Специальные методы штамповки
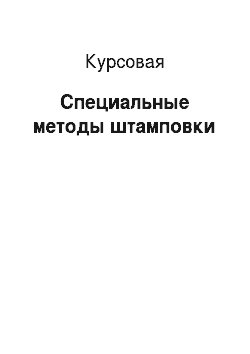
Установка для операций магнитно-импульсной штамповки, включающая выпрямительно-зарядное устройство, батарею емкостных накопителей энергии, разрядники и индуктор, отличающаяся тем, что она содержит генератор импульсов, счетчик, три задатчика времени, ключевые устройства и нормально замкнутые и нормально разомкнутые контакты, при этом генератор импульсов соединен со счетчиком, соединенным с тремя… Читать ещё >
Специальные методы штамповки (реферат, курсовая, диплом, контрольная)
Оглавление Введение
1. Физические основы процесса штамповки
1.1 Физические основы магнитно-импульсной штамповки
2. Оборудование
2.1 Оборудование для штамповки взрывом
2.2 Оборудование для электрогидравлической штамповки
2.3 Оборудование для магнитно-импульсной штамповки
2.4 Оборудование для ударной штамповки
3. Оснастка и инструменты
3.1 Оснастка для магнитно-импульсной штамповки
4. Режимы и условия обработки
4.1 Режимы обработки при магнитно-импульсной штамповке
4.2 Режимы обработки при гидровзрывной штамповке
5. Материалы и изделия
6. Патентное исследование
7. Расчетная часть Список литературы
Введение
Наряду с совершенствованием традиционной технологии обработки металлов давлением (ОМД) на базе автоматизации производства осуществляется поиск, развитие и совершенствование новых методов обработки. Специальные способы процессов ОМД экономически целесообразны в мелкосерийном и серийном производствах при изготовлении заготовок, и деталей сложной пространственной формы из малопластичных материалов в том случае, когда использование классических способов и методов ОМД оказывается либо не эффективным, либо невозможным. Рассматриваемые специальные способы ОМД позволяют существенно расширить технологические возможности промышленных предприятий. Совершенствование технологических процессов обработки металлов давлением, а также применяемого оборудования позволяет расширять номенклатуру деталей, изготовляемых обработкой давлением, увеличивать диапазон деталей по массе и размерам, а также повышать точность размеров полуфабрикатов, получаемых обработкой металлов давлением. Холодная деформация характеризуется изменением формы зерен, которые вытягиваются в направлении наиболее интенсивного течения металлов. При холодной деформации формоизменение сопровождается изменением механических и физико-химических свойств металла. Основной тенденцией развития ОМД является повышение эффективности технологических операций на базе ресурсо-энергосбережения, повышение культуры производства.
штамповка магнитный импульсный
1. Физические основы процесса штамповки Штамповка — процесс обработки металлов давлением, при котором формообразование детали осуществляется в специализированном инструменте — штампе. По виду заготовки различают объёмную штамповку и листовую штамповку, по температуре процесса — холодную штамповку и горячую.
Объемная штамповка это способ изготовления изделий, при котором металл деформируется по всему объему, а течение его ограничивается полостью штампа, очертания и размеры которой соответствуют очертаниям и форме заготовки. Объемная штамповка имеет большое применение в массовом и серийном производстве.
Поковки, полученные свободной ковкой, необходимо дополнительно обрабатывать; тогда как для поковок, полученных штамповкой, дополнительная обработка значительно меньше или она почти не требуется. Производительность труда при штамповке во много раз выше, чем при свободной ковке.
Штампы изготовляют из твердых и прочных сталей. Штампы (рис. 1) делают разъемными. Стенки вырезанных в штампах полостей, называемых ручьям и, не делаются вертикальными, а имеют уклоны от 5 до 10°, чтобы полости лучше заполнялись, и металл извлекался из них быстро и без усилий.
а б Рис. 1. Верхний (а)и нижний (б) штампы для горячей штамповки:
1 — заготовительный ручей. 2 — гибочный ручей. 3 — чистовой ручей Для выхода излишка металла вокруг полостей делают специальную канавку, в которую выдавливается металл, образующий вокруг изделия тонкие слои — заусенцы (облой). Штампуют изделия в нагретом или в холодном состоянии. Размеры полостей штампов при горячей штамповке должны быть больше размеров заготовки на величину, соответствующую уменьшению линейных размеров и объема при охлаждении металла заготовки. При штамповке особенное внимание должно быть уделено правильному определению количества металла, необходимого для заготовки. При недостаточном количестве металла полость штампа окажется незаполненной, а при избыточном — излишек металла образует слишком большие заусенцы, которые после извлечения заготовки из штампа удаляют на обрезных прессах. Штампуют нагретые заготовки на паровоздушных, фрикционных и других механических прессах, а также на горизонтально-ковочных машинах.
