Оборудование и технология производства сплава из стали марки 35Г в условиях предприятия ОАО «Ашинский металлургический завод»
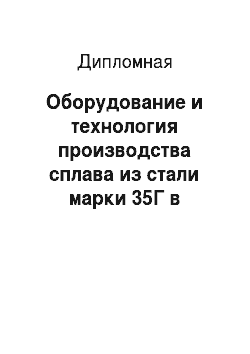
Рисунок 2 — Схема непрерывной разливки стали ь Подготовка промежуточных ковшей и погружных стаканов к разливке Разливщиком МНЛЗ принимается промковш с огнеупорного участка после сушки. При приемке не допускается наличие мусора и остатков раствора в рабочей полости. После приемки разливщик устанавливает стакан-дозатора и механизм «Интерстоп», огнеупорщик производит набивку стакан-дозатора после… Читать ещё >
Оборудование и технология производства сплава из стали марки 35Г в условиях предприятия ОАО «Ашинский металлургический завод» (реферат, курсовая, диплом, контрольная)
АННОТАЦИЯ
Науменко А. В. Оборудование и технология производства сплава из стали марки 35 Г в условиях предприятия ОАО «Ашинский металлургический завод» — Аша: ЮУрГУ, МПиО; 2013, 87с., 5 ил., библиограф. список 16 наим., 1 прил., 4листов чертежей ф. А1,4 листов техпроцесса
Целью работы является рассмотрение способа выплавки полупродукта в ДСП с целью получения, после внепечной обработки на АКП, стали марки 35 ГС в ЭСПЦ — 2 в ОАО «АМЗ». Всего в пояснительной записке: 8 разделов, 59 страниц, 24 таблицы, 6 рисунков, список литературных источников.
В данной работе описаны история и основные этапы развития ОАО «АМЗ», общая технология разливки стали на машине непрерывного литья заготовок, приведены технические характеристики основных металлургических агрегатов.
Целью технологической части работы является разработка технологии выплавки стали марки 35ГС в условиях электросталеплавильного цеха № 2 ОАО «АМЗ».
В работе также рассмотрены вопросы безопасности труда, экологии окружающей среды, ресурсои энергосбережения и рационального природопользования.
1. ТЕХНОЛОГИЧЕСКАЯ ЧАСТЬ
1.1 Назначение выплавляемого сплава
1.2 Описание сплава
1.3 Технология выплавки сплава и работа оборудования в условиях ОАО АМЗ
1.3.1 Выбор оборудования для выплавки
1.3.2 Выбор шихты для выплавки
1.3.3 Выбор огнеупорных материалов
1.3.4 Технологическая карта (схема) выплавки
1.3.5 Контроль качества продукции
2. РАСЧЕТНАЯ ЧАСТЬ
2.1 Назначить и рассчитать технологические параметры выплавки
2.2 Энергоемкость оборудования
2.3 Баланс плавки
2.4 Тепловой расчет печи
3. МЕРОПРИЯТИЯ ДЛЯ ПОВЫШЕНИЯ КАЧЕСТВА ВЫПУСКАЕМОЙ ПРОДУКЦИИ
3.1 Возможные способы нарушения технологического режима и способы борьбы с нарушениями
3.2 Возможные виды брака, методы борьбы с браком, способы устранения брака
3.3 Возможные направления модернизации технологии получения продукции
4 ЗАРУБЕЖНЫЙ ОПЫТ ПРОИЗВОДСТВА ПОДОБНОЙ ПРОДУКЦИИ
5. ОХРАНА ТРУДА И ТЕХНИКА БЕЗОПАСНОСТИ. ОХРАНА ОКРУЖАЮЩЕЙ СРЕДЫ ЗАКЛЮЧЕНИЕ
БИБЛИОГРАФИЧЕСКИЙ СПИСОК ПРИЛОЖЕНИЯ
ВЕДЕНИЕ Настоящий период развития черной металлургии характеризуется коренным изменением масштабов производства качественных и высококачественных марок стали, а также их доли в общем объеме производства металла. Наблюдаемое во всем мире развитие машиностроения и других металлопотребляющих отраслей обеспечивается мероприятиями, проводимыми металлургами с целью повышения степени чистоты стали (главным образом, за счет внепечной обработки) и выхода годного (в основном, в результате перехода на непрерывную разливку металла). Около 15 — 20 лет назад требования новых отраслей техники к качеству стали многих марок резко возросли и продолжают возрастать. Это привело к тому, что масштабы производства стали и сплавов, содержащих ничтожно малое количество газов, неметаллических включений и других нежелательных примесей, заметно увеличились.
Разработаны новые способы обработки металла как в самом агрегате, так и вне его. Возникла новая ситуация, когда масштабы выплавки стали уже не характеризуют промышленную мощь, главным становится высокое качество, чистота и надежность металлопродукции. Неизбежное при этом усложнение технологии оправдывается достигаемым результатом.
Мировой опыт настоящего периода характеризуется, прежде всего, интенсивным внедрением в практику различных методов внепечной обработки и непрерывной разливки стали.
ОАО «Ашинский металлургический завод» в настоящее время является безусловным лидером среди малых заводов чёрной металлургии Южного Урала по темпам развития, перевооружения производства, внедрения новейших технологий и последних образцов техники, организации научных исследований в области производства чёрных металлов.
В настоящее время на Ашинском металлургическом заводе (АМЗ) сталеплавильное производство представлено электросталеплавильным комплексом, работающем в составе дуговой сталеплавильной печью емкоскью 120 т и агрегатом ковш-печь.
Разливка ведется на машине непрерывного литья заготовок (МНЛЗ).
Для внепечной обработки стали сооружено отделение внепечной обработки стали, в котором размещен агрегат «ковш-печь», введенный в действие в 2003 г.
Сооружение нового электросталеплавильного цеха с объектами комплекса осуществили без потери производства в существующих цехах.
С вводом в действие электропечи и достижением проектной мощности мартеновский цех вывели из эксплуатации в 2010 году.
Особенностью проекта реконструкции сталеплавильного производства АМЗ со строительством нового электросталеплавильного комплекса взамен существующего мартеновского цеха является необходимость стыковки нового производства с существующим отделением агрегата ковш-печь и строящимся отделением непрерывной разливки стали.
Принятый на АМЗ порядок сооружения агрегатов в процессе замены мартеновского производства на новое электросталеплавильное производство не вызывает сомнения. Вначале — агрегат ковш-печь, затем — слябовая МНЛЗ (с работой от мартеновских печей) и потом — строительство электропечи с последующей остановкой мартеновского цеха.
Но такая серьезная реконструкция должна выполняться после проработки общей концепции строительства нового электросталеплавильного комплекса «в целом» с выделением из него отдельных этапов, то есть — от «общего» к «частному».
К сожалению, как показал анализ решений выполненных проектов отделений с агрегатом ковш-печь и МНЛЗ, эти отделения сооружались без возможности стыковки с новым отделением выплавки стали в электропечи, ни в части строительных и технологических решений, ни в части обеспечения одинаковой производительностью.
Этот факт накладывает дополнительные трудности при осуществлении строительства нового электросталеплавильного комплекса, а также необходимости решать в будущем все возникающие проблемы по технологической стыковке и совместной эксплуатации производственной линии «электропечь — печь-ковш — МНЛЗ» производительностью 1,0 млн. т стали.
Технологическое решение характеризуется выбором качественного и высокопроизводительного оборудования, благодаря которому можно добиться исключительно эффективных производственных результатов при незначительном количестве работающих и невысоком удельном энергопотреблении, что делает установку высоко конкурентоспособной.
Компоновочное решение разработано с учетом имеющихся в распоряжении производственных площадей:
— минимальная площадь занятых площадей;
— оптимизация количества требуемого персонала;
— оптимизация продолжительности производственных циклов и затрат.
В основу технических спецификаций оборудования положен обширный опыт компании DANIELI в области проектирования и ввода в строй металлургических предприятий и, в частности, самых современных компактных производственных агрегатов. Выбор различных систем, входящих в состав установки, строго связан с достижением следующих высокоприоритетных задач, а именно:
— ограниченные капитальные затраты;
— высокое качество продукции;
— высокая производительность;
— максимальная простота в эксплуатации;
— эксплуатационная надежность;
— максимальная гибкость для удовлетворения различной рыночной конъюнктуры.
Благодаря плодотворному сотрудничеству разных фирм, входящих в состав концерна DANIELI, мы можем поставить все технологическое оборудование, сопутствующие вспомогательные системы и инфраструктуру для всего ассортимента металлургических установок. Местные представительства фирмы готовы обеспечить техническое содействие на стадиях проектирования установки и ее монтажа и предоставить консультационные услуги после запуска установки в производство с целью улучшения ее эксплуатационных показателей путем внедрения передовых технологических инноваций. Услуги по обучению персонала Заказчика являются важной частью передачи технологии и ноу-хау компанией DANIELI, и обеспечивают оперативное и быстрое освоение установки в короткие сроки (и, следовательно, сокращение периода окупаемости инвестиций). Кроме того, при необходимости компания DANIELI предоставит техническое содействие в эксплуатации и техобслуживании производственных агрегатов после их приемки.
Высокая производственная мощность.
Благодаря высоким эксплуатационным показателям и условиям, предусмотренным для предлагаемой установки, цель обеспечения ею максимально достижимой производительности может быть достигнута путем:
— низкой потребности оборудования в техобслуживании;
— высокого уровня автоматизации;
— управления технологическим процессом;
— высокое качество готовой продукции.
Высокое качество готовой продукции как в отношении соблюдения сверх узких допусков, так и качества материала, является неизменной характеристикой оборудования DANIELI. Эта цель может быть достигнута путем внедрения:
Обширного ноу-хау в области выплавки, рафинирования и разливки стали, предоставляемого через дочернее предприятие фирмы Danieli Centro Met AB, в Швеции:
— рассчитанный на высокоскоростную разливку;
— конструкция промковша, разработанная на основе водяного моделирования;
— усовершенствованная система вторичного охлаждения;
— тянуще-правильные агрегаты с двумя точками изгиба, рассчитанные на снижение деформации.
Благодаря процессу интернационализации рынка металлопродукции, гибкость производства представляет собой ключевой залог успеха любого проекта. Высокая гибкость означает возможность быстрого реагирования на любые изменения в динамике развития рынка или возможность полной эксплуатации рыночных ниш. На установках DANIELI эта цель достигается с помощью следующих основных параметров:
— широкий диапазон продукции в плане ее типоразмеров;
— модульная конструкция оборудования с возможностью расширений в будущем (станция дегазации в вакууме для производства марочного сортамента специальных сталей);
— конструкция ДСП позволяет обеспечить различные комбинации состава шихты;
— технологический процесс выплавки стали в ДСП, позволяет обеспечить использование различных комбинаций электрической и химической энергии;
— компоновка оборудования, разработанная с целью обеспечения нескольких технологических маршрутов для повышения до максимума производственного потенциала установки и одновременно с этим для обеспечения гибких связей между различными производственными агрегатами.
Эффективность.
Без увеличения общих капиталовложений можно обеспечить повышение годовой производственной мощности установки за счет повышения эффективности ее работы, т. е. за счет повышения выхода годного и коэффициента использования оборудования. Выход годного оптимизируется благодаря:
— использованию современных моделей автоматизации с целью оптимизации характеристик разливки;
— конструкции механического оборудования, направленной на снижение образования настыли в промковше, уменьшение обрези передних и задних концов заготовок. Коэффициент использования повышается за счет автоматизации процесса производства. Фактически, благодаря обеспечению постоянного и высокого воспроизводства настройки каждой отдельной единицы оборудования и каждой отдельной операции, возможность человеческой ошибки сведена к минимуму. Сокращение времени, необходимого при переналадке производства в связи с переходом на выпуск другого типа продукции, обеспечиваемое за счет:
— конструкции кожуха ДСП, позволяющей осуществить его быструю замену при внепоточном проведении техобслуживания резервного кожуха;
— сокращение продолжительности ликвидации последствий прорывов жидкой стали на ручьях в связи с сокращением общего количества таких аварийных и ситуаций;
— простота конструкции оборудования позволяет сократить его техобслуживание. Более того, можно обеспечить поставку системы автоматизации с пакетом «Плюс техобслуживание» для оптимизации профилактического техобслуживания установки.
1. ТЕХНОЛОГИЧЕСКАЯ ЧАСТЬ
1.1 Назначение выплавляемого сплава Выплавляемый сплав используется для элементов сварных металлоконструкций и различных деталей, к которым предъявляются требования повышенной прочности и коррозионной стойкости с ограничением массы и работающие при температуре от -70 до 450 °C; проката, предназначенного для изготовления мостовых конструкций обычного и северного исполнения; несущих элементов различных сварных конструкций; деталей трубопроводной арматуры после закалки и отпуска; в качестве основного слоя. А так же применяется при изготовлении: тяги, оси, серьги, траверсы, рычаги, муфты, валы, звездочки, цилиндры, диски, шпиндели, соединительные муфты паровых турбин, болты, гайки, винты и другие детали, к которым предъявляются требования невысокой прочности.
1.2 Описание сплава Сталь марки 35ГС используется для изготовления арматуры периодического профиля класса А-III диаметром от 6 до 40 мм. Поставляется потребителю в виде сортового проката, в том числе фасонного: ГОСТ 5781–82, ГОСТ 2590–71. Заменители стали марки 35ГС: ВСт5сп, Ст6, Ст5пс. Химический состав и другие свойства стали приведены в таблицах 1, 2, 3.
Таблица 1 — Химический состав стали марки 35 ГС, масс. %
Химический элемент | C | Si | Mn | S | P | Cr | Ni | Cu | |
0,30 — 0,37 | 0,60 — 0,90 | 0,80 — 1,20 | ? 0,045 | ? 0,040 | ? 0,30 | ? 0,30 | ? 0,30 | ||
Таблица 2 — Механические свойства стали марки 35 ГС
Термообработка, состояние поставки | Сечение, мм | s0,2, МПа | sB, МПа | d5, % | KCU, Дж/м2 | HB | |
Сталь арматурная III класса горячекатаная | 6 — 40 | ||||||
Образец длиной 340 — 360 мм профиля № 14 стержневой арматуры горячекатаный | 410 — 450 | 690 — 710 | 15 — 21 | 48 — 64 | |||
Образец длиной 340 — 360 мм профиля № 14 стержневой арматуры после закалки 1000 °C, вода (35 °С), 4 с, отпуск 425 °С | 890 — 900 | 1000 — 1050 | 9 — 10 | 127 — 157 | |||
Таблица 3 — Температура критических точек
Критическая точка | оС | |
Ac1 | ||
Ac3 | ||
Mn | ||
Сталь марки 35ГС сваривается без ограничений.
1.3 Описание технологии выплавки сплава и работы оборудования в условиях ОАО «Ашинский металлургический завод»
1.3.1 Выбор оборудования для выплавки Производство стали марки 35 Г в условиях нового Электросталеплавильного цеха № 2 имеет следующую технологическую схему: производство полупродукта в основной электродуговой печи ДСП-120, рафинирование и доводка стали до требуемого химического состава на агрегате печь-ковш, разливка на одноручьевой вертикальной слябовой машине непрерывного литья заготовки.
Рисунок 1 — Технологическая схема Таблица 4 — Общие характеристики агрегата: дуговая электросталеплавильная печь (ДСП-120)
Тип печи | переменного тока с полной платформой | |
Система загрузки скрапа | система непрерывной загрузки — CONSTEEL | |
Tип выпуска жидкого металла | эркерный | |
Сталь на выпуске | 120 T | |
Зеркало расплавленного металла | 50 т | |
Диаметр кожуха | 6800 мм | |
Внутренний диаметр панелей | 6900 мм | |
Тип панелей | стальные и медные (нижние) трубы | |
Угол выпуска | 20° | |
Угол спуска шлака | — 15° | |
Емкость печи | 144,5 м³ | |
Тип электродных консолей | проводные | |
Круговой диаметр электродов | 1250 мм | |
Диаметр электрода | 610 мм | |
Длина электрода | 2700 мм | |
Емкость корзины для лома | 85 м3 | |
Таблица 5- Технические характеристики ДСП-120
Наименование показателей | Единица измерения | Обозначение | |
Конструкция футеровки свод | ; | Центральная часть свода в зоне прохода электродов выполняется футерованной (из периклазохромитового кирпича), периферийная часть из водоохлажадемых панелей | |
стены | ; | Водоохлаждаемые панели. Участок стен под водоохлаждаемыми панелями-кирпич периклазоплавленный обожженный. На внутреннюю поверхность панелей наносится защитная огнеупорная масса. | |
Температура воды: на подводе на сливе | °С °С | 70−80 90−100 | |
расход воды на охлаждение (свод и стены электропечи) | м3/т | ||
Организация пылегазоудаления устройство для отвода дымовых газов | ; | Водоохлаждаемый коленообразный патрубок от электропечи; диаметр газоходов — 2200 мм | |
Количество отводимых газов | м3/ч | ||
Тип газоочистки | ; | мокрая | |
Содержание пыли в отходящих газах: до газоочистки после газоочистки | г/нм3 г/нм3 | 1,164 0,205 | |
Оборудование для интенсификации расплавления шихты. Манипулятор | (см. ниже) | ||
Кислородная фурма: скорость перемещения фурмы | м/мин | ||
расход кислорода | м3/мин | ||
давление кислорода | кгс/см2 | 13−15 | |
Устройство измерения температуры металла и отбора проб скорость перемещения зонда | м/мин | не более 20 | |
управление работой устройства | ; | с помощью АСУТП, ручное | |
глубина погружения сменного блока зонда в расплав металла | мм | ||
длительность цикла измерения температуры и взятия пробы металла | сек | не более 10 | |
Устройство для загрузки добавочных материалов | ; | Загрузка в электропечь шлакообразующих и ферросплавов производится через специальное отверстие в водоохлаждаемой части свода | |
Диаметр загрузочной трубы и кессона | мм | ||
Электроды тип | ; | графитированные | |
диаметр | мм | ||
поставщик | ; | НЭЗ (г. Новочеркаск) НовЭЗ (г. Новосибирск), Италия, Испа-ния, Герма-ния, Япония и др | |
герметизация | ; | газодинамическое уплотнение | |
диаметр распада электродов | мм | ||
скорость перемещения электродов: в автоматическом режиме в ручном режиме | мм/сек мм/сек | 60−120 80−160 | |
привод исполнительного механизма перемещения электродов | ; | гидравлический | |
Кислородная фурма: скорость перемещения фурмы | м/мин | ||
расход кислорода | м3/мин | ||
давление кислорода | кгс/см2 | 13−15 | |
Механизм подъема и поворота свода | ; | Осуществляет подъем и поворот свода на величину, обеспечивающую полное раскрытие рабочего пространства печи Наклон печи в сторону рабочего окна для скачивания шлака производится на 10° | |
Длительность подъема и поворота свода с возвратом | сек | ||
Механизм наклона печи | ; | Осуществляет наклон пе-чи в сторону слива метал-ла на 40°, что обеспечива-ет полное удаление метал-ла и шлака. Наклон печи в сторону рабочего окна для скачивания шлака произ-водится на 10°. | |
Аппаратура контроля, автоматического регулирования и автоматизированного управления | ДСП-100И7 оснащена надежной системой контроля температуры подины с сигнали-зацией аварийного перегрева. Электропечь оснащена аппаратурой контроля параметров электрического и теплового режимов ее работы, автоматическим регулированием мощности и автоматизированной системой управления на базе вычислительной техники (АСУ ДСП). Автоматический регулятор мощности обеспечивает устойчивое горение электрических дуг при максимальных скоростях перемещения электродов во все периоды плавки. АСУ ДСП-100И7 реализует следующие функции: ? контроль и управление энерготехнологическим режимом плавки; ? контроль и управление системой газокислородных горелок; ? контроль и управление системой водоохлаждения; ? контроль и управление кислородной продувкой; ? контроль и управление отводом дымовых газов; ? контроль и управления системой дозирования и ввода в печь шлакообразующих материалов и ферросплавов; ? контроль состояния готовности основных узлов, технологических схем, устройств и пускорегулирующей аппаратуры. | ||
Агрегат ковш-печь, также называется агрегатом комплексной обработки стали (АКОС) — это звено в единой технологической схеме с дуговой печью, для доведения металла в ковше, после его выпуска из плавильного агрегата, до заданной температуры и химического состава.
В агрегате проводятся операции окончательного раскисления, десульфурации, легирования и модифицирования. Ковш накрывается водоохлаждаемым или футерованным сводом с отверстиями для введения графитированных электродов, подачи присадок и контроля процесса, наводят свежий высокоосновный шлак, обладающий высокой десульфурирующей способностью и защищающий металл от вторичного окисления окружающей атмосферой.
