Повышение качества поверхностного слоя деталей за счет совершенствования процесса комбинированного электроалмазного шлифования
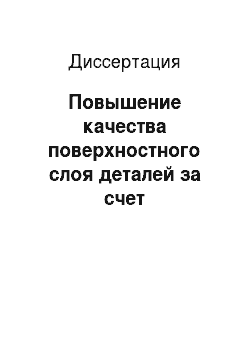
Эксплуатационные свойства и долговечность работы деталей в значительной степени зависят от качественного состояния их поверхностного слоя. Поэтому, рабочие поверхности ответственных деталей чаще всего обрабатывают шлифованием на чистовой операции. Анализ существующих методов финишной обработки деталей машин позволяет отметить, что использование шлифования повышает качество обработанной… Читать ещё >
Содержание
- Перечень условных обозначений
- Введение
- 1. Состояние вопроса повышение качества поверхностного слоя деталей за счет совершенствования процесса комбинированного электроалмазного шлифования
- 1. 1. Современные требования, предъявляемые к качеству деталей машин и их поверхностному слою
- 1. 1. 1. Поверхностный слой деталей машин и его строение
- 1. 1. 2. Оценка качества поверхностного слоя деталей машин
- 1. 2. Влияние процесса комбинированного шлифования на качество поверхностного слоя деталей
- 1. 2. 1. Контактное взаимодействие при комбинированном шлифовании
- 1. 2. 2. Тепловые процессы в зоне резания. Влияние температуры на качество поверхностного слоя детали
- 1. 2. 3. Потеря работоспособности круга и способы ее восстановления
- 1. 3. Производительность при комбинированном шлифовании деталей машин
- 1. 4. Способы совершенствования технологии комбинированного шлифования деталей машин
- 1. 1. Современные требования, предъявляемые к качеству деталей машин и их поверхностному слою
- Выводы, цель и задачи
- 2. Моделирование процесса комбинированного электроалмазного шлифования с одновременной правкой круга
- 2. 1. Зависимость удельного съема материала от режимов шлифования
- 2. 2. Зависимость напряжения и плотности тока травления от режимов шлифования
- 4. 2.3. Зависимость напряжения и плотности тока правки круга от режимов шлифования
- Выводы по второй главе
- 3. Регрессионные зависимости параметров исследуемых при комбинированном шлифовании и методы их получения
- 3. 1. Общие положения
- 3. 2. Планирование экспериментов
- 3. 3. Определение производительности при электроалмазном f шлифовании
- 3. 4. Определение шероховатости обработанной поверхности детали при комбинированном шлифовании
- 3. 5. Определение удельного расхода круга при комбинированном шлифовании
- 3. 6. Определение глубины дефектного слоя при комбинированном шлифовании
- 3. 7. Определение эффективной мощности резания при комбинированном шлифовании
- 3. 8. Определение радиальной составляющей силы резания Ру при комбинированном шлифовании
- Выводы по третьей главе
- 4. Определение рациональных режимов при комбинированном электроалмазном шлифовании
- 4. 1. Исследование шероховатости обработанной поверхности детали при комбинированном электроалмазном шлифовании
- 4. 2. Исследование глубины дефектного слоя обработанной поверхности при комбинированном электроалмазном шлифовании
- 4. 3. Исследование производительности при комбинированном электроалмазном шлифовании
- 4. 4. Исследование удельного расхода круга при комбинированном электроалмазном шлифовании
- 4. 4. 5. Исследование эффективной мощности резания при комбинированном электроалмазном шлифовании
- 4. 6. Исследование радиальной составляющей силы резания при комбинированном электроалмазном шлифовании
- 4. 7. Программа для расчета напряжения и плотности тока правки круга при комбинированном шлифовании
- Выводы по четвёртой главе
- 5. Управление процессом электроалмазного шлифования с «целью повышения качества поверхностного слоя деталей машин
- 5. 1. Способ управления процессом электроалмазного шлифования
- 5. 2. Сравнительная оценка качества поверхностного слоя деталей машин
- Выводы по пятой главе
Повышение качества поверхностного слоя деталей за счет совершенствования процесса комбинированного электроалмазного шлифования (реферат, курсовая, диплом, контрольная)
Эксплуатационные свойства и долговечность работы деталей в значительной степени зависят от качественного состояния их поверхностного слоя. Поэтому, рабочие поверхности ответственных деталей чаще всего обрабатывают шлифованием на чистовой операции. Анализ существующих методов финишной обработки деталей машин позволяет отметить, что использование шлифования повышает качество обработанной поверхности в несколько раз по таким параметрам, как шероховатость, глубина дефектного слоя, остаточные напряжения и др. В тоже время отмечается несовершенство данного метода из-за нестабильности процессов в зоне резания, что требует дополнительного изучения.
При комбинированном электроалмазном шлифовании используются круги на металлической связке значительно превосходящие по стойкости формы круги на органической и керамической связке, но из-за склонности к интенсивному засаливанию и сложности правки они не нашли широкого применения в машиностроительном производстве или используются неэффективно. Поэтому, необходимы новые, более совершенные способы восстановления работоспособности кругов, позволяющие снизить удельный расход круга и вспомогательное время, затрачиваемое на правку круга.
