Проект сталеплавильного цеха Оскольского электрометаллургического комбината
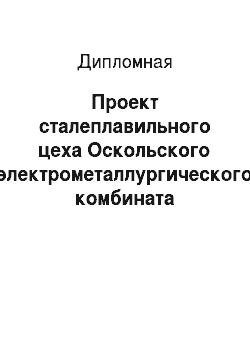
Шумом является беспорядочным сочетанием различных по силе и частоте звуков. Шум различной интенсивности и частоты оказывает на организм человека неблагоприятное воздействие и может вызвать различного рода болезненные состояния, в том числе тугоухость и глухоту. Источниками шума в цехе являются, главным образом, электропечи, а также мощные редукторы. Производственное оборудование, создающее шум… Читать ещё >
Проект сталеплавильного цеха Оскольского электрометаллургического комбината (реферат, курсовая, диплом, контрольная)
Содержание Введение
1. Характеристика ОАО «ОЭМК»
1.1 Характеристика основных цехов
1.1.1 Производство окисленных и металлизованных окатышей
1.1.2 Сталеплавильное производство
1.1.3 Прокатное производство
1.2 Грузопотоки между цехами
1.3 Технологическая схема производства литой заготовки
1.3.1 Производственная программа ЭСПЦ
1.3.2 Основное оборудование цеха
1.3.3 Технологический процесс получения литой заготовки
1.4 Определение производительности и числа основного оборудования электросталеплавильного цеха
1.4.1 Дуговые электропечи ДСП-150
1.4.2 Установки внепечной обработки стали
2. Дуговая сталеплавильная печь
2.1 Назначение и область применения ДСП-150
2.2 Описание узлов агрегата
3. Устройство, принцип работы и технические характеристики механизма наклона ДСП-150
3.1 Анализ конструктивных решений
3.2 Описание механизм наклона печи ДСП-150
3.3 Монтаж цилиндров наклона и фиксатора
3.4 Монтаж гидравлической установки
4. Технология ремонта
4.1 Система планово-предупредительных ремонтов
4.2 Описание типов ремонтов и их содержание для механизма наклона
4.3 Оценка и контроль качества ремонта
5. Выбор и расчет систем смазки узлов трения
5.1 Выбор типа смазки и способа смазывания
5.2 Выбор сорта смазки
5.3 Расчёт объёма пластичной смазки
5.4 Нормы расхода смазочных материалов
6. Безопасность жизнедеятельности и охрана окружающей среды
6.1 Правовые и нормативно-технические основы охраны труда и окружающей среды
6.2 Виды инструктажей
6.3 Анализ потенциально опасных и вредных факторов
6.4 Охрана окружающей среды Список использованных источников Введение Решающую роль в обеспечении высокого качества металлопродукции играют сталеплавильные цеха. Постоянное совершенствование оборудования сталеплавильных цехов, улучшение технических показателей и повышение надежности металлургических машин — непременное условие технического прогресса в сталеплавильном производстве.
Вместе с тем дальнейшее наращивание производства стали будет осуществляться путем развития кислородно-конверторного и электросталеплавильного производства.
Современное сталеплавильное производство характеризуется широким применением средств внепечной обработки стали. Создания оборудования для вакуумирования металла, продувки стали в ковшах инертными газами позволило вынести из сталеплавильных агрегатов и тем самым существенно повысить производительность агрегатов и качество выплавляемого металла.
1. Характеристика ОАО «ОЭМК»
Оскольский электрометаллургический комбинат (ОЭМК) расположен в 22 км от города Старый Оскол, вблизи крупных месторождений высококачественных железных руд, входящих в состав Курской магнитной аномалии.
В проектировании комбината, его строительстве, оснащении оборудованием и разработке технологии был применен передовой отечественный опыт и опыт зарубежных фирм таких как: «Мидрикс», «СМС. Шлеман-Зимаг», «Кизирлинг», «Сименс», и другие фирмы.
Первая промышленная продукция — окисленные железорудные окатыши — получена в цехе окомкования в ноябре 1982 года.
В настоящее время ОЭМК является наиболее современным высокоавтоматизированным и высокопроизводительным металлургическим предприятием в России и в Европе, на котором для выплавки стали используются металлизованное сырье — продукт прямого восстановления железа.
1.1 Характеристика основных цехов
1.1.1 Производство окисленных и металлизованных окатышей Цех окомкования производит окисленные окатыши из железорудного концентрата Лебединского горно-обогатительного комбината, транспортируемого на комбинат по пульпопроводу в виде пульпы на расстояние 26,5 км. Из пульпы на дисковых вакуумных фильтрах получают кек, из которого в свою очередь получают окатыши. Окисленные окатыши имеют размер 5−20 мм, содержание железа в окатышах не менее 67%, кремнезема не более 3,5% прочность не менее 250 кг/окатыш.
Цех металлизации производит металлизованные окатыши по технологии Мидрекс — нагретым восстановительным газом, полученным из природного газа после его конверсии в реформерах. Достоинством окатышей является:
— высокое содержание железа;
— широкий диапазон регулирования степени металлизации и содержания углерода;
— низкое содержание серы, фосфора и цветных металлов;
— низкая склонность к вторичному окислению;
1.1.2 Сталеплавильное производство Из цеха металлизации окатыши по транспортерам поступают в электросталеплавильный цех, где в электродуговых печах из них выплавляют сталь.
В состав ЭСПЦ входит следующее основное производственное оборудование:
— четыре 150-тонные электродуговые печи импортного производства, фирмы «Крупп»;
— три установки циркуляционные вакуумирования стали (УЦВС);
— две установки продувки аргоном;
— четыре четырех ручьевых МНЛЗ радиального типа;
— одна шести ручьевая МНЛЗ радиального типа;
— три АКОС — агрегаты комплексной обработки стали;
— четыре печи для замедленного охлаждения стали;
— две линии дробеструйной обработки, осмотра и зачистки поверхности абразивными кругами.
Производительность электросталеплавильного цеха (ЭСПЦ) составляет 3.365 058 млн. тонн непрерывнолитых заготовок в год.
1.1.3 Прокатное производство Из непрерывно-литых заготовок прокатывают сортовой прокат и трубную заготовку. Производство высококачественный прокат из конструкционных, подшипниковых, трубных, рессорно-пружинных и других марок сталей.
Оборудование, применяемая технология и системы управления прокаткой позволяют обеспечить более высокую точность геометрических размеров проката, чем предусмотрено международным и национальными стандартами технически развитых стран.
1.2 Грузопотоки между цехами Прием, подготовка и транспортировка железорудного концентрата с Лебединского ГОКа на ОЭМК поставляется по пульпопроводу. Затем пульпа подается насосами на участок фильтрации в центральный распределитель. Из распределителя пульпа самотеком поступает на дисковые вакуумфильтры, для обезвоживания. Для улучшения процесса фильтрования, концентрат подвергается нагреванию перегретым паром, разряжение создается вакуум-насосами. Съем кека с дисков вакуум фильтров осуществляется сжатым воздухом. Системой ленточных конвейеров концентрат и бентонит подаются в смесители «Ледеги» для получения однородной смеси.
Усредненная шихта транспортируется в отделение окомкования конвейерами. При помощи плужковых сбрасывателей распределяется в пяти расходных бункеров. Шихта из бункеров подается ленточными весовыми дозаторами и системой конвейеров в барабанные окомкователи, где формируются окатыши.
Разгружаемые из барабанных окомкователей окатыши сортируются на грохотах на фракции менее 9 мм, от 9 до 18 мм, более 18 мм. Окатыши крупностью от 9 до 18 мм собираются со всех окомкователей конвейером и транспортируются в отделение обжига.
Первоначально на обжиговые тележки конвейерной машиной загружается постель — обожженные окатыши крупностью от 10 до 12 мм, выделяемые в процессе грохочения обоженного продукта и транспортируемые в бункер постели объемом 150 м3 системой конвейеров.
Обожженный продукт разгружается в бункер — выравниватель, откуда подается виброжелобами на конвейеры, которыми транспортируется в отделения грохочения. На грохотах осуществляется сортировка окатышей по фракциям и конвейерами подаются в цех металлизации или на склад.
По системе транспорта сырья, окисленные окатыши подаются в промежуточный бункер шахтной печи, откуда самотеком через загрузочную трубу и двенадцать распределительных труб поступают в зону восстановления шахтной печи, где окатыши восстанавливаются горячим восстановительным газом.
Металлизованные окатыши распределяются в три бункера хранения продукта перед ЭСПЦ и в три бункера хранения перед отгрузкой внешним потребителям. Из бункеров ЦОиМ по конвейерам окатыши, а так же требуемые для плавки ферросплавы, плавиковый шпат, известь и т. д. подаются в дуговую печь (ДСП-150) через участок шихтоподачи ЭСПЦ. А стальной лом (копровый цех) и отходы собственного производства — через шихтовый двор в бадьях подаются на печи, то есть проводится подготовка дуговых печей к плавке. Емкость ДСП-150 тонн. После расплавки и добавки полученной стали производится выпуск металла в сталеразливочный ковш емкостью 160 тонн с температурой не выше 1630−1660С, слив шлака или удержание шлака.
Ковш подают на установку продувки аргоном (УПА) с целью усреднения и стабилизации химического состава и температуры в стали по всему объему ковша перед разливкой на УНРС.
Также сталь обрабатывается на установке порционного вакуумирования. Целью проведения обработки стали вакуумом является:
— сокращение длительности плавки и повышение производительности электропечей;
— рафинирование металла от газов и неметаллических включений;
— раскисление и доводка металла по химическому составу;
— стабилизация температурного режима и химического состава:
— повышение качества стали;
— улучшение технико-экономических показателей производства стали.
В настоящее время сталь-ковш подается на агрегат комплексной обработки стали (АКОС) обработка и доводка стали печь-ковш. И ковш подается на УНРС.
Стальковш устанавливается мостовым краном на подъемно-поворотный стенд (ППС) и поворотом передает сталь из разливочного пролета к УНРС, где через промежуточный ковш ведется разливка металла на МНЛЗ.
В кристаллизаторах МНЛЗ формируется литой слиток (300×360) и при помощи роликов и собственно веса подается к машинам газовой резки (МГР), где производится раскрой заготовок на мерные длины. По отводящим рольгангам и подъемно-транспортным шлепперам заготовки загружаются в печи замедленного охлаждения (ПЗО) температура поверхности заготовок перед посадкой в печи должна быть не менее 600С.
Печи замедленного действия предназначены для контролируемого охлаждения заготовок ресорно-пружинных и подшипниковых сталей. Охлажденные заготовки укладываются клещевыми кранами на приемный стеллаж шлеппера пакетами, укладывают заготовки только одной плавки.
Шлеппер подает заготовки к рольгангу линии отделки и укладывает их на него в положении «на ребро». По рольгангу заготовки поступают в дробеметную установку для очистки от окалины. Для очистки заготовок от окалины используют дробь сечением от 0.6 до 0.9 мм. Очистка поверхности от окалины должна быть равномерной по длине заготовки и ее четырем граням.
После очистки от окалины заготовки поступают по рольгангу на станцию визуального осмотра, где контролеры ОТК производят осмотр поверхности заготовки. Обнаруженные дефекты поверхности маркируют. Годную заготовку транспортируют по рольгангу к кантующему устройству, где укладывают на боковую поверхность и далее транспортируют на весы.
При необходимости, заготовки передают краном с кантующего рольганга на промежуточный склад. Заготовки разных плавок складывают таким образом, чтобы исключить их смешивание.
Заготовки, назначенные на шлифование, резку и скрап, транспортируют к кантующему устройству, с которого передают магнитной тележкой на стеллаж, приемный стол шлифовального станка или на рольганг линий резки.
После зачистки, заготовки передают при помощи магнитной тележки: годные на промежуточное складирование; требующие обрезки дефектных концов и забракованные на рольганг линии резки.
На промежуточном складе заготовки должны находится до тех пор, пока все заголовки этой плавки, назначенные на отделку, не пройдут ее и не будут приняты ОТК. Забракованные заготовки режут на установке газовой резки.
Передача заготовок сортопрокатному цеху осуществляется по рольгангам на склад литой заготовки (СЛЗ) СПЦ-1, предназначенный для складирования и накопления ее в монтажные партии, передачи металла на посад в печи нагрева СПЦ-1, а также для отгрузки товарной литой заготовки потребителям.