Широкое применение имеет холодная листовая штамповка для получения деталей сложной конструкции из листовой стали, латуни, меди, сплавов алюминия и др.
Операции листоштамповочных работ разнообразны и могут быть разделены на два основных вида:
1) операции разделительного характера: разрезание листов на полосы или ленты; разделение полос или лент на мерные части; вырубка — получение из листового материала заготовки нужного контура; пробивка — образование в заготовках отверстий нужной формы; обрезка припуска и др.;
2) формообразующие операции холодной листовой штамповки: гибка — сообщение листам и полосам определенной формы; вальцовка — образование на поверхности заготовок различных выступов — ребер жесткости, в том числе получение волнистой (гофрированной) поверхности; накатка — образование на листовых заготовках фасонной поверхности, например, резьбы на цоколях электроламп: вытяжка — получение углублений в листовом материале, например, при изготовлении сосудов.
Листовая штамповка производится с помощью вытяжных, вырезных, гибочных и других видов штампов.
Рис. 2 Штамп для пробивания отверстий в листе
1- пуансон 2- матрица 3 — лист
1.1 Физические основы магнитно-импульсной штамповки Импульсная штамповка относится к высокоскоростным методам штамповки. Особенностью таких методов является высокая скорость деформирования в соответствии с высокими скоростями преобразования энергии. Кратковременное приложение больших усилий разгоняет заготовку до скоростей 150 м/с. Последующее ее деформирование происходит за счет накопленной в период разгона кинетической энергии.
Магнитно-импульсная штамповка позволяет получать не только детали, но и производить неразборные соединения, в отдельных случаях достигая даже герметичности.
Сущность штамповки импульсом магнитного поля (ИМП) заключается в использовании электромеханических сил, возникающих в результате взаимодействия магнитных полей индуктора и заготовки, отталкивающих их друг от друга с высокой скоростью в весьма короткий промежуток времени.
Принципиальная схема магнитно-импульсной установки приведена на рис. 2.1. Через повышающий высоковольтный трансформатор и выпрямитель производят зарядку конденсаторной батареи, состоящей из групп параллельно включенных между собой импульсных конденсаторов. По окончании заряда конденсаторная батарея с помощью специального коммутирующего устройства-разрядника тригатрона разряжается на индуктор, внутри которого размещается заготовка.
Рис. 2.1 Принципиальная схема МИУ: 1- трансформатор повышающий; 2 — накопитель энергии (батарея конденсаторов); 3 -поджигающие устройства (разрядник); 4 — индуктор; 5 — заготовка В момент разряда конденсаторной батареи в индукторе протекают импульсные токи, распределенные по сечению весьма неравномерно, соответственно распределены силы и температуры. Их распределение влияет как на деформацию заготовки, так и на прочность и стойкость самого индуктора. При разряде конденсаторной батареи на индуктор вокруг него возникает магнитное поле большой мощности, наводящее вихревые точки в металлической заготовке. Взаимодействие магнитных полей индуктора и заготовки создает механическую силу, способную деформировать заготовку по матрице. Разряд происходит мгновенно (40—50 мкс), при этом заготовка получает ускорение (разгон) и развивает к моменту контакта с инструментом скорость до 200—300 м/с, а давление на заготовку достигает 2−10 ГПА и более.
Также магнитно-импульсная штамповка включает в себя такую особенность как эффект гиперспластичности.
Суть гиперпластичного эффекта заключается в действии кратковременных импульсных нагрузок. Относительные деформации образцов могут доходить до 200% (рис. 2.2).
Рис. 2.2 Деформация листового металла: Высокоскоростное деформирование листа Al, фоторегистрация процесса (интервал между импульсами 30 мс) Эффект гиперпластичности позволяет проводить обработку как в сочетании с традиционными методами, так и в отдельности, как самостоятельный метод высокоскоростной штамповки.
