Сопротивление разрушению модифицированных циркониевых сплавов для оболочечных труб атомных реакторов
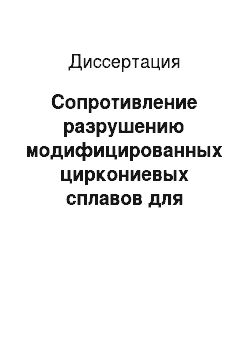
Э110Г и Э635М в сравнении со штатными составами сплавов после высокотемпературного окисления в паре при Т = 1100 °C и ЛГО = 18%. Показано, что основными структурными факторами, ограничивающими пластичность и трещиностойкость сплавов после высокотемпературного окисления, являются: доля крупных участков обогащенной кислородом а^г-фазы, доля структуры типа «корзиночное плетение» и содержание… Читать ещё >
Содержание
- 1. Аналитический обзор литературы
- 1. 1. Структура и механические свойства циркониевых сплавов
- 1. 1. 1. Химический состав, структура и свойства промышленных сплавов циркония
- 1. 1. 2. Технологический процесс производства циркония ядерной чистоты и промышленных сплавов на основе циркония
- 1. 1. 3. Совершенствование сплавов циркония
- 1. 2. Коррозионное разрушение сплавов циркония 28 1.2.1. Равномерная коррозия 28 1.2.2 Локальная коррозия (коррозионное растрескивание под напряжением)
- 1. 3. Охрупчивание оболочек ТВЭЛов при высокотемпературном окислении
- 1. 3. 1. Авария типа LOCA
- 1. 3. 2. Микроструктура и разрушение оболочек ТВЭЛов после высокотемпературного окисления
- 1. 3. 3. Требования, предъявляемые к ТВЭЛам, и исследование их поведения в аварийных условиях
- 1. 4. Методы оценки пластичности и сопротивления разрушению циркониевых сплавов
- 1. 5. Устойчивость пластического течения и технологическая пластичность циркониевых сплавов
- 1. 6. Применение метода акустической эмиссии для анализа процессов деформации и разрушения
- 1. 7. Выводы и постановка задачи исследования
- 1. 1. Структура и механические свойства циркониевых сплавов
- 2. Материал и методики исследования
- 2. 1. Материал
- 2. 2. Механические испытания
- 2. 2. 1. Определение параметров трещиностойкости оболочечных труб в состоянии поставки и после КРН-испытаний
- 2. 2. 2. Оценка трещиностойкости оболочечных труб по критическому коэффициенту интенсивности напряжений Кс
- 2. 2. 3. Оценка трещиностойкости оболочечных труб по энергетическому параметру нелинейной механики разрушения J— интеграл
- 2. 2. 4. Оценка трещиностойкости оболочечных труб после высокотемпературного окисления 63 2.3 Методика приготовления объектов исследования и анализ структуры и изломов
- 3. 1. Испытания на растяжение и анализ диаграмм деформации
- 3. 1. 1. Подготовка образцов и проведение испытания
- 3. 1. 2. Определение характеристик пластичности и деформационного упрочнения
- 3. 1. 3. Пластичность сплавов Э110, Э635 и их модификаций с разной степенью рекристаллизации
- 3. 1. 4. Трещиностойкость сплавов Э110, Э635 и их модификаций в состоянии поставки
- 3. 1. 5. Строение изломов образцов труб после испытаний на трещиностойкость
- 4. 1. Методика локальных КРН — испытаний тонкостенных оболочечных труб с измерением акустической эмиссии
- 4. 1. 1. Схема установки и условия испытаний
- 4. 1. 2. Измерение АЭ: аппаратура и информативные параметры
- 4. 1. 3. Количественная оценка коррозионной повреждаемости труб 84 4.2 Трещиностойкость образцов труб после КРН-испытаний с полным погружением в коррозионную среду
- 4. 2. 1. Предварительное нагружение образцов внутренним давлением
- 4. 2. 2. Трещиностойкость и количественный анализ коррозионных дефектов сплавов после КРН испытаний
- 5. 1. Проведение испытаний образцов труб после высокотемпературного окисления под внутренним давлением
- 5. 2. Структурные исследования
- 5. 2. 1. Методики анализа микроструктуры оболочечных труб после высокотемпературного окисления
- 5. 2. 2. Анализ параметров микроструктуры сплавов после высокотемпературного окисления
- 5. 3. Количественный анализ изломов образцов после испытаний на трещиностойкость
- 5. 4. Взаимосвязь параметра трещиностойкости Кс с характеристиками изломов
- 5. 5. Изменение микротвердости по толщине стенки охрупченных образцов
- 5. 6. Определение содержания кислорода и водорода
- 5. 7. Распределение химических элементов по толщине стенки трубы
- 5. 8. Микростроение изломов
- 5. 9. Влияние микроструктуры на трещиностойкость «ех-р"-слоя
Сопротивление разрушению модифицированных циркониевых сплавов для оболочечных труб атомных реакторов (реферат, курсовая, диплом, контрольная)
Актуальность работы.
