Технология восстановления и упрочнения поверхностей золотников гидроусилителей рулевого управления гальваногазофазным хромированием
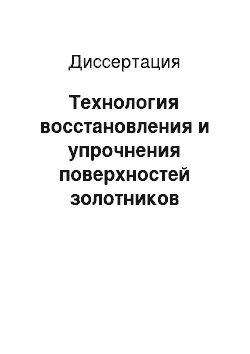
Следует отметить также, что использование традиционных методик исследования не позволяет полностью оценить качественный состав исследуемых покрытий. Поэтому, использование современных аналитических методов широкого пространственного разрешения на уровне атомных слоев и высокой элементной и фазовой чувствительности позволяет по-новому провести оценку качества покрытий. Использование приводимых… Читать ещё >
Содержание
- 1. Состояние проблемы и задачи исследований
- 1. 1. Принцип работы и причины утраты работоспособности золотниковых пар гидроагрегатов и пути снижения интенсивности их изнашивания
- 1. 2. Виды износов прецизионных пар и их характеристика
- 1. 3. Способы восстановления золотниковых пар гидроусилителей рулевого управления
- 1. 4. Цель и задачи исследования
- 2. Теоретическое обоснование восстановления золотников гидроусилителей рулевого управления гальваногазофазным хромированием
- 2. 1. Влияние подложки на сцепляемость и формирование электролитического хрома
- 2. 2. Выводы
- 3. Программа и методика экспериментальных исследований
- 3. 1. Программа экспериментальных исследований
- 3. 2. Методика экспериментальных исследований
- 3. 2. 1. Оборудование и технологическая оснастка гальванического участка. Выбор электролита и режимов нанесения электролитического хрома
- 3. 2. 2. Аппаратурное обеспечение, расчет и выбор системы нагрева образцов и деталей в реакционной камере для нанесения хромового покрытия из газовой фазы через его карбонил
- 3. 2. 3. Морфология и внутренняя структура подслоя и двухслойных гальваногазофазных покрытий
- 3. 2. 4. Обоснование необходимого комплекса методов для изучения комбинированного покрытия
- 3. 2. 5. Изучение элементного состава с применением рентгеновской спектроскопии
- 3. 2. 6. Исследования фазового состояния границы раздела с использованием рентгеновского анализа
- 3. 2. 7. Исследование микроструктуры и элементного состава границы раздела с использованием рентгеноспектрального микроанализа
- 3. 2. 8. Исследование элементного состава границы раздела с использованием масс-спектрометрии вторичных ионов с послойным анализом
- 3. 2. 9. Изучение микротвердости покрытий
- 3. 2. 10. Определение остаточных напряжений
- 3. 2. 11. Определение прочности сцепления покрытия с основой
- 3. 2. 12. Определение износостойкости покрытий
- 3. 2. 13. Планирование эксперимента по поиску оптимальных параметров процесса и построения его математической модели
- 3. 2. 13. 1. Методика поиска оптимальных параметров процесса
- 3. 2. 13. 2. Выбор параметра оптимизации
- 3. 2. 13. 3. Регрессионное моделирование и оптимизация процесса хромирования
- 4. 1. Механизм нанесения двухслойных гальваногазофазных покрытий
- 4. 2. 1. Морфология, внутренняя структура и микротвердость гальванического подслоя
- 4. 2. 2. Результаты исследования физико-механических свойств покрытий с помощью электронных, ионных и фотонных зондов
- 4. 2. 2. 1. Исследование технологии газофазного нанесения хрома
- 4. 2. 2. 2. Распределение газообразных компонентов в макродефектах покрытия
- 4. 2. 3. Физико-механические свойства двухслойных гальваногазофазных покрытий, исследуемых традиционными методами
- 4. 2. 3. 1. Сцепляемость покрытий
- 4. 2. 3. 2. Остаточные напряжения в покрытиях
- 4. 2. 3. 3. Износостойкость покрытий
- 4. 3. 1. Поиск оптимальных параметров
- 4. 3. 2. Построение математической модели процесса
- 4. 3. 3. Стендовые испытания
- 4. 3. 4. Эксплуатационные испытания
- 5. 1. Технология восстановления
- 5. 2. Экономическая эффективность способа и производственные рекомендации
- 5. 3. Выводы
Технология восстановления и упрочнения поверхностей золотников гидроусилителей рулевого управления гальваногазофазным хромированием (реферат, курсовая, диплом, контрольная)
В сельскохозяйственном производстве Российской Федерации работает в настоящее время около одного миллиона тракторов, более полутора миллионов автомобилей и значительный парк различных сельскохозяйственных машин. Однако, в федеральной целевой программе стабилизации и развития агропромышленного производства Российской Федерации на 1996 — 2000 годы говорится, что обеспеченность хозяйств основными видами сельскохозяйственной техники составляет 40.70%, сохраняется тенденция старения МТП, поскольку выпуск новых машин уменьшился в 20.80 раз, а целого ряда марок вообще прекратился, возрастает срок эксплуатации машин и оборудования. /1,2,3,4/.
