Приготовление нанесенных катализаторов и их химический анализ
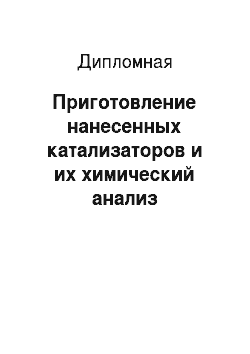
Процесс выхода катализатора на стационарный режим работы оказывается достаточно длительным (несколько часов, в зависимости от образца катализатора). При этом изменяется степень переработки метанола и производительность по отдельным продуктам: водороду, формальдегиду и метилформитату, тогда как концентрация диметилового эфира при данной температуре остается практически неизменной. Длительный… Читать ещё >
Приготовление нанесенных катализаторов и их химический анализ (реферат, курсовая, диплом, контрольная)
- Введение
- 1. Литературный обзор
- 1.1 Физико-химические процессы при приготовление многокомпонентных катализаторов (осажденных и нанесенных)
- Катализаторы получаемые методом осаждения
- Формирование поверхности гидроокисей и оксигидратов
- Влияние условий приготовления на величину поверхности силикагеля, получаемые через золь и гель
- Механизм формирования поверхностей силикагелей
- Механизм формирования поверхности гидроокисей
- 1.2 Катализаторы для процессов дегидрирования метанола
- 2. Экспериментальная часть
- 2.1 Приготовление и анализ катализаторов
- Приготовление осажденных катализаторов
- Приготовление нанесенных катализаторов
- Список литературы
Метанол — один из важнейших по значению и масштабам производства продукт, вырабатываемый химической промышленностью. На долю химической промышленности приходится три четверти потребляемого метанола, который используется в основном, как химический реагент или сырьё. Основной расход приходится на производство формалина, уксусной кислоты и продуктов метилирования. Интенсивное развитие производства метанола обуславливается постоянно расширяющимися многообразными сферами его применения. Он используется также в производстве различных аминов, поливинилхлоридных, карбамидных и ионообменных смол, в производстве красителей и полупродуктов, как растворитель, в том числе в лакокрасочной промышленности. Большие объёмы метанола расходуются для получения химикатов, например хлорофоса, карбофоса, метилхлорида и метилбромида, ацеталей и других веществ. Метанол в последнее время используется в производстве уксусной кислоты, как высокооктановая добавка к моторным топливам, сырьё для получения синтетического протеина, а также для топливно-энергетических целей. Самым крупным потребителем метанола является производство формальдегида. Формальдегид служит сырьем для производства формальдегидных смол: фенолформальдегидных, мочевиноформальдегидных, полиацетальных и прочих. В комплексе методов переработки метанола формальдегид является ключевым полупродуктом.
Наиболее рациональным с точки зрения технологии сырьём для синтеза метанола является природный газ и газы нефтедобычи, хотя метанол можно получать из различных твёрдых видов сырья, проводя его газификацию.
Все вещества получаются за счет использования катализаторов, которые должны соответствовать определенным требованиям в отношении активности и селективности. Высокая селективность может быть достигнута за счет применения многокомпонентных катализаторов, где отдельные компоненты выполняют специфические функции в общем химическом превращении.
Некоторые целевые продукты на основе метанола можно получать непосредственно из синтез-газа в одном реакторе на смеси катализаторов или на бифункциональном катализаторе, где метанол является промежуточным веществом. Эффективность производства при этом существенно возрастает. В данном процессе катализатор находится в реакционной среде содержащей водород и оксиды углерода, т. е. с высоким восстановительным потенциалом, тогда как большинство катализаторов для переработки метанола разработана для сред содержащих только метанол, или метанол и кислород. Но в восстановительных средах химическое состояние катализатора существенно меняется т.к. оксиды постепенно теряют кислород и переходят в металл, а стало быть и каталитические свойства системы также существенно меняются. Это требует проведение дополнительных исследований по влиянию состава реакционной среды на свойства катализатора, т. е. его активность, селективность и стабильность работы. Селективность катализатора определяет способ построения всей технологической схемы и экономическую эффективность производства, что стимулирует работы по исследованию и разработке селективных бифункциональных катализаторов для процессов синтеза и переработки метанола [3,4].
катализатор метанол силикагель дегидрирование
1. Литературный обзор
1.1 Физико-химические процессы при приготовление многокомпонентных катализаторов (осажденных и нанесенных)
Нанесенные металлические катализаторы представляют собой систему, состоящую из пористого материала-носителя, на поверхности которого расположены частицы металла — каталитически активного компонента.
Роль активного компонента состоит в том, что на его поверхности происходит активация молекул реагентов, их взаимодействие между собой с образованием продуктов реакции.
Носитель выполняет несколько функций:
обеспечивает высокую дисперсность и равномерность распределения активного компонента по поверхности;
играет определенную роль в отводе тепла, выделяемого в ходе химической реакции, от металлических частиц;
может изменять каталитические свойства металлических частиц за счет сильного химического взаимодействия с ними: так называемый эффект сильного взаимодействия металл-носитель;
пористая структура носителя обеспечивает транспорт молекул реагентов к активному компоненту;
геометрическая форма носителя обеспечивает необходимые гидродинамические характеристики слоя катализатора для конкретного реактора.
Для каждого типа реакций существует свой наиболее активный катализатор. Можно выделить факторы определяющие активность катализатора.
Первый фактор — это химический состав активного компонента, то есть тип химического элемента, присутствие других металлов или неметаллов, наличие на поверхности металлических частиц загрязнений и примесей.
Второй фактор-это характер взаимодействия реагирующих молекул с поверхностью металла, определяющий тип поверхностных структур, образующихся при хемосорбции реагентов, и их реакционную способность по отношению друг к другу.
Третий фактор-это структура активных центров на поверхности металлов. По сути, это влияние ближайшего окружения на химические свойства. Например, если активный центр состоит из одного атома, то его свойства определяются лигандным окружением и описываются химией координационных соединений. Если активный центр представляет собой кластер, т. е. содержит несколько атомов металла, связанных между собой химической связью, то на свойства такого центра заметное влияние оказывает объединённая система электронов всех атомов металла и лигандное окружение самой полиядерной частицы.
И, наконец, для окристаллизованных частиц их каталитические свойства зависят от структуры поверхности.
Основные требования, предъявляемые к катализаторам: высокая активность и селективность, стабильность в работе, стойкость к колебаниям температуры и большая механическая прочность в условиях реакционной среды.
Обычно при производстве нанесенных катализаторов пористую основу пропитывают раствором, содержащим не активные компоненты катализатора, а соединения, которые переходят в эти компоненты при соответствующей обработке. Чаще всего применяют соли, анионы которых можно легко удалить в процессе термообработки: нитраты, карбонаты, ацетаты и др. При синтезе металлических катализаторов сначала получают на носителях их оксиды, которые затем восстанавливают (чаще всего водородом) до металла.
Пропитка зернистого слоя в общем случае состоит из следующих стадий:
1) эвакуация газа из пор носителя;
2) обработка носителя раствором;
3) удаление избытка раствора;
4) сушка и прокаливание.
При определении числа пропиток надо учитывать, что многие широкопористые носители быстро насыщаются вносимым компонентом. При обработке же тонкопористых носителей каждая пропитка приводит к некоторому увеличению содержания активных компонентов в катализаторе и полное насыщение не наступает длительное время.
С другой стороны, следует иметь в виду, что тонкие поры при увеличении числа пропиток могут быть полностью забиты активным компонентом и не будут участвовать в катализе. При использовании пропиточных концентрированных растворов устья пор могут быть забиты солями. Для равномерного покрытия желательно иметь мультипористый носитель с крупными транспортными порами и развитой внутренней поверхностью за счет мелких пор, ответвляющихся от транспортных. В результате активный компонент в каждом конкретном случае наносится до определенного оптимума, который зависит от размера пор.