Таблица 6 — Технические характеристики агрегата Ковш-печь
Наименование параметра | Норма | Примечание | ||
Номинал | Допустимая | |||
1. Емкость ковша, т | ||||
2. Диаметр кожуха ковша, мм | ||||
— в верхней части | ; | |||
— в нижней части | ; | |||
3. Высота ковша, мм | ; | |||
4. Мощность трансформатора, МВА | ; | |||
5. Напряжение трансформатора, В | ||||
— высокое напряжение | + 5% | |||
— низкое напряжение | 318,5…132,5 | |||
6. Номинальный ток, кА | 32,6 | ; | ||
7. Число фаз | ; | |||
8. Напряжение цепей управления, В | 220; 24 | ; | ||
9. Напряжение силовых цепей приводов, В | ||||
10. Диаметр графитированных электродов, мм | ||||
11. Диаметр распада электродов, мм | 700+5 | |||
12. Ход электрода, мм | 2500-20 | |||
13. Скорость перемещения трех электродов одновременно вверх, мм/с | ; | |||
14. Скорость нагрева металла, 0С/мин | 3…4 | ; | расчетная | |
15. Расход охлаждающей воды, м3/ч | ||||
— на свод | ; | |||
— на вторичный токопровод | ; | |||
16. Расход аргона на продувку металла, м3/ч | 5−25 | |||
17. Расход азота на газодинамические уплотнители, нм3/ч | ||||
18. Давление аргона на продувку, МПа | 0,6 | 1,6 | ||
19. Масса агрегата ковш-печь, кг | ; | |||
Оборудование агрегата печь-ковш:
— Рабочие площадки;
— Водоохлаждаемый свод с системой подъема;
— Колонны электрододержателей с системой подъема;
— Печной трансформатор мощностью 18 МВА;
— Сталевоз для перемещения ковша;
— Система взвешивания и подачи сыпучих материалов;
— Система газоочистки отходящих газов;
— Система донной продувки металла аргоном с узлами продувки, измерения и регулирования расхода аргона;
— Система аварийной (верхней) продувки аргоном;
— Двухручьевой трайб-аппарат;
— Оборудование для определения температуры и взятия пробы металла;
— Система водяного охлаждения;
— Система сжатого воздуха;
— Гидростанция;
— Система автоматизированного управления оборудованием;
— Система автоматизированного управления процессом
— На агрегате контролируются следующие параметры:
— температура, окисленность жидкой стали и шлака;
— масса кусковых материалов по порциям и видам материалов;
— масса порошкообразных материалов, интенсивность подачи порошка;
— расход аргона на транспортирование порошкообразных материалов;
— расход аргона на аэрацию порошкообразных материалов;
— положение фурмы;
— положение механизма для ввода электродов в расплав;
— давление в пневмонасосе;
— расход аргона и давление на перемешивание металла;
— состав и давление газа под крышкой;
— электрические параметры нагрева (сила тока, напряжение, активная мощность);
— масса алюминиевой проволоки вводимой в металл;
— продолжительность обработки металла;
— давление и расход воды.
В настоящее время в сталеплавильном цехе имеется отделение непрерывной разливки стали со слябовой Машиной непрерывного литья заготовок поставки фирмы «STB».
МНЛЗ оснащена подъемно-поворотным стендом с независимым подъемом кронштейнов для приема сталеразливочных ковшей и манипулятором для установки на них крышек.
Разливка стали может осуществляться методом «плавка на плавку» полностью закрытой струей, то есть с применением защитной трубы, погружного стакана, с добавлением разливочного порошка и в защитной среде аргона.
Расчет максимальных скоростей разливки выполняется раздельно для толщин слябов 180 мм и 240 мм при этом максимально допустимые скорости разливки рассчитаны из условия принятой конструктивно металлургической длины МНЛЗ, равной 25,68 м, чтобы жидкая фаза слитка не попала в зону действия машины газовой резки.
Таблица 7 — Основные технические данные существующей МНЛЗ (по материалам фирмы «STB»)
Радиус разливочной дуги, м. | ||
Количество ручьев, шт. | ||
Металлургическая длина машины, м. | 25,68 | |
Скорость разливки | 1,72−2,17 м/мин — для сляба толщиной 180 мм ь0,97−1,22 м/мин — для сляба толщиной 240 мм | |
Размерный сортамент отливаемых слябов | 180×900 — 1600 мм 240×900 — 1600 мм длина слябов 4,5ч6,8 м | |
Вес плавки, т | ||
Емкость сталеразливочного ковша, т | ||
Цикл разливки, мин | 50−60 | |
Емкость промежуточного ковша, т | 27−30 | |
Кристаллизатор | прямой с изменением ширины и толщины | |
Тип затравки | Цепная | |
Механизм качания | Гидравлический | |
Вид резки заготовок | Газовая | |
1.3.2 Выбор шихты для выплавки Основными составляющими металлошихты являются привозной и оборотный металлолом, а также чугун.
Качество металлической шихты, ферросплавов, окислителей, шлакообразующих и заправочных материалов, используемых при выплавке стали, должно соответствовать требованиям нормативно-технической документации. Не допускается к использованию шихта, загрязненная цветными металлами.
Используемые шихтовые материалы должны удовлетворять следующим требованиям:
Максимальная масса кусков шихты, используемой на плавку, не должна превышать 30% от массы садки (с учетом загрузки завалочных устройств). Количество крупной шихты не должно превышать 40% завалки.
Размер кусков привозного углеродистого скрапа должен быть не более 600×350×250 мм.
Размер используемых прессованных пакетов должен быть не более 500×500×600 мм, плотность пакетов не менее 2 г/см3.
Размер кусков оборотного скрап из прокатного цеха (обрези): толщина куска 50…300 мм, ширина не более 1000 мм, длина не более 1500 мм.
Допускается использование стружки (без масла и воды) длиной 50.100 мм.
Суммарное содержание примесей, не удаляемых в процессе плавки, не должно превышать значений, установленных химическим составом выплавляемой стали, с учетом примесей, вносимых ферросплавами.
Перед завалкой шихты в печь мастером по плавке записывается химический состав ферросплавов, шихты, номера вагонов или автомобилей с шихтой, номера корзин, произвести в плавильной карте расчет элементов, вносимых составляющими металлошихты.
Расчет шихты производится на содержание в шихте углерода не менее 0,85%.
Содержание в металлошихте элементов, не удаляемых в процессе выплавки металла, не должно превышать значений заданного химсостава.
Требуемое содержание углерода по расплавлению шихты обеспечивается введением в металлошихту углеродосодержащих добавок (чугуном, электродным боем, кусковым коксом из расчета не более 15 кг/т).
1.3.3 Выбор огнеупорных материалов При выборе огнеупорных материалов для футеровки дуговых сталеплавильных печей необходимо учитывать, что отдельные участки футеровки работают в разных условиях. В связи с этим условия службы огнеупоров подины и откосов, стен и свода рассматривались отдельно.
Подина и откосы. В течение длительного времени огнеупорная футеровка подины непосредственно контактирует с расплавленными металлом и шлаком. После выпуска плавки и при загрузке холодной шихты происходит резкое охлаждение подины. При загрузке шихты корзиной подина в целом испытывает механический удар, а поверхностный слой подины повреждается врезающимися кусками скрапа. В период плавления при неудачно составленной завалке, когда под электродами оказывается легковесная шихта, электроды могут опуститься до подины прежде, чем на ней образуется достаточный слой жидкого металла. Горящие при тонком слое металла дуги перегревают и вымывают материал подины, образуя ямы.
В период плавления при неудачно составленной завалке, когда под электродами оказывается легковесная шихта, электроды могут опуститься до подины прежде, чем на ней образуется достаточный слой жидкого металла. Горящие при тонком слое металла дуги перегревают и вымывают материал подины, образуя ямы. Во время плавления и в окислительный период футеровка подины насыщается закисью железа. В восстановительный период окислы железа переходят в обратном направлении — из футеровки подины и откосов в металл и шлак.
Восстановительная среда после выпуска плавки снова меняется и становится окислительной.
При сливе и после слива металла футеровка подины непосредственно контактирует со шлаком и насыщается им. В значительно большей степени, чем подина, воздействию шлаков при высоких температурах подвержена футеровка откосов, поэтому откосы являются наиболее слабым участком футеровки электропечей. Футеровка подины и откосов не только подвержена влиянию указанных выше факторов, но и сама влияет на ход процесса в сталеплавильной ванне. Попадающая в шлак окись магния снижает жидкотекучесть шлака, уменьшает его химическую активность. В связи с этим не только увеличивается расход огнеупорных материалов, но и требуется больше времени на рафинирование металла, повышается расход шлакообразующих на нейтрализацию вредного влияния MgO, увеличивается расход электроэнергии.
Исходя из назначения и условий работы футеровки подины и откосов, к ней можно предъявить ряд требований. Рабочий слой подины, непосредственно контактирующий с металлом и шлаком, должен обладать высокой огнеупорностью, термостойкостью, противостоять химическому и механическому воздействию металла и шлака. Подина в целом должна быть достаточно механически прочной, чтобы воспринимать механические удары при загрузке шихты, и обладать большим тепловым сопротивлением. Стены. Температурные условия работы внутренней поверхности стен особенно тяжелы, так как в отдельные периоды плавки температура некоторых участков стен может превысить огнеупорность материала, а при открывании рабочего пространства и загрузке шихты стены быстро охлаждаются. Скорость изменения температуры внутренней поверхности стен может достигать, как уже отмечалось, 10 000 °С/ч, что создает значительные термические напряжения в футеровке. В связи с этим внутренний слой футеровки должен быть выполнен так, чтобы ему были свойственны высокая огнеупорность и термостойкость, низкий коэффициент теплового расширения и высокий коэффициент температуропроводности, а для получения большого теплового сопротивления футеровка стен печи должна быть хорошо теплоизолированной с внешней стороны. В особо тяжелых температурных условиях работает нижний пояс футеровки стен шириной 300—400 мм, находящийся под прямым излучением дуг переменного тока и воспринимающий нагрузку от верхних слоев кладки стен. Поэтому нижнюю часть стен следует выполнять из особо огнеупорных материалов, или в крайнем случае, делать ее достаточно большой толщины.
Свод является наименее долговечной частью футеровки дуговых печей. Как и футеровка стен, свод испытывает значительные температурные колебания. По ходу плавки свод может прямо воспринимать излучение выдуваемых из-под электродов дуг, а также поглощать отражаемое шлаком и футеровкой печи излучение. В результате температура свода, особенно его центральной части, может превысить огнеупорность материала, и свод может подплавляться. Особенно часто подплавление свода происходит при работе с очень жидкими шлаками, обладающими большой отражательной способностью. При открывании рабочего пространства и отвороте сводового кольца его излучение воспринимается холодными элементами конструкции печи, и свод быстро остывает.
Это вызывает появление больших термических напряжений, приводящих к скалыванию свода. Свод постоянно испытывает сжимающую нагрузку от распора, что снижает температуру начала его деформации. Выбивающиеся из печи раскаленные газы содержат много пыли, которая оседает на своде и при высокой температуре может вызвать его химическое разрушение. Исходя из особенностей службы огнеупоров в сводах дуговых печей, к ним можно предъявить ряд особых требований. Эти огнеупоры должны характеризоваться высокой огнеупорностью, термостойкостью, химической стойкостью по отношению к плавильной пыли, большим тепловым и электрическим сопротивлением. Последнее вытекает из того, что при недостаточном электрическом сопротивлении материала свода электрическая цепь между фазами может частично замкнуться по своду. Это может привести к возникновению электрических дуг между сводом и водоохлаждаемыми элементами уплотнений электродов в своде, прогоранию водяной рубашки и попаданию в печь воды.
Итак для футеровки электропечи используют периклазовые, в том числе из плавленого сырья огнеупоры, обладающие достаточно высокой огнеупорностью и термостойкостью.
В частности, ванна электропечи имеет комбинированную футеровку из периклазовых и периклазоуглеродистых кирпичей и периклазовой набивной массы, выпускное отверстие электропечи — специальные периклазовые огнеупоры, а огнеупорная часть свода электропечи выполняется из муллитовых (высокоглиноземистых) огнеупоров.
1.3.4 Технологическая карта (схема) выплавки Сталь в дуговой печи выплавляется по двум вариантам:
— с завалкой металлошихты на «болото» (40−50 т металла предыдущей плавки);
— с завалкой металлошихты на «сухую» подину, очищенную от остатков шлака и металла от предыдущей плавки. Проводятся: после холодного ремонта подины в течение первых двух плавок подряд. При превышении температуры подины в одной из нескольких замеряемых точек более чем 300 °C. По указанию старшего мастера печного участка с целью контроля за состоянием футеровки подины печи.
Подготовка печи Выплавка полупродукта производится при удовлетворительном твердом состоянии подины и откосов, с защитным гарнисажем на водоохлаждаемых панелях стен и свода, с хорошо очищенным и засыпанным эркерным отверстием, целыми электродами, при исправном состоянии и надежной работе охладительной системы, механизмов, электроаппаратуры и газоочистки. После холодного ремонта стен выплавляется две плавки стали общего назначения. После замены подины выплавляется 3 плавки стали общего назначения по специально утвержденному начальником цеха электрическому режиму.
Подготовка печи к завалке лома осуществляется в следующей последовательности: перед завалкой бадьи электроды выставляются на полный подъем и, по достижению верхнего концевого выключателя, автоматически блокируются в безопасном положении. Производится открытие свода печи. Предварительно необходимо отсоединить систему дымоотсоса, осуществить подъем и поворот свода и закрыть дверцу шлаковой летки. После выгрузки лома из бадьи (корзины), поправить лом внутри печного пространства, используя бадью. Затем закрыть свод и подать напряжение на электроды. Произвести опускание электродов в автоматическом режиме. После расплавления «болота» начинается ввод лома в печь при помощи системы непрерывной загрузки Consteel. Масса загруженного лома контролируется при помощи системы взвешивания, установленной на платформе печи. Выпуск первых двух плавок осуществлять «насухо», с обязательным контролем состояния подины и откосов и их заправкой. После выпуска предыдущей плавки производится удаление остатков шлака и настылей из канала эркера и торца концевой втулки эркерного выпуска. Отверстие снизу плотно заделывается каолиновой ватой на высоту от 250 до 300 мм, после чего эркер закрывается затвором. Далее отверстие засыпается массой марки Theramer Fill 226 до образования «горки» над уровнем футеровки подины.
Заправка подины и откосов:
Для заправки подины печи применяется торкрет-масса JEGUN. После выпуска металла печь наклоняют в сторону рабочей площадки для осмотра футеровки мастером и сталеваром с целью общей оценки состояния откосов, подины и выявления на ней остатков металла и шлака. Одновременно оценивается состояние свода и стен. Остатки металла с подины нужно удаляют повторным наклоном печи в сторону слива металла (операция выполняется после заделки эркерного отверстия). Остатки не удаленного металла необходимо заморозить в эркерной зоне печи. При выдувке кислородом остатков металла с подины необходимо обрез трубки держать на расстоянии от 150 до 200 мм от поверхности металла (определяется визуально), при этом для более полного удаления металла из углублений в подине до 100 мм глубиной рекомендуется давать под струю кислорода небольшие порции магнезитового порошка. Количество порошка определяется мастером (старшим мастером), порошок дается вручную — лопатой. При углублении подины более 100 мм и наличии в углублении остатков жидкого металла, в металл опускается специальная сляба с целью намораживания остатков металла. После выдержки и намораживания металла на слябу (определяется визуально) производится удаление слябы с намороженным металлом. После оценки состояния подины производится ремонт подины. Заправка подины и откосов производится механизированным способом. Допускается заправка вручную. Углубление ванны производить под руководством старшего мастера присадками кварцитового песка, кварцита или порошка ферросилиция.
Горячий ремонт подины проводить по мере необходимости в местах локального износа подины методом подсыпки ремонтных масс согласно ВТИ 123-ЭС-02−2010. После заправки подины, откосов и завалки шихты при необходимости производить частичный ремонт стен (подварка) массами согласно ВТИ 123-ЭС-02−2010. Порог рабочего окна должен быть заправлен до уровня, обеспечивающего сход шлака во время окислительной продувки. При работе на «болоте» общий износ футеровки подины контролируют не реже одного раза в смену путем измерений с помощью шомпола, изогнутого на конце под углом 90о (по визуальной оценке) и рулетки, а также по показаниям теплоприборов в зонах ванны. Шомполом прощупывают всю площадь подины. В случае нарушения твердости подины или обнаружения углублений, принимают меры к сливу плавки «насухо» и производят ремонт подины.
ь Подготовка скрапа для загрузки на конвейер Consteel
Изначально ДСП загружают при помощи скраповой бадьи, оборудованной зажимом на дне, используя основной и вспомогательный крюки загрузочного крана. Печь и скраповая бадья предназначены для выполнения загрузки за счет двух или трех бадей даже при завалке легковесного лома (плотностью< 0,7тонн/м3). Загрузка не должна превышать 90% объема печи во избежание проблем с закрытием свода. Последовательность загрузки лома в бадью — исключительно важна (особенно, первая загрузка или первоначальная загрузка при условии использования Consteel).
При погрузке лома на конвейер учитываются следующие моменты:
Лом должен быть разложен равномерно, его толщина должна составлять приблизительно 650 мм, что на 150 мм ниже высоты загрузочного конвейера. Если используются чугун и брикетированное железо, для получения равномерной выплавки они должны быть разложены на загрузочном конвейере тем же самым образом. При этом загрузка чугуна и брикетированного железа в ДСП должна быть остановлена приблизительно за 15 минут до выпуска для того, чтобы предотвратить любые задержки, вызванные высоким содержанием углерода. Из-за высокой плотности чугуна и брикетированного железа (ГБЖ), при использовании этих материалов нагрузка конвейера соответственно увеличивается. Следовательно, контур с системой взвешивания для содержащейся в ДСП жидкой стали затормозит скорость конвейера для того, чтобы соответствовать интенсивности подачи в рамках заданной системы продолжительности загрузки. Загружаемые на конвейер Consteel чугун и брикетированное железо, дойдут до печи приблизительно через 10 минут. Более крупные, тяжёлые куски скрапа могут поглотить больше тепла во время транспортировки через устройство предварительного подогрева, следовательно, по возможности, они должны быть размещены на верхнем слое.
ь Подготовка скраповой бадьи (корзины) Дно бадьи должно быть наполнено слоем легковесного лома без воды или масла; дробленный очищенный лом может использоваться вплоть до 10% от общего объема завалки. Данный слой действует в виде подушки для обеспечения защиты огнеупорного пода печи от возможных повреждений из-за тяжеловесных кусков скрапа. А также является неким уплотнением, предотвращающим потери через дно бадьи мелкого лома. Следующий слой должен содержать самые тяжелые (большие) куски лома вплоть до 15% от загрузки бадьи во избежание поломки электродов при падении лома во время плавления. На поверхность тяжеловесного лома добавляют науглероживающий материал, материал для образования шлака (известь, известняк и доломит), которые должны быть расположены вблизи стен бадьи вне области распада электродов. Следующий слой лома должен составлять основной объем веса шихты. Это слой лома среднего веса для защиты футеровки и водоохлаждаемых панелей от теплоизлучения дуги. Последний слой — это легковесный лом малого размера, необходимый для облегчения дугового зажигания и выравнивания дуги.
ь Шихтовка плавки Плавку шихтуют из расчёта получения в металле после расплавления значений массовых долей химических элементов не выше заданных в марке стали.
Основные требования к шихтовым материалам:
Масса тяжеловесных отходов (обрези) в составе общей массы завалки должна быть не более 50%. Во избежание риска взрыва следует загружать сухой скрап (без масла, воды) и не использовать герметизированные контейнеры.
Куски скрапа не должны превышать по длине 1,5 м, по ширине 0,5 м и по высоте 0,5 м. (по массе максимум ~ 1,5 т). В состав шихты может вводиться никель, медь, молибден на нижний предел марочного состава, а также отходы, легированные никелем, медью и молибденом. Шихтовку плавки по массовой доле углерода производят чугуном (твердым) или коксом (антрацитом). Отходы производства и лом, содержащие медь, никель и другие легирующие элементы складируются и хранятся раздельно по группам и сортам и использовать в завалку только при выплавке марок стали, легированных этими элементами. Общая масса металлошихты должна составлять от 125 до 135 т (без учета остатка жидкого металла в печи от предыдущей плавки). При шихтовке плавки загрузка металлошихты производиться загрузочной бадьей и с конвейера. Часть шлакообразующих материалов (2−3 т) вводить вместе с металлоломом в загрузочную бадью, остальное количество — в печь по ходу плавки порциями массой от 150 до 250 кг. Общий расход извести должен составлять от 5,0 до 6,0 т на плавку. Допускается вместо извести использовать в завалку от 2,5 до 3,0 т известняка. В этом случае расход извести в ДСП (через свод) должен составлять от 2,5 до 3,5 т. При отсутствии чугуна в металлошихте масса вводимой в печь (загружаемой сверху или вдуваемой через инжектора) коксовой мелочи или углеродсодержащего материала должна составлять не менее 1000−1200 кг.
Процесс завалки и подвалки металлошихты в печь осуществлять в следующем порядке. Перед опусканием корзины с ломом в печь полностью закрывают рабочее окно и шлаковую летку печи. Корзина с металлошихтой опускается так, чтобы ребро жесткости челюстных затворов находилось в створе верхнего среза каркаса электропечи. По команде сталевара крановщиком производится медленное раскрытие корзины. После того, как на подину просыплется первая порция металлошихты массой от 1 до 3 т, корзину медленно поднимают вверх до полного раскрытия челюстных затворов с одновременным освобождением ее от металлолома. Нахождение персонала на рабочей площадке перед печью во время завалки не допускается.
ь Ферросплавы Ферросплавы, предназначенные для присадки в жидкий металл, должны быть прокалены в нагревательной печи докрасна не менее 20 минут.
Продолжительность времени от конца прокалки (сушки) до использования ферросплавов, как правило, не должна превышать 8 часов.
Порошки, применяемые для раскисления шлака, должны иметь фракцию: ферросилиций, силикокальций и алюминий — не более 2 мм, кокс — не более 1 мм.