1.3 Технологическая схема производства литой заготовки
1.3.1 Производственная программа ЭСПЦ В электросталеплавильном цехе выплавляют большое число различных марок стали, с течением времени некоторые добавляются, а выпуск иных уменьшается или прекращается. В программе цеха можно выделить характерные группы сталей, занимающих в ней значительный объем. Марочный сортамент сталей:
— конструкционные углеродистые: 10…45;
— пониженной прокаливаемости: 54ПП, 55ПП, 60ПП;
— легированные: 15Х…45Х, 33ХС…40ХС, 15Г…50Г, 18ХГ, 15ХМ, 20ХМ, 18ХГТ…30ХГТ, 20ХН2М и др.;
— подшипниковые стали ШХ15, ШХ15СГ, ШХ4;
— стали нефтяного сортамента 30Г2, 32Г2, 32Г2С;
— инструментальные стали У7А… У10А, 9ХФ, 5ХНМ.
1.3.2 Основное оборудование цеха Кран для перевалки скрапа Количество — 3
Масса — 200 т Потребляемая мощность — 332 кВт Грузоподъемность — 50 т Угол опрокидывания мульд — 53 град Вылет стрелы — 25 м Скорости:
— перемещения крана — 2,08 м/с
— тележки — 1,05 м/с
— подъема — 0,2 м/с Дуговая сталеплавильная печь Вместимость — 150 т 5%
Мощность трансформатора — 105 МВА Диаметр печи — 7800 мм Диаметр электрода — 610 мм Подъем электрода — 4500 мм Высота подъема свода — 500 мм Угол наклона печи — 40 град Краны для завалки скрапа Количество — 4
Грузоподъемность — 125 т Пролет крана — 22,5 м Ширина крана — 12 м Скорости:
— подъема — 12,5…6,25 м/мин
— перемещение тележки — 20 м/мин
— перемещение крана — 63 м/мин Установка десульфурации и продувки аргоном Емкость — 7,5 м3
Длина продувочной фурмы — 4900 мм Предел взвешивания — 1300 кг Полезный объем — 1,5 м3
Скорость подачи — 6 м/с Мощность привода — 29 кВт Разливочный кран Масса — 400 т Грузоподъемность — 250/80/10 т Ширина крана — 8,6 м Скорости:
— подъема — 6 м/мин
— перемещения тележки — 40 м/мин
— перемещения крана — 100 м/мин Установка непрерывной разливки стали Количество — 4
Тип УНРС радиальный Радиус — 12 м Количество ручьев — 4
Ввод затравки снизу при помощи тянуще правильной клети Машина газовой резки заготовок Давление природного газа — 2,5 бар Давление кислорода — 12…16 бар Температура ручьев — 700…1000Со
Скорость резания — 340м/мин Отводящие рольганги Количество — 44 шт Мощность — 7 кВт Длина — 12 м Число роликов — 7
Длина бочки — 440 мм Диаметр ролика — 300 мм Скорость — 0,5 м/с Подводящий рольганг Количество — 4
Мощность — 13 кВт Длина — 22 м Длина бочки — 800 мм Диаметр ролика — 300 мм Печи для охлаждения заготовок Количество — 4
Температура:
На входе — 770С?
На выходе — 450С?
Количество зон — 6
Пропускная способность — 78 т/ч Длина печи — 45 м Ширина — 13 м Высота — 1,05 м Клещевой кран Количество — 3
Грузоподъемность — 30 т Ширина — 10,55 т Скорости:
Подъема — 12 м/мин Перемещения тележки — 63 м/мин Перемещения крана — 100 м/мин Закрывания клещей — 14,4 м/мин Магнитный кран Количество — 2
Грузоподъемность — 10/10 т Ширина — 8700 мм Вылет стрелы — 31 000 мм Скорости:
Подъема опускания — 15 м/мин Перемещения крана — 120 м/мин Перемещения тележки — 60 м/мин Пила холодной резки Количество — 1
Мощность — 25 кВт Диаметр пилы — 1120 мм Скорость резания — 7/10/14/18/24/35 м/мин Подача плавная — 0…40 мм/мин Скорость на скоростном ходу — 1000 мм/мин Скорость возврата — 1600мм/мин
1.3.3 Технологический процесс получения литой заготовки В электросталеплавильном цехе используются следующие основные материалы:
— металлизованные окатыши, поступающие в рабочие бункера конвейерным транспортом из расходных бункеров цеха металлизации;
— стальной скрап — оборотный легированный скрап электросталеплавильного и прокатных цехов комбината и привозной углеродистый скрап;
— ферросплавы — поступают железнодорожным транспортом в приемное отделение с бункерами, откуда конвейерами подаются в рабочие бункера цеха;
— известь (свежеобожженая) — поступает из известкового цеха в автосамосвалах в разгрузочные бункеры;
— порошки для десульфурации;
— науглероживатель;
— электроды;
— огнеупоры.
Выплавка стали предусматривается в электропечах емкостью 150 тонн с использованием в шихте металлизованных окатышей (65% от веса металлозавалки).
Металлизованные окатыши загружаются непрерывно со скоростью 18−35 кг/мин в ванну электропечи сверху, через отверстие в своде после расплавления порции скрапа. В окислительный период металл продувается кислородом, предусматривается также вдувание в металл порошка науглероживателя.
Выплавка подшипниковой стали предусматривается двушлаковым процессом (выпускается в ковш вместе со шлаком), остальных сталей — одношлаковым (без откачивания окисленного шлака). При одношлаковом процессе металл сливается в ковш с минимальным количеством печного шлака.
По окончании выпуска стали из печи в ковш, последний перемещают на сталевозе в распределительный пролет и, после измерения температуры и взятия проб, передают на внепечную обработку.
Сталь, выплавляемая одношлаковым процессом, подвергается вакуумированию на установке специального типа, внепечной десульфурации и, в случае необходимости, продувке аргоном сверху.
Стали, не обрабатываемые вакуумом, подвергаются доводке на специальных агрегатах (продувке аргоном и раскислению алюминием).
Вся выплавляемая в электропечах сталь разливается на четырехручьевых машинах непрерывного литья заготовок в заготовки сечением (300 360) мм и одна шестиручьевая машинах непрерывного литья заготовок радиального типа для заготовок (150 150) мм; (170 170) мм.
Разливка на МНЛЗ ввиду сложности марочного сортамента стали принята в основном одиночными плавками. Скорость разливки составляет 0,6 м/мин.
Возможна разливка методом «плавка на плавку» сериями.
Поступающая на ОНРС сталь в ковшах подается краном на подъемно—поворотный стенд, который передает ковш в положение разливки. После открытия шиберного затвора сталь поступает в промежуточный ковш, оттуда — в кристаллизатор. Дозирование стали постоянно контролируется.
В зоне вторичного охлаждения предусматривается система газовоздушного охлаждения непрерывнолитой заготовки, а также система электромагнитного перемешивания.
Далее в потоке УНРС установлено тянуще плавильное устройство, которое разгибает заготовку; машина газовой резки на мерные заготовки.
После маркировки заготовки проходят определенный, зависящий от марки стали режим обработки. Заготовки из углеродистой стали и низколегированной трубной стали охлаждаются на воздухе на стеллажах до температуры 2000С. Заготовки из остальных марок сталей охлаждаются с 7700С до 4600С со скоростью 350С/час в печах регламентированного охлаждения или под футерованными колпаками.
Загрузка заготовок в печь, а также выгрузка производится рольгангом.
После охлаждения мерных заготовок производят их зачистку от окалины, контроль и осмотр и, в случае необходимости, зачистку на шлифовальных станках и обрезку дефектов на пилах холодной резки. Затем заготовки собираются поплавочно для передачи на склад сортопрокатного цеха,.
Рисунок 1. Схема грузопотоков сталеплавильного участка
1.4 Определение производительности и числа основного оборудования электросталеплавильного цеха
Расчет потребности в оборудовании сталеплавильнолго цеха будем вести по [2], все данные взяты из.
1.4.1 Дуговые электропечи ДСП-150
Годовая производительность одной печи:
(1)
где Т — емкость печи (по массе жидкой стали), Т=150 т;
t — продолжительность плавки: при одношлаковом процессе: t=1,4;
а — выход годных слитков, а=97%;
n — число рабочих суток в году, n=349 суток;
24 — число рабочих часов в сутках.
Количество дуговых электропечей в цехе:
(2)
где — годовая производительность цеха, млн. т/год.
печей
1.4.2 Установки внепечной обработки стали Циркуляционное вакуумирование стали Производительность одной УЦВС рассчитываем по формуле:
(3)
где Р — масса стали в сталеразливочном ковше, Р=150т.;
— время цикла вакуумирования, t=40 мин;
— выход годного, а=0,95;
— число рабочих суток в году, n=354 суток;
тыс. т/год В общей сложности в цехе вакуумированию подвергают 50% всей стали:
тыс.т/год Фактическая загруженность одной установки не превышает 24%:
тыс.т/год Число УЦВС на участке:
(4)
Установка продувки аргоном Производительность одной УПА определяют по формуле:
(5)
где Р — масса жидкой стали в ковше, Р=150 т;
— время цикла обработки стали, =40 мин;
а — выход годного, а = 0,95;
n — число рабочих суток в году, n = 354сут;
тыс. т/год В общей сложности на участке продувке аргоном подвергают, 50% всей стали:
тыс. т/год Загруженность одной установки 44%, таким образом, фактическая пропускная способность одной УПА:
тыс. т/год Количество УПА на участке:
(6)
Агрегаты комплексной обработки стали.
Годовая производительность одного АКОС:
(7)
где Р — масса жидкой стали в ковше, Р=150 т;
— время цикла обработки стали, =60 мин;
а — выход годного, а = 0,95;
n — число рабочих суток в году, n=350 сут;
тыс. т/год На участке 82% всей стали направляется на АКОС:
тыс. т/год
(8)
Количество установок в цехе:
1.4.3 Машины непрерывного литья заготовок Годовая производительность МНЛЗ при разливке стали с паузами:
(9)
где Р — масса жидкой стали в ковше, Р=150 т;
а — выход годных заготовок при, непрерывной разливке стали, а=0,95;
n — число рабочих суток в году, n=285сут;
— пауза между разливкой двух последовательных плавок, =61 мин;
— машинное время разливки,
(10)
где N — число ручьев, N = 4;
— плотность стали, d = 7,8 т/м3 для спокойной стали;
F — площадь поперечного сечения отливаемой заготовки;
— скорость разливки, м/мин.
(11)
где — толщина отливаемой заготовки;
— ширина отливаемой заготовки.
— коэффициент, учитывающий марку отливаемой, стали им уровень совершенства конструктивных узлов УНРС, =0,21 — для углеродистых и легированных сталей, а также высоколегированных, инструментальных и шарикоподшипниковых.
Для МНЛЗ-4РУ
=0.3 м и =0.36 м;
м2
м/мин
мин
тыс. т/год Для МНЛЗ-6РУ
==0,17 м;
м2
м/мин
мин
тыс. т/год Количество МНЛЗ в цехе:
(12)
=3000 тыс. т/год П4РУ=2500 тыс. т/год;
П6РУ=500 тыс. т/год;
2. Дуговая сталеплавильная печь
2.1 Назначение и область применения ДСП-150
Электропечь ДСП-150 предназначена для выплавки в основном конструкционных (одношлаковым процессом), а также отдельных легированных (двухшлаковым процессом) марок сталей с использованием в качестве шихты стального лома и металлизованных окатышей в комплекте с агрегатом внепечной обработки и должна использоваться только в качестве плавильного агрегата. Электропечь предназначена для установки в технологической линии действующего электросталеплавильного цеха ОАО «Оскольский электрометаллургический комбинат» и должна обеспечивать выплавку около 800 тысяч тонн стали в год с высокими экономическими показателями. Электропечь предназначена для выплавки сталей широкого сортамента.
2.2 Описание узлов агрегата Механическое оборудование ДСП включает корпус, свод, опорную конструкцию, механизм наклона, электрододержатель, механизм передвижения электродов, вспомогательные механизмы и устройства, систему удаления и очистки газов.
Корпус, футерованный изнутри, формирует рабочее пространство ДСП.
Рабочее окно необходимо для обслуживания ДСП во время плавки.
Свод, закрывающий рабочее пространство ДСП, устанавливают на корпус. Свод имеет несколько отверстий разного диаметра для ввода графитированных электродов, топливных горелок, кислородных фурм и других технологических устройств, а также для организованного отвода печных газов (газоотсос). Поэтому на своде располагают необходимые уплотнители. Свод ДСП высокой и сверхвысокой мощности предназначен для крепления водоохлаждаемых панелей.
ДСП наклоняют для скачивания шлака в сторону рабочего окна на угол 10 и для слива металла в противоположную сторону на угол 40.
