Ремонт сельскохозяйственных машин
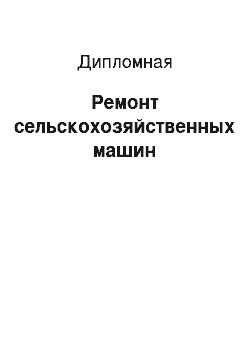
С учетом вышеизложенного принимаем за технологические базы при восстановлении корпуса перемены передач комплект баз основного производства, представляющие собой плоскость прилегания крышки коробки и расположенные в ней два базовых отверстия. При этом необходимо учесть, что использование комплекта заводских технологических баз при восстановлении корпуса КПП имеет свои особенности. Размеры базовых… Читать ещё >
Ремонт сельскохозяйственных машин (реферат, курсовая, диплом, контрольная)
Реферат
Организация, техническое обслуживание, ремонт, стенд, обкатка.
Цель проекта — совершенствование организации технического обслуживания и ремонта машин с усовершенствованием технологии ремонта КПП автомобиля ЗИЛ.
В данном дипломном проекте дана характеристика хозяйства ОАО «Барановичский райагросервис»; произведен расчет производственной программы; приведено обоснование технологии ремонта; спроектирован технологический процесс ремонта КПП; приведено обоснование трудоемкости ремонта и годовой объем работ; разработаны мероприятия по обеспечению охраны труда и противопожарные требования; предложены мероприятия по энергосбережению; произведен расчет технико-экономических показателей проекта.
Технико-экономическое обоснование принятых решений свидетельствует о том, что при капитальных вложениях 90,11 млн. рублей, годовой доход от инвестиций составит 20,5 млн.рублей. Срок окупаемости составит 7,7 лет.
Содержание Введение
1. Характеристика предприятия и обоснование темы проекта
1.1 Общая характеристика предприятия
1.2 Анализ производства продукции растениеводства
1.3 Краткие сведения развития животноводства
1.4 Анализ технологического процесса ремонта КПП
1.5 Анализ состояния технологии и организации производства
1.6 Характеристика отделения ремонта коробок перемены передач
1.7 Анализ существующей технологии ремонта КПП
1.8 Выводы и задачи проекта
2. Расчет производственной программы
2.1 Определение потребности в ремонте коробок перемены передач
2.2 Обоснование производственной программы ремонта коробок перемены передач
3. Обоснование технологии ремонта
4. Проектирование технологического процесса ремонта КПП
4.1 Разработка технологического процесса разборки КПП
4.2 Разработка технологического процесса дефектации корпуса коробки передач
4.3 Разработка технологического процесса восстановления корпуса коробки передач
4.4 Разработка технологического процесса сборки и обкатки коробки передач
5. Трудоемкость ремонта и годовой объем работ
5.1 Обоснование трудоемкости единицы ремонта
6. Проектирование участка ремонта коробок перемены передач
6.1 Режим работы предприятия и годовые фонды времени
6.2 Расчет количества рабочих
6.3 Расчет количества технологического оборудования
6.4 Расчет количества рабочих мест
6.5 Расчет площади и разработка технологической планировки участка
6.6 Расчет потребности в энергоресурсах
7. Проектирование средств механизации обкатки корпуса КПП
7.1 Обоснование актуальности разработки
7.2 Анализ прототипов
7.3 Описание конструкции и принципа работы
7.4 Технические расчеты
8. Охрана труда
8.1 Необходимость охраны труда
8.2 Анализ состояния безопасности труда в ОАО «Барановичский райагросервис»
8.3 Требования безопасности при работе с машинами семейства ЗИЛ
8.4 Организация пожарной безопасности в ОАО «Барановичский райагросервис»
9. Энергосбережение
9.1 Общие сведения
9.2 Энергосбережение при эксплуатации машинно-тракторного парка
9.3 Мероприятия по энергосбережению
10. Технико-экономическое обоснование проекта
10.1 Затраты на модернизацию стенда
10.2 Расчет инвестиций
10.3 Расчет себестоимости ремонта картера КПП
10.4 Определение отпускных цен на восстановления КПП
10.5 Оценка эффективности инвестиций
Заключение
Список использованных источников
Введение
Современное состояние инженерной службы АПК характеризуется общим положением дел в сельскохозяйственной отрасли народного хозяйства. Почти пятикратный диспаритет цен на промышленную и сельскохозяйственную продукцию привел к резкому снижению покупательной способности и рентабельности производства. Машиностроение резко уменьшило объемы производства техники для села. Морально и физически устарели машины перерабатывающих предприятий, из которых лишь 12…15% соответствует современному техническому уровню.
Уровень использования производственных мощностей объектов ремонтно-технических предприятий в настоящее время не достигает даже 50% рубежа. После 1990 г. практически прекращено серийное изготовление передвижных ремонтных мастерских и агрегатов технического обслуживания, средств диагностирования, доставки и заправки нефтепродуктов, оборудования для восстановления деталей.
При таких темпах снижения объемов работ на специализированных ремонтных предприятиях поддержание исправности машин производится силами их владельцев путем замены неисправных деталей и узлов в мастерских хозяйств в экстремальных условиях с нарушениями технологического процесса ремонта. Нарушается принятое во всем мире правило: кто реализовал, тот и отвечает за работу и качество проданных машин. Как считают специалисты, работники органов управления АПК, главный недостаток снабженческих организаций состоит в их отрыве от инженерного обеспечения непосредственно в период проведения механизированных работ в полеводстве и животноводстве.
Требуют соответствующего решения и такие перспективные направления в работе сервисных предприятий, как:
— Активное заинтересованное и обязательное участие изготовителя машин, оборудования и приборов в выполнении всего комплекса работ технического сервиса для полного, своевременного удовлетворения потребностей товаропроизводителя во всех отраслях АПК. Основной принцип — производители машин отвечают за их качество и эксплуатацию вплоть до списания. Представители заводов, фирм, их дилеры (центры фирменного сервиса) должны нести перед сельхозтоваропроизводителями полную ответственность за комплектность и качество реализуемой техники, предпродажное, гарантийное и послегарантийное обслуживание завесь срок ее службы.
— Разработку и реализацию мер по повышению производительности труда товаропроизводителя, качества и надёжности сельскохозяйственной техники и перерабатывающего оборудования;
— Оптимизацию размещения сети предприятий и производств технического сервиса по регионам страны, исключение монополии в этом деле;
— Совершенствование организационных форм и технологий ремонта и технического обслуживания машин и оборудования АПК с целью обеспечения их надёжной и эффективной работы, формирование прокатных пунктов специализированной техники, использование положительного опыта машинно-тракторных станций по выполнению сельскохозяйственных работ;
— Оказание услуг с целью продления срока службы машин, приобретение у потребителя бывшей в эксплуатации техники, её восстановление и продажа по льготным ценам с гарантией;
— Углубление кооперации между ремонтно-обслуживающим предприятиями и заводами изготовителями, применение дилерской модели в оказании услуг;
— Необходимо продолжить создание сети фирменных технических центров по обслуживанию сложных машин как одного из важнейших элементов реструктуризации технического сервиса в сельском хозяйстве;
— Наряду с развитием ремонта узлов и агрегатов машин и оборудования, а также много марочного ремонта техники ремонтные заводы должны полнее обеспечивать потребности АПК в специальном ремонтно-технологическом оборудовании, передвижных средствах заправки, диагностирования, обслуживания и ремонта техники, в слесарно-монтажном, контрольно-измерительном инструменте и приборах. Важное значение приобретает освоение и наращивание выпуска на заводах универсальных металлорежущих станков, токарных, фрезерных, расточных станков и т. д., всевозможных средств механизации для колхозов, совхозов, перерабатывающих предприятий и стройиндустрии АПК в особенности таких, которые промышленность не производит или выпускает в крайне ограниченных количествах. Необходимо предусмотреть наращивание ремонтными заводами объемов изготовления и восстановления наиболее дефицитных запасных частей.
Основой научно-технического прогресса в сфере централизованного ремонта агрегатов, машин и оборудования является повышение качества выполняемых работ на базе интенсификации производства и внедрения новых технологических процессов, развитие прямых производственных связей с заводами-изготовителями техники, создание совместных фирменных ремонтных предприятий или ремонтных предприятий-изготовителей на арендуемых площадях, применение современного металлообрабатывающего и контрольно-испытательного оборудования, всемерное развитие. методов и средств восстановления деталей с использованием упрочняющих технологий, плазменной и лазерной техники, ресурсо-, энергои трудосберегающих технологий. В области организационно-экономических отношений с заказчиками — повышение качества услуг за счет оперативности выполнения работ, транспортного обслуживания заказчика, расширения гарантийных обязательств, применения кооперативных форм производства.
— Для защиты интересов товаропроизводителей должна быть создана независимая система оценки (сертификации) качества технического сервиса, финансируемая органами государственного управления или межхозяйственными ассоциациями потребителей услуг. Требуют соответствующего решения и такие перспективные направления в работе сервисных предприятий, как организация вторичного рынка подержанной техники, восстановительный ремонт, модернизация вышедшей из строя и списанной. Анализ, проведенный ГОСНИТИ и соответствующими предприятиями и организациями в различных местах, показал, что в обслуживающей отрасли, иными словами в инженерной сфере АПК, имеют место значительные недостатки и недоработки.
1. Характеристика предприятия и обоснование темы проекта
1.1 Общая характеристика предприятия ОАО «Барановичский райагросервис» создан 27.12.12 г. путем реструктуризации КУСПТП «Барановичский райагросервис» который создан путем реорганизации БКУП «Райагропромтехника», КУП «Барановичский межрайагроснаб», КУП «Агрофирма Арабовщина», в соответствии с указом Президента Республики Беларусь указ № 40 от 27.01.2003 г.
Основной целью предприятия является осуществление хозяйственной деятельности, направленной на получение прибыли. Главной задачей предприятия является удовлетворение социальных и экономических интересов потребителей, членов трудового коллектива и собственника имущества предприятия на основе улучшения качества продукции, снижение затрат и роста заработной платы работающих.
ОАО «Барановичский райагросервис» осуществляет автотранспортные перевозки грузов и нефтепродуктов, монтаж оборудования доильных установок, монтаж зерносушильных комплексов, производит электромонтажные работы, электрофизические измерения, ремонт узлов и агрегатов к сельскохозяйственной технике, оказывает услуги по уборке зерновых культур, известкования кислых почв, химической защите сельскохозяйственных культур.
В состав предприятия входят 6 производственных и 4 сельскохозяйственных подразделения:
1. Станция технического обеспечения автомобилей (СТОА);
2. Станция технического обслуживания машинно-тракторного парка (СТО МТП);
3. Передвижная механизированная колонна (ПМК);
4. Автоколонна;
5. Механизированный отряд;
6. Отдел материально-технического снабжения и маркетинга
7. СХПУ «Северное»
8. СХПУ «Гута»
9. СХПУ «Арабовщина»
10. СХПУ «Молчадь»
Климат хозяйств ОАО «Барановичский райагросервис» вполне мягкий, с достаточным количеством осадков и благоприятен для возделывания всех традиционных для Беларуси сельскохозяйственных культур.
Рельеф — преимущественно равнинный, с небольшими перепадами высот. Почвы различны по механическому составу, степени оподзоленности и увлажнения. По механическому составу они дерновоподзолистые, супесчаные, подстилаемые мореной и обладают слабой реакцией почвенного раствора, объединены подвижными формами фосфора и калия, что указывает на необходимость систематического внесения минеральных и органических удобрений. Для сохранения восстановлению и повышению плодородия почв хозяйство проводит различные комплексы мероприятий. Для этого вносятся и закупаются органические и всевозможные комбинированные минеральные удобрения.
Основным источником водоснабжения населения и водопоя скота служат буровые скважины и шахтные колодцы, которые расположены на производственных центрах.
Естественный растительный покров на территории хозяйства представлен лесами, кустарниковой, травянистой и болотной растительностью. Заселенность и закустаренность по хозяйству составляет 10% от общей земельной площади хозяйства.
Связь между населенными пунктами хозяйства и пунктами сдачи продукций осуществляется по грунтовым и асфальтированным дорогам.
1.2 Анализ производства продукции растениеводства Результаты хозяйственной деятельности сельскохозяйственного предприятия во многом зависят от состояния и уровня развития его основных отраслей. Хотя отрасль растениеводства не является ведущей в данном предприятии, но от ее состояния во многом зависят как результаты хозяйственной деятельности, так и состояние ведущей отрасли — животноводства, которому она поставляет корма. Часть растениеводческой продукции реализуется государству, используется в качестве семенного и посадочного материала, обеспечивает другие каналы потребности. Но основная часть продукции растениеводства — корма для продуктивного общественного скота.
Составной частью системы отрасли растениеводства является структура посевных площадей, на выбор которой влияют многие факторы. Правильно установленная (оптимальная) структура посевных площадей имеет большое экономическое значение для хозяйства, так как она позволяет получать максимум продукции с единицы посевной площади и обеспечивать выход максимума стоимости валовой и товарной продукции.
В ОАО «Барановичский райагросервис» под влиянием природно-климатических и других условий хозяйствования сложилась определенная структура посевных площадей, которая претерпевает в динамике некоторые изменения с учетом меняющихся условий производства и представлена она в данных таблицы 1.1.
Наибольший удельный вес в структуре посевных площадей в среднем за последние три года занимали кормовые культуры — 60,76%.
Таблица 1.1 —Структура посевных площадей хозяйства, га
Площади | 2010 г. | 2011 г. | 2012 г. | |
Зерновых | ||||
Картофеля | ||||
Сахарной свеклы | ||||
Рапса | ||||
Льноволокна | ||||
Наибольший удельный вес в структуре посевных площадей в среднем за последние три года занимали зерновые и зернобобовые культуры — 56,8% или 2462 га. Удельный вес этой группы культур колебался по годам анализируемого периода от 61,3% (2010 г.), до 54% - в 2011 году. Из культур зернового клина удельный вес озимых и яровых культур не стабилен. За последние два года посевные площади озимых увеличились на 43 га, а яровых снизились на 104 га.
Учитывая животноводческое направление в хозяйстве, существенные площади пашни отводятся под производство кормовых культур. Причем доля кормовых культур в структуре посевов снизилась с 44,9% в 2010 году до 31,3% - в 2012 году.
В таблице 1.2 приведена динамика урожайности сельскохозяйственных культур в хозяйстве за последние три года.
Таблице 1.2 —Данные по урожайности возделываемых культур ц/га
Урожайность: | 2010 г | 2011 г | 2012 г | |
Зерновых всего: | 21,40 | 24,9 | 24,8 | |
в том числе: | ||||
СХПП «Арабовщина» | 33,5 | 30,8 | 36,5 | |
СХПП «Северное» | 24,1 | 23,7 | ||
СХПП «Гута» | 17,4 | 26,7 | 22,6 | |
СХПП «Молчадь» | 20,1 | 22,6 | 22,9 | |
Картофеля всего: | ||||
в том числе: | ||||
СХПП «Арабовщина» | ||||
СХПП «Северное» | ||||
СХПП «Гута» | ||||
СХПП «Молчадь» | ||||
Сахарной свеклы | ||||
в том числе: | ||||
СХПП «Северное» | ||||
СХПП «Гута» | ||||
СХПП «Арабовщина» | ||||
СХПП «Молчадь» | ||||
Рапса | 14,7 | 15,7 | 14,8 | |
в том числе: | ||||
СХПП «Северное» | 16,8 | 17,3 | 13,3 | |
СХПП «Гута» | 8,9 | 11,7 | 16,4 | |
СХПП «Молчадь» | 14,2 | 15,9 | 15,4 | |
Льноволокна | 7,5 | 4,9 | ||
в том числе: | ||||
СХПП «Северное» | 7,7 | 2,8 | ||
СХПП «Гута» | 6,8 | |||
СХПП «Молчадь» | 7,5 | |||
Выход к.ед.с 1га сх угодий | 26,1 | 29,9 | 28,2 | |
Анализ данных выше приведенной таблицы показывает, что уровень урожайности большинства сельскохозяйственных культур в хозяйстве за последние два года незначительно увеличился. Так, урожайность зерновых и зернобобовых культур в среднем за два года на 24,8 ц/га и 24,9 ц/га соответственно. Остается низкой продуктивность кормовых угодий.
Таблица 1.3 —Валовой сбор продукции, тонн
Производства зерн. (кукуруза) | 2010 г | 2011 г | 2012 г | |
Зерно после доработки | ||||
в том числе: | ||||
СХПП «Арабовщина» | ||||
СХПП «Северное» | ||||
СХПП «Гута» | ||||
СХПП «Молчадь» | ||||
Рапс (дораб.) | ||||
в том числе: | ||||
СХПП «Северное» | ||||
СХПП «Гута» | ||||
СХПП «Молчадь» | ||||
Сахарная свекла | ||||
в том числе: | ||||
СХПП «Северное» | ||||
СХПП «Гута» | ||||
СХПП «Арабовщина» | ||||
СХПП «Молчадь» | ||||
Картофель | ||||
в том числе: | ||||
СХПП «Арабовщина» | ||||
СХПП «Северное» | ||||
СХПП «Гута» | ||||
СХПП «Молчадь» | ||||
Льноволокно | ||||
в том числе: | ||||
СХПП «Северное» | ||||
СХПП «Гута» | ||||
СХПП «Молчадь» | ||||
Анализируя данные таблицы 1.3 можно сделать следующие выводы:
— наблюдается рост валового сбора по зерновым и зернобобовым культурам;
— по некоторым культурам наблюдается падение валового сбора, это связано как с погодными условиями, так и с уменьшением площади посевов этих культур.
1.3 Краткие сведения развития животноводства Главной отраслью животноводства в хозяйстве является мясомолочное скотоводство. Дойное стадо хозяйства насчитывало в 2010 г. 577 голов, а на выращивании и откорме содержалось на указанную дату 400 головы молодняка крупного рогатого скота. Поголовье КРС с каждым годом увеличивается — это связано с увеличением цен на производимую продукцию. О численности поголовья скота и птицы, имеющегося в ОАО «Барановичский райагросервис» дают представление материалы таблицы 1.4.
Таблица 1.4 — Поголовье скота
Показатели | 2010 г | 2011 г | 2012 г | |
Поголовье КРС | ||||
СХПП «Арабовщина» | ||||
СХПП «Северное» | ||||
СХПП «Гута» | ||||
СХПП «Молчадь» | ||||
Поголовье коров | ||||
СХПП «Арабовщина» | ||||
СХПП «Северное» | ||||
СХПП «Гута» | ||||
СХПП «Молчадь» | ||||
Из таблицы 1.4 видно, что поголовье дойного стада увеличивается, так же увеличивается и поголовье КРС на выращивании и откорме, также увеличивается поголовье птицы. Молочное стадо возрастав, по сравнению с 2010 годом, на 50,6% или 460 голов, поголовье КРС на откорме увеличилось на 34,1% или 578 голов. Это обуславливается тем, что хозяйство начало получать неплохую прибыль от реализации молока и мяса и решило расширить объемы производства и реализации.
Таблица 1.5 — Показатели эффективности животноводства
Показатели | Ед.изм | 2010 г | 2011 г | 2012 г | |
Поголовье КРС | гол. | ||||
СХПП «Арабовщина» | гол. | ||||
СХПП «Северное» | гол. | ||||
СХПП «Гута» | гол. | ||||
СХПП «Молчадь» | гол. | ||||
Поголовье коров | гол. | ||||
СХПП «Арабовщина» | гол. | ||||
СХПП «Северное» | гол. | ||||
СХПП «Гута» | гол. | ||||
СХПП «Молчадь» | гол. | ||||
Производство молока | тонн | ||||
СХПП «Арабовщина» | тонн | ||||
СХПП «Северное» | тонн | ||||
СХПП «Гута» | тонн | ||||
СХПП «Молчадь» | тонн | ||||
Удой на корову | кг | ||||
СХПП «Арабовщина» | кг | ||||
СХПП «Северное» | кг | ||||
СХПП «Гута» | кг | ||||
СХПП «Молчадь» | кг | ||||
Средн.сут. привес КРС | грамм | ||||
СХПП «Арабовщина» | грамм | ||||
СХПП «Северное» | грамм | ||||
СХПП «Гута» | грамм | ||||
СХПП «Молчадь» | грамм | ||||
Выход приплода на 100кор. | гол. | ||||
СХПП «Арабовщина» | гол. | ||||
СХПП «Северное» | гол. | ||||
СХПП «Гута» | гол. | ||||
СХПП «Молчадь» | гол. | ||||
Продукция КРС | тонн | ||||
свиньи | тонн | 0,3 | |||
Из таблицы 1.5 видно, что количество выхода телят на 100 голов коров уменьшилось. Удой на одну среднегодовую корову в 2012 году увеличился по сравнению с 2011 годом. Среднесуточный привес по сравнению с 2011 годом увеличился на 48 грамма. По сравнению с 2011 годом увеличились объемы производства молока, это связано с увеличением поголовья крупного рогатого скота. Также увеличилось количество приплода на 100 голов, что также связано с увеличением поголовья стада.
