Проектирование цеха по производству пресс-порошка для покрытия плиток
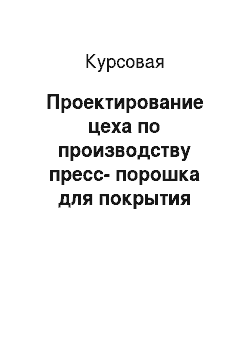
Также производится неколлекционная облицовочная плитка, глазурованная плитка для облицовки пола и различные виды керамического гранита — более 20 коллекций и видов. Предприятие производит санитарную керамику, стеновые строительные материалы (кирпич, камни). На сегодняшний день предприятие изготавливает 11 видов кирпича керамического, в том числе кирпич профильный и кирпич объёмного окрашивания… Читать ещё >
Проектирование цеха по производству пресс-порошка для покрытия плиток (реферат, курсовая, диплом, контрольная)
Введение
Открытое акционерное общество «Керамин» — крупнейшее в Европе предприятие по производству строительных материалов и санитарной керамики. Преемственность и верность традициям (историю предприятие ведёт с начала 20-го века), продуманная стратегия развития позволяют предприятию занимать лидирующие позиции на рынке.
Предприятие обеспечивает не только белорусский рынок — более 80 процентов производимой керамики напрямую поставляется во все регионы СНГ, государства Балтийского региона, Среднюю Азию и дальнее зарубежье.
Ассортимент выпускаемой продукции разнообразный. Это более 40 коллекций облицовочной плитки, которые состоят из светлой и тёмной плитки для стен; декоров и бордюров, включая объёмные декоративные элементы; напольной плитки. Коллекции выпускаются в различных цветовых вариантах.
Также производится неколлекционная облицовочная плитка, глазурованная плитка для облицовки пола и различные виды керамического гранита — более 20 коллекций и видов. Предприятие производит санитарную керамику, стеновые строительные материалы (кирпич, камни). На сегодняшний день предприятие изготавливает 11 видов кирпича керамического, в том числе кирпич профильный и кирпич объёмного окрашивания.
" Керамин" выпускает керамическую плитку следующих форматов:
— для облицовки стен:
10*10 см., 20*20 см., 20*30 см., 27,5*40 см., 30*60 см. — с декоративными элементами (декорами и бордюрами, включая объёмные фризы)
— для облицовки пола:
30*30 см., 40*40 см.;
— керамический гранит:
30*30 см., 40*40 см., 45*30 см., 45*9,8 см., 45*4,7 см., 30*15 см., 30*10см., 30*9,7 см., 15*15 см. — с декоративными вставками.
Они предназначены для покрытия полов внутри помещений жилых и общественных зданий, для покрытия полов в ванных, душевых, умывальных, туалетных комнатах и в бытовых помещениях промышленных зданий, а также для покрытия полов в лоджиях и на балконах (неглазурованные плитки).
В данной курсовой работе необходимо рассчитать:
1) Производственная программа;
2) Режим работы проектируемого цеха;
3) Инвестиции;
4) Численность и заработная плата;
5) Издержки;
6) Основные технико-экономические показатели.
1. Общая часть
1.1 Краткая характеристика выбранного способа производства Схема приготовления пресс-порошка для производства плиток для пола представлена на рисунке 1.
Рисунок 1 — Схема приготовления пресс-порошка для производства плиток для пола Плиточная масса готовится раздельным мокрым помолом непластичных и пластичных материалов. Практически доказано, что мокрый способ приготовления масс позволяет значительно улучшить качество плиток и механизировать сам процесс приготовления массы.
Непластичные материалы проходят стадию дробления, помол в шаровой мельницы с частью глинистых компонентов. Глинистые компоненты добавляют в количестве 5−10% при влажности 45−50% до остатка на сите № 0063 не более 1,5%. Соотношение материал: мелющие тела: вода — 1: 1,3: 1,8. В качестве мелющих тел применяются глиноземистые мелющие тела — цилиндры. Для компенсации износа мелющих тел производится их догрузка один раз в сутки 1,2% от первоначальной массы.
Загрузка шаровых мельниц отощающими материалами производится со специальной площадки через загрузочный люк после предварительного взвешивания на электровесовой тележке.
Ежесменно производится визуальный осмотр технического состояния шаровых мельниц (футеровка, количество и качество мелющих тел, наличие посторонних предметов).
Глинистая суспензия готовится отдельно. Грейферным краном глины подаются в приемные бункера и на глинорезку.
