Проект сельскохозяйственного авторемонтного предприятия на 1500 автомобилей
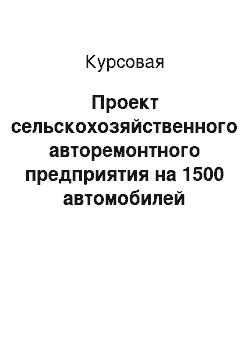
Основной задачей данного дипломного проекта было проектирование участка ремонта передних мостов автомобиля ГАЗ-53А сельскохозяйственного авторемонтного завода (АРЗ). В начале 90-х годов завод, в силу хорошо известных причин, производил лишь около 200 капитальных ремонтов полнокомплектных автомобилей и около 1200 ремонтов агрегатов в год, т. е. работал, практически, на 20% проектной мощности… Читать ещё >
Проект сельскохозяйственного авторемонтного предприятия на 1500 автомобилей (реферат, курсовая, диплом, контрольная)
1. ХАРАКТЕРИСТИКА РЕМОНТНОГО ПРЕДПРИЯТИЯ
1.1 КРАТКАЯ ИСТОРИЧЕСКАЯ СПРАВКА
1.2 ЭНЕРГОСНАБЖЕНИЕ ПРЕДПРИЯТИЯ
1.3 АНАЛИЗ ПРОИЗВОДСТВЕННОЙ ДЕЯТЕЛЬНОСТИ РЕМОНТНОГО ПРЕДПРИЯТИЯ
1.4 ХАРАКТЕРИСТИКА УЧАСТКА И ОБЪЕКТА РЕМОНТА
2. ОРГАНИЗАЦИОННЫЕ ПАРАМЕТРЫ ПРОИЗВОДСТВА
2.1 ОБОСНОВАНИЕ ПРОИЗВОДСТВЕННОЙ ПРОГРАММЫ ПРЕДПРИЯТИЯ
2.2 ОБОСНОВАНИЕ СХЕМЫ ТЕХНОЛОГИЧЕСКОГО ПРОЦЕССА РЕМОНТА И ЕЕ ОПИСАНИЕ
2.3 РАСЧЕТ ТРУДОЕМКОСТИ РЕМОНТА И ГОДОВОГО ОБЪЕМА РАБОТ, РАСПРЕДЕЛЕНИЕ ТРУДОЕМКОСТИ ПО ВИДАМ РАБОТ
2.4 ОРГАНИЗАЦИОННЫЙ РЕЖИМ РАБОТЫ И ФОНДЫ ВРЕМЕНИ РАБОЧИХ И ОБОРУДОВАНИЯ
2.5 РАЗРАБОТКА ГРАФИКА РЕМОНТНОГО ЦИКЛА
3. РАСЧЕТ УЧАСТКА
3.1 РАСЧЕТ ЧИСЛА РАБОТАЮЩИХ ПО РАБОЧИМ МЕСТАМ, СОСТАВЛЕНИЕ ШТАТНОЙ ВЕДОМОСТИ
3.2 ОБОСНОВАНИЕ НОМЕНКЛАТУРЫ И РАСЧЕТ КОЛИЧЕСТВА ОБОРУДОВАНИЯ
3.3 РАСЧЕТ КОЛИЧЕСТВА ПТО
3.4 РАСЧЕТ ПЛОЩАДИ УЧАСТКА
3.5 ТЕХНОЛОГИЧЕСКАЯ ПЛАНИРОВКА УЧАСТКА
3.6 ОРГАНИЗАЦИЯ РАБОЧИХ МЕСТ УЧАСТКА И ИХ ВЗАИМОСВЯЗЬ. ВЫБОР ОПТИМАЛЬНОГО ВАРИАНТА ПЛАНИРОВКИ РАБОЧЕГО МЕСТА
4. КОНСТРУКТОРСКАЯ ЧАСТЬ
4.1 ОБОСНОВАНИЕ КОНСТРУКЦИИ
4.1.1 Анализ существующих конструкций стендов
4.1.2 Предлагаемая конструкция стенда
4.2 ПРОЕКТНЫЕ РАСЧЕТЫ
4.2.1 Выбор масляного насоса
4.2.2 Расчет привода масляного насоса
4.2.3 Расчет конструкции масляного бака
4.2.4 Расчет трубопроводов
4.2.5 Выбор распределительного устройства
4.2.6 Расчет пальца
4.3 ОСНОВНЫЕ РЕГУЛИРОВКИ И РАБОТА НА СТЕНДЕ
4.3.1 Описание работы стенда, основные регулировки
4.3.2 Техника безопасности при работе на стенде
5. ОХРАНА ТРУДА И ТЕХНИКА БЕЗОПАСНОСТИ
5.1 ОРГАНИЗАЦИЯ РАБОТЫ ПО ОХРАНЕ ТРУДА И ТЕХНИКЕ БЕЗОПАСНОСТИ НА АРЗ
5.2 ОБЯЗАННОСТИ, ПРАВА И ОТВЕТСТВЕННОСТЬ АДМИНИСТРАТИВНО-ТЕХНИЧЕСКОГО ПЕРСОНАЛА
5.3. АНАЛИЗ ПРОИЗВОДСТВЕННОГО ТРАВМАТИЗМА НА АРЗ
5.4 СОСТОЯНИЕ ПРОИЗВОДСТВЕННОЙ САНИТАРИИ НА УЧАСТИЕ
5.5 ПОЖАРНАЯ БЕЗОПАСНОСТЬ
5.6 ИНСТРУКЦИЯ ПО ОХРАНЕ ТРУДА ПРИ РАБОТЕ НА СТЕНДЕ ХОЛОДНОЙ ПРАВКИ БАЛКИ ПЕРЕДНЕЙ ОСИ АВТОМОБИЛЯ ГАЗ-53А
5.6.1 Общие требования безопасности
5.6.2 Требования безопасности перед началом работы
5.6.3 Требования безопасности во время работы
5.6.4 Требования безопасности в конце работы
5.6.5 Требования безопасности в аварийных ситуациях
6. ТЕХНИКО-ЭКОНОМИЧЕСКАЯ ОЦЕНКА ПРОЕКТИРУЕМОГО УЧАСТКА ПО РЕМОНТУ БАЛКИ ПЕРЕДНЕЙ ОСИ ГАЗ-53А
6.1 РАСЧЕТ СТОИМОСТИ ОСНОВНЫХ ПРОИЗВОДСТВЕННЫХ ФОНДОВ
6.2 РАСЧЕТ СЕБЕСТОИМОСТИ РЕМОНТА ПЕРЕДНЕЙ ОСИ АВТОМОБИЛЯ ГАЗ-53А ПО ИЗМЕНЯЮЩИМСЯ СТАТЬЯМ
6.3 РАСЧЕТ ЭКОНОМИЧЕСКОЙ ЭФФЕКТИВНОСТИ ПРОЕКТА
6.4 ОСНОВНЫЕ ТЕХНИКО-ЭКОНОМИЧЕСКИЕ ПОКАЗАТЕЛИ УЧАСТКА
ЗАКЛЮЧЕНИЕ
Сельскохозяйственное производство сопряжено с большим объемом перевозок самых разнообразных грузов. Здесь — как собственно продукция земледелия (зерно, овощи, фрукты и т. п.), так и грузы необходимые для нормального функционирования самих сельскохозяйственных предприятий (химикаты, строительные материалы, металлопрокат, технологическое оборудование, сельскохозяйственная техника, запасные части). Подвижный состав аграрного сектора как никакой другой требует постоянного наблюдения и довольно частых ремонтов. Причины следующие:
· весьма жесткие условия эксплуатации, что, в первую очередь, определяется плохим состоянием сельских дорог, а порою — их полным отсутствием;
· большой, как правило, износ автомобилей, обусловленный экономическими проблемами хозяйств;
· слабая собственная ремонтная база сельхозпредприятий.
Именно эти обстоятельства делают весьма привлекательной далеко не новую идею создания межхозяйственных (например, районных) ремонтных баз (заводов), специализирующихся на ремонте автотракторной техники, эксплуатируемой сельхозпредприятиями.
Преимущества такого варианта очевидны и уже доказаны в прошлом. Здесь за счет специализации и концентрации средств появляется возможность:
· использовать самое современное высокопроизводительное технологическое оборудование;
· применять самые прогрессивные методы и технологии ремонта автомобилей и тракторов;
· развивать культуру производства и поддерживать необходимый профессиональный уровень работников;
· обеспечить высокое качество ремонта, что с учетом отмеченных выше жестких условий эксплуатации транспорта в сельских условиях весьма актуально.
Зачастую, такие предприятия, как в нашем случае, уже есть, и речь идет не об их создании с нуля, а об их развитии, совершенствовании, реконструкции.
В данном дипломном проекте для такого авторемонтного предприятия проектируется участок по ремонту переднего моста автомобиля ГАЗ-53А, а также производится модернизация одной из основных технологических установок участка — стенда для холодной правки балки передней оси.
1. Характеристика ремонтного предприятия
1.1 Краткая историческая справка
Авторемонтный завод был в свое время создан в соответствии с генеральным планом развития всесоюзного объединения ''Сельхозтехника''.
Изначально завод предназначался для ремонта широко использовавшихся в сельском хозяйстве автомобилей ГАЗ-51 и имел проектную мощность 1000 ремонтов в год.
Предполагалось, что завод будет обслуживать сельскохозяйственные предприятия достаточно большого региона, в состав которого входило 18 районов.
Завод дважды реконструировался, в результате чего был построен новый производственный корпус, несколько складов, реконструирована котельная.
После распада СССР АРЗ был преобразован в ТОО, а затем в акционерное общество. В настоящее время завод функционирует, и его можно считать достаточно успешным, однако, его оборудование во многом физически и морально устарело, а технологические линии и процессы не в полной мере соответствуют запросам заказчиков.
1.2 Энергоснабжение предприятия
Электроснабжение авторемонтного завода осуществляется от двух трансформаторных подстанций, где находятся 2 трансформатора с первичным напряжением 1000 В. Распределение электроэнергии потребителям, находящимся на территории завода, производится через понижающие трансформаторные подстанции. Напряжение питания на них U=380/220 В.
Общая нагрузки по заводу составляют:
Активная — 4000 кВт;
Реактивная — 1250 кВт;
Полная — 5250 кВт.
Снабжение АРЗ природным газом производится от городской газовой сети. Для обеспечения завода сжатым воздухом имеется собственная компрессорная станция.
Для снабжения АРЗ паром имеется собственная котельная на жидком топливе.
1.3 Анализ производственной деятельности ремонтного предприятия
Развитие и совершенствование авторемонтного производства требует правильной организации ремонта автомобилей, их агрегатов и узлов, которая зависит, в свою очередь, от целого ряда факторов, наиболее важными из которых являются:
рациональное размещение ремонтных предприятий;
специализация;
производственная мощность.
Данный авторемонтный завод был запроектирован на капитальный ремонт 1000 автомобилей ГАЗ-51, и после реконструкции увеличил свои мощности. После проведения реконструкции в старом корпусе производится ремонт двигателей, коробок передач, ремонт электорооборудования, восстановление деталей электромеханическим наращиванием. В новом корпусе производится общая разборка автомобилей, разборка агрегатов и узлов, восстановление деталей, сборка, испытания и окраска агрегатов и узлов, а также общая сборка и обкатка автомобилей. Тут же производится установка дизельных двигателей Д-240 и-240Л на автомобили ГАЗ-53А по специальному заказу с заменой трансмиссии.
В начале 90-х годов завод, в силу хорошо известных причин, производил лишь около 200 капитальных ремонтов полнокомплектных автомобилей и около 1200 ремонтов агрегатов в год. К концу 90-х ситуация усугубилась еще больше, что, в первую очередь, объясняется обвальным старением оборудования, несовершенством используемых технологий, снижением профессионального уровня работников. Все это привело к тому, что завод оказался не в состоянии выполнять необходимый объем работ при их необходимом качестве. В настоящее время, как уже говорилось выше, ситуация несколько выправилась, но все отмеченные проблемы пока еще стоят достаточно остро.
