Обеспечение качества ремонта унифицированных соединений сельскохозяйственной техники методами расчета точностных параметров
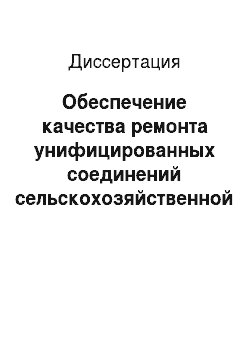
Результаты исследований реализованы в виде монографии и методических рекомендации «Методика расчета и выбора посадок неподвижных соединений при ремонте сельскохозяйственной техники», «Методика расчета и выбора посадок колец подшипников качения при ремонте сельскохозяйственной техники», рассмотренных и одобренных Научно-техническим советом департамента технической политики Минсельхоза России… Читать ещё >
Содержание
- Глава 1. СОСТОЯНИЕ ВОПРОСА И ЗАДА&trade- ИССЛЕДОВАНИЙ
1.1. Современные организационные, технические и экономические аспекты состояния сельскохозяйственной техники в России. 1.2. Технологические и точностные методы обеспечения долговечности и безотказности деталей,-сборочных единиц и агрегатов при-ремонте сельскохозяйственной техники.
1.2.1. Анализ методов выбора рациональных способов восстановления-элементов деталей.
1.2.2. Особенности нормирования трчности деталей и соединений при ремонте сельскохозяйственной техники.
1.3. Анализ существующих методов расчета точности геометрических параметров.
1.3.1. Исторические аспекты развития теорий точности и взаимозаменяемости.
1.3.1.1. Общая история развития.
1.3.1.2. Развитие методологии взаимозаменяемости.
I при ремонте сельскохозяйственной техники.
1.3.2. Методология решения задач по учению о точности.
1.3.3. Принципы выбора допусков и посадок.
1.3.4. Анализ методов расчета точности геометрических параметров подвижных соединений.
1.3.4.1. Классификация и эксплуатационные показатели работы -подвижных соединений.
1.3.4.2. Методы расчета.
1.3.4.3. Способы повышения долговечности подвижных соединений с помощью корректировки точности геометрических параметров.
1.3.5. Анализ существующих методов расчета точности геометрических параметров неподвижных соединений.
1.3.5.1. Классификация неподвижных соединений.
1.3.5.2. Анализ методов расчета и выбора посадок с натягом. 1.3.5.3. Методика расчета длительной прочности соединений с натягом.
1.3.5.4. Характеристика и расчет неподвижных соединений, имеющих посадки с зазором или переходные.
1.3.6. Анализ методов расчета точности геометрических параметров соединений колец подшипников качения.
1.3.6.1. Особенности нормирования точности колец подшипников качения и сопрягаемых с ними поверхностей.
1.3.6.2. Анализ методов расчета и выбора посадок циркуляционно-нагруженных колец подшипников качения.
1.3.6.3. Анализ методов расчета и выбора посадок местно-нагруженных колец подшипников качения.
1.3.6.4. Анализ методов расчета и выбора посадок колебательно-нагруженных колец подшипников качения.
1.4. Выводы, цели и задачи исследований.
Глава 2. ТЕОРЕТИЧЕСКИЕ ИССЛЕДОВАНИЯ В ОБЛАСТИ РАСЧЕТА ТОЧНОСТНЫХ ПАРАМЕТРОВ СОЕДИНЕНИЙ 81 2.1. Совершенствование теории точности изготовления и восстановления элементов соединений.
2.1.1. Применение теории надежности для определения точностных параметров соединения и его элементов.
2.1.1.1. Модели отказов машин.
2.1.1.2. Определение конструктивного допуска посадки теоретико-вероятностным методом расчета с учетом долговечности и ВБР при отказе по одному пределу.
2.1.1.3. Функции процесса старения. Относительная стойкость соединения и конструктивный допуск посадки.
2.1.1.4. Определение конструктивного допуска посадки теоретико-вероятностным методом расчета с учетом долговечности и ВБР при отказе по двум пределам.
2.1.2. Использование вероятностного сочетания зон рассеяния сопрягаемых деталей для повышения долговечности соединений
2.1.3. Использование вероятностного сочетания зон рассеяния сопрягаемых деталей для снижения стоимости обработки элементов соединений.
2.1.4. Технико-экономическая модель оптимизации стоимости восстановления (изготовления) и обработки деталей соединения на заданный ресурс с учетом точностных параметров.
2.1.4.1. Модель оптимизации стоимости ремонта соединения при восстановлении двух деталей на заданный ресурс.
2.1.4.2. Модель оптимизации стоимости ремонта соединения при восстановлении одной детали на заданный ресурс.
2.1.4.3. Модель оптимизации стоимости ремонта сборочной единицы или агрегата при восстановлении соединений на оптимальный ресурс
2.1.4.4. Особенности применения моделей.
2.1.5. Способ сборки методом процентной взаимозаменяемости.
2.2. Разработка и совершенствование теоретических методик расчета точностных параметров соединений сельскохозяйственной техники.
2.2.1. Разработка методики определения параметров предельного состояния соединения «вал — уплотнение».
2.2.2. Разработка методики определения предельных натягов и зазоров вал — втулка".
2.2.3. Разработка методики расчета и выбора посадок колец подшипников.
2.2.3.1. Цели и задачи методики.
2.2.3.2. Выбор посадки местно-нагруженного кольца.
2.2.3.3. Расчет и выбор посадки циркуляционно-нагруженного кольца.
2.2.3.4. Особенности расчета и выбора посадок колец конических подшипников качения при ремонте сельскохозяйственной техники.
2.3. Выводы.
Глава 3. МЕТОДЫ И СРЕДСТВА ЭКСПЕРИМЕНТАЛЬНЫХ ИССЛЕДОВАНИЙ.
3.1. Методы и средства экспериментальных исследований при анализе точности и надежности соединений «вал — уплотнение»
3.1.1. Методы и средства измерений отклонений и износа элементов соединения.
3.1.2. Методы и средства исследования динамики изнашивания соединения «вал — уплотнение».
3.1.3. Методики испытаний.
3:1.3.1. Методика испытаний с целью определения параметров предельного состояния соединения «вал — уплотнение».
3.1.3.2. Методика испытаний на износостойкость соединения вал — уплотнение".
3.1.3.3. Методика эксплуатационных испытаний.
3.1.3.4. Методика планирования и оценки результатов при многофакторном эксперименте.
3.1.5. Методика построения динамики и определения функции изнашивания.
3.2. Методы и средства экспериментальных исследований при анализе точности и надежности соединений «вал — втулка». 153 3.2.1. Методы и средства измерений отклонений и износа элементов соединения.
3.2.2. Методы и средства исследования динамики изнашивания соединения «вал — втулка».
3.3. Методы и средства экспериментальных исследований при анализе точности и надежности соединений колец подшипников качения.
3.3.1. Методы и средства измерений радиального зазора в подшипниках.
3.3.2. Методы и средства измерений отклонений и износа элементов соединений.
3.3.3. Методы и средства исследования динамики изнашивания соединений колец подшипников качения.
3.3.4. Устройство и принцип действия стенда.
3.3.5. Методика проведения стендовых испытаний с целью определения параметров предельного состояния соединения «внутреннее кольцо — вал».
3.3.5.1. Испытания радиальных шарикоподшипников.
3.3.5.2. Испытания радиально — упорных роликоподшипников.
3.3.6. Методика проведения эксплуатационных испытаний.
3.4. Выводы.
Глава 4. РЕЗУЛЬТАТЫ ИССЛЕДОВАНИЙ И ИХ АНАЛИЗ.
4.1. Результаты исследований и анализ соединений вал — уплотнение".
4.1.1. Анализ соединения и его элементов.
4.1.1.1. Классификация уплотнительных устройств, применяемых в сельскохозяйственной технике.
4.1.1.2. Основные характеристики соединения и его элементов 172 4.1.1.3: Анализ надежности и условий работы соединений «вал — уплотнение».
4.1.1.4. Способы восстановления и обработки элементов соединения.
4.1.1.5. Итоги анализа.
4.1.2. Исследования износа, износостойкости и герметичности соединений «вал — уплотнение».
4.1.2.1. Исследование износа соединения и его элементов.
4.1.2.2. Результаты исследования динамики изнашивания соединения вал — уплотнение".
4.1.2.3. Определение параметров предельного состояния соединения «вал — уплотнение».
4.1.3. Использование вероятностного сочетания зон рассеяния сопрягаемых деталей для повышения долговечности соединений
4.1.4. Разработка системы ремонтных размеров вала и методики подбора манжет.
4.1.5. Исследование влияния точностных и технологических параметров соединения «вал — уплотнение» на долговечность.
4.1.6. Разработка приспособления для дефектации, сортировки и контроля внутреннего диаметра манжет.
4.1.7. Выводы.
4.2. Анализ и результаты исследований соединений «вал — втулка»
4.2.1″. Анализ соединения и его элементов.
4.2.1.1. Нормирование точности соединений.
4.2.1.2. Анализ надежности и условий работы соединений «вал — втулка»
4.2.1.3. Способы восстановления и обработки элементов соединения.
4.2.1.4. Итоги анализа.
4.2.2. Исследования износа соединений «вал — втулка».
4.2.2.1. Исследования износа соединений «вал — втулка звездочки».
4.2.2.2. Исследования износа соединений «вал — втулка шестерни».
4.2.3. Апробация методики определения параметров предельного состояния на соединениях «вал — втулка».
4.2.4. Методика и результаты исследования фактического смятия шероховатости поверхностей в соединении «вал — втулка» при многократной разборке-сборке.
4.2.5. Результаты исследования динамики изнашивания соединения вал — втулка".