Для поддержания МТП в работоспособном состоянии требуются значительные затраты, связанные с выполнением мероприятий по его техническому обслуживанию и ремонту. Требуется также развитие инженерно-технической базы агропромышленного комплекса. В условиях дефицита запасных частей, морального и физического старения сельскохозяйственной техники еще острее, чем прежде ставится задача повышения долговечности деталей, узлов и агрегатов. Разорванные экономические связи вынуждают многие ремонтные предприятия организовывать восстановление и изготовление ремонтных единиц более широкой номенклатуры. Особое значение приобретает задача качественного восстановления запасных деталей, освоения новых прогрессивных технологий.
Восстановление деталей позволяет решать вопросы обеспечения сельскохозяйственной техники качественными запасными частями, ресурс которых зачастую выше, чем у новых за счет применения прогрессивных технологий и композиционных ремонтных материалов. При этом происходит экономия топливно-энергетических, материальных и трудовых ресурсов за счет повторного, а в отдельных случаях и многократного использования изношенных деталей, восстанавливаемых на производственной базе ремонтных предприятий. Известно, что ремонтное производство всегда отличалось многообразием применяемых технологий, что вполне оправдано, так как ремонт любой машины предполагает восстановление широкой номенклатуры деталей различного функционального назначения.
В номенклатуру восстанавливаемых деталей входят и детали прецизионных пар гидроагрегатов. Прецизионные пары являются особым классом соединений, техническое исполнение которых требует особо точного технологического оборудования, оснастки, контрольного и мерительного инструмента. Для изготовления прецизионных пар требуются высококачественные легированные стали с особыми свойствами. В качестве конструкционных материалов плунжеров и золотников используются хромистые стали ШХ15, 95X18, хромоникелевая сталь 12ХНЗА, хромоникеле-вольфрамовая 18ХНВА, стали с содержанием бериллия. Применяются такие стали 38Х2Ю, 38Х2МЮА и др. Термическая обработка деталей из хромистой стали состоит из закалки и последующего низкого отпуска до HRC3 56.
Детали прецизионных пар обычно изготавливают с точностью не ниже 7-го квалитета точности и шероховатостью поверхности не выше Ra 0,63 мкм. Диаметральный зазор в зависимости от размера и назначения прецизионной пары может быть от 2 до нескольких десятков мкм. Прецизионные пары, наиболее широко применяемые в гидравлических и топливных агрегатах, имеют зазоры порядка 10−15 мкм.
Высокая точность изготовления заставляет конструкторов изыскивать новые решения, а ремонтников новые технологические процессы. Следует отметить, что ресурс прецизионных пар невелик и поэтому 3040% их количества ежегодно приходится восстанавливать. Поэтому, изыскание новых и интенсификация имеющихся технологических процессов получения износостойких покрытий для восстановления изношенных деталей прецизионных пар, улучшение физико-механических и физикохимических свойств этих покрытий является задачей весьма актуальной.
