Разработка эффективного метода эмульсирования полушерстяной ленты
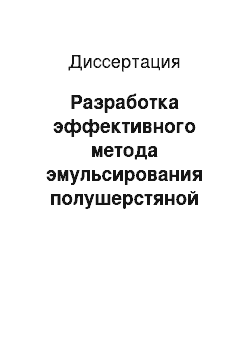
Для постановки конкретных задач исследования в первом разделе проведен анализ выполненных работ по состоянию современной технологии эмульсирования полуфабрикатов в прядениипо влиянию эмульсирования на свойства волоконпо влиянию свойств волокон на силовые поля вытяжных приборовпо движению волокон в вытяжных приборах и неровноте от вытягивания. Сырьевая составляющая себестоимости изделий, несмотря… Читать ещё >
Содержание
- 1. Анализ современной технологии эмульсирования полуфабрикатов в прядении и обоснование метода повышения ее эффективности
- 1. 1. Анализ современной технологии эмульсирования полуфабрикатов в прядении
- 1. 2. Анализ влияния эмульсирования на структуру и свойства волокон
- 1. 3. Анализ влияния свойств волокон на силовые поля вытяжных приборов
- 1. 4. Движение волокон в вытяжных приборах и неровнота от вытягивания 4″ ' ' гу
- ЛР*"'*
- Выводы по разделу
- 2. Аналитические зависимости для расчета сил, действующих на волокна в вытяжном приборе ровничной машины
- 2. 1. Классификация зон и контактов в вытяжном приборе
- 2. 2. Аналитические зависимости для сил, ускоряющих движение волокна в вытяжном приборе
- 2. 3. Аналитические зависимости для сил, сдерживающих движение волокна в вытяжном приборе
- выводы по разделу
- 3. Исследование влияния свойств волокон на закономерности их движения
- 3. 1. Общие положения методики определения параметров фрикционного взаимодействия в вытяжном приборе
- 3. 2. Определение зависимости между напряжением сжатия и плотностью продукта в поле вытягивания
- 3. 3. Исследование контактирования волокон полушерстяной ленты с плоской поверхностью
- 3. 3. 1. Методика получения отпечатков контактов волокон с плоской поверхностью
- 3. 3. 2. Определение числа контактов волокон с плоской поверхностью от коэффициента заполнения и массы образца
- 3. 4. Исследование статических сил трения между волокнами ленты
- 3. 5. Исследование конфигурации волокон в продукте
- 3. 5. 1. Метод определения характеристик элементов конфигурации волокна
- 3. 5. 2. Определение числа контактов между волокнами продукта
- 3. 6. Определение сил трения в зажиме выпускной пары
- 3. 6. 1. Определение напряжений сжатия мычки
- 3. 6. 2. Определение числа контактов между волокнами мычки и волокнами мычки с валиком и цилиндром
- 3. 6. 3. Определение удельных сил трения в эластичном зажиме
- 3. 7. Определение сил трения на неконтролируемых участках поля вытягивания и в зоне действия уплотнителя
- 3. 7. 1. Определение геометрических параметров мычки
- 3. 7. 2. Определение напряжения сжатия мычки
- 3. 7. 3. Определение числа контактов между волокнами мычки, волокнами мычки и уплотнителем
- 3. 7. 4. Определение удельных сил трения
- 3. 8. Определение сил трения в ремешковом зажиме
- 3. 8. 1. Определение числа контактов между волокнами мычки, волокнами мычки и ремешками
- 3. 8. 1. 1. Методика эксперимента по определению числа контактов волокон мычки с ремешками
- 3. 8. 1. 2. Анализ первичных данных по отпечаткам контактов волокон мычки с ремешками
- 3. 8. 1. 3. Определение числа контактов между волокнами мычки
- 3. 8. 2. Определение напряжения сжатия мычки
- 3. 8. 3. Определение удельных сил трения
- 3. 8. 1. Определение числа контактов между волокнами мычки, волокнами мычки и ремешками
- 3. 9. Определение вероятностей контактирования между волокнами мычки, волокнами мычки и рабочими органами вытяжного прибора
- 3. 9. 1. Определение вероятностей контактирования волокон мычки с рабочими органами
- 3. 9. 2. Определение вероятностей контактирования волокон с медленно и быстро движущимися волокнами мычки, вероятностей нахождения волокна в центральной и периферийной областях мычки
- 3. 10. Определение сил трения, действующих на волокна разной длины в вытяжном приборе
- 3. 11. Сравнительный анализ закономерностей движения волокон с разными свойствами
- выводы по разделу 4. Разработка метода изменения свойств волокон ленты путем пенного эмульсирования
- 4. 1. Обоснование места пенного эмульсирования на машинах ровничного ассортимента
- 4. 2. Определение пенообразующих свойств эмульсии
- 4. 3. Разработка и испытание лабораторной установки для пенного эмульсирования ленты
- 4. 4. Устройство, работа и лабораторные испытания опытного образца пеногенератора
- 4. 5. Испытание опытного образца пеногенератора в производственных условиях
- 4. 6. Совершенствование метода пенного эмульсирования
- 4. 6. 1. Исследование массы и числа капель эмульсии, полученных новым способом
- 4. 6. 2. Исследование влияния давления воздуха, уровня эмульсии и концентрации ПАВ в ней на расстояния между калиброванными пленками
Разработка эффективного метода эмульсирования полушерстяной ленты (реферат, курсовая, диплом, контрольная)
Главная задача текстильной промышленности России — повышение конкурентоспособности изделий, основными составляющими которой являются качество продукции и ее стоимость.
