Проект реконструкции производственной базы «Костанайавтотранс»
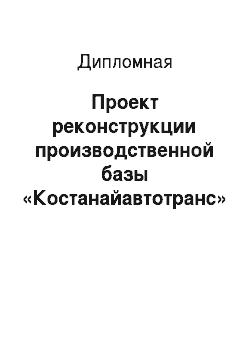
Количество автобусов в бывшем предприятии «Автобусный парк» поддерживалось до 90-х годов. Однако начиная с 1996 г их число стало сокращаться быстро, примерно 9% в год. Более устойчивое положение этой части автотранспортного предприятия объясняется существовавшей до середины 90-х годов государственной поддержкой городских пассажирских перевозок. На протяжении длительного периода, еще с советских… Читать ещё >
Проект реконструкции производственной базы «Костанайавтотранс» (реферат, курсовая, диплом, контрольная)
СОДЕРЖАНИЕ ВВЕДЕНИЕ
1. ОБЩИЕ СВЕДЕНИЯ ОБ АВТОПРЕДПРИЯТИИ «КОСТАНАЙАВТОТРАНС»
2. ПРОЕКТНАЯ ЧАСТЬ
2.1 Роль и цели автомобильного транспорта
2.2 Цели технической эксплуатации автомобильного транспорта
2.3 Анализ технического состояния автобусного парка
2.4 Испытания кузовов автобусов
2.5 Определение количества автобусов, нуждающихся в ремонте несущего основания кузова
3. ТЕХНОЛОГИЧЕСКАЯ ЧАСТЬ
3.1 Режим работы и фонды времени
3.2 Расчет трудоемкости
3.3 Определение годовой производственной программы
3.4 Расчет годового объема работ и численности рабочих
3.5 Расчет количества оборудования
3.6 Подбор технологического оборудования
3.7 Расчет площади участка
3.8 Объемно — планировочные и конструктивные решения
4. ТЕХНОЛОГИЯ РЕМОНТА АВТОБУСОВ
4.1 Технологический процесс капитального ремонта двигателя, коробки передач и сцепления
4.2 Технологический процесс разборки-сборки двигателя, коробки передач и сцепления
4.3 Участок капитального ремонта силовых агрегатов
4.4 Расчет количества и подбор технологического оборудования и технологическая компоновка участка
4.5 Устройство технологического оборудования
4.6 Расчет площади помещения
4.7 Планировка производственного участка
5. ОХРАНА ТРУДА
5.1 Анализ опасности и вредности
5.2 Обеспечение безопасности
6. ОХРАНА ОКРУЖАЮЩЕЙ СРЕДЫ
7. РАСЧЕТ ОСНОВНЫХ ЭКОНОМИЧЕСКИХ ПОКАЗАТЕЛЕЙ
7.1 Расчет капитальных затрат и фонда оплаты труда
7.2 Расчет текущих затрат на выполнение ремонтных работ и удельной себестоимости работ ЗАКЛЮЧЕНИЕ СПИСОК ИСПОЛЬЗОВАННОЙ ЛИТЕРАТУРЫ
ВВЕДЕНИЕ
Рост автомобильного парка нашей страны способствовал созданию новой отрасли — авторемонтного производства.
Потребность в ремонте машин не является случайной. Она возникает вместе с появлением машин, и, следовательно, деятельность человека, направленная на удовлетворение этой потребности, т. е. ремонт машин, существует столько же, сколько существует машина.
Авторемонтное производство повышает срок службы автомобиля и таким образом увеличивает парк автомобилей страны и обеспечивает эксплуатационную надежность подвижного состава автомобильного транспорта.
Направление развития авторемонтных предприятий обусловлено главным образом работой, выполняемой автомобилями.
На автомобильном транспорте, выполняющем централизованные перевозки пассажиров и грузов, автомобили эксплуатируются более интенсивно с большими годовыми пробегами, вызывающими износы деталей и механизмов. Поэтому эти автомобили подвергают строгому планово — предупредительному обслуживанию и ремонту вплоть до замены во время эксплуатации отдельных агрегатов и капитального ремонта полнокомплектных автомобилей.
Из общего количества перевозимых пассажиров на его долю приходится 53%. Основой эффективной работы автобусов является обеспечение высокой надежности — способности безотказно выполнять транспортную работу с сохранением во времени установленных параметров в заданных пределах для конкретных режимов и условий эксплуатации. Опыт эксплуатации автобусов показывает, что общий ресурс автобуса напрямую зависит от надежности и совершенства конструкции кузова. Подавляющее большинство кузовов автобусов являются несущей конструкцией (безрамными), и по выходе из строя кузова автобус списывают в утиль. Поэтому сохранению кузова в надлежащем техническом состоянии, путем обеспечения своевременного и качественного ремонта придают исключительно большое значение.
Благодаря ремонту срок службы автобусов значительно повышается. Объем перевозок, приходящихся на долю капитально отремонтированных автобусов, составляет 40% от общего объема перевозок пассажиров автобусами и в дальнейшем еще более увеличится.
Авторемонтное производство по своей природе динамично. Постоянно растущая потребность в ремонтах автомобилей, прогрессивные изменения их конструкции, ремонтного оборудования и технологии ремонта требуют непрерывного совершенствования авторемонтного производства, реконструкции действующих предприятий.
Актуальностью в дипломной работе является предложение реконструкции производственных участков в «Костанайавтотранс». На базе жестяно-сварочного участка планируется установка дополнительного оборудования предназначенного для изготовления ремонтных деталей, проведения дефектоскопии кузова без его разборки, устранения повреждений кузова и его несущей системе, а также организация работы по оказанию услуг автотранспортным предприятиям в ремонте кузовов автобусов.
Практическая ценность результатов нашей работы подтверждается наличием акта о внедрении.
Теоретическая ценность нашей дипломной работы состоит в расчете и его подробном описании.
Целью дипломной работы являлось организация мер по реконструкции производственной базы «Костанайавтотранс» для снижения текущих затрат на осуществление ремонтных услуг.
Для реализации идеи реконструкции в условиях «Костанайавтотранс» необходимо решить следующие задачи:
— доказать целесообразность организации поста по ремонту кузовов автобусов с технической экономической точки зрения;
— разработать технологические процессы ремонта кузовов автобусов;
— подобрать необходимое производственное оборудование и технологическую оснастку;
— изучить влияние производственных процессов на окружающую среду и человека, т. е. решить вопросы охраны труда и экологии.
Поставленные задачи и порядок их решения, определили структуру дипломной работы.
Для решения указанных задач и в соответствии с целью работы, были использованы следующие методы:
Теоретические: анализ научной, технической, нормативной и учебной литературы по теме исследования, систематизирование собранных и проанализированных данных.
Практические: расчет, методы математической статистики, эксперимент.
1. ОБЩИЕ СВЕДЕНИЯ ОБ АВТОПРЕДПРИЯТИИ «КОСТАНАЙАВТОТРАНС»
Количество автобусов в бывшем предприятии «Автобусный парк» поддерживалось до 90-х годов. Однако начиная с 1996 г их число стало сокращаться быстро, примерно 9% в год. Более устойчивое положение этой части автотранспортного предприятия объясняется существовавшей до середины 90-х годов государственной поддержкой городских пассажирских перевозок. На протяжении длительного периода, еще с советских времен, этот вид транспортной деятельности считался социально важным и дотировался из других источников. Но экономический кризис лишил государство и местные исполнительные органы всяких возможностей для «спонсорства» в этой области ввиду отсутствия средств на обслуживание и ремонт. Большой процент автобусов стал интенсивно выводиться из эксплуатации. И город стал склоняться к новой модели обслуживанияпринципу частной собственности, конкурентной борьбы и полной самоокупаемости транспортных компаний. Этот, так называемый, рыночный вариант системы городского пассажирского транспорта не требует какого-либо перераспределения бюджетных средств для поддержания городских пассажирских перевозок, потому что финансовые издержки по их обеспечению принимают на себя транспортные компании, получившие доступ к рынку по установленным местными властями правилам. Преимущество рыночной модели городского пассажирского транспорта заключается в прямом взаимоотношении «перевозчик-клиент», без каких-либо посреднических услуг. Одним из таких предприятий и стало транспортное предприятие «Костанайавтотранс», преобразовавшееся в новую компанию с 2002 г. во главе с Шаяхметовым М. Б. В настоящее время вышеназванное предприятие насчитывает на своей базе 120 автобусов, как собственных парковых, так и привлеченных (наем с личным транспортом). Оно является одним из звеньев в организации перевозок пассажиров городским автомобильным транспортом. Для водителей предприятия предоставляется комната отдыха, комната диспетчерского сообщения, которая оснащена необходимыми средствами связи: телефонной, радиосвязью, компьютерами. Также есть столовая для обеспечения пищей водителей, работников диспетчерского персонала, ремонтных и др. рабочих.
Одними из распространенных видов транспорта нашего города является в последнее время автобусы Икарус-280, МАН, Ивеко, Мерседес.
Главным звеном в транспортном процессе пассажирского автомобильного транспорта является перевозочный процесс, непосредственно осуществляющий конечную цель и основное значение системы. Рассмотрим основные цели функционирования системы пассажирского автомобильного транспорта.
К ним относятся:
— наиболее полное и своевременное удовлетворение потребностей населения в перевозках по каждому виду сообщения.
— высокая культура обслуживания и высокое качество работы.
— полная безопасность движения транспортных средств.
— эффективное использование подвижного состава.
— организация полного сбора доходов (оплаты проезда пассажирами)
— обеспечение рациональных условий научной организации труда рабочих, ИТР и служащих.
— оптимизация системы оплаты труда
— минимальные трудовые, материальные и финансовые затраты на функционирование системы.
Рациональная система управления оказывает существенное влияние на своевременное достижение и обеспечение конечной цели эффективной деятельности пассажирского автотранспорта.
Подвижной состав пассажирского автомобильного транспорта общего пользования оказывает значительное влияние не только на условия и качество транспортного обслуживания населения, но и на выбор рациональной системы эффективной организации перевозок, установление целесообразного режима труда и отдыха водителей, а так же влияет на экономические результаты основной деятельности транспортных предприятий. Городские автобусы предназначены для массовых перевозок в городах с различной численностью населения при хорошей дороге.
2. ПРОЕКТНАЯ ЧАСТЬ
2.1 Роль и цели автомобильного транспорта Автомобильный транспорт играет существенную роль в транспортном комплексе страны, регулярно обслуживая почти около миллиона предприятий и организаций всех форм собственности, крестьянских и фермерских хозяйств и предпринимателей, а также населения страны. В двухтысячном году автомобильный парк РК двадцати миллионов единиц, причем более 85% легковых и грузовых автомобилей и автобусов принадлежат гражданам на условиях личной собственности. Согласно данным Министерства транспорта РК, численность субъектов, осуществляющих автотранспортную деятельность, превысила рубеж в ста семьдесят тысяч, из них 61% - предприятия и 39% - физические лица. Согласно оценкам, вклад автомобильного транспорта в перевозки грузов составляет 77%, а пассажиров (без индивидуального легкового) — 53−55%. Регулярными автомобильными перевозками (основными в пассажирских перевозках) охвачено 1,3 тыс. городов и 78,9 тыс. сельских населенных пунктов. Общее число автобусных маршрутов протяженностью 0,9 млн. км превысило 12 тыс., из них 30% - городские, 49% - пригородные, 21% - междугородные и международные.
Целью автомобильного транспорта как сектора транспортного комплекса страны является удовлетворение потребности экономики и населения страны в грузовых и пассажирских перевозках при минимальных затратах всех видов ресурсов. Эта цель обеспечивается в результате повышения показателей эффективности автомобильного транспорта: роста производительности транспорта и транспортных средств; сокращения себестоимости перевозок; повышения производительности труда персонала; обеспечения безопасности транспортного процесса.
2.2 Цели технической эксплуатации автомобильного транспорта автобус ремонт кузов двигатель В качестве подсистемы автомобильного транспорта техническая эксплуатация автомобиля должна, во-первых, способствовать реализации целей автомобильного транспорта, во-вторых, иметь управляемые показатели эффективности, связанные с показателями эффективности системы, т. е. автомобильного транспорта.
Основными целями (и одновременно показателями эффективности) технической эксплуатации автотранспорта являются: обеспечение необходимого уровня работоспособности парка для реализации транспортного процесса; сокращение на обеспечение работоспособности (этот показатель влияет на себестоимость перевозок и конкурентоспособность); повышение производительности труда персонала, занятого техническим обслуживанием и ремонтом подвижного состава; сокращение отрицательного влияния автомобильного транспорта на население, обслуживающий персонал и окружающую среду.
Влияние технической эксплуатации автотранспорта на себестоимость перевозок определяется непосредственно статьями расходов на техническое обслуживание и ремонт, а также косвенным влиянием технической эксплуатации автотранспорта на другие статьи себестоимости. Непосредственные затраты на техническое обслуживание и ремонт, включая капитальный ремонт транспорта, накладные расходы инженерно-технической службы, составляют около 22−26% себестоимости перевозок. Уровень организации и качества технической эксплуатации автотранспорта оказывает существенное влияние на ряд других статей себестоимости перевозок, в частности на затраты на топливо — смазочные и эксплуатационные материалы. В общей сложности 45−50% себестоимости перевозок прямо или косвенно зависит от качества и эффективности технической эксплуатации автомобилей.
