Новые легированные кремнием износостойкие сплавы и технологии их нанесения
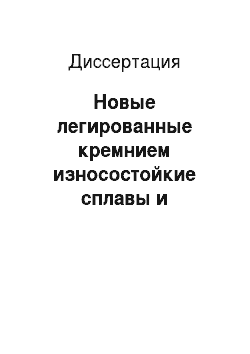
В современном машиностроении элементы пар трения изготавливают из износостойких сталей. Эта тенденция сохранится и в ближайшем будущем (несмотря на развитие высокоизносостойких композиционных материалов), так как они сочетают разнообразные (часто, почти исключающие друг друга) требования к условиям эксплуатации трущихся поверхностей. Как правило, целесообразно выполнить наиболее нагруженные… Читать ещё >
Содержание
- Страница
- 1. Аналитический обзор современных концепций разработки изностостойких сплавов на основе анализа механизмов изнашивания
- 1. 1. Трение металл по металлу при высоких температурах и удельных давлениях
- 1. 2. Изнашивание в газожидкостных абразивных потоках
- 1. 3. Абразивное изнашивание
- 1. 4. Изнашивание при резании металла
- 2. Методика исследования
- 2. 1. Трение металл по металлу при высоких температурах и удельных давлениях
- 2. 2. Обоснование комплекса металлофизических методов исследований изнашивания в газожидкостных абразивных потоках
- 2. 3. Абразивный износ
3 Дисперсионноупрочняемые сплавы 09Х32Н9МЗС2 (ОЗШ-6) и 09X32Н1ОМЗ С1ФЮ (ОЗШ-8) для изготовительной наплавки формообразующих деталей металлургического оборудования и тяжелонагруженной кузнечно-штамповой оснастки горячего деформирования.
4 Дисперсионноупрочняемый сплав 09Х30Н10С2М1 (ОЗН-8) для изготовительной наплавки уплотнительных поверхностей газопромысловой арматуры.
4.1 Влияние режима старения и дополнительного легирования на стойкость сплава 09Х32Н9МЗС2 (ОЗШ-6) при газоабразивном изнашивании.
4.2 Исследование возможности оптимизации свойств сплавов типа 09ХЭ2Н9МЗС2 для условий газоабразивного изнашивания.
4.3 Исследование механизма изнашивания дисперсионно-упрочняемых сплавов типа 09Х30Н10С2М
5 Гамма легированных кремнием износостойких сплавов для изготовительной наплавки рабочих органов горнодобывающих машин.
5.1 Электроды для наплавки металла средней твердости
НВ 250−400).
5.2 Экономнолегированные электроды ОЗН-6 (50С4Х4ГЗЮР) для условий абразивного изнашивания с интенсивными ударами (3−4 класс прочности грунтов).
5.3 Электроды ОЗН-7 (80Х6Г6СЗРАФ) для условий абразивного износа с интенсивными ударами (4−5 класс прочности грунтов), наплавка на сталь 110Г13Л.
5.4 Разработка технологии износостойкой наплавки шнеков центрифуг сточных вод (коррозионно-механическое изнашивание)
5.5 Разработка электродов ОЗН/ВСН-9 (140Х15НЗГЗС2РА) для условий интенсивного абразивного изнашивания (мерзлые грунты V категории прочности).
5.6 Разработка электродов ОЗН/ВСН-Ю (50Х8Н2С2Ф2) для износостойкой наплавки рабочих органов земснарядов (гидроабразивное изнашивание).
5.7 Разработка электродов ЗИО-11 (сталь 30ХН2МФА) для броневой защиты специальной техники.
5.8 Разработка технологии восстановления поршней судовых дизелей.
6 Износостойкая сталь ОЗИ-6 (110Х5М8В2С2Ю) для изготовительной наплавки многолезвийного металлорежущего инструмента.
7 Самофлюсующиеся Ре-Си-8ьВ и Ре-ЫьБьВ-сплавы для сварки ответственных конструкций из серого и высокопрочного чугуна.
7.1 Разработка самофлюсующихся Си-Ре-(81)-(В)-сплавов для холодной сварки чугуна.
7.2 Разработка экономнолегированных самофлюсующихся сплавов системы Ре-1чП-(81)-(В) для холодной сварки чугуна.
7.3 Разработка и апробация принципиально новой технологии сварки труб из ВЧТПГ.
8 Специальные стали: повышенной жаропрочности и жаростойкости для металлоформ и хладостойкая свариваемая для литых корпусов задвижек нефтепровода ВСТО.
8.1 Сталь 17Х2НМФЮ с повышенными эксплуатационными характеристиками для изготовления металлоформ литья труб изВЧШГ.
8.2 Хладостойкая свариваемая сталь 10ГНМЛ и технология сварки корпусов задвижек для нефтепровода «Восточная Сибирь
— Тихий Океан".
Новые легированные кремнием износостойкие сплавы и технологии их нанесения (реферат, курсовая, диплом, контрольная)
В современном машиностроении элементы пар трения изготавливают из износостойких сталей. Эта тенденция сохранится и в ближайшем будущем (несмотря на развитие высокоизносостойких композиционных материалов), так как они сочетают разнообразные (часто, почти исключающие друг друга) требования к условиям эксплуатации трущихся поверхностей. Как правило, целесообразно выполнить наиболее нагруженные элементы пар трения из низколегированной стали с изготовительной наплавкой износостойким сплавом: биметаллическая деталь лучше демпфирует напряжения, да и стоит меньше.
Анализ литературы и результатов предварительных экспериментов показал, что даже лучшие износостойкие сплавы для основных видов изнашивания имеют определенные недостатки, которые становятся лимитирующими по мере интенсификации технологических процессов и более рационального отношения к расходу дорогих и дефицитных элементов.
В этой связи, большой интерес представляют разработанные в ЦНИИТМАШ для условий трения металл по металлу дисперсионноупрочняе-мые хромоникелькремнистые сплавы, не содержащие дефицитных кобальтаи вольфрама. Широкое применение получили разработанные в НИИ-13 а-стареющие электроды УОНИ-13Н1/БК (09Х31Н8АМ2). Большой вклад в теорию и практику упрочняемых кремнием сплавов 08Х17Н8С6Г (ЦН-6) и 13X16Н8С5Г4МБ (ЦН-12), 15Х13Н9С5Ф2Г (ЦН-24) и 10Х28Н11С4АД (ЦН-25) внесли ученые ЦНИИТМАШ Яровинский Х. Л., Гельман A.C., Рунов А. Е., Старченко Е. Г., Степин B.C., Лобода A.C.