В реальных пористых носителях существует сложная система пор переменного сечения. В процессе сушки при уменьшении объема раствора в результате испарения капиллярные силы вызывают перемещение жидкости, стремящееся выровнять кривизну всех менисков.
Влияние пористости осложняется тем, что в природных и синтетических носителях существуют тупиковые поры, причем их объем сопоставим с общим объемом пор. То же можно сказать и о поверхности носителей. Возможны случаи, когда носители, имеющие сквозные поры, ведут селя подобно телам с тупиковыми порами. При полном погружении носителя в раствор пропитку будет тормозить сопротивление, которое оказывает перемещению фронта пропитки защемленный в тупиковых порах воздух. Частично такое же сопротивление оказывает и воздух, находящийся в сквозных капиллярах.
Наиболее часто применяемыми носителями для катализаторов являются оксиды алюминия, титана, циркония, хрома, цинка, кремния.
Оксид алюминия.
Оксид алюминия обладает всеми качествами хорошего носителя. Во-первых, его амфотерность, т. е. в основной среде он проявляет кислотные свойства, а в кислой — основные. Ценным для носителя качеством является высокая температура плавления оксида алюминия — немного выше 2000С. Он относится к тугоплавким оксидам, т. е. обладает замечательной способностью стабилизировать мелкодисперсные частицы катализатора и предотвращать их (имеющих более низкую температуру плавления) слипание или спекание, являясь как бы термостабилизатором катализатора.
Оксид кремния.
Подобно оксиду алюминия оксид кремния имеет несколько кристаллических форм. Оксид кремния как носитель обладает рядом свойств, которые делают его весьма полезным в тех случаях, когда оксид алюминия неприменим. Прежде всего, оксид кремния значительно более устойчив к воздействию кислой среды, а значит, в большей степени, чем оксид алюминия, пригоден для работ в таких средах. Однако щелочная среда разрушительно действует как на оксид кремния, так и на оксид алюминия, и ни один из них не пригоден для работы в основных средах.
Диоксид титана.
Подобно оксидам алюминия и кремния, образующим различные модификации в зависимости от температуры и давления, диоксид титана также имеет три модификации: брукит, анатаз и рутил.
Катализаторы получаемые методом осаждения
Осаждение-процесс образования твердой фазы в результате химической реакции при сливании растворов исходных компонентов. Переход растворенного вещества в осадок-совокупность двух процессов: образование зародышей твердой фазы и роста кристаллов или укрупнение гелеобразных частиц при одновременном их осаждении.
Методом соосаждения получают 80% катализаторов и носителей. Этот метод позволяет в широких пределах варьировать пористую структуру и внутреннюю поверхность катализаторов и носителей. Его недостаток в техническом отношении — значительный расход реактивов, большое количество сточных вод. В зависимости от природы выпадающего осадка эти контактные массы условно делят на солевые, кислотные и оксидные. Примером оксидных осажденных катализаторов являются оксидно железные контакты с различными промоторами, используемые при конверсии оксида углерода с водяным паром. В этом случае осадок представляет собой аморфный гидроксид железа в смеси с гидроксидами промоторов. При последующей термообработке полученные гидроксиды переходят в оксиды соответствующих металлов.
Различные силикагели, алюмогели, алюмосиликаты, применяемые для крекинга, гидратации, дегидратации алкилирования и изомеризации углеводородов, относятся к кислотным катализаторам. В процессе их получения при сливании соответствующих растворов выпадает в осадок кремниевая или алюмокремнивая кислота, гидроксид алюминия.
Образование солевых осажденных катализаторов сопровождается выпадением соли, из которой в последующих технологических операциях могут произойти существенные изменения, в частности разложение с образование оксидов и т. д. В плане формирования фазового состава процессы протекающие при приготовлении осажденных и нанесенных катализаторов во многом похожи (осаждение и разложение солей), но в нанесенных системах этого вещества по сравнению со всей массой катализатора относительно немного и пористая структура катализатора уже задана носителем, кроме этого там возможно химическое взаимодействие между носителем и нанесенным веществом, продукты которого могут существенно изменять каталитические свойства [5,6].
Формирование поверхности гидроокисей и оксигидратов
Гидроокиси и оксигидраты во многих случаях служат исходными или промежуточными веществами для получения катализаторов, носителей и адсорбентов. Дисперсность этих соединений является важной характеристикой, зачастую определяющей свойства конечного продукта. Наиболее распространённый способ получения гидроокисей — осаждение из раствора. Этот процесс состоит из типичных стадий, которые схематически могут быть выражены следующим образом:
Гидролиз соли> образование коагеля или геля > старение >
промывка >сушка
Каждая из этих стадий может оказать влияние на размер частиц, и следовательно, на величину поверхности конечного продукта.
Аморфные гидроокиси. Силикагель
В последнее десятилетие силикагель нашел широкое применение в промышленности. Наиболее известная область его применения — осушка различных газов и жидкостей. Силикагель широко используется также как носитель для самых различных каталитически активных веществ. Столь широкое использование силикагеля в качестве носителя обусловлено целым рядом свойств, главными из которых являются следующие:
1) Незначительная собственная каталитическая активность, в результате чего опасность протекания нежелательных побочных реакций, например изомеризации, полимеризации и др., значительно меньше, чем при использование других носителей;
2) Возможность в широких пределах изменять величину поверхности и пористую структуру, что позволяет сравнительно легко получать желаемую пористую структуру, оптимальную для данного процесса;
3) Высокая термостойкость, вследствие чего он может быть использован в широком интервале температур.
Существует много способов получения силикагеля, мы остановимся только на двух, которые представляются нам наиболее типичными для систем, получаемых через аморфные гели:
а) метод, основанный на взаимодействии исходных веществ с образованием золя и геля;
б) методы, включающие осаждение коагеля.
Влияние условий приготовления на величину поверхности силикагеля, получаемые через золь и гель
Золь обычно получают вливанием щелочного силиката при интенсивном перемешивании в сравнительно концентрированный раствор кислоты или путем одновременного сливания реагентов при интенсивном перемешивании безградиентных условиях, т. е. при постоянном рН, температуре и концентрации вещества в золе.
Полученный на первой стадии процесса золь не устойчив, с течением времени вязкость его возрастает и золь застудневает в гель, вначале мягкий и эластичный, становящийся затем твердым и хрупким. Процессы, происходящие в геле, объединяются общим названием «созревание», которое считается завершенным после наступления синерезиса, состоящего в уменьшении объема геля, появлении трещин и выделении части заключенной в нем жидкости. После окончания созревания гель промывают от солей и кислоты, сушат и прокаливают.
Авторами показано, что на величину поверхности силикагеля оказывают влияние: концентрация реагентов, рН золя, продолжительность созревания, температура и рН промывных вод [8,9].
Влияние концентрации исходного вещества на величину поверхности силикагеля, полученного через золь, исследовано Гертнером и Грисбахом [10], которые показали, что в случае золей, полученных при рН 2 и 4, при изменении концентрации SiO2 величина поверхности проходит через максимум. Положение максимума зависит от рН золя: при увеличении рН максимум снижается и смещается в область более высоких концентраций. Для золя, полученного при рН 6, величина поверхности не зависит от концентрации SiO2 в золе.
Значение рН золя также оказывает существенное влияние на величину поверхности силикагеля. При повышении рН золя кривая удельной поверхности также проходит через максимум, положение которого зависит от концентрации SiO2: для серии, А (концентрация золя 1.8 моль SiO2/л) максимум лежит при рН около 2, а для серии Б (концентрация SiO2 0,83 моль/л) — при рН около 3.5 при увеличении рН выше значений соответствующих максимальной поверхности наблюдается довольно резкое уменьшение величины поверхности от 700−800 до 200 м2/г.