1.4 Характеристика участка и объекта ремонта
Участок по ремонту передних мостов (передних осей) автомобиля ГАЗ-53А расположен в новом корпусе ремонтного завода и занимает порядка 85 м² производственной площади. Участок рассчитан на ремонт 1000 передних мостов. Имеется централизированный подвод электроэнергии и воды к технологическому оборудованию. К недостаткам участка следует отнести устаревшее оборудование, низкую квалификацию рабочих, плохую организацию труда, несоблюдение технических требований на ремонт и восстановление деталей.
Автомобиль ГАЗ-53А представлен на рисунке 1.1, а его техническая характеристика дана в таблице 1.1.
Рисунок 1.1. Внешний вид автомобиля ГАЗ-53А Таблица 1.1
Технические характеристики автомобиля ГАЗ-53А
Технические характеристики | ||
Завод-изготовитель: | Горьковский автомобильный завод, г. Горький | |
Время выпуска: | 1965;1994 гг. | |
Габаритные размеры: длина ширина высота | 6395 мм 2380 мм 2220 мм | |
Число мест | ||
Грузоподъемность | 4000 кг | |
Масса в снаряженном состоянии | 3250 кг | |
Полный вес | 7400 кг | |
База | 3700 мм | |
Минимальный дорожний просвет | 265 мм | |
Максимальная скорость | 85 км/ч | |
Расход топлива | 24 л/100км | |
Двигатель | ГАЗ-53, карбюраторный, V-образный, четырехтактный, восьмицилиндровый, верхнеклапанный | |
Объем двигателя | 4.25 л | |
Степень сжатия | 6.7 | |
Максимальная мощность | 115 л.с. | |
Сцепление | однодисковое, сухое | |
Коробка передач | четырехступенчатая | |
Главная передача | одинарная, коническая, гипоидная | |
Рулевой механизм | глобоидный червяк и трехгребеневый ролик | |
Размер шин | 8,25−20 | |
Техническая характеристика ходовой части автомобиля приведена в таблице 1.2.
Таблица 1.2
Техническая характеристика ходовой части автомобиля ГАЗ-53А
Технические параметры | Значения | |
1. Несущая система автомобиля | Рама лестничная | |
2. Количество мостов | ||
2.1. Передний ведомый мост | ||
2.2. Средний ведущий мост | ; | |
2.3. Задний ведущий мост | ||
3. Количество колес и подвеска | 4 колеса | |
а) подвеска передних колес | индивидуальная | |
б) подвеска задних колес | индивидуальная | |
3.1. Передняя подвеска | зависимая | |
3.2. Задняя подвеска | Индивидуальная, зависимая | |
4. Колеса | Дисковые, штампованные | |
4.1. Тип шин | 8.25−20 диагональные | |
4.2. Норма стойкости | ||
4.3. Размер обода | 6.5Б-20 | |
4.4. Ступица передних колес | есть | |
4.5. Ступица задних колес | есть | |
Управляемый ведомый мост автомобиля ГАЗ-53А (см. рисунок 1.2) представляет собой балку 18 с установленными по обоим концам поворотными кулаками 12. Балка кованная, стальная имеет двутавровое сечение. Средняя часть балки выгнута вниз, что позволяет более низко расположить двигатель. Шкворень 13 закреплен неподвижно в бобышке балки клиновым штифтом (стопором) 16. Поворотный кулак 12 установлен на шкворне на бронзовых втулках, запрессованных в отверстия проушин кулака. Для смазки втулок в поворотные кулаки ввернуты масленки. Поворотный рычаг 14 и рычаги рулевой трапеции 22 вставлены в конические отверстия проушин кулака и закреплены гайками.
Рисунок 1.2. Передний мост автомобиля ГАЗ-53А
1 — диск колеса; 2 — тормозной барабан; 3 — ступица колеса; 4 — винт крепления тормозного барабана к ступице; 5, 6 — внутренний и наружный подшипники ступицы; 7 — гайка крепления ступицы; 8 -шпилька ступицы; 9 — гайка крепления диска колеса; 10 — маслоотражатель; 11 — опорный диск тормозного механизма; 12 — левый поворотный кулак; 13 — шкворень поворотного кулака; 14 — поворотный рычаг; 15 — регулировочные шайбы; 16 — конусный стопор шкворня; 17 — опорный подшипник (металлические шайбы); 18 — балка переднего моста; 19 — сальник ступица; 20 — пресс-масленка; 21 — ограничитель (болт с контргайкой) поворота колес; 22 — рычаг рулевой трапеции; 23 — поперечная тяга с левым и правым наконечниками Между балкой моста и поворотным кулаком установлен опорный подшипник 17. Он состоит из двух шайб: верхней стальной и нижней из графитизированной бронзы, которая стоит неподвижно в расточке кулака и поворачивается вместе с ним.
Осевой зазор между поворотным кулаком и балкой регулируется шайбами 15. К поворотному кулаку болтами прикреплен опорный диск 11 колесного тормозного механизм. На цапфе поворотного кулака на двух конических роликовых подшипниках устанавливается ступица 3 переднего колеса. Подшипники ступицы закреплены гайкой 7, которая фиксируется замочным кольцом, шайбой и контргайкой. Гайкой также регулируется затяжка подшипников во время эксплуатации.
Балка передней оси, изготовлена из легированной стали 3ОХ. На верхней полке на расстоянии 806 мм друг от друга расположены две площадки, которыми ось прикреплена к рессорам.
Поворотный кулак, штампованный из легированной стали 35Х, имеет цапфу с двумя цилиндрическими отверстиями 30 и 45 мм под подшипники ступицы переднего колеса, шейку под втулку сальника ступицы и массивной фланец для центрирования щита тормоза. Шкворень 30 мм изготовлен из прутковой стали 45 и закален т.в.ч.
У автомобиля ГАЗ-53А зависимая передняя подвеска (рис. 1.3, а) состоит из двух продольных полуэллиптических рессор, расположенных под лонжеронами рамы вдоль автомобиля. Концы сдвоенного коренного листа 11 рессоры закреплены при помощи резиновых опор в прикрепленных к лонжерону кронштейнах 1 и 6. Концы одного коренного листа отогнуты вверх, а другого вниз, вследствие чего образуется торцовая упорная поверхность. Концы листов охвачены обоймами 7 и 12, увеличивающими давления рессоры на резиновые опоры, что уменьшает их износ. Для смены резиновых опор и демонтажа рессор кронштейны 1 и 6 имеют установленные на болтах съёмной крышки.
Рессора собрана из стальных листов разной длины, которые стянуты вместе хомутами и прикреплены к переднему мосту двумя' стремянками 10. С помощью этих же стремянок к верхней части рессоры крепят резиновый буфер 9, смягчающий удары при максимальных прогибах рессоры. Рессора при прогибе перемещается в продольном направлении В сторону ее заднего конца. В переднюю подвеску входит также гидравлический телескопический амортизатор 5, который при помощи резинометаллических шарниров 4 соединяет передний мост и кронштейн 3 лонжерона 2.
Заднюю подвеску автомобиля ГАЗ-53А (рис. 1.3, б) составляют две основные рессоры 28 с дополнительными рессорами 21 (подрессорниками), расположенными сбоку вдоль лонжеронов рамы в задней части автомобиля. Основная задняя рессора состоит из 14-ти листов и прикреплена к раме, так же как и передняя рессора, при помощи нижней и верхней резиновых опор 13. Передний конец рессоры упирается в дополнительный резиновый торцовый упор 14.
Рисунок 1.3. Подвески автомобиля Г АЗ-53А:
а — передняя; б — задняя; 1, 3 и 6 — кронштейны; 2 — лонжерон; 4 — шарнир; 5 — амортизатор; 7 и 12 — обоймы концов коренных рессорных листов; 8 и 13 — верхние и нижние опоры; 9 — буфер; 10 — стремянка; 11 — двойной коренной лист; 14 — торцовый упор; 15 и 25 — крышки соответственно переднего и заднего кронштейнов; 16 и 17 — нижняя и верхняя обоймы переднего конца рессоры; 18 — опора дополнительной рессоры; 19 — накладка; 20 — стремянка задней рессоры; 21 — дополнительная рессора; 22 и 24 — центровые болты; 23 — подкладка; 26 и 27 — верхняя и нижняя обоймы заднего конца рессоры; 28 — основная рессора; 29 — подкладка стремянок
2. Организационные параметры производства
2.1 Обоснование производственной программы предприятия
Авторемонтный завод производит капитальный ремонт автомобиля ГАЗ-53А. Зона обслуживания предприятия включает в себя 18 административных районов. Количественное распределение автомобилей по районам представлено таблице 1.1.
Таблица 1.1.
Количество автомобилей ГАЗ-53А по районам
№ п/п | Наименование районов | Количество автомобилей | |
Карабулакский | |||
Боровской | |||
Яснополянский | |||
Прииртышский | |||
Ишимский | |||
Зерендинский | |||
Сосновогорский | |||
Целиный | |||
Жанадалинский | |||
Кызылжарский | |||
Орловский | |||
Тимофеевский | |||
Заозерный | |||
Пролетарский | |||
Дубовский | |||
Жамбыльский | |||
Луговской | |||
Валихановский | |||
ИТОГО | |||
Количество капитальных ремонтов (КР) автомобилей определены по наличию охвата машин капитальным ремонтом:
NKP = NM K0, (2.1)
где NKP — количество автомобилей, нуждающихся в капитальном ремонте, шт;
NM — количество автомобилей в зоне обслуживания, шт;
К0 — коэффициент охвата машин капитальным ремонтом.
; (2.2)
где ВГ — среднегодовая наработка автомобиля, тыс. км.
ВГ = 40 000 км, по фактическим данным предприятия.
ВК — пробег автомобиля до капитального ремонта, тыс. км.
ВК = 160 тыс. км, по.
— поправочный коэффициент к нормативам на техническое обслуживание и ремонт, учитывающий категорию дорожных условий эксплуатации, по = 1,00
КЗ — зональный поправочный коэффициент по КЗ = 1,00.
Тогда .
Тогда NКР = 58 460,25 = 1462.
Принимаем NКР = W = 1500 шт.
2.2 Обоснование схемы технологического процесса ремонта и ее описание
Под технологическим процессом понимают часть производственного процесса, в течение которого происходит последовательная смена состояния ремонтируемого объекта. Принимаем схему технологического процесса представленную на рисунке 2.1.
Поступающая на участок передняя ось разбирается на узлы. Узлы разбираются на детали и отправляются на дефектацию. Продефектованные детали делятся на три группы: негодные, ремонтопригодные, годные. Ремонтопригодные детали направляются на ремонт и восстановление, негодные — в утиль. Годные, отремонтированные и новые детали со склада комплектуются и собираются в узлы. Из узлов осуществляется сборка передней оси, которая потом подвергается регулировке.
2.3. Расчет трудоемкости ремонта и годового объема работ, распределение трудоемкости по видам работ
Согласно [4] трудоемкость ремонта переднего моста автомобиля ГАЗ-53А составляет 7,7 чел. ч для предприятия с годовой программой 5000 шт. С учетом поправочного коэффициента КПР = 1,11 трудоемкость ремонта на предприятии с программой 1500 шт. составит 8,54 чел.ч.
Рисунок 2.1. Схема технологического процесса ремонта передней оси автомобиля ГАЗ-53А Трудоемкость ремонта на перспективу равна:
ТРП = ТРД КС КСЕР КПЕР КПР, чел.ч. (2.3)
где ТПР — трудоемкость ремонта машины данной марки на перспективу, чел.ч.;
ТРД — действительная трудоемкость ремонта машины данной марки, чел.ч.;
КС — коэффициент, учитывающий соотношение в программе предприятия полнокомплектных машин и комплектов агрегатов, КС = 1;
КСЕР — коэффициент, учитывающий влияние на трудоемкость производственной программы, по КСЕР = 0,7;
КПЕР — коэффициент, учитывающий рост производительности труда на перспективу, КПЕР = 0,98;
КПР — коэффициент приведения данной марки машины к аналогу основной модели, КПР = 1.
Подставив данные получим:
ТРП = 8,54 1 0,7 0,98 1 = 5,86 чел.ч.
Годовой объем работ на перспективу составит:
ТП = ТРП WПР = 5,86 1500 = 8790 чел.ч. (2.4)
Согласно и процентное содержание работ по ремонту передней оси автомобиля ГАЗ-53А равно: таблица 2.2.
