Повышение долговечности сборочных единиц с жесткими компенсаторами при ремонте машин
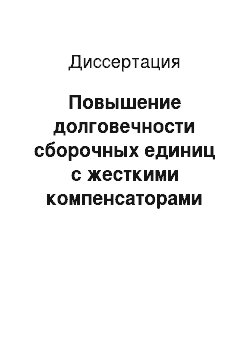
Точность изготовления машин непрерывно повышается и возросла за последние годы в 10 раз /19ЛВопросам же точности сборки машин на ремонтных предприятиях уделяется мало внимания. Между тем, без существенного повышения точности деталей и, особенно, сборки узлов при капитальном ремонте невозможно повысить качество ремонта и обеспечить ресурс отремонтированных машин не менее, чем 80% от новых… Читать ещё >
Содержание
- ВВЕДЕНИЕ '
- I. СОСТОЯНИЕ ВОПРОСА И ЗАДАЧИ ИССЛЕДОВАНИЯ
- I. I. Влияние точности сборки при ремонте на эксплуатационные показатели машин
- 1. 4. Причины нарушения точности сборки при ремонте машин
- 1. 5. Анализ теоретических методов обеспечения точности при ремонте
- 3. 2. Методика исследования точности сборочной единицы ведущей шестерни автомобиля ГАЗ-бЗА при капитальном ремонте
- 1. 2. Применение жестких компенсаторов для обеспечения точности сборочных единиц
- 1. 3. Точность сборки и долговечность подшипниковых сборочных единиц главных передач автомобилей
- 1. 6. Цели и задачи исследования
- 2. ТЕОРЕТИЧЕСКИЕ ПРЕДПОСЫЛКИ ПОВЫШЕНИЯ ТОЧНОСТИ СБОРОЧНЫХ ЕДИНИЦ С ЖЕСТКИМИ КОМПЕНСАТОРАМИ
- 2. 1. Расчет величины компенсации и задачи обеспечения точности сборки ведущей шестерни главной OQ передачи автомобиля ГАЗ-бЗА при ремонте
- 2. 2. Расчет жестких неподвижных компенсаторов в ремонтных размерных цепях с учетом нагрузки «» и других сборочных факторов
- 2. 3. Определение величины шага при дискретном контроле погрешности формы плоских деталей
- 2. 4. Выводы
- 3. МЕТОДИКА ЭКСПЕРИМЕНТАЛЬНЫХ ИССЛЕДОВАНИЙ ТОЧНОСТИ И
- ДОЛГОВЕЧНОСТИ СБОРОЧНЫХ ЕДИНИЦ
- 3. 1. Программа и общая методика исследований
- 3. 2. 1. Методика измерения величины предварительного натяга подшипников при сборке
- 3. 2. 2. Методика исследования точности деталей сборочной единицы ведущей шестерни
- 3. 3. Методика исследования влияния различных факторов на точность регулирования жесткими компенсаторами
- 3. 3. 1. Установка для исследования жестких неподвижных компенсаторов под нагрузкой
- 3. 3. 2. Методика экспериментальных исследований
- 3. 4. Методика исследования податливости деталей &bdquo-о сборочной единицы под нагрузкой
- 3. 5. Методика исследования макрогеометрии деталей
- 3. 5. 1. Измерительный комплекс для исследования макрогеометрии плоских деталей
- 3. 5. 2. Переналаживаемое приспособление для измерения погрешности формы плоских деталей
- 3. 5. 3. Методика экспериментальных исследований
- 3. 6. Методика стендовых испытаний
- 3. 6. 1. Приспособление для измерения осевого зазора в подшипниках ведущей шестерни главной передачи автомобиля ГАЭ-53А
- 3. 7. Методика эксплуатационных испытаний
- 3. 8. Выбор количества опытов, средств измерения, обработка экспериментальных данных и оценка их 90 точности
- 3. 1. Программа и общая методика исследований
- 4. РЕЗУЛЬТАТЫ ЭКСЖРИМЕНТАЛЬШХ ИССЛЕДОВАНИЙ И ИХ АНАЛИЗ
- 4. 1. Исследование точности сборочной единицы ведущей шестерни при капитальном ремонте
- 4. 1. 1. Исследование величины преднатяга подшипников при сборке ведущей шестерни
- 4. 1. 2. Исследование точности деталей, поступающих на сборку
- 4. 2. Исследование влияния различных факторов на точность регулирования жесткими компенсаторами
- 4. 3. Исследование макрогеометрии деталей
- 4. 3. 1. Исследование величины шага при дискретном контроле погрешности формы деталей
- 4. 3. 2. Исследование погрешностей формы деталей сборочной единицы
- 4. 4. Исследование податливости деталей сборочной единицы ведущей шестерни под нагрузкой
- 4. 5. Стендовые износные. испытания сборочных единиц
- 4. 6. Эксплуатационные испытания сборочных единиц ведущей шестерни 1IV
- 4. 7. Выводы
- 4. 1. Исследование точности сборочной единицы ведущей шестерни при капитальном ремонте
- 5. ВНЕЩРЕНИЕ РЕЗУЛЬТАТОВ ИССЛЕДОВАНИЯ В ПРОИЗВОДСТВО И
- ОЦЕНКА ИХ ЭКОНОМИЧЕСКОЙ ЭФФЕКТИВНОСТИ
- 5. 1. Разработка технологического процесса сборки ведущей шестерни при капитальном ремонте
- 5. 2. Приспособление для разборки, сборки и регулировки ведущей шестерни главной передачи автомобиля ГАЗ-58А
- 5. 3. Исходные данные душ определения годового экономи- ос ческого эффекта 1*
- 5. 4. Определение экономического эффекта от повышения долговечности сборочных единиц
Повышение долговечности сборочных единиц с жесткими компенсаторами при ремонте машин (реферат, курсовая, диплом, контрольная)
Надежное обеспечение страны продовольствием и сельскохозяйственным сырьем требует слаженной работы всех звеньев агропромышленного комплекса. Основными направлениями экономического и социального развития СССР на I98I-I985 гг. и на период до 1990 года предусматривается значительно улучшить использование тракторов, автомобилей, уборочных и других машин, повысить качество ремонта и обслуживания техники, проложить укрепление и специализацию ремонтно-обслуживащей базы / I /. Необходимость улучшения качества ремонта и подъема уровня технической готовности машин и оборудования была вновь подчеркнута на майском (1982 г.) Пленуме ЦК КПСС и нашла свое отражение в Продовольственной программе СССР / 2 /.
Диссертационная работа выполнена в соответствии с Координационным планом по решению научно-технической проблемы 0.51.II «Разработать и внедрить комплексную систему ремонта и технического обслуживания сельскохозяйственной техники, обеспечивающую доведение ресурса капитально отремонтированных тракторов новых марок не менее, чем 80% от новых», утвержденным ГКНТ СССР Постановлением № 450 от 26 ноября 1976 г.
Качество капитального ремонта машин на многих ремонтных предприятиях Госкомсельхозтехники СССР все еще не соответствует предъявляемым требованиям / 3 /. Одной из главных причин этого является недостаточная точность сборки при ремонте. Удельная трудоемкость сборочных работ в авторемонтном производстве составляет 20.25% / 4 /. Некачественная сборка особенно сильно сказывается на надежности наиболее точных и ответственных сборочных единиц. Точность замыкающих звеньев в таких сборочных единицах удается обеспечить лишь применением жестких ком- ¦ пенсаторов (регулировочных прокладок, колец и т. д.). Поэтому повышение точности сборки сборочных единиц с жесткими компенсаторами с целью увеличения их долговечности является актуальной задачей для ремонтного производства.