Качество продукции зависит прежде всего от сырья, из которого она вырабатывается, и технологии выработки пряжи, ткани и трикотажа.
Сырьевая база шерстяной промышленности России за 1991 — 2000 гг. подверглась существенным изменениям:
— радикально изменился ассортимент шерсти, поступающей на предприятия отрасли, из-за прекращения закупок ее по импорту и перехода территорий с развитым овцеводством под юрисдикцию государств СНГ;
— снизилось качество шерсти вследствие недостаточно четкого соблюдения стандартов в части качества рассортировки, увеличилась доля шерсти с большим содержанием растительных примесей;
— повысилась доля химических волокон в смесях с шерстью.
Сырьевая составляющая себестоимости изделий, несмотря на рост стоимости энергоносителей, продолжает оставаться высокой из-за высоких цен на волокна (цена 1 кг шерсти меринос 64к, I, н. составляла в марте 2000 г. -103,6 руб.). В связи со сказанным технология прядения должна предусматривать меры по рациональному использованию перерабатываемого сырья.
Важнейшим фактором, снижающим эффективность технологии прядения, является неровнота полуфабрикатов и пряжи по толщине и другим свойствам, которая ведет:
— к их повышенной обрывности в прядении, снижению производительности труда и оборудования, повышению отходов и снижению выхода пряжи из исходного сырья;
— к снижению качественных показателей пряжи, ее сортности и стоимости;
— к повышению отходов, снижению производительности оборудования и труда в ткачестве и трикотажном производстве, снижению качества готовых изделий.
Главным источником неровноты продуктов прядения является несовершенство технологических процессов, среди которых типичным в гребенной системе прядения тонкой шерсти является процесс вытягивания полупродуктов. Негативные последствия неровноты проявляются наиболее резко при вытягивании ленты, ровницы на заключительных стадиях технологии пряденияна ровничных и прядильных машинах, на которых продукты подвергаются резкому утонению.
Известно [1], что неровнота обладает свойством аддитивности, и в не-ровноту продукта после его вытягивания в качестве компоненты входит в видоизмененной форме неровнота от вытягивания соответствующего технологического перехода.
Среди неровнот по свойствам продуктов неровнота по толщине является главной причиной неровноты по крутке, разрывной нагрузке и по удлинению пряжи [2, 3], предопределяет возникновение резких утолщений и утонений (скрытых пороков) пряжи. Неровнота от вытягивания, проявляющаяся в виде колебаний толщины продукта вдоль его длины, вызвана в значительной мере соответствующей закономерностью движения волокон в вытяжном приборе.
Закономерность движения волокон в вытяжном приборе, которая характеризуется положением в поле вытягивания переднего кончика волокна утоняемого продукта в момент его перехода со скорости питающей на скорость выпускной пары, является следствием действующих на волокно сил трения. Часть этих сил являются ускоряющими и стремятся придать волокну скорость выпускной пары, а часть — тормозящими, удерживающими волокно на скорости питающей пары. Равенство этих сил при некотором положении волокна в поле вытягивания и предопределяет момент смены его скоростей и координату переднего кончика относительно, например, диаметральной плоскости выпускной пары вытяжного прибора.
Таким образом, процесс вытягивания должен быть организован так, чтобы действующие на волокно в вытяжном приборе силы минимизировали неровноту от вытягивания через соответствующую закономерность движения волокон.
Силовые поля вытяжных приборов могут формироваться различными методами:
— устройством и конструкцией вытяжного прибора;
— технологическими параметрами работы этого механизма;
— свойствами волокон.
В данной работе в качестве метода изменения силовых полей вытяжного прибора принят метод целенаправленного изменения свойств волокон путем их эмульсирования.
Целью данного исследования является разработка эффективного метода эмульсирования полушерстяной ленты, утоняемой на ровничной машине для снижения неровноты, скрытых пороков и обрывности пряжи в прядении.
Для постановки конкретных задач исследования в первом разделе проведен анализ выполненных работ по состоянию современной технологии эмульсирования полуфабрикатов в прядениипо влиянию эмульсирования на свойства волоконпо влиянию свойств волокон на силовые поля вытяжных приборовпо движению волокон в вытяжных приборах и неровноте от вытягивания.
Установлено, что:
— применяемые технологии эмульсирования не являются в достаточной мере I обоснованными, так как не учитывают конкретные цели и условия переработки полуфабрикатов прядения на разных стадиях технологического процесса;
— свойства волокон (извитость, жесткость и другие), изменяющиеся под действием эмульсирования, влияют на силовые поля вытяжных приборов, а значит, на закономерность движения волокон в вытяжных приборах, неров-ноту выпускаемого полупродукта и качество конечного продукта — пряжи;
— эмульсирование, как способ модификации свойств волокон, до настоящего времени не использовался применительно к полушерстяному продукту на заключительной стадии технологического процесса (ровничный переход);
— применяемые устройства эмульсирования неудобны в работе из-за налипания жировых компонентов эмульсии на поверхности форсунок, дисков, валиков и не отвечают принципу универсальности, то есть не могут быть применимы для обработки различных полуфабрикатов прядения.