Исходя из выше сказанного можно сделать вывод, повышается и стабилизируется удои молока от коров, повышается, и стабилизируются среднесуточный привес КРС на откорме.
1.4 Анализ технологического процесса ремонта КПП В ремонтной мастерской ОАО «Барановичский райагросервис» размещены следующие участки, на которых производится ремонт коробки передач ЗИЛ:
— участок наружной очистки;
— участок разборки;
— участок очистки деталей;
— участок дефектации;
— участок комплектования;
— слесарно-механический участок;
— кузнечно-термический участок;
— сварочно-наплавочный участок;
— участок сборки;
— участок обкатки и испытания;
— участок окраски;
— ИРК.
Сварочно-наплавочный участок имеет площадь 54 м2. Он оснащен постами для ручной дуговой сварки на постоянном токе (выпрямитель ПСО-500), установками для восстановления поверхностей валов в среде углекислого газа и электроконтактной приваркой ленты на базе токарно-винторезного станка (наплавочная головка А-580 для восстановления в среде СО2 и ОКС 9862 — для приварки ленты).
Кузнечно-термический участок имеет площадь 216 м2. На участке установлены токарные, сверлильные, фрезерные, расточные, шлифовальные и другие станки, верстаки, стеллажи и другое оборудование.
В настоящее время в мастерской при восстановлении валов используется: ручная дуговая наплавка, наплавка в среде СО2, электроконтактная приварка металлической ленты.
Валы, у которых имеется деформация (прогиб), подвергаются холодной правке на прессе. Повреждение резьбы, шпоночных пазов, износ посадочных мест под подшипники, шестерни, сальники, износ шлицев на наружной поверхности и ширине шлица восстанавливают наплавкой в среде СО2. Посадочные места под подшипники, сальники восстанавливают также электроконтактной приваркой металлической ленты.
После восстановления и токарной операции производят фрезерование шлицев на горизонтально-фрезерном станке 6Н-81 с использованием дисковых фрез и делительной головки. После термообработки на установке ТВЧ ЛЗГ-67 производят шлифование наружной цилиндрической поверхности на круглошлифовальном станке 3Б151; шлицы по толщине не шлифуют из-за отсутствия оборудования. Существующая технология восстановления не дает возможности получить высокое качество, точность, шероховатость поверхности и резко ограничивает номенклатуру восстанавливаемых и изготавливаемых деталей.
Технологический процесс ремонта коробки передач начинается с поступления их на участок наружной очистки. После наружной очистки в машине 1168 ПТИ производится разборка КПП на узлы и детали, которые направляются на очистку в машину ОМ-1366Г. В машинах применяются синтетические моющие средства «Лабомит-101», «Лабомит-102», «МС-6» и другие. Разборка КПП и ее узлов производится на стендах. После очистки детали поступают на дефектацию. С участка дефектации детали, требующие восстановления, поступают на восстановление (слесарно-механический, сварочно-наплавочный, кузнечно-термический участки); годные участки — на участок комплектования, бракованные — в утиль. Из отделения комплектования детали поступают на участок сборки узлов и агрегатов. Сборка КПП осуществляется на стационарных постах. Обкатка и испытание КПП производится на стендах Н-1312 машинно-тракторного завода; окраска и сушка — на участке окраски.
Участок по ремонту КПП оснащен подъемно-транспортным оборудованием (электрокары, кран-балки), правильно выбраны и оснащены грузовые потоки. Однако ощущается нехватка современных средств контроля, малой механизации, не производится предремонтное диагностирование, не всегда соблюдается технологическая дисциплина.
1.5 Анализ состояния технологии и организации производства Поступающие на завод объекты ремонта проверяются на соответствие техническим условиям на сдачу в ремонт, и после оформления приемно-сдаточного акта, поступают на склад ремфонда. Склад ремфонда оборудован подвесным краном для разгрузки автотранспорта и установки объектов ремонта на место хранения. Со склада ремфонда двигатели, КПП, компрессоры и другие объекты ремонта с помощью межцехового транспорта поступают на участок очистки и мойки, после которого направляются на соответствующие участки ремонта. На этих участках осуществляется их разборка на узлы и детали с последующей мойкой деталей в моечных машинах.
Детали, прошедшие очистку деффектуются, и сортируются на три группы: годные, подлежащие восстановлению, утильные. Годные детали поступают на соответствующие рабочие места, где" осуществляются комплектация и сборка объектов ремонта.
Подлежащие восстановлению детали укладывают в специальные контейнеры и транспортируют на участки.
После ремонта и восстановления детали проходят контроль и поступают на сборку. При этом перед сборкой блоки цилиндров, коленчатые валы, корпусы КПП и другие корпусные детали проходят очистку, а головки блок цилиндров, кроме того, проходят очистку после, сборки и притирки клапанов.
Собранные двигатели, коробки перемены передач, раздаточные коробки, компрессоры обкатываются и испытываются, после чего подвергаются контрольному осмотру и направляются на участок окраски. После окраски объекты ремонта транспортируются на склад готовой продукции.
Анализ технологии и организации производства на ОАО «Барановичский райагросервис"показал, что на заводе недостаточно высокий уровень технологической дисциплины, отсутствуют современные прогрессивные технологии, восстановление деталей, недостает средств технического контроля, оснащение рабочих мест не соответствует современным требованиям. Все это в конечном итоге сказывается на качестве отремонтированной продукции.
1.6 Характеристика отделения ремонта коробок перемены передач В отделении ремонта КПП осуществляется разборка коробки, дефектация ее деталей, восстановление картера КПП, сборка и обкатка. Для выполнения этих работ на участке имеется соответствующее оборудование: стенды для разборки-сборки КПП, тара для деталей, стенд кантователь для корпуса КПП, стол дефектовщика ОРГ-148 801−090, контейнеры для деталей требующих ремонта и для утиля, универсальный магнитный дефектоскоп М-217, шкаф с набором инструмента дефектовщика ОРГ-1661, горизонтально-расточный станок РР-4, радиально-сверлильный станок 2А55, пресс гидравлический 208ГАРО, стенд для обкатки КПП, верстак и др.
План расстановки оборудования не в полной мере соответствует схеме технологического процесса ремонта коробки передач, что приводит к нерациональной организации перемещения грузов. Межпостовая транспортировка картера КПП осуществляется в основном при помощи кранов с электрическими талями грузоподъемностью 0,25 т.
1.7 Анализ существующей технологии ремонта КПП Технологическая последовательность ремонта коробок перемены передач на ОАО «Барановичский райагросервис» следующая.
Поступающие в отделение очищенные коробки разбираются, после чего осуществляется мойка деталей и их дефектация. После дефектации годные детали поступают на склад, негодные в утиль, подлежащие восстановлению в сварочно-наплавочное и слесарно-механическое отделение. Операции по устранению дефектов картера КПП, кроме операции окраски, выполняются непосредственно в отделении: трещины завариваются, отверстия под подшипники первичного, вторичного и промежуточного валов восстанавливаются постановкой ремонтной втулки с последующей раздачей для обеспечения плотной посадки, износ отверстий под переднюю и заднюю шейки оси блока шестерен заднего хода устраняют с помощью полимерных материалов или обработкой под ремонтный размер, риски, задиры и износ внутренних торцевых поверхностей бобышек под блок шестерен заднего хода — обработкой торцевой поверхности до устранения дефектов, либо постановкой втулки с буртиком. Резьбовые отверстия восстанавливаются постановкой ввертышей или заваркой. После восстановления корпус коробки передач обдувается сжатым воздухом и поступает на сборку. Собранная коробка обкатывается. Как видно из описания применяемой на предприятии технологии ремонта КПП не все операции, используемые для устранения дефектов, отвечают современным требованиям и, следовательно, не могут обеспечить надлежащее качество ремонта Так, восстановление отверстий под переднюю и заднюю шейки оси блока шестерен заднего хода в зависимости от величины износа применением полимерных материалов или механической обработкой по ремонтный размер, не обеспечивает в первом случае требуемой долговечности восстановляемым отверстиям, во втором случае ухудшает условия взаимозаменяемости деталей. Применение сварки при устранении дефектов КПП вызывает возникновение остаточных напряжений в материале детали (Чугун СЧ18), и связанных с этим отрицательных явлений. Восстановление резьбовых отверстий постановкой ввертышей трудоемко, а посадочных отверстий пол подшипники постановкой ремонтных втулок с последующей раздачей малоэффективно из-за быстрого нарушения посадки втулок в корпусе.
Следует отметить невысокий уровень механизации и автоматизации как основных производственных процессов, так и вспомогательных.
Характерной особенностью предприятия являются относительно большая насыщенность нестандартным оборудованием с низким остаточнымресурсом.
1.8 Выводы и задачи проекта Анализ состояния технологии и организации ремонта КПП ЗИЛ на ОАО «Барановичский райагросервис» показал, что их уровень не отвечает современным требованиям. Так трещины в картера заваривают электродуговой сваркой электродами, посадочные отверстия под подшипники восстанавливают постановкой ремонтной втулки, отверстия под оси — применением полимерных материалов. Эти способы являются малопроизводительными и не могут обеспечить требуемого качества ремонта, кроме того технологии с применением полимерных материалов оказывают отрицательное воздействие на экологию и здоровье производственных рабочих.
В отделении ремонта КПП недостает средств технического контроля, отсутствуют прогрессивные и технически совершенные виды оборудования, невысокий уровень механизации и автоматизации основных и вспомогательных производственных процессов.
Совершенствование технологии ремонта КПП позволит повысить качество отремонтированных изделий, производительность труда, улучшить условия труда и экологическую обстановку на предприятии.
Для этого в проекте необходимо решить следующие задачи:
— обосновать оптимальную производственную программу ремонта КПП;
— разработать технологический процесс ремонта, в котором предусмотреть применение современных технологических решений и оборудования;
— определить трудоемкость ремонта и годовой объем работ отделения ремонта КПП;
— произвести расчет необходимого количества рабочих, оборудования и рабочих мест;
— рассчитать площади, выполнить компоновку производственногокорпуса и расстановку технологического оборудования в отделении;
— разработать мероприятия по охране труда и окружающей среды;
— сделать технико-экономическое обоснование предлагаемых в проекте решений.
— обеспечивающих технологическое формирование ремонтируемых объектов в строгом соответствии с требованием нормативно-технической документации.
Таким образом, совершенствование технологии ремонта агрегатов автомобилей является актуальным направлением, способствующим повышению качества ремонта и эффективности ремонтного производства.
2. Расчет производственной программы
2.1 Определение потребности в ремонте коробок перемены передач ОАО «Барановичский райагросервис» осуществляет ремонт автомобилей и агрегатов к ним для хозяйств агропромышленного комплекса.
Потребность в капитально отремонтированных агрегатах определим исходя из наличия машин в этих хозяйствах. Парк машин рассчитываем по нормативам потребности и размерам пахотных земель, используя следующую зависимость.
Nм =10-3Sрг (2.1)
где Sp — площадь пахотных земель (га), для Брестской области значение Sp = 32 000 га [22];
гmi — норматив потребности машин i-ой марки на тысячу га пашни;
Норматив потребности машин принимаем по данным.
Потребность в автомобилях ЗИЛг = 0,6 на тысяч га;
ЗИЛ-555 г =1,8;
ГАЗ-53 — г = 1,26;
ГАЗ-52 — г = 1,5;
ГАЗ-САЗ-53 — г = 3,7.
Тогда количество автомобилей ЗИЛ в агропромышленных предприятиях области будет равным.
N3ИЛ-5301 =10-3· 32 000·0,6=19,2ед.шт.
Аналогично рассчитываем наличие автомобилей других марок иполучаем:
N3ИЛ-5301= 19 шт.;
NГАЗ-53 = 40 шт.;
NЗИЛ-555 =58шт.;
NГАЗ-52 = 48 шт.;
NСАЗ-53 = 118шт.
Исходя из общего количества машин в зоне обслуживания ремонтного предприятия, коэффициентов охвата ремонтом, зонального и учитывающего возрастной состав парка автомобилей определим потребность в ремонте коробок перемены передач по маркам машин, используя следующую формулу:
NKРKПП = Nmik1?oik3kb(2.2)
где k 1 — количество агрегатов на автомобиле;
?oi — коэффициент охвата капитальным ремонтом коробокавтомобилей i-ой марки для капитальных и текущих ремонтов автомобилей;
к3 — зональный коэффициент; к = 1,1 [20]
кь — коэффициент, учитывающий возрастной состав машин в парке;
Значение коэффициента охвата капитальным ремонтом принимаем по данным [2]:
?oзил-5301=0,21;
?oгаз-52 =0,25;
?oзил-131 =0,21;
?oзил-555 =0,23;
?oгаз-53 =0,17;
?oсаз-53 =0,27;
Подставляя исходные данные в зависимость (2.2) получим:
ЗИЛ-5301
NкрКПП= 5 шт.
ГАЗ-53
N крКПП = 9 шт.
ЗИЛ-555
N крКПП = 18 шт.
ЗИЛ-131
NкрКПП= 5 шт.
ГАЗ-52
NкрКПП= 16 шт.
САЗ-53
NкрКПП= 42шт.
2.2 Обоснование производственной программыремонта коробок перемены передач Годовая производственная программ предприятия для выполнения последующих технологических расчетов должна быть приведена к одному агрегату-представителю. Агрегатом-представителем в нашем случае принимается коробка перемены передач автомобиля Зил-130.
Производственная программа ремонтного предприятия определяется по формуле:
Npn =NкрКПП +? NкрКППkпрikoci (2.3)
гдеkoci — коэффициент охвата специализированным ремонтом КПП автомобиля i-ой марки; на перспективу принимается для агрегатов всех автомобилей равным koci = 1;
kкрКППi — количество капитальных ремонтов коробок перемены передач автомобиля i-ой марки;
kKpi — коэффициент приведения коробки автомобиля i-ой марки к соответствующему агрегату автомобиля ЗИЛ-5301[2]
кпр ГАЗ-53=0,86;
кпр САЗ-53=0,86;
кпр ГАЗ-52=0,76;
Для коробок автомобилей марок ЗИЛ к пр = 1.
Подставляя исходные данные в зависимость (2.3) произведем расчетпроизводственной программы предприятия по ремонту КПП автомобилей.
N=5+5+18+9· 0,86+42·0,86+16·0,74 = 84 пр. рем.
С учетом выполнения работ по капитальному ремонту коробок перемены передач для парка автомобилей фермерских хозяйств принимаем программу ремонта КПП на ОАО «Барановичский райагросервис» равную 100 приведенных к КПП ЗИЛ-5301 ремонтов.
3. Обоснование технологии ремонта Выбор технологии ремонта определяется конструктивно-технологическими характеристиками объектов ремонта, объемом производственной программы, наличием оборудования для выполнения работ и расстоянием до специализированных предприятий.
К методам ремонта относятся с учетом принадлежности ремонтируемых составных частей к определенному экземпляру изделия необезличенный и обезличенный; исходя из организации выполнения ремонта — тупиковый и поточный.
При необезличенном методе ремонта сохраняется принадлежность восстановленных деталей и составных частей к объекту ремонта. При обезличенном методе ремонта принадлежность составных частей к определенному экземпляру изделия не сохраняется. При сборке они устанавливаются на очередную машину вне зависимости от того с какой были сняты. Из-за чего снижается общая ее надежность, так как в сопряжение между собой вступает большое количество неприработанных деталей с различными остаточными ресурсами. Этот метод применяется при значительных программах на специализированных ремонтных предприятиях, обеспечивающих глубокий контроль соответствия деталей техническим требованиям.
Исследованиями установлено, что обезличенный капитальный ремонт эффективен в том случае, если все характеристики надежности восстанавливаются не менее чем на 70…80%. При уровне 60…70% эффективность капитального ремонта близка к нулю, при уровне менее 60% он просто экономически не оправдан.
Поточный метод ремонта применяется на ремонтных предприятиях со значительной производственной программой, позволяющей выполнить производственный процесс на специализированных рабочих местах с определенными технологическими последовательностью и ритмом поточное производство специализируется на одном или нескольких объектах. Этот метод наиболее производителен, так как за каждым постом поточной машины закрепляется ограниченное количество операций технологической оснастки и оборудования.
При небольших программах на рабочих местах выполняются разнообразные ремонтные работы. Рабочие места в этом случае носят широкоуниверсальный характер. При этом разборку, сборку машины и ряд специализированных робот выполняют группы исполнителей. Ремонт же отдельных узлов, агрегатов и базовых деталей производят на специализированных рабочих местах, оснащенных необходимым оборудованием и инструментом. Размещение рабочих мест на участках согласовывают с общим технологическим процессом.
Таким образом с учетом величины производственной программы и целью обеспечения высокого качества отремонтированных КПП для условий райагросервиса принимаем тупиковый необезличенный метод ремонта.
4. Проектирование технологического процесса ремонта КПП Объектом разработки технологического процесса является сборочная единица, поэтому в процессе его проектирования необходимо разработать технологические процессы разборки, дефектации, восстановления, сборки, обкатки и испытания отремонтированной коробки перемены передач.
4.1 Разработка технологического процесса разборки КПП Основными этапами проектирования являются разработка схемы разборки с выделением последовательностей технологического процесса, выбор оборудования и инструмента, нормирование операций и оформление документации единичного технологического процесса.
Поступающие в ремонт коробки перемены передач должны быть подвергнуты наружной очистке. На наружных поверхностях коробок после очистки не должно быть грязи, остатков смазки и смолистых веществ.
Технология разборки должна исключать повреждаемость деталей и сборочных единиц.
При разборке узлов необходимо пользоваться съемниками, приспособлениями и специальным инструментом, обеспечивающими центрирование снимаемой детали и снятие ее без разрушения. Подшипники с валов должны сниматься на прессе, при этом передача усилия через тела вращения не допускается. При выпрессовке подшипников, сальников, уплотнений из стаканов и корпуса выколотки с более мягкими наконечниками, а также монтажные приспособления, обеспечивающие выполнение заданных технологических операций.
При отвертывании крепежных деталей грани головок болтов, винтов и гаек не должны сниматься.
При разборке коробки передач разукомплектовка (обезличивание) основных приработавшихся деталей (корпусов со стаканами, цилиндрических зубчатых пар, нелицевых соединений), годных для дальнейшей работы агрегата не допускается.
Подъем агрегатов, узлов и деталей (весом более 20 кг) должен выполняться с помощью специально предусмотренных схваток, захватов и скоб, предохраняющих детали от смятия, сколов, излома и других дефектов. Захват детали за рабочие поверхности не допускается.
Разборочно-моечные участки должны иметь тщательно разработанную технологию, предусматривающую порядок разборки, установки и размещения в таре деталей, направляемых на мойку, а также маршруты движения и режимы транспортирования деталей.
При разработке схемы разборки представляем в условном изображении рекомендуемую для конкретных условий ремонтного производства очередность снятия разборочных групп, подгрупп и деталей с ремонтируемого объекта.
На схеме разборки показывается сборочная единица. Непосредственно из сборочной единицы демонтируются разборочные группы, которые располагаются в очередности их снятия. Разборочные группы разбираются на детали. Детали также изображаются на схеме с учетом очередности их снятия. Заканчивается схема разборки изображением базовой детали.
С учетом этих требований схема разборки коробки перемены передач ЗИЛ будет строиться в следующий последовательности.
