Технология послеуборочной обработки и хранения зерна (гречихи семенной)
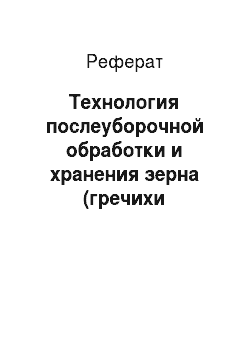
Технологические потери по своему характеру можно разделить на неизбежные и устранимые. К неизбежным относят, обусловленные воздействием на урожай машин и механизмов при его перемещении на зернотоках и комплексах по технологическим машинам, причем величина этих потерь оговорена соответствующими ТНПА. К устранимым относят потери, возникающие по причине неправильной настройки, неисправности машин… Читать ещё >
Технология послеуборочной обработки и хранения зерна (гречихи семенной) (реферат, курсовая, диплом, контрольная)
Содержание Введение Технология послеуборочной обработки и хранения зерна Список используемой литературы Приложения Введение Сельское хозяйство занимает особое место среди других отраслей народного хозяйства. Оно призвано обеспечить потребности населения в продуктах питания, животноводства — в кормах, перерабатывающей промышленности — в сырье. Производство зерна — ведущая отрасль растениеводства. По объёму производства зерна Россия занимает 7 место среди стран мира, её доля в мировом производстве — 2,8% (А.В. Хохлов, 2014).
Одной из ценных продовольственных и кормовых культура является овес, который по сравнению с другими хлебными культурами обладает повышенным содержанием незаменимой аминокислоты — лизина. Его используют для получения крупы, хлопьев, толокна, муки. Следовательно, сохранение и рациональное использование выращенного урожая, получение максимума продуктов из сырья — важнейшая государственная задача.
Одним из основных этапов производства зерна является послеуборочная обработка, заключающаяся в его очистке и сушке. Послеуборочная обработка зерна в себестоимости составляет около 40%, а в затратах труда — более 50% (С.С. Ямпилов, 2006). В связи с этим послеуборочная обработка и хранение зерна являются неотъемлемой и важной составной частью всего сельскохозяйственного производства. При этом, перед сельхозпроизводителями стоят задачи получить не только хороший урожай, но и сохранить его таким образом, чтобы избежать потерь. Потери зерна и продуктов его переработки могут иметь место вследствие целого ряда причин. Значительное количество выращенного зерна теряется при перевозке зерна, в период послеуборочной доработки и хранения. Чтобы снизить потери зерна до минимума необходимо защитить его от воздействия неблагоприятной среды, создать условия при которых заторможен обмен веществ. Для решения этих задач необходимы зернохранилища, оборудованные соответствующей техникой, для сушки, активного вентилирования, обеззараживания зерна, поступающего на предприятия, осуществляющие приём и размещение, хранение больших масс зерна.
Технология хранения зерна — это приемы и способы воздействия на зерновые массы и окружающую среду, позволяющих обеспечить количественно-качественную сохранность зерновых масс с учетом их особенностей: какие режимы хранения применять, какая продолжительность хранения, как бороться с вредителями хлебных запасов, как сушить и вентилировать зерно и т. д.
Зерно — это живой организм, оно дышит, при определенных условиях может прорасти, может погибнуть или испортиться. Жизненные процессы в зерне могут при благоприятных условиях интенсифицироваться, а при неблагоприятной ситуации — замедлиться. Интенсивность жизненных процессов зависит от условий хранения, т. е. от состояния окружающей среды (тепло, холод, влажность), от состояния самого зерна (влажность, температура, содержание сорной и зерновой примесей). Это имеет большое значение, т.к. лишь на основе знания биохимических процессов, отмеченных в хранящейся продукции и влияния на них, возможна более рациональная организация хранения больших масс того или иного растительного сырья и сведение потерь до минимума.
Поэтому перед работниками зерноприёмных предприятий поставлена задача так организовать поточную обработку зерновой массы, чтобы:
— сохранить зерно без потерь в массе или с минимальными потерями;
— сохранить зерно без ухудшения качества, повысить качество зерновых;
— сократить затраты труда и средств на единицу массы зерна при наилучшем сохранении его количества и качества.
Цель данной работы: закрепление теоретических и практических знаний в области обработки и хранения зерна, а именно — овса продовольственного.
Работа состоит из введения, основной части, списка литературы и приложений.
Технология послеуборочной обработки и хранения зерна (гречихи семенной) Увеличение производства продукции растениеводства требует соблюдения условий, способствующих повышению качества и сохранности продукции: методов заготовок, хранения, технологий первичной обработки и последующей переработки.
Решая проблему хранения, нельзя забывать, что растительное сырье — это живой биологический материал, который представляет собой огромное количество отдельных зерен, клубней, корнеплодов, клубнеплодов, корней, плодов, овощей, проявляющих в зависимости от многих условий в той или иной степени свою жизнедеятельность. Задачей обработки, хранения и ухода за этим биологическими объектами является применение таких методов, которые свели бы к минимуму все жизненные процессы, сохранили бы жизнеспособность семян и посадочного материала.