Опыт разработки [91] и успешной эксплуатации сплавов 15Х28Н10СЗГТ и 15Х28Н10СЗМ2ГТ (ЦН-19 и ЦН-20, ГОСТ 10 051–75), а также результаты предварительных экспериментов вселили в нас уверенность в том, что легирование кремнием может стать основой разработки сталей и сплавов для различных видов изнашивания в металлургии, машиностроении, энергетике, нефтяной, газовой и горнодобывающей промышленности.
А присущий высокохромистым сплавам эффект дисперсионного упрочнения и высокая теплостойкость кремнийсодержащей су-фазы [91] позволят максимально эффективно реализовать прогрессивный процесс изготовительной наплавки тяжелонагруженной кузнечно-штамповой оснастки и деталей газопромыслового оборудования.
Системное исследование влияния кремния на износостойкость при удар-ноабразивном и газоабразивном изнашивании было проведено также впервые. При разработке износостойких сплавов применили апробированную нами ранее двухэтапную схему исследования:
— изучение зависимостей «химический состав-структура-свойства»;
— оптимизация состава сплава на основе изучения механизма его изнашивания с привлечением результатов последних исследований в трибологии, считали, что, кроме очевидной практической ценности, применение разработанных нами принципов легирования кремнием поможет исследователю новых сплавов правильно выбрать пути поиска и сократит время разработки.
Актуальность проблемы подтверждается тремя тезисами:
— износостойкость тяжелонагруженных пар трения: уплотнительных поверхностей газопромысловой арматуры, кузнечно-штамповой оснастки горячего деформирования формообразующих деталей металлургического оборудования, рабочих органов горнодобывающей техники, — определяет эффективность технологических процессов и возможность их интенсификации;
— по результатам предварительных экспериментов, даже лучшие износостойкие сплавы имеют недостаточно высокие технико-экономические характеристики, которые становятся лимитирующими по мере освоения новых технологических процессов и более рационального отношения к расходу дорогих и дефицитных элементовкак правило, сплавы рассчитаны на однослойную плакировку (что существенно снижает ее технико-экономическую эффективность) и нетехнологичны при изготовительной наплавке;
— в этой связи, актуальна разработка теории и практики создания гаммы унифицированных экономнолегированных износостойких сталей и сплавов на основе твердорастворного и зернограничного упрочнений кремнием, оптимальность трибологических характеристик которых очевидна с позиций теории дислокаций, а экономическая эффективность безусловна. Повышение ресурса предопределяет также совершенствование изготовительной наплавки на основе разрабатываемых нами принципиально новых дисперсинноупрочняемых легированных кремнием сплавов, обеспечивающих высокую технологичность при наплавке, механической обработке и упрочнении.
Нам представляются важными и актуальными приведенные в диссертации примеры разработки легированных кремнием сплавов на основе изучения механизмов их изнашивания, позволившие эффективней использовать достижения трибологии в металловедении и построить новую концепцию создания износостойких сплавов.
Цель диссертационной работы:
— разработать и реализовать концепцию создания гаммы высокоизносостойких сталей и сплавов на основе твердорастворного упрочнения кремнием и в сочетании с сигма-фазой или карбидами, карбоборидами, карбонитридами;
— разработать экономнолегированные износостойкие стали и сплавы, обладающие комплексом свойств для изготовительной наплавки, и технологию их нанесения.
Для реализации поставленной цели изучена принципиальная возможность (а при положительных результатах исследования разработаны новые износостойкие сплавы) создания легированных кремнием сплавов для основных видов изнашивания в металлургии и машиностроении:
— трение металл по металлу при высоких температурах и удельных давлениях, характерное для условий эксплуатации тяжелонагруженной кузнечно-штамповой оснастки;
— газоабразивное изнашивание, применительно к уплотнительным поверхностям газопромысловой арматуры;
— абразивный износ с интенсивными ударами (строительнодорожная и горнодобывающая техника);
— износ при резании (многолезвийный металлорежущий инструмент).
Кроме того изучили влияние кремния и бора на самофлюсующие свойства железомедных и железоникелевых сплавов с целью повышения сварочно-технологических и служебных характеристик электродов для сварки ответственных конструкций из серого чугуна.
Оценили эффективность полученных знаний при разработке специальных сталей: стали с повышенной жаропрочностью и жаростойкостью для металло-форм и хладостойкой свариваемой стали для литых корпусов арматуры нефтепровода «Восточная Сибирь — Тихий океан» («ВСТО»).
Научная новизна результатов работы:
1 Разработана концепция создания экономнолегированных износостойких сплавов на основе твердорастворного упрочнения кремнием, показана эффективность его сочетания с о-фазой или карбидами, карбоборидами, карбонитридами. Экспериментально установлены концентрации кремния, обеспечивающие высокую износостойкость для основных видов изнашивания. Близкие значения «критического» содержания кремния для сплавов различных структурных классов и видов изнашивания указывают на универсальность свойств исследованных твердорастворного и зерно-граничного уплотнений и их ведущую роль в повышении износостойкости.
2 Предложена физическая модель изнашивания легированных кремнием сплавов при высокотемпературном трении металл по металлу, согласно которой износостойкость обеспечивает взаимодействие трех факторов: жаростойкой, с высокой регенерирующей способностью кремнийсодержащей пленки вторичных структур, жаропрочного подповерхностного слоя поверхности трения и его упрочнения диффундирующими атомами молибдена, для которых окислы кремния — барьер для диффузии.
Модель реализована при разработке стали 09Х32Н9МЭС2 для наплавки супертяжел онагруженной кузнечноштамповой оснастки.
3 На основе электроннои рентгенографических исследований предложена гипотеза механизма повышения кремнием износостойкости при газоабразивном изнашивании: диффузия кремния к поверхности раздела «металл-окисная пленка» упрочняет подповерхностный слой поверхности трения и замедляет образование и слияние микропустоткремний также уменьшает количество мартенсита деформации и тем самым увеличивает релаксацию напряжений трения.
Плотность дислокаций растет до см" 2, а исчерпание возможностей их скольжения, из-за высокой дисперсности а-фазы приводит к фрагментации тонкой структуры и двойникованию, это снижает энергию внутреннего трения и повышает износостойкость разработанной стали 09Х30Н10С2М1.
ОБЩИЕ ВЫВОДЫ И РЕЗУЛЬТАТЫ РАБОТЫ.
1 На основе изучения влияния кремния на механизм упрочнения и изнашивания, созданы методика разработки и гамма унифицированных легированных кремнием сталей и сплавов для изготовительной наплавки тяжелонагру-женных элементов пар трения в металлургии, машиностроении, энергетике, нефтяной, газовой и горнодобывающей промышленности.
На основе изучения структурных и фазовых превращений в наплавленном соединении, разработана технология изготовительной наплавки новых сталей и сплавов, обеспечивающая высокую эксплуатационную надежность биметаллических деталей и узлов.