Исходя из вышесказанного, метод обоснования эмульсирования лент, утоняемых на ровничной машине должен включать в себя:
— разработку аналитических зависимостей для определения сил, действующих на волокна в вытяжном приборе ровничной машины;
— проведение экспериментов для нахождения параметров, входящих в аналитические зависимости;
— расчет сил, действующих на волокна в вытяжном приборе ровничной машины, при утонении эмульсированной и неэмульсированной лент и прогнозирование закономерности движения волокон;
— разработку устройства для локального эмульсирования лент и оценку эффективности этого процесса.
Разработке аналитических зависимостей для расчета сил, действующих на волокна в вытяжном приборе ровничной машины, посвящен второй раздел работы. Обоснованы аналитические зависимости для сил, действующих на волокна в вытяжном приборе ровничной машины РМ- 3 фирмы «Шлюмберже».
Установлено:
— поле вытягивания вытяжного прибора ровничной машины РМ-З представляет совокупность девятнадцати зон с повторяющимися конструктивными элементами контроля за движением волокон;
— эти зоны можно классифицировать и выделить из них восемь типичных, в которых силы, действующие на волокна, описываются определенными аналитическими зависимостями.
Эти зависимости основаны на известных, но модифицированных применительно к вытяжному прибору, формулах, при этом были использованы современные методы математического анализа, сведения из областей материаловедения, сопротивления материалов, теории машин и механизмов.
Полученные аналитические зависимости позволяют оценить силы, действующие на волокна, в поле вытягивания вытяжного прибора и, следовательно, прогнозировать закономерности движения волокон в зависимости от их свойств, изменяемых путем эмульсирования.
Для использования полученных зависимостей в практических целях необходимо знание входящих в них параметров. Определение этих параметров было задачей третьего раздела работы.
Объект исследования являлась полушерстяная лента с последнего перехода ленточных машин ровничного ассортимента, выработанная по технологии ЗАО «Фряновская фабрика».
Расчетно-экспериментальными методами были определены:
— напряжение сжатия мычки в поле вытягивания;
— число контактов между волокнами, а также волокнами и рабочими органами, приходящееся на 1 мм длины волокна в поле вытягивания;
— эмпирические характеристики фрикционного процесса (в соответствии с известной [4] формулой Линкольна);
— вероятности контактирования волокон с быстро, медленно движущимися волокнами и с поверхностями цилиндра, валика выпускной пары, ремешками и уплотнителем мычки.
Нахождение этих параметров базировалось на методах, разработанных на кафедре технологии шерсти МГТУ им. А. Н. Косыгина и применяемых в учебно-исследовательском комплексе «Фрикционные процессы в прядении» для определения [5]:
— напряжения сжатия продукта в зависимости от его плотности;
— числа контактов волокон ленты с плоской поверхностью;
— статических сил трения между волокнами ленты;
— числа контактов между волокнами ленты (расчетный метод) на основе экспериментально оцениваемых характеристик конфигурации волокон;
— напряжений сжатия продукта в эластичном зажиме вытяжного прибора;
— оптимальной функции движения волокон.
В рамках данного исследования разработан и применен метод определения напряжений сжатия в ремешковом зажиме. Этот метод основан на оценке числа контактов волокон мычки с ремешками и моделировании сжатия мычки на стенде, позволяющем определять напряжение сжатия от числа контактов с плоской поверхностью.
Полученные данные позволили:
— рассчитать статические и динамические силы, действующие на волокна в вытяжном приборе ровничной машины;
— прогнозировать закономерности движения волокон в вытяжном приборе и сравнить эти закономерности с оптимальной.
На основе этих результатов установлено, что эмульсирование лент 0,5%-ым водным раствором коприна-А при проценте нанесения, равном 3%, способствует улучшению закономерностей движения волокон разных длин и, следовательно, создаются предпосылки для снижения неровноты пряжи, выработанной из эмульсированной ленты.
Полученные результаты позволяют прогнозировать эффективность метода эмульсирования лент.
В четвертом разделе работы разработано новое устройство для нанесения эмульсии на ленту и изменения свойств ее волокон, для чего:
— создана лабораторная установка, позволяющая экспериментальным путем обосновать выбор важнейшего элемента устройства для эмульсирования лент в пенной среде — дискретизатора воздуха;
— изучены пенообразующие свойства эмульсии;
— разработана конструкция, изготовлено и апробировано в лабораторных условиях опытное устройство для пенного эмульсирования лент;
— проведена апробация метода эмульсирования лент в производственI ных условиях ЗАО «Фряновская фабрика».
Эффективность разработанного метода эмульсирования полушерстяных лент характеризуется снижением характеристик неровноты по физико-механическим свойствам пряжи от 5,4% до 18,3% (отн.) — скрытых пороков в пряже — на 33% (отн.) — обрывности пряжи на прядильных машинах — на 35% (отн.).
ВЫВОДЫ ПО РАБОТЕ.
1. Разработан метод эмульсирования полушерстяной ленты, обеспечивающий снижение неровноты по свойствам пряжи, числа пороков и обрывности ее на прядильной машине.