Зерно является основным продуктом сельского хозяйства. В сложной цепи агротехнических и технологических приемов, направленных на получение и сохранение высоких посевных и урожайных качеств семян, важнейшая роль принадлежит послеуборочной обработке, технология которой складывается из целого ряда последовательных технологических операций, способствующих обеспечению сохранности зерновых масс и применению определенных режимов хранения, в результате которых получают зерно необходимого качества. К основным из них относят: приемку зерна и формирование партий, очистку от примесей, временное консервирование влажного зерна, сушку, вторичную очистку или сортирование, калибровка и активное вентилирование.
Каждую из операций необходимо проводить в определенные сроки. Весь процесс целесообразно проводить на поточных технологических линиях методом полного потока, т. е. операции выполняются последовательно за один проход не прерывая процесса вплоть до приведения зерна в стойкое при хранении состояние. При этом применяют машины и средства механизации, включаемые в поточные линии предприятий. Продовольственное и фуражное зерно зерновых культур обрабатывают на зерноочистительных агрегатах ЗАВ (в сухих зонах) и на зерноочистительных комплексах типа КЗС (во влажных зонах) различной производительности (Л.Б. Винничек, А. А. Галиуллина, 2005).
Для правильной организации приемки и размещения зерна нового урожая на хлебоприемном предприятии целесообразно проводить предварительную оценку качества зерна в поле. Из обмолоченных апробационных снопов отбирают пробы, в которых определяют тип, подтип, стекловидность, натуру, количество и качество клейковины (для пшеницы). Массу принимаемого зерна определяют по результатам взвешивания. Непосредственно при приемке из каждой партии зерна отбирают щупом точечные пробы в соответствии со стандартом. Из точечных проб формируют объединенную пробу, которую подвергают быстрому анализу: дают органолептическую оценку (цвет, запах), определяют тип, подтип, зараженность и влажность по электровлагомерам. По этим показателям направляют машину на разгрузку в соответствии с планом размещения зерна, разработанным перед приемом урожая.
Поступающее на хлебоприемное предприятие зерно направляют для подработки, формирования товарных партий и хранения исходя из их качества. Формирование однородных партий зерна его размещение осуществляют по культурам, классам, типам, подтипам и другим специфическим показателям качества, характеризующие его технологические свойства в соответствии с государственными стандартами на заготавливаемое и поставляемое зерно, а также по состоянию влажности и засоренности (Е.Н. Вобликов и др., 2001).
Сушка и очистка являются основными приемами послеуборочной обработки зерна и семян с целью доведения их до требуемых кондиций по влажности и засоренности.
Очистка зерна от примесей — важнейший прием в обработке зерна, существенно влияющий на стабильность качества хранящегося зерна; улучшающий качество партий зерна, передаваемых в переработку; повышающий эффективность работы и производительность технологического оборудования, включенного в схему процесса после очистки; повышающий степень использования зерна за счет использования выделенных отходов на фуражные цели.
В зависимости от состояния и целевого назначения зерна могут проводить различные виды очистки: предварительную, первичную и вторичную (для доведения семян до кондиций посевных стандартов).
Очистка проводится на воздушно-решетных сепараторах, в триерах и других зерноочистительных машинах. При очистке используются различия зерна и семян основной культуры и примесей по таким физическим свойствам, как размеры, аэродинамические свойства (парусность), плотность, состояние поверхности, форма. Принцип работы сепарирующих органов основан на различии физико-механических свойств отдельных частиц зерновой смеси. Способы очистки и сортирования семян определяются в зависимости от физико-механических свойств составляющих исходного вороха. На практике получили распространение следующие способы очистки (Е.И. Трубилин и др., 2009):
а) очистка семян воздушным потоком;
б) разделение семян по размерам на решетках;
в) разделение семян по длине на триерах;
г) разделение семян по форме и свойствам их поверхности;
д) очистка и сортирование семян по плотности;
е) электрические методы разделения зерна Технологический эффект от очистки тем выше, чем больше отделимых примесей удаляется из зерновой массы. Минимальный технологический эффект первичной очистки зерна должен составить не менее 60%. Это значит, что в зерновой массе после очистки должно остаться не более 40% содержавшихся в ней первоначально примесей.
Предварительная очистка проводится сразу после поступления зерна на ток. Её цель состоит в снижении физиологической активности вороха и повышение его сыпучести за счёт выделения наиболее влажных, крупных и лёгких фракций сорной примеси. Предварительную очистку проводят на самоходных и стационарных ворохоочистителях, которые рассчитаны на обработку зерновой массы с влажностью до 40% и содержанием сорной примеси до 20%, в том числе фракции соломистых примесей — до 5%. Их паспортная производительность составляет 20 — 25 т/ч (самоходные) и 50 т/ч (стационарные). Операция считается удовлетворительно выполненной в том случае, когда содержание соломистых примесей длиной частиц до 50 мм не более 0,2%, а частиц длиной более 50 мм нет вообще. При этом потери полноценного зерна в отход не должны превышать 0,05% от массы зерна основной культуры в исходном материале (С.С. Ямпилов, 2003).