Диссертационная работа посвящена повышению качества поверхностного слоя деталей машин за счет совершенствования процесса комбинированного электроалмазного шлифования и создания устройств автоматического управления непрерывной правкой абразивного круга на металлической связке. Работа поддержана грантом Федерального агентства по образованию в области машиностроения А04−3.18−462.
Научная новизна работы заключается в следующем: разработаны математические модели технологического процесса комбинированного электроалмазного шлифования, позволяющие определить значения электрических параметров плотности тока правки круга inp и плотности тока травления imp, учитывающие изменения условий обработки, при которых достигается наилучшее качество обработанной поверхностиполучены эмпирические зависимости шероховатости обработанной поверхности, глубины дефектного слоя, удельного съема металла, удельного расхода круга, эффективной мощности и радиальной составляющей силы резания от режимов обработки при комбинированном электроалмазном шлифовании, на основе которых определяются рациональные режимы шлифованияпредложены способ и устройство управления процессом комбинированного электроалмазного шлифования, позволяющие автоматически поддерживать заданные условия в зоне резания, значительно повысить качество обработанной поверхности и производительность шлифовальной операции.
Практическая ценность работы: результаты исследований позволяют прогнозировать качественные показатели обработанной поверхности и обоснованно назначать режимы работы оборудования при комбинированном электроалмазном шлифованииразработанные способы (положительное решение о выдаче патента на изобретение по заявке № 2 004 112 821/02(13 632) от 26.04.2004, положительное решение о выдаче патента на изобретение по заявке № 2 004 118 239/02(19 541) от 15.06.2004) и устройства (Патент на изобретение № 2 239 525 от 10.11.2004 г., Патент на полезную модель № 42 193 от 27.11.2004 г.) позволяют автоматически поддерживать постоянную работоспособность абразивного круга на токопроводящей связке в течение всей операции, при этом достигается максимальная производительность с гарантированными качественными показателями поверхностного слоя обработанной поверхности.
В первой главе диссертационной работы приведён обзор состояния вопроса повышения качества поверхностного слоя детали путем совершенствования процесса комбинированного электроалмазного шлифования. Дана оценка современных требований, предъявляемых к качеству деталей машин, описана структура поверхностного слоя детали и рассмотрены дефекты, образующиеся на поверхности детали в процессе ее обработки при комбинированном электроалмазном шлифовании. Рассмотрены различные способы управления процессом шлифования и сделан вывод, что эта проблема остается актуальной на сегодняшний день. На основании вышеизложенного сформулированы цель и основные задачи исследования.
Во второй главе приведены теоретические модели, описывающие процессы в зоне контакта инструмент-деталь и позволяющие на основании известных законов физики определить электрические режимы обработки (плотности токов травления и правки) при комбинированном электроалмазном шлифовании, обеспечивающие наилучшее качество поверхностного слоя деталей машин.
В третьей главе описываются общие положения планирования и методика проведения экспериментов. Обоснован выбор верхнего и нижнего пределов варьируемых факторов. Шаг варьирования определен исходя из технических характеристик оборудования и требований к исследуемому процессу. В качестве нулевого уровня принято среднее значение интервала эксперимента.
На основании экспериментальных данных получены эмпирические зависимости: удельного съема металла, шероховатости обработанной поверхности, глубины дефектного слоя, удельного расхода круга, мощности и радиальной составляющей силы резания от режимов обработки при комбинированном электроалмазном шлифовании сталей 45, 9ХС, У7, Р6М5.
В четвёртой главе проводится анализ полученных зависимостей, оценивается влияние каждого фактора на выходные параметры и их значимость на технологический процесс комбинированного шлифования. Описана программа для ЭВМ по расчету электрических параметров шлифования.
Совместным решением системы из эмпирических зависимостей предлагается определение рациональных режимов резания при комбинированном электроалмазном шлифовании сталей.
В пятой главе приводится описание разработанного способа управления процессом электроалмазного шлифования и принцип работы блока управления непрерывной электрохимической правкой абразивных кругов на металлической связке. Электрическая схема блока управления позволяет автоматически стабилизировать заданную величину тока в цепи правки и при необходимости изменять ее в заданном интервале в зависимости от условий резания.
В разделе общие выводы и рекомендации предлагается использование разработанного способа управления комбинированным электроалмазным шлифованием и управляющего устройства для непрерывной электрохимической правки круга при создании нового металлорежущего оборудования. На защиту диссертационной работы выносится:
1. Теоретические модели электрических параметров, плотности тока правки круга inp и плотности тока травления imp, позволяющие определить их значения, при которых достигается наилучшее качество обработанной поверхности.
2. Эмпирические зависимости удельного съема металла Q, шероховатости обработанной поверхности Ra, глубины дефектного слоя А, удельного расхода круга q, мощности N и радиальной составляющей силы резания Ру от режимов обработки при комбинированном электроалмазном шлифовании, на основе которых определяются рациональные режимы шлифования.