Корпус 1 устанавливают на опорную конструкцию 2 с подвижными опорами в виде двух круговых сегментов 3, перекатывающихся по горизонтальным фундаментным балкам 4 под действием механизма наклона 5.
Рисунок 2. Дуговая сталеплавильная печь
1 — электрододержатель; 2 — электрод; 3 — газоотборный патрубок; 4 — кронштейн; 5 — сводовое кольцо; 6 — корпус; 7 — опорная тумба; 8 — опорная конструкция; 9 — гидроцилиндр механизма наклона; 10 — статор электромагнитного перемешивания; 11 — гидроцилиндр механизма подъема свода; 12 — гидроцилиндр механизма поворота свода; 13 — гидроцилиндр механизма передвижения электродов; 14 — опорно-поворотный вал; 15 — Г-образная стойка; 16 — гибкие кабели; 17 — трубошины; 18 — сливной желоб; 19 — фундаментная балка; 20 — опорный сегмент; 21 — рабочее окно; 22 — песчаный затвор; 23 — уплотнитель электродного отверстия в своде Механизм наклона является весьма ответственной частью ДСП и должен обеспечить надежность работы и долговечность механизма; легкий, плавный и регулируемый наклон корпуса на соответствующий угол и с соответствующей скоростью. Механизм наклона должен быть защищен от попадания на него жидкого металла в случае проедания подины и от попадания шлака при скачивании последнего.
Давление рабочей жидкости в гидроприводе порядка 18 МПа создают специальной насосной станцией, входящей в комплект оборудования ДСП.
Рисунок 3. Схема механизма наклона ДСП: 1 — корпус; 2 — опорная конструкция; 3 — круговые сегменты; 4 — балка; 5 — механизм наклона Надежность работы ДСП-150 зависит от прочности и жесткости люльки — конструкции (как рамы, так и опорных секторов), на которой установлена печь. Люлька служит не только для установки корпуса печи, но и для удержания корпуса при наклоне на слив металла и скачивание шлака. Печь ДСП-150 с секторным механизмом наклона опирается на два сектора. На нижнем горизонтальном листе (подошве) каждого сектора установлены шипы, которые при перекатывании опорного сектора по фундаментной балке при наклоне печи входят в отверстия в горизонтальном листе фундаментной балки. Шипы предназначены для предотвращения перекоса печи относительно продольной вертикальной плоскости при наклоне печи.
Следовательно, они являются ответственными элементами конструкции опорного сектора. Во время эксплуатации ДСП-150 в период между двумя капитальными ремонтами печи происходит смятие и износ шипов в среднем количестве 10 штук из 36, по причине забития окалиной отверстий в фундаментных балках. Восстановление шипов, контроль износа шипов и отверстий фундаментных балок, а так же очистка нижней конструкции люльки и отверстий в фундаментных балках от окалины проводится во время капитального ремонта.
Электрододержатель служит для крепления графитированного электрода и для подвода к нему электрического тока.
Электрододержатель работает в тяжелых условиях: воздействие горячих печных газов, повышенная температура и запыленность окружающей среды, тепловой поток от нагретого электрода, интенсивное тепловыделение по закону Джоуля — Ленца при протекании через электрододержатель тока силой 50—100 кА и более.
Поэтому конструкция электрододержателя должна быть надежной, долговечной, механически прочной и жесткой, обеспечивать хороший контакт с поверхностью электрода, создавать необходимую силу трения для уравновешивания веса электрода и удержания его без проскальзывания в процессе плавки, иметь минимальные электрические потери.
Для загрузки металлошихты сверху при помощи загрузочной бадьи (корзины) необходимо открыть рабочее пространство ДСП. Из всех возможных способов (выкат корпуса, откат или наклон свода) на ДСП-150 свод поворачивают соответствующим механизмом в сторону трансформаторного помещения (печная подстанция) к разливочному пролету на 76. На таких ДСП — наименьшая масса металлоконструкций, нет сотрясений свода и электродов при открывании печи, свободна часть корпуса, противоположная стойкам, и рабочая площадка перед печью, что удобно для ее обслуживания.
Рисунок 4. Схема механизма подъема-поворота свода: 1 — свод; 2 — подвеска; 3 — кронштейн; 4 — опорно-поворотный вал; 5 — гидроцилиндры поворота; 6 — гидроцилиндр подъема; 7 — фиксатор
3. Устройство, принцип работы и технические характеристики механизма наклона ДСП-150
3.1 Анализ конструктивных решений Во всем мире при строительстве металлургических мини-заводов, как правило, предпочтение отдают дуговым электропечам трехфазного переменного тока с высоким полным электрическим сопротивлением контура, которые работают с вторичным напряжением 1000 В и более (ДСП) и дуговым печам постоянного тока (ДППТ) с одним катодом. В мире насчитывают около 1200 дуговых электропечей, из них около 15% составляют ДППТ. Как показывает опыт промышленной эксплуатации, печи переменного и постоянного тока создаются в соответствии с единым принципом проектирования и управления, поэтому технология переплава металлошихты в этих печах и технико-экономические показатели плавки не имеют принципиальных отличий в силу одинакового принципа теплогенерации и перераспределения тепла в рабочем пространстве.
В настоящее время на металлургических предприятиях в основном устанавливают электропечи ДСП вместимостью 12, 25, 50, 100, 150 и 200 т., в которых нашли отражение новейшие достижения электротермии и электрического машиностроения. Практически все дуговые сталеплавильные печи для удобства обслуживания выполняются наклоняющимися на угол 40°-45 в сторону желоба для выпуска жидкого металла и на 10°-15 в сторону рабочего окна для удаления шлака. По типу конструкции опорного узла механизмы наклона делятся на секторные, роликовые и цапфовые (см рис. 5), по месту нахождения привода — с боковым или нижним расположением, а по типу привода — на электрические и гидравлические. Наиболее широкое распространение в промышленности получили печи с секторным механизмом наклона. Основное их преимущество — перемещение сливного носка при выпуске металла из печи в сторону разливочного пролета. Механизмы наклона печей с боковым расположением привода более удобны в эксплуатации, но одностороннее приложение нагрузки к корпусу не позволяет использовать их на печах средней и большой производительности.
На последних устанавливают механизмы наклона с нижним расположением привода, что обеспечивает хорошую устойчивость корпуса. Привод монтируют на фундаменте под печью со стороны рабочего окна, поэтому в процессе эксплуатации он может быть залит металлом или шлаком.
а) б) в) Рисунок 5. Схемы механизмов наклона печей: а — секторный; б — роликовый; в — цапфовый (1 — привод наклона); 2 — корпус печи; 3 — люлька; 4 — опорная плита; 5 — роликовая обойма; 6 — опора цапфы) Электропечи средней серии ДСП-12, ДСП-25 и ДСП-50 выполняют с гидравлическими приводами основных механизмов, электропечи крупной серии ДСП-100, ДСП-150 и ДСП-200 изготавливают с электроприводами или с гидроприводами всех механизмов.
Гидравлические приводы механизмов имеют преимущества по сравнению с электромеханическими: более компактны, благодаря чему металлоемкость печей ниже на 15−20%, а площадь занимаемая печами, примерно меньше на 15%. Однако применение гидроприводов для механизмов электропечей ограничено ввиду трудности изготовления гидроцилиндров большой длины.
Независимо от конструкции к механизму наклона предъявляются высокие требования долговечности и надежности работы, обеспечения легкого и плавного наклона печи на требуемый угол с необходимой скоростью и исключения опрокидывания печи при наклоне.
Для повышения производительности крупных электросталеплавильных печей возникает актуальный вопрос по снижению продолжительности периодов плавки за счет внедрения результатов научно-исследовательских и опытно-конструкторских работ, совершенствования энергетического и электрического режима ДСП, более полной механизации и автоматизации трудоемких операций, повышения уровня организации ведения плавки и уменьшения различного рода задержек.
Дуговая сталеплавильная печь (ДСП-150) представляет собой сложный агрегат, оснащенный большим количеством узлов и механизмов, основным из которых является механизм наклона печи, выполняющий важную роль для обеспечения технологического процесса ДСП-150 выплавки стали. Механизм наклона должен обеспечивать плавный наклон корпуса печи на слив стали и скачивания шлака. Составными частями механизма наклона являются опорная конструкция печи (люлька) и гидропривод. По принципу работы дуговая сталеплавильная печь (ДСП-150) относится к трехфазным дуговым электропечам с зависимой дугой.
Механизм наклона ДСП-150 нижнего типа, цилиндры наклона печи крепятся вверху шарнирными опорами в кронштейнах подшипников, жёстко расположенных на секторах люльки. Внизу — шарнирными опорами в кронштейнах подшипников, жестко закрепленных в фундаменте печи.
Важнейшим требованием к механизму наклона является невозможность самопроизвольного опрокидывания печи при наклоне. Ось люльки смещена, относительно оси печи в сторону слива стали на 500 мм. Для предотвращения возможного опрокидывания самопроизвольного печи в сторону выпуска стали, печь опирается на стойку с гидравлическим приводом. Основные преимущества этого привода — малые габариты, плавность работы, но требует высококвалифицированного обслуживания.
В настоящее время гидравлическая установка обеспечивает следующие продолжительность операций:
— максимальный угол наклона печи:
для слива металла — 40°
для скачивания шлака — 10°
— время наклона печи от 0° до 40°-50 сек.
— время возврата печи в исходное положение после слива стали — 20 сек.
— рабочее давление в системе — 18 МПа
3.2 Описание механизм наклона печи ДСП-150
Механизм наклона печи служит для наклона корпуса печи на — выпуск стали и слив шлака. Он состоит из следующих частей:
— два масляных гидравлических цилиндра наклона двойного действия с хромированными штоками, с шарнирными подшипниками;
— стопорный механизм со стопорным пуансоном, масляно-гидравлическим цилиндром двойного действия, твердохромированным штоком с шарнирным подшипником, концевым выключателем и управляющей планкой;
— копировальный механизм, включающий передачу, приводную цепь, противовес для контроля положения люльки печи и датчик угла поворота.
Контроль положения печи относительно вертикали осуществляют концевые выключатели. Сигналы с них выведены на мнемосхему печи.
Рисунок 6. Схема механизма наклона печи: 1 — люлька; 2 — цилиндр наклона; 3 — цилиндр стопорный Цилиндры наклона крепятся вверху шарнирными опорами в кронштейнах подшипников, расположенных на сегментах люльки. Внизу — шарнирными опорами в кронштейнах подшипников, жестко закрепленных в фундаменте печи. Цилиндры двойного действия, уплотнение полостей цилиндров осуществляется шевронными манжетами. Для предохранения от загрязнения на выходе штока расположены грязесъёмники.
Если при наклонённой печи произойдет разрыв подающего шланга или трубопровода, то размыкаемые обратные клапаны, предотвращают возврат печи в «нулевое» положение. Стопорный механизм служит для фиксации печи в «нулевом» положении и снятия нагрузки на узлы механизма наклона.
Стопор расположен справа на стороне рабочего окна. Установлен на специальный фундамент на анкерных болтах. Стойка стопорного механизма имеет на верхнем конце поперечину, регулируемую по высоте, соединённую посредством основной рамы с цилиндром.
В нулевом положении печи стопор препятствует наклону печи в сторону скачивания шлака. Для наклона печи в сторону скачивания шлака, гидроцилиндр наклоняет стопорную стойку в горизонтальное положение.
При поднятом своде и неотведенном поворотном жёлобе механизм наклона печи блокируется.
3.3 Определение опрокидывающего момента Рисунок 7. Расчетная схема механизма наклона ДСП для определения опрокидывающих моментов:
а — расчетная схема от силы тяжести корпуса; б — расчетная схема от силы тяжести жидкого металла (1 — корпус; 2 — опорный сегмент; 3 — фундаментная балка; 4 — гидроцилиндр механизма наклона) Усилие гидроцилиндра будем рассчитывать в соответствии с рекомендациями. Расчет усилия гидроцилиндра связан с определением опрокидывающих моментов от силы тяжести ДСП, силы тяжести жидкого металла, силы трения в опорно-ходовой части ДСП. [1]
(13)
где — прокидывающий момент от силы тяжести ДСП;
— прокидывающий момент от силы тяжести жидкого металла
— прокидывающий момент от силы трения в опорно-ходовой части ДСП.
В связи с тем, что момент опрокидывания печи будет максимальным при наклоне ее на угол =40−45, когда весь металл будет слит в ковш, момент от силы веса жидкого металла приравниваем к нулю =0.