Влияние продолжительности созревания. Большое влияние на величину поверхности формирующегося ксерогеля оказывает степень старения (глубина синерезиса). Уже давно показано [11], что гель, полученный из сильнокислого золя и не претерпевший синерезиса, обладает меньшей поверхностью, чем гель после синерезирса. Влияние продолжительности старения на величину поверхности силикагеля зависит от условий приготовления геля. Например, при увеличении продолжительности старения до 120 часов поверхность образцов, приготовленных при рН 6,5 остается постоянной, равной 700 м2/г.
Влияние состава промывной жидкости и пропитки гидрогелей на величину поверхности силикагелей было предметом многочисленных исследований Ней Марка с сотр. [12,13], которые обнаружили большое влияние рН промывной воды. Силикагели, промытые подкисленной водой, не зависимо от рН золя обладает поверхностью около 600 м2/г. Гели, промытые при рН 10, имеют поверхность около 400 м2/г. Поверхностью приблизительно 300 м2/г обладают гели, промытые водопроводной водой. Увеличение поверхности силикагеля, полученного в щелочной среде, при промывке подкисленной водой объяснено обменом катионов натрия на ионы водорода; уменьшение поверхности силикагеля полученного в кислой среде, при промывке водопроводной водой объяснено обменом ионов водорода на катионы кальция.
Влияние природы адсорбированных катионов на величину поверхности ксерогеля SiO2 исследовано в работе Высоцкого и Шаля. Гель, полученный при рН 4 промывали раствором соляной кислоты и растворами бикарбонатов или хлоридов натрия, кальция и калия, а затем дистиллированной водой. Найдено, что удельная поверхность силикагеля определяется природой катионов, а именно: уменьшается в ряду Н+, Са2+, Na+, K+. Уменьшение поверхности силикагеля под влиянием катионов авторы связывают с понижением гидрофильности частиц гидрогеля в местах адсорбции, что способствует их агрегации. Влияние природы катиона на величину удельной поверхности связывается с теплотой гидратации.
Температура промывки и старения также оказывает большое влияние на формирование поверхности силикагеля: с увеличением температуры величина поверхности уменьшается. Так, в работе Вольфа и Байера [15], было показано, что при увеличении температуры промывных вод от 50 до 100? С величина поверхности уменьшается от 618 до 320 м2/г. Особенно резко это влияние проявляется при температурах выше 100? С в гидротермальных условиях.
Механизм формирования поверхностей силикагелей
Изложенный выше материал позволяет сделать вывод, что для силикагелей, приготовленных описанными методами, наблюдаются сходные закономерности формирования поверхности:
а) при получении гидрогелей в условиях низких значений рН и температур образуются ксерогели с высокоразвитой поверхностью;
б) при повышении рН, продолжительности промывки и старения, а в ряде случаев и температуры величина поверхности уменьшается, особенно резко особенно в условиях гидротермальной обработки;
в) включение в состав геля катионов вследствие неполного гидролиза или в результате хемосорбции из маточного раствора обусловливает уменьшение размера поверхности.
Работами ряда авторов [16], показано, что при введении щелочного силиката в кислоту возникает мономерная кремневая кислота, которая с течением времени конденсируется, образуя молекулы поликремневых кислот:
Относительно порядка присоединения молекул мономера, мнения различных авторов расходятся: некоторые предполагают, что конденсация идет по концевым группам вследствие чего, на начальной стадии процесса полимолекула имеет линейное строение, другие считают, что конденсация протекает во всех трех направлениях. Однако, независимо от начального механизма частицы золя, образующегося в результате конденсации, имеют гигроскопические исследования, позволяющие непосредственно наблюдать образование и поведение частиц в золе. На основании этих исследований можно сделать вывод, что внутренняя часть глобулы состоит из компактной SiO2, а внешняя оболочка представлена двойным слоем, состоящим из ионов металла, гидроксильных групп и молекул воды.
Золь кремнекислоты неустойчив: с течением времени происходит дальнейшая агрегация глобул, вязкость возрастает и по истечении некоторого времени золь превращается в гель.
Согласно работе [18], имеет место следующий механизм конденсации кремневой кислоты: при рН меньше 2, когда существует динамическое равновесие между Н+ в растворе и группами ОН, на поверхности макромолекул SiO2 образуется положительно заряженные группы:
которые могут реагировать с мономерными молекулами кремневой кислоты:
При рН больше 2 поверхность частиц несет отрицательный заряд и может реагировать со следующими мономерными молекулами:
Автор считает, что так как величина поверхности силикагеля определяется размером частиц, из которых он построен, то она должна зависит от скорости и продолжительности конденсации. Поскольку при рН около 2 скорость конденсации мала, удельная поверхность силикагеля велика. При более высоких рН, скорость конденсации возрастает и соответственно снижается величина поверхности.
Если бы эти представления были справедливы, то повышения рН при осаждении, созревании и промывки приводило бы к необратимым изменениям величины поверхности. Однако, исследование [10,11,12] показали, что при снижении рН в зависимости от возраста геля происходит более или менее полное восстановление первоначальной величины поверхности. Только в случае геля, старевшего в течении длительного времени наблюдается существенная необратимость изменения поверхности.
Окончательное формирование поверхности силикагеля в основном происходит в процессе сушки, когда под действием мощных поверхностных сил, развивающихся при обезвоживании, происходит сближение глобул между собой. В результате становится возможным взаимодействия поверхностных гидроксильных групп с образованием химических связей, что и обусловливает необратимость изменений величины поверхности высушенных образцов. При этом возможны два случая: размер первичных частиц может остаться неизменным, как это наблюдалось в работе Киселева и соавт. [19], либо может существенно увеличиваться в результате коалесценции двух или нескольких частиц.
Механизм формирования поверхности гидроокисей
Дисперсность и величина поверхностей гидроокисей могут сильно варьировать в зависимости от их природы и условий приготовления. Даже для одного и того же вещества при изменении рН, температуры осаждения и других факторов величина поверхности может изменяться более чем на 2 порядка.
Рассмотрим более подробно протекание отдельных стадий процесса формирования гидроокисей.
Гидролиз. Первая стадия образования гидроокиси — гидролиз исходного вещества. Установлено, что уже при растворении соли в воде происходит быстрая гидратация катиона. С течением времени или повышением рН происходит гидролиз гидратированной частицы, при котором имеет место перенос протона по связи Ме-ОН2. Результатом этого является замещение аква группы внутри комплексного иона на гидроксил и освобождение протона. Продукты гидролиза, образовавшиеся на этой стадии процесса, конденсируются. Состав продуктов зависит как от условий образования (способа получения, рН среды), так и от природы катиона.
Конденсация. В результате полимеризации и конденсации первичных продуктов гидролиза образуются полимолекулы, которые наряду с гидроокисью могут содержать большее или меньшее количество основных (или кислых) солей. Возникающие в результате этого сравнительно крупные макромолекулы являются первичными частицами золя. Во многих случаях они имеют сферическую форму. Можно было предполагать, что для большинства гидроокисей это действительно имеет место, что частицы золя и являются первичными элементами будущей структуры ксерогеля.
Известно что, процесс образования новой фазы состоит из двух основных стадий: образование зародыша и его роста. Размер частиц определяется соотношением скоростей этих стадий.