Успешная реализация эффекта гиперпластичности позволит:
возможность объёмной штамповки изделий различной номенклатуры с фиксированным профилем и определенным уровнем четкости без разрывов и повреждений;
вытягивание заданных участков металла, например, для удаления вмятин на его поверхности и придания ей формы, достаточно близкой к первоначальной, то есть, до появления повреждений.
2. Оборудование
2.1 Оборудование для штамповки взрывом Различают основное и вспомогательное оборудование для гидровзрывной штамповки.
К основному оборудованию относят бассейновые и безбассейновые установки, в которых непосредственно осуществляется гидровзрывная штамповка деталей.
В качестве бассейновых установок могут использоваться естественные водоемы, стационарные бассейны и съемные емкости многократного и разового пользования, устанавливаемые на матрицу.
Безбассейновые установки подразделяются на установки закрытого типа (вакуумные камеры и взрывные прессы) и установки, в которых штамповая оснастка при подрыве заряда ограждается от помещения цеха (бронеямы, бронекамеры, установки с водовоздушной завесой).
Имеются также комбинированные установки, в которых реализуются преимущества схем бассейновой и безбассейновой штамповки. Стационарные бассейны используют для получения крупногабаритных деталей в условиях серийного производства. Бассейны могут быть металлическими, железобетонными и комбинированными. Схемы металлического и железобетонного стационарных бассейнов показаны на рис. 3.
Стационарные бассейны должны удовлетворять следующим требованиям: минимальные капитальные затраты на их проектирование и строительство; надежность в работе, прочность и. долговечность; удобство и простота при обслуживании; универсальность, т. е. возможность использования для штамповки широкой номенклатуры деталей; минимальное сейсмическое воздействие на окружающие здания и сооружения.
Рис. 3
Стационарные бассейны для гидровзрывной штамповки: а — железобетонный; б — металлический На рис. 3.1. Изображена классификация схем взрывной штамповки.
Рис. 3.1 Классификация схем взрывной штамповки
2.2 Оборудование для электрогидравлической штамповки Одной из первых электрогидравлических установок является установка «Молния-3» (рис 4). При помощи минимальных массогабаритных установок «Молнии-3» обрабатываются плоские заготовки размером 0,2?0,2 м, а также цилиндрические заготовки диаметром и высотой до 0,15 м. Кроме того, на этой установке можно выполнять запрессовку труб в трубных досках теплообменных аппаратов. Установка состоит из генератора импульсов тока и технологического узла.
Рис. 4. Установка «Молния-3»
На установке «Удар-5» была применена схема, предусматривающая одновременно с внутренним радиальным давлением осевое сжатие цилиндрической заготовки. Как видно из рис. 5, деформируемую заготовку 4 устанавливают в полости матрицы 5. Подвижной контейнер 3, связанный с рабочей камерой 2, вводят одним концом в матрицу и с помощью подвижного упора 1 перемещают до соприкосновения с торцом штампуемой заготовки. С другой стороны заготовки вводят заглушку 6.
Если при обычной формовке степень деформации (отношение диаметров готовой детали к заготовке) не превышает 1,2−1,4, то при создании одновременно с внутренним радиальным давлением осевого сжатия заготовки можно подучить детали со степенью деформации 1,8 и более.
Рис. 5 Схема осевого и радиального нагружения заготовки Электрогидравлическая установка «Удар-1» предназначена для штамповки плоских крупногабаритных деталей путем последовательного перемещения рабочей камеры по поверхности заготовки. Благодаря оригинальности конструкции установка позволяет штамповать детали практически неограниченных размеров.
Установка состоит из технологического узла, генератора импульсов тока, системы подачи воды, устройства подачи инициирующей проволочки в зону разряда и пульта управления. На рис. 6 показана схема этого технологического узла (соответственно вид в плане и поперечный разрез). Технологический узел содержит основание 1, служащее одновременно резервуаром для жидкости и местом укладки матрицы 3. На матрице размещена заготовка 5, которая по периметру прижата рамой 6. На последней смонтированы направляющие 4 и 7 для перемещения рабочей камеры 10 соответственно в продольном и поперечном направлениях. Движением рабочей камеры управляют с пульта 11. В нижней части рабочей камеры свободно установлено прижимное кольцо 12, выполняющее роль второго электрода и прижимающее одновременно заготовку к матрице в момент штамповки. Электрод 8 установлен в рабочей камере вертикально над прижимным кольцом.