4.2.6. Использование вероятностного сочетания зон рассеяния сопрягаемых деталей для снижения стоимости обработки элементов соединений.
4.2.7. Применение процентной взаимозаменяемости.
4.2.8. Исследование влияния точностных и технологических параметров на долговечность.
4.2.9. Выводы.
4.3. Оптимизация норм взаимозаменяемости соединений колец подшипников качения.
4.3.1. Анализ соединения и его элементов.
4.3Л.1. Нормирование точности соединений.
4.3.1.2. Анализ надежности и условий работы соединений колец подшипников качения.
4.3.1.3. Способы восстановления и обработки элементов соединений.
4.3.1.4. Итоги анализа.
4.3.2. Исследования износа соединений колец подшипников.
4.3.2.1. Исследования износа соединений «вал — внутреннее кольцо».
4.3.2.2. Исследования износа соединений «наружное кольцо — корпус»
4.3.3. Апробация методики расчета и выбора посадок колец подшипников качения.
4.3.4. Результаты стендовых испытаний и их анализ.
4.3.4.1. Определение взаимосвязи параметров предельного состояния посадки для радиальных шарикоподшипников.
4.3.4.2. Определение взаимосвязи параметров предельного состояния посадки-для радиально — упорных роликоподшипников.240*
4.3.4.3. Результаты исследования динамики изнашивания соединений колец подшипников качения.
4.3.5. Исследование влияния точностных и технологических параметров соединения «вал — втулка» на долговеность.
4.3.6. Выводы.
Глава 5. ПРАКТИЧЕСКАЯ РЕАЛИЗАЦИЯ И ЭКОНОМИЧЕСКАЯ ЭФФЕКТИВНОСТЬ РЕЗУЛЬТАТОВ ИССЛЕДОВАНИЙ
5.1. Практическая реализация результатов исследований.
5.1.1. Результаты эксплуатационных испытаний.
5.1.2. Внедрение и производственная проверка результатов исследований.
5.1.3. Внедрение методик расчета точностных параметров.
5.2. Оценка экономической эффективности.
5.2.1. Существующие методики расчета.
5.2.2. Основные положения Методики
5.2.3. Расчет экономической эффективности от внедрения технологического процесса восстановления валов соединения «вал — уплотнение».
5.2.4. Расчет экономической эффективности от внедрения технологического процесса восстановления валов соединения «вал — подшипник качения».
5.2.5. Выводы.
Обеспечение качества ремонта унифицированных соединений сельскохозяйственной техники методами расчета точностных параметров (реферат, курсовая, диплом, контрольная)
Возрождение российской экономики немыслимо без подъема сельскохозяйственного производства, которое зависит от качества применяемой техники.
Повышение качества ремонта сельскохозяйственных машин, их надежности и долговечности — одно из важных направлений технического прогресса. Соблюдение норм точности геометрических параметров деталей, соединений, сборочных единиц, агрегатов — необходимые факторы обеспечения качества.
Низкая надежность отечественной сельскохозяйственной техники вынуждает сельхозпроизводителей приобретать лишние машины, покупать большое количество запасных частей, затрачивать средства на внеочередной ремонт и иметь потери от простоя техники. Это отрицательно сказывается на себестоимости сельскохозяйственной продукции.
Из отчетов ЦМИС Минсельхоза России за последние годы видно, что сельскохозяйственная техника в свыше 90% случаев изготавливается с нарушениями технических условий, среди которых несоблюдение допусков превышает 15.20%. Анализ технической документации на изготовление и ремонт этой техники показал, что допуски и посадки для большинства соединений не рассчитываются для конкретных параметров функционирования, а назначаются по методам прецедентов и подобия. Универсальных расчетных методик либо не существует, либо они недостаточно совершенны и не имеют широкого распространения.
Ресурс отремонтированной сельскохозяйственной техники составляет 40.80% от ресурса новой. Если не исследованы точностные параметры соединений, то использование современных методов восстановления не приведет к значительному повышению надежности. Таким образом, обеспечение качества ремонта неразрывно связано с применением научно обоснованных норм точности соединений, сборочных единиц и агрегатов.
В период эксплуатации машины соединения, сборочные единицы и агрегаты приходится ремонтировать неоднократно. Надежность машины возрастет, если технологические процессы, применяемые при ремонте, будут находиться на уровне основного производства или выше его по двум главным параметрам: а) обеспечению долговечности путем повышения износостойкости поверхностейб) применению научно обоснованных норм точности изделий.
Научная деятельность, посвященная изучению вопросов обеспечения заданнойточностигеометрических^ параметров изделий (деталей", соединений, узлов, агрегатов, комплексов), имеет два взаимоувязанных направления — теория точности и взаимозаменяемость.
При проектировании и ремонте сельскохозяйственной техники нужно совмещать прогрессивные способы восстановления в сочетании с научно обоснованными нормами точности и взаимозаменяемости.
Рассмотрим термин «Взаимозаменяемость». В 1969;1975 гт. профессор А. И. Иванов в своих работах дал следующее определение: «Взаимозаменяемостью называется принцип конструирования, производства и эксплуатации машин, обеспечивающий возможность сборки или замены в процессе ремонта независимо изготовленных соединяемых деталей и узлов без дополнительной обработки и подгонки при условии, что эксплуатационные показатели работы машин будут находиться в заданных пределах».
Профессор А. И. Якушев в те же годы дает другое определение: «Взаимозаменяемостью изделий (машин, механизмов и т. д.), их частей или других видов продукции (сырья, материалов, полуфабрикатов и т. д.) называют их свойство равноценно заменять при использовании любой из множества экземпляров изделий, их частей или иной продукции другим однотипным экземпляром».
Международный стандарт ISO 8402:1994 (E/F/R) «Управление качеством и обеспечение качества — словарь» дает такое определение: «Взаимозаменяемость — способность объекта быть использованным без модификаций вместо другого для выполнения тех же требований».
В международном стандарте? БО/ШС С>иГОЕ 2:1996 (Е/Р/Л) приводится уже следующее определение: «Взаимозаменяемость — пригодность одного изделия, процесса или услуги для использования вместо другого изделия, процесса или услуги в целях выполнения одних и тех же требований», причем функциональный аспект взаимозаменяемости называется «функциональная взаимозаменяемость», а размерный аспект — «размерная (геометрическая) взаимозаменяемость». Данный-документ дает более полное определение понятию «взаимозаменяемость» с точки зрения широты и унификации его использования, а понятия функциональной и размерной взаимозаменяемости были рассмотрены и описаны нашими учеными (А.И. Иванов, Л.И. Якушев) более глубоко и подробно применительно к изделиям машиностроения.
В последнее время ученые стремятся изучить функциональную взаимозаменяемость, т. е. не только исследовать формирование точности геометрических параметров (размеров, формы, взаимного расположения поверхностей, шероховатости), но и изучить их влияние на кинематические и динамические показатели, износ и трение, надежность и долговечность. Такая постановка задачи требует рассмотрения изучения совместного влияния геометрических параметров и физико-механических свойств материалов (особенно их поверхностного слоя) на указанные характеристики.
Основными критериями функциональной взаимозаменяемости при ремонте машин становятся уже не предельные зазоры или натяги в конкретном соединении, а их влияние на эксплуатационные показатели и показатели надежности сборочных единиц, агрегатов и машины в целом.
В процессе технического обслуживания и ремонта машин необходимо добиваться, чтобы все функциональные параметры ремонтируемого изделия находились в заданных пределах длительное время, иначе снизится долговечность и увеличатся потери материальных и трудовых ресурсов, связанные с необходимостью повторного ремонта, возрастут убытки от простоя машин и т. д.
Нахождение этих пределов — сложная инженерная задача, требующая конкретизации и учета множества факторов.
В теоретических основах ремонта машин уже существуют методики по выбору рационального способа восстановления детали, а в науке о взаимозаменяемости — методики расчета и выбора посадок с учетом влияния эксплуатационных факторов. Специалисты в области восстановления деталей чаще исследуют способы восстановления одной детали соединения, реже — двух, при этом точность геометрических параметров назначается на новые детали. Параметры соединения рассматривают не в полном объеме, функциональные параметры практически не определяют. Методики выбора наилучших способов восстановления элементов, образующих соединения, в настоящее время не существует.
Разработке расчетных и практических методик определения функциональных и конструктивных параметров точности основных унифицированных соединений сборочных единиц и агрегатов, применяющихся в сельскохозяйственной технике, исследованию их влияния на долговечность, а также совместному применению оптимальных норм точности и рациональных методов восстановления посвящена настоящая работа.
Настоящие исследования выполнены в соответствии с Федеральным законом «Об инженерно-технической системе агропромышленного комплекса» (№ 100-ФЗ от 24 мая 1999 г.), «Федеральной целевой программой стабилизации и развития агропромышленного производства в Российской Федерации на 1996;2000 гг.» (Указ Президента Российской Федерации № 933 от 18 июля 1996 г.), «Стратегией развития тракторного и сельскохозяйственного машиностроения России» (Протокол совещания у Председателя правительства Российской Федерации № МК-П5~14пр от 15 сентября 2000 г.), на кафедре метрологии, стандартизации и квалиметрии ФГОУ ВПО МГАУ.
Целью работы является разработка теоретических и практических принципов и методик расчета точностных параметров при ремонте унифицированных соединений сельскохозяйственной техники.
Поставленная цель достигается решением следующих основных задач:
1. Разработать универсальную методику расчета точности геометрических параметров соединения с учетом: вероятностной природы обработки и сборки элементов соединениявероятностной природы динамики его изнашиваниявероятности безотказной работы (ВБР) на заданный ресурсстоимости восстановления и обработки элементов соединения.
