Разработка комплексной технологии переработки сложной полиметаллической руды месторождения Санта Люсия (Республика Куба)
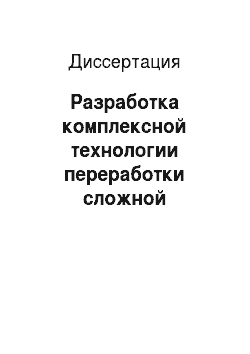
Установлено, что высокотемпературное (900 — 1250°с) хлорирование различных огарков окислительного обжига, содержавших 6,54 — 8,2% цинка- 2,45 — 2,55% свинца- 2,08 — 7,0% серы, в оптимальных условиях процесса (температуры .окислительного обжига руды и хлорирования огарка соответственно 500 — 700 и 1000 — Ц00°С расход хлорида натрия 8 $, продолжительность 3 ч) позволяет извлекать в возгоны 96 — 98… Читать ещё >
Содержание
- ВВВДЕНИЕ
- 1. Характеристика руды месторождения Санта Лгосия
- 2. Технологическая и аппаратурная схемы завода имени П. Думумбы («Сульфометалес»)
- 3. Результаты предшествующих исследований и современные методы переработки свинцово-цинковых руд и концентратов
- 4. Пирометаллуршческий вариант переработки огарка окислительного обжига
- 4. 1. Термодинамический анализ хлорирования огарка
- 4. 2. низкотемпературное хлорирование огарка. .
- 4. 3. Высокотемпературное хлорирование огарка
- 4. 4. Переработка хвостов и возгонов хлорирования
- 4. 4. 1. Переработка хвостов
- 4. 4. 2. Переработка возгонов
- 4. 5. Общее строение технологической схемы и ожидаемые показатели «.»
- 5- Гидрометаллургический вариант переработки огарка окислительного обжига
- 5. 1. Подготовка окатышей и показатели перколяционного выщелачивания гранул
- 5. 2. Низкотемпературное выщелачивание огарка
- 5. 3. Автоклавное выщелачивание кека
- 5. 4. Строение и оценка предлагаемой схемы сернокислотного выщелачивания огарка
- 5. 5. Переработка хвостов сернокислотного выщелачивания гидрометаллургическими методами
- 5. 5. 1. Растворимость хлоридных комплексов свинца
- 5. 5. 2. Экспериментальные исследования
- 5. 5. 3. Переработка хвостов солевого выщелачивания, строение общей технологической схемы и ожидаемые показатели.. V
Разработка комплексной технологии переработки сложной полиметаллической руды месторождения Санта Люсия (Республика Куба) (реферат, курсовая, диплом, контрольная)
Создание материально-технической базы социализма является одной из важнейших проблем кубинской революции, В этой задаче одно из первых мест принадлежит развитию отечественной горнометаллургической промышленности. По данным СйПЮЛМа и других институтов [бО] минералогический состав месторовдения своеобразен. Первичные минералы представлены сульфидами цинка, свинца и железаКак спутники встречаются барит и серебро. Первичные сульфидные минералы ассоциированы с карбонатами и сульфатами. По минералогическому составу, структурно-текстурным особенностям и генетическим признакам на месторождении могут быть выделены блоки: собственно колчеданной, свинцово-цинковой, баритовой свинцово-цинковой и окисленной лимонито-свинцовой руды. Колчеданные свинцово-цинковне руды составляют главную промышленную ценность месторозвдений (98,2^ запасов руды), они характеризуются минералогическим однообразием и простотой. Показанные компоненты, в основном, представлены сульфидными формами. Распространение разностей неравнозначно. Массивные руды составляют 85,6^ всех запасов, вкравленнне — 14,4^- брекчиевидные руды встречаются лишь в единичных случаях. По распределению основных рудных компонентов (серы, железа, свинца и цинка) выделяются три главные зоны: в подошве рудной залежи со средним содержанием цинка 6i9 — 8t8% и свинца 1,8 2.2- в средней части залежи с максимальным содержанием цинка 9.3 — 14,8% и свинца 1,9 — 7,8%- в верхней части залежи, которая характеризуется содержанием цинка 5,2 9,1% и свинца 1,7 4.8%.Текстура руды имеет чрезвычайно тонкую зернистость. В большинстве случаев величина зерен рудных минералов составляет несколько микронов. Наблюдаемая полосчатость связана с чередованием различных сульфидов и прослоек рудных и нерудных влинералов. Преобладающая мощность прослоек 0,8 — 1"5 мм. Основным минеральным компонентом криптокристаллических руд является микрозернистый марказит в тонком срастании с галенитом и сфалеритом, размеры зерен сульфидных. агрегатов колеблются в пределах 4 — 1 5 мкм. нерудная часть представлена карбонатным материалом.2. ТЕШ) Ж)ШЧЕ (ЖАЯ И АППАРАТУРНЫЕ СХЕМЫ ЗАВОДА И М Ш. Л Ж 7 М Ш («СУЛЬФОМЕГАЛЕС») Завод им. П.Лумумбы был введен в эксплуатацию в I96I году с целью переработки пиритной руды рудника им. хулио А.Мелья. Завод проектировали, исходя из среднего содержания в руде {%): 2,0 меди- 3,5 цинка- 1,2 свинца- 35 железа- 41 серы и (г/т) 75 серебра и 6 золота при производительности по руде 100 000 т/год.