Схема строится в направлении слева направо, и начинается с условного изображения коробки передач в сборе с указанием номера по каталогу. Со сборочной единицы первоначально снимается крышка коробки, затем крышка вала первичного, шарикоподшипники с валом первичным, которые являются разборочными группами и обозначаются Рб-1, Рб-2 и т. д. Номера разборочных групп соответствуют последовательности снятия их со сборочной единицы. После них снимаются разборочные группы и соответственно обозначаются — крышка, вал вторичный, блок шестерен заднего хода, крышки и вал промежуточный. Заканчивается схема разборки изображением картера КПП с указанием его номера по каталогу. Далее разборочные группы разбираются на детали, на схеме показываемые в условном изображении и с номером по каталогу. Разборка каждой разборочной группы заканчивается условным изображением и указанием номера по каталогу базовой детали. По разработанной схеме разборки оформляем технологические процесс разборки КПП.
При выборе технологического оборудования и оснастки для разборки КПП руководствуемся рекомендациями справочников и каталогов оборудования для ремонта сельскохозяйственной техники.
Принятая техническая оснащенность рабочих мест разборки должна удовлетворять требованиям механизации и автоматизации технологических процессов ремонта. С учетом этого выбираем следующие оборудование и инструмент.
Разборка коробки осуществляется на стенде, позволяющем располагать объект ремонта в удобное для рабочего пространственное положение. Установка сборочной единицы на стенд производится с помощью консольно-поворотного крана. Для разборки резьбовых соединений используем, гайковерт ИЭ-3113 и наборы ключей и головок ПИМ-6310−01.
Разборка соединений с натягом осуществляется на прессе 208ГАРО, а также при помощи съемников 40П-5019, И-803.20.
4.2 Разработка технологического процесса дефектации корпуса коробки передач Поступающие в ремонт картеры коробки передач имеют следующие дефекты:
— забоины и заусеницы на обработанных поверхностях картера;
— трещины, не проходящие через основания двух ушек или отверстия под подшипник;
— износ отверстий под подшипники первичного и вторичного валов;
— износ отверстий под передний и задний подшипник;
— промежуточного вала;
— износ отверстий под переднюю и заднюю шейки оси блока шестерен заднего хода;
— риски, задиры или износ внутренних торцевых поверхностей бобышек под блок шестерен заднего хода;
— износ или повреждение резьбы под болты крепления крышек. Обломы или трещины, захватывающие посадочные поверхности под подшипники являются выбраковочными признаками. При наличии таких дефектов корпус КПП не принимается на восстановление.
Допустимые без ремонта размеры посадочных отверстий под подшипники первичного и вторичного валов не должны превышать 110,05 мм, отверстий под передний подшипник промежуточного вала 72,04 мм, отверстий под задний подшипник промежуточного вала 90,05 мм, отверстий под переднюю и заднюю шейки оси блока шестерен заднего хода соответственно 30,05 и 32,0 мм. При износе отверстий под подшипники и ось сверх допустимых размеров картер подлежит восстановлению.
Повреждение резьбы в отверстиях картера допускается в пределах не более двух ниток.
Коэффициент повторяемости дефектов, поступающих в ремонт корпусов коробок имеют следующие значения:
— износ отверстий под подшипники — 0,81…0,9;
— износ отверстий под ось блока шестерен заднего хода — 0,74…0,8;
— повреждение резьбы — 0,41…0,68.
Меньшие значение коэффициентов повторяемости дефектов приведены от общего количества поступающих на дефектацию деталей, большие — от общего количества ремонтно-пригодных деталей.
При определении последовательности обнаружения дефектов руководствуемся следующими требованиями:
— в начале выявляются дефекты, при наличии которых деталь выбраковывается в первую очередь применяем способы обнаружения дефектов, не требующие точного инструмента и значительных затрат времени.
С учетом этих требований первоначально визуально осматриваем корпус коробки на наличие трещин и обломов, границы трещин определяем капиллярным методом.
Для контроля износа отверстий под подшипники первичного и вторичного валов применяется пробка 110,05 ГОСТ 2015;89, отверстий под передний подшипник промежуточного вала — пробка 72,04 ГОСТ 2015;89,отверстий под задний подшипник промежуточного вала пробка 90,05 ГОСТ 2015;89, отверстий под переднюю и заднюю шейки оси блока шестерен заднего хода соответственно пробка 30,05 ГОСТ 2015;89 и пробка 32,06 ГОСТ 2015;89, внутренних торцевых поверхностей бобышек под блок шестерен заднего хода — калибр 161,5. Износ резьбовых отверстий контролируется пробками резьбовыми М10−6Н и М12−6Н.
Нормы времени контрольных промеров составляют [11]:
— пробкой односторонней и калибром — 0,041 мин.;
— пробкой резьбовой — 0,45 мин.;
— визуальный осмотр 0,95 мин.
В комплект технологической документации ЕТП дефектации входят:
— титульный лист
— карта эскизов
— карта технологического процесса дефектации.
КТП дефектации выполняем на бланке маршрутной карты (МК). В этом случае в МК вводим строку со служебным символом «Д/Т» на которой записываем данные по контролируем дефектам, параметрам и средствам контроля. В соответствующих графах КТП дефектации указываем наименование и номер дефекта, номинальное значение контролируемого параметра, допустимое значение контролируемого параметра, наименование и обозначение применяемых средств контроля.
4.3 Разработка технологического процесса восстановления корпуса коробки передач От уровня технологии и качества восстановления корпуса коробки передач в значительной мере зависит ресурс отремонтированного агрегата. Основная задача при восстановлении корпусов состоит в правильном выборе способа нанесения покрытия, схемы базирования и технологии механической обработки, позволяющих восстановить и износостойкость, и заданные параметры точности. Комплексное решение этой задачи представляет основную сложность технологического процесса восстановления корпусной детали.
Определение применяемости способов восстановления КПП Для устранения каждого дефекта корпуса КПП выбираем рациональный способ, то есть способ технической обоснованности и экономически целесообразный.
Рациональный способ восстановления определяем пользуясь критериями: технологическим (применимости), техническим (долговечности), и технико-экологическим (обобщенным).
Технологический критерий характеризует принципиальную возможность применения нескольких способов восстановления, исходя из конструктивно-технологических особенностей детали: материала, геометрических размеров и конфигурации, физико-механических свойств восстанавливаемой поверхности и другие.
Так как корпус коробки передач ЗИЛ изготовлен из чугуна СЧ-18, то при выборе способов восстановления необходимо учитывать то, что при значительных термических воздействиях в материал детали возникают остаточные напряжения вызывающие деформацию корпуса, нарушение взаимного расположения отверстий, параллельность и перпендикулярность осей отверстий между собой и относительно установочных баз. С учетом этого для устранения дефектов корпуса КПП выбираем следующие способы.
Заделка трещин: полимерными композициями, штифтованием, фигурными вставками.
Восстановление резьбовых отверстий: обработка под ремонтный размер, установка ввертыша, постановка резьбовой спиральной вставки, полимерными материалами.
Восстановление посадочных мест под подшипники: местное железнение, электродуговая металлизация, газотермйческое напыление порошковых материалов, постановка ремонтной втулки, электроконтактная приварка ленты, постановка свертного кольца.
Выбранные способы, в первую очередь обеспечивают восстановление размеров и формы изношенной детали. Дальнейшая оценка каждого способа, выбранного по технологическому признаку, осуществляется по техническому критерию, то есть с точки зрения восстановления или улучшения свойств поверхностей — обеспечение работоспособности за счет достаточной твердости, износостойкости и сцепляемости покрытия восстанавливаемой детали.
Для каждого выбранного способа даем комплексную качественную оценку по значению коэффициента долговечности Кд, определяемую по формуле:
Кд= КиКВКсКП (4.1)
где Ки, Кв, Кс — коэффициенты соответственно износостойскости, выносливости и сцепляемости покрытий, принимаем по данным [7];
Кп — поправочный коэффициент, учитывающий фактическую работоспособность восстановленной детали в условиях эксплуатации, Кп = 0,8…0,9.
По физическому смыслу коэффициент долговечности пропорционален сроку службы детали в эксплуатации, и, следовательно, рациональным по этому критерию будет способ, у которого коэффициент долговечности (Кд) будет максимальным. С учетом накопленного опыта при ремонте корпусных деталей и рекомендаций для заделки трещин наиболее рациональным является способ постановки фигурных вставок, для которого коэффициент долговечности Кд = 0,81 [7], в то время как в случае применения полимерных материалов в для этих целей Кд = 0,42 [7], а штифтование эффективно только при заделке трещин малой длины (до 50мм).
Из выбранных способов восстановления резьбовых отверстий наиболее приемлемым является — установка спиральной вставки. Этот способ рекомендуется применять при ремонте ответственных деталей и агрегатов. Так как благодаря равномерному распределению нагрузки по виткам и увеличению диаметра значительно повышается прочность соединения, особенно в алюминиевых и чугунных деталях, снижаются концентрация напряжений и улучшается восприятие динамических нагрузок. Коэффициент долговечности для этого способа Кд = 0,9. В то время как при постановке ввертыша требуется значительное увеличение отверстия, что снижает прочность восстанавливаемой детали. Стабилизация резьбовых соединений полимерными материалами эффективно только при износе резьбы, суммарная величина которого должна быть не более 0,3 мм.
Восстановление резьбовых отверстий по ремонтный размер требует увеличения отверстий сопрягаемых с корпусом деталей. Коэффициент долговечности для этого способа Кд = 0,86.
Результаты расчета коэффициента долговечности для способов, рекомендуемых при восстановлении посадочных мест под подшипники, сведены в табл. 4.1.
Таблица 4.1 — Исходные данные и результат расчета коэффициентов долговечности
Способ восстановления | Значения коэффициентов | |||||
Ки | Кв | Кс | Кп | Кд | ||
Местное железнение | 0,91 | 0,82 | 0,65 | 0,9 | 0,53 | |
Электродуговая металлизация | 0,72 | 0,87 | 0,7 | 0,9 | 0,40 | |
Газотермическое напыление порошковых материалов | 0,84 | 0,9 | 0,75 | 0,9 | 0,51 | |
Постановка ремонтной втулки | 0,9 | 0,85 | 0,8 ' | 0,9 | 0,55 | |
Электроконтактная приварка ленты | 0,9 | 0,85 | 0,87 | 0,9 | 0,6 | |
Постановка свертного кольца | 0,95 | 0,9 | 1,0 | 0,9 | 0,77 | |
Анализ результатов расчета коэффициента долговечности показывает, что наиболее рациональный способ восстановления посадочных мест под подшипники в корпусе перемены передач — постановка свертного кольца. Коэффициент долговечности для этого способа в сравнении с другими предлагаемыми способами имеет максимальное значение и равен Кд = 0,77.
Выбор технологических баз.
Технологические базы применяются для определения положения детали в процессе ее обработки. Точность восстановления изношенных поверхностей ремонтируемых деталей зависит от правильного выбора технологических баз. При этом следует учитывать, что выбор технологических установочных баз в значительной степени предопределяет общий план технологического процесса и возможности использования того или иного оборудования.
Выбирая технологические базы необходимо учитывать возможность их совмещения с конструкторскими базами, то есть, базами, которые используются для определения положения детали в сборочной единице. При этом во внимание принимаем следующие специфические особенности: оставлены ли базы после изготовления корпуса, имеют ли место деформации детали (из-за деформации точность расположения базовых поверхностей нарушается), подвергались ли базовые поверхности износу, возможны ли повреждения базовых поверхностей в процессе эксплуатации либо при разборке машины. Чтобы обеспечить точность взаимного расположения поверхностей необходимо использовать соответствующие методы базирования. Принципы их основаны на создании новых баз у изношенных или деформированных деталей, использовании в качестве баз неизношенных поверхностей, восстановление правильной геометрической формы базовых поверхностей. Необходимо стремиться к тому, чтобы одни и те же базы использовались при выполнении всех операций технологического процесса Наиболее приемлемой схемой базирования большинства корпусных деталей является схема базирования, используемая на предприятии-изготовителе (заводская).
С учетом вышеизложенного принимаем за технологические базы при восстановлении корпуса перемены передач комплект баз основного производства, представляющие собой плоскость прилегания крышки коробки и расположенные в ней два базовых отверстия. При этом необходимо учесть, что использование комплекта заводских технологических баз при восстановлении корпуса КПП имеет свои особенности. Размеры базовых поверхностей корпусов, поступивших в ремонт, отличаются от размеров, указанных на рабочих чертежах. Неиспользуемые при эксплуатации базовые отверстия изнашиваются в процесс многократных установок и снятия корпуса на установочных приспособлениях при их изготовлении. Поэтому в технологический процесс восстановления необходимо внести слесарную операцию по развертыванию технологических базовых установочных отверстий. Также необходимо учесть то, что у корпусов, поступающих на восстановление, на базовой плоскости имеются забоины, возникающие в процессе разборки агрегатов и транспортирования корпусов. Наличие забоин в местах контакта корпуса с установочными пластинами приводит к увеличению припуска на обработку отверстий, нарушению взаимного расположения осей отверстий и плоских поверхностей, а также осей резьбовых отверстий относительно восстановленных отверстий в результате чего может быть не обеспечена собираемость сопряжений. Поэтому в технологии восстановления необходимо предусмотреть зачистку базовой поверхности.
Обоснование последовательности устранения дефектов.
Составление маршрута восстановления детали или разработка последовательности устранения дефектов детали с учетом схем базирования состоит в разработке общего плана технологического процесса восстановления, содержания операций и выборе типа оборудования. Маршрут восстановления деталей на ремонтном предприятии начинается с очистки. Затем следует дефектация. Дальнейшее построение маршрута должно обеспечивать изменение состояния детали, отвечающей требованиям ремонтного чертежа.
При разработке маршрута восстановление корпуса руководствуемся следующими правилами:
— предусматриваем операции по восстановлению или изготовлению технологических баз;
— перед установкой свертных колец выполняем операции по удалению дефектных слоев металла, восстановлению формы (циллиндричность, прямолинейность и т. д.) и созданию необходимой шероховатости поверхности;
— в первую очередь выполняем операции по восстановлению поверхностей, имеющих невысокую точность;
— легко повреждаемые и точные поверхности (посадочные поверхности под подшипники) обрабатываем в конце маршрута;
— каждая последующая технологическая операция должна улучшать качество поверхности детали;
— черновую и чистовую механическую обработки детали со значительными припусками выделяем в отдельные операции.
Выполнение операций технологического процесса восстановления корпуса коробки передач осуществляется на оборудовании и в применением технологической оснастки в соответствии с рекомендациями.
При заделке трещин фигурными вставками применяется комплект оснастки ОР-11 362 и электродрель.
Восстановление резьбового отверстия осуществляется с помощью комплекта приспособлений ОР5526 и использованием «электродрели.
Растачивание отверстий под свертные кольца с нарезанием винтовых канавок в отверстиях под подшипники осуществляется на радиально-сверлильном станке 2А55.
Запрессовка ремонтных втулок и свертных колец в отверстия выполняется прессом 208 ГАРО.
Раскатывание свертных колец чистовое растачивание посадочных поверхностей под подшипники осуществляется на горизонтально-расточном станке РР-4.
Обоснование технологических режимов и норм времени Техническая норма времени на выполнение операций рассчитывается по формуле:
Тн = То + Тв + Тд + Тп (4.2)
где Тн — норма времени или штучно-калькуляционное время, мин;
То — основное время, мин;
Тв — вспомогательное время, мин;
n — количество деталей в партии, шт.
Количество деталей в партии определяется по зависимости:
n=Nр.n./Дн (4.3)
где DH — номинальное количество рабочих дней в году, DH = 252 дня.
n=100/252?1
Штучное время определяется по формуле:
Тшт=То+Тв+Тд (4.4)
Произведем расчет режимов и норм времени по операциям технологического процесса восстановления корпуса коробки передач. Необходимые для расчетов сведения о дефекте, технических требованиях и размерах восстанавливаемых поверхностей принимаем по данным ремонтного чертежа.
005 Дефектовочная При дефектации коробки контролировать размеры и технические требования.
Штучное время на контроль размеров принимаем равным Тш = 4,0 мин, на контроль технических требований Тш = 2 мин; Тп3 = 3 мин. [11]
TH = 4 + 2+3/1= 9
010 Слесарная Сверлить отверстия по кондуктору под фигурные вставки, установить уплотняющие фигурные вставки.
Диаметр отверстий Ш4,6 мм, отверстия глухие, глубина сверление 3,5 мм, количество отверстий при длине трещины 100 мм -28шт.
По данным [11]рассчитываем неполное штучное время на сверление отверстий.
Штучное время нанесения состава на основе эпоксидной смолы на поверхность трещины длиной 100 мм:
Тшт = 0,6 мин.
Неполное штучное время на установку в подготовленные отверстия 7фигурных вставок с последующим расклепыванием:
Тнш2 = 0,3 *7 = 2,1 мин Вспомогательное время на установку детали Тву = 0,9 мин.
Подготовительно-заключительное время на выполнение работы вредней сложности — 4 мин.
Тогда норма времени на выполнение слесарной операции:
Тн = 8,9+ 0,6+ 2,1+0,9 =12,5 мин
015 Слесарная Рассверлить резьбовое отверстие, нарезать резьбу и установить резьбовую вставку.
Вспомогательное время на установку детали Тву = 0,9 мин.
Диаметр отверстия под резьбу Ml2 — 10,1 мм.
Глубина сверления 25 мм.
Неполное штучное время на рассверливание электродрелью отверстия до диаметра 10,1 мм Тнш1 = 0,3 мин, на нарезание резьбы M12 — Тнш2= 3 *0,8 = 2,4 мин, установку резьбовой спиральной вставки и обрубку технологического поводка Тнш3 = 0,5 мин; Тпл = 4 мин.
Норма времени на восстановление резьбового отверстия постановкой спиральной вставки:
Тн = 0,9 + 0,3 + 2,4 + 0,5 + 4= 8,1 мин
020 Токарная Изготовить ремонтную втулку в отверстие под ось.
При выполнении данной операции необходимо:
установить заготовку в патрон токарного станка проточить наружную поверхность до Ш 34,5 мм сверлить отверстие на глубину 30 мм, Ш12мм рассверлить до Ш 28 мм.
зенкеровать отверстие в размер 29,6 + 0,1
отрезать втулку Режимы резания при точении принимаем по данным[11]:
Vр= 158 м/мин;
S=0,4 мм/об;
Тогда число оборотов детали:
n=1000Vр/рД (4.4)
где Vp — скорость резания, м/МИН;
D — диаметр заготовки, мм, D = 35 мм.
n=1000· 158/3,14·35=1430 мин-1
Режим резания при сверлении отверстия Ш12 мм
Vр= 20 м/мин ;
S=0,1 мм;
n=1000*20/3,14*12=180 мин-1
При рассверливании до Ш 28 мм и зенкеровании:
Vр= 46 м/мин;
S=0,1 мм.
n=1000*46/3,14*28=520 мин-1
Режимы резания при отрезании втулки:
Vр= 95 м/мин ;
S=0,18 мм/об.
n=1000*95/3,14*30=1000об/мин-1
Основное время при точении и сверлении определяется:
То=L*i/n*S (4.5)
гдеL — длина обрабатываемой поверхности;
i — число проходов Основное и вспомогательное, связанное с проходами, время: на точение наружной поверхности:
То =30*1/1430*0,2=0,11мин; Тв =0,5 мин на сверление:
То =30*1/180*0,3=0,6мин; Тв =0,6 мин на рассверливание и зенкерование:
То =30*1/520*0,1=1,2мин; Тв =0,8 мин на отрезание втулки То =35*1/1000*0,18=0,2мин; Тв =0,2 мин Основное время на выполнение механической обработки
То= 0,11 + 0,6 + 1,2 + 0,2 = 2,11 мин Вспомогательное время на установку и снятие детали Тв = 0,95 мин, тогда вспомогательное время с учетом времени связанного с проходами:
Тв = 0,95 + 0,5 + 0,6 + 0,8 + 0,2 =3,05 мин Тд = 0,08 (2,11 + 3,05) = 0,43 мин Подготовительное заключительное время Тпз= 7 мин.