Опрокидывающий момент М от сил тяжести элементов механизма наклона и от сил трения в механизме определяют при известной конструкции ДСП.
Основой правильного расчета опрокидывающего момента является точное определение общих координат центра тяжести печи.
Массу наклоняемых элементов ДСП принимаем по таблице 1.
Таблица 1
Масса наклоняемых элементов печи
Наименование | Масса | |
Люлька | 52 000 кг | |
Подина | 120 000 кг | |
Корпус | 31 600 кг | |
Свод | 44 800 кг | |
Консоли электрододержателей | 3 9000=27 000 кг | |
П/портал | 78 700 кг | |
Электроды | 3 6000=18 000 кг | |
Согласно данным таблицы 1 общая масса наклоняемых элементов ДСП составляет:
372 100 кг Сила тяжести порожней ДСП будет равна:
G = g (14)
где — общая масса наклоняемых элементов ДСП
g = 9,81 м/с — ускорение свободного падения
G = 372 100 9,81 =3 650 301 Н Для определения координат центра тяжести печи вычертим печь в масштабе. Введем систему координат XOY. Найденные координаты центров тяжести отдельных элементов печи отложим на чертеже и занесем в таблицу 2.
Таблица 2
Координаты центров тяжести элементов печи
НАИМЕНОВАНИЕ ЭЛЕМЕНТА | Координаты Y Ц.Т. (мм.ч) | |
Люлька | ||
Подина | ||
Корпус | ||
Портал с механизмом подъема электродов | ||
Свод | ||
Координату центра тяжести печи определим по формуле:
(15)
где — масса iтого элемента печи;
— координата центра тяжести iтого элемента;
Х= 0
Y = 74 мм.ч.
Связываем координаты центра тяжести с осью вращения печи через радиус-вектор :
(16)
где=500 мм, e=1050 мм — координаты центра тяжести печи относительно центра вращения:
мм Угол наклона радиуса-вектора к оси печи —, равен:
(17)
25,45
Плечо — силы тяжести порожней ДСП G = g (с учетом данных таблицы 2) относительно оси вращения при наклоне ДСП на угол зависит от угла между радиусом-вектором и вертикалью:
(18)
где плюс или минус характеризуют направление наклона ДСП.
мм С учетом формулы опрокидывающий момент от силы тяжести порожней ДСП составляет:
= Gа = g ()(19)
= 36 503 011,095 = 3 997 079,5 Нм.
от силы трения в опорно-ходовой части ДСП, вследствии упругости сжатия опорных сегментов определяем по формуле:
(20)
где l = 0,25р — плечо деформации;
р = 2,16 — ширина площади сопротивления опорного сегмента с фундаментной балкой как опорной плоскостью;
k = - нагрузка, приходящаяся на единицу длины образующей сегментов;
В=800 мм — суммарная длина образующих двух опорных сегментов ДСП;
D = = 10 м — диаметр опорного кругового сегмента;
E — модуль упругости (модуль Юнга) материала опорно-ходовой части ДСП (сталь E=0,2 МПа).
l= = 11,53 мм М = 36 503 010,01153 = 42 088 Н м Суммарный опрокидывающий момент М равен:
М = = 3 650 301 + 42 088 = 3 692 389 Н м Для определения усилия F, действующего на шток гидроцилиндра привода наклона ДСП, необходимо найти плечо S действия этой силы. Для этого нужно знать уравнение траектории движения шарнира N () в результате вращательного и поступательного движения опорного сегмента по фундаментной балке при наклоне ДСП на угол .
Координаты подвижного шарнира N штока гидроцилиндра при наклоне ДСП на угол = 45:
X = [()-sin ([()] (21)
Y = (1-cos ()] (22)
где = 32 — угол наклона линии NO к оси печи
X = 5000 [0,17 453 (32 +45)-sin (32+45)]1869 мм
Y = 5000[1-cos (32 +45)]3875 мм Плечо S находим по формуле:
S = [1 — cos () + А sin ()]/ А +1 (23)
где, А — коэффициент из уравнения продольной оси штока Ш, для которой плечо S является перпендикуляром :
А = ()/() (24)
где = -5000 мм, = 0 — координаты неподвижного шарнира гидроцилиндра, А = (-5000 — 3875)/(0 — 1869) = 4,75
S = 5000[1 — cos (32 +45)+4,75 sin (32 +45)]/ 5567 мм Искомое усилие, действующее на шток гидроцилиндра находим по формуле:
(25)
= 661 047,4 Н663 кН Также для расчета гидравлического привода необходимо определить силу сопротивления F перемещению штока в уплотнениях гидроцилиндра.
= 0,1=0,1 663 263 = 66 326 Н Полное усилие гидроцилиндра:
F = +=66 326+663263 = 729 589 Н
3.4 Расчет гидроцилиндра Расчет гидроцилиндра будем вести в соответствии с рекомендациями [3],[4].
Перед началом расчета определим исходные величины:
Усилие гидроцилиндра: F = 730 кН, Ход гидроцилиндра: Н = 3450 мм, Время наклона корпуса печи от 0 — 45: t = 50 сек, Рабочее давление в маслянно-гидравлической системе: Р=180 атм.
Определим скорость движения штока:
(26)
м/с Показатель вида нагрузки :
(27)
Определяем по графику зависимости от показателя нагрузки относительную предельную скорость ([4]. стр. 90).
= 0,5 м/с Определяем скорость установившегося движения :
(28)
м/с Определяем ускорение при разгоне:
(29)
Так как в знаменателе получается ноль, значит в движении штока нет этапов разгона и торможения.
Полная внешняя нагрузку на выходном звене F будет равна силе F=730 кН.
Мощность на выходном звене:
(30)
Вт
Рассчитываем удельный рабочий объем :
(31)
где F — движущая сила объемного гидропривода, F = 730 000 Н;
— гидравлический КПД 0,75—0,9; принимаем =0,75;
— КПД гидродвигателя, для гидроцилиндров 0,85.
Посчитаем расчетный диаметр поршня:
(32)
м Принимаем диаметр поршня = 300 мм Уточняем удельный объём:
(33)
Диаметр штока гидроцилиндра выбираем конструктивно исходя из рекомендаций [5]:
(34)
С учетом больших нагрузок принимаем:
тогда:
мм Принимаем =250 мм.
Определяем толщину стенки гидроцилиндра :
Минимальная толщина стенки гидроцилиндра составляет:
(35)
(36)
где =110 МПа — допускаемое напряжение растяжения для стали 45.
условие выполняется Принимаем согласно ГОСТ толщину стенки 30 мм.
3.5 Расчет штока на устойчивость Произведем проверочный расчет штока гидроцилиндра на устойчивость используя формулу Эйлера:
(37)
где — предельная нагрузка,
— коэффициент, учитывающий закрепление гидроцилиндра, так как гидроцилиндр закреплен шарнирно с обоих сторон, то принимаем равным 2;
E — модуль упругости (модуль Юнга для стали E = МПа);
L — длина сжатого участка, в данном случае полный ход гидроцилиндра L = Н = 3450 мм;
— момент инерции сечения штока.
(38)
условие прочности выполняется.
3.6 Расчет гильзы гидроцилиндра на прочность Расчет напряжений ведется в зависимости от типа напряженного состояния в стенке гидроцилиндра, которое зависит от способа закрепления. Напряженное состояние может быть плоским и объемным.
Рисунок 8 — Схема крепления гидроцилиндра с опорой на дно
(39)
где и — соответственно наружный и внутренний радиусы цилиндра, м, м;
Р — давление, Р =180 атм=18 МПа
МПа
(40)
МПа
3.7 Расчёт осей на прочность Перед началом расчета осей гидроцилиндра выберем материал, из которого они будут изготовляться. Для изготовления осей выберем сталь марки 30Х3МФ, которая обладает высокой износостойкостью при высоких давлениях, теплоустойчива — работает при температуре до +450. Эти эксплуатационные характеристики являются большим достоинством этой стали, в условиях в которых работает механизм наклона печи, в частности оси крепления гидроцилиндра.
Рисунок 9. Расчетная схема оси Данные для расчета:
F = 730 кН ,
a= b = 0,32 м
l = 0, 64 м
= 950 МПа — предел текучести стали 30Х3МФ .
Максимальный момент при данном виде нагружения равен:
(41)
Нм Запишем условие прочности:
(42)
где — допускаемое напряжение;
— момент сопротивления сечения.
(43)
где — коэфициент запаса прочности, с учетом того что для изготовления осей используем высококачественную сталь, принимаем коэффициент запаса прочности = 2.
МПа Момент сопротивления для круглого сечения:
(44)
Преобразуем неравенство (29) и подставив (31) в (29) получим:
тогда Выполнив арифметические преобразования получаем:
Рассчитаем диаметр осей:
м Так как пальцы не нагружены в осевом направлении, то расчет на устойчивость проводиться не будет.
технологический сталеплавильный металлизованный литой
3. Технология монтажа
3.1 Общие требования Перед началом монтажа осуществляются следующие подготовительные работы:
— все необходимые для этого монтажа фундаменты подметаются до чистоты метлой, все крепёжные отверстия освобождаются от мусора;
— монтаж печной площадки 7.8 м должен быть завершён;
— имеются в распоряжении монтажный кран для элементов печи и подъёмные механизмы для помещения гидравлической системы;
— для осуществления монтажа печи должны быть предусмотрены смещённые друг относительно друга на 90° оси отсчёта и апогей. С этой целью в трёх точках фундамента заливаются по стальной пластинке так, чтобы они не могли смещаться, замеряются, помечаются и снабжаются постоянными координатами. На одной из этих трёх табличек дополнительно приваривается апогей, который также замеряется и маркируется. Полученные таким образом оси служат исходными размерами при осуществлении всего комплектного монтажа. Они используются в течение многих лет (при крупных ремонтах). Точно в центре печи на высоте около + 8.5 м устанавливаются шнуровые каркасы (2 оси). Шнуровой каркас необходим для определения координат нижней конструкции люльки, цилиндров наклона (предварительный монтаж) и опорного кольца механизма наклона и поворота свода печи;
— контролируется соблюдение заданных размеров соответствующего участка фундамента и помещения гидравлики, допуск при соблюдении отметок -5 мм. Оси фундаментов для деталей оборудования соблюдать с допуском — 1 мм.
Необходимо также соблюдать следующие общие указания:
— каждая часть перед монтажом проверяется после её распаковки на наличие транспортных повреждений;
— соблюдаются указанные допуски при монтаже;
— голые части машин, покрытые для защиты во время транспортировки защитным антикоррозионным слоем, очищаются от этого слоя непосредственно перед монтажом (без повреждения поверхности);
— в качестве растворителя для защиты от коррозии обработанных поверхностей можно применять бензин или нитрожидкость;
— поверхности, которые во время эксплуатации смазываются, необходимо уже при монтаже снабдить каким-то минимальным количеством смазочного вещества;
— монтаж осуществляется только инструментами или вспомогательными средствами, которые не могут повести за собой повреждение монтируемых частей;
— заливка машин не должна быть менее 50 мм;
— обрабатываемые поверхности для монтажных сварных швов обрабатываются антикоррозийным защитным средством тектил. Для получения прочных сварных швов нужно перед сваркой тщательно удалить этот антикоррозийный слой. В противном случае получаются пористые сварные швы. Пористые сварные швы не являются прочными.
3.2 Монтаж люльки Нижняя конструкция состоит из 2 балок. Эти балки помечаются валиками (I или II или III или IV). Для каждой отдельной печи можно брать только балки, отмеченные одинаковыми номерами. После монтажа люльки и балок осуществляют попытку скатывания люльки с балок. При этом определяются контрольные размеры и набиваются на балках. Балки укладываются на соответствующий фундамент вместе с вдетыми крепёжными болтами. Футеровочные листы укладываются вблизи крепёжных болтов. Приблизительное расположение осуществляется на основании набитых контрольных размеров. Крепёжные болты заливаются до верхнего края фундамента. После затвердевания заливочной массы осуществляют точную юстировку и затяжку всех крепёжных болтов. При точной юстировке соблюдаются все набитые контрольные размеры с допуском 1 мм. Расстояние от центра печи до оси балки с монтажной стороны (3950 мм) и расстояние от центра печи до оси люльки (500 мм) устанавливаются с допуском на каждое расстояние 1 мм. Высотные отметки верхнего края балки допускаются 1 мм.
