превосходной адгезии к большинству конструкционных материалов (металлам, бетону, стеклу, камню и др.) в сочетании с хорошими физико-механическими свойствами, минимальной усадке в процессе отверждения, отсутствию в их составе легко омыляемых групп, что обеспечивает низкий уровень внутренних напряжений, основной областью применения ЭС являются защитные покрытия. Широкое применение они нашли и в качестве клея, поскольку обеспечивают очень высокую прочность, надёжность, влаго и термоустойчивость, просты в приготовлении и применении, доступны по цене. Эти же свойства обусловили их применение в строительноремонтных работах. Как видно из приведённых примеров, довольно часто ремонтные работы во избежание больших затрат материалов и времени, а также остановки производства или движения транспорта проводились с использованием эпоксидных смол.
С сожалением приходится констатировать, что в настоящее время Россия полностью утратила ранее завоёванные позиции на рынке этих материалов. Достаточно сказать, что за все годы, прошедшие с распада СССР, в стране не появилось ни одной (!) выпускаемой в крупном промышленном масштабе новой марки ЭС. Не выдержав конкуренции с зарубежными изготовителями и в силу ряда других причин прекратили свою работу крупные производства, ранее обеспечивавшие весь СССР. Необходимо как можно скорее восстанавливать их работу, т. к. эпоксидным смолам находят всё новое и новое применение, да и традиционное по-прежнему имеет место. Тогда деньги российских потребителей не утекали бы за границу, а стимулировали и укрепляли бы экономику страны.
IV.
Литература
.
1. Пат. 2 136 928 США.
2. Пат. 2 521 911 США.
3. Пат. 211 116 Швейцария.
4. Паксен А.. Эпоксидные соединения и эпоксидные смолы. М.: Госхимиздат, 1962. 963 с.
5. Ли Х., Невилл К. Справочное руководство по эпоксидным смолам. М.: Энергия, 1973. С. 70 108.
6. Благонравова А. А., Непомнящий А. И. Лаковые эпоксидные смолы. М.: Химия, 1970. 184 с.
7. Еселев А. Д., Бобылев В. А. ЛКМ. 2008 № 10. С. 1215.
8. www.pslc.wsrussianeposyn.ru.
9. www. t22.nm.ru.
10. www.techno.x51.ru.