Норма времени на изготовление втулки (операция 020)
Тн = 2,11 + 3,05 + 0,43 + 7/10 = 6,3 мин
025 Сверлильная Рассверлить отверстие под ось блока шестерен заднего хода для установки ремонтной втулки до диаметра 34 мм и зенкеровать в размер 34,4-002 мм.
Режимы резания при рассверливании
Vр= 30 м/мин;
S=0,17 мм/об.
n=1000· 30/3,14·34,4=290 об/мин-1
Режимы резания при зенкеровании:
Vр=30м/мин ;
S=0,4 мм/об;
n=290 мин-1
Основное и вспомогательное, связанное с проходом, время при рассверливании:
То =25· 1/290·0,17=0,5мин; Тв =0,12мин Основное и вспомогательное связанное связанное с проходом время назенкерование:
То =25· 1/290·0,4=0,2мин; Тв =0,12мин Вспомогательное время на установку и снятие детали Тв = 1,3 мин.
Общее вспомогательное время:
Тв = 1,3 + 0,12 + 0,12 = 1,54 мин Основное время на рассверливание и зенкерование:
То = 0,5 + 0,2 = 0,7 мин Для сверления дополнительное время рассчитываем по формуле:
Тд = 0,06 (То + Тв) (4.7)
Тд = 0,06 (0,7 + 1,54) = 0,14 мин Тпз= 5 мин.
Норма времени на выполнение сверлильной операции 025:
Тн = 0,7 + 1,54 + 0,14 + 5/10 = 2,9 мин
030 Слесарная Запрессовать втулку в отверстие коробки перемены передач.
Штучно-калькуляционное время на запрессовку втулки под прессом выбираем из.
Тшт.к= 1,39 мин.
Время на наладку пресса (для наладки средней сложности) равно 2 мин.
Тогда норма времени на выполнение слесарной операции 030:
Тн = 1,39+2 = 2,39 мин
035 Сверлильная Развернуть отверстие во втулке под ось блока шестерен заднего хода в размер 30+0,05
Режимы резания при развертывании:
S = 2,2мм/об;
Vp = 6,2 м/мин;
n= 49 мин-1
Основное и вспомогательное связанное с проходом время:
То =25· ½, 2·49= 0,23 мин; Тв = 0,15 мин.
Вспомогательное время на установку и снятие детали Тв = 1,3 мин.
Тдоп = 0,06 (0,23 + 0,15 + 1,3) = 0,1 мин Тп.з = 5 мин.
Норма времени на выполнение сверлильной операции 035:
Тн= 0,23 + 0,15 + 1,3 + 0,1 + 5/10 = 2,28 мин
040 Расточная Расточить два отверстия на проход под подшипники первичного и вторичного валов до выведения следов износа и с учетом толщины стенкисвертного кольца в размер 112+0,07и нарезать винтовые канавки треугольного профиля глубиной 0,35…0,45 мм и шагом 3 мм.
Режимы резания при растачивании отверстия
Vр= 87 м/мин ;
S=0,125 мм/об.
n=1000· 87/3,14·112=148 мин-1
Принимаем по паспортным данным станка 2А55:
n= 290 мин, тогдаVр= 100 м/мин Режимы резания при нарезания винтовой канавки:
Vр= 65 м/мин ;
S=3 мм/об.
n=1000· 65/3,14·112=185 мин-1
Принимаем n = 204 мин, тогда Vp = 72м/мин;
Основное и вспомогательное связанное с проходом времяна растачивание отверстия:
То =18· 1/290·0,14= 0,45 мин; Тв = 0,8 мин.
Нарезание винтовой канавки:
То =18· 1/204·3= 0,03 мин; Тв = 0,5 мин.
Основное время на механическую обработку одного отверстия:
То = 0,45 + 0,03 = 0,48 мин. Двух отверстий 0,96 мин Вспомогательное время на механическую обработку одного отверстия:
Тв = 0,8 + 0,5 = 1,3 мин Двух отверстий 2,6 мин;
Вспомогательное время на установку и снятие детали Тв = 3 мин.
Дополнительное время:
Тдоп = 0,08 (0,96 + 2,6 + 3) = 0,52 мин Тп.з = 6 мин.
Норма времени на выполнение расточной операции 040:
Тн=0,96+2,6+3+0,52+6/10=7,7мин
045 Расточная Расточить отверстие под передний подшипник промежуточного вала на проход под свертное кольцо в размер 74+0,06 и нарезать винтовую канавку шагом 3 мм.
Режимы резания при растачивании отверстий:
Vр= 100 м/мин ;
S=0,125 мм/об.
n=1000· 100/3,14·74=442 об/мин-1
Принимаем n=407об/мин, тогда Vp = 92 м/мин; при нарезании винтовой канавки:
S = 3 мм;
V = 65 мм/мин.
n=1000· 65/3,14·74=287 об/мин-1
Принимаем n= 290, тогда Vp = 66 м/мин.
Основное и вспомогательное связанное с проходом время:
на растачивание отверстия:
То =25· 1/0,125·407= 0,49 мин; Тв = 0,8 мин.
на нарезание винтовой канавки:
То =25· 1/290·3= 0,03 мин; Тв = 0,5 мин.
Вспомогательное время на установку и снятие детали Тв = 0,5 мин.
Тдоп = 0,08 (0,49 + 0,03 + 0,8 + 0,5 + 3) = 0,38 мин Тпз = 6 мин;
Норма времени на выполнение расточной операции 045:
Тн = 0,49 + 0,03 + 0,8 + 0,5 + 3 + 0,38 +4 = 5,80 мин
050 Расточная Расточить отверстие под задний подшипник промежуточного вала на проход под свертное кольцо в размер 9Ј+0'07 и нарезать винтовую канавку шагом 3 мм.
Режимы резания:
при растачивании отверстия
Vр= 87 м/мин ;
S=0,125 мм/об.
n=1000· 87/3,14·92=308 об/мин-1
Принимаем n= 290об/мин, тогда Vp = 82мм/мин;
при нарезании винтовой канавки:
Vр= 65 м/мин ;
S=3 мм/об.
n=1000· 65/3,14·92=230 об/мин-1
Принимаем n= 204об/мин, тогда Vp = 58мм/мин;
Основное вспомогательное связанное с проходом время на растачивание отверстия на растачивание отверстия:
То =14· 1/0,125·290= 0,39 мин; Тв = 0,8 мин.
на нарезание винтовой канавки:
То =14· 1/204·3= 0,03 мин; Тв = 0,5 мин.
Вспомогательное время на переустановку детали Тв = 3 мин.
Тдоп = 0,08 (0,39 + 0,02 + 0,8 + 0,5 + 3) = 0,37 мин Тп.з= 6 мин;
Норма времени на выполнение расточной операции 050:
Тн= 0,39 + 0,02 + 0,8 + 0,5 + 0,37 + 3 + 6/10= 5,7 мин
055 Слесарная Изготовить свертные кольца под подшипники первичного и вторичного валов, передний и задний промежуточного вала с размерами по наружному диаметру соответственно Ш112 мм; Ш112мм;Ш72мм; высотой соответственно 17 мм; 15 мм; 24 мм; 13 мм из листовой углеродистой стали (сталь 20) толщиной 1,3 мм.
При изготовлении свертных колец выполняют:
разметку полосы;
вырезку ножницами заготовок;
гибку из заготовок колец.
Вспомогательное время на установку листа на стол Тв = 0,7 мин;
Штучное время на разметку одной заготовки 0,5 мин, четырех — 2 мин.
Штучное время на вырезку заготовки — 1,3 мин, четырех — 5,2 мин.
Штучное время на гибку кольца из заготовки — 1,6 мин, четырех колец — 6,24 мин.
Штучное время на изготовление четырех свертныл колец:
Тшт = 2+ 5,2+ 6,24= 13,44 мин Тп.з=4 мин Норма времени на выполнение слесарной операции 055:
Тн= 13,44 + 0,7 + 4/10= 14,54 мин
060 Слесарная Запрессовать свертные кольца в соответствующие отверстия коробки перемены передач.
Штучно-калькуляционное время на запрессовку одного свертного кольца Тшт.к= 1,39 мин [11], четрех колец — 5,56 мин.
Время на наладку пресса (для наладки средней сложности) равно 2 мин.
Тогда норма времени на выполнение слесарной операции 060:
Тн = 5,56 + 2 = 7,56 мин
065 Раскаточная Раскатать свертные кольца в отверстиях под подшипники первичного и вторичного валов.
Режимы раскатывания:
натяг = 0,45 мм; S = 0,2мм/об; n= 153об/мин;
Основное и вспомогательное на проход время на раскатывание:
отверстия под подшипник первичного вала:
То =18· 1/153·0,2= 0,6 мин; Тв = 0,4 мин.
отверстия под подшипник вторичного вала:
То =16· 1/153·0,2= 0,53 мин; Тв = 0,4 мин.
Вспомогательное время на установку и снятие детали Тв = 3 мин.
Тдоп = 0,08· (0,6 + 0,53 + 0,4 + 0,4 + 3) = 0,18 мин Тп.з= 6 мин;
Норма времени на выполнение раскаточной операции 065:
Тн= 0,6 + 0,53 + 0,4 + 0,4 + 3 + 0,18 + 6/10 = 5,1 мин
070 Раскаточная Раскатать свертные кольца в отверстиях под передний и задний подшипник промежуточного вала Режимы раскатывания натяг- 0,45 мм; S = 0,2 мм/об; n= 153об/мин;
Основное и вспомогательное время на проход время на раскатывание:
отверстия под передний подшипник:
То =24· 1/153·0,2= 0,8 мин; Тв = 0,4 мин.
отверстия под задний подшипник То =14· 1/153·0,2= 0,47 мин; Тв = 0,4 мин.
Вспомогательное время на установку и снятие детали Тв = 3 мин.
Тдоп = 0,08· (0,8 + 0,47 + 0,4 + 0,4 + 3) = 0,4 мин Тп.з=6 мин;
Норма времени на выполнение раскаточной операции 070:
Тн= 0,8 + 0,47 + 0,4 + 0,4 + 3 + 0,4 +6/10= 6,1 мин
075 Расточная Расточить отверстия на проход с одновременным упрочняющим выглаживанием под подшипники первичного и вторичного валов в размер 110 +0,023
Режимы резания
Vр= 100 м/мин ;
S=0,58 мм/об.
n=1000· 100/3,14·110=290 об/мин-1
Основное и вспомогательное связанное с проходом время на растачивание с одновременным выглаживанием одного отверстия:
То =18· 1/290·0,08= 0,78 мин; Тв = 0,8 мин.
Вспомогательное время на установку и снятие детали Тв = 3 мин;
Тдоп = 0,08 (0,8 + 0,78 + 3) = 0,4 мин Тп.з=6 мин;
Норма времени на выполнение расточной операции 075:
Тн= 0,8 + 0,78+ 3 + 0,4 +6/10= 5,6 мин
080 Расточная Расточить отверстие под передний и подшипники промежуточного вала с одновременным упрочняющим выглаживанием в размер соответственно 90+0,023 и 72+0,020
Режимы резания:
Vр= 100 м/мин ;
S=0,58 мм/об.
n=1000· 100/3,14·72=442 об/мин-1
По паспортным данным станка HH-4 принимаем n = 407об/мин, тогда Vр= 92 м/мин То =25· 1/407·0,08= 0,77 мин; Тв — 0,8 мин Вспомогательное время на установку и снятие детали Тв = 3 мин;
Тдоп = 0,08 (0,77 + 0,8 + 3) = 0,37 мин Тп.з= 6 мин;
Норма времени на выполнение расточной операции 080:
Тн = 0,77 + 0,8 + 3+ 0,37+6/10 = 5,54 мин
085 Контрольная Контролировать размеры и технические требования.
Время на контроль размеров Тшт=5мин;
Время на контроль технических требований:
Тшт =2,0 мин; Тп.з = 6мин Норма времени на выполнение контрольной операции 090:
Тн =2+5+6/10=7,6 мин
4.4 Разработка технологического процесса сборки и обкатки коробки передач При сборке коробки перемены передач необходимо соблюдать требования на установку деталей и сборочных единиц.
Сопрягаемые поверхности деталей, имеющие в процессе эксплуатации относительное перемещения (трение), должны быть гладкими, без рисок и задиров.
Перед сборкой детали должны быть смазаны маслом. Для смазки трущихся поверхностей следует применять масло того сорта, которым они смазываются в процессе эксплуатации.
Подшипники должны поступать на сборку смазанными. При установке подшипников необходимо соблюдать следующие условия:
— перед установкой подшипников посадочные поверхности сопрягаемых деталей должны быть тщательно промыты, просушены и смазаны тонким слоем масла. На посадочных поверхностях, заплечиках вала и корпуса заусеницы, забоины и коррозионные налеты не допускаются;
— перед напрессовкой на вал подшипники, имеющие посадку с натягом, должны быть нагреты в масленой волне до 80…90°С;
— при напрессовке подшипника на вал усилие необходимо прилагать к его внутреннему кольцу, а при запрессовке в гнездо — к наружному. Для выполнения этих операций следует пользоваться гидравлическим прессом, винтовым приспособлением или наставкой. Установка шариковых и роликовых подшипников с перекосом, а также ударами молотка не допускается;
— наружные и внутренние кольца роликоподшипников должны быть напрессованы на валы и в стаканы до упора в стопорное кольцо или буртик.
Подшипники должны работать без повышенного шума, стуков и нагрева колец. Подшипник, напрессованный на вал или запрессованный в гнездо, должен вращаться без заеданий. Наружное кольцо должно останавливаться плавно без рывков и стуков. При вращении должен быть слышен глухой звук.
Отремонтированные посадочные места под подшипники должны иметь нормальные размеры. Накернивание или лужение посадочных мест под подшипники при ослаблении посадки не допускается.
Поверхность валов, сопрягаемые с манжетами, должны быть чистыми, без рисок и задиров.
При запрессовке манжет усилие должно прилагаться только к корпусу. Монтаж манжет производится только с помощью наставок.
Корпус манжеты должен плотно сидеть в гнезде. Течь масла в месте сопряжения манжеты с гнездом не допускается.
Перед сборкой коробки передач все внутренние полости должны быть промыты и продуты сжатым воздухом.
Передвижение скользящих шестерен по шлицам валов должно происходить свободно, от руки без заеданий. При нейтральном положении рычага коробки перемены передач и при включении каждой передачи первичный вал должен свободно вращаться от усилия руки через рукоятку с плечом 150 мм.
Валы и шестерни на всех передачах должны вращаться без заеданий и включать заданную передачу.
Зубья ведущих и ведомых шестерен во включенном состоянии должны соприкасаться по всей длине. Расстояние между торцами венцов постоянно замкнутых шестерен допускается до 2 мм.
Фиксаторы должны надежно стопорить вилки, как в нейтральном, так и во включенном положениях; при этом зазор между торцами зубьев шестерен в нейтральном положении должен быть не менее 1,5 мм.
При вращении скользящих шестерен заедание вилок переключения в кольцевых канавках не должно ощущаться.
Рычаг переключения должен легко, плавно включать и выключать все передачи.
Все резьбовые соединения должны быть затянуты до отказа соответствующим моментом и надежно застопорены.
Разработка схемы сборки коробки передач.
Построение схемы начинается с изображения базовой детали, которой является корпус КПП. В корпусе коробки устанавливаются сборочные единицы, представляющие собой на схеме сборочные группы. На схеме сборочные группы изображаются в последовательности и установки в корпус. Сборки сборочных единиц также начинается с базовой детали.
Так, на вал промежуточный устанавливается шпонка, шестерня второй передачи, втулка, шестерня четвертой передачи, шайба упорная, шестерня заднего хода, кольцо замочное, шестерня третьей передачи, шайба упорная, шестерня приводного вала, кольцо замочное, подшипник. Собранная сборочная единица, являющаяся первой сборочной группой — вал промежуточный в сборе — и соответственно обозначаемая на схеме Сб-1, с подшипниками устанавливается в корпус КПП. Далее устанавливаются крышки с прокладками вала промежуточного. Затем осуществляется сборка следующих сборочных групп — блока шестерен заднего хода, вала вторичного, крышки вала вторичного, вала первичного, вала первичного, крышки вала первичного, крышки коробки передач. Собранные сборочные единицы обозначаются соответственно Сб-2, Сб-3 и т. д. и в последовательности соответствующей обозначению устанавливаются в корпус коробки. Заканчивается схема сборки условным изображением коробки перемены передач в сборе с указанием ее номера по каталогу.
Разработанная схема служит основой для разработки технологического процесса сборки.
В процессе сборки коробки перемены передач следует руководствоваться техническими требованиями на ее сборку.
Технологический процесс обкатки коробки передач.
Собранную коробку передач обкатывают без нагрузки и под нагрузкой на специальном стенде. Во время обкатки осуществляется приработка сопрягаемых поверхностей деталей и улучшение их качества. Помимо этого обкатка позволяет выявить дефекты сборки, которые обнаруживаются по нагреву отдельных узлов или деталей, возникновению стуков, шумов, течи масла.
Перед обкаткой в коробку заливается необходимое количество масла, которое используется в процессе эксплуатации.
Обкатку без нагрузки производят в течение 2 минут на каждой передаче, постепенно повышая обороты до нормальных, Во время обкатки проверяется нагрев подшипников, подтекание масла, легкость переключения передач, определяют правильность сборки коробки по величине вибраций и шумности работы.
Обкатку под нагрузкой осуществляют путем создания нагрузки на шестерни испытуемой коробки передач посредством электромагнитного порошкового нагрузочного тормоза. Обкатку ведут в течение 20 минут, по 4 минуты на каждой передаче, начиная с 25% нагрузки в течение 1 минуты и последующим нагружением с шагом 25% до полной нагрузки и продолжительностью 1 мин. при каждом увеличении нагрузки.
Во время испытания коробок основным критерием исправности их работы являются температура нагрева и шумность. Температура нагрева подшипников, зубчатых колес и масла при обкатке под нагрузкой не должна превышать 50…60 °С. Шумность работы определяется рабочим на слух или с помощью электроакустического прибора, позволяющего измерять силу звука, возникающего в отдельных работающих узлах, что дает возможность не только оценить работу коробки в целом, но и выявить дефектные места.
После обкатки из коробки сливается масло, очищается магнитная пробка, заливается в картер керосин или дизельное топливо и прокрутив коробку без нагрузки в течении 2 минут производят промывку. После прокручивания промывочная жидкость сливается и коробка снимается со стенда.
5. Трудоемкость ремонта и годовой объем работ
5.1 Обоснование трудоемкости единицы ремонта Для обоснования трудоемкости ремонта машин или их сборочных единиц на перспективу и годового объема работ рекомендуется применять наиболее распространенный и апробированный способ, когда искомая величина отыскивается по известным значениям трудоемкости ремонта машин-аналогов или их сборочных единиц уже освоенных на ремонтных предприятиях.
Для расчета трудоемкости ремонта коробки перемены передач можно применить формулу:
То =Трдkсерkпрkпер (5.1)
где Трд — трудоемкость капитального ремонта коробки передач при эталонной программе, ч;
Трд=5,8 ч [2];
kсер — коэффициент, учитывающий влияние величины производственной программы;
При N = 100 kсер = 1,14 [2];
knp — коэффициент приведения объекта ремонта к основной модели,
knp=1;
кпер — коэффициент, учитывающий рост производительности труда на перспективу, кпер = 0,97.
Тогда трудоемкость ремонта коробки перемены передач ЗИЛбудет равна:
Тр = 5,8−1,14−1 -0,97 = 6,4 ч.
Трудоемкость ремонта корпуса коробки перемены передач определить как сумма штучно-калькуляционного времени по каждой из операций технологического процесса его восстановления:
Трк =У Тшкi, (5.2)
где Тшкi,— норма времени на выполнение i-ой операции, принимаем по расчетам выполненным в разделе 4.3 пояснительной записки.
Трк = 6,33 + 12,5 + 4,5 + 6,3 + 2,9 + 2,39 + 2,28 + 7,7 + 5,8 + 5,7 + 14,54 + 7,56 + 5,1 + 6,1 + 5,56 + 5, 54 + 7,6 = 108,4 мин.
Следовательно, трудоемкость ремонта корпуса коробки перемены передач составляет в Трк = 1,8 ч.
