Анализ производственного процесса предприятия ООО «Промтрактор-Промлит»
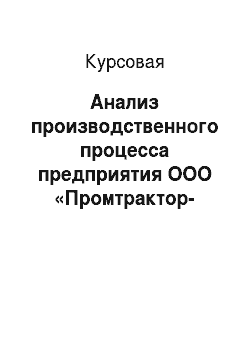
Рис. 2. Отливка (а), модель (б) и стержневой ящик (в) С помощью модели в песчанной форме получают внутреннюю полость, соответствующей конфигурации отливки. В стержневом ящике изготавливается стержень для образования внутренних полостей отливки. Модели и стержневые ящики делают неразъемными, разъемными, из двух и более частей и с отъемными частями, что облегчает выемку модели из формы и стержны… Читать ещё >
Анализ производственного процесса предприятия ООО «Промтрактор-Промлит» (реферат, курсовая, диплом, контрольная)
Содержание Введение
1. История предприятия ООО «Промтрактор-Промлит»
2. Производственная система и модернизация предприятия ООО «Промтрактор-Промлит»
3. Производственная деятельность предприятия ООО «Промтрактор-Промлит»
4. Сущность и характеристика литейного производства
5. Встряхивающая формовочная машина 703 М Заключение Список литературы
Введение
Проектирование продуктов в процессе производства включает разработку производственных операций, определение производственных мощностей и само проектирование изделий и процессов производства. Проектирование продуктов производится в соответствии с потребностями покупателей.
Критерии проектирования продуктов: стоимость, экономичность эксплуатации, качество, элементы роскоши, размер, мощность, прочность, срок службы, надежность в эксплуатации, простота эксплуатации, безопасность эксплуатации и универсальность использования.
Проектировщик должен принять решения относительно: размеров и формы, материалов, соотношения стандартных и специфических элементов, компонентов, элементов безопасности.
После того, как продукт спроектирован, определяются этапы процесса производства этого продукта. Критерии проектирования процесса производства: производственные мощности, экономическая эффективность, гибкость, надежность, производительность, пригодность к ремонту, стандартизация, постоянство результатов, безопасность, удовлетворение потребностей рабочих.
Проектировщик процесса производства должен принять решения относительно: типа перерабатывающей системы, то есть типа производства, собственно производства, комплектующих изделий, методов переработки, степени механизации и автоматизации, специализации рабочих.
Проектировщики изделий и процесса производства обязательно должны тесно сотрудничать между собой, так как разработка продукта и разработка процесса производства тесно взаимосвязаны.
Проектирование услуг и процесса их производства включает несколько факторов:
— месторасположение организации по оказанию услуг (оно обычно определяется месторасположением потребителя);
— потребности покупателей;
— календарное планирование работы;
— определение качества;
— навыки общения работников с потребителями;
— производственные мощности;
— эффективность работы служащих.
Любое предприятие рождается и воспроизводится как социально-экономическая система. Оно представляет собой органически целостную, вероятностную, динамическую совокупность объективно обусловленных элементов, взаимодействие которых создает возможность эффективного воспроизводства в зависимости от характера внутренних и внешних условий, реализации целей данной системы. Системный подход обусловливает исследование предприятий в качестве единого целого, единой системы, включающей другие, находящиеся в определенном взаимодействии составные элементы. Такая система представляет собой часть другой системы (более высокого уровня), в которой взаимодействует с другими подсистемами. Предприятие как система сохраняет внутреннюю целостность ее составных частей, а также обладает их общими свойствами. В результате получается качественно новое объединение.
При изучении предприятия как социально-экономической системы необходимо понять единство функционального и структурного подходов. Функции предприятия проявляются в его действиях во внутренней и поведении во внешней среде. Связь предприятия с внешней средой весьма многообразна. Внешняя среда оказывает самое непосредственное воздействие на все, что происходит внутри предприятия, и предприятие должно реагировать на все изменения внешнего мира. Таким образом, функциональный подход дает представление об основных рычагах и организационных механизмах, приводящих в действие предприятия и обеспечивающих им устойчивую и сбалансированную работу. Наличие прямой и обратной связи с внешней средой является одной из характерных черт системы и важнейшим фактором эффективного производства.
Структурный подход характеризуется разделением предприятия на составные элементы по определенным признакам и сложившимися связями между этими элементами. В состав элементов предприятия входят объекты двоякой природы. С одной стороны, это факторы, определяющие социально-экономическую структуру предприятия (работники подразделений, распределение полномочий, потоки информации и т. д.). С другой — элементы, определяющие производственно-техническую структуру предприятия (орудия труда, материальные ресурсы, технологии и т. д.).
Целью данной работы является изучение производственного процесса предприятия ООО «Промтрактор-Промлит».
Задачи работы — изучить методы проектирования продукта, а именно встряхивающей формовочной машины 703 М в литейном производстве.
1. История предприятия ООО «Промтрактор-Промлит»
Строительство Чебоксарского завода промышленных тракторов (ЧЗПТ) было начато 12 января 1972 года на основании Постановления ЦК КПСС и Совета Министров СССР № 606 от 3 августа 1966 года «Об ускорении развития в 1966;1970;х гг. производства тракторов, самоходных шасси и запасных частей к ним» и № 157 от 29 февраля 1972 года «О строительстве 1 очереди ЧЗПТ и реконструкции Волгоградского моторного завода МТСХМ (Министерство тракторного сельскохозяйственного машиностроения)».