2. Создать новые методы расчета оптимального сдвига и расширения полей допусков, предложенные в полуэмпирическом виде А. И. Ивановым.
3. В качестве решения проблемы достижения заданной точности на изношенном технологическом оборудовании разработать и апробировать новый метод сборки — процентную взаимозаменяемость.
4. Выбрать унифицированные соединения и сборочные единицы, наиболее распространенные в сельскохозяйственной технике, с целью проведения практических исследований.
5. Провести анализ условий работы, изнашивания, надежности, способов восстановления и обработки, посадок, отклонений и др. геометрических параметров элементов соединений и сборочных единиц.
6. Разработать методику определения параметров предельного состояния каждого из исследуемых соединений с учетом влияния их на эксплуатационные параметры сборочной единицы или агрегата в целом.
7. Изучить закономерности изменения геометрических параметров соединений в процессе эксплуатации.
8. Определить номинальные геометрические параметры для различных способов восстановления.
9. Выбрать оптимальные способы восстановления и обработки элементов соединения на дифференцированные значения ресурса с различными параметрами допусков посадок.
10. Разработать рекомендаций по восстановлению оптимальной точности деталей и соединений. Внедрить рекомендаций в производство.
В сельскохозяйственной технике около 70% соединений являются унифицированными, значительную часть которых составляют соединения колец подшипников качения с валами и корпусами, а также типа «вал — втулка» и «вал — уплотнение», поэтому именно они выбраны объектом исследований.
Методы исследований выбирались на основе системного подхода к объекту исследований с использованием методов системного и математического анализа, элементов теории точности, теории надежности, теории вероятностей и математической статистики, теории прочности и сопротивления материалов. Применялась современная отечественная и зарубежная аппаратура. В ряде случаев разрабатывались оригинальные методы и приборы.
Научная новизна работы заключается в совершенствовании теории расчета и выбора посадок гладких цилиндрических соединений:
Аналитически получены зависимости, позволяющие определить требуемый конструктивный допуск посадки на заданном ресурсе работы соединений с учетом вероятностной природы процесса старения, заданного уровня брака и вероятности безотказной работы.
Предложен новый алгоритм для определения относительной износостойкости соединения в зависимости от износостойкости отверстия и вала при применении различных способов восстановления.
Предложено теоретическое решение проблемы определения оптимальных величин сдвига и расширения зоны рассеяния размеров в посадке с учетом необходимой долговечности соединений и снижения себестоимости обработки.
Получена математическая модель определения оптимальных способов восстановления и обработки элементов деталей, образующих соединение. Теоретически обоснован оптимальный ресурс работы соединения, сборочной единицы или агрегата, обеспечивающий минимальные затраты при ремонте, а также равный или кратный ресурс соединений.
Разработан и теоретически обоснован новый метод обеспечения неполной взаимозаменяемости — метод процентной взаимозаменяемости, открывающий возможности сборки бракованных валов и отверстий с соблюдениями всех норм точности соединений.
Разработана методика расчета точностных параметров для унифицированных соединений «вал — уплотнение» по критерию начала утечек.
Разработана комплексная методика расчета и выбора посадок колец подшипников качения с целью обеспечения наибольшей долговечности как посадок, таю иподшипникового узла.
Дополнена методика расчета норм точности для соединения «вал — втулка». Достоверность результатов работы обеспечена использованием базовых концепций теории точности, теории надежности, теории вероятности, теории прочности и сопротивления материалов, заданной величиной доверительной вероятности (не ниже 0,9. 0,95), допускаемой величиной ошибки вычислительных операций (до 1. 3%) и подтверждена многократной экспериментальной проверкой полученных данных в производственных условиях.
Практическая значимость работы заключается в широком внедрении на практике алгоритмов и результатов расчетов, методов исследований и практических рекомендаций в области расчета и нормирования точности соединений, а именно: в разработке рекомендаций по определению научно обоснованных параметров посадок унифицированных соединений типа «вал — уплотнение», «валвтулка» «сопрягаемая деталь — кольцо подшипника качения» в сочетании с рациональными способами восстановленияв разработке оригинальных методик и рекомендаций по определению параметров предельного состояния унифицированных соединенийв разработке специальных стендов, методик и приспособлений для проведения исследований по каждому виду соединенийво внедрении в учебный процесс перспективных-'методов расчета точностных параметров унифицированных соединений.
Результаты исследований реализованы в виде монографии и методических рекомендации «Методика расчета и выбора посадок неподвижных соединений при ремонте сельскохозяйственной техники», «Методика расчета и выбора посадок колец подшипников качения при ремонте сельскохозяйственной техники», рассмотренных и одобренных Научно-техническим советом департамента технической политики Минсельхоза России. Вторая из названных методик была рассмотрена на заседании сотрудников и специалистов Всероссийского научно-исследовательского института подшипниковой промышленности (ОАО «ВНИПП») — откуда получено положительное заключение. Результаты исследований широко используются в учебном процессе, в частности, в разработанном автором учебном пособии «Курсовое проектирование по метрологии, стандартизации и сертификации», допущенным УМО вузов по агроинженерно-му образованию в качестве учебного пособия для студентов, обучающихся по направлению 660 300 «Агроинженерия».
Результаты теоретических и экспериментальных исследований рассмотрены, апробированы, одобрены и внедрены в КБ ГНУ «Всероссийский научно-исследовательский институт механизации (ВИМ)» РАСХН, в ОАО «МОССЕЛЬМАШ», в ОАО «ВНИПП», в ОАО «Клинское РТП», в ОАО «Со-бинское РТП», в ОАО «Агросервис», во Владимирской МИС и на других предприятиях, что подтверждено соответствующими актами.
Автором лично получены и выносятся на защиту следующие основные положения: общетеоретические основы расчета конструктивного допуска посадки по модели параметрического отказа соединения с учетом динамики и вероятностных характеристик процесса старения, относительной износостойкости соединения, заданного уровня брака и вероятности безотказной работы при моделировании отказа соединения по одному и двум пределамматематическая модель для определения относительной износостойкости соединения в зависимости от износостойкости отверстия и вала при применении различных способов восстановленияметодика определения оптимальных величин сдвига и расширения зоны рассеяния размеров в посадке с учетом необходимой долговечности соединения и обеспечения снижения себестоимости обработкитеоретические основы решения проблемы определения наилучших способов восстановления и обработки элементов соединения (поверхностей деталей), под расчетные значения допусковматематическое-обоснование способа сборки соединений методом процентной взаимозаменяемостикомплексная методика расчета и выбора посадок соединений колец подшипников каченияметодика расчета предельных и конструктивных натягов для соединений «вал — уплотнение" — совершенствование методики расчета и выбора посадок для соединений «вал — втулка».
Апробация работы. Основные положения и результаты исследований обсуждены и одобрены: на научно-методическом совете Минсельхоза России, секция «Техническая политика» (г. Москва, 2003 г.) — на международной научно-технической конференции «Проблемы и перспективы развития двигателестроения» (г. Самара 2003 г.) — на международном научно-техническом семинаре «Сборка в машиностроении и приборостроении» (г. Брянск, 2001 г.) — на международных научно-технических конференциях, посвященных памяти Генерального конструктора аэрокосмической техники академика Н. Д. Кузнецова (г. Самара 1999, 2001 гг.) — на международном симпозиуме «Надежность и качество 2000» (г. Пенза, 2000 г.) — на международной научно-практической конференции «Методы и средства испытаний и сертификации технологий, техники и сельскохозяйственной продукции» (г. Москва, 2000 г.) — в материалах международной научной школы «Теоретические и прикладные проблемы точности и качества машин, приборов, систем» (г. Санкт-Петербург 1997 г.) — на всероссийской научно-технической конференции «Новые материалы и технологии НМТ-98» (г. Москва, 1998 г.) — на международной научно-технической конференции «Агротехиспыта-ния — 98» (г. Солнечногорск, 1998 г.) — на всероссийской научно-технической конференции «Машиностроительные технологии» (г. Москва, 1998 г.) — на международной научно-технической конференции, посвященной памяти академика В. П. Горячкина (г. Москва, 1998 г.) — на международной научно-технической конференции «Вопросы совершенствования технологических процессов механической обработки и сборки изделий машиностроения» (г. Тула, 1996 г.) — на семинаре «Современные технологии восстановления и упрочнения деталей — эффективный способ повышения надежности машин» (г. Москва, 1996 г.) — на заседаниях кафедры метрологии, стандартизации и квалиметрии и научных конференциях профессорско-преподавательского состава, научных работников и аспирантов МГАУ имени В. П. Горячкина (г. Москва, 1990.2003 гг.).
Основные положения теоретических исследований и практических рекомендаций по теме диссертации опубликованы в 65 научных работах, в том числе в одной монографии, двух нормативных документах, двух учебных пособиях, в 60 статьях (5 из них — в центральных журналах, рекомендованных ВАК РФ) и тезисах докладов, в одном отчете о научно-исследовательской работе, зарегистрированном в ВНТИ-центре.
1. СОСТОЯНИЕ ВОПОСА И ЗАДАЧИ ИССЛЕДОВАНИЙ.
1.1- Современные организационные, технические и экономические аспекты состояния сельскохозяйственной техники в России.
Состояние российского рынка техники для АПК характеризуется значительным сокращением продаж новых машин отечественного производства и слабо организованной’торговлей, как новой, так и подержанной техникой и запасными частями. В ближайшее время в России нельзя ожидать существенного обновления моделей сельскохозяйственной техники. Поэтому использование восстановленной подержанной техники и запасных частей является важным направлением ресурсосбережения в АПК.
В 2002 г. в связи со снижением покупательной способности сельскохозяйственных товаропроизводителей и выбытием изношенной техники в сельском хозяйстве продолжалось сокращение машинотракторного парка. Количество тракторов сократилось на 45 тыс., сеялок — на 20 тыс. единиц [147].