После глинорезки системой транспортеров глинистое сырье поступает на турбораспускатель, где происходит роспуск. После роспуска суспензия через вибросито поступает в расходный бассейн, а затем — в смесительный бассейн.
При подготовке глинистых компонентов вводятся электролиты (жидкое стекло). Они позволяют уменьшить количество воды, получить шликер с необходимой плотностью.
Готовый шликер из шаровых мельниц пневмокамерным насосом перекачивается в сливные бассейны с мешалками, пройдя предварительно магнитное и ситовое обогащение. Слив мельниц производится на несколько сит одновременно. Очистка магнитов производится каждый час в процессе слива мельницы.
Параметры шликера:
Продолжительность помола, ч | не менее 6 | |
Массовая доля влаги, % | не более 37 | |
Плотность, г/см3 | не менее 1,64 | |
Массовая доля остатка на сите с сеткой № 0064 или № 0063(10 000 ячеек/см2), % | не более 2,0 | |
Вязкость шликера, 0Е | 2,0 — 2,4 | |
Затем шликер при помощи мембранного насоса поступает в атомизатор для обезвоживания под давлением 2−2,5 МПа. Максимальная испарительная способность атомизатора АТМ — 140 — 14 м3/ч.
1.2 Определение показателей использования производственной мощности Производственная мощность цеха характеризуется максимально возможным выпуском продукции в натуральном выражении при полном использовании основных и всех резервов производства.
Производственная мощность цеха определяется мощностью основных производственных участков, важнейших групп оборудования по формуле 1:
Мц = П * Пч * Треж, т (1)
где П — количество единиц ведущего оборудования цеха (участка);
Пч — часовая производительность единицы оборудования;
Треж — режимный фонд времени работы оборудования (в часах);
Мц=1*24*8400=201 600, т Режимный фонд времени работы оборудования определяется по формуле 2:
Треж = К * Т * Д, ч (2)
где К — количество смен в сутки;
Т — количество часов в смену;
Д — количество рабочих дней в году;
Треж=3*8*(365−15)=8400, ч Уровень использования производственной мощности цеха характеризуется коэффициентом интенсивности загрузки (Ки), экстенсивной загрузки (Кэ) и интегральным коэффициентом использования производственной мощности (Кинт).
Коэффициент интенсивного использования производственной мощности определяется по формуле 3:
Ки = В / Мц (3)
где В — планируемый объем выпускаемой продукции на год в натуральных единицах измерения;
Ки=18 183,04/201 600=0,09
Коэффициент экстенсивного использования производственной мощности в данном случае может быть определен отношением режимного времени работы к календарному по формуле 4:
Кэ = Треж / Т (4)
Кэ=8400/8760=0,96
Календарный фонд времени определяется по формуле 5:
Тк = 24 * Дк, ч (5)
где Дк — число календарных дней в году;
Тк=24*365=8760, ч Интегральный коэффициент использования производственной мощности определяется произведением коэффициента интенсивной и экстенсивной загрузки производственной мощности по формуле 6:
Кинт = Ки * Кэ (6)
Кинт=0,09*0,96=0,09
Разность между намеченным к производству объемом выпускаемой продукции (В) и величиной производственной мощности цеха свидетельствует о резерве роста производства и определяется по формуле 7:
Р = В — Мц, т (7)
Р=18 183,04−201 600=-183 416,96, т
2. Расчетная часть В данном разделе производится расчет основных данных, характеризующих объем производства, состав работающих, использование инвестиций, а также определяются такие показатели, как производительность труда, себестоимость продукции, прибыль, рентабельность, срок возврата инвестиций.
Все эти и другие показатели собраны в единую таблицу, что позволяет с достаточной степенью точности определить качественный уровень данного проекта и сделать выводы об экономической целесообразности строительства цеха по разработанному проекту.
2.1 Производственная программа Выпуск и реализация продукции планируется в натуральном и стоимостном выражении. Производственная программа цеха по производству пресспорошка приведена в таблице 1.
Таблица 1- Производственная программа
Наименование продукции | Единица измерения | Отпускная цена за единицу, тыс. руб. | Объем производства | ||
в натуральном выражении | в стоимостном выражении | ||||
Пресс-порошок | т. | 1220,9512 | 18 183,04 | ||
2.2 Режим работы проектируемого цеха Режим работы предприятия принимается на основе норм технологического проектирования ОНТП — 07 — 05.
Номинальное количество рабочих суток в году — 261суток.
Расчетное количество рабочих суток в году для технологического оборудования при агрегатно-поточном способе составляет 350.