28 июня 1988 г. приказом № 560 в составе ПО «ЧЗПТ» был образован Чебоксарский Литейный завод (ЧЛЗ). В марте 1990 г. приказом № 157 ЧЛЗ выделен в самостоятельное структурное подразделение, а приказом № 146 от 22.03.1994 г. образовано АООТ «Промтрактор-ЧЛЗ». Сегодняшнее название предприятия — ООО «Промтрактор-Промлит». Предприятие находиться под управлением Дивизиона железнодорожного литья и вагоностроения (ДЖДЛиВ) Компании Корпоративного Управления «Концерн «Тракторные заводы».
Технический проект строительства ЧЗПТ разрабатывался Харьковским институтом проектирования тракторных заводов и заводов с/х машиностроения, Государственным проектным институтом «Саратовпромпроект» и его филиалом в г. Чебоксары, ГО Электропроект, Гипрокоммундортранс, Магнитогорский «Проектавтоматика», Промтрансниипроект, Рижское отделение Теплоэлектропроект и др.
Первая очередь завода была рассчитана на производство 5 тысяч тракторов в год, из них: 4 тыс. Т-330 и 1 тыс. Т-500. В 1977 году Постановлением ЦК КПСС и Совета Министров СССР № 869 «О мерах по созданию мощностей по производству промышленных тракторов Т-330 и Т-500 и двигателей к ним на предприятиях Минсельхозмаша» программа выпуска была скорректирована до 6 тысяч тракторов в год. В состав ее входили следующие производственные объекты:
ь сдаточный корпус площадью 28 тыс. кв.м.;
ь прессово-сварочный — сборочный корпус — 198 тыс.кв.м.;
ь блок механических цехов № 1 — 115 тыс. кв.м.,
ь цех тяжелых стальных отливок мощностью на 120 тыс. тонн литья в год;
ь ремонтно-литейный цех мощностью на 30 тыс. тонн;
ь деревомодельный корпус площадью 15 тыс.кв.м.;
ь экспериментальный цех;
ь корпус приготовления формовочных материалов;
ь инженерные, складские, административные здания и вспомогательные объекты.
Литейное производство в составе ЧЗПТ включало в себя комплекс подразделений и производств, необходимых для изготовления чугунных и стальных отливок, а также цветного литья проектной мощностью 150 тыс. тонн литья в год. Основная продукция — крупногабаритные стальные и чугунные отливки деталей промышленных тракторов, крупногабаритные отливки для предприятий МТСХМ. Масса отливок от 50 г до 15 тонн, габариты — до 2000×1000×800 мм. Первым объектом литейного производства на строящемся ЧЗПТ был ремонтно — литейный цех (РЛЦ). Его строительство началось в феврале 1974 года. В январе 1978 года Госкомиссия приняла первые мощности на 10 тыс. т. литья в год — 1 очередь, в июле 1978 г — на 7 тыс. тонн — 2 очередь, в январе 1979 г. — на 13 тыс.т. — 3 очередь РЛЦ. Вторым объектом литейного производства стал Цех тяжелых стальных отливок (ЦТСО). 6 октября 1982 года здесь была проведена первая плавка.
Сейчас ЦТСО — это в ЛЦ-1 (литейный цех). Он является основным литейным цехом ООО «Промтрактор-Промлит». В проектировании ЦТСО участвовали специалисты Гипротракторсельхозмаша, а также ведущие иностранные фирмы по проектированию литейных предприятий. При выборе технологического оборудования помогла выставка литейного оборудования в Москве 1978 года. Наиболее важное литейное оборудование: система смесеприготовления, формовочные линии, стержневое оборудование, системы разливки металла, очистки литья, транспортировки отливок и регенерации смеси было закуплено у ведущих фирм США.
В 1982 году сданы первые мощности ЦТСО на 40 тыс. тонн литья В 1984 г. сданы мощности на 20 тыс. тонн и 40 тыс. тонн В 1987 г. сданы мощности на 10 тыс. тонн чугунного литья В настоящее время в комплекс литейного производства входят еще ряд объектов:
ь цех электрошлакового литья — организован в июне 1980 г. (впервые в отрасли);
ь деревомодельный корпус с цехом литейной оснастки — построен в 1981 году;
ь корпус приготовления формовочных материалов на 2,5 тыс. т. — сдан в эксплуатацию в 1982 году;
ь термообрубной корпус — построен в 1984 году.
В начале 90-х годов распались налаженные производственные связи, спрос на литье в России резко снизился, а у оставшихся партнеров не было средств для оплаты продукции. В этих условиях завод смог найти заказчиков за рубежом. При этом для получения разрешения на поставки пришлось пройти сертификацию на соответствие международному стандарту ISO 9002 и европейским стандартам EN 124 и EN 545. В мае 1993 г. предприятие начало отправку первой партии отливок (люки, решетки, корпуса затворной арматуры) во Францию, Испанию. Предприятие также поставляло свою продукцию в Англию, Испанию, Италию, Францию, Германию, Израиль, США.