Для выполнения полевых работ в оптимальные агротехнические сроки недоставало 685 тыс. тракторов, 379 тыс. плугов, 165 тыс. культиваторов, 210 тыс. сеялок, 178 тыс. зерноуборочных комбайнов, 22 тыс. кормоуборочных комбайнов. Обеспеченность основными видами сельскохозяйственной техники на конец 2002 года составила: тракторами — 52%, плугами — 37, культиваторами — 60, сеялками — 59, зерноуборочными комбайнами — 51, кормоуборочными комбайнами — 71%, что на 1 .3% ниже, чем в предыдущем году [147].
Нагрузки на технику в 2002 г. составили на: тракторы — не более 140 га при нормативе 73 га, плуги — соответственно 464 и 173 га, культиваторы — 416 и 250 га, сеялки — 213 и 123 га, зерноуборочные комбайны — 267 и 131 га, кормо-уборочные комбайны-223 и 157 га [147].
По предварительным данным, в 2002 г. энергообеспеченность составила всего 315 л.с. на 100 га посевной площади, что ниже, чем в 2001 г. (321 л.с.), и намного меньше, чем в передовых зарубежных странах [147].
Сложившееся положение с обеспеченностью сельского хозяйства техническими средствами усугубляется еще и тем, что 55.70% имеющегося машинно-тракторного парка выработало свой срок службы, находится за пределами сроков амортизации и требует повышенных затрат на поддержание в работоспособном состоянии.
Техническая готовность основных видов сельскохозяйственных машин в период полевых работ-в-2000~. 2002 гг. характеризовалась показателями, представленными в табл. 1.1 [147].
Таблица 1.1 Техническая готовность тракторов и основных видов сельскохозяйственных машин к сезону полевых работ, %.
Вид сельскохозяйственной техники Техническая готовность.
2000 г. 2001 г. 2002 г.
Тракторы 78 79 80.
Грузовые автомобили 77 79 80.
Сеялки 76 76 79.
Зерноуборочные комбайны 72 74 75.
Кормоуборочные комбайны 74 76 78.
Свеклоуборочные машины 68 70 76.
Та б л и ц, а 1.2.
Выпуск тракторов и основных видов сельскохозяйственной техники в 2002 г., штук.
2002 г. 2001 г.
Виды техники в%к в%к штук 2001 г. 2000 г.
Тракторное и сельскохозяйственное машиностроение, % - 77,6 87,3.
Тракторы 10 000 65,8 118,6.
Тракторные плуги 2166 68,9 27,0.
Тракторные сеялки- 5283 82,2 188,3.
Тракторные культиваторы 5262 93,4 64,6.
Зерноуборочные комбайны 7561 83,4 78,5.
Тракторные косилки 3677 105,5 37,6.
Комбайны кормоуборочные 648 68,9 84,8.
Погрузчики универсальные сельскохозяйственного назначения 1173 81,3 79,8.
После оживления в последние года вновь произошло серьезное сокращение выпуска продукции тракторного и сельскохозяйственного машиностроения. Его объем уменьшился в 2002 г. по сравнению с 2001 г. на 22,4%. Вместе с тем, несмотря на большую потребность в технике и при недостатке на ее приобретение, цены на нее продолжались расти, табл. 1.2, рис. 1.1 [147].
126,2.
Грузовые Тракторы Плуги Сеялки тракторные Комбайны автомобили • зерноуборочные.
Рис. 1.1. Динамика цен на основные виды сельскохозяйственной техники в 2002 г. (к 2001 г.), %.
Крайне негативное влияние на развитие рынка материально-технических ресурсов оказывает низкое качество поставляемой отечественной промышленностью техники. Так, по данным Гостехнадзора, из 3 тыс. предъявленных претензий поставщикам техники в 76% случаев признана их вина. При этом почти у 50% машин, вышедших их строя по вине завода-изготовителя, дефекты устраняются силами и средствами сельскохозяйственных товаропроизводителей. По этим причинам доля продаж отечественных тракторов на внутреннем рынке в 2002 году составила 25% [147].
По данным испытаний серийных машин за период 1998.2002 годов свыше 95% образцов изготовлены с отклонениями от технических условий, табл. 1.3. Нормативам по надежности не соответствуют до 30% представленных образцов. По результатам испытаний безотказность тракторов в 2002 году в сравнении с 1991 г. снизилась по различным классам и производителям от 30 до 80%. Не улучшилось за последние годы качество изготовления и зерноуборочных комбайнов. Диапазон варьирования средней наработки на отказ отечественных комбайнов в 2002 году составил от 16 до 40 часов. Это в 5.20 раз ниже, чем у импортных аналогов. Не удовлетворяют требованиям надежности и качества изготовления и другие виды сельскохозяйственной техники: плуговоколо 30%, борон — 35%, культиваторов — 60%, сеялок — 45%, косилок — 60%. Свыше 40% сельскохозяйственной техники не соответствует техническим условиям по показателям назначения (эксплуатационным показателям) [147].
Острая потребность сельских товаропроизводителей в сельскохозяйственной технике стимулирует выход на рынок производителей регионального уровня в основном относительно несложной почвообрабатывающей, кормозаготовительной техники, а также оборудования для животноводства. Она изготавливается, как правило, по заимствованной документации малыми сериями (20. 100 штук) по упрощенной технологии и не представляется на государственные испытания.
Таблица 1.3.
Анализ качества сельскохозяйственной техники за 1991 .2002 годы.
Год Испытано машин, шт. Кол-во машин, имеющих отклонения от ТУ, % Кол-во машин, имеющих Кг ниже норматива, % Кол-во машин, имеющих отклонения от ССБТ, % Доля отклонений по эксплуатационно-технолошче-ским показателям, % Кол-во машин, имеющих показатель «Наработка на отказ» ниже норматива, %.
1991 1071 93,0 17,8 79,3 30,7.
1992 220 95,9 24,1 85,9 32,2 28,6.
1993 194 94,3 19,1 90.2 31,0 23,4.
1994 121 98,0 20,9 82,9 33,2 28,1.
1995 82 96,0 24,4 75,6 34,8 28,0.
1996 105 96,0 29,0 88,0 38,1 43,8.
1997 67 97,0 31,3 82,0 38,0 38,8.
1998 103 96,0 27,2 85,4 40,7 26,0.
1999 77 95,0 27,2 77,0 40,5 39,0.
2000 135 98,0 27 83,0 39 30,0.
2001 136 96,0 22,0 72,0 35,5 27,0.
2002 160 97,0 22,5 70,0 34,6 31,0.
Приемочные испытания новой техники показали, что уровень конструктивных разработок остается невысоким: 47% испытанных образцов являлись модификациями серийно выпускаемых машин. Только 33% машин для основной обработки почвы, 31% машин для поверхностной обработки почвы, 38% сеялок, 30% машин для заготовки кормов, 65% машин и приспособлений для. уборки зерновых культур соответствовали нормативной документации.
Анализ данных^ по применению импортной техники показывает, что зарубежные конструкции имеют более продолжительный срок службы и значительно меньший процент затрат на ремонт и плановое техническое обслуживание. Однако за счет значительно более высокой стоимости техники в (4.7 раз), основных запчастей (в 8.12 раз) и расходных материалов стоимость одного часа работы машин в 2. 16,5 раза превышает российские аналоги.
Большое количество деталей при ремонте техники выбраковывается с износом, не превышающим предельные значения. В худшем случае списанная техника ржавеет у заборов предприятий и хозяйств. Такая же ситуация сложилась и с деталями списанных автомобилей, комбайнов и другой сложной техники. Побудительным мотивом для всех участников вторичного рынка служит прибыль, которая ориентирует владельца на грамотную и экономичную эксплуатацию техники, чтобы получить максимальную выручку, а исполнителяна увеличение объема, расширение номенклатуры, повышение качества вторичных технических ресурсов. Установлено, что капитальный ремонт машины обходится в 2.3 раза дешевле, чем приобретение новой. На средства, затрачиваемые на приобретение одной новой, можно отремонтировать 4−5 неисправных машин. Применение в качестве запасных частей деталей со списанной техники, годных для вторичного использования без ремонта, экономически и технически выгодно и целесообразно. Себестоимость восстановленных деталей не превышает 50.70% цены на новые детали при ресурсе 80.90% ресурса новых. При восстановлении деталей производственных операций проводится в 5.8 раз меньше, чем при их изготовлении [143].
Опыт США, Англии, Германии и других экономически развитых стран показывает, что рынок подержанной техники является важным резервом сохранения технического потенциала сельских товаропроизводителей. В США, Германии и странах ЕЭС на один новый трактор приходится три-четыре подержанных. Во многих западных странах мира более 50% механизированных работ в фермерских хозяйствах выполняют подержанными машинами со сроками службы от 7 до 15 лет и более. Машины в плохом техническом состоянии приобретаются фирмами по разборке изношенной техники на агрегаты и запасные части, которые реализуются как подержанные. Хозяйства считают выгодной замену отказавших элементов такими деталями, это выравнивает сроки службы эксплуатируемых агрегатов, сборочных единиц и соединений в машинах [143].
В некоторых регионах Российской Федерации организуется купля-продажа как отечественной, так и зарубежной подержанной техники. Определенный опыт накоплен ОАО «Клинское РТП», которое покупает, восстанавливает и продает энергонасыщенные тракторы, кормоуборочные комбайны (в том числе производства Германии), их узлы и агрегаты, двигатели всех марок, оборудование для животноводческих ферм. Это предприятие одно из первых в стране получило сертификат на соответствие качества требованиям и нормативной документации на ремонт тракторов, кормоуборочных комбайнов отечественного и зарубежного производства, техническое обслуживание и ремонт оборудования животноводческих ферм.
