Газораспределение в шахтной печи металлизации
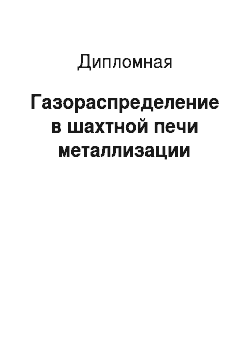
Из трубы материал попадает в камеру выгрузки продукта, снабженную разгрузочным скребковым устройством, стимулятором потока, двумя роликовыми грохотами и двумя отводами для удаления и выгрузки из камеры в наружный бункер крупных кусков (спеков). В нижней своей части камера соединяется с пятью трубами для подачи горячего материала в брикетные прессы и с одной байпасной трубой. С помощью байпасного… Читать ещё >
Газораспределение в шахтной печи металлизации (реферат, курсовая, диплом, контрольная)
1. Общая часть
1.1 Восстановление железа газовыми восстановителями
1.2 Характеристика сырья используемого в процессе ХИЛ III
1.3 Характеристика основного оборудования процесса ХИЛ III
1.4 Технология восстановления железа в процессе ХИЛ III
1.5 Технология получения восстановительного газа в процессе ХИЛ III
2. Расчетная часть
2.1 Газораспределение в шахтной печи металлизации
2.2 Расчет баланса твердых веществ в процессе металлизации
2.3 Определение расхода восстановительного газа
2.4 Расчет состава колошникового газа
2.5 Расчет времени пребывания окатышей в конусной части реактора
2.6 Расчет материального баланса процесса металлизации в процессе ХИЛ III
3. Организационно технологическая часть
3.1 Организационно управленческая характеристика Лебединского горно-обогатительного комбината
3.2 Организационно-управленческая характеристика цеха ГБЖ1
3.3 Оценка эффективности деятельности ОАО «Лебединский ГОК»
4. Экономическая часть
4.1 Расчет тарифного фонда оплаты труда цеха ГБЖ 1
4.2 Расчет затрат по статьям себестоимости 1 тонны металлизованных окатышей с содержанием железа 66,77
5. Охрана труда и окружающей среды
5.1 Общие требования техники безопасности для работников ОАО «ЛебединскийГОК»
5.2 Действие теплового излучения на организм человека и защита от него
5.3 Охрана труда женщин Заключение Список использованных источников
Важный параметр для процесса восстановления — подбор шихтовых материалов, подходящих для обработки в печи. Это требует оценки химических и физических характеристик сырья. Необходимо учитывать восстановимость, газопроницаемость и склонность шихты к разрушению.
Прочность металлизованного продукта зависит почти полностью от характеристик подаваемой шихты. При работе на окисленных окатышах прочность металлизованного продукта связана с прочностью окисленного сырья. При работе на кусковой руде, напротив, не прослеживается подобная связь. Некоторые очень прочные руды дают слабый металлизованый продукт. Каждая руда должна быть оценена с точки зрения прочности готового продукта.
Химический состав шихты также очень важен, так как примеси и пустая порода переходят из шихтовых материалов в металлизованый продукт Высокое содержание пустой породы увеличивает расход электроэнергии и огнеупоров в сталелитейном переделе. Таким образом, на качество и стоимость металлизованного продукта и пригодность его для дальнейшей обработки непосредственно влияет химический состав шихты. Известь, магнезия и окись титана влияют на восстановимость окиси железа и, следовательно, могут снизить степень металлизации Большинство производителей стали имеет определенные ограничения максимального количества серы, фосфора и ванадия в металлизованом продукте.
1. Общая часть
1.1 Восстановление железа газовыми восстановителями
Процесс восстановления железа из оксидов по принципу Байкова о последовательности превращений протекает ступенчато путем последовательного перехода от высших оксидов к низшим по схеме
Fe203 > Fe304 > FeO > Fe (выше 570°C) или Fe203 > Fe304 > Fe (ниже 570°C).
Исходя из вида газообразного продукта восстановления, по аналогии с доменной плавкой различают прямое и непрямое (косвенное) восстановление. Восстановление, в ходе которого продуктом является СО, называют прямым, а восстановление, в ходе которого образуются С02 или Н20, — косвенным. С этой точки зрения реакцию С02 + С = = 2СО можно также рассматривать как прямое восстановление (если углекислота не является продуктом диссоциации карбонатов).
Реакция является удобной схемой для объяснения механизма прямого восстановления. Действительно, трудно представить протекание суммарной реакции прямого восстановления в изображенном виде. В этом случае (реакция в твердой фазе) следовало бы считаться с невозможностью протекания реакции в большем объеме из-за малой протяженности контактных поверхностей оксидов железа и углерода. В действительности же эта реакция при высоких температурах проявляется достаточно сильно, что свидетельствует о том, что кислород от оксида отделяется газом (СО или Н2).
Однако механизм прямого восстановления в достаточной мере еще не расшифрован. Обычно принимают (в согласии с экспериментальными данными), что косвенное восстановление соответствует умеренным температурам (до 900—1000 °С), а прямое — высоким.
Выше рассмотрены особенности прямого восстановления при отсутствии твердых растворов. Появление твердых растворов изменяет реакцию в том смысле, что частично вместо чистого углерода появляется связанный или растворенный в железе углерод.
1.2 Характеристика сырья используемого в процессе ХИЛ III
В качестве сырья в процессе ХИЛ III используют железорудные окатыши и природный газ для производства восстановительного газа.
1) Химический состав железорудных окатышей.
— Feобщее % по массе 66.95
— Fe2+ % по массе 0.21
— Пустая порода % по весу 4.3
— Кислород сбалансированный В любом случае, рекомендуемые для технологического процесса окатыши должны соответствовать требованиям типичного химического анализа:
— Feобщее
— Fe2+ % по массе 0.80 максимально
— TiO2 %по массе 0.20 максимально
— К2О + Na2О % по массе 0.10 максимально
2) Физические свойства Физические и механические свойства окатышей для технологического процесса не должны значительно отклоняться от следующих характеристик:
а) Гранулометрический анализ после грохочения Распределение по размеру [% по массе]
+16 мм 5,0 максимальная
— 16/+10 мм сбалансировано
— 10 мм 9,0 максимально
6,3 мм 1,0 максимально б) Насыпной вес (т / м3) 2.0 минимально
в) Пористость частиц (%) 20.0 минимально
г) Механическая прочность
Прочность на сжатие
(кг / окатыш) (+ 10 мм — 16 мм) 200 минимально Индекс ударной прочности
(%; + 6.3 мм) 95 минимально Барабанный индекс
(%; + 6.3 мм) 95 минимально
(%; - 500 mм) 4 максимально
* согласно методике стандартного испытания ХИЛ.
3) Металлургические характеристики
Металлургические свойства окатышей для технологического процесса не должны существенно отклоняться от следующих характеристик (согласно стандартным методикам ХИЛ):
а) Индекс слипаемости
при 950 0С непокрытые 30 максимально
после покрытия 45 максимально
б) Индекс разбухания (%)
при 800 0С 10 максимально
при 950 0С 10 максимально
в) Индекс восстановительной способности
(k х 102 мин -1)
при 800 0С 3.0 минимально
при 950 0С 4.0 минимально
г) Низкотемпературное разрушение
%; 500 0С; + 6.3 мм 88 минимально
%; 500 0С; - 3.2 мм 10 максимально
4) Брикетируемость
Окатыши должны иметь необходимую брикетируемость для достижения гарантируемых характеристик
Природный газ
Компонент Объема %
CH4 98/64
C2H6 0.36
C3H8 0.09
C4H10 и тяжелее 0.02
N2 0.89
CO2 0.0
H2S 0.002 г/Нм3
Меркаптаны 0,016 г/Нм3
Низшая теплотворная способность 8520 ккал/Нм3*
Давление 13 кг/см2А
Температура 1 … 25 0С
На основе метода I.S.O. (коэффициент нагрева, рассчитан при 250С;
стандартный объем при 1 атм. и 0 0С)
Перерасчет на объем при 1 атм. и 20 0С.
Электроэнергия
На установку HBI будет подаваться энергия от внешней электрической сети:
— Напряжение 6 кВ
— Частота переменного тока 50 Гц (+/- 1%)
— Количество независимых электролиний 2 (одна аварийная)
— Мощность каждой линии согласно требуемой максимальной мощности установки
1.3 Характеристика основного оборудования процесса ХИЛ III
Шахтная печь включает, кроме собственно печи систему загрузки окисленных окатышей
Система загрузки состоит из загрузочного бункера с уровнемерами и устройствами аварийной сигнализации, верхней уплотнительной трубы, дозировочного бункера (распределительного устройства) и 16 загрузочных труб. Система обеспечивает постоянное и равномерное распределение окатышей по сечению печи и благодаря этому равномерный поток восстановительного газа и его интенсивное взаимодействие с восстанавливаемыми окатышами. Кроме того, в результате применения надежного газодинамического уплотнения система эффективно препятствует выбросам печного газа в атмосферу.
Собственно шахтная печь состоит из зоны нагрева и восстановления, зоны вдувания горячего восстановительного газа, зоны с верхними и средними питателями постоянного действия и транзитной зоны. Кожух печи сварной с общей высотой около 33 м.
На вертикальном участке печи высотой 4−5 м в зоне верхних и средних питателей постоянного действия имеется опорное кольцо, с помощью которого печь опирается на металлоконструкции этажерки.
Для обеспечения равномерного схода материалов без образования застойных зон, эффективного использования всего объема печи, высоких ее производительности и степени металлизации продукта в печи устанавливаются питатели постоянного действия, а также коническая вставка.
Печь имеет тонкостенную износостойкую футеровку и изоляционный слой, выполненные из огнеупорного кирпича и плавленых огнеупоров.
Скруббер колошникового газа Для очистки от пыли и охлаждения колошникового газа применяется скруббер с трубой Вентури.
В скруббере газ разделяется на два потока (технологический и топливный), проходящие через отдельные секции с насадками, в которых он дополнительно охлаждается.
С целью регулирования температуры газовых потоков для их охлаждения подается вода с различной температурой. Для охлаждения технологического газа — 67 оС, а для охлаждения топливного газа — 32 оС. Благодаря подаче горячей воды обеспечивается требуемое по условиям конверсии природного газа соотношение Н2О / СО2 в технологическом газе. Колошниковый топливный газ с целью повышения его теплотворной способности охлаждается до более низкой температуры холодной водой.
Скруббер рассчитан на очистку и охлаждение максимального количества колошникового газа (380 тыс. нм3/ч).
Система выгрузки горячих металлизованных окатышей Горячий восстановленный материал (температура около 700 оС) выдается из печи через нижнюю уплотнительную трубу и камеру выгрузки продукта. При этом пропускная способность нижнего питателя постоянного действия обеспечивает необходимую скорость выдачи продукта из печи.