2 Предложена физическая модель изнашивания легированных кремнием сталей при высокотемпературном трении металл по металлу, согласно которой износостойкость обеспечивает взаимодействие трех факторов: жаростойкой, с высокой регенерирующей способностью, кремнийсодержащей пленки вторичных структур, жаропрочного подповерхностного слоя поверхности трения и механизма его упрочнения диффундирующими атомами молибдена, для которых 8Юг — барьер для диффузии.
Эта модель легла в основу разработки дисперсионноупрочняемой стали 09Х32Н9МЭС2 (ОЗШ-6), теплостойкость. (1080°С), жаропрочность «0°» = 190 МПа) и износостойкость которой при наплавке супертяжелонагруженной куз-нечно-штамповой оснастки горячего деформирования (бойки РКМ, ножи и раскатные валки МГР) в 1,5−2,0 раза выше лучших функциональных аналогов: сталей 4Х5МФС и ЗХ2В8 и износостойких сплавов 90Х4М4ВФ и 10К18В11М10X3 СФ.
Характерная особенность изнашивания стали ОЗШ-6 — отсутствие микросхватывания поверхностей трения, подтверждающая влияние кремния на обе его составляющие: молекулярную и механическую.
3 На основе изучения влияния уровня легирования Бе-О-М-БьМо-сталей на кинетику а-упрочнения, разработан способ повышения сопротивляемости образованию трещин при многослойной наплавке сплава ОЗШ-6 путем уменьшения температурно-временного интервала дисперсионного упрочнения и изменения морфологии а-фазы высокотемпературными карбидами ванадияи, наряду с легированием ОД-0,3% алюминия, измельчающим структуру стали, реализован при создании стали 09Х32Н10МЗС1ФЮ (ОЗШ-8).
Экспериментально установлена возможность упрочнения наплавленной оснастки автоматических ковочных комплексов непосредственно в контакте с первыми штампуемыми деталями, что впервые в мировой практике сокращает технологию с семи до двух операций: наплавка (без подогрева и отпуска) и механическая обработка (без отжига).
4 На основе исследования фрактограмм поверхности трения: микротрещины и наплывы, свидетельствующие о многократном передеформировании, -определили усталостный характер изнашивания в газоабразивном потоке сталей типа 09Х30Н10С2М1. С учетом этого, экспериментально установили содержание кремния (—1,7% при резком скачке износостойкости) и режим старения (580°С, 4ч), фиксирующие процесс ст-старения на стадии предвыделения, когда параметры решетки второй фазы и аустенита когерентны и релаксационная способность сплава еще велика.
Для стали 09Х30НЮС2М1 характерно редкое качество — высокая износостойкость как при, а = 15, так и 90°, что можно объяснить двумя факторами: упрочнением поверхностного слоя диффундирующими к поверхности раздела «металл-окисная пленка» атомами кремния и, как следствие, замедлению образования и слияния микропустот, и уменьшением кремнием количества мартенсита деформации (при, а = 90° увеличение кремния от 0,20 до 3,79%) уменьшает количество мартенсита от 32 до 14%) и, как результат, повышением релаксационной способности при изнашивании.
Плотность дислокаций, за счет интенсификации сигмаи мартенситного упрочнении, растет до 1010−10п см" *". Исчерпание возможностей скольжения дислокаций из-за высокой дисперсности су-фазы приводит к фрагментации тонкой структуры и двойникованию, эти процессы релаксируют напряжения трения и повышают износостойкость сплава.
5 Установлено, что при содержании 81 ~ 1,1% в сталях типа 15ГЗС1 и 17Г4С2 мартенситное упрочнение переходит в твердорастворное и зерногра-ничное. Это позволило решить научно-техническую задачу обеспечения стабильности свойств наплавленного металла электродов. средней твердости (250−400НВ): разработанные электроды ОЗН-ЗООМ и ОЗН-400М отличает повышенная стабильность служебных характеристик наплавленного металла, практически не зависящая от погонной энергии наплавки и скорости охлаждения детали.
Зависимость «кремний-размер блоковмикродеформации» носит бимодальный характер: наименьшие блоки и микродеформации кристаллической решетки при 81 = 0,94 и 3,84%, — что хорошо коррелирует с повышением износостойкости в этих точках и подтверждает принятую концепцию усталостного характера изнашивания и переход к прогнозируемому твердорастворному упрочнению.
6 На примере стали 80Х6Г6СЗРАФ (ОЗН-7) показана эффективность комплексного упрочнения кремнием (твердорастворного) и карбидного. Изучено влияние структурного и фазового состава на механизмы упрочнения и изнашивания легированных кремнием сталей. Аустенитная структура стабильна.
5 2 при изнашивании (вплоть до энергии удара 2,5×10 Дж/м), напряжения решетки минимальны (Емакс = 0,01−0,03×10″), а их рост в процессе изнашивания (до.
0,63×10 2) релаксирует часть энергии трения и, как результат, 2-х кратное повышение износостойкости, по сравнению со сталью 110Г13Л.
При метастабильности аустенита, у—>а — превращение активно уже при небольшой энергии удара, сталь 80Х6Г6Р1АФ исчерпывает запас внутренней энергии и истирается.
Эти результаты коррелируют с характером зависимости «кремний-размер блоков-величина микродеформаций-износостойкость» для Ре-С-Мп-81-сплавов типа 15ГЗС1 и 17Г4С2 и подтверждают общность процессов твердорастворного и зернограничного упрочнений кремнием для сплавов разного структурного и фазового состава.
7 Решена научно-техническая задача повышения жаростойкости, красностойкости и износостойкости при резании металла низколегированных вольфрамом молибденванадиевых сталей до уровня стали Р18. Этот эффект наиболее ярко выражен при ~ 1,1% кремния и объясняется термической стабильностью твердорастворного упрочнения и высокой активностью ионов кремния в формировании жаростойкой окисной пленки при отжиге и резании. На основе стали 110Х5М8Ф2В2С2Ю (ОЗИ-6) разработана технология изготовительной наплавки многолезвийного инструмента автоматических линий, ресурс которого в 1,4−2,5 раза превышает сталь Р18.
8 Установлено, что легирование кремнием (0,5−0,8%) и бором (0.2−0,5%) уменьшает протяженность зоны отбела при сварке разработанными железомед-ными (ОЗЧ-6) и железоникелевыми электродами (ОЗЧ-7) за счет достижения самофлюсующих свойств сплавов.
Более того, достигнутое свойство самофлюсования позволяет существенно уменьшить содержание никеля от 50−55% (принятый уровень) до 31−32% без снижения уровня служебных характеристик сварного соединения, что наряду с разработанной технологией легирования никелем через шлам, существенно повышает технико-экономические показатели разработанных электродов ОЗЧ-7.