От качества работы служб технической эксплуатации автотранспорта зависит:
1. Загрязнение окружающей среды автотранспортом, особенно недостаточно удовлетворительного технического состояния, а также отходами, образующимися при хранении, заправке, техническом обслуживании и ремонте автотранспорта;
2. Безопасность транспортного процесса, количество дорожно-транспортных происшествий, вызванных технической неисправностью автомобилей;
3. Количество несчастных случаев и профессиональных заболеваний персонала инженерно-технической службы.
2.3 Анализ технического состояния автобусного парка В нашей стране среди всех видов пассажирского транспорта автобусный является самым массовым. Из общего количества перевозимых пассажиров на него приходится 53%.
На сегодня приоритетной задачей подразделений технического надзора является снижение количества ДТП, совершаемых по вине водителей автобусов. При изучении обстоятельств дорожно-транспортных происшествий установлено, что главными причинами аварий явились грубые нарушения правил эксплуатации транспортных средств и неудовлетворительное техническое состояние транспортных средств. Более того, в ходе расследований выявлены факты несанкционированных изменений конструкции автобусов. В частности, случаи установки дополнительных топливных баков, организации спальных мест вместо пассажирских сидений, блокирования запасных выходов. Кроме того, во многих автохозяйствах не проводится предрейсовый осмотр автобусов, ослаблены службы технической эксплуатации. Практически везде сокращены отделы безопасности дорожного движения, которые по идее должны существовать в каждом автобусном парке. В итоге при обследовании автотранспортных предприятий в 2008 году выявлено технически неисправных автобусов на 4,1% больше по сравнению с 2007 годом.
При длительной эксплуатации автобусный парк достигает такого состояния, когда затраты средств и труда, связанные с поддержанием его в работоспособном состоянии, превосходят доходы, поступающие от дальнейшей эксплуатации (пассажирских перевозок). Такое состояние автобуса считается предельным и обусловлено неравнопрочностью его деталей и агрегатов. Известно, что создать равнопрочную машину, все детали которой изнашивались бы равномерно и имели бы одинаковый срок службы практически невозможно. Следовательно, ремонт подвижного состава даже только заменой некоторых деталей, имеющих небольшой ресурс, всегда целесообразен и с экономической точки зрения оправдан.
Основным источником экономической эффективности ремонта автобусов является использование остаточного ресурса их деталей. Около 50% деталей автобуса прошедших срок службы до ремонта, имеют остаточный ресурс и могут быть использованы повторно либо без ремонта, либо после ремонтного воздействия.
Для поддержания надежности и работоспособности кузова автобуса в эксплуатации необходимо выполнить работы по техническому обслуживанию и ремонту. Экономически эффективное использование ресурса долговечности парка автобусов обусловливает необходимость текущего и капитального ремонта.
В «Костанайавтотранс» уже осуществляют техническое обслуживание и ремонт кузовов автобусов, а в результате реконструкции будет установлено дополнительное оборудование, позволяющее механизировать технологические процессы по техническому обслуживанию и ремонту кузовов автобусов.
В результате реконструкции агрегатного участка, предприятие сможет на современном техническом уровне обслуживать не только собственный автобусный парк, но и автобусы, принадлежащие предприятиям, организациям и населению города. Реконструкция — это способ развития и совершенствования номенклатуры услуг. Для организаций и населения города будут доступны следующие услуги:
Ремонт деталей несущего основания кузова автобуса
— ремонт рамы;
— ремонт консолей;
— изготовление стоек салона кузова;
— изготовление и замена порогов;
— изготовление и замена наружных панелей;
— изготовление и замена внутренних панелей;
— ремонт поперечных изломов в фермах и балках кузова;
— ремонт каркаса фермы пола, ремонт боковых ферм.
Ремонт узлов и деталей арматуры кузова автобуса
— ремонт и установка поручней;
— ремонт остовов сидений;
— ремонт и установка дверей;
— настилка линолеума или резинового покрытия на пол;
— снятие и установка молдингов;
— замена поврежденных стекол кузова.
2.4 Испытания кузовов автобусов Автобус направляется в капитальный ремонт при необходимости капитального ремонта кузова. За срок службы автобус подвергается не более одному капитальному ремонту, не считая капитальный ремонт агрегатов и узлов до и после капитального ремонта автобуса.
С увеличением долговечности кузова полнокомплектный ремонт автобуса максимально ограничивается до полного исключения за счет замены агрегатов и узлов, требующих капитальный ремонт, на исправные, взятые из оборотного фонда. Но пока долговечность кузовов ниже ресурса силового агрегата или моста. Поэтому после списания кузова в утиль, агрегаты автобуса включают в оборотный фонд предприятия.
На предприятии провели форсированные испытания автобусных кузовов. По результатам испытаний можно понять насколько важно качественно и своевременно осуществлять ремонт кузова автобуса.
Надежность конструкций автотранспортных средств можно оценивать двумя способами: либо по статистике реальной эксплуатации, либо по результатам специальных испытаний. Первый способ, очевидно, точнее. Зато второй — быстрее, что особенно важно для вновь создаваемой техники: он позволяет оценить зависимость надежности автобуса от главных эксплуатационных факторов — усталости материала от действия переменных нагрузок и изнашивания. При чем оценить за сравнительно непродолжительное время. На предприятии идут по второму пути, применяя свою, во многом оригинальную технологию. Ее главное отличие от традиционных технологий состоит в том, что проверяется несущая способность конструкции не только в стандартных, но и самых разных встречающихся в эксплуатации условиях нагружения.
Доказано, что зонами значительных по величине сосредоточенных сил являются, независимо от конструкции кузова, места крепления к нему элементов подвески и рулевого управления, а скручивающие статические и динамические нагрузки больше влияют на усталостную долговечность элементов каркаса кузова, обшивки, основания, рамы, причем это влияние напрямую зависит от конструкции (безрамная, с несущим основанием, закрытого типа). Для безрамных несущих и безрамных с несущим основанием кузовов опаснее всего вибрационные нагрузки, за ними скручивающие и изгибающие, а влияние инерционных нагрузок незначительно.
В качестве объекта были взяты автобусы Павловского автобусного завода. Пробеговым испытаниям и исследованиям нагруженности были подвергнуты два новых автобуса ПАЗ-3205. При этом один из них (образец № 1) подвергался активному и равномерному воздействию коррозии: через каждые 300 км пробега его на 6 часов помещали в коррозионную камеру.
У обоих автобусов на специальных дорогах кузова повреждались так же, как и в эксплуатации: появились трещины на нижних полках задних и средних лонжеронов, на поперечных и консолях, разрушались опоры рессор. Но у автобуса, подвергавшегося активному воздействию коррозии, неисправности возникли при меньшем в 1,5−2 раза пробеге, чем у второго автобуса, не подвергавшегося воздействию коррозии. Кроме того, на панелях его крыши, боковин, на каркасе, дверях и т. д. образовалась сплошная ржавчина со значительным (до 50−60%) коррозионными потерями. Все это заставило проверить, как изменяется угловая жесткость кузова в процессе эксплуатации. Установлено (таблица 2.1), что после пробега 300−350 тыс. км угловая жесткость их кузовов снижается до 1,0*10−4 — 1,5*10−4 Нм/рад. У автобусов же, проходивших полигонные испытания и достигших по кузову предельного состояния, угловая жесткость уменьшилась на 60−70% и составила 2,25*10−4 — 2,28*10−4 Нм/рад.
Таблица 2.1
Зависимость угловой жесткости от пробега автобуса
Параметр | Полигонные испытания автобусов | Автобус, поступивший в капитальный ремонт | |||||||||||||
№ 1 | № 2 | № 3 | № 4 | № 5 | № 6 | № 7 | № 8 | № 9 | № 10 | № 11 | № 12 | ||||
Пробег к моменту определения жесткости, тыс. км | 9,9 | 117,6 | |||||||||||||
Угловая жесткость, Нм/рад 10−4 | 338,2 | 115,4 | 332,8 | 110,3 | 221,6 | 111,5 | 115,2 | 110,5 | 9,9 | 88,1 | 11,8 | 6,9 | 9,0 | ||
Таким образом, результаты исследования оказывают, что снижению угловой жесткости способствует разрушения силовых элементов несущей системы, разрушения кузовного оборудования и ослабление соединений внешних и внутренних панелей, связанные с силовым воздействием дороги и активным коррозионным воздействием.
Режим форсированных полигонных испытаний по своему воздействию на элементы несущих систем кузова равноценен 5−7 годам реальной эксплуатации. В качестве количественного критерия предельного состояния несущей системы в первом приближении можно принять снижение угловой жесткости кузова автобуса на 60- 70%, что соответствует пробегу в 350 — 400 тыс. км.
Кузов подвергается не более, чем одному капитальному ремонту, а силовые агрегаты и мосты капитально ремонтируются не менее 3 раз. Поэтому получается, что срок службы силовых агрегатов и мостов (с учетом всех капитальных ремонтов) на 10−25% больше чем у кузова. Нормы пробега до капитального ремонта кузова и основных агрегатов приведены в таблице 2.2.
Таблица 2.2
Нормы пробега кузовов и основных агрегатов автобусов до первого капитального ремонта
Модель автобуса | Норма пробега, тыс. км | ||||||
кузова | двигателя | КПП, ГМП | переднего моста | заднего моста | рулевого управления | ||
МАН Ивеко ЛиАЗ-5256 Икарус-260.18 | 350 400 450 360 | ||||||
Известно, что после первого капитального ремонта работоспособность агрегата восстанавливается на 80%, после второго капитального ремонта на 60%.
Совершенство конструкции автобусов способствует повышению технико-эксплуатационных свойств и значительному увеличению ресурса агрегатов.
2.5 Определение количества автобусов, нуждающихся в ремонте несущего основания кузова Автобусный парк «Костанайавтотранс» состоит из 64 автобусов различных марок и моделей. Перечень автобусов по годам ввода в эксплуатацию приведен в таблице 2.3.
Таблица 2.3
Перечень автобусов по годам ввода в эксплуатацию
Марка автобуса | Количество, шт. | Год ввода в эксплуатацию | |||||||||||||
До 1990 | |||||||||||||||
МАН Ивеко ЛиАЗ-5256 Икарус Лаз | |||||||||||||||
Техническое обслуживание кузовов автобусов, включает ежедневное обслуживание, первое, второе технические обслуживания и сезонное обслуживание.
Первое техническое обслуживание (ТО-1) проводится через каждые 3 тыс. км. Второе техническое обслуживание (ТО-2) чаще всего осуществляется после текущего ремонта (ТР), поэтому их периодичность практически совпадает и составляет 12 тыс. км. Известно, что среднегодовой пробег автобуса в составляет 39,8 тыс. км в результате получается, что в течение года ТО-1 автобусы проходят примерно тринадцать раз, а ТО-2 и ТР по три раза.
ТО-1 и ТО-2 проводится на универсальных постах в основном производственном корпусе. ТР кузовов автобусов выполняется только на жестяно-сварочном участке, который находится отдельно от основного производственного корпуса.
Для того, чтобы определить какое количество автобусов нуждается в ремонте несущей системы кузова, необходимо провести простой расчет.
Определим срок службы кузова Q, лет:
Из форсированных испытаний известно (раздел 2.4), что кузов достигает предельного состояния через 350 — 400 тыс. км, данный пробег назовем пробегом при достижении которого кузов достигает предельного состояния (Тп.с.).
Среднегодовой пробег автобуса (Тср. год) составляет 39,8 тыс. км. По формуле (1) определим срок службы кузова:
. (2.1)
Результат деления Тср. год на Тп.с. означает, что кузов достигнет предельного состояния, через 9 лет.
Анализ таблицы 2.3 показал, что 46 автобусов эксплуатируется более 9 лет, можно предположить, что эти автобусы нуждаются в ремонте кузова. Поэтому повышение уровня технического обслуживания и ремонта на жестяно-сварочном участке экономически целесообразно.
На базе предприятия возможна организация работы по оказанию услуг автотранспортным предприятиям в ремонте кузовов автобусов на коммерческой или договорной основе. Услуги по ремонту кузовов направлены на узкий сегмент транспортного рынка, который составляют организации и предприятия, осуществляющие пассажирские перевозки.
Техническое состояние автобусного парка считается удовлетворительным, так как его основную часть составляют автобусы до 2000 года выпуска.
В автобусном парке, который составляют автобусы, эксплуатируемые не более пяти лет, наблюдается сокращение коэффициента технической готовности с 0,98 до 0,78, среднесуточного пробега — с 200 до 140.
Требования к техническому состоянию, дорожной и экологической безопасности автобусов повлияют на развитие потребности в услуге ремонта кузовов автобусов. На предприятии в свою очередь сделает все возможное для реализации первоочередных мероприятий, направленных на создание условий осуществления услуг ремонта автобусов, на рынке транспортных услуг города Костаная.
Развитие конкуренции на транспортном рынке требует от предприятия детального и оперативного учета и оценки статей расходов и доходов полученных при оказании услуг. Выход с новой услугой осуществляется в совершенно свободную нишу транспортного рынка, так как нет конкуренции.
Предприятие, которое восстанавливает работоспособность собственного подвижного состава путем качественного ремонта изношенных кузовов. Конкуренцию для предприятия не составит, так как не оказывает услуги по техническому обслуживанию и ремонту транспортных средств, принадлежащих физическим и юридическим лицам.