Для отсечки печи от атмосферы в нижней ее части предусматривается подача под давлением сухого уплотнительного газа. Этот газ отводится из камеры выгрузки продукта в систему обеспыливания нижнего уплотнительного газа.
Из трубы материал попадает в камеру выгрузки продукта, снабженную разгрузочным скребковым устройством, стимулятором потока, двумя роликовыми грохотами и двумя отводами для удаления и выгрузки из камеры в наружный бункер крупных кусков (спеков). В нижней своей части камера соединяется с пятью трубами для подачи горячего материала в брикетные прессы и с одной байпасной трубой. С помощью байпасного разгрузочного устройства шнекового типа материал, минуя брикетные прессы, подается на конвейеры — охладители продукта. Обычно таким путем выгружаются из печи реметы, образующиеся при ее запусках и остановках.
Система горячего брикетирования окатышей и охлаждения ГБЖ Система горячего брикетирования включает пять брикетных прессов, пять сепараторов брикетов, одну байпасную линию и три конвейера — охладителя брикетов.
Горячие металлизованные окатыши задаются в пресс с помощью шнекового питателя. Для получения брикетов в форме «подушек» применяются прессы роликового типа с формующими штампами, расположенными в два ряда по окружности
Непрерывная брикетная лента из пресса подается в сепараторы, где разделяется на отдельные брикеты. После сепараторов брикеты поступают на охлаждающие конвейеры и там подвергаются замедленному охлаждению водой. Количество воды подаваемой из форсунок, регулируется таким образом, что позволяет не только охладить, но и высушить брикеты за счет их тепла.
Системы обеспыливания Как указывалось ранее, большая часть нижнего уплотнительного газа отводится из камеры выгрузки продукта в соответствующую систему обеспыливания.
После отвода из камеры выгрузки продукта газ разбавляется воздухом, очищается от пыли в скруббере и вентилятором через трубу сбрасывается в атмосферу. Предусматривается резервирование этой системы с очисткой уплотнительного газа в барботере.
Отдельная система предусматривается для обеспыливания брикетных прессов. В систему отводится газ от самих прессов, их загрузочных труб и сепараторов брикетов. Этот газ вначале попадает в циклон, а затем после грубой очистки от пыли — в скруббер и далее вентилятором через трубу сбрасывается в атмосферу. Горячая пыль, уловленная в циклоне, возвращается в брикетный пресс.
Для отвода пара от конвейеров — охладителей брикетов предусматривается отдельная система, включающая вентилятор и трубу.
Реформер Конверсия природного газа осуществляется в реформере, корпус которого с футерованным рабочим пространством представляет газоплотную сварную конструкцию длиной около 60 м, шириной около 20 м и высотой около 9 м.
В реформере устанавливается 510 реакционных труб, в которых происходит пароуглекислотная конверсия природного газа. Трубы расположены в 17 отсеках по 30 труб в каждом. Катализатор конверсии природного газа, заполняющий реакционные трубы, состоит из наполнителя, содержащего в качестве активного компонента никель. Общая масса катализатора, единовременно загружаемого в трубы реформера, составляет 295 т.
Реакционные трубы выполнены из жаростойкого хромоникелевого сплава и подвешены к металлоконструкции над сводом реформера.
Конвертированный газ из труб поступает в три коллектора, которые за пределами конструкции реформера соединяются в один, транспортирующий газ к шахтной печи. Коллекторы футеруются огнеупорами.
Отопление реформера осуществляется с помощью горелок, расположенных в его подине. В каждом отсеке реформера установлены 14 главных горелок.
В главных горелках сжигается предварительно нагретый топливный газ в нагретом воздухе, во вспомогательных — холодный природный газ в холодном воздухе. Главные горелки, расположенные симметрично относительно реакционных труб, обеспечивают необходимый их нагрев по всей высоте за счет радиационного теплообмена. Вспомогательные горелки используются для нагрева реформера в период запуска, а также для поддержания температуры во время кратких остановок (холостой ход).
Продукты сжигания топлива отводятся из рабочего пространства реформера в два коллектора дымового газа, расположенные вдоль его продольных стен, и подаются в рекуператор для утилизации физического тепла.
Рекуператор Система рекуперации тепла состоит из двух параллельных линий (блоков), каждая из которых соединена с одним из двух коллекторов дымовых газов реформера.
Каждый блок представляет собой стальной футерованный корпус с трубными секциями. По ходу движения дымовых газов в каждом блоке рекуператора расположены:
нагреватель воздуха для главных горелок с преимущественно радиационной теплопередачей (воздух нагревается до 650 оС);
нагреватель питательного газа до температуры 560 оС;
нагреватель технологического газа перед десульфурацией до температуры 370 оС;
нагреватель природного газа до температуры 350 оС;
нагреватель топливного газа до температуры 290 оС;
нагреватель предварительного нагрева до примерно 270 оС холодного воздуха от главной воздуходувки.
Компрессоры, воздуходувки и вентилятор Для компрессии технологического газа, используемого в оборотном цикле, применяются две последовательно расположенные центробежные машины (1-й и 2-й ступени), которые повышают давление газа с 0,28 бар изб. до 1,19 бар изб. после 1-й ступени и до 2,2 бар изб. после 2-й ступени. Тем самым, обеспечивается непрерывный поток технологических газов по замкнутому контуру, включающему шахтную печь, скруббер колошникового газа и реформер.
Каждый компрессор рассчитан на пропускную способность 232 тыс. нм3/ч технологического газа, но может работать автономно при пониженной производительности печи.
Подача воздуха горения на главные горелки реформера (через две секции рекуператора) обеспечивается главной воздуходувкой радиально-центробежного типа с максимальной производительностью 264 тыс. нм3/ч. Такого же типа воздуходувка (максимальная производительность 45 тыс. нм3/ч) используется для подачи воздуха горения на вспомогательные горелки. Для эжектирования дымовых газов используется вентилятор центробежного типа производительностью 435 тыс. нм3/ч.
1.4 Технология восстановления железа в процессе ХИЛ III
Технологическая схема ГБЖ предусматривает подачу в цех окисленных окатышей, их грохочение с выделением мелочи. После грохочения на окисленные окатыши наносят защитное покрытие (бентонит). Затем окисленные окатыши ссыпаются в шахтную печь, где происходит их восстановление.
На выходе металлизованные окатыши брикетируются, охлаждаются и поступают на грохот, где разделяются на готовые продукты (брикеты), чипсы мелочь.
В процессе ХИЛ III используется непрерывный поток восстановительных газов для химического удаления кислорода из руды. Восстановительный газ Н2 и СО образуется в реформере и вводятся в шахтную печь при регулируемой концентрации и температуре. Газ двигается противотоком вверх на встречу окисленным окатышам.
Восстановительный газ нагревают восстанавливают и науглероживают окатыши до заданного состава. В зоне восстановления происходят следующие реакции:
Fe2O3 + 3H2 = Fe + 3H2O
Fe2O3 + 3CO = 2Fe + 3CO2
Восстановительный газ проходит в обратном направлении к потоку оксидов. При перемещении газы CO и H2 образуется постепенно в CO2 и водяной пар. Пока загружаемый материал восстанавливается до металлического железа, скорость, при которой происходят данные реакции, определяет время пребывания, необходимое для металлизованного продукта (4−6 часов).
Достигается степень металлизации 92%, отходящий восстановительный газ (колошниковый) отводится из колошника печи с температурой 350−450 ОC. Колошниковый газ идёт на скруббер где он охлаждается и очищается от воды и пыли. До подачи в реформер.
Материал загружается горячим в брикет пресс, брикетируются и охлаждаются для предотвращения вторичного окисления. Затем отправляют на склад готовой продукции.
1.5 Технология получения восстановительного газа в процессе ХИЛ III
Колошниковый газ, покидающий шахтную печь с температурой 300−400оC и давлением 0,1, подвергается очистке от пыли и охлаждается в скруббере и делится на 2 потока:
1) основной поток технологического газа, который используется для конверсии природного газа в реформере, охлаждается до 60 C
2) топливный газ, который после смешивания с небольшим количеством природного газа 3%, идет на отопление горелок в реформере. Этот поток охлаждается до 42оC, в них газ охлаждается меньше для сохранения в нем повышенного количества паров воды, которые используются в качестве конвертирующего агента при конверсии природного газа после последующих сжатий в компрессорах.
Этот газ нагревается в рекуператоре до 370Cпосле чего подвергается отчистки от соединений с помощью оксидов цинка и смешиваются с природным газом образуя питательный газ после нагрева в рекуператоре до 570C питательный газ поступает в трубы реформера где подвергается конверсии в присутствии цинкового катализатора происходит углекислотная конверсия природным газом и на выходе имеет температуру 950C и давление 0,4.
После добавления конвертируемого газа, необходимое количество газа в рекуператоре нагревается до 350оC. Этот газ в качестве восстановительного при температуре 880−900C и давлением 0,35 вдувается в шахтную печь.
В печи газ, проходя через слой опускающихся окатышей, восстанавливает их с достижением гарантируемой степенью металлизации до 92−94%.
Восстановительный газ, используемый в печи прямого восстановления Midrex образуется при рециркуляции части колошникового газа, отводимого из выходной трубы печи. Данный газ очищается в скруббере колошникового газа и затем сжимается, смешивается (с природным газом) и проходит через каталитические трубы. Данные трубы нагреваются в печи с огнеупорной футеровкой, называемой реформером. Процессы восстановления, которые используют природный газ, CO и H2, необходимые для восстановления, происходят при взаимодействии реформирующего природного газа с водяным паром и/или CO2 при повышенных температурах. Природным газом является, как правило, CH4. Ниже приведены основные реакции конверсии, для каждой из которых требуется значительное количество тепла, и каждая оканчивается с увеличением объема:
CH4 + H2O > CO + 3H2
CH4 + CO2 > 2CO + 2H2
Из соображений равновесия протекания в указанном направлении вышеуказанные реакции не должны быть завершены. Там всегда должен быть некоторый избыток H2O в смеси для реформинга во избежание проблем с отложением углерода на трубах реформера. В результате чего в горячем реформированном газе остается H2O и CO2. Более эффективный реформинг может быть достигнут при содержании в горячем реформированном газе CO и H2 около 95,0% плюс CO2 и H2O 5.0% .
Каталитический реформинг (конверсия) природного газа происходит при использовании никелевого катализатора при температуре в пределах от около 900 °C — 1000 °C. В то время как газ поднимается по трубе, он нагревается, и, таким образом, катализатор ускоряет реакции, в результате которых получается восстановительный газ. Реакции конверсии вызывают приблизительно 30% увеличения в объеме газа. После прохождения через зону восстановления, образовавшийся избыточный газ смешивается с природным газом и используется в качестве топлива в горелках реформера.