ь Окислители Твердые окислители — железорудные окатыши, железная руда (в дальнейшем — окатыши) перед использованием должны быть прокалены в нагревательной печи докрасна в течение не менее 20 мин. Газообразный кислород, применяемый для продувки металла в печи, должен содержать не более 0,8 г/м влаги.
ь Шлакообразующие Шлакообразующие, применяемые в рафинировку, должны быть прокалены в нагревательных печах докрасна и иметь размер отдельных кусков не более 150 мм.
ь Плавление на ДСП После завалки металлошихты свод переводят в рабочее положение и сталевар производит включение печи в соответствии с утверждённым электрическим режимом. Сразу после включения печи, включают в установленном режиме стеновые комбинированные фурмы-горелки. После расплавления первой загрузки до определенной степени подают лом, чугун, ГБЖ, углеродсодержащие материалы фракцией 5−20 мм через отверстие Consteel, расположенное на боковой стене ДСП. Шлакообразующие материалы (известь, плавиковый шпат, глиноземсодержащие материалы) подают посредством системы перемещения материалов через свод. Объем подаваемого лома регулируется за счет компьютерной программы в зависимости от потребляемой мощности, доступной электрической и химической энергии, а также температуры ванны. Данная программа учитывает также объем вводимого углеродсодержащего материала фракцией 0,1−3 мм (далее УСМ) и извести или известняка. В случае недостаточной пенистости шлака или чрезмерной подачи лома необходимо: сократить интенсивность подачи лома; увеличить мощность; увеличить объем шлака путем добавления УСМ (образование пены). Ввиду низкого уровня металла в печи на этом этапе, а также с целью получения заданного химического состава шлака, вместе с ломом добавляют известь, доломит и УСМ.
Кислород используют для формирования пенистого шлака. Пенистый шлак сохраняют для обеспечения защиты водоохлаждаемых панелей и огнеупорной футеровки, сокращения расхода электроэнергии и времени работы под током. Кислород и УСМ используют с начала плавки для получения химической энергии посредством окисления углерода и производства достаточного объема печного газа для формирования пенистого шлака с целью обеспечения защиты дуги и боковых стен, а также для сокращения времени работы под током Кислород подают при помощи кислородных модулей. Во время данного этапа процесса плавления интенсивность подачи лома и других железосодержащих материалов, извести определяется сталеваром для получения температуры ванны примерно 1560 °C. После отработки 20−25 МВтч производят отбор пробы металла для определения массовых долей углерода, марганца, фосфора, серы, хрома, никеля и меди, пробы шлака для определения массовых долей CaO, Si02, FeO, MnO, MgO и измерение температуры металла. Пробы шлака отбирают намораживанием на кислородную трубку. Основность шлака (CaO/ Si02), должна составлять 1,7−2,5. Пробу металла отбирают с помощью специального пробоотборника. Если проба металла из-за неудовлетворительного качества (проба в раковинах) бракуется, то производят повторный ее отбор. Результаты химического анализа пробы металла и шлака фиксируются в паспорте плавки сталеваром. Контроль массовой доли углерода в металле производят по результатам химического анализа пробы металла. Для защиты футеровки печи от теплового излучения электрических дуг и увеличения объёма полезной мощности трансформатора, а также предотвращения насыщения стали азотом, на протяжении всей плавки запрещается допускать оголение дуг. Шлак должен находиться во вспененном состоянии, для чего в процессе шлакообразования в печь сверху присаживают сначала коксовую мелочь массой от 300 до 600 кг (при наличии нерасплавленной шихты в районе инжекторов для УСМ) с последующим вдуванием углеродсодержащего материала от 800 до 1200 кг. При неисправной установке для вдувания УСМ разрешается в печь вводить через свод коксовую мелочь массой от 800 до 1000 кг порциями массой от 20 до 60 кг. Допускается вдувание УСМ проводить через три устройства. В процессе продувки кислородом вспененный шлак удаляют из печи самотёком, не допуская схода металла и оголения дуг. Основность шлака в печи должна быть от 1,8 до 2,2. Известь вводят в печь равномерно в процессе окисления и нагрева металла порциями по 200−300 кг. Для предотвращения повышенного износа футеровки печи массовая доля оксида магния (MgO) в шлаке должна быть от 5,0 до 9,0%, для чего в печь после спуска шлака вводят доломит массой 700−800 кг порциями по 200−300 кг. Содержание оксида магния (MgO) в шлаке корректируется в зависимости от основности шлака и содержания в нем FeO. Продолжительность от последнего измерения температуры до начала выпуска плавки должна быть не более 3 минут. Температура металла перед выпуском плавки должна быть не менее 1620 °C. В процессе наведения рафинировочного шлака отбирают 2−3 пробы шлака. Последнюю пробу шлака отбирают перед выпуском, намораживанием на кислородную трубку. В пробе не должно быть посторонних примесей. При отправке пробы по пневмопочте сообщают лаборанту номер плавки и номер пробы.
ь Доводка плавки Скрап подают до определенной степени в соответствии с доступной мощностью. Как только достигнуто примерно 85−90% общей загрузки, автоматически начинается процесс доводки плавки, электроэнергия уменьшается примерно на 10 — 15%, интенсивность подачи скрапа также уменьшается для обеспечения увеличения температуры в ванне жидкой стали до получения температуры для выпуска плавки.
ь Подготовка к выпуску плавки За 5−8 минут до выпуска печь отклоняют не более чем на 2 градуса в сторону шлаковой летки для скачивания шлака. Когда скачивание шлака завершено, наклоняют печь обратно в горизонтальное положение. Отбирают пробу металла и шлака для проверки химического состава. Интенсивность вдувания кислорода и УСМ регулируются по мере необходимости для того, чтобы достичь температуры выпуска. Для повышения температуры ванны до уровня не менее 1620 оС замедляют ход конвейеров. Температура металла перед выпуском корректируется в зависимости от количества отдаваемых материалов в ковш. Сталь-ковш подготавливается и перемещается в положение для выпуска плавки. Температура футеровки сталь-ковша должна быть не менее 1000о С за 10 минут до выпуска. Ферросплавы для выпуска должны быть подготовлены основываясь на результат химанализа пробы, взятой после скачивания шлака. При необходимости увеличения окончательной температуры ванны можно уменьшить скорость конвейера до минимума. Необходимо, чтобы соединяющая тележка в этот период двигалась. Измеряют температуру ванны, чтобы убедиться в том, что температура выпуска достигнута. После достижения температуры выпуска кислородную и углеродную фурмы отключают. Несущие электрододержатели поднимают до «половины хода» поворачивая управляющее устройство элетрододержателя в положение «быстрый подъём». Отодвигают соединяющую тележку. Как только соединяющая тележка начинает двигаться обратно, двигатель отключится автоматически. Гидравлический цилиндр останавливается автоматически, когда достигнет координаты отвода. Регулирование переключают с основного пульта управления на пульт поста управления выпуска. Сообщают оператору пульта управления выпуска о том, тележка готова к выпуску.
ь Выпуск и подготовка к перезапуску Как только с пульта управления получено сообщение о том, что всё готово к выпуску, начинают процедуру:
— убедившись, что сталь-ковш правильно расположен под печью и включена донная продувка аргоном. Он не должен быть непосредственно центрирован к выпускному отверстию, должен находиться немного впереди;
— убедившись, что ферросплавы готовы для разгрузки в сталь-ковш;
— убедившись, что пульт управления для выпуска включён и соответствует настроенным значениям выпуска;
— наклоняют печь на сторону выпуска, останавливают приблизительно на четырёх градусах. Это увеличивает объём стали над выпускным отверстием, который способствует выпуску стали без шлака. Если печь слишком наклонена, есть риск, что жидкая сталь может вступить в контакт с охлаждаемой водой панелью эркера;
— когда печь наклонена на немного более чем 2 градуса на сторону выпуска, буферы на стороне шлака должны автоматически передвинуться назад. Тем не менее до выпуска печи необходимо убедиться в том, что оба буфера печи передвинуты назад. Буферы должны быть передвинуты назад для того, чтобы дать возможность наклонить печь обратно в исходное положение, когда выпуск завершён;
— передвигают назад механизм блокировки эркера;
— открывают выпускное отверстие;
— после того, как сталь начинает течь в ковш, запускают систему загрузки ферросплавов, которые дозированы и готовы к загрузке;
— постепенно увеличить угол наклона печи для поддержания объёма жидкой стали над выпускным отверстием. При выпуске слегка изменяют положение ковша, так как угол наклона печи увеличивается;
— поднимающийся уровень стали в ковше контролирует оператор визуально на пульте управления выпуском. Когда уровень стали достигнет необходимого уровня свободного борта, начинают обратный наклон. Быстрая скорость возвращения в обратное положение способствует уменьшению объёма шлака, который проходит через выпускное отверстие, так как жидкое болото перемещается на сторону шлака. Продолжают наклон обратно при нормальной скорости до тех пор, пока печь доходит до примерно 6 или 7 градусов на стороне шлака. После наполнения ковша до необходимой массы его вывозит сталевоз из-под печи для дальнейшей его транспортировки на АКП.
При выпуске полупродукта в ковш присаживать следующие материалы:
— алюминий из расчета содержания углерода в последней пробе согласно табл.8:
Таблица 8 — Расчетное количество присаживаемого алюминия, кг
Массовая доля углерода в стали перед выпуском, % | Масса алюминия для присадки в ковш, кг | |
<0,05 | ||
0,05−0,07 | ||
0,07−0,09 | ||
0,10−0,15 | ||
0,16−0,20 | ||
0,20 не менее | ||
— науглероживатель (УСМ, УМВК и т. п.) на нижний предел марочного состава (ориентировочное усвоение 70%);
— ферросилиций (ФС 45, ФС 75) по расчету на нижний предел кремния в марке с учетом угара 30%;
— ферро (силико)марганец (МнС12 или МнС17) по расчету на нижний предел марочного состава по марганцу с учетом угара 20%.
— феррохром (ФХ 100А, ФХ 200А, ФХ 800А, ФХ 850А) но не более 1 т;
— 700 — 800 кг свежеобожженной извести;
— глиноземсодержащий материал (АШБ, СГГ и т. п.) из расчета введения 350 кг Al2O3. При отсутствии материалов, содержащих Al2O3 в ковш вместо глиноземсодержащего материала присаживают плавиковый шпат массой 250−300 кг.
Температура металла перед выпуском и количество отданных материалов должны обеспечивать поступление металла на АКП со следующими параметрами:
Таблица 9 — Требования к полупродукту при поступлении на АКП
Температура полупродукта, оС | Содержание элементов в первой пробе на АКП, % | ||||
S | P | Si | Mn | ||
Не ниже 1580 | Не более 0,060 | Не более 0,015 | На нижнем пределе по марке (см. приложение 4) | ||
Для обеспечения максимального контакта металла и шлака во время и после выпуска осуществляют продувку аргоном через донную фурму сталь-ковша не менее 10 минут. По окончании продувки производят измерение температуры металла в ковше и отбирают пробу металла. Продолжительность транспортировки ковша с металлом от выпуска из ДСП до постановки его на стенд АКП должна быть не более 20 минут.
ь Описание технологических операций обработки стали на АКП Полупродукт передается в ОНРС в ковше, перевозимом на передаточной тележке (сталевозе). С целью удаления печного шлака, ковш с полупродуктом сначала устанавливают на машину скачивания шлака. Уровень металла не должен быть выше 400 мм от верхнего края ковша. В случае его превышения на машине скачивания шлака излишки металла сливаются в шлаковую чашу.
ь Скачивание шлака на МСШ Удаление шлака с поверхности стали производится механическим скребком. Для начала скачивания шлака с помощью МСШ ковш слегка наклоняют, а стрелу МСШ поднимают на такую высоту, чтобы скребок пришел в соприкосновение со шлаком по центру ковша. Затем для разламывания корки скребок перемещают к дальнему борту ковша. Во избежание выплеска шлака и металла из ковша запрещается производить прорыв корки шлака чрезмерным наклоном ковша. После пробивания корки по середине ковша, ее ломают скребком, расширяя зону взломанного шлака. Затем начинают скачивать, перемещая скребок «на себя». Скачивание шлака производят до появления зеркала металла. Уровень металла в ковше не должен быть выше 400 мм от верхнего края ковша. При скачивании шлака не допускают ударов скребка о футеровку ковша. Не разрешается срывать скребком настыли стали с ковша. Не следует погружать скребок в сталь. После скачивания шлака устанавливают очищенный от шлака ковш с металлом на сталевоз АКП. Установка ковша с металлом на стенд наклона МСШ и установка ковша на сталевоз № 2 под обработку на АКП-100 осуществляется с помощью крана.
ь Обработка стали на АКП Производится стыковка аргонопровода с ковшом для донной продувки. Устанавливается сталевоз с ковшом в положение «под крышкой». Опускается свод на ковш, состыковав газоход с газоотводящим патрубком свода, создать разрежение в газоходе до начала обработки стали. Устанавливается рабочий расход аргона для продувки стали (устанавливается визуально по «пятну» продувки не более 0,5 м). Для открытия забитой, «закозлившейся» продувочной пробки разрешается кратковременная подача аргона с давлением 1,6 МПа. В случае невозможности продувки ковша через донный продувочный узел дальнейшую обработку металла ведут по резервной схеме с использованием аварийной фурмы верхней продувки, предварительно просушенной на специальном стенде. При нормальной работе пробки в автоматическом режиме, режимы подачи аргона согласуются с выбранным режимом нагрева (ступенью мощности) работы АКП, состоянием шлака и периодом обработки:
— расход аргона по периодам обработки стали на АКП может изменяться в зависимости от состояния продувочного узла, при нормальном состоянии продувочного узла расход аргона составляет 5 — 25 м3час;
— если во время нагрева наблюдается повышенный шум от электродов при неустойчивом горении дуг и значительных бросках напряжения, снижают расход аргона или переходят на более низкую ступень напряжения до наведения необходимого уровня шлака.
— визуальный контроль продувки проводят каждые 5 — 10 минут, особенно при работе на высоких ступенях нагрева, оголение зеркала металла должно составлять не более 0,5 м в диаметре.
Измеряется температура стали. Для повышения стойкости футеровки шлакового пояса сталь-ковшей вводится магнезитовый порошок марки ППК-88 в количестве до 0,6 кг/т. Вводится ТШС в количестве 300 кг. Включается АКП. Нагрев металла начинается с более низких ступеней мощности и переходит к более высоким ступеням после образования достаточно жидкоподвижного шлака. Во избежание повышенного износа футеровки ковша не работают на повышенных ступенях мощности при малых расходах аргона. Избегают повышенного расхода аргона, при котором наблюдается нестабильная работа электродов — броски тока по фазам, а также образование оголенных участков поверхности стали. Для уменьшения прямого излучения от дуг на футеровку ковша и уменьшения износа футеровки дуга прикрывается шлаком. Прогревается металл в течение 5−8 мин. Производится первая стадия нагрева стали в ковше до полного расплавления и усреднения шлака.
Измеряют температуру металла, отбирают пробу металла и шлака. По результатам химического анализа определяют последующий режим обработки и производят доводку химического состава стали вводом ферросплавов, наведением рафинирующего шлака. После получения заданного химического состава и температуры на АКП в ковш с металлом отдают 1 м3 теплоизоляционной смеси марки ТИС-250ВД и передают в разливочный пролет. После обработки металла на АКП-100 ковш с металлом снимается со сталевоза и передается на разливку, или стенд ожидания, с помощью крана.
Для обеспечения накопления ковшей для серийной разливки на МНЛЗ температура окончания обработки стали на АКП может быть увеличена с учетом последующей продувки на стенде ожидания, но не выше, чем 1650оС.
ь Раскисление рафинирующего шлака и металла. Легирование стали Для марок стали с массовой долей углерода в готовом металле более 0,12% используют углеродсодержащие материалы (фракции до 5мм), присаживаемые на поверхность шлака равномерно по всему зеркалу шлака порциями от 10 до 50 кг в зависимости от заданной массовой доли углерода в выплавляемой марке стали. Для раскисления шлака сталей с содержанием углерода в готовом металле менее 0,12% используют гранулированный или дробленый алюминий, алюминий содержащий концентрат, либо алюмо-шлаковые брикеты.
Присадки ферросплавов производят в следующем порядке:
— добиваются получения однородного высокоосновного хорошо раскисленного жидкоподвижного шлака;
— устанавливают повышенный расход аргона (до 25 м3/ч);
— вносят присадки порций ферросплавов, визуально контролируя их прохождение и усвоение;
— через 2 минуты после прохождения последней порции, расход аргона уменьшают.
Рекомендуемая масса разовой порции ферросплавов — не более 100 кг. Корректировка содержания массовой доли углерода в металле производится путем присадки углеродсодержащих материалов фракции 0,5- 10 мм, через систему сыпучих материалов, на продувочное пятно (порциями, массой не более 50 кг), или вводом углеродсодержащих материалов через устройство для вдувания порошкообразных материалов. Окончательную корректировку химического состава стали, вне зависимости от количества присаживаемых материалов, производят не позднее, чем за 10 минут до окончания обработки металла на АКП Показанием к окончанию процесса является достижение заданной температуры, при обеспечении заданного химического состава стали. После получения положительного анализа последней пробы и оптимальной температуры стали подают ковш на разливку.
ь Разливка стали на слябовой машине непрерывного литья заготовок Непрерывная разливка стали состоит в том, что жидкую сталь из ковша 1 через промежуточное разливочное устройство 2 непрерывно подаются в водоохлаждаемую изложницу без дна — кристаллизатор 3, из нижней части которого вытягивается затвердевающий слиток 5 (рис.1).
Перед заливкой металла в кристаллизатор вводится затравка — стальная штанга со сменной головкой, имеющей паз в виде ласточкиного хвоста, которая в начале заливки служит дном кристаллизатора. Вследствие интенсивного охлаждения жидкий металл у стенок кристаллизатора и на затравке затвердевает, образуется корка, соединяющая металл с затравкой. Затравка движется вниз при помощи тяговых роликов 6, постепенно вытягивая затвердевающий слиток из кристаллизатора. После прохождения тяговых роликов 6, затравку отделяют. Скорость вытягивания составляет в среднем 1 м/мин. Окончательное затвердевание в сердцевине происходит в результате вторичного охлаждения водой из форсунок 4. Затем затвердевший слиток попадает в зону резки, где его разрезают газовым резаком 7, на куски заданной длины. Слитки имеют плотное строение и мелкозернистую структуру, отсутствуют усадочные раковины.
Рисунок 2 — Схема непрерывной разливки стали ь Подготовка промежуточных ковшей и погружных стаканов к разливке Разливщиком МНЛЗ принимается промковш с огнеупорного участка после сушки. При приемке не допускается наличие мусора и остатков раствора в рабочей полости. После приемки разливщик устанавливает стакан-дозатора и механизм «Интерстоп», огнеупорщик производит набивку стакан-дозатора после чего разливщик устанавливает стопор. Футерованный промковш накрывается крышкой и устанавливается на тележку промковша. Предварительный разогрев промежуточных ковшей для разливки производится на специальном стенде высокотемпературного разогрева промежуточных ковшей, оборудованного газовыми горелками. Во время нагрева промковша стопор открыт. При транспортировке промковша стопор закрыт. Время установки промежуточного ковша на разогрев отмечается в технологическом журнале. Разогрев производится до температуры 1100 — 1200 °C. При разогреве промежуточного ковша под стакан-дозатором применяется труба для разогрева (эжектор). Погружной стакан устанавливается за 1−1,5 часа до начала разливки и разогревается вместе с разогревом футеровки промковша. Перед установкой погружного стакана визуально проверяется состояние канала стакан-дозатора на предмет засоренности и работоспособность стопора. Запасной стакан разогревается на передвижной станции разогрева в течении 45 — 90 мин. Время между окончанием разогрева погружного стакана и началом разливки не превышает 5 мин. Погружной стакан разогревается до температуры 700 °C (желто-красного цвета, оценка визуальная). Производится проверка целостности стакана, геометрия, отсутствие трещин и сколов (визуально), готовность аварийного шибера промковша.
ь Проверка и подготовка кристаллизатора После установки и регулировки исходной ширины и конусностикристаллизатора, оператором МНЛЗ проверяется поверхности широких и узких плит кристаллизатора на отсутствие повреждений. Зазор в стыках узких и широких медных плит не должен превышать 0,2 мм. Медные плиты визуально контролируются на наличие механических повреждений. Глубина канавок и царапин не должна превышать 0,5 мм в верхней части и 1,5 мм в нижней части кристаллизатора. При превышении пределов дефекты зачищают наждачной бумагой. Проверяют кристаллизатор на отсутствие течи воды в рабочую полость при максимальном расходе воды, путем установки максимального расхода воды на кристаллизатор.
ь Ввод затравки Перед введением затравки оператор проверяет:
— надежность крепления головки к телу затравки. Головка затравки должна быть сухой, очищена от остатков металла, заусенец, не иметь трещин и других видимых дефектов. Перед заведением затравки в кристаллизатор проверяет работу всех механизмов.
При помощи тележки перемещения затравки перемещают её из «зоны парковки» до рольганга. После установки затравки на рольганг, производят её центровку, перемещают в направлении машины автоматически со скоростью 3,5 м/мин.
При достижении головки затравки середины бендера, она автоматически останавливается, введение затравки в кристаллизатор выполняется вручную с помощью толчкового режима продвижения со скоростью 0,4 м/мин. Выполнив указанные проверки оператор нажимает на пульте кнопку «Введение затравки». Расстояние между затравкой и верхней гранью кристаллизатора должно составлять не более 600 мм.