По проекту рафинировочного цеха медный цементат предварительно гранулировали, сушили и плавили на черновую медь. Ее подвергали огневому и электролитическому рафинированию. Щламы, содержащие благородные металлы, отправляли на извлечение золота и серебра. Свинцовый цементат сплавляли с черновым свинцом, получаемым при плавке свинцовых шламов (из отделения промывки печных сернистых газов) и рафинировали известными огневыми способами. из серебряной пены отгоняли цинк, остаток, вместе с медным шламом, купелировали до металла Д, оре. Последний намечено было перерабатывать известными приемами аффинажа^' в 1978 Г0. ИУ, в связи с закрытием рудника им'.хулжо А*Мелья, на окислительный обжиг и на производство серной кислоты стала поступать сульфидная руда Санта Люсия. в настоящее время свинцово-цинковый огарок складируется. Для его переработки могла бы быть использована аппаратура, которая, как сказано выше, сейчас частично законсервирована, а частично используется по эпизодическим заданиям. Естественно, что эти обстоятельства могут существенно влиять на выбор и обоснование перспективных технологических схем. Практически, как требующие наименьших капитальных затрат оптимальными кажутся варианты, начинавдиеся с операции окислительного обжига, однако, в этом случае малоизученной проблемой является образование ферритов цинка, До-вцдимому, их выход неизбежен и обусловлен минералогическим составом рудн^ Соответственно, должны быть непригодными обычные методы низкотемпературного сернокислотного выщелачивания. Требует дополнительной экспериментальной проверки малоизученная операция перколяционного выщелачивания огарков, так как обжиг руды даже в печах Герресгофа сопровождается значительным ее измельчением', малая степень десульфуризации, наблюдаемая при существующей переработке руды грубого помола, может сопровождаться повышенными расходами реагентов и недостаточно высоким извлечением цветных и благородных металлов при хлорировании, наконец, вполне своевременной и актуальной задачей является замена устаревших многоподовых печей современными печами КС, Новые технологические схемы должны зачитывать изменение физических свойств и вещественного состава получаемых огарков [4, 5, 8, 15, 1б]. I I к произВодстВи H2SO4, I. Мостовой, кран Z. Склад сырья 3. Бункер для сырья к.СкипоЬыи. элебатор 5. бункер печи б.Лентобыи. пи. щатель 7. Многоподобая пень в. Абарианая дымобая труба 9. Котел-j/тилизатор 10. Вентилятор II. Циклон 12. Скруббер 13. Сгуститель /4. бак 15. Насос 16. Ленточный транспортер 17. КобшеВои. элебатор 18. бункер для охлахаенною огарка 19. Склаа для огарка Z0. Бункер для огарка 21. Бункер для Natl 2Z. бункер для медного концентрата Z3. Грохот ZM. Балковая дробилка 25. Бункер для шихты Z6. Бункер печи Рис. 1. Схема цепи, аппаратов завода им. П. Лумум5ы. t = ^ Z7. Печь хлорирующего обжига Z&. и^ихлон Z9. Вентилятор 30. Проныбиая dauiHji 31. Дымобая труда 32. Увланнитель 33. Склад для огарка 3−4. Перколятор 35. Бак для растВороВ 36. барабанный цемешттор 37. Отстойник 3&. Нутч — фильтр 39. Вагонетка 40. bijHKep для с^ементата 4/. Барабанная сушилка.2. Рафинировочная печь 43. Кран 44. Электролитные банны 45. ВайербарсоЬая печь 4 В. Короткодарабанная печь 47. РаФинироВочные котлы 43. Разливочная машина 49. Дистиляционная тигельная печь 50. Купелящоиная печь 51. Электролизер 5Z. Тигельная печь 3. РЕЗУЛЬТАТЫ ПРЕЩЩЕСТВШВДХ ИССЛЕЩОМНИЙ И СОВРЕМЕННЫЕ 1У1ЕТ0ДЫ ПЕРЕРАВЗТЕСИ СВЙЩОВО-ЦЙНКОШХ РУД И КОНЦЕНТРАТОВ В настоящее время основное количество цинка и свинца получают из сульфи. дных и частично окисленных руд. условно их можно разделить на сложные свинцово-цинковые, медно-цинковые и свинцово-медно-цинковые или полиметаллические. Практически все известные технологические схемы их переработки построены на предварительном обогащении и получении богатых селективных концентратов. Соответственно, расположение металлургических заводов преимущественно тяготеет к месту потребления готовой продукции самих металлов и серы (в ви. де серной кислоты) [20, 29]. Результаты исследований, связанных с особо сложными минералогическими и структурными особенностями руды Санта Люсия, показали на малз^ перспективность традиционных методов обогащения. Вместе с тем, они определили целесообразность металлургической переработки самой руды вблизи места ее добычи'.