2. На основе анализа литературных источников установлено: отсутствует научно обоснованный метод проектирования технологии эмульсирования полушерстяных лент на заключительных стадиях их обработки, ориентированной на снижении неровноты пряжи и ее обрывности на прядильных машинахобосновано направление исследования, включающее:
— разработку теоретических положений, позволяющих рассчитывать силы трения, действующие на волокна в процессе вытягивания;
— обоснование параметров, входящих в указанные закономерности;
— расчет сил, действующих на волокна, и прогнозирование закономерностей их движения, что позволяет обосновать технологию эмульсирования, как способ изменение свойств волокон;
— разработку нового способа эмульсирования.
3. Разработана классификация контрпар трения в вытяжном приборе ровничной машины с сучильными рукавами фирмы «Шлюмберже» модели БМ — 3 (Франция), которая с наибольшей полнотой учитывает имеющиеся в вытяжном приборе фрикционные взаимодействия, обусловленные конструкцией и технологическим режимом работы вытяжного прибора.
4. Обоснованы аналитические зависимости, учитывающие условия процесса вытягивания в вытяжном приборе рассматриваемого типа, в том числе: напряжение сжатия мычкичисла контактов между волокнамичисла контактов между волокнами и поверхностями рабочих органоввероятности расположения волокон в разных зонах по сечению мычки (центральная и периферийная зона) — вероятности контактирования волокон с различными рабочими органами (валиком, цилиндром, ремешками, уплотнителем), вероятности контактирования с медленно и быстро движущимися волокнами.
5. Разработан метод определения напряжений сжатия и числа контактов волокон мычки с поверхностями рабочих органов.
6. В различных сечениях поля вытягивания определены: напряжения сжатия волокнистой мычки (методом численного моделирования, расчетным методом и экспериментально) — число контактов на 1 мм длины волокнаэмпирические коэффициенты, используемые в аналитических зависимостяхвеличины, отражающие вероятностный характер процесса вытягивания.
7. Проведен расчет сдерживающих и ускоряющих сил трения, действующих на волокна в вытяжном прибореобоснованы закономерности движения для волокнистой ленты, выработанной по обычной технологии и ленты подвергнутой эмульсированию.
8. Проведено прогнозирование закономерностей движения волокон в процессе вытягивания в вытяжном приборе ровничной машины при изменении свойств волокон методом эмульсирования и их сравнение с оптимальной функцией движения волокон.
9. Обоснован метод эмульсирования полушерстяной ленты, включающий: разработано устройство для пенного эмульсирования полушерстяных лентпроведена производственная апробация устройства и технологии эмульсированияразработаны предложения для дальнейшего совершенствования метода эмульсирования.
Эффективность применения метода характеризуется снижением пороков в пряже на 33% (отн.) — ее обрывности — на 35% (отн.) — неровноты по свойствам от 5,4 до 18,3% (отн.).
Список литературы
- Севостьянов А.Г. Методы исследования неровноты продуктов прядения. М.: Ростехиздат, 1962.-c.386.
- Протасова В.А., Белышев Б. Е., Капитанов А. Ф. Прядение шерсти и химических волокон. М.: Легпромбытиздат, 1988, — 334с.
- Протасова В.А., Капитанов А. Ф. Исследование взаимосвязей свойств пряжи //Известия вузов. Технология текстильной промышленности. № 5,1985.
- Мортон В.Е., Хёрл Д.В. С. Механические свойства текстильных волокон. -М.: Легкая индустрия. 1971. — 182 с.
- Капитанов А.Ф. Фрикционные процессы в прядении. /Лабораторный практикум. М.: МГТУ им. А. Н. Косыгина. — 2000. — с.22
- Гусев В.Е., Музылев Л. Т., Эммануэль М. В., Слываков В. Е. Прядение шерсти и химических волокон. М.: Легкая индустрия, 1974, — 551с.
- Протасова В.А., Белышев Б. Е., Панин П. М., Хутарев Д. Д. Прядение шерсти и химических волокон. М.: Легпромбытиздат, 1987, — 296с.
- Anthony P. Pierlot. Water in Wool. //Textile Research Journal.- V 69. -N2.-1999, — pp.97−103.
- Панин П.М., Падегимас В.-С.Б. Замасливание и увлажнение волокон в шерстопрядении. -М.: Легпромбытиздат, 1986.- 175с.
- Перепелкин К.Е. Структура и свойства волокон. М.: Химия, 1985, — 208с.
- П.Кононенко Т. В. Исследование технологических режимов переработки полиэфирного волокна лавсан в камвольной системе прядения. Дисс.к.т.н. М.:МТИ, 1962,-231с.
- Вспомогательные вещества для полимерных материалов. Справочник. /Под ред. К. В. Пиотровского и К. Ю. Салнис. М.: 1966.
- Пакшвер A.B. Свойства и особенности переработки химических волокон. М.: Химия, 1975, — с. 6−81.
- Данилова С.А. Разработка технологии эмульсирования химического жгута наштапелирующихмашинах. Дисс.к.т.н. М.: МГТА, 1998.- 368с.
- Капитанов А.Ф. Теоретическое обоснование и разработка способа модификации фрикционных свойств волокон в процессах прядения. Дисс. д.т.н. М.: МГТА, т:1,2, 1996.-c.666.