Жидкость по трубопроводу 9 поступает в рабочую камеру 10. Излишки жидкости сливаются в сборник 2, а оттуда стекают в резервуар 1.
После укладки заготовки на матрицу и опускания прижимной рамы рабочую камеру устанавливают в исходную точку и включают насос подачи жидкости из основного резервуара в рабочую камеру. Заполняя рабочую камеру, жидкость свободно проникает в зазор между камерой и заготовкой.
Секционная разборная матрица позволяет штамповать различное количество типоразмеров заготовок. Переналадка матрицы на новый типоразмер производится за 15−20 мин перестановкой отдельных секций.
Рис. 6. Схема технологического узла установки «Удар-1» (в плане и поперечный разрез)
2.3 Оборудование для магнитно-импульсной штамповки Основными элементами установок для магнитно-импульсной обработки металлов являются трансформатор, высоковольтный выпрямитель, конденсаторная батарея и технологический блок, включающий рабочий индуктор и матрицу либо оправку. Принципиальная схема установки показана на рис. 7.
Рис. 7
Принципиальная схема магнитно-импульсной установки: АТр — автотрансформатор; Тр — трансформатор; В — выпрямитель; С — конденсатор; Р — разрядник; U — индуктор; R — зарядное сопротивление.
На рис. 8 показаны основные схемы магнитно-импульсного формоизменения. Они бывают по матрице и по пуансону.
Рис. 8
Основные схемы магнитно-импульсного формоизменения: а, в — деформация по матрице; б — деформация по пуансону; 1 — индуктор; 2 — заготовка; 3 — матрица (оправка) Магнитно-импульсные установки характеризуются высокой производительностью, возможностью легкой автоматизации и механизации технологического процесса, широкими технологическими возможностями, отсутствием передаточной среды, простой и дешевой оснасткой, возможностью получения высоких давлений (до 108 Н/м2 без разрушения индуктора и до 109 Н/м2 при использовании одноразового индуктора), высокой культурой производства и простотой обслуживания, положительным влиянием на характеристики отдельных обрабатываемых материалов и др.
Выпускают установки для штамповки ИМП, состоящие из зарядного устройства, блока-накопителя и пульта управления. К их числу относятся установки: УМШ-15/5 (рис. 8.1) мощностью 15 кДж при рабочем напряжении 5 кВ, на которой можно штамповать детали из плоских заготовок толщиной до 1,5 мм, пробивая в них отверстия размером 150X150 мм Рис. 8.1 Установка УМШ-15/5
2.4 Оборудование для ударной штамповки Сущность ударной штамповки заключается в деформировании заготовки импульсом давления, созданного в ограниченном объеме жидкости ударом по ней твердого тела (бойка), предварительно разогнанного до высокой скорости. В качестве передающей среды возможно использование эластичного материала.
Принципиальная схема ударной штамповки при помощи пресс-пушки, использующей энергию пороховых газов, показана на рис. 9. В верхней части ствола 3 расположен патрон 1 и боек 2. В нижней части над заготовкой 4 возвышается столб жидкости 5. При срабатывании патрона пороховые газы разгоняют боек до определенной скорости и бьют им по жидкости, создавая мощный импульс давления" который деформирует заготовку.
Рис. 9. 1 — патрон; 2 — боек; 3 — ствол; 4 -заготовка; 5 — столб жидкости В двух следующих схемах энергоносителем является сжатый газ. Схема процесса ударной штамповки, в котором в качестве передающей среды используется жидкость, показана на рис. 10, а. На матрицу 1 установлена камера 2, внутренний объем которой заполнен водой. На камере крепится ствол 3 гидроударного пресса так, чтобы внутренние диаметры ствола и матрицы совпадали. Внутри ствола перемещается боек 4. Соосно стволу расположен аккумулятор 5, в котором размещен сжатый газ. Заготовка 6 уложена на матрице и прижимается сверху камерой. Накопленный в аккумуляторе 5 сжатый газ, расширяясь, разгоняет по стволу 3 боек 4. Скорость движения бойка достигает 150 м/с. В результате боек создает мощный импульс давления, который штампует заготовку на матрице. Энергия удара регулируется изменением давления сжатого газа в аккумуляторе.
На рис. 10, б показана схема процесса ударной штамповки, где роль передающей среды выполняет эластичный материал, например полиуретан. От предыдущей схемы она отличается только передающей средой.