Возможным технологическим вариантом может быть схема с операциями окислительного обжига и последующего вельцевания. Она характеризуется значительно потребностью в металлургическом топливе, неизбежными потерями других цветных и благородных металлов с клинкером, а также высокими капитальными затратами на строительство новых сооружений. Например, по практике работы цинковых заводов СССР, сквозное извлечение цинка при переработке даже намного более богатых железных кеков (15 — 2D % цинка) не превышает 70^ при расходе коксика до 55^ от массы сзгхого кека [40]. В большинстве случаев новые схемы являются многостадийными, что определяется комплексным характером перерабатываемого сырья, Их характерной особенностью является расширение масштабов использования автоклавной технологии, в этом отношении любопытны последние сообщения о широком распространений метода окислительного автоклавного выщелачивания сульфидных цинковых концентратов оборотным электролитом [36]t намного более совершенного, чем стандартный, к сожалению, этот способ применим только к относительно богатым концентратам. Автоклавная технология обладает рядом определенных преимуществ. в частности, к ним относится возможность достижения более высоких температур и концентраций газообразных реагентов. Эти факторы обеспечивает благоприятные сдаиги химических равновесий и увеличение скорости многих реакций. По этим причинам она позволяет эффективно осуществлять такие процессы, которые в обычных условиях протекают крайне медленно и неполно. Таблица I результаты выщелачивания цинковызс кеков отработанным электролитом, содержащим 130 г. дм" ^ N504 Продолжительность выщелачивания 2 часа Температура, Извлечение в раствор, % остаточная кислотность раствора, г-дм" «^ 2п Fe 80 66,0 74,2 77 100 77,0 79,6 77 130 83,2 80,1 82 160 95,3 72,8 81 190 97,47 69,4 85 220 98,31 44,3 77 В связи со сравнительно высоким содержанием в руде Санта Люсия свинца и его спутников необхо. димо вкратце остановиться на обсуждении современных технологических методов его получения. Доминирующая технология производства свинца на основе агломерации и шахтной плавки, связана с известными недостатками: громоздкостью и трудоемкостью, большим количеством оборотов, невозможностью использования тепла окисления сульфидов, низким извлечением серы, загрязнениями окружающей среды и др. В связи с этим, в последние годы большое внимание стали уделять автогенным и подуавтогенным методам прямой выплавки [з1. рафинирование свинца, в основном, ведут по двум методам: традиционному пирометаллургическому и новому электролитическому, В настоящее время удельное значение электролитического метода достигает 20^. наибольшее распространение он получил в Японии, Италии и Канаде [31]. Автоклавные методы переработки свинцового сырья пока не вышли из стадии поисковых опытов, в которых, однако, наметились два принципиально новых и различных метода, К первым могут быть отнесены приемы, основанные на окислительном выделачивании сульфида свинца в атмосфере кислорода, ко второму — выщелачиванию галенита под давлением газа-восстановителя. По первому методу стремятся окислить сульфидную серу галенита до элементарной или сульфатной формы и связать свинец или в малорастворимый сульфат, или в хорошо растворимое соединение. По второму методу свинец, по мере его перехода в раствор, восстанавливают водородом до металлического состояния f24]. Из первых методов обращает на себя внимание способ, разработанный во Франции и основанный на гицрометаллургической переработке низкосортной сульфидной руды, он повволяет селективно переводить в раствор цинк, свинец и серебро, оставляя в нерастворимом остатке пирит [48]. Его осуществляют в несколько стадий. Как сле.дует из приведенного обзора современных методов переработки полиметаллического сырья сложного состава для руды месторовдения Сайта Люсия могут быть предложены многие метода. Их выбор, обеспечивающий наиболее полное извлечение ценных компонентов при наименьших материальных затратах, одновременно требует учета производственных возможностей существующего завода им. П.Лумумбы. Наиболее перспективные из них, принятые к экспериментальной проверке, детально рассматриваются ниже, 4. ШРОгЛЕТАМУРТМЕСМЙ BAHIAHT ПЕРЕРАБОТКИ ОГАРКА ОКИСЖТЕЛЬЮГО ОББИТА Как известно, топливные ресурсы Кубы заметно ограничены, и это обстоятельство практически отвергает возможность промышленной реализации таких хорошо освоенных (и, вместе с тем, технически устаревших) способов, как дистилляции, вельцевания и др. Для сравнительно бедного полиметаллического сырья, как огарок руды Сайта Люсия, современным и прогрессивным методом переработки материалов близкого вещественного состава, например, пиритных огарков, следует считать приемы хлорирования, различные варианты этой технологии хорошо освоены во многих промышленноразвитых странах [II]. ЕЕ сущность сводится к реакциям взаимодействия ценных компонентов сырья (тяжелых цветных и благородных металлов) выбранным хлорирующим агентом, например хлоридом натрия, протекающим с получением соответствующих хлоридов», известные ограничения промвшиленной реализации технологии, по существу, сводятся к высоким затратам на приобретение хлоринатора и возможности образования легкоплавких солевых эвтектик за счет хлорирующихся металлов 2-й группы (Со, Мд и др.). В данном случае эти ограничения существенного значения не имеют. В настоящей работе исследованы технологические особенности и