Коагуляция. Образовавшиеся на предыдущей стадии высокодисперсные системы — золи в принципе неустойчивы и с течением времени в зависимости от условий образований и природы гидроокиси более или менее быстро коагулируют. Процесс коагуляции протекает ступенчато: в результате столкновений из первичных частиц возникают агрегаты, имеющие форму «цепей» и «гроздей» [20], в которых частицы объединены слабыми коагуляционными силами. Размеры рыхлых агрегатов первичных частиц, достигающая порядка сотен ангстрем, зависит от химической природы вещества, а для одного и того же вещества от условий образования (концентрации, рН и т. д.). В зависимости от условий получений-температуры, рН и наличия коагуляторов в среде — вторичные образования («цепи» и «гроздья») постепенно объединяются в крупные хлопья, которые со временем теряют агрегативную устойчивость и коагулируют. В отличие от первичных частиц величина агрегатов в зависимости от условий получений и возраста систем может колебаться в широких пределах: в ряде работ показано, что различные гидроокиси образую агрегаты от 200 до 1000 ангстрем. Коагуляция приводит к образованию геля (студня) или коагеля. Коагуляционные связи непрочны, и образовавшийся гель или осадок при изменении условий, например механическом воздействии или введении пептизатора, может снова превратиться в золь. Однако по мере старения геля реакционно способные группы, находящиеся на поверхности различных частиц, могут реагировать между собой с выделением воды и образованием кислородных мостиков между частицы. Возникающие, в результате этого «конденсационные структуры» значительно прочнее коагуляционных, и происходящие при их образовании изменения свойств геля необратимы.
Стадия коагуляции оказывает существенное влияние на процесс приготовления катализатора или носителя, так как от нее зависят физические свойства осадка — его объем, количество связываемой воды, фильтруемость и прочее.: чем лучше скоагулирован осадок, т. е. чем крупнее и плотнее образовавшиеся агрегаты, тем легче протекают фильтрации и отмывка продукта.
Переконденсация и коалесценция. Наряду с образованием крупных агрегатов, происходящим без изменения размеров первичных частиц, понижение свободной энергии системы может осуществляться в результате роста первичных образований. Это возможно благодаря процессам переконденсации и коалесценции. Причина переконденсации заключается в более высокой растворимости высокодисперсных частиц по сравнению с грубодисперсными, вследствие чего при подходящих условиях происходит растворение мелких частиц с последующим выделением вещества на более крупных. По аналогии с известным изменением дисперсности жидких капель этот процесс обычно называют «перегонкой» или «переконденсацией». Протеканию процесса по этому механизму благоприятствует высокая концентрация исходного вещества в растворе, и при повышении температуры и растворимости доля этого механизма возрастает.
Более распространенным процессом, приводящим к уменьшению поверхности, является коалесценция первичных частиц во время сушки гидрогеля. Глубина протекания процесса коалесценции в основном зависит от степени гидролиза исходных веществ: при малом содержании продуктов неполного гидролиза коалесценция незначительна и размер частиц близок к минимальному. С увеличением содержания основных (или кислых) солей размер частиц возрастает, а величина поверхности уменьшается.
Кристаллизация и старение. Если гидроокись способна кристаллизоваться, то скорость и глубина кристаллизации могут оказать существенное влияние на формирование поверхности ксерогеля. Наиболее четко проявляется это влияние в случае медленно кристаллизующихся и склонных к фазовым превращениям гидроокисей, для которых возможны измерения скоростей всех стадий. Типичные представители этого типа — гидроокиси алюминия, железа, хрома, меди и др. Многими авторами показано, что в большинстве случаев свежеосажденные гидроокиси этого типа не имеют определенного химического состава, содержат большие или меньшие количества сверхстехнометрической «воды» и продуктов неполного гидролиза. Различными методами установлено, что не старевшие гидроокиси состоят из сравнительно крупных бесформенных агрегатов более мелких частиц. При старении свежего осадка в воде или маточном растворе наряду с изменениями химического состава (гидролизом и дегидратацией) происходит кристаллизация. При этом крупные агрегаты распадаются, оставляя россыпь первичных частиц размером 30−60 ангстрем.
1.2 Катализаторы для процессов дегидрирования метанола
При дегидрировании метанола на гетерогенных катализаторах в качестве продуктов чаще рассматриваются метилформиат и формальдегид, хотя известны и более сложные соединения, например диметилметан (метаналь). Все эти вещества широко используются далее при получении полимерных материалов, поэтому вопросы исследования механизма этих реакций и подбора катализаторов достаточно подробно освещены в литературе [2,5]. Метилформиат образуется на медьсодержащих катализаторах в диапазоне температур 200−300 ?С, где в качестве промоторов используются щелочные металлы, т.к. активность и селективность катализатора зависит от кислотно-основных свойств поверхности. При более высоких температурах реакции, равновесная концентрация метилформиата увеличивается, поскольку реакция эндотермическая, однако, начинает преобладать маршрут его разложения на водород и монооксид углерода. В работах Розовского А. Я. обнаружено, что интенсивность маршрута разложения зависит от парциального давления метанола и метилформиата в реакционной смеси, что принципиально позволяет организовать процесс получения метилформиата не достигая глубокой степени переработки метанола за один проход через реактор. В работе [24], исследованы катализаторы CuO/ZnO с различными соотношениями меди и цинка, в данной реакции и установлено, что метилформиат, наряду с маршрутом дегидрирования метанола может получаться по реакции карбонилирования метанола. Это имеет место на катализаторах с высоким содержанием оксида цинка и большой концентрации монооксида углерода в реакционной смеси.
На медьсодержащих катализаторах наряду с метилформиатом можно получить и формальдегид. В частности, в работе исследовали нанесенную систему CuO/слюда, где состояние меди направленно изменяли от Сu2+ до Cu0, и было установлено, что на не восстановленной меди (Сu2+) при температуре до 240? С образуется только метилформиат, а на металлической меди в интервале температур 240−400 ?С только формальдегид. В катализаторах Сu0/SiO2 имеет место образования как метилформиата, так и формальдегида.
Авторы работы для подобной системы (Сu0/SiO2) констатировали, что в зависимости от состоянии меди: мелкие кристаллы СuО, кластеры Сu-O-Cu, изолированные ионы меди Cu-O-Si и парциальном давлении метанола в реакционной смеси, наряду с метилформиатом образуется диметоксиметил или происходит глубокое окисление метанола до диоксида углерода.
Методами ИК-спектроскопии показано, что разложение метанола происходит с образованием метокси групп (СН3О-), формильных групп (О-сН2), который близок по структуре хемосорбированному формальдегиду. Эти группировки взаимодействуют с поверхностными гидроксидными группами (ОН) образующие поверхностные форматы (), которые могут разлагаться или на диоксид углерода и водород, или на монооксид углерода и гидроксидную группу. Соотношение между этими группировками и скоростью взаимных переходов в конечном итоге определяют селективность катализатора.
В последнее время большой интерес вызывает реакция паровой конверсии метанола с получением водорода, который также проводится на медных катализаторах при температуре порядка 250? С [28,29]. В данной реакции высокое парциальное давление водяного пара в системе ингибирует маршруты образования различных углеводов и продуктами является только водород и диоксид углерода. В частности, в работе показано, что после удаления хемособрбированной воды, которая собственно участвует в реакции паровой конверсии основанной реакцией конверсии метанола, становится образование метилформиата. Для получения формальдегида предложен более широкий круг гетерогенных катализаторов, причем температурный диапазон их работы существенно выше. Для этой цели пригодны катализаторы, содержащие оксиды цинка, титана, натрия, в том числе и нанесенные системы на основе пористого диоксида кремния [31,32]. В тоже время, их селективность и стабильность кажутся недостаточными для промышленного использования. Из последних достижений в этой области следует отметить катализаторы Ag-SiO2-MgO-Al2O3 приготовленных так называемым золь-гель методом, заявленная степень переработки метанола и селективность по формальдегиду достигает 100%.