Применение жестких компенсаторов для обеспечения точности сборочных единиц обусловлено значительными удельными нагрузками как на составляющие детали, так и на сами компенсаторы. В ранее проведенных исследованиях вопрос обеспечения точности сборочных единиц с жесткими компенсаторами при ремонте с учетом нагрузки и других сборочных факторов исследован недостаточно.
В настоящей работе разработана методика расчета жестких компенсаторов в ремонтных размерных цепях, учитывающая параметры рассеяния действительных размеров деталей, влияние на них нагрузки, макрогеометрии и других сборочных факторов, а также влияние указанных факторов на размеры самих компенсаторовполучены выражения и разработана программа расчета на ЭВМ величины шага при дискретном контроле макрогеометрии плоских поверхностей деталей с установленной точностью.
Типичной сборочной единицей, точность сборки которой достигается регулированием жесткими неподвижными компенсаторами, является ведущая шестерня главной передачи автомобиля ГАЗ-бЗА, нашедшего наибольшее применение в сельскохозяйственном производстве.
В работе исследовано влияние нагрузки и других факторов на изменение размера компенсаторов и деталей сборочной единицы ведущей шестерни главной передачи автомобиля ГАЗ-бЗА, влияние величины зазора-натяга подшипников ведущей шестерни на долговечность сборочной единицы.
На основе теоретических и экспериментальных исследований разработан технологический процесс сборки ведущей шестерни главной передачи автомобиля ГАЭ-53А и комплект технологической оснастки, позволяющие обеспечить качественную сборку ведущей шестерни. Технологический процесс сборки ведущей шестерни внедрен на Краснопахорском ремонтно-механическом заводе Госкомсельхозтехни-ки РСФСР.
Работа выполнена на кафедре основ взаимозаменяемости и технических измерений Московского ордена Трудового Красного Знамени института инженеров сельскохозяйственного производства имени В. П. Горячкина. Состоит из введения, пяти глав, выводов, списка литературы и приложений.
Основные положения диссертационной работы доложены, обсуждены и одобрены на:
— научных конференциях профессорско-преподавательского состава, научных работников и аспирантов Московского ордена Трудового Красного Знамени института инженеров сельскохозяйственного производства имени В. П. Горячкина в 1979;1984 гг.;
— научной конференции Саратовского института механизации сельского хозяйства им. М. И. Калинина в 1982 г.;
— объединенном заседании кафедр ремонта и тдежности машин и основ взаимозаменяемости и технических измерений в 1985 г.;
— на техническом совете Краснопахорского РМЗ в 1985 г.
По материалам диссертации в периодических изданиях и сборниках опубликовано II статей.
На защиту выносится:
— теоретическое обоснование расчета жестких компенсаторов в ремонтных размерных цепях и величины шага при дискретном контроле макрогеометрии плоских деталей;
— результаты исследований влияния нагрузки и других факторов на изменение размера компенсаторов и деталей сборочной единицы ведущей шестерни главной передачи автомобиля ГАЗ-бЗА, а также влияния величины зазора-натяга подшипников ведущей шестерни на долговечность сборочной единицы;
— конструктивные разработки элементов оборудования для проведения исследований и технологической оснастки для сборки ведущей шестерни;
— результаты внедрения разработанных технологического процесса и техоснастки.
I. СОСТОЯНИЕ ВОПРОСА И ЗАДАЧИ ИССЛЕДОВАНИЯ.
I.I. Влияние точности сборки при ремонте на эксплуатационные показатели машин.
Вопросы обеспечения необходимой точности при производстве машин были поставлены самим развитием производства, особенно крупносерийного и массового. Основы расчета машин на точность заложены в трудах Б. С. Балакпщна / 5 / и Н. А. Бородачева / 6 /. Дальнейшее развитие теория точности машин получила в работах Б. А. Тайца, А. И. Якушева, Ю. Н. Ляндона, М. А. Палея, П. Ф. Дунаева, И.В.Дунина-Барковского, А. Л. Маркова и других советских ученых. Принятие стандартов ГОСТ 16 319–80 и 16 320−80 подняло эту работу на новый уровень.
В области ремонта машин большой вклад в решение проблемы повышения их точности и долговечности внесли А. И. Иванов / 7 / и Л. В. Дехтеринский / 8 /.
Ведущие ученые указывают на неразрывную связь точности изготовления и сборки машин с их эксплуатационными показателями, надежностью и долговечностью. «Наличие погрешностей в расположении поверхностей деталей усиливает неравномерность контакта деталей, — пишет А. И. Якушев. — Этим объясняется, что часто детали изнашиваются очень быстро, понижается точность, нарушается герметичность соединений и появляются другие дефекты» / 9 /.
И.Я.Аяыпиц, отмечая большое значение изучения состояния деталей и узлов машин, поступающих в капитальный ремонт, подчеркивает, что монтаж, при котором не обеспечивается необходимая точность, приводит к значительному сокращению ресурса изделия / 10 /. «При ремонте машины, — отмечает А. И. Иванов, — важно восстановить не только посадки цилиндрических соединений, но и точность замыкающих звеньев размерных цепей, определяющих качество работы, надежность и долговечность машины» / II /.
Вопросы влияния точности на эксплуатационные показатели и долговечность машин подробно рассмотрены в диссертационных работах В. О. Агузарова, И. Е. Ддшна, И. А. Ратникова, В. В. Целикова, П. И. Гринберга и других.
В сельскохозяйственном машиностроении одной из первых работ, связывающих точность изготовления с эксплуатационными показателями машины является диссертационная работа П. В. Полещенко / 12 /, в которой были получены уравнения, связывающие недомолот и дробление зерна с величиной бокового зазора молотильного устройства.
И.С.Серым / 13 / установлено, что смещение геометрических осей цилиндров и коленчатого вала в плоскости продольного сечения двигателя вызывает увеличение износа цилиндров, который при смещениях, имеющих место в двигателях, возрастает на 15−20%.
Исследования, проведенные Х. Я. Аасамяэ / 14 /, показали, что имеющее место при эксплуатации нарушение точности топливного насоса вызывает увеличение удельного расхода топлива более чем на 11% от номинального, а эффективная мощность двигателя уменьшается при этом более чем на 10% от номинальной.
Согласно / 15 / смещение в паре конических шестерен одной из них от нормального положения всего на 0,4 мм вызывает снижение их долговечности в 2,7 раза.
В ряде работ отмечается, что геометрическая точность деталей несравнимо существеннее влияет на эксплуатационные показатели, чем технологические режимы их восстановления / 16 /.
Многими авторами отмечается влияние макрогеометрии деталей на ресурс машин. Академик Ю. И. Петров подчеркивает, что при наличии макрогеометрических отклонений деталей у работающей машины быстрее будут возникать неисправности и снизится ее надежность / 17 /. Авторы / 18 / отмечают, что погрешности формы деталей и точность взаимного расположения поверхностей вызывают усиленный износ и оказывают большое влияние на собираемость узлов и механизмов, на их долговечность и надежность.