Годовой фонд работы технологического оборудования в часах:
— в три смены:
350*8*3=8400 часов.
2.3 Инвестиции (капитальные вложения) Капитальные вложения на строительство цеха складываются из затрат на:
— возведение зданий, передаточных устройств;
— приобретение и монтаж оборудования;
— прочие затраты (расходы на изыскательные, геологоразведочные и проектные работы, на содержание дирекции строящегося производства, затраты на привязку и др.)
Таблица 2- Расчет суммы амортизации
Наименование оборудования | Количество установленных единиц | Стоимость, тыс. руб. | Норма амортизации, % | Годовая сумма амортизации, тыс. руб. | ||
единицы | всего | |||||
Атомизатор | ||||||
Приемный бункер | 3,3 | |||||
Ленточный питатель с рыхлительными ножами | 5,1 | 428,4 | ||||
Глинорезка | ||||||
Ленточный конвейер | 5,2 | |||||
Турбораспускатель | ||||||
Шаровая мельница | ||||||
Вибросито | ||||||
Насос мембранный | 3,5 | 122,5 | ||||
Пропеллерная мешалка | ||||||
Электровесовая тележка | ||||||
Итого учтенное оборудование | ; | 227 186,9/1 491 100*100=15,24 | 227 186,9 | |||
Неучтенное оборудование (принимается 10% полной первоноч. стоимости учтенного оборудования) | ; | ; | 1 491 100*0,1=149 110 | 22 718,69/149 110*100=15,24 | 227 186,9*0,1=22 718,69 | |
ВСЕГО: | ; | ; | 249 905,59/1 640 210*100=15,24 | 249 905,59 | ||
Общая сумма инвестиций на организацию производства данного вида продукции составляет и рассчитывается по формуле 8:
Ио = Ц * К * U, тыс. руб. (8)
где Ц — расчетная цена;
К — коэффициент;
U — объем продукции.
Ио =1017,459*1,12*18 183,04=20 720 557,42, тыс. руб.
2.4 Численность и заработная плата Расчет численности и фонда заработной платы осуществляется отдельно по категориям работающих. Явочная численность рабочих определяется по агрегатам и рабочим местам исходя из норм и зон обслуживания.
Для определения списочной численности рабочих рассчитывается коэффициент перевода явочной в списочную, исходя из баланса времени 1 рабочего.
Примерный расчет баланса рабочего времени 1 списочного рабочего в год приведен в таблице 3.
Таблица 3- Баланс рабочего времени 1 списочного рабочего в год
Показатели | Количество дней в условиях | |
непрерывного производства | ||
Календарный фонд времени | ||
Выходные дни | ||
Праздничные дни | ||
Номинальный фонд времени | 365−104=261 | |
Невыходы на работу: | ||
— очередные и дополнительные отпуска; | ||
— болезни; | ||
— отпуска в связи с родами; | ; | |
— выполнение государственных обязанностей; | ||
— отпуска по учебе | ; | |
Эффективный фонд времени | 261−40=221 | |
Коэффициент перехода от явочного состава к списочному в условиях непрерывного производства определяется отношением календарного фонда времени к эффективному (полезному), а в условиях прерывного производства отношением номинального фонда времени к эффективному по формуле 9:
Кпер = Фк / Фэ (9)
где Фк — календарный фонд времени;
Фэ — эффективный фонд времени.
Кпер =365/221=1,65
Списочная численность рабочих определяется по формуле 10:
Чсп = Чя * Кпер, чел. (10)
где Чя — явочная численность.
Чсп.машин. =6*1,65=10, чел.
Чсп.дозир. =3*1,65=5, чел.
Чсп.опер. =3*1,65=5, чел.
Чсп.элект. =6*1,65=10, чел.
Чсп.налад. =3*1,65=5, чел.
Расчет прямой заработной платы рабочих-повременщиков осуществляется исходя из количества часов, которые необходимо отработать всеми рабочими в году и часовых тарифных ставок повременщиков.
Ниже приводится пример расчета заработной платы рабочих-повременщиков.
Расчет сводим в таблицу 4.