определены технические показатели обоих вариантов хлорирования огарка. В обычных условиях окисление. диоксида серы до триоксида SOz + '/гОг-5=^ 5 0 з идет крайне медленно и практически возможно лишь в присутствии катализаторов — металлической платины, пятиокиси ванадия и др. Хотя эти реакции 8 и протекают с небольшим изменением энергии гиббса, но их црактическое развитие, по-видимому, должно определяться реакционной, способностью оксидов шихты и, в частности, скоростью промежуточных реакций ферритов цинка (свинца) с хлористыгл водородом. Соответственно, вариант низкотемпературного хлорирования предопределяет последующее выщелачивание всего потока рудного материала, По сравнению с высокотемпературным вариантом он позволяет использовать имеющиеся печи завода им. П.Лумумбы, но менее предпочтителен в части выщелачивания. Опыты вели с пробой производственного огарка окислительного обжига завода им. П.Лумумбы, содержавшей (%): 7,61 цинка- 3,60 свинца- 43,7 железа и 5"6 серы. Крупность огарка — 3 мм. Схема экспериментальной установки показана на рис. 5. Кварцевая реторта вмещала до 300 г огарка. Во время опытов шихту периодически перемешивали специальной рукоятью. Огарки хлорирующего обжига выщелачивали слабым раствором серной кислоты (50 г. дм" '^) при отношении Т I 1 = I: I. Вместе с тем было установлено, что высокое количество сульфидов в огарке окислительного обжига (содержание серы 5f6^)f связанное с особенностями переработки крупнозернистой руды Санта Люсия Б многоподовых печах с механическим перезтребанием, требует повышенного расхода хлоринатора и может сопровождаться спеканием шихты, в этом отношении технология низкотемпературного хлорирования требует дополнительной экспериментальной проверки, Кеки, получаемые после извлечения цинка, дополнительно выщелачивали концентрированными растворами хлорида натрия (табл, 7).Было показано, что в растворы может быть извлечено до 72^ всего свинца при сравнительно низкой его концентрации (около 13 г-дм-^).Повторное использование таких растворов потребует дополнительной аппаратуры и, по-видимому, нерационально. В связи с недостаточно удовлетворительными результатами дальнейшие опыты по хлорированию были выполнены при повышенных температурах. Так как потери железа с возгонами были незначительными (в пределах 1%), то извлечение цветных металлов в газы подсчитывали по изменению содержания железа в исходном огарке и получаемых хвостах. Этот метод не требовал определения масс и, как основанный на пряглых аналитических определениях, обеспечивал получение более точных результатов, результаты опытов представлены на рис. 8 и 9 и в табл.8 — II. ЮО 80 Ь 20 и •SSSlTs При meMnepamijpe окис У1ите/)ьного обжига. Последующее выделение металлов из растворов такого состава может быть осуществлено многими методами [ Ю, 12, 21, 23, 36, 38, 40]. Можно использовать, например, известные приемы охяавдения и кристаллизации солей, цементации свинцом, железом и цинком, методы электролитического осаждения, методы сорбции и экстракции и др. На заводе «тобато», перерабатывающего ме. дистые пжритные огарки, свинец, серебро и золото, при принятом водном выщелачивании, остаются в шламах, медь цементируют железным скрапом, цинк осаждают добавками СаО. Хиглический состав руды Сайта Люсия и получаемых растворов хлоридовозгонки своеобразен и требует. других решений.Ожидаемые объемы материальных потоков, реагентов и готовой продукции показаны на рис. 12.
ВЫВОДЫ.
Настоящие исследования направлены на выполнение решений П-го Съезда ШЖ и Программы научно-исследовательских работ Министерства основной промышленности республики Куба по развитию производства цинка, свинца и барита на заводе им. П.Лумумбы из руды месторождения Санта Люсия. Эта руда отличается чрезвычайно тонкой вкравленностью сульфидных минералов и практически непригодна .для ее переработки традиционными методами флотационного обогащения. На заводе им. П.Лумумбы руду Санта Люсия используют только для получения серной кислоты, а получаемый свинцово-цин-ковый огарок временно складируют. Многие производственные возможности завода используются неполно и не по назначению. Предшествующие научно-исследовательские работы показали, что, как сама руда, так и огарок окислительного обжига, могут быть переработаны только по сложным технологическим схемам, не обеспечивающим ни полноты извлечения ценных компонентов, ни экономичности общего производства, целью настоящих исследований была разработка более прогрессивных технологических схем, построенных на современных достижениях отечественной и зарубежной металлургии. Конечные результаты исследований представлены в форме двух технологических вариантов, экспериментальные параметры и конкретное обоснование которых могут быть суммированы в следующем виде.
