Разработка проекта отделения для термической обработки деталей и инструментов в условиях машиностроительного завода с годовой производственной программой 5
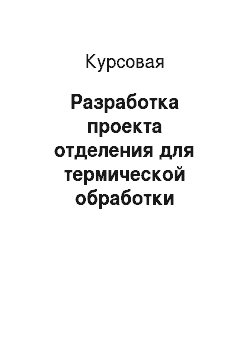
Для удовлетворения требований пуансона из стали 3Х3М3Ф назначен следующий режим термической обработки: закалка с подогревом и двукратным отпуском. Для предотвращения окисления и обезуглероживания поверхности изделия во время нагрева, нагревать следует в защитной атмосфере. Для получения высокой твердости стали при закалки, нагревать следует до температуры 1030−1050°С. Такая температура нагрева… Читать ещё >
Разработка проекта отделения для термической обработки деталей и инструментов в условиях машиностроительного завода с годовой производственной программой 5 (реферат, курсовая, диплом, контрольная)
МИНИСТЕРСТВО ОБРАЗОВАНИЯ И НАУКИ УКРАИНЫ ДОНЕЦКИЙ НАЦИОНАЛЬНЫЙ ТЕХНИЧЕСКИЙ УНИВЕРСИТЕТ Кафедра «физического материаловедения»
ПОЯСНИТЕЛЬНАЯ ЗАПИСКА к курсовой работе по дисциплине
«Технологические основы термической обработки металлов»
на тему: «Разработка проекта отделения для термической обработки деталей и инструментов в условиях машиностроительного завода с годовой производственной программой 500 тонн»
Выполнила: ст. гр. ПМ-14м Ермаченко Д. И.
Проверил: профессор, д. т. н.
Алимов В. И.
Донецк 2014
СОДЕРЖАНИЕ ВВЕДЕНИЕ
1. РАЗРАБОТКА ГОДОВОЙ ПРОИЗВОДСТВЕННОЙ ПРОГРАММЫ
2. ОПИСАНИЕ ИЗДЕЛИЙ, УСЛОВИЯ ИХ РАБОТЫ И ТРЕБОВАНИЯ К НИМ
2.1 Условия работы зубчатого колеса и требования к нему
2.3 Условия работы пружины и требования к ней
2.4 Условия работы плашки и требования к ней
2.5 Условия работы пуансона и требования к нему
3. ВЫБОР И ОБОСНОВАНИЕ ВЫБОРА МАРОК СТАЛЕЙ
3.1 Выбор материала для изготовления зубчатого колеса
3.2 Выбор материала для изготовления шестерни
3.3 Выбор материала для изготовления пружины
3.4 Выбор материала для изготовления плашки
3.5 Выбор материала для изготовления пуансона
4.1 Разработка технологии термической обработки зубчатого колеса
4.2 Разработка технологии химико-термической обработки шестерни
4.3 Разработка технологии термической обработки пружины
4.4 Разработка технологии термической обработки плашки
4.5 Разработка технологии термической обработки пуансона
5. ВЫБОР ОБОРУДОВАНИЯ ДЛЯ ТЕРМИЧЕСКОЙ ОБРАБОТКИ И РАСЧЕТ ЕГО КОЛИЧЕСТВА
5.1 Выбор и расчет основного оборудования
5.1.1 Выбор оборудования для обработки зубчатого колеса
5.1.2 Выбор оборудования для обработки шестерни
5.1.3 Выбор оборудования для обработки пружины
5.1.4 Выбор оборудования для обработки плашки
5.1.5 Выбор оборудования для обработки пуансона
5.2 Оборудование для охлаждения
5.2.1 Выбор оборудования для охлаждения зубчатого колеса
5.2.2 Выбор оборудования для охлаждения шестерни
5.2.3 Выбор оборудования для охлаждения пружины
5.2.4 Выбор оборудования для охлаждения плашки
5.3 Выбор вспомогательного оборудования
5.4 Выбор дополнительного оборудования
5.5 Выбор подъемно-транспортного оборудования
6. РАЗРАБОТКА ПЛАНИРОВКИ ТЕРМИЧЕСКОГО ОТДЕЛЕНИЯ
7. ТЕХНИКА БЕЗОПАСНОСТИ О ОХРАНА ОКРУЖАЮЩЕЙ СРЕДЫ
8. КОНТРОЛЬ КАЧЕСТВА ЗАКЛЮЧЕНИЕ ПЕРЕЧЕНЬ ССЫЛОК
Место термической обработки в общем технологическом процессе должно определяться в процессе разработки технологии производства данной детали, инструмента. При этом стоит учитывать размеры, форму, массу изделий, требования к их свойствам, которые исходят из условий их эксплуатации, особенности термической обработки и возможность формообразования до и после термической обработки.
Термическая обработка металлов и сплавов являет собой совокупность технологических операций, связанных с нагревом, выдержкой и охлаждением. Цель термической обработки — изменение в нужном направлении механических, физико-химических и технологических свойств без изменения основных размеров и формы изделий. Термическая обработка является окончательным этапом производства изделий, поэтому именно от нее зависит качество продукции. Большинство металлопродукции, произведенной в нашем регионе уходит, на экспорт. Во втором полугодии 2013 г экспорт металлопроката составил 5417 тыс. тонн, чугуна — 1030 тыс. тонн, стали — 1120 тыс тонн.
Объем внутреннего потребления отечественного металлопроката уменшился и составил 1980 тыс тонн (14,6% от общего производства) против 2650 тыс тонн (18,3% от общего производства) в первом полугодии 2013 года.
Для реализации термической обработки необходимо правильно подобрать оборудование для ее проведения.
Таким образом, елью данного проекта является разработка термического отделения машиностроительного завода с годовой производственной программой 500 т. При проэктировании отделения производится расчет основного, вспомогательного и дополнительного оборудования для реализации разработанных технологии термической обработки деталей и инструментов.
1. РАЗРАБОТКА ГОДОВОЙ ПРОИЗВОДСТВЕННОЙ ПРОГРАММЫ
Для определения производственной мощности цеха рассчитывается производственная программа, определяется необходимое основное и вспомогательное оборудование, транспортные приспособления.
При расчете производственной программы максимально учитывается возможности оборудования, качественные характеристики, предусматривается рациональное использование всех материальных факторов предприятия (материалов, энергии, топлива). Годовая производственная программа задается в виде номенклатуры и количества изделий, которые подвергают термической обработки.
Годовое количество отделения, которое проектируется, определяется по формуле 1.1
Qвып=Qзад*а/100 (1.1)
где Qзад — годовая программа выпуска, кг;
а — процент данного изделия в общем объёме производства, %.
Расчет программы запуска ведем по формуле 1.2
Qзап= Qвып*(1+в/100) (1.2)
где Qзап — программа запуска изделий, кг;
Qвып — программа выпуска изделий, кг;
в — плановый процент на технологические пробы (в = 0,02%).
Результат расчета производственной программы приведен в таблице 1.1.
Таблица 1.1 — Годовая производственная программа термического отделения
Наименование изделия | Размеры, мм (*) | Масса детали, кг | Процент в годовом объёме производства, % | Программа выпуска | Программа запуска | |||
кг | шт | кг | шт | |||||
Зубчатое колесо | D=135, d = 69, h = 55 | |||||||
Шестерня | D=173, d = 77, h = 46 | |||||||
Пружина | L=140, h = 100, d = 15 | 2,5 | ||||||
Плашка | H = 35, h =15, L = 230 | |||||||
Пуансон | D= 130, L = 170 | |||||||
Итого | ||||||||
*- условное обозначение: D — внешний диаметр, d — внутренний диаметр, L — длина, h — толщина, Н — ширина.
2. ОПИСАНИЕ ИЗДЕЛИЙ, УСЛОВИЯ ИХ РАБОТЫ И ТРЕБОВАНИЯ К НИМ
2.1 Условия работы зубчатого колеса и требования к нему
Зубчатое колесо работает в редукторе шпиндельной бабки. Оно предназначено для передачи крутящего момента вдоль своей оси. Зубчатое колесо приведено на рисунке 2.1.
Рисунок 2.1 — Зубчатое колесо Зубчатое колесо работает в условиях средних удельных нагрузок и скоростей. Основными нагрузками, которым поддается деталь, является кручение и ударные нагрузки. Зубья зубчатого колеса поддаются контактным нагрузкам и абразивному износу.
Исходя из условий эксплуатации и основных нагрузок, которым поддается зубчатое колесо, оно должно иметь высокие свойства прочности и пластичности, а также высокое сопротивление хрупкому разрушению.
Для обеспечения высокой работоспособности зубчатого колеса необходимо обеспечить следующие его свойства: твердость по сечению 180−220 НВ; ??в=650−670Н/мм2; ??т=350−380Н/мм2; ??>10%; KCU>48Дж/см2.
2.2 Условия работы шестерни и требования к ней Шестерня работает в коробке передач автомобиля. Ее предназначение — передача крутящего момента вдоль своей оси. Шестерня представлена на рисунке 2.2.
Рисунок 1.1 — Шестерня Шестерня работает при больших скоростях, высоких удельных усилиях. Сердцевина шестерни поддается кручению, ударным нагрузкам.
Зубья шестерни в процессе эксплуатации поддаются изгибу при максимальном однократном нагружении (при резком торможении, заклинивании, приложениие максимального крутящего момента); изгибу при многократных циклических нагрузках, в результате чего в корне зуба развиваются наибольшие напряжения и может происходить усталостное разрушение; контактным напряжениям на боковых рабочих поверхностях зубов, что приводит также к контактно-усталостному разрушению; износу боковых поверхностей (из-за попадания абразивных частиц, грязи, пыли в зону контакта) или торцевых поверхностей (при переключении передач). Для нормальной работы шестерни на протяжении длительного времени необходимо обеспечить ее достаточную твердость по сечению, износостойкость и высокую твердость зубьев при достаточной пластичности сердцевины.
Исходя из условий эксплуатации, шестерня должна иметь такие свойства: твердость поверхностного слоя глубиной 0,8−1,0 мм — 59−61 HRC, твердость сердцевины 30−32 HRC, ??в=750−780Н/мм2; ??т=630−650Н/мм2, ?? = 9−10%, ?? = 42−45%, KCU = 60Дж/см2.
2.3 Условия работы пружины и требования к ней
На рисунке 2.3 представлена цилиндрическая винтовая пружина. которая входит в состав гидроблока насосной станции и предназначена для взаимодействия колец с плунжером. Количество витков пружины — 6. В процессе работы она подвергается растягивающим напряжениям и сжимающим при большом количестве импульсов. Пружина эксплуатируется в обычных атмосферных условиях.
Рисунок 2.3 — Пружина Пружина должна иметь высокое сопротивление малым пластическим деформациям, достаточно высокие пластичность и стойкость к хрупкому разрушению, повышенную релаксационную стойкость и высокий предел упругости.
Исходя из условий эксплуатации, пружина должна иметь такие свойства: твердость по сечению 388−412 НВ; ??в=1200−1250Н/мм2; ??т=1300−1400Н/мм2; ??>6%; ??>25%; ??уп=500−570Н/мм2.