Реформер нагревается приблизительно до 1100 °C с помощью горелок в поде реформера. Горелки, расположенные в поде реформера, обогревают трубы реформера, и газ нагревается, когда поднимается вверх по заполненным катализатором реакционным трубам. Горелки спроектированы так, чтобы сохранить относительно постоянные температуры реформера даже в режиме холостого хода, а также предотвратить повреждение оборудования, вызванное тепловыми нагрузками из-за циклического воздействия температуры. Кроме того, высокие температуры, поддерживаемые в реформере, предотвращают отложение углерода внутри реакционных труб.
Основные горелки обеспечивают тепло для питающего газа, когда тот проходит через реакционные трубы, благодаря этому могут происходить эндотермические реакции конверсии. Воздух к основным горелкам подается подогретым из системы рекуперации тепла.
Вспомогательные горелки используются для нагрева до температуры холостого хода и поддержания температуры реформера на холостом ходу. Воздух на вспомогательные горелки не подогревается.
Дымовой газ от горелок удаляется сквозь отводы дымового газа, расположенные наверху каждого отсека. Отводы соединяются с газоходами на каждой стороне реформера. Большая часть дымового газа используется в системе рекуперации тепла для подогрева воздуха для горения, питающего газа, технологического газа, природного газа и колошникового топливного газа. Часть дымового газа удаляется через отвод уплотнительного газа, расположенный на торцевой стенке реформера, и используется как инертный газ для всей установки.
Восстановительный газ на входе в шахтную печь имеет следующие параметры:
Таблица 1 — Состав восстановительного газа [%]
Химический состав, % | СО | СО2 | Н2 | Н2О | СН4 | N2 | С3Н8 | С4Н10 | SO2, ppmv | |
33,29 | 2,29 | 53,28 | 5,52 | 4,28 | 1,24 | 0,09 | 0,02 | |||
расход номинальный, 295 705 нм3/час расход максимальный, 345 294 нм3/час средний расход, 1600 нм3/т продукта температура номинальная, 881 °C
температура максимальная, 920 °C
давление номинальное, 1,676 бар изб.
давление максимальное, 2,050 бар изб.
2. Расчетная часть
2.1 Газораспределение в шахтной печи металлизации
Все потери напора в столбе шихты шахтной печи можно разделить на две группы:
Потери тепла на трение при движении газа через слой сыпучих материалов.
Потери напора на местные сопротивления.
Потери напора на трение в слое окатышей предполагают равномерное восходящее движение газового потока, без изменения его направления относительно вертикальной оси шахтной печи металлизации.
Основные виды местных потерь напора можно условно разделить на следующие группы:
потери, связанные с изменением сечения потока (или его средней части). К ним относятся случаи внезапного расширения, сужения, а так же постепенного расширения и сужения потока;
потери, вызванные изменением направления потока (различного рода повороты);
потери, связанные с отделением одной части потока от другой или слиянием двух потоков в один общий.
Все эти виды местных потерь имеются в шахтной печи. Прежде всего, возникает внезапное расширение потока дутья при выходе его из фурм. Эта форма местного сопротивления известна, но обычно связывается с общим значением коэффициента сопротивления в формуле потерь давления по высоте печи. Следуя по направлению газового потока вверх, требуется учитывать постепенное расширение потока в заплечиках, а затем постепенное сужение газового потока в шахтной печи. Влияние постепенного расширения и сужения газового потока можно оценить соотношением площади поперечного сечения меняющихся размеров заплечиков и шахты.
Отмеченные виды местного сопротивления не исчерпывают особенностей движения газового потока в шахтной печи металлизации.
В шахте печи вследствие образования слоев различных материалов возникают местные сопротивления, связанные с изменением направления потока. Здесь же происходит отделение одной части потока от другой, а затем слияние нескольких потоков в общий.
Таблица 2 — Параметры окатышей
сi, мм | +16 | +12,5 | +11,2 | +8 | +5 | — 5 | |
qi,% | 1,5 | 21,5 | 25,5 | 49,1 | 2,3 | 0,3 | |
Насыпная или кажущаяся плотность сн=2,18 т/м3
Плотность дисперсной фазы сд=3900 кг/м3
Плотность сплошной фазы со.с=0,315 кг/м3
Динамический коэффициент вязкости сс=8,42*10-6 Па*с Объемный расход сплошной фазы Vс=240 000 м3/ч Количество фурм n=122
Давление на уровне фурм Ру.ф=5атм Температура восстановительного газа Т=930 оС Плотность сплошной фазы в условиях печи:
(1)
Динамический коэффициент вязкости при Т=1193 К (коэффициент с=73)
(2)
Объемный расход сплошной фазы в условиях печи:
(3)
Порозность слоя:
(4)
Площадь сечения шахты на уровне фурмы:
(5)
Площадь свободного пространства в сечении шахты на уровне фурм:
(6)
Скорость движения сплошной фазы (скорость фильтрации):
(7)
Эквивалентный диаметр окатышей:
(8)
Для расчета потерь давления в металлургической практике при анализе гидродинамики плотного слоя обычно используют формулу Эргана:
(9)
которая учитывает наличие инерционных сил в движущемся потоке (второе слагаемое в правой части).
(10)
Высота слоя окатышей от уровня фурм составляет 7,2 м.
(11)
2.2 Расчет баланса твердых веществ в процессе металлизации
Химический состав железорудного материала.
Таблица 3 — Химический состав окисленных окатышей (% по массе)
Fе | Fe2О3 | FeO | SiO2 | Al203 | CaO | MgO | MnO | Р2О5 | S | |
66,2 | 95.98 | 0.52 | 3.1 | 0.07 | 0.2 | 0.06 | 0.04 | 0.02 | 0.01 | |
Степень металлизации h=93%
Определяем состав металлизованых окатышей.
Расчет ведем на 100 кг окисленных окатышей.
При переработке 100 кг окисленных окатышей образуется металлического железа:
Fe*hмет=Feмет (12)
66,2*0,93=61,56
принято допущение об отсутствии трехвалентного железа:
(Fe*Feмет)*72/56
(66,2−61,56)*72/56=5,98 кг Масса других элементов составляет:
3,1+0,07+0,2+0,06+0,04+0,02+0,01=4,83 кг Масса металлизованых окатышей:
61,56+5,98+4,83=72,38 кг расход окисленых окатышей получаем
g=100/72,38=1,38кг/кг
Для производства 100 кг металлизованного продукта, необходимо 138 кг окисленых окатышей.
Определяем состав металлизованного сырья:
Feмет=61,56/0,7238=85,05%
SiO2=3,1/0,7238=4,28%
Al2O3=0,07/0,7238=0,09%
CaO=0,2/0,7238=0,27%
MgO=0,06/0,7238=0,08%
MnO=0,04/0,7238=0,05%
P2O5=0,02/0,7238=0,02%
S=0,01/0,7238=0,01%
Сумма всех компонентов кроме железа:
4,28+0,07+0,27+0,08+0,05+0,02+0,01=4,8%
FeO=100-(85,05+4,8)=10,15%
Fe=FeO+Feмет=85,05+10,15=95,2%
Таблица 4 — Состав металлизованных окатышей, %
Fе | Feмет | FeO | SiO2 | Al203 | CaO | MgO | MnO | Р2О5 | S | |
95,2 | 85,05 | 10,15 | 4,28 | 0,07 | 0,27 | 0,08 | 0,05 | 0,02 | 0,01 | |
2.3 Определение расхода восстановительного газа
Таблица 5 — Состав восстановительного газа, (% по объему)
СН4 | СО | СО2 | Н2 | O2 | N2 | |
2,6 | 16,4 | 6,7 | 73,5 | 0,6 | 0,2 | |
Степень использования восстановительной способности газа hг. Принимаем hСО = hН2 = hг, колеблется чаще всего в интервале 0,3 — 0,4. В расчете принято hг = 0,35.
Температура колошникового газа tк.г изменяется в пределах 200 — 400 оС. Задаемся tк.г = 300 оС. Температура восстановительного газа tв.г зависит от условий процесса и изменяется от 700 до 1000 оС.
В расчете принято tв.г = 800 оС. Теплоемкость компонентов восстановительного и колошникового газов приведена в табл. 2.4.
Определение расхода восстановительного газа Расчет ведется на 100 кг металлизованных окатышей.
Количество газифицируемого кислорода шихты При проведении процесса металлизации в шахтной печи в газовую фазу переходит кислород оксидов железа. Ввиду крайне незначительного количества примесей восстановлением других элементов пренебрегаем.
; (13)
где Fe2o3ок.ок., FeOок.ок. — содержание соответствующих оксидов в окисленных окатышах в %;
FeOм.о. — содержание FeO в металлизованных окатышах в %.
g — расход окисленных окатышей на единицу металлизованного сырья в кг/кг.
кг;
; (14)
где VОш — объем кислорода шихты в нм3;
МОш — масса кислорода шихты в кг;
М — молярная масса кислорода.
нм3.
Количество газов-восстановителей
В качестве восстановителей используют смесь СО и Н2. При восстановлении одного объема кислорода требуется для отнятия двух объемов СО или Н2. С учетом степени использования восстановительной способности газа:
; (15)
нм3.
Расход восстановительного газа:
; (16)
где СО и Н2 — содержание соответствующих компонентов в восстановителном газе в %.
нм3.
Объем и масса компонентов восстановительного газа представлены в таблице
VCO = 2,55 ?0,164= 0,418 нм3; МСО = (0,418 ? 28) / 22,4 = 0,522 кг ;
VCO2 = 2,55 ? 0,067 = 0,171 нм3; МСО2 = (0,171 ? 44) / 22,4 = 0,335 кг ;
VН2 = 2,55 ? 0,735= 1,87 нм3; МН2 = (1,87 ? 2) / 22,4 = 0,167 кг ;
VН2О = 2,55 ? 0,006 = 0,0153 нм3; МН2О = (0,0153 ? 18) / 22,4 = 0,012 кг;
VN2 = 2,55 ? 0,002 = 0,0051нм3; МN2 = (0,0051? 28) / 22,4 = 0,006 кг ;
VCН4 = 2,55 ? 0,026 = 0,0663нм3; МСН4 = (0,0663? 16) / 22,4 = 0,047 кг.
Результаты заносим в таблицу 6
Таблица 6 — Состав восстановительного газа [% (объёмн.)/нм3/кг]
Компоненты | СО | СО2 | Н2 | Н2О | N2 | СН4 | ||
% | 16,4 | 6,7 | 73,5 | 0,6 | 0,2 | 2,6 | ||
нм3 | 0,418 | 0,171 | 1,87 | 0153 | 0051 | 0,0663 | 2,54 | |
кг | 0,522 | 0,335 | 0,167 | 0,012 | 0,006 | 0,047 | 1,09 | |
2.4 Расчет состава колошникового газа
Количество водорода, переходящего в колошниковый газ:
VН2к.г = VН2в.г ? (1 — hг); (17)
VН2к.г = 1,87* (1−0,35)=1,21 нм3 ;
МН2к.г = VН2к.г ? М / 22,4; (18)
МН2к.г = 1,21? 2 / 22,4 = 0,108 кг.