Вопросы влияния точностных параметров на эксплуатационные показатели и долговечность машин рассматриваются также в диссертационных работах С. М. Бабусенко, А. Я. Маренич, Р. Меметова, Р. А. Исхакова, Н. В. Дворянинова, Е. И. Кривенко, Х. К. Якубова и многих других.
В последние десятилетия наука о ремонте достигла определенных успехов. Разработано множество различных методов восстановления деталей, созданы специализированные поточные линии, высокопрочные материалы (проволока, порошки и т. д.), позволяющие получать покрытия, в отдельных случаях, во много раз превосходящие по износостойкости новые детали. Однако, нарушение взаимного расположения деталей при сборке сводит на нет это преимущество. На ремонтных предприятиях Госкомсельхозтехники СССР точность машин значительно уступает точности новых. Объясняется это следующими причинами:
— различие технологических процессов при изготовлении и ремонте машин (целый ряд дополнительных технологических процессов, использование прошедших эксплуатацию деталей и т. д.);
— невозможность использовать на ремонтных предприятиях оборудование, оснастку и инструмент, применяемые на машиностроительных заводах из-за небольшой программы;
— невысокая точность технологического оборудования, технологической и контрольно-измерительной оснастки, особенно оборудования и оснастки собственного изготовления;
— низкий уровень организации и контроля на ремонтных предприятиях.
Точность изготовления машин непрерывно повышается и возросла за последние годы в 10 раз /19ЛВопросам же точности сборки машин на ремонтных предприятиях уделяется мало внимания. Между тем, без существенного повышения точности деталей и, особенно, сборки узлов при капитальном ремонте невозможно повысить качество ремонта и обеспечить ресурс отремонтированных машин не менее, чем 80% от новых. Нарушение точности и взаимного расположения деталей в процессе сборки при капитальном ремонте является одной из основных причин низкого качества и невысокой долговечности капитально отремонтированных машин. Таким образом, надежность капитально отремонтированных машин непосредственно связана с обеспечением точности при ремонте. Особенно это касается агрегатов и сборочных единиц, непосредственно лимитирующих долговечность машин: двигателя, зубчатых передач, подшипниковых устройств и т. д.
Необходим тщательный анализ причин низкого ресурса машин, рекламаций, выявление сборочных единиц, лимитирующих долговечность, технологическое обеспечение точности их сборки при капитальном ремонте, разработка и изготовление технологической и контрольно-измерительной оснастки, обеспечивающей необходимую точность.
1.2. Применение жестких компенсаторов для обеспечения точности сборочных единиц.
Метод регулирования является одним из методов достижения заданной точности замыкающего звена. Требуемая точность замыкающего звена достигается при сборке за счет изменения размера компенсирующего звена без снятия стружки. Как отмечается в ГОСТ 16 319–80 — метод «весьма широко распространен во всех произволствах, особенно для цепей, отличающихся высокой точностью». Он находит применение в тех случаях, когда достижение заданной точности методами полной или неполной взаимозаменяемости экономически нецелесообразно или технически невозможно.
По назначению все типы компенсаторов делятся на следующие группы:
— для поглощения ошибок размеров длины;
— для поглощения ошибок диаметральных размеров;
— для поглощения ошибок угловых размеров;
— для поглощения ошибок от соосности и перекоса и т. п. / 20 /.
Для достижения требуемой точности замыкающего звена используют неподвижные или подвижные компенсаторы. Наиболее полная их классификация дана в работе / 21 / (рис. I. I).
Метод регулирования находит широкое применение благодаря своим преимуществам ., основными из которых являются:
— возможность достижения высокой точности механизма;
— возможность поддерживать ее во время эксплуатации;
— возможность расширения допусков всех размеров цепи;
— возможность использования в цепях с меняющимися при эксплуатации размерами;
— возможность обеспечения (в некоторых случаях) автоматичности регулирования точности.
Указанные преимущества позволяют наиболее широко применять метод компенсации в размерных цепях высокой точности с большим числом звеньев. Однако он имеет и ряд недостатков:
— возможное усложнение конструкции изделия;
— увеличение (в некоторых случаях) количества деталей в размерной цепи;
— усложнение сборки из-за необходимости регулировки и измерений .
Неподвижные жесткие компенсаторы (регулировочные шайбы, прокладки, втулки и т. д.) находят применение там, где невозможно применить подвижные компенсаторы непрерывного и периодического автоматического или ручного регулирования. Основная. область их применения — в узлах высокой точности с большой удельной нагрузкой. Они отличаются простотой конструкции, стабильностью регулирования в условиях динамических нагрузок. Основные области их применения:
— регулирование зацепления в конических, гипоидных и других передачах;
— регулирование натягов и зазоров в подшипниковых узлах;
— регулирование положения базовых деталей.
Достаточно сказать, что только в переднем ведущем мосту трактора МТЗ-82 имеется 16 мест регулирования жесткими компенсаторами. На рис. 1.2 показаны компенсаторы, применяемые для регулирования предварительного натяга подшипников ведущей шестерни и зацепления главной передачи автомобиля ГАЗ-бЗА.
Наиболее характерные места применения жестких компенсаторов в тракторов, автомобилях и комбайнах приведены на рис. 1.3. Анализ рис. 1.3 показывает, что жесткими неподвижными компенсаторами осуществляется регулирование наиболее ответственных сборочных единиц, лимитирующих качество и долговечность тракторов, автомобилей и сельскохозяйственных машин.
Таким образом, простота конструкции, стабильность регулирования и преимущества метода регулирования при обеспечении точности сборочных единиц обусловливают широкое применение жестких компенсаторов в конструкциях машин.
1.3. Точность сборки и долговечность подшипниковых сборочных единиц главных передач автомобилей.
Подшипники являются одним из наиболее распространенных в конструкциях машин изделием. Количество их в современных тракторах, автомобилях и сельскохозяйственных машинах постоянно возрастает. Так, по данным / 22 / в тракторе К-700 их около 200. В целом по стране на ремонт сельскохозяйственной техники ежегодно расходуется свыше 100 млн. подшипников качения.
Широкое применение подшипников в сельскохозяйственных машинах определяет и их место среди деталей, лимитирующих надежность машины. К этому следует добавить, что подшипники устанавливаются в наиболее динамически нагруженных, сложных сборочных единицах, а выход из строя подшипника приводит к выходу всей сборочной единицы. К числу таких сборочных единиц относятся и главные передачи автомобилей.
Долговечность подшипников была предметом исследования ряда авторов. Кручинин В. А. / 23 /, Бабусенко С. М. / 24 /, Гальперин Г. Л. / 25 / и др. показали влияние различных факторов на долговечность подшипников.
Остановимся более подробно на подшипниках регулируемого типа, широко применяемых в трансмиссиях тракторов и автомобилей. К ним, в первую очередь, относятся конические роликовые подшипники. Долговечность этих подшипников непосредственно определяет долговечность машин. Авторы / 22 / указывают, что основными факторами, определяющими долговечность большинства подшипников качения тракторов является наличие абразива в смазке и величина зазора в подшипниках. В работе / 26 / проведен анализ неисправностей выбракованных подшипников (табл. 1.3).
Классификация компенсаторов по М. Х. Сабирову / 21 /.
Рис. I.I.