2.4 Условия работы плашки и требования к ней
Подвижная плашка подвергается высоким истирающим нагрузкам. Плашка используется для накатки резьбы болтов на метизных заводах. Ее относят к штамповому инструменту холодного деформирования. Характеристика плашки определяется твердостью поверхности и используемой марки стали. Инструмент работает при высоких динамических нагрузках и сильно поддается истирающему действию. Плашка приведена на рисунке 2.4.
Рисунок 2.4 — Плашка Плашка должна удовлетворять следующим требованиям: твердость 59−61HRC, KCU=16Дж/см2.
2.5 Условия работы пуансона и требования к нему
Пуансон — штамповый инструмент, который предназначен для обработки материалов давлением. Пуансон работает в условиях циклических напряжений, высоких температур и давления (до 2500Мпа), а также динамической нагрузке. Пуансон приведен на рисунке 2.5.
Рисунок 2.5 — Пуансон Для длительной безаварийной работы пуансона, материал для его изготовления должен иметь следующие свойства: твердость 55−60HRC, ??в=1620−1650Н/мм2; ??т=1250−1300Н/мм2; ??>14%; ??>40%.
3. ВЫБОР И ОБОСНОВАНИЕ ВЫБОРА МАРОК СТАЛЕЙ
3.1 Выбор материала для изготовления зубчатого колеса
Исходя из условий эксплуатации. Сталь для изготовления зубчатого колеса должна отвечать следующим требованиям:
— иметь достаточно высокую прокаливаемость для получения необходимой твердости по сечению изделия;
— хорошую обрабатываемость резанием;
— высокую ударную вязкость.
Соответственно материал для изготовления зубчатого колеса необходимо выбирать из группы конструкционных улучшаемых сталей: 45, 45Г2 и 40Х.
В таблицах 3.1 и 3.2 приведены механические свойства и прокаливаемость сталей 45, 45Г2 и 40Х, после закалки и отпуска.
Таблица 3.1 — Механические свойства сталей 45, 40Х и 40ХН после закалки и отпуска [3]
Марка стали | Термическая обработка | Сечение, мм | ув, Н/мм2 | ??т, Н/мм2 | % | KCU, Дж/см2 | НВ | ||
закалка | отпуск | ||||||||
840 °C вода | 550 °C в-х | 700−750 | 187−229 | ||||||
45Г2 | 850 °C масло | 650 °C вода | 670−680 | 187−200 | |||||
40Х | 860 °C масло | 500 °C вода | 174−217 | ||||||
Таблица 3.2 — Прокаливаемость сталей 45, 45Г2, 40Х[3]
Марка стали | Критический диаметр, мм | Количество мартенсита, % | ||
вода | масло | |||
15−35 | ; | |||
45Г2 | 23−64 | 6−38 | ||
40Х | 23−58 | 6−35 | ||
Из приведенных данных видно, что свойства стали 45 и 40Х после закалки и отпуска не удовлетворяют требованиям. Сталь 40Х более дорогая по сравнению со сталью 45Г2 из-за наличия в ее составе легирующего элемента хрома, поэтому ее использование не целесообразно.
Таким образом, для изготовления зубчатого колеса целесообразно использовать сталь 45Г2, которая удовлетворяет всем требованиям. Химический состав, температуры критических точек и влияние температуры отпуска на механические свойства стали 405Г2 приведены в таблицах 3.3, 3.4 и 3.5 соответственно.
Таблица 3.3 — Химический состав стали 45Г2,% масс. [3]
С | Si | Mn | Cr | Ni | Cu | S | P | |
не более | ||||||||
0,41−0,49 | 1,4−1,8 | 0,17−0,37 | 0,30 | 0,3 | 0,30 | 0,035 | 0,035 | |
Таблица 3.4- Температура критических точек стали 45Г2,°С [3]
Ас1 | Ас3 | Аr3 | Ar1 | Мн | |
Таблица 3.5 — Зависимость механических свойств стали 45Г2 от температуры отпуска[3]
Температура отпуска, °С | ув, Н/мм2 | ??т, Н/мм2 | % | KCU, Дж/см2 | НВ | |
Рисунок 3.1 — Зависимость твердости стали 45Г2 от температуры отпуска Из приведенных данных видно, что для обеспечения необходимых свойств зубчатого колеса из стали 45Г2 отпуск необходимо проводить при температуре 650−670°С.
3.2 Выбор материала для изготовления шестерни
Исходя из условий эксплуатации шестерни, материал для ее изготовления должен иметь:
— достаточно высокую прокаливаемость, что позволит обеспечить необходимую твердость поверхностного слоя и сердцевины зубьев при закалке в масле (углеродистые стали не применяются, т. к. при охлаждении их в воде после закалки наблюдается повышенная деформация);
— хорошую обрабатываемость резанием.
Для ответственных тяжелонагруженных шестерен с высокой прочностью сердцевины зуба применяют конструкционные цементуемые стали 20, 20Х и 18ХГТ. Механические свойства и прокаливаемость этих сталей приведены в таблицах 3.6, 3.7 соответственно.
Таблица 3.6 — Механические свойства сталей 20, 20Х, 18 ХГТ (сечение 50мм) [3]
Марка стали | Режим термообработки | ув, Н/мм2 | у0,2, Н/мм2 | % | ш, % | KCU, Дж/см2 | HRC поверх. | HRC сердц. | |
Ц 920−950°С З 800−820°С вода, но 180−200°С, в-х | 490−590 | 290−340 | 58−60 | 20−25 | |||||
20Х | Ц 920−950°С подст. З 800−820°С масло, но 180−200°С, в-х | 58−60 | 30−33 | ||||||
18ХГТ | Ц 920−950°С подст. З 820−860°С масло, но 180−200°С, в-х | 58−61 | 32−34 | ||||||
Таблица 3.7 — Прокаливаемость сталей 18ХГТ, 20Х, 20ХГР [3]
Марка стали | Критический диаметр в масле, мм | Количество мартенсита, % | |
; | ; | ||
20Х | 20−35 | ||
18ХГТ | 12−50 | ||
Из приведенных данных видно, что сталь 20 не обеспечивает необходимые свойства изделия. Стали 20Х и 18ХГТ обеспечивают необходимый комплекс свойств. Однако, сталь 18ХГТ из-за легирования хромом, марганцем и титаном имеет более высокую стоимость, что делает ее применение не целесообразным. Таким образом, для изготовления шестерни с заданными свойствами целесообразно использовать сталь 20Х.
Основными легирующими элементами стали 20Х является хром, Основное предназначение хрома — это повышение прокаливаемости. Химический состав стали 20Х приведен в таблице 3.8.
Таблица 3.8 — Химический состав стали 20Х, % масс. [3]
C | Si | Mn | Cr | P | S | Cu | Ni | |
0,17−0,23 | 0,17−0,37 | 0,5−0,8 | 0,7−1,0 | 0,035 | 0,035 | 0,035 | 0,30 | |
Температуры критических точек приведены в таблице 3.9.
Таблица 3.9 — Температуры критических точек стали 20Х, °С [3]
Ас1 | Ас3 | Аr3 | Аr1 | Мн | |
Изменение свойств стали в зависимости от температуры отпуска приведено в таблице 3.10.
Таблица 3.10 — Влияние температуры отпуска на механические свойства стали 20Х[3]
Тотп, °С | ув, Н/мм2 | у0,2, Н/мм2 | % | ш, % | KCU, Дж/см2 | Твердость, HRC | ||
сердц. | поверх. | |||||||
Из приведенных в таблице 3.10 данных видно, что необходимые свойства материала можно обеспечить, если в качестве химико-термической обработки применять цементацию с закалкой с цементационного нагрева и низкий отпуск при температуре 180−200°С.
3.3 Выбор материала для изготовления пружины
Как материал для изготовления пружин, которые работают в разных механизмах, применяют пружинно-рессорные стали общего назначения.
При выборе материала необходимо учитывать вид изделия и условия его эксплуатации:
— пружина имеет сечение 15 мм;
— не испытывает высоких нагрузок;
— работает в обычных атмосферных условиях;
— не является изделием ответственного назначения.
Исходя из этого, пружину целесообразно изготавливать из конструкционных рессорно-пружинных сталей легированных кремнием: 55С2, 60С2, 70С3.
В таблице 3.11 приведен сравнительный анализ механических свойств сталей 55С2, 60С2 и 70С3 после типовой термической обработки.
Таблица 3.11 — Механические свойства сталей 55С2, 60С2 и 70С[3]
Марка стали | Термическая обработка | ув, Н/мм2 | у0,2, Н/мм2 | % | ш, % | НВ | ??упр, Н/мм2 (при n=106) | ||
закалка | отпуск | ||||||||
55С2 | 870 °C, масло | 460 °C в-х | 445−341 | ||||||
60С2 | 870 °C, масло | 477−388 | |||||||
70С3 | 860 °C, масло | 445−388 | |||||||
Из таблицы 3.11 видно, что по величинам относительных удлинений и сужений при разрыве, а также усталостной прочности все предлагаемые стали отвечают требованиям. Однако, сталь 55С2 обеспечивает значения твердости ниже необходимого, поэтому ее использование является не целесообразным для изготовления данной пружины. Сталь 70С3 обеспечивает сильно высокие пределы прочности и текучести, кроме того, эта сталь склонна к графитизации и обезуглероживанию.
Таким образом, для изготовления пружины с заданным комплексом свойств, необходимо использовать сталь 60С2. Химический состав, температуры критических точек и прокаливаемость стали 60С2 приведены в таблицах 3.12, 3.13 и 3.14 соответственно.
Таблица 3.12 — Химический состав стали 60С2, % масс. [3]
C | Si | Mn | Cr | P | S | Cu | Ni | |
0,57−0,65 | 1,5−2,0 | 0,6−0,9 | 0,3 | 0,035 | 0,03 | 0,2 | 0,25 | |
Таблица 3.13 — Температуры критических точек стали 60С2, °С [3]
Ас1 | Ас3 | Аr3 | Аr1 | Мн | |
Таблица 3.14 — Прокаливаемость стали 60С2[3]
Количество мартенсита, % | Твердость, HRC | Критический диаметр, мм | ||
вода | масло | |||
52−53 | 47−82 | 24−53 | ||
58−60 | ||||
Изменение свойств стали 60С2 в зависимости от температуры отпуска приведены в таблице 3.15.
Таблица 3.15 — Влияние температуры отпуска на механические свойства стали 60С2 после закалки с температуры 870 в масле[3]
Тотп, °С | ув, Н/мм2 | % | ш, % | НВ | |
; | |||||
На рисунке 3.2 показано влияние температуры отпуска на твердость стали 60С2.
Рисунок 3.2 — Зависимость твердости стали 60С2 от температуры отпуска Из рисунка 3.2 видно, что необходимые свойства пружины из стали 60С2 можно обеспечить, если применять термическую обработку: закалку с дальнейшим отпуском при температуре 430−450°С.
3.4 Выбор материала для изготовления плашки
Плашку для накатки резьбы необходимо изготавливать прочных инструментальных сталей, например У8, У10А и У12.