Рама люльки поставляется разобранной на четыре части: элемент люльки, монтажная сторона (сверхгабаритная часть), 2 поперечные балки и элемент люльки, внешняя сторона. Эти элементы подвергались пробному монтажу в мастерской. Элементы люльки и поперечные балки помечаются наплавленными валиками (I или II или III или IV). Каждая печь получает элементы с одинаковыми номерами. Люлька может монтироваться только на балках с одинаковым номером. Обе поперечные балки соединяются с элементом люльки, монтажная сторона, с помощью винтовых соединений на сварных стыках.
Такой предварительный монтаж осуществляется за пределами печного фундамента. Перед тем, как насадить эти предварительно смонтированные элементы люльки на балки, нужно между фундаментом монтажной стороны люльки и фундаментом её внешней стороны установить вспомогательную подпорку с двумя гидравлическими прессами с целью опоры обеих поперечных балок. Перед насадкой элементов люльки нужно также осуществить предварительный монтаж цилиндров наклона. После такой подготовки можно установить предварительно смонтированную люльку на балки и вспомогательную подпорку. Затем можно установить элемент люльки, внешняя сторона. Оба элемента затем подгоняться друг к другу и соединяются винтовыми соединениями на сварных стыках.
Попыткой скатывания люльки на балках с помощью крана получают пятно контакта на нижней конструкции люльки и контролируют соосность рядов болтов продольных стенок люльки с рядами отверстий в балках. Люльку можно тщательно сварить и за пределами фундамента и затем насаживать ее на центрированные балки. Оси болтов отверстий на стороне, прилежащей к электропомещению, должны совпадать друг с другом с допуском 2 мм.
Пятно контакта сегментов люльки на балках должно составлять минимум 70% поверхности. Перед скатыванием люльки на нижней, конструкции люльки опорную поверхность можно натирать мелом. Таким образом, после попытки скатывания видно будет полученное пятно контакта на опорной поверхности. Сегменты люльки теперь предохраняются от опрокидывания и можно приступить к сварочным работам. По окончании сварочных работ снова повторяют скатывание люльки. По получении положительного результата скатывания заливаются балки люльки и еще раз затягиваются крепежные болты. Затем люлька возвращается в нулевое положение и производится временное соединение люльки с балками. Точками измерения служат обработанные поверхности для установки кривошипов. Затем к люльке приваривают наклоняемую совместно печную площадку.
Печная площадка поставляется разобранной на пять элементов и поручни. Необходимо получить заданное расстояние между неподвижной частью печной площадки и её частью, наклоняемой совместно с люлькой. При этом наклоняемая часть может быть укорочена по необходимости на величину до 20 мм. Допустимая нагрузка на печную площадку составляет 150 кг/м. На консолях рамы люльки устанавливаются эксцентриковые опоры. Эта установка осуществляется таким образом, чтобы цапфы находились в нулевой позиции. Теплозащитные листы могут монтироваться только после того, как на люльке монтируются все трубопроводы и мелкие элементы. Монтаж лестницы к несущей конструкции свода может осуществляться независимо от монтажа люльки. Отдельные части лестницы привинчиваются друг к другу. Поручни привариваются. После монтажа несущей конструкции свода лестницу подгоняют к нему. Затем можно сваривать плиты основания лестницы с крепёжными плитами на неподвижной части печной площадки.
3.3 Монтаж цилиндров наклона и фиксатора Цилиндры наклона и фиксатор монтируются предварительно перед насадкой люльки. Оба цилиндра наклона и цилиндр фиксатора поставляются заполненными маслом. Необходимо слить антикоррозийную защитную жидкость, а отверстия закрыть до прокладки гидравлических трубопроводов, чтобы не попадала пыль. При предварительном монтаже цилиндров наклона с цилиндром монтируются верхние и нижние подшипниковые стойки. Для крепления нижних стоек в фундаменте в отверстия к залитым крепёжным слиткам вставляются болты с прямоугольными головками. Направление прямоугольной головки контролируется прорезью на конце резьбы болта. Цилиндры наклона насаживаются вместе с установленными подшипниковыми стойками. Футеровочные листы располагаются вблизи болтов. Затем подгоняют и насаживают гайки и шайбы. Точная юстировка цилиндров наклона осуществляется только после сборки и монтажа люльки.
При предварительном монтаже фиксатора подшипниковая стойка с плунжером и цилиндр фиксатора вместе с вдетыми крепёжными болтами укладываются на соответствующий фундамент. Футеровочные листы располагаются вблизи крепёжных болтов. После выравнивания крепёжные болты заливаются до верхнего края фундамента бетоном. После затвердевания бетона заливки можно затянуть эти болты. Точная юстировка фиксатора осуществляется только после сборки и монтажа люльки.
При точной юстировке фиксатора полностью выводятся гидроцилиндры. При этом стойка должен находиться в вертикальной позиции относительно фиксатора. Головка стойки, регулируемая по высоте, должна находиться на средней высоте. При этом верхняя кромка головки должна иметь высотную отметку + 5.5 м с допуском 5 мм. Теперь можно установить головку по высоте таким образом, чтобы люлька в своей нулевой позиции точно прилегала к головке плунжера. Подшипниковая стойка к фиксатору заливается заливочной массой, которая не подвергается усадке. Гайки крепёжных болтов дозатягиваются.
При точной юстировке цилиндров наклона они приводятся в вертикальное положение при нулевом положении люльки. Цилиндры выводятся до такого положения, чтобы уже при предварительном монтаже установленные на цилиндрах подшипниковые стойки полностью налагались на люльке. Опорные плиты подшипниковых стоек привариваются к люльке. Если выдвинутый цилиндр имеет ход, отличающийся от 435 мм, то нижняя подшипниковая стойка цилиндра наклона корректируется по высоте с помощью подкладывания футеровочных листов до тех пор, пока ход цилиндра при нулевом положении люльки не будет составлять 435 мм. По завершении этих работ отверстия вокруг резьбовых пальцев болтов с прямоугольными головками в залитых в фундаменте крепёжных слитках заполняются до верхнего края фундамента песком. Затем нижние подшипниковые стойки заливаются заливочной массой, которая не подвергается усадке. По затвердевании заливочной массы крепёжные болты дозатягиваются.
3.4 Монтаж гидравлической установки Монтажные работы начинают в гидравлическом помещении. В первую очередь монтируются агрегаты, находящиеся на наибольшем удалении от входных ворот. Предварительно смонтированные узлы имеют на своих точках подводов транспортные заглушки. Эти транспортные заглушки удаляются только непосредственно перед подводом гидравлических трубопроводов. При установке агрегатов и резервуаров необходимо работать очень тщательно с соблюдением абсолютной чистоты. Агрегаты устанавливаются на фундамент с соответствующими фундаментными болтами, равняются после подкладывания футеровочных листов, дающих примерно 5 см. Затем крепёжные болты заливаются. После затвердевания заливочной массы агрегаты точно выверяются и крепёжные болты затягиваются. После этого агрегаты бетонируются. Можно использовать только предусмотренные прокладки. Не допустимы пенька и замазка. Нельзя использовать для чистки ветошь, поскольку нельзя допускать проникновения волокон в агрегаты и клапаны. Трубопроводы перед их прокладкой освобождаются от всевозможных загрязнений, если таковые имеются. Трубопроводы должны лежать при прокладке свободно без напряжений. Расстояние между пластиковыми или алюминиевыми зажимами должно составлять от 1 до 1,5 м, если нет других данных.
4. Технология ремонта
4.1 Система планово-предупредительных ремонтов Главная задача службы обслуживания состоит в том, чтобы обеспечить эффективную, безаварийную работу оборудования при минимальных затратах трудовых и материальных ресурсов.
Одним из важнейших условий решения этой задачи является применение системы технического обслуживания и ремонта, суть которой состоит в четком чередовании и регламентации периодов ритмичной работы оборудования в соответствии с установленным режимом профилактических мероприятий с целью предупреждения преждевременного его износа, включая плановые ремонты и межремонтное техническое обслуживание.
Согласно этой системе оборудование в процессе эксплуатации подвергается техническому обслуживанию и плановым ремонтам, направленным на восстановление его работоспособности, частично утраченной в период работы.
4.2 Описание типов ремонтов и их содержание для механизма наклона Содержание оборудования в работоспособном состоянии обеспечивается его техническим обслуживанием и плановым ремонтами.
На предприятиях черной металлургии предусмотрены плановые ремонты двух видов: текущие и капитальные.
Текущий ремонт выполняется для обеспечения или восстановления работоспособности оборудования и состоит в замене или восстановлении быстро изнашивающихся деталей или узлов, выверке отдельных узлов, Элементов металлоконструкции, трубопроводов, смене масла в емкостных системах смазки, проверке креплений и замене вышедших из строя крепежных деталей.
Капитальный ремонт выполняется для восстановления исправности и полного или близкого к полному восстановлению ресурса оборудования с заменой или восстановлением любых его частей, включая базовые. В состав работ по капитальному ремонту входят также работы по модернизации оборудования и внедрению новой техники, выполняемые по заранее разработанным и утвержденным проектам.
Периодичность остановок оборудования на текущие и капитальные ремонты определяется сроком службы деталей и техническим состоянием узлов и механизмов агрегата, продолжительность остановок — временем, необходимым для выполнения наиболее трудоемкой (из запланированной на данный ремонт) работы[19]. Периодичность ремонтов установлена исходя из трехсменной работы оборудования при непрерывном графике. Так как механизм наклона печи связан с технологическим процессом плавки стали, то структура ремонтного цикла механизма аналогична структуре ремонтного цикла печи: 17Т1+К.
Рисунок 9. Структура ремонтного цикла дуговой сталеплавильной печи: Т1? первый текущий ремонт; К капитальный ремонт Для механизма наклона печи в текущий ремонт будут входить следующие работы:
— проверка крепления гидроцилиндров к фундаменту; при необходимости выполнить затяжку болтовых соединений, замену гаек;
— проверка шплинтовых соединений, при необходимости их замена;
— проверка элементов присоединения трубопроводов;
— проверка уровня масла в баке; при необходимости долив;
— дозаполнение смазкой узлов трения;
— очистка поверхностей механизма от производственной пыли.
При капитальном ремонте механизма наклона печи производят демонтаж цилиндров наклона с транспортированием его в участок по ремонту гидропневмооборудования, осуществляют монтаж отревизированного гидроцилиндра с заменой пальцев и сферических подшипников, производят замену шипов, производят опробование механизма.
4.3 Оценка и контроль качества ремонта По завершении ремонта гидроустройств важными операциями, характеризующими качество выполненного ремонта и техническое состояние, являются испытание, настройка, обкатка с определением характеристик и параметров гидроустройств.
Погрешности изготовления поверхностей деталей и неточности сборки обуславливают малую фактическую площадь взаимного контакта сопрягаемых деталей. У неприработанных поверхностей в отдельных точках контакта удельные давления превосходят номинальные в десятки и даже сотни раз. По мере износа неровностей площадь контакта увеличивается, и удельные давления уменьшаются. Приработка подготавливает гидроустройства к восприятию эксплуатационных нагрузок. Поэтому нельзя допускать больших нагрузок в первый период приработки, так как под их влиянием происходит заклинивание, заедание и нагрев трущихся пар.
Во время приработки должны быть реализованы два явления: износ поверхностей на вершинах волн шероховатости и на участках, где исходные технологические неточности, дефекты монтажного происхождения, силовые и тепловые деформации препятствуют распространению пятна контакта до проектного; изменение исходной шероховатости поверхности и формирование новой c определёнными параметрами.
Рисунок 10. Зависимость износа трущихся пар от времени работы
1 — общий случай развития износа;
2 — износ при неблагоприятных условиях приработки;
3 — износ при улучшенных условиях приработки Важную роль играет выбор рационального метода контроля за протеканием процесса приработки. Эффективный контроль позволяет своевременно изменять режимы приработки, чтобы избежать схватывания и разрушения деталей, а также определять время окончания этого процесса. Показателями протекания процесса приработки гидроприводов и их элементов могут служить: уровень шума, температура поверхностей трения и рабочей жидкости, сила трения, к.п.д., вибрация, состояние поверхностей трущихся пар, устойчивость движения. Приработку начинают с режима холостого хода на малых скоростях, постепенно увеличивая нагрузки и плавно повышая скорости движения. Обкатку насосов и гидромоторов с восстановленными плунжерными парами, распределительными устройствами и другими прецизионными элементами следует проводить по регламентам, соответствующим режимам обкатки на заводах-изготовителях данных изделий.
Критериями оценки окончания приработки являются; минимальная мощность, потребляемая на холостом ходу; стабилизация к.п.д., силы трения и температуру; устойчивость движения при малых скоростях; достижение определенной степени прилегания контактирующих поверхностей; снижение вибрации и шума.