Общий вид компенсаторов, применяемых для регулирования преднатяга подшипников и положения ведущей шестерни автомобиля ГАЭ-53А.
Рис. 1.2.
Таблица 1.3.
Распределение выбракованных подшипников качения тракторов по видам повреждений / 26 /.
Вид повреждений (выбраковочный признак).
Частота возникновения выбраковочного признака, %.
Увеличение зазоров сверх предельных значений.
Нарушение плотности посадки.
Макроскопические повреждения дорожек и тел качения.
Поломки деталей подшипника.
65−75 17−21.
4-II.
5−9.
Наиболее часто подшипники качения тракторов выбраковывают из-за увеличения зазоров выше предельных значений. То же можно сказать и о регулируемых подшипниках качения автомобилей. Зазор в подшипниках качения приводит к перекосу валов, нарушению межцентровых расстояний, увеличению динамических нагрузок на шестерни и ускоренному выходу последних из строя. На рис. 1.4 и 1.5 представлены характерные усталостные разрушения подшипников сборочной единицы ведущей шестерни и самой шестерни автомобиля PA3−53A.
Н.В.Дворяниновым / 27 / установлено, что основной вид повреждения зубьев главной передачи автомобилей ГАЗ — усталостное выкрашивание и что износ и пластическая деформация зубьев не лимитируют, при соответствующей смазке, долговечность.
В процессе исследования качества сборки главных передач ЗИЛ-130 Р. А. Исхаковым / 28 / выявлено, что большинство дефектов подшипников редукторов ЗИЛ-130 возникают вследствие работы их в условиях значительного перекоса колец.
Исследования, проведенные в НАМИ / 29 /, показали, что разрушение обойм подшипников ведущей шестерни и коробки сателлитов.
Характерные места регулирования жесткими компенсаторами в тракторах, автомобилях и зерноуборочных комбайнах.
Рис. 1.3.
ОбЬЕКГы РЕГУЛИРОВАНИЯ ЖЕСТКИМИ КОМПЕНСАТОРАМИ зацепление при8оЗацепление привода Ла wnffifcftr*** замасляного насоса осе8ой зазор Htippn стартера регулятор топлцбног о насоса.
Усталостные разрушения подшипников ведущей шестерни, выбракованных на Рязанском опытном АРЗ Госкомсельхоз-техники РСФСР.
Рис. 1.4. являются характерными отказами деталей и узлов заднего моста.
Эксплуатационные испытания 30 автомобилей ГАЗ-бЗА, проведенные Горьковским автомобильным заводом в г. Киеве показали, что ведущая и ведомая шестерни являются деталями, лимитирующими надежность автомобиля по расходу запасных частей / 30 /.
Большой осевой зазор ведущей шестерни, — указывает А. Д. Просвирин, — нарушает правильность зацепления зубьев шестерен главной передачи и вызывает перераспределение нагрузок на подшипники. В этом случае. преждевременно изнашиваются торцы фланца и других деталей и, как следствие, выходят из строя подшипники или зубья ведущей шестерни, а также может поломаться задний хвостовик ведущей шестерни" / 31 /.
Таким образом, нарушение точности регулировки подшипниковой сборочной единицы приводит к уменьшению долговечности главной передачи и выходу машины из строя. В связи с этим, тщательной регулировке конических подшипников автомобилей всегда уделялось особое внимание. Специально этому вопросу посвящено пособие / 30 /. Большая работа по обеспечению точности сборки подшипниковых узлов была проведена Х. К. Якубовым / 33, 34 /. Вопросам повышения долговечности подшипниковых узлов в тракторах посвящены работы / 35, 36 /.
Долговечность сборочной единицы снижается как при увеличении, так и при уменьшении величины оптимального предварительного натяга подшипников. В работе / 37 / для определения требуемой величины преднатяга предложен графоаналитический метод, применение которого рассмотрено для конкретной сборочной единицыведущей цилиндрической шестерни главной передачи автомобиля КамАЭ-5320.
В последние годы целый ряд вопросов теоретического плана по обеспечению точности сборки и долговечности сборочных единиц с подшипниками был решен А. В. Ворониным. В работе / 38 / экспериментально установлено, что монтажные размеры конических подшипников изменяются в зависимости от величины прикладываемой к ним нагрузки, относительного проворота колец и других факторов. Влияние каждого из этих факторов на величину компенсаторов может превышать заданную точность выходных параметров редуктора. В / 39 / качественно и количественно установлены деформации конического кольца и степень влияния указанных деформаций на изменение монтажной высоты для подшипника 7606УШ. А. В. Воронин подчеркивает / 40 /, что преднатяг подшипников определяет качество сборки редуктора и работоспособность агрегата, регламентация его по моменту трения является вынужденным решением и что только воспроизведение усилий в контурах размерной цепи способно обеспечить наиболее высокую точность и стабильность его. Предложен также / 41 / метод расчета долговечности сборочных единиц по максимальным касательным напряжениям в контактных площадках рабочих тел в зависимости от результатов сборки неподвижных соединений колец подшипников с корпусом и валом.
Основные способы регулирования зазоров-натягов (осевой игры) конических подшипников представлены на рис. 1.6.
В тракторах и сельскохозяйственных машинах в основном используются первые два способа, причем регулирование перемещением резьбовых деталей осуществляется непрерывно, а не ступенчато, как при использовании жестких неподвижных компенсаторов. Однако, резьбовые детали обладают нестабильностью регулирования из-за их невысокой жесткости и ослабления затяжки со временем, поэтому в наиболее ответственных сборочных единицах применяются жесткие неподвижные компенсаторы.
Главная передача является одной из наиболее нагруженных сборочных единиц автомобиля и от ее надежной работы во многом йдада увшвш дарш шестерни автомобиля ГАЗ-бЗА, вышедшей из строя из-за нарушения зацепления.
Рис. 1.5.
Основные способы регулирования конических подшипников.
Рис. 1.6. Л зависит долговечность машины в целом.
Вопросам повышения надежности и долговечности главных передач посвящены исследования Х. К. Якубова, Н. А. Дворянинова, В. В. Чумакова, Е. И. Кривенко, Р. А. Исхакова, В. И. Полушкина. Х. К. Якубовым исследован ряд размерных цепей главной передачи ЗИЛ-130, обоснованы технические требования и даны рекомендации по повышению точности сборки при капитальном ремонте / 34 /.
Н.В.Дворяниновым / 27 / всесторонне исследованы причины снижения жесткости и точности главной передачи PA3−53A, экономический эффект только от части внедренных рекомендаций составил 730 тыс. руб.
Работы Н. А. Дворянинова, В. В. Чумакова позволили существенно повысить качество и долговечность главных передач ГАЭ-53А при изготовлении машин / 42 /. В настоящее время главная передача, в целом, не лимитирует долговечность нового автомобиля ГАЗ-53А. По данным НИИА. Т / 43 /, процентное соотношение отказов к общему числу отказов по заднему мосту составляло 2,6%, наработка на отказ — 71,5 тыс.км. Проведенные в ВАШ испытания автомобилей-самосвалов ГАЗ-53Б / 29 / за период с начала эксплуатации до капитального ремонта показали, что средний ресурс до постановки на ремонт составил 174,16 тыс. км, удельное количество отказов по заднему мосту — 3,07 отказов на автомобиль, процент отказов по заднему мосту от общего количества отказов — 2,97%.