Таблица 2.2.
Процентное содержание работ по ремонту передней оси автомобиля ГАЗ-53А
Наименование работ | Разряд работы | % | Трудоемкость, чел.ч. | |
Разборка на узлы 1. Снятие стремянок, накладок, рессор | 2,24 | 0,1 | ||
2. Снятие рулевых тяг | 1,54 | 0,07 | ||
3. Снятие рычагов рулевого управления | 1,88 | 0,08 | ||
4. Снятие ступиц | 2,73 | 0,12 | ||
5. Снятие поворотных кулаков | 3,07 | 0,13 | ||
6. Разборка на детали | 11,3 | 0,5 | ||
7. Мойка деталей | 2,56 | 0,11 | ||
8. Дефектация и комплектация | 24,4 | 1,04 | ||
9. Сборка узлов | 28,6 | 1,22 | ||
Сборка передней оси 10. Установка поворотных кулаков | 6,14 | 0,26 | ||
11. Установка ступиц | 3,92 | 0,17 | ||
12. Установка рычагов рулевого управления | 3,24 | 0,14 | ||
13. Установка рулевых тяг | 2,24 | 0,1 | ||
14. Установка стремянок, накладок | 2,56 | 0,11 | ||
15. Регулировка | 3,58 | 0,15 | ||
ИТОГО | 4,30 | |||
С учетом процентного содержания работ разряда составим таблицу (2.3) распределения трудоемкости ремонта передней оси по видам работ.
Таблица 1.3.
Трудоемкость ремонта передней оси автомобиля ГАЗ-53А
Наименование работ | Разряд работ | % | Трудоемкость, чел.ч. | ||
на 1 объект | на програм. | ||||
Разборка на узлы 1. Снятие стремянок, накладок, рессор | 2,24 | 0,13 | |||
2. Снятие рулевых тяг | 1,54 | 0,09 | |||
3. Снятие рычагов рулевого управления | 1,88 | 0,11 | |||
4. Снятие ступиц | 2,73 | 0,16 | |||
5. Снятие поворотных кулаков | 3,07 | 0,18 | |||
6. Разборка на детали | 11,3 | 0,67 | |||
7. Мойка деталей | 2,56 | 0,15 | |||
8. Дефектация и комплектация | 24,4 | 1,43 | |||
9. Сборка узлов | 28,6 | 1,67 | |||
Сборка передней оси 10. Установка поворотных кулаков | 6,14 | 0,36 | |||
11. Установка ступиц | 3,92 | 0,23 | |||
12. Установка рычагов рулевого управления | 3,24 | 0,19 | |||
13. Установка рулевых тяг | 2,24 | 0,13 | |||
14. Установка стремянок, накладок | 2,56 | 0,15 | |||
15. Регулировка | 3,58 | 0,21 | |||
ИТОГО | 5,86 | ||||
2.4 Организационный режим работы и фонды времени рабочих и оборудования
Под режимом работы предприятия понимается количество рабочих дней в году, продолжительность смены, число смен, количество рабочих часов в неделю в днях и часах.
На АРЗ принят следующий режим работы: пятидневная рабочая неделя, продолжительность смены 8 часов, работа в одну смену.
Номинальный фонд времени работы определим по формуле [9]:
ФН = (КР tСМ — КП tС) n, (2.5)
где КР — число рабочих дней в году;
tСМ — число часов в смене, tСМ = 8 ч;
КП — число предвыходных и предпраздничных дней, КПП = 5;
tС — время, на которое сокращается смена в предпраздничные и предвыходные дни.
КР = КК — КВ — КПР, (2.6)
КК — число календарных дней в 2000 году, КК = 366;
КВ — количество выходных дней, КВ = 106;
КПР — количество праздничных дней, КПР = 10.
КР = 366 — 106 — 10 = 250 дней
n — число смен.
ФН — (250 8 — 5 1) 1 = 1995 ч.
Действительный годовой фонд времени рабочего:
ФД = (ФН — К0 tСМ) Р, (2.7)
где К0 — количество дней отпуска, К0 = 20 дней;
Р — коэффициент потерь рабочего времени, Р = 0,97.
ФД = (1995 — 20 8) 0,97 = 1780 ч.
Коэффициент штатности:
(2.8)
Действительный годовой фонд времени работы оборудования:
ФД.О. = ФН О n (2.9)
где О — коэффициент использования оборудования, О = 0,97;
n — количество смен.
ФД.О. = 1995 0,97 1 = 1935 ч.
2.5 Разработка графика ремонтного цикла
Исходные данные:
W — программа предприятия, шт;
W = 1500 шт.;
ФН — номинальный годовой фонд времени участка;
ФН = 1995 ч.;
Наименование операций технологического процесса участка;
Разряд работы операций;
Трудоемкость операций.
Определим такт производства [10]:
; (2.10)
ч/шт.
Определим расчетное количество рабочих по каждому виду работ:
; (2.11)
где Тi — трудоемкость вида работ, чел.ч.
Загрузку рабочих органов определим по формуле:
(2.12)
Полученные данные сводим в таблицу 2.4.
Определим коэффициенты параллельности и последовательности выполнения работ по формулам:
; (2.13)
; (2.14)
где ТПАР, ТПОС — трудоемкость параллельно и последовательно выполняемых работ, чел.ч.
ТОБ — общая трудоемкость ремонта передней оси.
Таблица 2.4
График ремонтного цикла
Наимено-вание рабочего места | № раб. Места | № п/п | Наименование операций (работ) | Разряд работы | Трудо-емко-сть, чел.ч. | Количество рабочих | Процент загрузки | ||
расч. | прин. | ||||||||
Разборо-моечное | Разборка на узлы: Снятие стремянок, накладок, рессор | 0,13 | 0,1 | ||||||
Снятие рулевых тяг | 0,09 | 0,07 | |||||||
Снятие рычагов рулевого управления | 0,11 | 0,08 | |||||||
Снятие ступиц | 0,16 | 0,12 | |||||||
Снятие поворотных кулаков | 0,18 | 0,13 | |||||||
Разборка на детали | 0,67 | 0,5 | |||||||
Мойка деталей | 0,15 | 0,11 | |||||||
Дефектации и комплектации | Дефектация и комплектация | 1,43 | 1,08 | ||||||
Сборочно-регулировочное | Сборка узлов | 1,67 | 1,26 | 110,5 | |||||
Сборка передней оси Установка поворотных кулаков | 0,36 | 0,27 | |||||||
Установка ступиц | 0,23 | 0,17 | |||||||
Установка рычагов рулевого управления | 0,19 | 0,14 | |||||||
Установка рулевых тяг | 0,13 | 0,1 | |||||||
Установка стремянок, накладок | 0,15 | 0,11 | |||||||
Регулировка | 0,21 | 0,16 | |||||||
Фронт работ равен:
(2.15)
где tЦ — время пребывания машины в ремонте.
.
3. Расчет участка
3.1 Расчет числа работающих по рабочим местам, составление штатной ведомости
Явочное количество рабочих и работающих по рабочим местам согласно графику ремонтного цикла.
1 рабочее место RЯ = 1,0 чел.
2 рабочее место RЯ = 1,0 чел.
3 рабочее место RЯ = 2,0 чел.
Списочное количество рабочих равно:
; (3.1)
где = 0,9 — коэффициент штатности.
Тогда: 1 рабочее место RСП = 1,11, принимаем 1 чел.
2 рабочее место RСП = 1,11, принимаем 1 чел.
3 рабочее место RСП = 2,11, принимаем 2 чел.
Таблица 3.1
Состав и количество работающих
Категория работающих | Количество работающих | |||||
явочное | списочное | |||||
расчетн. | принят. | расчетн. | принят. | |||
Производственные рабочие | 4,4 | 4,44 | ||||
Вспомогательные рабочие, 14% | 0,36 | 0,4 | ||||
Руководящие и ИТ, 14% | 0,36 | 0,4 | ||||
Служащие (СКП), 12% | 0,32 | 0,36 | ||||
МОП, 2% | 0,08 | 0,09 | ||||
Таблица 3.2.6.
Штатная ведомость производственных рабочих
№ п/п | Наименование рабочих мест | Профессия | Коли-чество | Количество по разрядам | Количе-ство | |||||||
муж | жен. | |||||||||||
1 раб. место | слесарь-ремонтник | |||||||||||
3 раб. место | слесарь-ремонтник | |||||||||||
2 раб. место | дефектовщик | |||||||||||
ИТОГО: | ||||||||||||
3.2 Обоснование номенклатуры и расчет количества оборудования
Номенклатура технологического оборудования должна соответствовать выполнению всех операций технологического процесса. По производственному назначению технологическое оборудование подразделяется на основное, подъемно-транспортное, общего назначения. Расчету подлежит основное оборудование, остальное выбирается по табелю оборудования для участка.
Количество моечных машин равно [11]:
; (3.2)
где: W — годовая программа предприятия, шт.;
Фд.о. — действительный годовой фонд времени оборудования; ч.;
q — часовая производительность моечной машины, шт/ч;
Км — коэффициент учитывающий использование моечного оборудования по времени, Км=0,85 по.
.
Принимаем Nм=1.
Количество разборо-сборочного оборудования равно по [3]:
(3.3)
где Тр.с. — трудоемкость разборо-сборочных работ, выполняемых на стендах, чел.-ч.
.
Принимаем Nр.с.=2.
Количество оборудования для контрольно-дифектовочных и комплектовочных работ равна по [3]:
; (3.4)
где: W — годовая программа, шт;
tk — продолжительность контроля одного объекта ремонта, ч;
Кс — коэффициент, учитывающий использование оборудования по времени, Кс=0,8 по.
.
Принимаем Nс=1/
Количество станочного оборудования равно по [3]:
(3.5)
где Тст — общая годовая трудоемкость станочных работ, ч;
Кз — коэффициент загрузки оборудования по времени, Кз=0,9.
.
Принимаем Nст=2.
Таблица 3.3
Технологическое оборудование и оснастка участка
№ п/п | Наименование и марка оборудования | Коли-чество | Размеры | Площадь, м2 | |
Разборо-сборочный стенд ОР-6361-ГОСНИТИ | 850×1250 | 2,125 | |||
Машина моечная ОМ-5300 | 3360×2760 | 9,27 | |||
Верстак слесарный ОРГ-1468−01−060А-ГОСНИТИ | 1200×800 | 1,92 | |||
Стол монтажный ОРГ-1468−01−080А-ГОСНИТИ | 240×800 | 1,92 | |||
Стол дефектовочный ОРГ-1468−01−090А-ГОСНИТИ | 2400×1610 | 3,86 | |||
Стенд для холодной правки балки переднего моста автомобиля ГАЗ-53А | 2120×352 | 0,75 | |||
Пресс гидравлический ОКС-1671А-ГОСНИТИ | 1250×500 | 0,63 | |||
Контейнер для деталей | 3,24 | ||||
Шкаф для инструмента ОРГ-1468−07−040-ГОСНИТИ | 860×360 | 0,62 | |||
Стеллаж для деталей ОРГ-1468−05−230А-ГОСНИТИ | 1400×500 | 2,8 | |||
Ларь для обдирочных материалов ОРГ-1468−07−090А-ГОСНИТИ | 1000×500 | 1,0 | |||
ИТОГО: | ; | 28,1 | |||
3.3 Расчет количества ПТО
Количество подъемно-транспортного оборудования равно по [12]:
(3.6)
где nоп — количество крановых операций в час, nоп=3;
Ткр — средняя продолжительность крановой операции, мин;
Кпр — коэффициент учитывающий простои крана Кпр=0,87.
(3.7)
где L — средняя дальность транспортирования груза за одну операцию, м. L=20м;
V — скорость передвижения крана, V=20 м/мин
tз — среднее время загрузки крана за одну операцию, tз=4мин;
tр — среднее время разгрузки крана за одну операцию, tр=3мин;
Тогда:
;
.
Принимаем Nкр=1.
В качестве ПТО принимаем кран-балку грузоподъемностью 3 тонны. Догрузка кран-балки осуществляется за счет соседних участков.