Сопротивление разрушению является, важнейшей характеристикой оболочек ТВЭЛов — наиболее ответственных элементов тепловыделяющих сборок (TBC) атомных реакторов. Растрескивание циркониевых изделий при изготовлении повышает процент бракана производстве, а при эксплуатацииснижает ресурс, эксплуатационную надежность и безопасность, работы реакторов. Поэтому задача получения новых знанит о деформации и разрушениициркониевых сплавов для повышения их технологической пластичности и сопротивления разрушению чрезвычайно-актуальна.
Основным из направлений: совершенствования сплавов циркония для TBC является создание новых модификаций промышленных сплавов, в которых за счет изменения химического состава по легирующим и примесным элементам достигается повышение прочностных характеристик, коррозионной и радиационной стойкости. Основной целью совершенствования промышленных циркониевых сплавов и разработки их новых модификаций? является' для? сплава Э110 повышение прочности, а для сплава Э635 — повышение коррозионной’стойкости.
Для обоснования использования новых модификацийциркониевых сплавов в качестве конструкционных материалов активной зоны помимо экспериментально-подтвержденных закономерностей влияния химического состава сплавов на коррозионную стойкость и радиационную ползучесть необходимо оценить их влияние на пластичность и сопротивление разрушению в различных условиях нагружения.
При эксплуатации ТВЭЛов в составе TBC в реакторах, возможны ситуации, при которых сопротивление разрушению является наиболее критическим параметром. Это различного рода аварии (аварии с потерей теплоносителя, реактивностные аварии, скачки мощности при маневренных режимах работы реактора и др.). При авариях с потерей теплоносителя (аварии типа LOCA), циркониевые оболочки нагреваются до высоких температур (900 -1100 °С) и активно окисляются в паре, после чего резко охлаждаются системой аварийной защиты. Это приводит к охрупчиванию, в результате чего трубы могут разрушиться при последующей выгрузке TBC из активной зоны реактора. Наиболее крупными авариями типа LOCA, произошедшими на атомных станциях в мире являются авария на АЭС «Три-майл-Айлэнд» (США, 1979 г.) и авария на АЭС «Фукусима-1» (Япония, 2011 г.).
Не менее опасным процессом, ограничивающим эксплуатационную надежность элементов TBC особенно после достаточно глубокого выгорания топлива, является коррозионное растрескивание под напряжением (КРН) оболочек ТВЭЛов под воздействием механических напряжений, возникающих в результате расширения топлива, и воздействия йода, выделяющегося в качестве продукта деления топлива. Процесс КРН может привести к образованию сквозных трещин в оболочках и их разгерметизации.
Поэтому важной задачей является выявление основных факторов, определяющих сопротивление разрушению оболочек ТВЭЛов в условиях КРН и LOCA, определение параметров, адекватно характеризующих степень охрупчивания труб из различных модификаций сплавов.
Для определения сопротивления разрушению тонкостенных труб из достаточно пластичных циркониевых сплавов в различных условиях необходимы новые нестандартные высокочувствительные методы, позволяющие не только исследовать механизмы и кинетику разрушения на разных (особенно на начальных) стадиях, но и определять характеристики вязкости разрушения.
Актуальность диссертационной работы подтверждается её выполнением в рамках договоров и контрактов НИТУ «МИСиС», с предприятиями Госкорпорации «Росатом» и Топливной компании «ТВЭЛ» по направлениям, определенным ФЦП «Развитие атомного энергопромышленного комплекса России на 2007;2010 годы и на перспективу до 2015 года», корпоративной Программой «Обеспечение потребностей атомной энергетики и промышленности конкурентоспособными циркониевыми материалами и изделиями», рассчитанной на 2009;2015 годы, а также при финансовой поддержке Российского Фонда Фундаментальных Исследований (проект № 08−03−490-а) и Министерства образования и науки Российской Федерации (проект № 2.1.2/14 024).