Исследования, проведенные Горьковским автомобильным заводом на автотранспортных предприятиях Самарканда, Одессы, Киева показали, что на автомобилях ГАЗ-бЗА 1973;1975 гг. выпуска фактические ресурсы автомобилей и их агрегатов, за исключением карданной передачи и коробки передач, превышали нормативные пробеги до капитального ремонта / 30 /.
В автомобилях же, прошедших капитальный ремонт, задний мост лимитирует надежность. Согласно данным НИИАТ / 44 /, отказы по заднему мосту капитально отремонтированных автомобилей ЗИЛ-130 по количеству находятся на четвертом месте после тормозов, сцепления и подвески, пробег капитально отремонтированного заднего моста ГАЗ-51 составляет 86,2 $ от нормативного.
Низкая долговечность главных передач прямо связана с точностью сборки. Р. А. Исхаковым установлено, что у 11% капитально отремонтированных редукторов ЗИЛ-130 не обеспечивается необходимый натяг подшипников или нарушается взаимное положение конических шестерен.
Согласно исследованиям Е. И. Кривенко на долю редуктора приходится 80% всех отказов заднего моста / 45 /.
Авторы / 46 / указывают, что техническое состояние ведущих мостов грузовых автомобилей не отвечает установленным требованиям.
Недостаточная точность сборки ведущей шестерни объясняется невозможностью применения при капитальном ремонте оборудования и оснастки, используемых для регулирования преднатяга на заводах-изготовителях. Работы по повышению точности регулирования при капитальном ремонте ведутся как в практическом, так и теоретическом плане. Х. К. Якубовым предложен метод селективного подбора при сборке редуктора / 47 /. Авторы / 39, 48, 34 / рассматривают теоретические вопросы точности сборки и долговечности узла ведущей шестерни. В. Я. Поповым / 49 / предложен комплект приспособлений для повышения точности сборки главной передачи автомобиля УАЗ, заменяющий несколько сложных стендов из комплекта Ульяновского автомобильного завода. Рязанским филиалом ЦКТБ Госкомсельхозтехники РСФСР разработаны приспособления для подбора прокладок при регулировании конических подшипников (70−7879−5906), а также при установке ведущей шестерни.
70−7879−5907) совместно с (70−7826−5910) / 50 /.
Однако, ввиду сложности и неудобства использования указанные приспособления не нашли широкого применения. На ремонтных предприятиях Госкомсельхозтехники СССР сборка узла ведущей шестерни ГАЗ-5ЭА осуществляется, в основном, регулировкой предна-тяга подшипников вручную методом попыток по усилию поворота шестерни. Обычно, для достижения «нормального» преднатяга требуется до 3−4 попыток с полной разборкой и последующей сборкой ведущей шестерни, что приводит к увеличению нормы времени на сборку. При этом необходимая величина преднатяга 50+ 30 мкм / 51 / в большинстве случаев не обеспечивается.
Недостаточная точность сборки ведущей шестерни приводит к быстрому возрастанию зазора в подшипниках. Повышенный зазор ведет к росту контактных напряжений и усталостному разрушению колец подшипников (рис. 1.4), перекосу ведущей шестерни, росту контактных напряжений на зубьях и усталостному разрушению последних (рис. 1.5). Это приводит к выходу машин из строя, перерасходу запасных частей при капитальном ремонте. Таким образом, для повышения долговечности главной передачи после капитального ремонта необходимо обеспечить требуемую точность сборки ведущей шестерни по величине предварительного натяга подшипников.
ОБЩИЕ ВЫВОДЫ И РЕКОМЕНДАЦИИ.
1. Жесткие компенсаторы находят широкое применение в наиболее ответственных и точных сборочных единицах, долговечность которых лимитирует ресурс машины. В ранее проведенных исследованиях вопрос обеспечения точности сборочных единиц с жесткими компенсаторами при ремонте с учетом нагрузки и других сборочных факторов исследован недостаточно.
2. Исследования, проведенные на Рязанском и Краснопахор-ском ремонтных заводах Госкомсельхозтехники РСФСР, показали, что точность сборочных единиц ведущей шестерни главной передачи автомобиля ГАЗ-бЗА по величине предварительного натяга подшипников при капитальном ремонте не обеспечивается из-за несовершенства технологии сборки (46,2% сборочных единиц имеют вместо натяга зазор, брак в сборке составляет 85,89%).
3. Теоретическими и экспериментальными исследованиями установлено, что величина компенсации, определенная по действительным размерам деталей, составляет 1328 мкм, то есть в 4,22 раза превышает значение, полученное по данным завода-изготовителя (315 мкм). При ремонте зона рассеяния действительных размеров деталей, определяющих величину предварительного натяга подшипников, в 3,0.7,2 раза превышает величину допуска на изготовление. Точность сборки не может быть обеспечена существующей технологией ремонта и применением типоразмеров компенсаторов, используемых при изготовлении машины.
4. Разработана методика расчета жестких компенсаторов в ремонтных размерных цепях, учитывающая рассеяние действительных размеров деталей, влияние на них нагрузки и других сборочных факторов, а также деформацию под нагрузкой самих компенсаторов.
5. Разработана методика и программа расчета на ЭВМ величины шага при дискретном контроле погрешности формы плоских деталей с заданной точностью. Возможность использования расчетных значений шага подтверждена экспериментально.
6. В результате корреляционно-регрессионного анализа изменения размера пакета компенсаторов под нагрузкой получено уравнение регрессии и номограмма, позволяющие определить величину изменения размера при удельной нагрузке от 0,13 до 1,32 МПа и количестве прокладок от I до 12.
7. Проведены исследования и получены зависимости размеров деталей, определяющих величину предварительного натяга подшипников, от нагрузки в свободном состоянии и с учетом сборочных факторов.
8. Ускоренными стендовыми испытаниями установлено, что скорость возрастания зазора в подшипниках ведущей шестерни зависит от величины начального зазора-натяга. Увеличение начального зазора с 0 до 0,5 мм вызывает возрастание скорости нарастания зазора в 5,27 раза, то есть некачественная сборка резко сокращает долговечность сборочной единицы.
9. Сравнительными эксплуатационными испытаниями установлено, что качественная сборка ведущей шестерни с использованием одиночного компенсатора определенного типоразмера повышает долговечность сборочной единицы в среднем на 30,2% по сравнению с существующей технологией.
10. Разработан технологический процесс сборки ведущей шестерни и комплект технологической оснастки (приспособление для измерения зазора в подшипниках ведущей шестерни, переналаживаемое приспособление для измерения погрешности форш компенсаторов и приспособление для разборки, сборки и регулировки ведущей шестерни). Технологический процесс внедрен на Краснопахорском.
РМЗ. Годовой экономический эффект от внедрения составляет 40 364 руб. при программе ремонта 1000 сборочных единиц.
Список литературы
- Материалы ХХУ1 съезда КПСС. — М.: Политиздат, 1982. -- 223 с.
- Продовольственная программа СССР на период до 1990 года и меры по ее реализации: материалы майского Пленума ЦК КПСС 1982 г. М.: Политиздат, 1982. — III с.