Дегидрирование метанола до формальдегида констатировано, как и на определенных гранях монокристаллов меди, так и на модельных медьсодержащих катализаторах, причем имеет место некоторая конкуренция маршрутов образования формальдегида и метилформиата [34,35].
Разложение адсорбированного метанола на оксиде цинка также сопровождается образованием формальдегида, однако температурный диапазон данной реакции существенно выше, чем на медных системах. Медь — цинковая композиция, является основой низкотемпературных катализаторов, для синтеза метанола и паровой конверсии монооксида углерода. Причем, оксид цинка, наряду с функцией диспергирования обеспечивает возможность обратимых фазовых переходов медного компонента и резервуара активного водорода в каталитическом процессе.
В работе [38], в реакции конверсии метанола, как в присутствии водорода, так и в его отсутствии, максимальная активность была достигнута для системы содержащей 70% CuO и 30% ZnO.
Авторы полагают, что в данной системе имеет место синергетический эффект между компонентами, а именно: метанол активируется на металлической меди образуя формильную группировку, что является лимитирующей стадией, а оксид адсорбируется и предварительно активируется метанол, образуя также метокси — и гидрокс группы, которые находятся в динамическом равновесии с таковыми на металлической меди, таким образом повышая их концентрацию и увеличивая скорость реакции. Относительно инертный пористый оксид кремния, выключающий небольшие концентрации кальция проявляет каталитические свойства при разложении метанола с образованием формальдегида при температурах примерно 500? С. Авторы работ [40], также предложен катализатор для получения формальдегида на основе SiO2, для температурного диапазона 800−900?С, что довольно сложно реализовать технически. Ими же предложено для получения производительности катализатора вести процесс в присутствии перекиси водорода. Авторы считают, что перекись водорода препятствует образованию кокса на поверхности катализатора. Таким образом, в реакции дегидрировании метанола можно ожидать синергетического эффекта при введении в состав катализатора данных компонентов.
Цель работы:
1. Приготовить катализаторы на основе соединений кремния, меди, цинка и калия и изучить влияние состава солевых систем на физико-химических свойства образцов, получаемых методом нанесения и осаждения компонентов.
2. Изучить каталитические свойства полученных модельных катализаторов в реакции дегидрирования метанола с целью получения формальдегида.
2. Экспериментальная часть
2.1 Приготовление и анализ катализаторов
Приготовление осажденных катализаторов
В наших ранних работах обнаружено [41], что при соединении аммиачно-карбонатных растворов меди и цинка и силиката калия образуются осадки, которые после отделения, сушки и прокаливания идентифицированы методами рентгенографии. В настоящей работе варьировали соотношение между исходными растворами так, чтобы получить, возможно, более дисперсные оксидные и силикатные соединения меди и цинка.
В таблице 1 представлены результаты изменения концентрации растворов от начала смешения компонентов до получения и отделения осадка (т.е. маточника). Концентрация меди в растворе несколько уменьшается, но существенно ниже по сравнению с концентрацией цинка, которая уменьшается почти на порядок. Концентрация калия снижается в меньшей степени (примерно в 5 раз), а кремния очень существенно (примерно в 30 раз), т. е. в осадке следует ожидать гидроксосиликатные соединения цинка и калия с включением меди. Анализ катализатора, в общем, подтверждает это положение. Пересчет состава прокаленной массы на оксиды показывает, что их сумма превышает 100%. Это может быть обусловлено тем, что в твердой фазе находятся также в виде гидрокарбонатов (например, КНSiO3), где роль катиона выполняет ион Н+ малярная масса которого 1, а тогда как у калия 39. Поэтому формальный пересчет состава на оскиды меди, цинка и калия неправомерен. В частности, справочные данные по фазовому составу гидросиликатов цинка и калия [42], указывают на существование именно гидрокарбонатов калия и кремния (KHSi2O5). Соединения цинка представлены гидротироанными гидрокарбонатами кремния (например, Zn4Si2O7 (OH) 2 (H2O). По нашим данным мольное соотношение катионов и анионов (Cu+Zn+K) /Si <1и соотношение зарядов катионов к анионам, также меньше единицы, что подтверждает данный тезис — в прокаленном осадке присутствуют гидроксосиликатные соединения.
Таблица 1
Анализ при приготовлении осажденного катализатора (SU-27)
№ | Анализируемые растворы и катализаторы | Концентрации компонентов, моль/л | ||||
Cu | Zn | K | Si | |||
Исходный раствор МЦАКР (120 мл) К2SiO3 (180 мл) | 0.100 | 0.490 | 1.200 | 0.600 | ||
Начальные концентрации при смешении растворов | 0.040 | 0.196 | 0.720 | 0.360 | ||
Фильтрат после отделения осадка | 0.035 | 0.026 | 0.120 | 0.014 | ||
Прокаленный катализатор (400°С) пересчет на металлы пересчет на оксиды | Содержание компонентов, мас. % | |||||
1.57 1.96 | 25.44 31.66 | 10.34 12.96 | 33.00 70.70 | |||
Сумма оксидов 117.28 мас. % | ||||||
Мольное соотношение компонентов в катализаторе | 0.021 | 0.33 | 0.22 | 1.00 | ||
[ (Cu+K+Zn) /Si] мол. =0.571 ?Zi+/? Zi—=0.46 | ||||||
В таблице 2 сведены результаты анализа осажденного катализатора, где варьировали составы и соотношения исходных аммиачно-карбонатных и силикатных растворов. Установлено, что принципиально можно варьировать состав катализатора, хотя, разумеется, соотношения между составов растворов и осадка нелинейное, и для каждого интервала концентрации требуется детально экспериментальная проработка системы.
Удельная поверхность образцов определенная методом бэт дает значение от 10 до 23 м2/г в интервале прокаливания образцов 400−600 ?С, при более высокой температуре пористая структура осажденного катализатора существенно меняется, за счет агломерации частиц и спекания. Удельная поверхность существенно уменьшается порядка до 2−3 м2/г.