Таблица 4— Расчет прямой заработной платы рабочих-повременщиков
Разряд | Явочное число рабочих, человек | Списочное число рабочих, человек | Число часов, подлежащих отработке в году | Часовая тарифная ставка, тыс. руб. | Прямой фонд заработной платы, тыс. руб. | ||||
в смену | в сутки | всеми рабочими | одним рабочим | ||||||
Машинист грейферного крана | 5,2 | ||||||||
Дозировщик | 2,94 | 30 693,6 | |||||||
Оператор шаровой мельницы | 3,18 | 33 199,2 | |||||||
Электрик | |||||||||
Наладчик | 2,88 | 30 067,2 | |||||||
ИТОГО: | ; | ; | ; | ||||||
В качестве расчетных данных необходимо принять тарифные ставки для рабочих основных производственных цехов, действующих на базовом предприятии. Общий фонд заработной платы рабочих состоит из основной и дополнительной зарплаты.
Основную зарплату составляют:
прямой фонд зарплаты рабочих-сдельщиков и повременщиков (итог по таблице 4);
премии из фонда заработной платы (положение о премировании);
доплаты (за работу с вредными условиями труда, с тяжелыми условиями труда, за интенсивность труда, за ненормированный рабочий день, за выполнение обязанностей бригадира, за совмещение профессий, за работу в сверхурочное время, в ночное время и т. д.) и надбавки (за высокие квалификационные классы, за высокое профессиональное мастерство, за продолжительность непрерывной работы и т. д.)
Премия рассчитывается по формуле 11:
Премия = (ФЗПпр * 40%) / 100%, тыс. руб. (11)
Премия =(306 936*40)/100=122 774,4, тыс. руб.
Доплаты и надбавки рассчитываются по формуле 12:
Доплаты и надбавки = (ФЗПпр * 45%) / 100%, тыс. руб. (12)
Доплаты и надбавки =(306 936*45)/100=138 121,2, тыс. руб.
Основная зарплата рассчитывается по формуле 13:
ФЗосн = ФЗПпр + Премия + Доплаты и надбавки, тыс. руб. (13)
ФЗосн =306 936+122774,4+138 121,2=567 831,6, тыс. руб.
Дополнительная зарплата составляет 20% от основного фонда заработной платы и рассчитывается по формуле 14:
ФЗПдоп = ФЗПосн * 0,2, тыс. (14)
ФЗПдоп =567 831,6*0,2=113 566,32, тыс. руб.
Общий фонд заработной платы рабочих состоит из основной и дополнительной заработной платы и рассчитывается по формуле 15:
ФЗПобщ = ФЗПосн + ФЗПдоп, тыс. руб. (15)
ФЗПобщ =567 831,6+113 566,32=681 397,92, тыс. руб.
Затем определяется среднегодовая зарплата одного производственного рабочего путем деления общего фонда зарплаты на списочную численность рабочих по формуле 16:
ЗПср.г. 1-го раб = ФЗПобщ / Чсп, тыс. руб. (16)
ЗПср.г. 1-го раб =681 397,92/35=19 468,512, тыс. руб.
Среднемесячная заработная плата одного производственного рабочего определяется путем деления среднегодовой заработной платы на 12 по формуле 17:
ЗПср.м. 1-го раб = ЗПср.г. 1-го раб / 12, тыс.руб. (17)
ЗПср.м. 1-го раб =19 468,512/12=1622,376, тыс. руб.
С учетом выплат и премий сверх фонда оплаты труда среднемесячная зарплата одного рабочего умножается на 1,1 (принимается, что премии составляют 10%) и рассчитывается по формуле 18:
ЗП мин = ЗПср.м. * 1,1, тыс. руб. (18)
ЗП мин =1622,376*1,1=1784,6136, тыс. руб.
Из общего фонда заработной платы выплачиваются отчисления в размере 34% в фонд социальной защиты населения и рассчитываются по формуле 19:
Офсзн = ФЗПобщ * 0,34, тыс. руб. (19)
Офсзн =681 397,92*0,34=231 675,29, тыс. руб.
Фонд заработной платы ИТР, служащих и младшего обслуживающего персонала состоит из заработной платы, определенной должностными окладами.
Расчет сводим в таблицу 5.
Таблица 5-Численность и фонд зарплаты цехового персонала
Категории и должности работников | Количество штатных единиц | Месячный должностной оклад, тыс. руб. | Годовой фонд зарплаты, тыс. руб. | |
Сменный мастер | ||||
Начальник цеха | ||||
Инженер | ||||
Технолог | ||||
Уборщик | ||||
Лаборант | ||||
ИТОГО: | ; | |||
Тарифные ставки рабочих и должностные оклады ИТР, действующие на заводе, принимают за исходные.
Общий фонд заработной платы цехового персонала состоит из основной и дополнительной зарплаты.