Обеспеченность АПК новой отечественной техникой падает. Количество машин различного наименования уменьшилось с 1991 г. на 30.45%, 60.70% эксплуатируемых машин и более половины тракторов отработали амортизационные сроки. Выбытие техники превышает ее приобретение в 8−25 раз. В списанной технике остаются сборочные единицы и детали, имеющие значительный остаточный ресурс. Так, в каждом списанном тракторе типов МТЗ и ЮМЗ в среднем содержится 30.35% деталей, годных для вторичного использования без технологических воздействий, 40.45% - подлежащих восстановлению, только 25.30% - не подлежащих ему. По цене 40% деталей шасси годны для вторичного использования без ремонта, 37% - для восстановления и только 23% - подлежат выбраковке. По массе эти показатели составляют соответственно 37, 35 и 28%. Аналогичная картина наблюдается по деталям списанных автомобилей, комбайнов и другой сложной техники [143].
Отношение стоимости капитального ремонта машин к цене новых с 1990 г. по 1996 п уменьшилось с 30.40 до 20.28%, а двигателей — с 40.60 до 22.30% [143]. Эти изменения обусловлены ростом цен на новые машины и снижением цены ремонта из-за сокращения выбраковки деталей с недоиспользованным ресурсом, внедрением ресурсосберегающих технологий, снижением рентабельности РТП и оплаты труда работникам, увеличением доли работ, выполняемых владельцами техники. Применение в качестве запасных частей деталей со списанной техники, годных для вторичного использования без ремонта, экономически целесообразно. Их цена невысока, а остаточный ресурс значителен. Это относится к дорогим, крупногабаритным, металлоемким деталям (рама, подвеска, направляющие колеса, поддерживающие ролики, конечная передача гусеничных тракторов и т. д.).
Таким образом, восстановление изношенных деталей является наиболее весомым резервом снижения стоимости услуг технического сервиса и повышения эффективности как предприятий, занимающихся эксплуатацией сельскохозяйственной техники, так и ее ремонтом.
По данным Россельхозакадемии, в России планируется в ближайшем будущем задействовать на вторичном рынке 40.45% парка машин, а 80.90% парка будет функционировать за пределами сроков службы [143]. Это потребует освоения новых методов технического обслуживания, более совершенного оборудования для восстановления и упрочнения деталей машин, расширения исследований по надежности машин за пределами сроков службы, возобновления государственных испытаний отремонтированных машин.
ОБЩИЕ ВЫВОДЫ.
1. Получены аналитические зависимости, позволяющие определить требуемый конструктивный допуск посадки на заданном ресурсе работы соединений с учетом вероятностной природы процесса старения, заданного уровня брака и вероятности безотказной работы при исследовании модели отказа соединения по одному и двум пределам.
2'. Получена математическая модель для определения относительной износостойкости соединения в зависимости от износостойкости отверстия и вала при применении различных способов восстановления.
3. Предложен новый алгоритм для определения оптимальных величин сдвига и расширения зоны рассеяния размеров в посадке с учетом необходимой долговечности соединений и снижения себестоимости обработки. Полученные зависимости универсальны и применимы для расчета размерных цепей.
4. Предложено теоретическое решение проблемы определения оптимальных способов восстановления и обработки элементов деталей, образующих соединение. Теоретически обоснован оптимальный ресурс работы соединения, сборочной единицы или агрегата, обеспечивающий минимальные затраты при ремонте, а также равноили кратноресурсность соединений.
5. Разработан и теоретически обоснован новый способ сборки соединений методом процентной взаимозаменяемости, открывающий возможности расширения технологических допусков размеров валов и отверстий с соблюдением всех норм точности соединений.
6. Разработана методика определения параметров предельного состояния в соединении «вал — уплотнение» по критерию начала утечек.
7. Существенно дополнена и уточнена методика расчета и выбора посадок неподвижных соединений типа «вал — втулка».
8. Разработана комплексная методика расчета и выбора посадок колец подшипников качения позволяющая обеспечить наибольшую долговечность подшипникового узла.
9. Разработано специальное приспособление для контроля и дефектации резиновых армированных манжет по внутреннему диаметру, позволяющее контролировать диаметры манжет в условиях мелкосерийного производства.
10. Для соединений «вал — уплотнение»: установлена эмпирическая: зависимость между натягом, радиальным биением и частотой вращения вала по критерию начала утечекразработано специальное устройство для определения взаимосвязиэтих параметровпредложена методика определения" ремонтного размера вала и подбора манжет, позволяющая увеличить ресурс соединения в 1,2 разаприменен сдвиг зоны рассеяния размеров в посадке, в результате чего ресурс соединения повысился на 10. 13%.
11.Для соединений «вал — втулка»: выявлено, что интенсивность изнашивания предлагаемого соединения 030Я6/у6 в 12 раз меньше, чем у серийного 030 0°'17/-0,05) — интенсивность изнашивания предлагаемого соединения 04О#9/х8 в 3 раза меньше, чем у серийного 04ОЯ7/&-6- использованы возможности расширения полей допусков, что позволило применить посадку 03ОЯ7/у6- реализован метод процентной взаимозаменяемости, что привело к значительному увеличению технологических допусков на обработку.
12. Для соединений «вал — кольцо подшипника качения»: установлено, что на начало проворачивания кольца относительно вала самое существенное влияние оказывает величина натяга в соединениивыявлено, что интенсивность изнашивания предлагаемых соединений 035ЬО/рб в 1,3.1,5 раза меньше интенсивности изнашивания серийных 035Ь0/кб.
13. Годовой экономический эффект от повышения долговечности соединений «вал — уплотнение» составит 48 615 р. (при программе ремонта 1000 соединений в год), при применении новых посадок колец подшипников качения — 38 177 р. (при программе ремонта 400 соединений в год).
14. Теоретические и практические результаты исследований получили широкое распространение. По теме работы издана монография. Опубликованы методические рекомендации «Методика расчета и выбора посадок неподвижных соединений при ремонте сельскохозяйственной техники», «Методика расчета и выбора посадок колец подшипников качения при ремонте сельскохозяйственной техники», рассмотренные и одобренные Научно-техническим советом департамента технической политики Минсельхозпрода России (протокол № 14 от 3 июля 2003 г.). Вторая из названных методик была рассмотрена, нарасширенномзаседаниисотрудникови- специалистов-Всероссийского научно-исследовательского института подшипниковой промышленности (ВНИПП), откуда получено положительное заключение. Результаты исследований используются в двух учебных пособиях и в процессе подготовки специалистов с высшим образованием по направлению 660 300 «Агроинженерия».
15. Результаты теоретических и экспериментальных исследований рассмотрены, апробированы, одобрены и внедрены в КБ ГНУ ВИМ РАСХН, в ОАО «МОССЕЛЬМАШ», в ОАО «ВНИПП», в ОАО «Клинское РТП», в ОАО «Собинское РТП», в ОАО «Агросервис», во Владимирской МИС и на других предприятиях, что подтверждено соответствующими актами.
Список литературы
- Bogdanoff J.L., Kozin F. Probabilistic Models of Comulative Damage. New York. Chichester. Bristane. Toronto. Singapore: John Wiley & Sons, 1985. -334 p.
- Chase K.W. Technical overview of the CATs Sistem for tolerance analysis of mechanical assemblies // ADCATS Reports, 1993, № 9.
- Computer aided tolerancing / Edited by Fumihiko K. London: Chapman & Hall, 1996. 342 p.
- Damezt K., Balzer D. Nichi Lineare Optimiezung fiiz modeliezung und Prozesstoezung (Algorihmen. Programmen. Anwendungen). Berlin: Akademie — Vezlag, 1976. — 202 s.
- Development of a new Radial lip seal withnibber and PTFE lips. Saito T., Iida S., Wada N., Heinzen S.R., Nishina H. \ ASLE Transactions, vol. 13 n.4., 1971, -P. 289−295.
- Greenwood W.H., Chase K.W. A new tolerance analysis method for designers and manufactureses // I. Eng. Industry. Trans. ASME. 1987. Vol. 109, № 2. -P.l 12−116.
- Parkinson D.В. The applikation of reliability methods to tolerancing // ASME. 1982. Vol 104. № 3. p 50−59.
- Анурьев В.И. Справочник конструктора-машиностроителя. В 3-х т. / Под. ред. И. Н. Жестовой. -М.: Машиностроение, 1999.
- Артемьев Ю.Н. Качество ремонта и надежность машин в сельском хозяйстве. М.: Колос, 1983. — 389 с.
- Ачкасов К.А. Прогрессивные способы ремонта сельскохозяйственной техники. — М.: Колос, 1984. 356 с.
- Бабусенко С.М. Исследование проворачивания колец подшипников качения в процессе работы: Дис. канд. техн. наук. — М.: МИИСП, 1976. — 203 с.
- Бабусенко С.М. Проектирование ремонтных предприятий. — М.: Колос, 1981.-295 с.
- Балашов В.А. Исследование длительной прочности посадок с натягом и отбор полей допусков из системы ИСО: Дис. канд. техн. наук. Пенза: 1974.-188 с.
- Баранов Г. Г. О выборе допусков, обеспечивающих заданную точность и наименьшею стоимость его изготовления // Кн.: Труды института машиноведения.-Вып. 2. AH GGGP, 1956:-G. 130−134:
- Баскаков В.Н., Лельчук A.JI. Методические указания по оценке динамики изнашивания деталей машин в условиях специализированных ремонтных предприятий / Под общ. ред. Н. Ф. Тельнова. М.: МИИСП, 1985. — 42 с.