9 На основе принципиально новых конструкции соединения (раструбно-конусного) труб, технологии монтажа и сварочной проволоки впервые в мировой практике разработана и аттестована технология сварки электродами теплотрасс из труб ВЧШГ. Элементы технологии защищены тремя патентами, а теплотрассы проложены в С.-Петербурге, Липецке, Коломне, Ростове и успешно эксплуатируются в течение 5−7 лет.
10 Опыт изучения зависимостей «химический состав-структура-свойства» применили при разработке специальных сталей:
— впервые разработаны сталь (17ХН2МФЮ) и технология производства (на ОАО «ВТЗ» и «ЧТПЗ») трубных заготовок металлоформ для центробежного литья труб из ВЧШГ, повышающие ресурс кокилей до 2,5-крат, по сравнению с обычно применяемыми в мировой практике коваными заготовками из стали 20ХМ;
— по заданию ОАО «Транснефть» для проекта «нефтепровод Восточная Сибирь — Тихий океан» разработаны хладостойкая повышенной прочности свариваемая сталь для литых корпусов задвижек DN150−1200 мм, PN 8,0- 12,5 МПа, отвечающая требованиям «API Standard 600», технология автоматической приварки днищ и катушек. Высокие значения прочностных свойств и свариваемости достигли, в основном, существенным измельчением зерна, по сравнению со сталью 20ГМЛ, что отвечает современным тенденциям в разработке конструкционных сталей.
11 Экспериментально установлены концентрации кремния, обеспечивающие высокую износостойкость сталей и сплавов для основных видов изнашивания. Близкие значения «критического» содержания кремния для сплавов различных структурных классов и видов изнашивания указывают на универсальность свойств исследованных твердорастворного и зернограничного упрочнений и их ведущую роль в обеспечении износостойкости.
Научную и практическую значимость разработанных в диссертационной работе износостойких сплавов и системы их унификации подтверждают 30-летний опыт серийного изготовления (ведущими электродными заводами) и применения в различных отраслях техники семнадцати созданных сплавов (электродов) для изготовительной наплавки тяжелонагруженных пар трения основных видов изнашивания: трение металл по металлу при высоких температурах и удельных давлениях, абразивный и газоабразивный износ различной интенсивности, коррозионно-механический износ, импульсно-ударное нагру-жение.
Разработанная технология изготовительной наплавки новых сплавов обеспечивает высокую эксплуатационную надежность биметаллических деталей и узлов. Апробирована технология нанесения новых сплавов методами пайки, индукционной наплавки и прокатки.
27 6.
Список литературы
- А., Плескач В. М. Установка для испытания на износ в струе свободного абразива: Заводская лаборатория, 1969, № 10, с. 1256−1257.
- Абрамян A.A. Исследование влияния некоторых факторов на коррозию стального газопромыслового оборудования под воздействием СОг: Дисс. канд. техн. наук —М., 1972
- Адугина H.A. Влияние твердости нержавеющих сталей и сплавов на их коррозионно-эрозионную стойкость в сернокислых средах: Химическое и нефтяное машиностроение, 1974, № 9, с. 21−22.
- Анастасиади Г. П., Сильников М. В. Работоспособность броневых материалов: Астерион, СПб, 2004.
- Андреев А.К. Пути повышения ресурса литых сталей в условиях низких температур автореферат канд.техн.наук, С.-Петербург, 2010.
- Багнюк Л.Н. Разработка способов повышения качества стали на основе изучения механизма образования, морфологии и расположения сульфидных включений: Автореферат дисс. на соик. уч. степ. канд. техн. наук, Днепропетровск, 1988.
- Баранов М.А., Дубов Е. А. Микроискажения кристаллических решеток неупорядоченных у-фазных твердых растворов на основе системы Fe-Cr-Ni-Ti-W-A1: Труды АГТУ, 2009.
- Бельченко Г. И., Губенко С. И. Неметаллические включения и качество стали: Техшка, Киев, 1980.
- Блесков И.Д. Электронная структура и параметры основного состояния жаропрочных сплавов Физика твердого тела, 2010, т. 52, вып. 9, с. 16 811 688.
- Богачев И.Н. Металлография чугуна: Машгиз, М., 1952, 366 с.
- Бокштейн С.З. Диффузия и структура металлов: Металлургия, М., 1973,205 с.
- Бокштейн С.З. Диффузия в металлах с ОЦК решеткой: Металлургия, М., 1969,412 с.
- Боуден Ф.П., Тейбор Д. Трение и смазка твердых тел: Н., Машиностроение, 1982, 254 с.
- Браун М.П. Микролегирование стали: Наукова думка, 1982.
- Брыков H.H. Оценка износостойкости сталей при абразивном изнашивании: Трение и износ, 1988, т. 9, № 2, с. 317−321.
- Бунин К.П. Основы металлографии чугуна: Металлургия, 1969, 414 с.
- Бунин К.П. О механизме влияния кремния на графитизацию железных сплавов: РАН СССР, Физическая химия, 1954, т. XCV, 1, с.97−99.
- Буров C.B. Роль стабильности структуры поверхностных слоев в обеспечении износостойкости металлических материалов: Автореферат дисс. на со-иск. уч. степ. канд. техн. наук, Новосибирск, 2007.
- Ван Флек. Теоретическое и прикладное материаловедение: Атомиздат, М., 1975, 199 с.
- Виноградов В.Н., Сорокин Г. М., Албагачиев А. Ю. Изнашивание при ударе: Машиностроение, М., 1982, 192 с.
- Виноградов В.Н. и др. Методика расчета газоабразивного износа: Трение и износ, 1982, т. 3, № 2, с. 197−203.
- Виноградов В.Н., Червяков И. Б. Китаев В.Д. Влияние коррозионно-активной среды на параметры контактного взаимодействия твердой сферической частицы с поверхностью стали: Трение и износ, т. 7, № 6, 1986, с. 11 021 106.
- Винокур Б.В. и др. Взаимосвязь механических свойств и износостойкости марганцовистых сталей: Трение и износ, т. 9, № 1, 1988, с. 73−82.
- Герцрикен С.Д. и Дехтяр И .Я. Диффузия в металлах и сплавах в твердой фазе: ГИФМЛ, М., 1960, 562 с.
- Герцрикен С.Д. и др. Физические основы прочности и пластичности металлов: Металлургиздат, М. 1963, 322 с.
- Герасимова Л.П., Ежов A.A., Маресев М. И. Изломы конструкционных сталей. Справочник: Металлургия, М. 1987, 271 с.
- Горпенюк H.A. и др. Электроды КПИ-РИ-1 для наплавки режущего инструмента: Сварочное производство, 1976, 11.
- Гольдштейн М.И., Фарбер В. М. Дисперсионное упрочнение стали: Металлургия, М., 1979.