3. Способ управления процессом электроалмазной обработки, позволяющий автоматически поддерживать заданные условия в зоне резания и тем самым значительно повысить качество обработанной поверхности и производительность операции шлифования.
4. Устройство для автоматического управления процессом непрерывной правки алмазного круга на металлической связке, дающее возможность снизить удельный расход круга.
ОБЩИЕ ВЫВОДЫ И РЕКОМЕНДАЦИИ.
1. Разработан способ управления процессом комбинированного электроалмазного шлифования, позволяющий обрабатывать детали машин на финишной операции с достижением гарантированного качества обработанной поверхности при минимальных затратах времени и средств (положительное решение по заявке № 2 004 112 821/02(13 632) от 26.04.2004).
2. Выведены теоретические модели электрических параметров (плотности тока правки круга inp и плотности тока травления imp), на основе которых рассчитываются значения данных параметров, при которых достигается наилучшее качество обработанной поверхности и минимальный удельный расход круга.
3. Получены эмпирические зависимости удельного съема металла Q, шероховатости обработанной поверхности Ra, глубины дефектного слоя А, удельного расхода круга q, мощности N и радиальной составляющей силы резания Ру от режимов обработки при комбинированном электроалмазном шлифовании, позволяющие обоснованно назначать режимы шлифования, при которых достигается наилучшее качество обработанной поверхности.
4. Установлено, что при комбинированном электроалмазном шлифовании углеродистых и легированных сталей можно создать условия в зоне резания, при которых процесс засаливания блокируется, и абразивный круг не теряет работоспособность во время работы, что повышает качество обработанной поверхности в 1,5.2 раза и производительность операции в 3.4 раза.
5. Разработаны устройства для автоматического управления процессом непрерывной электрохимической правки алмазного круга на металлической связке, позволяющие поддерживать постоянную работоспособность круга, снизить его удельный расход в 1,5.2,5 раза, силы и мощность резания на 30−40% в сравнении с алмазным шлифованием (патенты № 2 239 525, № 42 193).
6. На основе выполненных исследований возможно совершенствовать существующие технологии комбинированного электроалмазного шлифования и создавать новое оборудование, отличающееся расширенными технологическими возможностями, одновременно позволяющее значительно повысить качественные показатели обработанной поверхности.
7. Результаты диссертационной работы используются на: ОАО «Центральный ремонтно-механический завод», г. БратскОАО «БратскЭнер-гоСтройТранс-1» Авторемонтный завод, г. БратскОАО «Братском деревообрабатывающем заводе», г. БратскОАО «СибНИИстройдормаш» им. А. Б. Суховского, г. КрасноярскЦКБ «Геофизика», г. Красноярскв учебном процессе Братского государственного университета и Красноярского государственного технического университета на кафедрах «Технология машиностроения» для студентов, магистрантов и аспирантов.
Список литературы
- Абасав В.А. Исследование путей повышения эффективности процесса электроалмазного шлифования твёрдых сплавов: Автореф. Дис. канд. техн. наук/ В. А. Абасав. — М., 1975. — 20с.
- Антропов Л.И. Теоретическая электрохимия/ Л. И. Антропов. — М.: Высшая школа, 1969. 512с.
- Артамонов Б.А. Размерная электрическая обработка металлов/ Б. А. Артамонов, А. Л. Вишницкий, Ю. С Волков. — М.: Высшая школа, 1978.-336с.
- Баранов А.Н. Защита металлов от коррозии: Учебн. Пособие/ А. Н. Баранов, Б. Н. Михайлов. Иркутск: Изд-во ИрГТУ, 2004. — 157с.
- Белостоцкий В.Л. Изыскание условий повышения производительности алмазной заточки твердосплавного инструмента: Автореф. Дис. канд. техн. наук/ В. Л. Белостоцкий. М., 1971. — 22с.
- Бердичевский Е.Г. Смазочно-охлаждающие технологические средства для обработки материалов/ Е. Г. Бердичевский. М.: «Машиностроение», 1984.-224с.
- Бунин К.П. Металлография/ К. П. Бунин, А. А. Баранов. М.: «Металлургия», 1970.-256с.
- Бурочкин Ю.П. Исследование физических особенностей и технологических показателей электроалмазного шлифования твёрдых сплавов торцом круга: Автореф. Дис. канд. техн. наук/ Ю. П. Бурочкин. Куйбышев, 1974.-23с.
- Винарский М.С. Планирование эксперимента в технологических исследованиях/ М. С. Винарский, М. В. Лурье. Киев: «Технпса», 1975. -168с.
- Вульф A.M. Резание металлов/ A.M. Вульф. Л.: Машгиз., 1963. -428с.
- Гостев В.В. Алмазно-электрохимическое шлифование твердых сплавов/ В. В. Гостев. Киев: Вища школа, 1974. — 124 с.
- Гридин Г. Д. Исследование процесса высокочистового электрохимического шлифования сталей: Автореф. Дис. канн. техн. наук/ Г. Д. Гридин. Минск, 1970.