- Батищев А.Н., Голубев И. Г., Лялякин В. П. Восстановление деталей сельскохозяйственной техники. М.: Информагротех, 1985. — 294 с.
- Батищев А.Н. Ресурсосберегающие технологии восстановления деталей гальваническими покрытиями: Дис. докт. техн. наук в виде научного доклада. М., 1992. — 53 с.
- Баусов A.M. Повышение долговечности подшипниковых узлов, вентиляторов тракторов кл. 0,6 и 0,9 применением магнитожидкостных уплотнений: Дис. канд. техн. наук. М. МИИСП, 1991. — 136 с.
- Башта Т.М. Машиностроительная гидравлика. Справочное пособие — М.: Машиностроение, 1971. — 671с.
- Белов В.М. Коэффициент запаса точности как критерий расчета ресурса деталей // Надежность и контроль качества. 1988. — № 6. С.32−36.
- Белоусов А.П. Проектирование станочных приспособлений. — М.: Высшая школа, 1980.-240 с.
- Белявцев A.B., Крутилин В. А. Механизация сельскохозяйственного производства. М.: Агропромиздат, 1991. — 207 с.
- Бобровников Г. А. Исследование прочности прессовых соединений с антикоррозионными покрытиями//Известия вузов. — 1964.-№ 5.—С. 90—97.
- Болотин В.В. Прогнозирование ресурса машин и конструкций. — М.:
- Машиностроение, 1984. 280 с.
- Борисов М.В., Павлов И. А., Постников В. И. Ускоренные испытания соединений на износостойкость как основа повышения их качества. — М.: Издательство стандартов. 1976. — 352 с.
- Бочкарев В.Н. Решение задачи по экономической оптимизации допусков // Стандарты и качество. 1980. — № 6. — С. 17−25.
- Бугаев В. НГ Восстановление деталей и повышение ресурса топливной аппаратуры тракторных и автомобильных дизелей термодиффузионной металлизацией: Дис. д-ра техн. наук. М.: МИИСП, 1987. — 289 с.
- Биргер И.А. и др. Расчет на прочность деталей машин: Справочник- 4-е изд., перераб. и доп. М.: Машиностроение, 1993. — 640 с.
- Булатов А.П. и др. Основы теории точности машин и приборов / Под ред. Иванова В. А. СПб. Институт проблем машиноведения РАН, 1993. — 233 с.
- Васьков В.И. Исследование влияния динамических нагрузок на долговечность сопряжений вал подшипник: Дис. канд. техн. наук. — Саратов.: ССХИ, 1973. — 142 с.
- Вечтомов A.A., Куликов A.A., Методические указания и задания к курсовой работе по взаимозаменяемости, стандартизации и техническим измерениям. 4.1 и II.- М.: МИИСП, 1989.
- Волков Б.Н., Кубарев А. И. Надежность изделий и функциональная взаимозаменяемость // Кн.: Применение методов функциональной взаимозаменяемости в решении задач надежности. — М.: ВНИИНмаш, 1978.-С. 1−12.
- Восстановление автомобильных деталей: Технология и оборудование/ В. Е. Канарчук, А. Д. Чигринец, O.JI. Голяк, П. М. Шоцкий. М.: Транспорт, 1995.-305 с.
- Вучков И, Боязжиева JL, Солаков Е. Прикладной регрессионный анализ — М.: Финансы и статистика, 1987. 274 с.
- Галь И.Е., Прокофьев A.A., Суржин B.C. Восстановление натяга внеподвижных соединениях // Вестник машиностроения. — 1966. — № 10. — С. 47−58.
- Гнеденко Б.В. Курс теории вероятностей. М.: Наука, 1988. — 448 с.
- Голубев А.И., Кондаков JI.A. Уплотнения и уплотнительная техника. — М.: Машиностроение, 1985. —463 с.
- Голубев Г. А. О динамическом эффекте, возникающем в манжетных уплотнителБныхг узлах быстровращающихся валов // Сборник вопросов трения и проблем смазки. М.: Наука, 1988. 252 с.
- Голубев Г. А., Кукин Г. Н., Лазарев Г. Е., Чичинадзе A.B. Контактные уплотнения вращающихся валов. М.: Машиностроение, 1976. — 264 с.
- Голубев И.Г. Обеспечение долговечности восстановленных деталей и соединений сельскохозяйственной техники и увеличенными допусками размеров и посадок: Дис. д-ра техн. наук.- М.: РГАУ, 1997. 285 с.
- Гольденберг М.Б. Исследование износов и способов восстановления прессовых соединений на примере неподвижных сопряжении ролик-шпиндель: Автореф. дис. канд. техн. наук. Саратов, ССХИ, 1972. — 31 с.
- ГОСТ 23.001−77. Обеспечение износостойкости изделий. Основные положения.- М.: Изд-во стандартов, 1986.
- ГОСТ 23.002−78. Обеспечение износостойкости изделий. Трение, изнашивание и смазка. Термины и определения. М.: Изд-во стандартов, 1985.
- ГОСТ 23.224−86. Обеспечение износостойкости изделий. Методы оценки износостойкости восстановленных деталей. М.: Изд-во стандартов, 1989.
- ГОСТ 25 346–89. Основные нормы взаимозаменяемости. Единая система допусков и посадок. Общие положения, ряды допусков и основных отклонений. -М.: Изд-во стандартов, 1989.
- ГОСТ 25 347–82 ЕСДП. Поля допусков и рекомендуемые посадки. М.: Изд-во стандартов, 1988.
- ГОСТ 27.302−86. Надежность в технике. Методы определениядопускаемого отклонения параметра технического состояния и прогнозирования остаточного ресурса составных частей агрегатов машин. -М.: Изд-во стандартов, 1987.
- ГОСТ 27 310–87. Комбайны картофелеуборочные. Общие технические условия. — М.: Изд-во стандартов, 1987.
- ГОСТ 27 860–88. Детали трущихся сопряжений. Методы измерения износа.-М.: Изд-во стандартов,-1988-
- ГОСТ 3325–85. Подшипники качения. Поля допусков и технические требования к посадочным поверхностям валов и корпусов. Посадки. — М.: Изд-во стандартов, 1986.
- ГОСТ 4.17−80. СПКП. Уплотнители резиновые контактные. Номенклатура показателей. -М.: Изд-во стандартов, 1988.
- ГОСТ 8.009−84. ГСИ. Нормируемые метрологические характеристики средств измерений. М.: Изд-во стандартов, 1984.
- ГОСТ 8.051−81. ГСИ. Погрешности, допускаемые при измерении линейных размеров до 500 мм. М.: Изд-во стандартов, 1986.
- ГОСТ 8.207−76. ГСИ. Прямые измерения с многократными наблюдениями. Методы обработки результатов наблюдений. М.: Изд-во стандартов, 1988.
- ГОСТ 8752–79. Манжеты резиновые армированные для валов. Технические условия. М.: Изд-во стандартов, 1990.
- Гурьев И.В. Исследование применения упрочняюще калибрующего инструмента для восстановления сопряжении под подшипники качения при ремонте машин: Автореф. дис. канд. техн. наук.-М.: МИИСП, 1974.— 20 с.
- Дагис З.С. Методические указания по определению допустимых и предельных износов деталей и их соединений. — Алексеевка: Целинный филиал ГОСНИТИ, 1982. 139 с.
- Дехтеринский Л.В., Апсин В. П. Размерный анализ ремонтируемыхсоставных частей автомобилей и дорожных машин. М.: МАДИ, 1988. 47 с.
- Демиденко Е.З. Оптимизация и регрессия. М.: Наука, 1989. — 286 с.
- Демко А. А. Исследование фреттинг-процесса в условиях работы сопряжении сельскохозяйственных машин: Дис. канд. техн. наук. Киев.: КСХА, 1972.-178 с.
- Дмитриев JI.H. Исследование влияния погрешностей формы сопрягаемых деталей на- прочность прессовых* соединений: — Автореф. Дис- канд: техн- наук. Ростов на Дону.: РДТУ, 1964. — 16 е.
- Демин Ф.И., Суков О. С. Прогнозирование и обеспечение точности сборочных параметров изделий сложной конструктивной формы // Проблемы машиностроения и автоматизации, 1996, № 1−2. С. 108—113.
- Допуски и посадки: Справочник. В 2 ч. / М. А. Палей, А. Б. Романов, В. А. Брагинский. Т.1. СПб.: Политехника, 1992. 543 е.- Т. 2. СПб.: Политехника, 1993.-448 с.
- Дунаев П.Ф., Леликов О. П. Расчет допусков размеров. М.: Машиностроение, 2001. — 240 с.
- Ерохин М.Н. Принципы повышения надежности и эффективности эксплуатации сельскохозяйственной техники (на примере картофелеуборочных комбайнов): Дис. д-ра техн. наук в форме научного доклада. М.: МГАУ, 1994. — 76 с.
- Житомерский В.К. Уплотнения. М.: Машиностроение, 1964. — 154 с.
- Иванов А.И. Повышение эффективности ремонта и эксплуатации сельскохозяйственных машин (путем оптимизации размерных параметров): Дис. д-ра техн. наук. — М.: МИИСП, 1973. 412 с.
- Иванов А.И., Полещенко П. В., Бабусенко С. М. и др. Взаимозаменяемость в ремонте и эксплуатации машин. — М.: Колос, 1969. — 320 с.
- Иванов В.П. Технологическая подготовка ремонтного производства в условиях рынка // Механизация и электрификация сельского хозяйства. — 1994. -№ 11. С. 27−28.
- Иванов М.Н. Детали машин. М.: Высшая школа, 1998. — 338 с.
- Исиват X., Хирано Ф. Влияние эксцентриситета вала на работу гидравлических уплотнений // Кн.: Проблемы современной уплотнительной техники. — М.: Мир, 1967.