Таблица 2
Условия приготовления и состав осажденных катализаторов
№ | Наименование и тип катализатора | Условия приготовления | Химический состав катализатора, мас. % | Уд. Поверхность, м2/г | |
SU-15 СuO. ZnO. K2O. SiO2 Начальные концентрации: (Сu+Zn) =1.33моль/л K=0.66 моль/л Si=0.33 моль/л | Осаждение из раствора МЦАКР (100 мл). Состав: Cu=1 моль/л, Zn=1 моль/л. раствором K2SiO3 (50 мл) Si=1 моль/л | Cu=12.6 Zn=44.8 K=1.2 Si=21.9 | Не определяли | ||
SU-22 СuO. ZnO. K2O. SiO2 Начальные концентрации: (Сu+Zn) =0.9 моль/л K=0.4 моль/л Si=0.2 моль/л | Осаждение из раствора МЦАКР (150 мл). Состав: Cu=0.25 моль/л, Zn=0.94 моль/л. раствором K2SiO3 (50 мл) Si=0.81 моль/л | Cu=3.0 Zn=30.0 K=7.1 Si=13.0 | 15.1 12.1 (Tпр=600?C) | ||
SU-24 СuO. ZnO. K2O. SiO2 Начальные концентрации: (Сu+Zn) =0.3 моль/л K=1.2 моль/л Si=0.6 моль/л | Осаждение из раствора МЦАКР (100 мл). Состав: Cu=0.25 моль/л, Zn=0.94 моль/л. раствором K2SiO3 (300мл) Si=0.81 моль/л | Cu=3.2 Zn=27.3 K=14.0 Si=18.3 | 23.3 12.7 (Tпр =600?C) | ||
SU-27 СuO. ZnO. K2O. SiO2 Начальные концентрации: (Сu+Zn) =0.24 моль/л K=0.65 моль/л Si=0.324 моль/л | Осаждение из раствора МЦАКР (120 мл). Состав: Cu=0.10 моль/л, Zn=0.49 моль/л раствором K2SiO3 (180мл) Si=0.54 моль/л | Cu=1.6 Zn=25.4 K=10.3 Si=33.0 | 18.0 2.3 (Tпр =600?C) | ||
Разложение осадка при термообработке методом термографии которая представлена на рисунке 1. Потеря массы происходит на всем изученном интервале температур от комнатной до 700? С, что сопровождается выделением в газовую фазу паров воды примерно с постоянной скоростью. Но в интервале температуры примерно 140−220?С имеет место, резкое падение уменьшения массы образца с выделением в газовую фазу углекислоты, аммиака и воды, что можно отнести к разложению аммиачно-карбонатного комплекса меди и цинка по реакции:
Zn (NH3) 4CO3. nH2O>ZnO + 4NH3+ CO2 +nH2O (1)
Данные рентгенографического анализа прокаленных образцов представлены на рисунке 2. В зависимости от состава катализатора существенно изменяется дисперсность оксидных фаз меди и цинка. В образцах с относительно высоким содержание меди и цинка и низким содержанием калия, оксиды меди и цинка представлены крупными кристаллитами, но на всех изученных образцах проявляется так называемый диффузный галлофон в районе углов дифракции 2и от 22 до 25 градусов, которая принципиально отличается от галлофона чистого SiO2 расположенного в районе углов дифракции от 16 до 27 градусов. Его мы относим к мелкодисперсной фазе силикатов цинка и меди, характеризующимся максимумом межплоскостного расстояния порядка 3,1 ангстрем. Поскольку, гидросиликаты цинка имеют слоистую структуру данные значения рефлекса очевидно характерно расстояние между слоями. при более высокой температуре прокаливания 600? С кристалличной данной фазы увеличивается, а расстояние между слоями практически не меняется.
Приготовление нанесенных катализаторов
Качественно данный состав катализатора можно реализовать и в нанесенных системах, где в качестве носителя используется силикагель с большой удельной поверхностью. В наше работе мы использовали марки ШСМ (шариковый силикагель мелкопористый) с удельной поверхностью примерно 200 м2/г и марки КСК (кусковой силикагель крупнопористый) с удельной поверхностью 150 м2/г. В качестве пропитывающих растворов также использовали аммиачно-карбонатные растворы меди и цинка, а также карбонатные и силикатные растворы калия. Перечень приготовленных Т.о. образцов, приведен в таблице 3. Данный метод представляет большею возможность для регулирования химического состава катализатора, что достигается изменением качественного состава и концентрации пропитывающего раствора. Калий в систему вводили двумя способами:
1) в аммиачно-карбонатном растворе растворяли гидрокарбонат калия и этим раствором пропитывали силикагель, далее образцы просушивали при температуре 100? С и далее прокаливали при температуре 400? С;
2) носитель пропитывали раствором силиката калия, образец просушивали и пропитывали аммиачно-карбонатным раствором меди и цинка, просушивали и прокаливали. При повторной пропитке, часть калия растворялась в растворе, поэтому концентрация в готовом катализаторе получается ниже, чем в модифицированном силикате (K2SiO3/SiO2). При сушке пропитанного носителя удаляется вода и происходит кристаллизация гидроксидов или силикатных солей. Но в отличие от осажденных катализаторов, этот процесс усложняется взаимодействием растворенного вещества носителем, т. е. центры кристаллизации располагаются на поверхности носителя и следовательно, образующиеся твердые фазы будут иметь некую деформированную решетку по сравнению со свободными соединениями. Эти эффекты проявляются при небольших концентрациях нанесенного вещества. Поскольку, удельная поверхность нанесённых катализаторов изменяется не слишком сильно по сравнению с исходным носителем и пористая структура катализатора в общем задается носителем, данные эффекты должны проявляться в катализаторах приготовленные в на шей работе.
Таблица 3
Приготовление и химический состав нанесенных катализаторов
№ | Наименование и тип катализатора | Приготовление | Химический состав. масс. % | ||
SU-28 CuO. ZnO/SiO2 | Пропитка раствором МЦАКР Cu-0.10 моль/л. Zn-0.49 моль/л | Cu=1.50 Zn=9.35 K=0.20 | |||
SU-29 CuO. ZnO. К2О/SiO2 | Пропитка раствором МЦАКР Cu-0.1 моль/л. Zn-0.49 моль/л | Cu=1.00 Zn=7.30 K=0.97 | |||
SU-30 CuO. ZnO/К2SiO3/SiO2 (К2SiO3/SiO2 провяленный) | 1. Пропитка раствором K2SiO3 K=0.2 моль/л 2. Пропитка раствором МЦАКР Cu-0.10 моль/л. Zn-0.49 моль/л | Cu=0.90 Zn=8.83 K=0.90 | |||
SU-31 CuO. ZnO/К2SiO3/SiO2 (К2SiO3/SiO2 прокаленный К=2.6 мас. %) | 1. Пропитка раствором K2SiO3 K=0.2 моль/л 2. Пропитка раствором МЦАКР Cu-0.10 моль/л. Zn-0.49 моль/л | Cu=0.71 Zn=7.83 K=1.90 | |||
SU-32 CuO. ZnO/К2SiO3/SiO2 (К2SiO3/SiO2 K=6.1 мас. %) | 1. Пропитка раствором K2SiO3 K=0.6 моль/л 2. Пропитка раствором МЦАКР Cu-0.10 моль/л. Zn-0.49 моль/л | Cu=1.73 Zn=7.64 K=4.00 | |||
SU-33 CuO. ZnO/К2SiO3/SiO2 (К2SiO3/SiO2 K=8.04 мас. %) | 1. Пропитка раствором K2SiO3 K=1.2 моль/л 2. Пропитка раствором МЦАКР Cu-0.10 моль/л. Zn-0.49 моль/л | Хим. состав, мас. % | Уд. поверхность, м2/г | ||
Cu=1.65 Zn=6.95 K=5.77 | 170.1 | ||||
DM-30 CuO. ZnO/К2SiO3/SiO2 | 1. Пропитка раствором K2SiO3 K=0.4 моль/л 2. Пропитка раствором МЦАКР Cu-0.30 моль/л. Zn-0.40 моль/л | Cu=4.15 Zn=8.00 K=3.10 | 164.6 | ||
Если модифицированный носитель (K2SiO3/SiO2) прокалить примерно 400? С, то обменное взаимодействие при пропитке МЦАКРом получается меньшим, чем при пропитке такого же носителя, но только высушенного, и в последнем случае химический состав катализатора характеризуется большей концентрацией меди и цинка, и меньшей калия за счет растворения соединений калия в пропиточном растворе. Очевидно, такие катализаторы будут по свойствам ближе к образцам полученных методом осаждения.
Описание установки для исследования каталитических свойств образцов и расчетные формулы
Определение каталитических свойств производили на микрокаталитической установке в проточном режиме. Хроматографический анализ продуктов реакции позволяет разделить и количественно определить состав и содержание продуктов катализа. Для контроля каталитических свойств в реакциях, где выход целевого продукта при атмосферном давлении очень низок, необходим детектор высокой чувствительности, достаточной для количественного определения органических соединений (спиртов, эфиров и т. п.). Поэтому в газовой схеме наряду с катарометром использовали пламенно-ионизационный детектор.