Среди методов восстановления деталей прецизионных пар должно быть обращено внимание на технологические процессы, которые, повышая прочностные характеристики деталей пар, в свою очередь, не влияли бы на микроструктуры собственно материалов деталей и позволяли наращивать значительные слои, а также являлись высокотехнологичными, экологически безопасными и предохраняли восстанавливаемые детали от коррозии. К их числу следует отнести многие виды технологических процессов, реализующихся с помощью гальваники. До последнего времени чаще всего детали прецизионных пар восстанавливали электролитическим железнением и хромированием. Большой вклад в развитие технологий восстановления деталей гальваническими покрытиями внесли: Ачкасов К. А., Батшцев А. Н., Бурумкулов Ф. Х., Воловик E. JL, Ерохин М. Н., Мелков М. П., Петров Ю. Н., Шлугер М. А. и др. Однако, несмотря на широкую гамму положительных свойств, в частности электролитического хрома, процесс остается малопроизводительным, даже при использовании в практике хромирования скоростных электролитов и интенсивных процессов. К тому же наиболее часто применяемые стандартные электролиты не обеспечивают постоянной концентрации компонентов в процессе нанесения покрытия, что часто приводит к неоднородности формируемых слоев.
Особое место в ряду технологических процессов, которые в настоящее время мало изучены и недостаточно апробированы в ремонтной практике, занимает способ осаждения износостойких покрытий из газовой фазы при термическом разложении металлоорганических соединений (МОС).
Газофазная металлизация позволяет получать покрытия с заданными свойствами при высоких скоростях осаждения на наружных и внутренних поверхностях деталей, порошковых материалах, искусственных и синтетических волокнах. Этот процесс экологически безопасен, легко поддается автоматизации.
Современная химия МОС обеспечивает синтез различных видов этих соединений практически всех металлов периодической системы Д. И. Менделеева. Однако, осаждение МОС, в том числе и газофазного хрома на подложки из конструкционных легированных сталей не обеспечивает необходимой сцепляемости покрытия.
Согласно теории ориентационного и размерного соответствия особенно благоприятными будут условия для возникновения прочной связи, если наносимый материал относится к той же группе периодической системы Менделеева, что и металл основы, имеет близкий по величине ионный радиус и одинаковые химические свойства. /74/.
В данной работе задача адгезионной прочности решается путем соединения двух различных по физической сущности технологий — гальванической и газофазной. Для получения диффузионного подслоя была использована технология пористого хромирования с последующим нанесением на этот подслой газофазного хрома.
Следует отметить также, что использование традиционных методик исследования не позволяет полностью оценить качественный состав исследуемых покрытий. Поэтому, использование современных аналитических методов широкого пространственного разрешения на уровне атомных слоев и высокой элементной и фазовой чувствительности позволяет по-новому провести оценку качества покрытий. Использование приводимых методов элементного и фазового состава с помощью РФА, РФЭС, РСМА, МСВИ позволяет проследить физико-химические характеристики на отдельных этапах разрабатываемого технологического процесса с целью его корректировки в желаемом направлении.
ОБЩИЕ ВЫВОДЫ:
1. Решена задача повышения прочностных характеристик поверхностей прецизионных деталей при их восстановлении двухслойным гальваногазофазным хромированием. Комбинация способов позволила нарастить слой гальваногазофазного хрома, достигающий 250−300 мкм, при оптимальных технологических режимах, обладающий прочностными свойствами, превышающими свойства гальванического хрома в 1,2−1,3 раза. При этом варьируя толщинами одного и другого слоев, можно получать различные по физико-механическим свойствам покрытия.
2. Обоснована высокая адгезионная способность при нанесении газофазного хрома на гальванический хром, полученный из скоростного саморегулирующегося электролита, содержащего комбинации труднорастворимых солей-катализаторов следующего состава, г/л: СгОз -230−250- SrS04 — 5−6- K2SiF6—8−10. Максимальный выход хрома по току в этом электролите составляет 23−25% на оптимальных режимах электролиза.