Для обеспечения стойкости инструмента материал для его изготовления должен обладать высокими показателями прочности, износостойкости и достаточной вязкости. С этой целью нужно выбирать стали с небольшой прокаливаемостью. За счет несквозной прокаливаемости на поверхности изделия образуется твердый износостойкий слой, а сравнительно вязкая сердцевина дает возможность работать при ударных нагрузках. Прокаливаемость сталей У8, У10А и У12 приведена в таблице 3.16
Таблица 3.16 — Прокаливаемость сталей У8, У10А и 8Х3[3]
Марка стали | Твердость, HRC | Критический диаметр, мм | ||
вода | масло | |||
У8 | 15−20 | ; | ||
У10А | ; | |||
8Х3 | ; | |||
Механические свойства сталей У8, У10А и 8Х3 приведены в таблице 3.17.
Таблица 3.17 — Механические свойства сталей У8, У10А и 8Х3[3]
Марка стали | Режим термической обработки | KCU, Дж/см2 | HRC | |
У8 | Закалка 760−780°С вода, отпуск 180−200°С, в-х | 55−60 | ||
У10А | Закалка 770−800°С вода, отпуск 280−350°С, в-х | 57−61 | ||
8Х3 | Подогрев 650−700°С, закалка 820−850°С, масло, отпуск 280−350°С | 55−57 | ||
Исходя из таблицы 3.17, можно сделать вывод, что сталь У8 не обеспечивает необходимую твердость и ударную вязкость изделия. Сталь 8Х3 имеет близкие свойства, но также является более дорогой по сравнению со сталью У10А из-за содержания в ней 3% дорогого легирующего элемента — хрома. Поэтому для изготовления плашки целесообразно использовать сталь У10А которая удовлетворяет требованиям.
Химический состав, температуры критических точек стали У10А приведены в таблицах 3.18, 3.19 соответственно.
Таблица 3.18 — Химический состав стали У10А, % масс. [3]
C | Si | Mn | S | Cu | Ni | P | |
0,96−1,03 | 0,17−0,33 | 0,17−0,28 | 0,018 | 0,20 | 0,20 | 0,025 | |
Таблица 3.20 — Температуры критических точек стали У10А, °С [3]
Ас1 | Асm | Аr1 | Мн | |
Изменение свойств стали У10А в зависимости от температуры отпуска приведены в таблице 3.15.
Таблица 3.15 — Влияние температуры отпуска на механические свойства стали У10А после закалки с температуры 760−780 в воде[3]
Тотп, °С | Твердость, HRC | |
На рисунке 3.3 показано влияние температуры отпуска на твердость стали У10А.
Рисунок 3.3 — График зависимости твердости стали У10А от температуры отпуска Из рисунка 3.3 видно, что необходимые свойства плашки из стали У10А можно обеспечить, если применять термическую обработку: закалку с дальнейшим отпуском при температуре 160−180°С.
3.5 Выбор материала для изготовления пуансона
Для пуансона первой операции наиболее важным является прочность, вязкость и износостойкость.
Для штампов холодного деформирования, которые работают плавно, но с повышенным разогревом, необходимы: высокая теплостойкость и сопротивление малым деформациям. При этом вязкость может быть занижена. Штампы для деформирования изготавливаются с высокой точностью, они могут быть сложными и большими, именно поэтому стали для их изготовления должны иметь большое количество легирующих элементов. Стали должны обладать удовлетворительными технологическими характеристиками: обработка резанием, закаливаемость и прокаливаемость, стойкость к обезуглероживанию, малая деформация во время термической обработки.
Пуансон можно изготовить из следующих марок сталей: 3Х3М3Ф, 4ХМФС, 3Х2В8Ф. Механические свойства и теплостойкость данных сталей приведены в таблице 3.21и 3.22 соответственно.
Таблица 3.21 — Механические свойства сталей 3Х3М3Ф, 4ХМФС, 3Х2В8Ф[3]
Марка стали | Режим термообработки | ув, Н/мм2 | у0,2, Н/мм2 | % | ш, % | KCU, Дж/см2 | HRC | |
4ХМФС | Закалка 910 °C, отпуск 400°С | |||||||
3Х3М3Ф | Закалка 1040 °C, отпуск 500°С | |||||||
3Х3В8Ф | Закалка 910 °C, отпуск 400°С | |||||||
Таблица 3.22 — Теплостойкость сталей 3Х3М3Ф, 4ХМФС, 3Х2В8Ф[3]
Марка стали | Теплостойкость, °С | Время, ч | Твердость, HRC | |
4ХМФС | ||||
3Х3М3Ф | ||||
3Х2В8Ф | 600−630 | 45−51 | ||
Из таблицы 3.21 видно, что необходимую твердость обеспечивают все три марки стали. Но сталь 4ХМФС обладает пониженной твердостью при рабочей температуре, что недопустимо условиями работы данного изделия. Сталь 3Х2В8Ф легирована дорогим вольфрамом, поэтому с экономической точки зрения ее использование является невыгодным. Поэтому целесообразным будет использование стали 3Х3М3Ф для изготовления пуансона.
Химический состав стали 3Х3М3Ф приведен в таблице 3.23.
Таблица 3.23 — Химический состав стали 3Х3М3Ф, % масс. [3]
C | Si | Mn | Cr | S | Cu | Ni | P | Mo | V | |
0,27−0,34 | 0,1−0,4 | 0,2−0,5 | 2,8−3,5 | 0,03 | 0,03 | 0,35 | 0,03 | 2,5−3 | 0,4−0,6 | |
IV РАЗРАБОТКА ТЕХНОЛОГИИ ТЕРМИЧЕСКОЙ ОБРАБОТКИ ИЗДЕЛИЙ
4.1 Разработка технологии термической обработки зубчатого колеса
термический технология обработка зубчатый
Для обеспечения необходимых свойств зубчатого колеса его подвергают термической обработке — улучшению, которое включает закалку и высокий отпуск.
Режим термической обработки зубчатого колеса из стали 45Г2приведен на рисунке 4.1.
Рисунок 4.1 — Режим закалки и отпуска зубчатого колеса из стали 45Г2
Температура нагрева при закалке определяется химическим составом стали и критическими точками:
tн = т. Ас3+(30 ч 50 оС) = 765 + (30−50) = 795−815 °С. (4.1)
Время нагрева рассчитаем по формуле А. П. Гуляева;
фн=0,1* К1* К2*К3*Д1, (4.2)
где фн — время нагрева, мин;
К1=2 — коэффициент формы изделия, для цилиндрического изделия;
К2=2 — коэффициент среды, для нагрева в газовой среде;
К3=2 — коэффициент равномерности нагрева.
Схема укладки в печь изображена на рисунке 3.2.
Рисунок 4.2 — Схема укладки зубчатых колес в печи Д1=33 мм — минимальный размер максимального сечения изделия.
Таким образом, фн=0,1*2*2*2*35 = 26,4 мин.
Так как сталь 45Г2 легированная необходимо учесть коэффициент легирования Кл=1,5.
фн= 26,4*1,5 = 39,6мин.
Так как зубчатое колесо будет нагреваться в печи с приспособлением, то необходимо учесть и время нагрева на приспособление, по формуле:
фпр=(0,2ч0,3)*фн, (4.3)
где фпр — время нагрева на приспособление;
фн — время нагрева без приспособления.
фпр= 0,2*39,6 = 7,92 мин Тогда общее время нагрева зубчатого колеса будет определяться как:
фн об= 39,6+7,92 = 47,5?48 мин.
Примем общее время нагрева 48 мин.
Время выдержки фв при закалке зубчатого колеса определяется из формулы:
фв=(0,2ч0,3)*фн, (4.4)
и для данного зубчатого колеса составит:
фв = 0,25*48 = 12 мин.
Закалка зубчатого колеса осуществляется в масле при температуре масла 20−80 0С.
После закалки осуществляется промывка зубчатого колеса от масла в 10% растворе NaOH.
После промывки зубчатое колесо подвергается отпуску при температуре:
tотп= 650−670 оС Длительность отпуска определяется по формуле:
фотп = (10+д*фуд)*Кпр мин, (4.5)
где д = 33 мм — толщина изделия;
фуд = 1 мин/мм — удельное время нагрева.
Кпр =1,2 — коэффициент учитывающий нагрев на приспособление;
Значит, время отпуска составит:
фотп=(10+33*1)*1,2=52мин.
Охлаждение после отпуска производится в воде, т. к. сталь 45Г2 склонна к отпускной хрупкости.
4.2 Разработка технологии химико-термической обработки шестерни
Шестерня из стали 20Х для обеспечения необходимых свойств поддается химико-термической обработки, режим которой приведен на рисунке 4.3. Режим ХТО шестерни включает цементацию, закалку с отдельного нагрева и низкий отпуск.
Рисунок 4.3 — Режим цементации, закалки и отпуска шестерни из стали 20Х Газовая цементация проводится в присутствии смеси природного газа с эндогазом при температуре 930−950 °С, т. е. нагрев стали производится в аустенитную область.
Необходимая глубина цементованого слоя для шестерни — 0,9 мм.
Время нагрева под цементацию определяется по формуле Гуляева А. П. с учетом коэффициентов:
фн=0,1* К1* К2*К3*Д1*кл*кпр=0,1*2*2*2*48*1,5*1,2=69мин.
где фн — время нагрева, мин;
К1=2 — коэффициент формы изделия, для цилиндрического изделия;
К2=2 — коэффициент среды, для нагрева в газовой среде;
К3=2 — коэффициент равномерности нагрева;
Д1=48 мм — минимальный размер максимального сечения изделия;
кл= коэффициент легирования;
кпр = коэффициент приспособления.
Схема укладки в печь изображена на рисунке 4.4.
Рисунок 4.4 — Схема укладки валов в печи Время выдержки при цементации:
??ц = ??/Vц, ч (4.6)
где Vц — скорость насыщения поверхности детали углеродом, которая зависит от температуры цементации и необходимой толщины насыщаемого слоя.
??ц = 0,9/0,2 = 4,5 часа = 270 мин.
Необходимая толщина цементованого слоя 0,9 мм, скорость насыщения стали углеродом для такой толщины и температуры цементации 930−950 °С составляет 0,2 мм/час.
Далее проводится закалка.
Температура нагрева при закалке определяется химическим составом стали и критическими точками по формуле:
tн = т. Ас1+(50 ч 70 оС) = 750 + (50−70) = 800−820 °С. (4.7)
Время нагрева под закалку такое же как и время нагрева под цементацию ??н = 69 мин.
Время выдержки фв при закалке шестерни определяется из формулы:
фв=(0,2ч0,3)*фн, (4.8)
и для данного зубчатого колеса составит:
фв = 0,25*69 = 18 мин.
Закалка шестерни осуществляется в масле при температуре масла 20−80 0С.
После закалки осуществляется промывка шестерни от масла в 10% растворе NaOH.
После промывки шестерня подвергается отпуску при температуре:
tотп= 180−200 оС Длительность отпуска определяется по формуле:
фотп = (120+д*фуд)*Кпр мин, (4.9)
где д = 33 мм — толщина изделия;
фуд = 1 мин/мм — удельное время нагрева.