Первичная очистка зерна проводится после сушки. Цель первичной очистки заключается в доведении зерновой массы по чистоте до требований стандарта на продовольственной зерно обрабатываемой культуры. При проведении операции из зерна удаляется как сорная, так и зерновая примеси.
При первичной очистке исходную зерновую смесь сепарируют на следующие фракции: продовольственное зерно 1 сорта, фуражное зерно 2 сорта, мелкие отходы, крупные отходы и легкие примеси. Проводится первичная очистка на воздушно-решётных машинах типа ЗВС. При оптимальных режимах работы за один проход через машину из зерна удаляется приблизительно 60% примесей. Допустимые суммарные потери основного зерна в отходы не должны превышать 1,5%. Данный класс машин рассчитан на обработку зерновых масс влажностью до 18% и содержанием сорной примеси до 8%. Их паспортная производительность составляет 20 т/ч (Е.И. Трубилин и др., 2009).
Вторичная очистка или сортировка применяется после проведения первичной очистки при подготовке семенного материала, или в случае необходимости выделения трудноотделимых примесей из партии продоволь-ственного зерна. Сортировка отличается от всех видов очистки тем, что при её проведении из зерновой массы помимо примесей выделяется зерно II сорта, полноценное в семенном отношении. Для проведения этой операции используются воздушно-решётные машины типа СВУ с паспортной производительностью 5 т/ч, триерные блоки, пневмосортировальные столы и т. д. К операции предъявляются следующие требования: количество семян основной культуры, попадающих в отходы, не должно превышать 1%, а попадание полноценных семян во II сорт — не более 3% от массы основной культуры в исходном материале. В процессе триерования содержание полноценных зёрен не должно в отходах превышать 0,5% при обработке продовольственного зерна и 3% - при очистке семян. Общее дробление семян допускается до 1%. Влажность и содержание сорной примеси в зерне, поступающем на обработку, должны быть менее 18% и 3% соответственно (С.С. Ямпилов, 2006).
Сушка является основной технологической операцией по приведению зерна и семян в устойчивое при их хранении состояние. Только после того, как из зерновой массы удалена вся избыточная влага (то есть свободная вода) и зерно доведено до сухого состояния (влажность должна быть ниже критической), можно рассчитывать на его надежную сохранность в течение длительного периода времени.
Влажность свежеубранного зерна нередко составляет 20−35%. Такое зерно необходимо в короткий срок высушить, доведя его влажность до кондиционной. Согласно агротехническим требованиям на длительное хранение следует засыпать зерно влажностью до 14%. С увеличением влажности возрастает интенсивность дыхания зерна, увеличивается выделение теплоты и происходит самосогревание массы. Снизить влажность зерна можно естественной сушкой на открытой площадке, вентилированием атмосферным или подогретым воздухом и искусственной сушкой в зерносушилках.
Для естественной сушки зерно рассыпают на току слоем 10−15 см и периодически перелопачивают или перебрасывают с места на место зернопультом, зерно метателем, зернопогрузчиком. Естественную сушку применяют, если влажность зерновой смеси меньше 20%.
Для временной консервации семян применяют активное вентилирование — принудительное продувание воздухом зерновой массы, находящейся в покое, то есть без перемещения. Воздух с помощью вентиляторов, обеспечивающих необходимую подачу и развивающих нужный напор, через систему специальных каналов или труб нагнетается в больших количествах в зерновую массу и оказывает существенное влияние на ее состояние. Этот технологический прием имеет разностороннее значение и поэтому может применяться в различных целях: для сушки, охлаждения, послеуборочного дозревания зерна и семян, ликвидации самосогревания.
Для активного вентилирования зерно помещают в напольные или бункерные установки и пропускают через неподвижный слой зерна атмосферный воздух. Очень важно установить правильный режим активного вентилирования: оптимальные количество и параметры (температура, влажность) воздуха. Удельная подача воздуха, т. е. его количество в м3, нагнетаемое на 1 т зерна в час, должно быть достаточным для достижения ожидаемого эффекта и предотвращения образования в зерновой массе застойных зон. Чтобы повысить эффективность этих процессов, воздух в первом случае охлаждают, во втором — нагревают на 2−6°С, в третьем — снижают его влажность (В.В. Цык, 2006).
Для искусственной сушки зерно помещают в сушилку и нагревают до установленной температуры. При нагреве влага из внутренних слоев зерна перемещается на поверхность и испаряется, а затем в виде пара удаляется в окружающую среду. Интенсивность испарения влаги зависит от температуры нагрева зерна и скорости движения газов через зерновой слой. Чем больше показатели этих процессов, тем выше скорость испарения влаги.
Температура нагрева зерна при сушке ограничивается его термостойкостью, т. е. предельно допустимой температурой нагрева, при которой сохраняются семенные и хлебопекарные качества зерна. Допустимая температура нагрева зерна зависит от культуры, сорта, влажности и продолжительности его пребывания в нагретом состоянии.