3. Определен оптимальный режим нанесения газофазного хромового покрытия на гальваническое покрытие: температура нагретого образца или детали в реакционной камере 450−500°С, температура сублимации 40−60°С, в условиях вакуума 2,2−3,5 Па. Установлены корреляционные зависимости между микротвердостью, износостойкостью, внутренними напряжениями и структурой покрытий.
4. Установлено, что способность водорода к концентрации как в гальваническом, так и газофазном покрытии, проявляется одинаково, он обладает высокой диффузионной подвижностью и способностью к десорбции с поверхности образцов. Что касается его высокой концентрации, то она объясняется включениями в пустотах, порах, трещинах и других дефектах покрытия. В гальваническом покрытии по мере удаления от поверхности содержание водорода уменьшается, так как его атомы переходят в газовую фазу в процессе термического воздействия при операциях газофазного нанесения. Данное обстоятельство позволяет сделать заключение о том, что при нанесении газофазного хрома на гальванический происходит процесс обезводороживания гальванического покрытия, что повышает адгезионную способность и прочность полученных покрытий.
5. С помощью диагностики поверхностей зондовыми методами установлено в газофазном покрытии наличие карбидной фазы, составляющей по объему ~ 15−20%, которая увеличивает микротвердость покрытия ~ на 25%. Следует сказать также, что углерод диффундирует и в гальванический хром, образуя карбиды в верхних слоях гальваники. Это приводит к плавному изменению физико-механических свойств двухслойного хромового покрытия сначала в объеме, а затем на поверхности. С помощью РФА также установлено, что на границе раздела гальванический-газофазный хром фазовое состояние не изменяется, что также указывает на фазовую однородность двухслойных покрытий.
6. Проведенные лабораторные, стендовые и эксплуатационные испытания двухслойных хромовых покрытий показали, что их износостойкость по сравнению с гальваническими покрытиями возрастает ~ на 2530%.
7. Разработан и внедрен в производство технологический процесс восстановления золотников ГУР тракторов МТЗ гальваногазофазным хромированием и даны практические рекомендации. При этом ресурс золотниковых пар восстановленных гальваногазофазным хромом возрастает в 2−2,5 раза по сравнению с серийными ив 1,2−1,3 раза по сравнению с восстановленными гальваническим хромом. Экономический эффект от внедрения разработанной технологии на программу в 60 тыс. золотников в год составляет 175 тыс. руб.
Список литературы
- Федеральная целевая программа стабилизации и развития агропромышленного производства в Российской Федерации на 19 962 000 годы. Утв. Указом Президента РФ от 18.06.1996 г. № 933 М., 1996.-60 с.
- Черноиванов В.И. Состояние и перспективы технического сервиса в АПК Российской Федерации. -М.: ГОСНИТИ, 1993. 67 с.
- Надежность и ремонт машин. / В. В. Курчаткин, Н. Ф. Тельнов и др., Под ред. В. В. Курчаткина. М.: Колос, 2000. — 776 с.
- Башта Т.М. Гидравлические приводы летательных аппаратов. М., «Машиностроение», 1967. 496 с.
- Белянин П.А., Черненко Ж. С. Авиационные фильтры и очистители гидравлических систем. М., «Машиностроение», 1964. 294 с.
- Никитин Г. А., Чирков С. В. Влияние загрязненности жидкости на надежность работы летательных аппаратов. М., «Транспорт», 1969. -183 с.
- Крагельский И.В. Трение и износ. М., «Машиностроение», 1968 480 с.
- Костецкий Б.И. Трение, смазка и износ в машинах. Киев, «Техника», 1970−395 с.
- Айбиндер С.Б. Холодная сварка металлов. Рига, изд-во АН Лат. ССР.
- Ахматов А.С. Молекулярная физика граничного трения. М., Физматгиз, 1963 472 с.
- Матвеевский P.M. Температурная стойкость граничных смазочных слоев и твердых смазочных покрытий при трении металлов и сплавов. М., «Наука», 1971 227 с.