Кпр =1,2 — коэффициент учитывающий нагрев на приспособление;
Значит, время отпуска составит:
фотп=(120+48*1)*1,2=202мин.
Охлаждение после отпуска производится на воздухе.
4.3 Разработка технологии термической обработки пружины
Необходимый комплекс свойств пружины из стали 60С2 можно обеспечить термической обработкой, которая включает закалку и средний отпуск. Режим закалки и среднего отпуска приведен на рисунке 4.5.
Рисунок 4.5 — Режим закалки и среднего отпуска пружины из стали 60С2
Температура нагрева при закалке определяется химическим составом стали и критическими точками по формуле:
tн = т. Ас3+(30 ч 50 оС) = 820 + (30−50) = 850−870 °С. (4.10)
Время нагрева рассчитаем по формуле А. П. Гуляева:
фн=0,1* К1* К2*К3*Д1,
где фн — время нагрева, мин;
К1=2 — коэффициент формы изделия, для цилиндрического изделия;
К2=2 — коэффициент среды, для нагрева в газовой среде;
К3=2 — коэффициент равномерности нагрева.
Схема укладки в печь изображена на рисунке 4.6.
Рисунок 4.6 — Схема укладки пружин в печи Д1=15 мм — минимальный размер максимального сечения изделия.
Таким образом, фн=0,1*2*2*2*15 = 12 мин.
Так как сталь 60С2 легированная необходимо учесть коэффициент легирования Кл=1,5.
фн= 12*1,5 = 18мин.
Так как пружина будет нагреваться в печи с приспособлением, то необходимо учесть и время нагрева на приспособление, по формуле:
фпр=(0,2ч0,3)*фн, (4.11)
где фпр — время нагрева на приспособление;
фн — время нагрева без приспособления.
фпр= 0,2*18 = 3,6 мин Тогда общее время нагрева пружины будет определяться как:
фн об= 18+3,6 = 21,6?22 мин.
Примем общее время нагрева 22 мин.
Время выдержки фв при закалке пружины определяется из формулы:
фв=(0,2ч0,3)*фн, (4.12)
и для данной пружины составит:
фв = 0,25*22 = 6 мин.
Закалка пружины осуществляется в масле при температуре масла 20−80 0С.
После закалки осуществляется промывка пружины от масла в 10% растворе NaOH.
После промывки пружины подвергается отпуску при температуре:
tотп=430−450 оС Длительность отпуска определяется по формуле:
фотп = (20+д*фуд)*Кпр мин, (4.13)
где д = 15 мм — толщина изделия;
фуд = 1 мин/мм — удельное время нагрева.
Кпр =1,2 — коэффициент учитывающий нагрев на приспособление;
Значит, время отпуска составит:
фотп=(20+15*1)*1,2=42мин.
Охлаждение после отпуска производится на воздухе.
4.4 Разработка технологии термической обработки плашки
Для обеспечения удовлетворительной работы плашки из стали У10А она подвергается такому виду термической обработки как закалка с низким отпуском. Режим закалки с низким отпуском приведен на рисунке 4.7.
Рисунок 4.7 — Режим закалки с низким отпуском плашки из стали У10А Температура нагрева при закалке определяется химическим составом стали и критическими точками:
tн = т. Ас1+(50 ч 70 оС) = 730 + (50−70) = 780−800 °С. (4.14)
Время нагрева рассчитаем по формуле Е. А. Смольникова:
фн= фскв.п+ физ.в. = К1 **Кф*Кк (4.15)
где фскв.п — время сквозного прогрева, мин;
физ.в. — время изотермической выдержки, мин;
К1 — коэффициент, характеризующий среднее удельное время нагрева, мин/см;
— геометрический показатель;
Кф — коэффициент формы изделия;
Кк — коэффициент конфигурации.
Время сквозного прогрева определяется по формуле:
??с. п. = К1*W*Кф*Кк*Кпр (4.16)
Тогда:
К1 = 12,5−0,025(Тн-800),
где Тн — температура нагрева, °С К1 = 12,5−0,025(800−800) =12,5 мин/мм Геометрический показатель формы изделия для фрезы определяется по формуле:
Де a — це ширина плашки, яка дорівнює 3,5 см;
b — висота плашки, b=1,5 см;
l — довжина плашки, l=23 см.
Коэффициент формы тела определяется по формуле:
Коэффициент конфигурации для плашки равен Кк = 0,75.
Коэффициент приспособления Кпр=1,2
Схема размещения плашек в печи представлена на рисунке 4.8
Рисунок 4.8 — Схема размещения плашек в печи С учетом всех коэффициентов:
??с. п. = 12,5*0,502*1,09*0,75*1,2 = 6,2?7мин Сталь У10А не является легированной, поэтому время изотермической выдержки 1мин, тогда:
фн = 7. + 1 = 8 хв..
Закалка плашки производится в воде. После закалки плашка подвергается низкому от пуску при температуре 160−180°С. Время отпуска расчитывается по формуле:
фотп = (120 + д * фуд) * кпр = (120 + 1 * 5) * 1,2 = 150 мин (4.19)
где д — удельное сечение, в данном случае д = Д1 = 5 мм;
фуд — удельное время нагрева определяется как 1 мин/мм сечения изделия.
После отпуска плашка охлаждается на воздухе.
4.5 Разработка технологии термической обработки пуансона
Для удовлетворения требований пуансона из стали 3Х3М3Ф назначен следующий режим термической обработки: закалка с подогревом и двукратным отпуском. Для предотвращения окисления и обезуглероживания поверхности изделия во время нагрева, нагревать следует в защитной атмосфере. Для получения высокой твердости стали при закалки, нагревать следует до температуры 1030−1050°С. Такая температура нагрева стали необходима для растворения карбидов и образования однородного твердого раствора. Для того, чтобы уменьшить уровень напряжений во время нагрева под закалку, проводим ступенчатый нагрев. Температура подогрева составляет 820−850єС, состав ванны: 70%BaCl + 30%NaCl, температура плавления данной соли составляет 7100С, рабочий интервал температур 750−9500С.
Т. к. следующий нагрев до температуры закалки будем осуществлять в печи-ванной, время нагрева пуансона следует рассчитывать по формуле Е. А. Смольникова 4.9 для жидких сред:
фн= фскв.п+ физ.в. = К1 **Кф*Кк (4.20)
где фскв.п — время сквозного прогрева, мин;
физ.в. — время изотермической выдержки, мин;
К1 — коэффициент, характеризующий среднее удельное время нагрева, мин/см;
— геометрический показатель;
Кф — коэффициент формы изделия;
Кк — коэффициент конфигурации.
Время сквозного прогрева определяется по формуле:
??с. п. = К1*W*Кф*Кк*Кпр (4.21)
Тогда:
К1 = 8−0,013(Тн-1000),
где Тн — температура нагрева, °С К1 = 8−0,013(1030−1000) =7,61 мин/мм Геометрический показатель формы изделия для пуансона определяется по формуле:
W = (D-d)*l/4*l+2*(D-d),
где D — внешний диаметр пуансона, см;
d — внутренний диаметр пуансона, см;
l — длина пуансона, см.
W = (13−3,5)*19/4*19+2*(13−3,5) = 1,9 см Коэффициент формы тела определяется по формуле:
Кф = 1+0,2*(D-d)/l
Кф = 1+0,2*(13−3,5)/19 = 1,1 см.
Коэффициент конфигурации для пуансона равен Кк = 1.
Коэффициент приспособления Кпр=1,2
С учетом всех коэффициентов:
??с. п. = 7,61*1,9*1,1*1*1,2 = 16,7?17мин Схема расположения пуансона в печи представлена на рисунке 4.8.
Рисунок 4.9 — Схеме расположения пуансонов в печи Время изотермической выдержки для легированной стали примем 2 мин.
Определим время подогрева:
ф820−850 = 2*фс.п. = 2*17 = 34 мин Охлаждение при закалке производится ступенчато. При этом температура изотермической выдержки составляет 450−500 0С. Время выдержки при этой температуре соответствует времени сквозного прогрева пуансона под закалку и составляет 17 мин.
В качестве охлаждающей среды применяется соль 50% KNO3 + 50%NaNO3. Температура плавления этой соли 400 єС, рабочая температура 450−650 єС. После выдержки пуансон охлаждают на воздухе, промывают в 10%-ном растворе NaОН с температурой 70−80 0С и сушат.
Далее проводят двухкратный отпуск при температуре 550−5600С длительностью 1 час каждый. В качестве среды нагрева используют соль 100% KNO3. Температура плавления этой соли 337 0С, интервал рабочих температур 400−570 0С.
Охлаждение после отпуска производится на воздухе.
Далее следует очистка фрезы от соли в моечно-сушильной машине.
На рисунке 4.7 приведен режим термической обработки пуансона из стали 3Х3М3Ф.
Рисунок 4.10 — Режим закалки и 2х кратного отпуска пуансона из стали 3Х3М3Ф
5. ВЫБОР ОБОРУДОВАНИЯ ДЛЯ ТЕРМИЧЕСКОЙ ОБРАБОТКИ И РАСЧЕТ ЕГО КОЛИЧЕСТВА
5.1 Выбор и расчет основного оборудования
К основному оборудованию относится оборудование, предназначенное для осуществления основных операций технологического режима термической обработки (нагрев, выдержка, охлаждение), то есть печи, печи-ванны, закалочные баки. Тип оборудования избирается на основании технологических процессов и режимов термической обработки изделий. При выборе оборудования необходимо учитывать:
1) характер загрузки изделий определяется количеством изделий сады, непрерывностью процесса, положением изделий в процессе обработки;
2) режим работы оборудования зависим от периодичности (непрерывности) операций;
3) режим термической обработки;
4) точность регулирования параметров (температуры, среды, времени);
5) источник получения тепла;
6) характер обработки изделий (размеры, масса, форма);
7) теплотехнический элемент конструкции (циркуляция атмосферы, герметизация рабочего пространства и др.).
Для расчета необходимого количества оборудования необходимо иметь:
1) номенклатуру обрабатываемых изделий и объем их выпуска в год;
2) производительность выбранного оборудования;
3) фонд времени работы оборудования.
В зависимости от применяемой методики расчета можно выделить следующие типы печей:
Тип 1 — печи периодического действия: камерные с неподвижным подом, шахтные печи-ванны с внешним и внутренним обогревом, электродные, с графитовым тиглем.
Часовая продуктивность печей определяется по формуле:
Qг=Мс/ф, (5.1)
где Qг— часовая продуктивность, кг/ч;
Мс— масса садки, кг;
фвремя обработки, ч.
ф=фн+фв+фо+фпот, (5.2)
где фн— время нагрева, ч;
фв— время выдержки, ч;
фо— время охлаждения, ч;
фпот— неучитываемые потери времени, ч.
Мс=(mвир*nn), (5.3)
где mвир — маса одного изделия, кг;
nn— количество изделий садки.
Qn=mвир*nn/ф, кг/год (5.4)
Тип 2 — печи непрерывного действия толкательного и пульсирующего типа:
Q2=(60/ф')*nт, (5.5)
где ф'- такт работы, мин;
nт— число деталей в партики, приспособлении, паддоне.