- Дудник А.И. Камвольное прядение. М.: Гизлегпром, 1940, — 452с.
- Патент Германии № 682 512 кл.76 В 6/01. Die Einrichtung fur die Emulsirung den Faserstoff /Tetzlaff G, Phoa T.T. (Германия).
- Дудник А.И. Гребенное прядение шерсти. М.: Легкая индустрия, 1964,-295с.
- Распыливание жидкостей /Ю.Ф. Дитякин, Л. А. Клячко, Б. В. Новиков, В. И. Ягодкин. М.: Машиностроение, 1977.- 207с.
- Канарский Н.Я. Курс суконного производства. М.: Государственное издание легкой промышленности, 1933, — 620с.
- Пат. 3 894 314 США, МКИ D 01 В 3/ 04. Treatment of spinning fibers in a textile mill /Nayfa James E (США).
- Пат. 7 518 124 Франция, МКИ D 06 Р 7/00. Procede de teinture sanseffluaents et machune pour sa realisation /Da Silva Cardona Carlos Humberto (Франция).
- Пат. 584 300 США, МКИ D 01 G 37/00. Mill fiber treatment apparatus /Nayfa James E (США).
- Пат. 744 673 США, МКИ D 06 В 1/ 02. Fluid treating system for textile fibers /Robertson James H. (США).
- A.C. 6 900 091 СССР, МКИ3 D 01 G 29/00. Устройство для эмульсирования волокнистого материала /Л.К. Колядин (СССР).
- A.C. 168 381 ЧССР, МКИ D 01 G 29/00. Zpusob nanaseni mastici avivazni nebo jine kapaliny na vlakenny material a zarizeni k provadeni tohoto zpusobu /Michal Pavel (ЧССР).
- Пат. 137 336 ПНР, МКИ D Ol G 29/00. Aparat do nattuzsczania surowca wto-kienniczego transportowanego pneumatycznie rurociagiem /Kmiecik Jozef (ПНР).
- Пат. 8 815 323 Великобритания, МКИ4 D 06 В 23/26. Apparatus for fiber preparation /Brydon Alan (Великобритания).
- A.C. 1 203 145 СССР, МКИ D 01 G 29/00.Устройство для эмульсирования волокнистого материала /В.М. Клюнин (СССР).
- A.C. 153 149 ЧССР, МКИ В 05 С 5/00. Zarizeni k nanaseni mastici emulze nebo jine tekutiny na luzkovany volny vlakenny material /Michal Pavel, Zeman Jaroslav, Matoska Jaroslav (ЧССР).1.
- Резвяков A.B. Поточные линии в прядении шерсти. М.: Легкая индустрия, 1966, — 236с.
- Пат. 2 660 763 США, кл. 19−66, 1953. Method and apparatus for applying liquids to fibers /Robinson RD (США).
- Юдаева H.C. и др. Парозамасливающее устройство //Текстильная промышленность. -№ 8, — 1990, — с.43−44.
- Клюнин В.Н., Москвин Ю. Г. Исследование характеристики распределения пневматической форсункой в системе эмульсирования волокнистой массы //Сб. научных трудов. -М., 1982.
- Пат. 3 818 863 США, МКИ В 05 С 5/ 02. Centrifugal spring apparatus /Pierre Richard St., Halpern Melvin А. (США).
- A.C. 556 200 СССР, МКИ3 D 01 G 29/00. Устройство для увлажнения волокнистого материала в процессе его обработки на текстильной машине /А.Л. Абромайтис (СССР).
- А.С. 633 944 СССР, МКИ3 D 01 G 29/00. Устройство для увлажнения волокнистого материала в процессе его обработки на текстильной машине /А.П. Алиешюс, В.-С.Б. Падегимас (СССР).
- Тихомиров В.К. Пены. Теория и практика их получения и разрушения. -М.: Химия, 1983. -255с.
- Канн К.Б. Капиллярная гидродинамика пен. Новосибирск: Наука, Сиб. Отделение, 1989. — 166с.
- Капитанов А.Ф. Теоретические основы стабильности процесса жидкостной обработки волокнистых продуктов в пенной среде //Известия вузов. Технология текстильной промышленности. № 3, — 1990, — с.84−88.
- Капитанов А.Ф., Конрад О. В., Севрюк Л. Н. Исследования работы пеноге-нератора для эмульсирования лент //Известия вузов. Технология текстильной промышленности. -№ 4, — 1988, — с.35−37.
- Капитанов А.Ф. Теоретическое обоснование условий равномерного распределения жидкости в волокнистом продукте // Известия вузов. Технология текстильной промышленности. № 6, — 1990.- с.91−94.
- Капитанов А.Ф. Теоретическое обоснование принципов автоматического регулирования процесса жидкостной обработки продуктов прядения в пенной среде // Известия вузов. Технология текстильной промышленности. -№ 5, — 1990, — с.84−87.
- Капитанов А.Ф. Оптимизация процесса жидкостной обработки волокнистых продуктов в пенной среде // Известия вузов. Технология текстильной промышленности. -№ 4, — 1990, — с.73−76.
- Капитанов А.Ф. Исследование жидкостной обработки ровницы в пенной среде // Известия вузов. Технология текстильной промышленности. -№ 1,1987.- с.37−39.
- Александер П., Хадсон Р. Ф. Физика и химия шерсти. Пер. с англ. М.: 1958.