3.4 Расчет площади участка
Площадь участка рассчитывается по формуле:
Fуч=FобК, (3.8)
где Fоб — суммарная площадь пола занимаемая технологическим оборудованием, м2;
К — коэффициент проходов и проездов.
Fуч= Fрм1+ Fрм2+ Fрм3, (3.9)
Где Fрмi — площадь i-го рабочего места, м2.
Тогда: Fрм1=12,335=61,65 м²;
Fрм2=1,924=7,68 м²;
Fрм3=10,15=50,5 м²;
Fуч=61,65+7,68+50,5=119,83 м².
Принимаем Fуч=120м2.
3.5 Технологическая планировка участка
Планировка участка выполняем в соответствии с компоновочным планом здания, указываем наружные и внутренние стены, колонны здания, окна, ворота, транспортное оборудование, верстаки, стеллажи и т. п., проходы и проезды. Технологическое оборудование на плане изображаем упрощенными контурами с учетом крайних положений перемещающихся частей.
Все виды оборудования нумеруем сквозной порядковой нумерацией. Вне контура указываем. Условные обозначения подвода электроэнергии, воздуха, воды.
Расстановку оборудования выполняем с учетом существующих требований, норм расстояний между оборудованием и элементами зданий, норм ширины проездов и норм расстояний между оборудованием [14, 15].
Оборудование располагаем в порядке выполнения технологических операций. Также оборудование располагаем с учетом возможности изменения планировки при использовании более прогрессивных технологических процессов.
Размеры планируемого участка согласно расчетам равны: длина L=12м, ширина В=10 м.
План размещения оборудования на участке представлен на рисунке 3.1.
3.6 Организация рабочих мест участка и их взаимосвязь. Выбор оптимального варианта планировки рабочего места
Рабочее место — это первичная производственная ячейка, в которой происходит соединение трех элементов труда: средств труда, предметов труда и самого труда (человека).
Рабочее место представляет собой часть площади участка, оснащенную необходимым оборудованием и оснасткой, закрепленную за одним или несколькими рабочими, на которой выполняется определенные операции технологического процесса ремонта узла.
Под организацией рабочего места понимается создание условий, способствующих качественному выполнению операций технологического процесса, рациональному использованию рабочего времени и средств труда, повышению производительности труда и сохранению здоровья рабочих.
Рисунок 3.1. План размещения оборудования на участке ремонта переднего моста
1 — разборочно-сборочный стенд; 2 — моечная машина; 3 — верстак слесарный; 4 — стол монтажный; 5 — стол дефектовочный; 6 — стенд для холодной правки балки переднего моста; 7 — пресс гидравлический; 8 — контейнер для деталей; 9 — шкаф для инструмента; 10 — стеллаж для деталей; 11 — ларь для обтирочных материалов; 12 — кран-балка; 13 — ящик с песком и огнетушителями; 14 — сверлильный станок
ремонтный участок завод трудоемкость
Современное ремонтно-обслуживающее предприятие представляет собой сложный механизм, в каждом его составляющие (участок, рабочее место) настолько взаимосвязаны, что от организации труда на любом из них, зависит общий ритм работы предприятия. Поэтому рабочие места нельзя рассматривать изолированно друг от друга, независимо от выполняемой организации и технологии ремонта.
Оснащение рабочего места.
В зависимости от типа, характера производства, действующего технологического процесса рабочее место оснащается:
основным технологическим оборудованием (станок, агрегат, верстак и т. д.);
предметами труда (сырье, заготовки, детали);
основной технологической оснасткой (инструмент, приборы, приспособления);
вспомогательным оборудованием и оснасткой, которые непосредственно не участвуют в изменении предмета труда, но создают условия наилучшего проведения этого процесса.
Обоснование оптимального варианта организации рабочего места
Первым этапом обоснования оптимального варианта планировки является изучение содержания трудовых процессов на рабочем месте. Основное внимание уделяется на установку и снятие деталей, смену инструментов, контроль и сортировку продукции. В зависимости от частоты смены видов работ, а следовательно и использование инструмента, оборудования решается вопрос об их расположении на рабочем месте с учетом принципа: что чаще берется — располагается ближе к рабочему. Главной задачей организации рабочего места является наиболее рациональное расположение узлов, деталей, оборудования, оснастки, грузоподъемных и транспортных средств с тем, чтобы обеспечить минимальные затраты труда на выполнение простейших трудовых движений: переходов, поворотов, нагибаний и т. д.
Решение задачи нахождения оптимального варианта организации рабочих мест может быть значительно упрощено с помощью специальных систем бальной оценки различных вариантов. Сущность методики заключается в том, что любое рабочее место схематично можно разделить на ряд зон в зависимости от состава трудовых движений, необходимых для перемещения предмета труда к месту его установки, перестановки, обработки. При построении данной схемы рабочее место в плане разделено на две основные зоны: А, находящуюся спереди от основной линии, и Б, находящуюся сзади этой линии. Каждая из основных зон разделена на ряд секторов в зависимости от расположения к рабочему, а каждый сектор, в свою очередь разделен концентрическими окружностями, определяющими расстояние места расположения предметов труда от рабочего (в м.). Зоны делятся также в зависимости от расположения предмета по высоте на верхние (В) и нижние (Н). Цифровая индексация построена таким образом, что меньшее значение индексов соответствует более удобным зонам.
Оценив во времени затраты труда на выполнение манипуляций, связанных с предметами труда и технологической оснасткой, в той части, в какой эти манипуляции зависят от организации рабочего места, можно создать систему бальной оценки организации рабочих мест. Бальная система основана на принципе экономии движений с уменьшение затрат времени на манипуляции с предметом труда или с инструментом число баллов возрастает, т. е. большее значение бальной оценки соответствует лучшей организации рабочего места, и наоборот.
Так если работы выполняются с помощью оборудования (разборка, сборка, дефектация и т. д.) то число баллов рассчитывают по формуле по [16]:
; (3.10)
где n — число единиц (деталей) задействованных при выполнении данной операции не считая базовой;
— бальная оценка расположения на рабочем месте базового объекта при выполнении операции;
1 — бальная оценка расположения на рабочем месте базового объекта до выполнения операции;
0 — бальная оценка расположения на рабочем месте остальных объектов (деталей) которые должны быть установлены на базовом объекте.
Оптимальный вариант организации рабочего места соответствует большему числу баллов. Экономия рабочего времени за смену или после выполнения работ на одном объекте в результате рационализации рабочего места определяют по формуле по [16]:
Э=0,01(Бн-Бс), (3.11)
где Бс — бальная оценка организации рабочего места до рационализации;
Бн — бальная оценка организации рабочего места после рационализации.
Рассмотрим рабочее место слесаря-сборщика до рационализации (рисунок 3.1) и после рационализации (рисунок 3.2). На рабочем листе представлена базовая деталь при сборке В, базовая деталь до сборки В1, пять деталей, подлежащих установке в базовую деталь 01−05, узел после сборки У.
Бальная оценка рабочего места, определяемая по формуле (3.10) согласно [16], будет равна:
· до рационализации:
;
· после рационализации:
.
Экономия рабочего времени после выполнения работ на одном объекте в результате рационализации составит:
Э=0,01(22,1−20,25)=0,02ч.
Таким образом, предлагаемая организация рабочего места является более рациональной.
Рисунок 3.1. Рабочее место до рационализации Рисунок 3.2. Рабочее место после рационализации
4. Конструкторская часть
4.1 Обоснование конструкции
Поступающая на ремонт передняя балка автомобиля ГАЗ-53А имеет несколько дефектов, из которых наиболее опасным является прогиб в горизонтальной или вертикальной плоскостях, а также скрученность. Устранения данных дефектов добиваются путем правки передней балки без нагрева, так как последний вызывает изменение внутренней структуры металла и возникновение внутренних напряжений, которые могут привести к появлению трещин и излому балки.
Конструкция стенда для холодной правки балки автомобиля ГАЗ-53А должна иметь раму, на которой монтируются силовые цилиндры для устранения прогибов в вертикальной и горизонтальной плоскостях, а также — силовые цилиндры для устранения скрученности передней балки.
Цилиндры для устранения прогибов могут быть неподвижно прикреплены к раме стенда, в то время как цилиндры для устранения скрученности должны быть подвижными и перемещаться по направляющим рамы. Стенд должен быть снабжен измерительными приборами для уточнения величины прогибов и скрученности. Усилия силовых цилиндров должны быть достаточными для правки балки. Конструкция стенда должна обеспечивать безопасность работы и иметь оптимальные габаритные размеры, а также оптимальную стоимость.
4.1.1 Анализ существующих конструкций стендов
По перечисленным выше требованиям к конструкции стенда наиболее подходящими являются: стенд для холодной правки переднего моста, модель 9001, а также стенд для холодной правки переднего моста, модель 115, предназначенные для правки переднего моста автомобиля ГАЗ-51, причем модель 115 предназначена также для правки переднего моста автомобиля ЗИЛ-164А.
Из двух перечисленных моделей, модель 9001 имеет меньшую стоимость, так как имеет привод ручной, а не гидрофицированный как у модели 115. Однако стенд модели 9001 имеет более низкую производительность и нуждается в модернизации. И все же, даже после модернизации и увеличения производительности, данная модель будет иметь меньшую стоимость.
Характеристика стенда
Тип: стационарный
Привод домкратов: ручной
Грузоподъемность, кг:
среднего 14 000
крайних 4000
бокового 4000
Рисунок 4.1. Стенд для холодной правки балки переднего моста, модель 9001
Ход домкратов, мм:
среднего 330
крайних 300
бокового 300
Усилие на рукоятку домкратов, кг:
среднего 30
крайних 25
бокового 25
Габаритные размеры, мм 3618×1670×1690
Вес, кг 1512.
Данная конструкция представляет собой стенд для холодной правки балки переднего моста автомобиля ГАЗ-51. Основанием стенда является сварная станина 7 (рис. 4.1), на которой расположены крайние домкраты 2, боковой домкрат 9, средний домкрат 8. Ремонтируемую балку 4 устанавливают на опоры 3. Прогиб балки определяется угломером 5. Средний и боковой домкраты стационарные, крайние — передвижные, перемещаются по направляющим 1 и 6. Прогиб оси в горизонтальной плоскости устраняется боковым домкратом 9. Для правки оси в вертикальной плоскости служит средний домкрат 8. Для устранения скученности балки служат крайние подвижные домкраты 2.
Как уже говорилось выше, существенными недостатками данной конструкции является низкая производительность, из-за ручного привода, а также однонаправленность стенда, т. е. он рассчитан на работу только с автомобилем ГАЗ-51, автомобилем существенно устаревшей конструкции.
Усовершенствовать данную конструкцию можно, установив на данном стенде гидроили пневмопривод. Это заметно уменьшит время работы, человеческие затраты, а следовательно повысит производительность труда при незначительных капиталовложениях.
4.1.2 Предлагаемая конструкция стенда
Предлагаемая конструкция стенда (см. рисунок 4.2) выполнена на базе стенда для холодной правки балки переднего моста автомобиля ГАЗ-51, модель 9001. Особенностью конструкции стенда является установка гидропривода.
При этом ручные домкраты заменяются гидроцилиндрами. Рабочее давление в системе, равное 100 кг/см2, обеспечивается насосом, который получает вращение от электродвигателя. Подача масла на гидроцилиндры регулируется распределителем, соединенным с цилиндрами резиновым трубопроводом высокого давления.
Процесс правки аналогичен процессу правки на базовой модели, однако при этом эффективность стенда резко возрастает и снижается время правки балки.
Существенным достоинством данного стенда является возможность работы с балками передних мостов различных марок грузовых автомобилей.
Процесс правки аналогичен процессу правки на базовой модели, однако при этом эффективность стенда резко возрастает и снижается время правки балки.
Расчет и выбор элементов гидропривода модернизированного стенда (насоса, приводного электродвигателя, гидравлического бака и т. д.) выполнен в разделе 4.2.