Пирометаллургический вариант.
I. Топливные и энергетические ресурсы Кубы сравнительно ограничены, и целесообразность промышленной реализации традиционных пирометалдургических способов переработки огарка маловероятна. Вместе с тем, могут быть перспективными современные приемывысокотемпературного хлорирования, протекающие с применением тверда хлоринаторов при сравнительно умеренных расходах топлива.
2. Термодинамический анализ возможных реакций хлорирования огарка с применением хлорида натрия показал, что в области температур 973 — 1473 К энергия Гиббса возрастает, а реакционная способность компонентов огарка снижается в следующей последовательности:
PBS—* PBD—*P?SO".
Влияние температуры неоднозначно. Вместе с тем, была подчеркнута катализующая роль образующегося хлористого водорода.
3. Экспериментальные исследования хлорирования с добавками хлорида натрия (4 — 8%) рядового производственного огарка завода (7.61 $ цинка- 3,60 $ свинца- 5,60 $ серы) при 400 — 750 °C, при которых образующиеся хлориды цветных металлов, в основном, оставались в твердой фазе, достаточно удовлетворительных результатов не дали. В оптимальных условиях (550 — 560 °C, 8% NaCL, продолжительность хлорирования 5 ч) извлечение цинка и свинца в растворы последующего выщелачивания составляло всего лить 70 — 80%. Вариант низкотемпературного хлорирования казался также непрактичным из-за необходимости более сложной 2-х ступенчатой гидрометаллургической переработки всей массы материала (водой и растворами хлорида натрия) и, связанными с этим, усложнениями общей схемы.
4. установлено, что высокотемпературное (900 — 1250°с) хлорирование различных огарков окислительного обжига, содержавших 6,54 — 8,2% цинка- 2,45 — 2,55% свинца- 2,08 — 7,0% серы, в оптимальных условиях процесса (температуры .окислительного обжига руды и хлорирования огарка соответственно 500 — 700 и 1000 — Ц00°С расход хлорида натрия 8 $, продолжительность 3 ч) позволяет извлекать в возгоны 96 — 98% цинка и 98 — 99% свинца. Хвосты хлорирования содержат всего лишь около 0.15% цинка, 0,03% свинца и, после отмывки от растворимых солей (сульфата и хлорида натрия), доступны для последующего обогащения с целью получения железного и баритового концентратов. Возгоны, после их улавливания в системе мокрой газоочистки и выделачивания, обеспечивают получение достаточно концентрированных растворов, исходя из их состава, предложена новая технологическая схема переработки, включающая стадии цементации тяжелых цветных и благородных металлов цинком и получения свинцовой лигатуры (доступной .для последующей переработки в существующем аффинажном цехе завода), упарки и электролиза солевого расплава хлоридов с получением металлического цинка и элементарного хлора.
5. При промышленной реализации возможная производительность завода (при переработке 100 ООО т руды/год), составит (т/год): железного концентрата — 50 ООО, баритового концентрата — 4 ООО, цинка — 6 ООО, свинца — 2 500, меди — 20, кадмия — 90.
6. По практике работы аналогичных производств можно ожидать, чтов в конечную продукцию завода также удовлетворительно будет извлекаться рудное серебро.
7. В варианте хлорирования, рекомендуемое снижение температуры окислительного обжига руды (до 600 — 700° вместо 700 -850°с), по-видимому, йудет сопровождаться некоторым снижением производительности действующих печей.
Гидрометаллургический вариант.
8. Опыты по гранулированию огарков, имевшие целью использование имеющегося перколяционного оборудования завода им. П.Думум-бы, не дали положительных результатов. Хотя и было найдено связующее (окись кальция), обеспечивающее достаточно высокую устойчивость гранул при последующем сернокислотном и солевом (хлорид натрия) выщелачивании, показатели этих операций были неудовлетворит ельными. Извлечение цинка и свинца в растворы не превышало 40 — 60%• При этом, продолжительность выщелачивания достигала 50 — 72 ч. Кроме того, условия сернокислотной обработки казались несовместимыми с выполнением задач по очистке растворов в «нейтральной» стадии типовой 2-х ступенчатой схемы.
9. Ери механическом перегревании материала в многоподовых печах и наблюдаемой декрипитации пирита рудные огарки Санта Лю-сия заметно измельчаются. Эти изменения ориентируют на гидрометаллургическую обработку суспензий.