- Карепин П.А. Обоснование технических требований на предремонтное диагностирование тракторного двигателя (на примере кривошипно-шатунного механизма двигателя^ СМД-14): Дис. канд: техн- наук: — М: г МИИСП, 1981.- 189 с.
- Карепин П-А. Теоретические законы распределения и их обоснование в задачах анализа точности многогранных размерных цепей. — М.: МГАУ, 1999.-256 с.
- Карпузов В.В. Повышение долговечности сборочных единиц с жесткими компенсаторами при ремонте машин. Автореф. дис. канд. техн. наук. — М.: МИИСП, 1985.-16 с.
- Касавченко Е.В. Исследование и разработка методов повышения надежности уплотнительных узлов тракторов «Кировец» при капитальном ремонте: Дис. канд. тех. наук. — Л. Пушкин: ЛСХИ, 1980. — 196 с.
- Касьянов В.Е. Повышение надежности машин за счет оптимизации и нормирования допусков на параметры деталей // Надежность и контроль качества. 1989. — № 5. — С. 28−41.
- Коваленко И.Н., Филиппова АА. Теория вероятностей и математическая статистика. — М.: Высшая школа, 1982. — 256 с.
- Кожуро Л.М. Технологические основы восстановления и упрочнения деталей машин электромагнитной наплавкой: Автореф. дис. д-ра техн. наук. М: МГАУ, 1995. — 32 с.
- Коморницкий-Кузнецов В. К. Исследование фрикционных характеристик уплотнений вращающихся валов: Автореф. дис. канд. техн. наук — М.: МИИСП, 1973.-19 с.
- Конкин Ю.А. Экономика ремонта сельскохозяйственной техники. — М.:
- Агропромиздат, 1990. 384 с.
- Косов М.Г., Кутин A.A., Саакян Р. В., Червяков JI.M. Моделирование точности при проектировании технологических машин. — М.: СТАНКИН, 1997. 104 с.
- Крагельский И.В., Добыгин М. Н., Комбалов B.C. Основы расчетов на трение и износ. М.: Машиностроение, 1997 — 526 с.
- Кряжков В: М: Надежность и качество сельскохозяйственной" техники. — М.: Машиностроение, 1989.-335 с.
- Курчаткин В.В. Восстановление посадок подшипников качения сельскохозяйственной техники полимерными материалами. Дис. д-ра техн. наук. М.: МГАУ, 1989. — 333 с.
- Левицкий Ю.А. Исследование предельного износа и способов восстановления деталей манжетных уплотнений вращающихся валов при ремонте тракторов и сельскохозяйственных машин: Автореф. дис. канд. техн. наук. Челябинск: ЧИМЭСХ, 1974. — 18 с.
- Лезин П.П. Формирование надежности сельскохозяйственной техники при ее ремонте. Саратов: СГУ, 1987. — 196 с.
- Лельчук Л.М. и др. Оценка предельных износов и зазоров в сопряжениях сельскохозяйственных тракторов. — М.: ВНИИНМАШ, 1983. 18 с.
- Леонов O.A. Повышение долговечности подвижных соединений «вал-уплотнение» оптимизацией точностных параметров (на примере редукторов картофелеуборочных комбайнов): Дис. канд. техн. наук. — М: МГАУ, 1993.- 185 с.
- Леонов O.A., Вечтомов A.A. Расчет оптимального сдвига полей допусков для любого числа сопрягаемых размеров // Технический сервиис в АПК: Сб. науч. трудов МГАУ. М.: МГАУ, 1995. — С.45−48.
- Леонов O.A. Курсовое проектирование по метрологии, стандартизации и квалиметрии. М.: МГАУ, 2002. — 168 с.
- Леонов O.A. Взаимозаменяемость унифицированных соединений при ремонте мельскохозяйственной техники. Монография. — М.: ФГОУ ВПО МГАУ, 2003: 167 с.
- Марков H.H. Нормирование точности в машиностроении— М.: Изд-во «Станкин», 1992 320 с.
- Манжеты резиновые армированные для валов. М.: Министерство тракторного и сельскохозяйственного машиностроения. Министерство перерабатывающей и нефтехимической промышленности. СССР. ОНТИ — М.: НАТИ, 1972.-58 с.
- Машиностроение. Энциклопедия / Ред. совет: К. В. Фролов (пред) и др.— -М.: Машиностроение. Детали машин. Конструкционная прочность. Трение, износ, смазка. T. IV-1 / Д. Н. Решетов, А. П. Гусенков, Ю. Н. Дроздов и др.- Под общ. ред. Д. Н. Решетова. 864 с.
- Методика технико-экономического обоснования способов восстановления деталей машин. М.: ГОСНИТИ, 1988. — 24 с.
- Методические рекомендации. Надежность в технике. Методы прогнозирования показателей параметрической надежности изделий машиностроения по результатам кратковременных испытаний или эксплуатации.- М.: ВНИИММАШ, 1980. 48 с.
- МИ 1967−89. ГСИ. Выбор методов и средств измерений при разработке методик выполнения измерений. Общие положения. — М.: Изд-во стандартов, 1989.
- МР 238−87. Надежность в технике. Методы расчета допускаемых значений износа типовых элементов изделий. — М.: ВНИИНМАШ, 1987. — 52 с.
- Михлин В.М. Прогнозирование технического состояния машин. — М.: Колос, 1976. -288 с.
- Михлин В. М и др. Таблицы показателей для определения надежности элементов, вида и срока ремонта машин по результатам прогнозирования. М.: ГОСНИТИ, 1980. — 28 с.
- Михлин В.М., Пащунов С. А. Особенности определения допускаемых износов деталей и-сопряжении-пркгремонте машин: Т. 75. // КнггТрудьг ГОСНИТИ. М.: ГОСНИТИ, 1985. — С. 54−59.
- Моделирование процессов восстановления машин / ВДТ Апсин, JI.B. Дехтеринский, С. Б. Норкин, В. М. Приходько. — М.: Транспорт, 1996. — 311с.
- МР 238−87. Надежность в технике. Методы расчета допускаемых значений износа типовых элементов изделий. М.: Изд-во стандартов, 1988.
- Мякушкин А.П. Полимеры в узлах трения и уплотнениях при низких температурах.-М.: Машиностроение, 1993.-288 с.
- Надежность в технике. Функциональная взаимозаменяемость. Общие требования к методам расчета. Методические рекомендации. М.: ВНИИНмаш, 1980.-38 с.
- Надежность и эффективность в технике. Справочник: В 10 т. / Ред. совет: В. С. Авдуевский (пред.) и др. М.: Машиностроение, 1986.
- Надежность и ремонт машин / Под ред. В. В. Курчаткина. — М.: Колос, 2000. 776 с.
- Никифоров А.Д. Взаимозаменяемость, стандартизация и технические измерения. М.: Высшая школа, 2000. 510 с.
- Никифоров А.Д., Бойцов В. В. Инженерные методы обеспечения качества в машиностроении. М.: Изд-во стандартов, 1987.- 384с.
- Новицкий П.В., Зограф И. А. Оценка погрешностей результатов измерений. — JL: Энергоатомиздат, 1991. — 304 с.
- Орсик JI.C. Основные приоритеты технической политики в АПК // Тракторы и сельскохозяйственные машины, 2001, № 3. С. 3−5.
- Палей М.А., Брагинский В. А. Международные и национальные нормы взаимозаменяемости в машиностроении. Справочник транслятор. — М.: Издательский центр «Наука и техника», 1997.
- Палей М.А., Романов А. Б., Брагинский В. А. Допуски и посадки, т. 2. Л.: Политехника, 1991.-607с.
- Паркинсон Д.В. Применение методов теории надежности при назначении допусков // тр. Амер. о-ва инженеров- механиков: Конструирование и технология машиностроения. № 3/ Пер. с англ. М.: Мир, 1982. с.50−58.
- Панышев Д.Д. Отделочно-упрочняющая обработка поверхностно-пластическим деформированием. М.: Машиностроение, 1978. — 188 с.
- Перель Л.Я., Филатов A.A. Подшипники качения. Расчет, проектирование и обслуживание опор: Справочник. М.: Машиностроение, 1992. — 608 с.
- Повышение долговечности соединений сельскохозяйственной техники методом оптимизации точностных и технологических параметров. Леонов O.A., Белов В. М., Куликов A.A., Кисенков Н. Е. Отчет о НИР. ВНТИЦентр. №ГР 01.9.70 3 933. — М.: МГАУ, 1996. — 58 с.
- Поляк A.A., Лернев М. И. Содержание критерия предельного состояния в зависимости от области его применения // Обеспечение надежности тракторной техники. М.: ГНТИ НПО «НАТИ», 1984.
- Поляченко A.B. Увеличение долговечности восстанавливаемых деталей контактной приваркой износостойких покрытий в условиях сельскохозяйственных ремонтных предприятий: Дис. д-ра техн. наук. — М. МИИСП, 1984. 374 с.
- Попов В.Н. Исследование работоспособности и выбор рациональных способов восстановления деталей уплотнительных узлов сельскохозяйственных тракторов: Дис. канд. техн. наук. Л. — Пушкин: ЛСХИ, 1975.- 191 с.
- Р 50−601—20−91. Рекомендации по оценке точности и стабильности технологических процессов (оборудования). — М.: ВНИИС, 1994. 132 с.
- Ракин Я.Ф. Эксплуатация подшипниковых узлов трения.- М.: Россельхозиздат, 1982. 111 с.
- Расчет и выбор допусков и посадок при проектировании изделий. Рекомендации. М.: Госстандарт СССР. — 1978. — 253 с.