- Аксенов А.Ф. Авиационные топлива, смазочные материалы и специальные жидкости. М., «Транспорт», 1970 255 с.
- Лихтман В.И., Щукин Е. Д., Ребиндер А. А. Физико-химическая механика металлов. М., Изд. АН СССР, 1962 303 с.
- Уотерхауз Р.Т. Контактная коррозия. // Сб. «Усталость металлов». М, Изд-во иностр. лит., 1961 с. 109−111.
- Лозовский В.Н. Надежность и долговечность золотниковых и плунжерных пар. М., «Машиностроение», 1971.
- Бугаев В.Н. Ремонт деталей топливной аппаратуры и агрегатов гидросистем на предприятиях Госкомсельхозтехники СССР: // Обзорная информация ЦНИТЭ и Госкомсельхозтехники СССР. М., 1985 35 с.
- Батшцев А.Н. Исследование условий ремонта деталей тракторов и с/х машин холодным осталиванием на ассиметричном переменном токе. // Автореферат кандидатской диссертации. М., 1973.
- Богатин Д.Е. Производство металло-керамических деталей. М., «Металлургия», 1968 128 с. с ил л.
- Батшцев А.Н. Восстановление деталей гальваническими покрытиями. // Учебное пособие. ВСХИЗО, М&bdquo- 1991 72 с.
- Дасоян М.А., Палыпская И. Я., Сахарова Е. В. Технология электрохимических покрытий. Л., «Машиностроение», 1989. -391 с.
- Основы ремонта машин. Под общей ред. проф., д.т.н. Петрова Ю. Н. -М., Колос, 1972, 527 с.
- Михайлова А.А., Игнатьев Р. А., Ерохин Р. Н., Горохов А. В. Восстановление изношенных деталей. -М., Россельхозиздат, 1973. 85 с.
- Левинзон А.И. Электрохимическое осаждение металлов подгруппы железа. Л., Машиномтроение, Ленинградское отделение, 1983. — 208 с.
- Черкез М.Б., Богорад Л. Я. Хромирование. — Л., Машиностроение, Ленинградское отделение, 1978. 104 с.
- Ильин В.А. Цинкование, кадмирование, оловянирование и свинцевание. Л., Машиностроение, Ленинградское отделенние, 1983. — 87 с.
- Батшцев А.Н. Пособие гальваника-ремонтника. М., Агропромиздат, 1986. — 192 с.
- Ваграмян А.Т., Соловьева З. А. Методы исследования электроосаж-денных металлов. М., Изд. АН СССР, 1960, 488 с. с ил.
- Вассерман Г. И., Тревен И. Текстуры металлических материалов. Пер. с нем. М., Металлургия, 1969, 654 с. с ил.
- Горбатый В.К. Исследование электролитического проточного хромирования, как способа упрочнения цилиндров автотракторных двигателей. // Автореферат кандидатской д иссертации, 1958.
- Дидур В.А. Исследование некоторых путей повышения ресурса распределителей тракторных гидросистем при ремонте. // Автореферат дисс. канд. тех. наук. 05.20.03. Мелитополь, 1972 24 с.
- Вороницын И.С. Исследование механических свойств хромовых покрытий, применяемых для упрочнения и восстановления деталей машин. Л., 1963.
- Левин Л.И. Теоретическая электрохимия. М., Металлургия, 1972, 543 с. с ил.
- Горбунова К.И., Данков П. Д. О сцеплении цинковых покрытий с железной основой. //Журнал «Физическая химия», 1953, т. 27, № 11.
- Левитский Г. с. Хромирование деталей и инструмента, Машгиз, 1951.
- Антипов В.В. Износ плунжерных пар и нарушение характеристик топливной аппаратуры дизелей. М., Машиностроение, 1965 132 с.
- Шлугер И.А. Ускорение и усовершенствование хромирования деталей машин. Машгиз, 1961.