10. При низкотемпературном (35 — 40°С) выщелачивании огарка, полученного при 800 °C и содержащего (%): 7,25 цинна- 4,38 свинца;
47,2 железа- 2"80 серы, в реакторе с механическим перемешиванием я при Ж: Т = 5: I и начальной кислотности раствора 5−50 г. да в раствор извлекается до 40 $ цинка и до 0,3 $ железа. При этом, основная масса экстратигуемого цинка (кадмия, меди и железа) переходила в раствор в течение первых нескольких минут, увеличение продолжительности выщелачивания и кислотности растворов сказывается незначительно. Было показано, что неактивные формы цинка представлены упорными ферритами. Условия «нейтрального» выщелачивания надежно сохраняются до полноты извлечения цинка около.
II. Для разложения ферритов цинка и выполнения последующей «кислотной» стадии типовой схемы были выбраны условия высокотемпературного (автоклавного) выщелачивания, из соображений устойчивого формирования гематитного осадка и окисления сульфидов опыты вели при возможно минимальной температуре 200 °C и отношении Ж: Т = = 2: I. Сборный кек нескольких опытов низкотемпературного выщелачивания (ом.п.10) содержал (%)г 4,59 цинка- 4,25 свинца;
51,5 железа и 1,7 серы, установлено, что в первую очередь происходит окисление сульфидов до сульфатов, а затем, при достаточной кислотности растворов (20 — 25 г. дм" «^ и более), избирательно разрушаются ферриты цинка. При продолжительности процесса 3 ч в раствор переходит 94 — 96% цинка и сопутствующие ему кадмий и медь. Снижение содержания железа в растворах до равновесных значений (около 0,5 г. даГ^), достигается небольшими добавками пиролюзита.
12. Автоклавное выщелачивание кека нейтральной стадии вели при интенсивности перемешивания = 1300 — 1500. Соответственно, промышленная аппаратура этой операции должна иметь простые конструктивные решения.
13. Балансовыми расчетами материальных потоков узла выщелачивания, составленными на основе полученных экспериментальных данных, определено, что с учетом растворения части цинка (кадмия, меди) на первой стадии, общее извлечение цинка будет достигать 96,5%, удельный расход кислоты составит ИЗ кг/т руды или около 13 $ от общего количества, получаемого на заводе.
14. При технически возможных отношениях Ж: Т при нейтральном и кислотном выщелачивании огарка (соответственно 5: I и 2:1) конечные растворы получаются сильно разбавленными (содержание цинка около 14 г. дм" ^). в предлагаемой технологической схеме выделение тяжелых цветных металлов принято в форме карбонатов.
15. После извлечения цинка (кадмия, меди) логически последовательной операцией будет экстракция свинца и его спутников. Традиционными методами извлечения этих металлов из материалов близкого вещественного состава (главным образом, сульфатов) являются приемы выщелачивания сырья концентрированными растворами хлоридов. Теоретическое исследование равновесий в системе хлориды свинца — вода показало, что хвосты должны выщелачиваться растворами с возможно высокой концентрацией посторонних хлоридов. Применительно к условиям Кубы предложены растворы с содержанием хлорида натрия 300 г. дм" «3. Экспериментально установлено, что выщелачивание хвостов, содержащих ($): 0,22 цинка- 4,35 свинца и 52,3 железа при Ж: Т = 5: I и 90 °C позволяет извлекать до 92 $ свинца и получать сравнительно богатые растворы (до 8 г. дм» 3). Для их переработки предложены известные методы цементации свинца и его спутников (висмута, серебра) железным скрапом с последующим рафинированием свинцового сплава на имеющемся оборудовании завода им. П.Лумумбы. Отвальные кеки богаты железом (около 55 $ масс.) и могут рассматриваться как потенциальное сырье черной металлургии. Определено строение общей технологической схемы, ожидаемые показатели, возможная производительность завода. Применительно к условиям, изложенным в п. 10 — 15, она составит (т/год): железного концентрата — 50 ООО, баритового концентрата — 4 ООО, цинка, меди и кадмия в карбонатном концентрате, соответственно, 6 100, 20 и 90, свинца — 2 100.
Техническое сравнение вариантов.
16. За исключением хлора, количество материальных ценностей в возможной продукции завода (см. п.5 и 15) приблизительно однозначно. однако, в качественной оценке продукции, расходов реагентов, содержанию и объемам строительства новых сооружений, оба варианта заметно различны. При переработке руды в количестве 100 ООО т/год они характеризуются следующими показателями:
Продукция завода Пирометаллургический Гидрометаллургический вариант вариант.
Цинк, т/год 6 ООО 6 100.
Свинец т/год 2 500 2 100.
Медь т/год 20 20.
Кадмий т/год 90 90 Хлор т/год 6 700.
Качественная оценка Лигатура, содержаЧерновой свинец, основной продукции завода щая рй.си.сл/в^/ц) содержащий вси а<,.