Для того чтобы привлечь предприятия и организации к деятельности, необходимо провести комплекс информативной рекламы. Задачей информативной рекламы является донесение до автотранспортных предприятий и организаций информации о новых услугах. Комплекс рекламы включает в себя: рекламное обращение в прессе и прямую почтовую рекламу. Данный рекламный комплекс экономичен, а главное целенаправлен, т. е. рассчитан на конкретных потребителей.
3. ТЕХНОЛОГИЧЕСКАЯ ЧАСТЬ
3.1 Режим работы и фонды времени В результате реконструкции агрегатного участка автотранспортного управления, его режим работы и фонды времени не изменятся.
Под режимом работы участка понимают количество рабочих дней в году, количество смен работы, длительность смены и рабочей недели в часах.
Количество рабочих дней в году зависит от того, является ли данное производство прерывным или непрерывным. Производственный процесс жестяно-сварочного участка осуществляется в одну смену с перерывами в выходные и праздничные дни. Режим работы агрегатного участка представлен в таблице 3.1.
Таблица 3.1
Режим работы агрегатного участка
Данные | Пятидневная неделя | |
Количество календарных дней в году | ||
Количество рабочих дней в году | ||
Количество праздничных дней в году | ||
Количество дней отдыха | ||
Количество сокращенных рабочих дней в году | ||
Длительность рабочей недели, ч | ||
Длительность смены, ч | 8,2 | |
Исходя из режима работы агрегатного участка, возможно подсчитать фонды времени работы оборудования и рабочих. Различают два вида годовых фондов времени: номинальный и действительный.
Номинальный годовой фонд времени рабочего Тф.н. определяется количеством рабочих дней в году и продолжительностью рабочих недель:
Тф.н. = (365 — (104 +11)) tсм +11 (tсм — tсок) — 8 (tсм — tсок), (3.1)
где 365 — число календарных дней в году;
104 — число выходных дней в году;
11 — число праздничных дней в году;
8 — число предпраздничных дней в году;
tсм — продолжительность удлиненной смены, ч;
tсок — продолжительность смены в предпраздничный день, ч.
По данным таблицы 3.1 получим:
Тф.н. = [365 — (104 +11))tсм +11(tсм — tсок) — 8(tсм — tсок)] = [365 — (104+11))8,2+11(8,2 — 7,2) — 8(8,2 — 7,2)] = 2053 ч.
Действительный годовой фонд времени рабочего Тф.д. определяется как разность номинального годового фонда и величины неизбежных потерь рабочего времени:
Тф.д.=Тф.н. — Тп, (3.2)
где Тф.н. — номинальный годовой фонд времени рабочего, ч;
Тп — неизбежные потери рабочего времени, ч.
Неизбежные потери рабочего времени составляют 48 ч.
Тогда:
Тф.д. = Тф.н. — Тп = 2053 — 48 = 2005 ч Неизбежные потери рабочего времени учитывают продолжительность профессиональных отпусков, учебных отпусков, отпусков по болезни, а также отпусков, связанных с выполнением государственных обязанностей и прочими уважительными причинами.
Номинальным годовым фондом времени работы оборудования Тф.о.н. называется время в часах, в течение которого может работать оборудование при заданном режиме работы. Номинальный годовой фонд времени работы оборудования не может быть полностью использован, так как имеются неизбежные простои оборудования в ремонтах. Числовые значения номинальных фондов времени рабочего и оборудования при односменной работе идентичны.
Действительный годовой фонд времени работы оборудования Тф.о.д. представляет собой время в часах, в течение которого оборудование может быть полностью загружено производственной работой:
Тф.о.д.=Тф.о.н. 0, (3.3)
где Тф.о.н. — номинальный годовой фонд времени работы оборудования, ч;
0 — коэффициент использования оборудования, учитывающий простои оборудования в ремонтах (его принимают равным 0,93 ч 0,98).
Принимаем, что 0= 0,97. Тогда получим:
Тф.о.д. = Тф.о.н. 0= 20 530,97 = 1991,4 ч.
3.2 Расчет трудоемкости Трудоемкостью продукции называется время, которое нужно затратить производственным рабочим непосредственно на выработку данной продукции. Трудоемкость выражают в человеко-часах. Часто трудоемкость измеряют в нормо-часах, то есть то время, которое надо затратить на ремонт изделия по действующим (плановым) нормам. Нормы трудоемкости (t) на разборку-сборку и ремонт деталей взяты из карт технологических процессов. Их выбирают по видам работ, по постам или по типам оборудования.
Трудоемкость определяется по следующей формуле:
(3.4)
где K1 — коэффициент приведения, учитывающий конструктивно-технологические особенности объекта ремонта;
К2 — коэффициент приведения, учитывающий масштаб производства (годовую программу предприятия, участка, поста);
К3 — коэффициент приведения, учитывающий количество ремонтируемых автомобилей;
К4 — коэффициент приведения, учитывающий соотношение в программе предприятия полнокомплектных автомобилей и комплектов агрегатов;
tэ — трудоемкость агрегата для эталонных условий, чел-ч.
По формуле (3.2) рассчитаем трудоемкость кузовных, жестяно-сварочных работ:
Коэффициенты приведения взяты из справочника.
Нормы трудоемкости должны быть прогрессивными, т. е. определены на основе передового опыта, новейших достижений науки и техники и лучших проектных решений.
3.3 Определение годовой производственной программы Годовая производственная программа выражается в количестве ремонтируемых автомобилей, в нашем случае автобусов.
Агрегатный участок предварительно рассчитан на техническое обслуживание и ремонт собственного автобусного парка, состоящего из 64 автобусов марок ЛиАЗ, ЛАЗ, Икарус, МАН. На данный момент известно, что 46 автобусов нуждаются в ремонте элементов несущего основания кузова. Ремонт несущей системы кузова будет возможен после реконструкции агрегатного участка.
По данным автоинспекции, в городе Костанай зарегистрировано 800 автобусов различных моделей, принадлежащих юридическим и физическим лицам. Более 90% автобусов принадлежит автотранспортным предприятиям и организациям, выполняющим перевозочный процесс. Не каждое предприятие имеет собственную производственную базу, т. е. многие являются специализированными транспортными предприятиями. Поэтому при организации работы по оказанию услуг автотранспортным предприятиям в ремонте кузовов автобусов целесообразно рассчитывать на 10% от числа автобусов, зарегистрированных в нашем городе.
Согласно вышесказанному, годовую производственную программу агрегатного участка принимаем в количестве 120 автобусов.
В будущем возможен рост производственной программы за счет увеличения обслуживаемых автобусов, принадлежащих организациям и предприятиям.
3.4 Расчет годового объема работ и численности рабочих Годовым объемом работ называют время, которое нужно затратить производственным рабочим для выполнения годовой производственной программы. Годовой объем работ представляет собой годовую трудоемкость ремонта агрегатов и выражается в человеко-часах (чел-ч). Годовой объем работ Тгд подсчитывается по формуле:
(3.5)
где t — трудоемкость на автомобиль (агрегат), ч;
N — годовая производственная программа, шт.
Так как N=120 шт, то:
.
Количество производственных рабочих определяется как частное от деления годового объема работ на годовой фонд времени рабочего. Различают списочный и явочный состав рабочих.
Списочный состав — это полный состав рабочих, включающий в себя как фактически явившихся на работу, так и находящихся в отпусках и отсутствующих по прочим уважительным причинам.
Явочный состав — это количество рабочих, фактически явившихся на работу.
Списочное количество рабочих определяется по следующей формуле:
(3.6)
где Тг.д. — годовой объем работы поста, чел-ч;
Тф.д. — действительный годовой фонд времени рабочего, ч.
Явочное количество рабочих рассчитывается по выражению:
(3.7)
где Тг.д. — годовой объем работы поста, чел-ч;
Тф.н. — номинальный годовой фонд времени рабочего, ч.
Зная, что Тг.д. = 21 568 чел-ч, а Тф.д. = 2005 ч, Тф.н. = 2053 ч, Списочное количество рабочих в среднем на 10 — 12% превышает явочное количество.
Кроме основных производственных рабочих, непосредственно выполняющих технологические операции (слесари, сварщики и др.), имеются еще вспомогательные рабочие. К ним относятся рабочие, не принимающие непосредственного участия в технологических операциях, выполняемых на участке, посту (уборщики, транспортные рабочие и т. п.). Число вспомогательных рабочих mвсп. определяют в процентах от списочного числа производственных рабочих:
(3.8)
где П — процент вспомогательных рабочих (П = 0,25 — 0,35).
Тогда:
Таким образом, всего на агрегатном участке работают 15 человек (явочное количество рабочих). Из них 7 человек осуществляют основные ремонтные работы (ремонт несущей системы, оперения, узлов и деталей арматуры салона кузова). Двое рабочих проводят приемку кузова в ремонт и его дефектовку для выявления скрытых повреждений. Частичную разборку кузова перед дефектовкой и ремонтом выполняют три человека. Вспомогательные рабочие участвуют при частичной разборке кузова и основных ремонтных операциях.
3.5 Расчет количества оборудования Число единиц технологического оборудования рассчитывают или подбирают. Методы расчета зависят от назначения оборудования и характера технологических операций, выполняемых на нем.
Существуют три метода расчета:
по трудоемкости технологических операций;
по продолжительности технологических операций;
по физическим параметрам ремонтируемых агрегатов, узлов (массе и площади поверхности) В соответствии с этими методами оборудование подразделяют на три группы. Таким образом, оборудованию каждой группы присущ определенный метод расчета.
По трудоемкости технологических операций рассчитывается оборудование, применение которого связано с ручным или машинно-ручным способом работы (оборудование для кузовных, жестяницких, медницких, радиаторных работ, разборочно-сборочное оборудование). Количество единиц оборудования определяется по следующей формуле:
(3.9)
где Тг.д. — годовой объем работ, чел-ч;
Тф.о.д — действительный годовой фонд времени работы оборудования, ч.
По продолжительности технологических операций рассчитывают число единиц технологического оборудования для наружной мойки шасси автомобиля и агрегатов, для испытания агрегатов и автомобилей, для сушки изделий после покраски. Число единиц оборудования определяют по выражению:
(3.10)
где t0 — продолжительность технологической операции, ч;
N — годовая производственная программа предприятия, участка, шт;
n — число изделий, ремонтируемых одновременно на каждой единице оборудования, шт.
По физическим параметрам ремонтируемых агрегатов, узлов, изделий рассчитывают число единиц технологического оборудования для нагрева и кузнечной обработки деталей, моечно-очистных работ, сварки и наплавки:
(3.11)
где Gи.г. — масса агрегатов, изделий, обрабатываемых в течение года, кг;
g — производительность единицы оборудования, кг/ч;
Тф.о.д.- действительный годовой фонд времени работы оборудования, ч.
(3.12)
где Sи.г. — площадь поверхности обрабатываемых изделий, (дм2);
So — часовая производительность единицы оборудования, м2/ч (дм2/ч);
Тф.о.д — действительный годовой фонд времени работы оборудования, ч.
Большинство оборудования разборочно-сборочных, кузовных участков, демонтажно-монтажных постов обычно не рассчитывают, а выбирают по данным технологического процесса из условий обеспечения выполнения комплекса технологических операций.
Расчету по формуле подлежит специальное оборудование. Зная, что годовой объем работ Тг.д. =21 568 чел-ч, а действительный годовой фонд времени работы оборудования Тф.о.д=1991,4 ч, рассчитаем количество оборудования по формуле (10) т. е., по трудоемкости технологических операций:
Без расчета, исходя из количества рабочих на участке (посту), определяется количество единиц производственного инвентаря (верстаков и пр.).
3.6 Подбор технологического оборудования Подбор оборудования осуществляется из числа типового оборудования, выпускаемого промышленностью, по каталогам и прейскурантам.
Принятое для агрегатного участка основное и вспомогательное оборудование зафиксировано в таблице 3.2 с указанием его наименования, краткой характеристики, количества, размеров в плане и занимаемой оборудованием площади. Технологическое оборудование, уже существующее на агрегатном агрегатного участке, также указано в таблице 3.2.