Зазор между стенками кристаллизатора и головкой затравки должен составлять:
— со стороны широких стенок — не более 3 — 8 мм
— со стороны узких стенок — не более 4 — 15 мм.
После установки головки затравки в исходное положение производят следующее:
— обдувают сжатым воздухом головку затравки для удаления загрязнений и влаги;
— тщательно заделывают зазоры между головкой затравки и стенками кристаллизатора бумажным шнуром или шнуром асбесто-пуховым, не ранее чем за 30 мин до начала разливки. Набивку затравки необходимо начать с малого радиуса;
— по периметру на набивку кладут окалину или чугунную стружку толщиной 20−25 мм, или обрезь тонколистового проката (2- 3 мм);
— на поверхность стенок кристаллизатора наносится тонкий слой смазки (смесь отработанного масла и ШОС);
— на всех кристаллизаторах стыки узких и широких стенок (углы) по всей высоте кристаллизатора замазывают чугунной замазкой либо замазкой, замешанной до густого состояния, состоящей из солидола и графита или солидола и ШОС. Также допускается замазку углов производить густым водным раствором алебастра.
— ложат на головку затравки слой металлической сечки и материалы-холодильники (охлаждающие клети), которые должны быть прокалены и не иметь масляного загрязнения.
ь Подготовка МНЛЗ к приёму жидкого металла Готовят ёмкости для аварийного слива металла. Наличие влаги, шлака, металла в них не допускается. Проверяют наличие рабочего инструмента, шлакообразующей и теплоизолирующей смеси на рабочей площадке разливки. Содержание влаги в шлакообразующей и теплоизолирующей смесях должно быть не более 0,5%. Не реже одного раза в неделю в ЦЗЛ проводится определение влажности смеси, для чего отбирается проба объемом не менее 0,5 л. Контроль, отбор проб и доставка их в ЦЗЛ осуществляется ОТК. Шлакообразующие смеси с истекшим сроком хранения и содержанием влаги более 0,5% используют только в промежуточном ковше.
Перед окончанием обработки плавки на АКП на МНЛЗ выполняют следующие операции:
— проверяют готовность электросхем, гидросистем, аварийных систем;
— проверяют давление воды, сжатого воздуха, природного газа и кислорода, аргона;
— проверяют расходы воды на охлаждение кристаллизатора, узлов и механизмов МНЛЗ;
— проверить исправность работы пароотсоса;
— устанавливают рецепт разливки согласно заданной марки стали и заданного сечения.
По команде старшего разливщика устанавливают сталеразливочный ковш с металлом на поворотный стенд МНЛЗ и убедившись в правильной установке ковша на стенде, освобождают его от грузозахватного устройства и производят подсоединение гидравлического цилиндра на шиберный затвор. Затем сталеразливочный ковш перемещают в положение разливки. После установки стальковша в позицию разливки отключают горелки стенда разогрева промковша, снимают малую крышку и промковш вместе с погружным стаканом перемещают в положение разливки. Погружной стакан центрируют относительно кристаллизатора с помощью механизма юстировки установленного на тележке промковша. Допустимое отклонение относительно центра кристаллизатора не более 2 мм (оценка — визуально). Производят центровку шиберного затвора сталеразливочного ковша относительно приемного устройства промежуточного ковша. После капитального ремонта МНЛЗ в первой серии разливают сталь марки Ст3сп.
ь Начало разливки Разливку стали начинают по команде мастера или старшего разливщика, для чего открывают шиберный затвор и приступают к заполнению металлом промежуточного ковша с максимальной скоростью. После появления металла, оператор главного пульта объявляет по внутренней связи: «Металл в промежуточном ковше». После наполнения промежуточного ковша ~10 т разливщик стали производит проверку работоспособности шиберного затвора сталеразливочного ковша на открытие и закрытие. После этого на зеркало металла присаживают ТИС марок GLUTIN MH-B, GLUTIN RS-10 в соотношении 1:1 c расходом 0,5−0,6 кг/т. После наполнения промежуточного ковша до 15−20 т опускают сталь-ковш до погружения защитной трубы в металл. Доводят уровень металла до рабочего 18−25 т и поддерживают его в течение всей разливки. Дальнейшую подачу ТИС производить по мере необходимости, не допуская оголения зеркала металла.
Минимально-допустимый уровень металла в промковше при смене сталеразливочного ковша — 10 т. При снижении уровня металла в промковше менее 10 т разливку прекращают. В стык соединения огнеупорной трубы с коллектором шиберного затвора подают аргон через специальное устройство, которым оборудована защитная труба. Расход аргона при этом должен находиться в пределах 30−50 Нл/мин при давлении 2−6 бар. В случае не поступления металла в промежуточный ковш выполнить следующие операции: 2 раза закрыть / открыть шиберный затвор.
По громкой связи оператор главного пульта МНЛЗ производит отсчет времени с начала наполнения кристаллизатора через каждые 30 секунд. При достижении уровня металла в кристаллизаторе выше выходных отверстий погружного стакана, проверяют работу стопора промковша. Затем в кристаллизатор подают ШОС (шлакообразующую смесь) равномерно по всему зеркалу металла.
Кристаллизатор считается наполненным, если уровень металла находится в пределах от 80 до 100 мм от верхнего среза медных плит кристаллизатора. Стакан должен быть погружен в металл на глубину 100−140 мм до верхнего среза его выходных отверстий (оценка визуальная). При наполнении кристаллизатора металлом до уровня от 100 до 150 мм от его верхней кромки старший разливщик на рабочей площадке МНЛЗ включает: качание кристаллизатора; через 5−10 секунд привод вытягивания сляба на скорости 0,20 м/мин; режим автоматического регулирования уровня металла в кристаллизаторе.
Набор скорости производить по 0,02−0,04 м/мин через каждые 10 секунд до скорости 0,40 м/мин. Разливку на скорости 0,40 м/мин производить в течение 1 мин. Дальнейший набор скорости до 0,60 м/мин производить по 0,0,4−0,06 м/мин через каждые 10 секунд. После достижения скорости 0,60 м/мин производят замер температуры металла в промежуточном ковше, в зависимости от которой при необходимости плавно корректировать скорость разливки. При выходе на рабочую скорость разливки старший разливщик дает команду оператору главного пульта управления МНЛЗ на включение автоматического режима системы прогнозирования прорыва «ERGOLINE». Любые изменения скорости разливки выполняют при отключенном автоматическом режиме, т. е. в ручном.
Измерение температуры жидкой стали, в промежуточном ковше на МНЛЗ осуществляет разливщик стали, с помощью термопар марок TC 360 312, CE 36 011 290 или ПТПР-91−900. Первый замер температуры металла производят после достижения скорости разливки 0,60 м/мин. Второй и последующие замеры температуры производят через каждые 20 т разлитой стали. Результаты замеров регистрируют в паспорте разливки. В зависимости от результата замера, марки разливаемой стали и сечения сляба, устанавливают рабочую скорость разливки.
При разливке первой плавки в серии и при смене промежуточных ковшей, температуру металла в сталеразливочном ковше после внепечной обработки допускается увеличить на 5−10 °С выше верхнего предела. Разница показаний температур воды на выходе и на входе в кристаллизатор (DT) по широким и узким стенкам должна быть 6−7,5 °С. При увеличении DT более 7,5 °С по команде оператора МНЛЗ энергетик должен увеличить расход воды на стенки кристаллизатора до достижения значения рабочего уровня DT. При увеличении DT более 12 °C разливку прекратить. При разливке металла по мере расходования ШОС в кристаллизаторе ее новые порции равномерно рассыпают по поверхности металла до получения темного цвета засыпки. Расход смеси согласно плановым нормам расхода.
Бурление в кристаллизаторе и оголение зеркала металла не допускается. Периодически около стенок кристаллизатора проверяют наличие гарнисажа, отсутствие твердых шлакометаллических образований на мениске металла. Грубые шлаковые корки, твердые шлакообразования при этом удаляют.
Разливщик стали немедленно закрывает шибер, как только визуально определит начало появления шлака из сталеразливочного ковша, при помощи манипулятора снимает защитную трубу. При замене сталеразливочного ковша разливщик стали очищает кислородом внутренний канал защитной трубы, проверяет ее целостность. Поворотный стенд разворачивают на 180о, отсоединяют гидроцилиндр шиберного устройства, с помощью крана снимают ковш с поворотного стенда и передают в разливочный пролет мартеновского цеха для кантовки оставшегося шлака.
ь Отделение затравки После выхода головки затравки из последней пары роликов горизонтального участка оператор ПУ-2 контролирует ее отделение в автоматическом режиме и поперечную транспортировку в позицию ожидания. Затем в позиции ожидания при необходимости выполняют замену головки затравки и техническое обслуживание.
ь Окончание разливки и резка металла на слябы Окончание разливки производят только на мерной длине сляба, с учетом обрезки хвостовой части сляба длиной 0,70 м. Во время слива последних порций металла промежуточный ковш приподнимают так, чтобы отверстия погружного стакана открылись на треть. Удаляют полностью шлак из кристаллизатора. При достижении мерной длины с учетом хвостовой обрези стопор немедленно закрывают и поднимают промежуточный ковш, нажимают кнопку «окончание разливки» при этом скорость автоматически увеличивается до 0,28 м/мин, до момента вывода сляба из кристаллизатора. После нажатия кнопки «окончание разливки» автоматически включается программа «ОПТИМИЗАЦИЯ РЕЗКИ», на ПУ МГР-1 с целью минимизации обрезки автоматически производится расчет оптимальной порезки и на мониторе выдаются варианты порезки. Оператор МГР-1 должен выбрать наиболее оптимальный вариант порезки и начать процесс. С целью исключения ошибки программы «ОПТИМИЗАЦИЯ РЕЗКИ» оператор МГР-1 отрезку последнего сляба должен производить в ручном режиме.
Разливка на МНЛЗ стали марки 35 Г Таблица 10 — Температурно-скоростные режимы разливки стали марки 35Г
Параметры разливки металла | |||||
Марка стали | 35Г | ||||
Сечение сляба, мм | 240×1300 | ||||
Рабочий интервал температур в п/к, оС | 1524−1540 | ||||
Температура металла в с/к, оС | 1560−1575 | ||||
Температура металла в п/к, оС | и ниже | 1525−1534 | 1535−1540 | 1541 и выше | |
Скорость разливки, м/мин* | 0,85 | 0,84−0,71 | 0,70−0,60 | не более 0,60 | |
Примечание: * С увеличением температуры металла в промковше скорость разливки уменьшать. | |||||
Таблица 11 — Распределение расхода воды по зонам ЗВО
Зоны | Распределение по зонам, % | |
Узкие грани (подбой) | 3,4 | |
Широкие грани (подбой) | 9,4 | |
Бендер, верх | 17,7 | |
Бендер, низ | ||
Сегмент № 1 малый радиус | 4,1 | |
Сегмент № 1 большой радиус | 4,5 | |
Сегмент № 2, 3 малый радиус | 5,5 | |
Сегмент № 2, 3 большой радиус | 6,4 | |
Сегмент № 4, 5 малый радиус | ||
Сегмент № 4, 5 большой радиус | 4,6 | |
Сегмент № 6, 7 малый радиус | 2,8 | |
Сегмент № 6, 7 большой радиус | 3,2 | |
Сегмент № 8,9,10 малый радиус | 8,5 | |
Сегмент № 8,9,10 большой радиус | 12,9 | |
ь Контроль химического состава и температуры металла в ДСП Отбор проб металла производят пробоотборниками марок SAE 1200/900, SAE 1200/900 P6 или ПМ-39, ПН-10−900. Замер температуры металла выполняют разовыми термопарами марок TC 360 312, CE 36 011 290 или ПТПР-91−900. Первый замер температуры производят после полного расплавления металлошихты. Последний замер температуры производят не ранее чем за 3 мин до выпуска. Промежуточный контроль температуры металла рекомендуется проводить через 10−15 мин работы под током (в зависимости ступени нагрева), через 1−2 мин после подъема электродов.
При отборе проб и замере температуры в ручном режиме:
— отбор проб стали и замер температуры вручную производят через 1−2 мин после разрыва электрической дуги;
— пробоотборник и термопреобразователь погружают в расплав стали на глубину 2/3 длины пробоотборника;
— время отбора проб — от 5 до 8 сек, время замера температуры — 5 сек;
— пробу охлаждают сжатым воздухом до потемнения, затем в воде до температуры, достаточной для последующего высыхания пробы.
Последнюю пробу отбирают не ранее, чем за 10 мин до выпуска плавки. При необходимости вместе с последней пробой отбирают стержневую пробу для определения газов. Проба металла не должна содержать шлак. В случае появления на пробе шлаковых включений, трещин и других дефектов — пробу бракуют и отбирают новую. Перед взятием пробы металла и шлака из печи прекращается подача кислорода, углеродсодержащего материала и шлакообразующих материалов.
Пробы металла на химический анализ после отбора и охлаждения подручный или сталевар передает по пневмопочте в лабораторию экспресс-анализа и сообщает лаборанту № плавки и № пробы.
1.3.5 Контроль качества продукции В процессе обработки металла на АКП фиксируются и заносятся в плавильный журнал и паспорт плавки следующие параметры:
— дата, номер плавки, заданная марка стали;
— номер сталеразливочного ковша и стойкость его футеровки (количество плавок);
— высота свободного борта
— количество минут продувки пробки (на предыдущих плавках)
— количество минут продувки аргоном через донную пробку на данной плавке
— суммарное количество минут продувки на пробке (на предыдущих плавках плюс на данной плавке, по окончании обработки металла на АКП)
— давление аргона на пробку при обработке металла на АКП
— начало, окончание и общая продолжительность обработки (час: мин);
— вес ковша со сталью т;
— вес жидкой стали, т;
— температура металла по ходу обработки, оС;
— расход аргона, за обработку (м3);
— вид и количество присаживаемых материалов;
— количество теплоизолирующей смеси;
— химический состав металла по ходу обработки;
— расход электроэнергии, кВт час/т;
— фамилия, имя, отчество мастера смены и сталевара.
2. РАСЧЕТНАЯ ЧАСТЬ
2.1 Технологические параметры выплавки Рассмотрим технологию выплавки стали 35ГС в дуговой печи с последующей обработкой в ковше-печи в электросталеплавильном цехе № 2 на ОАО «АМЗ». Доводка стали в ковше-печи освобождает от необходимости жестко контролировать содержание серы в металле по ходу плавки в ДСП.
Исходными данными требования к данной марке стали. Состав стали 35ГС согласно ТИ 123-ЭС-01−2011 приведен в таблице 12.
Таблица 12 — Химический состав стали марки 35ГС, масс. %
Химический элемент | C | Si | Mn | S | P | Cr | Ni | Cu | |
? 0,37 | ? 0,9 | ? 1,2 | ? 0,070 | ? 0,020 | ? 0,30 | ? 0,30 | ? 0,30 | ||
ь Шихтовка плавки Изначально ДСП загружают при помощи скраповой бадьи, оборудованной зажимом на дне, используя основной и вспомогательный крюки загрузочного крана. Печь и скраповая бадья предназначены для выполнения загрузки за счет двух или трех бадей даже при завалке легковесного лома (плотностью менее 0,7 т/м3).Вес лома в бадье должен составлять не более 50 т, объемом не более Ѕ бадьи.
Загрузка не должна превышать 90% объема печи во избежание проблем с закрытием свода. Последовательность загрузки лома в бадью — исключительно важна (особенно, первая загрузка или первоначальная загрузка при условии использования Consteel).
При погрузке лома на конвейер должны быть учтены следующие моменты:
Лом должен быть разложен равномерно, его высота должна составлять приблизительно 650 мм, что на 150 мм ниже высоты загрузочного конвейера. Если используются чугун и брикетированное железо, для получения равномерной загрузки они должны быть разложены на загрузочном конвейере тем же самым образом. При этом загрузка чугуна и брикетированного железа в ДСП должна быть закончена за 15 минут до выпуска для того, чтобы предотвратить любые задержки, вызванные высоким содержанием углерода.
Из-за высокой плотности чугуна и брикетированного железа (ГБЖ), при использовании этих материалов загрузка конвейера соответственно увеличивается. Программа АСУ ТП ДСП уменьшит скорость конвейера для того, чтобы соответствовать интенсивности подачи в рамках заданной системы продолжительности загрузки.
Загружаемые на конвейер Consteel чугун и брикетированное железо, дойдут до печи приблизительно через 10 минут. Более крупные, тяжёлые куски скрапа могут поглотить больше тепла во время транспортировки через устройство предварительного подогрева, следовательно, по возможности, они должны быть размещены на верхнем слое.
В зимнее время во избежание примерзания компонентов металлошихты к конвейеру Consteel и блокирования его движения, запрещается оставлять металлошихту на конвейере на длительный период времени (более 1 часа). Перед остановкой печи на ремонт, загрузку шихты вести таким образом, чтобы после завалки плавки перед ремонтом конвейер остался пустым. В случае аварийных остановок печи на длительный срок (более 1 часа) загруженную шихту снять с открытого участка конвейера на участок складирования металлошихты.
При завалке через конвейер тяжеловесного лома для исключения поломки электродов обязательно производить заблаговременно отключение печи и подъем электродов. Отключение производить через промежуток времени с момента захода тяжелого (объемного) лома в горячую зону конвейера (под прижимной ролик) до подхода лома к печи. Данное время определяется скоростью конвейера Consteel.
Скорость конвейера, % 100 95 90 85 80 75 70 65 60
Время до печи, мин 5,8 6,1 6,5 6,8 7,3 7,8 8,3 9,0 9,7
Завалка печи бадьей.
Дно бадьи должно быть наполнено слоем легковесного лома без воды или масла; дробленный очищенный лом может использоваться вплоть до 10% от общего объема завалки. Данный слой действует в виде подушки для обеспечения защиты огнеупорного пода печи от возможных повреждений из-за тяжеловесных кусков скрапа. А также является неким уплотнением, предотвращающим потери через дно бадьи мелкого лома.
Следующий слой должен содержать самые тяжелые (большие) куски лома вплоть до 15% от загрузки бадьи во избежание поломки электродов при падении лома во время плавления.
Следующий слой лома должен составлять основной объем веса шихты. Это слой лома среднего веса для защиты футеровки и водоохлаждаемых панелей от теплоизлучения дуги.
Последний слой — это легковесный лом малого размера, необходимый для облегчения зажигания и выравнивания дуги.
Максимальный размер лома для загрузки бадьи не более 1000Ч500Ч500 мм с массой не более 1000 кг.
Расчет ведем на 100 кг металлошихты. Среднее содержание хрома в шихте для большинства выплавляемых марок стали не должно превышать 1%. В противном случае образующиеся соединения оксидов хрома сильно понижают жидкотекучесть шлака, что затруднит ведение плавки.
В качестве шихты используем собственные отходы стали марки Ст3сп, образовавшиеся в ходе обработки сляб в ЛПЦ — 1, а также отходы стали марки 65 Г. Исходя из этого, зададим в шихту 70 кг отходов стали Ст3сп и 30 кг отходов стали 65 Г. Данные о фактическом химическом составе используемых материалов приведены в табл. 13 и 14.
Таблица 13 — Химический состав металлической части шихты, масс. %
Материал | C | Si | Mn | Cr | P | S | Fe | |
Ст3сп | 0,20 | 0,20 | 0,50 | 0,20 | 0,04 | 0,03 | 98,83 | |
65Г | 0,67 | 0,25 | 0,95 | 0,20 | 0,02 | 0,02 | 97,89 | |
Таблица 14 — Химический состав шлакообразующих и огнеупорных материалов, %
Материал | CaO | SiO2 | MgO | Cr2O3 | Al2O3 | Fe2O3 | CaF2 | P | S | п.п.п. | |
Плавиковый шпат | 0,5 | 3,6 | _ | _ | 0,2 | 1,2 | 94,0 | ; | ; | 0,2 | |
Известь | 78,0 | 9,3 | 2,0 | ; | 0,8 | 1,2 | ; | ; | ; | 8,7 | |
Периклазо-углерод | ; | 0,2 | 86,0 — 95,0 | ; | 0,5 | 0,2 | ; | Углерод 6,0 — 15,0 | ; | ||
С учетом массы компонентов и их химического состава определим массу элементов, вносимых каждым компонентом шихты, и представим результаты также в виде табл. 15.
Таблица 15 — Масса элементов, вносимых шихтовыми материалами, кг
Компонент шихты | C | Si | Mn | Cr | P | S | Fe | Всего | |
Отходы Ст3сп | 0,140 | 0,140 | 0,350 | 0,140 | 0,028 | 0,021 | 69,181 | 70,00 | |
Отходы 65Г | 0,201 | 0,075 | 0,285 | 0,060 | 0,006 | 0,006 | 29,367 | 30,00 | |
Всего | 0,341 | 0,215 | 0,635 | 0,200 | 0,034 | 0,027 | 98,548 | 100,00 | |
Кроме металлической части шихты, в завалку сверху добавляют известь. Для наведения шлака в завалку на 1 т металлошихты обычно дают 15…30 кг извести.
ь Плавка в дуговой сталеплавильной печи ь Период плавления В период плавления происходит расплавление металлошихты, сопровождающееся окислением химических элементов, которые в виде оксидов переходят в шлак. Помимо продуктов окисления шлак периода плавления образуется из вносимой в завалку извести и материала футеровки печи, попадающего в шлак в результате разрушения футерованной части печи.