Под годовым объемом работ или годовой трудоемкостью ремонтного предприятия или производственных цехов, отделений и участков понимают величину трудозатрат производственных рабочих, необходимую для выполнения годовой производственной программы.
Годовой объем работ связанных с ремонтом коробок перемены передач определяется с учетом трудозатрат на единицу ремонта по зависимости:
Tr = Tp-Nпр.р (5.2)
где Nnр.р — величина производственной программы, выраженной в приведенных ремонтах;
Тр — трудоемкость ремонта коробки перемены передач ЗИЛ.
Тг = 6,4· 100=640ч Годовая трудоемкость восстановления корпусов коробок перемены передач также определяется из трудоемкости восстановления одного корпуса и величины производственной программы:
Тгк= 1,8· 100 = 180 ч.
На участке ремонта коробки перемены передач будут выполняться работы связанные с разборкой, дефектовкой, комплектовкой, подгонкой, сборкой, испытанием и регулировкой объекта ремонта. Кроме перечисленных видов работ на участке восстанавливается корпус коробки перемены передач.
В соответствии с рекомендациями трудоемкость выполняемых на участке работ по видам в процентах от трудоемкости ремонта КПП составляют: разборочные — 6,3; дефектовочные — 4,3; слесарно-подгоночные -16,4; сборочные — 16,9; испытательно-регулировочные — 3,9; комплектовочные — 3,3.
Моечные, станочные (за исключением операций восстановления корпуса), кузнечно-термические, сварочно-наплавочные и малярные выполняются на соответствующих участках.
Результаты расчета трудоемкости работ, выполняемых на участке ремонта коробок перемены передач сведены в таблице 5.1.
Таблица 5.1 — Результаты расчета трудоемкости по видам работ
Вид выполняемых работ | Трудоемкость | ||
% | час | ||
Разборочная | 6,3 | ||
Дефектовочная | 4,3 | ||
Комплектовочная | 3,3 | ||
Слесарно-подгоночная | 16,4 | ||
Сборочная | 16,9 | ||
Испытательно-регулировочная | 3,9 | ||
Итого | ; | ||
В объем работ выполняемых на участке включаются работы по восстановлению корпуса КПП связанные с механической обработкой за исключением токарной операции (изготовление втулки), а также слесарные и контрольные работы.
Тогда годовая трудоемкость работ по восстановлению корпуса коробки выполняемых на участке будет равна:
Тгв = (108,4· 6,33·6,3)· 100/60 = 159 ч Используя данные таблицы 4.1 годовой объем работ по восстановлению корпуса КПП выполняемый на участке распределяем по следующим видам работ:
Слесарные: Тгсл= (12,5 + 4,5 + 2,39 + 14,54 + 7,56· 100/60 = 69,2 ч.
Сверлильные: Тгсв= (2,9 + 2,28) · 100/60 = 8,6 ч.
Раскаточно-расточные: Тгр= (7,7 + 5,8 + 5,7 + 5,1 + 6,1 + 5,56 + 5,54)· 100/60=69ч.
Контрольные: Тгк=7,6 · 100/60 = 12,7 ч.
Годовой объем работ участка ремонта коробок передач будет равен:
Тгу = 5110+ 319 =5429ч
6. Проектирование участка ремонта коробок перемены передач
6.1 Режим работы предприятия и годовые фонды времени Режим работы предприятия характеризуется количеством рабочих дней в году, количеством смен работы в сутки, длительностью рабочей смены.
Количество рабочих дней в году определяется по формуле:
Nрд = 365 — Nв — Nn (6.1)
где Nв — количество выходных дней в году;
Nn — количество праздничных дней в году.
По трудовому законодательству Республики Беларусь для ремонтных заводов принимается пятидневная 40-часовая рабочая неделя с продолжительностью смены 8 часов, число праздничных дней Nn = 9.
Исходя из принятого режима работы завода определяем номинальные и действительные фонды времени рабочих, оборудования, рабочих мест.
Номинальный фонд времени рабочих:
Фнр = (365 — Nв — Nn) -tсм — tск — Nпп (6.2)
Действительный фонд времени рабочих:
Фдр = [(365 — N. — N. — No) -tсм — tск -Nnn)]г, (6.3)
где tсм — продолжительность рабочей смены; tсм = 8 ч;
tск — продолжительность сокращения рабочей смены в предпраздничные дни; tск = 1 ч;
Nnn— количество предпраздничных дней;
No — продолжительность отпуска; No = 24 дня;
г — коэффициент, учитывающий потери времени по уважительным причинам, у = 0,97.
Фнр = (365 — 104 — 9) *8 — 1 *9 = 2007 ч Фдр = [(365 — 104 — 9 — 24) 8 -1*9)] *0,97 = 1760 ч Номинальный и действительный годовые фонды времени оборудования находятся по формулам:
Фно = Фнрс; (6.4)
Фдо = Фнр с?; (6.5)
где с — число смен работы в сутки, с = 14.
? — коэффициент, учитывающий простое оборудования при фонд рабочего места.
Фно = 2007· 1=2007ч Фдо =2007· 1·0,97=1946ч
6.2 Расчет количества рабочих Число производственных рабочих рассчитывается по трудоемкости выполняемых им работ и фонду времени рабочего. Расчету подлежит списочное и явочное число рабочих:
nря=Тг.i/Фн.р. (6.6)
nрс=Тг.i/Фр.д. (6.7)
где Tri — годовой объем i-гo вида работ, ч.
Число рабочих занятых на разборке коробок будет равно:
пря= 630/2007 = 0,3
прс= 630/1760 = 0,35
С учетом совмещения работ принимаем 1-го человека.
Аналогично выполняем расчеты по другим операциям, результаты расчетов сведены в таблице 6.1.
Таблица 6.1 — Штатная ведомость производственных рабочих
Наименование вида работ | Специальность | Разряд | Трудоемкость | Число рабочих | ||||
Явочное | Списочное | |||||||
расч. | принят. | расч. | принят. | |||||
Разборочные | слесарь | 0,3 | 0,35 | |||||
Дефектовочные | дефек-товщик | 0,21 | 0,24 | |||||
Комплектовочные | слесарь | 0,16 | 0,18 | |||||
Слесарно-подгоночные | слесарь | 0,8 | 0,9 | |||||
Сборочные | слесарь | 0,84 | 0,96 | |||||
Испытательно-регулировочные | слесарь | 0,19 | 0,22 | |||||
Слесарные | слесарь | 69,2 | 0,03 | 0,04 | ||||
Сверлильные | сверлов. | 8,6 | 0,04 | 0,05 | ||||
Раскаточно-расточные | расточ. | 0,03 | 0,04 | |||||
Контрольная | контрол | 12,7 | 0,006 | 0,007 | ||||
Итого | ||||||||
Предусматриваем совмещение работ:
— дефектовочных, контрольных и сборочных;
— слесарно-подгоночных и испытательно-регулировочных.
Число вспомогательных рабочих рассчитывается в пределах 14…17% от числа основных рабочихnвсп.р=0,14· 5=0,75. Принимаем пвспр= 1. Число ИТР-8…10% от числа вспомогательных ипроизводственных:
nИТР=0,10(5+1)=0,6
Принимаем nИТР = 1.
6.3 Расчет количества технологического оборудования Расчету подлежит только число основного технологического оборудования. Количество единиц одноименного оборудования рассчитываем исходя из величины годового объема i-ro вида работ:
nря =Тг.i /Фн.рсзи (6.8)
где зи — коэффициент использования оборудования по времени;
зи = 0,85…0,95.
Число стендов для разборки-сборки коробок передач:
nст = 630 + 1690/1946· 0,9 = 1,07
Принимаем 1 стенд.
Количество дефектовочного оборудования:
Nдеф =430/1946· 0,85 = 0,18
Принимаем один дефектовочный стол ОРГ-1468−01−080А. Число оборудования для комплектования и контроля:
пком= 330 + 12,7/1946· 0,85 = 0,15
Принимаем один стол контролера ОРГ-1468−01−090А. Количество технологического оборудования для расточных и сверлильных работ
nраст= 69 + 8,6/1946· 0,85 = 0,03
Принимаем 1 станка (2А78 и РР-4), с учетом выполнения на этом оборудовании части слесарно-подгоночных работ.
Число верстаков для выполнения слесарных и слесарно-подгоночных работ:
nвер= 1640 + 69/1946· 0,9 = 0,88
Принимаем 1 верстак и пресс гидравлический.
Количество стендов для обкатки собранных коробок перемены передач определится по зависимости:
nст=Nр.н.*a*tр.н./n1Фд.о.сзи (6.9)
где Np.n -величина производственной программы ремонта коробок передач;
tnp— продолжительность обкатки коробки, ч;
n1 — количество одновременно обкатываемых коробок передач, n = 1.
а — коэффициент, учитывающий время на установку и снятие коробки со стенда, а также повторность обкатки; а = 1,2.
nст = 100· 0,5·1,2/1·1946·0,90 = 0,03
Принимаем один обкаточный стенд.
При выборе оборудования учитывалось серийность производства. Рассчитанное количество оборудования обеспечивает выполнение разработанного технологического процесса.
Внутризаводской транспорт предназначен. для подъема и перемещения всех грузов ремонтного предприятия в пределах отдельных подразделений, между подразделениями и между отдельными объектами на территории предприятия.
Подъемно-транспортные работы на ремонтных предприятиях отличаются большим разнообразием и составляют до 30% трудовых затрат от общей трудоемкости работ по восстановлению деталей. Правильный выбор подъемно-транспортного оборудования снижает трудоемкость и затраты на ремонт, резко улучшая условия работы предприятия.
Машины и устройства внутризаводского транспорта по своему назначению разделяют на две основные группы: грузоподъемные и транспортирующие.
Грузоподъемные машины и оборудование в основном предназначены для подъема единичных грузов на определенную высоту и незначительного перемещения с целью установки их в необходимое место. К группе грузоподъемных машин относят консольно-поворотные краны и пневмоподъемники.
Транспортирующие машины и оборудование предназначены для перевозки различных грузов. Они должны обеспечивать непрерывное или периодическое (циклическое) перемещение единичных грузов или их групп. К транспортирующим машинам, обслуживающим участок, относят электрокары с тележками.
Виды и количество подъемно-транспортного оборудования, необходимого для эффективного обеспечения производственного процесса ремонтного предприятия, зависят от номенклатуры ремонтируемых объектов, их массы и размеров, типа производства и формы организации труда, типа и размеров производственных помещений, а также от производительности выбранного оборудования. и схем путей транспортирования грузов.
На участке ремонта коробок перемены передач, для перемещения, установки и снятия объектов ремонта (коробок и корпусов коробок) предусматриваем консольно-поворотные краны.
Выбираем консольный кран 4045, грузоподъемность 5 кН; выход, стрелы 4 м, установленная мощность электродвигателя 2,2кВт.
Транспортировка коробок передач на участок и с участка производится с помощью тележек и электрокар.
6.4 Расчет количества рабочих мест При расчете количества рабочих мест учитывается годовая трудоемкость выполняемых работ, годовой фонд времени рабочего места и принятый метод производства.
Для обоснованного нами тупикового метода ремонта количество рабочих мест определится по зависимости
nр.м. =Тг.i / nрФн.р.С (6.10)
где пр— количество рабочих на одном рабочем месте; nр= 1. Количество рабочих мест для разборки-сборки КПП
пр.м= 630 + 1690/2007· 1·1 = 1,04
Принимаем 2 рабочих места.
Количество мест для дефектации:
nр.м. = 430/2007· 1·1 = 0,18
Принимаем одно рабочее место.
Количество рабочих мест для контроля и комплектования:
nр.м. =330 + 12,7/2007· 1·1 = 0,14
Принимаем одно рабочее место.
Число рабочих мест доя выполнения слесарно-механической обработки:
nр.м. = 69 + 1640/2007· 1·1= 0,83
Принимаем два рабочих места.
Количество рабочих мест для выполнения подгоночных и регулировочных работ:
nр.м= 390/2007· 1·1 = 0,03
Принимаем два рабочих места.
Для выполнения обкатки коробок после сборки, предусматриваем одно рабочее место.
6.5 Расчет площади и разработка технологической планировки участка Для выполнения технологической планировки участка вначале произведем расчет его площади по формуле:
Sу=?Sok (6.11)
где So — площадь пола, занимаемая i-ым видом оборудования к — коэффициент, учитывающий рабочие зоны, проходы, проезды.
Для участков, на которых выполняются разборочно-сборочные работы, механическая обработка К = 4,0…6,0.
Принимая во внимание габариты оборудования (ведомость оборудования) определяем площадь участка ремонта, коробок перемены передач:
Sу=(0,96· 2+2,1·2+4,5+2,7+2,0+0,96+0,96)·5=70,9 м2
Принимаем площадь участка равную 72 м2.
При разработке технологической планировки участка обозначаем структурные элементы здания, оказывающие влияние на расстановку технологического и подъемно-транспортного оборудования, местонахождение рабочих при выполнении операций, места подвода электроэнергии, сжатого воздуха и др. Оборудование располагаем таким образом, чтобы к нему имелся доступ для подачи объектов ремонта, в соответствии с нормами технологического проектирования и правилами безопасности труда. Принятое оборудовании размещаем на участке придерживаясь следующих принципов: расстояние об' стены до тыльной поверхности оборудования 600 мм, между двумя соседними станками1700…2100 мм. Для установки, снятия и перемещения коробок и корпусовкоробок передач с одного рабочего места на другое предусматриваем консольно-поворотные краны. Проходы, проезды и расположение оборудования позволяет проводить монтаж, демонтаж и ремонт оборудования, а также убирать отходы производства.
6.6 Расчет потребности в энергоресурсах В качестве исходных данных для определения потребности в энергоресурсах принимается технологическая планировка участка ремонта коробок передач, режим работы потребителей энергии, средний и максимальный часовой ее расход.
Расчет потребности в электрической энергии определяем раздельно по силовой и осветительной нагрузкам. Суммарная потребность электроэнергии определяется:
W = Wс + Wо, (6.12)
где Wc и Wo — соответственно годовой расход силовой и осветительной электроэнергии, кВтч.
Годовой расход силовой электроэнергии определяется:
Wс = РэФо.д.зззс, (6.13)
где Рэ — суммарная установленная мощность электрооборудования, кВт; принимается по ведомости оборудования;
Зз — коэффициент загрузки оборудования; зз = 0,7…0,8 [26];
Зс— коэффициент спроса, учитывающий неодновременность работы оборудования, зс = 0,3…0,4.
Wc=(1,2· 2+7,95+30+1,7+2,2+1)19460,7 0,3 = 18 001дкВт· ч Расход электроэнергии на освещение определяется по выражениию
Wо = Тосв10-3 ?Si *Wуд, (6.14)
где Тосв — среднее количество электрического освещения в год. При односменной работе Тосв = 800 ч [26];
Si — площадь пола i-ro освещаемого помещения, м2; Si = 72 м.
Wуд— удельный расход электроэнергии на освещение 1 м2 площадь пола помещения.
Для отделения ремонта коробок перемены передач принимается:
Wуд =15…25Вт/м2, [26];
Wo = 800 -10-3· 72·25 = 1440 кВтч.
Суммарная потребность электроэнергии будет равна:
W = 18 001+ 1440 = 19 441кВт-ч.
Потребность в сжатом воздухе рассчитывают исходя из наличия воздухопотребителей и их расхода. На участке сжатый воздух используется на обдувку деталей.
Годовая потребность в сжатом воздухе:
Qв=KсKпKэ?Qср.iФд.о, (6.15)
где Kс — коэффициент спроса на воздух потребителей, Kс=0,4…0,6;
Kп — коэффициент, учитывающий потери воздуха из-за не плотности соединений, Kп =1,5;
Kэ — коэффициент, учитывающие условия эксплуатации, Kэ =1,3;
Qср.i — средний расход сжатого воздуха i-ым потребителем. Для обдувки деталей Qср.=20 м3 /ч.
Qв=0,5· 1,5·1,3·20·1946=37 947м3
7. Проектирование средств механизации обкатки корпуса КПП
7.1 Обоснование актуальности разработки Для увеличения срока эксплуатации при капитальном ремонте агрегатов и узлов необходимо проведение операций обкатки и испытания отремонтированных изделий. Обкатка позволяет выявить все явные недочеты ремонта и сборки, позволяет устранить их и дать возможность плавной приработки работающих попарно деталей.
В процессе обкатки КПП проверяют нормальное включение передач, отсутствие повышенных шумов шестерен в зацеплении и стуков, отсутствие течи масла в манжетах и стыках, а также отсутствие друг .х неисправностей.
Предлагаемая конструкция стенда позволяет проделать предложенные выше операции с минимальными потерями ручного труда. В краткие сроки произвести обкатку КПП на трех нагрузочных режимах, поочередно испытывая и обкатывая каждую передачу.
Простота стенда, кратковременность работы, большая производительность позволяет использовать его как в специализированных предприятиях, так и в ремонтных мастерских хозяйств.
7.2 Анализ прототипов Собранные коробки передач обкатывают без нагрузки и под нагрузкой и испытывают. Для обкатки и испытания используют специальные стенды и установки, которые по принципу нагружения разделяют на разомкнутые и замкнутые.
Обкатку разомкнутым методом производят по следующей схеме.
Рисунок 7.1 — Схема обкатки коробок передач: 1 — электродвигатель, 2 — коробка передач, 3 — ускоряющий редуктор, 4 — тормоз Коробку передач 2 (рисунок 7.1) устанавливают на стенд, первичный вал соединяют с электродвигателем 1. Во время обкатки коробку нагружают тормозными (механическими, гидравлическими или электрическими) устройствами 4. Такие стенды просты в устройстве и обслуживании. Энергия развиваемая электродвигателем должна переводиться в' другой вид энергии через тормозное устройство. Их легко изготовить, из-за чего область применения данных стендов распространена как на МОИ, ЦРМ, так и на специальные ремонтные предприятия.
Кроме таких стендов часто используют специальные приспособления с электродвигателем, устанавливаемые на раму и корпус трансмиссии автомобилей и позволяющие обкатывать КПП совместно с задним мостом. Недостатком этих устройств является отсутствие специальных тормозных нагружающих устройств.
7.3 Описание конструкции и принципа работы Стенд состоит из следующих составных частей: привода, нагрузочного тормоза, пульта управления, тележки механизма зажима, механизма перемещения, рамы. Рама сварной конструкции выполнена из швеллеров. Привод является механизмом, через который первичный вал испытуемой коробки передач получает вращение. Основной несущей частью привода является стойка.
С одной стороны к стойке закреплен двигатель, противоположный торец стойки предназначен для закрепления испытуемой коробки передач. Закрепление коробки производится за проушины картера коробки передач двумя прижимами от двух цилиндров.
Соединение вала двигателя с первичный валом, коробки передач осуществляется через фрикционную муфту. В стенде. в качестве муфты применено сцепление автомобиля ЗИЛ. Включение и выключение муфты производится рычагом сцепления.
В качестве нагрузочного устройства в стенде применен электромагнитный порошковый нагрузочный тормоз. Тормоз установки на подвижной плите, которая имеет возможность продольного перемещения по направляющим. Перемещение тормоза осуществляется при помощи механизма перемещения.
На конце вала тормоза установлена муфта, которая имеет возможность соединения с фланцем вторичного вала испытуемой коробки передач. Муфта имеет подвижное защитное ограждение.
Фиксация необходимого положения подвижной плиты вместе с тормозом после соединения с коробкой передач производится механизмом зажима.
Тележка предназначена для установки испытуемой коробки передач и имеет подпружиненную площадку с регулируемым усилием сжатия пружины, что дает возможность центрировать по вертикали ось коробки передач с осью привода и тормоза. Конструкция тележки позволяет перемещать ее в продольном и поперечном направлениях для центрирования испытуемой коробки в горизонтальной плоскости. Верхняя часть тележки сменная.
Пульт управления отдален от основной части стенда и устанавливается в удобном для обслуживания месте. Пульт управления выполнен в виде электрического шкафа. На наружной панели размещены органы управления.
Принцип работы стенда заключается в создании нагрузки на шестерки испытуемой коробки передач посредством электромагнитного порошкового нагрузочного тормоза.
Регулирование нагрузки тормоза производится изменением напряжения постоянного тока, подаваемого на катушки тормоза от выпрямителя.