Рисунок 4.2. Стенд для холодной правки балки переднего моста автомобиля ГАЗ-53А
1 — станина; 2 — домкрат крайний; 3 — гидравлический распределитель; 4 — домкрат боковой; 5 — опора левая; 6 — домкрат центральный; 7 — опора центральная; 8 — клапан предохранительный; 9 — гидробак; 10 — насос шестеренный; 11 — электродвигатель
4.2 Проектные расчеты
4.2.1 Выбор масляного насоса
Производительность насоса равна по [17]:
(4.1)
где Q — производительность насоса, л/мин;
d — диаметр поршня цилиндра, см;
ln — ход поршня рабочего цилиндра, определяется при кинематическом расчете проектируемого оборудования, см;
t — время рабочего хода исполнительного органа технологического оборудования, с, принимаем t=5с;
n — объемный КПД гидросистемы оборудования, n=0,8;
n — число одновременно работающих цилиндров, n=4.
Суммарная площадь поршней гидроцилиндров в зависимости от усилия по [17]:
; (4.2)
где Fп — суммарная площадь поршней цилиндров в рабочем положении, см2;
Р — усилие, прилогаемое к рабочему органу технологического оборудования, Р=24 000Н;
— рабочее давление в гидросистеме, Па, =100кг/см2=100 105Па;
мех — механический КПД цилиндра, принимаем мех=0,95.
;
т.к. .
см.
Принимаем по ГОСТ 8755–88 d = 55 мм Тогда по ГОСТ 8755–88 принимаем гидроцилиндр марки ЦС-55.
Производительность насоса равна по [18]:
л/мин.
Принимаем насос шестеренчатый по ГОСТ 8753–88: НШ-40 В.
Частота вращения вала насоса:
(4.3)
где q — теоретическая производительность насоса за 1 оборот приводного вала, см3/об., q = 32,57 см3/об.;
0 — объемный кпд насоса, 0 = 0,9.
Тогда об/мин При установке насоса высота столба рабочей жидкости под всасывающей трубкой должна быть не менее 150 мм.
4.2.2 Расчет привода масляного насоса
Требуемая мощность электродвигателя привода масляного насоса определяется по формуле:
; (4.4)
где N — мощность электродвигателя, кВт;
Р1 — давление настройки предохранительного клапана, МПа;
Q — производительность насоса, л/мин;
n — полный кпд насоса, n = 0,85.
Р1= (0,10…0,50) р.
Р1= 0,13 100 105 = 1,3 МПа Тогда кВт По данной мощности принимаем электродвигатель по ГОСТ 19 523–81 4А80АЧУЗ Его мощность: N = 1,1 кВт;
число оборотов: n = 1500 об/мин;
отклонение .
4.2.3 Расчет конструкции масляного бака
Наиболее целесообразно изготавливать баки плоской и кубической формы.
Расчетная поверхность охлаждения равна:
(2.5)
где р — давление масла в системе, кг/см2, р = 100 кг/см2;
Q — производительность насоса, л/мин, Q = 42,8 л/мин;
КС — коэффициент использования рабочего времени, КС = 0,75;
КЦ — коэффициент использования расчетной мощности за один ра-бочий цикл к расчетной мощности, КЦ =0,5;
К — коэффициент теплоотдачи от масла через стальную стенку в воздух, ккал/м2чград, К = 40 ккал/м2чград;
Т — максимально допустимая температура масла в баке. 0С, Т = 70 0С;
Т0 — температура окружающего воздуха, принимаем Т0 = 20 0С.
Тогда: м2
Принимаем бак с размерами 0,60,60,6 м.
4.2.4 Расчет трубопроводов
Диаметры всасывающих и нагнетательных трубопроводов определяются в зависимости от скорости рабочей жидкости.
Скорость рабочей жидкости в трубопроводе определяем по формуле:
(4.6)
где Q — расход жидкости, л/мин, Q = 42,8 л/мин;
d — внутренний диаметр трубопровода, мм.
Скорость не должна превышать для всасывающего трубопровода 1,5 м/с, а для нагнетательного 4…5 м/с.
Тогда .
Всасывающий трубопровод:
мм/
Принимаем по ГОСТ 8755–88 d = 25 мм;
Нагнетательный трубопровод:
мм.
Принимаем по ГОСТ 8755–88 d = 16 мм;
Толщина стенки трубы маслопровода:
(4.7)
где S — толщина стенки, мм;
доп — допустимое напряжение на разрыв, кг/см2, для резинового трубопровода доп = 80 кг/см2.
Тогда для всасывающего трубопровода:
мм.
Принимаем S = 2 мм.
Для нагнетательного трубопровода:
мм.
Принимаем S = 2 мм;
Следовательно по ГОСТ 5496–78 принимаем резиновый трубопровод:
трубка 4П252, О ГОСТ 5496–78 и трубка 4П162,0 ГОСТ 5496–78.
4.2.5 Выбор распределительного устройства
В гидросистемах технологического оборудования применяются тракторные распределители, выпускаемые согласно ГОСТ 8754–88.
Принимаем распределитель Р-75.
Таблица 4.1
Характеристика распределителя
Наименование показателя | Значение | |
Максимальная пропускная способность, л/мин | ||
Давление срабатывания предохранительного клапана, кг/см2 | ||
Рабочее даление, кг/см2 | ||
Количество золотников | ||
Таблица 4.2
Основные параметры клапанов
Клапаны | Пропускной | |||
номинальный | наибольший | наименьший | ||
При внутреннем диаметре трубопроводов ДУ, мм ДУ = 16 ДУ = 25 | ||||
4.2.6 Расчет пальца
Проводим расчет пальца-держателя крепления балки.
Рисунок 4.3. Приведенная схема расположения пальца Палец проверяем на срез:
(4.8)
где Р — усилие развиваемое цилиндром, Н, Р = 24 000 Н;
F — площадь поперечного сечения пальца, мм;
[СР] - допустимое напряжение на срез.
Материал пальца — сталь 40Х; [СР] = 120 нмм2.
Тогда мм2. (4.9)
Так как, то диаметр пальца d
мм.
Принимаем по ГОСТ 8755–88 d = 20 мм.
4.3 Основные регулировки и работа на стенде
4.3.1 Описание работы стенда, основные регулировки
Стенд работает следующим образом: масляный насос, приводимый в движение электродвигателем, создает в системе рабочее давление. При перемещении какой-либо рукоятки распределителя масло направляется в соответствующий гидроцилиндр, который, создавая необходимое усилие, воздействует на балку, закрепленную на стенде, и выправляет ее до необходимой величины.
Средний гидроцилиндр устраняет прогиб балки в вертикальной плоскости.
Боковой гидроцилиндр устраняет прогиб балки в горизонтальной плоскости.
Крайние, подвижные гидроцилиндры ликвидируют скрученность балки.
Правку балки проводят согласно показаниям угломеров, расположенных на стенде.
После правки балку проверяют на наличие трещин, которые не допускаются при эксплуатации балки.
При работе стенда не допускается закипание масла, попадание в гидросистему воды и инородных тел. В этих случаях, а также при изменении цвета и окончании срока эксплуатации масло заменяется. При выходе из строя узлов и агрегатов их ремонтируют или заменяют новыми одноименными. При истечении масла через уплотнители, последние заменяют. При падении давления проверяется работа распределителя и масляного насоса, при неисправности их заменяют. При эксплуатации стенда необходимо следить, чтобы не было перегрева электродвигателя. Так как рама стенда сварная, необходимо время от времени проводить осмотр сварных швов, при наличии трещин их заваривать.
Основными регулировками стенда являются регулировки предохранительного и перепускного клапанов.
4.3.2 Техника безопасности при работе на стенде
Перед началом работы осмотреть стенд на наличие трещин, порезов трубопровода, а также течи через уплотнения, проверить надежность соединения трубопроводов с агрегатами гидросистемы.
Осмотреть конструкцию рамы на наличие трещин сварных швов.
Произвести проверочный пуск стенда. Электродвигатель должен работать ровно, без рывков, давление в системе должно соответствовать норме рабочего давления.
Произвести проверочное последовательное включение всех гидроцилиндров. Движение штоков цилиндров должно быть без рывков, необходимый ход штоков должен обеспечиваться за установленное время.
5. Охрана труда и техника безопасности
5.1 Организация работы по охране труда и технике безопасности на АРЗ
Вся работа по охране труда и технике безопасности проводится в соответствии с планом организационно-технических мероприятий по профилактике производственного травматизма и профессиональных заболеваний.
Общее руководство работой по охране труда и технике безопасности возлагается на руководителя (директора) и главного инженера предприятия. Непосредственную работу по охране труда и технике безопасности осуществляет старший инженер (инженер) по технике безопасности, находящийся в подчинении главного инженера предприятия.
При количестве работающих менее 250 человек функции инженера по технике безопасности выполняет технический руководитель (главный инженер).
Рабочие, инженерно-технические работники и служащие могут быть допущены к самостоятельной работе только после прохождения инструктажа по технике безопасности с последующей проверкой знаний, а в необходимых случаях после курсового обучения.
Вновь принятый на предприятие административно-технический персонал должен быть ознакомлен с обязанностями и ответственностью за состояние охраны труда и техники безопасности на порученном участке работы, с действующими инструктивно-методическими материалами, директивами, приказами по охране труда, технике безопасности к производственной санитарии.
Администрация предприятия обязана организовать своевременное и качественное проведение инструктажа со всеми работающими, а также обучение основам законодательства о труде, охраны труда, техники безопасности, производственной санитарии и гигиены, противопожарной техники.
Инструктаж проводится на основе законодательства о труде, правил внутреннего трудового распорядка, правил техники безопасности, противопожарных правил, а также утвержденных инструкций.
Инструктаж рабочих безопасным приемам и методам работы проводится по следующим основным видам:
— вводный инструктаж;
— первичный инструктаж на рабочем месте;
— повторный инструктаж;
— внеплановый инструктаж.
Вводный инструктаж проводится старшим инженером (инженером) по технике безопасности (а там, где его нет — лицом, выполняющим его обязанности) со всеми вновь принимаемыми на предприятие рабочими, инженерно-техническими работниками и служащими, практикантами и учениками производственного обучения.
При проведении вводного инструктажа должны быть разъяснены:
— основные положения законодательства о труде Республии Казахстан;
— правила внутреннего трудового распорядка на предприятии;
— правила поведения на территории, в производственных и бытовых помещениях;
— значение предупредительных надписей, сигнализации и т. п.;
— особенности условий работы соответствующего участка и меры по предупреждению несчастных случаев;
— требования личной гигиены и производственной санитарии;
— порядок, нормы выдачи и правила пользования спецодеждой, спецобувью и другими средствами защиты работающих;
— порядок оформления несчастного случая на производстве;
— правила оказания доврачебной помощи пострадавшим.
При проведении вводного инструктажа каждому рабочему должна быть выдана под расписку инструкция по охране труда. Независимо от этого в цехах и участках на рабочих местах должны быть вывешены инструкции по охране труда для рабочих соответствующих профессий, утвержденные администрацией и согласованный с заводским (местным) комитетом профсоюз, если таковой имеется.
После вводного инструктажа проводится первичный инструктаж на рабочем месте.
Первичный инструктаж на рабочем месте проводится мастером или начальником участка (цеха) до начала работы со всеми вновь принятыми на предприятие рабочими, практикантами и учениками производственного обучения, а также временными и прикомандированными работниками. Инструктаж должен сопровождаться практическим показом правильных и безопасных приемов труда.
В программу первичного инструктажа на рабочем месте входит:
— общее ознакомление с технологическим процессом на данном участке производства, порядком подготовки к работе, проверке оборудования и инструмента;
— ознакомление с устройством оборудования, приспособлений, блокировок, оградительных устройств, а также с применением средств индивидуальной защиты (спецодежды, спецобуви и предохранительных приспособлений);
— ознакомление с требованиями правильной организации и содержания рабочего места;
— ознакомление с правилами техники безопасности при выполнении работ, которые должен выполнять данный рабочий индивидуально или совместно с другими рабочими.
Все рабочие, независимо от их квалификации, не реже 1 раза в 3 месяца проходят повторный инструктаж по программе первичного инструктажа на рабочем месте.
Внеплановый инструктаж проводится в случаях изменения технологического процесса, оборудования, условий работы, либо когда из-за недостаточного инструктажа имели место несчастные случаи или профессиональные заболевания, либо когда рабочими нарушались правила и инструкции по охране труда и технике безопасности.