По сравнению с традиционной ударная штамповка имеет следующие преимущества: возможность получения деталей сложной формы из трудно деформируемых материалов за один переход; легкость управления формой импульса давления; простота конструкции и низкая себестоимость оснастки; низкая металлоемкость оборудования и др.
Рис. 10 Схема процесса ударной штамповки жидкостью (a) и эластичной средой (б): 1 — матрица; 2 — камера; 3 — ствол; 4 — боек; 5 — аккумулятор; 6 — заготовка
3. Оснастка и инструменты
3.1 Оснастка для магнитно-импульсной штамповки Основным рабочим органом при магнитно-импульсной штамповке является индуктор. Его изготовляют из медных трубок, ленты или проволоки круглого или прямоугольного сечения. В связи с тем, что плотность тока, протекающего по виткам индуктора, неравномерна (ток течет в основном по периферии проводника), целесообразно делать индукторы из стали, плакированной металлом высокой электропроводности. Такие индукторы обладают более высокой прочностью при высоких электрических показателях. Выделение теплоты, происходящее при разряде, разогревает индуктор. Поэтому для увеличения срока службы индуктора его выполняют пустотелым для обеспечения возможности охлаждения проточной водой. Индуктор монтируют в специальном стальном корпусе и заливают изоляционным материалом — армированным стеклопластиком, пропитанным эпоксидной смолой. На рис. 11 приведены некоторые типы индукторов для штамповки плоских заготовок: двухвитковый индуктор, создающий наибольшее давление в средней части; индуктор для гофрирования; индуктор с пропусканием импульсного тока через плоскую заготовку.
Рис. 11 Типы индукторов: а — двухвитковый; б — для гофрирования; в — с пропусканием импульсного тока; 1 — заготовка; 2 — изоляция Для концентрирования сил, создаваемых магнитным полем на отдельных участках штампуемой детали, а также более равномерного распределения сил по обмотке индуктора применяют концентраторы магнитного поля, изображенные на рис. 12, которые представляют собой массивные диски с центрально расположенным отверстием, изготовленные из высокопрочного металла, обладающего хорошей электропроводностью (например, бериллиевая бронза). Концентратор имеет радиальный шлиц, служащий для предотвращения возможности образования в них вихревых токов.
Рис. 12. Концентраторы магнитного поля Концентратор сжимает магнитный поток, увеличивает его напряженность в требуемых участках деформируемой заготовки.
4. Режимы и условия обработки
4.1 Режимы обработки при магнитно-импульсной штамповке В результате применения магнитно-импульсной обработки представляется возможной штамповка листовых и трубчатых заготовок толщиной до 5 мм.
Размеры заготовок (диаметр, обрабатываемая площадь) обуславливаются запасом энергии установки, толщиной обрабатываемого материала, конструктивными возможностями индуктора и технологической оснастки.
По типу применяемого инструмента и по характеру деформации обрабатываемой заготовки все операции, выполняемые на МИУ, можно разделить на три схемы:
Раздача;
Листовая формовка;
Обжим.
Установлено, что с использованием магнитно-импульсной обработки возможно получение биметаллических соединений, изготовление шарнирных соединений, сварка трубчатых заготовок, запрессовка труб в дисках, трубных досках и т. д., соединение двух изоляционных или металлических деталей путем раздачи трубы с одновременной отбортовкой, поперечная волнистая и плоская в сечении рифтовка, формообразование выступа, продольная рифтовка, формообразование конуса, концевая раздача труб, отбортовка, пуклевка, изготовление резьбы, рифление, калибровка, пробивка отверстий, вырубка, порезка.
При использовании магнитно-импульсной обработки для листовой штамповки применяются плоские спиральные индукторы.
Технологические операции, выполняемые по схеме «листовая формовка»: сборка диска с осью, отбортовка диска, сварка двух листов металла, напрессовка втулок на оси и запрессовка вкладышей в трубках, изготовление деталей типа тарелки или днища, кольцевая заготовка, продольная и поперечная зиговка, пуклевка, неглубокая отбортовка по периферии диска, прямоугольника, круглых и прямоугольных отверстий, формовка тороидальных крышек, рельефная формовка с одновременной рихтовкой недеформируемой части заготовок, калибровка листовых заготовок, пробивка отверстий, вырубка и порезка.