- Дабаин Г. Н. Исследование высокопроизводительного алмазно-электролитического шлифования твёрдых сплавов: Автореф. Дис. канд. техн. наук/ Г. Н. Дабаин Челябинск, 1980. — 25с.
- Дальский A.M. Технология конструкционных материалов/ A.M. Даль-ский, И. А. Арутюнова, Т. М. Барсукова и др.- Под ред. A.M. Дальско-го. М.: «Машиностроение», 1985. — 448с.
- Дьяконов В.П. Mathcad 8 PRO в математике, физике и Internet/ В. П. Дьяконов, И. В. Абраменкова. М.: «Нолидж», 1999. — 512с.: ил.
- Залога В.А. Исследование процесса высокопроизводительного электроалмазного шлифования инструментальных материалов кругами из АСБ: Автореф. Дис. канд. техн. наук/ В. А. Залога. Харьков, 1974. -20с.
- Захаренко И.П. Алмазно-электролитическая обработка инструмента/ И. П. Захаренко, Ю. Я. Савченко. Киев: Наук. Думка, 1978. — 224с.
- Золоторевский B.C. Механические свойства металлов: Учебник для вузов. 2-е изд/ B.C. Золоторевский. М.: «Металлургия», 1983. -352с.
- Иванский В.В. Повышение качества поверхностного слоя деталей машин путем управления параметрами термических циклов в технологических процессах комбинированной обработке: Дис. канд. техн. наук: 05.02.08/ В. В. Иванский. Новосибирск, 1996.
- К вершинам совершенства: Практическое пособие соискателям ученых степеней и ученых званий/ В. П. Горелов, А. Н. Качанов, Ю. С. Степанов, М. М. Никитин. М.: «Машиностроение — 1», 2003. — 380 с.
- Кабанов Б.Н. Электрохимия металлов и адсорбция/ Б. Н. Кабанов. —1. М.: «Химия», 1968.-462с.
- Керша Г. А. К вопросу определения величины электрохимического съема при электроабразивном шлифовании/ Г. А. Керша и др.// Реферативный журнал, ВИНИТИ. 1978. — № 11. — С. 56−59.
- Клокова Н.П. Тензорезисторы: Теория, методики расчета, разработки/ Н. П. Клокова. М.: «Машиностроение», 1990. — 224с.: ил.
- Ковалёв C.JI. Алмазное электрохимическое шлифование твёрдо-сплавных прорезных фрез: Автореф. Дис. канд. техн. наук/ C.JI. Ковалёв. Тула, 1991. — 25с.
- Козлов A.M. Повышение качества и точности цилиндрических деталей при шлифовании/ A.M. Козлов. Липецк: ЛГТУ, 2004. — 181с.
- Колесов И.М. Основы технологии машиностроения: Учеб. для маши-ностроит. спец. вузов. 3-е изд., стер./ И. М. Колесов. — М.: Высшая школа, 2001. — 591с.: ил.
- Короткое А.Н. Повышение работоспособности шлифовальных инструментов на основе эффективного использования свойств зёрен: Автореф. Дис. канд. техн. наук/ А. Н. Короткое. М., 1993. — 23с.
- Курдюков В.И. Научные основы проектирования, изготовления и эксплуатации абразивного инструмента: Дис. д-ра. техн. наук: 05.03.01/ В. И. Курдюков. Курган, 2000.
- Лоладзе Т.Н. Износ алмазов и алмазных кругов/ Т. Н. Лоладзе, Г. В. Бокучава. М.: Металлургия, 1972. — 543 с.
- Лурье Г. Б. Шлифование металлов/ Г. Б. Лурье. М.: «Машиностроение», 1969.- 172с.
- Макаров А.Д. Оптимизация процессов резания/ А. Д. Макаров. М.: «Машиностроение», 1976. —278с.: ил.
- Маталин А.А. Технология машиностроения: Учебник для машиностроительных вузов по специальности «Технология машиностроения, металлорежущие станки и инструменты"/ А. А. Маталин. Л.: „Машиностроение“. Ленингр. отд-ние, 1985. -496с.: ил.
- Мелков М.П. Гальваническое наращивание деталей машин железом/ М. П. Мелков. М.: „Лесная промышленность“, 1971. — 136с.
- Направленное формирование свойств изделий машиностроения. Под ред. д-ра техн. наук А.И. Кондакова/ А. С. Васильев, A.M. Дальский, Ю. М. Золоторевский, А. И. Кондаков. М.: „Машиностроение“, 2005. — 352с.: ил.
- Немилов Е.Ф. Справочник по электроэрозионной обработке материалов/ Е. Ф. Немилов. Л.: „Машиностроение“, 1989. — 164с.
- Никитин А.П. Вскрытие зерен алмазных кругов травлением/ А. П. Никитин, Г. И. Степанов// „Станки и инструмент“, 1969. № 8. С. 32−33.