Кроме инструктажей по технике безопасности со всеми принятыми на предприятие рабочими не позднее трех месяцев со дня поступления их на работу проводится обучение безопасным методам и приемам работ по программе, утвержденной администрацией предприятия.
После обучения и в дальнейшем ежегодно комиссией проводится проверка знания рабочими безопасных методов и приемов работ с документальным оформлением проверки.
Рабочие, занятые на работах с повышенной опасностью допускаются к самостоятельной работе только после курсового обучения по типовым программам, сдачи экзаменов в установленном порядке в соответствующих организациях и получения удостоверения на право производства работ.
Обучение инженерно-технических работников проводится на специально организованных курсах (семинарах) по программе, утвержденной администрацией предприятия, с последующей проверкой знания правил техники безопасности и выдачей удостоверения по установленной форме. Периодичность обучения и проверки знаний — один раз в год.
Все виды инструктажей (кроме вводного) оформляются записями в журнале, хранящимся у мастера, начальника участка (цеха).
5.2 Обязанности, права и ответственность административно-технического персонала Руководитель (директор) предприятия обязан [23]:
— организовать планирование организационно-технических мероприятий по совершенствованию охраны труда, техники безопасности и производственной санитарии, следить за своевременным финансированием этих мероприятий, контролировать расходование средств, ассигнованных на улучшение и оздоровление, условий труда, обеспечить выполнение соглашения по охране труда коллективного договора к комплексного плана улучшения условий, охраны труда и санитарно-оздоровительных мероприятий;
— утверждать комплексные, перспективные и годовые планы улучшения условий, охраны труда и санитарно-оздоровительных мероприятий и планы номенклатурных мероприятий по охране труда;
— организовать обучение административно-технического персонала вопросам охраны труда в соответствии с установленной программой;
— не допускать ввод в эксплуатацию вновь построенных и реконструированных предприятий, цехов и участков 6ез разрешения органов, осуществляющих государственный санитарный и технический надзор, технической инспекции труда;
— обеспечивать строгое соблюдение законодательства о труде, о рабочем времени, времени отдыха, о труде женщин и подростков;
— обеспечивать высокую культуру и организацию труда на производстве;
— обеспечивать выполнение предписаний технической инспекции труда, органов государственного надзора, предложений общественных инспекторов и комиссий охраны труда и вышестоящих организаций по вопросам охраны труда и техники безопасности;
— своевременно обеспечивать рабочих качественной спецодеждой, спецобувью и другими средствами индивидуальной защиты (очки, респираторы, диэлектрические перчатки и др). мазями, пастами, моющими веществами и мылом, а также спецпитанием (молоко, пектин и др.) в соответствии с действующими нормами;
— обеспечивать нормальную работу и использование по назначению санитарно-бытовых помещений и устройств (душевых, гардеробных, умывальных и др.);
— организовать своевременную разработку и утверждение совместно с заводским (местным) комитетом профсоюза (если таковой имеется) инструкций по охране труда для отдельных работ и профессий;
— принимать личное участие в расследовании групповых, тяжелых и смертельных несчастных случаев на производстве.
Главный инженер (технический руководитель) предприятия обязан:
— осуществлять руководство работой по охране труда, технике безопасности и производственной санитарии и контроль соблюдения всеми руководителями производственных участков предприятия норм и правил по охране труда, технике безопасности и производственной санитарии;
— разрабатывать и согласовывать с местным комитетом профсоюза (если таковой имеется) планы по дальнейшему улучшению и оздоровлению условий труда, а также осуществлять контроль выполнения этих планов;
— требовать от главного механика и руководителей участков производства своевременного устранения обнаруженных нарушений в области охраны труда и производственной санитарии, правильного содержания оборудования и инструмента;
— руководить разработкой и составлением инструкций по безопасным приемам и методам труда по профессиям и видам работ в соответствии с действующими правилами и нормами по охране труда, технике безопасности и производственной санитарии применительно к конкретным условиям производства и обеспечения всех цехов (участков) инструкциями, памятками и другими наглядными пособиями по охране труда и технике безопасности;
— организовывать и контролировать своевременное проведение всех видов инструктажей и обучение рабочих безопасным методам труда;
— обеспечивать своевременное проведение расследований несчастных случаев на производстве и оформление их актами в установленном порядке, своевременное составление отчета о пострадавших при несчастных случаях на производстве и освоении средств на мероприятия по охране труда. Выявлять причины и обстоятельства, вызывающие несчастные случаи, проводить в жизнь мероприятия, направленные на ликвидацию и предупреждение причин несчастных случаев;
— обеспечивать проведение предварительных при поступлении на работу и периодических медицинских осмотров рабочих в соответствии с действующим законодательством;
— проводить совместно с профсоюзной организацией смотры по вопросам охраны труда, техники безопасности и культуры производства, обобщать предложения рабочих по охране труда и осуществлять контроль выполнения принятых предложений;
— руководить разработкой и внедрением более совершенных средств по охране груда и технике безопасности, механизации трудоемких работ, а также улучшать санитарно-бытовые условия;
— руководить работой по обмену опытом в области охраны труда, культуры производства и технической эстетики между цехами;
— осуществлять контроль своевременной выдачи исправной спецодежды, спецобуви и других средств индивидуальной защиты, а также — стиркой и ремонтом спецодежды в сроки, устанавливаемые по согласованию с заводским (местным) комитетом профсоюза и местными органами МЧС;
— обеспечивать выполнение предписаний технической инспекции труда и предложений общественных инспекторов и комиссий по охране труда;
обеспечить своевременное выполнение организационно-технических и номенклатурных мероприятий по охране труда;
— руководить работой старшего инженера (инженера) по технике безопасности и контролировать работу кабинета (уголка) по технике безопасности;
— организовывать систематическую пропаганду безопасных и здоровых условий труда путем проведения оперативных совещаний, лекций, докладов, бесед, выпуска газет и т. д.
Главный механик (энергетик) предприятия обязан:
— обеспечить составление и выполнение плана организационно-технических мероприятий по охране труда, а также плана профилактического ремонта оборудования, средств коммуникации, работающих под давлением или электрическим напряжением установок и приборов;
— осуществлять технический надзор за состоянием зданий, сооружений, оборудования, электросиловых и осветительных сетей и установок;
— своевременно проводить испытания и осуществлять контроль правильной эксплуатации паровых котлов, приборов, сосудов, аппаратов, работающих под давлением, кранов и других грузоподъемных механизмов, абразивных кругов;
— следить за исправностью и своевременным проведением испытаний контрольной измерительной аппаратуры и средств индивидуальной защиты;
— организовать проведение работ по устройству заземлений и занулений станочного оборудования, машин, механизмов, аппаратов, приборов, а также проверку их в установленные сроки;
— контролировать техническое состояние и эффективность работы вентиляционных установок и отопительных систем;
— устранять обнаруженные неисправности и недостатки в оборудовании и механизмах, связанные с их безопасным функционированием;
— обеспечивать работающих соответствующими инструкциями по охране труда, организовать проведение инструктажа и обучения рабочих, обслуживающих паровые котлы, приборы, сосуды, аппараты работающие под давлением, краны, подъемные механизмы, а также других рабочих, подчиненных главному механику (энергетику);
— принимать участие в расследовании аварий и несчастных случаев, а также в разработке общих мероприятий по предупреждению несчастных случаев, связанных с работой на объектах, подведомственных главному механику (энергетику) .
Старший инженер (инженер) по технике безопасности предприятия обязан:
— систематически контролировать осуществление мероприятий по обеспечению здоровых и безопасных условий труда, а также по предупреждению производственного травматизма;
— проверять соблюдение руководителями цехов, участков и других подразделений действующего законодательства, приказов и распоряжений вышестоящих организаций, а также правил, норм и инструкций по охране труда, технике безопасности и производственной санитарии;
— участвовать в разработке инструкций по охране труда и контролировать их выполнение;
— подготавливать проекты приказов и распоряжений по вопросам техники безопасности;
— разрабатывать мероприятия по улучшению условий труда, составлять проекты комплексных перспективных и годовых планов по улучшению условий, охраны труда и санитарно-оздоровительных мероприятий, а также планов номенклатурных мероприятий по охране труда и контролировать ход их выполнения;
— участвовать в разработке и внедрении в производство более совершенных конструкций ограждений, предохранительных устройств, средств защиты работающих, а также внедрять предложения научно-исследовательских институтов и передовых предприятий в области охраны труда и техники безопасности;
— проверять выполнение мероприятий по оздоровлению и облегчению условий труда, предусмотренных коллективным договором;
— участвовать в комиссиях по рассмотрению проектов строительства, реконструкции, капитального ремонта зданий, сооружений, установок, аппаратов, оборудования и подготовке заключений по проектам в части соответствия их требованиям техники безопасности и производственной санитарии;
— проводить вводный инструктаж с вновь поступившими на предприятие рабочими, служащими, инженерно-техническими работниками, а также практикантами и учениками;
— осуществлять контроль за своевременным и качественным проведением первичного и других инструктажей;
— организовывать обучение инженерно-технических работников и рабочих правилам безопасности;
— участвовать в работе комиссий по проверке знаний в области техники безопасности;
— оборудовать кабинет (уголок) по технике безопасности, стенды, витрины, организовать использование плакатов, предупредительных надписей по технике безопасности;
— принимать личное участие в расследовании обстоятельств и причин несчастных случаев, происшедших на производстве, и разрабатывать мероприятия по устранению и предупреждению этих причин;
— вести учет и регистрацию несчастных случаев на производстве, проводить анализ производственного травматизма;
— составлять отчеты (по предприятию в целом) об авариях с механизмами и оборудованием, о пострадавших при несчастных случаях на производстве и освоении средств на мероприятия по охране труда;
— контролировать соблюдение установленных сроков испытания механизмов, оборудования и средств индивидуальной защиты, подлежащих испытанию;
— осуществлять контроль состояния воздушной среды, микроклимата, уровней шума, вибрации и освещенности на рабочих местах и производственных участках;
— контролировать своевременность выдачи рабочим положенных по нормам спецодежды, спецобуви и других средств индивидуальной защиты, а также их хранение, стирку и ремонт.
Начальник цеха, отдела, участка, старший мастер (мастер), механик и другие административно-технические работники, каждый на своем участке, обязаны:
— обеспечивать соблюдение рабочими норм и правил охраны труда, техники безопасности и производственной санитарии, проводить инструктаж и обучение рабочих безопасным приемам труда и осуществлять надзор за выполнением предписываемых мер предосторожности при производстве работ;
— следить за правильной эксплуатацией машин, механизмов, станков и оборудования, за обеспечением наличия и исправности оградительных приспособлений и средств защиты работающих;
— обеспечивать наличие на всех опасных местах производства на видном месте предупредительных надписей, плакатов и знаков безопасности;
— производить выбраковку инструмента не реже 1 раза в неделю, а также обеспечивать рабочих исправными инструментами;
— следить за правильным использованием и исправным состоянием одеж ды спецобуви и других средств индивидуальной защиты, а также за работой рабочих, занятых на работах с вредными условиями труда;
— принимать личное участие в расследовании обстоятельств ил причин несчастных случаев, происшедших на участке, рабочем месте, оформлять их актами, изучать причины, вызвавшие эти случаи, принимать меры для предупреждения их возникновения;
— принимать участие в составлении планов мероприятий по охране труда и технике безопасности.
Старший инженер (инженер) по технике безопасности имеет право:
— проверять в любое время состояние техники безопасности во всех цехах (отделах, производственных участках) предприятия;
— давать указания руководителям участков работ об устранении нарушений правил охраны труда, техники безопасности и производственной санитарии и улучшении условий труда, требуя их выполнения в установленные сроки. Эти указания могут быть отменены только руководителем (директором) или главным инженером предприятия;
— давать заключения по вопросам охраны труда, техники безопасности и производственной санитарии при распределении всех видов материального поощрения;
— прекращать работы и закрывать отдельные производственные участки в тех случаях, когда продолжение работ непосредственно угрожает жизни и здоровью окружающих, немедленно ставя об этом в известность главного инженера или директора предприятия;
— ставить перед руководством предприятия вопрос о привлечении к дисциплинарной ответственности вплоть до отстранения от работы рабочих и инженерно-технических работников грубо нарушающих правила техники безопасности и охраны труда;
— делать представление руководителю (директору) предприятия о поощрении работников способствовавших улучшению охраны труда, техники безопасности и производственной санитарии, а также о наложении взыскания на лиц, нарушающих требования охраны труда;
— принимать меры к изъятию оборудования, инструментов, приспособлений при несоответствии их требованиям техники безопасности.