Качество ремонта гидроустройств оценивается по результатам приемочных испытаний, при проведении которых необходимо руководствоваться стандартами на правила приемки и методы испытаний, в том числе: ГОСТ 14 658–75 Насосы объемные гидроприводов; ГОСТ 20 719–75 Гидромоторы; ГОСТ 18 464–80- Гидроцилиндры и ГОСТ 20 245–74 Гидроаппаратура. Проверка гидравлического оборудования на герметичность должна осуществляться не менее 1 мин при давлении, составляющем 1,25 номинального давления и температуре жидкости 50−60°С. Наружная герметичность гидроцилиндров дополнительно проверяется при давлении холостого хода после не менее чем пятидесяти полных двойных ходов. При этом допускается образование масляной пленки на поверхности штока без каплеобразования. Появление рабочей жидкости в неподвижных соединениях не допускается.
5. Выбор и расчет систем смазки узлов трения
5.1 Выбор типа смазки и способа смазывания В механизме наклона печи смазываются шарнирные опоры гидроцилиндров наклона 1 (см. рисунок), шарнирные опоры гидроцилиндра фиксирования 2 и опора стойки 3. В этих узлах скорость вращения мала при больших удельных нагрузках. Использование жидкой смазки нецелесообразно. Будем использовать консистентные смазки, так как они наиболее эффективны в подшипниках скольжения сравнительно тихоходных и работающих при высоких нагрузках.
Вследствие рабочего перемещения смазываемых узлов использование централизованной системы густой смазки затруднено, поэтому выбираем индивидуальный способ смазывания.
Рисунок 11. Схема мест смазки
5.2 Выбор сорта смазки При недостаточной смазке, малой скорости скольжения и большой удельной нагрузке подшипники скольжения работают в области граничного и сухого трения, критерием при выборе сорта смазки служит удельная нагрузка и окружная скорость.
Для узла 1:
Усилие, действующее на шток гидроцилиндра: 730 кН Узел смазывания 1 имеет вид шарнирной сферической опоры. Площадь рабочей поверхности шарнирной опоры рассчитаем по формуле:
(45)
где:d — диаметр цапфы (вала), d=160 мм;l
l — длина подшипника, по рекомендации принимаем, находим l=128 мм.
мм2
Рассчитываем удельную нагрузку:
(46)
МПа Рассчитываем окружную скорость:
Угол поворота =8=0,14 рад;
Время наклона корпуса печи от 0° до 40° t =50 сек.
(47)
рад/сек Тогда окружная скорость цапфы равна:
(48)
м/с Для узла 2:
Площадь рабочей поверхности шарнирной опоры рассчитаем по формуле (45):
мм2
Рассчитываем удельную нагрузку по формуле (46):
МПа Рассчитываем окружную скорость по формуле (47):
рад/с Тогда окружную скорость цапфы определяем по формуле (48):
м/с Для узла 3:
Площадь рабочей поверхности шарнирной опоры рассчитаем по формуле (45):
мм2
Рассчитываем удельную нагрузку по формуле (46):
МПа Рассчитываем окружную скорость по формуле (47):
рад/с Тогда окружную скорость цапфы определяем по формуле (48):
м/с С учетом того, что подшипники эксплуатируются в условиях высоких температур и расчетных значений, выбираем из пластичную смазку согласно рекомендациям [13];
Для всех узлов смазывания выбираем консистентную смазку ВНИИ НП-225 ГОСТ 19 782–74, которая применяется для тяжело нагруженных узлов трения при температуре до + 350С.
5.3 Расчёт объёма пластичной смазки Норма расхода пластичной смазки в единицу времени на единицу площади смазываемой поверхности определяется из выражения:
(49)
где — коэффициент, учитывающий зависимость расхода смазки от диаметра подшипника;
— коэффициент, учитывающий зависимость расхода смазки от числа оборотов подшипника;
— коэффициент качества трущихся поверхностей, при хорошем качестве = 1;
— коэффициент, учитывающий рабочую температуру подшипника;
— коэффициент, учитывающий нагруженность подшипника.
Для узла 1:
Для узла 2:
=1 (диаметр цапфы меньше 100 мм) Для узла 3:
Не рассчитываемые коэффициенты принимаем из [12]
— для всех узлов;
— для всех узлов;
— для всех узлов;
— при тяжёлой нагрузке для всех узлов.
Для узла 1:
см3/(м2ч) Для узла 2:
см3/(м2ч) Для узла 3:
см3/(м2ч) Рассчитаем объём пластичной смазки периодически подаваемой к подшипнику:
(50)
где: — площадь контактной поверхности;
— период, между двумя последовательными подачами.
Для узла 1:
см3
Для узла 2:
см3
Для узла 3:
см3
5.4 Нормы расхода смазочных материалов В производственных условиях нормы расхода смазочных материалов можно определить в зависимости от поверхности трения, конструктивного расположения, периодичности работы и системы смазки по формуле:
(51)
где Q — единовременный расход масла;
Kпоправочный коэффициент;
S — площадь смазываемой поверхности.
Поправочный коэффициент выбирается в соответствии с рекомендациями.
Для узла 1:
K=12
г Для узла 2:
K=12
г Для узла 3:
K=12
г Полученный расход примем расходом дозаполнения, который представлен в таблице 16.
Таблица 11
Карта смазки
Обозначение | Смазочное вещество | Кол-во первого заполнения, см3 | Интервалы смазывания, ч | Количество дозаполняемой смазки, г | Способ смазывания | К-во узлов | |
1. Подшипник цилиндра наклона | ВНИИНП-225 ГОСТ 19 782–74 | 46,93 | 2,5 | Индивид заклад. | |||
2. Подшипник цилиндра фиксации | ВНИИНП-225 ГОСТ 19 782–74 | 7,24 | 0,5 | Индивид заклад. | |||
3. Опора стойки | ВНИИНП-225 ГОСТ 19 782–74 | 27,98 | 1,6 | Индивид заклад. | |||
6. Безопасность жизнедеятельности и охрана окружающей среды В данном разделе, произведем анализ вредных и опасных факторов в электросталеплавильном цехе ОЭМК. Опишем средства и меры защиты от этих факторов работников цеха. Рассмотрим соответствия производственных помещений требованиям санитарных норм, законодательную и правовую основу охраны труда и охраны окружающей среды, а также произведем расчет аэрации участка выплавки стали.
6.1 Правовые и нормативно-технические основы охраны труда и окружающей среды Законодательную и правовую основы охраны труда составляют соответствующие законы и постановления, принятые представительными органами РФ, а также подзаконные акты, указы Президента РФ, местных органов власти и предписания специально уполномоченных органов.
Среди законодательных актов по охране труда следует отметить:
— Конституцию РФ (статьи 2, 7, 24, 37, 41, 42, 45, 60);
— Трудовой кодекс РФ. Он был введен в действие с 1 февраля 2002 года. Устанавливает государственные гарантии трудовых прав и свобод граждан, создание благоприятных условий труда, обеспечивает защиту прав работников и работодателей;
— Федеральный закон «О промышленной безопасности опасных производственных объектов» от 20 июня 1997 г., определяющий правовые, экономические и социальные основы обеспечения безопасной эксплуатации опасных производственных объектов и направленный на предупреждение аварий и обеспечение готовности их ликвидации;
— Закон Белгородской области «Об охране труда» от 25 марта 1999 г., определяющий систему управления охраной труда на территории Белгородской области;
— Закон «Об охране окружающей природной среды», введенный в действие с 3 февраля 1992 г. и направленный на обеспечение экологической безопасности;
— Закон «О санитарно-эпидемиологическом благополучии населения» (1991 г.), устанавливающий критерии безопасности и безвредности факторов среды обитания человека;
— Закон РФ «О защите населения и территории от чрезвычайных ситуаций природного и техногенного характера» (1994 г.), составляющий правовую основу организации работ в чрезвычайных ситуациях.
Следует учесть и нормативные требования, которыми руководствуются на предприятии согласно постановлению Правительства РФ от 12 августа 1994"О государственных нормативных требованиях по охране труда в РФ": ГОСТ Р ССБТ, ОСТ Р ССБТ, СП, СН, ГН, СанПиН, СНиП, ПБ, ПУБЭ, СТП. Особо следует отметить СаНПиН 2.2.2.542−96 «Гигиенические требования к видео дисплейным терминалам, персональным электронно-вычислительным машинам и организации работы».
В настоящее время на ОЭМК действует общая инструкция по охране труда для работников комбината ИОТ 00.001.2007 с изм. № 1 и инструкция по противопожарной безопасности ИПБ 62.002.2004 с изм. № 1. Кроме этих, в каждом цехе действуют инструкции по охране труда для каждой специальности.
6.2 Виды инструктажей В силу закона в любых организациях должны проводиться инструктажи по охране труда, а потом проверяться полученные работниками знания. В соответствии со ст. 212, 225, 214 ТК РФ, сотрудники организации обязаны проходить эти инструктажи.
Основные характеристики инструктажей и правила их проведения описаны в ГОСТ 12.0.004−90 и Порядке обучения по охране труда (утв. Постановлением Минтруда России, Минобразования России от 13.01.2003 № 1/29).
Положения указанные в Порядке обучения обязательны для всех организаций без ограничений.
Согласно нормативным документам существуют четыре основных вида инструктажей по охране труда: вводный, первичный (первичный на рабочем месте), повторный и целевой. Дополнительным видом является внеплановый инструктаж. Ниже рассмотрим особенности каждого из них.
Программа вводного инструктажа по охране труда разрабатывается в каждой организации индивидуально на основе действующих нормативно-правовых актов РФ. При этом необходимо учитывать особенности организации и отрасли в целом.
Инструктаж проводит инженер по охране труда либо другой сотрудник, на которого возложили приказом эти обязанности. Проводиться вводный инструктаж с использованием методических материалов или разных тренажеров и других технических средств. Это может быть как кабинет охраны труда, так и иное помещение.
Вводный инструктаж, как правило, осуществляется по утверждённой работодателем программе с фиксированием результатов в журнале.
При этом проводится проверка знаний в устной форме, после которой вносятся сведения в журнал регистрации вводного инструктажа. Подпись сотрудника, проводившего инструктаж и проверку знаний, и инструктируемого обязательно вносятся в журнал.
Вводный инструктаж обычно проводят:
а) с каждым из работников, включая руководителя, которых принимают или переводят на новое место работы;
б) с учащимися и проходящими практику;
в) с работниками, командированными в организацию другими работодателями;
г) с другими лицами, которые участвуют в производственной деятельности организации.
Проводить первичный инструктаж на рабочем месте имеет право только непосредственный руководитель, который до начала самостоятельной деятельности работника прошел обучение и проверку знаний по охране труда.
В этом виде инструктажа обязательно наличие практических занятий для более быстрого и комплексного усвоения знаний и приемов безопасной работы на конкретном рабочем месте.
Программа первичного инструктажа утверждается приказом руководителя организации. Непосредственно разрабатывает программу начальник структурного подразделения на основе законодательства и локальных нормативных актов организации (положение о структурном подразделении, должностные инструкции, инструкции по ОТ и т. д.).
Программа первичного инструктажа по охране труда, утвержденная работодателем, включает в себя:
а) ознакомление работников с имеющимися вредными или опасными производственными факторами;
б) изучение требований охраны труда, которые содержатся в инструкциях по охране труда, локальных нормативных актах организации, эксплуатационной и технической документации, а также применение безопасных приемов и методов выполнения работ.
Факт проведения инструктажа подтверждается собственноручной подписью работника и лица, проводившее его, и указывается дата его проведения.
Если сотрудник не прошел проверку знаний, то приказом он отстраняется от работы до успешного прохождения проверки знаний и умений, приобретенных на первичном инструктаже. Основанием для приказа может стать служебная записка от сотрудника, проводившего инструктаж или проверку знаний.
Первичный инструктаж допустимо проводить с каждым работником по отдельности и сразу с группой лиц, если они работают на однотипном оборудовании или на одном и том же рабочем месте.
На рабочем месте первичный инструктаж по охране труда проводится:
а) со всеми вновь принятыми работниками, которые выполняют обязанности на условиях:
— заключённого на неопределенный срок трудового договора;
— работы на дому;
— заключённого срочного трудового договора (в том числе и на период выполнения сезонных работ или на срок до двух месяцев);
— совместительства;
б) с переведенными из другого структурного подразделения работниками;
в) с работниками, которым поручено выполнение новой для них работы;
г) с лицами, деятельность которых не связанна с организацией трудовых отношений:
— командированные работники сторонних организаций;
— учащиеся образовательных учреждений, которые проходят производственную практику;
— работники сторонних организаций, которые выполняют работы на выделенном участке;
— другие лица, участвующие в производственной деятельности.