Цель работы.
Исследование деформации и сопротивления разрушению тонкостенных оболочечных труб из модифицированных сплавов циркония в сравнении со сплавами штатных составов в различном структурном состоянии, определение характеристик сопротивления разрушению при различных условиях нагружения для уточнения химического состава и деформационно-термической обработки оболочечных труб.
Основные задачи:
1. Разработать методики и провести' испытания по оценке запаса пластичности и трещиностойкости тонкостенных оболочечных труб из циркониевых сплавов Э110 и Э635 различного химического состава, определить характеристики пластичности и трещиностойкости новых модификаций сплавов циркония в различных условиях нагружения.
2. Определить факторы, ограничивающие пластичность и трещиностойкость оболочечных труб из циркониевых сплавов Э110, Э635 и их модификаций в состоянии поставки, при КРН в среде метанол-йод, а также после высокотемпературного окисления в паре (испытания типа LOCA).
3. Изучить механизмы и кинетику КРН модифицированных сплавов циркония и определить влияние коррозионных повреждений на вязкость разрушения оболочечных труб.
Научная новизна работы:
1. Разработаны новые методики определения характеристик пластичности и трещиностойкости тонкостенных труб из циркониевых сплавов, что позволило выявить основные факторы, ограничивающие их пластичность и трещиностойкость, в том числе, после агрессивного воздействия коррозионной среды и высокотемпературного окисления.
2. Впервые при испытании образцов труб внутренним давлением с измерением акустической эмиссии от старта трещины определены характеристики вязкости разрушения тонкостенных труб из новых модификаций циркониевых сплавов в состоянии поставки, после КРН-испытаний и высокотемпературного окисления в паре.
3. Показано, трубы из сплава Э1 ЮМ в состоянии поставки при прочности в 1,3 раза выше, чем для труб-из сплава Э110, характеризуются^ сравнимой с ним деформационной способностью. При этом вязкость разрушения труб из сплава Э1 ЮМ в 3 раза ниже, чем для сплава Э110.
4. Показано, что при одинаковых условиях КРН-испытаний для труб из сплава Э110М время до начала разрушения в 2 раза меньше, а количество и площадь коррозионных дефектов в 1,5 раза больше, чем для сплава Э1Ю при одинаковом механизме разрушения. Образование и накопление коррозионных дефектов в образцах труб из сплавов Э1Ю и Э110М при КРН-испытаниях в течение 8 часов не повлияло на их трещиностойкость.
5. Впервые определены количественные характеристики структуры, изломов и трещиностойкости Кс образцов труб из модифицированных сплавов Э110М, Э635М и Э1ЮГ после высокотемпературного окисления в паре в сравнении со штатными составами сплавов.
6. Показано, что основными факторами, ограничивающими пластичность и трещиностойкость сплавов после высокотемпературного окисления являются: доля крупных участков обогащенной кислородом а^гфазы, доля структуры типа «корзиночное плетение» и содержание выделений водородосодержащей гидридной фазы в «ех-(3"-слое. Уменьшение суммарного содержания примесей в сплавах уменьшает степень охрупчивания труб.
Практическая ценность работы.
1. Разработанные методики испытаний на растяжение и статическую трещиностойкость с измерением АЭ использованы при исследовании механических свойств и разрушения циркониевых оболочечных труб для оптимизации их химического состава и микроструктуры, обеспечивающих необходимую технологическую пластичность и трещиностойкость при сохранении комплекса коррозионных и других механических свойств.
2. Результаты работы использованы для совершенствования режимов деформационно-термической обработки труб из новых модификаций циркониевых сплавов Э110 и Э635.
3. Результаты исследований будут использованы при разработке новых усовершенствованных модификаций циркониевых сплавов для элементов ТВС, что позволит обеспечить высокое сопротивление разрушению при их изготовлении и эксплуатации в реакторах нового поколения в условиях запланированных высоких нагрузок.
Выводы.