ф'=ф/г, (5.6)
где гчисло преспособлений.
г=L/l, (5.7)
где L-полезная длина печи, м;
l-длина, занятая изделием, приспособлением, м
Q2= mвир* nт*L/ф*l, кг/год (5.8)
Для расчета необходимого количества оборудования необходимо определить действительный фонд рабочего времени.
Фонд рабочего времени принимается равным для всех печей и определяется по формуле:
Ф = (Д — В — Пр) * С * фс * (1 — b/100), (5.9)
где Ф — годовой фонд времени работы оборудования, ч;
Д — число дней в году, Д=365;
В — число выходных дней, В=105;
Пр — число праздничных дней, Пр =10;
Сколичество смен, С = 3;
фс — число робочих часов в смену, ч, фс = 8;
bпотери времени на ремонт и перенастройку оборудования, %, b= 8%.
Тогда, Ф = (365−105−10)*8*3(1−8/100)=5520 ч Количество оборудования определяется по формуле:
Ср = (5.10)
где Ср — расчетное количество данного вида оборудования;
Q — обьем выпуска данного изделия в год, кг;
Qr— часовая продуктивность печей, кг/ч;
Ф — годовой фонд времени оборудования, ч.
Полученное значение Cр округляется до целого числа в большую сторону, таким образом определяется Cпр — принятое количество оборудования данного типа.
Коэффициент загрузки оборудования исчисляется по формуле:
Кз = Cр / Cпр (5.11)
где Кз — коэффициент загрузки;
Cпр — принятое количество оборудования, шт.
5.1.1 Выбор оборудования для обработки зубчатого колеса
Для нагрева под закалку зубчатого колеса можно использовать эл-ческую шахтную печь СШЗ-6.6 / 10 и СШО-6.12/7. Основные технические характеристики данных печей приведены в таблице 5.1.
Таблица 5.1 — Технические характеристики печей СШЗ-6.12/10 и СШО-6.12/7[5]
Индекс печи | Размеры рабочего пространства, мм | Максимальная рабочая температура, ?С | Габарити, мм | Мощность, КВт | Подуктивность, кг/год | |
СШЗ-6.12/10 | 0,6×1,2 | 2800×2700×3800 | ||||
СШО-6.30/7 | 0,6х3 | 2800×2800×6000 | ||||
Детали размещают на подвеске, которая состоит из поддона по 4 деталей на каждой. Для выбраных печей таких подвесок можна поставить 6.
Определим часовую производительность печи СШЗ-6.6 / 10 и массу садки по формулам (5.3) и (5.1):
МС = 6 * 24 = 144 (кг),
QР = 144 / 1 = 144 (кг/ч) Необходимое количество оборудования рассчитывается по формуле (5.8):
СР = 205 041/ (144 * 5520) = 0,26
Принимаем СПР = 1 Тогда коэффициент загрузки оборудования определяется по формуле (5.11):
.
Так как коэффициент загрузки маленький, поэтому не рационально использовать оборудование круглый год. Тогда изменим фонд рабочего времени для шахтной печи. Данная печь будет использоваться только первые две недели каждого месяца. Тогда расчетный фонд рабочего времени уменьшится вдвое:
СР = 205 041 / (144 * 2760) = 0,52.
Таким образом, коэффициент загрузки шахтной печи составит 0,52.
Закалку проводять в масле. Дальше без изменения садки детали подвергают високому отпуску в печи СШО-6.30 / 7.
Определим часовую производительность печи СШО-6.12 / 7 и массу садки:
МС = 6 * 24 = 144 (кг),
QР = 144 / 0,86 = 167 (кг/ч) Необходимое количество оборудования:
СР = 205 041 / (167 * 5520) = 0,22
Принимаем СПР = 1. Тогда коэффициент загрузки оборудования определяем по формуле (5.9):
.
Охлаждение после отпуска производят на воздухе.
Таким образом для обработки зубчатого колеса из стали 45Г2 необходима одна печь СШЗ-6.12 /10 и одна печь типа СШО-6.30/7.
5.1.2 Выбор оборудования для обработки шестерни
Для проведения цементации, закалки и низкого отпуска шестерни из стали 20Х выбираем шахтную печь типа СШЦМ-6.6/9, СШЗ-6.6/10 и СШО-6.6/7. Их технические характеристики приведены в таблице 5.2.
Таблица 5.2 — Технические характеристики печей СШЦМ-6.6/9, СШЗ-6.6/10 и СШО-6.6/7[5].
Индекс печи | Размеры рабочего пространства, м | Температура,°С | Габарити, м | Садка, т | Продук тивн-сть, кг/ч | Мощность, кВт | ||
диаметр | высота | |||||||
СШЦМ-6.6/9 | 0,6 | 0,6 | 2,7Ч2,6Ч3,0 | 0,6 | ||||
СШЗ-6.6/10 | 0,6 | 0,6 | 2,8Ч2,7Ч3,0 | 0,6 | ||||
СШО-6.6/7 | 0,6 | 0,6 | 2,8Ч2,7Ч3,0 | 0,5 | ||||
Детали размещают на подвеске, которая состоит из поддона по 4 деталей на каждой. Для выбраных печей таких подвесок можна поставить 6.
Определим часовую производительность печи СШЦМ-6.6/9и массу садки по формулам (5.3) и (5.1):
МС = 4 * 24 = 96 (кг),
QР = 96 / 5,65 = 17 (кг/ч) Необходимое количество оборудования рассчитывается по формуле (5.8):
СР = 175 035/ (17 * 5520) = 1,8
Принимаем СПР = 2 Тогда коэффициент загрузки оборудования определяется по формуле (5.11):
0,9
Дальше без изменения садки детали подвергают закалке в печи СШЗ-6.6/10
Определим часовую производительность печи СШЗ-6.6/10 и массу садки по формулам (5.3) и (5.1):
МС = 4 * 24 = 96 (кг),
QР = 96 / 1,45 = 66 (кг/ч) Необходимое количество оборудования рассчитывается по формуле (5.10):
СР = 175 035/ (66 * 5520) = 0,5
Принимаем СПР = 1 Тогда коэффициент загрузки оборудования определяется по формуле (5.11):
0,5
Закалку проводять в масле. Затем без изменения садки детали отправляют на отпуск в печи СШО-6.6/7.
Определим часовую производительность печи СШО-6.6/7 и массу садки по формулам (5.3) и (5.1):
МС = 4 * 24 = 96 (кг),
QР = 96 / 3,36 = 29 (кг/ч) Необходимое количество оборудования рассчитывается по формуле (5.10):
СР = 175 035/ (29 * 5520) = 1,1
Принимаем СПР = 2 Тогда коэффициент загрузки оборудования определяется по формуле (5.11):
0,55
Охлаждение после отпуска проводять на воздухе.
Таким образом, для проведения химико-термической обработки шестерни из стали 20Х не обходимо 2 печи СШЦМ-6.6/9, 1 печь СШЗ-6.6/10 и 2 печи СШО-6.6/7.
5.1.3 Выбор оборудования для обработки пружины
Для закалки и среднего отпуска пружины из стали 60С2 можно выбрать электрические печи с защитными атмосферами СНЗ/СНО-6.12.4/10. Технические характеристики этих печей приведены в таблице 5.3.
Таблица 5.3 — Технические характеристики печей СНЗ/СНО-6.12.4/10[5]
Индекс печи | Размеры рабочего пространства, мм | Максимальная рабочая температура, ?С | Габарити, мм | Мощность, КВт | Подуктивность, кг/год | |
СНЗ/СНО-6.12.4/10 | 600×1200×400 | 2000×2800×2500 | ||||
Для проведения закалки и отпуска пружины в специальных стаканах размещают на поддоне (500×500мм), который вмещает на себе 30 деталей.
Определим часовую производительность печи СНЗ-6.12.4/10 и массу садки по формулам (5.3) и (5.1):
МС = 1,5 * 30 = 45 (кг),
QР = 45 / 0,47 = 96 (кг/ч) Необходимое количество оборудования рассчитывается по формуле (5.10):
СР = 70 014/ (96 * 5520) = 0,13
Принимаем СПР = 1 Тогда коэффициент загрузки оборудования определяется по формуле (5.11):
0,13
Коэффициент загрузки очень маленький, потому не раціонально использовать оборудование целый год. Тогда изменим фонд рабочего времени для печи. Предположим, что дання печь будет использоваться только по одному месяцу в каждом полугодии. Тогда расчетный фонд рабочего времени значительно сократится, расчетное количество оборудования увеличится.
СР = 70 014 / (96 * 972) = 0,75.
Принимаем СПР = 1 Тогда коэффициент загрузки оборудования определяется по формуле (5.11):
0,75
Пружины охлаждают в масле. Затем без изменения садки детали размещают в печи СНО-6.12.4/10 на отпуск.
Определим часовую производительность печи СНЗ-6.12.4/10 и массу садки по формулам (5.3) и (5.1):
МС = 1,5 * 30 = 45 (кг),
QР = 45 / 0,7 = 64 (кг/ч) Необходимое количество оборудования рассчитывается по формуле (5.10):
СР = 70 014/ (64 * 5520) = 0,2
Принимаем СПР = 1 Тогда коэффициент загрузки оборудования определяется по формуле (5.11):
0,2
Коэффициент загрузки очень маленький, потому не раціонально использовать оборудование целый год. Тогда изменим фонд рабочего времени для печи. Предположим, что дання печь будет использоваться только по одному месяцу в каждом полугодии. Тогда расчетный фонд рабочего времени значительно сократится, расчетное количество оборудования увеличится.
СР = 70 014 / (64 * 972) = 1,1.
Принимаем СПР = 2 Тогда коэффициент загрузки оборудования определяется по формуле (5.11):
0,55
Охлаждение после отпуска производится на воздухе.
Таким образом, для проведения термической обработки пружины из стали 60С2 не обходимо 1 печь СНЗ-6.12.4/10 для закалки и 2 печи СНО-6.12.4/10 для отпуска.
5.1.4 Выбор оборудования для обработки плашки
Для термической обработки плашки из стали У10А используются электрические соляные ванны для закалки, а именно СВС-6.9.4,5/8,5. Для отпуска можно использовать электрическую камерную печь — СНО-6.12.4/10. Технические характеристики даннях печей приведены в таблице 5.4.
Таблица 5.4 — Технические характеристики печей СВС-6.9.4,5/8,5 и СНО-6.12.4/10[5]
Індекс печі | Розміри робочого простору, м | Температура,°С | Габарити, м | Прод-сть кг/ч | Мощ-сть, кВт | |||
ширина | довжина | висота | ||||||
СВС-6.9.4,5/8,5 | 0,6 | 0,9 | 0,45 | 1,7Ч2,1Ч1,5 | ||||
СНО-6.12.4/7 | 0,6 | 1,2 | 0,4 | 2,0Ч2,8Ч2,5 | ||||
Для закалки плашки размещают на поддоне. Каждый поддон вмещает 8 плашок.