- Расчет точности машин и приборов / В. П. Булатов, И. Г. Фридлендер, А. П. Баталов и др. // Под общ. ред. В. П. Булатова и И. Г. Фридлендера. — СПб: Политехника, 1993.-495 с.
- Расчет точностных параметров сельскохозяйственной техники: Учебное пособие / Л: Ю. Андрющенко, В. М. Белов, A.A.Bечтомов и др. М.: МИИСП, 1990.-121 с.
- Романов А.Б. Исследование и расчет функциональных допусков некоторых деталей машин с учетом времени эксплуатации: Дис. .канд. техн. наук. Л., 1972. 161с.
- РД 50−98−86. Методические указания. Выбор универсальных средств измерений линейных размеров до 500 мм (по применению ГОСТ 8.051— 81). М.: Изд-во стандартов, 1986. — 84 с.
- РД 70.0009.002−86. Определение нормативов надежности и износостойкости восстановленных деталей. Руководящий документ. — М.:1. ГОСНИТИ.- 1986.-31 с.
- РД 50−635−87. Цепи размерные. Основные понятия. Методы расчета линейных и угловых цепей. Методические указания. — М.: Изд-во стандартов, 1987. 43 с.
- Ремонт машин: Учебное пособие / К. А. Ачкасов, В. В. Курчаткин, С. С. Некрасов и др. / Под ред. Н. Ф. Тельнова М.: Агропромиздат, 1992. — 560 с.135: Реклейтисг Г., Рейвиндран А"., Гэгсдел К. Оптимизация в технике. В'2-х кн.-М.: Мир, 1986.
- Рекомендации по герметизации и уплотнению узлов и агрегатов тракторов и автомобилей М.: ГОСНИТИ, 1983.- 147 с.
- Решетов Д.Н. Детали машин. М. Машиностроение, 1989. — 496 с.
- Романов А.Б. Исследование и расчет функциональных допусков некоторых деталей машин с учетом времени эксплуатации: Дис. канд. техн. наук. Л.: ЛГУ, 1972. — 161 с.
- РТН 70.0001.246−84. Критерии предельного состояния тракторов и их основных частей. М.: ГОСНИТИ, 1985.
- РТМ 10.16.0001.008—89. Предельные и допустимые параметры дизелей, их деталей и сопряжений. — М.: ГОСНИТИ, 1989. 100 с.
- Сабиров М.Х., Карепин П. А., Голубев И. Г. Расчет и оптимизация допусков на размеры восстановленных деталей. Методические указания.— М.: ВНИИНМАШ Госстандарта СССР. 1981. 39 с.
- Сафронов П.Н. Выбор рационального способа восстановления сопряжения вал подшипник качения тракторов и агрегатов: Дис. канд. техн. наук. — Л. — Пушкин: ЛСХИ- 1974. — 202 с.
- Северный А.Э., Буклагин Д. С., Халфин М. А. и др. Организация вторичного рынка сельскохозяйственной техники (Состояние, опыт, перспективы). М.: ФГНУ «Информагротех», 2001. — 92 с.
- Серый И.С. Взаимозаменяемость, стандартизация и технические измерения. 2-е изд. доп. и перераб. М.: Агропромиздат, 1987. — 367 с.
- Сковородин В.Я. Долговечность сопряжений деталей отремонтированной сельскохозяйственной техники (на примере сельскохозяйственных тракторов): Дис. д-ра техн. наук. Л. — Пушкин: ЛСХИ, 1985. — 284 с.
- Сковородин В .Я., Тишкин Л. В. Справочная книга по надежности сельскохозяйственной техники. — Л.: Лениздат, 1985. — 216 с.
- Состояние и меры по развитию агропромышленного производства Российской Федерации. Ежегодный доклад (предварительный) 2002 год. — M.: ФПТУ «Информагротех», 2003. 236 с.
- Справочник по триботехнике. В 3 т. / Под общ. ред. М. Хебды, A.B. Чигинадзе. М.: Машиностроение, 1989.
- Степанов М.В. Повышение эксплуатационной надежности цепных передач сельскохозяйственных машин. Дис. канд. техн. наук. М.: МГАУ, 1986.-223 с.
- Справочник по теории вероятностей и математической статистике / Королюк B.C., Портенко Н. И., Скороход A.B., Турбин А. Ф. М.: Наука,.1985.-640 с.
- Справочник технолога-машиностроителя. В 2-х т. / Под ред. A.M. Дальского, А. Г. Косиловой, Р. К. Мещерякова, А. Г. Суслова. М.: Машиностроение-1, 2001.
- Справочник нормировщика/Под ред. Л. В. Ахунова. -Л.: Машиностроение.1986.-458 с.
- CT СЭВ 3404−87. Теория вероятностей и прикладная статистика. Термины, определения и обозначения-М.: Изд-во стандартов, 1988. — 44с.
- Стрельников В.П. Модели отказов механических объектов // Знание. Киев, 1982.-20 с.
- Сушкевич М.В. Контроль при ремонте сельскохозяйственной техники-М.: Агропромиздат, 1988.- 254с.
- Сычев H.A. Массовое восстановление деталей сельскохозяйственной техники // Инженерно-техническое обеспечение АПК. — 1995. — С. 20—21.
- Суханов В.А. Исследование деформаций и повреждений V-образных блоков цилиндров и совершенствование технологии их ремонтах целью повышения послеремонтного ресурса (на базе двигателя ЗИЛ-130): Дис. канд. техн. наук. М.: МИИСП, 1980. — 223 с.
- Технический контроль в машиностроении. Справочник проектировщика / Под ред. В. Н. Чупырина, А. Д. Никифорова. М.: Машиностроение, 1987. -512 с.
- Технический сервис в сельском хозяйстве / П. А. Андреев. В. М. Баутин, В. Ю. Грицык и др. //Под общей ред. В. И. Черноиванова. -М., 1993. -48 с.
- ТР 10.16.0001.004−88. Технические требования на ремонт. Комбайн картофелеуборочный, прицепной КПК-3. М.: ГОСНИТИ., 1988.
- Трение, изнашивание и смазка: Справочник. / Под ред. И. В. Крагельского, В. В. Алисина. -М.: Машиностроение, 1978. -400 с.
- Труханов В.М. Надежность изделий машиностроения. Теория и практика. М.: Машиностроение, 1996 — 336 с.
- Уплотнения и уплотнительная техника: Справочник / JI.A. Кондаков, А. И. Голубев, В. В. Гордеев и др. / Под общ. ред. А. И. Голубева, JI.A. Кондакова — М.: Машиностроение, 1994. 448 с.
- Файнштейн Г. З. Вероятностные расчеты допусков с учетом технологической точности изготовления деталей. В кн.: Взаимозаменяемость и технические измерения в машиностроении / Машиностроение. Л., 1972. Вып. 6. — С. 46−54.
- Фрейдберг В.З. Исследование влияния микрогеометрии посадочных поверхностей на прочность посадки подшипников качения: Дис.. канд. техн. наук. М., 1949. — 187 с.
- Фридлендер И.Г. Расчеты точности машин при проектировании. Киев- Донецк, 1980.- 183с.
- Фролов К.В. Износостойкость и ресурс машин.- В сб.: Долговечность трущихся деталей машин. Вып.1. М.: Машиностроение, 1986.
- Халфин М.А. Качество и надежность новой и отремонтированной сельскохозяйственной техники // Техника и оборудование для села, 1998, № 5. С. 4−8.
- Хворостухин A.A., Шишкин C.B., Устинов В. Д. Восстановление несущей способности соединений с натягом. Вестник машиностроения. 1980, № 9.-С. 22−25.
- Хрусталев A.A., Булкин В. А., Дулатов Ю. А. Уплотнения вращающихся валов. Казань, 1978 39с.
- Цыпцын В.И. Повышение долговечности отремонтированных дизелей совершенствованием технологии приработки и применением упрочняющих покрытий: Автореф. дис. д-ра техн. наук. — М.: МИИСП, 1991.-36 с.
- Челпан JI.K. Предельные и допускаемые технико-экономические параметры дизелей, размеры деталей и соединений при ремонте: Автореф. дис. канд. техн. наук. М.: МИИСП, 1990. — 44 с.
- Черепанов С.С., Михлин В. М., Халфин М. А. Северный А.Э. Научные основы технической эксплуатации сельскохозяйственных машин. — М.: ГОСНИТИ, 1996.-360 с.
- Черноиванов В.И. Организация и технология восстановления деталей машин. М.: Агропромиздат, 1989. — 336 с.
- Черноиванов В.И., Халфин М. А. Качество и надежность техники в сфере ее производства и эксплуатации // Тракторы и сельскохозяйственные машины, 2000, № 11. С. 41−43.
- Шпилько A.B., Драгайцев В. И. Методика определения экономической эффективности технологий и сельскохозяйственной техники. — Ч. 1,2. — М., 1998.
- Экономическое обоснование внедрения мероприятий научно-технического прогресса в АПК (методические рекомендации и примеры расчета). Конкин Ю. А., Пацкалев А. Ф., Лысюк А. И. и др. М.: МИИСП, 1991.-81 с.
- Юрченко Н.И. Повышение работоспособности поверхностей деталей, сопряженных с манжетами уплотнительных устройств сборочных единиц энергонасыщенных тракторов: Дис. канд. техн. наук. -М.: МИИСП, 1991. 324 с.
- Якушев А.И., Бежелукова Е. Ф., Плуталов В. Н. Допуски и посадки ЕСДП СЭВ для* гладких"цилиндрических: деталей (расчет и выбор): — М.: Изд-во стандартов, 1978. 256 с.
- Якушев А.И., Воронцов JI.H., Федотов И. М. Взаимозаменяемость, стандартизация и технические измерения — М.: Машиностроение, 1986. — 420 с.