1. Разработаны и применены методики определения характеристик пластичности и трещиностойкости тонкостенных оболочечных труб из циркониевых сплавов при нагружении образцов внутренним давлением и регистрации старта трещины по измерениям акустической эмиссии. Определены значения вязкости разрушения Кс и Зс оболочечных труб из сплавов Э110 и Э635 и их модификаций* в состояниипоставки, после испытаний на КРН в йодсодержащей среде и после высокотемпературного окисления в паре.
2. Прямым сопоставлением значений истинной равномерной деформации и показателя степени деформационного упрочнения" при* растяжении^ образцов труб показано, что в состоянии поставки образцы труб из сплава Э110М при прочности в 1,4 раза выше, чем, для труб-из сплава Э110, характеризуются сравнимой с ним деформационной' способностью. При этом вязкость разрушения Кс труб из. сплава Э1 ЮМ в 1,5 раза ниже, чем для сплава Э110:
Образцы труб из сплавов Э635 и Э635М в состоянии поставки имеют близкие характеристики. пластичности и статической трещиностойкости.
3. Совместным анализом* АЭ1 и коррозионной повреждаемости определены различия^ в сопротивлении коррозионному разрушению под напряжением (КРН) в среде метанол-йод образцов труб из сплавов штатного и модифицированного составов. Показано, что при одинаковых условиях КРН-испытаний для труб из сплава Э110М время до начала разрушения в 2 раза меньше, а количество и площадь коррозионных дефектов (питтингов, трещин и зон ЗГР) в 1,5 раза больше, чем для сплава Э1Ю при одинаковом механизме разрушения.
Образование и накопление коррозионных дефектов в образцах труб из сплавов Э1Ю и Э110М при КРН-испытаниях в течение 8 ч не повлияло на значения вязкости разрушения Зс.
4. Определены количественные характеристики структуры, изломов и трещиностойкости Кс образцов труб из модифицированных сплавов Э110М,.
Э110Г и Э635М в сравнении со штатными составами сплавов после высокотемпературного окисления в паре при Т = 1100 °C и ЛГО = 18%. Показано, что основными структурными факторами, ограничивающими пластичность и трещиностойкость сплавов после высокотемпературного окисления, являются: доля крупных участков обогащенной кислородом а^г-фазы, доля структуры типа «корзиночное плетение» и содержание выделений водородосодержащей гидридной фазы в «ех-р"-слое. Уменьшение суммарного содержания примесей в сплаве Э110Г на основе губки уменьшает степень охрупчивания труб.
5. Установлено, что трещиностойкость Кс труб из сплава Э110М после высокотемпературного окисления в 1,5 раза ниже, а из сплава Э110Г в 1,6 раза выше по сравнению со сплавом Э110 штатного состава.
6. Показано, что изменение химического состава сплавов Э635М и содержания примесей в сплаве Э110Г по сравнению со сплавами штатного состава не повлияло на пластичность и трещиностойкость труб в состоянии поставки и после КРН-испытаний.
7. Установленные зависимости пластичности и статической трещиностойкости, структуры и изломов образцов труб из новых модификаций циркониевых сплавов использованы для совершенствования химического состава и технологии их деформационно-термической обработки при изготовлении тонкостенных труб.
Список литературы
- Займовский A.C., Никулина A.B., Решетников Н. Г. Циркониевые сплавы в ядерной энергетике.- М: Энергоатомиздат, 1994, с. 256.
- G.P. Sabol. ZIRLO-An Alloy Development Success. Journal of ASTM International, February 2005, Vol. 2, No.2, Paper ID JAI12942.
- H.K. Yueh, R.L. Kesterson, et. al. Improved ZIRLO Cladding Perfomance through Chemistry and Process Modifications. Journal of ASTM International, June 2005, Vol. 2, No.6, Paper ID JAI123441
- Бескоровайный H. M., Калин Б. А., Платонов П. А., Чернов И. И. Конструкционные материалы ядерных реакторов. — М.: Энергоатомиздат, 1995, с. 618.
- Никулина A.B. Циркониевые сплавы в атомной энергетике/ТМиТОМ № 11,2004, с. 8−12.
- С.А. Никулин*. Перспективные конструкционные сплавы для атомной энергетики. В книге «Новые материалы». Москва: МИСиС, 2002, с. 360−371
- Фазовые диаграммы двойных металлических систем. Москва, Машиностроение, 2000^ Том 3, книга 2, с. 356−358.