- Горский В.В. и др. Поверхностные слои трения и износостойкость легированной ванадием стали 130X15: Трение и износ, 1981, т. 2, № 2, с. 277−282.
- Гребнев Л. В. Пенкин Н.С. О зависимости газоабразивного изнашивания стали от угла атаки, коэффициента трения и формы твердых частиц: Трение и износ, 1987, т. 8, № 4, с. 713−719.
- Григорович В.К. Электронное строение и термодинамика сплавов железа: Наука, М., 1970, 275 с.
- Григорович В.К. Жаропрочность и диаграммы состояния: Металлургия, М. 1969.
- Грецкий Ю.Я. (ред.). Металлография сварных соединений чугуна: Наукова думка, Киев, 1987, 189 с. Грецкий Ю. Я., Метлицкий В. А. Сварка чугунных деталей в ремонтом производстве: Знание, Киев, 1985, 16 с.
- Гриник Э.У. и др. Оценка вязкости разрушения корпусных материалов реактора ВВЭР-1000: Институт ядерных исследований HAH Украины, Киев.
- Гринберг H.A. Износостойкость и сопротивление ударным нагрузкам наплавочных материалов при разработке различных грунтов: Сварочное производство, 1961, № 11, с. 7−9.
- Гринберг H.A. Применение в северных условиях износостойких наплавок для упрочнения деталей машин: ЦНТИ ВНИИСТ, М., 1974, 57 с.
- Гринберг H.A., Драгилев Б. Л., Лужанский И. Б. Наплавочный материал для упрочнения высокомарганцовистой стали 110Г13Л В сб. Наплавка износостойких и жаростойких сталей и сплавов: ИЭС им. Е. О. Патона. Киев, 1985, с. 35−39.
- Гринберг H.A., Куркумели Э. Г., Лужанский И. Б. Износостойкость различных наплавочных сплавов, эксплуатируемых в условиях абразивного изнашивания в воде: Сварочное производство, 1987.
- Геллер Ю.А. Современные инструментальные стали для режущих инструментов и их термическая обработка: Машиностроение, М., 1972.
- Гуляев А.П. Низколегированные вольфрамом и молибденом быстрорежущие стали: ГНТИ, М-Л, 1941.
- Гутерман В.М., Тененбаум М. М. Влияние микроструктуры на износостойкость углеродных сталей при абразивном изнашивании: МИТОМ, 1956, 11, с. 97−104.
- Геллер Ю.А. Инструментальные стали: Металлургия, М., 1975.
- Данькин A.A., Федосеев В. Ф. О температурном поле в зоне контакта при газоабразивном изнашивании материалов: Трение и износ, 1984, т. 5, № 3, с. 556−561.
- Джербетян А.К. Повышение износостойкости дисперсионнотвердею-щего сплава для наплавки уплотнительных поверхностей запорной арматуры: Дисс. канд. техн. наук, М., 1988.
- Драгилев Б. Л" Гринберг H.A., Лужанский И. Б., Куркумели Э. Г. И Волкова Т. Н. Наплавочный сплав для упрочнения деталей из стали 110Г13Л и механизм его изнашивания: Сварочное производство, 1988, № 11.
- Драгилев Б.Л. Повышение срока службы деталей машин из высокомарганцовистых сталей разработанными наплавочными и сварочными материалами: Дисс. канд. техн. наук, М., 1986.
- Еремин Н.И., Лебедянская П. И. Исследования фазовых превращений магнитным микроструктурным методом — В кн.: Физико-химические исследования аустенитных сплавов: М., 1957. С. 75−86.
- Елагина О.Ю., Коновалов A.B., Зинченко К. А. Исследование влияния тепловых процессов на взаимодействие абразивной частицы с поверхностью металла при трении: Трение и смазка в машинах и механизмах. 2007, № 9, с. 36.
- Елизаветин М.А. Повышение надежности машин: М., Машиностроение, 1973, 430 с.
- Ершов Н.В. и др. Искажения кристаллической решетки вокруг примесных атомов в сплавах a-FeixSix Физика твердого тела, 2007, том 49, вып. 1.
- Зайцев А.К. Методика лабораторного испытания материалов на износ (методы и машины) — В сб.: Трение и износ в машинах, М., Изд-во АН СССР, 1939, № 1, с. 310−327.
- Заморуев Г. М. Структурные изменения поверхностных слоев стальных тел при изнашивании — В сб.: Повышение износостойкости и срока службы машин. М., Машгиз, 1953, с. 5−21.
- Келли А. и Гровс Г. Кристаллография и дефекты в кристаллах: М., Мир, 1974, 485 с.
- Коновалов A.B. Моделирование и анализ силовых процессов на поверхностях трения оборудования нефтегазовой отрасли, работающего в условиях скольжения по закрепленному абразиву: Технология нефти и газа, 2005, № 2, с. 62−68.
- Коттрелл А.Х. Строение металлов и сплавов: М., Металлургиздат, 1961.
- Криштал М.А. Внутренне трение и структура металлов: М., Металлургия. 1972.
- Клейс И.Р., Ууэмыйс Х. Х. Износостойкость элементов измельчителей ударного действия: М., Машиностроение, 1986, 157 с.
- Кривцов A.M. Деформирование и разрушение твердых тел с микроструктурой: М., Физматлит, 2007. 304 с.
- Келли, Никлсон Р. Дисперсионное твердение: М., Металлургия, 1966.
- Каталог металлопродукции ОАО «Северсталь», 2006.
- Кан Р. (ред). Физическое металловедение: М., Мир. 1967, 1295 с.
- Корниенко JI.A. и др. Механизм твердорастворного упрочнения и разрушения на пределе текучести при легировании железа кремнием: ФММ, 1975, т. 39, вып. 1, с.189−195.
- Кофстад П. Высокотемпературное окисление металлов: М., Мир, 1959.
- Кубашевский О., Гопкинс В. Окисление металлов и сплавов: М., Металлургия, 1965.
- Кащеев В.И. Абразивное разрушение твердых тел: М., Наука, 248 с.
- Каковкин О.С. Исследование износостойкости сплавов и разработка наплавочных материалов для упрочнения черпаков драг: Автореферат на соиск. уч. степ. канд. техн. наук, М., 1975.
- Крагельский И.В. Об усталостной природе износа твердых тел — В кн. Вопросы механической усталости: М., Машиностроение, 1966, с. 128−132.
- Куркумели Э.Г., Гринберг H.A., Лившиц Л. С. Влияние бора на свойства износостойких хромистых и хромоникелевых наплавок: МИТОМ, 1974, № 5, с. 60−62.
- Карасюк Е.А. и др. О соотношении коррозионного и эрозионного факторов в кавитационном разрушении материалов: Физико-химическая механика материалов, 1976, т 12, № 5, с. 87−91.