После прохождения реактора — (2), в котором поддерживается необходимая температура, не прореагировавшие исходные вещества и продукты реакции направляются в хроматографическую колонку с адсорбентом porapak Q — (6) для разделения отходящих газов. При температуре адсорбента 120 °C газы СО, СО2, Н2 и СН4 на нем практически не удерживаются выходя из колонки разделения и направляются сначала в катарометр, а затем в рабочую ячейку ДИП- (7), а затем удаляются в атмосферу. Регистрация сигналов от проходящих легких газов и компонентов продуктов реакции, имеющих большое время удерживания регистрируются на приборе КСП.
С целью разделения «легких» газов (СО, СО2, Н2, СН4) отбираемые газовые пробы направляются в хроматографическую колонку (6) с активированным углем, и последовательно проходят два детектора — катарометр (9) и ДИП (7).
Для предотвращения конденсации компонентов газовой смеси в регулирующей аппаратуре и коммуникациях и сокращения размеров аппаратуры все регистрирующие узлы вместе с колонкой для разделения смеси компонентов помещены в термостат крана-дозатора — (1). Избыточное давление в системе определяется гидравлическим сопротивлением двух разделительных колонок и составляет ~ 0,2 МПа.
Расчетные формулы:
Расчет степени разложения метанола проводился по следующей формуле:
И=,
где: Sхол — площадь холодного пика, мм2
Si — площадь i-ого хроматографического пика, мм2
— приведённая высота пика метанола, мм;
— поправочный коэффициент;
— высота холостого пика в день эксперимента, мм
— высота холодного пика в день калибровки, мм Расчет концентрации по метанолу:
N=, м. д.
где
S-площадь хроматографического пика, мм2
КСН3ОН-калибрвочный коэффициент по метанолу, мкмоль/мм2
22,4-мольный объем газа при н. у., см3/моль
0,5-объем дозы, см3
0,845-фактор н. у. для крана дозатора
S=hпривСН3ОН• (a+b•exp (-c• hпривСН3ОН), мм2
где a, b, c — параметры модели получаемые при аппроксимации данных Расчет удельной производительности по метанолу при i — температуре
G=, мкмоль/с•г, где: Vсг — объем сухого газа без метанола,
1,047-коэффициент соответствующий концентрации метанола паро-газовой смеси 4,5об. %.
mнав — масса навески, г Расчет количества израсходованного метанола (удельная производительность):
?G=, мкмоль/с•г Расчет удельной производительности катализатора по ДМЭ, водороду, при i — температуре.
где:
hпрв-ва — высота пика соответствующего вещества при данной температуре, мм;
kв-ва — калибровочный коэффициент по соответствующему веществу, мкмоль/мм;
суммарный расход газовой смеси (газ-носитель + испарившийся метанол) на входе в реактор, см3/мин;
Vг/н — расход газа-носителя;
— мольная доля паров метанола в исходной газовой смеси на входе в реактор;
— средняя высота пика метанола в холодном реакторе, мм;
и — фактор нормальных условий для газа, находящегося в петле крана-дозатора и газа проходящего реометр;
Vд — объём петли в кране-дозаторе.
Обсуждение результатов измерения каталитической активности
Конверсия метанола в условиях эксперимента сопровождается образованием следующих продуктов, которые определялись методами газовой хроматографии и фотокалориметрии: водород, метан, метилформиат и диметиловый эфир, образование которых можно отобразить следующими уравнениями реакции:
CH3OH>CH2O+H2 (2), CH3OH> CH3-O — CH3 + H2O (3)
CH3OH> CH3OCOH +2H2 (4), 2 CH3OH> CH4+2 H2O+C (5)
Процесс выхода катализатора на стационарный режим работы оказывается достаточно длительным (несколько часов, в зависимости от образца катализатора). При этом изменяется степень переработки метанола и производительность по отдельным продуктам: водороду, формальдегиду и метилформитату, тогда как концентрация диметилового эфира при данной температуре остается практически неизменной. Длительный процесс формирования обуславливает наблюдаемый дебаланс между образовавшимся количеством водорода и формальдегида, т.к. согласно стехиометрии реакции мольное соотношение этих веществ должно быть равно 1. Весьма вероятно, наблюдаемое зауглераживание катализатора происходит через образование поверхностных гидроксометиленовых полимерных части по следующей реакции: CH3OH> (CH2O-) n+ n H2г (6), которые далее уплотняются с образованием более сложных графеновых структур (рис. 4−6). Далее на рисунках приведены данные по активности катализатора, полученный при выдержке в реакционной среде не менее часа. В исследуемых образцах при температуре 500? С дебаланс водорода и формальдегида уменьшается, то есть катализатор постепенно выходит на стационарный режим работы. Внесение в катализатор калия улучшает как активность, так и селективность, а именно уменьшает количество диметилового эфира и количество выделяющегося углерода. Увеличение содержание калия уменьшает время выхода на стационар, очевидно за счет уменьшения образования твердых углеродистых соединений (рис.7). Эти же зависимости проявляются и в катализаторах осажденного типа, продуктами являются формалин и водород, причем соотношение их не сильно отличается от единицы, поскольку эти образцы содержат большую концентрацию калия (рис.12). Но каталитическая активность в их меньше, поскольку это обусловлено низкой удельной поверхностью катализатора. Прокаливание при высокой температуре приводит к спеканию катализатора, что собственно и приводит к уменьшению его производительности (рис.13). Оптимизация состава соосажденного катализатора путем введения большого количества кремния позволяет несколько увеличить активность катализатора, но тем не менее остается ниже нанесенных систем.
Таблица 4
Производительность модельных катализаторов при t=500?С
№ | Название и тип образца | Каталитическая активность | O/C | H/C | |||
И, д. е. | FD | H2 | |||||
SU-28 CuO. ZnO/SiO2 | 0.96 | 18.5 | 30.3 | 1.0 | 5.0 | ||
SU-29 CuO. ZnO. К2О/SiO2 | 0.89 | 21.8 | 27.4 | 1.0 | 4.4 | ||
SU-30 CuO. ZnO/К2SiO3/SiO2 (К2SiO3/SiO2 провяленный K=0.9 мас. %) | 0.79 | 20.3 | 23.9 | 0.9 | 3.5 | ||
SU-32 CuO. ZnO/К2SiO3/SiO2 (К2SiO3/SiO2 K=6.17 мас. %) | 0.53 | 16.4 | 18.6 | 1.0 | 4.0 | ||
DM-30 CuO. ZnO/К2SiO3/SiO2 | 0.40 | 13.4 | 13.2 | 1.0 | 4.0 | ||
SU-27 СuO. ZnO. K2O. SiO2 | 0.28 | 8.5 | 8.9 | 1.0 | 4.0 | ||
Выборочные данные по активности сведены в таблицу 4, которые принципиально подтверждают предшествующую трактовку изменения каталитических свойств модельных образцов.
Выводы:
1. Методами соосаждения силикатных соединений меди, цинка и калия из аммиачно-карбонатных растворов и пропитки пористого силикагеля приготовлены модельные катализаторы с различным соотношением компонентов цинка, меди, калия и кремния.
2. Установлены концентрационные интервалы растворов, позволяющие получать гидроксосиликаты меди, цинка и калия с мелкодисперсной структурой и удельной поверхностью прокаленных образцов порядка 15 м2/г.
3. Показано, что выход на стационарный режим силикатных катализаторов достаточно длительный процесс, который обусловлен образованием поверхностных углеводородных соединений и на образцах содержащие силикаты калия он существенно сокращается.
4. Разработан способ введения калия в нанесенные катализаторы, который позволяет сократить процесс формирования катализатора и улучшить его селективность в отношении целевого продукта реакции дегидрирования метанола — формальдегида.