- Решетников Ф. Г., Бибилашвили Ю. К., Головнин И. С. и др. Разработка, производство и эксплуатация тепловыделяющих элементов энергетических реакторов.-М.: Энергоиздат, 1995, с. 95.
- Дуглас Д., Металловедение циркония. М.: Атомиздат, 1975, с. 411.
- A.B. Никулина, Н. Г. Решетников, П. В. Шебалдов и др. Технология изготовления канальных труб из сплава Zr-2,5%Nb, установленных в реакторах РБМК/ВАНТ, Сер. Материаловедение и новые материалы. 1990. Вып. 2(36), с. 46−54.
- А. В. Добромыслов, Н. И. Талуц. Структура циркония и его сплавов. -Екатеринбург: УрО РАН, 1997.
- М.И. Солонин, Ю. К. Бибилашвили, А. В. Никулина, В. А. Маркелов. Цирконий-ниобиевые сплавы для оболочек твэлов и. ТВС энергетических реакторов и установок типа ВВЭР и РБМК. Избранные труды ВНИИНМ, 2002, с. 65−71.
- Никулина А.В. Циркониевые сплавы для элементов активных зон реакторов с водой под давлением //МиТ (c)М, 2003, № 8, с. 7−13.
- W.W. Stephens. Extractive Metallurgy of Zirconioum 1945 to the Present //Zirconium in the Nuclear Industry: Sixth International Conference, ASTM STP 824, D.G. Franklin and R.B. Adams, Eds., American Society for Testing and Materials. 1984, p. 5−36.
- S. Doriot, D. Gilbon, et. al. Microstructural Stability of M5 alloy Irradiated up to High Neutron Fluences. Journal of ASTM International, July/August 2005, Vol. 2, No.7, Paper ID JAI12332.
- J.P. Mardon, D. Charquet, J.L. Aubin et al. Industrial Development and Irradiation Performance of M5™ Alloy. 13th International Symposium on Zirconium in the NuclearJndustry, June 10−14, 2001, Annecy, France. Program and Abstracts, p. 66−67.
- J.P. Mardon, A. Frichet, et. al. The M5 fuel rod cladding. International Top. Meeting TopFuel99, LWR Nuclear Fuel Highlights at the beginning of the third Millenium. 1999, Sept, p. 407−414'.
- G.L. Garner, J.P. Mardon. Performance of alloy M5 lead assemblies after 3 cycles in a high DyTV U.S. Reactor. Int: Symposium., Fontervraud 5, Sept. 2002.
- Y. Etoh, S. Shimada et. al. Development of new zirconium alloys for- aBWR. ASTM STP 1295,1996, p. 825−848.
- J.P. Mardon, G. Garnner, et. al. Update on the development on advanced zirconium alloys for PWR fuel rod cladding, Int. Top. Meeting on LWR Fuel Perfomance, Portland, 1997, p. 405−412.
- A.M. Garde, G.P. Smith, et.al. In-PWR irradiation performance of dilute Tin-Zirconium advance alloys, Int. Symposium of Zirconium in the Nuclear Industry. ASTM STP 1423,2001, p. 490−504.
- A.K. Шиков, А. Д. Никулин, В .А. Никулина и др. Современное состояние и перспективы развития производства циркония и его сплавов и изделий из них //Физика и химия обработки материалов. 2001, № 6, с. 5—14.
- A.V. Nikulina, V.A. Markelov, M: M.Peregudet.al.Zirconium Alloy E635 as a Material for Fuel’Rod Cladding and other components ofWER and RBMK Cores. «Zirconium in the nuclear industry"-11th International Symposium, STP 1295,1996, p. 785−804.
- Гончаров В. И. Влияние структуры на деформацию и сопротивление разрушению сплава Zr-l%Nb-l, 3%Sn-0−4%Fe применительно к изготовлению изделий активной зоны. атомных реакторов: Дисс. канд. техн. наук.-М., 1994. .
- J.R. Theaker, R. Chonbey, et. al. Fabrication of Zr-2,5Nb pressure tubes tothminimize the harmful effects of trace elements- 12 International Symposium on Zirconium in the Nuclear Industry, ASTM STP 1245,1994, p. 221−242.