- Постановление Президиума АН СССР и коллегии Госкомсель-хозтехники СССР 16 130/19 от 30.06.82 «О мерах по ускорению научно-технического прогресса в ремонтно-обслуживающем производстве».- М.: рот. бюро ГСХТ СССР, 1982. 13 с.
- Гусев В.И. Проектирование сборочных технологических процессов. М.: Изд-во Московского автомобильно-дорожного института, 1980. — 87 с.
- Балакшин Б.С. Энциклопедический справочник: Машиностроение. М.: Машгиз, 1947, т. 5, с. I00-II8.
- Бородачев Н.А. Основные вопросы теории точности производства. М.-Л.: Изд-во АН СССР, 1950, — 416 с.
- Иванов А.И. Повышение эффективности ремонта и эксплуатации сельскохозяйственных машин (путем оптимизации размерных параметров): Дис. д-ра техн.наук. М., 1972. — 271 л.
- Дехтеринский Л.В. Исследование способов восстановления прямозубых шестерен автомобильных коробок передач:Дис. канд.техн.наук. М., 1951. — 253 л.
- Якушев А.И. Направления развития взаимозаменяемости в машиностроении. Вестник машиностроения, 1971, № 12, с. 42−44.
- Альшиц И.Я. Вопросы продления долговечности машин, улучшения их качества. Вестник машиностроения, 1980, № II, с. 19−20.
- Иванов А.И. Основы взаимозаменяемости и технические измерения. М.: Колос, 1975. — 496 с.
- Полещенко П.В. Исследование точности изготовления и ремонта молотильного устройства комбайна «Сталинец-6»: Дис. канд. техн. наук. М., 1953. — 220 л.
- Серый И.С. Исследование некоторых размерных цепей тракторного двигателя и методов их восстановления в процессе ремонта: Дис. канд. техн. наук. М., 1956. — 125 л.
- Громан М.Б., Шжейфер М. А. Конические передачи с круговым зубом. М.: Машиностроение, 1964. — 176 с.
- Голубев И.Г. Исследование долговечности неподвижных соединений, восстановленных железнением при ремонте сельскохозяйственной техники: Дис. канд. техн. наук. М., 1981. -135 л.
- Основы ремонта машин / Петров Ю. Н. и др. М.: Колос, 1972. — 527 с.
- Взаимозаменяемость в ремонте и эксплуатации машин / Иванов А. И., Полещенко П. В., Бабусенко С. М. и др. М.: Колос, 1969. — 320 с.
- Птуха Л.И. Достижение точности сборочной единицы с учетом количественной связи показателей точности деталей: Дис. канд. техн. наук. М., 1978. — 237 л.
- Допуски и посадки: Справочник: В 2-х т. I.- Машиностроение, 1978. — 1032 с.
- Сабиров М.Х. Классификация методов и средств компенсации погрешностей сборки машин. Сб. научн. тр. / Моск. ин-т инженеров с.-х. производства, 1980, т. ХУТ, вып. 9, с. 19−25.
- Костецкий Б.И., Моисеев А. А., Гальперин Г. Л. Анализ причин поврездаемости подшипников качения тракторов. Труды / ГОСНИТЙ, 1970, т. 23, с. 22−23.
- Кручинин В.А. Аналитическое и экспериментальное определение перекосов и зазоров в подшипниках качения. Автомобильная промышленность, 1974, № 6, с. 11−14.
- Бабусенко С.М. Исследование износа и долговечности подшипниковых узлов тракторов, автомобилей и сельскохозяйственных машин: Дис. канд. техн. наук. М., 1963. — 145 л.
- Гальперин Г. Л. и др. К обоснованию оптимального зазора в подшипниках качения регулируемого типа. Тракторы и сельхозмашины, 1976, № 11, с. 19−20.
- Моисеев А.А., Гальперин Г. Л. Тракторные подшипники качения. М.: Колос, 1979. — 112 с.
- Дворянинов Ы.В. Исследование работоспособности главных передач грузовых автомобилей средней грузоподъемности: Дис. канд. техн. наук. М., 1974. — 208 л.
- Исхаков Р.А. Технологическое обеспечение качества сборки главной передачи при капитальном ремонте автомобиля ЗИЛ-130: Дис. канд. техн. наук. М., 1975. — 240 л.
- Результаты эксплуатационных испытаний автомобилей-самосвалов ГАЭ-53Б за период с начала эксплуатации до капитального ремонта: Отчет / НАМИ зхз — ±7. — Горький, 1978. — 215 с.
- Автомобиль ГАЗ-бЗА / Под ред. А. Д. Просвирина. М.: Машиностроение, 1968. — 382 с.
- Кузнецов С.И. Регулировка конических подшипников и зубчатых зацеплений автомобилей. М.: Оборонгиз, 1956. — 119 с.
- Якубов Х.К. Сборка ведущей конической шестерни главной передачи. Автомобильный транспорт, 1976, № 7, с. 39−41.
- Якубов Х.К. Исследование точности сборки главной передачи автомобилей ЗИП при капитальном ремонте: Дис. канд. техн. наук. М., 1974. — 330 л.
- Скундин Г. И. и др. О долговечности подшипников тракторных трансмиссий. Тракторы и сельхозмашины, 1965, № 5,с. 9-II.
- Сергеев М.П. и др. Когда регулировать подшипники опорных катков? Техника в сельском хозяйстве, 1968, № 5, с.63−65.
- Барун В.Н., Цивилева О. Б., Капустин Ю. И. Графоаналитический метод расчета предварительного натяга конических роликоподшипников. Вестник машиностроения, 1980, № 10, с. 11−13.
- Воронин А.В., Шандров Б. В., Герасимов И. К. Поведение конических подшипников и качество сборки редукторов ведущих мостов автомобилей. Автомобильная промышленность, 1973, 10, с. 28−30.
- Воронин А.В., Котеров Н. И., Шандров Б. В. К вопросу технологического обеспечения сборки редукторов ведущих мостов. -Автомобильная промышленность, 1977, № 2, с. 32−35.
- Воронин А.В. Преднатяг подшипниковых узлов и принципы его технологического обеспечения. Автомобильная промышленность, 1979, № 8, с. 24−28.
- Воронин А.В., Воронин С. А. К расчету на долговечность радиально-упорных конических подшипниковых узлов. Автомобильная промышленность, 1980, .№ 12, с. 15−18.
- Просвирин А.Д., Дворянинов Н. А., Чумаков В. В. Повышение долговечности главной передачи автомобиля ГАЗ-бЗА. Автомобильная промышленность, 1969, № 10, с. 20−23.
- Исследование эксплуатационной надежности и разработка рациональных нормативов по режимам технического обслуживания автомобилей семейства ГАЗ-бЗА, работавших во П и Ш категории условий эксплуатации: Отчет / НИИАТ Н-06−72. — М., 1972. — 101 с.
- Кривенко Е.И. Исследование надежности агрегатов трансмиссии грузовых автомобилей. Автомобильный транспорт, 1976, № 8, с. 26−30.
- Семкович А.Д., Сидорчук А. В. Исследование технического состояния автомобильных ведущих мостов. Механизация и электрификация социалистического сельского хозяйства, 1979,1. II, с. 43−44.
- Кожин К.Г., Кациграс Г. А., Сергеев А. И., Якубов Х. К. Сборка редуктора и передней оси методом селективного подбора. -Автомобильный транспорт, 1963, № 11, с. 26−30.