- Охтень В.Д. Экспериментально-теоретические основы механики процесса электроалмазного шлифования магнитотвердых сплавов: Дис. канд. техн. наук/ В. Д. Охтень. Новосибирск, 1971.
- Патент № 2 215 641 РФ, МКИ 7 В24 В49/00, G01 L5/00. Приспособление для измерения малых сил при электроалмазном шлифовании/ Янюшкин А. С., Попов В. Ю., Сурьев А. А., Янпольский В. В. (РФ) -№ 2 001 116 428/28, заяв. 13.06.2001. опубл. 10.11.2003. — Бюл. № 31.
- Патент № 1 293 914 РФ, МКИ В23Н7/00. Способ автоматического регулирования режущей способности шлифовального круга электроэрозионным методом/ Р. Б. Мартиросян, Р. В. Князян, С. Р. Маркарян, P.P. Мартиросян. Опубл. 08.09.1995.
- Патент № 1 792 022 РФ, МКИ В23Н5/06. Способ контроля режущей способности и правки шлифовального круга на металлической связке/ Д. М. Алексеенко. Опубл. 30.04.1995.
- Патент № 2 014 183 РФ, МКИ В23Н7/00. Способ электроэрозионной правки алмазных кругов на металлической связке/ Ш. А. Бахтиаров. Опубл. 15.06.1994.
- Патент № 2 152 295 РФ, МКИ В24В53/00. Способ управления процессом правки шлифовального круга/ JI.B. Худобин, В. Ф. Гурьянихин, B.C. Юганов, Д. В. Куренков. Опубл. 10.07.2000.
- Патент № 2 169 656 РФ, МКИ В24В53/00. Устройство для правки шлифовального круга/ В. Г. Дампипон, Н. М. Лебедев, Б. А. Новоселов, И. П. Тютиков. Опубл. 27.06.2001.
- Пахалин Ю.А. Исследование и разработка эффективного технологического процесса профилирования и правки алмазных шлифовальных кругов электроэрозионным способом: Автореф. Дис. канд. техн. наук/ Ю. А. Пахалин. Минск, 1978. — 22с.
- Петровский Э.А. Агрегатно-модульные левитационные устройства для управления качеством при механической обработке: Дис. докт. техн. Наук: 05.02.13/ Э. А. Петровский. Красноярск, 2005. — 428с.
- Поверхностная прочность материалов при трении. Под ред. д-ра техн. наук Костецкого Б.И./ Б. И. Костецкий, И. Г. Носовский, А. К. Караулов и др. Киев: „Техшка“, 1976. — 296с.
- Подураев В.Н. Технология физико-химических методов обработки/ В. Н. Подураев. М.: „Машиностроение“, 1985. — 168с.
- Попилов Л.Я. Электрофизическая и электрохимическая обработка материалов/ Л. Я. Попилов. М.: „Машиностроение“. 1982. — 400с.
- Попов В.Ю. Определение режущей способности шлифовальных кругов через силу Ру/ В. Ю. Попов, А. А. Сурьев, В.В. Янпольский// Механики XXI веку. Межвузовская студенческая научно-техническая конференция: Сборник докладов. Братск: БрГТУ, 2001. С. 194−195.
- Попов С.А. Электроабразивная заточка режущего инструмента/ С. А. Попов, В. Л. Белостоцкий. М.: „Высшая школа“, 1988. — 175с.
- Правиков Ю.М. Повышение эффективности операций шлифования путём снижения засаливания рабочей поверхности шлифовальногокруга (на примере алюминия): Автореф. Дис. канд. техн. наук/ Ю. М. Правиков. Саратов, 1983. — 24с.
- Пряхин Н.П. Определение доли механического резания при электрохимическом шлифовании/ Н.П. Пряхин// Станки и инструмент, 1968. -№ 7. С. 34−36.
- Свидет. об офиц. Регистр, программы для ЭВМ. № 2 004 611 425 (РФ). Расчет напряжения и плотности тока правки в электрической цепи при комбинированном шлифовании (Electrode v. 1.0)/ А. С. Янюшкин, А. А. Сурьев, Е.А. Слепенко- Зарегистр. Роспатент 07.06.2004.
- Семенов А.П. Схватывание металлов/ А. П. Семенов. М., 1958. -280с.
- Семко М.Ф. Высокопроизводительное электроалмазное шлифование инструментальных материалов/ М. Ф. Семко, Ю. Н. Внуков, А. И. Грабченко и др. — Киев: „Вища школа“, 1979. 232с.
- Скрипченко Ю.С. Топография алмазного круга и её влияние на процесс формирования качества поверхности: Автореф. Дис. канд. техн. наук/ Ю. С. Скрипченко. Минск, 1984. — 25с.
- Соколов В.О. Исследование точности профилирования и правки ал-мазноабразивных инструментов на металлических связках электроэрозионным методом: Автореф. Дис. канд. техн. наук/ В. О. Соколов. -Минск, 1982.-26с.