- Feughelman М. A Two phase structure for keratin fibers //Textile Research Journal. — № 3.- 1959.- pp. 223−227.
- Denby E.F. Young’s modulus of keratin in compression //Textile Research Journal. № 1.- 1960, — pp. 69−70.
- Mc. Vitte Iody, De Barr A.E. Fibre motion in roller and apron drafting //The Journal of the Textile Institute.-№ 4.-1960.-pp. 147−156.
- King G.I. Some frictional properties of wool and hylon fibres //The Journal of the Textile Institute.-Vol.41.-№ 4.-1959.-pp.l35−144.
- Roder H.L. Measurements of the influence of finiching agents of the friction of fibres //Society of Textile and cellulose Industry, Japan.- № 16.-1960.-pp. 105, 160.
- Matsusima M., Matsuo T. Compressional resilience of blankets and carded fibre mass sourn // The Journal of the Textile Institute.-Vol.41.^-№ 4.-1959.-pp. 135 144.
- Henshaw D.E. The ole of a lubricant and its viscosity in worsted carding //The Journal of the Textile Institute.-Vol.52.-№ 12.-1961.-pp.536−556.
- Филинковская Е.Ф., Серебрякова З. Г. Текстильно-вспомогательные вещества в производстве химических волокон. М.: Химия. 1970. — с.265.
- Пакшвер А.Б., Мельников Б. Н., Усенко В. А., Кукин Г. Н., Соловьев А. Н. Свойства и особенности переработки химических волокон. М.: Химия. -1975.-c.495.
- Капитанов А.Ф., Данилова С. А., Зубарева Н. И., Матвеева И. В. Метод и результаты исследования распределения эмульсии в продуктах прядения. //Изв. вузов. Технология текстильной промышленности, № 5.-1997. с.29−32.
- Лебель В., Шуман В., Лохмюллер О. Статическое электричество при переработке химических волокон. Пер. с немец. /Лебель В., Шуман В., Лохмюллер О. 1966. с. 80.
- Ахматов A.C. Молекулярная физика граничного трения. М.: Физматгиз. -1963.-с. 472.
- Феклистов В.Н., Канн К. Б., Дружинин С. А. Пены. Получение и применение. М.: Химия. 1974. -С.180.
- Васильев H.A. Вопросы теории прядения. М.: Гизлегпром, 1932.-с.368.
- Васильев H.A. Вопросы теории прядения (опыт применения методов математического анализа к технологическим процессам прядения). //Сб. ст. /под ред. Н. В. Власова, В. Казутина, А. Брюхина. М.: — Л.: Гос. изд. легкой промышленности. -1932. -275с.
- Будников В.И. К вопросу о движении волокон в вытяжном прибо-ре.//Хлопчатобумажная промышленность. -№ 9.-1940.-с. 10
- Гинзбург Л.Н. Некоторые вопросы динамики процесса вытягивания. //Научно исследовательский сб. «Прядение». -№ 6.- 1962.-с.12−21.
- Севостьянов А.Г. Магнитные валики и силы, действующие в вытяжных приборах. -М.: Гизлегпром, 1963, — 99с.
- Отыншиев М.Б. Оптимизация процесса замасливания смесей и полупродуктов в гребенном прядении шерсти. Автореферат дисс.к.т.н.-М.: МТИ, 1985,-24с.
- Васильев H.A. Процесс вытягивания в механическом прядении. М.: 1915,-с.54.
- Зотиков В.Е. Определение коэффициента трения хлопкового волокна и сил трения в вытяжном механизме. Бюллетень НИТИ, № 3, 1934.-с.42.
- Афончиков Ф.А. Метод аналитического исследования работы вытяжных аппаратов хлопкопрядильных машин. Дисс. д.т.н. М.:МТИ, 1948.-е. 159.
- Белов М.Ф. Трение хлопковых волокон в зажиме вытяжной пары и исследование задней зоны с изогнутым полем вытяжного прибора прядильной машины. Дисс. к.т.н. М.: МТИ, 1964.-c.279.
- Севостьянов А.Г. Исследования неровноты, возникающей при смешивании текстильных волокон и при вытягивании продуктов прядения. Дисс.д.т.н.1. М.:МТИ, 1960.-с.544.
- Балясов П.Д. Применение уплотнителей мычки на ровничных и прядильных машинах. М.: Гизлегпром, 1951.-с.95.
- Балясов П.Д. Сжатие текстильных волокон в массе и технология текстильного производства. М.: Легкая индустрия, 1975.-с. 176.
- Жоховский В.В. Силы, действующие при вытягивании, и распрямленность волокон. Сб. научно-исслед. работ ТТН, вып.6,1959.-е.195−203.
- Самойлов И.А. Исследование и сравнительное испытание вытяжных приборов на прядильной машине. Тезисы доклада ЦНИХБИ, 1959.-е. 156.
- Шукуров М.М. Исследование работы вытяжных пар скоростных ленточных машин для переработки хлопка. Автореферат дисс.к.т.н. Ташкент, 1969.-c.16.
- Протасова В.А. Вопросы теории и практики процесса вытягивания. Автореферат дисс. д.т.н. М.:МТИ, 1973.-c.50.