5.3 Анализ производственного травматизма на АРЗ
Изучив, и ознакомившись с актами расследований несчастных случаев на предприятии по форме Н-1 за последние 3 года, заполним следующие таблицы.
Таблица 5.1
Распределение несчастных случаев (Н.С.) и дней нетрудоспособности (д.м.) по месяцам года
год | Пока-затели | Месяцы | Итого | Спис. число рабоч. | ||||||||||||
н.с. | ||||||||||||||||
д.с. | ||||||||||||||||
н.с. | ||||||||||||||||
д.с. | ||||||||||||||||
н.с. | ||||||||||||||||
д.с. | ||||||||||||||||
Из анализа таблицы 5.1, видно, что большая часть несчастных случаев приходится на май и декабрь месяц.
Таблица 5.2
Распределение несчастных случаев по стажу работы
Стаж работы Пострадавших | Количество пострадавших | Среднее за три года | |||
До 1 года | 1,0 | ||||
От 1года до 3лет | ; | ; | 0,7 | ||
Более 3 лет | ; | 2,0 | |||
Как следует из таблицы 5.2, большая часть несчастных случаев приходится на работающих со стажем работы более 3 — лет.
Таблица 5.3
Распределение несчастных случаев по отраслям и видам работ
Вид работ | Количество пострадавших | Среднее за 3 года | |||
Слесарные | ; | 1,33 | |||
Токарные | ; | ||||
Кузнечные | ; | ; | 0,33 | ||
сварочные | ; | ||||
Проведя анализ данных таблицы 5.3, делаем вывод, что основная часть несчастных случаев связана со слесарными работами.
Таблица 5.4
Распределение несчастных случаев по причинам
Причины | Количество пострадавших | Среднее за 3 года | |||
Неисправности машин и оборудования | ; | ; | 0,7 | ||
Отсутствие ограждений | ; | ||||
Нарушение правил техники безопасности | 1,7 | ||||
Из данных таблицы 5.4. видно, что несчастные случаи происходят в основном по причине нарушения правил техники безопасности.
Определение показателей травматизма на предприятии проведет с помощью статистического метода анализа, который заключается в определении коэффициентов: частоты и потерь рабочего времени.
Коэффициенты частоты
(5.1)
Где T — число несчастных случаев за определенный период
Pсреднее списочное число работающих за этот же период Коэффициент тяжести
(5.2)
где D — общее количество дней нетрудоспособности пострадавших за учетный период
T1 — число несчастных случаев со смертельным исходом.
Показатели потерь рабочего времени:
. (5.3)
Данные определенные по формулам 5.1, 5.2, 5.3 сводим в таблицу 5.5.
Таблица 5.5
Коэффициенты | ||||
Кч | 37,9 | 4,9 | 5,1 | |
КТ | 7,1 | |||
Кн | 269,1 | 102,0 | ||
Анализируя данные таблицы 5.5, видим, что наибольшим коэффициент частоты был в 2005 году, а коэффициент тяжести в 2007 году.
5.4 Состояние производственной санитарии на участие по ремонту мостов ГАЗ — 53А
На участке по ремонту мостов автомобиля ГАЗ — 53А предусматриваются работы по мойке, разборке, восстановлению деталей мостов, их сборке и окраске. При проектировании данного участка предусматривается вытяжная вентиляция согласно СН и П 20 405−91. Концентрация канцерогенных веществ в воздухе должна быть согласно с ГОСТ 12.10.14 — 84. «Воздух рабочей зоны» требованиям санитарно — гигиенических норм. Согласно ГОСТ 12.1.007 — 90 контроль за концентрацией вредных веществ осуществляется периодически, не реже одного раза в месяц. Естественное и искусственное освещение рабочих мест соответствует требованиям СН и П 23−05−95. Согласно требованиям на участке достаточно общего освещения. Норма освещенности 300 лк.
Помещение участка оборудовано центральным отоплением СНИП 20 405 — 91 и вентиляцией, чтобы обеспечить равномерную температуру и состояние воздушной среды. Средняя температура воздуха на участке находится в пределах 15−18 градусов С.
Относительная влажность воздуха на участке, находится в пределах 60 — 40%. Скорость движения воздуха не менее 0,1 м/с и не более 0,5 м/с.
В бытовом секторе установлены душевые и умывальники с бесперебойным обеспечением горячей и холодной водой, установлены сан-узлы (туалеты).
Уровень вибрации в помещении не должен превышать норм установленных ГОСТ 12.1.012 — 90 ССБТ «Вибрация. Общие требования безопасности».
На участке находится медицинская аптечка. Работникам выдаются средства индивидуальной защиты и предохранительные приспособления. При работе, работнику выдаются: очки, хлопчатобумажный костюм, рукавицы комбинированные, ботинки кожаные. Для обеспечения рабочих питьевой водой на участке предусмотрено устройство водопроводной колонки.
5.5 Пожарная безопасность
За пожарную безопасность на АРЗ отвечает директор. Он ежегодно приказом закрепляет ответственность за пожарную безопасность за руководителями подразделений. Разработка инструкций по пожарной безопасности, лекции, осмотр боевой готовности на предприятии проводятся инженером по охране труда.
При предприятии создана и действует добровольная пожарная дружина, члены которой обучаются методике пожаротушения. На зданиях предприятия установлена молниезащита.
На АРЗ имеются следующие средства пожаротушения: мотопомпа МП-800А; пожарные автомобили, имеются пожарные гидранты в соответствии с требованиями СниП 2.04.02−84 пожарные щиты. В комплект пожарного щита входят: две лопаты; два пожарных ведра, топор, три порошковых огнетушителя, два багра.
5.6 Инструкция по охране труда при работе на стенде холодной правки балки передней оси автомобиля ГАЗ-53А
5.6.1 Общие требования безопасности
К работе на стенде допускаются лица не моложе 18 лет, ознакомленные с устройством стенда и прошедшие инструктаж по технике безопасности и медицинскую комиссию.
Рабочий должен выполнять только ту работу, которая ему поручена мастером или начальником цеха (участка) Рабочему запрещается: касаться электропроводки или корпусов работающих электродвигателей; стоять под грузом и на пути его перемещения; курить в цехах, на рабочих местах и других местах, где применяются легковоспламеняющиеся материалы и газы. Курить разрешается только в специально отведенных местах.
Необходимость соблюдения правил внутреннего распорядка, запрещается распитие спиртных напитков. Спецодежда, спецобувь и другие средства индивидуальной защиты должны соответствовать установленным нормам. На рабочем месте необходимо иметь аптечку и разные средства пожаротушения. Необходимо знать и применять способы устранения опасностей и оказать помощь пострадавшему.
5.6.2 Требования безопасности перед началом работы
Перед началом работы необходимо: одеть и застегнуть спецодежду (ГОСТ 12.5.48 — 83 ССБТ), чтобы не было свисающих концов, волосы подобраны под головной убор. Проверить заземление двигателя, целостность привода (согласно ГОСТ 12.1.009 — 89), проверить исправность механизмов управления, трубопроводов высокого давления и их крепление, отсутствие подтеканий масла в местах соединения, комплектность средств пожаротушения, медицинские аптечки.
5.6.3 Требования безопасности во время работы
Во время работы установить опору на нужную высоту для укладки передней балки. Во время установки балки на стенд с помощью кран-балки, не находится под поднятым грузом. Перед включением стенда убедится, что пуск никому не угрожает. Производить разборку моста при выключенном электродвигателе. Детали превышающие допустимый вес снимать со стенда только с помощью кран-балки.
Во время работы запрещается: находится посторонним лицам на участке; отлучаться с рабочего места; принимать пищу на рабочем месте.
Регулировка и устранение неисправности во время работы стенда не разрешается категорически запрещается монтаж, демонтаж и ремонт элементов и узлов электрооборудования установки при наличии напряжения в сети питания.
5.6.4 Требования безопасности в конце работы
По окончании работы снять передний мост со стенда и убрать рабочее место, обеспечить электропривод и закрыть кран гидропривода. Привести в порядок рабочее место. Доложить руководителю работ о всех нарушениях, которые выявлены в процессе работы, а так же о мерах, принятых по их устранению. Спецодежду сдать в место хранения. Вымыть руки и лицо теплой водой с мылом, принять душ.
5.6.5 Требования безопасности в аварийных ситуациях
При появлении посторонних шумов, запахи гари, дыма, выявление неисправностей, искрение электрооборудования, нагрева электрооборудования и других неисправностей необходимо немедленно остановить стенд и вызвать ремонтных рабочих.
При возгарании электрической части стенда немедленно отключить электроэнергию, подать сигнал тревоги и приступить к тушению.
В случае травмирования принять меры по оказанию доврачебной помощи, позвать медицинского работника и сообщить руководителю работы.
После аварийной остановки стенд должен быть освобожден от предмета ремонта.
6. Технико-экономическая оценка проектируемого участка по ремонту балки передней оси ГАЗ-53А
Расчет всех показателей экономического обоснования проекта производим в двух вариантах.
а) исходный (существующий) вариант;
б) проектируемый.
6.1 Расчет стоимости основных производственных фондов
Стоимость основных производственных фондов определим по формуле [25]:
С0 = СЗД + СОБ + СПИ, (6.1)
где СЗД и СОБ — соответственно стоимость производственного здания и установленного оборудования, тенге.
СПИ — стоимость приборов, приспособлений, инструмента и инвентаря, цена одного наименования которых превышает 41 500 тенге.
Стоимость производственного здания:
СЗД = С’ЗД Sn, (6.2)
где С’ЗД — средняя стоимость строительно-монтажных работ, отнесенная к 1 м² производственной площади ремонтного предприятия, тен.;
Sn — производственная площадь участка, м2.
Так как проектом предусмотрено размещение участка ремонта передней оси в существующей мастерской, то:
(6.3)
где СБАЛ — балансовая стоимость ремонтной мастерской, равная 50 394 000 тенге;
Sn — производственная площадь ремонтной мастерской, равная 4360 м².
Тогда, тенге/м2.
тен.
тен.
Стоимость оборудования (СОБ) и стоимость приспособлений, приборов и ценного инструмента (СПИ) рассчитываем исходя из их перечня и балансовой стоимости единицы каждого наименования. Расчет СОБ и СПИ представим в виде таблицы 6.1.
Таблица 6.1
Стоимость оборудования, приборов, приспособлений и ценного инструмента
Наименование | Балан-совая стои-мость, тенге | Кол-во, шт. | Сумма, тенге | Установл. мощность, кВт | ||||
исходн. | проект. | исходн. | проект. | исходн. | проект. | |||
1. Стенд ОР-6361-ГОСНИТИ | 3,0 | 3,0 | ||||||
2. Машина ОМ-5300 | 4,5 | 4,5 | ||||||
3. Пресс гидравли-ческий | 5,0 | 5,0 | ||||||
4. Стенд для холодной правки балки переднего моста автомобиля ГАЗ-53А | ; | ; | ; | 1,1 | ||||
5. Верстак слесарный ОРГ-1468−01−060А-ГОСНИТИ | ; | ; | ||||||
6. Стол дефектовочный ОРГ-1468−01−090А-ГОСНИТИ | ; | ; | ||||||
ИТОГО | 12,5 | 13,6 | ||||||
Стоимость остального оборудования и оснастки не превышает 5000 тенге за единицу, поэтому из расчета опускается.
Тогда
6.2 Расчет себестоимости ремонта передней оси автомобиля ГАЗ-53А по изменяющимся статьям
Расчет программы в приведенных ремонтах произведем по формуле:
(6.4)
где АПР — количество приведенных ремонтов, шт.;
Ti — трудоемкость единицы каждого вида продукции, чел.-ч.;
Ai — программа ремонта каждого вида продукции, чел.-ч.;
— трудоемкость единицы каждого вида продукции, к которой приводится вся программа, чел.-ч.