Существует несколько способов нагрева и сушки зерна: конвективный, кондуктивный (контактный), излучение, электрический, сорбционный способы. Большую часть влажного зерна сушат конвективно-контактным способом в зерносушилках периодического или непрерывного действия в неподвижном, подвижном и псевдосжиженном слое зерновой массы. Зерносушилки бывают стационарные и передвижные, открытого исполнения и с установкой в здании. По конструкции сушильных и охладительных камер различают сушилки барабанные, шахтные, колонковые, карусельные, конвейерные, бункерные и др. Промышленность выпускает сушилки малой (до 2,5 т/ч), средней (до 15 т/ч) и высокой (до 40 т/ч) производительности.
Для выбора режимов сушки большое значение имеет степень зрелости зерна. Свежеубранное зерно отличается пониженной термоустойчивостью по сравнению с зерном, прошедшим послеуборочное дозревание. Для того, чтобы сохранить качество свежеубранного зерна, его сушат при более мягких режимах, т. е. при пониженных температурах агента сушки и нагрева зерна (при t1 = 70…80 С — Qпр. д = 38…40 °С). При этих параметрах повышаются всхожесть и энергия прорастания зерна, а также улучшаются хлебопекарные свойства. При температурах агента сушки и нагрева зерна соответственно t1 = 90 °C и n|прд = 45 °C всхожесть понижается, но хлебопекарные свойства еще сохраняются. Применение в данном случае ступенчатых режимов сушки позволяет избежать перегрева зерна и ухудшения его свойств. Принцип заключается в следующем: повышение температуры агента сушки осуществляется по мере снижения влажности зерна. При этом на первой ступени сушки целесообразно применять большие подачи агента сушки и скорости смеси, чем на второй.
После сушки зерно охлаждают. Для этого на завершающем этапе сушки зерно обрабатывают холодным воздухом. Снижение температуры зерна значительно ослабляет интенсивность дыхания. Чем ниже температура, тем меньше интенсивность дыхания. При температуре 5 °C и ниже на зерне с влажностью до 16% жизнедеятельность всех компонентов зерновой массы резко снижается, а жизнедеятельность вредных насекомых и микроорганизмов полностью прекращается. Снижение температуры зерна до отрицательных значений (промораживание) обеспечивает глубокий анабиоз (покой) зерновой массы и длительный консервирующий эффект. Сухие зерна при промораживании не снижают всхожести, так как связанная вода не замерзает. (Г.Е. Чепурин, 2011).
Что касается овса, то сразу после уборки он менее устойчив в хранении, чем другие зерновые культуры. Период самосогревания у него наступает наиболее быстро, так как в свежеубранном овсе содержится много недозревших зерен. Поэтому очистка овса перед закладкой на хранение будет способствовать уменьшению самосортирования и повышению стойкости хранения.
При размещении и хранении учитывают состояние зерна овса по влажности, засоренности и натуре. К чистому зерну относят зерно с содержанием сорной примеси до 1% включительно и зерновой до 2% включительно, средней чистоты соответственно свыше 1 до 3% включительно и свыше 2 до 4% включительно, к сорному соответственно свыше 3 и свыше 4%. К высоконатурному овсу относится зерно с натурой свыше 510 г/л, средненатурному свыше 460 до 510 включительно и низконатурному и ниже.
Первым этапом хранения зерна овса, является сортирование и предварительная очистка собранного урожая. Первичная очистка зерна проводится сразу после уборки, что позволяет сэкономить при дальнейшей сушке зерна овса. Контроль состояния сортированного зерна определяется по количеству содержащегося углекислого газа между зёрнами. Накопление углекислого газа прямо говорит о неблагоприятных процессах внутри насыпи. Увеличение количества нестойких зёрен овса может привести к быстрому увеличению температуры внутри насыпи. При первых признаках самосогревания овес охлаждают путем провеивания на очистных машинах или перелопачиванием.
После очистки овса от крупных примесей в ворохоочистителе зерно поступает в воздушно-ситовые сепараторы. Крупную фракцию получают сходом с подсевных сит с отверстиями размером 2×20 мм, мелкую (проходом этих сит) далее очищают в сепараторе на подсевных ситах с отверстиями размером 1,8Ч20 мм. Для выделения из овса овсюга и других длинных примесей применяют триеры с ячеями ф 14…16 мм. Для выделения из овса коротких примесей (гречихи вьюнковой, вьюнка полевого, пшеницы, ржи, ячменя, голых зерен овса, семян редьки дикой и др.) используют триеры с ячеями 0 8…9,5 мм. Для выделения легких примесей, шелушеных зерен овса и овсюга в пневмосепарирующих каналах скорость воздушного потока устанавливают в пределах 5…6 м/с.
Режимы сушки продовольственного зерна показаны в табл. 1.1.