Определим часовую производительность печи СВС-6.9.4,5/8,5 и массу садки по формулам (5.3) и (5.1):
МС = 2 * 8 = 16 (кг),
QР = 16 / 0,13 = 123 (кг/ч) Необходимое количество оборудования рассчитывается по формуле (5.10):
СР = 30 006/ (123 * 5520) = 0,04
Принимаем СПР = 1 Тогда коэффициент загрузки оборудования определяется по формуле (5.11):
0,04
Коэффициент загрузки очень маленький, потому не раціонально использовать оборудование целый год. Тогда изменим фонд рабочего времени для печи. Предположим, что дання печь будет использоваться только две недели в каждом полугодии. Тогда расчетный фонд рабочего времени значительно сократится, расчетное количество оборудования увеличится.
СР = 30 006 / (123 * 442) = 0,55.
Принимаем СПР = 1 Тогда коэффициент загрузки оборудования определяется по формуле (5.11):
0,55
Закалка плашки производится в воде. Затем плашки подвергают низкому от пуску в печи СНО-6.12.4/7. В печи используют защитную атмосферу. Инструмент в печь загружают на большем поддоне, который вмещает 14 деталей. В рабочее пространство печи помещается два таких поддона.
Определим часовую производительность печи СНО-6.12.4/7и массу садки по формулам (5.3) и (5.1):
МС = 2 * 28 = 56 (кг),
QР = 56 / 2,5 = 23 (кг/ч) Необходимое количество оборудования рассчитывается по формуле (5.10):
СР = 30 006/ (23 * 5520) = 0,24
Принимаем СПР = 1 Тогда коэффициент загрузки оборудования определяется по формуле (5.11):
0,24
Охлаждение после отпуска производится на воздухе.
Таким образом, для проведения термической обработки плашки из стали У10А необходимо 1 печь СВС-6.9.4,5/8,5 для закалки и 1 печь СНО-6.12.4/7 для отпуска. Так как коэффициент загрузки отпускной печи маленький, эту же печь можно использовать для отпуска пружин.
5.1.5 Выбор оборудования для обработки пуансона
Для термической обработки пуансона из стали 3Х3М3Ф используются соляные печи-ванны, а именно СВС-1,5.2,5.3,2/13 — для нагрева под закалку, СВС-6.9.4,5/8,5- для подогревов под. закалку и непосредственно закалки, СВС-3,5.8,3.5/6 — для закалки и шахтную печь типа СШО-6.6/7 — для отпуска. Технические характеристикиданных печей приведены в таблице 5.5.
Таблица 5.5 — Технические характеристики печей СВС-1,5.2,5.3,2/13, СВС-6.9.4,5/8,5 и СШО-6.6/7[5]
Индекс печи | Размеры рабочего пространства, м | Темпера; тура,°С | Габарити, м | Продуктивность, кг/ч | Мощность, кВт | |||
ширина диаметр | длина | высота | ||||||
СВС-2.3,5.3,2/13 | 0,2 | 0,35 | 0,32 | 1,6Ч3,0Ч2,0 | ||||
СВС-6.9.4,5/8,5 | 0,6 | 0,9 | 0,45 | 1,7Ч2,1Ч1,5 | ||||
СШО-10.20/7 | 1,0 | ; | 2,0 | 3,7Ч3,5Ч5,0 | ||||
Для размещения пуансонов в печи используют подвески. На подвеске 6 пуансонов. В рабочее пространство печи помещается 2 подвески.
Определим часовую производительность печи СВС-6.9.4,5/8,5 и массу садки по формулам (5.3) и (5.1):
МС = 6 * 12 = 72 (кг),
QР = 72 / 0,85 = 85 (кг/год) Необходимое количество оборудования рассчитывается по формуле (5.10):
СР = 20 004/ (85 * 5520) = 0,04
Принимаем СПР = 1 Тогда коэффициент загрузки оборудования определяется по формуле (5.11):
0,04
Коэффициент загрузки очень маленький, потому не раціонально использовать оборудование целый год. Тогда изменим фонд рабочего времени для печи. Предположим, что дання печь будет использоваться только по две недели в каждом полугодии. Тогда расчетный фонд рабочего времени значительно сократится, расчетное количество оборудования увеличится.
СР = 20 004/ (85 * 442) = 0,53
Принимаем СПР = 1 Тогда коэффициент загрузки оборудования определяется по формуле (5.11):
0,53
Далее без изменения садки інструмент размещают в печи для закалки.
Определим часовую производительность печи СВС-2.3,5.3,2/13 и массу садки по формулам (5.3) и (5.1):
МС = 6 * 12 = 72 (кг),
QР = 72 / 0,6 = 120 (кг/год) Необходимое количество оборудования рассчитывается по формуле (5.10):
СР = 20 004/ (120 * 5520) = 0,03
Принимаем СПР = 1 Тогда коэффициент загрузки оборудования определяется по формуле (5.11):
0,03
Коэффициент загрузки очень маленький, потому не рационально использовать оборудование целый год. Тогда изменим фонд рабочего времени для печи. Предположим, что дання печь будет использоваться только по две недели в каждом полугодии. Тогда расчетный фонд рабочего времени значительно сократится, расчетное количество оборудования увеличится.
СР = 20 004/ (120 * 442) = 0,38
Принимаем СПР = 1 Тогда коэффициент загрузки оборудования определяется по формуле (5.11):
0,38
Закалку проводят ступенчато, изначально охлаждение происходит в соли, затем на воздухе.
Затем инструмент подвергается отпуску в шахтной печи СШО-10.20/7. При отпуске изменяется садка. В данню печь пожно загрузить 6 таких подвесок.
Определим часовую производительность печи СШО-6.6/7 и массу садки по формулам (5.3) и (5.1):
МС = 6 * 36 = 216 (кг),
QР = 216 / 1 = 216 (кг/год) Необходимое количество оборудования рассчитывается по формуле (5.10):
СР = 20 004/ (216 * 5520) = 0,02
Принимаем СПР = 1 Тогда коэффициент загрузки оборудования определяется по формуле (5.11):
0,02
Коэффициент загрузки очень маленький, потому не раціонально использовать оборудование целый год. Тогда изменим фонд рабочего времени для печи. Предположим, что дання печь будет использоваться только по две недели в каждом полугодии. Тогда расчетный фонд рабочего времени значительно сократится, расчетное количество оборудования увеличится.
СР = 20 004/ (216 * 442) = 0,21
Принимаем СПР = 1 Тогда коэффициент загрузки оборудования определяется по формуле (5.11):
0,21
Охлаждение после отпуска осуществляют на воздухе.
Таким образом, для проведения термической обработки пуансона из стали 3Х3М3Ф необходимо 1 печь СВС-6.9.4,5/8,5 для подогрева под. закалку и 1 печь СВС-2.3,5.3,2/13для закалки и 1 печь СШО-10.20/7 для отпуска.
Так как при подогреве под закалку коэффициент загрузки очень меленький, то эту же печь можно использовать для закалки плашок (рабочая температура соли это позволяет), а шахтную печь для отпуска можно использовать для отпуска зубчатих колес и шестерен.
5.2 Оборудование для охлаждения
В качестве охлаждаемого оборудования используются закалочные баки, а при промывке изделий, в случае охлаждения их в масле или соли — промывочные баки. Расчет производится по уравнению теплового баланса, из которого можно найти необходимый объем закалочной жидкости по формуле:
Vр =
где Gмаса деталей с поддоном, кг;
С1, С2 — средняя теплоемкость метал лов в интервале температур от 0 0С до tMe.н и от 0 0С до tMe.к, кДж/л*К;
tMe.н, tMe.к -начальная и конечная температура металла, 0С;
Сж — теплоемкость закалочной жидкости, кДж/л*К;
t.н, t.к — начальная и конечная температура закалочной жидкости, 0С.
Отношение массы закалочной жидкости и охлаждаемого металла должно быть в пределах 5−7 т:
(5.12)
где сж — плотность закалочной жидкости, кг/м3.
Размеры сливного кармана:
Dзовн = Dвн+0,3, м; (5.13)
Длина сливного кармана:
м (5.14)
где Dзовн, Dвн — внешний и внутренний діаметр сливного кармана, м;
ДV — изменение обьема жидкости, м3
ДV=, м3 (5.15)
где г — плотность металла, кг/м3;
гtп, гtк — плотность масла при температуре tп и tк, кг/м3.
5.2.1 Выбор оборудования для охлаждения зубчатого колеса
Для шахтной печи СШЗ-6.12 /10 с максимальной рабочей температурой 1000єС рассчитаем параметры закалочного бака для охлаждения зубчатого колеса из стали 45Г2 в масле, масса садки — 144 кг, одновременно нагревают 24 детали, диаметр приспособления — 180 мм.
Рассчитаем объем масла в баке по формуле (5.11):
При этом: С1=0,695 кДж/кг· К; С2=0,486 кДж/кг· К;
Ср=2 кДж/л· К (для масла) [4];
При закалки в масле начальная температура масла составляет 30 — 40 єС, а конечная — 60 — 80 єС[6]. Принимаем tм.п. = 815 °C, tм.к. = 100 °C.
Рассчитаем отношение массы закалочной жидкости и охлаждающегося металла по формуле (5.12):
Это отвечает требованиям, поскольку
Определим по формуле (5.15) объем сливного кармана:
При этом: г = 7800 кг/м3; гtп = 925 кг/м3, гtк = 905 кг/м3 [4];
Примем Dвн = 0,2 м, тога по формуле (5.13):
Dвнеш = 0,2 +0,3=0,5 м;
Длина сливного кармана расчитывается по формуле (5.14):
Выбираем закалочный масляный вертикальный бак круглого сечения диаметром 0,8 м, высотой 1,5 м — БПВ-8.15. Такой же бак выбираем для промывки зубчатого колеса от масла.
При охлаждении зубчатого колеса, как охлаждающая среда при отпуске используется вода, поэтому при термообработке этого изделия требуется оборудование для охлаждения.
Для шахтной печи СШО-6.30 /7 с максимальной рабочей температурой 1000єС рассчитаем параметры закалочного бака для охлаждения зубчатого колеса из стали 45Г2 в воде, масса садки — 144 кг, одновременно нагревают 24 детали, диаметр приспособления — 180 мм.
Рассчитаем объем воды в баке по формуле (5.11):
При этом: С1=0,645 кДж/кг· К; С2=0,486 кДж/кг· К;
Ср=4,2 кДж/л· К (для воды) [4];
При закалки в воде начальная температура воды составляет 15−20єС, а конечная — 30−40 єС. Принимаем tм.п. = 670 °C, tм.к. = 80 °C.
Рассчитаем отношение массы закалочной жидкости и охлаждающегося металла по формуле (5.12):
Это отвечает требованиям, поскольку
Определим по формуле (5.15) объем сливного кармана:
При этом: г = 7800 кг/м3; гtп = 999,23 кг/м3, гtк = 992,24 кг/м3[4];
Примем Dвн = 0,2 м, тога по формуле (5.13):
Dвнеш = 0,2 +0,3=0,5 м;
Длина сливного кармана расчитывается по формуле (5.14):
Выбираем закалочный вертикальный бак круглого сечения диаметром 0,8 м, высотой 1,5 м — БПВ-8.15.