- Воронин А.В., Шандров Б. В. Некоторые особенности сборки главных передач автомобилей. Автомобильная промышленность, 1978, № 5, с. 36−38.
- Попов В.Я. Комплект приспособлений для подбора прокладок. Техника в сельском хозяйстве, 1980, й 4, с. 57−60.
- Оборудование и оснастка для капитального ремонта грузовых автомобилей ГАЗ: Каталог: В / 5-ти частях. М.: ЦБНТИ, 1980, часть 5. — 72 с.
- РК 200 РСФСР 2/1−2036−80. Автомобиль ГАЗ-53А (без двигателя): Руководство по капитальному ремонту. — М.: 1981, ч. I, 2. — 309 с.
- Черневский Л.В. Теоретические основы, методы и средства обеспечения точности сборки прецизионных изделий (на примере подшипников качения): Дис. д-ра техн. наук. М., 1978.- 290 л.
- Тимошкин Н.И. Исследование и обоснование комплексного метода дефектовки деталей типа корпус коробки передач: Дис. канд. техн. наук. Кинель, 1973. — 217 л.
- Селиванов А.И., Артемьев Ю. Н. Теоретические основы ремонта и надежности сельскохозяйственной техники. М.: Колос, 1978. — 248 с.
- Артемьев Ю.Н. Качество ремонта и надежность машин в сельском хозяйстве. М.: Колос, 1981. — 239 с.
- Дунин-Барковский И.В., Карташова А. И. Измерения и анализ шероховатости, волнистости и некруглости поверхности. М.: Машиностроение, 1978. — 232 с.
- Ознобишин Н.С., Лурье A.M. Технический контроль в механических цехах. М.: Высшая школа, 1979. — 221 с.
- Жирнов В.Н. Исследование некоторых вопросов влияния макрогеометрии деталей в процессе их обработки при ремонте на селективную сборку: Дис. канд. техн. наук. М., 1972.-189 л.
- Билик Ш. М. Макрогеометрия деталей машин. 2-е изд. -М.: Машиностроение, 1972. — 344 с.
- Рыжов Э.В. Контактная жесткость деталей машин. М.: Машиностроение, 1966. — 196 с.
- Левина З.М., Решетов Д. Н. Контактная жесткость машин.- М.: Машиностроение, 1971. 264 с.
- Чижевский К.Г. Расчет круглых и кольцевых пластин. -Л.: Машиностроение, 1977. 184 с.
- Ляндон Ю.Н. Функциональная взаимозаменяемость в машиностроении. ГЛ.: Машиностроение, 1967. — 219 с.
- К.Hartmut, М. Schwertz Digitate Formprufung am Beispiel derE6enheitsmessung.- VDI~Z> i378tri2lts.9S1−987.
- Беспалов E.JI. Методика количественной оценки непрямолинейности и неплоскостности больших плоскостей. Вестник машиностроения, 1957, В 10, с. 29−33.
- Бычков О.Д. Математическая обработка результатов измерений при контроле неплоскостности поверхностей. Вестник машиностроения, 1969, J& I, с. 60−62.
- Тайц Б.А. Погрешность результата при контроле форды и взаимного положения поверхностей в ограниченном числе точек. -Измерительная техника, 1970, № 3, с. 21−23.
- Одитис И.А., Лукьянов B.C., Рудзит Я. А. О выборе длины трассы измерения среднего арифметического отклонения Raс заданной точностью. В кн.: Приборостроение. Рига, Изд-во Рижского политехнического института, 1972, вып. 6, с. I-I9.
- Schneider- С. А., Aachen H.G. Mefctattemrerar-fteLiuhq mii Tischrechner Bei der ErmittZunq geomet-rischer Fehier. VDI «1,1973, N21,3. 962−968.
- Филькин В.П., Колтунов И. Б. Измерительно-вычислительный комплекс для автоматического анализа погрешностей формы деталей. Вестник машиностроения, 1976, J? I, с. 25−27.
- Устройство обработки результатов измерений с использованием ЭКВМ / Бренер В. Н., Медреш В. Г. и др. Измерительная техника, 1979, 6, с. 24−25.
- Чернов В.Г. Выбор параметров частотно и время-импульсного преобразования для измерительно-информационных систем. -Метрология, 1979, № 6, с. 13−18.
- Сабиров М.Х. Анализ и обзор развития теории размерных цепей. Сб. научн. тр. / Моск. ин-т инженеров с.-х. пр-ва, 1978, т. ХУ, вып. 9, с. 14−21.
- Сабиров М.Х. Метод селективного регулирования жесткими компенсаторами. Сб. научн. тр. / Моск. ин-т инженеров с.-х. пр-ва, 1979, т. ХУ1, вып. 9, с. 26−31.
- Суханов В.А. Исследование деформаций и повреждений -образных блоков цилиндров и совершенствование технологииих ремонта с целью повышения послеремонтного ресурса на базе двигателя ЗИЛ-130: Дис. канд. техн. наук. М., 1978. — 195 л.
- Дунаев П.Ф. Размерные цепи. М.: Машгиз. 1963. -308 с.
- Полещенко П.В., Чернов Г. Г. Допуски и размерные цепи в сельскохозяйственных машинах. М.: Машгиз, 1963. — 255 с.
- Полещенко П.В. Некоторые особенности суммирования допусков во взаимосвязанных размерных цепях. М.: ЦБНТИ, 1957. -12 с.
- Маренич А.Я. Исследование и обоснование размерной цепи при ремонте главной передачи тракторов (на примере трактора Т-74): Дис. канд. техн. наук. М., 1971. — 138 л.
- Карепин П.А. Обоснование технических требований на предремонтное диагностирование тракторного двигателя (на примере кривошипношатунного механизма двигателя СВД-14): Дис. канд. техн. наук. М., 1981. — 137 л.
- Воронин А.В. Размерные цепи агрегатов в процессе сборки и эксплуатации. Автомобильная промышленность, 1977, № 5, с. 32−34.
- Дехтеринский J1.В. Некоторые теоретические вопросы технологии ремонта машин. М.: Высшая школа, 1970. -194 с.
- Дунаев П.Ф., Леликов О. П. Расчет допусков размеров. -М.: Машиностроение, 1981. 189 с.
- Расчет и оптимизация допусков на размеры восстанавливаемых деталей: Методические указания. 1-я ред. — М.: Госстандарт, ВНИИШШП, 1980. — 22 с.
- Цепи размерные. Расчет допусков с учетом условий контактного сопряжения деталей: Методические указания. М.: ВНШНМАШ, 1980. — 81 с.
- Цепи размерные. Основы метода оптимизированного подбора деталей в сборочные комплекты: Методические рекомендации. -М.: ВНИИНМАШ, 1982. 23 с.
- Цепи размерные. Расчет динамических размерных цепей. РД 50−426−83: Методические указания. М.: Изд-во стандартов, 1984. — 26 с.
- Справочник контролера машиностроительного завода: Допуски, посадки, линейные измерения / А. Н. Виноградов, Ю. А. Воробьев, Л. Н. Воронцов и др. Под ред. А. И. Якушева. 3-е изд., пе-рераб. и доп. — М.: Машиностроение, 1980. — 527 с.
- Якушев А.И. Взаимозаменяемость, стандартизация и технические измерения. 5-е изд., перераб. и доп. — М.: Машиностроение, 1979. — 343 с.