Основную зарплату составляют:
прямой фонд зарплаты цехового персонала (итог по таблице 5);
премии из фонда заработной платы (положение о премировании);
доплаты (за работу с вредными условиями труда, с тяжелыми условиями труда, за интенсивность труда, за ненормированный рабочий день, за выполнение обязанностей бригадира, за совмещение профессий, за работу в сверхурочное время, в ночное время и т. д.) и надбавки (за высокие квалификационные классы, за высокое профессиональное мастерство, за продолжительность непрерывной работы и т. д.)
Премия рассчитывается по формуле 20:
Премия = (ФЗПпр * 40%) / 100%, тыс. руб. (20)
Премия =(217 680*40)/100=87 072, тыс. руб.
Доплаты и надбавки рассчитываются по формуле 21:
Доплаты и надбавки = (ФЗПпр*45%)/100%, тыс. руб. (21)
Доплаты и надбавки =(217 680*45)/100=97 956, тыс. руб.
Основная зарплата рассчитывается по формуле 22:
ФЗосн = ФЗПпр + Премия + Доплаты и надбавки, тыс. руб. (22)
ФЗосн =217 680+87072+97 956=402708, тыс. руб.
Дополнительная зарплата составляет 20% от основного фонда заработной платы и рассчитывается по формуле 23:
ФЗПдоп = ФЗПосн * 0,2, тыс. руб. (23)
ФЗПдоп =402 708*0,2=80 541,6, тыс. руб.
Общий фонд заработной платы цехового персонала состоит из основной и дополнительной заработной платы и рассчитывается по формуле 24:
ФЗПобщ = ФЗПосн + ФЗПдоп, тыс. руб. (24)
ФЗПобщ =402 708+80541,6=483 249,6, тыс. руб.
Отчисления фонда заработной платы ИТР составляют 34% в фонд социальной защиты населения и рассчитываются по формуле 25:
Офсзн итр = ФЗПитр * 0,34, тыс. руб. (25)
Офсзн итр =483 249,6*0,34=164 304,86, тыс. руб.
Среднегодовая зарплата на одного работающего рассчитывается по формуле 26:
ЗПср.г. 1-го раб = (ФЗПобщ + ФЗПитр) / (Чсп + ИТР), тыс. руб./чел. (26)
ЗПср.г. 1-го раб =(681 397,92+483 249,6)/(12+35)=24 779,73, тыс. руб.
Средняя минимальная заработная плата одного работающего рассчитывается по формуле 27:
ЗП мин 1-го раб = (ЗПср.г. 1-го раб / 12) * 1,1, тыс. руб./чел. (27)
ЗП мин 1-го раб =(24 779,73/12)*1,1=2271,475, тыс. руб.
Определяем производительность труда в натуральном и стоимостном выражении на одного рабочего и одного работающего и трудоемкость:
1) выработка одного рабочего в натуральном выражении рассчитывается по формуле 28:
Внатур. = V / Чсп, т/чел. (28)
Внатур. =18 183,04/35=519,5, т/чел.
V — выпуск продукции в натуральном выражении
2) выработка одного рабочего в стоимостном выражении рассчитывается по формуле 29:
Встоим. = (V * Ц) / Чсп, тыс. руб./чел. (29)
Встоим. =(18 183,04*1220,9512)/35=634 303, тыс. руб./чел.
Ц — отпускная цена единицы продукции
3) выработка одного работающего в натуральном выражении рассчитывается по формуле 30:
Внатур = V / (Чсп + ИТР), шт (кг, м.куб., м.кв. и т. п.) /чел. (30)
Внатур =18 183,04/(35+12)=386,87, т/чел.
4) выработка одного работающего в стоимостном выражении рассчитывается по формуле 31:
Встоим. = (V * Ц) / (Чсп + ИТР), тыс. руб./чел. (31)
Встоим. =(18 183,04*1220,9512)/(35+12)=472 353,3, тыс. руб./чел.
Определяем трудоемкость по формуле 32:
Тр. = число отработанных часов / годовая программа, час /т. (32)
Тр. =73 080/18183,04=4,019, чел./т.
2.5 Расчет издержек (себестоимости продукции)
Себестоимость рассчитывается по всем статьям калькуляции в расчете на весь выпуск и единицу продукции.
Расчет стоимости сырья и других исходных материалов, потребляемых в производстве данного вида продукции, производится исходя из потребного их количества на весь выпуск, удельных норм расхода сырья, материалов на единицу продукции, планово-заготовительных цен за единицу сырьевых компонентов.
Удельные нормы принимаются с учетом технологических потерь, рассчитанные в курсовом проекте по технологии, принятые по нормам проектирования или данным базового завода.