5.2.2 Выбор оборудования для охлаждения шестерни
Для шахтной печи СШЗ-6.6 /10 с максимальной рабочей температурой 1000єС рассчитаем параметры закалочного бака для охлаждения шестерни из стали 20Х в масле, масса садки — 93 кг, одновременно нагревают 24 детали, диаметр приспособления — 180 мм.
Рассчитаем объем масла в баке по формуле (5.11):
При этом: С1=0,695 кДж/кг· К; С2=0,486 кДж/кг· К;
Ср=2 кДж/л· К (для масла) [5];
При закалки в масле начальная температура масла составляет 30 — 40 єС, а конечная — 60 — 80 єС. Принимаем tм.п. = 820 °C, tм.к. = 100 °C.
Рассчитаем отношение массы закалочной жидкости и охлаждающегося металла по формуле (5.12):
Это отвечает требованиям, поскольку
Определим по формуле (5.15) объем сливного кармана:
При этом: г = 7800 кг/м3; гtп = 925 кг/м3, гtк = 905 кг/м3[4];
Примем Dвн = 0,2 м, тога по формуле (5.13):
Dвнеш = 0,2 +0,3=0,5 м;
Длина сливного кармана расчитывается по формуле (5.14):
Выбираем закалочный масляный вертикальный бак круглого сечения диаметром 0,8 м, высотой 1,5 м — БПВ-8.15. Такой же бак выбираем для промывки шестерни от масла.
При охлаждении шестерен, как охлаждающая среда при отпуске используется воздух, поэтому при термообработке этого изделия не требуется оборудование для охлаждения.
5.2.3 Выбор оборудования для охлаждения пружины
Для печи СНЗ-6.12.4 /10 с максимальной рабочей температурой 1000єС рассчитаем параметры закалочного бака для охлаждения пружины из стали 60С2 в масле, масса садки — 45 кг, одновременно нагревают 60 деталей, диаметр приспособления — 500 мм.
Рассчитаем объем масла в баке по формуле (5.11):
При этом: С1=0,687 кДж/кг· К; С2=0,486 кДж/кг· К;
Ср=2 кДж/л· К (для масла)[4];
При закалки в масле начальная температура масла составляет 30 — 40 єС, а конечная — 60 — 80 єС. Принимаем tм.п. = 870 °C, tм.к. = 100 °C.
Рассчитаем отношение массы закалочной жидкости и охлаждающегося металла по формуле (5.12):
Это отвечает требованиям, поскольку
Определим по формуле (5.15) объем сливного кармана:
При этом: г = 7800 кг/м3; гtп = 925 кг/м3, гtк = 905 кг/м3[4];
Примем Dвн = 0,2 м, тога по формуле (5.13):
Dвнеш = 0,2 +0,3=0,5 м;
Длина сливного кармана расчитывается по формуле (5.14):
Выбираем закалочный масляный горизонтальный бак прямоугольного сечения раз мерами 1,5Ч0,6Ч0,6 — БПГ-15.6.6 .
При охлаждении пружин, как охлаждающая среда при отпуске используется воздух, поэтому при термообработке этого изделия не требуется оборудование для охлаждения.
5.2.4 Выбор оборудования для охлаждения плашки
Для печи-ванны СВС-6.9.4,5 / 8,5 с максимальной рабочей температурой 850 ° C рассчитаем параметры закалочного бака для охлаждения плашек из стали У10А после закалки, которая проводится в воде. Масса садки 16 кг. Размер поддона 500 Ч 350 мм, на одном поддоне размещается 8 деталей.
Рассчитаем объем воды в баке по формуле (5.11):
При этом: С1=0,625 кДж/кг· К; С2=0,486 кДж/кг· К;
Ср=4,2 кДж/л· К (для воды) [4];
При закалки в воде начальная температура воды составляет 15−20єС, а конечная — 30−40 єС. Принимаем tм.п. = 800 °C, tм.к. = 80 °C.
Рассчитаем отношение массы закалочной жидкости и охлаждающегося металла по формуле (5.12):
Это отвечает требованиям, поскольку
Определим по формуле (5.15) объем сливного кармана:
При этом: г = 7800 кг/м3; гtп = 999,23 кг/м3, гtк = 992,24 кг/м3[4];
Примем Dвн = 0,2 м, тога по формуле (5.13):
Dвнеш = 0,2 +0,3=0,5 м;
Длина сливного кармана расчитывается по формуле (5.14):
Выбираем закалочный масляный горизонтальный бак прямоугольного сечения раз мерами 1,5Ч0,6Ч0,6 — БПГ-15.6.6 .
При охлаждении плашек, как охлаждающая среда при отпуске используется воздух, поэтому при термообработке этого изделия не требуется оборудование для охлаждения.
5.3 Выбор вспомогательного оборудования
К вспомогательному оборудованию относят оборудования для получения контролируемой атмосферы и вакуума.
Выбор контролируемой атмосферы зависит от обрабатываемого материала, технологического процесса, необходимого вида поверхности и температуры. При выборе также стоит учитывать стоимость газа, и наличие на заводе сырья для его получения. Установка выбирается из общего расчета потребления печами контролируемых атмосфер. В среднем каждая печь тратит 10 м3 / ч, тогда Vобщ = 10 * 5 = 50 м3 / ч. Таким образом, выбираем установку для получения контролируемых атмосфер из природного газа ЭН-60 М2, технические данные которого представлены в таблице 5.7[5].
Таблица 5.7 — Технические данный установки ЭН-60М2 [5]
Продуктивность, кг/ч | Мощность, кВт | Расход природного газа, м3/год | Габарити, м | Масса, т | |
37,0 | 12,4 | 2,8Ч1,6Ч2,9 | 3,6 | ||
Эта установка предназначена для получения эндотермической контролируемой атмосферы из природного газа. Эндогаз состоит из 20% CO, 40% H2, 1% CO2 и 1% CH4, другое азот.
5.4 Выбор дополнительного оборудования
Для промывания изделий используются промывочные баки с содержанием 10% раствора NaOH с температурой 20−30°С. Рассмотрим их размеры:
Для промывания зубчатых колес, шестерен и пуансонов после закалки используется промывочный вертикальный бак круглого сечения размерами 0,8 Ч 1,5 м — БПВ 8.15.
Для промывания пружин после закалки используется промывочный вертикальный бак прямоугольного сечения с размерами 1,5Ч0,6Ч0,6 м — БПГ 15.6.6.
5.5 Выбор подъемно-транспортного оборудования
В организации работы термического отделения большое значение имеет межоперационный транспорт. Транспорт должен обеспечить согласованность нагрузки и перемещения деталей с технологическим процессом, поточность производства, механизацию трудоемких процессов с полным использованием мощности подъемно-транспортных механизмов.
Для обслуживания печей используют кран-балку. Руководят им снизу с помощью кнопочного устройства. Грузоподъемность составляет 1 т и 0,5 т, скорость подъема груза составляет 6 — 8 м / мин., Скорость движения — 60 — 120 м / мин.
Для транспортировки деталей по отделению и за его пределы применяют ручную и самоходную (с подъемной платформой) тележки. Также в отделении имеются столы для формирования садок и столы для контроля качества изделий.
6. РАЗРАБОТКА ПЛАНИРОВКИ ТЕРМИЧЕСКОГО ОТДЕЛЕНИЯ
Для размещения термического отделения применяется одноэтажный дом прямоугольной формы. Площадь цеха делится на производственную и вспомогательную. Производственную площадь предварительно рассчитывают по увеличенным показателям путем суммирования площади для каждого вида выбранного оборудования по формуле:
Sпов=У (Si * ni),
где Sпов— полезная необходимая площадь, м2;
Si — укрупненная норма площади на 1 единицу и-го типа печи, агрегата или установки;
ni — количество единиц оборудования и-го типа.
В таблице 7.1 приведены данные принятых укрупненных норм площади оборудования и расстояние для их размещения.
На основе данных таблицы, производственная площадь цеха по укрупненным показателям составляет: 420 м2.
С учетом проездов, проходов общая площадь цеха составит:
Ѕ=420*1,3=546 м2.
Вспомогательная площадь цеха определяется по увеличенным показателям и принимается в размере 30% производственной площади:
Sвсп=Sпов * 0,30=546 * 0,30=164 м2
Sзаг=Sпов+Sвсп=546+164=710 м2
Выбираем ширину пролета 18 м, длина 42 м. Шаг ж / б колонн составляет 6 м. Окна, шириной 3 м, выполненные одинарными застиклением. Размер цеховых ворот составляет 4 м. Ширина проезда 4 м. Размещение контрольно-бытовых помещений в отделении предусмотрено. Они находятся в этом же здании.
Таблица 7.1 — Габаритные размеры оборудования, принятые нормы площади и расстояния для их размещения
Вид оборудования | Габаритные размеры (ширина, длина, высота) м | Норма площади на 1 ед., м2 | Общая площадь на данный вид, м2 | Расстояние, м, между печами/ к др. оборудованию/ к стене (колонны) | |
1.Термические печи 1.1СШЗ-6.12/10 1.2 СШО-6.30/7 1.3 СШЦМ-6.6/9 1.4 СШЗ-6.6/10 1.5 СШО-6.6/7 1.6 СНЗ-6.12.4/10 1.7 СНО-6.12.4/10 1.8 СВС-6.9.4,5/8,5 1.9 СВС-2.3,5.3,2/13 1.10 СШО-10.20/7 | 2,8Ч2,7Ч3,8 2,8Ч2,7Ч4,0 2,7Ч2,6Ч3,0 2,8Ч2,7Ч3,0 2,8Ч2,7Ч3,0 2,0Ч2,8Ч2,5 2,0Ч2,8Ч2,5 1,7Ч2,1Ч1,5 1,6Ч3,0Ч2,0 3,7Ч3,5Ч5,0 | 1/1/1,5 2/½ 1/1/1 1/1/1 1/1/1 1/1/1,5 1/1/1,5 1/1/1 1/1/1 1/1/1,5 | |||
2. Закалочные баки 2.1Немеханизированный бак d=0,8 м 2.2Немеханизированный бак | 0,8Ч1,5 1,5Ч0,6Ч0,6 | -/1/1 -/1/1 | |||
3. Дополнительное и вспомогательное оборудование 3.1 Промывочный бак d=0,8 м 3.2 Промывочный бак 4.3Ендогазовая установка ЭН-60М2 4.4Токарно-шлифовачный станок — «Герцог» | 0,8Ч1,5 1,5Ч0,6Ч0,6 2,8Ч1,6Ч2,9 0,95Ч0,7Ч1,7 | -/1/1 -/1/1 -/2/1,5 -/2/1,5 | |||
Для улучшения освещенности здания применяют продольные фонари с вертикальным застеклкнием. Для установки вертикальных печей, закалочных баков делают местные углубления, а для трубопроводов устраивают каналы, которые перекрываются сверху плитами. Газопроводы прокладывают над землей, трубопроводы крепят на ж / б колонках на высоте не менее 3 м, а вне цеха на высоте 5−6 м.