Металлический карбонатный кон-цинк центрат, содержащий 1п, Са, СА.
Расход основных реагентов.
Хлорид натрия, т/год 14 ООО.
Сода кальцинированная, т/год — II ООО.
Серная кислота, т/год — II 300.
Пиролюзит, т/год — 430.
Скрап железный, т/год — 600.
Объемы потока перерабатываемых растворов, тыс.куб.м/год 100 700.
Новые металлургические Агрегат по высокотеустановки для сер-установки на заводе мпературному хлоринокислотного выщерованию огарка лачивания огарка установки для выщеустановки .для со-лачивания возгонов и левого выщелачива-переработке раствония свинца и спут-ров с последующей ников с последую-цементацией цветных щей цементацией металлов цветных металлов.
Электролизер для получения металлического цинка.
В целом, из анализа предшествующих научно-исследовательских работ, определения свойства руды Санта Люсия и производственных возможностей завода им. п.ЛУмумбы, результатов собвтвенных экспериментальных исследований и их обработки, выявлены и предложены два перспективных технологических варианта. Их техническое обоснование достаточно для проектирования и строительства опытной пилотной установки.
Список литературы
- Авершин И.Н., Батищева Т. А., Берман Ю. А. и др. Справочник по обогащению руд. Специальные и вспомогательные процессы, испытания обогатимости, контроль и автоматика. Под ред. О. С. Богданова, В. И. Ревнивцева, 2-е изд. м., Недра, 1983, 384 с.
- Бородина В. А. Соколов М.А., Иванова м.Т. и др. Бия. «Цветная металлургия», 1965, J? 18, с. 9 12.
- Васкевич А.Д." Зайцев В.Я." Ванюков A.B., и др. «Цветные металлы», 1979, Ш II, с. 45 48.
- Гецкин I.e., Абрамовская I.A., Ярыгин В.й. «Цветные металлы», 1980, й 5, с.32 35.
- Гецкин I.C., Ярыгин В. И., Ремизов Ю. С. «Цветные металлы», 1979, & 10, с.9 13.
- Громов Б.В. Физико-химические основы гидрометаллургического извлечения свинца. М., 1946.
- Громов Б.В. Ж1Х, 1940, Ш 3, с.337 344.
- Гудима Н.В., Шейн Я. П. Краткий справочник по металлургии цветных металлов, М., Металлургия, 1975, 536 с.
- Доброхотов Г. Н. Известия ВУЗов «Цветная металлургия», 1979, № 3, с.65 79.
- Доброхотова Е.Г. Известия ВУЗов, «цветная металлургия», 1983, № I, с.75 78.
- Зак М. С. Переработка бедного полиметаллического сырья методом хлорирования. М., ЦНИИЦВЕТМЕТ, 1980, 48 с.
- Зак М.С., Пилипчук H.A., Клушин Д.н. и др. В сб. «применение кипящего слоя в цветной металлургии», № 40, ШН^ЕГМЕТ, М., Металлургия, 1975, с. 84 90.
- Зеликман А.Н., Больдман Г. М., Беляевская I.B. Теория гидрометаллургических процессов. М., Металлургия, 1983, 423 с.
- Киргинцев А.Н., Трушникова л.Н." Лаврентьева в.Г. Растворимость неорганических веществ в воде. Л., Химия, 1972, 248 с.
- Клушин Д.И., Бессер А. Д., Бимбаеов K.M. и др. «Цветная металлургия», Вол. НТИ. 1972, 17, с. 23 26.
- Клушин Д.Н., Бессер А. Д., Бимбаеов K.M. «Цветные металлы», 1971, № 3, с.31 32.
- Клушин Д.Н., Резник И. Д., Соболь С. И. Применение кислорода в цветной металлургии, М., Металлургия, 1983, 264 с.
- Коренман И.М. ЮХ. Т. ХУ1, Вып.2, 1946, с.157 164.
- Коршунов И.А., Креснякова З. В. ЗЮХ, Т. XX, Вып.2, 1950.
- Лексин В.Н., Токарева А. Г. Экономика комплексного использования полиметаллического сырья. М., Металлургия, 1968.
- Лексин В.Н., Токарева А. Г. Экономика комплексного использования сырья в цветной металлургии. М., Металлургия, 1976.
- Лурье Ю.Ю. Справочник по аналитической химии. М., 1979, 480 с.
- Маргулис Е.В. В сб. Итоги науки и техники. Металлургия цветных металлов. М., ВИНИТИ, 1982, т.14, с.67 102.
- Масленицкий И.Н., Доливо-Добровольский В.В., Доброхотов г. Н. и .др. Автоклавные процессы в цветной металлургии. М., Металлургия, 1969, 349 с.
- Мурач H.H. Справочник металлурга. М., ГНТИ, 1953, 1154 с.