Таблица 3.2
Оборудование агрегатного участка
Наименование оборудования | Краткая характеристика | Число единиц оборудования | Размеры единицы оборудования, мм | Площадь единицы оборудования, м2 | |
1 Подъемник ПП-16 | Передвижной. Грузоподъемность 16 т. Мощность электро-двигателя 3 кВт | 7,68×1,46 | 11,2 | ||
2 Тележка для снятия, установки и внутрига-ражной транспортировки ГМП автобуса; привод гидравлический | Грузоподъемность 0,5 т. Напольное усилие при транспортировке 150 Н (15 кгс), при поднятии груза 200 Н (20 кгс) | 0,8×0,99 | 0,79 | ||
3 Тележка для снятия, установки и внутрига-ражной транспортировки мостов автобуса | Грузоподъемность 1 т, привод гидравлический | 1,45×0,8 | 1,16 | ||
4 Тележка для транспортировки двигателя | Грузоподъемность 1 т | 0,9×1,2 | 1,08 | ||
5 Кран гидравличес-кий для снятия, установки и внутригаражной транспортировки двигателя | Грузоподъемность при максимальном вылете стрелы 0,8 т, высота подъема 3,25 м | 2,29×1,16 | 2,6 | ||
6 Приспособление навесное (траверса) для снятия и установки двигателей автобусов | Грузоподъемность 0,6 т | 1,2×0,08 | 0,096 | ||
7 Катучая кран-балка промышленного типа с управлением с пола | Грузоподъемность 3,2 т, мощность электродви-гателя 4,5 кВт | 13,5×2,2 | 29,7 | ||
8 Комплект ручного инструмента слесаря-монтажника | Состоит из 56 и 37 оксидированных инструментов и металлического ящика для них | 0,38×0,27 | 0,1 | ||
9 Набор приспособлений и инструментов с гидроприводом для правки кузовов и деталей оперения (с тележкой) | Передвижной | 0,84×0,44 | 0,36 | ||
10 Трансформатор сварочный для ручной и автоматической сварки в однокорпусном исполнении, однофазный | Номинальный сварочный ток 300А, номинальная мощность 20,5 кВт | 0,6×0,5 | 0,3 | ||
11 Аппарат для точечной сварки | Максимальная толщина свариваемых деталей 2+2. Производительность при сварке деталей толщиной 0,8+0,8 — 170 точек в минуту. Мощность сварочного трансформатора 25 кВт | 0,8×0,65 | 0,52 | ||
12 Аппарат для клепки деталей (клещи) | Переносной, производительность 100 циклов/мин | ; | ; | ||
13 Верстак жестянщика | ; | 1,4×0,5 | 0,7 | ||
14 Верстак слесарный | ; | 1,2×0,8 | 0,96 | ||
15 Электроножницы для прямолинейной и фасонной резки листовой стали | Наибольшая толщина разрезаемого листа 2,7 мм, мощность электродвигателя 0,27 кВт | 0,34×0,6 | 0,204 | ||
16 Гильотина для резки стальных уголков | Мощность электродвигателя 1,5 кВт | 1,4×0,69 | 0,96 | ||
17 Зигмашина для зиговки, отбортовки, рифления и резки листового материала | Наибольшая толщина обрабатываемого материала 1,8 мм, мощность электродвигателя 1,8 кВт | 1,47×0,81 | 1,19 | ||
18 Передвижной обдирочно — шлифовальный станок | Два круга диаметром 300 мм, мощность электродвигателя 1,7 кВт | 0,7×0,6 | 0,42 | ||
19 Вертикально-сверлильный станок | Наибольший диаметр сверления 18 мм, масса 450 кг | 0,87×0,53 | 0,51 | ||
20 Стенд для рихтовки рессор | Стационарный | 1,1×0,85 | 0,93 | ||
21 Горн кузнечный на один огонь | Стационарный, расход угля 8 -10 кг/ч | 1,2×1,03 | 1,23 | ||
22 Молот ковочный гидравлический | Номинальная масса падающих частей 75 или 150 кг | 2,2×0,93 | 2,04 | ||
23 Вертикально-гибочный пресс (гидравлический) | Стационарный | 0,6×0,4 | 0,24 | ||
24 Наковальня | Масса 100 кг | 0,5×0,12 | 0,06 | ||
25 Правочная плита | ; | 1,5x1 | 1,5 | ||
26 Стеллаж для деталей кузова | ; | 1x1,5 | 1,5 | ||
27 Подставка для листового металла | ; | 1,5×0,5 | 0,7 | ||
28 Стеллаж | ; | 2,5×0,6 | 1,5 | ||
29 Верстак для арматурных работ | ; | 0,8×1,4 | 1,12 | ||
3.7 Расчет площади участка Площадь производственных участков определяют двумя способами:
а) По удельным площадям на единицу оборудования, одно рабочее место, на одного производственного рабочего или на выпуск одного капитального ремонта. Площадь производственного участка определяют по одной из нижеследующих формул:
(3.13)
(3.14)
(3.15)
(3.16)
где fоб., fp, fрм, fпр. — соответственно удельная площадь на единицу оборудования, одного рабочего, одно рабочее место и один приведенный капитальный ремонт;
Хоб., mяв, Хрм., Nпр. — соответственно расчетное количество оборудования, количество явочных рабочих в наиболее многочисленной смене, количество рабочих мест и годовая программа в приведенных капитальных ремонтах.
б) По площади пола, занятой оборудованием, и коэффициенту на рабочие места, проезды и проходы. Габаритные размеры оборудования принимают из каталогов, альбомов и обмерных чертежей, а коэффициенты — по справочникам.
Площадь производственного участка рассчитывается по формуле:
(3.17)
где Fоб. — площадь пола, занятая оборудованием, м2;
Крм. — коэффициент на рабочие места, проезды и проходы.
Найдем площадь агрегатного участка по формуле (18). В таблице 6 приведены площади, занятые оборудованием. Коэффициент на рабочие места, проезды и проходы для жестяно-сварочного участка 4,0 — 4,5. Тогда:
Площадь агрегатного участка на предприятии «Костанайавтотранс» составляет 400 м² (площадь автомобилей-мест 125 м², площадь, занимаемая оборудованием 161,2 м2). Данной площади достаточно, чтобы рационально разместить дополнительное технологическое оборудование (устанавливаемое в результате реконструкции участка).
3.8 Объемно — планировочные и конструктивные решения На предприятиях по обслуживанию транспортных средств должны предусматриваться отдельные производственные помещения для размещения кузнечно-рессорного, агрегатного и медницкого участков. На предприятии кузнечно-рессорный участок объединен с агрегатным участком, который находятся в отдельном здании. На данных участках обслуживают автобусы и грузовые автомобили. От категории автомобилей зависит расстояние между автомобилями, между автомобилями и элементами здания и минимальная ширина ворот в помещении для обслуживания и ремонта. В нашем случае осуществляется обслуживание автомобилей (автобусов и грузовых автомобилей) третьей категории, т. е. длина автомобиля 8,1−11,0 м, а ширина 2,6−2,8 м. Учитывая характеристику категории автомобилей, расстояние между автомобилями принимаем равную 2 м, между автомобилями и элементами здания 1,5 м.
Наружные ворота здания раздвижные с механизированным приводом, который блокируется с электродвигателями тепловых завес. Блокировка обеспечивает автоматическое включение тепловых завес при открывании ворот и выключение при закрытии ворот. Размеры ворот (ширина х высота) 3,6×4,2 м.
Здание агрегатного участка имеет прямоугольную конфигурацию, одноэтажное, сетка колонн 24×12 м. Применение сетки колонн с шагом 12 м позволяет лучше использовать производственные площади и на 4−5% снизить стоимость строительства по сравнению с аналогичными зданиями, с шагом колонн 6 м. Высота здания 9,6 м.
Расстановка оборудования внутри агрегатного участка выполнена с учетом норм безопасности и удобства выполнения технологических процессов.
Реконструкция агрегатного участка приведет к перестановке существующего оборудования и установке нового дополнительного оборудования.
4. ТЕХНОЛОГИЯ РЕМОНТА АВТОБУСОВ
4.1 Технологический процесс капитального ремонта двигателя, коробки передач и сцепления Капитальный ремонт двигателя, коробки передач и сцепления состоит из ряда технологических операций. Совокупность этих операций, выполняемых в определенной последовательности, представляет собой технологический процесс капитального ремонта.
Постовая работа на осмотровой канаве по текущему ремонту двигателя, коробки передач и сцепления предусматривает замену неисправных агрегатов, узлов и деталей, требующих ремонта, а также выполнения регулировочных работ непосредственно на автомобиле, поставленным на осмотровую канаву.
Работы по ремонту агрегатов включают разборочно-сборочные и ремонтно-восстановительные операции. Агрегаты, снятые с автомобиля, частично или полностью разбираются на стендах. Для выпрессовки подшипников, втулок и других деталей применяют гидравлический пресс и универсальные съемники.
Для выполнения ремонтных работ агрегаты и детали подвергаются мойке в моечной ванне, расположенной на участке.
Агрегаты и узлы автомобиля по участку транспортируются на тележке.
Основными видами ремонтных работ двигателя являются: замена кривошипно-шатунного механизма, разборка на узлы и детали, очистка, мойка, разбраковка, комплектование, сборка из узлов и деталей; разборка, ремонт и сборка узлов двигателя, а также испытание и регулировка.
Общая схема технологического процесса капитального ремонта двигателя, коробки передач и сцепления представлена на рисунке 4.1.
Двигатели, прошедшие капитальный и текущей ремонт с заменой деталей кривошипно-шатунного и газораспределительного механизмов, поступают на испытательный стенд и на контрольный осмотр.
Рисунок 4.1 Схема технологического процесса текущего и капитального ремонта агрегатов
4.2 Технологический процесс разборки-сборки двигателя, коробки передач и сцепления Снятие и установка двигателя в связи с тем, что двигатели большинства легковых и некоторых грузовых автомобилей конструктивно объединены с коробкой передач и сцеплением в единый силовой агрегат, который крепится к кузову или к раме автомобиля на амортизирующих опорах, при необходимости капитального ремонта снимают целиком силовой агрегат.
Для снятия силового агрегата автомобиль устанавливают на осмотровую яму и после отсоединения двигатель от кузова (рамы) вынимают из моторного отсека вверх с помощью тали или любого другого подъемного устройства грузоподъемностью не менее 200 кгс.
На переднеприводных автомобилях возможно снятие двигателя из моторного отсека вниз. В этом случае автомобиль вывешивают и устанавливают на опоры, а двигатель после отсоединения его от кузова устанавливается на подведенную под стоящий на опорах автомобиль специальную тележку.
В зависимости от компоновки и конструктивных особенностей силовых агрегатов последовательность и технология выполнения работ по их снятию и установке может различаться, однако общий порядок выполнения этих работ примерно одинаков для всех автомобилей и приводится ниже.
1. Снять капот (капот можно не снимать, если силовой агрегат вынимается вниз или, если это грузовой автомобиль с опрокидывающейся кабиной, то поднять кабину).
2. Слить масло из двигателя.
3. Слить охлаждающую жидкость.
4. Отсоединить шланги системы охлаждения, идущие к радиатору и отопителю.
5. Отсоединить электропровода от аккумуляторной батареи, генератора, стартера, катушки зажигания, ЭПХХ карбюратора, датчиков и выключателей.
6. Отсоединить шланг вакуумного усилителя тормозов.
7. Отсоединить шланги подачи топлива к топливному насосу и шланг перепуска топлива от карбюратора (топливопроводы от ТНВД дизельного двигателя).
8. Отсоединить приводы воздушной и топливной заслонки карбюратора (привод ТНВД дизельного двигателя).
9. Отсоединить тросовый привод или рабочий гидроцилиндр сцепления.
10. Отсоединить приемные трубы глушителя.
11. Отсоединить привод передних колес или карданную передачу.
12. Отсоединить коробку передач от рычага переключения передач и отсоединить от нее гибкий вал привода спидометра.
13. Закрепить двигатель на подъемном устройстве.
14. Отвернуть крепления двигателя.
15. Вынуть двигатель в сборе со сцеплением и коробкой передач.
После этого двигатель, коробку передач или сцепление при помощи подъемного механизма устанавливают на стенд разборки — сборки и производят его полную разборку согласно последовательности выполнения операций для каждой модели двигателя, коробки передач и сцепления. Установка двигателя на автомобиль производится в порядке, обратном его снятию.
4.3 Участок капитального ремонта силовых агрегатов Каждое рабочее место должно быть оснащено картой комплексной организации труда, в которой указаны наиболее рациональные методы и приемы труда, последовательность выполнения работ, порядок обслуживания рабочего места, требования к исполнителю.
При длительной эксплуатации автомобильный парк достигает такого состояния, когда затраты средств и труда, связанные с поддержанием его в работоспособном состоянии, превосходят доходы, поступающие от дальнейшей эксплуатации (грузовых и пассажирских перевозок). Такое состояние автомобиля считается предельным и обусловлено неравнопрочностью его деталей и агрегатов. Известно, что создать равнопрочную машину, все детали которой изнашивались бы равномерно и имели бы одинаковый срок службы практически невозможно. Следовательно, ремонт подвижного состава даже только заменой некоторых деталей, имеющих небольшой ресурс, всегда целесообразен и с экономической точки зрения оправдан.
Основным источником экономической эффективности ремонта двигателей, коробок передач и сцепления является использование остаточного ресурса их деталей. Около 50% деталей двигателя прошедших срок службы до ремонта, имеют остаточный ресурс и могут быть использованы повторно либо без ремонта, либо после ремонтного воздействия.
Одним из основных агрегатов автомобиля является силой агрегат, т. е. двигатель, коробка передач и сцепления. Силовой агрегат автомобиля — одна из самых дорогих (15−25% общей стоимости) и самых сложных в изготовлении и ремонте часть автомобиля. Надежность и долговечность агрегата увеличивают срок службы автомобиля. Выход из строя силового агрегата практически означает выход из строя автомобиля.
Для поддержания надежности и работоспособности силового агрегата автомобиля в эксплуатации необходимо выполнить работы по техническому обслуживанию и ремонту. Экономически эффективное использование ресурса долговечности парка автомобилей обусловливает необходимость текущего и капитального ремонта.