С помощью магнитно-импульсной обработки по схеме «обжим» можно выполнить следующие технологические операции: соединение металлических деталей с керамикой, стеклом, пластмассой и другими неметаллическими материалами, опрессовка кабельных наконечников, соединение двух проводов соединительной трубкой, опрессовка наконечников на канаты и др., шлангов высокого давления, опрессовка труб на металлические наконечники, сварка трубчатых заготовок, поперечная волнистая, поперечная плоская в сечении и продольная рифтовка, формообразование впадины, формообразование конуса, редуцирование труб, отбортовка, пуклевка, изготовление резьбы, рифление, калибровка, пробивка отверстий и вырубка, порезка труб.
К недостаткам метода и установок можно отнести трудность получения деталей с глубокой вытяжкой обрабатываемого материала; необходимость в промежуточных металлических прокладках-" спутниках" для металлов с низкой электропроводностью, ограниченность формы и геометрических размеров обрабатываемых заготовок для магнитно-импульсной обработки; низкая стойкость индукторов, особенно при обработке стальных заготовок.
Металлы с высокой электропроводностью (малым электрическим сопротивлением) — медь, алюминий, латунь и др. лучше деформируются ИМП, чем металлы с низкой электропроводностью — сталь, титан и др. Последние деформируются ИМП при условии покрытия их тонким слоем меди или алюминия электролитическим способом или при условии использования медных или алюминиевых прокладок («спутников») в виде фольги, устанавливаемых между заготовкой и индуктором.
4.2 Режимы обработки при гидровзрывной штамповке Существует три основных направления повышения КПД штамповки: использование энергии отраженной волны, замыкание взрывной системы и метание передающей среда, совмещение нескольких операций на одном переходе.
Использование энергии отраженной волны позволяет направить отраженные волны в направлении заготовки, что ведет за собой резкое увеличение КПД процесса. Форма отражателя выбирается в зависимости от формы расположения заряда так, чтобы отраженная волна была с плоским фронтом распространения. Разновидностью использования эффекта отражения является система, когда отражатель помещается в пространстве, в котором находится передающая среда. Принципиальная схема такого устройства приведена на рис.13
Рис. 13 Закрытая система штамповки с отражателем 1 — ударник; 2 — заряд ВВ; 3 — крышка-отражатель; 4 — шпильки; 5 — заготовка; 6 — прижимное кольцо; 7 — вытяжное кольцо; 8 — рабочая полость; 9 — уплотнение; 10 — присоединительная поверхность с уплотнением
Принцип действия сооружения состоит в том, что внутренняя поверхность крышки 5 оформлена в вида параболического отражателя, в фокусе которого умещается заряд ВВ 2, который приводится в действие ударным устройством 1. Крышка-отражатель примыкает плотно к прижимному кольцу 6 и, так как по поверхности 10 крышки размещается уплотнение, пространство над заготовкой S заполняется водой. Заготовку 5 укладывают на вытяжное кольцо 7, а прижим к ним осуществляется прижимным кольцом 6, воздух с рабочей полости 8 удаляется. Уплотнение 9 гарантирует герметичность рабочей полости. Импульс заряда, действующий в верхней точке отражателя, принимается от шпилек 4. Рабочую полость можно использовать для свободной вытяжки только при помощи вытяжного кольца или для расположения матриц разного типа, две из которых показаны на рис. 13, б, в.
Еще один способ увеличения КПД — это совмещение операций в одном бассейне в случае штамповки одинаковых или различающихся между собой малогабаритных деталей. Схематически этот процесс показан на рис. 14
Рис. 14. Схема совмещения операции во времени: 1 — бассейн; 2 — вода; 3 — матрицедержатель; 4 — канаты; 5 — стойка; 6 — заряд ВВ; 7 — центрирующее устройство; 8 — матрица; 9 — заготовка; 10 — коллектор; 11 — гибкий шланг; 12 — вакуум-помпа В небольшом стационарном бассейне 1, заполненном водой 2, подвешивается, круглый (в форме массивного кольца) матрицедержатель 3 при помощи каната 4 на стойке 5. Заряд ВВ 6 размещают в центре матрицедержателя при помощи центрирующего устройства 7. Матрицы 8, число которых применяют от трех до восьми, располагают симметрично в матрицедержателе. Каждая матрица имеет свое прижимное кольцо и заготовку. Удаление воздуха из матрицы осуществляется коллектором 10, гибким шлангом 11 и вакуумным насосом 12. Совмещение операций в одном бассейне встречается часто. Такое совмещение можно подучить, рассматривая жидкую передающую среду как универсальный пуансон, при помощи которого можно осуществить почти одновременно разные по виду операции.