По соглашению, заключенному с ОАО «РЖД» в июне 2002 года, предприятие приступило к выпуску новой продукции — железнодорожного литья, а в декабре 2003 г. был заключен долгосрочный договор на поставку ж/д продукции между ООО «Промтрактор-Промлит» и ОАО «РЖД». Освоение новой продукции потребовало модернизации производственных мощностей: существующие автоматические формовочные линии производства американской фирмы HERMAN были подвергнуты серьезной модернизации — был увеличен размер опок, произведена замена устаревших и изношенных узлов. Дополнительно было закуплено новое оборудование. Ссылка на стр. «Модернизация производства».
Благодаря модернизации имеющегося и установки нового оборудования, с 2003 по 2005 г. г. были освоены следующие виды продукции: рама боковая, балка надрессорная, крышка крепительная буксового узла, клин фрикционный, корпус буксы, корпус поглощающего аппарата, хомут тяговый, автосцепка СА-3 в сборе.
Для выпуска готовой продукции требовались мощности по их механической обработке. И в марте 2004 г. из состава Механического завода ОАО «Промтрактор» был выведен и передан на ООО «Промтрактор-Промлит» механический цех № 11 (МЦ-11).
В цехе смонтированы поточно-механизированные линии по обработке рамы боковой и балки надрессорной, налажена работа по их механической обработке. Линии рассчитаны на обработку соответственно 90 тыс. рам боковых и 50 тыс. балок надрессорных в год.
В 2007 г. в ТОЦ принята в эксплуатацию новая линия обработки корпуса автосцепки СА-3 собственной разработки и изготовления. Это позволило значительно увеличить выпуск этой продукции и повысить ее качество.
Оснащенность самым современным оборудованием и правильный выбор технологии изготовления отливок позволили предприятию за очень короткий срок занять ведущие позиции среди производителей отливок для нужд ОАО «РЖД». Система качества на предприятии сертифицирована на соответствие международному стандарту ISO 9001.
2. Производственная система и модернизация предприятия ООО «Промтрактор-промлит»
Для промышленного предприятия характерно производственно-техническое, организационно-экономическое единство, а также организационно-административная и финансово-экономическая самостоятельность.
Производственно-техническое единство обеспечивается технологической связью отдельных подразделений предприятия, общностью перерабатываемого сырья и материалов. Технологическая взаимосвязь дополняется наличием вспомогательного и обслуживающего хозяйств.
Организационно-экономическое единство характеризуется наличием единых органов управления, единого производственного коллектива, административной обособленности, взаимосвязью плана производства с обеспечивающими его выполнение материальными, техническими и финансовыми ресурсами, организацией деятельности на основе коммерческого расчета.
Указанное единство определяет хозяйственную самостоятельность предприятий, предусматривающую самообеспеченность необходимыми основными и оборотными средствами для осуществления производственной деятельности, самостоятельный сбыт своей продукции, наличие самостоятельной законченной системы отчетности и бухгалтерского баланса.
Организационно-административная самостоятельность заключается в предоставлении предприятию прав юридического лица, в организации всей его деятельности на основе полного самофинансирования, в пропорциональности и соподчиненности всех его звеньев, то есть производственное предприятие может приобретать, продавать средства и предметы труда, готовую продукцию предприятиям и организациям, быть истцом и ответчиком по своим обязательствам Финансово-экономическая самостоятельность предприятия выражается в разработке и утверждении своих планов, наличии расчетного счета в банках, законченной системы учета и бухгалтерской отчетности с выявлением окончательных финансовых результатов (прибыли, дохода).
Рис. 1. Схема функционирования производственной системы Производственная система — это особый класс систем, включающий работников, орудия и предметы труда и другие элементы, необходимые для функционирования системы, в процессе которого создаются продукция или услуги.
В широком смысле под системой понимается определенная совокупность элементов, образующих целое (составленное из частей), обладающее особенностями, которые отсутствуют у составляющих его элементов.
Предприятие рассматривается в качестве производственной системы, так как ему присущи все характерные для системы признаки. Подразделения предприятия (цехи, участки, службы, отделы и др.) в этом смысле выступают в качестве подсистем, состоящих из элементов различной степени сложности (трудящиеся, предметы и орудия труда и т. д.).
Схема функционирования производственной системы представлена на рисунке 1. В ней происходит преобразование входных материальных М, энергетических Е и информационных I потоков с целью обеспечения требуемого качества Q выпускаемых изделий за предписанный промежуток времени t. В результате выполнения операций Ci производственного процесса на выходе производственной системы будем иметь материальный M' и информационный поток I' потоки.