Продукты окисления компонентов металлического расплава вносят в шлак следующее количество оксидов.
Кремний. К окончанию периода весь кремний окисляется до SiO2. Количество окислившегося кремния 0,215 · 1 = 0,215 кг. На окисление этого количества кремния потребуется 0,215 · 32/28 = 0,246 кг кислорода. При этом в шлак будет внесено 0,215 · 60/28 = 0,461 кг SiO2.
Марганец. В период плавления до MnO окислится 35% от вносимого шихтой марганца, т. е. 0,635 · 0,35 = 0,222 кг. На его окисление потребуется 0,222 · 16/55= = 0,065 кг кислорода. При этом в шлак будет внесено 0,222 · 71/55 = 0,286 кг MnO.
Хром. При современной технологии плавки хром окисляется незначительно. Учитывая относительно невысокое содержание хрома в шихте, в период плавления до Cr2O3 окислится около 5% от вносимого шихтой хрома, т. е. 0,200· 0,05 = 0,010 кг. На его окисление потребуется 0,010 · 48/104 = 0,005 кг кислорода. При этом в шлак будет внесено 0,010 · 152/104 = 0,015 кг Cr2O3.
Железо. В период плавления окислится 0,4% от вносимого шихтой железа, т. е. 98,548 · 0,004 = 0,394 кг. Из них половина окислившегося железа уносится с пылью в виде Fe2O3. На окисление этого количества железа потребуется 0,394· 0,5·48/112 = 0,084 кг кислорода. При этом образуется 0,394 · 0,5 · 112/160 = = 0,138 кг Fe2O3. В шлак будет внесено 0,394 · 0,5 · 72/56 = 0,253 кг FeO. На его образование требуется 0,394 · 0,5 · 16/56 = 0,056 кг кислорода.
Фосфор. В период плавления в шлак из металла переходит 30% фосфора в виде P2O5. Окислится 0,034 · 0,3 = 0,010 кг фосфора, на что потребуется 0,010 · 80/62 = = 0,013 кислорода. При этом в шлак будет внесено 0,010 · 142/62 = 0,023 кг P2O5.
В период плавления углерод не окисляется, сера из металла не удаляется.
Учтем, что в завалку вместе с металлошихтой вводили известь в количестве около 2% от массы завалки или 2 кг на 100 кг шихты. С учетом получения необходимой основности скорректируем это значение до 1,5 кг. С известью вносится в шлак, кг:
CaO: 0,780 · 1,5 = 1,170 кг;
MgO: 0,020 · 1,5 = 0,030 кг;
SiO2: 0,093 · 1,5 = 0,140 кг;
Al2O3: 0,008 · 1,5 = 0,012 кг;
Fe2O3: 0,012 · 1,5 = 0,018 кг или в пересчете на FeO 0,018 · 112/160 · 72/56 = 0,016.
Вследствие потерь при прокаливании из извести удалится в атмосферу 0,087· 1,5= 0,131 кг CO2.
Во время работы печи происходит износ футерованной части подины и свода, продукты износа в виде соответствующих оксидов переходят в шлак. Печь имеет периклазоуглеродистую набивную подину, водоохлаждаемые стены и свод, расход периклазоуглеродистых огнеупоров около 3 кг/т (или 0,3 кг на 100 кг металлошихты.
По результатам выполненных расчетов определяем состав и количество шлака в конце периода плавления (таб. 16). Отдельно составляем баланс металла за этот период (таб. 17).
Таблица 16 — Количество и состав печного шлака периода плавления
Источник | SiO2 | CaO | MnO | FeO | Cr2O3 | Al2O3 | MgO | P2O5 | У | |
Известь | 0,140 | 1,170 | ; | 0,016 | ; | 0,012 | 0,030 | ; | 1,368 | |
Футеровка | 0,004 | ; | ; | ; | ; | ; | 0,276 | ; | 0,280 | |
Продукты окисления | 0,461 | ; | 0,286 | 0,253 | 0,015 | ; | ; | 0,023 | 1,038 | |
Всего, кг | 0,605 | 1,170 | 0,286 | 0,269 | 0,015 | 0,012 | 0,306 | 0,023 | 2,686 | |
Всего, % | 22,524 | 43,560 | 10,648 | 10,015 | 0,558 | 0,447 | 11,392 | 0,856 | ||
При составлении баланса металла учтем, что в процессе плавки происходит науглероживание металла в результате износа графитированных электродов. Расход электродов на плавку в современных печах составляет 1,7…2,5 кг/т стали. В ДСП на ОАО «АМЗ» расход электродов 2 кг/т или 0,2 кг на 100 кг шихты и усвоение углерода ванной 75%. С учетом того, что продолжительность периода плавления составляет 2/3 общего времени плавки, в металл дополнительно перейдет 0,2 · 0,75 · 2/3 = 0,100 кг углерода и выделится 0,2 · 0,25 · 28/12 · 2/3 = = 0,078 кг СО. На это потребуется 0,2 · 0,25 · 2/3 · 16/12 = 0,044 кг О2.
Таблица 17 — Баланс составляющих металла за период плавления
Элемент | Поступило с шихтой | Перешло в шлак | Содержится в металле | ||
кг | % | ||||
C | 0,341 | ; | 0,441 | 0,445 | |
Si | 0,215 | 0,215 | ; | ; | |
Mn | 0,635 | 0,222 | 0,413 | 0,416 | |
Cr | 0,200 | 0,010 | 0,190 | 0,191 | |
S | 0,027 | ; | 0,027 | 0,027 | |
P | 0,034 | 0,010 | 0,024 | 0,024 | |
Fe | 98,548 | 0,197 | 98,154* | 98,897 | |
У | 100,000 | 0,654 | 99,249 | ||
*С учетом потерь с пылью.
Основность полученного шлака, выраженная через отношение % CaO / % SiO2= = 1,93. Это удовлетворяет требованиям к шлаку в период плавления.
ь Период окисления Сразу после окисления жидкого шлака его начинают вспенивать, и по мере наполнения ванны печи жидким металлом часть шлака через рабочее окно самотеком покидает рабочее пространство печи. С ним удаляется значительная часть фосфора. Потери шлака в течение всей плавки компенсируют небольшими присадками извести, поддерживая необходимый уровень шлака и его основность.
Задачами окислительного периода являются:
— окисление углерода и фосфора в металле до их требуемого содержания в готовом полупродукте и частично удаление серы;
— нагрев металла до необходимой температуры.
Окисление металла проводят продувкой техническим кислородом с чистотой не менее 99,5%. В случае затруднений с удалением фосфора в ванну печи можно присадить железную руду. В нашем случае для получения не более 0,12…0,20% фосфора в металле достаточно поддерживать в этот период основность не ниже 2,7…3,0 при содержании FeO в шлаке около 12…15%.
Для интенсификации массои теплопереноса в сталеплавильной ванне, способствующей нормальному развитию в ней физических и физико-химических процессов, в это время необходимо обеспечить возможность окисления не менее 0,3…0,5% углерода.
Обезуглероживание и окисление примесей. С учетом того, что углеродистые ферросплавы значительно дешевле, чем низкоуглеродистые, используем в дальнейшем для легирования углеродистые ферросплавы. Поэтому с учетом количества вводимых ферросплавов необходимо в конце периода иметь содержание углерода в металле на нижнем пределе по марке или несколько ниже. Примем, что содержание углерода в металле в конце окислительного периода должно составлять 0,10%.
Углерод. После окончания периода плавления в металле с учетом науглероживания электродами содержится 0,441 кг углерода. Учтем науглероживание электродами за период окисления и определим количество углерода, которое необходимо окислить.
За окислительный период при расходе электродов 2 кг/т в металл с учетом 75% усвоения попадает дополнительно 0,2 · 0,75 · 1/3 = 0,050 кг. углерода. Всего требуется окислить углерода
(0,441 + 0,050) — 0,10 = 0,391 кг.
Примем, что весь углерод окисляется до СО. Тогда для окисления 0,481 кг углерода потребуется 0,391 · 16/12 = 0,641 кг О2 и образуется 0,391 · 28/12 = 1,122 кг СО.
Марганец. В окислительный период окислится примерно 45% оставшегося в металле марганца: 0,413 · 0,45 = 0,186 кг. На его окисление необходимо 0,186· 16/55 = 0,054 кг О2. При этом образуется 0,186 · 71/55 = 0,240 кг MnO.
Хром. С учетом относительно невысокого содержания хрома в металле за этот период окислится 5% хрома, поступившего с металлом: 0,190 · 0,05 = 0,010 кг. На его окисление необходимо 0,010 · 48/104 = 0,005 кг О2 и в результате образуется 0,010 · 152/104 = 0,015 кг Cr2O3.
Железо. В окислительный период окислится около 0,4% железа из металла, 85% от этого количества переходит в шлак в виде FeO, а 15% удаляется в виде пыли Fe2O3 с отходящими газами. Всего окисляется 0,004 · 98,154 = 0,393 кг железа.
В шлак перейдет 0,393 · 0,85 = 0,334 кг железа, на его окисление израсходуется 0,334 · 16/56 = 0,095 кг О2 и образуется 0,334 · 72/56 = 0,429 кг FeO. С пылью теряется 0,393 — 0,334 = 0,059 кг железа, на его окисление до Fe2O3 требуется 0,059 · 48/112 = 0,025 кг кислорода. Образуется 0,059 · 160/112 = 0,084 кг Fe2O3.
Сера. В окислительный период из металла удаляется около 20% содержащейся в нем серы: 0,027 · 0,2 = 0,005 кг.
Фосфор. В окислительный период в шлак переходит 30% имеющегося в металле фосфора: 0,024 · 0,30 = 0,007 кг. На его окисление до P2O5 требуется 0,007· 80/62 = 0,009 кг O2 и в шлак переходит 0,007 · 142/62 = 0,016 кг P2O5.
Шлакообразование в окислительный период. К концу периода плавления в печи остается 1/3 шлака, состав которого приведен в табл. 10. После этого в печи наводится новый шлак присадками извести. Шлак окислительного периода образуется из остатков шлака предыдущего периода, извести, оксидов — продуктов окисления металла, компонентов износа футеровки. С учетом требуемой величины основности примем, что в окислительный период присаживают 0,5 кг извести. С ней в шлак попадет:
CaO: 0,780 · 0,5 = 0,390 кг;
MgO: 0,020 · 0,5 = 0,010 кг;
SiO2: 0,093 · 0,5 = 0,047 кг;
Al2O3: 0,008 · 0,5 = 0,004 кг;
Fe2O3: 0,012 · 0,5 = 0,006 кг или в пересчете на FeO 0,006 · 112/160 · 72/56 = 0,005.
Вследствие потерь при прокаливании из извести удалится в атмосферу 0,087· 0,5= 0,044 кг CO2.
Из футеровки при расходе за период 0,2 кг на 100 кг металлошихты в шлак переходит:
MgO: 0,920 · 0,2 = 0,184 кг;
SiO2: 0,012 · 0,2 = 0,002 кг.
Аналогично периоду плавления подсчитываем количество и состав шлака (см. таб. 18) и определяем баланс металла (таб. 19).
сплав печь брак шихта Таблица 18 — Количество и состав шлака в конце окислительного периода
Источник | SiO2 | CaO | MnO | FeO | Cr2O3 | Al2O3 | MgO | P2O5 | У | |
Известь | 0,047 | 0,390 | ; | 0,005 | ; | 0,004 | 0,010 | ; | 0,456 | |
Футеровка | 0,002 | ; | ; | ; | ; | ; | 0,184 | ; | 0,186 | |
Продукты окисления | ; | ; | 0,240 | 0,429 | 0,015 | ; | ; | 0,016 | 0,700 | |
Шлак периода плавления | 0,202 | 0,390 | 0,095 | 0,090 | 0,005 | 0,004 | 0,102 | 0,008 | 0,896 | |
Всего, кг | 0,251 | 0,780 | 0,335 | 0,524 | 0,020 | 0,008 | 0,296 | 0,024 | 2,238 | |
Всего, % | 11,215 | 34,853 | 14,969 | 23,414 | 0,894 | 0,357 | 13,226 | 1,072 | ||
Примечание. Основность % CaO / % SiO2 = 3,1. Это удовлетворяет требованиям ведения плавки.
Таблица 19 — Баланс составляющих металла за окислительный период
Элемент | Поступило в период плавления | Перешло в шлак | Содержится в металле | ||
кг | % | ||||
C | 0,391 | ; | 0,10 | 0,10 | |
Si | |||||
Mn | 0,413 | 0,186 | 0,227 | 0,232 | |
Cr | 0,190 | 0,010 | 0,18 | 0,183 | |
S | 0,027 | 0,005 | 0,022 | 0,022 | |
P | 0,024 | 0,007 | 0,017 | 0,017 | |
Fe | 98,154 | 0,334 | 97,761* | 99,536 | |
У | 99,249 | 0,542 | 98,217 | ||
*С учетом потерь с пылью.
Химический состав полупродукта удовлетворяет условиям ТИ 123-ЭС-01−2011.
2.2 Энергоемкость оборудования Диаметр электрода:
dЭ= (1)
где: dЭ — диаметр электрода, мм;
I — максимальный ток, А;
i — допустимая плотность тока, А/см2
Для современных графитированных электродов i=30−35 А/см2
Принимаю I=30 кА
dЭ= =0,6 м Выбираю стандартный электрод dЭ=610 мм.
Диаметра распада электрода выбирается с учетом необходимости быть достаточным для размещения электрододержателей без замыкания при перемещении электродов и при условии необходимой прочности центральной части свода. Он равен:
dР=(2,5−3,5)
dР=3610=1830 мм
2.3 Материальный баланс Продувку кислородом прекращают, когда содержание углерода в металле достигнет заданного.
После выполнения всех расчетов составляем итоговый материальный баланс плавки, в который заносим все вводимые в печь материалы и все получаемые при этом продукты. Количество материалов суммируем за всю плавку. Поскольку точно определить долю кислорода из атмосферы, пошедшую на окисление элементов нельзя, то считается, что получено значение расхода кислорода суммарное. Реальный расход кислорода несколько меньше (таб. 20).
Таблица 20 — Материальный баланс плавки
Поступило | Получено | |||
Материал | Количество, кг | Продукт | Количество, кг | |
Отходы Ст3сп | Сталь | 97,761 | ||
Отходы стали 65Г | Шлак | 4,924 | ||
Известь | 2,0 | СО | 1,935 | |
Из футеровки | 0,5 | СО2 | 0,175 | |
Из электродов | 0,2 | Пыль | 0,256 | |
Кислород на плавку | 1,342 | Невязка | — 1,009 | |
Итого | 104,042 | Итого | 105,051 | |
Невязка составляет 1,009 кг или 0,97%.
2.4 Тепловой расчет печи ь Приход тепла Тепло, вносимое электрической энергией, Q1
На ОАО «АМЗ» расход электрической энергии фиксируется приборами учета электроэнергии. Важным параметром, характеризующим использование электроэнергии, является коэффициент полезного действия, учитывающий потери энергии при подводе ее к рабочему пространству печи на ДСП — 120 в ЭСПЦ — 2 з = 90%. Расход электроэнергии, с учетом подогрева лома и наличия газокислородных горелок и времени их работы, равен 350 кВт· ч/т. Для пересчета кВт· ч в МДж используется переводной коэффициент 3,6 (1 Вт/ч = 3600 Дж/ч).
Расчет проведем на 100 кг шихты. Зададимся расходом электрической энергии, равным 350 кВт· ч/т стали, или 35 кВт· ч на 100 кг. Тогда с учетом электрического КПД з = 0,9
Q1 = 35 · 3,6 · 0,9 = 113,40 МДж.
Тепло, вносимое газокислородными горелками, Q2
Вносимое горелками тепло определяется по формуле:
Qгор = Nгор · ф · Ргор · 3,6, (2)
где Nгор — число горелок на печи, шт.;
ф — время работы горелки, ч;
Ргор — мощность горелки, кВт;
3,6 — переводной коэффициент кВт· ч в МДж.
ДСП на «АМЗ» оборудована 4 газокислородными горелками по 3,3 МВт каждая. Продолжительность их работы за плавку 10 минут (0,17 часа).
Qгор = 4 · 0,17 · 3,3 · 103 · 3,6 = 8078,4 МДж.
С учетом емкости печи количество тепла, внесенного горелками, приведенное к 100 кг металлошихты составит: Q2 = 6,73 МДж.
Тепло, вносимое в печь шихтовыми материалами, Q3
Расчет энтальпии ведется по формуле:
ДHк = Мк · ск · Дtк, (3)
где ДHк — изменение энтальпии соответствующего компонента;
Мк — масса компонента;
ск — теплоемкость компонента;
Дtк — изменение температуры компонента.
Энтальпия лома, заваливаемого в печь, подогретого до 400 оС состави:
Hл = 100 · 0,538 · 10- 3 · 400 = 21,52 МДж.
Энтальпией остальных компонентов пренебрегаем, т. к. их подается очень мало.
Итого энтальпия шихты составит:
Q3 = ДН = 21,52 МДж.
Тепло, вносимое при протекании экзотермических реакций, Q4
В процессе ведения плавки происходит окисление имеющихся в шихте компонентов (в первую очередь Si, Mn, C и Fe). Точно учесть количество тепла, выделившееся при их протекании, на практике сложно из-за неоднородности химического состава шихты. Кроме того, при введении в печь избытка кислорода происходит избыточное окисление железа, а при введении малого количества кислорода часть углерода может не окислится.
Q4 = MSiqSi + MMnqMn + MCqC + MFeqFe + MCrqCr, (4)
где Mi — масса соответствующего элемента, окислившегося за всю плавку по материальному балансу;
qi — тепловой эффект реакции его окисления.
В расчете условно принимаем, что все элементы окисляются по реакции:
xMe+yO = MexOy. (5)
С учетом материального баланса запишем, что окислится:
Si до SiO2: 0,215 · 28,4 = 6,11 МДж;
Mn до MnO: (0,222 + 0,186) · 6,99 = 2,85 МДж;
Cr до Cr2O3: (0,010 + 0,010) · 11 = 0,22 МДж;
Fe до FeO: (0,197 + 0,334) · 4,76 = 2,53 МДж;
Fe до Fe2O3: (0,197 + 0,059) · 7,36 = 1,88 МДж;
С до СО: (0,033 + 0,481) · 11,3 = 5,81 МДж.
Итого Q4 = 19,40 МДж.
В процессе плавки часть графита окисляется до СО, часть — до СО2, часть попадает в металл, а часть выносится в виде пыли с отходящими газам. При составлении теплового баланса принимают те же допущения, что и при составлении материального баланса (расход электродов 2 кг/т, 2/3 этого количества попадает в металл и учитывается при окислении углерода из расплава, остальное сразу окисляется до СО).
Итого за плавку приход тепла в печь:
Qп = Q1 + Q2 + Q3 + Q4, Дж, (6)
Qп = 113,40 + 6,73 + 21,52 + 19,40 = 161,05 МДж.
ь Расход тепла Тепло, идущее на нагрев, плавление и перегрев до заданной температуры металла, шлака и легирующих добавок, Q5
В процессе плавки происходит расплавление лома, шлакообразующих и легирующих элементов (если они вводятся в шихту). Количество тепла каждой составляющей определяется исходя из материального баланса по формулам:
HМ = MM · [c1 · (tпл — tо) +qM + c2 · (tвып + tпл)], (7)
где ММ — масса компонента данного вида, вносимого в печь за плавку;
с1 — средняя теплоемкость этого материала в интервале температуры от загрузки до плавления;
с2 — средняя температура металла в интервале температуры от плавления до выпуска;
to — температура скрапа при завалке;
tпл — температура плавления стали;
tвып — температура стали на выпуске;
qМ — теплота плавления металла.
Теплоемкость компонентов определяется по справочным данным. Средняя теплоемкость определяется следующим образом. Так как лом подогревали до 400 оС, то берется средняя теплоемкость материала в диапазоне от 400 оС до температуры плавления.
Для стали рядовых марок можно принять qМ = 284 кДж/кг, qшл = 58 кДж/кг, сжидк.ст = 0,79 кДж/град, сшл = 1,05 кДж/кг. Температура плавления углеродистой стали 1350 оС, образующего шлака — 1550 оС.
Средняя теплоемкость для стали 3сп:
c1 = (0,536 + 0,670)/2 = 0,603 кДж/град, тогда НСт3сп = 70 · [0,603 · (1350 — 400) + 284 + 0,79 · (1630 — 1350)] = 75,46 МДж.
Для стали 65 Г с1 = (0,683 + 0,540)/2 = 0,612 кДж/град, тогда Н65Г = 30 · [0,612 · (1350 — 400) + 284 + 0,79 · (1630 — 1350)] = 30,23 МДж.
Для сталеплавильного шлака можно принять сумму энтальпий нагрева и плавления q = 1890 кДж/кг и записать уравнение:
Ншл = 4,92 · [1890 + 1,05 · (1630 — 1550)] = 9,71 МДж.
Итого: Q5 = 75,46 + 30,23 + 9,71 = 115,4 МДж.
Тепло идущее на протекание эндотермических реакций, Q6
Данная статья определяется по материальному балансу плавки и включает в себя потери тепла на разложение карбонатов извести.