Таблица 1.1
Культура | Влажность зерна до сушки, % | Шахтные и колонковые сушилки | Барабанные сушилки | ||
t теплоносителя ±10 град. | предельная t нагрева зерна, град. | предельная t нагрева зерна, град. | |||
Пшеница | до 18 от 18 до 22 свыше 22 | ||||
Рожь, ячмень | до 18 от 18 до 22 свыше 22 | ||||
Овес | до 18 от 18 до 22 свыше | ||||
Гречиха | до 18 от 18 до 22 свыше | ||||
При сушке овса в шахтных прямоточных сушилках и в шахтных рециркуляционных сушилках без дополнительных устройств предельная температура нагрева зерна 50 °C независимо от первоначальной влажности зерна. Предельная температура агента сушки при одноступенчатом режиме 140 °C (в шахтных прямоточных зерносушилках) и при двухступенчатом в обеих сушилках в I зоне 130°, во II — 160 °C. Овес высушивают для крупяной и комбикормовой промышленности до влажности 14,5…15,5%, если крупяные предприятия не имеют сушилок, овес высушивают до 12,5…13,5%; для переработки на солод в спиртовом производстве до 15…16%, для хранения 13…14%. 88
При просушивании семенного зерна овса производительность сушильных агрегатов должна быть вдвое меньше чем при сушке товарного зерна. Зерновая масса овса при влажности до 21% один раз пропускается через сушильный агрегат, при влажности до 27% два раза, при влажности свыше 27% три. На длительное хранение зерно овса закладывается при влажности не более 15% После сушки и охлаждения овес следует по возможности быстрее направить на шелушение, отволаживать его рекомендуется не более 20−30 мин, так как оболочки при этом впитывают влагу, отчего эффективность шелушения снижается.
Следует отметить, что в процессе послеуборочной обработки и хранения на всех этапах и операциях, происходят неизбежные потери зерна.
Технологические потери по своему характеру можно разделить на неизбежные и устранимые. К неизбежным относят, обусловленные воздействием на урожай машин и механизмов при его перемещении на зернотоках и комплексах по технологическим машинам, причем величина этих потерь оговорена соответствующими ТНПА. К устранимым относят потери, возникающие по причине неправильной настройки, неисправности машин и механизмов, несовершенства их конструкции, а также возникающие по вине обслуживающего персонала (неправильная организация работ, приводящая к порче и снижению качества урожая и т. д.). Технологически допустимый уровень потерь зерна в процессе послеуборочной обработки на зерноочистительно-сушильных комплексах и зернотоках — не более 3%. Результаты испытаний зерноочистительных и сушильных агрегатов, а также выборочный контроль за их работой в производственных условиях показывают, что при высокой засоренности бункерного зерна (8…10%) и его дроблении комбайнами при уборке (2…3%) на этапах предварительной и первичной очистки при ненадлежащем подборе решет и других режимов (загрузка, скорость воздушного потока) в неиспользуемые отходы уходит до 8% зерна. В процессе сушки за счет выдувания (уноса) зерна из камер потери могут возрастать на 2…3%. В целом же, если не выдерживаются требования к качеству хлебного вороха и нарушаются режимы его переработки на стадии послеуборочной доработки, отходы могут составлять около 30% бункерного урожая. Из этого объема немногим более 10% составляют используемые отходы (проход сортировальных решет), а в остальных 20% (сорная примесь, усушка) безвозвратно теряется до 10% зерна. При этом, неправильный подбор сортировальных рабочих органов (решет) также приводит либо к потерям зерна в отходы, либо к некачественной очистке.
Меры по предупреждению потерь зерна (С.С. Ямпилов, 2004):
— четкое следование рекомендациям по настройкам и регулировкам машин, изложенным в инструкциях и руководствах по эксплуатации заводов изготовителей;
— использование лабораторных классификаторов (лабораторных машин) соответствующего назначения для подбора рабочих поверхностей и режимов работы сортировальных машин. Эти меры позволят избежать ошибок в настройках машин, а в итоге — снизить потери зерна;
— использование более современных средств управления машинами, сокращая время на перенастройку (уменьшается время холостой работы машин и, как следствие, снижается общий расход электроэнергии). Применение автоматизации технологических процессов позволяет сократить время настройки машин на требуемый режим работы на 30…50%, что особенно актуально на комплексах и линиях подготовки семян, где происходит частая смена обрабатываемых культур, сортов, соответственно, требуются перенастройки;
— обучение персонала, более четкая организация труда также позволяют сократить время «холостой работы» машин и оборудования в процессе настройки и тем самым уменьшить непроизводительные расходы электроэнергии.
Значительные потери зерна происходят в процессе хранения, связанные с дыханием зерна и с жизнедеятельностью микроорганизмов и вредителей. Чтобы правильно организовать хранение зерна, необходимо иметь ясное представление о зерновой массе как объекте хранения, о компонентах, входящих в состав зерновой массы и придающих ей специфические свойства, которые при хранении обязательно должны быть учтены.
Сложность хранения зерна связана со специфичностью продукта: зерно — живой растительный организм, в клетках и тканях которых протекают различные физиолого-биологические процессы. Все они находятся в тесной взаимосвязи с окружающей средой, а поэтому режимы и способы хранения базируются на изучении взаимосвязей между хранимым объектом и окружающей средой.
Основными факторами являются влажность зерна, количество и состав примесей, относительная влажность воздуха, температура и другие, которые оказывают действие также на биохимические и физиологические процессы и в значительной мере определяют успех хранения зерновых масс.