Израсходовано водорода на восстановление и перешло в H2О:
VН2вос = VН2в.г — VН2к.г; (19)
VН2вос = 1,87 — 1,21 = 0,66нм3.
Количество водяных паров в колошниковом газе:
VН2Ок.г = VН2Ов.г + VН2вос; (20)
VН2Ок.г = 0,0153 +0,66 = 0,675 нм3;
МН2Ок.г = 0,675 ? 18 / 22,4 = 0,542 кг.
Объем кислорода, отнятого от оксидов железа водородом:
VОш Н2 = 0,5 ? VН2вос; (21)
VОш Н2= 0,5 ? 0,66 = 0,33 нм3.
Объем кислорода, отнятого от оксидов железа оксидом углерода:
VОш СО = VОш — VОш Н2; (22)
VОш СО = 0,402 — 0,33 = 0,072нм3.
Объем оксида углерода, израсходованного на восстановление:
VСОвос = 2 ? VОш СО; (23)
VСОвос = 2 ? 0,072 = 0,144 нм3.
Количество оксида углерода, переходящего в колошниковый газ:
VСОк.г = VСОв.г — VСОвос; (24)
VСОк.г = 0,418- 0,144 = 0,274 нм3 ;
МСОк.г = 0,274 ? 28 / 22,4 = 0,342 кг.
Количество диоксида углерода, переходящего в колошниковый газ:
VСО2к.г = VСО2в.г + VСОвос; (25)
VСО2к.г = 0,171 + 0,144 = 0,315 нм3 ;
МСО2к.г = 0,315 ? 44 / 22,4 = 0,618 кг.
Количество азота в колошниковом газе:
VN2к.г = VN2в.г = 0,0051 нм3; (26)
МN2к.г = (0,0051? 28) / 22,4 = 0,006 кг Количество метана в колошниковом газе:
VСН4к.г = VСН4в.г = 0,0663нм3; (27)
МСН4к.г = (0,0663? 16) / 22,4 = 0,047 кг Объем и масса компонентов колошникового газа представлены в таблице 7.
Таблица 7 — Состав колошникового газа [% (объёмн.)/нм3/кг]
Компоненты | СО | СО2 | Н2 | Н2О | N2 | СН4 | ||
% | 10,7 | 12,34 | 46,9 | 27,26 | 0,2 | 2,6 | ||
нм3 | 0,247 | 0,315 | 1,21 | 0,675 | 0,0051 | 0,0663 | 2,54 | |
кг | 0,342 | 0,618 | 0,108 | 0,542 | 0,006 | 0,047 | 1,66 | |
Проверка степени использования восстановительной способности газа
; (28)
Составляем материальный баланс процесса.
Таблица 8 -Материальный баланс процесса
Поступило в печь, кг | Получено в печи, кг | |||
Окисленные окатыши | 1,38 | Металлизованные окатыши | ||
Восстановительный газ | 1,09 | Колошниковый газ | 1,66 | |
Итого | 2,47 | Итого | 2,66 | |
Невязка
2.5 Расчет времени пребывания окатышей в конусной части реактора
Насыпная плотность окатышей: снас = 2,18 т/м3 =2180 кг/м3
Расход металлизованных окатышей: сB= 117т/ч = 1950 кг/мин Расход окисленных окатышей:
VB=kVB (29)
где k — коэффициент пересчета
k (30)
где Feоб.мет. — количество железа в металлизованных окатышах;
Feоб.ок. — количество железа в окисленных окатышах.
Расход окисленных окатышей:
VB=кг/мин (31)
Объем окатышей:
V=рH (Dв2+Dн2+DвDн)/12,м3 (32)
где H — высота слоя окатышей Масса окатышей:
m=V?снас (33)
Время пребывания окатышей в зоне:
ф=m/VB, мин (34)
Таблица 9 — Параметры печи
Зона | Dв, м | Dн, м | Н, м | |
7,7 | 5,65 | 2,85 | ||
5,65 | 4,65 | 2,15 | ||
4,65 | 3,3 | 2,9 | ||
3,3 | 2,9 | |||
0,3 | ||||
0,862 | 2,95 | |||
V = 3,14?2,85?(7,72+5,652+7,7?5,65)/12 = 104,47 м3
m = 2180?104,47 = 227 744,6 кг ф =
V = 3,14?2,15?(5,652+4,652+5,65?4,65)/12 = 44,9 м3
m = 2180?44,9 = 97 882 кг ф =
V = 3,14?2,9?(4,652+3,32+4,65?3,3)/12 = 36,32 м3
m = 2180?36,32 = 79 177,6 кг ф =
V = 3,14?2,9?(3,32+22+3,3?2)/12 =16,31 м3
m = 2180?16,31 = 35 555,8 кг ф =
V = 3,14?0,3?(22+22+2?2)/12 = 0,942 м3
m = 2180?0,942 = 2053,56 кг ф =
V = 3,14?2,95?(22+0,8622+2?0,862)/12 = 4,99 м3
m = 2180?4,99 = 10 878,2 кг ф =
Общее время пребывания:
83,4+35,85+29,01+13,02+0,75+3,98 = 166,01 мин = 2,8ч
2.6 Расчет материального баланса процесса металлизации в процессе ХИЛ III
При расчете материального баланса по ЦГБЖ, масса окатышей, находящихся в печи, на начало и на конец отсчетного периода принимается равной, так как отсутствует полная выгрузка продуктов из печи на начало и конец отсчетного периода.
Расчет баланса составляется по массе окатышей, поступивших в ЦГБЖ с ФОК за вычетом отсева окатышей который является товарной продукции.
Таблица 10 — Исходные данные для расчета
Наименование продукта | Сухой вес, т | Качественные показатели | |||||
Feобщ,% | FeO/Feмет | M,% | С,% | Р, т/м3 | |||
Окатыши железорудные офлюс | 66,2 | 0,52 | |||||
Отсев железорудных окатышей | 66,2 | ||||||
Цемент | |||||||
Возврат реметов в печь | 88,83 | 79,81 | 89,85 | 1,16 | |||
Брикеты жел руды: | 95,20 | 85,05 | 1,33 | 4,89 | |||
Высшего сорта | 95,3 | 85,55 | 93,13 | 1,34 | 4,91 | ||
Первого сорта | 95,01 | 84,89 | 92,63 | 1,26 | 4,78 | ||
Мелочь брикетов жел руды | 91,01 | 86,59 | 95,14 | 1,35 | |||
Шлам железорудный | 64,29 | 25,69 | 39,96 | 1,88 | |||
Уравнение:
О-В+П+С+Рвозв+ЗБнм+ОРнм=Б+М+ОБ+Р+Ш+ПВ+Qт+ЗБкм+Оркм, где О-масса окатышей В-масса отсева окатышей П-масса материалла покрытия окатышей С-масса углерода Рвозв-масса реметов, возвращеных в печь Б-масса брикетов М-масса мелочи ОБ-масса отсева брикетов Р-масса реметоа Ш-масса шлама ПВ-уменьшение количества кислорода, связанного с железом
Qт-масса технологических потерь ЗБнм, ЗБкм — остатки в бункерах суточного запаса на начало и конец отчетного периода Орнм, Оркм — масса окатышей находящихся в печи на начало и конец отчетного периода соответственно.
Уравнение технологического баланса:
Feo-Feв+Feвозв=Feб+Feм+Feоб+Fep+Feш+Qт, где Feo Feв Feвозв Feб Feм Feоб Fep Feш Qт — масса полезного компонента (железа) в окатышах, отсеве, реметах, возвращенных в печь, брикетах, мелочи, отсеве брикетов, реметых, шламе и технологических потерях Уменьшение веса при восстановлении за счет уменьшения количества кислорода, связанного с железом, определяется по разности между массой кислорода в исходном материале и массой остаточного кислорода в металлизованной продукции:
ПВ=О2ок-О2ост
где О2ок -масса кислорода, связанного с железом в окатышах О2ост -масса остаточного кислорода Масса кислорода поступившего в печь определяется по формуле:
О2ок = (35)
где Feокобщ, Feвозвобщ — массовая доля железа общего в окатышах, реметах, возвращенных в печь соответственно, %
Feвозвмет — массовая доля железа металлического в реметах, возвращенных в печь, %
FeO — массовая доля оксида в окатышах, %
О2ок =
Масса остаточного кислорода, связанного с железом, в металлизованной продукции, определяется по формул:
(36)
Уменьшение веса при восстановлении за счет уменьшения количества кислорода, связанного с железом, определяется по формуле:
ПВ=О2ок-О2ост (37)
ПВ=47 211,59−1666,06=45 544,53 т Масса углерода, поступившего в металлизованную продукцию из восстановительного газа, определяется путем произведения масс металлизованной продукции в сухом весе на соответствующую массовую долю углерода:
С= (38)
где Сб, См, Соб, Срем, Сш — массовая доля углерода;
С=
Масса технологических потерь в процессе производства металлизованной продукции определяется как разность между массой поступивших в печь исходных материалов и массой продуктов технологического процесса с учетом потерь веса окатышей при восстановлении:
Qт= (39)
Qт=171 100−5000+1000+0+395,65+600+1605,40−106 790−11 900;0−0-1300;
— 44 704,94−1000−0=4006,11 т В процентном соотношении:
(40)
где м — общая масса поступившего или полученного материалла, т;
определяется на основании товарного баланса:
м=О-В+П+С+Рвозв +ЗБнм+ОРнм=Б+М+ОБ+Р+Ш+ПВ+Qт+ЗБкм+ОРкм
м=171 100−5000+395,65+600+1605,40+1000= 6 790+11900+0+0+1300+44 704,94+4006,11+1000+169 701,05=169 701,05
По результатам расчета составляем материальный баланс, данные заносим в таблицу 11.