Завод обладает модернизированным производством. За 2003;2006 г. г. коренным образом были реконструированы все производственные участки, внедрены и введены в эксплуатацию:
ь автоматическая линия VDK-10 вакуумно-пленочной формовки (ВПФ) фирмы Heinrich Wagner Sinto (HWS), Германия с системой пескооборота, с габаритом опок 1800×3000×500/500 цикловой производительностью 20 форм/час, что позволило значительно увеличить выпуск высококачественного железнодорожного литья. Формовочная линия VDK-10 предназначена для производства стальных отливок «Балка надрессорная» и «Рама боковая» для грузовых вагонов, а также других отливок для машиностроения;
ь манипулятор модели C510E для выемки отливок из форм;
ь установку для выбивки стержней;
ь охладитель песка в кипящем слое с установкой охлаждения воды;
ь две установки пылеулавливания;
ь реконструирована автоматическая система транспортировки отливок «Кливленд Крейн», США, которая предназначена для транспортировки отливок из литейного в термообрубной корпус;
ь стержневые автоматы фирмы «LAEMPE» в количестве 7 шт. по технологии Cold Box альфа-сет процесс с газоочистным оборудованием для обеспечения стержнями работы трех автоматических формовочных линий;
ь капитально отремонтированы две и продолжается инвестирование на приведение к уровню современных требований остальных дуговых сталеплавильных печей ДСП-25;
ь отработана конструкция и используются водоохлаждаемые своды на печах ДСП-25;
ь осуществлен переход на выпуск металла в ковши емкостью 12,5 т и 30 т взамен ковшей емкостью 9 т, что позволило стабилизировать качество металла в форме и обеспечить его однородность;
ь продувка аргоном жидкой стали в ковше уменьшает количество вредных примесей и неметаллических включений, способствует выравниванию химического состава и температуры;
ь технология микролегирования и раскисления жидкой стали в ковше алюминиевой проволокой при помощи трайбаппаратов обеспечивает стабильное содержание вводимых элементов;
ь приобретена установка для экспресс-анализа химического состава металла фирмы «Спектролаб»;
ь внедрена и адаптирована система автоматизированного моделирования литейных процессов «MAGMAsoft». Внедрение данной системы позволило отрабатывать литейную технологию на стадии проектирования без дорогостоящих натурных экспериментов, оптимизировать конфигурацию литниковой системы, прибылей, температуры и режима заливки. Появилась возможность значительно усовершенствовать процесс проектирования и производства отливок. Это, в свою очередь, даёт экономию важнейших ресурсов — металла, рабочего времени, электроэнергии, позволяет повысить качество продукции и снизить ее себестоимость;
ь капитально отремонтированы камеры дробеструйной очистки крупного литья, поточные линии по зачистке и обрубке литья значительно повысили производительность финишных операций;
ь две новые линии станков по механической обработке позволяют отгружать потребителю все изделия с механической обработкой и сборкой;
ь программное обеспечение и станки с ЧПУ позволяют осуществлять сквозное проектирование, отработку технологического процесса и изготовление модельно-стержневой оснастки с высокой точностью и качеством;
ь гидравлический пресс для динамических и статических испытаний отливок позволяет осуществлять отработку конструктивных и технологических улучшений с контролируемыми результатами;
ь контрольно-измерительная машина с программным управлением используется для разметки модельно-стержневой оснастки и отливок;
ь лентопильные станки для порезки отливок по контролируемым сечениям для оценки дефектности.
3. Производственная деятельность предприятия ООО «Промтрактор-Промлит»
ООО «Промтрактор-Промлит» (полное название предприятия: общество с ограниченной ответственностью «Чебоксарский завод промышленного литья») — одно из самых современных литейных производств в России.
Производство ООО «Промтрактор-Промлит» состоит из следующих подразделений (производственных площадок):
1) ЛЦ-1 (литейный цех)
2) ЛЦ-2 (литейный цех)
3) ЛЦ-3 (цех электрошлакового литья)
4) ТОЦ (Термообрубной цех)
5) Механический цех (МЦ — 11)
Производственная мощность предприятия:
ь 80 тыс. тонн стального литья в песчано-глинистые формы на двух автоматических формовочных линиях фирмы Герман (США) с размерами опок 1300×1400×500/500 мм и 2500×1600×600/600 мм;
ь 55 тыс. тонн стального литья в сухие песчаные формы на линии вакуумно-пленочной формовки VDK-10 фирмы HVS (Германия) в опоках размером 3000×1800×500/500мм;
ь 5 тыс. тонн высококачественных стальных отливок, получаемых методом электрошлакового литья и центробежной заливкой в металлические формы;
ь 1тыс. тонн металлокерамических (порошковых) изделий в год.
Продукция предприятия сертифицирована Государственным регистром сертификации на федеральном железнодорожном транспорте (РС ФЖТ).
Литейный цех № 1
Литейный цех-1 — производство тяжелых стальных отливок.
Проектная мощность цеха:
ь 60 тыс. тонн стального литья. Отливки в песчано-глинистые формы производятся на двух автоматических формовочных линиях (АФЛ) фирмы Герман (США), размеры опок 1300×1400×500/500мм и 2500×1600×600/600 мм (АФЛ-2, АФЛ-3).
ь 55 тыс. тонн стального литья осуществляется в сухие песчаные формы на линии вакуумно-пленочной формовки VDK-10 фирмы HWS (Германия) в опоках размером 3000×1800×500/500мм (АФЛ-1).
Общая площадь цеха — 130 тыс. кв. м, в том числе 48 тыс. кв. м — производственной площади.
Основные технические данные АФЛ-1:
Ш оборудование: автоматическая формовочная линия вакуумно-пленочной формовки типа VDK-10;
Ш годовой выпуск литья — 55 тыс. т;
Ш производительность — 20 форм/час;
Ш размер опок в свету — 3000×1800×500/500мм.;
Ш максимальная металлоемкость формы — 2 т;
Ш оборот песка — 220 т./час.