- Крамер, Денц. Экспериментальное определение средних характеристик газового потока с твердыми частицами: Теоретические основы инженерных расчетов, 1972, № 2. Т. 94, с. 254−262.
- Лившиц Л.С., Гринберг H.A., Куркумели Э. Г. Основы легирования наплавленного металла: М. Машиностроение, 1969, 188 с.
- Лившиц Л.С., Платова С. Н., Соколова Т. Н. Поведение сталей с нестабильным аустенитом в условиях газоабразивного изнашивания: Изв. ВУЗов, сер. Нефть и газ. 1980. № 4, с. 80−84.
- Левченков В.И. Состояние и перспективы развития сварки чугуна: Сварочное производство. № 2, 1988.
- Любарский И.Н., Палатник Л. С. Металлофизика трения: М., Металлургия, 1976, 176 с.
- Лужанский И.Б. Исследование и разработка технологии автоматической плазменной наплавки с токоведущей проволочной присадкой уплотнительных поверхностей энергетической арматуры: труды ЦНИИТМАШ, 1974, 120.
- Лужанский И.Б. Разработка наплавочных сплавов для различных условий износа на основе их легирования кремнием В сб. Повышение качества и эффективности сварочного производства на предприятиях г. Москвы: М., МДНТП, 1984.
- Лужанский И.Б. Легирование кремнием при разработке сплавов для различных условий износа: Сварочное производство, 1985, № 2, с. 6−9.
- Лужанский И.Б. Прогрессивные способы наплавки: М., Машиностроение, 1984, 55 с.
- Лужанский И.Б. Разработка технологии автоматической плазменной наплавки уплотнительных поверхностей энергетической арматуры с изысканием проволочных присадочных материалов: Дисс. канд. техн. наук, М.', ЦНИИТМАШ, 1975, 225 с.
- Лужанский И.Б. Высокоэффективные легированные кремнием износостойкие стали для изготовительной наплавки деталей строительно-дорожной и горнодобывающей техники. // Технология металлов, 2011, 5, с. 19−22.
- Лужанский И.Б. Износостойкая дисперсионноупрочняемая сталь для изготовительной наплавки газопромысловой арматуры. // Производство проката, 2011,5, с. 35−40.
- Лужанский И.Б. Быстрорежущая сталь для наплавки многолезвийного металлорежущего инструмента. // Технология машиностроения, 2011, 6, с. 5−9.
- Лужанский И.Б. Теплостойкие стали для наплавки формообразующих деталей металлургического оборудования. // Производство проката, 2011, 6, с. 38−40.
- Лужанский И.Б. Высокоэффективные износостойкие стали, легированные кремнием. // Металловедение и термическая обработка металлов, 2011, 6, с. 3−8.
- Лужанский И.Б. Исследование и разработка высокоэффективной дис-персионноупрочняемой стали 09Х30Н10С2М1 для условий газоабразивного изнашивания. // Трение и смазка в машинах и механизмах, 2011, 6, с. 30−35.
- Лужанский И.Б. Износостойкие наплавочные стали 09X32H9M3C2 и 09Х32Н10МЗС1ФЮ, теплостойкость которых достигает 1080°С. // Сталь, 2011, 7.
- Макаров A.B. Повышение износостойкости сплавов железа за счет создания метастабильных и нанокристаллических структур: Автореферат на соиск. уч. степ. докт. техн. наук, Челябинск, 2009, 48 с.
- Маклинток Ф., Аргон А. Деформация и разрушение материалов: М., Мир. 1970, 433 с.
- Марченко Е.А. О природе разрушения поверхности металлов при трении: М., Наука, 1979, 118 с.
- Михайлычев В.Н. Методика и стенд для испытания на газоабразивное изнашивание в потоке природного газа: Заводская лаборатория, 1976, № 3, с. 334−336.
- Мертон и Смит. Основы физики сплавов: М., Металлургиздат. 1980,352 с.
- Муллакаев М.С., Габитов Э. В. Влияние особенностей электронной структуры на твердорастворное упрочнение сплавов на основе никеля, легированного переходными металлами: Вестник Башкирского университета, 2000, № 2−3. С. 15−19.
- Мокрова A.M. Кинетика и механизм деформирования защитных покрытий на сталях: Дисс. докт. техн. наук, Тула, 2000.
- Миркин Л.И. Рентгеноструктурный анализ: М., Наука, 1976, 325 с.
- Миркин Л.И. Справочник по рентгеноструктурному анализу поликристаллов: М., ФМ, 1961, 855 с.
- Михин Н.М. Трение в условиях пластического контакта: М., Наука, 1968, 101 с.
- Михин Н.М. Внешнее трение твердых тел: М., Наука, 1977, 215 с.
- Носовский И.Г. Влияние газовой среды на износ металлов: Киев, Техшка, 1968, 177 с.
- Нестеренко В.Б. (ред.) Рентгеноспектральный и электронно-микроскопический методы исследования структуры и свойств: Минск, Наука и техника, 1980. 189 с.
- Николин Б.И. Влияние кремния и марганца на параметры кристаллических решеток у-, e-фаз и объемные эффекты при у 8 превращениях в сплавах Г20: Физика металлов и металловедение, т. 44, № 3, 1977, с. 639−641.
- Новик Ф.С. Математические методы планирования экспериментов в металловедении: М., 1972, 106 с.
- Позняк JI.A., Скрыненко Ю. М., Тишаев С. И. Штамповые стали: М., Металлургия, 1980, 243 с.
- Портной К.И., Бабич Б. Н. Дисперсионноупрочняемые материалы: М'., Металлургия, 1974, 200 с.
- Прейс Г. А. О природе коррозионно-механического изнашивания металлов: Трение и износ, 1987, т. 8. № 5, с. 792−797.
- Петров И.В., Каковкин О. С., Никаноров М. М. Выбор наплавок износостойкого материала при высоком коэффициенте динамических нагрузок: Сварочное производство, 1973, № 3, с. 29−30.
- Пикеринг Ф.Б. Физическое металловедение и разработка сталей: М., Металлургия, 1982.
- Попов A.A., Попова JI.E. Изометрическая и термокинетическая диаграмма аустенита: Изв. АН СССР, Металлургия, с. 430.
- Платова С.Н., Левин С. М. Лившиц Л.С. Влияние условий газоабразивного изнашивания на структурные изменения в углеродистых сталях: Изв. ВУЗов, сер. Черная металлургия. 1979, № 3. С. 101−106.
- Рафф А.Х., Виндерхорн С. М. Эрозия при ударе твердых частиц В кн. Эрозия: М., Мир, 1982, с. 80−139.
- Резников А.Н. Теплофизика резания: М., Машиностроение, 1969.
- Рыбин В.В. Большие пластические деформации и разрушение металлов: М., Металлургия, 1986, 224 с.