Таблица 11 — Материальный баланс по ЦГБЖ-1
№ | Наименование | Сухой вес | Качественные показатели, % | ||||||
Feобщ | FeO/Feмет | М | С | с, т/м3 | |||||
Приход | |||||||||
Окатыши железорудные офлюсованные | 67,00 | 0,52 | |||||||
1.1 | Отсев Железорудных окатышей | 67,00 | |||||||
Поступило в производство окатышей | 67,00 | ||||||||
Цемент | 395,65 | ||||||||
Возврат реметов в печь | 88,83 | 79,81 | 89,85 | 1,16 | |||||
Прирост массы метпродукции за счет углерода | 1605,4 | ||||||||
ИТОГО | 169 701,05 | 66,87 | 66,87 | ||||||
Расход | |||||||||
Брикеты железной руды | 95,17 | 86,73 | 1,33 | 4,89 | |||||
Мелочь брикетов железной руды | 91,01 | 86,59 | 95,14 | 1,35 | |||||
Шлам железорудный | 64,29 | 25,69 | 39,96 | 1,88 | |||||
Итого выпущено металлизованного продукта | 90,67 | 85,81 | 94,64 | 1,34 | |||||
Масса удаленного кислорода при восстановлении | 44 704,94 | ||||||||
Технологические потери полезного компонента | 4006,11 | 84,72 | |||||||
Технологические потери полезного компонента | 2,3% | ||||||||
ИТОГО | 169 701,05 | ||||||||
3. Организационно технологическая часть
3.1 Организационно управленческая характеристика Лебединского горно-обогатительного комбината
ОАО «Лебединский горно-обогатительный комбинат» (ЛГОК) входит в состав холдинга «МЕТАЛЛОИНВЕСТ» и является крупнейшим в России предприятием по добыче и обогащению железной руды и производству высококачественного сырья для черной металлургии. Сырьевая база комбината — уникальные по масштабам и качеству запасы железистых кварцитов Лебединского месторождения Курской магнитной аномалии. Прогнозные запасы руды Лебединского ГОКа составляют более 6 млрд. тонн, что гарантирует обеспеченность комбината высококачественным сырьем для бесперебойной работы более чем на 250 лет.
Сведения о ценных бумагах
Компания ОАО «ХК «МЕТАЛЛОИНВЕСТ»
Учтавный капитал 3 984 950 000 руб.
Количество акций 79 699 000 000 шт.
Тип акций Обыкновенные именные бездокументарные Лебединский горно-обогатительный комбинат — единственный в России производитель брикетов железной руды (горячебрикетированного железа). На долю предприятия приходится 21% внутреннего рынка ЖРС.
История
1967 год — основание комбината, начало горно-капитальных работ.
1971 год — введен в эксплуатацию Лебединский кварцитный карьер.
1972 год — введена в эксплуатацию 1-я очередь горно-обогатительного комбината, получена первая тонна железорудного концентрата.
1975 год — вступила в строй первая очередь фабрики окомкования, получены первые окатыши.
1982 год — введена в эксплуатацию фабрика дообогащения концентрата, получен первый концентрат с повышенным содержанием железа (70%).
1995 год — начато строительство первой очереди цеха горячебрикетированного железа (ЦГБЖ-1), получена первая продукция.
2001 год — с вводом в строй цеха горячебрикетированного железа и его выходом на проектную мощность ОАО «Лебединский ГОК» приобрел статус горно-металлургического предприятия.
2003 год — добыта миллиардная тонна железистых кварцитов, внедрена единая автоматизированная информационная система управления производством.
2005 год — Лебединский ГОК удостоен звания лауреата в конкурсе соискателей национальной экологической премии «ЭкоМир» и награжден Дипломом II степени за проект «Выпуск экологически чистой продукции брикетов».
Лебединский ГОК стал первым предприятием отрасли в России и в Европе, прошедшим процедуру сертификации по международному стандарту ISO 14 001:2004.
2006 год — полномочия единоличного исполнительного органа ОАО «Лебединский ГОК» переданы управляющей компании ООО «УК МЕТАЛЛОИНВЕСТ».
2007 год — январь — Лебединский ГОК подтвердил членство в Международной Ассоциации производителей горячебрикетированного железа (HBIA, Pittsburgh, USA);
— март сертификационным аудитом Британского
Института стандартов подтверждено соответствие Системы менеджмента качества Лебединского ГОКа требованиям международного стандарта ISO 9001:2000;
— октябрь — закончено строительство второй очереди цеха горячебрикетированного железа (ЦГБЖ-2) производительностью 1,4 млн. тонн брикетов в год. Уже в 2008 году вывод позволит комбинату довести объем выпуска металлизованных брикетов до 2,4 млн тонн;
— ноябрь — произведена 500-миллионная тонна железорудного концентрата; завершено строительство пятой технологической секции дообогащения обогатительной фабрики. В результате ввода секции в эксплуатацию производство высококачественного концентрата увеличится на полтора миллиона тонн в год.
2008 год:
— январь сертификационным аудитом Британского Института стандартов подтверждено соответствие Системы управления охраной труда и промышленной безопасности Лебединского ГОКа требованиям международного стандарта OHSAS 18 001;
— апрель начата реализация масштабного проекта внешнего электроснабжения.
2009 год:
— ноябрь пройден ресертификационный аудит системы менеджмента качества на соответствие требованиям международного стандарта ISO 9001:2008 и выпущена 100 миллионная тонна концентрата;
— декабрь пройден ресертификационный аудит системы менеджмента качества на соответствие требованиям международного стандарта ISO 9001:2008.
Органами управления Общества являются:
Общее собрание;
Единоличный исполнительный орган — Генеральный директор Общества (далее — Генеральный директор). Органом контроля за финансово-хозяйствен-ной деятельностью Общества является Ревизионная комиссия Общества (далее Ревизионная комиссия). Продукция Лебединского ГОКа:
— рядовой железорудный концентрат.
Массовая доля железа — около 68%.
Нетоксичный, невоспламеняющийся, невзрывоопасный, с низким содержанием примесей серы, фосфора и оксида титана;
— дообогащенный железорудный концентрат.
Массовая доля железа — около 70%;
Производится путем дообогащения рядового концентрата;
— сушеный железорудный концентрат
Массовая доля железа — около 68%;
Благодаря низкому содержанию влаги, этот концентрат не смерзается при низких температурах, а потому пригоден для производства агломерата в зимнее время;
— железорудные неофлюсованные окатыши.
— Массовая доля железа — 66%;
— офлюсованные окатыши
Массовая доля железа — 66,5%;
Применяются в производстве ГБЖ и металлизованных окатышей;
— ГБЖ
Массовая доля железа — около 90%;
Степень металлизации порядка 93,7%;
Низкое содержание серы и фосфора;
— отсев железорудных окатышей и мелочь горячебрикетрованного железа
Cубпродукты ЛГОКа, используемые в производстве агломерата.
Таблица 12 — Объем выпуска основных видов продукции на ЛГОКе, [тыс. тонн]
Виды продукции | 2008 г | 2009 г | 2010 г | 1 кв. 2011 г | 2 кв. 2011 г | |
Первичная железная руда | ||||||
Рядовой железорудный концентрат | ||||||
5400 Дообогащенный железорудный концентрат | ||||||
Сушеный железорудный концентрат | ||||||
Неофлюсованные окатыши | ||||||
Офлюсованные окатыши | ||||||
ГБЖ | ||||||
Отсев железорудных окатышей и мелочь ГБЖ | ||||||
Среди основных потребителей железной продукции комбината на внешнем рынке — предприятия Украины, Польши, Венгрии, Чехии, Китая, Южной Кореи.
В последние годы Лебединский ГОК существенно укрепил свои позиции на принципиально новых рынках Восточной и Западной Европы, а также Юго-Восточной Азии без потери традиционных рынков сбыта.
Лебединский горно-обогатительный комбинат является акционерным обществом открытого типа. Управление предприятием осуществляется централизованно. Общее собрание является главным органом управления предприятием. Ему подотчетны:
— председатель правления — генеральный директор;
— заместитель генерального директора по социальным вопросам;
— заместитель генерального директора — главный экономист;
— заместитель генерального директора по быту;
— главный инженер;
— заместитель генерального директора по коммерции.
Главному экономисту подотчетны:
— директор по труду и кадрам, который руководит отделом труда и зарплаты и отделом кадров и ТО;
— финансовый директор — главный бухгалтер, в ведении которого находятся финансовый отдел, отдел налогообложения и расчетов с бюджетом, отдел расчетно-финансовых операций, отдел учета финансирования и учета затрат, отдел ревизий, методологии и автоматизации, отдел учета затрат на производство и сводной отчетности;
— экономическое управление, в ведении которого находятся отдел анализа и прогнозирования, плановый отдел, отдел планирования строительства и ремонта, отдел недвижимости.
Главному инженеру подотчетны:
— технический директор и директор по производству;
— отдел планирования договоров и балансов;
— транспортный отдел; ЖДЦ и АТЦ;
— начальник УВС, отвечающий за отдел экспорта, отдел импорта, экономический отдел.
3.2 Организационно-управленческая характеристика цеха ГБЖ1
Организационная схема управления ЦГБЖ-1 представлена в приложении Б. Цех горячебрикетированного железа является структурным подразделением ОАО ЛГОКа и связан в технологической цепочке со следующими цехами
— лаборатория охраны окружающей среды;
— ОТК и ЛИ;
— управление по ремонту оборудования;
— фабрика окомкования;
— энергоуправление;
— цех хвостового хозяйства;
— цех железнодорожного транспорта.
Управление цехом осуществляется централизованно директором завода, которому подчиняется главный инженер Главному инженеру подчиняются начальник цеха металлизации и заместитель начальника по участку строительства, взаимодействующий со сторонними строительными организациями.
Начальнику цеха металлизации подчиняются:
— экономическое бюро,
— заместитель по производству, которому подчиняются:
а) транспортный участок;
б) конструктивный отдел;
в) ПТБ;
— заместитель по технологии, в ведении которого находятся:
а) основной технологический участок;
б) участок водоподготовки;
в) участок газоснабжения;
— заместитель по ремонтам, которому подчиняются:
а) участок по ремонту технологического оборудования;
б) главный механик, отвечающий за участок по ремонту механического оборудования;
в) главный энергетик, отвечающий за участок по ремонту энергетического оборудования, участок по ремонту электрооборудования, участок КИП и А.
3.3 Оценка эффективности деятельности ОАО «Лебединский ГОК»
Особенностью прошедшего года стало улучшение экономической ситуации в стране и мире. В настоящее время анализ всех факторов — не только рыночных, но и таких, которые могут оказывать косвенное влияние на рынок, показал, что объёмы производства в металлургической отрасли восстанавливаются.
Ориентация на производство продукции более высокого передела позволяет увеличивать добычу руды, при этом производство базового продукта остаётся в рамках существующих схем и объёмов отгружаемого железорудного сырья.
В 2010 году максимальная загрузка производственных мощностей Комбината произведена в соответствии со следующими принципами:
обеспечение потребностей в железорудном сырье металлургических предприятий Холдинга «МЕТАЛЛОИНВЕСТ»;
производство продукции только в тех объёмах, которые подтверждены контрактами;
поддержание производства на максимально возможном уровне с целью сохранения персонала и социальной стабильности в коллективе.