Ведущим процессом жизнедеятельности зерна и семян во время хранения является дыхание. При дыхании зерна наблюдается не только потери сухого вещества, но и происходит увеличение влажности зерновой массы, изменение состава воздуха межзерновых пространств и накопление тепла. Этот процесс крайне нежелателен, так как происходит образование этилового спирта, который оказывает неблагоприятное влияние на жизненные функции клеток зерна и приводит к потере его жизнеспособности. Крайне нежелательное явление в период хранения — прорастание зерна, так как активизируется деятельность ферментов, что приводит к необратимым изменениям его химического состава.
Процесс жизнедеятельности зерна и семян, тесно связанный с нарушением метаболизма в клетках и приводящий к необратимым процессам как в химическом составе, так и в структуре зерновок — старение. С ним связана долговечность зерна (хозяйственная, технологическая и биологическая). Надо обратить внимание на факторы, ускоряющие и замедляющие процесс старения, а также изменения, происходящие в химическом составе зерна и семян.
Постоянным компонентом зерновой массы являются микроорганизмы, которые при благоприятных условиях проявляют свою активную жизнедеятельность в виде дыхания, питания и размножения, что приводит к потере сухих веществ и снижению посевных и товарных качеств зерна.
При хранении важное значение имеет технология хранения зерна, задача которой — создать условия, благоприятные для сохранения надлежащего качества зерна. Способы хранения зерна в зависимости от его состояния классифицируют на сырое, сухое, охлажденное и т. д., при этом учитываются конструктивные особенности хранилища. Способы хранения базируются на их физических и физиологических свойствах. Применение определенного способа хранения зависит от технического и экономического уровня и климатических особенностей.
Хорошая сыпучесть зерновых масс позволяет хранить их в различных емкостях, начиная от мешков и кончая большими силосами. Хранение в мешках получило название хранение в таре, а размещение в больших хранилищах — складах, силосах, бункерах — хранение насыпью.
Основной способ хранения зерновых масс — хранение насыпью. В этом случае полнее используются зернохранилища, больше возможностей для механизации операций, отпадают расходы на тару и перетаривание продуктов, легче бороться с вредителями. В таре хранят некоторые партии семенного зерна, семена с хрупкой оболочкой.
Технология хранения овса не предусматривает каких-то специальных норм укладывания и насыпи по высоте собранных зёрен. В зернохранилищах размещение овса происходит точно так же, как и пшеницы, ячменя, ржи.
Основными типами зернохранилищ являются склады с горизонтальными или наклонными полями и элеваторы. Основное преимущество элеваторов — высокая механизация работ с зерновыми массами, основной недостаток — в них можно хранить только сухое зерно, обладающее хорошей сыпучестью.
В практике хранения зерна применяют три основных режима: хранение в сухом состоянии; хранение в охлажденном состоянии и хранение без доступа воздуха, т. е. в герметических условиях. В основном применяют два первых.
Важнейшим мероприятием, обеспечивающим успешное хранение зерновых масс как по качеству, так и по экономическим показателям, является правильное размещение их в зернохранилищах. Соблюдая правила размещения, можно организовать рациональное хранение зерновых масс, то есть избежать их излишнего перемещения, эффективно провести их обработку, хорошо использовать вместимость хранилищ, предотвратить потери в качестве и до минимума сократить потери в массе.
В основу правил размещения зерновых масс в зернохранилищах положены следующие принципы: учет показателей качества каждой партии зерна и связанных с этим возможностей использования ее по тому или иному назначению; учет устойчивости каждой партии зерна при различных условиях хранения. Запрещается смешивать партии зерна различного назначения и разной устойчивости. При этом учитывают ботанические признаки (тип, подтип и сорт зерна), целевое назначение, важнейшие показатели качества (влажность, засоренность, зараженность).
Влажность зерна, температура и газовый состав воздуха в межзерновых пространствах зерновой массы — основные определяющие факторы сохранности и режимов хранения зерна и семян. Динамическое состояние этих факторов в зерновой массе требует постоянного контроля за ним, и в случае необходимости, внесения соответствующих корректив в технологический процесс хранения. Наблюдать за зерновыми массами необходимо систематически в течение всего периода хранения, т.к. это позволяет своевременно предотвратить все нежелательные явления и с минимальными затратами довести зерновую массу до состояния консервирования или реализовать ее без потерь.
Наблюдение организуют за каждой партией зерна. К числу показателей, по которым при систематическом наблюдении можно безошибочно определить состояние зерновой массы, относят ее температуру, влажность, содержание примесей, зараженность, показатели свежести (цвет и запах). В партиях семенного зерна дополнительно проверяют его всхожесть и энергию прорастания.
Периодичность проверки зерновой массы по этим показателям зависит от ее состояния и условий хранения (времени года, типа хранилищ, высоты насыпи). Так, чем физиологически активнее зерновая масса, тем чаще проверяется ее температура. Например, в сухом зерне она измеряется один раз в 15 дней, а в сыром неохлажденном зерне — ежедневно.
Сроки проверки зерна на зараженность клещами и насекомыми зависят от температуры: при температуре выше 15 оС — один раз в 10 дней, при температуре ниже 5 оС — один раз в месяц. В зависимости от влажности и температуры установлены и сроки наблюдений по другим показателям. Результаты наблюдений в хронологическом порядке заносят в журнал наблюдений.