- Справочник металлиста в 5-ти тамах, т. 2. Под ред. А. Г. Рахштадти и В. А. Брострема. 3-е изд., перер. М., «Машиностроение», 1976 717 с.
- Шмелева Н.М. Контролер работ по металлопокрытиям. М., Машиностроение, 1985 176 с.
- Дидур В.А., Ефремов В. Я. Диагностика и обеспечение надежности гидроприводов сельскохозяйственных машин. Киев, Техника, 1986 — 128 с.
- Черкун В.Е. Ремонт тракторных гидравлических систем. М., Колос, 1984−253 с.
- Адлер Ю.П., Маркова Е. В., Грановский Ю. В. Планирование эксперимента при поиске оптимальных условий. М., Наука, 1976 279 с.
- Шахназарова C. JL, Кафаров В. В. Методы оптимизации эксперимента в химической технологии. М., Высшая школа, 1985 327 с.
- Плешаков В.В. Повышение надежности деталей, восстанавливаемых гальваническими покрытиями. М., Россельхозиздат, 1983 56 с.
- Гаркунов Д.Н. Повышение износостойкости деталей машин. М., Машгиз, 1960.
- Гаркунов Д.Н., Лозовский В. Н., Поляков А. А. О механизме взаимного атомарного переноса меди при трении бронзы о сталь. // «Доклады АН СССР», 1960, т. 133, № 5, с. 1128−1129.
- Гаркунов Д.Н., Крагельский И. В., Поляков А. А. Избирательный перенос в узлах трения. М., «Транспорт», 1969 109 с.
- Ван Бюрн. Дефекты в кристаллах. Пер. с англ. под ред. А. Н. Орлова и В. Р. Регеля. М., изд. иностр. лит., 1962 584 с.
- Рябой А.Я., Шлугер М. А. Электроосаждение хрома из тетрахро-матных ванн. «Прикладная химия».
- Грибов Б.Г., Домрачев Г. А., Жук Б.В. и др. Осаждение пленок и покрытий разложением металлоорганических соединений. М., «Наука», 1982−322 с.
- Carlton Н.Е., Oxley N. Am. Just. Chem.End. Journal V13, № 1,1967, P.86.99, Vll № 1, 1965, P. 165.
- Saburo Konishi and Mitsuaki Tadagishi Metal Finish № 1, 1974.
- Борисов Г. А., Mooc E.H., Сыркин В. Г., Уэльский A.A., Семенова E.E. Способ нанесения хромового покрытия. // Патент № 2 109 844, 1998.
- Сыркин В.Г. Карбонильные металлы. М., «Металлургия», 1978, 256 с.
- Сыркин В.Г. Химия и технология карбонильных материалов. М., «Химия», 1972.
- Сыркин В.Г. Карбонильные соединения в науке и технике. М., «Знание», 1981, 64 с.
- Сыркин В.Г. ЖФХ, 1974, т.48, № 12, с. 2927−2930.
- Юдин И.И., Стукопин Н. И., Ширай О. Г. Организация ремонтно-обслуживающего производства в сельском хозяйстве: // Учебник/КГАУ. Краснодар, 2002, — с. 944.
- Авдеев М.В., Воловик Е. В., Ульман И. Е. Технология ремонта машин и оборудования. М., Агропромиздат, 1986. — 248 с.
- Батшцев А.Н. Обоснование рационального способа восстановления деталей // Механизация и электрификация сельского хозяйства. 1992. № 9−12.-с. 30−31.
- Бурумкулов Ф.Х., Лельчук Л. М., Денисов В. А. Методика прогнозирования остаточного ресурса по результатам ускоренных стендовых испытаний на усталость восстановленных коленчатых валов // Труды ГОСНИТИ. т. 89. -М., ГОСНИТИ, 1989. с. 51−59.
- Гурьянов Г. В. Структура и механические свойства электролитических железных покрытий. Кишинев: ИПФ АН МССР, 1989. — 63 с.