Повторный инструктаж полностью повторяет первичный инструктаж на рабочем месте. Единственное отличие заключается в сроках проведения инструктажа. А именно, он проводится не реже одного раза в шесть месяцев для тех, кто проходил первичный инструктаж.
Для оформления внепланового инструктажа по охране труда издаётся приказ или распоряжение, в котором должны быть указаны сотрудники, с которыми он будет проводиться, причина проведения такого инструктажа, его программа и ответственные лица.
Хотя программа и должна определяться в каждом конкретном случае индивидуально, чаще всего внеплановый инструктаж по охране труда проводится по программе первичного инструктажа. Особый упор делается на пункты, связанные с причиной проведения этого инструктажа.
Внеплановый инструктаж проводится непосредственно руководителем работ с сотрудниками, которые указаны в приказе, в следующих случаях:
а) при внесении изменений или введении в действие новых нормативных правовых актов или инструкций по охране труда;
б) при модернизации или замене оборудования, инструмента или приспособлений;
в) при изменении технологических процессов;
г) по требованию должностных лиц органов государственного контроля и надзора;
д) при нарушении работниками требований охраны труда;
е) при перерыве в работе (по решению работодателя; более 30 календарных дней для работ во вредных условиях труда; более двух месяцев);
ж) по решению работодателя или уполномоченного лица.
Целевой инструктаж по охране труда, как правило, оформляется приказом о проведении работ с оформлением наряда-допуска для лиц, которые участвуют в работе.
Целевой инструктаж по охране труда осуществляется при:
а) выполнении разовых работ;
б) ликвидации стихийных бедствий и последствий аварий;
в) производстве работ, на которые оформляются разрешение, наряд-допуск или иные специальные документы;
г) проведении массовых мероприятий в организации (корпоративы и праздники).
6.3 Анализ потенциально опасных и вредных факторов Металлургическое производство характеризуется непрерывностью технологических и трудовых операций и работы механизмов и машин. В этих условиях опасные и вредные производственные факторы проявляют себя постоянно.
Наиболее травмоопасными являются электросталеплавильные цеха. В них около 50% всех несчастных случаев происходит при выполнении основных технологических операций, около 20% при ремонте и наладке оборудования и почти столько же при производстве подъемно-транспортных работ.
Опасными основными производственными факторами являются:
а) расплавленный металл и шлак;
б) движущиеся и вращающиеся машины и механизмы;
в) тяжести, перемещаемые грузоподъемными механизмами;
г) электрический ток;
д) пламя;
е) расположение рабочих мест и оборудования на высоте.
Вредные факторы производственного процесса при длительном и интенсивном их воздействии на человека могут привести к возникновению профессиональных заболеваний трудящегося. К этим факторам относятся:
а) тепловые, ультрафиолетовые, ионизирующие и другие излучения;
б) электромагнитные поля;
в) яркое слепящее световое излучение;
г) выделяющиеся в атмосферу производственного помещения пыль и газ;
д) высокий уровень шума и вибрации, ультразвук.
Рабочие ЭСПЦ подвергаются воздействию всех вышеперечисленных факторов. Данные замеров основных производственных факторов участка и их нормативные значения приведены в таблице.
Таблица 6.1
Условия труда при транспортировке стали
Наименование рабочего места | Фактор производств. среды | Единицы измерения | Значение норматива | Данные замера | Отклонение | |
Участок ДСП-150 (процесс слива стали) | Шум | дбА | ||||
T0 | 0С | 16 … 24 | 42,4 | 18,4 | ||
Влажность | % | -; | ||||
Пыль | мг/м3 | 14,6 | 10,6 | |||
Теплообл. | Вт/м3 | |||||
Рабочая площадка установки вакуумирования (процесс вакуумирования) | Шум | дбА | ||||
T0 | 0С | 16 … 24 | 32,8 | 8,8 | ||
Влажность | % | -; | ||||
Пыль | мг/м3 | 16,9 | 12,9 | |||
Теплообл. | Вт/м3 | |||||
MnO2 | мг/м3 | 0,05 | 0,121 | 0,071 | ||
C4O3 | мг/м3 | 0,01 | не обн. | -; | ||
NO2 | мг/м3 | 2,5 | -; | |||
CO | мг/м3 | не обн. | -; | |||
Рабочая площадка установки вакуумирования | Шум | дбА | ||||
T0 | 0С | 16 … 24 | 32,8 | 8,8 | ||
Влажность | % | -; | ||||
Теплообл. | Вт/м3 | |||||
Пыль | мг/м3 | 21,5 | 17,5 | |||
MnO2 | мг/м3 | 0,05 | 0,182 | 0,132 | ||
C4O3 | мг/м3 | 0,01 | не обн. | -; | ||
Рабочая площадка продувки аргоном | Шум | дбА | ||||
T0 | 0С | 16 … 24 | ||||
Влажность | % | -; | ||||
Пыль | мг/м3 | 9,9 | 5,9 | |||
Теплообл. | Вт/м3 | |||||
MnO2 | мг/м3 | 0,05 | 0,374 | 0,324 | ||
C4O3 | мг/м3 | 0,01 | не обн. | -; | ||
NO2 | мг/м3 | 4,1 | -; | |||
CO | мг/м3 | 8,3 | -; | |||
Разливочный стенд МНЛЗ (процесс разливки стали) | Шум | дбА | ||||
T0 | 0С | 16 … 24 | 38,7 | 14,7 | ||
Влажность | % | -; | ||||
Пыль | мг/м3 | 11,3 | 7,3 | |||
Теплообл. | Вт/м3 | |||||
MnO2 | мг/м3 | 0,05 | 0,047 | -; | ||
C4O3 | мг/м3 | 0,01 | не обн. | -; | ||
NO2 | мг/м3 | 3,9 | -; | |||
CO | мг/м3 | 7,5 | -; | |||
Анализируя результаты проведенных замеров, можно прийти к следующему выводу, что работа на основных рабочих местах этого участка является неблагоприятной, в различной степени по каждому фактору производственной среды.
Из всех вредных выше перечисленных производственных факторов, имеющихся в цехе, наиболее значительными являются шум, теплооблучение и высокая температура.
Шумом является беспорядочным сочетанием различных по силе и частоте звуков. Шум различной интенсивности и частоты оказывает на организм человека неблагоприятное воздействие и может вызвать различного рода болезненные состояния, в том числе тугоухость и глухоту. Источниками шума в цехе являются, главным образом, электропечи, а также мощные редукторы. Производственное оборудование, создающее шум снабжают паспортом, в котором указывают шумовые характеристики его работы. Для снижения шума в электросталеплавильном цехе предусмотрены звукоизолирующие кожухи вокруг электропечей, шумопоглотители на пароинжекторных насосах вакуумных установок и системах вентиляции, отделен стенами шихтовый пролет и предусмотрена звукоизоляция служебных помещений и постов управления. На приточных и вытяжных системах, обслуживающих помещение, на всасывающих и нагнетательных линиях вентиляторов устанавливаются, как правило, пластинчатые шумопоглотители. Особую опасность представляют собой совместное влияние шума и вибрации.
Вибрацию порождают неуравновешенные силовые воздействия, возникающие при работе машин. Вибрации создают станки участка отделки, удары клеймовочных машин, передвижение мостовых кранов. Для ослабления вибрации все агрегаты, создающие ее (двигатели, вентиляторы, рабочие машины), устанавливают на самостоятельных фундаментных, виброизолированных от пола и других конструкций зданий. В качестве средств специальной защиты от вибрации используют рукавицы с двойным слоем: резиновые (снаружи) и хлопчатобумажные (внутри) и виброгасящую обувь.
Повышенная температура воздуха рабочей зоны и тепловое излучение металла приводят к возможности получения теплового удара. Этот фактор присутствует практически на всех участках цеха, поэтому как средства индивидуальной защиты рабочим выдается суконный костюм с пропиткой и защитные очки со светофильтрами.
Еще одним вредным фактором является запыленность рабочих мест. Пыль образуется при транспортировке сыпучих материалов к расходным бункерам и непосредственно при засыпке их в печь. Также источниками образования пыли являются шлифовальные станки и дробеструйные установки для зачистки литой заготовки и сбива окалины. Для защиты слизистых оболочек органов дыхания применяются респираторы типа «лепесток».
В сталеплавильном цехе постоянно существует опасность возникновения взрыва и пожара, потому что широко используются огнеопасные жидкости в качестве смазочных материалов. Пары огнеопасных жидкостей образуют с воздухом смеси, которые могут взрываться при определенных концентрациях. На предприятиях черной металлургии используют в качестве топлива или получают в результате производственной деятельности различные газы. Независимо от состава газы обладают опасными и вредными свойствами. К опасным свойствам относят способность газов воспламеняться и гореть со взрывом.
Мероприятия по предупреждению взрыва газа сводятся главным образом к предотвращению образования взрывоопасной газовоздушной смеси и к предотвращению вероятности взрыва. Взрывоопасным считаются помещения, где вследствие не плотности газовых сетей возможны утечки газа.
Правила безопасности при эксплуатации газового хозяйства предприятия предусматривают проведение специального обучение обслуживающего персонала; постоянного поддержания сверхатмосферного давления газа в газопроводе для исключения подсоса атмосферного воздуха и образования в нём опасной газовоздушной смеси; исключение источников открытого огня и искр около газопроводов и газового оборудования; постоянный контроль качества применяемого газа и атмосферы рабочих мест.
Составные части газов и некоторые, содержащиеся в нем примеси оказывают на организм человека вредное воздействие: отравляющее и удушающее. Удушающее воздействие обусловлено недостатком кислорода во вдыхаемом воздухе. При содержании кислорода в воздухе на уровне 6% дыхание останавливается. Отравляющие газы, даже при большом содержании кислорода в воздухе вызывают различные нарушения функций организма человека. Окись углерода СО разрушает гемоглобин крови, препятствуя передаче кислорода в организм. Допустимая концентрация СО в помещениях рабочих мест-0,02мг/л. Признаком отравления являются: головная боль, шум в ушах слабость, тошнота. При более тяжелых степенях отравления — потеря сознания, прекращение дыхания, остановка сердца.
Работы по локализации аварий до устранения прямой угрозы людям и разрушению оборудования могут выполняться без оформления наряда-допуска. После устранения такой угрозы газоопасные работы производятся после оформления наряда-допуска.
При выполнении газоопасных работ для защиты от отравляющих и удушающих воздействий газов используют газозащитные изолирующие аппараты. Применение фильтрующих противогазов недопустимо по следующим причинам: в фильтрующих противогазах вдыхаемый воздух предварительно очищается от вредных примесей в фильтрах с разными поглотителями. Эти противогазы очищают вдыхаемый воздух, когда в нём не менее 16−17% кислорода. Изолирующие противогазы в отличие от фильтрующих полностью изолируют органы дыхания человека от окружающей атмосферы, содержащей вредные газы.
Газозащитные аппараты периодически, а также перед применением и после каждого случая применения подвергают проверке в соответствии с действующими инструкциями.
При выполнении газоопасных работ используется инструмент, исключающий образование искр при ударе. Для изготовления взрывобезопасных инструментов применяют цветные металлы (медь, бронза, алюминий).
Для исключения образования искр при выполнении газоопасных работ предъявляются определённые требования к обуви персонала. Последняя должна быть без стальных гвоздей и подков; в противном случае на такую обувь одевают калоши. При выполнении газоопасных работ применяются переносные светильники во взрывозащитном исполнении.
Для обнаружения самой первоначальной стадии пожара (загорания) и сообщения о месте его возникновения в цехе установлена вспомогательная сигнальная установка, подключенная к главной сигнальной установке пожарной службы комбината. На постах управления устанавливаются термодифференционные извещатели, которые реагируют на повышение температуры на единицу времени и кнопочные сигнализаторы для ручной подачи сигналов тревоги диспетчеру.
Тушение пожаров сводится к прекращению реакции горения путем технического, физического или химического воздействия. Тушение пожаров в цехе осуществляется водой, которая поступает из сети трубопроводов через гидранты. При тушении пожаров в электросталеплавильном цехе следует учитывать, что серьезную опасность представляют взрывы при контакте расплавленного металла с водой, при чем взрывы происходят при внутреннем контакте жидкого металла с водой (при поступлении жидкого металла или шлака в воду и при поступлении воды в расплав), в то время как попадание ее только на поверхность расплава приводит к охлаждению верхних слоев и образованию твердой корки.