Потребное количество сырьевых материалов на весь выпуск определяется путем умножения удельной нормы расхода на годовой объем производства продукции.
Планово-заготовительные цены принимаются действующие на предприятии. Они складываются из прейскурантной цены и оплаты услуг автомобильного и железнодорожного транспорта (в техпромфинплане не каждого предприятия имеется таблица «Планово-заготовительные цены на сырье и материалы»).
Расчет стоимости сырья и материалов, потребляемых в производстве данного вида продукции, ведется в таблице 6.
Таблица 6-Расчет стоимости сырья и материалов
Наименование сырья и материалов | Единица измерения | Расход на весь выпуск | Цена за единицу, тыс. руб. | Сумма, тыс. руб. | |
Песок | м. куб. | 1493,03 | 201 559,05 | ||
Глина ДН-2 | м. куб. | 1010,43 | 147 522,78 | ||
Глина Техник-Веско | м. куб. | 4160,03 | 723 845,22 | ||
Каолин | м. куб. | 2516,83 | 4 756 808,7 | ||
Полевые шпаты | м. куб. | 3413,77 | 235 550,13 | ||
ИТОГО: | ; | 12 594,09 | ; | 6 065 285,88 | |
Расчет стоимости топлива Расчет стоимости топлива осуществляется исходя из удельных норм расхода на единицу продукции и стоимости 1 м³ газа, Гкал или Джоуль и т. п.
Удельную норму расхода можно принять по нормативам или отчетным данным завода (из расшифровки прямых статей калькуляции, здесь же указывается и цена приобретения).
Расчет топлива и энергии, потребляемых в производстве, ведется в таблице 7.
порошок плитка цех рентабельность Таблица 7- Расчет стоимости топлива и электроэнергии
Наименование | Единица измерения | Удельная норма расхода | Расход на весь выпуск | Цена за единицу, тыс. руб. | Сумма, тыс. руб. | |
Газ | м. куб. | 363 660,8 | 0,8 | 290 928,64 | ||
Электроэнергия | кВТ | 230,75 | 4 195 670,1 | 0,7 | 2 936 969,07 | |
ИТОГО: | ; | ; | ; | ; | 3 227 897,71 | |
Потребность в силовой энергии Рассчитывается исходя из установленной мощности электродвигателей (Муст), количества часов, которое будет отработано оборудованием в течение года (Фреж), коэффициента спроса (Кс) и коэффициента электроэнергии в сети (КПД).
Установленная мощность электродвигателей оборудования определяется в таблице 8.
Таблица 8-Установленная мощность электродвигателей оборудования
Наименование оборудования | Количество единиц | Установленная мощность электродвигателей, кВТ | ||
единицы | общая | |||
Атомизатор | ||||
Приемный бункер | ||||
Ленточный питатель с рыхлительными ножами | ||||
Глинорезка | ||||
Ленточный конвейер | ||||
Турбораспускатель | ||||
Шаровая мельница | ||||
Вибросито | ||||
Насос мембранный | ||||
Пропеллерная мешалка | ||||
Электровесовая тележка | ||||
ИТОГО: | ||||
Потребность в силовой энергии рассчитывается по формуле 33:
Wс.э. = (Муст * Фреж * Кс) / КПД, кВТ * ч (33)
Wс.э. =(969*8400*0,5)/0,97=4 195 670,1, кВТ * ч
где Муст — установленная мощность электродвигателей оборудования, кВТ (из таблицы 8);
Фреж — режимный фонд времени, в часах;
Кс — коэффициент спроса, характеризующий степень использования установленной мощности при максимальной нагрузке (при двухсменной работе равен 0,6, при трехсменной — 0,5);
КПД — коэффициент потерь электроэнергии в сети (0,97).
Удельная норма расхода электроэнергии в кВт * ч рассчитывается по формуле 34:
УНР = Wс.э. / ГП, кВт * ч (34)
УНР =4 195 670,1/18 183,04=230,75, кВт * ч где ГП — годовая программа в натуральном выражении Заработную плату основную и дополнительную производственных рабочих и отчисления принимаются рассчитанные в разделе ''Численность и фонд заработной платы работающих''.
Расчет цеховых расходов Цеховые расходы составляют 180% от основной заработной платы производственных рабочих и рассчитываются по формуле 35:
Рцех = ФЗПосн * 1,8, тыс. руб. (35)
Рцех =567 831,6*1,8=1 022 096,88, тыс. руб.