На предприятии уже осуществляют техническое обслуживание и ремонт двигателей автомобилей, а в результате реализации проекта участка будет установлено дополнительное оборудование, позволяющее максимально механизировать технологические процессы по техническому обслуживанию и ремонту двигателя, коробки передач и сцепления.
В результате внедрения участка капитального ремонта двигателя, коробки передач и сцепления, на предприятии сможет на современном техническом уровне обслуживать не только собственный парк автомобилей, но и автомобили, принадлежащие другим предприятиям. На участке будут осуществляться следующие операции:
— капитальный ремонт двигателя;
— ремонт головки цилиндров;
— ремонт ГРМ;
— регулировка клапанов;
— ремонт КШМ;
— ремонт ЦПГ.
Ремонт коробки передач:
— ремонт и замена синхронизаторов;
— ремонт и замена шестерен;
— ремонт и замена валов.
Ремонт сцепления:
— замена и ремонт дисков сцепления;
— регулировка сцепления.
4.4 Расчет количества и подбор технологического оборудования и технологическая компоновка участка Количество основного технологического оборудования по всем участкам основного производства определяются расчетом. Исключение составляют отдельные виды оборудования в разборочно-сборочных, кузовных, медницко-радиаторных и некоторых других участков, когда комплект оборудования подбирается по данным технологического процесса из условий обеспечения выполнения комплекса технологических операций. Также без расчета, исходя из количества рабочих на участке и организации рабочих мест, определяется количество единиц производственного инвентаря (верстаков, стеллажей и пр.)
При расчете по укрупненным показателям общие затраты на оборудование определяются по анализу данных, характеризующих структуру затрат на строительство предприятия. При необходимости расчетным путем определяют потребность только по основному технологическому оборудованию необходимому для выполнения годового объема работ.
В зависимости от метода количество оборудования рассчитывают по:
? трудоемкости объектов ремонта;
? продолжительности технологических операций;
? физическим параметрам (массе, поверхности и т. п.) объектов ремонта.
По трудоемкости выполняемых работ рассчитывается оборудование, применение которого связанно с ручным или машинно-ручным способом работы.
К такому оборудованию относятся моечные ванны и установки для мойки изделий методом погружения, сушильные камеры, стенды для испытания двигателей и агрегатов, разборочно-сборочные стенды, оборудование для кузовных и жестяницких работ, медницких т.п.
По продолжительности технологических операций рассчитывается то оборудование, при работе на котором затраты связаны только с загрузкой (установкой) и выгрузкой (снятием) объектов ремонта или изделий, а также с периодическим наблюдением за ходом технологического процесса, продолжительность которого является величиной постоянной.
Разрабатываемый участок будет обслуживать сравнительно небольшой парк автомобилей, поэтому целесообразнее провести расчет необходимого количества оборудования по методу трудоемкости объектов ремонта.
Количество испытательных и разборочно-сборочных стендов, ванн мойки изделий рассчитывается по следующей формуле.
(4.1)
где хО — количество оборудования, шт.;
tТ.О — трудоемкость технологической операции с учетом затрат на загрузку и выгрузку объектов ремонта, чел.-ч;
А — количество объектов ремонта (изделий) на годовую программу, шт.;
kН — коэффициент неравномерности (на основе практики проектирования авторемонтных предприятий принимается обычно равным 1,1 — 1,2);
kП — коэффициент повторности (принимают равным 1,10 — 1,15);
Тф.о — действительный годовой фонд времени оборудования (применяется как равный действительному годовому фонду времени рабочего), ч.
Если авторемонтное предприятие обслуживает автопарк с разномарочным составом, то продолжительность технологической операции с учетом затрат времени на загрузку и выгрузку объектов ремонта определяется формуле:
(4.2)
где: ti — откорректированная с учетом условий эксплуатации нормативная трудоемкость операции, установленная ОНТП в зависимости от класса и модели автомобиля;
Кi — коэффициент, учитывающий долю капитального ремонта данной марки автомобиля от общего числа капитальных работ, принимается в соответствии с таблицей;
Рассчитаем по формуле (4.2) продолжительность операций, результаты сведем в таблицу 4.1.
Пользуясь формулой (4.1) рассчитаем количество оборудования:
Стенд сборки и разборки двигателей:
Принимаем один стенд сборки и разборки двигателей (хО = 1).
Стенд сборки и разборки коробки передач:
Принимаем один стенд сборки и разборки коробки передач (хО = 1).
Испытательный стенд:
Принимаем один испытательный стенд (хО = 1).
Моечная ванна:
Принимаем одну моечную ванну (хО = 1).
Из расчетов видно, что загрузка выбранного оборудования мала, но, несмотря на это, для выполнения капитального ремонта, данное оборудование необходимо установить на участке, т.к. без такого оборудования невозможно качественно осуществить капитальный ремонт. Кроме того, такая загрузка оборудования, в случае увеличения автопарка, дает возможность обслужить большее количество автомобилей, без увеличения общего числа оборудования, что не значительно повлияет на капитальные затраты участка.
Подбор оборудования осуществляется из числа типового оборудования, выпускаемого фирмой «РАСО» и рекомендованного передовыми предприятиями и Центром по научной организации труда и управления производства Министерства транспорта РК, для проведения капитальных ремонтов автомобилей.
При разборочно-сборочных работах и ремонте агрегатов автомобиля требуется специальный набор инструмента. Поэтому для автослесарей выпускают специальные большие и малые комплекты (наборы) таких инструментов. В комплект входят: гаечные открытые и торцевые (рожковые) двухсторонние ключи, накладные (накидные) ключи, баллонный ключ, молоток, зубило, бородок, шарнирная головка с удлинителем, отвертки простые и крестообразные, ключ для шпилек, специальные ключи (для опорных пальцев, головки цилиндров, свечей и др.), динамометрическая рукоятка с набором головок разных размеров, коловорот, монтажная лопатка, пассатижи. Для выполнения разборочно-сборочных работ дизельных двигателей необходим специальный набор ключей (ОР-15 727).
При разборке механизмов или узлов для снятия подшипников, шестерен и других деталей применяют съемники. Их использование облегчает и ускоряет процесс разборки и обеспечивает сохранность спрессовываемых деталей. Съемники бывают универсальные и специальные. Универсальные съемники позволяют снимать детали, различные по размерам и форме, поэтому с учетом того, что на участке капитального ремонта обслуживается разномарочный состав автомобилей, необходим набор съемников универсальный (СУ-13 554).
При выполнении разборочно-сборочных работ применяют стенды и приспособления, на которые крепят агрегаты и узлы автомобиля. Проектируемый участок капитального ремонта двигателя, коробки и сцепления обслуживает автомобили марок ВАЗ, ГАЗ, ЗИЛ, КамАЗ, МАЗ, УРАЛ, УАЗ, поэтому для выполнения капитального ремонта двигателя, коробки передач и сцепления необходимы универсальные стенды разборочно-сборочных работ. Из всего существующего ассортимента данного оборудования подходит только стенд разборки-сборки двигателей ЗИЛ, ЗМЗ, ВАЗ, АЗЛК, КамАЗ, ЯМЗ (ручной) марки Р-770 (рисунок 3.34), универсальный стенд для разборки-сборки коробок передач марки БС-09−000 (рисунок 3.4) и стенд для сборки и регулировки сцеплений универсальный марки Р-746 (рисунок 3.5).
После сборки двигатель необходимо обкатать и проверить его работу, поэтому для выполнения этих работ необходим испытательный стенд двигатель. Из всего перечня оборудования, предлагаемого отечественными производителями, подходит только универсальный испытательный стенд марки КС-276−031.
Для перемещения агрегатов автомобиля по участку необходима тележка для перевозки агрегатов грузоподъемностью не менее 350 кг. Для выполнения ремонтных работ необходим металлический двухтумбовый верстак.
Для временного хранения деталей двигателя, коробки передач и сцепления необходимы стеллажи и полки, а для хранения инструмента необходимо использовать инструментальный шкаф.
4.5 Устройство технологического оборудования Стенд сборки и разборки двигателей Р-770
Таблица 4.1
Технические данные стенда сборки и разборки двигателей
Характеристика | Р-770 | |
Тип | стационарный | |
Обслуживаемые двигатели | ЯМ3, КАМA3, ЗМЗ, ЗИЛ, ВАЗ, АЗЛК. | |
Способ поворота | вручную через червячный редуктор | |
Габаритные размеры, мм, не более: | ||
— длина | ||
— ширина | ||
— высота | ||
Масса, кг, не более | ||
Срок службы, лет | ||
Ресурс до среднего ремонта, ч | ||
Рисунок 4.2 Стенд разборки и сборки двигателей Р-770
1-стойка стационарная с редуктором; 2-стойка передвижная; 3-крестовина; 4-фиксатор стойки; 5-опора подшипниковая; 6-траверса; 7-траверса; 8-опора раздвижная (4шт.); 9-шпонка (4шт.); 10-фиксатор опоры (4шт.); 11-штырь (4шт.); 12-винт (4шт.); 13-поддон; 14-скалка; Ррукоятка поворота двигателя (90о-13 оборотов рукоятки).
Принцип работы стенда.
Двигатель, установленный на стенд, поворачивается вращением тихоходного вала основного червячного редуктора в положение наиболее удобное для работы. Вращение быстроходного вала основного червячного редуктора осуществляется через рукоятку ручного вращения.
Двигатель надежно фиксируется в любом положении, благодаря тому, что редуктор самотормозящий.
Устройство стенда.
Стенд состоит из двух стоек, стационарной и передвижной. Стационарная стойка жестко закреплена на крестовине и снабжена редуктором с ручным приводом. Основной редуктор с передаточным отношением i = 52. Передаточное число вспомогательного редуктора i = 16…31,5.
На передвижной опоре смонтирована подшипниковая опора. На цилиндрической поверхности опор имеются шпоночные пазы, в которые входят шпонки, ограничивающие перемещение опор по длине и по углу. Концы опор выполнены в виде кулаков и снабжены выдвижными штырями 11. Положение опор фиксируется подпружиненными фиксаторами 10.
На выходном валу редуктора и на валу подшипниковой опоры смонтированы траверсы. Траверсы трубчатого сечения, в них телескопически входят раздвижные опоры. Траверса на стационарной стойке поворачивается вращением электродвигателя, либо рукояткой редуктора. Траверса устанавливается в горизонтальном положении благодаря подпружиненному шарику в подшипниковой опоре.
Стойка в основании смонтирована на скалке, входящей в трубу крестовины. Вертикальное положение передвижной стойки обеспечено шпоночным соединением, которое одновременно ограничивает положение стойки по длине. Стойка фиксируется фиксатором.
Стенд снабжен поддоном для слива отработанного масла.
Подготовка изделия к работе.
Установить стенд на ремонтном участке, расконсервировать его.
Стенд установить на пол и закрепить фундаментными болтами согласно планировке (см. рисунок 4.3).
Проверить вращение шпинделя.
Рисунок 4.3 План фундамента под стенд Р-770
Рисунок 4.4 Схема установки двигателя на стенде.
Стенд сборки и разборки коробки передач БС-09−000
Таблица 4.2
Технические данные стенда сборки и разборки коробки передач БС-09−000
Характеристика | БС-09−000 | |
Тип | стационарный | |
Обслуживаемые коробки передач | ВАЗ, ГАЗ, ЗИЛ, КамАЗ, МАЗ, УРАЛ, УАЗ | |
Габаритные размеры, мм, не более: | ||
— длина | ||
— ширина | ||
— высота | ||
Масса, кг, не более | ||
Срок службы, лет | ||
Ресурс до среднего ремонта, ч | ||
Рисунок 4.5 Схема стенда сборки и разборки коробки передач БС-09−000
Рисунок 4.6 Общий вид стенда сборки и разборки коробки передач БС-09−000
Устройство стенда.
Стенд состоит из стационарной стойки, которая жестко закрепляется на фундаменте, двух (верхний и нижний) столиков для размещения инструмента и деталей.
На стойке смонтирована опора для тисков-захватов коробок передач. На опоре закреплены два захвата коробок передач с подвижным внутренним захватом, который перемещается винтовой рукояткой.
Тиски-захваты вращаются вокруг вертикальной оси на угол 90°, что позволяет закрепить коробку, как в вертикальной, так и в горизонтальной плоскостях.
Стенд для сборки и регулировки сцепления Р-746
Стенд состоит из столика, винтового пресса, предназначенного для сжатия пружин сцепления.
На столе размещены регулирующиеся центрирующие болты для закрепления корзины сцепления, а также винтовой пресс с направляющей для ведомого диска сцепления.
Таблица 4.3
Технические данные стенда сборки и регулировки сцепления Р-746
Характеристика | Р-746 | |
Тип | стационарный | |
Обслуживаемое сцепление двигателей | ВАЗ, ГАЗ, ЗИЛ, КамАЗ, МАЗ, УРАЛ, УАЗ. | |
Габаритные размеры, мм, не более: | ||
— длина | ||
— ширина | ||
— высота | ||
Масса, кг, не более | ||
Срок службы, лет | ||
Ресурс до среднего ремонта, ч | ||
Рисунок 4.7 Стенд сборки и регулировки сцепления Р-746
Вертикально-сверлильный станок ВСС 6002
Вертикально-сверлильный станок (рисунок 4.8) с комплектом насадок предназначен для сверления отверстий разного диаметра.