Согласно материальному балансу, при прокаливании недообоженной извести выделяется 0,131 кг (в период плавления) + 0,044 кг (в окислительный период) = = 0,175 кг СО2. При нормальных условиях это количество газа займет 22,4· 10- 3· 175/44 = 89,09 · 10- 3 м3. На это потребуется 89,09 · 10- 3 · 7,21 = 0,64 МДж.
Итого: Q6 = 0,64 МДж.
ь Потери тепла через футеровку, Q7
Для удобства расчета всю печь делят на 3 основные элемента — подину, стены и свод. В печи в ЭСПЦ — 2 на ОАО «АМЗ» футерована только подина, а стены и свод, кроме центральной керамической части, представляют собой конструкции из сборных водоохлаждаемых панелей, расчет потерь тепла в которых приведен отдельно.
В условиях постоянно действующего металлургического производства можно считать, что печь работает в стационарных условиях и аккумуляции тепла футеровкой не происходит, т. к. ее температура изменяется незначительно. Можно считать, что все тепло, подводимое к футеровке внутри печи, передается теплопроводностью к ее наружной поверхности. Поэтому достаточно рассчитать количества тепла, передаваемого теплопроводностью через какой-либо слой футеровки, или рассчитать теплоотдачу с внешней поверхности (кожуха печи).
Тепло, переданное теплопроводностью через слой футеровки Qсл, можно определить по уравнению
Qсл = л · (t1 — t2) · F · ф/д, (8)
где л — коэффициент теплопроводности материала слоя, Дж/(м· ч·К);
t1, t2 — температура на внутренней и внешней поверхностях слоя, К;
F — площадь поверхности теплообмена, м2;
ф — время, ч;
д — толщина слоя, м.
Тепло, отдаваемое поверхностью кожуха Qкож, можно определить по уравнению
Qкож = б · (tк — tв) · F · ф, (9)
где б — суммарный коэффициент теплоотдачи излучением и конвекцией, Дж/(м· ч·К);
tк — температура на внешней поверхности кожуха, К;
tв — температура окружающего воздуха, К.
На действующей печи известны степень черноты кирпичной кладки и кожуха, значения температуры tк геометрия печи. Для ДСП температура внутренней поверхности кладки tвн для подины принимается равной температуре жидкого металла в ванне. Средняя температура воздуха принимается равной 20 оС. При этом значение б зависит от другой неизвестной — температуры кожуха tк. Значение же tк в свою очередь зависит от температуры подины печи, толщины и теплопроводности материала кладки. На теплопроводность материала влияет средняя температура футеровки. Поэтому Q7 рассчитывают методом последовательных приближений. Для этого в первую очередь задаются температурой кожуха tк. Так как есть дополнительный слой теплоизоляции tк равно 100 оС.
Затем определяем среднюю температуру футеровки:
tср = (tвн — tк)/2. (10)
По справочной литературе для данной tср находим коэффициент теплопроводности материала л по рис. 6 определяем значение б, соответствующее данной температуре кожуха. Далее вычисляем значение теплового потока q7 =Q7/F и сравниваем его величину с приведенным на том же рисунке qокр.
Определяем среднюю температуру футеровки, зная, что в среднем за плавку температура металла составит 1500 оС, продолжительность плавки — 45 минут, диаметр кожуха ~ 6,85 м2:
tср = (1500 — 100) = 700 оС.
Рисунок 3 — Зависимость коэффициента суммарной теплоотдачи б и удельного теплового потока, теряемого поверхностью печи в окружающую среду при tв: 10оС — 1; 20оС — 2; 30оС — 3
Согласно справочным данным коэффициент теплопроводности магнезиальной футеровки при:
700 оС л = 6,28 — 0,0027 · 700 = 4,39 Вт/(м2 · оС).
По рис. 3 находим б :
б= 0,059 МДж/м2· ч.
Тогда:
Qкож = 0,059 · (100 — 20) · 6,85 · 0,75 = 24,25 МДж.
Проверяем:
q = 24,25/6,85 = 3,54 МДж/(м2 · ч).
Согласно рис. 3 qокр ~ 3,85 МДж/(м2 · ч). Разница не превышает 10%, расчет считается законченным и окончательно принимаем Qкож = 24,25 МДж. С учетом того, что расчет выполняется на 100 кг, Q7 = 0,02 МДж.
ь Потери тепла через водоохлаждаемые панели Q8
Потери тепла с охлаждающей водой можно определить, исходя из расхода воды и разницы значений температуры воды на входе в систему охлаждения и на выходе из нее. Температура и расход воды на рабочей печи измеряются непосредственно. Температура воды на входе 20 оС, на выходе температура воды 40 о С, чтобы избежать образование накипи на внутренних поверхностях панелей.
Q8 = cв · Vв · (tвых — tвх) · ф, (11)
где св — теплоемкость воды, 4,2 МДж/(м3· К);
Vв — часовой расход воды через элемент (или всю печь), м3/ч;
tвых — температура воды на выходе, оС;
tвх — температура воды на входе, оС;
ф — время, ч.
Анализ работы ДСП на ОАО «АМЗ» показал, что при соблюдении температурного режима расход воды на охлаждение стеновых панелей составляет ~ 350 м3/ч, и 95 м3/ч на охлаждение сводовых панелей.
Потери тепла на охлаждение стен составят:
Qст = 4,2 · 350 · (40 — 20) · 0,75 = 25 200 МДж на плавку (120 т) или 18,38 МДж на 100 кг.
Потери тепла на охлаждение свода составят:
Qсв = 4,2 · 95 · (40 — 20) · 0,75 = 5985 МДж на плавку (120 т) или 4,98 МДж на 100 кг.
Итого:
Q8 = 18,38 + 4,98 = 23,36 МДж.
Потери тепла излучением через открытые окна и отверстия, Q9
Во время плавки рабочее окно постоянно закрыто, поэтому потерями тепла через рабочее окно можно пренебречь, так как расчет ведется на 100 кг металлошихты.
ь Потери тепла с отходящими газами, Q10
Холодный воздух, попадая в печь через неплотности, нагревается и уносится в систему газоочистки, приводя к потерям тепла. Прежде чем попасть в газоочистку, поток горячего воздуха проходит через горячую зону конвейера Consteel и подогревает собой металлошихту. Помимо атмосферного воздуха в газоочистку уносятся газы, образующиеся при продувке расплава кислородом, а также продукты сгорания топлива при использовании дополнительных горелок.
На печи в системе газоходов имеются специальные датчики, фиксирующие температуру, состав и расход газа. Измеряя скоростной напор Дp, рассчитывают скорость и расход уходящих газов по формуле:
(12)
где щ — скорость газового потока, м/с;
g — ускорение свободного падения (9,81 м/с2);
Др — скоростной напор, Па;
сг — плотность уходящих газов, кг/м3;
V1 — количество газов, уходящих из печи (фактически), м3/ч;
F — площадь сечения патрубка, м2;
Vо — количество газов, уходящих из печи (приведенные к температуре 0 оС), м3/ч;
Тух — температура уходящих газов, К.
Количество тепла, уносимого из печи с газовым потоком, можно определить по формуле:
Q10 = Vo · cсух · Тсух · ф, (13)
где ссух — средняя теплоемкость уходящих газов, Дж/(м3· К).
В среднем на печи перепад давления между печью и атмосферой составляет 2 Па, плотность отходящих газов — 1,5 кг/м3, площадь сечения патрубка газоотсоса из печи — 6 м2, температура отходящих газов в среднем за плавку — 1200 оС. Тогда:
щ = 5,1 м/с;
V1 = 3600 · 5,11 · 4,5 = 82 782 м3/ч;
Vо = 273 · 82 782/1200 = 18 833 м3.
Тогда количество тепла, уносимое газами из печи за плавку,
Q10 = 18 833 · 1430 · 1200 · 0,75 = 24,23 · 109 Дж, или в пересчете на 100 кг 20,2 МДж.
Итого за плавку расход тепла:
Qр = 115,4 + 0,64 + 0,02 +23,36 + 0,0 + 20,2 = 159,62 МДж.
Полученный тепловой баланс плавки стали 35ГС в ДСП — 120 приведен в таблице 21. Невязка 0,9%.
Таблица 21 — Тепловой баланс плавки стали в ДСП — 120
Поступило тепла, МДж | Расход тепла, МДж | |
Электроэнергия 113,40 (70,41%) | Энтальпия продуктов 115,40 (72,30%) | |
Тепло горелок 6,73 (4,18%) | Тепло хим. реакций 0,64 (0,40%) | |
Энтальпия шихты21,52 (13,36%) | Потери с охлаждающей водой (23,36)(14,64%) | |
Тепло химических реакций 19,40 (12,05%) | Потери с отходящими газами (20,20)(12,66%) | |
Итого 161,05 | Итого 159,62 | |
3. ПОВЫШЕНИЕ КАЧЕСТВА ВЫПУСКАЕМОЙ ПРОДУКЦИИ
3.1 Возможные способы нарушения технологического режима выплавки сплава и борьба с ними К нарушениям технологического режима выплавки сплава относят:
1. Неравномерная температура: вверху горячий металл, внизу — холодный.
2. Прогар футеровки.
3. Неисправности в работе электродов (например, поломка электродов).
4. Попадание воды в печь.
5. Нарушение системы водоохлаждения (свод, кожух, эркер, газоотсос).
Во всех случаях требуется отключить печь от питания. Если необходимо, провести наладочные работы (заменить неработоспособный электрод, заделать футеровку, наладить систему водоохлаждения) или создать необходимое перемешивание металла (для равномерного обеспечения температуры).
Также, для предотвращения нарушения технологического режима выплавки сплава необходимо:
Своевременно проверять знания обслуживающего персонала.
Использовать материалы соответствующего качества.
Проводить периодический метрологический контроль.
Своевременно проводить планово-предупредительные ремонты.
Проводить исследовательские работы для выяснения конкретных причин брака.
Осуществлять контроль за соблюдением технологии.
3.2 Виды брака и методы борьбы с ним Кристаллическая структура непрерывнолитого слитка схожа со структурой слитков, полученных разливкой в изложницы — наружная корка из мелких неориентированных кристаллов (ее толщина 10 — 20 мм), далее столбчатые кристаллы и в осевой части слитка различно ориентированные равноосные кристаллы; в слитках мелкого сечения зона столбчатых кристаллов может простираться до центра слитка. Целесообразно уменьшение зоны столбчатых кристаллов, обладающей пониженной прочностью и пластичностью и расширение центральной зоны равноосных кристаллов; это достигается при снижении температуры разливаемого металла, электромагнитном перемешивании жидкой фазы слитка и при снижении интенсивности вторичного охлаждения.
Непрерывный слиток благодаря малой толщине и быстрому вследствие этого затвердеванию отличается меньшим развитием химической неоднородности, более равномерным распределением неметаллических включений. От слитков, разливаемых в изложницы, он отличается также более чистой и гладкой поверхностью.
Ниже перечислены основные дефекты слитков, получаемых непрерывной разливкой. Сильно развита в них осевая пористость, что объясняется наличием в кристаллизующемся слитке очень глубокой и узкой лунки жидкого металла. Образование в ней «моста» сросшихся кристаллов может привести к появлению больших по протяженности зон, в которых металл кристаллизуется без доступа жидкой стали сверху, и, следовательно, к появлению пустот. Особенно сильно осевая пористость проявляется в квадратных и круглых слитках; в плоских слитках она развита слабее, так как усадка металла здесь рассредоточена по продольной оси поперечного сечения слитка. Осевая пористость заметно усиливается при увеличении перегрева металла и повышенной скорости разливки, иногда переходя в осевые усадочные пустоты. Заметно выражена в непрерывных слитках осевая ликвация, при этом по длине слитка располагаются отдельные участки увеличенной ликвации; это объясняется тем, что ликвирующие примеси скапливаются в пустотах под сросшимися кристаллами осевой части слитка.
В слитках криволинейных и особенно горизонтальных УНРС наблюдается некоторая несимметричность структуры и распределения составляющих стали, поскольку зона затвердевания последних порций металла, а следовательно, и усадочная пористость, и скопление ликвирующих примесей смещены к верхней грани слитка; у верхней грани наблюдается также повышенное содержание неметаллических включений вследстиие их всплывания.
Иногда наблюдается искажение формы слитка. Для слитков квадратного сечения характерна ромбичность — искажение профиля слитка в кристаллизаторе, когда квадратное сечение деформируется в ромбическое. Причины: перекос слитка к кристаллизаторе под воздействием несоосно расположенных с ним опорных роликов, неравномерное охлаждение различных граней слитка в кристаллизаторе. Раздутие слитка (выпуклость его поперечного сечения) возникает под воздействием ферростатического давления столба жидкой стали в слитке; возникновению дефекта способствуют повышенные скорость разливки и температура металла, что уменьшает толщину затвердевшей корки; недостаточная интенсивность вторичного охлаждения; отклонения в настройке опорных роликов; увеличенное расстояние между опорными роликами.
Распространенным дефектом являются трещины — поверхностные и внутренние. Продольные поверхностные трещины на гранях слитка имеют длину до 1−1,5 м и более и глубину до 10−15 мм. Эти трещины являются результатом усадочных напряжений и образуются при неравномерном прилегании формирующейся корки к стенкам кристаллизатора в местах уменьшенной ее толщины, которые возникают из-за снижения теплоотвода там, где корка отходит от стенок (например, в результате ее деформации или коробления стенок кристаллизатора). Трещины представлены на рисунке 5. Местное уменьшение толщины корки и образование трещин может также происходить вследствие размывания корки струей металла, особенно при его подаче в кристаллизатор вертикальной струей. Вероятность возникновения продольных трещин повышается при перегреве стали и увеличении скорости разливки, при увеличении содержания серы в металле и снижении величины отношения
[Mn]/[S], при увеличении ширины плоского слитка и при содержании углерода в нелегированных сталях в пределах 0,18−0,25%.
Рисунок 4 — Основные виды трещин в вытягиваемом из кристаллизатора УНРС слитке
1 — центральная трещина; 2 — диагональные трещины; 3 — осевые; 4 -внутренние трещины перпендикулярные широким граням слитка; 5 — продольные поверхностные трещины на гранях слитка; 6 — трещины, перпендикулярные узким граням слитка; 7 — продольные трещины по ребрам (углам); 8 — паукообразные и сетчатые трещины; 9 — поперечные трещины в углах слитка; 10 — поперечные поверхностные трещины (надрывы корки).
Действенным средством борьбы с этим дефектом является разливка с защитным шлаковым покрытием, поскольку образующаяся между коркой и стенками кристаллизатора тонкая шлаковая прослойка существенно снижает неравномерность теплоотвода.
Продольные трещины по ребрам (углам), образуются в квадратных слитках при искажении профиля в кристаллизаторе (ромбичность). В слябах такие трещины возникают на расстоянии ~ 350 мм от уровня металла в кристаллизаторе в случае отхода корки слитка от узкой стенки кристаллизатора вследствие ее износа или изменения угла ее наклона (неправильная установка кристаллизатора).
Поперечные поверхностные трещины 10 (надрывы корки) возникают в кристаллизаторе вследствие усиленного трения при недостаточной смазке стенок и вследствие зависания корки при наличии на стенках кристаллизатора царапин, вмятин. Такие трещины могут также возникать при изгибании или выпрямлении слитка на МНЛЗ с криволинейной осью. Поперечные трещины в углах слитка 9 могут также образовываться в результате слишком интенсивного вторичного охлаждения.
Паукообразные и сетчатые трещины, схожи, каждая трещина распространяется из одного центра в нескольких направлениях. Паукообразные трещины возникают в кристаллизаторе при неравномерном прилегании корки к его стенкам в местах плотного прилегания, т. е. в участках наиболее сильного охлаждения. Пораженность этими трещинами снижается при разливке со шлаковым покрытием в кристаллизаторе, так как шлаковая прослойка предотвращает непосредственный контакт стенок с коркой, уменьшая неравномерность ее охлаждения. Сетчатые трещины образуются в зоне вторичного охлаждения при температурах 700−900 °С в результате чередования нагревов и охлаждений поверхности слитка (охлаждение у форсунок и разогрев за счет внутреннего тепла слитка при его движении между форсунками). Количество этих трещин сильно снижается при переходе от водяного к более мягкому водовоздушному вторичному охлаждению.
Многообразные внутренние трещины образуются в результате совместного воздействия термических напряжений в охлаждаемом слитке и механических усилий от опорных, тянущих и изгибающих роликов. Распространены внутренние трещины, перпендикулярные широким граням слитка основной причиной их возникновения считают механическое воздействие роликов на затвердевающую корочку слитка и средством борьбы с ними — правильную настройку роликовой проводки и сохранение постоянства расстояния между роликами. Такие трещины могут также возникать из-за термических напряжений при неравномерном вторичном охлаждении (например, при разогреве поверхности после интенсивного охлаждения).
Гнездообразные трещины — скопления мелких, схожих с трещинами типа и располагающихся ближе них к центру слитка образуются при разгибании слитка с жидкой сердцевиной.
Осевые трещины в слябах располагаются по их большой оси в зоне смыкания фронтов кристаллизации. Считают, что эти трещины образуются в результате усадки стали, если она не компенсируется сжимающим усилием опорных роликов; особенно они проявляются при выпучивании широких граней слитка, когда сжимающие усилия явно недостаточны. В слитках квадратного сечения, где усадка сконцентрирована в центре слитка, форма осевых трещин иная.
Трещины, перпендикулярные узким граням и расположенные вблизи от них, возникают при выпучивании широких граней слитка, т. е. при недостаточном поддерживании оболочки слитка опорными устройствами. Диагональные трещины на стыке кристаллов, растущих от двух смежных граней, встречаются преимущественно в слитках квадратного сечения при искажении профиля (ромбичности) в тупых углах.
Газовые пузыри в корковом слое слитка возникают при недостаточно раскисленном металле, высоком содержании в нем водорода, повышенном содержании влаги в защитной шлаковой смеси, вводимой в кристаллизатор. Ряд поверхностных дефектов слитка связан с неудовлетворительной организацией разливки. Шлаковые включения на поверхности возникают при заливке жидким металлом прилипающих к стенкам кристаллизатора частиц шлака или размытых огнеупоров. Ужимины (поперечные углубления на поверхности слитка) возникают в результате резкого изменения напора струи и колебаний уровня металла в кристаллизаторе, при местном размывании корки струей металла и в участках неплотного прилегания корки к стенкам кристаллизатора.
3.3 Возможные направления модернизации технологии получения стали C345
ь Применение порошковых проволок для наплавки роликов МНЛЗ Современное металлургическое производство немыслимо без технологии непрерывной разливки стали и обусловлено существенной экономией энергетических и временных затрат, повышением производительности и качества продукции, снижением производственных потерь, реализацией более эффективного инвестирования. В связи с этим проводится системное внедрение МНЛЗ и, как следствие, ожидается рост объема их производства и ремонта. Опыт металлургических предприятий показывает, что технические и технико-экономические показатели машин непрерывного литья заготовок (МНЛЗ) в значительной степени зависят от долговечности роликов поддерживающих систем. Ролики поддерживающих и разгибающих узлов работают в тяжелом температурном режиме термоциклирования, максимальная температура поверхности роликов может достигать 650—750 °С. Ролики воспринимают усилия от ферростатического раздутия и усилия от разгиба слитка. На прямолинейных участках ролики подвергаются абразивному износу. Разрушение рабочей поверхности роликов проявляется в виде износа поверхностного слоя и образования трещин разгара. В соответствии с требованиями производства интенсивность изнашивания материала рабочих поверхностей не должна превышать 0,1—0,25 мм на 1 тыс. плавок, при этом МНЛЗ должна выпустить не менее 1 млн. тонн заготовок без смены роликов. Известно, что электродуговая наплавка рабочих поверхностей роликов износои коррозионностойкой сталью — наиболее эффективный и распространенный способ увеличения срока службы подобных деталей. Данный способ упрочнения роликов применяется большинством фирм, создающих МНЛЗ как в нашей стране, так и за рубежом.
Реализуются технологии наплавки под флюсом по винтовой линии одиночной и расщепленной дугой, без колебаний и с поперечными колебаниями начиная от диаметра 70 мм и более. Наиболее распространена технология двухслойной наплавки, а на ряде ремонтных служб применяется трехслойная наплавка. Для данного способа наплавки выпускаем проволоки диаметром от 2,0 до 4,0 мм. Предлагаемые порошковые проволоки позволяют наплавить на рабочую поверхность роликов слой металла стойкий к много-факторному износу. Сочетание порошковой проволоки с флюсом позволяет получить высокохромистый (Cr-Mn-Ni-Mo-N, Cr-Mn-Ni-Mo-V-Nb) наплавленный металл с пластичной структурой низкоуглеродистого мартенсита, упрочненный дисперсными карбидами и нитридами при минимизации содержания д феррита 5—10% .
Применение наплавки в защитном газе наиболее эффективно в смеси 82Ar+18CO2или Ar по сравнению с углекислым газом вследствие более высокой стабильности процесса, снижения окислительной способности защитного газа, уменьшения проплавления основы. К преимуществам можно отнести приемлемую производительность процесса, визуальный контроль за процессом наплавки, химический состав задается композицией проволоки и нет влияния характерного для флюса, меньшее содержание водорода в наплавленном металле по сравнению с флюсом, проще реализация процесса с поперечными колебаниями проволоки. Процесс наплавки характеризуется хорошим формированием металла, легкой отделимостью шлаковой корки и возможностью наплавки последующего слоя без удаления шлака. К недостаткам можно отнести: необходимость защиты от брызг и излучения дуги, менее ровная поверхность наплавленного металла, необходимость применения дымососов, забрызгивание сопла подачи защитного газа. Для данного способа наплавки выпускаем проволоки диаметром от 1,6 до 2,4 мм как для нанесения подслоя, так и рабочих слоев наплавленного металла.