Расчет расходов на содержание и эксплуатацию оборудования (РСЭО) Расходы на содержание и эксплуатацию оборудования состоят из:
1. Затрат на содержание оборудования, транспортных средств и других рабочих мест — это стоимость смазочных и обтирочных материалов, зарплата основная и дополнительная, с отчислением на социальное страхование рабочих по обслуживанию оборудования, транспорта и других рабочих мест.
2. Амортизации оборудования и транспортных средств.
3. Текущего ремонта оборудования и транспортных средств.
4. Возмещения износа малоценных и быстроизнашивающихся предметов.
5. Прочих неучтенных расходов.
Расчет расходов на содержание и эксплуатацию оборудования производим по формуле 36:
РСЭО = А + Спервонач * 20% / 100 (36)
РСЭО =249 905,59+1 640 210*20/100=577 947,59, тыс. руб.
где, А — сумма амортизации всего за год из таблицы 2;
Спервонач — первоначальная стоимость оборудования и транспортных средств всего из таблицы 2.
Сумма цеховых расходов и РСЭО дают нам величину общепроизводственных расходов и рассчитывается по формуле 37:
Робщепр. = Рцех + РСЭО, тыс. руб. (37)
Робщепр. =1 022 096,88+577 947,59=1 600 044,47, тыс. руб.
Общехозяйственные расходы рассчитываются общей суммой без расшифровки и составляют 270% от основной заработной платы производственных рабочих и рассчитывается по формуле 38:
Робщехоз. = ФЗПосн * 2,7, тыс. руб. (38)
Робщехоз. =567 831,6*2,7=1 533 145,32, тыс. руб.
Прочие производственные расходы составляют 120% от основного фонда заработной платы производственных рабочих и рассчитывается по формуле 39:
Рпр. = ФЗПосн * 1,2, тыс. руб. (39)
Рпр. =567 831,6*1,2=681 397,92, тыс. руб.
Внепроизводственные расходы составляют 1,5% от производственной себестоимости.
Коммерческие расходы связаны со сбытом продукции. К ним относятся затраты на тару, упаковку, хранение, транспортировку продукции, расходы, связанные с исследованием рынка (маркетинговые операции), участие в торгах, на товарных биржах, расходы на рекламу и др.
Проектируемая калькуляция себестоимости продукции Все произведенные в разделе 2.5 расчеты служат основанием для составления калькуляции себестоимости продукции. Здесь указывается калькуляционная единица.
Таблица 9— Калькуляция себестоимости продукции и ценообразование
Статьи расходов | Сумма затрат по проекту, тыс. руб. | Структура себестоимости, % | ||
на выпуск | на единицу | |||
Сырье и материалы | 6 065 285,88 | 333,568 | 42,619 | |
Топливо на технологические цели | 290 928,64 | 2,044 | ||
Энергия на технологические цели | 2 936 969,07 | 161,52 | 20,637 | |
Заработная плата основная и дополнительная производственных рабочих | 681 397,92 | 37,47 | 4,7875 | |
Отчисления на зарплату (34%) | 231 675,29 | 12,7 | 1,62 267 | |
Общепроизводственные расходы | 1 600 044,47 | 87,997 | 11,24 | |
Прочие производственные расходы | 681 397,92 | 37,47 | 4,7875 | |
Общехозяйственные расходы | 1 533 145,32 | 84,317 | 10,77 | |
Производственная себестоимость | 14 020 844,51 | 771,09 | 98,5 | |
Внепроизводственные расходы (коммерческие расходы) | 210 312,67 | 11,566 | 1,5 | |
Полная себестоимость | 14 231 157,18 | 782,66 | ||
Прибыль | 4 269 347,15 | 234,789 | ||
Расчетная цена | 18 500 504,33 | 1017,459 | ||
НДС | 3 700 100,866 | 203,49 | ||
Отпускная цена | 22 200 605,2 | 1220,9512 | ||
2.6 Расчет основных технико-экономических показателей
1. Общая прибыль рассчитывается по формуле 40:
По = (Ц — С) * В, тыс. руб. (40)
где Ц — расчетная цена единицы продукции, тыс. руб.;
С — полная себестоимость единицы продукции, тыс. руб.;
В — годовой выпуск продукции в натуральном выражении.
По =(1017,459−782,66)*18 183,04=4 269 359,609, тыс. руб.
2. Срок окупаемости капитальных вложений определяется по формуле 41:
Т = И / П, лет (41)
где И — инвестиции (капитальные вложения КВ), тыс. руб.