Оборудование в термическом цехе расположено рационально с точки зрения технологического процесса и удобства его обслуживания. План отделения изображен в масштабе 1: 100 на листе А1. Спецификация представлена в приложении Б.
Планировка цеха включает выбор наиболее рациональных элементов его компоновки, определения геометрических размеров, нанесение на чертеж строительных элементов, оборудования, транспортных средств.
Площадь цеха равномерно распределяется между нагревательными приборами. Производственная площадь цеха по укрупненным показателям составляет: 710 м2.ширина пролета 18 м. Исходя из этого длина цеха составляет 39,4 м, так как длина цеха должна быть кратной 6, то принимаем длину равную 42 м.
7. ТЕХНИКА БЕЗОПАСНОСТИ О ОХРАНА ОКРУЖАЮЩЕЙ СРЕДЫ
На каждом промышленном предприятии действует система управления охраной труда. Это совокупность органов управления предприятием, которые проводят планомерную деятельность по обеспечению здоровых, безопасных и высокопроизводительных условий труда.
Основными задачами управления охраной труда являются: образование работников безопасным методам труда и пропаганде вопросов охраны труда; обеспечение безопасности технологических процессов, производственного оборудования, зданий и сооружений; нормализация санитарно-гигиенических условий труда; обеспечение оптимальных режимов труда и отдыха; организация лечебно-профилактического обслуживания; профессиональный отбор работников отдельных профессий; совершенствование нормативной базы по вопросам охраны труда.
К опасным факторам данного производства относятся:
— возможность поражения электрическим током;
— повышенная температура воздуха рабочей зоны;
— большое количество пыли.
Для исключения поражения человека электрическим током используются защитное заземление.
С целью снижения влияния лучистой энергии на организм человека следует использовать спецодежду.
При закалке и отпуске должны выполняться правила, касающиеся обслуживания печей, работающих с электрическим нагревом. Основное внимание должно быть обращено на выполнение правил электробезопасности.
В печи-ванны нужно загружать только предварительно высушенную соль. Уровень расплава солей в печах не должны превышать ¾ высоты ванны.
Меры безопасности при работе с маслом: верный выбор необходимого масла, контроль его температуры, организация систем слива масла, наличие средств тушения.
При работе с контролируемыми атмосферами следует применять автоматическую продувку инертным газом.
Основным источником загрязнения окружающей среды на термическом участке являются соляные, закалочные, цементационные, отпускные печи и масляные закалочные баки.
На термической участке, воздух, который выбрасывается, загрязнен парами и продуктами горения масла, аммиаком и другими веществами, которые попадают в систему местной вытяжки.
При закалке и отпуске деталей в масляных баках в воздухе, выходящем из баков помещается до 1% паров масла от веса металла.
Во избежание попадания паров масел, соли, продуктов сгорания в атмосферу на термическом участке предусмотрено установление над печами и холодильной баками вытяжки; чтобы очистить газ, содержащий пыль устанавливают пылеулавливающих камеру; во избежание выброса паров масел и солей используют волокнистые фильтры.
Кроме газообразных и жидких отходов при термообработке образуются твердые отходы. К ним относятся окалина, бракованные детали.
Окалина может быть использована как добавка к основной шихты в литейном цехе, а бракованные изделия отправляют на переплав.
8. КОНТРОЛЬ КАЧЕСТВА
В цикле производственного процесса изготовления деталей термическая обработка является последней операцией, от которой во многом зависит качество выпускаемой продукции. Поэтому контроль качества продукции в термическом отделении имеет важное значение. Хорошо организованный и правильно поставленный контроль способствует повышению качества продукции, улучшению технологии изготовления деталей. Технический контроль продукции проводится сотрудниками отделения технического контроля (ОТК) и заводской лаборатории. В термическом отделении осуществляется текущий контроль качества обрабатываемой продукции. Основными моментами контроля качества деталей являются: осмотр деталей с целью выявления внешних пороков (трещин, окалины), контроль соответствия размеров детали допускам, контроль твердости.
Зубчатые колеса после улучшающей обработки контролируют по твердости. Изначально проводится контроль поверхностных дефектов невооруженным глазом, измеряются линейные размеры. Затем измеряется твердость на твердомере Бринелля. После чего, с помощью микроскопа изучается структура.
Шестерни после химико-термической обработки контролируются по следующим показателям:
ь толщина цементованого слоя: оценивается по твердости и микроструктуре обычно на образцах-свидетелях, изготовленных из той же марки стали и обработанных по тому же режиму, что и детали;
ь твердость поверхности, распределение твердости по слою: измеряется непосредственно в потоке обработки деталей на различных зонах поверхности торированным напильником (НRС 57−60) — 10% от партии термообработанных деталей;
ь твердость по сечению определяется в лаборатории на шлифах (НRС 30−35) — 10% от партии термообработанных деталей;
ь содержание углерода: осуществляется послойным спектральным анализом на установке ДФС-51.
Контроль качества пружин осуществляется по следующим признакам:
ь внешний осмотр: на поверхности пружин не допускаются риски, трещины, волосовины и другие грубые дефекты — не менее 20% от партии термообработанных деталей;
ь контроль твердости — 10% от партии термообработанных деталей.
Контроль качества плашек осуществляется по следующей схеме:
ь контроль твердости — 10% от партии термообработанных деталей.
ь выявление дефектов выходящих на поверхность или находящихся на небольшой глубине — 10% от партии термообработанных деталей.
ь проверка коробления-20% от партии термообработанных деталей.
ь контроль линейных размеров-20% от партии термообработанных деталей.
Контроль качества пуансонов:
ь твердость рабочей части на твердомер — ТК-2М — 10% от партии;
ь микроструктуру — на микроскопе Neophot.
Также контроль качества включает в себя проверку всех параметров, которые предусмотрены чертежами деталей и инструментов: визуальная оценка, контроль размеров, контроль корабления детали, степень очистки, наличие или отсудствие трещин, рисок и т. д.
Для проведения контроля качества термообработанной продукции необходимы:
— твердомеры ТК-2М,
— торированный напильник;
— микроскоп Neophot;
— eстановка спектрального анализа ДФС-51.
Таблица 8.1 — Технические и расчетные характеристики оборудования
Тип оборудования | Габаритные размеры, м | Размеры рабо рабо пространства, м | Мощность, кВт | Продуктивность, кг/год | Расчетное кол-во единиц | Принятое количество | Коэффициент загрузки | ||
паспортная | расчетная | ||||||||
СШЗ-6.12/10 | 2,8Ч2,7Ч3,8 | 0,60Ч1,2 | 0,52 | 0,52 | |||||
СШО-6.30/7 | 2,8Ч2,7Ч4,0 | 0,60Ч0,3 | 0,22 | 0,22 | |||||
СШЦМ-6.6/9 | 2,7Ч2,6Ч3,0 | 0,60Ч0,60 | 1,8 | 0,90 | |||||
СШЗ-6.6/10 | 2,8Ч2,7Ч3,0 | 0,60Ч0,60 | 0,50 | 0,50 | |||||
СШО-6.6/7 | 2,8Ч2,7Ч3,0 | 0,60Ч0,60 | 0,55 | 0,55 | |||||
СНЗ-6.12.4/10 | 2,0Ч2,8Ч2,5 | 0,6Ч1,2Ч0,4 | 0,75 | 0,75 | |||||
СНО-6.12.4/10 | 2,0Ч2,8Ч2,5 | 0,6Ч1,2Ч0,4 | (23) | 1,1 (0,24) | 0,79 | ||||
СВС-6.9.4,5/8,5 | 1,7Ч2,1Ч1,5 | 0,6Ч0,9Ч0,45 | 0,55 | 0,55 | |||||
СВС-2.3,5.3,2/13 | 1,6Ч3,0Ч2,0 | 0,2Ч0,35Ч0,32 | 0,38 | 0,38 | |||||
СШО-10.20/7 | 3,7Ч3,5Ч5,0 | 1,0Ч2,0 | 0,21 | 0,21 | |||||
Закалочный бак с маслом | 0,8Ч1,5 | ||||||||
Закалочный бак с маслом | 1,5Ч0,6Ч0,6 | ||||||||
Закалочный бак с водой | 1,5Ч0,6Ч0,6 | ||||||||
Отпускной бак с водой | 0,8Ч1,5 | ||||||||
Промывочный бак | 0,8Ч1,5 | ||||||||
Промывочный бак | 1,5Ч0,6Ч0,6 | ||||||||
Твердомер ТК-2М | |||||||||
Микроскоп Neophot | |||||||||
Установка спектрального анализа ДФС-51 | |||||||||
Токарно-шлифовачный станок — «Герцог» | |||||||||
Кран-балка | |||||||||
Щит управления | |||||||||
Установка эндогаза | 2,8Ч1,6Ч2,9 | ||||||||
Правильная машина | |||||||||
Общее кол-во, шт | |||||||||
ЗАКЛЮЧЕНИЕ
В курсовой работе для обработки шестерни, зубчатого колеса, пружины, пуансона, плашкиы при заданной производственные программе 500 тонн разработали термический отделение. Были рассмотрены условия работы деталей и инструментов и требования, предъявляемые к ним. Для их изготовления были выбраны материалы, которые наиболее экономичные и полностью удовлетворяют необходимым свойствам. Разработаны рациональные режимы упрочняющей термической обработки изделий. Предусмотрено проведение контроля качества изделий после окончательной термообработки. Выбраное основное, вспомогательное и дополнительное оборудование. Оборудование в цехе расположено рационально с точки зрения технологического процесса и удобства его обслуживания.
ПЕРЕЧЕНЬ ССЫЛОК
1. Производство прокатной продукции [Електронный ресурс] / МЕТАЛЛУРГПРОМ. — Режим доступа: http://www.nait.ru/journals/index.php?p_journal_id=7 — 27.12.2013 г. — Заголов. с экрана.
2. Детали машин [Електронный ресурс] / Режим доступа: http:// http://www.ngeom.ru/teorgraf13.html — Заголов. с экрана.
3. Сорокин В. Г. Стали и сплавы: Марочник / В. Г. Сорокин, М. А. Гервасьев, В. С. Палеев, И. В. Гервасьева, С. Я. Палеева — М.: Машиностроение, 1989. — 638с.
4. Методические указания к лабораторным работам по курсу «Оборудование для упрочняющей термообработки» — Донецк, ДонНТУ, 2013. — 32 с.
5. Соколов К. Н. Оборудование термических цехов/К.Н. Соколов — Киев: Вища школа.1984. — 328.
6. Анурьев, В. И. Справочник конструктора-машиностроителя. Т.1. / В. И, Анурьев. — 8-е изд., перераб. и доп. — М.: Машиностроение, 2001. — 920 с.
7. Гуляев А. П. Инструментальные стали. Справочник./ А. П. Гуляев — М. Машиностроение, 1975. -270 с.
8. Тылкин М. А. Справочник термиста ремонтной службы./М.А. Тылкин — М.: Металлургия, 1981. — 648с.
9. Контроль качества металлических изделий [Електронный ресурс] / Режим доступа: http://www.tehnoinfa.ru/tehnologijaobrobotki/71.html — Заголов. с экрана.