- Капитанов А.Ф. Теоретический анализ сжатия волокнистого продукта в зажиме эластичных валиков. //Изв. вузов. Технология текстильной промышленности, № 3.-1991, с.23−27.
- Капитанов А.Ф., Крутовский В. В., Мошечков В. Б. Сжатие волокнистой ленты в зажиме эластичных валиков. //Изв. вузов. Технология текстильной промышленности, № 5.-1991, с.21−24.
- Капитанов А.Ф. Математическая база метода расчета формы и размеров сечений продукта в эластичном зажиме. //Изв. вузов. Технология текстильной промышленности, № 3. 1996. — с. 24−28.
- Левин A.A. Исследование условий зажима волокнистого продукта в вытяжных парах ленточных машин. Автореферат дисс.к.т.н. М.: МТИ, 1974.-c.16.
- Капитанов А.Ф., Трускова Н. В., Зайцева H.H. Напряжение сжатия продукта в эластичном зажиме вытяжного прибора //Известия вузов. Технология текстильной промышленности. № 5. -1999. — с. 28−31.
- Капитанов А.Ф. Метод расчета нормального давления в ремешковом зажиме вытяжного прибора. //Изв. вузов. Технология текстильной промышленности, № 2.-1995, с.17−21.
- Капитанов А.Ф., Морович В. В., Коровина О. Н., Конкина С. Г. Влияние сжимающей нагрузки на характеристики контактов волокон полуфабрикатов прядения с плоской поверхностью. //Изв. вузов. Технология текстильной промышленности, № 1 .-1994, с. 17−21.
- Капитанов А.Ф. Контактирование волокон при поперечном сжатии полупродукта параллельными поверхностями. //Изв. вузов. Технология текстильной промышленности, № 3.-1995, с.20−24.
- Капитанов А.Ф. Классификация фрикционных контактов и сил, действующих на волокна в вытяжном приборе. /Межвузовский сб. научных трудов/М.: МГТА, — 1997, — 156с.
- Капитанов А.Ф., Морович В. В., Мошечков В. Б. Напряжение поперечного сжатия полуфабрикатов прядения. //Изв. вузов. Технология текстильной промышленности, № 6.-1993, с.28−31.
- Зубарева Н.И., Люсова Н. Е., Капитанов А. Ф. Исследование фрикционных характеристик гребенной крученой ровницы. //Сб. тезисов межвузовской научно-технической конференции «НАУКА 99», Димитровград, 1999, с. 165.
- Протасова В.А., Капитанов А. Ф., Данилова С. А., Зубарева Н. И., Матвеева И. В. Метод построения случайных конфигураций волокон полуфабрикатов в условиях их поперечного сжатия. //Депонирование статьи за № 3751 пр. от 16.10.1997, с. 6.
- Гинзбург Л.Н. Процесс вытягивания в льнопрядении. //Текстильная промышленность, № 7.-1948, с. 18.
- Кузин В.А. Влияние параметров заправки ремешковых вытяжных приборов на силу вытягивания и неровноту, возникающую в процессе вытягивания. Автореферат дисс.к.т.н. М.: МТИ, 1967.-с.21.
- Ковнер С.С. Пояснения к работам профессора Васильева H.A. по теории вытягивания. //Текстильная промышленность, № 10.-1952, с.21−25.
- Ковнер С.С. К теории автоматического регулирования процесса вытягивания. М.: Гизлегпром, 1962. с. 154.
- Немура A.A. Управление процессом вытягивания. Научный ред. Кведарас Б. В. Вильнюс, 1968.-c.154.
- Зотиков В.Е. Неровнота в хлопкопрядении. Дисс.к.т.н., 1939. с. 297.
- Слываков В.Е. Третий вид движения волокон в поле вытягивания и его теоретическое обоснование, /конспект лекций/. М.: МТИ, 1978.-с.21.
- Слотинцев М.Н. Экспериментальное изучение поведения волокон в вытяжном поле. Дисс.к.т.н. М.: МТИ, 1948.-c.298.
- Спесивцева О.М. Движение хлопковых волокон в поле вытягивания. Дисс. к.т.н. М.: МТИ, 1953. с. 186.
- Юн Ден-Сек. Распрямленность волокон и ее значение в процессе вытягивания продуктов в хлопкопрядении. Дисс.к.т.н. М.: МТИ, 1956. с. 219.
- Зотиков В.Е., Будников И. В., Трыков П. П. Основы прядения волокнистых материалов. М.: Гизлегпром, 1959.-c.508.
- Зубарева Н.И., Капитанов А. Ф. Исследование движения волокон в процессе вытягивания ленты в вытяжном приборе ленточной машины. //Сб. тезисов межвузовской научно-технической конференции РосЗИТЛП. М., 1998.-c.187.
- Taylor D.S. Some observations on the movement of fibres during drafting //The Journal of the Textile Institute.-Vol.45. № 4, — 1954.-p.310.
- Taylor D.S. Some observations on the movement of fibres during drafting //The Journal of the Textile Institute.-Vol.45. № 4.- 1955.-pp.284−294.
- Севостьянов А.Г. Уравнения кривой утонения при стационарных условиях процесса вытягивания. //Изв. вузов. Технология текстильной промышленности, № 1,2, 1952.