Конструктивное решения узлов стенда выполнено с учетом технологии обкатки.
Техническая характеристика стенда:
основные параметры и размеры производительность стенда, ш/ч время на установку КПП, мин габаритные размеры стенда, мм (длина, ширина, высота) масса, кг Подготовка стенда к работе.
Подготовить рабочую смесь и залить ее в электромагнитный порошковый нагрузочный тормоз. Отрегулировать при необходимости усилие пружины тележки, исходя из массы коробок передач ЗИЛ.
Установить в вал привода шлицевую муфту с маркировкой ЗИЛ для коробок передач автомобилей ЗИЛ.
Залейте в картер испытуемой коробки передач масло согласно техническим условиям на капитальный ремонт данной марки автомобиля и установить коробку на тележку стенда. Включить сцепление.
Переместить рукояткой подвижную плиту с тормозом к коробке передач так, чтобы муфта тормоза или переходное кольцо соединялось с фланцем вторичного вала коробки или тормозным барабаном. Продолжать подачу плиты с тормозом и коробкой передач вращением рукоятки так, чтобы шлицы первичного вала ее вошли в муфту привода, а торец картера дошел до полного соприкосновения со стойкой привода.
Повернуть рукоятку крана в положение «Зажим плиты». Открыть вентиль для подачи воды в тормоз. Включиться двигатель привода. Включить сцепление. Испытать коробку передач без нагрузки согласно техническим условиям на капитальный ремонт на каждой передаче. Испытать коробку передач под нагрузкой на каждой передаче. Снять напряжение на выпрямительном устройстве, переведя, переключатель и выключатель в исходное положение. Нажать кнопку «стоп». Снять коробку передач. Отключить стенд.
Стенд транспортируется потребителю упакованным в ящики любым видом транспорта.
7.4 Технические расчеты Расчет шпоночного соединения Тс и [Тс] - расчетное и допускаемое напряжение на срез для шпонки, МПа ([Тс] = 60…90МПа) Рисунок 7.2 — Схема шпоночного соединения Рабочая длина шпонки:
гдедлина шпонки, мм;
ширина шпонки, мм.
Выступ шпонки:
где — высота шпонки, мм;
— глубина паза, мм.
Таким образом, прочность шпонки обеспечена.
Выбор электродвигателя зобщ. =з2муфт з4тд =0,982 -0,994 = 0,923
Рассчитаем требуемую мощность электродвигателя:
Так как муфту подбирают по ГОСТ 21 424–75, то расчет ее осуществляем как проверочный.
Расчет муфты МУВП (рас 6.2) состоит из проверочного расчета упругих элементов на смятие:
усм = 2Tк/(ZD + ld)<[усм], (7.3)
уu=Ткl/0,1dzD1< [уи], (7.4)
где Тк — расчетный крутящий момент муфты;
D1 — диаметр окружности расположения центров пальцев (D1 = 108 мм);
d — диаметр пальцев под резиновыми кольцами или втулкой (d = 14 мм);
1 — длина втулки (1 = 32 мм);
Z — число пальцев (Z— 6);
усм — расчетное напряжение смятия между палыцами и втулкой;
[усм] = 2. .4 МПа — допускаемое напряжение смятия для резины;
уи — расчетное напряжение на изгиб для пальцев;
[уи] = 60. .80 МПа — допускаемое напряжение на изгиб для пальцев.
Расчет схемы упругой втулочно-пальцевой муфты Рисунок 7.3 — Упругая втулочно-пальцевая муфта Тк=кТ, (7.5)
где Т — крутящий момент, передаваемый муфтой при установившемся режиме работ (номинальный момент);
к — коэффициент динамичности или режима работы, учитывающий дополнительные инерционные динамические нагрузки на муфту, его значения зависят от рода приводного двигателя и назначения рабочей машины (к = 1,5).
Передаваемый телом вращения крутящий момент Тсвязан с мощностью Р и угловой скоростью W зависимостью:
Т =Р/W, (7.6)
где Т — крутящий момент, Н· м;
Р — передаваемая мощность, Вт (3 = 15 000 Вт);
Wугловая скорость, рад/с.
Т= 15 000/104,7 =143,3 Н· м Тк= 1,5 143,3 = 215 Н· м усм = 1,48 МПа < [усм] = 2…4 МПа, уи=38,7МПа<[уи] = 60…80Мпа.
Условия выполняются. Работоспособность муфты обеспечена. Расчет шпоночного соединения. В нашей машине в приводе на валу электродвигателя двигателя установлена полумуфта МУВП посредством шпоночного соединения. В данном случае установлена призматическая шпонка 16×10×90 по ГОСТ 23 360–78.
Достаточность принятых размеров шпонки проверяем расчетом соединения на прочность. Расчет шпоночных соединений на прочность осуществляется обычно как проверочный.
Расчет призматической шпонки производим по следующим формулам на смятие:
усм =2Т/dlрK<[усм], (7.7)
Тс=2Т/dlрb<[Тс], (7.8)
где Т — передаваемый вращающий момент, Н· мм;
dдиаметр вала, мм (d = 56 мм);
b и 1р — соответственно ширина и рабочая длина шпонки, мм;
К — справочный размер для расчета на смятие, мм;,
усм и [усм] - расчетное и допускаемое напряжение на смятие для шпоночного соединения МПа ([а см] = 100… 150 МПа).
Ртр=Рк/зобщ=27,2/0,923=29,5 кВт Выбираем электродвигатель серии АИР с номинальной мощностью: Р = 30 кВт.
Таблица 7.1 — Варианты электродвигателей
Вариант | ТипЭД | кВт | Частота вращения | |||
синхронная | ||||||
1 2 | АИР180М2 АИР180М4 | 30 30 | 2950 1470 | 1,4 1,4 | 2,5 2,3 | |
По условиям обкатки n= 1000 + 1400 об/мин.
Из двух вариантоввыбираем второй.
Расчет угловой скорости:
W=Wном=рnном/30=3,14· 1470/30=154 с-1
Рассчитаем вращающий момент:
Т =Рдв/Wном=30· 103/154=194,8 Н· м
8. Охрана труда
8.1 Необходимость охраны труда Охрана труда — одна из важнейших социально-экономических проблем. Она предусматривает широкую систему законодательных, социально-экономических, организационных, технических, гигиенических и лечебно-профилактических мероприятий и средств, обеспечивающих сохранение здоровья и работоспособности человека в процессе труда.
В настоящее время ещё не везде и не в полной мере используются эффективные меры профилактики травматизма. Причины несчастных случаев, как правило, связаны с использованием неисправных машин и оборудования, неправильной организацией отдельных производственных процессов, слабым техническим надзором со стороны должностных лиц. Целью раздела «Охрана труда» является анализ состояния охраны труда в хозяйстве и разработка мероприятий, благодаря которым можно добиться снижения количества несчастных случаев и создать здоровые и безопасные условия труда.
Техника безопасности — один из разделов охраны труда, представляющий собой систему организационных и технических мероприятий и средств, предотвращающих воздействие на работающих опасных производственных факторов. Проведение мероприятий по Т.б., а также создание и применение технических средств Т.б. осуществляются на основе утвержденной в установленном порядке нормативно-технической документации — стандартов, правил, норм, инструкций.
Организационные мероприятия по Т.б. включают: инструктаж и обучение работающих безопасным и безвредным методам и приёмам работы; обучение пользованию защитными средствами, применяемыми на основе норм производственной санитарии и гигиены труда; разработку и внедрение регламентов труда и отдыха при выполнении тяжёлых работ и работ во вредных условиях.
Технические мероприятия по Т.б. основываются на определённых нормах и правилах. Например, габаритно-планировочные нормы учитывают площади и объёмы помещений, расстояния между оборудованием, необходимые для создания благоприятных и безопасных условий труда; параметрические нормы ограничивают эксплуатационные параметры оборудования, конструкционно-расчётные — определяют оптимальные размеры, качество, методику расчёта.
8.2 Анализ состояния безопасности труда в ОАО"Барановичский райагросервис"
Планирование мероприятий по улучшению условий труда, предупреждению травматизма и заболеваемости на производстве является одной из функций управления охраной труда на предприятии и осуществляется в соответствии с Положением о планировании и разработке мероприятий по охране труда (утверждено постановлением Министерства труда Республики Беларусь от 23.10.2000 № 136).
Ответственность за состояние охраны труда и безопасность жизнедеятельности на производстве несет инженер по охране труда и технике безопасности. Он проводит все необходимые мероприятия, включая: контроль за соблюдением действующих законодательств, инструкций, правил и норм по охране труда, технике безопасности, производственной санитарии, противопожарной защите, изучает условия труда на рабочих местах участвует в проверке технического состояния оборудования, осуществляет контроль за состоянием предохранительных приспособлений и защитных устройств, разрабатывает инструкции по охране труда и технике безопасности, организует пропаганду и изучение работниками правил техники безопасности, производственной санитарии и противопожарной защиты. Проводит вводные инструктажи работников предприятия. Участвует в расследовании случаев производственного травматизма, непрофессиональных заболеваний, изучает их причины, при необходимости проводит расследование по данному случаю. Расследование несчастного случая должно быть проведено в срок не более трех дней. Контролирует правильность составления заявок на спецодежду, защитные устройства и т. д. Составляет отчетность в сроки и по формам вышестоящим организациям.
Каждый специалист в хозяйстве отвечает за состояние охраны труда и безопасность жизнедеятельности непосредственно в своем структурном подразделении, которое закреплено за ним.
При трудоустройстве нового работника инженер по ОТ проводит вводный инструктаж, а затем непосредственно на рабочем месте начальник подразделения или участка проводит первичный инструктаж. Первичный инструктаж на рабочем месте проводят в соответствии с инструкциями по охране труда, разработанными для отдельных профессий или видов работ, индивидуально с практическим показам приёмов и методов труда. После первичного инструктажа на рабочем месте и проверки знаний в течении 2…5 смен все рабочие выполняют работу под наблюдением руководителя, после чего оформляется их допуск к самостоятельной работе, который фиксируется датой и подписью инструктирующего в журнале регистрации инструктажа на рабочем месте.
Динамику травматизма на предприятии за последние три года можно проследить по таблице 8.1.
Таблица 8.1 — Показатели производственного травматизма
Показатели | Формулы и обозначения | 2010 г | 2011 г | 2012 г | |
Среднесписочное число рабочих | Р | ||||
Число несчастных случаев | Т | ||||
Число дней нетрудоспособности | Д | ||||
Показатель частоты травматизма | Кч = 1000Т/Р | 11,1 | 5,5 | 5,2 | |
Показатель тяжести травматизма | КТ = Д/Т | ||||
Показатель потерь рабочего времени | КП = КчКТ | 177,6 | 82,5 | 93,6 | |
Как показывают данные таблицы 8.1, количество лиц, пострадавших при несчастных случаях, остаётся практически на одном и том же уровне. Наибольший уровень травматизма наблюдался в 2010 году. Однако, в связи с принятыми мерами и мероприятиями по улучшению охраны труда, показатель частоты травматизма в 2012 году по сравнению с 2011 годом снизился на 6,1%.
Травматизм в хозяйстве сохраняется по нескольким причинам. Одна из них — недоиспользование средств, выделяемых на мероприятия по охране труда (таблица 8.2).
Таблица 8.2—Выделение и использование средств на мероприятияпо охране труда
Показатель | 2010 г. | 2011 г. | 2012 г. | ||||
План | Факт | План | Факт | План | Факт | ||
Всего затрат, млн. руб., в т. ч: | |||||||
На номенклатурные мероприятия | 8,5 | ||||||
На средства индивидуальной защиты | 12,5 | ||||||
На лечебно-профилактическое питание и молоко | |||||||
Ассигновано на одного работника, тыс.руб. | 47,5 | ||||||
Данные таблицы 8.2 показывают, что идёт постепенное увеличение затрат на мероприятия по охране труда. Однако фактические затраты невелики и их явно недостаточно для проведения качественной защиты работников.
Анализируя состояние охраны труда на в ОАО «Барановичский райагросервис, необходимо отметить ряд нарушений норм и правил охраны труда:
— контроль за соблюдением требований охраны труда рабочими и служащими производится нерегулярно;
— проведение инструктажей сводится главным образом к росписи работника в журнале регистрации инструктажа;
— слабо ведётся работа по пропаганде безопасности труда;
— территория фермы не ограждена, освещение территории недостаточное;
— выгульные площадки для животных не имеют твёрдого покрытия;
— помещения для содержания животных не оборудованы системой вентиляции, освещение не соответствует норме;
— низкий уровень механизации производственных процессов приводит к значительному применению ручного труда.
В данном дипломном проекте предусматривается решение некоторых, наиболее важных с точки зрения безопасности труда, проблем.
8.3 Требования безопасности при работе с машинами семейства ЗИЛ
1. После получения наряда-задания водитель грузового автомобиля обязан:
а) в целях обеспечения безопасной и бесперебойной работы на линии проверить техническое состояние грузового автомобиля, обратив внимание на исправность шин, тормозов, рулевого управления, болтов крепления карданного вала, исправность проводки, фар, стоп-сигнала, указателей поворотов, звукового сигнала, контрольно-измерительных приборов, зеркал заднего вида;
б) произвести ежесменное техническое обслуживание и заправку грузового автомобиля топливом, маслом, водой, антифризом (в холодное время года) и тормозной жидкостью, проверить уровень электролита в аккумуляторной батарее;
2. Водитель грузового автомобиля не должен выезжать на линию при следующих нарушениях требований безопасности:
а) неисправностях механизмов и систем, при которых запрещается эксплуатация автомобиля;
б) несоответствии характеристик грузового автомобиля характеристикам груза по объему, грузоподъемности, длине и другим параметрам;
в) отсутствии или неисправности осветительных приборов, зеркал заднего вида, сигнального устройства, огнетушителей.
3. Для заливки горячей воды при разогреве двигателя следует использовать специальные ведра с носиком в верхней части, создающим направленную струю. При разогреве двигателя при помощи пара или горячего воздуха шланг необходимо присоединить к горловине радиатора и надежно закрепить,
4. После использования калорифера для прогрева двигателя кабину автомобиля следует проветрить для удаления продуктов сгорания.
5. При выполнении ремонтных работ водитель обязан выключить двигатель, затормозить автомобиль стояночным тормозом и включить первую передачу.
6. При остановке на уклоне необходимо подложить под колеса не менее чем два противооткатных упора.
7. Перед подъемом автомобиля домкратом следует удалить пассажиров из кабины, затормозить автомобиль стояночным тормозом, подложить противооткатные упоры под колеса, не подлежащие подъему, выровнять площадку под домкрат и подложить под него широкую подкладку из древесины.
8. При накачивании шины колеса, снятого с автомобиля, следует пользоваться приспособлением, предохраняющим от удара при выскакивании замочного кольца.
9. Запрещается выполнять работы по ремонту и обслуживанию автомобиля под приподнятым кузовом самосвала, а также во время погрузочно-разгрузочных работ и в случае установки автомобиля в опасной зоне действующих грузоподъемных механизмов.
10. Грузы, превышающие габариты грузовой платформы автомобиля по длине на 2 м и более (длинномерные грузы), должны перевозиться на автомобилях с прицепами-роспусками, к которым грузы должны надежно крепиться.
Требования безопасности в аварийных ситуациях грузового автомобиля:
11. В случае возгорания топлива или перевозимого груза водитель должен погасить огонь при помощи огнетушителей, кошмы, брезента, песка и других подручных средств. При невозможности самостоятельной ликвидации пожара водитель должен вызвать пожарную охрану в установленном порядке и сообщить руководителю работ.
Автомобиль должен обслуживаться водителем не ниже 4-го разряда, прошедшим специальное обучение и имеющим удостоверение машиниста с разрешающей отметкой в графе (категории)С, Е. Запрещается использовать автомобиль для перевозки людей. Не допускайте присутствия посторонних на рабочей площадке. Следите за тем, чтобы на автомобиле постоянно находился огнетушитель. Каждый работающий на автомобиле должен знать, как пользоваться огнетушителем в случае необходимости. В кабине предусмотрено место под установку огнетушителя порошкового 0П-1 В (Момент-2) производства Лидского завода сельскохозяйственных машин.
8.4 Организация пожарной безопасности в ОАО «Барановичский райагросервис»
Правовая основа и принцип организации системы пожарной безопасности и государственного пожарного надзора в РБ определены в законе «О пожарной безопасности», принятом Верховным Советом Республики Беларусь в 1993 г. Согласно этому закону государственное управление в области обеспечения пожарной безопасности осуществляется Советом Министров РБ, Министерством внутренних дел РБ, местными Советами депутатов. Государственный надзор за обеспечением пожарной безопасности предприятиями, учреждениями и организациями независимо от форм собственности, а также гражданами осуществляет орган Государственного пожарного надзора МВД РБ.
Требования по обеспечению пожарной безопасности народнохозяйственного комплекса предусматриваются в стандартах, нормах, правилах и других документах.
Обязанности и ответственность должностных лиц за пожарную безопасность отдельных территорий, технологического оборудования определяет руководитель хозяйства своим приказом (распоряжением).
Предприятиями и организациями создаются межхозяйственные опорные пункты пожарной охраны, внештатные пожарные формирования — добровольная пожарная дружина (ДПД). Все расходы по содержанию ДПД несет предприятие.
При планировке сельскохозяйственных объектов противопожарные разрывы между ними определяют от степени огнестойкости .
Чтобы принудительно прекратить горение, необходимо исключить возможность совокупного действия трех факторов: горючего вещества, окислителями температуры. Поэтому задачи при пожаротушении состоят в том, чтобы остановить испарение или разложение жидких и твердых сгораемых веществ и образования горючих паровых газов; прекратить поступление кислорода воздуха в зону горения или разбить кислород до концентрации ниже 13%, понизить температуру горящих веществ. Наиболее применимым естественным огнетушащим веществом является вода, земля, песок. Недостатками воды как огнетушащего вещества являются: затруднение использования ее при минусовой температуре вследствие замерзания воды. Недостатком земли и песка является отсутствие охлаждающего действия, поэтому после ликвидации огня возможны повторные возгорания.
К высокоэффективным специальным веществам относится пена — смесь газа с жидкостью, имеющей относительно высокий коэффициент поверхностного натяжения. Для получения пены применяют негорючий и не поддерживающий горение газ и негорючие жидкости. Пена изолирует горящую поверхность от постоянного поступления кислорода воздуха, препятствует нагреванию испарению газообразного горящего вещества.
Высокоэффективным средством пожаротушения являются специальные порошковые составы. Порошковое тушение заключается в механическом сбивании пламени, разбавление кислорода в зоне горения и изоляции горящих материалов. Кроме того, порошки тормозят химическую реакцию горения.
Наиболее эффективными первичными средствами пожаротушения являются огнетушители. Большое распространение в сельском хозяйстве имеют химические пенные огнетушители ОХП-10. Они предназначены для тушения очагов пожара твердых материалов и горючих жидкостей, за исключением электроустановок, находящихся под напряжением, щелочных материалов и карбида кальция.
Огнетушители воздушно-пенные ОВП-5,ОВП-10, имеют в сравнении с ОХП преимущество в том, что заряд их не содержит химически активных веществ, а состоит из 6% водного раствора пенообразователя ПО-1.
Имеются пожарные щиты оснащенные инвентарем.
Огнетушители углекислотные — предназначены для тушения различных веществ и материалов, а также электроустановок под напряжением до 1000 В.
Все работники организации, в том числе ее руководитель, регулярно проходят обучение по охране труда и подвергаются проверке знаний и требований охраны труда в установленном порядке. Для обучения работающих безопасности труда, проведения инструктажей ОАО «Барановичский райагросервис» имеется кабинет, оборудованный стендами, знаками, оснащенный плакатами, наглядным пособием и литературой.
В ОАО «Барановичский райагросервис» проводятся следующие виды инструктажей: вводный, первичный на рабочем месте, целевой, повторный и внеплановый.