Процесс наплавки открытой дугой обладает преимуществами присущими процессу в защитном газе и дополняется отсутствием необходимости применения защитного газа, более упрощенной комплектацией наплавочной установки, но наиболее существенно его преимущество в металлургическом аспекте. При данном способе наплавки реализуется возможность легирования наплавленного металла азотом. Необходимость такого металлургического решения обусловлена актуальностью увеличению ресурса роликов МНЛЗ за счет повышения стойкости наплавленного металла к разгару и коррозии. Наиболее успешно это решение реализовано английской фирмой Welding Alloys. Рабочая поверхность ролика подвергается циклическому воздействию высоких температур, что приводит изменению структурного состояния при-поверхностного слоя металла.
Наблюдается укрупнение зерен и формирование на их границах карбидов хрома, что приводит к развитию межзеренной коррозии. Потеря мартенситной матрицей углерода приводит к формированию мягкого ферритного слоя, обладающего низким сопротивлением механическому износу. Замена части углерода азотом подавляет процессы укрупнения зерен и формирования на границах зерен карбидов хрома. Образующиеся нитриды равномерно распределены в структуре металла, проявляется эффект вторичного упрочнения в процессе термоциклирования. Реализация этих механизмов позволяет повысить ресурс роликов. Для данного способа наплавки выпускаем проволоки диаметром 2,0—2,4 мм.
4. ЗАРУБЕЖНЫЙ ОПЫТ ПРОИЗВОДСТВА ПОДОБНОЙ ПРОДУКЦИИ ь Китай Компания «Lingyuan Iron & Steel» («Linggang») начала горячие испытания новой семиручьевой МНЛЗ производительностью 1,2 млн т/год, которая будет отливать заготовку из углеродистых и пружинных сталей, а также сталей для холодной высадки. Заготовка предназначена для строящегося мелкосортного стана производительностью 500 тыс. т/год.
ь Украина Компания «ArcelorMittal Kryviy Rih» начала строительство на комбинате блюмовой МНЛЗ, которая позволит исключить используемую в настоящее время разливку в слитки. МНЛЗ, стоимость которой оценивается в 100 млн долл., будет иметь производительность 1,2 млн т/год заготовки и должна быть пущена в сентябре 2011 г. В сооружении МНЛЗ примет участие фирма «Siemens VAI», однако 80% работ будут выполнены украинскими компаниями.
ь Малайзия Компания «Perwaja Steel» перенесла установку новой ДСП производительностью 700 тыс. т/год со второй половины 2010 г. на середину 2011 г. Строительство 90-т печи на заводе «NSC Steelmaking plant» в г. Кемаман (Kemaman), принадлежащем «PerwajaSteel», ведет фирма «Concast». После пуска новой печи компания планирует приступить к модернизации двух существующих ДСП производительностью600 тыс. т/год каждая.
ь Катар Один из крупнейших производителей стали на Ближнем Востоке компания «Qatar Steel» подписала контракт с фирмой «Siemens VAI» на расширение сталеплавильных мощностей на 30%. В настоящее время мощность ДСП компании составляет 1,47 млн. т/год. Пуск новой печи планируется на II кв. 2012 г., после чего производство заготовки в течение следующих пяти лет будет доведено до 4 млн т/год. В настоящее время компания производит заготовку, пруток и катанку.
5. ОХРАНА ТРУДА И ТЕХНИКА БЕЗОПАСНОСТИ. ОХРАНА ОКРУЖАЮЩЕЙ СРЕДЫ Безопасность жизнедеятельности (БЖД) — это деятельность, направленная на сохранение жизни и здоровья человека в среде обитания, призванная выявлять и идентифицировать опасные и вредные факторы, разрабатывать методы и средства с целью снижения негативного влияния их на организм до приемлемых значений, вырабатывать меры по ликвидации последствий чрезвычайных ситуаций мирного и военного времени.
Решение вопросов БЖД необходимо для создания безопасных и безвредных условий жизнедеятельности, проектирования новых технологий и технологических процессов в соответствии с современными требованиями по экологии и безопасности их эксплуатации с учетом устойчивости функционирования объектов народного хозяйства и технических систем, прогнозирования и принятия грамотных решений в условиях чрезвычайных ситуаций по защите населения и производственного персонала от возможных последствий аварий, катастроф, стихийных бедствий, а также в ходе их ликвидации.
Соблюдение правил, норм и требований БЖД обязательно для учреждений всех организационно-правовых форм, независимо от сферы деятельности и ведомственной подчиненности при проектировании, строительстве, реконструкции и эксплуатации цехов и участков, при проектировании, изготовлении, монтаже и наладке нового оборудования, эксплуатации, техническом обслуживании, ремонте и модернизации действующего оборудования, разработке, внедрении и совершенствовании технологических процессов.
При организации и эксплуатации сталеплавильных цехов и участков должны соблюдаться действующие правила Конституции РФ, Трудового кодекса РФ (ТК РФ), «Системы стандартов безопасности труда» (ССБТ) и другие нормативно-правовые акты по охране труда, утвержденные в установленном порядке.
Конституция РФ закрепляет право человека на охрану здоровья. Это право обеспечивается развитием и совершенствованием техники безопасности и производственной санитарии, проведением широких профилактических мероприятий.
В ТК РФ отражены: правила организации охраны труда на предприятиях, планирование и финансирование мероприятий по охране труда; правила по технике безопасности и производственной санитарии; правила и нормы по специальной охране труда женщин, молодежи и лиц с пониженной трудоспособностью; правила, регулирующие деятельность органов государственного надзора и общественного контроля в области охраны труда; правовые нормы, в которых предусматривается ответственность за нарушения ТК РФ.
Проектирование, строительство, эксплуатация, реконструкция, расширение, техническое перевооружение, консервация, ликвидация сталеплавильных производств, изготовление, монтаж, наладка, обслуживание и ремонт технических устройств, проведение подготовки и аттестации работников осуществляются в соответствии с требованиями ССБТ, «Общих правил промышленной безопасности для организаций, осуществляющих деятельность в области промышленной безопасности опасных производственных объектов» (ПБ 11−552−03), утвержденных постановлением Госгортехнадзора РФ от 18.10.02 № 61-А, «Общих правил безопасности для металлургических и коксохимических предприятий и производств» (ПБ 11−493−02), утвержденных постановлением Госгортехнадзора РФ от 21.06.02 № 35 и других юридических документов.
Важность и необходимость обеспечения безопасности труда очевидна, так как жизнь и здоровье человека признаны главной ценностью общества. Полностью безопасных и безвредных производств не существует. Реальные производственные условия характеризуются наличием некоторых опасных и вредных производственных факторов. Задача охраны труда — свести к минимальной вероятность поражения или заболевания работающего с одновременным обеспечением комфорта при максимальной производительности труда.
ь Порядок обучения по охраны.
Для всех принимаемых на работу лиц, а также для работников, переводимых на другую работу, работодатель обязан проводить инструктаж по охране труда. Все принимаемые на работу лица, а так же командированные на работу работники и работники сторонних организаций, выполняющие работы на выделенном участке проходят в установленном порядке вводный инструктаж, который проводит специалист по охране труда.
Кроме вводного инструктажа по охране труда, проводится первичный инструктаж на рабочем месте, повторный, внеплановый и целевой инсруктаж.
Первичный, повторный, внеплановый и целевой инструкажи проводит непосредственный руководитель работ (мастер, прораб ит.д.), прошедший в установленном порядке обучение по охране труда и проверку знаний требования охраны труда.
Проведение инструктажей по охране труда включает в себя ознакомление работников с имеющимися опасными и вредными факторами изучение охраны труда, эксплуатационной документации, а так же применение безопасных методов работ.
Инструктажи завершаются устной проверкой знаний.
Первичный инструктаж на рабочем месте проводится до начала самостоятельной работы.
Повторный инструктаж проходят все работники не реже одного раза в шесть месяцев.
Внеплановый инструктаж проводится: при введении в действие новых или изменении законодательных и иных нормативных правовых актов. При изменении технологических процессов. При нарушении работниками требований охраны труда. По требованию должностных лиц органов государственного контроля и надзора. При перерывах в работе.
Целевой инструктаж проводится при выполнении разовых работ.
ь Описание природно-климатических условий района расположения предприятия Открытое акционерное общество «Ашинский металлургический завод» спланировано с учетом производственных, транспортных, экономических и других требований. Площадка завода удовлетворяет санитарным требованиям в отношении прямого солнечного света, естественного проветривания, имеет относительно ровную поверхность и уклон, обеспечивающий отвод поверхностных и сточных вод. Предприятие относится ко второму классу по санитарной классификации СанПиН 2.2.½.1.1.567−96. Деятельность ОАО «АМЗ» связана с эксплуатацией опасных производственных объектов.
В геоморфологическом отношении площадка приурочена ко второй правобережной надпойменной террасе реки Сим. Территория паводковыми водами в весенний период не затапливается. Основание сложено толщей галечников, мощность которых достигает шести метров.
В геологическом отношении территория района предприятия расположена на границе Уральской геосинклинальной области с Предуральским краевым прогибом. В геологическом строении структур принимают участие осадочные, различной степени метаморфизованные, породы широкого возрастного диапазона.
Естественный рельеф площадки нарушен в процессе строительства и эксплуатации существующих сооружений. На заболоченной ранее территории выбраны биогенные грунты и торф, поверхность спланирована насыпными грунтами, представляющими собой механическую смесь различных природных грунтов, металлургического шлака, щебня.
Климатическая характеристика района. Температурный режим в результате высокой континентальности климата характеризуется резким колебанием как внутри года, так и в течение суток. Среднемесячные и экстремальные значения температуры воздуха за многолетний период приведены в таблице 4.1.
Крайние значения температуры, наблюдающиеся в течение года, изменяются в пределах от +37С летом до — 48С зимой. Среднегодовая температура воздуха положительна и равна 1,4С.
Ветер. Преобладающими ветрами данного района являются ветры юго-западного и западного направлений. Среднегодовая скорость ветра равна 3,3 м/с.
Осадки. Исследуемый район располагается на западном склоне Уральского хребта, норма годовой суммы осадков для которого более 700 мм, для предприятия ОАО «АМЗ» она равна 539 мм. Наибольшее количество осадков выпадает летом. В таблице 3.1 приводится среднее многолетнее количество осадков по месяцам.
Снежный покров. Среднее число дней со снегом 172. Наибольшей высоты снежный покров достигает в марте перед началом таяния. Средняя высота снежного покрова на открытых участках равна 42 см.
Таблица 22 — Среднемесячные и экстремальные значения температуры воздуха и среднее многолетнее количество осадков
Месяцы | Температура воздуха, С | Месячные суммы осадков, мм | Сут. макс. осадков | ||||
среднемесячная | абсолютный минимум | абсолютный максимум | макс. | мин. | |||
январь | — 15,0 | — 48 | |||||
февраль | — 13,7 | — 45 | |||||
март | — 7,1 | — 38 | |||||
апрель | 3,2 | — 30 | |||||
май | 10,8 | — 14 | |||||
июнь | 15,2 | — 3 | |||||
июль | 17,0 | ||||||
август | 15,0 | — 2 | |||||
сентябрь | 9,3 | — 9 | |||||
октябрь | 1,4 | — 26 | |||||
ноябрь | — 6,4 | — 38 | |||||
декабрь | — 12,3 | — 45 | |||||
год | 1,4 | ||||||
Гидрогеологические условия исследованной территории не благоприятны для строительства: подземные воды обнаружены во всех скважинах. Глубина заложения фундаментов согласно техническому заданию составляет 2,0 — 2,5 м, а для ямы окалины — не менее 10,0 м, подземные воды существенно влияют на выбор инженерного решения устройства оснований и фундаментов. Территория по положению уровня подземных вод относится к затопляемым. По химическому составу вода гидрокарбонатно-сульфато-кальциево-магниевая с минерализацией 0,409 — 1,879 г/л. По степени минерализации воды относятся к пресным и слабосолоноватым. Углекислотная агрессивность отсутствует. Подземные воды являются неагрессивными по отношению к бетонам. Агрессивность подземных вод к арматуре железобетонных конструкций в условиях периодического смачивания слабая, в условиях постоянного погружения подземные воды являются неагрессивными. Степень агрессивного воздействия подземных вод по отношению к металлическим конструкциям при свободном доступе кислорода — средняя.
Подтопление оказывает решающее влияние на выбор проектных решений, поэтому площадка по сложности инженерно-геологических условий отнесена к III категории. К осложняющим строительство факторам относятся также наличие насыпных разнородных, тиксотропных и чрезмерно пучинистых грунтов.
В соответствии с «Рекомендациями по формированию программы развития системы управления промышленной безопасностью (СУПБ) на предприятии» разработана «Программа развития системы управления промышленной безопасностью открытого акционерного общества «Ашинский металлургический завод», которая предлагается в качестве эффективного инструмента контроля обеспечения промышленной безопасности на предприятии. Цели СУПБ состоят в обеспечении промышленной безопасности при эксплуатации опасных производственных объектов на основе системного подхода к принятию управленческих решений и практических мер по предупреждению или уменьшению опасности промышленных аварий для жизни человека, снижению случаев травматизма, заболеваемости, ущерба имуществу и окружающей среде.
ь Описание ЭСПЦ — 2 и отделения непрерывной разливки стали ОАО «АМЗ»
Площадь застройки — электросталеплавильного цеха № 2 с ОНРС — составляет ~ 40 000 м2, объем ~ 1 500 000 м3. Каркас здания металлический, стены выполнены из шлакоблока, кирпича, профнастила, кровля металлическая без утепления. Здание неотапливаемое, вентилируемое.
Здание цеха расположено в центре территории предприятия, что является оптимальным вариантом с точки зрения обеспечения поточности технологического процесса производства стали.
Производственное здание имеет въезды и выезды железнодорожного и автомобильного транспорта через металлические ворота размерами 5,2×4,5 м. Объем производственного помещения на каждого рабочего более 20 м3, площадь более 4,5 м2. Ширина проходов не менее 1,5 м. Все площадки на высоте более 0,6 м от пола, лестницы, переходные мостки, проемы, люки ограждены перилами высотой 1,2 м со сплошным ограждением по нижней части на высоту 0,2 м. Лестницы имеют уклон не более 40. Пол земляной, бетонный, металлический. Для обслуживания мостовых кранов имеются подкрановые проходные галереи, огражденные перилами.
По взрывопожарной и пожарной опасности здание цеха относится к категории Г, используются негорючие вещества и материалы в горячем, раскаленном и расплавленном состоянии, а также твердые вещества, жидкости и газы, которые сжигаются и утилизируются в качестве топлива (НПБ 105−95). Степень огнестойкости здания по СНиП 21−01−97 — первая.
По степени поражения электрическим током помещение цеха относится к особо опасным, так как оно характеризуется наличием токопроводящей пыли, токопроводящих полов и токопроводящей смазочно-охлаждающей жидкости.
К основным особенностям выполняемой работы относятся непосредственная близость работника к раскаленным элементам агрегатов и оборудования, расплавленным веществам и токоведущим частям.
Рабочая площадка имеет металлическое ограждение на высоту 1,2 м сплошное по низу на высоту 0,2 м, что соответствует нормам (ПБ 11−493−02). Все тоководы и электрические кабели скрыты кабель-каналами, вращающиеся, движущиеся части и элементы оборудования находятся в кожухах, либо свободный доступ к ним отсутствует, а также снабжены конечными выключателями, трубопроводы, тракты подачи сыпучих веществ и проволок находятся на достаточном удалении от обслуживающего персонала. Рабочее место освещено, достаточно вентилируемое.
Характерной особенностью является большое количество выделяющихся высоконагретых сильнозапыленных газов. Рассматриваемое место работы снабжено мощным современным газоотводящим трактом и системой пылегазоулавливания.
Коэффициент риска в рассматриваемом цехе составляет:
(14)
где N — количество травм, полученных обслуживающим персоналом за год;
K — общее количество работающих в цехе.
5,6510-4 (15)
Данный показатель превышает значение приемлемого риска по России (Rср = 1,4Ч10-4).
Снижение коэффициента риска на производстве является одной из основных задач охраны труда. В связи с этим рассмотрим предлагаемые мероприятия по уменьшению коэффициента риска.
Главным условием обеспечения безопасности на производстве является глубокое осознание самими работающими необходимости соблюдения правил безопасности, требований норм и инструкций. Этому способствует обучение персонала грамотной работе с технологическим оборудованием, разъяснительные беседы.
Необходимость своевременного проведения технического осмотра, планово-предупредительных ремонтов оборудования и агрегатов очевидна, также как поддержание рабочего места в соответствии с требованиями норм и правил.
Эффективность всех мероприятий существенно возрастает при наличии жесткого независимого контроля со стороны компетентных органов за соблюдением техники безопасности на производстве, техническим состоянием оборудования, инструментов, а также при разработанном механизме несения ответственности за нарушения в области охраны труда.
ь Анализ опасных производственных факторов и мероприятия по снижению их воздействия Опасным производственным фактором называется такой производственный фактор, воздействие которого на работающего в определенных условиях приводит к травме или к другому внезапному, резкому ухудшению здоровья.
К опасным производственным факторам на анализируемом участке работы относятся:
— подвижные части оборудования, вращающиеся и перемещающиеся механизмы;
— электрический ток;
— раскаленные элементы агрегатов и оборудования, а также металл в расплавленном состоянии.
Основными мероприятиями по защите от травм подвижными частями оборудования, вращающимися и перемещающимися механизмами являются: использование защитных кожухов, блокировки для отключения оборудования при попадании человека в опасную зону, оборудование пультов управления защитными экранами, создание ограждений, безопасных пешеходных проходов, переходов и галерей, установки предостерегающих надписей.
Для работы на оборудовании участка цеха допускаются лица, прошедшие специальную подготовку по технике безопасности и имеющие допуск к работе на этом оборудовании.
Подъемно-транспортное оборудование для перемещения грузов в цехе представлено рольгангами, поперечными и продольными транспортерами с цепными шлепперами, передаточными тележками и мостовыми кранами. При эксплуатации этого оборудования возможно травмирование персонала движущимися частями, падающим грузом, электрическим током. Серьезная опасность возникает при обрыве несущих органов (канатов, тросов). Все части подъемно-транспортного оборудования, представляющие опасность при эксплуатации, надежно ограждены. Непредусмотренный контакт работающих с перемещаемыми грузами исключен, обеспечена надежная прочность механизмов. Запас грузовой устойчивости не менее 25%. На каждом устройстве находятся бирки с указанием всех технических характеристик, а так же отмечен последний срок проверки и допуск к работе. К работе с подъемно-транспортными машинами допускаются только лица прошедшие специальную подготовку, инструктаж по технике безопасности и имеющие допуск к работе с этими машинами.
Не все требования по обеспечению защиты от данного опасного производственного фактора на участке работы соблюдаются. В связи с этим предлагаются следующие мероприятия по ее улучшению: постоянный контроль за состоянием световой и звуковой сигнализации на оборудовании и механизмах (в первую очередь на мостовых кранах и самоходных передаточных тележках); поддержание проходов, переходов и галерей не загроможденными технологическими материалами, что обеспечит безопасное перемещение обслуживающего персонала.
Электробезопасность — это система организационно-технических мероприятий и средств обеспечения защиты людей от вредного и опасного воздействия электрического тока, электрической дуги, электромагнитного поля, статического электричества. ОНРС относится к помещению с повышенной электрической опасностью. Максимальная мощность электрического тока на рабочем месте — 30 МВт, максимальный ток — 10 кА. Все металлические и токонесущие части оборудования, которые из-за нарушения изоляции могут оказаться под напряжением заземлены и занулены. Сопротивление заземления не более 4 Ом. Рабочие не имеют права самостоятельно проводить ремонт электротехнического оборудования. На участках, связанных с опасностью поражения электрическим током, имеются предостерегающие таблички и надписи. Персонал проинструктирован по электробезопасности и обучен оказанию первой медицинской помощи при поражении электрическим током.
Раскаленные элементы агрегатов и оборудования, а также металл в расплавленном состоянии могут стать причиной термических ожогов работников при несоблюдении правил и требований безопасности и неосторожном обслуживании агрегата внепечной обработки. Они же являются источником теплового излучения. Для защиты рабочего персонала от теплового излучения источники излучения закрываются защитными экранами. С целью уменьшения времени пребывания персонала в зоне повышенных температур используются способы дистанционного и автоматического управления процессами.
Кроме того, с целью снижения воздействия на организм человека обязательным является использование средств коллективной и индивидуальной защиты. К средствам коллективной защиты относятся:
— средства нормализации воздушной среды (системы газоочистки и аэрации);
— средства нормализации освещения;
— средства защиты от теплоизлучения (теплоизоляционные покрытия ковшей, нагревательных стендов);
— средства защиты от поражения электрическим током (ограждения, изолирующие устройства, покрытия, предохранительные устройства, знаки предупреждения, световая и звуковая сигнализация);
— средства защиты от воздействия механических факторов (предохраняющие, сигнальные и тормозные устройства);
— средства защиты от воздействия химических факторов (герметизирующие, вентилирующие, очистные устройства);
— средства защиты от шума;
— стационарные или инвентарные ограждения открытых проемов;
— средства защиты от попадания в подвижные и вращающиеся части оборудования (защитные кожухи и ограждения).