- Севостьянов А.Г. Уравнения кривой утонения, получающейся при вытягивании продукта, неравномерного по структуре. //Изв. вузов. Технология текстильной промышленности, № 4,1959.
- Севостьянов А.Г. Уравнения кривой утонения, получающейся при вытягивании продукта, неравномерного по толщине. //Изв. вузов. Технология текстильной промышленности, № 6, 1959.
- Севостьянов А.Г. Уравнения кривой утонения при нестационарной работе вытяжного прибора. //Изв. вузов. Технология текстильной промышленности, № 1,1960.
- Духовная Г. В. Оптимизация регулируемого процесса вытягивания на ленточных машинах для шерсти. Автореферат дисс.к.т.н. Л.: ЛИТЛП, 1991.-c.17.
- Николаева В.А. Влияние способов обработки рифленых цилиндров вытяжных приборов на качество продуктов прядения и обрывность пряжи. Автореферат дисс.к.т.н. Кострома, 1975.-с.20.
- Козубенко В.А. Способы и устройства для определения нагрузки на валики вытяжных приборов машин прядильного производства. М.: 1974.-c.20.
- Маркарян С.С. Исследование параметров вытяжного прибора с контролируемым прутком скоростных ленточных машин в хлопкопрядении. М.: 1975.-c.24.
- Шукуров М.М., Мусаханов P.A. Вопросы совершенствования вытяжных приборов машин прядильного производства. Ташкент, 1991.-с.53.
- Никишин В.А., Трушина И. П. Вытяжной прибор фирмы SKF в шерстопрядении. //Текстильная промышленность, № 1.-1998, с. 24.
- Гудков Г. И., Усенко Б. В. Влияние частных вытяжек и разводок в задней зоне вытяжного прибора на качество пряжи. //Текстильная промышленность, № 1.-1998, с. 21.
- Решетников Я.Я. Ленточные машины фирмы «Ритер» гарантия конкурентоспособной продукции. //Текстильная промышленность, № 1.-1997, с. 16−20.
- Ch. Cherif, R. Achnitz, В. Wulfhorst. Neue Erkenntnisse uber Verzugsvorgange an Hochleistungs-Baumwollstrecren. //Melliand Textilberichte, № 6.-1998, s.403−407.
- Wegener W. Die Streckwerke der Spinnereimaschinen, Springer-Verlag, Berlin /Heidelberg/ New York, 1995.
- Peter Artzt, Joachim Bolze. Verzugserhohung an Ringspinnmaschinen verbessert Flexibilitat und Produktivitat im Gesamtprozess. ITB, № 1.-1998, s.39−42.
- Peter Artzt. Struktur der Verdichtungsgarne- vorteile in der Weiterverarbeitung. ITB, № 2.-1997, s.41−48.
- S. Ganzoni. Anforderungen an Strecken mit dem Ziel hoher Produktivitat. //Textile Praxis international, № 1.-1985, s.15.
- Зубарева H.H., Матвеева И. В., Капитанов А. Ф. Результаты анализа не-ровноты полуфабрикатов прядения ЗАО «Краснохолмский камвольный комбинат»., //Сб. тезисов научно-технической конференции МГТА, — М., 1998, с. 157.
- Капитанов А.Ф. Численное моделирование контактирования волокон при поперечном сжатии продукта. /Вестник МГТА.- 1995, с.30−34.
- Комягин В.Б., Коцюбинский А. О. Современный самоучитель работы на персональном компьютере. М.: «Триумф». — 1997. — с. 391.
- Справочник. Поверхностно-активные вещества. /Под ред. Абрамзона A.A., Гаевого Г. М., — Л.: Химия, 1979, — 376с.
- Соловьев А.Н. Измерение и оценка свойств текстильных материалов. М.: Легкая индустрия,-1966, — 210с.
- Справочник по машиностроительным материалам. Неметаллические материалы. /Под ред. Левина А. Н., Т.4, М.: Машгиз, I960.- 723с.
- Крагельский И.В. Трение волокнистых веществ. М.: Гизлегпром, 1941.-127с.
- A.C. RU 12 132 U1 Российская Федерация, 6 D 01 Н 13/30. Устройство для эмульсирования волокнистого продукта на текстильной машине/ Капитанов А. Ф., Зубарева Н. И., Струк С. А. (Российская Федерация).
- Справочник по шерстопрядению. /Под ред. В. К. Афанасьева и др., М.: Легкая и пищевая промышленность, 1983, — 488с.
- ГОСТ 6611.2−73 Определение разрывной нагрузки и разрывного удлинения нитей.
- ГОСТ 6611.3 73 Определение крутки и укрутки нитей.
- Лувишис Л.А., Биренбаум Е. И. Методы испытаний волокна, пряжи и ткани в шерстяной промышленности. М.: Легкая индустрия, 1967. — 219с.
- A.C. RU 9224 U1 Российская Федерация, 6 D 01 G 29/00. Устройство для эмульсирования ленты на текстильной машине/ Капитанов А. Ф., Зубарева Н. И., Матвеева И. В. (Российская Федерация).
- Определение тонины и длины волокон
- Определение тонины и длины волокон, составляющих ленту, производилось стандартными методами 135. Относительная ошибка этих экспериментов не превышала 5,0% при доверительной вероятности 0,95 [128]. Результаты испытаний приведены в таблицах 1−3.