- O.C. Иванов, A.C. Адамова,.E.M. Тарараева, И. А. Трегубов. Структура циркониевых сплавов. Москва, Наука, 1973.
- F. Cazarolli, H. Stehle, E.Steinberg. Behaviour and properties of Zircaloys in power reactors. A short review of pertinent aspects in SIEMENS LWR Fuel. 11th Symposium on Zirconium in the Nuclear Industry, STP 1295, 1995, p. 12−34.
- M. Limback, T. Andersson. A model for the analysis of the effect of finalLannealing on the in- and out-of-reactor creep behaviour of Zircaloy cladding. 11 International Symposium on Zirconium in the Nuclear Industry, ASTM STP 1295 (1995), p. 448−460.
- S.P. Pati, P. Jourdain, et. al. Performance of standard and advanced fuel rod cladding for high burn up applications in PWRs. International-Top. Meeting on LWR Fuel performance, (1994), p. 286−295.
- M.M. Peregud, A.V. Nikulinaet. al. E635 alloy cladding tube properties as dependent on its chemical» composition and structure. 12 International symposium on Zirconium In the Nuclear Industry, 1998.
- A.B. Никулина, B.H. Шишов, В. Ф. Коньков, A.E. Новоселов, В. К. Шамардин, Г. П. Кобылянский. Цирконий ниобиевые сплавы для" элементов активных зон реакторов с водой под давлением. ВАНТ, Сер.: Материаловедение и новые материалы, 2003, Вып. 1(61), с. 16−31.
- Б. Г. Парфенов, B.B. Герасимов, Г. И. Бенедиктова. Коррозия циркония и его сплавов. Атомиздат, 1967.
- Сох В., Wood J. С. Iodine induced cracking of zircaloy fuel cladding// Corrosion Problems in Energy Conversion and Generation. 1974, p. 275
- B. Cox. Pellet-Clad Interaction (PCI) Failures of Zirconium Alloy Fuel Cladding-A review. Journal of Nuclear materials 172, 1990, p. 249−292.
- Стеклов О. И. Стойкость материалов и конструкций к коррозии под напряжением. М.: Машиностроение, 1990, с. 263.
- Исаев Н.И. Теория коррозионных процессов.-М. Металлургия, 1997, с. 270.
- T.Kido, Y. Senda ae.al. Quantitative assessment of irradiation effect on creep and corrosion properties of Zr-base alloys. ASTM STP 1423,2002, pp. 780−794.
- G.P. Sabol et. al. In-reactor corrosion performance of ZIRLO and Zircaloy-4. 10- th International Symposium on Zirconium in the Nuclear Industry, 1994, ASTM STP 1245, p. 724−744.
- J. Bohmert, M. Dietrih, J. Linek. Comparative studies on high-temperature corrosion of ZrlNb and Zircaloy-4. Nuclear Engineering and Design 147 (1993), p. 53−62.
- B.B. Новиков. Механизм йодного растрескивания циркониевых оболочек. Атомная энергия, т. 71, вып. 1., июль 1991, с. 33−38.
- Iodine Induced Stress Corrosion Cracking of Zircaloy Fuel Cladding Materials. International Atomic Energy Agency. LAEA-TECDOC-1185, November 2000, p. 165.
- B.B. Новиков. Механизм йодного растрескивания циркониевых оболочек. Атомная энергия, т. 71, вып. 1., июль 1991, с. 33−38.
- В. Сох. Environmentally-Induced Cracking of Zirconium Alloys-A review. Journal of Nuclear materials 170, 1990, p. 1−23.
- В.В. Новиков. Оценка сопротивления разрушению при коррозии под напряжением материалов оболочек твэлов. //Заводская лаборатория. 1985. Т. 51. Вып. 3. с. 67−70.
- Yu. К. Bibilashvili, A.V. Medvedev, В. I. Nesterov, V.V. Novikov, V.N. Golovanov, S.G. Eremin, A. D: Yurtchenko. Influence of Irradiation on KjScc of Zr-l%Nb claddings. Journal of Nuclear Materials-280 (2000), p. 106−110.
- Yu.K. Bibilashvili, Yu.N. Dolgov, B.I. Nesterov, V.V. Novikov. Propagation of stress corrosion cracks in Zr-l%Nb claddings. Journal of Nuclear Materials 224 (1995), p. 307−310.