- Степанов Ю.С. Исследование алмазоносного слоя кругов на металлической связке при обработке твердых сплавов различными методами/ Ю. С. Степанов, А.С. Янюшкин// Известия ОрелГТУ: Научный журнал. Серия „Машиностроение, приборостроение“, 2003. № 1−2. С. 28.
- Студенский Е.И. Электроалмазное шлифование/ Е. И. Студенский,
- B.И. Богатырев, Н. Б. Кадышев. — М.: „Машиностроение“, 1971. — 81с.
- Сурьев А.А. Влияние формы катода на процесс электрохимической правки абразивного круга/ А. А. Сурьев, А.С. Янюшкин// Труды Братского государственного технического университета. Том 2. -Братск: ГОУВПО „БрГТУ“, 2004. С. 91−95.
- Суслов А.Г. Научные основы технологии машиностроения/ А. Г. Суслов, A.M. Дальский. М.: „Машиностроение“, 2002. — 684с.: ил.
- Съянов С.Ю. Технологическое обеспечение качества поверхностного слоя деталей при электроэрозионной обработке: Дис. канд. техн. наук/ С. Ю. Съянов. Брянск, 2002.
- Танкиева Т.А. Управление показателями качества поверхности при комбинированных технологических воздействиях: Дис. канд. техн. наук/ Т. А. Танкиева. Тула, 2002.
- Тарахнов Н.С. Исследование режущих свойств алмазных кругов на металлических связках при электролитическом шлифовании безвольфрамовых твёрдых сплавов: Автореф. Дис. канд. техн. наук/ Н. С. Тарахнов. М., 1978. — 22с.
- Тензометрия в машиностроении. Справочное пособие/ Под ред. канд. техн. наук Р. А. Макарова. М.: „Машиностроение“, 1975. — 288с.: ил.
- Технологические основы управления качеством машин/ А. С. Васильев, A.M. Дальский, С. А. Клименко и др. М.: „Машиностроение“, 2003.-256с.: ил.
- Технология и экономика электрохимической обработки/ Под ред. Ф. В. Седыкина. М.: „Машиностроение“, 1980. — 192с.
- Технология машиностроения: В 2 т. Т. 1. Основы технологии машиностроения: Учебник для вузов /В.М. Бурцев, А. С. Васильев, A.M. Дальский и др.- Под ред. A.M. Дальского. — 2-е изд., стереотип. — М.: Изд-во МГТУ им. Н. Э. Баумана, 2001. 564с. ил.
- Технология металлов/ Б. В. Кнорозов, Л. Ф. Усова, А. В. Третьяков и др. М.: „Металлургия“, 1978. — 880с.
- Труды Уфимского авиационного института им. Орджоникидзе. Выпуск XIX. Серия „Вопросы оптимизации процесса резания металлов“. -Уфа, 1971.- 184с.
- Турчак Л.И. Основы численных методов: Учебное пособие. — 2-е изд., перераб. и доп/ Л. И. Турчак, П. В. Плотников. — М.: ФИЗМАТЛИТ, 2003.-304с.
- Узунян М.Д. Высокопроизводительное шлифование безвольфрамовых твердых сплавов/ М. Д. Узунян, Ю. С. Краснощек. М.: „Машиностроение“, 1988. — 80с.: ил. — (Новости технологии).
- Уманский Я.С. Кристаллография, рентгенография и электронная микроскопия/ Я. С. Уманский, Ю. А. Скаков, А. Н. Иванов, Л. Н. Расторгуев. М.: „Металлургия“, 1982. — 632с.
- Флид М.Д. Исследование методов правки алмазных кругов и кругов из эльбора/ М.Д. Флид// „Станки и инструмент“. М.: „Машиностроение“, 1974. — вып. 12. С. 3 — 10.
- Худобин Л.В. Исследование процесса шлифования с целью повышения его эффективности: Дис. докт. техн. наук/ Л. В. Худобин. — М., 1969.
- Чеповецкий И.Х. Механика контактного взаимодействия при алмазной обработке/ И. Х. Чеповецкий. Киев: Наукова думка, 1978. — 228 с.
- Штремель М.А. Прочность сплавов. 4.1. Дефекты решетки. Учебное пособие для вузов/ М. А. Штремель. М.: „Металлургия“, 1982. — 280с.
- Щербак М.В. Основы теории и практики электрохимической обработки металлов и сплавов/ М. В. Щербак, М. А. Толстая, А.П. Аниси-мов, В. Х. Постаногов. М.: „Машиностроение“, 1981. — 263с.
- Яковенко Л.Д. Электроалмазное шлифование и заточка металлорежущих инструментов/ Л. Д. Яковенко. Львов: Каменяр, 1971. — 64с.
- Янюшкин А.С. Влияние контактных процессов при шлифовании на качество машиностроительной продукции/ А. С. Янюшкин, Н.Р. Лосева// Пути повышения качества машиностроительной продукции. Сборник докладов НТК. Саранск, 1989. — С. 31−32.
- Янюшкин А.С. Заточка инструментов методом двойного травления/ А.С. Янюшкин// Теория трения, смазки и обрабатываемости металлов. Чебоксары: ЧТУ, 1981. — С. 85 — 87.