1. Караев М. М., Леонов В. Е., Попов И. Г. Технология синтетического метанола // Под ред. Караева М. М. — М.: Химия, 1984. — 240 с
2. Шелдон Р. А. Химичесие продукты наоснове синтез-газа // М.: Химия. 1987, 248 с.
3. Сеттерфилд Ч. Практический курс гетерогенного катализа // М.: Мир, 1984 г.520 с.
4. Розовский А. Я. Катализатор и реакционная среда // М. Наука. 1988. — 303с
5. Носков А. С. Промышленный катализ в лекциях // М.: Калвис. 2005, 128 с.
6. Мухленов И. П., Добкина Е. И., Дерюжкин В. И. и др., Технология катализаторов // Под ред. проф. Мухленова И. П.3-е издание, перераб. — Л.: Химия, 1989, 272 с.
7. Дзисько В. А., Карнаухов А. П., Тараева Д. В. Физико-химические основы синтеза окисных катализаторов // Наука, 1978, 384 с.
8. Неймарк Е. И. Силикагель, свойства, применение и методы его получения // Успехи химии, 1956, т.25, № 6, с.748−769
9. Айлер Р. К. Коллоидная химия кремнезема и силикатов // М., Стройиздат, 1959, 288 с.
10. Garather K., Grissback R. Oberflachengrosse und Porenstruktur von Kieselglen in abhangigkeit von iher vorgeschichte // Kolloid Z, 1958, bd.100, № 1, s.21−26
11. Бресков Г. К., Борисова М. С., Джигат О. А. и др., Влияние условий приготовления на структуру силикагеля // ЖФК, 1948, т.22, № 5
12. Неймарк Е. И., Шейнфан Р. Ю. О влиянии промывной жидкости на процесс формирования структуры силикагеля // Коллоидный журнал, 1953, т.15, № 1, с.45−59
13. Слинякова И. Б, Неймарк И. Е. Структура и адсорбционные свойства силикагелей, полученных из щелочных сред // Коллоидный журнал, 1958, т. 20, № 1, с.84−91
14. Высоцкий З. З, Шаля В. В. Теплоты гидратации некоторых катионов и влияние адсорбции последних на структуру силикагеля // Коллоидный журнал, 1958, т. 20, № 1, с.29−33
15. Wolf F., Beyer H. Ober beriechungenu zwischen herstellungsbedingen und oberf la chen strukturen von kiesilgelen // Kolliod Z, 1959, Bd.165, № 2, S.151−155
16. Стрелко В. В. Механизм кремневой кислоты // Коллоидный журнал, 1970, т.32, № 3, с.430−435
17. Берестнева З. Я., Корецкая Т. А., Каргин В. А. Электронно-микроскопическое и адсорбционное исследование SiO2 золей // Коллоидный журнал, 1949, т.11, № 6, с.369−370
18. Оккерсе К. Пористый кремнезем, В. кн. «Строение и свойства адсорбентов и катализаторов // Под ред. Линсела Б. Г. пер. с англ.М., «Мир», 1973, с.233−284
19. Киселев А. В., Лыгин В. И., Неймарк Е. И. и др., Электронно-микроскопическое и адсорбционное исследование силиказолей и силикагелей // Коллоидный журнал, 1958, т. 20, № 1. С.52−58
20. Берестнева З. Я., Корецкая Т. А., Каргин В. А Электронно-микроскопическое исследование TiO2 золей и механизм образования коллоидных частиц // Коллоидный журнал, 1950, т.12, № 5, с.338−341
21. Рыжак И. А. Исследование генезиса морфологических структур гидроокисей и окисей алюминия и железа // Канд. дис., Навосибирск, 1971, 128с.
22. Al M. Dehydrogenation of methanol formate over copper-based catalyst // Applied Catalisis, 1984, p.259−270
23. Горшков C.В., Лин Г. И., Розовский А. Я. Механизм дегидрирования метанола в метилформиат и пути управления селективностью процесса // Кинетика и катализ, 1999, том40, № 3, с.372−375
24. Chung M. — J., Park K. — Y., Lee B. — J. and Ihm S. — K. Methylformate formation from methanol and CO ON Cu/ZnO catalysts // Korean Journal of Chemical Engineering, 1993, V.10, Is.3, pp.188−190
25. Okamoto Y., Fukino K., Imanaka T., and Teranishi S. Synergy Between Cu and ZnO methanol conversion over Cu-ZnO catalysts // Chemistery letters, 1984, pp.71−74
26. Tsoncheva T., Sarkadi-Priboczki E.11C-radiolabeling study of methanol decomposition on copper oxide modified mesoporous SBA — 15 silica // Appl. Surf. Science, 2011, том 257, с.6661−6666
27. Соломатин Г. И., Соболевский В. С., Григорьев В. В. и др. Ик-спектры катализаторов и адсорбированных молекул
28. Антонюк С. Н., Егорова Е. В., Якерсон В. И. и др. Каталитические превращения метанола с целью получения метилформиата, водорода и монооксида углерода
29. Hong X., Ren S. Selective hydrogen production from methanol oxidative steam reforming over Zn-Cr catalysts or without Cu loading // International journal of hydrogen enerdgy 33, 2008, p.700−708
30. Шлегель Л., Гутшик Д., Розовский А. Я. Разложение метанола на Сu-содержащих катализаторах синтеза метанола // Кинетика и катализ, 1999, том40, № 3
31. Усачев Н. Я., Круковский И. М., Канаев С. А. Неокислительное дегидрирование метанола в формальдегид // Нефтехимия, 2004, том 44, № 6, с.411−427
32. Music A., Batista J., Levec J. Gas-phase catalytic dehydrogenation of methanol to formaldehyde over ZnO/SiO2 based catalysts, zeolites, and phosphates // Appl. Catalysis, 1997, V.165, № 1, P.115−131
33. Li J. X., REN L. — P., Dai W. — L., Yong CAO and FAN K. — N. Novel Flower-Like Ag-SiO2-MgO-Al2O3 Material: Preparation, Characterization and Catalytic Application in Methanol Dehydrogenation // Chinese Journal of Chemistry, 2008 V, 26, Is.6, p.1045−1051
34. Chen A. K., Masel R. Direct conversion of methanol to formaldehyde in the absence of oxygen on Cu (210) // Surf. Science. 1995, V.343, № 1, Р.17−23.
35. Zhang R., Sun Y., Peng S. In situ FTIR studies of methanol adsorption and dehydrogenation over Cu/SiO2 catalyst // Fuel. 2002, V.81, № 11, Р.1619−1624
36. Сhan L., Griffin J. Methanol decomposition on oriented ZnO thin films // Surf. Science. 1985, V.155, № 3, Р.400−412
37. Okamoto Y., Fukino K., Imanaka T., and Teranishi S. Synergy Between Cu and ZnO methanol conversion over Cu-ZnO catalysts // Chemistery letters, 1984, p.71−74
38. Юрьева Т. М., Плясова Л. М., Кринер Т. А., Макарова О. В. // Кинетика и катализ, 1995, т.36, № 5, с.769−773
39. Matsumura Y., Hashimoto K., Yoshida S. Degydrogenation of methanol to formaldehyde over silicalite // J. Catalysis. 1986, V.100, № 3, Р.392−400.
40. Третьяков В. Ф., Бурдейная Т. Н., Давыдова М. Н. Каталитическое неокислительное дегидрирование метанола в формальдегид // Ученые записки МИТХТ, 2003, выпуск 9
41. Уменушкина С. И. Приготовление катализаторов на основе силикатов цинка для конверсии метанола // Дипломная работа, кафедра ТНВ, ИГХТУ, 2012, 75с
42. База данных AST