- Li Peizhi, Zhu Hongyao et al. Effect of Alloying Elements on the Corrosion Resistance of Zr-Nb System Alloys. «Zirconium in. the nuclear industry"-12th International Symposium- 2000, ASTM Abstracts, p. 103−104.
- C.A. Никулин, А. Б. Рожнов. Коррозионное растрескивание циркониевых оболочечных труб (обзор). I. Методы исследования и механизмы разрушения//МиТОМ, № 2,2005, с. 31- 39:
- G.A. Никулин, А. Б. Рожнов. Коррозионное растрескивание циркониевых оболочечных труб (обзор). II. Влияние внешних факторов воздействия, структуры и свойств сплавов. МиТОМ, № 9, 2005, с. 30−37
- Б.Г.Парфенов и Г. А. Некрасова. Поведение оболочек ТВЭЛов в условиях аварии с потерей теплоносителя: обзорная информация. Цирконий в атомной промышленности. Вып.9. АИНФ567.М.: ЦнииАтоминформ. — 1982, с. 52.
- М.И. Солонин, Ф. Г. Решетников, А. Г. Иолтуховский, А. В: Никулина. Новые конструкционные материалы активных зон ядерных энергетических установок //Физика и химия обработки материалов. 2001, № 4, с. 17−27.
- С.А.Никулин, В. Г. Ханжин, А. Б. Рожнов, В. А. Белов. Поведение циркониевых оболочечных труб твэлов атомных реакторов в экстремальных эксплуатационных условиях.// Металловедение и термическая обработка металлов № 5. 2009, с. 32−39.
- A.R. Massih, T. Andersson, P. Witt, M. Dahlback, M. Limback. Effect of quenching rate on the ?-to-a phase transformation: structure in zirconium alloy. Journal of Nuclear materials 322 (2003), p. 138−151.
- H-J. Sell, E. Ortlieba. Effects of Alpha-Beta Transformation* on high temperature (LOCA) Creep Behavior of Zr-Alloys. Zirconium in the Nuclear Industry: 13th Int. Symposium, ASTM STP 1423,2002, p. 658−672.
- L. Portier, Th. Bredel, et. al. Influence of Long Service Exposures on the Thermal-Mechanical Behavior of Zy-4 and M5 Alloys in LOCA Conditions. Journal of ASTM International, Febraury 2005, Vol., No.2, paper ID JAI124468.
- M. Ozava, Т. Takahashi, Т. Homma, К. Goto. Behavior of Irradiated Zircaloy-4 Fuel Cladding Under Simulated LOCA Conditions. Zirconium in the Nuclear Industry: 12 th Int. Symposium, ASTM STP 1354,2000, p. 279−299:
- Нее M. Chung. Fuel behavior under loss-of-coolant accident situations //Nuclear engineering and technology. 2005, v. 40, № 4, p. 327−362.
- L. Yegorova, K. Lioutov, N. Jouravkova, A. Konobeev, V. Smirnov, V. Chesanov, A. Goryachev. Experimental Study of Embrittlement of Zr-l%Nb WER Cladding under LOCA-Relevant Conditions. Washington- U.S. Nuclear Regulatory Commission- 2005, p. 274.
- C. Grandjean, G. Hache. A state of the art review of past programme devoted to fuel behavior under loss of coolant condition. Part 3. Cladding Oxidation Resistance-to Quench and Post-Quench Loads. 2008.
- ГОСТ 25.506−85 Расчеты- и испытания на- прочность. Методы механических испытаний. металлов. Определение характеристик трещиностойкости (вязкости разрушения) при статическом, нагружении. М. Издательство стандартов- 2005, с. 38.
- Begley JlA., Landes J.D. The J-integral as a fracture criterion. In: Fracture Toughness, Part II, ASTM STP 514,1972, p.1−20.
- Landes J.D., Begley J.A. The1 effect of specimen geometry on Jic.— In Fracture Toughness, Part II, ASTM STF514,1972, p. 24−39.'74'. Бекофен. В. А. Процессы деформации.-М.: Металлургия. 1977. с. 288.
- Ludvik P. Elements der Technologischen*Mechanik.-Berlin: Springer, 1909, s. 32.
- Hollomon J. H. Tensile defoimanion // Trans. AIME.-l945. v. 162. p. 268−290.