- Надинская О.В., Халемский В. М., Романова Г. В. и др. В сб. Применение кипящего слоя в цветной металлургии. В 40, ШНЦВШЕГ, М., Металлургия, 1975, с. Ш П5.
- Равдель A.A., Пономарева А. М. Краткий справочник Физико-химических величин. Л., Химия, 1983, 232 с.
- Рузинов Л.П., Гуляницкий Б. С. равновесные превращения металлургических реакций. М., Металлургия, 1975, 416 с.
- Севумян Ю.Р. Оптимальное распределение полиметаллическогосырья. М., металлургия, 1982, 112 с.
- Смирнов В.И., Тихонов А. И. Обжиг медных руд и концентратов. М., Металлургия, 1966, 256 с.
- Смирнов м.П. Рафинирование свинца и переработка полупродуктов. М., Металлургия, 1977, 282 с.
- Снурников А.П. Гидрометаллургия цинка. М., Металлургия, 1981, 384 с.
- Соболь С.И. В сб.обогащение, Металлургия цветных металлов и метода анализа. Научные труда. № Ю ШНПВЕТМВГ, 1955, с.155−168.
- Тарабаев С.И. Солянокислотный метод в металлургии свинца и цинка. АН Каз. ССР, Алма-Ата, 1962, 196 с.
- Теслицкая M.B., Разгон Е. С. Новые способы переработки цинк-сод ержащего сырья за рубежом. М., ЦНИИЦВЕТМЕТ, 1980, 44 с.
- Теслицкая M.B., Разгон Е. С. Новые способы переработки цинк-содержащего сырья за рубежом. М., ЦНИИЦВЕТМЕТ, вы.1, 1984, 44 с.
- Цефт А.Л., Васильева В. А., В сб. металлургическая и химическая промышленность Казахстана. Алма-Ата, 1962, с. 33 40.
- Чйжиков Д.И. Металлургия тяжелых цветных металлов. АН СССР, М., 1948, 1057 с.
- Шнеерсон Я.М., Онецкая A.A., Борбат В. Ф. и др. Выщелачивание сульфидных материалов. М., ЩШЦВЕТМЕТ, Вып.2, 1984, 46 с.
- Ярославцев A.C., Смирнов В. И. Цветные металлы, 1965, № 5, с.26 29.
- Яцилирский К.Б., Васильев в.П. Константы нестойкости комплексных соединений, М., АН СССР, 1959, 207 с.
- Исследования о возможной оценке руда месторождения «Санта. „Люсия“. отчет IMNR RUMANIA, 1974.
- Изучение обогатимости руда месторождения „Сайта Люсия“. Куба. Отчет ЦНИГРЙ. М. 1975.
- Технологическое опробование на обогатимость руды Санта Люсия. Отчет НИПРОРУДА» Болгария, 1974.
- Състояние и нясоки на развитие в гидрометалургията на цинка. Металургия, 1982, 37, Л 9, с. 25 29.46″ Basset J.L. Eng.a.Min.J. 1931, V.182,H° 9, р.99−101.
- Bounds O.J. of Metals, 1983, V.36, № 8, p.30−36,
- Demarthe J. M Georgeaux A" Hydro metallurgical treatment of complex sulphides. Complex Metallurgy*78,1978, p.113−120.49. (Jarcia Graciela, Serak Alois. Enriquecimiento de las menas del yacimiento Santa Lucia por metodos hidrometalurgicos, С1РШМ, 1973.
- Hernandez Е.Б. La Mineria en Cuba, 1977″ V.3, № p.38−43.5Ie Kuxman U. Esna-Ashari M. Erzmetall, 1975, 5, s.244−248- № 6, s. 277−283.
- Michael J. Meixner, Erzmetall, 1977″ Bd 30, Hf 5, s.204−208.
- Nogueira E.D. Chemistry and Industry, 1980, Jan, p.63−67.
- Nogueira E.D. Complex Sulphide Ores. Pap.Cont.Rome, 1980, p.227−233.
- Shelton S. Int.Met.Eevs. 1976, 7.21 ,№ 9, p.141−147.
- Lineamientos economicos y sociales para el quinquenio 1981−1985. Editora Politica, La Habana, 1981.57. «Mining Mag», 1975, 132, 5, c. 342−347.
- Энгельгарт Д.В. Электрометаллургия водных растворов. Л., ОНТИ ХИЖЕОРЕГ" 1937, 464 с.
- Егер Г. Справочное руководство по технической электрохимии. Электрометаллургия водных растворов, м., Металлургия, 1966, 550 с.
- Кунаев A.M., Кожахметов С. М., Онаев И. А., Тонконогий A.B. Циклонная плавка. Алма-Ата, Наука, 1974, 388 с.
- Сычев А.П., Чередник И. М., Поляков й.П. Кивцетный способ переработки полиметаллических•сульфидных концентратов, м., ЦШИЦВЕГМЕТ, 1978, 48 с.