Основные преимущества процесса вакуумно-пленочной формовки:
ь высокое качество поверхности и геометрическая точность отливок;
ь значительное уменьшение поверхностных и внутренних дефектов литья;
ь снижение трудоемкости финишных операций и механической обработки;
ь возможность использования недорогой деревянной модельной оснастки;
ь снижение расхода формовочных материалов;
ь высокая экологичность процесса;
ь автоматизация управления технологическим процессом.
Основные технические данные АФЛ-2:
Ш формовочная встряхивающая линия Herman;
Ш годовой выпуск литья — 40 тыс. т;
Ш производительность — 30 форм/час;
Ш размер опок в свету — 2500×1600×600/600;
Ш максимальная металлоемкость формы — 1,2 т.
Основные технические данные АФЛ-3:
ь формовочная встряхивающая линия Herman
ь годовой выпуск литья — 18 тыс. т;
ь производительность — 22 форм/час;
ь размер опок в свету — 1400×1300×500/500мм.;
ь максимальная металлоемкость формы — 0,6 т.
Подготовка производства начинается с разработки технологии изготовления отливок с использованием программы MAGMAsoft, разработки чертежей оснастки для изготовления отливок с использованием конструкторской САПР на базе программы «Solid Edge».
Изготовление оснастки производиться на автоматических станках с ЧПУ.
Изготовление стержней производится на автоматах фирмы «Laempe» (Германия).
Выплавка стали осуществляется на 5 дуговых электропечах ДСП-25-Н2-У4.
Транспортировка отливок в термообрубной цех осуществляется монорельсовой системой с тележками «Кливленд Крейн», США.
Литейный цех № 2
Производство стальных и чугунных отливок Проектная мощность цеха: 30 тыс. тонн литья в год, в том числе 22,4 тыс. тонн стального литья, 7 тыс. тонн чугунного, 400 тонн бронзового литья.
Литейное производство расположено в отдельном двухуровневом корпусе общей площадью 57 888 м 2 и включает в себя следующие участки:
ь формовочный — 5 760 м2;
ь смесеприготовительный — 11 016 м2;
ь плавильный — 9 360 м2;
ь стержневой — 4 320 м2;
ь участок изготовления уплотнительных колец;
ь термообрубной — 912 м²;
ь участок грунтовки литья — 1 152 м2.
Основные участки и оборудование:
1) Формовочный участок.
На участке имеются встряхивающие формовочные машины трех типов:
703 М -10 машин (5 пар),
6 формовочных машины 703 М с размерами опок 950×610×250/250 — стальные отливки,
4 формовочные машины 703 М с размерами опок Ш950×250/250- чугунные отливки.
Оба конвейера работают с применением единых песчано-глинистых смесей средней влажности.
Производительность: 19 форм/час.
ВВФ -2,5 — 4 машины (2 пары) Габариты опок: 1400×1000×400/400 мм. и 1400×1000×700/700 мм.
производительность: 4,5 форм/час.
Ф/машины ВВФ-2,5 работают с применением единой песчано-глинистой смеси средней влажности и с применением облицовочной песчано-глинистой смеси высокой влажности с последующей сушкой форм.
225−07 — 3 машины (1,5 пары) Габариты опок до 2500×1600×700 мм.
Ф/Машины работают попеременно с применением единой песчано-глинистой смеси средней влажности и с применением облицовочной песчано-глинистой смеси высокой влажности с последующей сушкой форм.
Производительность: 3 форм/час.
2) Смесеприготовительный участок.
Смесеприготовительный участок включает в себя 6 смесителей мод. АМК-2000Н производительностью 60м3/час каждый и системы конвейеров подачи готовой смеси и возврата горелой смеси с бункерами, полигональными ситами и магнитными сепараторами.
3) Плавильный участок.
Шесть дуговых печей ДС-6Н1 номинальной емкостью 6 тонн.
Средняя продолжительность плавки — 3 часа.
Футеровка: 4 печи — кислая; 2 печи — основная.
миксер «Piks» — 20/800 объемом 20 тонн.
4) Стержневой участок.
Стержневой участок разделен на два отделения:
— изготовления стержней из ХТС;
— изготовления стержней из смеси со связующим КО с термической сушкой.
Развес стержней от 5 до 3200 кг.
5) Термообрубной участок.
— дробеметные барабаны мод.42 213 — 4ед.
Производительность: 0,7 тн/час. Объем: 0,8 тн.
— дробеметная камера проходная Л203.61СБ — 1ед.
Производительность: 1,2 тн/час.
Грузоподъемность подвески: 2 тн.
— дробеметные камеры с выкатным столом мод.42 612 — 2ед.
Производительность: 3,2тн/час.
Грузоподъемность стола: 10 тн.
— дробеметный барабан «Вилибрейтор Фрай» — 1ед.
Производительность: 3,4тн/час. Объем: 5 тн.
— дробеметный барабан мод.42 246 — 1ед.
Производительность: 2 тн/час. Объем: 3 тн.
На участке имеется термическое оборудование:
— толкательный агрегат ВНИПИ «Теплопроект» Т36 663 — 2 ед. предназначенный для нормализационного отжига стального литья.
Агрегат двухрядный, по 8 поддонов в каждом ряду, максимальная г/п поддона 0,6 тн., средняя загрузка литья на поддон 0,48 тн. Темп толкания 0,5 часа.