При хранении проводят количественно-качественный учет зерна, в процессе которого в приходно-расходной книге указывают количество поступившего на склад и выбывшего из него зерна, выявляют неизбежные потери в массе (естественную убыль), потери массы, связанные с изменением качества (уменьшение влажности), и неоправданные (сверхнормативные) потери. По окончании срока хранения составляется и утверждается акт зачистки зернохранилища с указанием всех видов и величины потерь.
Большой вред зерну причиняют вредители хлебных запасов, которые могут развиваться в условиях складов и элеваторов. Большая часть насекомых-вредителей (до 90%) развивается в верхней части силоса. Там еженедельно и берут пробы зерна специальными ловушками, оценивая скорость прироста насекомых.
Меры борьбы с вредителями: предупредительные (профилактические) и истребительные. Истребительные меры, направленные на уничтожение насекомых и клещей, получили название дезинсекции. Применяемые способы дезинсекции можно разделить на две большие группы физико-механические и химические (с применением ядохимикатов — пестицидов). Наиболее распространенным способом дезинсекции зернохранилищ является фумигация (газация) — обеззараживание парами или газами отравляющих веществ. В настоящее время для фумигации складов и зерна вместо бромистого метила применяют более эффективные препараты на основе соединений фосфида водорода с металлами. Это магтоксин, фостоксин и другие препараты в виде таблеток. Их размещают на полу, на поверхности зерна, между штабелей мешков с семенами. Продолжительность фумигации при температуре 5−10 оС составляет 10 суток; при 11−15 оС — 7; при 16−20 оС — 6; при 21−25 оС — 5 суток; выше 26 оС — 4 суток. Реализация продукции разрешается через 20 суток после фумигации.
Истребление грызунов называется дератизацией и может проводиться различными способами: механическим (отлов с помощью капканов и ловушек) и химическим (применение ядовитых приманок).
Таким образом, все мероприятия по повышению устойчивости зерновых масс при хранении должны быть экономически выгодными. Они обязательно проводятся, если это необходимо для предотвращения порчи зерна и снижения потерь. Применение вышеперечисленных технологических приемов, способов хранения и интенсификации процессов в послеуборочной обработке, используемых в различной последовательности и различных сочетаниях, позволяют сократить потери зерна на 7−10%.
Факторы и технологические процессы послеуборочной обработки и хранения зерна наглядно представлены на схеме в Приложении 1.
Как уже было сказано ранее, половина всех потерь зерна приходится на послеуборочную обработку и, в основном, на хранение. По экспертной оценке потери зерна в среднем в России составляют 17%. В отдельных регионах при неблагоприятных погодных условиях хозяйства теряют по 25−40% собранного урожая. Причем только 25% потерь связано с технологией уборочных работ, 1% - транспортировкой и до 74% потерь приходится на послеуборочный период (переработку и хранение). Послеуборочные потери зерна превосходят по объему экспортный потенциал страны, в то время как средний мировой показатель потерь составляет около 5% (В.М. Дринча, 2010).
Обусловлено это, в первую очередь, различным уровнем технологического и технического обеспечения зернопроизводства. При этом, эти потери можно уменьшить, если применить более эффективные способы послеуборочной обработки зерна и его сохранности. Например, сократить их поможет мобильная зерносушилка.
За рубежом мобильные зерносушилки весьма распространены и пользуются большой популярностью. В России также заинтересованы в использовании мобильных зерносушилок, поскольку благодаря именно этому типу сушилок увеличивается период эксплуатации зерноуборочных комбайнов. Они отличаются компактностью и имеют ряд преимуществ (Я.В. Кулагин, 2013):
— занимают мало места, не требуют строительных, монтажных и пусконаладочных работ;
— при необходимости легко перемещаются в другое место;
— по мере увеличения объёмов производства зерна наращивание мощности возможно путём установки дополнительных мобильных зерносушилок;
— ввод в эксплуатацию после переезда на новое место составляет всего 2−3 часа;
— возможность использования весной для контрольной сушки перед продажей зерна;
— после применения зерносушилки по назначению, можно использовать её тепловой модуль для других целей: отопления теплиц, складов, производственных помещений и т. п.;
Кроме того, при изменении производственной деятельности возможна перепродажа мобильных зерносушилок, так как они не требуют демонтажа, пользуются спросом и имеют большой срок службы.
Они могут работать на дизельном топливе, природном газе, метане, пропане, в т. ч. сжиженном. Установок, работающих без подвода электричества на сегодня нет. Для запуска рабочего процесса требуется электрическая мощность от 16 до 90 кВт в зависимости от производительности. Поскольку для получения горячего воздуха приходится проводить два процесса: сжигание топлива и последующую выдувку нагреваемого установкой воздуха, то на этих процессах теряется общий КПД машины, максимально составляющий до 60% (В.Ф. Сорочинский, 2011).
Как альтернатива существующим установкам, в ГНУ ВИЭСХ разрабатывается микротурбина (МТУ), работающих на любом жидком и газообразном топливе. Выработка электричества в МТУ сопровождается созданием высокотемпературной струи выхлопных газов. Тепловая мощность струи зачатую сопоставима с вырабатываемой электрической мощностью. Температура газовой струи 300- 400С соответствует температуре газа, подаваемого в зерносушилку. Общий КПД газотурбинной установки доходит сегодня до 85% (И.З. Полещук, 2003).