5. Материалы Наиболее эффективно магнитно-импульсным методом обрабатываются заготовки из меди, алюминия, магния и их сплавов. Заготовки из углеродистых (Ст3, Ст10) и легированных (1Х18Н9Т, 30ХГСА) сталей, а также из титановых сплавов можно обрабатывать только с применением прокладок-" спутников", изготовленных, например, из отожженной меди марки М1.
6. Патентное исследование
№ патента | Название патента | Автор | Формула изобретения | |
Устройство для магнитно-имульсной штамповки трубчатых заготовок | Костров Ю.А., Крисеев Н. В., Мамотюк В.И. | 1. Устройство для магнитно-имульсной штамповки трубчатых заготовок содержащее смонтированный на основании индуктор, полуматрицы с формообразующей поверхностью, охватывающие индуктор, и механизм зажима полуматриц, отличающееся тем, что, с целью расширения технологических возможностей и повышения производительности труда, полуматрицы выполнены в виде полуцилиндров, механизм зажима выполнен в виде двух бандажных колец, одно из которых связано с приводной втулкой, охватывающих концы полуматриц, а на внутренней поверхности полуматриц между их торцами со стороны бандажного кольца, связанного с приводной втулкой и формообразующей поверхностью, выполнена кольцевая проточка с режущими кромками с углом, не превышающим 90o. 2. Устройство по п. 1, отличающееся тем, что ширину проточки выбирают из соотношения a? 6s, глубину b? s + 0,5 мм, где s толщина стенки трубчатой заготовки, а дно проточки выполнено вогнутым с длиной образующей p? a + 0,3 мм. | ||
Устройство для магнитно-импульсной штамповки заготовок из материалов с низкой электропроводностью. | Самохвалов В.Н., Лебедев Г. М., Краснов В. Г. Цуканов В.Ф. Голиусов Т.А. | Устройство для магнитно-импульсной штамповки заготовок из материалов с низкой электропроводностью, содержащее индуктор, технологический спутник из материала с высокой электропроводностью и штамповую оснастку, отличающееся тем, что при штамповке тонкостенных трубчатых заготовок спутник выполнен коническим. | ||
Установка для операций магнитно-импульсной штамповки | СелищевВ.А. ОрловС.Ю. ПроскуряковН. Е ТалалаевА.К. Череватый Р.С. | 1. Установка для операций магнитно-импульсной штамповки, включающая выпрямительно-зарядное устройство, батарею емкостных накопителей энергии, разрядники и индуктор, отличающаяся тем, что она содержит генератор импульсов, счетчик, три задатчика времени, ключевые устройства и нормально замкнутые и нормально разомкнутые контакты, при этом генератор импульсов соединен со счетчиком, соединенным с тремя задатчиками времени, каждый из которых соединен с соответствующим ключевым устройством, ключевые устройства соединены параллельно через нормально замкнутые контакты друг с другом и параллельно нормально разомкнутому контакту, включенному последовательно в цепь, содержащую повышающий трансформатор, выпрямительное устройство и нормально разомкнутый контакт; параллельно каждому ключевому устройству подсоединена цепь, состоящая из резистора и конденсатора, соединенных последовательно и подключенных каждый к своему резистору, соединенному с управляющим входом соответствующего разрядника, при этом каждый из емкостных накопителей энергии соединен с индуктором через соответствующий разрядник. 2. Установка по п. 1, отличающаяся тем, что каждый из разрядников включен последовательно в цепь, состоящую из выпрямительного устройства, повышающего трансформатора и емкостного накопителя, а емкостные накопители соединены параллельно индуктору. 3. Установка по п. 1 или 2, отличающаяся тем, что она содержит три одинаковых канала, каждый из которых содержит задатчик напряжения, прибор контроля напряжения, блок формирования импульсов, общее для всех каналов устройство счета, ключевое устройство, контактор и источник напряжения, при этом задатчик напряжения соединен с прибором контроля напряжения, блоком формирования импульсов и соответствующим емкостным накопителем энергии, блок формирования импульсов соединен с ключевым устройством, а ключевое устройство соединено с контактором, при этом контакторы подключены к источнику напряжения. 4. Установка по любому из пп.1−3, отличающаяся тем, что она содержит второй генератор импульсов, счетчики импульсов и индикаторы, при этом устройство счета присоединено к выводу второго генератора импульсов и имеет два вывода, каждый из которых соединен со своим счетчиком импульсов, а каждый счетчик импульсов соединен со своим индикатором. | ||
7. Расчетная часть.