П — прибыль, тыс. руб.
Т =20 720 557,42/4 269 359,604,85, лет
3. НДС определяется по формуле 42:
НДС = Ц * 0,2, тыс. руб. (42)
НДС =1017,459*0,2=203,49, тыс. руб.
4. Коэффициент эффективности определяется по формуле 43:
Ен = 1 / Т (43)
Ен =¼, 85=0,206
5. Расчет рентабельности производства производится по формуле 44:
Р = По / (Оф + ОС) * 100% (44)
где Р — показатель рентабельности;
Оф — стоимость основных фондов;
ОС — стоимость нормируемых оборотных средств;
Р =4 269 359,609/(18 234 090,53+2 486 466,89)*100=20,6%
Стоимость нормируемых оборотных средств определяется по формуле 45:
ОС = 0,12 * И, тыс. руб. (45)
ОС =0,12*20 720 557,42=2 486 466.89, тыс. руб.
Стоимость основных фондов определяется по формуле 46:
Оф = И — ОС, тыс. руб. (46)
Оф =20 720 557,42−2 486 466,89=18 234 090,53, тыс. руб.
6. Расчет рентабельности продукции определяется по формуле 47:
Р = (Ц — С) / С * 100% (47)
где Ц — расчетная цена единицы продукции, тыс. руб.;
С — полная себестоимость единицы продукции, тыс. руб.
Р =(1017,459−782,66)/782,66*100=30%
7. Расчет фондоотдачи производится по формуле 48:
ФО = ВП / Оф (48)
где ВП — выпуск продукции, тыс. руб.
ФО =22 200 605,2/18 234 090,53=1,2
8. Расчет фондоемкости производится по формуле 49:
Фёмк = 1 / ФО (49)
Фёмк =1/1,2=0,8
9. Расчет фондовооруженности труда производится по формуле 50:
Фв.т. = Оф / Чсп, тыс. руб./чел. (50)
где Чсп — списочная численность рабочих, чел.
Фв.т. =18 234 090,53/35=520 974,02, тыс. руб./чел.
10. Расчет удельных капитальных вложений производится по формуле 51:
Куд. = КВ / В, тыс. руб./н.е. (51)
где В — выпуск продукции в натуральном выражении.
Куд. =20 720 557,42/18 183,04=1139,55, тыс. руб./т
11. Расчет материалоемкости продкции производится по формуле 52:
Мёмк. = (Мз / С) * 100% (52)
где Мз — материальные затраты (стоимость сырья и материалов) на единицу продукции, тыс. руб.;
С — полная себестоимость единицы продукции, тыс. руб.
Мёмк. =(333,568/782,66)*100=42,6%
12. Расчет энергоёмкости производится по формуле 53:
Эёмк. = (Зт + Зэ) / С * 100% (53)
где Зт и Зэ — затраты на топливо и энергию на единицу продукции, тыс. руб.
Эёмк. =(16+161,52)/782,66*100=22,68%
13. Техническая вооруженность труда определяется по формуле 54:
Тв = Офа / Чсп, тыс. руб./чел. (54)
где Офа — активная часть основных фондов.
Тв =1 640 210/35=46 863,14 тыс. руб./чел.
Рассчитанные основные технико-экономические показатели сводим в таблицу 10.
Таблица 10- Основные технико-экономические показатели
Показатели | Единица измерения | Величина | |
Годовая программа | тыс. руб. | ||
Прибыль общая | тыс. руб. | 4 269 359,609 | |
Рентабельность продукции | % | ||
Рентабельность производства | % | 20,6 | |
Себестоимость единицы продукции | тыс. руб. | 782,66 | |
Срок возврата капитальных вложений | лет | 4,85 | |
Фондовооруженность труда | тыс. руб./чел. | 520 974,02 | |
Коэффициент эффективности | 0,206 | ||
Фондоотдача | 1,2 | ||
Фондоемкость | 0,8 | ||
Материалоемкость | % | 42,6 | |
Энергоемкость | % | 22,68 | |
Капитальные вложения | тыс. руб./т. | 1139,55 | |
НДС | тыс. руб. | 203,49 | |
Заключение
В результате произведенных расчетов технико-экономических показателей производства данного вида продукции можно сделать вывод, что производство этого вида строительного материала является целесообразным и эффективным, так как:
1) рентабельность производства составляет 20,6%;
2) рентабельность продукции составляет 30%;
3) срок окупаемости капитальных вложений составляет 4,85 лет;
4) прибыль составляет 4 269 359,609 тыс. руб.