К средствам индивидуальной защиты относятся:
— спецодежда (суконные брюки, куртка, рукавицы, каска, и др.);
— средства защиты глаз (защитные очки с металлической сеткой);
— средства защиты органов дыхания (марлевые повязки типа «Лепесток-200», респираторы и др.).
ь Анализ вредных производственных факторов и мероприятия по снижению их воздействия.
Вредным производственным фактором называется такой производственный фактор, воздействие которого на работающего в определенных условиях приводит к заболеванию или снижению трудоспособности.
К вредным производственным факторам на анализируемом участке работы в первую очередь относятся:
— запыленность воздуха рабочей зоны;
— загазованность воздуха рабочей зоны;
— производственный шум и вибрация;
Параметры микроклимата (фактические и допустимые) приведены в таблице 23.
Таблица 23 — Фактические и допустимые параметры микроклимата на рабочем месте
Параметры микроклимата | Значения | ||
фактические | допустимые | ||
Температура воздуха, оC: | |||
в холодное время года | 21,2 — 23 | ||
в теплое время года | 22,1 — 27 | ||
Относительная влажность, % | |||
в холодное время года | 15 — 75 | ||
в теплое время года | 15 — 75 | ||
Скорость движения воздуха, м/с | |||
в холодное время года | 0,1 | <0,2 | |
в теплое время года | 0,5 | 0,2 — 0,4 | |
Теплоизлучение от источников, Вт/м2 | |||
Освещенность, лк | |||
Уровень шума, дБА | |||
Источниками запыленности являются: взаимодействие струи несущего перемешивающего газа с жидким металлом (выносы и выбросы мельчайших капель окислов железа); химическое взаимодействие металла с вводимыми материалами, результатом, которого является пылегазовыделение; механическое разрушение хрупких технологических материалов при транспортировке и подаче в агрегат.
По пылевой нагрузке (Р 2.2.755−99, ГОСТ 12.1.005−88 ССБТ) производство относится к классу 3.1 (вредный).
Основной технологической особенностью выполнения работы является периодическое пребывание персонала в зоне запыленности (в течение 40 мин с перерывом в 3 часа).
Основное коллективное средство защиты от данного вредного производственного фактора — система пылеулавливания и отведения выделяющихся газов, а также изоляция человека от источника пыли посредством автоматизации, механизации и дистанционного управления процессами. Индивидуальные средства защиты от пыли (респираторы, очки, местная вытяжная вентиляция), как правило, применяются при ремонтах, техническом осмотре оборудования и разгрузочных работах. Все пульты управления представляют собой изолированные кабины, где имеется местная вентиляция.
Основными источниками газовыделения на рабочем месте являются: химическое взаимодействие металла с вводимыми материалами; утечки технологических газов (природного газа, аргона, азота, кислорода) через неплотности газоподводящих трактов.
По загазованности (Р 2.2.755−99, ГОСТ 12.1.005−88 ССБТ) производство относится к классу 2 (допустимый).
Средства защиты от загазованности такие же, как от запыленности, с установкой датчиков регистрации давлений и утечки газов на газопроводах, а также звуковой и световой сигнализации, позволяющих своевременно заметить и предотвратить возникновение нежелательных ситуаций.
Работа агрегата сопровождается повышенным шумом и вибрацией. Основными источниками шума в цехе являются: работа оборудования и механизмов, работа вентилирующих устройств, погрузочно-разгрузочные работы. Вибрацию вызывает работа некоторых видов механического оборудования.
По уровню общей вибрации (СН 2.2.4/2.1.8.566−96) производство относится к классу 2 (допустимый). Для предотвращения её вредного воздействия применяется балансировка оборудования и удаление рабочего персонала из опасных зон.
По уровню шума (СН 2.2.4/2.1.8.562−96) производство относится к классу 3.3 (вредный). Меры по борьбе с шумом осуществляются согласно ГОСТ 12.1.003−83, который определяет допустимый уровень шума не более 85 Дб. Основные мероприятия по снижению уровня шума: установка звукоизолирующих кожухов, применение шумозащитных наушников, заглушек, которые снижают уровень шума на 5 — 15 Дб. Все пульты управления звукоизолированы.
ь Пожарная безопасность В соответствии с техническим регламентом «О требованиях пожарной безопасности» (ФЗ № 123 от 22.07.2008 г.) по взрывопожарной и пожарной опасности здание цеха относится к категории Г, используются негорючие вещества и материалы в горячем, раскаленном и расплавленном состоянии, а также твердые вещества, жидкости и газы, которые сжигаются и утилизируются в качестве топлива. Степень огнестойкости здания по — первая. Все строительные материалы и конструкции в цехе сделаны из несгораемых материалов (естественные и искусственные неорганические минеральные материалы и используемые при строительстве металлы).
Главную пожарную опасность в черной металлургии представляют взрывы газа, а также прорывы и выбросы металла и шлака из основных металлургических агрегатов.
На территории предприятия находится пожарная часть ОППЧ-50, которая призвана локализовывать и ликвидировать возможные очаги возгораний. Для проезда пожарных машин используются дороги, предназначенные для производственных нужд. Подъезды к зданиям пересекаются железнодорожными путями, поэтому для обеспечения своевременного прибытия пожарных машин переезды через находятся на расстоянии не менее длины расчетного состава поезда.
Для тушения пожаров применяют противопожарный цеховой инвентарь. Пожарный инструмент и оборудование размещены у входа или вблизи помещения на специальных щитах так, чтобы в случае возникновения пожара ими быстро можно воспользоваться. К основным средствам тушения пожаров, которые применяют в мартеновском цехе, относят воду, твердые огнегасительные вещества (сухой песок, асбестовые плиты) и огнетушители. Огнетушители предназначены для тушения возгораний и пожаров на начальной стадии их возникновения до прибытия пожарных подразделений. В соответствии с нормами оснащения помещений ручными огнетушителями используются порошковые огнетушители вместимостью 5 л — ОП-5, 10 л — ОП-10 (предназначены для тушения возгораний легковоспламеняющихся жидкостей, щелочноземельных металлов, электроустановок, находящихся под напряжением) и пенные вместимостью 10 л — ОХП-10 (предназначены для тушения твердых горючих материалов, различных горючих жидкостей).
На случай возникновения пожара в здании цеха предусмотрены пути эвакуации персонала (безопасные проходы, переходы, галереи). Ширина проходов не менее 1,5 м, загромождение их не допускается. В цехе выполнено аварийное и эвакуационное освещение.
ь Чрезвычайные ситуации Возникновение и развитие чрезвычайных ситуаций может привести к дезорганизации и остановке производства, нанести материальный ущерб, а также создать угрозу жизни и здоровью производственного персонала. Среди возможных чрезвычайных ситуаций на ОАО «АМЗ» рассмотрим воздействие грозы, сейсмическую и радиоактивную опасности.
Для предотвращения ударов грозовых разрядов в производственные здания на территории предприятия устроены двойные стержневые молниеотводы, которые находятся на наиболее высоких строениях — осветительных прожекторных столбах, расположенных по периметру завода вдали от хранилищ горюче-смазочных материалов, кислородо-, газои мазутопроводов, электрических кабелей высокого напряжения.
За время существования данного предприятия ударов молний в производственные здания на его территории зафиксировано не было, также не наблюдалось повышения сейсмической активности в районе расположения завода и превышения допустимого радиоактивного фона.
На случай возникновения сейсмической или радиоактивной опасности для персонала созданы специальные укрытия бункерного типа, разработана схема оповещения работающих, локализации воздействия и ликвидации последствий. Работники всех подразделений предприятия проинструктированы о действиях в случае возникновения чрезвычайных ситуаций.
Для управления объектом в условиях чрезвычайных ситуаций создано формирование гражданской обороны, которое возглавляет начальник цеха. Он осуществляет руководство через штаб отряда.
Отряд состоит из:
— санитарной дружины;
— спасательной команды;
— звена связи и электроснабжения;
— специального эвакуационного пункта;
— комендатуры места эвакуации;
— четырех команд (технологические смены);
— звена обеззараживания;
— звена материально-технического снабжения;
— звена охраны.
При невозможности изоляции работающих от воздействия сейсмической или радиоактивной опасности на территории предприятия основным мероприятием является эвакуация в безопасные районы. Грамотно разработанная схема по своевременной и полной эвакуации персонала, а также действие работников предприятия согласно инструкций по действию в случае ЧС является условием сохранения жизни и здоровья человека. Эвакуация персонала начинается по команде начальника цеха и осуществляется в соответствии с заранее разработанным планом. Выход рабочих производится централизованно после прекращения подачи электроэнергии к оборудованию и механизмам и после тушения технологического пламени через безопасные проходы, переходы, галереи, аварийный балкон к пункту сбора персонала. Дальнейшее передвижение за пределы предприятия в специальный эвакуационный пункт осуществляется автомобильным транспортом силами заводского автотранспортного цеха и МЧС. Защита рабочих и служащих при возникновении чрезвычайных ситуаций является важнейшим фактором повышения устойчивости работы любого объекта.
ь Описание выбросов, жидких, твердых и газообразных отходов.
Вопрос экологии и защиты окружающей среды особенно остро стоит на ОАО «Ашинский металлургический завод» прежде всего в связи с тем, что предприятие расположено в экологически чистом районе Челябинской области, все производство размещено в непосредственной близости от водоема (р. Сим). Основная тяжесть негативного воздействия предприятия на экосистему приходится на долю водной и воздушной сред.
Большинство технологических операций цепочки производства основной продукции завода связано с интенсивным газопылевыделением, загрязнением воды и тепловым загрязнением окружающей среды.
Источники загрязнения воздушного бассейна:
— источники выделения: технологические агрегаты (установки, устройства, аппараты и т. п.), производственные участки (шлакоотвалы, места разгрузки материалов и т. п.), выделяющиеся в процессе эксплуатации загрязняющие вещества;
— источники выбросов: специальные устройства (аэрационные фонари, выбросные трубы, вентиляционные шахты и т. п.), посредством которых осуществляется выброс загрязняющих веществ в атмосферу;
— организованные источники выделения загрязняющих веществ, от которых последние поступают в систему газоходов или воздуходувов с газоочистными и пылеулавливающими установками;
— неорганизованные источники выделения, загрязняющие вещества от которых поступают непосредственно в цех или атмосферу вследствие негерметичности технологического оборудования, транспортных устройств, резервуаров, также сюда относят пылящие отвалы, открытые склады и т. п.
Валовые выбросы загрязняющих веществ в атмосферу представлены в таблице 24.
Таблица 24 — Валовые выбросы вредных веществ в атмосферу за 2012 год
Наименование вредного вещества | Класс опасности | ПДК, мг/м3 | Фактический выброс, т/год | |
азота диоксид (NO2) | ||||
азота оксид (NO в пересчете на NO2) | ||||
углерода оксид (CO) | ||||
железа оксиды (FexOy) | ||||
соединения серы (в пересчете на серу элементарную) | ||||
марганца оксиды (в пересчете на MnO2) | 0,2 | |||
ь Системы очистки и утилизации отходов ь Защита атмосферного воздуха Основными источниками пылегазовыделения ОНРС являются:
— агрегат печь-ковш;
— машина непрерывного литья заготовок;
— участок ремонта подготовки и промежуточных ковшей.
От источников в атмосферу и производственные помещения попадает пыль, окислы азота и окислы углерода.
На всех указанных участках предусматривается комплекс мероприятий, обеспечивающих улавливание и удаление пылегазовых выделений и исключающих попадание пыли и газов в производственные помещения.
На МНЛЗ зона вторичного охлаждения размещается в специальном бункере, из которого производится отсос образующейся при охлаждении поверхности заготовки паровоздушной смеси. Образующаяся на машинах газовой резки парогазовоздушная смесь очищается на газоочистке за МГР.
В отделении предусмотрены также местные вытяжные и аспирационные установки, включающие фильтры, вентиляторы и выбросные трубы.
Защита водных объектов.
Для обеспечения отделения водой заданных параметров по качеству и создания бессточной системы водоснабжения, применяют 3 оборотных цикла:
— «грязного» цикла водоснабжения газоочисток;
— «грязного» цикла водоснабжения МНЛЗ;
— «чистого» цикла оборудования отделения.
Конструкцией МНЛЗ предусмотрено наличие системы гидросмыва окалины и шламов. В процессе разливки металла на МНЛЗ в зоне вторичного охлаждения заготовки и при дальнейшей её порезке на мерные длины на участках первичной и вторичной газорезок образуется большое количество окалины. Кроме того в систему гидросмыва попадает достаточно большое количество нефтепродуктов (в основном, это смазочные материалы и масла) и шламов (часть затвердевшей шлакообразующей смеси, подаваемой в ходе разливки металла в кристаллизатор, несгоревшие элементы забивки затравки, асбестового шнура, шлака и др.). Удаление всех этих нежелательных элементов из разливочного ручья и ванн грануляции окалины первичной и вторичной газорезок — основное предназначение системы гидросмыва МНЛЗ.
ь Схема работы системы гидросмыва окалины и шламов на МНЛЗ В яму окалины по каналам и лоткам поступают сточные воды, загрязненные окалиной (600 — 1340 мг/л) и нефтепродуктами (50 мг/л) с температурой 55єС. Количество сточных вод, поступающих в яму окалины 726 м3/ч. Сточные воды поступают от:
— зоны вторичного охлаждения — 300 м3/ч;
— гидросмыва окалины — 426 м3/ч.
Сточные воды по лоткам гидросмыва окалины поступают в первичный отстойник, состоящий из двух секций.
Из приёмной камеры осветлённая вода насосами СМ200−150−315/4 (2 рабочих и 2 резервных) с электродвигателями мощностью N=75 КВт, установленными в насосной станции, перекачивается на дальнейшую очистку на очистные сооружения и на гидросмыв окалины.
Качество воды после первичного отстойника:
— окалины — 100 мг/л;
— нефтепродуктов — 10 — 20 мг/л.
Часть воды в количестве 426 м3/ч подается во всасывающий трубопровод повысительных насосов СМ200−150−540/4 (1 рабочий и 1 резервный) с электродвигателями мощностью N=250 КВт, установленных в помещении первичного отстойника и подающих воду на гидросмыв окалины.
Насосы работают в автоматическом режиме от уровня воды в приёмной камере. Постоянный уровень воды поддерживается с помощью частотного преобразователя. Все насосы взаимозаменяемые. При выходе из строя одного из рабочих насосов автоматически включается резервный.
В насосной станции для откачки воды из дренажного приямка во время аварии установлены насосы ПРВП 63/22,5. Для откачки случайных вод из дренажного приямка установлен насос ВКС 2/26. Насосы работают в автоматическом режиме от уровня воды в дренажном приямке. Постоянный и аварийный дренаж поступает в приёмную камеру первичного отстойника.
Окалина, выпавшая в первичном отстойнике, подвесным мостовым краном с грейфером г/п 5,0 т подаётся в бункеры для обезвоживания окалины, затем автотранспортом вывозится на утилизацию.
Для улавливания нефтепродуктов из сточных вод устанавливаются 2 маслосборных устройства производительностью 60 л/ч по маслу. Нефтепродукты собираются в баки ёмкостью по 100 л и далее вывозятся на утилизацию.
Для опорожнения отстойника при ремонте предусматриваются 2 погружных насоса ГНОМ10−10 (1 рабочий и 1 резервный).
ь Размещение отходов В ОНРС нет мест постоянного хранения отходов, только люминесцентные лампы временно хранятся в металлических контейнерах с герметическими крышками. Вывозятся они один раз в год. Максимальный объем, который можно накапливать-0,4 т. Класс опасности — 1.
Виды отходов:
В процессе работы ОНРС образуются следующие отходы:
— шлам от очистки газа (в том числе шлам газоочистки за МГР);
— окалина МНЛЗ (шлам);
— шлак печной и агрегата печь-ковш;
— просыпи сыпучих материалов;
— металлоотходы.
Шлак печной и агрегата печь-ковш образуется непосредственно при выплавке и обработке стали. Это нелетучая, твердая нерастворимая смесь. Класс опасности — 4. Не хранится. Удаляется в шлаковых чашах.
Шлам от очистки газов — это нелетучая, нерастворимая смесь. Класс опасности — 4. Не хранится, удаляется постоянно.
Просыпи сыпучих материалов — продукт потерь сыпучих материалов, связанных с технологией обработки и разливки стали. Это твердая, нелетучая, нерастворимая смесь. Класс опасности — 4. Нормативное количество образований 350 т/год. Не хранится. Удаляется ежесуточно ж/д транспортом.
Окалина МНЛЗ (шлам) образуется при охлаждении металла при непрерывном литье заготовок стали. Класс опасности — 4. Химический состав: влага — 15%, твердые — 85%. Не хранится. Удаляется постоянно по шламопроводу в отстойник и далее автотранспортом.
Металлоотходы образуются при разливке стали, подготовке и ремонте ковшей. Это нелетучая, нерастворимая, твердая смесь. Перерабатываются в цехе.
ЗАКЛЮЧЕНИЕ
Настоящий период развития черной металлургии характеризуется коренным изменением масштабов производства качественных и высококачественных марок стали, а также их доли в общем объеме производства металла. Требования новых отраслей техники к качеству металла резко возросли и продолжают возрастать.
В связи с этим становится очевидна необходимость расширения сортамента производимой продукции, направленного на производство более дорогих качественных марок сталей, востребованных на рынках металлопродукции, как внутреннем, так и внешнем.
Цель данной работы: поиск возможностей по производству в условиях ОАО «АМЗ» востребованной в настоящее время на рынке черных металлов стали марки 35ГС и разработка технологии её выплавки и разливки на МНЛЗ.
Первым этапом в цепочке производства готовой продукции в электросталеплавильном цехе № 2 ОАО «АМЗ» является получение полупродукта. Основная задача данного этапа — выплавка в ДСП — 120 полупродукта, химический состав которого удовлетворяет требованиям, обусловленным особенностями дальнейшей его обработки на агрегате печь-ковш с целью получения стали марки 65 Г. Основной особенностью на данном этапе является борьба с фосфором. В связи с тем, что при дальнейшей обработке металла в условиях восстановительного процесса на АКП возможности по удалению фосфора отсутствуют, он должен быть удален на этапе получения полупродукта до соответствующих значений с учетом небольшого последующего роста в результате внесения его в расплав ферросплавами. Требования по содержанию фосфора в полупродукте для производства стали марки 65 Г не более 0,015%. Борьба с фосфором в условиях окислительного электродугового процесса не вызывает трудностей.
На стадии внепечной обработки металла на АКП происходит доводка полупродукта до готовой стали марки 35ГС, химический состав которой удовлетворяет требованиям ГОСТ 5781. Подготовит металл к разливке на МНЛЗ.
БИБЛИОГРАФИЧЕСКИЙ СПИСОК
1. Сталеплавильное производство: Справочник: В 2 т. / Под ред. А. М. Самарина. — М.: Металлургия, 1964.-1039 с.
2. Металлургия стали / В. И. Явойский, Ю. В. Кряковский, В. И. Григорьев и др.; Под ред. В. И. Явойского и Ю. В. Кряковского. — М.: Металлургия, 1983.-583 с.
3. Кудрин В. А. Металлургия стали. — М.: Металлургия, 1989. 560 с.
4. Бигеев А. М. Математическое описание и расчеты сталеплавильных процессов. М.: Металлургия. 1982.-160 с.
5. Поволоцкий Д. Я., Рощин В. Е., Мальков Н. В. Электрометаллургия стали и ферросплавов. Учеб. для вузов. М.: Металлургия, 1995. -592 с.
6. Поволоцкий Д. Я. Основы технологии производства стали. Учеб. пособие для вузов. Челябинск: ЮуРГУ, 2000.-198с.
7. Бигеев А. М., Бигеев В. А. Металлургия стали. Теория и технология плавки стали. Учебник для вузов, 3-е издание переработанное. Магнитогорск: МГТУ, 2000.-544с.
8. Кудрин В. А., Парма В. Технология получения качественной стали. — М.: Металлургия, 1984.-320 с.
9. Воскобойников В. Г., Кудрин В. А., Якушев А. М. Общая метталургия. Учебник для вузов.М.: Металлургия:, 1998. — 768 с.
10. Проектирование систем контроля и автоматического регулирования металлургических процессов /Под ред. Г. М. Глинкова. -2-е изд.-М.: Металлургия, 1986.-352 с.
11. Автоматическое управление металлургическими процессами /А.М. Беленький, В. Ф. Бердышев и др. -2-е изд. -М.: Метал-лургия, 1989.-379 с.
12. Глинков Г. М., Косырев А. И., Шевцов Е. К. Контроль и автоматизация металлургических процессов. — М.: Металлургия, 1986.-351 с.
13. Яценко А. К., Кочо В. С. Методы оптимального управления сталеплавильными процессами.- М.: Металлургия, 1990.-213 с.
14. Безопасность жизнедеятельности / Н. Г. Занько, Г. А. Корсаков, К. Р. Малоян и др.; Под ред. Русака О. Н. -С/Пб.: 1996.-230 с.
15. Управление охраной труда на металлургическом предприятии / Н. Н. Карнаух, Ф. Ю. Авраменко, Т. Н. Хорошев и др.- М.: Металлургия, 1985.-192 с.
16. Бринза В. Н., Зиньковский М. М. Охрана труда в черной металлургии. — М.: Металлургия, 1982.-152 с.
ПРИЛОЖЕНИЕ А