Со всеми поступающими на предприятие работниками (при оформлении на работу до приказа) независимо от их образования, квалификации и стажа работы по данной профессии или должности проводится вводный инструктаж. Первичный инструктаж и стажировка на рабочем месте проводится после вводного инструктажа перед допуском к самостоятельной работе со всеми рабочими, принятыми на работу или переведенными из одного подразделения в другое. Программа первичного инструктажа составляется руководителем подразделения предприятия, учебного заведения, согласовывается со службой охраны труда и утверждается руководителем предприятия. Повторный инструктаж проводится не реже, чем через 3 месяца по программе первичного инструктажа с дополнением некоторых вопросов. При необходимости также проводятся внеплановый и целевые инструктажи.
Прием работника на работу, непосредственно связанную с движением транспортных средств, производится после обязательного предварительного медицинского осмотра в установленном порядке.
С целью озеленения по периметру предприятия расположена посадка деревьев. Общее техническое и санитарно-гигиеническое состояние производственных объектов находится в удовлетворительном состоянии. В производственных корпусах ТО и ремонта автомобилей полы загрязнены масленой коркой, плохо работает приточно-вытяжная вентиляция, слабое освещение рабочих мест, недостаточное отопление бокса, санитарные узлы требуют необходимой замены и ремонта.
Производственные здания и сооружения построены в соответствии с требованиями СНиП 11−280 и СНиП 11−89−80. Все они, в том числе и вспомогательные помещения, оборудованы центральным отоплением, а также имеют вытяжную вентиляцию.
В целях обеспечения санитарно-бытового и лечебно-профилактического обслуживания работников в организации по установленным нормам оборудованы санитарно-бытовые помещения, помещения для приема пищи, помещения для оказания медицинской помощи, комнаты для отдыха в рабочее время.
В соответствии со статьей 213 Трудового Кодекса РБ работники, занятые на тяжелых работах и на работах с вредными и опасными условиями труда, а также на работах, связанных с движением транспорта, проходят за счет средств предприятия обязательные предварительные и периодические медицинские осмотры. В каждом цехе предприятия оборудованы пожарные щиты, укомплектованные необходимым инструментом и средствами пожаротушения: огнетушителями из расчета один огнетушитель на 50 м2 площади, но не менее двух на одно помещение, ящиками с песком вместимостью 0,5 м3 на 100 м2, лопатами и т. д., имеются краны гидранты.
Также объекты производства обеспечены гардеробными помещениями, умывальными, душевыми, уборными, комнатами отдыха. На предприятии имеется транспорт для перевозки людей на работу и с работы.
Расстановка применяемого оборудования производится в соответствии с технологическим процессом и требованиями техники безопасности. Расстояния между элементами оборудования, оборудованием и элементами зданий не ниже нормативных. Расстояния между стеной и слесарным оборудованием 0,5 м., между боковыми и тыльными сторонами оборудований не менее 0,5 м., между автомобилем и оборудованием не менее 1 м. Полы в помещении с твердым бетонным покрытием, устойчивые к воздействию кислот, щелочей и масел.
К технологическим работам по ТО допускаются автослесари, прошедшие первичный инструктаж и инструктаж на рабочем месте. При производстве технического обслуживания по разработанной технологии необходимо проверять исправность зануления. После выключения электродвигателя необходимо дождаться полной остановки вращающихся деталей конструкции. Необходимо следить за состоянием подшипников и болтовых соединений. Регулярно производить смазку подшипников, цепи и других подвижных деталей. Перед началом работы слесарь должен: надеть установленные по нормам средства индивидуальной защиты (спец. одежду, обувь), проверить состояние рабочего места, исправность ручного инструмента и подготовить его к работе.
При включении подъемника возможен случай замыкания фазового провода на корпус электродвигателя. Для предотвращения поражения работников электрическим током применяем защитное зануление, т. е. преднамеренное электрическое соединение с нулевым проводом сети металлических нетоковедущих частей электродвигателя, которые могут оказаться под напряжением.
9. Энергосбережение
9.1 Общие сведения Важнейшим приоритетом государственной энергетической политики в Республике Беларусь наряду с устойчивым обеспечением страны энергоносителями является создание условий для функционирования и развития экономики при максимально эффективном использовании топливно-энергетических ресурсов (ТЭР).
Республика Беларусь не располагает значительными собственными запасами ископаемых ТЭР и вынуждена до 85 процентов ТЭР импортировать из-за рубежа.
Стратегической целью деятельности в области энергосбережения является снижение энергоемкости внутреннего валового продукта (ВВП) и, как следствие, снижение зависимости республики от импорта ТЭР, что может быть достигнуто за счет:
— повышения эффективности использования энергоносителей в результате внедрения новых энергосберегающих технологий, оборудования, приборов и материалов, утилизации вторичных энергоресурсов и др.;
— структурной перестройки отраслей экономики и промышленности;
— оптимизации топливного баланса республики с увеличением доли местных видов топлива, нетрадиционных и возобновляемых источников энергии.
Эффективность проводимой государственной политики в сфере энергосбережения подтверждается тем фактом, что с 1996 года прирост валового внутреннего продукта (ВВП) обеспечивается практически без увеличения энергопотребления, за последние 9 лет значение показателя энергоемкости ВВП снижено более чем в 1,75 раза.
Программными документами, определяющими пути реализации потенциала экономии энергоресурсов в Республике Беларусь, являются Республиканские программы по энергосбережению, утверждаемые в установленном законодательством порядке Правительством Республики Беларусь на 5 лет.
В Республике Беларусь выстроена четкая система финансирования энергосбережения. Финансирование мероприятий по энергосбережению осуществляется за счет:
— собственных средств предприятий;
— средств целевого фонда энергосбережения;
— средств инновационных фондов министерств и ведомств;
— средств республиканского и местных бюджетов;
Для усиления работы по энергоэффективности, выполнения повышенных заданий по энергосбережению в республике широко используется передовой зарубежный опыт эффективного использования ТЭР и активно привлекаются средства международных финансовых организаций, в том числе Всемирного Банка, ПРООН, ГЭФ.
Постановлением Совета Министров Республики Беларусь от 30 декабря 2004 года № 1680 утверждена Целевая программа обеспечения в республике не менее 25 процентов объема производства электрической и тепловой энергии за счет использования местных видов топлива и альтернативных источников энергии на период до 2012 года.
В условиях ограниченности собственной ресурсной базы актуальными являются проблемы энергетической безопасности. Под энергетической безопасностью подразумевается гарантия надежного и бесперебойного энергоснабжения страны в нормальных условиях и чрезвычайных ситуациях.
9.2 Энергосбережение при эксплуатации машинно-тракторногопарка Основные потери при эксплуатации техники в растениеводстве связаны с наличием не оптимально скомплектованного машинно-тракторного парка сельскохозяйственных предприятий с неправильным выбором состава и режимов работы агрегатов, нарушением правил использования и технического обслуживания тракторов, автомобилей и комбайнов.
Потери топлива при транспортировке, хранении и заправке машин непосредственно связаны с эксплуатацией машинно-тракторного парка, и поэтому их целесообразно рассматривать в едином комплексе.
Для сокращения потерь нефтепродуктов при транспортировке необходимо применять технически исправные герметизированные цистерны. Заполнять их рекомендуется нижним наливом «под уровень», так как заполнение свободно падающей струёй способствует разбрызгиванию и испарению топлива. В этом случае потери бензина составляют 2…3 кг на тонну перевозимого продукта. Особое внимание нужно обращать на герметичность всех соединений и уплотнений, исправность дыхательных клапанов и окраску цистерн в светлые тона для уменьшения нагрева. Необходимо полностью сливать топливо из соединительных рукавов и шлангов.
Во время хранения в результате неплотного соединения трубопроводов, негерметичности люков и крышек резервуаров, неисправности дыхательных клапанов, трещин в сварных швах, а также нагрева солнечными лучами может происходить непосредственная утечка топлива, его испарение, окисление, а также загрязнение пылью и атмосферной влагой. В результате количественных потерь и качественных изменений нефтепродукт перестает соответствовать требованиям ГОСТа и ТУ и его невозможно использовать. Весьма значительны потери топлива от испарения в зависимости от заполнения резервуара (таблица 9.1).
Таблица 9.1 — Интенсивность испарения бензина от степени заполнения резервуара
Степень заполнения, % | |||||||
Потери в год, % | 0,3 | 0,6 | 1,0 | 1,6 | 3,6 | 9,6 | |
Потери бензина за год составляют 70−140 кг, и поэтому хранить его в незаполненных резервуарах запрещается. Следует израсходовать топливо полностью из одного резервуара, а затем уже переходить к отпуску из следующего.
На испарение топлива влияет нагрев резервуара, что связано с его окраской. Испарение топлива и его нагрев всегда меньше, если резервуар окрашен в светлые тона и находится в тени. Нагрев сказывается на окислении топлива, при котором образуются смолисто-асфальтовые соединения, вызывающие усиленное нагарообразование в камере сгорания двигателя, что способствует снижению экономичности и повышению расхода топлива примерно на 6−8%. Кроме того, при испарении из бензина удаляются легкие пусковые фракции, снижаются противодетонационные качества, что ухудшает запуск двигателя, делает работу двигателя неэкономичной.
Хранение нефтепродуктов на нефтескладах с подземным размещением резервуаров позволяет поддерживать постоянный температурный режим, что уменьшает потери топлива от испарения.
К мероприятиям по сокращению потерь нефтепродуктов от испарения и загрязнения при хранении можно отнести:
— создание емкостей повышенной прочности, работающих под избыточным давлением;
— термостатирование резервуаров;
— уменьшение газового пространства;
— установка газоуравнительных систем для емкостей;
— усовершенствование конструкций дыхательной арматуры.
Для хранения нефтепродуктов под избыточным давлением требуются емкости повышенной прочности, при этом резко сокращается объем малых дыханий и, следовательно, загрязнение и испарение топлива. Топливо с высокой упругостью паров лучше хранится в шаровых, каплевидных, горизонтальных цилиндрических и других резервуарах, которые выдерживают давление до 0,197 МПа, что позволяет почти полностью устранить малые дыхания.
Внедрение механизированных заправочных средств сокращает не только количественные, но и качественные потери нефтепродуктов, а также длительность простоев машин на заправке. При рациональном применении механизированных заправочных средств, благодаря снижению простоев тракторных агрегатов под заправкой и потерь времени на перегон тракторов к стационарным пунктам заправки, производительность МТА увеличивается.
Требования к оборудованию нефтескладов предусматривают: сохранение качества нефтепродуктов в процессе хранения; ликвидацию потерь при заправках, приемке и хранении; сокращение времени заправки машин; обеспечение учета количества выданных топлива и масел.
Эти требования могут быть обеспечены, когда оборудование нефтескладов находится в исправном состоянии и содержится в постоянной технической готовности. Для этого необходимо совершенствование и качественное проведение технического обслуживания и ремонта оборудования, что позволяет сократить простои МТП; снизить затраты на ремонт топливной аппаратуры и машины в целом; сократить время на заправку машин, уменьшить потери нефтепродуктов и сэкономить дизельного топлива до 2,5, бензина — до 3,5 и моторного масла до 6%.
Важный резерв экономии моторных масел — повторное их использование после регенерации, для чего необходимо организовать сбор отработанных масел.
Большое значение имеет организация в нефтехозяйствах контроля качества нефтепродуктов. Основным документом, характеризующим соответствие данного продукта стандарту или ТУ, является паспорт качества, в котором приводят показатели качества, определенные в лаборатории изготовителя нефтепродукта. При обнаружении несоответствия этих показателей — продукт признают нестандартным и бракуют.
С целью экономии горюче-смазочных материалов (ГСМ) при эксплуатации МТП необходимо постоянно поддерживать составные части тракторов, автомобилей и самоходных машин в технически исправном состоянии:
— контролировать мощность и расход топлива двигателем методами технической диагностики;
— поддерживать нормальный тепловой режим работы двигателя;
— применять нефтепродукты в соответствии со временем года;
— периодически удалять накипь из системы охлаждения, нагар и смолистые отложения из трубопроводов и глушителя;
— своевременно проводить соответствующие виды периодических и сезонных обслуживаний;
— соблюдать правила технической эксплуатации прицепных и навесных сельскохозяйственных машин;
— не допускать перегрузку двигателей и буксование тракторов и самоходных сельскохозяйственных машин и комбайнов;
— повышать уровень технической эксплуатации машинно-тракторного парка.
Исследования, проведенные БелНИТИАТ на автомобилях МАЗ в автотранспортных предприятиях показали, что из 30 проверенных 80% топливных насосов не обеспечивали допустимого значения цикловой подачи на номинальных оборотах, что приводило к снижению мощности двигателей до 27 л. с. Из 38 проверенных автомобилей на 40% не соответствовал допустимым значениям угол начала подачи топлива, который находился, а пределах 3−27о вместо нормативных 19−21; 72% двигателей имели заниженную до 1500 об/мин или завышенную до 2500 об/мин максимальную частоту вращения холостого хода (вместо 2225−2275 об/мин); 56% имели отклонение от допустимых значений мощности на ведущих колесах до 20%.
Вероятно, еще большие отклонения существуют у тракторных дизелей в сельскохозяйственных предприятиях, где нет соответствующего диагностического оборудования и недостаточно подготовленных кадров мастеров-наладчиков.
Применение малосернистых топлив (с содержанием серы до 0,5%) повышает ресурс дизельных двигателей на 20−30%, а использование топлива с содержанием серы до 1% приводит к дополнительным затратам на ТО, ремонт и запчасти примерно равным 10% стоимости израсходованного топлива.
Использование экологически чистого дизельного топлива на основе метилового эфира кислот рапсового масла позволяет получить экономию денежных средств до 10% за счет более низкой стоимости биотоплива из рапса. При этом следует иметь в виду, что биотопливо обладает значительными преимуществами:
— при использовании до минус 12 оС не требуются присадки;
— лучше смазывающее действие, следовательно, меньший износ деталей двигателя;
— очень низкое содержание диоксида серы, поэтому меньше износ двигателя, не засоряется окружающая среда, исключаются кислотные дожди;
— сгорает с меньшим количеством сажи, чем обычное дизтопливо;
— меньше испаряется, отсутствует улетучивание при заправке;
— биологически расщепляется на 100% (не засоряет окружающую среду).
Важным фактором, влияющим на расход топлива, является поддержа-ние тракторов и сельскохозяйственных машин в технически исправном состоянии. Например, неисправность или неправильная регулировка одной форсунки дизельного двигателя увеличивает расход топлива на 15−20%. При отклонении угла начала подачи топлива на 3−5° удельный расход возрастает на 4−8%. Понижение температуры, охлаждающей жидкости на 30−40 0С приводит к увеличению расхода топлива на 5−10% из-за ухудшения процесса сгорания. Увеличение толщины накипи на стенках системы охлаждения на 1,1 мм повышает расход топлива на 7−8%. Износ цилиндро-поршневой группы на 0,01 мм ведет к перерасходу топлива на 0,5%. Велико влияние состояния ходовой системы тракторов на сопротивление движению и, следовательно, на расход топлива. Поддержание нормального давления в пневматических шинах и оптимального напряжения гусениц тракторов — важные условия его экономии топлива.
Несвоевременное обслуживание воздухоочистителя приводит к перерасходу топлива на 3−6%, а при сильном загрязнении — до 15%.
Уменьшение угла опережения впрыска топлива у дизельного двигателя на 2 градуса повышает удельный расход топлива на 10%. Снижение частоты вращения коленчатого вала на 150−200 оборотов в минуту вызывает падение его мощности на 7−10% и соответствующее снижение топливной экономичности.
Наибольшая мощность и экономичность достигается при оптимальных значениях угла опережения впрыска. Отклонение от этих значений вызывает снижение показателей работы двигателя, мощность снижается на 1,5% на каждый градус отклонения от оптимального угла опережения впрыска.
Износ обратного клапана топливного насоса приводит к возрастанию часового расхода топлива до 31%, так как в результате увеличивается цикловая подача топлива, продолжительность и запаздывание впрыскивания, вследствие чего нарушается нормальный процесс сгорания топливной смеси в цилиндрах, двигатель работает жестко, с дымным выхлопом, детали перегреваются, износ увеличивается, быстро закоксовываются распылители форсунок. Из-за износа разгрузочного пояска обратного клапана не происходит четкой отсечки подачи топлива, в результате чего давление в трубопроводе высокого давления падает медленно, распылители форсунок подтекают, а сами распылители закоксовываются и форсунка выходит из строя.
Опыт передовых хозяйств, где техническое обслуживание машин на высоком уровне, показывает, что затраты на ремонт и ТО снижаются на 17−20%, мощность двигателя больше на 8−20%, а расход топлива ниже на 7−12% по сравнению с тем, что есть в хозяйствах, где не налажено регулярное техническое обслуживание.
В последнее время на дизельных автомобилях зарубежного производства применяется дизельная топливная аппаратура системы «CommonRail», которая позволяет производить впрыск топлива при давлении 1200−1700 кг/см2. При этом улучшается распыление и, следовательно, полнота сгорания топлива, что улучшает экономические и экологические показатели двигателей.
В улучшении использования машинно-тракторного парка важное место принадлежит укрупнению размеров рабочих участков (контуров) и полей севооборота. Мелкая контурность пашни снижает производительность агрегатов, ведет к увеличению расхода горючего и затрат на эксплуатацию техники, препятствует внедрению прогрессивных методов и форм ее использования сдерживает перевод сельского хозяйства на промышленную основу.
Кроме размеров участков, на эффективность использования сельскохозяйственной техники влияют факторы, сопутствующие мелкой контурности. Это прежде всего низкий коэффициент распаханности сельскохозяйственных угодий, вследствие чего хозяйства с мелкоконтурным землепользованием имеют меньшие размеры по площади пашни, что приводит к недоиспользованию техники, снижению ее наработки.
9.3 Мероприятия по энергосбережению Учитывая огромные объемы использования восстанавливаемых природных ресурсов и энергоносителей, проблема сбережения последних становится едва ли не самой насущной. Конкретные источники и пути сбережения ресурсов реализуются путем применения соответствующих интенсивных технологий, использования экономичного оборудования, борьбы с потерями и др.
Ресурсосберегающие мероприятия нередко являются одновременно природоохранительными. Такова, например, утилизация производственных отходов и др.
Для перевода энергосбережения в хозяйстве на более высокий уровень предлагаем следующие мероприятия:
— обновление парка машин, закупка современных высокопроизводительных комбинированных, посевных агрегатов позволяющих сократить число проходов по полю тем самым сэкономить топливо при выполнении технологических операций. Так же обновление парка машин позволит организовать рациональное комплектование машинно-тракторных, что приведет к увеличению производительности МТА и снижению расхода топлива;
— производство работ в растениеводстве необходимо осуществляется в составе рационально скомплектованных технологических комплексов, что повышает эффективность использования машинно-тракторного парка (повышается производительность, снижается расход топлива);
— исходя из рельефа местности предлагается при выращивании зерновых и других культур в хозяйстве перейти на машины (опрыскиватели, разбрасыватели для подкормки растений удобрениями), имеющие ширину захвата 18 м. Чтобы при посеве обеспечить такое расстояние между технологическими проходами (колеями), посевные агрегаты должны иметь ширину захвата 6 м;
— необходимо изменить технологию выращивания сельскохозяйственных культур в сторону использования минимальной и нулевой обработок почвы. По сравнению с традиционной, они уменьшают также эрозионные процессы почвы. Для этого необходимо приобрести комбинированные посевные широкозахватные;
— зерноуборочные комбайны должны быть оборудованы стеблеподъемниками для работы в сложных погодных условиях и приставками, позволяющими проводить одновременно с уборкой измельчение и равномерное распределение по полю соломы.
10. Технико-экономическое обоснование проекта
10.1 Затраты на модернизации стенда Расчёт затрат для модернизации стенда проводится по следующей формуле:
где З — затраты на для для модернизации стенда, тыс. руб.;
М — стоимость материала, тыс. руб.;
— расходы на оплату труда, тыс. руб.;
— общепроизводственные расходы, тыс. руб.;
Стоимость материала, используемого для модернизации стенда рассчитывается по формуле:
где — стоимость одного килограмма металла, тыс.руб.,
— масса заготовки, кг.
М=382,5 тыс. руб.
Расходы на оплату труда определяются:
где — заработная плата производственных рабочих;
— дополнительная заработная плата производственных рабочих;
— отчисления на социальное страхование;
— единый платеж чрезвычайного налога и обязательных отчислений в государственный фонд содействия занятости.