- Раметняк Х.Д., Каллас П. К. Прочность и износ вольфрамокобальто-вых твердых сплавов в струе абразива: Трение и износ, 1988, № 3, с. 519−523.
- Самсонов Г. В. и др. Силициды: М., Металлургия, 1979.
- Силин A.A. Метод оценки влияния окружающей среды на процессы внешнего трения и износа В сб. Научные принципы и новые методы испытаний материалов для узлов нагружения: М., Наука, 1968.
- Сон Л. И. Статистическое и термодинамическое моделирование сигма-фазы. Доклады конференции «Проблемы физики твердого тела», Сочи, 2010.
- Сарафанов Г. Ф. Коллективные эффекты в ансамбле дислокаций и формирование границ при деформации металлов: Автореферат дисс. доктора физ-мат. наук, Белгород, 2008.
- Самохвалов Г. В., Шумилов М. А. К вопросу о принципе компенсационного легирования стали: Металлофизика, № 4, 2010.
- Степин B.C. Разработка и исследование износостойких технологичных железохромоникелькремнистых материалов для наплавки уплотнительных поверхностей энергетической арматуры: Дисс. канд. техн. наук, М., ЦНИИТМАШ, 1986.
- Степин B.C. Противозадирная стойкость Fe-Cr-Ni-Si наплавочных сплавов, применяемых в энергоарматуростроении: Тр. ЦЬЖИТМАШ, № 179. М., 1983.
- Студенок Е.С. и др. Износостойкость нестабильных марганцево-кремнистых аустенитых сталей при трении скольжения: Трение и износ. Том 4, № 4, 1983, с. 704−709.
- Солнцев Ю.П. и др. Литейные хладостойкие стали: М., Металлургия, 1991.
- Самсонов Г. В. и др. Температура поверхностных слоев сталей при аэроабразивном изнашивании: ИФЖК, 1975, № 3, с. 545−546.
- Серегин A.A., Скляр В. А. К вопросу о механизме изнашивания и разрушения подшипников качения с энергетических позиций: Трение и смазка в машинах и механизмах, 2011, № 1, с. 46−48.
- Сорокин Г. М. О природе износостойкости сталей при абразивном изнашивании: Вестник машиностроения, 1984, № 12, с. 25−27.
- Сорокин Г. М. и др. Влияние структуры стали на ее износостойкость в коррозионноактивных средах: Коррозия и защита в нефтегазовой промышленности, 1978, № 8, с.25−27.
- Ступницкий A.M. и др. Об изнашивании технически чистых металлов скользящей струей абразива — Сб. трудов Таллинский политехнический институт: Таллин, 1975, сер. А, № 381, с. 28−32.
- Тадольдер Ю.А. Некоторые количественные зависимости изнашивания технически чистых металлов — Сб.трудов. Таллинский политехнический институт: Таллин, сер. А, № 237, с. 3−13.
- Тененбаум М.М. Сопротивление абразивному изнашиванию: М., Машиностроение, 1976, 271 с.
- Тарбар П.И., Скорыгин Ю. В. Исследование структуры поверхностного слоя при трении: Машиноведение, 1975, 5, с. 106−109.
- Ууэмыйс Х.Х., Клейс И. Р. О влиянии концентрации абразивной струи на интенсивность изнашивания — Сб. трудов НИПИ Силикатобетон: Таллин, 1967, № 1, с. 92−114.
- Фомин В.В. Гидроэрозия металлов: М., Машиностроение, 1977, 287 с.
- Хрущев М.М., Бабичев M.А. Сопротивление абразивному изнашиванию и модуль упругости металлов и сплавов: ДАН СССР, 1960, т. 131, № 6, с. 1319.
- Цыпин И.И. Белые износостойкие чугуны, структура и свойства: М., Металлургия, 1983, 175 с.
- Червяков И.Б., Лужанский И. Б., Джербетян А. К., Левитский М. Ю. Сплав для износостойкой наплавки деталей газопромыслового оборудования: Доклады, Кишинев, 1985, сЛ 13−114.
- Червяков И.Б., Джербетян А. К. Высокотехнологичный сплав для износостойкой наплавки: Тезисы докладов, Андропов, 1986, с. 69−70.
- Червяков И.Б., Бирюков В. И., Шарапов А. Н. Повышеие долговечности клиновых задвижек — Сб. трудов МИНХиГП: М., 1985, вып. 195, с. 39−43.
- Червяков И.Б. и др. Полуэмпирическая модель прогнозирования износостойкости материалов в потоке твердых частиц — В кн. Триботехника: Машиностроение, М., 1983, с. 173.
- Черепанов Г. П. Механика хрупкого разрушения: М., Наука, 1974, 640'с.
- Черненко Н.Л. Структура и трибологические свойства хромомарган-цевых сталей: ФММ, 1999, т. 87, № 4, с. 91−98.
- Чичинадзе A.B. Расчет и исследование внешнего трения при торможении: М., Наука, 1967, 232 с.
- Шелдон. Сходства и различия в эрозионном поведении материалов: Теоретические основы инженерных расчетов, 1970, № 3, с. 208−214.
- Янг, Рафф. Определение эрозии металлов при ударном воздействии частиц Тр. ASME, сер. Д, 1977, № 2, с. 25−30.150.173 Авторские свидетельства и патенты, разработанные в. диссертации:
- Электродное покрытие, авт. св. № 431 977, пр. 8.06.72. // Рунов А. Е. и Лужанский И.Б.
- Сварочный материал, авт. св. № 441 126, пр. 9.06.72. // Рунов А. Е., Лужанский И. Б., Лобода A.C.
- Сплав на основе железа, авт. св. № 498 353, пр. 9.06.72. // Рунов А. Е., Лужанский И. Б., Вернигора Д. А. и др.
- Сплав для броневой защиты, авт. св. № 120 289. // Лужанский И. Б., Бы- ков Д.Н., Мельник В. Н. и др.
- Сварочный флюс, авт. св. № 613 871, пр. 7.12.76. // Потапов H.H., Лаза- рев Б.И., Вивсик С. Н., Лужанский И.Б.
- Плавленый флюс, авт. св. № 733 933, пр. 12.04.77. //Лужанский И.Б., Потапов H.H., Харин В. П., Рубцов И.Х.
- Состав электродного покрытия, авт. св. № 833 407, пр. 28.09.79. // Терс- кий Ф.Н., Левченков В. И., Юрин Г. Г., Соколов Е. В., Лужанский И. Б. и Др.
- Состав электродного покрытия, авт. св. № 1 074 691, пр. 24.12.82. // Лужанский И. Б., Терский Ф. Н., Левченков М. И. и др.