Важнейшим итогом 2010 года является рост загрузки производственных мощностей с 90% в 2009 году до 100% в 2010 году. Это один из лучших показателей в металлургической отрасли России. Каждый процент загрузки в условиях кризиса — это сотни сохранённых рабочих мест.
Таблица 13 — Динамика производственных показателей за 2008;2010 гг. [тыс. тонн]
Наименование показателей | 2008 г. | 2009 г. | 2010 г. | |
Добыча кварцитов | 47 559 | 38 614 | 47 362 | |
Объёмы производства продукции: | ||||
— концентрат железорудный | 19 732 | 16 040 | 19 829 | |
— окатыши железорудные (с отсевом окатышей) | 8 370 | 7 824 | 9 120 | |
— металлизованная продукция* | 2 259 | 2 292 | 2 360 | |
* металлизованная продукция: горячебрикетированное железо (брикеты железной руды) высшего сорта, горячебрикетированное железо (брикеты железной руды) первого сорта, горячебрикетированное железо (брикеты железной руды) класса крупности менее 25 свыше 4 мм, мелочь горячебрикетированного железа (брикетов железной руды), реметы.
Качественные показатели по всей номенклатуре произведённой железорудной продукции традиционно соответствуют техническим условиям.
Производственная программа ОАО «Лебединский ГОК» базируется на основе сбалансированности производства и отгрузки железорудного сырья.
На ближайшие годы приоритетной задачей Комбината является восстановление объёмов производства базовой продукции до докризисных уровней. При этом необходимо значительное увеличение объёмов добычи руды, вскрышных работ.
Реализация железорудной продукции
На протяжении многих лет ОАО «Лебединский ГОК» постоянно расширяет номенклатуру производимой высококачественной железорудной продукции. Инвестиционные проекты, реализованные в предыдущие годы, политика Общества, направленная на постоянное развитие, позволили предприятию, как в период экономического спада, так и в период преодоления последствий экономического кризиса, выпускать конкурентную высококачественную продукцию, отвечающую отечественным и мировым стандартам, а значит — востребованную потребителем. Особенностью прошедшего года является постепенное восстановление спроса на железорудную продукцию со стороны металлургических предприятий.
Основное направление сбытовой политики — продажа железорудной продукции в соответствии с принятыми планами производства и реализации, заключенными договорами и контрактами на продажу продукции на наиболее выгодных для Общества условиях.
Высокое качество продукции позволяет успешно конкурировать как на рынке в Российской Федерации, так и на мировом рынке.
Конкуренты Общества
Основными конкурентами Общества на внутреннем рынке являются ОАО «Стойленский ГОК», ОАО «Качканарский ГОК «Ванадий», ОАО «Карельский окатыш».
Основные конкуренты на внешнем рынке — АО «Соколовско-Сарбайское ГПО» (Казахстан), горно-обогатительные комбинаты Украины.
Конкурентными преимуществами ОАО «Лебединский ГОК» на рынке железорудного сырья являются:
качественные показатели продукции (высокое содержание железа в концентрате и небольшое содержание вредных примесей);
широкий ассортимент предлагаемых продуктов с различными металлургическими свойствами в зависимости от потребности потребителя;
максимально удобное географическое положение (возможность отгрузки продукции предприятиям в Центральном и Уральском регионах, в Восточную Европу и СНГ);
безупречная деловая репутация и устойчивые партнёрские отношения с потребителями.
Данные преимущества обуславливают устойчивые позиции Комбината на рынках железорудной продукции и снижают риски возникновения сбытовых проблем при резком изменении конъюнктуры рынка.
Финансовые результаты
Мировое снижение спроса на железную руду и сталь в 2009 году привело к падению цен и доходов горно-металлургических компаний России, в том числе и ОАО «Лебединский ГОК».
В экономических условиях 2010 года Обществом получены следующие финансовые результаты деятельности:
Таблица 14- Отчёт о прибылях и убытках (динамика показателей за 2008;2010 гг.) (тыс. руб.)
Наименование показателей | 2008 г. | 2009 г. | 2010 г. | |
Выручка (нетто) от продажи товаров, продукции, работ, услуг | 54 966 935 | 28 670 459 | 61 043 830 | |
Себестоимость проданных товаров, продукции, работ, услуг | (17 340 317) | (17 010 681) | (20 193 035) | |
Валовая прибыль | 37 626 618 | 11 659 778 | 40 850 795 | |
Коммерческие расходы | (2 349 938) | (1 776 590) | (3 137 288) | |
Управленческие расходы | (1 764 639) | (1 383 741) | (1 740 189) | |
Прибыль (убыток) от продаж | 33 512 041 | 8 499 447 | 35 973 318 | |
Проценты к получению | 238 493 | 1 250 266 | 575 944 | |
Проценты к уплате | (4 732 376) | (6 709 123) | (6 667 463) | |
Доходы от участия в других организациях | ; | ; | ||
Прочие доходы | 52 323 156 | 23 082 686 | 26 171 323 | |
Прочие расходы | (62 673 482) | (25 584 776) | (27 496 703) | |
Прибыль (убыток) до налогообложения | 18 668 397 | 538 500 | 28 556 419 | |
Отложенные налоговые активы | 66 174 | (12 585) | (22 225) | |
Отложенные налоговые обязательства | (309 812) | 91 121 | (183 238) | |
Текущий налог на прибыль | (4 817 992) | (446 346) | (5 726 789) | |
Налог на прибыль прошлых лет и прочие обязательства | 5 007 | (2 370) | 6 260 | |
Чистая прибыль (убыток) отчётного периода | 13 611 774 | 168 320 | 22 630 427 | |
Выручка от продажи товаров, продукции, работ, услуг
Выручка (нетто) от продажи товаров, продукции, работ, услуг (за минусом налога на добавленную стоимость, акцизов и иных обязательных платежей) за 2010 год составляет 61 043 830 тыс. рублей, в 2,1 раза превышает аналогичный показатель прошлого года (28 670 459 тыс. рублей).
Основные факторы, оказавшие влияние на формирование показателя выручки от продажи товаров, продукции, работ, услуг:
рост цен железорудной продукции на внутреннем и внешнем рынках, увеличение объёмов производства и реализации железорудной продукции.
Выручка от продажи железорудной продукции получена на сумму 60 211 264 тыс. рублей, что составляет 98,6% общего объёма продаж товаров, продукции, работ, услуг.
Определение выручки от продажи товаров, продукции (работ, услуг) осуществляется по методу начисления, по ценам, указанным в договорах сторонами сделки.
Себестоимость проданных товаров, продукции, работ, услуг
Себестоимость проданных товаров, продукции, работ, услуг, с учётом коммерческих и управленческих расходов, за 2010 год составляет 25 070 512 тыс. рублей, превышает аналогичный показатель прошлого года на 24,3%.
Основными факторами влияния на себестоимость проданных товаров, продукции, работ, услуг являются:
увеличение объёмов производства;
рост цен и тарифов услуг естественных монополий (электроэнергия, газ, железнодорожные перевозки);
рост цен на покупные материалы, топливо, услуги сторонних организаций.
В себестоимости основную долю (30,6%) занимают затраты на энергоресурсы. Разработана программа технических мероприятий, связанных с повышением эффективности энергопотребления и снижением затрат на энергоресурсы. В результате проведения мероприятий по снижению потребления энергетических ресурсов в 2010 году получен экономический эффект в сумме 21,3 млн. рублей, в том числе:
электроэнергии — 10,32 млн. кВт*ч на сумму 17,2 млн. рублей;
тепловой энергии 6,0 тыс. Гкал на сумму 4,1 млн. рублей.
Совокупные затраты на оплату использованных в 2010 году энергетических ресурсов составили:
природного газа — 2 712 583,3 тыс. рублей,
электроэнергии — 4 715 828,6 тыс. рублей.
Таблица 15 — Фактические объёмы и стоимость потребления природного газа и электроэнергии за 2008;2010 гг.
Период | Природный газ | Электроэнергия | |||
Объём, тыс. м3 | Стоимость, тыс. руб. | Объём, тыс. кВт*ч | Стоимость, тыс. руб. | ||
2008 г. | 864 556,3 | 1 753 968,1 | 2 983 109,7 | 3 474 946,0 | |
2009 г. | 873 665, 9 | 2 017 327,2 | 2 658 486,3 | 3 450 299,0 | |
2010 г. | 923 246,0 | 2 712 583,3 | 3 092 925,9 | 4 715 828,6 | |
При увеличении объёмов потребления электроэнергии в 2010 году на 434 439,6 тыс. кВт*ч или на 16,3% по сравнению с аналогичными показателями прошлого года получено увеличение затрат на 1 265 529,6 тыс. рублей или на 36,7% в результате роста объёмов потребления и в большей степени роста цен на электроэнергию.
Себестоимость реализованной железорудной продукции — 24 209 915 тыс. рублей, что составляет 96,6% себестоимости проданных товаров, продукции, работ, услуг.
Прибыль от продаж
Прибыль от продаж продукции, работ, услуг за 2010 год составляет 35 973 318 тыс. рублей, в 4,2 раза превышает аналогичный показатель прошлого года (8 499 447 тыс. рублей).
Изменение показателя прибыли от продаж в сравнении с прошлым годом получено за счёт следующих факторов:
увеличения выручки от продажи на сумму (+) 32 373 371 тыс. рублей,
увеличения себестоимости продаж на сумму (-) 4 899 500 тыс. рублей.
Прибыль от продаж железорудной продукции — 36 001 349 тыс. рублей.
4. Экономическая часть
4.1 Расчет тарифного фонда оплаты труда цеха ГБЖ 1
Средства, направляемые на потребление, объединяют денежные и натуральные выплаты, носящие индивидуальный характер. Фонд потребления включает, кроме того, выплаты за счет фонда социальной защиты и расходов на содержание объектов здравоохранения, культуры и спорта. В состав средств, направляемых на потребление, включаются: средства фонда оплаты труда.
В состав фонда заработной платы включаются начисленные предприятием, учреждением, организацией суммы оплаты труда в денежной и натуральной формах за отработанное и неотработанное время, стимулирующие доплаты и надбавки, компенсационные выплаты, связанные с режимом работы и условиями труда, премии и единовременные поощрительные выплаты, а также выплаты на питание, жилье, топливо, носящие регулярный характер.