- Марков Н.Н., Кайнер Г. Б., Сацердотов П. А. Погрешность и выбор средств при линейных измерениях. М.: Машиностроение, 1976. 392 с.
- Воронин А.В. Оценка точности сборки подшипниковых автомобильных агрегатов. Автомобильная промышленность, 1978, J? 4, с. 4−6.
- Колесов И.М. Исследование связей между формой, поворотом и расстоянием плоских поверхностей деталей машин: Дис. д-ра техн. наук. М., 1962. -247 л.
- Hegi D. yWeotjonov l/.M. 2си» Aus^eriting iiSerzixhiioier Messungen Set der bestLmmuncj oier FormaBweichLLnqen. Feinqer&ietechnik Bd. 24, 1975, Nr5, s. 211−21^.
- Суриков А.Я. Технические пути повышения долговечности дорожных машин. М.: Высшая школа, 1972. — 96 с.
- Сергованцев В.Т., Бледных В. З. Вычислительная техника в инженерных и экономических расчетах. М.: Статистика, 1978. — 223 с.
- Завалишин Ф.С., Манцев М. Г. Методы исследований по механизации сельскохозяйственного производства. М.: Колос, 1982. — 231 с.
- Атлас конструкций автомобилей ГАЗ-бЗА, ГАЗ-66, ГАЗ-52−04. 2-е изд. — М.: Транспорт, 1979. -495 с.
- Подшипники качения: Справочник-каталог / Под ред.
- B.Н.Нарышкина, Р. В. Коросташевского. М.: Машиностроение, 1984. — 280 с.
- Испытания автомобилей / В. Б. Цимбалин, В. Н. Кравец,
- C.М.Кудрявцев, И. Н. Успенский, В. И. Песков М.: Машиностроение, 1978. — 199 с.
- Полушкин В.И. Исследование влияния технологических, эксплуатационных и конструктивных факторов на динамическую нагруженное ть главной передачи автомобиля средней грузоподъемности: Дис. канд. техн. наук. Горький, 1976. — 148 л.
- Статистические методы обработки эмпирических данных: Рекомендации / ВНИИНМАШ М., Изд-во стандартов, 1978. — 232 с.
- Мельников С.В., Алешкин В. Р., Рощин П. М. Планирование эксперимента в исследованиях Сельскохозяйственных процессов. -Л.: Колос, 1980. 168 с.
- Веденяпин Г. В. Общая методика экспериментального исследования и обработки опытных данных. М.: Колос, 1973. -199 с.
- Политова И.Д. Дисперсионный и корреляционный анализ в экономике сельского хозяйства. М.: Колос, 1978. — 192 с.
- Хованский Г. С. Номография и ее возможности. М.: Изд-во Наука, 1977. — 128 с.
- Методические указания по определению экономической эффективности использования новой техники, изобретений и рационализаторских предложений на предприятиях и в организациях системы «Союзсельхозтехника» / ВНИИПИ. М.: 1983. — 100 с.
- Автомобиль ГАЗ-бЗА: Типовые нормы времени на капитальный ремонт для специализированных предприятий. М.: ГОСНИТИ, 1977. — 99с.
- Анурьев В.И. Справочник конструктора-машиностроителя: В / 3-х т. М.: Машиностроение, 1980. — т. 3.- 5-е изд., пе-рераб. и доп. — 557 с.
- ПО. Расчеты экономической эффективности новой техники: Справочник / под ред. К. М. Великанова. Л.: Машиностроение, 1975. — 432 с.
- Методика определения цен на новую сельскохозяйственную технику /Под ред. М. П. Колотуркиной.- М.: Колос, 1969. 215 с.
- Дополнительный прейскурант № 24-I8−3I-I98I/2 / ЦНИИТЭИ. М.: ЦНИИТЭИ, 1981. — 12 с.
- Точность и производственный контроль в машиностроении: Справочник / И. И. Балонкина, А. К. Кутай, Б. М. Сорочкин, Б. А. Тайц.
- Под общ.ред. А. К. Кутая, Б. М. Сорочкина. Л.: Машиностроение, 1983. — 368 с.
- Справочная книга по технологии ремонта машин в сельском хозяйстве,/ Под ред. А. И. Селиванова. М.: Колос, 1975. -600 с.
- Рекомендации для расчета ремонтного фонда и производственных мощностей предприятий по ремонту агрегатов и узлов тракторов, комбайнов и автомобилей / ГОСНИТИ. М.: ГОСНИТИ, 1979. — 108 с.
- Результаты расчета на ЭВМ «НАИРИ-К» величины шага при дискретном контроле погрешности формы плоских деталей (среднеарифметические значения при с =* 1, мм)
- Установленная точность, А = 0,001 мм
- Допуск, мкм ! Длина детали, мм
- Продолжение прилож. 1 Установленная точность Л = 0,01 мм
- Ф «о t) t> <о со ss --а ел •¦а <Г4 см см in cm см
- OC0<0C0<0<0 • НИИ «14 п 1Л Ю Ю 1Л Ю9 is ч ч ^ ч п ч ч'^'аягэч'ч'чга
- IS К> IS Г* «О Ч> <М n-^^COyjr^Nri И N и*»• О ' —1 «I *»1.I t М ч>1.— «т ГП О I w С ю г^ «» t «I «I «» I
- II гзм II **
- II II CN СЧ а.1. II, а II II г 4с U II X
- X II II м M M M M M M м M M м м ^ Г4 14 м м м —1
ts '"¦ ч-: ' «» в г, ' Е ' к • «г Т ч •S • «5 к i 5 о t 2 4! - II II «сч S <9 Q 19 IS S <9 «а <9 X аз. •
- РГ II II в в S*"S>«i<5' в’Ц’в 15'в • в’Ч' в’в <5"в С is в ее в. Utir ' г- в <^» «5 В: 2 С3 и и ¦ • • ••••• • ¦ • • • • • • • • • • • • • X • к» • •> s Г5 iu РЭ
- II та и и и «4 И И v4 И см см см X to «г о» 45 о г> fS s о 19г- 1! II «я X к> СМ * • • • 1Г
- II IL' < ««с о R • СМ
- II, а а 1 W
- II ® S IS s s s s eg в в5 к Я S s S S S S cs о: S «с KI и «о Сч ю с о
- II ca S <9 в) 19 Ql <9 fa (9 is» см см ~ 1 см •
- И II о» *o ю о v аю № ю С"4 —• О» со IN tS> CS К п- «г 1Л ч- о>» ш в X ^ к>
- И II • • • ••••• «т т • • • • • • • • • • • • • s «X. • X UJ X
- Л. II — и со в) о гл w га 45 «т га ю ^ <> см «О э f» 3 CM Z3 ea Г»» X <9
- Ь. II II —4 сч с* —1 N —1 CJ см v* 9 < V* < см <с • • ^ ca m О ш
- X II II 1 1 1 1 1 1 1 к г э< X о» X fa Г»» ca X
- Ц м X II а. а о о о r*N «о ая II п ш ш <с fa п е- • • • ш
- II czl ч аэ ао ш ←* •"9с- II • и О о о кч v 1 о 1 ош и II о о ы см о1. С4 Ю чгd CN (Ч N7 It м и |1. О.а.