Помещения трансформаторов на участке выплавки и помещения гидроустановок оснащаются стационарными углекислотными огнетушителями с автоматическом включении при пожарах. В помещениях с повышенной пожарной опасностью, например, насосно-аккумуляторных станциях, запроектирована система пожаротушения с автоматическим управлением. Для тушения пожаров в электропомещениях предусматриваются ручные, передвижные огнетушители и огнезащитные покрытия.
В производственных помещениях оборудуют противопожарные уголки, снабженные ящиками с песком, емкости с водой и пожарно-инвентарным щитом с набором инвентаря: лопат, багров, крюков топоров и т. д. для тушения небольших очагов пожара при воспламенении твердых горючих материалов применяют ручные пенные огнетушители.
При обнаружении возгорания или пожара обслуживающий персонал производственного подразделения (цеха) обязан незамедлительно принять меры по тушению загорания (пожара) всеми имеющимися на рабочем месте средствами пожаротушения, известить руководство цеха и пожарную охрану по телефону 01 или с помощью пожарного извещателя. Ответственность за обеспечение пожарной безопасности цеха несёт начальник цеха, а на участке — руководитель участка.
В цехе необходимо строгое соблюдение электрои газобезопасности. Электробезопасность — система организационных мероприятий и технических средств, обеспечивающих защиту людей от вредного воздействия электрического тока и электрической дуги.
Безопасная эксплуатация электрооборудования может быть достигнута при безукоризненном выполнении требований действующих правил, норм и инструкций по электробезопасности. Надежность и безопасность электрооборудования значительно повышается при применении межремонтного обслуживания, основой которого являются ежедневные осмотры оборудования, поддержание его в рабочем состоянии.
При размыкании электрических цепей в момент отключения электроустановок возникает электрическая дуга, для исключения этого применяют выключатели различных конструкций — воздушные, масляные и безмасляные.
Полную безопасность от поражения электрическим током обеспечивают магнитные пускатели. Для защиты электроустановки от перегрузок применяют плавкие предохранители. Для распределения и передачи электроэнергии по территории предприятия прокладывают электрические кабели. Для питания стационарных установок используют бронированные кабели со свинцовой или алюминиевой оболочкой, а для питания передвижных установок и электрифицированного инструмента — гибкие кабели с резиновой оболочкой. Прокладка силовых кабелей производится в металлических трубах под землей в специально устроенных кабельных каналах и тоннелях. В производственных помещениях кабели прокладывают, открыто по стенам, перекрытиям или металлоконструкциям.
Для безопасного обслуживания электроустановок сети систематически проверяется изоляция на электропрочность. При нормальных производственных условиях изоляцию сети проверяют не реже одного раза в год, в сырых помещениях проверку проводят не реже двух раз в год. Изоляция в электроустановках считается удовлетворительной, если ее сопротивление на участке сети между предохранителями не менее 0,5 Ом.
Для защиты от поражения электрическим током рабочих осуществляется защитное заземление нетоковедущих металлических частей электроустановок. Заземление является обязательным в помещениях повышенной опасности или особо опасных при напряжении электроустановок выше 36 В переменного тока или 110 В постоянного тока, а в помещениях без повышенной опасности — при напряжении 500 В и выше. Во взрывоопасных помещениях заземление выполняется независимо от величины напряжения.
В качестве молниеприемников при ударах молнии используется металлическая кровля здания цеха. В качестве магистралей заземлителя и молниеотводов используется специально проложенные для этой цели проводники, либо естественные магистрали заземления (металлоконструкции здания).
Чтобы исключить возможность прикосновения или опасного приближения к не заизолированным токоведущим частям, предусмотрены ограждения и блокировки. Токоведущие части располагают на недоступной высоте или в недоступных местах.
При обслуживании электроустановок применяют основные и дополнительные защитные средства. К основным защитным средствам относятся те средства, изоляция которых надежно выдерживает рабочее напряжение установки. К дополнительным относятся средства, усиливающие действие основных средств.
Для обслуживания распределительных устройств должен иметься комплект защитных средств, в который входят: изолирующая штанга, изолирующие клещи, диэлектрические боты, диэлектрические перчатки или рукавицы, изолирующие подставки, изолирующий коврик, изолирующие прокладки, защитные очки, переносные ограждения, указатели напряжения, переносные защитные заземлители — закоротки и не менее двух противогазов.
Все работы на электроустановках производятся с письменного или устного разрешения вышестоящего лица. На электроустановках напряжением выше 1000 В работы выполняются только по наряду-допуску. Работы проводятся: при полном снятии напряжения; при частичном снятии напряжения на электрооборудовании; без снятия напряжения, например при осмотре, уборке помещения с обязательным применением средств индивидуальной защиты.
В обеспечение безопасных условий труда входит своевременное обучение персонала и проведение периодического контроля знаний персонала, работающего с электроустановками. Обслуживающий персонал цеха должен быть обучен правилам оказания первой медицинской помощи лицам, пораженным электрическим током.
6.4 Охрана окружающей среды При строительстве комбината была разработана новая стратегия природоохранной деятельности: внедрение технологий уменьшающих вредное воздействие предприятия на окружающую среду. Комбинат расположен в 22 километрах от города Старый Оскол. Вокруг комбината организована санитарно-защитная зона, на границе которой концентрации соединений азота, серы, пыли, оксидов углерода составляют 0,3 — 0,7 ПДК.
Вода используется в оборотных циклах. Разделение промышленной, хозбытовой и ливневой канализации позволяет исключить смешивание стоков. Ливневые воды с площадки комбината собираются в накопители, очищаются и частично возвращаются на комбинат.
Данная технология включает в себя подготовку железорудного сырья, производство окатышей, их металлизация в шахтных печах и плавку в электродуговых печах.
Основными источниками загрязнения в ЭСПЦ № 2 являются 4 электропечи ДСП-150, печи замедленного охлаждения, устройства и стенды для сушки и нагрева ковшей, вакуум-камеры, аспирационные системы участка шихтоподачи, отделений приемных и расходных бункеров.
Каждая электропечь укрыта специальным кожухом, позволяющим предотвратить поступление в цех и атмосферу дымовых газов, выделяющихся при загрузке печей, сливе стали, шлака, а также газов, выбивающихся из межэлектродных зазоров, при открывании дверцы печи.
Отвод газов из 4 отверстия сводов печей и из кожуха печи — в общую для каждой электропечи газоочистную систему в рукавных фильтрах для очистки до остаточной концентрации взвешенных веществ не более 50 мг/м3. После очистки газы сбрасываются в атмосферу через одну трубу, высотой 120 метров.
Шлак, окалина и обрезь, являющиеся отходами производства тоже требуют переработки и решений по их дальнейшему использованию. Окалина и обрезь идут на переплавку, а шлак вывозится на шлаковые отвалы, а потом может использоваться в строительстве.
Топливом для нагревательных печей, печей замедленного охлаждения, устройств и стендов для подогрева промковшей, вакуум-камеры и т. д. является природный газ, при сгорании которого в атмосферу поступают: диоксид азота, серы, диоксид и оксид углерода. Дымовые газы от 4 печей замедленного охлаждения выбрасываются в 2 дымовые трубы высотой по 120 м.
Очистка воздуха всех аспирационных систем цеха предусмотрена в тканевых фильтрах, за исключением газов от транспортирующих устройств извести и металлизованных окатышей, для которых, в целях взрывобезопасности, предусмотрено мокрая очистка в скрубберах. Все установки газоочистки работают эффективно, остаточная запыленность составляет от 30 до 100 мг/м3. Очистка газов от агрегатов АКОС-150 осуществляется до остаточной запыленности 50г/м3.
Для эффективной трудовой деятельности необходимо обеспечить требуемую чистоту воздуха. Это достигается при помощи вентиляции. Ниже приводится расчет аэрации печного участка.
Необходимый воздухообмен определяется по формуле:
кг/ч ()
где — избыток явного тепла, ккал/ч;
С — теплоемкость воздуха, С = 0,24 ккал/(кг* ?С);
— температура уходящих газов, ?С;
— температура наружного воздуха, tн = 20? С.
Избыток явного тепла определяется по формуле:
()
где — производительность участка т/ч, П=231 т/ч;
— удельное выделение тепла на одну тонну стали; q = 190 000 ккал/т;
ккал/ч Температура уходящих газов определяется по формуле:
()
где — температура рабочей зоны, tр.з. = 30С;
— коэффициент воздействия тепла на температуру воздуха в рабочей зоне, m = 0,3.
Необходимый воздухообмен:
кг/ч Определяем площадь приточных и вытяжных отверстий. При условии их равенства, площадь каждой из них равна:
м2 ()
где — разность температур уходящих газов и наружного воздуха, t = 16,6;
— средний коэффициент расхода, = 0,5;
— расстояние от пола до центра проемов, Н =24.5 м.
м2
Площадь вытяжных отверстий определяют по формуле:
м2 ()
где — объем вытяжки воздуха, м3/ч;
— скорость воздуха на выходе, м/с.
Объем воздуха определяется по формуле:
м3 ()
где — объемный вес воздуха, = 1,1182 кг/м3.
м3
Скорость воздуха при отношении равном равно 3 м/с.
м2
Учитывая, что площадь вытяжных отверстий в цехах с избытками явного тепла должна превышать площадь приточных отверстий приблизительно на 20%, принимаем площадь вытяжных отверстий м2.
В целом работа по охране труда и технике безопасности в цехе поставлена хорошо. Устанавливаемые в местах вредных выбросов газоочистные сооружения уменьшают объем выброса веществ в атмосферу до допустимых норм. На случай возможных аварий разработан план ликвидации для каждого производственного участка цеха. В соответствии с анализом потенциально опасных и вредных производственных факторов выбраны средства коллективной и индивидуальной защиты.
Согласно санитарным нормам и правилам на предприятии для персонала цеха предусмотрены мероприятия по гигиене и бытовым условиям, такие как душевые, туалеты, питьевые фонтаны, комнаты отдыха, буфеты, столовые. Медицинские пункты работают 24 часа в сутки. Скорая помощь, располагающая реанимационным автомобилем, дежурит круглосуточно. На каждом рабочем месте, в каждой слесарке, на всех постах управления имеются аптечки. Каждая аптечка содержит: шприц одноразовый (5мл), термометр, аспирин в таблетках, анальгин в таблетках и ампулах (50% раствор), бинт марлевый медицинский, валидол в таблетках, вата медицинская, гигроскопическая гигиеническая нестирильная, напальчник, нитроглицерин в таблетках, раствор бриллиантового зелёного спиртовой 1%, настойка валерианы, раунатин, йод спиртовой 5%, валокордин, корвалол.
Список использованных источников
1. Проект сталеплавильного цеха ОЭМК. Технологические решения. М.: Гипромез, 1986. 235с.
2. Якушев А. М. Основы проектирования и оборудование сталеплавильных и доменных цехов. М.: Металлургия, 1982. 422с.
3. Свешников В. К. Станочные гидроприводы: Справочник. 3-е издание перераб. и доп. М.:Машиностроение, 1995.
4. Навродский К. Л. Теория и проектирование гидрои пневмоприводов. М.: Машиностроение, 1991.
5. Анурьев В. И. Справочник конструктора-машиностроителя: в 3-х т/под ред. И. Н. Жестковой. М.: Машиностроение 2001. (КП)
6. Надежность, ремонт и монтаж металлургических машин. Учебник для вузов. Плахтин В. Д. М., Металлургия, 1983.
7 Иванов, М. Н. Детали машин [Текст]: учебник для машиностроительных специальностей вузов / М. Н. Иванов, В. А. Финогенов — 9-е изд., испр. — М.: Высш. шк., 2005. — 408с.;
9. Гедык П. К., Калашникова М. И. Смазка металлургического оборудования. — М.: Металлургия, 1971. 483с.
18. Притыкин Д. П. Надежность, ремонт и монтаж металлургического оборудования: Учебник для вузов. М.: Металлургия, 1985. 386 с.
19. Положение о техническом обслуживании и ремонтах (ТОиР) механического оборудования предприятий системы Минчермета СССР. М.: Минчермет СССР, 1983. 390с.
21. Общие правила безопасности для предприятий и организаций металлургической промышленности. М. 1986. 76 с.
22. Правила безопасности в сталеплавильном производстве. М.: Металлургия. 1984. 144 с.
23. Ипатов П. П. Безопасность труда при ремонте металлургических агрегатов. М.: Металлургия. 1976. 88 с.
24. Положение о ремонте механического оборудования комбината. Старый Оскол. 1994. 36 с.