Включению в фонд заработной платы, в частности, подлежат:
1) Оплата за отработанное время:
— заработная плата, начисленная работникам по тарифным ставкам и окладам за отработанное время;
— заработная плата, начисленная за выполненную работу работникам по сдельным расценкам. В процентах от выручки от реализации продукции (выполнения работ и оказания услуг);
— премии и вознаграждения, (включая стоимость натуральных премий), носящие регулярный или периодический характер независимо от источников их выплаты;
— стимулирующие доплаты и надбавки к тарифным ставкам и окладам (за профессиональное мастерство, совмещение профессий и должностей,
допуск к государственной тайне и т. п.);
— ежемесячные или ежеквартальные вознаграждения (надбавки) за выслугу лет, стаж работы;
— компенсационные выплаты, связанные с режимом работы и условиями труда;
— выплаты, обусловленные районным регулированием платы труда: по районным коэффициентам за работу в пустынных, безводных местностях и в высокогорных районах, процентные надбавки к заработной плате за стаж работы в районах крайнего Севера, в приравненных к ним местностях и других районах с тяжелыми природно-климатическими условиями;
— доплаты за работу во вредных или опасных условиях на тяжелых работах;
— доплаты за работу в ночное время;
— оплата работы в выходные и праздничные дни; оплата сверхурочной работы; оплата работника за дни отдыха (отгулы), предоставленные в связи с работой сверх нормальной продолжительности рабочего времени при вахтовом методе организации работ, при суммированном учете рабочего времени и в других случаях, установленных законодательством;
— доплаты работникам, постоянно занятым на подъемных работах, за нормативное время их передвижения в шахте (руднике) от ствола к месту работы и обратно;
— оплата труда квалифицированных рабочих, руководителей, специалистов предприятий и организаций, освобожденных от основной работы и привлекаемых для подготовки, переподготовки и повышения квалификации работников;
— оплата специальных перерывов в работе;
— выплата разницы в окладах работникам, трудоустроенным из других предприятий и организаций, с сохранением в течение определенного срока размеров должностного оклада по предыдущему месту работы; выплата разницы в окладах при временном заместительстве;
— оплата труда лиц, принятых на работу по совместительству;
— оплата труда работников не списочного состава;
— оплата труда лиц, не состоящих в списочном составе работников предприятия (организации), за выполнение работ по гражданским договорам, если расчеты за выполненную работу производятся предприятием с физическими, а не юридическими лицами. При этом размер средств на оплату труда этих физических лиц определяется, исходя за сметы на выполнение работ (услуг) по этому договору и платежных документов;
— оплата услуг (гонорар) работников не списочного состава (за переводы, консультации, чтение лекций, выступление по радио и телевидению и т. д.);
2) Оплата за неотработанное время:
— оплата ежегодных и дополнительных отпусков (без денежной компенсации за неиспользованный отпуск);
— оплата дополнительно предоставленных по коллективному договору (сверх предусмотренных законодательством) отпусков работникам;
— оплата льготных часов подростков;
— оплата учебных отпусков, предоставленных работникам, обучающимся в образовательных учреждениях;
— оплата на период обучения работников, направленных на профессиональную подготовку, повышение квалификации или обучение вторым профессиям;
— оплата на период обучения работников, направленных на профессиональную подготовку, повышение квалификации или обучение вторым профессиям;
— оплата труда работников, привлекаемых к выполнению государственных или общественных обязанностей;
— оплата, сохраняемая по месту основной работы за работниками, привлекаемыми на сельскохозяйственные и другие работы;
— суммы, выплаченные за счет средств предприятия, за не проработанное время работникам, вынужденно работавшим неполное рабочее время по инициативе администрации;
— оплата работникам-донорам за дни обследования, сдачи крови;
— оплата простоев не по вине работника; оплата за время вынужденного прогула;
3) Единовременные поощрительные выплаты:
— единовременные (разовые) премии независимо от источников их выплаты;
— вознаграждение по итогам работы за год, годовое вознаграждение за выслугу лет (стаж работы);
— материальная помощь, предоставленная всем или большинству работников;
— дополнительные выплаты при предоставлении ежегодного отпуска (сверх нормальных отпускных сумм в соответствии с законодательством.);
— денежная компенсация за неиспользованный отпуск;
— стоимость бесплатно выдаваемых работникам в качестве поощрения акций или льгот по приобретению акций;
— другие единовременные поощрения, включая стоимость подарков;
4) Выплаты на питание, жилье, топливо.
В фонд потребления входят, но не включаются в состав средств, направляемых на потребление: затраты на командировочные расходы, надбавки к зарплате взамен суточных работникам, направляемым для выполнения монтажных, наладочных и строительных работ, стоимость спецодежды, спецпитания, выплаты за счет средств фонда социальной защиты, включая пособия по временной нетрудоспособности, по беременности, по уходу за ребенком, пенсии, возмещение причиненного ущерба, а также расходы за счет чистой прибыли, остающейся в распоряжении предприятия.
Всю начисленную на предприятии заработную плату можно подразделить на следующие виды:
— основная заработная плата;
— дополнительная заработная плата;
— премии, вознаграждения по итогам работы за год.
Основная заработная плата начисляется в зависимости от принятых на предприятии форм оплаты труда. Основная заработная плата согласно действующему трудовому законодательству не должна выплачиваться работникам реже, чем два раза в месяц.
Дополнительная заработная плата начисляется на основании документов, подтверждающее право работника на оплату за неотработанное время. К таким выплатам относятся:
— оплата основного, дополнительного или учебного отпуска;
— компенсация за неиспользованный отпуск;
— выплаты выходного пособия при увольнении;
— выплаты при направлении работника на курсы повышения квалификации;
— оплата времени выполнения государственных обязанностей;
— прочие выплаты согласно действующему законодательству.
Выплаты работнику дополнительной заработной платы производятся в сроки, определенные действующим законодательством.
Вознаграждение по результатам финансово-хозяйственной деятельности предприятия выплачиваются за счет прибыли, остающейся в распоряжении предприятия, за вычетом средств, направляемых на потребление. Размер вознаграждения устанавливается по нормативу, определяемому как соотношение 12-ти месячных окладов к сумме указанной прибыли за предшествующий календарный год. Периодичность выплаты вознаграждения определяется предприятием самостоятельно.
В качестве источников вознаграждения за труд на предприятии создаются фонды социальной поддержки и развития, фонд развития производства, резервный фонд. Эти фонды создаются для распределения доходов и дивидендов между работающими с целью повышения их заинтересованности.
4.2 Расчет затрат по статьям себестоимости 1 тонны металлизованных окатышей с содержанием железа 66,77%
Себестоимость — денежное выражение затрат на производство и реализацию единицы продукции. Выступает качественной характеристикой деятельности производителя, показателем конкурентоспособности. Включает в себя: затраты на сырье и материалы; оплату труда; отчисления на социальные нужды; амортизацию основных фондов; прочие расходы. Затраты делятся на прямые, т. е. непосредственно относящиеся на себестоимость конкретных видов продукции, и косвенные, связанные с производством в целом и относимые в определенной пропорции на себестоимость продукции (например административно-управленческие расходы). Состав затрат, включаемых в себестоимость, определяется нормативными актами. В России действует Постановление Правительства РФ от 5 августа 1992 г. «Об утверждении Положения о составе затрат по производству и реализации продукции (работ и услуг) и о порядке формирования финансовых результатов, учитываемых при налогообложении прибыли». В каждой отрасли имеются свои специфические особенности при калькуляции себестоимости выпускаемой продукции.
Главной деятельностью предприятия в современном секторе экономики является выпуск продукции, оказание услуг и выполнение работ. Целью всех этих мероприятий является получение прибыли. Чтобы получить максимальную прибыль, нужно оптимизировать соотношение объемов и издержки производства. Под издержками производства понимаются затраты общественного труда, связанные с производством и реализацией продукции. В некоторых странах понятия «затраты» и «издержки» трактуются по-разному, но в отечественной практике для характеристики издержек используется термин «затраты на производство».
Важным для управления затратами является их классификация. Для планирования, анализа, учета и калькулирования себестоимости существует следующая классификация затрат по элементам:
одноэлементные и комплексные (по составу);
статьи калькуляции и экономически однородные элементы (по видам);
основные и накладные (по назначению);
постоянные и временные (по типу отношения к объему производства);
производственные и внепроизводственные (по характеру затрат);
прямые и косвенные (по способу отнесения отдельных видов продукции на себестоимость);
планируемые и не планируемые (по степени охвата планом).
Для наиболее удобного расчета себестоимости и прибыли, выделяется следующая классификация затрат:
входящие — здесь имеются приобретенные ресурсы, которые в данный момент имеются в наличии. Ожидается, что такие ресурсы в будущем должны принести неплохой доход. В балансе такие ресурсы отображаются как активы незавершенного производства, производственных запасов, товаров, готовой продукции.
истекшие — это израсходованные ресурсы, из которых уже получен доход, и которые большие его не смогут принести. В балансе они отражаются в виде расходов на производство реализованной продукции, иными словами, входящие затраты переводятся в истекшие.
Следует обратить внимание на то, что классификация затрат на входящие и истекшие имеет важное значение для оценки активов предприятия, исчисления прибыли и убытков.
Для удобного расчета себестоимости используется также классификация затрат на:
прямые (сумма затрат имеет прямую зависимость от объема производства) и косвенные (затраты, не зависящие от объема производства);
внепроизводственные (не учитывающиеся при оценке запасов) и входящие в себестоимость готовой продукции (производственные затраты, связанные с незавершенным производством и производством готовой продукции до момента ее реализации).
одноэлементные (выделяют материальные затраты, отчисления на специальные нужды, затраты на оплату труда, амортизационные затраты, прочие затраты) и комплексные (состоящие из нескольких экономических элементов).
накладные (затраты, связанные с облуживанием и управлением производства) и общепроизводственные (затраты, связанные с содержанием оборудования, аппарата производственных подразделений и т. п.).
Таблица 16 — Расчет затрат себестоимости 1 тонны металлизованных окатышей
Наименование статей расхода | Сумма по плану | Сумма фактически | |
Сырье: Окатыши офлюсованные Реметы в производство Отсев брикетов железной руды | 909,952 909,952 | 874,951 867,832 5,986 1,133 | |
отходы: концентрат 1 сорта (шлам) отсев окатышей реметы отсев брикетов железной руды мелочь брикеьтов безвозвратные потери итого задано за (-) отходов | 56,962 17,587 18,057 0,000 21,318 0,0000 852,990 | 72,212 26,813 16,463 5,388 1,133 22,415 0,0000 802,740 | |
технологическое топливо | 390,793 | 384,902 | |
энергетические затраты | 44,681 | 56,216 | |
вспомогательные затраты цемент химреагенты химреагенты (импортные) | 23,771 12,180 6,279 5,311 | 29,833 12,843 10,891 6,099 | |
Итого условнопеременных затрат | 1312,235 | ||
основная зароботная плата | 25,183 | 21,195 | |
есн | 6,741 | 5,830 | |
расходы на рекультивацию нарушенных земель и природоохранного мероприятия | 0,000 | 0,011 | |
расходы на подготовку и освоение производства | 0,000 | 0,000 | |
затраты по внутризоводскому перемещению грузов | 12,524 | 12,418 | |
амортизация | 167,463 | 156,933 | |
стоимость ОС до 10 тыс. руб. | 0,471 | 0,128 | |
содержание основных фондов | 125,102 | 111,009 | |
услуги цехов ЛебГОКа | 18,677 | 17,587 | |
ремонты | 189,911 | 156,398 | |
прочие цеховые расходы | 61,412 | 82,300 | |
Итого условно-постоянные затраты | |||
передел | 657,258 | 632,472 | |
Цеховая себестоимость | 1901,041 | 1820,113 | |
5. Охрана труда и окружающей среды
5.1 Общие требования техники безопасности для работников ОАО «Лебединский ГОК»
Для того, чтобы сохранять эффективную и безопасную рабочую среду, следует следовать одному правилу: персонал должен отвечать по крайней мере минимальным требованиям по знанию техники безопасности и наличию знаний о работе по каждой отдельной задаче, которую ему предстоит выполнить.