- Янюшкин А.С. Исследование засаливания алмазных кругов на металлической связке/ А.С. Янюшкин// Справочник. Инженерный журнал, 2003.-№ 7.-С. 15−18.
- Янюшкин А.С. Исследование поверхностного слоя алмазных кругов на металлической связке при различных методах заточки/ А.С. Янюшкин// Теория трения, смазки и обрабатываемости металлов. — Чебоксары, 1982. С. 56−59.
- Янюшкин А.С. Исследование силы Ру при шлифовании методом двойного травления/ А. С. Янюшкин, В. Ю. Попов, А.А. Сурьев// Новые материалы и технологии в машиностроении. Сборник научных трудов. Выпуск 1. Брянск, 2002. С. 83−86.
- Янюшкин А.С. Конструкция катода для непрерывной правки шлифовального круга/ А. С. Янюшкин, В. Ю. Попов, Р.А. Янюшкин// XXI
- НТК БрГТУ: Материалы конференции. Братск: БрГТУ, 2000. С. 166 — 167.
- Янюшкин А.С. Контактное взаимодействие при комбинированном электроалмазном затачивании твердосплавных инструментов: Дис. докт. техн. наук/ А. С. Янюшкин. Иркутск, 2004.
- Янюшкин А.С. Контактные процессы при электроалмазном шлифовании/ А. С. Янюшкин, B.C. Шоркин. М.: „Машиностроение-1“, 2004.-230с. Ил
- Янюшкин А.С. Модернизация оборудования под процессы электроалмазной обработки/ А. С. Янюшкин, В. Ю. Попов, Р. А. Янюшкин // XXI НТК БрГТУ: Материалы конференции. Братск: БрГТУ, 2000. С. 168- 170.
- Янюшкин А.С. Повышение качества твёрдосплавного инструмента путём совершенствования процесса электроалмазного затачивания: Дис. канд. техн. Наук/ А. С. Янюшкин. Чебоксары, 1984. — 124с.
- Янюшкин А.С. Проблемы и решения количественной оценки процесса засаливания шлифовальных кругов на металлической связке/ А. С. Янюшкин, B.C. Шоркин// Справочник. Инженерный журнал, 2004. -№ 5.-С. 56−62.
- Янюшкин А.С. Роль адгезии и диффузии в процессе засаливания алмазных кругов на металлической связке/ А. С. Янюшкин, B.C. Шоркин// Справочник. Инженерный журнал, 2004. № 7. — С. 32−40.
- Янюшкин А.С. Технология алмазной обработки неэлектропроводных материалов/ А. С. Янюшкин, JI.A. Мамаев, А. А. Сурьев, С.П. Ереско// Горные машины и автоматика, 2003. -№ 11. С. 43−46.
- Янюшкин А.С. Технология комбинированного электроалмазного затачивания твердосплавных инструментов/ А. С. Янюшкин. М.: „Машиностроение-1“, 2003. — 242с. ил.
- Янюшкин А.С. Шероховатость поверхности после шлифования по методу двойного травления/ А. С. Янюшкин, В.Ю. Попов// Объединенный научный журнал. М.: Тезарус, 2002. — № 21. — С. 65−67.
- Янюшкин А.С. Электроалмазное затачивание твердосплавных инструментов/ А. С. Янюшкин, А. А. Сурьев, С.П. Ереско// Труды Братского государственного технического университета. — Том 2. — Братск: ГОУВПО „БрГТУ“, 2003. С. 100−111.
- Ящерицын П.И. Электроэрозионная правка алмазно-абразивных инструментов/ П. И. Ящерицын, В. Д. Дорофеев, Ю. А. Пахалин. Минск: „Наука и техника“, 1981. — 232с.
- Herridge T.W. Expansion of De Beers industrial diamond centre of Shannon. Mach. And Prod. Eng., 1971, vol. 119, № 3085, p. 922−927.
- Reinhart H., Gruenwald W. Zum elektrolytischen Abtrag von Harmetallen mit Diamantschlifsheiben. Werkstatt und Betrieb, 1962, № 4 (95), p. 212−218.
- Повышение качества поверхностного слоя деталей за счет совершенствования комбинированного электроалмазного шлифования» научный руководитель д.т.н., профессор А.С. Янюшкин
- Настоящим актом подтверждается, что результаты диссертационной работы А. А. Сурьева внедрены при шлифовании деталей машин из закаленных сталей, а именно:
- Устройство для комбинированной электроалмазной обработки с непрерывной правкой круга (патент № 2 239 525).
- Устройство для автоматического управления процессом непрерывной электрохимической правки абразивного круга на металлической связке.
- Программа для ЭВМ «Electrode v. 1.0″ (Свид. № 2 004 611 425 РФ) для расчета напряжения и плотности тока правки круга в электрической цепи при комбинированном шлифовании.
- Использование программы для ЭВМ „Electrode v. 1.0″ снижает время расчета режимов резания при комбинированном электроалмазном шлифовании в 3−4 раза и позволяет определить плотность тока правки при минимальном удельном расходе круга.