Ремонтируемые кабины и кузова должны устанавливаться и надежно закрепляться на специальных подставках (стендах).
Детали, подлежащие правке, должны устанавливаться на специальные оправки. Запрещается править детали на весу.
Перед правкой крыльев и других деталей из листовой стали их следует очистить от ржавчины металлической щеткой у местного отсоса.
При изготовлении деталей и заплат из листовой стали острые углы, края и заусенцы должны быть зачищены.
При резке на механических ножницах и гибке на гибочных станках работать разрешается только с металлом, толщина которого не превышает допустимую величину для данного оборудования.
При вырезке заготовок и обрезке деталей больших размеров на механических ножницах и другом оборудовании необходимо применять поддерживающие устройства (откидные крышки, роликовые подставки и т. п.).
Перед подачей воздуха для работы пневматического резака необходимо установить резак в рабочее положение.
Переносить, править и резать детали из листового металла разрешается только в рукавицах.
В процессе работы обрезки металла необходимо складывать в специально отведенное место (ящики).
Работы, связанные с выделением вредных испарений, а также работы по зачистке деталей должны выполняться при включенных местных отсосах.
Рисунок 4.8 Вертикально-сверлильный станок ВСС 6002
Техническая характеристика приведена в таблице 4.4.
Таблица 4.4
Технические характеристики сверлильного станка ВСС 6002
Тип | Электрический, стационарный | |
Максимальный диаметр сверла, мм | ||
Частота вращения шпинделя, мин'1 | ||
Наружный конус шпинделя | Морзе В 18 либо Морзе 1 | |
Напряжение, В | ||
Частота тока, Гц | ||
Сила тока, А | 2,2 | |
Потребляемая мощность, Вт | ||
Режим работы | Продолжительный | |
Временное сопротивление обрабатываемых материа; | ||
лов воздействию сверла, МПа, не более | ||
Габаритные размеры, мм | 835Ч680 | |
Масса, кг | ||
Устройство вертикально-сверлильного станка ВСС 6002. Станок состоит из следующих основных частей: стола-фундамента, рамы, плиты, стойки, ручки, редуктора, двигателя, выключателя и устройства для подавления радиопомех.
Передача вращающегося момента коленчатого вала двигателя к шпинделю осуществляется через двухступенчатый редуктор.
Для станков с наружным конусом Морзе В 18 сверло устанавливается в сверлильный патрон, который расположен на шпинделе станка. Для станков имеющих шпиндель с внутренним конусом Морзе 1, при работе следует использовать сверла диаметром 10… 18 мм с коническими хвостовиками. При работе сверлами с цилиндрическими хвостовиками диаметром менее 10 мм необходимо использовать сверлильный патрон, насаженный на конусную оправку, расположенную в шпинделе станка. Станки, имеющие шпиндель с внутренним конусом Морзе 1, дополнительно комплектуются клином и оправкой.
4.6 Расчет площади помещения
Площади зданий, участков и постов авторемонтных предприятий по своему функциональному назначению подразделяются на две основные группы: производственно-складские и вспомогательные. В состав производственно-складских площадей предприятия входят все площади участков основного и вспомогательного производства, склады, помещение сантехнических и энергетических служб, общезаводские проходы и проезды.
Площади производственно-складских помещений рассчитывают в зависимости от стадии выполнения проектных работ двумя способами:
? на стадии технико-экономического обоснования и при предварительных расчетах при проектировании предприятия по укрупненным показателям — по удельным площадям;
? на стадии технических проектов, разрабатываемых по данным технологического процесса — по физическим показателям (расчетной суммарной площади, занятой оборудованием, площадям складирования изделий и т. п.).
При проектировании по укрупненным показателям площади отдельных участков и служб предприятия определяют или на основании структурной характеристики состава площадей предприятия, или на основании удельных площадей, рассчитываемых по количеству рабочих, оборудования и рабочих мест.
Площади участков (в квадратных метрах) по физическим показателям (суммарной площади занятой оборудованием) рассчитываются по следующей формуле:
(4.3)
где k — коэффициент расстановки оборудования, учитывающий свободное расстояние для рабочего места, проходов и проезда, для участка капитального ремонта принимают 3,0−3,5;
fo1, fo2,…fon — площади в плане, занятые однотипными видами оборудования, м2;
хо1, хо2,…хоn — количество единиц однотипного оборудования, шт.;
i — количество позиций однотипного (по площади в плане) оборудования.
Для проведения работ по текущему ремонту двигателя, коробки передач и для организации работ по снятию и установке силового агрегата автомобиля целесообразно организовать специализированный пост на осмотровой канаве площадью 4,2 м² (6000Ч700Ч750).
Ниже приведены габаритные размеры оборудования применяемого на участке капитального ремонта двигателей, коробки передач и сцепления, таблица 4.5.
Таблица 4.5
Габаритные размеры оборудования участка капитального ремонта
Наименование оборудования | Марка | Габаритный размер, мм. | Площадь в плане, м2. | |
Стенд разборки-сборки коробки передач универсальный | БС-09−000 | 815Ч640Ч1100 | 0,52 | |
Стенд разборки сборки двигателей ЗИЛ, ЗМЗ, ВАЗ, АЗЛК, КамАЗ, ЯМЗ передвижной (ручной) | Р-770 | 1850Ч1050Ч1050 | 1,94 | |
Стенд для сборки и регулировки сцепления | Р-746 | 550Ч550Ч1030 | 0,31 | |
Испытательный стенд двигателей | КС-276−031 | 1850Ч1230Ч1200 | 2,28 | |
Тележка для перевозки агрегатов грузоподъемностью 350 кг | -; | 1240Ч540 | 0,67 | |
Верстак металлический двухтумбовый | В-2 | 2052Ч658Ч1035 | 1,35 | |
Стеллаж для временного складирования агрегатов, узлов и деталей | -; | 2500Ч1000Ч1600 | 2,5 | |
Гидравлический пресс | ГП-325 | 800Ч420Ч1230 | 0,34 | |
Инструментальный шкаф | -; | 435Ч274Ч245 | 0,12 | |
Ванна моечная | -; | 950Ч500Ч435 | 0,24 | |
Станок точильный | СТ-17 | 600Ч420Ч1235 | 0,25 | |
Вертикально-сверлильный станок | ВСС 6002 | 835Ч680Ч1750 | 0,57 | |
Рассчитаем по формуле (3.11) площадь участка капитального ремонта:
Из этого видно, что площадь помещения для участка КР двигателей, коробки передач и сцепления должна быть не менее 59,08 м².
4.7 Планировка производственного участка План расстановки оборудования выполняется на основе строительного чертежа здания (участка), где должны быть показаны строительные элементы здания: наружные и внутренние стены, перегородки, ворота, двери, окна и антресоли.
На плане расстановки оборудования необходимо показать технологическое оборудование, производственный инвентарь, подъемно-транспортное оборудование и устройства, а также площадки накопления изделий или материалов и проезды. Оборудование изобразим условным упрощенным контуром с габаритными размерами, учитывающими крайние положения движущихся частей, открывающихся кожухов (дверок), а также с учетом устанавливаемых на оборудование изделий, если последние в плане выходят за габаритные размеры оборудования.
Расстановка оборудования предопределяется следующими основными положениями:
? общей организацией рабочего процесса на участке;
? расчетом технологического оборудования;
? последовательностью выполнения технологических операций;
? принимаемой транспортной схемой (выбранными средствами механизации для межкорпусной, межучастковой и межоперационной транспортировки материалов, деталей и изделий);
? нормами технологического проектирования данного участка.
При проектировании предприятия по укрупненным показателям последовательность технологических операций принимается по схеме технологического процесса, составляемой на основании типовых технологических решений и обобщения опыта действующих предприятий.
Весьма существенное влияние на расстановку оборудования оказывают виды автотранспортных средств обслуживаемых участком. От этого зависят не только размеры проездов для транспортировки агрегатов, узлов и деталей, но и расположение и ориентация оборудования по отношению к транспортным проездам.
Расстановка оборудования должна выполняться с учетом обеспечения необходимых условий техники безопасности, удобства обслуживания и монтажа оборудования. Эти требования расстановки оборудования указываются в нормах технологического проектирования, которые разрабатываются ведущими проекторными организациями для соответствующих производств. В нормах технологического проектирования указываются допустимые габаритные размеры приближения оборудования к конструктивным элементам зданий (колоннам и стенам), допустимые расстояния между оборудованием, а также от оборудования до границ проездов.
Нормы технологического проектирования участка ремонта агрегатов, узлов и деталей автомобилей:
? расстояние от стен до тыльной стороны оборудования — 350 мм;
? расстояние между станками по фронту — 700 мм.
Наиболее целесообразно размещать участок ремонта двигателей, коробки передач и сцепления в помещении первого и второго боксов, потому что это единственное помещение, где существует свободное место для расположения оборудовании в непосредственной близости от осмотровой канавы.
На разрабатываемом участке капитального ремонта двигателя, коробки передач и сцепления расположим оборудование, основываясь на схему технологического процесса ремонта.
Одна из первых операций капитального ремонта — мойка силового агрегата, подразумевается, что на капитальный ремонт автомобиль останавливается после полной мойки, в том числе и после мойки силового агрегата.
Двигатель после демонтажа с автомобиля при помощи подвижной тали устанавливается на разборочно-сборочный стенд, поэтому стационарное место для стенда необходимо разместить как можно ближе к автомобилю — месту, оно при этом он не должно быть расположено в отдаление от верстака. Стенд разборки-сборки коробок передач, а также стенд сборки и регулировки сцепления целесообразно разместить в непосредственной близости от моечной ванны. Моечная ванна, в свою очередь, должна располагаться по возможности как можно ближе к верстаку, где будет осуществляться разборка-сборка узлов и деталей агрегатов, которые необходимо после разборки и перед сборкой отчистить от загрязнений и промыть.
Вертикально-сверлильный станок установлен на фундаменте в правом дальнем углу, его перестановка приведет к значительным затратам, поэтому не целесообразно перемещать вертикально-сверлильный станок, а верстак лучше расположить по фронту вдоль правой стены около станка.
Сразу за верстаком установим точильный станок, для заточки инструмента и обработки поверхностей деталей, а за точильным станком определим стационарное место для гидравлического пресса.
Испытательный стенд двигателей необходимо расположить слева от вертикально-сверлильного станка, т.к. над этим местом установлена вытяжная вентиляция, кроме того, здесь возможно разместить светильники местного освещения.
Инструментальные шкафы расположим слева от испытательного стенда двигателей вдоль фронтальной стены, что обеспечит удобство доступа к инструменту при выполнении операции снятия и установки агрегатов с автомобиля.
Стеллаж для временного хранения деталей, узлов и агрегатов установим вдоль правой стены за основным оборудованием. Стационарное место тележки для перевозки агрегатов определим в непосредственной близости от стеллажа.
5. ОХРАНА ТРУДА
5.1 Анализ опасности и вредности Условия труда — совокупность факторов производственной среды оказывающей влияние на здоровье и работоспособность человека. Все факторы производственной среды подразделяются на опасные и вредные производственные факторы.
Опасный производственный фактор — это фактор, воздействие которого на работающего, в определенных условиях приводит к травме.
Вредный производственный фактор — это фактор, воздействие которого на работающего, приводит к профессиональному заболеванию.
Современный технический уровень автотранспортного управления, мастерство и опыт сотрудников служат гарантией того, что экологическая служба предприятия способно решать широкий круг задач по обеспечению работоспособности системы организационных и технических средств, предотвращающих воздействие опасных и вредных производственных факторов на работающих.
Зона технического обслуживания и ремонта оснащена необходимым оборудованием для надежного контроля технического состояния всех классов эксплуатируемых машин и оперативного устранения неисправностей.
Традиционно высокий подход к подготовке кадров, охране труда и технике безопасности, а также высокий социальный статус работников определяют стабильности профессионализм коллектива.
«Костанайавтотранс» имеет государственные лицензии по всем направлениям своей деятельности, подлежащим лицензированию.
На предприятии соблюдаются требования к освещению, вентиляции, отоплению производственных помещений. Ежегодно экологическая служба предприятия проводит контроль условий труда в соответствие с действующими стандартами и нормативами. Результаты измерений по факторам опасности и вредности представлены в таблицах 5.1 и 5.2
Таблица 5.1
Фактическое состояние условий труда на рабочих местах жестянщиков по вредности и опасности
Наименование фактора | Допус-тимое значение | Факти-ческое значе-ние | Класс условий труда | Продолжи-тельность воздействия, час. | |
1 Шум: выполнение всех видов работ на постоянных рабочих местах в производственных помещениях и на территории предприятий, дБ | 3.1 | ||||
2 Температура воздуха для производственных помещений в холодный период года (категория работ II б), °С | 15,4 | ||||
3 Скорость движения воздуха в холодный период года (категория работ II б), м/с | 0,4 | 0,2 | |||
4 Относительная влажность воздуха в холодный период года, % | |||||
5 Естественное освещение (КЕО), % | 0,6 | 0,6 | |||
6 Освещенность рабочей поверхности, лк | |||||
7 Пульсация освещенности (коэффициент пульсации), % | 7,8 | ||||
Таблица 5.2
Фактическое состояние условий труда на рабочих местах сварщиков по факторам вредности и опасности
Наименование фактора | Допус-тимое значение | Факти-ческое значе-ние | Класс условий труда | Продол-житель-ность воздей-ствия, час. | |
1. Азота оксиды (в пересчете на N02), мг/мЗ | не обнаружен | ||||
2. Углерода оксид, мг/мЗ | 6,25 | ||||
3. Марганец в сварочных аэрозолях при его содержании до 20%, мг/мЗ | 0,2 | 0,03 | |||
4. Шум: выполнение всех видов работ на постоянных рабочих местах в производственных помещениях и на территории предприятий, дБА | |||||
5. Температура воздуха для производственных помещений в холодный период года (категория работ II а),°С | 17,1 | ||||
6. Скорость движения воздуха в холодный период года (категория работ II а), м/с | 0,3 | 0,22 | |||
7.Относительная влажность воздуха в холодный период года, % | |||||
8. Естественное освещение (КЕО),% | 0,6 | 0,9 | |||
9. Освещенность рабочей поверхности, лк | 3.1 | ||||
10. Пульсация освещенности (коэффициент пульсации), % | 10,3 | ||||
5.2 Обеспечение безопасности Ремонтируемые кабины и кузова должны устанавливаться и надежно закрепляться на специальных подставках (стендах).