- Ермолов Е.С., Кряжков В. И., Черкун В. Е. Основы надежности сельскохозяйственной техники. -М.: Колос, 1982. -271 с.
- Лившиц Л.Г., Поляченко А. В. Восстановление автотракторных деталей. -М.: Колос, 1966.
- Серебровский В.И. К вопросу об износостойкости электролитических покрытий // Повышение эффективности функционирования АПК. -Курск: КурскаяГСХА, 1995. с. 72.,.73.
- Состояние и перспективы восстановления, упрочнения и изготовления деталей. М.: ВНИИТУВИД, 1999. — 213 с.
- Технология восстановления и упрочнения деталей машин // Под ред. М. И. Юдина и В. П. Лялякина. Краснодар: КГАУ, 2000. — 345 с.
- Определение предельных размеров сопряжений дизелей // Труды ГОСНИТИ.-Т.86.-М.: ГОСНИТИ, 1989.-е. 101−117.
- Гнеденко Б.В. Курс теории вероятностей. М.: Наука, 1956. — 400 с.
- Горелик С.С., Расторгуев И. И., Скаков Ю. А. Рентгенографический и электроннографический анализ. М., «Металлургия», 1970. 368 с.
- Голего Н.Л. Схватывание в машинах и методы его устранения. Киев: «Техника», 1965. — 231 с.
- Горбунов В.Н. Диффузионные покрытия на железе и стали. — М.: Наука, 1978.-208 с.
- Грибов Б.Г., Домрачев Г. А., Жук Б.В. и др. осаждение пленок и покрытий разложением металлоорганических соединений. М.: Наука, 1982.-322 с.
- Гришин С.Г., Плешаков В. В. и др. Программы для построения регрессионных моделей. Тезисы докладов IV Всесоюзной школы-семинара. // Теория и практика программирования на ЭВМ- серия «Мир», Душанбе, 1974.-е. 51−52.
- Дьяченко П.Е., Сушкова Т. В. Износостойкость и остаточные напряжения в поверхностных слоях металла. Вестник машиностроения, 1955, № 4.
- Джонс В.Д. Свойства и применение порошковых материалов. М.: Мир, 1965.-390 с.
- Зусманович Г. Г. Восстановление плунжерных пар химическим никелированием. // Сб. работ ВИМ, № 16, 1961.
- Исследование физико-механических свойств гальванических марганцевых покрытий применительно к восстановлению золотников распределителей гидросистемы тракторов. // Отч. № 4119, ГОСНИТИ. Лаб. № 15 по теме Р18−2, № гос. per. 72 046 178, М.: 1974.
- Иванова B.C. Роль дислокаций в упрочнении и разрушении металлов. М.: Наука, 1965.- 180 с.
- Китайгородский А.И. Рентгеноструктурный анализ мелкокристаллических и аморфных тел. М.: ГИТЛ, 1952 588 с.
- Кащеев В.Н. Абразивное разрушение твердых тел. М.: Наука, 1970 -247 с.
- Костецкий Б.И., Бертадский Л. И., Чукреев Е. Н. О явлении саморегулирования при износе металлов. // «Доклады АН СССР, 1970, т. 191, № 6, с. 1339−1342.
- Крагельский И.В., Виноградова И. Э. Коэффициенты трения. М.: Машгиз, 1962 220 с.
- Кремень З.И., Павлючук А. И. Абразивная доводка. М: Машиностроение, 1967 -115 с
- Крылов К.А., Кораблев А. И. Износ деталей авиационных агрегатов. // Сб. «Вопросы надежности гидравлических систем», вып. IV, КИИГА, 1967, с. 144−152.
- Козырев С.П. Гидроабразивный износ металлов при кавитации. М.: Машиностроение, 1974 259 с.
- Кальдераццо Ф., Эриоли Р., Натта Д. Карбонилы металлов, их получение, структура и свойства. // В к.н.Органические синтезы через карбонилы металлов. М.: Мир, 1970, с. 11−211.
- Кипнис А.Я. Карбонильная металлургия. М.: Знание, 1973, 64 с.