Производительность: 4 поддона/час.
— печь с выкатным подом ГТСХМ 626 101 ПС в количестве 2 ед. предназначенных для проведения термической обработки чугунных и крупногабаритных стальных отливок по различным режимам:
искусственное старение (для чугуна) продолжительностью 12 часов;
нормализация (для стали) продолжительностью 5 часа; Количество поддонов в печи: 6 шт.
Максимальная г/п поддона 0,6 тн., средняя загрузка литья на поддон 0,56тн.
— закалочно — отпускной комплекс состоящий из двух камерных печей ГТСХМ 853 060 ПС (поз. 413 и 415) и закалочного водяного бака предназначенного для проведения улучшения стали, а также имеется возможность проведения других видов термической обработки литья в отдельной печи. Количество поддонов в каждой печи: 2 шт. Максимальная г/п каждого поддона 0,6 тн., средняя загрузка литья на поддон 0,52 тн. Средняя продолжительность режима 3,5 часа.
Литейный цех № 3
Цех электрошлакового литья (ЭШЛ, ЛЦ-3) осуществляет изготовление заготовок методом электрошлакового литья и изделий из металлических порошков из железографитовых и бронзовых материалов (фасонные заготовки типа шестерня, ступица, ось).
Мощность цеха — 5 тыс. тонн стального литья. Площадь — 2 252 кв. м, в том числе производственная — 1299 кв. м.
Основными формообразующими способами при получении заготовок методом ЭШЛ являются формирование металла в водоохлаждаемом кристаллизаторе или получение заготовок центробежным литьем. Имеющиеся оборудование позволяет получать заготовки массой до 2,5 тн с максимальными размерами до 1200 мм в диаметре и длиной до 1500 мм в водоохлаждаемом кристаллизаторе, а методом центробежного литья — массой от 100 до 350 кг с максимальным диаметром 1000 мм. Общая производственная мощность цеха электрошлакового литья — 5000 тн/год.
Отливки ЭШЛ обеспечивают высокие механические свойства и позволяют получать комбинированные заготовки с попутным приплавлением проката (труб, круга, квадрата и другого профиля) или кованого полуфабриката. Литая часть может быть более сложной формы, чем приплавляемая часть проката (поковки). Металл составных частей комбинированных заготовок может быть, как одной марки стали, так и разных. Возможно получение биметаллических заготовок.
Порошковое производство специализируется на изготовлении широкого спектра антифрикционных и конструкционных изделий на основе железа (с добавлением меди, никеля, графита, серы), на основе меди (бронзы оловянистые, свинцовистые (БрО10С10)), а также изделий из электротехнических материалов (медные, медно-графитные).
Завод имеет уникальный 1000-тонный гидравлический пресс для прессования порошковых изделий: из железографитных материалов — до 200 см², из медных и бронзовых порошков — до 400 см².
Термообрубной цех Цех занимается предварительной очисткой кустов в дробеметных камерах «Виллибрейтор Фрай», США, их разделкой, заточкой остатков литниковой системы, заливов, исправлением дефектов заваркой, термообработкой отливок в печах, очисткой отливок в дробеметных камерах, механической обработкой.
Установленное оборудование:
ь две нормализационные печи туннельные ВНИПИ Т 39 355−01 ПС для крупного литья;
ь две закалочно-отпускные печи Т 39 359−01 ПС для среднего литья;
ь шесть камерных печей для закалки, отпуска и нормализации ТР 55 302−01 ПС (для среднего литья).
Для увеличения производительности в 2007 г. в ТОЦ принята в эксплуатацию новая линия обработки корпуса автосцепки СА-3 собственной разработки и изготовления. Это позволило значительно увеличить выпуск этой продукции и повысить ее качество.
С вводом линии производительность увеличилась 6 до 10 корпусов автосцепок в смену на 1 человека.
Механический цех № 11
Цех занимается мехобработкой рамы боковой и балки надрессорной.
В цехе смонтированы поточно-механизированные линии по обработке рамы боковой и балки надрессорной, налажена работа по их механической обработке. Линии рассчитаны на обработку соответственно 90 тыс. рам боковых и 50 тыс. балок надрессорных в год.
На специальных агрегатных и специальных фрезерных станках обрабатываются:
ь рессорный проем, буксовый проем, кронштейны (рама боковая);
ь подпятниковое место, наклонные плоскости, скользуны (балка надрессорная).
Установленное оборудование изготовлено в России и странах ближнего зарубежья.
4. Сущность и характеристика литейного производства Основу деятельности любого машиностроительного предприятия составляет промышленно-производственная работа по изготовлению определенной продукции.
По признаку применяемых методов изготовления изделий выделяют виды производства — литейное, сварочное, сборочное и т. д.
В зависимости от вида продукции и потребностей в ней рынка, общего уровня технической вооруженности страны, развитости в ней прогрессивных форм обобществления труда машиностроительные предприятия отличаются и масштабами, и организационными формами ведения технологического процесса, имеют различную структуру и состав производственных цехов и оснащаются конкретными видами производственного оборудования.
По характеру выполняемой работы производственное оборудование делят на основное (технологическое) и вспомогательное. К основному относят производственное оборудование, непосредственно выполняющее операции технологического процесса. Вспомогательное — это оборудование, не участвующее непосредственно в технологическом процессе изготовления.