Детали, подлежащие правке, должны устанавливаться на специальные оправки. Запрещается править детали на весу.
Перед правкой крыльев и других деталей из листовой стали их следует очистить от ржавчины металлической щеткой у местного отсоса.
При изготовлении деталей и заплат из листовой стали острые углы, края и заусенцы должны быть зачищены.
При резке на механических ножницах и гибке на гибочных станках работать разрешается только с металлом, толщина которого не превышает допустимую величину для данного оборудования.
При вырезке заготовок и обрезке деталей больших размеров на механических ножницах и другом оборудовании необходимо применять поддерживающие устройства (откидные крышки, роликовые подставки и т. п.).
Запрещается:
— при вырезке газовой сваркой поврежденных мест придерживать вырезаемые части руками;
— работать без защитного кожуха абразивным кругом, насаженным на конец гибкого вала;
— зажимать зачистную машину в слесарные тиски для крепления к ней абразивного круга, а пользоваться следует двумя ключами;
— при резке листового металла на механических ножницах подавать металл, держа руки против режущих роликов.
Перед подачей воздуха для работы пневматического резака необходимо установить резак в рабочее положение.
Переносить, править и резать детали из листового металла разрешается только в рукавицах.
В процессе работы обрезки металла необходимо складывать в специально отведенное место (ящики).
Работы, связанные с выделением вредных испарений, а также работы по зачистке деталей должны выполняться при включенных местных отсосах.
Перед ремонтом и пайкой емкости из-под взрывопожароопасных и ядовитых жидкостей необходимо обработать ее любым способом (в том числе промывкой горячей водой с каустической содой, пропаркой, просушкой, горячим воздухом и т. п.) до полного удаления следов этих жидкостей с последующим анализом воздушной смеси в емкости с помощью газоанализатора.
Разрешается производить пайку емкостей из-под горючих жидкостей без предварительной обработки, наполнив емкость нейтральным газом, при этом в процессе пайки газ должен подаваться в емкость непрерывно в течение всего времени пайки. Пайку емкостей следует производить при открытых пробках (крышках).
Паять радиаторы, топливные баки и другие крупные детали необходимо на специальных подставках (стендах), оборудованных поддонами для стекания припоя.
Прочищая трубки радиатора шомполом, не следует держать руки на противоположной стороне трубки. Запрещается вводить шомпол в трубку до упора рукоятки.
Давление сжатого воздуха при испытании радиатора не должно превышать величины, указанной в руководстве по капитальному ремонту автомобилей конкретных марок.
Транспортировку бутылей с кислотой разрешается производить в таре, надежно укрепленной на тележках или носилках.
Травление кислоты должно производиться в небьющейся кислотоупорной емкости и только в вытяжном шкафу (запрещается применение стеклянной тары). Запрещается при травлении опускать в кислоту сразу большое количество цинка.
Хранить флюс и материалы для изготовления флюсов необходимо в вытяжном шкафу в количестве, не превышающем суточной потребности.
Для предупреждения загрязнения рабочего места расходуемый припой должен храниться в специальных металлических ящиках.
Паяльные лампы перед началом работы и периодически не реже одного раза в месяц должны подвергаться осмотру и проверке с последующей регистрацией в специальном журнале Неисправные лампы необходимо сдавать в ремонт.
При работе с паяльной лампой необходимо соблюдать следующие правила: перед разжиганием проверить ее исправность; резервуар лампы не должен иметь трещин и запаек легкоплавким припоем; пробка наливного отверстия должна быть завернута до отказа; разбирать паяльную лампу можно лишь после стравливания сжатого воздуха; гасить пламя паяльной лампы следует только запорным вентилем.
Запрещается:
— разжигать неисправную паяльную лампу;
— заливать лампу горючим более чем на ¾ емкости ее резервуара;
— использовать для заправки этилированный бензин;
— заправлять паяльную лампу горючим, выливать горючее или разбирать паяльную лампу вблизи открытого огня;
— наливать горючее в неостывшую лампу;
— выпускать сжатый воздух через наливное отверстие горящей лампы или при неостывшей горелке;
— работать с паяльной лампой вблизи нахождения легковоспламеняющихся и горючих веществ;
— разжигать паяльную лампу, наливая горючее через ниппель горелки;
— работать с лампой, не прошедшей периодическую проверку.
При обнаружении неисправностей (подтекание резервуара, просачивание топлива через резьбу горелки, деформация резервуара и т. п.) нужно немедленно прекратить работу с этой лампой.
Свинец и цветные металлы необходимо плавить только в вытяжном шкафу. Сосуд с расплавленным металлом запрещается ставить на сырой пол.
В помещениях для производства медницко-жестяницких и кузовных работ должны всегда находиться кислотонейтрализующие растворы.
6. ОХРАНА ОКРУЖАЮЩЕЙ СРЕДЫ Вредное воздействие автотранспортного комплекса (АТК) на окружающую среду выражается в ее негативном изменении в результате попадания в атмосферный воздух, воду, почву токсичных компонентов отработавших газов, продуктов изнашивания деталей, дорожного полотна, отходов производственно — эксплуатационной деятельности, образующихся при движении, в процессе погрузочно-разгрузочных работ, заправке, мойке, хранении, техническом обслуживании и ремонте автомобилей.
Доля выбросов в атмосферу с ОГ автомобилей в ходе производственной деятельности предприятий АТК незначительна и составляет 1−3% от общих выбросов всего автопарка.
Основными производственными вредностями следует считать:
в помещениях для хранения, ТО и ТР автомобилей — окись углерода, окислы азота, альдегиды;
в жестяно-сварочном отделении — аэрозоли марганца и пылевыделения;
в кузнечно-прессовом отделении — теплоизбытки, окись углерода, сернистый газ.
Основными источниками загрязнения водного бассейна являются сточные воды от мойки автомобилей, содержащие взвешенные вещества и нефтепродукты (80−85% производственных стоков); сточные воды от производственных участков, содержащие тяжелые металлы, кислоты, щелочи, краску, растворители; поверхностные сточные воды с территории, содержащие нефтепродукты, тосол, тормозные жидкости и другие вредные вещества. Основными загрязнениями в сточных водах являются взвешенные вещества и нефтепродукты.
Деятельность предприятий АТК сопровождается образованием большого количества промышленных отходов. Наиболее распространенными являются: отработанные масла и смазки, технические жидкости, осадки водоочистных установок; металлический, в том числе свинцовый, лом, отработавшие свой срок автомобильные шины и аккумуляторы, отходы красок, шламы и шлаки.
В соответствии с рекомендациями Министерства транспорта РК на крупных и средних АТП контроль токсичности следует осуществлять на специальных контрольно-регулировочных пунктах (КРП). Их размещают на постах диагностирования Д-1 и оборудуют газоанализаторами, дымомерами, тахометрами, набором регулировочного инструмента. Ежедневно при возвращении с линии часть автомобилей проходит через КРП, где определяются и регистрируются выбросы СО и СХНУ или дымность ОГ. На следующий день проверяется другая группа автомобилей и т. д. В результате каждый автомобиль один раз в три недели проходит проверку и весь парк находится под постоянным контролем ИТС.
Если на КРП не удается привести токсичность ОГ в соответствие с требованиями действующих стандартов, информация об этом передается диспетчеру отдела управления производством, который направляет автомобиль на участок диагностирования Д-2. Если в ходе углубленного диагностирования неисправности, вызвавшие повышенную токсичность ОГ, устраняются, автомобиль выпускается на линию, а если нет — направляется в зону ТР для проведения необходимых ремонтных воздействий.
Очистка сточных вод, сбор и утилизация отходов производства Сточные воды от производственных зданий и хозяйственно-бытовых сооружений, а также ливневые стоки с их территории могут сбрасываться в городской водосток, в поверхностные водоемы и на почву только после их очистки. Поэтому АТП имеет участок для мойки ПС, оснащенный очистными сооружениями с системой оборотного водоснабжения, локальные очистные сооружения для предварительности очистки стоков от производственных участков и накопитель-отстойник для очистки стоков с территории. Осадки и нефтепродукты, скапливающиеся в очистных сооружениях, обезвоживают и утилизируют.
Промышленные отходы (отслужившие аккумуляторы и шины, отработанные масла, пластические смазки, технические жидкости и др.) периодически вывозят в места утилизации или сдают специализированным организациям, занимающимся сбором и переработкой вторичного сырья.
В качестве основных мероприятий по защите от вредных веществ следует выделить: своевременный контроль за содержанием вредных веществ в воздухе рабочей зоны; устройство местной вентиляции. Местная вытяжная вентиляция служит для улавливания и удаления загрязненного воздуха с места его образования.
7. РАСЧЕТ ОСНОВНЫХ ЭКОНОМИЧЕСКИХ ПОКАЗАТЕЛЕЙ
«Костанайавтотранс» предполагается реконструкция агрегатного участка. Реконструкция предприятия предусматривает установку нового технологического оборудования, которое позволит расширить номенклатуру услуг, оказываемых населению города, автотранспортным предприятиям и организациям. В результате установки нового оборудования на агрегатном участке будут оказывать следующие услуги:
Ремонт деталей автобуса:
Ремонт рамы;
Ремонт консолей;
Изготовление стоек салона кузова;
Изготовление и замена порогов;
Изготовление и замена наружных панелей;
Изготовление и замена внутренних панелей;
Ремонт поперечных изломов в фермах и балках кузова;
Ремонт каркаса фермы пола, ремонт боковых ферм.
Ремонт узлов и деталей арматуры и оборудования кузова автобуса:
Ремонт и установка поручней;
Ремонт и установка каркасов сидений;
Ремонт и установка дверей.
Для того, чтобы доказать экономическую целесообразность предполагаемой реконструкции агрегатного участка необходимо провести расчет основных экономических показателей.
7.1 Расчет капитальных затрат и фонда оплаты труда Капитальные затраты — это затраты предприятия на покупку, доставку и монтаж технологического оборудования. Перечень оборудования приведен в таблице 7.1.
Таблица 7.1
Оборудование агрегатного участка
Наименование | Число единиц | Стоимость, тнг. | |
1 Подъемник | |||
2 Тележка для снятия, установки и транспортировки ГМП | |||
3 Тележка для снятия, установки и транспортировки мостов автобуса | |||
4 Тележка для транспортировки двигателя | |||
5 Кран гидравлический | |||
6 Комплект ручного инструмента слесаря-монтажника | |||
7 Набор приспособлений и инструментов с гидроприводом для правки кузовов и деталей оперения | |||
8 Верстак жестянщика | |||
9 Зигмашина | |||
10 Передвижной обдирочно-шлифовальный станок | |||
11 Вертикально-сверлильный станок | |||
12 Вертикально-гибочный пресс | |||
13 Шлифовальный станок | |||
14 Правочная плита | |||
15 Стеллаж для деталей кузова | |||
16 Подставка для листового металла | |||
17 Стеллаж | |||
18 Верстак для арматурных работ | |||
19 Дефектоскоп ВИТ-4М | |||
Капитальные затраты вычисляют по следующей формуле:
Кз= Зоб + Зд + Зм, (7.1)
где Зоб — затраты на покупку оборудования, тнг;
Зд — затраты на доставку оборудования, тнг;
Зм — затраты на монтаж оборудования, тнг.
Затраты на доставку и монтаж оборудования равны 10% от затрат на покупку оборудования.
Согласно формуле (7.1) капитальные затраты равны:
Кз= Зоб + Зд + Зм = 2 402 900+120145+120 145 = 2 643 190 тнг.
Оплата труда — это система отношений, связанных с обеспечением и осуществлением работодателем выплат работникам за их труд в соответствии правовых актов, договоров и норм.
Заработная плата — это вознаграждение за труд в зависимости от квалификации работника, сложности, количества, качества и условий выполняемой работы, а также выплаты компенсационного и стимулирующего характера.
На агрегатном участке работает 15 человек, из них 3 человека выполняют вспомогательные работы, 7 человек осуществляет основные ремонтные работы, 2 рабочих проводят приемку и дефектоскопию кузовов транспортных средств, 3 рабочих совмещают ремонтные и демонтажные работы.
Рассчитаем заработную плату за месяц технологов работающих на жестяно-сварочном участке.