- Кипнис А.Я., Михайлова И. Ф., Повзиер Г. Р. Карбонильный способ получения никеля. М.: // ЦНИИ тех. экон. исслед. цвет, металлургии, 1972- 104 с.
- Кострижицкий А.И., Лебединский О. В. Многокомпозиционные вакуумные покрытия. М.: Машиностроение, 1987 — 208 с.
- Иванов В.Е., Нечипаренко Е. П., Криворучко В. М., Сагакович В. В. Кристаллизация тугоплавких металлов из газовой фазы. М.: Атом-издат, 1974−264 с.
- Корнеев В.Н. Исследование долговечности и разработка методов ускоренных стендовых испытаний распределителей тракторных гидросистем. // Автореферат диссертации. Канд. техн. наук: 05.20.03. М.: 1974.
- Козлов И.П., Юрьев Л. И., Борисов Г. А. Прочность сцепления и износостойкость хромовых покрытий, полученных из саморегулирующихся электролитов. М.: // Сборник научных трудов МИИСП, т. ХП, вып. 4, 1975.
- Козлов И.Г. Современные проблемы электронной спектроскопии. М.: Атомиздат, 1978.
- Левин Л.И. Теоретическая электрохимия. М.: Металлургия, 1972 543 с.
- Лозовский В.Н. Схватывание в прецизионных парах трения. М.: Наука, 1972−83 с.
- Лабораторно-промышленная установка карбонильной металлизации № 21−3259-КАР-90. Рабочие проекты. М.: ГНИИХТЭОС, 1985−45 с.
- Мягков В.Д. и др. Допуски и посадки. // Справочник в 2-х частях. Л.: Машиностроение, 1978.
- Миркин Л.И. Справочник по рентгеноструктурному анализу поликристаллов. М.: Физмашгиз, 1961 863 с.
- Марченко Е.А. О природе разрушения поверхности металлов при трении. М.: Наука, 1979 117 с.
- Мельник П.И. Технология диффузионных покрытий. Киев: Техниеа, 1978- 151 с.
- Конкин Ю.А., Осипов В. И., Бурдуков Ю. В. Методические указания по определению себестоимости восстановления узла, агрегата, машины. М.:МИИСП, 1983.
- Разуваев Г. А., Грибов Б. Г., Домрачев Г. А., Саламатин Б. А. Металло-органические соединения в электронике. М.: Наука, 1972 — 480 с.
- Магомедов Г. К., Сыркин В. Г., Морозова Л. В. Коолрдинационная химия, 1976, т.2, № 3, с.326−327.
- Магомедов Г. К., Френкель А. С., Сыркин В. Г. Координационная химия. 1976, т.2, № 2, с. 257−264.
- Общемашиностроительные нормативы времени на гальванические покрытия и механическую обработку поверхностей до и после покрытия. М.: Экономика, 1988 123 с.
- Осаждение из газовой фазы. Под ред. К. Пауэлла, Дж. Оксли, Дж. Блогера. Перевод с англ. М.: Атомиздат, 1970 472 с.
- Шадричев В.А. Основы выбора рационального способа восстановления автомобильных деталей металлопокрытиями. М.-Л.: Машгиз, 1962.
- Шульман А.Р., Фридрихов С. А. Вторично-эмиссионные методы исследования твердого тела. М.: Наука, 1977.
- Щуппе Г. Н. Диагностика поверхностей электронными, ионными и фотонными зондами. Рязань. 1968.
- Мальцев М.В. Рентгенография металлов. М.: ГНТИ, 1952 256 с.
- Borisov G.A., Moos E.N. Depth profiling of the Cr films on Zn-Cu Substrate.// In abs. book ESASLA 97 7-th European Confereuce on Applications of Surface and Interface Coteborg, 1997, p.285.
- Borisov G.A., Moos E.N. Gas phase Technology for Hardening Coating.// In abs. book European Materials For Advanged Metallization Workshop MAM'97, Franse, p. 218.