Тогда:
Себестоимость ремонта передней оси определим по следующим статьям:
Материалы основные и вспомогательные.
Запасные части.
Транспортно-заготовительные расходы.
Основная зарплата.
Дополнительная зарплата.
Начисления соцстраху.
Электроэнергия.
Амортизация оборудования.
Текущий и капитальный ремонты.
Так как проектируемый вариант участка не предусматривает изменения технологического процесса ремонта, то изменений по статьям 1, 2 и 3 не будет, следовательно, расчеты по данным статьям можно опустить.
4. Основная заработная плата производственным рабочим (ЗР) определяется по формуле:
ЗР = ТР РСР, (6.5)
где ТР — трудоемкость ремонта передней оси, чел.-ч.;
РСР — часовая тарифная ставка среднего разряда, тен.;
Часовая тарифная ставка по среднему разряду (РСР) определяется по формуле:
(6.6)
где Р1, Р2, … Р6 — часовые тарифные ставки рабочих соответствующих разрядов по установленной тарифной сетке, тен./ч.;
М1, М2, … М6 — количество рабочих соответствующих разрядов, участвующих в ремонте передней оси, чел.
По данным РТП ОАО «Авторемонтник» Р2 = 148,5 тен./ч; Р3 = 171 тен./ч; Р4 = 197 тен./ч; Р5 = 226 тен./ч.
Трудоемкости ремонта передней оси в исходном и проектируемом вариантах равны соответственно 8,54 чел.-ч. и 5,86 чел.-ч.
тен./ч.
тен./ч.
Тогда тен.
тен.
5. Дополнительная зарплат производственным рабочим определяется в процентах к основной зарплате. Величина процента по данным РТП ОАО «Авторемонтник» составляет 14,7%. Тогда для исходного предприятия это будет 224,87тен., а для проектируемого 168,19 тен.
6. Отчисления в пенсионный фонд и подоходный налог 19% от суммы основной и дополнительной зарплат. Для исходного варианта 333,37 тен., для проектируемого 183,73 тен.
7. Затраты на силовую электроэнергию (ЭЛ) рассчитываются укрупненно по формуле:
(6.7)
где FС — установленная мощность оборудования, кВт;
КС, КОБ — средние коэффициенты соответственно спроса и использо-вания оборудования;
ЦЭ — стоимость одного кВт. ч электроэнергии, (8,39 тенге);
ФД.О. — действительный фонд времени работы оборудования, ч.;
А — производственная программа, шт.
8. Амортизационные отчисления (АО) определяются по формуле:
(6.8)
где СЗД, СОБ, СПИ — балансовая стоимость соответственно здания, оборудования, ценного инструмента и инвентаря, тен.
аЗД, аОБ, аПИ — средняя норма амортизационных отчислений соответственно здания, оборудования, ценного инструмента и инвентаря, %.
9. Отчисления на капитальный и текущий ремонт (КТр) основных производственных фондов определяются по формуле:
где РЗД, РОБ, РПИ — средняя норма отчислений на ремонты соответственно здания, оборудования, ценного инструмента и инвентаря, %.
Себестоимость ремонта передней оси по каждой статье сводим в таблицу 6.2.
Таблица 6.2
Себестоимость ремонта передней оси по изменяющимся статьям
Наименование статей | Себестоимость ремонта по существующему варианту (СУО) | Себестоимость ремонта по проектируемому варианту (СУ1) | |
Основная зарплата производственным рабочим | 1529,73 | 1144,165 | |
Дополнительная зарплата производственным рабочим | 224,87 | 168,19 | |
Отчисления в пенсионный ф. и пн | 333,37 | 183,73 | |
Электроэнергия | |||
Амортизационные отчисления | 40,13 | ||
Капитальный и текущий ремонты | 54,42 | 64,16 | |
ИТОГО: | 2253,39 | 1653,375 | |
6.3 Расчет экономической эффективности проекта
Годовая экономия от снижения себестоимости (ЭГ) равна:
ЭГ = (СУ0 — СУ1) А1, (6.9)
где СУО, СУ1 — себестоимость ремонта передней оси соответственно в исходном и проектируемом вариантах, тен.;
А1 — производственная программа по проекту, шт.
ЭГ = (2253,39 — 1653,375) 1500 = 900 022,5 тен.
Годовой экономический эффект от снижения приведенных затрат (Э) равен:
Э = [(СУ0 + ЕНКУ0) — (СУ1 + ЕНКУ1)] А1,(6.10)
где ЕН — нормативный коэффициент эффективности капиталовложений, равный 0,15 /10/;
КУ0, КУ1 — удельные капиталовложения в исходном и проектируемом вариантах.
Тогда Э = [(2253,39 + 0,15 1695,955) — (1653,375+0,15 1442,65)] 1500 = 957 015 тенге.
Срок окупаемости дополнительных капиталовложений равен:
(6.11)
где К0, К1 — полные капиталовложения, соответственно по существующему и проектируемому вариантам, тен.;
ТОК — срок окупаемости дополнительных капиталовложений, лет.
6.4 Основные технико-экономические показатели участка
На основании приведенных ранее расчетов составляем таблицы 6.3 и 6.4.
Таблица 6.3
Абсолютные показатели участка
Наименование показателя | Условные обозначения | Значение показателя для участка | ||
исходн. | проектир. | |||
1. Общая площадь участка, м2 | S0 | |||
2. Производственная площадь, м2 | Sn | |||
3. Производственная программа, шт. | А | |||
4. Количество производственных рабочих, чел. | Pn | |||
5. Количество промпроизводствен-ного персонала, чел. | ППР | |||
6. Установленная мощность токоприемников, кВт | FC | 12,5 | 13,6 | |
7. Стоимость основных производ-ственных фондов, тен. | Ф | |||
8. Полные капиталовложения в основные фонды, тен. в том числе капиталовложения в технические средства (оборудо-вание, приспособления, инвен-тарь), тен. | К0, К1 КТ | |||
9. Дополнительные капиталовложения в основные фонды, тен. | К = К1 -К0 | ; | ||
10. Себестоимость ремонта передней оси по изменяющимся статьям, тен. | СУ | 2253,39 | 1653,375 | |
Таблица 6.4
Удельные показатели участка
Наименование показателя | Формула исчисления | Значение показателя для участка | ||
исходн. | проектир. | |||
1. Коэффициент использования площади участка | ||||
2. Техническая вооруженность труда, тен./чел. | 27 006,3 | 38 848,75 | ||
3. Энерговооруженность труда, кВт/чел. | 3,13 | 3,4 | ||
4. Производительность труда, шт/чел. | ||||
5. Повышение производительности, % | ; | |||
6. Выпуск продукции на 1 м² произ-водственной площади, шт. | 12,5 | |||
7. Коэффициент эффективности дополнительных капиталовложений | ; | 0,26 | ||
8. Срок окупаемости дополнительных капиталовложений, лет. | ; | 0,52 | ||
Заключение
Основной задачей данного дипломного проекта было проектирование участка ремонта передних мостов автомобиля ГАЗ-53А сельскохозяйственного авторемонтного завода (АРЗ). В начале 90-х годов завод, в силу хорошо известных причин, производил лишь около 200 капитальных ремонтов полнокомплектных автомобилей и около 1200 ремонтов агрегатов в год, т. е. работал, практически, на 20% проектной мощности. К концу 90-х ситуация усугубилась еще больше, что, в первую очередь, объясняется обвальным старением оборудования, несовершенством используемых технологий, снижением профессионального уровня работников. Все это привело к тому, что завод оказался не в состоянии выполнять необходимый объем работ при их необходимом качестве.
В настоящее время ситуация несколько выправилась, но все отмеченные проблемы пока еще стоят достаточно остро. Все это требует безотлагательной модернизации производства, обновления парка технологического оборудования, создания новы технологических участков и линий. Именно в направление реализации указанной необходимости выполнен данный дипломный проект. В ходе его выполнения было проделано следующее:
· определена оптимальная производственная программа участка;
· изучен предмет труда (передний мост автомобиля ГАЗ-53А), составлена технологическая схема ремонта и подобрано необходимое технологическое оборудование;
· произведены расчет трудоемкости ремонта, годового объема ремонтных работ и распределение последнего по видам работ;
· определено необходимое число работающих на участке;
· осуществлена модернизация стенда для холодной правки балки автомобиля ГАЗ-53А;
· произведена оценка экономической целесообразности создания участка.
Расчеты показали, что пуск в эксплуатацию участка ремонта передних мостов автомобилей ГАЗ-53А позволяет получить годовой экономический эффект в размере 957 015 тенге. Срок окупаемости проекта составляет при этом 0,52 года.
1. Сабинин А. А. Автомобили ЗИЛ-130 и ГАЗ-53А. Учебное пособие. — М., «Высш. школа», 1973. 216 с.
2. Ламака Ф. И. Лабораторно-практические работы по устройству грузовых автомобилей. — М.: Изд-во «Академия», 2006. — 224 с.
3. Бабусенко С. М. Проектирование ремонтно-обслуживающих предирижтий.- М.: Агромпоромиздат, 1990. — 352 с.
4. Черепанов С. С. Комплексная система технического обслуживания и ремонта машин в сельском хозяйстве. — М.: 1985.
5. Смелов А. П. Курсовое и дипломное проектирование по ремонту машин. — М.: Колос, 1984.
6. Напольский Г. М. Технологическое проектирование автотранспортных предприятий и станций технического обслуживания: Уч. для вузов.-2-е изд. — М.: Транспорт, 1993.-271 с.
7. Типовые нормы времени на капитальный ремонт для специализированных предприятий. Автомобиль ГАЗ-53А. — М.: 1977.
8. Полуян А. Г. Методическое указание по составлению графика цикла восстановления (ремонта) деталей. — Зерноград, АЧИМСХ, 1983.
9. Малышев Г. А. Теория авторемонтного производства. М.: Транспорт, 1977.
10. Петров Ю. Н. Основы ремонта машин. — М.: Колос, 1972.
11. Тельков Н. Ф. Ремонт машин. — М.: Агропромиздат, 1992.
12. Левитский И. С. Организация ремонта и проектирование сельскохозяйственных ремонтных предприятий. — М.: Колос, 1977.
13. Справочник по кранам: В 2 т. Характеристики материалов и нагрузок. Основы расчета кранов, их приводов и металлических конструкций /В. И. Брауде, М. М. Гохберг, И. Е. Звягин и др.; Под общ. ред. М. М. Гохберга. — М.: Машиностроение, 1988
14. Шадрычев В. А. Основы технологии автостроения и ремонт автомобилей. — М.: Машиностроение, 1976.
15. Левитский И. С. Технология ремонта машин и оборудования. — М.: Колос, 1975.
16. Полуян А. Г. Методическое указание по обоснованию оптимального варианта рабочего места. — Зерноград, АЧИМСХ, 1983.
17. Гидравлика, гидромашины и гидроприводы: / Т. М. Башта, С. С. Руднев, Б. Б. Некрасов и др.- М.: Машиностроение, 1982. — 423с.
18. Гейер В. Г., Дулин В. С., Заря А. Н. Гидравлика и гидропривод. — М.: Недра, 1991. — 334 с.
19. Васильченко В. А. Гидравлическое оборудование мобильных машин: Справочник.-М.: Машиностроение, 1983. — 301 с
20. Свешников В. К. Станочные гидроприводы: Справочник. — М.: Машиностроение, 2008. — 640 с.
21. Курсовое проектирование деталей машин/ С. А. Чернавский, К. Н. Боков, И. М. Чернин и др. — М.: Изд-во «Альянс», 2005. — 415 с.
22. Типовые инструкции по охране труда для основных профессий и видов работ на автомобильном транспорте.- Алматы: Товарищество специалистов охраны труда Республики Казахстан, 2003. — 159 с.
23. Салов Ф. М. Охрана труда на предприятиях автотранспорта. 1991.
24. Правила пожарной безопасности в Республике Казахстан. — Алматы, 2006. — 184 с.
25. Полуян А. Г. Методическое указание по составлению графика цикла восстановления (ремонта) деталей. — Зерноград, АЧИМСХ, 1983.