Основная заработная плата, в тнг/мес рассчитывается по следующей формуле:
ЗП = Т + ПП + ДВ, (7.2)
где Т — тариф, тнг/мес;
ПП — производственная премия, тнг/мес;
ДВ — доплата за работу во вредных условиях, тнг/мес.
Известно, что технолог работает 164 час/мес, всего на агрегатном участке работают два технолога. Тарифная ставка технолога равна 125,0 тнг/час (принята по 8 разряду).
Тариф рассчитывают как произведение количества работающих (технологов), фонда рабочего времени и тарифной ставки:
Т = КР ФРВ ТС, (7.3)
где КР — количество работающих, чел;
ФРВ — фонд рабочего времени, час/мес;
ТС — тарифная ставка, тнг/час.
Рассчитаем тариф по формуле (7.3):
Т = КР ФРВ ТС = 2 164 125 = 41 000 тнг/мес
Производственную премию примем равную 50% от тарифа, а доплату за работу во вредных условиях 30% от тарифа. В результате получим:
ПП = Т 0,5 = 41 000 0,5 = 20 500 тнг/мес, ДВ = Т 0,3 = 5520,2 0,3 = 12 300 тнг/мес.
Так, как известны все необходимые данные, определим основную заработную плату технологов по формуле (7.2):
ЗП = Т + ПП + ДВ = 41 000+20500+12 300 = 73 800 тнг/мес Основная заработная плата, это оплата труда работника со всеми причитающимися ему надбавками и премиями.
К основной заработной плате осуществляется надбавка по району. Надбавка по районному коэффициенту принимается, как 15% от основной заработной платы.
Основную заработную плату с учетом районного коэффициента определим по следующей формуле:
ЗПК = ЗП + (ЗП 0,15) = 73 800+(73 800 0,15) = 84 870 тнг/мес.
Таблица 7.2
Расчет фонда оплаты труда за месяц
Наименование | Единицы измер | Основные рабочие | Вспомогательные рабочие | Руководители | Всего по предприятию | ||||||
сварщик-ремонтник | дефектов-щик | Тех-нолог | всего | слесарь | всего | начальник участка | всего | ||||
1 Разряд | |||||||||||
2 Тарифный коэффициент | 2,44 | 3,12 | 3,12 | 1,91 | 3,99 | ||||||
3 Тарифная ставка | тнг/час | 65,8 | 84,15 | 84,15 | 52,5 | ||||||
4 Система оплаты | ПП | ПП | ПП | ПП | ПП | ||||||
5 Количество работающих | чел | ||||||||||
6 Фонд рабочего времени | час/мес | ||||||||||
7 Основная зарплата | тнг/мес | ||||||||||
8 Тариф | тнг/мес | ||||||||||
9 Доплата за работу во вредных условиях | тнг/мес | ||||||||||
10 Производственная премия | тнг/мес | ||||||||||
11 Доплата по районному коэффициенту | тнг/мес | ||||||||||
12 Основная зарплата с учетом районного коэффициента | тнг/мес | ||||||||||
13 Дополнительная зарплата | тнг/мес | ||||||||||
Всего ФОТ | тнг/мес | ||||||||||
Дополнительная заработная плата — оплата вне рабочего времени (все виды отпускных). Определяется процентом к основной заработной плате (17,5%). Определим дополнительную заработную плату:
ДЗП = ЗПК 0,175 = 84 870 0,175 = 14 852,25 тнг/мес.
Всего фонд оплаты труда (ФОТ) для технологов составит:
ФОТ = ЗПК + ДЗП = 84 870 + 14 752,25 = 99 722,25 тнг/мес.
Расчет фонда оплаты труда для других работников агрегатного участка осуществляется аналогично.
Результаты расчета фонда оплаты труда за месяц для всех работников агрегатного участка приведен в таблице 7.2
7.2 Расчет текущих затрат на выполнение ремонтных работ и удельной себестоимости работ При характеристике и классификации издержек предприятия существенное значение имеет процесс их учета в ходе расчета стоимости осуществляемой услуги. Затраты, по их роли в процессе осуществления услуг делят на основные и накладные.
Основные затраты связаны непосредственно с производственным процессом.
Накладные затраты связаны с хозяйственной деятельностью предприятия (водоснабжение, отопление и т. д.).
Затраты изменяющиеся при изменении объема работ называются переменными (сырье, материалы).
Постоянные затраты, это затраты, которые изменяются при изменении объема выполняемых работ (амортизация оборудования, повременная заработная плата).
Удельную себестоимость в тенге рассчитывают по следующей формуле:
(7.4)
где ТЗ — текущие затраты, тнг;
Тг.д. — годовой объем работ, чел-час.
Калькуляция — это поэлементная группировка затрат, от которых зависит себестоимость услуги или продукции. Калькуляция на выполнение ремонтных работ приведена в таблице 7.3.
Таблица 7.3
Калькуляция на выполнение ремонтных работ
Статья калькуляции | Пояснения | Сумма, тнг. | |
1 Основные затраты | |||
1.1 Трудозатраты (зарплата основных рабочих) | |||
1.2 ЕСН — социальные отчисления | [1.1] 35,6% | ||
1.3 Зарплата РСС | |||
1.4 ЕСН — социальные отчисления | [1.3] 35,6% | ||
1.5 Затраты на материалы для ТР | |||
1.6 Амортизация производственного оборудования | Кз/10 | ||
2 Накладные затраты | |||
2.1 Электрическая энергия | |||
2.2 Водоснабжение | |||
2.3 Отопление | |||
2.4 Служебный транспорт | |||
2.5 Реклама | |||
3 Непредвиденные затраты | [1.1] 10 | ||
Всего текущие затраты | без НДС с НДС | ||
В таблице 7.3 показатели накладных затрат приняты условно. Величина показателей накладных затрат аналогична показателям действующих авторемонтных предприятий.
Значения текущих затрат приведены в калькуляции на выполнение ремонтных работ, а значение годового объема работ смотри в разделе 3.4.
Себестоимость — затраты на производство и исполнение услуг в денежном выражении. Согласно формуле (7.4) удельная себестоимость на ремонтные работы составит:
без НДС с НДС Средняя цена на ремонтные работы на авторемонтных предприятиях города равна 750 тнг/ч (с НДС). Расчет рентабельности, удельной прибыли, выручки вычисляют по следующей формуле:
(7.5)
где Ц — цена норма-часа на ремонтные работы, тнг/час.
Рассчитаем рентабельность по формуле (7.5):
Удельную прибыль вычислим по формуле:
Пуд = Ц — Уд. с/с = 750−457 = 297 тнг/ч Выручку рассчитаем по следующей формуле:
ВР = Ц. Тг.д. = 750 21 568 = 16 176 000 тнг без НДС Чистый доход (прибыль) рассчитывается как разница между суммами доходов и расходов.
Доход включает в себя выручку от деятельности агрегатного участка и амортизационных отчислений на оборудование.
Расход включает в себя капитальные затраты (затраты на приобретение оборудования) и текущие затраты (ФОТ, основные и накладные затраты). Зная показатели дохода и расхода за год (известны из выше приведенного расчета), можно определить чистый доход (прибыль):
ЧД = Д — Р = 2 804 984 — 2 269 603 = 535 381 тнг в первый год Показатели дохода и расхода, а также распределение прибыли приведены в таблице 7.3.
Таблица 7.3
Расчет и распределение прибыли
Наименование | Сумма, тнг. | |||
в первый год | во второй год | в третий год | ||
1 Доход без НДС | ||||
1.1 Выручка от оказания услуг | ||||
1.2 Амортизация оборудования | ||||
2 Расход без НДС | ||||
2.1 Капитальные затраты | ; | ; | ||
2.2 Текущие затраты | ||||
3 Чистый доход (прибыль) | ||||
Срок окупаемости рассчитаем по формуле:
Из формулы следует, что срок окупаемости составляет 8 месяцев.
Известно, что наиболее важным на рынке услуг является уровень спроса. Проведен анализ устойчивости проекта при условии снижения спроса на жестяно-сварочные услуги на 30%. Снижение спроса на услуги приведет к снижению объема выполняемых работ. Насколько снизится объем работ и как это отразится на удельной себестоимости услуг видно из расчета.
Найдем объем работ в случае снижения спроса на услуги:
Т = Тг.д. 70% = 21 568 0,7 = 15 153,6 чел-ч.
Тогда получим:
В случае снижения спроса снизится рентабельность:
Выручка при снижении спроса составит:
ВР=Ц Т=750 15 153,6= 1 926 305 тнг без НДС Срок окупаемости значительно увеличится и составит:
Из расчета следует, что проект останется экономически целесообразным даже при значительном снижении спроса на услуги.
ЗАКЛЮЧЕНИЕ
В дипломной работе разработан вариант реконструкции агрегатного участка в условиях автотранспортного предприятия «Костанайавтотранс». На предприятии Проектирование осуществлялось путем организационно-технологического расчета основных параметров и показателей участка, по которым подбиралось технологическое оборудование, и разрабатывалась схема технологических процессов ремонта кузовов автобусов.
Для обоснования реконструкции в условиях «Костанайавтотранс» было выполнено следующее:
— доказана целесообразность организации поста по ремонту кузовов автобусов с технической экономической точки зрения;
— разработаны технологические процессы ремонта кузовов автобусов;
— подобрано необходимое производственное оборудование и технологическую оснастку;
— было изучено влияние производственных процессов на окружающую среду и человека, т. е. решить вопросы охраны труда и экологии.
Планируемый комплекс мероприятий, реализуемый на агрегатном участке необходим для поддержания автобусного парка в работоспособном состоянии в течение установленного срока эксплуатации, повышают коэффициент технической готовности.
Планируется организация работы по оказанию услуг автотранспортным предприятиям в ремонте кузовов автобусов.
В работе проведен анализ опасных и вредных факторов, возникающих в процессе производственной деятельности, и предложены меры безопасности.
В экономической части доказана экономическая целесообразность работы, рассчитана рентабельность внедрения и период его окупаемости.
1. Ухарский В. Б. Техническое обслуживание и ремонт автобусов. — М.: Транспорт, 1986.
2. Семенов Н. В. Техническое обслуживание и ремонт автобусов. — М.: Транспорт, 1987.
3. Наумов Б. А., Чередников А, А., Косарев И. Д. Автомобиль. — М: Транспорт, 1973.
4. Лапин В. С, Вольберг В. В. Ремонт и восстановление кузовов автомобилей. — М.: Высшая школа, 1988.
5. Грибков В. М., Карпекин П. А. Справочник по оборудованию для технического обслуживания и текущего ремонта автомобилей. — М.: Россельхозиздат, 1984.
6. Еремин В. Г., Сафронов В. В. Методы и средства обеспечения безопасности труда в машиностроении. — Высшая школа, 2002.
7. Рысин Ю. С. Охрана труда: Требования безопасности при ремонте автотранспорта. — М.: Транспорт, 2000.
8. Карташов В. П. Проектирование автотранспортных предприятий: Пособие для дипломного проектирования. — М.: Транспорт, 1981.
9. Кузнецов Е. С. Техническая эксплуатация автомобилей. — М.: Наука, 2001.
10. Дехтеренский Л. В., Абелевич Л. А., Карагодин В. И. Проектирование авторемонтных предприятий. — М.: Транспорт, 1981.
11. Автомобильный справочник BOSCH. — М.: За рулем, 2000.
12. Нормы расхода запасных частей, материалов и инструментов на капитальный ремонт автобусов. — М.: Транспорт, 1974.
13. Типовые проекты рабочих мест на автотранспортном предприятии. — М.: Транспорт, 1977.
14. Кузнецов А. С, Белов Н. В. Малое предприятие автосервиса. — М.: Машиностроение, 1995.
15. Веревкин Н. И., Тарасенко В. В. Режимы работы и надежность автобусов в эксплуатации. — ЦНИЛ., 1983.
16. Рудников Ю. М., Дагович В. М, Засорин Ю. Л. Автомобиль категории Д. — М.: Транспорт, 1986.
17. Кошкин К. Т. Технология авторемонтного производства. — М.: Транспорт, 1969.
18. Козлов В. П., Васильев В. Н. Справочник водителя автобуса. — Кишинев: Карта молдовянскэ, 1979.
19. Афанасьев Л. Л., Маслов А. А., Колясинский Б. С. Гаражи и станции технического обслуживания автомобилей. -М.: Транспорт, 1980.
20. Волжин Г. Н., Шаранович Г. А., Барановский В. И. Оборудование, оснастка и приборы для механизации работ по техническому обслуживанию и текущему ремонту грузовых автомобилей. — М.: ЦНИИОМПТ, 1970.
21. Костин К. А., Цикун Д. С. Технологические постовые карты на ТР агрегатов автомобилей. — М: Транспорт, 1965.
22. .Кац А. М. Автомобильные кузова. — М.: Транспорт, 1980.
23. Ермолов Р. С, Колесник В. К., Ивашов Р. А. Электроизмерительные устройства для диагностики машин и механизмов. — Л.: Энергия, 1979.
24. Ермолов И. Н., Останин Ю. Я. Методы и средства неразрушающего контроля качества. — М.: Высшая школа, 1988.
25. Напольский Г. М. Технологическое проектирование автотранспортных предприятий и СТО. — М.: Транспорт, 1985.