- Swift H. W. Description of stress-strain curves // J. Mech. Phys. Solids.-1952v. 1, № 1. p. 1−7.
- Грешников В.А., Дробот Ю. Б. Акустическая Эмиссия.-М.: Атомиздат, 1976, с. 287.
- Семашко Н.А., Шпорт В. И., Марьин Б. Н. и др. Акустическая эмиссия в экспериментальном материаловедении. М.: Машиностроение, 2002.
- В.Г. Ханжин, С. А. Никулин. Применение метода акустической эмиссии при испытаниях материалов для ядерной энергетики. Учеб. Пособие. — М.: МИСиС, 2007, с. 95.
- В. Lustman, F. Kerze. The Metallurgy of Zirconium. New-York-Toronto-London, 1955.
- Г. А. Некрасова, Б. Г. Парфенов, A.C. Пиляев, Г. П. Клыпина, И. Г. Шутько. Цирконий в атомной промышленности. Выпуск 10. Ползучесть и радиационный рост циркониевых сплавов при> облучении. Москва, ЦНИИатоминформ, 1982.
- Сох В. Reviews on coatings and corrosion // Ed: J. Yahalon. V. 1. № 4.-Freund.-Tel Aviv, 1975. p. 366.
- P. Jacques, F. Lefevbre, C. Lemaignan: Deformation-Corrosion Interaction for Zr Alloys during I-SCC Crack Initiations. Part I: Chemical Contributions. Journal of Nuclear materials 264 (1999), p. 239−248.
- V. Grigoriev, R. Jakobsson. Delayed Hydrogen Cracking and> J-integralth
- Measurements on Irradiated^ BWR Gladding- 14- International Symposium on Zirconium in the Nuclear Industry, Journal of ASTM International, p. 711−726, 2004.
- V. Grigoriev, B. Josefsson, B.Rosborg. Fracture toughness of zircaloy cladding tubes. 11th International Symposium on Zirconium in the Nuclear Industry, ASTM STP 1295,1996, p: 431−447.
- V. Grigoriev, K. Petterson and S.Andersson. Influence of Texture on the Fracture Toughness of Unirradiated Zircaloy Cladding. 12 International Symposium on Zirconium in the Nuclear Industry, ASTM STP '1354, 2000, p. 303−315.
- С.А. Никулин, В. Г Ханжин, А. Б. Рожнов, А. В. Бабукин, В. А. Белов. Методы анализа процессов деформации и разрушения тонкостенных изделий из сплавов с низкой прочностью. Металловедение и термическая обработка металлов, 2005, № 5, с. 43−50.
- Rice J.R. Fracture An Advanced Treatise (edited by H. Liebovits), Academic Press, New York, 191,1968.
- Хеллан К. Введение в механику разрушения. Пер. с англ. — М.: Мир, 1988- с. 364.
- FOGT Г1701−84 Металлы. Метод испытания на растяжение тонких листов и лент. М: Издательство стандартов. 1985. с. 16:
- Рожнов А.Б., Белов В. А., Никулин С. А., Ханжин В:Г. Коррозионное растрескивание под напряжением циркониевых оболочечных, труб. Часть I. Экспресс-метод локальных КРН испытаний. Деформация и разрушение материалов, № 6, Москва, 2009, с. 44−48.
- К. Takeda, Н. Anada. Mechanism of Corrosion Rate Degradation*Due to Tin. «Zirconium in the nuclear industry"-^111 International-Symposium, 2000- p. 592−608.
- ГОСТ 5639–82 Стали и. сплавы. Методы выявления и определения величины зерна. М. ИПК Издательство стандартов. 2003. с. 39.
- S.A. Nikulin, А.В. Rozhnov, V.A. Belov, N.V. Lyaschenko, A.V. Nikulina, A.V. Margin. Influence of Structure Changes in El 10 Alloy Claddings on Ductility Loss Under LOCA Conditions. Journal of ASTM International, Vol. 5, No. 8, 2008, p. 231−247.
- Masatoshi Kuroda, Shinsuke Yamanaka, Fumihisa Nagase, Hiroshi Uetsuka. Analysis of the fracture behavior of hydrided fuel cladding by fracture mechanics. Nuclear Engineering and Design 203 (2001) p. 185−194.