- Состав электродного покрытия, авт. св. № 1 050 837, пр. 24.05.82. // Лужанский И. Б., Яровинский Х. Л., Батурин А. И. и др.
- Состав электродного покрытия, авт. св. № 1 089 871, пр. 7.01.83. // Яровинский Х. Л. Лужанский И.Б., Батурин А. И., Гусев В.В.
- Состав электродного покрытия, авт. св. № 1 131 120, пр. 5.07.83. // Грин- берг H.A., Лужанский И. Б., Мамаев П. Н. и Черемисов М.М.
- Состав электродного покрытия для износостойкой наплавки, авт. св. № 1 112 670, пр. 18.04.83. // Лужанский И. Б., Гринберг H.A., Драгилев Б. Л. и др.
- Состав электродного покрытия, авт. св. № 1 358 251, пр. 28.10.85 // Лужанский И. Б., Просин В. Н., Китаев Я. А., Лучкина Н.М.
- Состав электродного покрытия, авт. св. № 1 358 252, пр. 14.01.86. // Лужанский И. Б., Червяков И. Б., Джербетян А.К.
- Состав сплава для износостойкой наплавки, полож. решение № 4 006 983/23−27(10 104), пр. 14.01.86. // Лужанский И. Б., Червяков И. Б., Джербе- тян А.К.
- Состав электродного покрытия для наплавки, авт. св. № 1 406 945, пр. 3.02.87. // Лужанский И. Б. и Китаев Я.А.
- Состав электродного покрытия для износостойкой наплавки, авт. св. № 1 412 146, пр. 5.02.87. //Калинин Л.Н., Куркумели Э. Г., Гринберг Н. А., Лу-жанс- кий И.Б. и Густов Ю.И.
- Состав электродного покрытия для наплавки деталей, эксплуатируемых при высоких удельных давлениях и температурах, авт. св. № 1 478 537, пр. 18.12.87. //Лужанский И.Б., Яровинский Х. Л., Коротенкова Л. Г. и др.
- Способ восстановления поршней, авт. св. № 1 770 110, пр. 23.04.90. // Киперник В. И., Дегтярь В. И., Слободенюк И. М., Лужанский И. Б. и др.
- Сталь для изготовления металлоформ, патент № 22 637−24, пр. 09.11.2003. //Лужанский И.Б.
- Способ монтажной сварки изделий из чугуна с шаровидным графитом, патент № 2 257 984, пр. 07.08.2003. // Лужанский И.Б.
- Способ изготовления узла трубопровода. Решение о выдаче патента № 2 004 120 766/02/22 346. //Лужанский И.Б.
- Сплав для монтажной сварки трубопроводов из высокопрочного чугуна, патент № 2 263 723, пр. 17.09.2003. //Лужанский И.Б.
- Сталь хладостойкая свариваемая, патент № 2 340 698, пр. 21.05.2007. //Лужанский И.Б., Анисимов В. П. и Панченко И.В.
- Alleten A. An Fe-Cr-Mo-Ni Sigma-Phase. Jomnal of Metals, Vol. 6, 1954, № 8.
- Amson J. Analysis of the gas shielded consumable metal arc welding system British Welding Journal, 1962, № 4.
- Beckmann G. A theory of abrasive wear based on shear effects in metal surfaces. Wear, 1980, vol. 59, p. 421−432.
- Bell G. Sprayed and fused metal coating. Welding and Metal Fabrication, 1962, № 10.
- Bowden F., Hughes T. The friction of clean metals and the influence of adsorbed gases. Proc. of the Royal Soc. A. 172, 1939, № 949.
- Brass L. The effects of microstructure of ductile alloys of solid particle erosion. M. S. Thesis, California, 1977.
- Buckley D., Gohnson R. The influence of silicon addition on friction and wear of nickel alloys of temperature to 1000°F. ASLE trans, vol. 3, 1960, № 1.
- Cooks M. The role of atmospheric oxidation high speed sliding phenomena. ASLE trans. Vol. 1, 1958, № 1.
- Finnie I. The mechanism of erosion of ductile metals ASME, 1958, p. 527−532.
- Finnie I. Erosion of surface by solid particles. Wear, 1960, vol. 3, p. 87 103.
- Gieman J. Hardening of high-chromium steels by sigma phase formation. ASME trans, vol. 43, 1951. Gupta K.P., Rajan N.S., Beck P.A. Trans. Met. Soc. AIME, 218, 617, 1960.
- Goodwin J.E., Sagew. Study of erosion by solid particles. Proc. Inst. Mech. Ing., 1969, vol. 184, p: 279−292.
- Head W.I., Harr M.E. The development of model to predict the erosion" of materials by natural contaminate. Wear, 1970, vol. 15, p. 1−46.
- Jahanmir S., Abrahamson E.P. The effect of second phase particles on Wear. Pittsburg, 1975, p. 854−864. The mechanics of subsurface damage in solid particle erosion. Wear, vol. 61, p. 309−324.
- Kleis I. et. al. The physical mechanism of the formation of metal micro-sheres in the wear process, Wear, 1979, vol. 53, № 1, p. 79−85.
- Moller E., Noland M. Cold-Welding tendencies and frictional studies of clean metals in ultra-high vacuum. — ASLE trans, vol. 10, 1967.
- Moor M.A. The relationship between the abrasive wear resistance hardness and mikrostructure of ferrite metals. Wear, 1974, vol. 28, № 1, p. 59−68.
- Muttion P.I., Watson T/D/ Some effects of mikrostructure of the abrasion resistance of metals. Wear, 1978, vol. 48, № 2, p. 385−398/
- Neilson J.H., Gilchrist A. Erosion by a stream of solid particles. Wear, 1968, vol. 11, p. 111−122.
- Peterson M., Florek J., Lee R. Sliding characteristics of metals at high temperatures/ ASLE trans, vol. 3, 1960, № 1.
- Robinson A. On the motion of stall particles in a potential field of flow. Communication on Pure and applied mathematics. 1956, vol. 9, p. 69−78.
- Rounds F. Effects of additives on the friction of steel on steel. ALSE trans, vol. 7, 1964, № 1.
- Tilly G.P., Sade W. The interaction of particle and material behavior in erosion process. Wear, 1970, vol. 16, p. 447−465. Sato A., Meschii M., Acta Met., 1973,21,753.
- Tuitt D. A. Erosion tests of metallic coatings. Proc. 4-th Jnt. Conf. of Rain Erosion. Meersburg, 1974.
- Tisma I.G. Sigma nucleation times in stainless steels. J. of Metals, 1956,6.
- Wilson W. The contact resistance and mechanical properties of surface film of surface film of metals. — Proc. Phyc. Soc. Vol. 68B, 1955.
- Winter R.E., Hutching I.M. The role of adiabatic shear in solid particle erosion. Wear, 1975, vol. 34, p. 141−148.