Параметры соленоида, в который помещена электропроводящая оболочка — экран, удобно исследовать, используя схему последовательной цепи с сосредоточенными и постоянными емкостью ©, индуктивностью (L) и активным сопротивлением ®. На рисунке 15 представлена схема замещения магнитно-импульсной установки с индуктором и заготовкой.
Рис. 15 Схема замещения магнитно-импульсной установки с индуктором и заготовкой Конденсаторная батарея с индуктивностью (Li) и активным сопротивлением (Ri) и внешняя нагрузка, состоящая из индуктора и заготовки (L1, L2; R1, R2 — индуктивность и активное сопротивление соответственно), образуют колебательный контур, который описывается дифференциальным уравнением:
(1)
Используя теорию расчета колебательного контура, решение для первичного тока можно записать в следующем виде:
(2)
при этом
(3)
(4)
где Imмаксимальное значение амплитуды разрядного тока;
где б — коэффициент, учитывающий затухание;
где щ — круговая частота разрядного тока.
Выражения (1) — (4) применимы для трех возможных случаев колебаний, характеризуемых фактором колебаний:
(5)
где D<1 — периодическое затухание;
где D=1- апериодическое пограничное затухание;
где D>1- апериодическое затухание На рисунке 16 изображено изменение разрядного тока в индукторе в зависимости от условий затухания.
Рис. 16 Изменение разрядного тока в индукторе в зависимости от условий затухания
Наивысшее значение тока будет в случае периодического затухающего колебания, т. е. при D<1. Из формулы (5) видно, что D будет наименьшим при R>0, отсюда следует важное условие: колебательный контур должен иметь малое активное сопротивление.
В зазоре между соленоидом и экраном магнитная индукция B имеет следующее значение:
(6)
при этом
(7)
где B0 — амплитудное значение магнитной индукции;
где м0 — магнитная постоянная, равная 1,256*10−6Г/м;
где n — число витков соленоида;
где l — длина соленоида.
Ток, протекающий в цепи индуктора при разряде конденсаторной батареи, вычисляют выражением:
(8)
где U — рабочее напряжение, В;
где t — время разряда, с.
Максимальный ток, определяющий максимум индукции и напряженности магнитного поля:
(9)
где
(10)
Боковая поверхность оболочки испытывает давление, численно равное объемной плотности энергии магнитного поля (11):
(11)
Также максимальное давление на заготовку рассчитывается по формуле (12). В случае для индуктора без концентратора формула принимает вид:
(12)
где Sa — внешняя поверхность заготовки, м;
где — зазор между индуктором и заготовкой, м.
Это выражение может быть использовано лишь для предварительной оценке технологического процесса, так как не отличается высокой точностью.
1. Губарева Э. М. Высокопроизводительные методы обработки металлов давлением. Учеб. пособие. Пермь: Пермский государственный технический университет. 1996.
2. Коликов А. П., Подухин П. И., Крупин А. В. Новые процессы деформации металлов и сплавов: Учеб. пособие для вузов. М.: Высшая школа, 1986.
3. Петров А. П., Масловский П. А., Ершов С. В. Прогрессивные технологические процессы ковки и объемной штамповки. М.: Высшая школа. 1988
4. Ю. В. Батыгин, А. В. Гнатов, Щ. В. Гнатова, А. А. Степанов, Е. А. Чаплыгин. Особенности магнитно-импульсной обработки металлов в технологиях современности // Электротехника и электромеханика. 2011. № 1.
5. СелищевВ.А., ОрловС.Ю., Проскуряков Н. Е, Талалаев А. К., Череватый Р. С. Патент: Установка для операций магнитно-импульсной штамповки
6. СамохваловВ.Н. Лебедев Г. М. Краснов В.Г. Цуканов В. Ф. Голиусов Т.А. Патент: Устройство для магнитно-импульсной штамповки заготовок из материалов с низкой электропроводностью.
7. Костров Ю. А. Крисеев Н.В. Мамотюк В. И. Патент: Устройство для магнитно-имульсной штамповки трубчатых заготовок
8. Миронов В. А. Магнитно-импульсное прессование порошков. стр. 47−52.