Литейное производство представляет собой процесс получения разнообразных литых деталей в качестве заготовок или готовых изделий. Эти детали называются отливками. В процессе литейного производства расплавленным металлом заполняется специальная литейная форма. Литейная форма представляет собой систему элементов, образующих рабочую полость, при заливке которой расплавленным металлом формируется отливка. Внутренняя полость литейной формы имеет конфигурацию будущей отливки. При охлаждении залитый металл затвердевает и сохраняет форму этой полости. В случае необходимости последующей механической обработкой отливкам придают точные размеры и форму. Во многих случаях литье — единственный способ изготовления нужных деталей. Особенно это существенно при изготовлении деталей больших размеров и массы, сложной конфигурации, а также в случае, когда сплав (например, чугун) малопластичен и не поддается обработке давлением (ковке, штамповке). В машиностроении около 50% всех деталей изготовляют литьем.
Отливки получают различными способами:
— литьем в песчаные формы (около 80% общего выпуска)
— специальными видами литья (остальная часть).
По количеству заливок литейные формы делятся на разовые и многократные (постоянные), разовые формы разрушаются при извлечении отливок.
Литейными свойствами называются технологические характеристики сплавов, которые непосредственно влияют на качество отливок. Наиболее важными литейными свойствами являются жидкотекучесть, усадка, трещиностойкость, газонасыщение.
Литье в песчаные формы. В песчаных формах изготавливают отливки из:
серых и белых чугунов;
бронзы;
латуни;
литейных алюминиевых, магниевых, цинковых сплавов;
литейных тугоплавких сплавов (на основе титана ниобия, ванадия, молибдена, вольфрама).
Основными операциями технологического процесса изготовления отливок в песчаных формах являются:
изготовление модели получение литейной формы (формовка);
плавка металла и заливка ее в формы;
выбивка застывших отливок из форм;
обрубка, очистка литья Для изготовления литейной формы необходимы модельный комплект, формовочная смесь.
В модельный комплект входит модели (рис. 2. б), подмодельные, подопочные и сушильные плиты, стержневые ящики (рис. 2. в), опоки, приспособления для контроля форм и стержней и др.
Рис. 2. Отливка (а), модель (б) и стержневой ящик (в) С помощью модели в песчанной форме получают внутреннюю полость, соответствующей конфигурации отливки. В стержневом ящике изготавливается стержень для образования внутренних полостей отливки. Модели и стержневые ящики делают неразъемными, разъемными, из двух и более частей и с отъемными частями, что облегчает выемку модели из формы и стержны из ящика. Опокиметаллические рамы, служащие для удержания формовочной смеси и образования литейной песчаной формы. Подопочные плиты предназначаются для установки на них опок, а также готовых форм под заливку. Сушильные плиты служат для сушки стержней и форм. Модельный комплект изготовляют по черчежам отливки. На рис. 2 показаны отливка (а), разъемная модел (б) и стержневой ящик (в). На модели имеются специальные выступы К, называемые стержневыми знаками, для создания в форме опорных выемок, необходимых для установки стержня.
Литниковая система. Совокупность каналов, по которым жидкий металл поступает в форму, называется литниковой системой. Она обеспеивает подвод металла в полость формы и заполнение ее с требуемой скоростью, задержание шлака и прочих неметаллических включений, выходов газов и паров из полости формы, непрерывное питание отливки при затвердевании.
По способу подвода расплавленного металла в полость литейной формы литниковые системы делятся на:
боковые, верхние, нижние (сифонные),
ярусные (многоэтажные).
Формовочные и стержневые смеси. Материалы, из которых изготавливают литейные формы, называют формовочными смесями. Они должны обладать прочностью, пластичностью, огнеупорностью, газопроницаемостью и податливостью.
Выбор состава формовочных и стерневых смесей зависит главным образом от вида сплава, из которого получают отливки.
5. Встряхивающая формовочная машина 703 М Производство ООО «Промтрактор-Промлит» состоит из подразделений, которые мы уже рассмотрели. Более подробно хочу остановиться на литейном цехе № 2 на примере встряхивающей формовочной машине 703 М (рисунок 3).
Машина 703 М имеет накатную прессовую траверсу, которая пневматическим толкателем перемещается по направляющим, закрепленным на верхней части двух специальной формы стоек, жестко связанных со станиной машины. Съем готовой полуформы производится четырьмя расположенными по углам встряхивающего стола штифтами, которые приводятся в движение двумя цилиндрами вытяжки. Стол встряхивания имеет встроенный вибратор. Для правильной работы машины сумма высот подмодельной плиты и опоки не должна выходить за пределы 300- 340 мм, при этом высота подмодельной плиты должна быть не менее 90 мм. В машине регулируются торможение траверсы в конце хода, ее переднее положение, скорость подъема вытяжных штифтов, число ударов и высота встряхивания.
Рис. 3. Формовочная встряхивающая машина модели 703М:
1 — встряхивающий и подпрессовочный механизм, 2 — стол, 3 — траверса, 4 — подпрессовочная плита, 5 — стойки Технические характеристики формовочной встряхивающей машины 703 М с допрессовкой без поворота полуформ указана в таблице 1.