Таким образом, зерносушилка на основе МТУ может заменить обычную, а в районах с отсутствием централизованного электроснабжения просто не заменима.
Сама установка компактнее за счет меньшего веса на 1 кВт мощности и будет отличаться от обычной только используемым теплогенератором и наличием собственного электрогенератора.
Ремонтопригодность выше за счет использования в конструкции серийных узлов и деталей выпускаемые Российской промышленностью. Это особенно важно для сельских условий и работы сервисных служб. При этом, МТУ, как теплогенератор, дешевле существующих импортных газовых горелок.
Мобильная зерносушилка МЕПУ М150к представлена в Приложении 2.
Таким образом, сегодня в России расширяются посевные площади зерна, увеличиваются валовые сборы. Необходимость новой государственной программы производства отечественных зерносушилок очевидна. Новые технологии и конкурентные преимущества МТУ дают возможность создания современных установок, не имеющих аналогов за рубежом. По этой причине недорогая мобильная зерносушилка — оптимальный способ повышения эффективности зернопроизводства.
Список используемой литературы зерно сушка продовольственный потеря
1. Атаназевич В. И. Сушка зерна / В. И. Атаназевич. — М.: ДеЛи принт, 2007. — 480 с.
2. Вобликов Е. М. Послеуборочная обработка и хранение зерна / Е. М. Вобликов. — Ростов н/Д.: МарТ, 2001. — 240 с.
3. Войсковой А. И. Хранение и оценка качества зерна и семян: учебное пособие / А. И. Войсковой и др. — Ставрополь: Агрус, 2008. — 146 с.
4. Дринча В. М. Резервы снижения потерь зерна при хранении / В. М. Дринча, Б. Ж. Цыдендоржиев // Комбикорма. — 2010. — № 7.
5. Изотова А. И. Технология элеваторной промышленности. Учебно-практическое пособие / А. И. Изотова. — М.: МГУТУ, 2012. — 148 с.
6. Кулагин Я. В. Возможность применения микро газотурбинных установок для мобильных зерносушилок / Я. В. Кулагин // Журнал «Инновации в сельском хозяйстве». — 2013. — 2 (4). — 78 с. С. 2−9.
7. Малин Н. И. Технология хранения зерна / Н. И. Малин. — М.: КолосС, 2005. — 280 с.
8. Мобильные зерносушилки сократят расходы // Информационное агентство. Аграрные новости. — 2012. -№ 11.
9. Пилипюк В. Л. Технология хранения зерна и семян: учебное пособие / В. Л. Пилипюк. — М.: Вузовский учебник, 2009. — 455 с.
10. Полещук И. З.
Введение
в теплоэнергетику: Учебное пособие / И. З. Полещук, Н. М. Цирельман. — Уфа: УГАТУ, 2003. — 108 с.
11. Проблемы и перспективы развития агропромышленного производства: монография / Под ред. Л. Б. Винничек и др. — Пенза: РИО ПГСХА, 2014. — 220 с.
12. Сорочинский В. Ф. Снижение энергозатрат при конвективной сушке зерна / В. Ф. Сорочинский // Хранение и переработка зерна. — 2011. — № 7.
13. Тихонов Н. И. Хранение зерна: учеб. пособие / Н. И. Тихонов, А. М. Беляков. — Волгоград: Изд-во ВолГУ, 2006. — 108 с.
14. Трубилин Е. И. Механизация послеуброчной обработки зерна и семян / Е. И. Трубилин, Н. Ф. Федоренко, А. И. Тлишев. — Краснодар: КГАУ, 2009. — 96 с.
15. Тумановская Н. Б. Технология хранения зерна: Учебно-практическое пособие / Н. Б. Тумановская. — М.: МГУТУ, 2012. ?192 с.
16. Цык В. В. Активное вентилирование зерна и семян: Лекция / В. В. Цык. — Горки: БелГСА, 2006. — 24 с.
17. Чепурин Г. Е. Уборка и послеуборочная обработка зерновых культур в экстремальных условиях Сибири / Г. Е. Чепурин и др. — М.: ФГНУ «Росинформагротех», 2011. — 176 с.
18. Юкиш А. Е. Техника и технология хранения зерна / А. Е. Юкиш, О. А. Ильина. — М.: ДеЛи принт, 2009. — 718 с.
19. Ямпилов С. С. Технологические и технические решения проблемы очистки зерна / С. С. Ямпилов. — Улан-Удэ: Изд-во ВСГТУ, 2006. -167 с.
20. Ямпилов С. С. Технологическое и техническое обеспечение ресурсо-энергосберегающих процессов очистки и сортирования зерна и семян / С. С. Ямпилов. — Улан-Удэ: Изд-во ВСГТУ, 2003. — 262 с.
Приложения Приложение 1
Факторы и технологические процессы послеуборочной обработки и хранения зерна Приложение 2
Мобильная зерносушилка МЕПУ М150к