- Открытое акционерное общество „БратскЭнергоСтройТранс 1″ Авторемонтный завод
- Почтовый адрес: 665 709, г. Братск, 9 а/я 255 Тел. 36−30−87, 36−30−82, гл.бух. 36−32−701. ГлавныйрЩЖ^АЮ:
- Х<�БЭСТ-1″ АРЗ Щ: В. В. Жданкин HJ 2004 г. 1. СПРАВКА
- Об использовании результатов диссертационной работы А.А. Сурьева
- Повышение качества поверхностного слоя деталей за счет совершенствования комбинированного электроалмазного шлифования“ научный руководитель д.т.н., профессор А.С. Янюшкин
- Гл. технолог ОАО „БЭСМ“ АРЗ1. УТВЕРЖДАЮ1. УТВЕРЖДАЮ
- Главный инженер Братского деревообрабатывающего завода А.В. ОдинцовiiTn^^m^li 2002 г. технический Акдцширмки СДАЧИ НИР
- Годовой экономический эффект на линии сращивания древесины прииспользовании 2-х комплектов сложноспрофильных фрез составляетболее 120 тысяч рублей.
- Пре аказчика: Представители Исполнителя:1. Н.В. Жарова1. А.В. Турков1. А.С. Янюшкин1. Hti^Zr В.В. Янпольский1. А.В. Платицын1. А А- сУРьев1. Российская Федерацияsg ОАО „СибНИИстройдормаш“
- СИБНИИСДМ им. А.Б. Суховского
- Юридический адрес: 660 079 Красноярск ИНН: 24 640 594 195ул. 60 лет Октября, д. 105 Р/с 40 702 810 200 600 002 560 в Красноярском филиале
- Для писем: 660 079, 60 лет Октября, д. 105 ОКБ „Банк Москвы“, г. Красноярск
- Телефон: (8−3912)36−33−06, факс (8−3912)36−41−56 к/с 30 101 810 900 000 002 048, БИК 40 407 967 ОКПОe-mail: Sibniisdmmaijjii 240 980 ОКОНХ 95 130,14511,14 512,149411. Исх. №г. Красноярск
- УТВЕРЖДАЮ“ ьный директор тройдормаш» В Л. Шустов 2005 г. 1. Акт внедрениярезультатов научно-исследовательской работы кафедры «Технология машиностроения» ГОУВГЮ «Братский государственный университет»
- Зам. директора по научной работе, к.т.н. доцент1. В.Г. Жубрии
- ФЕДЕРАЛЬНОЕ АГЕНТСТВО ПО ОБРАЗОВАНИЮ
- ГОСУДАРСТВЕННОЕ ОБРАЗОВАТЕЛЬНОЕ УЧРЕЖДЕНИЕ ВЫСШЕГО ПРОФЕССИОНАЛЬНОГО ОБРАЗОВАНИЯ
- Декан механического факультета к.т.н., профессор1. Г. В. Голованов
- Генеральный директор-Главный конекандидат технических наук1. А.С. Дегтерев1. Утверждаю:
- Первый проректор шсноярского государственногос т
- В.М. Журавлев s г2*- «• 4 rM’ri^V^i>Я // 2005ГЧ1. АКТ
- О внедрении результатов научных исследований в учебный процесс1. А.А. Сурьева
- Заведующий кафедрой «Технология машиностроения» к.т.н., доцент1. Ю.И. Гордеев
- ФЕДЕРАЛЬНОЕ АГЕНТСТВО ПО ОБРАЗОВАНИЮ
- ГОСУДАРСТВЕННОЕ ОБРАЗОВАТЕЛЬНОЕ УЧРЕЖДЕНИЕ ВЫСШЕГО ПРОФЕССИОНАЛЬНОГО ОБРАЗОВАНИЯ
- ФЕДЕРАЛЬНОЕ АГЕНТСТВО ПО ОБРАЗОВАНИЮ
- ГОСУДАРСТВЕННОЕ ОБРАЗОВАТЕЛЬНОЕ УЧРЕЖДЕНИЕ ВЫСШЕГО ПРОФЕССИОНАЛЬНОГО ОБРАЗОВАНИЯ
- БРАТСКИЙ ГОСУДАРСТВЕННЫЙ УНИВЕРСИТЕТ"665 709, г. Братск, ул. Макаренко, 40. ГОУ ВПО «БрГУ» Тел.: (395−3) 33−20−08 Факс- (194) 33−20−08 http://www.brstu.ru E-Mail: [email protected]. Л"1. На Лаот1. Г П1. СПРАВКА
- Работа в составе экспозиции БрГУ была отмечена 3-мя дипломами и 3-мя золотыми медалями Международного выставочного комплекса Сибэкспоцентра.
- Проректор по на- д.т.н., профессор-
- Начальник УНИД тел. (395−3) 325−3251. П. М. Огар Г. Б. Городецкий1. ПШ* и Ш D1. П? D О Н?1. U!•(I1. И if? 3ш ап1. И vnш шв