Таблица 1
Технические характеристики формовочной встряхивающей машины 703 М с допрессовкой без поворота полуформ
Параметр | 703 М | |
Размеры опок в свету, мм: | ||
длина | ||
ширина | ||
Высота опоки, мм, не более | ||
Грузоподъемность **, т | 0,9 | |
Усилие прессования **, кН | ||
Производительность наибольшая цикловая, полуформ/ч | ; | |
Продолжительность цикла, с | ||
Ход вытяжки, мм | ||
Размеры встряхивающего стола, мм: | ||
длина | ||
ширина | ||
Размеры протяжной рамки в свету, мм: | ||
длина | ; | |
ширина | ; | |
Высота встряхивания, мм | ||
Частота встряхивания, 1/мин | ||
Масса падающих частей, кг | ||
Ход прессования поршня, мм | ; | |
Диаметры основных цилиндров, мм: | ||
прессового | ; | |
встряхивающего | ; | |
вытяжного | ; | |
поворотного | ; | |
Количество масла, заливаемого в резервуары вытяжных цилиндров, дм3 | ; | |
Габаритные размеры, мм: | ||
длина | ||
ширина | ||
высота | ||
Ширина при отведенной траверсе, мм | ; | |
Масса, кг | ||
Заключение
На сегодняшний день ООО «Промтрактор — Промлит» — крупнейший в России производитель литых заготовок для машиностроения (тракторного, железнодорожного, коммунального и др.), который специализируется на серийном и массовом производстве крупных отливок из углеродистых и низколегированных сталей, серого и высокопрочного чугуна габаритными размерами до 2000 мм и весом от 10 до 2000 кг.
В заключение хочу выделить основные особенности, достижения предприятия в области машиностроения.
Промлит полностью обеспечивает литыми заготовками Чебоксарский завод промышленных тракторов, производящий бульдозеры, тракторы, и трубоукладчики мощностью до 750 л.с., поставляет литье по кооперации Волгоградскому моторному заводу, Онежскому тракторному заводу и другим многочисленным потребителям в Российской Федерации и других странах СНГ.
Промлит имеет большой опыт производства и поставки крупных литых заготовок запорной арматуры для предприятий России и зарубежных стран.
С помощью введения в эксплуатацию новой автоматической линии вакуумно — пленочной формовки производства фирмы Генрих Вагнер — Синто (Германия), предприятие смогло увеличить объемы и значительно повысить качество выпускаемой продукции.
Одним из направлений производственной деятельности предприятия является получение заготовок методом электрошлакового литья и изделий из металлических порошков на основе железографитовых и бронзовых материалов. Заготовки из ЭШЛ успешно применяются при производстве крановых колёс, валков прокатных станов, заготовок прессового, механообрабатывающего и другого оборудования. Продукция, получаемая центробежным электрошлаковым литьем, закупается ведущими арматурными заводами России.
Выпускаемая продукция широко используется в автомобилестроении (втулка клапана, втулка статора, сухарь шаровой опоры); станкостроении; тракторостроении (втулки, шайбы опорных катков промышленных тракторов Т-170, втулки солнечной шестерни ДТ-75, распорные втулки звеньев гусениц); электротехнической промышленности (скользящие электроконтакты, статоры электродвигателей). Предприятие постоянно расширяет номенклатуру заказов и круг своих заказчиков.
Список литературы
литейный производство формовочный
1. Ансеров, Ю. М. Машины и оборудование машиностроительных предприятий. / В. А. Салтыков, В. Г. Семин. — Ленинград: Политехник, 1991. 365 с.
2. Артамонов, Б. А. Электрофизические и электрохимические методы обработки материалов / Ю. С. Водков — М.: Высшая школа, 1983.
3. Васильев, В.Н. Организационно-экономические основы производства: учебное пособие для машиностроительных спец. вузов. — М.: Высшая школа, 1988. — 277 с.
4. Колесов, И. М. Основы технологии машиностроения: учебник для машиностроительных вузов. — М.: Машиностроение, 1997. — 591 с.
5. Малеева, С.Б. / Экономические основы технологического развития: конспект лекций. — СПб.: Политехника. 2000. — 41 с.
6. Мельников, Г. Н. Проектирование механосборочных цехов / Под ред. А. М. Дальского — М.: Машиностроение, 1990. — 380 с.
7. Организация и оперативное управление машиностроительным производством: учебник / под ред. Н. С. Сачко. — Мн.: Новое знание, 2009. — 636 с.
8. Основы автоматизации машиностроительного производства: учебник для вузов. / Под. ред. Е. Р. Ковальчук, М. Г. Косов, В. Г. Косов. — М.: Высшая школа, 1991. — 312 с.
9. Проектирование машиностроительного производства: учебник для вузов / В. П. Вороненко, Ю. М. Соломенцев, А. Г. Схиртладзе; по ред. чл.-корр. РАН Ю. М. Соломенцева. — 2-е изд., стереотип. — М.: Дрофа, 2006. — 380 с.
10. Туровец, О. Г. Организация производством на предприятии. — М.: ИНФРА-М, 2007. — 207 с.
11. Управление организацией: учебник / под ред. А. Г. Поршнева, Н. Л. Румянцевой, Н. А. Саламотина. — 2-е изд, перераб. и доп. — М.: ИНФРА-М