(10.4)
гдесредняя часовая тарифная ставка, тыс.руб. /ч;
— трудоемкость производственной программы (12 ч),
— коэффициент, учитывающий доплаты стимулирующего характера, Кув=1,6.
Средняя часовая тарифная ставка определяется по формуле:
где — часовая тарифная ставка i — го разряда, тыс.руб.,
— количество производственных рабочих iго разряда, чел.
На участке работает 1 рабочий четвертого разряда, часовая тарифная ставка четвертого разряда составляет 2,175 тыс. руб /ч., и два рабочих третьего разряда, часовая тарифная ставка составляет 2,1тыс.руб/ч.
где — норматив отчислений на дополнительную заработную плату производственных рабочих (в % от основной заработной платы).
где — ставка отчислений на социальное страхование, %.
где — ставка единого платежа чрезвычайного налога и отчислений в государственный фонд содействия занятости, %.
Величину общепроизводственных расходов принимаем в % от основной платы производственных рабочих, занятых изготовлением приспособления (Rоп = 145%):
Затраты на модернизацию составят:
10.2 Расчет инвестиций Капитальные вложения представляют собой затраты денежных средств на восстановление и расширение основных средств производства, что способствует увеличению выпуска продукции, росту производительности труда, снижению себестоимости продукции.
Первоначальная стоимость основных фондов принимается по их фактической стоимости и включает в себя:
где — сметная стоимость производственных зданий, тыс. руб.;
— балансовая стоимость оборудования, тыс. руб.;
— стоимость приборов, приспособлений, инструмента и инвентаря, тыс. руб.
Для определения балансовой стоимости оборудования, пригодного к дальнейшей эксплуатации, составляем смету на оборудование предприятия до реконструкции. На основании сметы производим выборку технологического оборудования, подлежащего списанию, и определяем его стоимость. Тогда балансовая стоимость оборудования, пригодного к дальнейшей эксплуатации составит:
где — балансовая стоимость всего имеющегося оборудования, тыс. руб.;
— балансовая стоимость оборудования, подлежащего списанию, тыс. руб.
Стоимость приборов, приспособлений, инструмента и инвентаря, которые пригодны к дальнейшей эксплуатации, определяется по их фактической стоимости за вычетом суммы ежегодного их обновления:
где — стоимость приборов, приспособлений, инструмента и инвентаря, пригодных к дальнейшей эксплуатации, тыс. руб.;
— стоимость имеющихся в мастерской приборов, приспособлений, инструментов и инвентаря, тыс. руб.;
— ежегодный коэффициент обновления приборов, приспособлений, инструментов и инвентаря, (0,2…0,3).
Тогда первоначальная стоимость основных фондов составит:
Стоимость основных фондов по проектируемому варианту равна сумме первоначальной стоимости фондов и капитальных вложений на реконструкцию.
Для определения величины капитальных вложений рассчитываем балансовую стоимость дополнительно приобретенного оборудования для организации производства после реконструкции и стоимость дополнительно приобретенных приборов, приспособлений, инструмента и инвентаря.
Стоимость дополнительного оборудования определяется с использованием таблицы 10.1.
Таблица10.1 — Расчет стоимости дополнительного оборудования
Наименование оборудования (тип, модель) | Количество единиц шт. | Общая стоимость оборудования, тыс. руб. | |
1. Станок радиально-сверлильный 2А55 | |||
2. Станок радиально-расточной РР-4 | |||
Итого: | |||
Сумма транспортно-складских расходов (7% от стоимости оборудования), тыс. руб. | 5300,8 | ||
Затраты на монтаж оборудования (4% от стоимости оборудования), тыс. руб. | |||
Капитальные вложения на приобретение дополнительного оборудования | 84 055,8 | ||
Стоимость дополнительно приобретаемых приспособлений, инструментов, инвентаря определяем по укрупненным нормативам:
где — процент стоимости приборов, приспособлений, инструмента, инвентаря от стоимости оборудования, Капитальные вложения:
10.3 Расчет себестоимости ремонта картера КПП Покупные комплектующие изделия, полуфабрикаты и услуги коммерческих предприятий:
где — стоимость запасных частей на единицу продукции, тыс. руб.;
— годовая производственная программа.
Ремонтные материалы:
где — стоимость ремонтных материалов на единицу продукции, тыс.руб.
Основная заработная плата производственных рабочих:
где — средняя часовая тарифная ставка, тыс.руб./ч;
— трудоёмкость производственной программы;
— коэффициент учитывающий доплаты стимулирующего характера (1,5−2).
Средняя часовая тарифная ставка:
где — часовая тарифная ставка i-го разряда, тыс. руб.;
— количество производственных рабочих i — го разряда, чел.
Дополнительная заработная плата производственных рабочих:
гденорматив отчислений на дополнительную заработную плату производственных рабочих (10%).
Отчисления на социальные нужды:
Единый платёж:
Таким образом, расходы на оплату труда производственных рабочих с отчислениями равны:
Расходы на содержание и эксплуатацию оборудования Амортизация оборудования и приспособлений:
где — норма амортизационных отчислений на оборудование (10%);
— норма амортизационных отчислений на приспособление (13%);
— стоимость оборудования и приспособлений соответственно.
Затраты на текущий ремонт оборудования:
где — норматив отчислений на текущий ремонт оборудования (3%).
Стоимость электроэнергии и воды:
где — годовой расход электроэнергии (кВтч);
— стоимость соответственно 1 кВтч электроэнергии, тыс. руб.
Прочие неучтённые расходы (расходы на охрану труда, изобретательство и т. д.) принимаются в размере 5% от суммы вышеперечисленных расходов:
Расходы на содержание и эксплуатацию оборудования:
Цеховые расходы в общем виде определяются:
где — основная заработная плата аппарата управления, тыс. руб.;
— дополнительная заработная плата управления, тыс. руб.;
— отчисления на социальное страхование аппарата управления, тыс.руб.;
— единый платёж чрезвычайного налога и отчислений в государственный фонд содействия занятости, тыс. руб.;
— амортизация производственного здания, тыс. руб.,
— текущий ремонт производственного здания, тыс. руб.;
— прочие неучтённые расходы статьи, тыс.руб.
Основная заработная плата:
где-должностной оклад по категориям ИТР, тыс. руб.;
— коэффициент, учитывающий доплаты стимулирующего характера к основной заработной плате ().
Дополнительная заработная плата принимается в размере 10% от основной заработной платы:
Отчисления на социальные нужды для промышленных предприятий принимаются в размере 35% от расходов на оплату труда:
Чрезвычайный налог и обязательные отчисления в государственный фонд содействия занятости:
Амортизация зданий определяется по формуле:
где — норма амортизации зданий (2%);
— первоначальная стоимость здания, тыс.руб.
Затраты на текущий ремонт и содержание зданий:
где — норматив затрат на текущий ремонт зданий (1%).
Прочие неучтённые расходы принимаются в размере 5% от суммы вышеперечисленных расходов:
Общая сумма общепроизводственных расходов составит:
Общехозяйственные и внутрипроизводственные расходы Для предприятий, выпускающих ремонтную продукцию на сбыт, определяют себестоимость, в которую кроме цеховых расходов учитывают общехозяйственные и внепроизводственные (коммерческие) и прочие производственные расходы (
где — процент общехозяйственных расходов от величины основной заработной платы производственных рабочих (100%);
— процент на коммерческие расходы от основной заработной платы производственных рабочих (5%);
— процент прочих производственных расходов от величины основной заработной платы производственных рабочих (5%).
Полная себестоимость рассчитывается:
Определяем себестоимость одного условного ремонта:
Результаты расчётов сводятся в таблицу 10.2.
Таблица 10.2 — Структура себестоимости восстановления КПП
Статьи затрат | Базовый вариант (1) | Проектируемый вариант (2) | Отклонение +/ ; | |||
Сумма, тыс. руб. | %к итогу | Сумма, тыс. руб. | %к итогу | |||
Расходы на оплату труда производственных рабочих с отчислениями | 13,02 | 20 710,3 | 12,53 | — 0,49 | ||
Затраты на запчасти | 43,47 | 43,55 | 0,08 | |||
Затраты на ремонтные материалы | 20 197,4 | 14,67 | 14,82 | 0,15 | ||
Расходы на эксплуатацию и содержание оборудования | 10 143,3 | 7,37 | 12 388,6 | 7,49 | 0,12 | |
Цеховые (общепроизводственные) расходы | 17 019,9 | 12,37 | 20 826,3 | 12,6 | 0,23 | |
Прочие производственные расходы | 605,1 | 0,44 | 677,3 | 0,4 | — 0,04 | |
Общехозяйственные расходы | 8,2 | 8,19 | — 0,01 | |||
Внепроизводственные расходы | 605,1 | 0,44 | 677,3 | 0,4 | — 0,04 | |
Себестоимость восстановления блоков | 137 611,8 | 165 324,8 | x | |||
Выводы: из выше приведенных расчетов видно, что основу текущих затрат на осуществление восстановления КПП складывают затраты на запасные части, и затраты на ремонтные материалы, остальные затраты имеют примерно равный вес в себестоимости продукции.
10.4 Определение отпускных цен на восстановления КПП где — налоговые платежи из выручки.
Прибыль:
Выручка:
где — ставка отчислений в республиканский и местный фонд поддержки сельскохозяйственных производителей и аграрной науки (3,9%).
Определяем в денежном эквиваленте налог НДС:
Определяем отпускную цену на единицу продукции с учётом НДС:
10.5 Оценка эффективности инвестиций Эффективность капиталовложений отражает экономический результат целесообразности осуществления капиталовложений.
Годовой доход от инвестиций в общем виде рассчитывается:
где — прибыль до инвестирования, тыс. руб.;
— прибыль после инвестирования, тыс. руб.;
— амортизация зданий, оборудования, приспособлений доинвестирования, тыс. руб.;
— амортизация зданий, оборудования, приспособлений послеинвестирования, тыс.руб.;
— налоги, уплачиваемые из прибыли до инвестирования, тыс. руб.;
— налоги, уплачиваемые из прибыли после инвестирования, тыс. руб.
Амортизационные отчисления:
где — амортизация зданий после инвестирования, тыс. руб.;
— амортизация оборудования и приспособлений после инвестирования, тыс. руб.
Рассчитаем налоги, уплачиваемые из прибыли:
где — налог на недвижимость (1% от стоимости ОПФ);
— налог на прибыль после инвестирования (18% балансовой прибыли);
— отчисления на развитие инфраструктуры и транспортный сбор (3,5% и 0,5% соответственно от балансовой прибыли).
В свою очередь:
где — балансовая стоимость зданий, тыс. руб.;
— балансовая стоимость оборудования, тыс. руб.;
— балансовая стоимость приспособления, тыс. руб.;
— ставка налога на недвижимость, тыс. руб.
Рассчитаем налог на прибыль после инвестирования:
где — ставка налога на прибыль, тыс. руб.
Отчисления на развитие инфраструктуры и транспортный сбор:
где — величина налога на развитие инфраструктуры и транспортный сбор.
Налог, уплачиваемый из прибыли:
Рассчитаем налоги, уплачиваемые из прибыли до инвестирования.
Прибыль до инвестирования:
Амортизационные отчисления до инвестирования:
Налог на недвижимость до инвестирования:
Рассчитаем налог на прибыль до инвестирования:
Отчисления на развитие инфраструктуры и транспортный сбор до инвестирования:
Рассчитаем налоги, уплачиваемые из прибыли до инвестирования:
Годовой доход от инвестиций:
Показателей эффективности капитальных вложений Чистый дисконтированный доход:
гдекоэффициент приведения;
— величина инвестиций, тыс. руб.
где — процентная ставка (15%);
Т — расчётный срок (10 лет).
Срок возврата капитала:
где — коэффициент возврата капитала:
Индекс доходности:
Таблица 10.3 — Технико-экономические показатели проекта
Наименование показателей | Базовый вариант | Проектируемый вариант | Отклонение, +/; | |
Годовая производственная программа, шт. | ||||
Среднегодовое количество производственных рабочих, чел | ||||
Энерговооруженность труда, кВт./чел. | 6,1 | — 1,9 | ||
Энергоемкость продукции, кВт· ч/шт. | 7,54 | 8,26 | 0,72 | |
Величина инвестиций, тыс. руб.: | ; | 90 113,9 | ; | |
Себестоимость единицы продукции (услуги), тыс. руб. | 1909,8 | 1653,2 | — 256,6 | |
Отпускная цена единицы продукции (услуги), тыс.руб. | 2546,4 | 2477,1 | — 69,3 | |
Годовой доход от инвестиций, тыс.руб. | ; | 20 500,6 | ; | |
Чистый дисконтированный доход, тыс. руб. | ; | 12 799,1 | ; | |
Срок окупаемости капитала, лет | ; | 7,7 | ; | |
Индекс доходности | ; | 1,14 | ; | |
ремонт автомобиль коробка машина
Заключение
1. Анализ состояния организации и технологии ремонта КПП ЗИЛ на ОАО «Барановичский райагросервис» показал, что их уровень не отвечает современным требованиям. Так трещины в корпусе коробки, изготовленном из чугуна, завариваются электродуговой сваркой, посадочные поверхности под подшипники восстанавливают постановкой ремонтной втулки, дефектные резьбовые отверстия заваривают и на этом же месте сверлят новые. Эти способы не обеспечивают требуемого качества ремонта.
2. Расширение рынка сбыта позволяет увеличить годовую производственную программу предприятия. Расчетная на ближайшую перспективу программа ремонта коробок перемены передач автомобилей составит 100 приведенных к КПП ЗИЛ ремонтов.
3. С учетом величин производственной программы и с целью обеспечения высокого качества отремонтированных КПП обоснован необезличенный подход их ремонта.
4. Ресурс отремонтированных КПП во многом зависит от уровня технологии восстановления корпуса коробки. С учетом материала корпуса разработана технология его восстановления, предусматривающая заделку трещин производить фигурными вставками, посадочных мест под подшипники — применением свертных втулок, резьбовых отверстий — постановкой резьбовых спиральных вставок.
5. Годовой объем работ участка ремонта коробок составляет 640 ч, годовая трудоемкость восстановления корпуса коробки — 180 ч. Для выполнения годового объема работ необходимо — 5 производственных рабочих, работающих на 6 рабочих местах и 6 единиц технологического оборудования — стенды для разборки-сборки, столы для дефектовки, комплектования и контроля, сверлильный и расточной станки, пресс гидравлический и стенд для обкатки собранных коробок.
6. В качестве конструкторской разработки предложен стенд для обкатки коробки без нагрузки и под нагрузкой. Экономическая эффективность применения стенда составляет.
Технико-экономические показатели проекта составляют: Чистый дисконтный доход за расчетный период (10 лет) составляет 12 799,1 срок окупаемости капитала 7,7 лет.
Список использованных источников
Надежность и ремонт машин / В. В. Курчаткин, Н. Ф. Тельнов, К. А. Ачкасов и др. Под редакцией В. В. Курчаткина — М.: Колос, 2000. — 776 с.
Миклуш В.П., Шаровар Т. А., Уманский Г. М. Организация ремонтно-обслуживающего производства и проектирование предприятий технического сервиса АПК — Мн.: Ураджай, 2001. — 661 с.
Ремонт машин: курсовое и дипломное проектирование: учебное пособие. Под редакцией Миклуша В. П. Мн.: БГАТУ, 2004. — 490с.
Молодык Н.О., Зенкин А. С. Восстановление деталей машин. Справочник — М: Машиностроение, 1989. — 479 с.
Авдеев М.В. и др. Технология ремонта машин, оборудования. М.: Агропромиздат, 1986 — 247 с.
Концепция развития технического сервиса АПК до 2005 года. — М.: ГОСНИТИ.
Курсовое и дипломное проектирование по ремонту машин. Под редакцией Смелова А. П. М: Агропромиздат, 1991. — 192 с.
Техническое обслуживание и ремонт машин. Под редакцией И. Е. Улёмана — М.: Агропромиздат, 1990. — 339 с.
Черновалов В. И. Организация и технология восстановления деталей машин — М.: Колос, 1989. — 336 с.
10.Воловик Е. Л. Справочник по восстановлению деталей. — М.: Колос, 1981. — 351 с.
П.Матвеев В. А., Пустовалов И. И. Техническое нормирование ремонтных работ в сельском хозяйстве — М.: Колос, 1979 г. — 354 с.
12.Сушкевич М. В. Контроль при ремонте с/х техники — М.: Агропромиздат, 1988. — 250 с.
13.Шадричев В. А. Основы технологии автостроения и ремонта автомобилей. — М: Машиностроение, 1976. — 376 с.
14.Ремонт автомобилей. Под редакцией СИ. Румянцева — М.: Транспорт, 1988. — 327 с.
15.Сидоров А. И. Восстановление деталей машин напылением и наплавкой — М.: Машиностроение, 1987. — 192 с.
16.Колясинский З. С., Сархомьян Г. Н., Лисковец A.M. Механизация и автоматизация авторемонтного производства — М.: Транспорт, 1982. — 160 с.
П.Кричевский М. Е. Применение полимерных материалов при ремонте сельскохозяйственной техники — М.: Росагропромиздат, 1988. — 143 с.
18.Бобусенко СМ. Проектирование ремонтно-обслуживающих предприятий — М.: Колос, 1991. — 295 с.
19.Дехтеринский Л. В. и др. Проектирование авторемонтных предприятий — М.: Транспорт, 1981. — 218 с.
20.Техническая эксплуатация сельскохозяйственной техники (Энциклопедическая книга с нормативными материалами). — М.: ГОСНИТИ, 1993. — 327 с.
21.Дипломное проектирование на факультете «Технический сервис в АПК» Учебно-методическое пособие. — Мн.: БГАТУ, 2003. — 124 с.
22.Проектирование ремонтно-обслуживающих предприятий НПК. Методическое пособие по курсовому и дипломному проектированию для студентов специальности С 03.01.00 «Механизация сельского хозяйства». -Мн.: БГАТУ, 1998. — 143 с.
23.Ведомственные нормы технологического проектирования ремонтно-обслуживающих предприятий Ч 1, 2. Участки основного производства. -Саратов: Гипропромсельстрой, 1984. — 162 с.
24. Оборудование ремонтных предприятий. Под редакцией В. В. Курчаткина. — М.: Колос, 1999 — 176 с.
25.Баранов Л. Ф. Техническое обслуживание и ремонт машин: Учеб. Пособ. Ростов Н/Д: Феликс, 2001. — 401 с.
26.Бетеля Г. Ф., Аляскович Г. И. Проектирование энергетических I / ресурсов предприятий технического сервиса АПК. Методические указания к курсовому и дипломному проектированию — Мн.: БГА" 'У, 2001. — 19 с.
27.Воробьев Л. А. Менеджмент организации. — Мн.: Дизайн-ПРО, 1999.
28.Воробьев Л. А. Основы управления производством: Учеб. Пособие. -Мн.: НПЖ «Финансы. Учет. Аудит», 1997. — 200 с.
29.Дурович А. П. Маркетинг в предпринимательской деятельности. -Мн.: НПЖ «Финансы. Учет. Аудит», 1997.
З0.Долинская М. Г., Соловьев И. А. Маркетинг и конкурентоспособность промышленной продукции. — М.: Издательство стандартов, 1991. 128 с.
31.Котлер Ф. Основы маркетинга: Пер. с англ. / Общ.ред. и вступ. ст. Е. М. Пеньковой. — Новосибирск: Наука, 1992.
32.Эванс Дж., Берман Б. Маркетинг: пер. с англ. — М.: Экономика, 1990.
33.Защита населения и объектов народного хозяйства в чрезвычайных ситуациях. Под ред. М. И. Постнина. Мн: Ушверс1тэцкае, 1997. — 278 с.
34.Методические указания. Методика расчета выбросов загрязняющих веществ в атмосферный воздух для предприятий агропромышленного комплекса. — Мн, 1996. — 74 с.
35.Охрана труда. Под редакцией Ф. М. Канарева. М.: Агропромиздат, 1998. — 350 с.
36.В. Т. Квасов Охрана труда в сельском хозяйстве. Мн.: Ураджай, 2000 — 245с.