1. Персонал должен быть приписан к соответствующей рабочей зоне и соответствующим образом экипирован для безопасной работы. Должна иметься следующая основная экипировка, необходимая в цеху:
а) защитная спецодежда: не следует использовать синтетические материалы, поскольку они легко воспламеняются. Предпочтительнее будут хлопковые материалы, поскольку она предоставляют лучшую защиту от высокой температуры. Эта одежда должна быть плотно пригнана с целью не допустить соприкосновения с движущимися частями оборудования и тем самым стать причиной несчастного случая. Персонал, имеющий дело с химическими веществами, должен носить резиновый фартук. Персонал, имеющий дело со сварочным оборудованием, должен носить резиновый фартук и защитные краги;
б) защитная обувь: не должна скользить, должна быть маслонепроницаемой и водонепроницаемой. Она также должна иметь носок из стали для лучшей зашиты ног. Персонал, имеющий дело с электрооборудованием, должен быть снабжен изолированной обувью из диэлектрика без носков и) стали. Персонал, имеющий дело с химическими веществами, должен быть снабжен резиновой обувью;
в) каски: должен быть козырек, а также система поглощения для сопротивления удару, чтобы обеспечить защиту от падающих предметов или ударов о выступающие части на заводе, такие как клапаны, трубы, балки или иное низко расположенное оборудование. Электрики должны носить каски из диэлектрика;
г) защитные очки: следует изготавливать из закаленного небьющегося стекла, с защитой сбоку, чтобы избежать попадания мелких частиц или пыли. Они также должны ударостойкими. В некоторых случаях он могут изготавливаться из особого пластика. Персонал, которому требуются предписанные врачами очки должен иметь их, изготовленных по схожим или одинаковым спецификациям техники безопасности. Люди, работающие в лабораториях, должны носить полностью закрытые пластиковые защитные очки. Сварщикам следует носить сварочные очки или маски в зависимости от вида выполняемых сварочных работ;
д) наушники или беруши: наушники полностью закрывают уши, в то время как беруши, изготовленные из мягкого пластика, вставляются непосредственно в уши;
е) защитные перчатки: должны быть изготовлены из теплозащитных материалов для защиты от ожогов при прикосновении к сильно нагретому оборудованию или трубам, а также они не должны скользить. Перчатки, как правило, изготавливаются из кожи или хлопка. Сварщикам требуются перчатки с длинными рукавами, а персоналу, работающему с химическими веществами, требуются резиновые перчатки;
з) респираторы: В запыленных местах или в местах, где могут быть испарения химикатов, рекомендуется носить респираторы. Респираторы, используемые для защиты от испарений химикатов или дыма, должны быть оборудованы специальным фильтрующим элементом или картриджем в зависимости от вида составов, от которых он должен защищать.
Использование защитного оборудования значительно уменьшает количество несчастных случаев, а также их тяжесть.
2. Персонал должен быть соответствующим образом обучен как для работы, так и для соблюдения правил техники безопасности в соответствии с возложенной на него ответственностью, прежде чем отсылать его на рабочее место.
3. Персонал не должен пытаться выполнить какую-то работу, выходящую за пределы своей компетенции.
4. Как при выполнении работы, так и при осуществлении технического осмотра, персонал должен убедиться, что для эффективного выполнения подобных действий используются требуемые инструменты и запасные части.
5. Никто не должен работать с тяжелой техникой или оборудованием при отсутствии специальных знаний или полномочий.
6. Следует развесить предостерегающие и предупреждающие знаки.
7. Следует ограждать места потенциального риска.
8. Поддерживать рабочую среду в чистоте и порядке.
9. Если необходимо использование пламени, сначала необходимо проверить детектором пожароопасной среды потенциально опасные места.
10. Огородить место работ веревкой.
11. Обычный технический осмотр оборудования и осмотр инструментов. Сварочное оборудование и оборудование для кислородо-ацетиленовой сварки должно проверяться каждые полгода. Следует также проверять состояние набора инструментов через каждые три месяца.
12. Осмотр места работы.
13. Никто не должен работать или проходить под подвесными грузами.
14. Телефоны для вызова помощи, установленные в стратегически важных местах, должны использоваться только в аварийных ситуациях.
15. Поместить огнетушители в соответствующих местах и периодически проверяйте наличие их на месте.
16. Следует соблюдать некоторые правила при использовании лифта:
a) не перегружайте лифт;
б) при выходе из лифта закрывайте двери;
в) не используйте лифт для перевозки тяжелых предметов.
17. Для сварки в стратегически важных местах на заводе следует разместить розетки и места для подключения заземления. Обычно они используются во время запланированной ежегодной остановки. Не позволяется также использование износившихся кабелей для подключения сварочных аппаратов к заземлению и питанию.
18. В тех местах, где используются химические вещества, следует установить душевые для чрезвычайных случаев и устройства для промывки глаз.
5.2 Действие теплового излучения на организм человека и защита от него
Инфракрасное (тепловое) излучение, поглощаясь тканями, вызывает тепловой эффект. Наиболее поражаемые ИК-излучением — кожный покров и органы зрения. При остром повреждении кожи возможны ожоги, резкое расширение капилляров, усиление пигментации кожи. При хроническом облучении появляется стойкое изменение пигментации, красный цвет лица, например у стеклодувов, сталеваров. Повышение температуры тела ухудшает самочувствие, снижает работоспособность человека.
Для зашиты от теплового излучения применяются СКЗ и СИЗ. Основными методами защиты являются: теплоизоляция рабочих поверхностей источников излучения теплоты, экранирование источников или рабочих мест, воздушное душирование рабочих мест, радиационное охлаждение, мелкодисперсное распыление воды с созданием водяных завес, общеобменная вентиляция, кондиционирование.
Средства защиты от теплового излучения должны обеспечивать: тепловую облученность на рабочих местах не более 0,35 кВТ/м2, температуру поверхности оборудования не более 35 °C при температуре внутри источника теплоты до 100 °C и 45 °C при температуре внутри источника теплоты более 100 °C.
Теплоизоляция горячих поверхностей (оборудования, сосудов, трубопроводов и т. д.) снижает температуру излучающей поверхности и уменьшает общее выделение теплоты, в том числе ее лучистую часть, излучаемую в инфракрасном диапазоне ЭМИ. Для теплоизоляции применяют материалы с низкой теплопроводностью.
Конструктивно теплоизоляция может быть мастичной, оберточной, засыпной, из штучных изделий и комбинированной.
Мастичную изоляцию осуществляют путем нанесения на поверхность изолируемого объекта изоляционной мастики.
Оберточная изоляция изготовляется из волокнистых материалов — асбестовой ткани, минеральной ваты, войлока и др. и наиболее пригодна для трубопроводов и сосудов.
Засыпная изоляция в основном используется при прокладке трубопроводов в каналах и коробах. Для засыпки применяют, например, керамзит.
Штучная изоляция выполняется формованными изделиями — кирпичом, матами, плитами и используется для упрощения изоляционных работ.
Комбинированная изоляция выполняется многослойной. Первый слой обычно выполняют из штучных изделий, последующие — мастичные и оберточные материалы.
Теплозащитные экраны применяют для экранирования источников лучистой теплоты, зашиты рабочего места и снижения температуры поверхностей предметов и оборудования, окружающих рабочее место. Теплозащитные экраны поглощают и отражают лучистую энергию. Различают теплоотражающие, теплопоглощающие и теплоотводящие экраны. По конструктивному выполнению экраны подразделяются на три класса: непрозрачные, полупрозрачные и прозрачные.
Непрозрачные экраны. Экраны выполняются в виде каркаса с закрепленным на нем теплопоглощающим материалом или нанесенным на него теплоотражающим покрытием.
В качестве отражающих материалов используют алюминиевую фольгу, алюминий листовой, белую жесть; в качестве покрытий — алюминиевую краску.
Для непрозрачных поглощающих экранов используется теплоизоляционный кирпич, асбестовые щиты.
Непрозрачные теплоотводяшие экраны изготавливаются в виде полых стальных плит с циркулирующей по ним водой или водовоздушной смесью, что обеспечивает температуру на наружной поверхности экрана не более 30…356С.
Полупрозрачные экраны применяют в тех случаях, когда экран не должен препятствовать наблюдению за технологическим процессом и вводу через него инструмента и материала. В качестве полупрозрачных теплопоглощающих экранов используют металлические сетки с размером ячейки 3…3,5 мм, завесы в виде подвешенных цепей. Для экранирования кабин и пультов управления, в которые должен проникать свет используют стекло, армированное стальной сеткой. Полупрозрачные теплоотводяшие экраны выполняют в виде металлических сеток, орошаемых водой, или в виде паровой завесы.
Прозрачные экраны изготовляют из бесцветных или окрашенных стекол — силикатных, кварцевых, органических. Обычно такими стеклами экранируют окна кабин и пультов управления. Теплоотводящие прозрачные экраны выполняют в виде двойного остекления с вентилируемой воздухом воздушной прослойкой, водяных и вододисперсных завес.
Воздушное душирование представляет собой подачу на рабочее место приточного прохладного воздуха в виде воздушной струи, создаваемой вентилятором. Могут применяться стационарные источники струи и передвижные в виде перемещаемых вентиляторов. Струя может подаваться сверху, снизу, сбоку и веером.
Средства индивидуальной защиты. Применяется теплозащитная одежда из хлопчатобумажных, льняных тканей, грубодисперсного сукна. Для защиты от инфракрасного излучения высоких уровней используют отражающие ткани, на поверхности которых нанесен тонкий слой металла. Для работы в экстремальных условиях (тушение пожаров и др.) используются костюмы с повышенными теплозащитными свойствами
5.3 Охрана труда женщин
Особенности регулирования труда женщин, лиц с семейными обязанностями посвящена глава 41 Трудового кодекса Российской Федерации (далее по тексту ТК РФ).
Статьей 253 ТК РФ определены работы, на которых ограничивается применение труда женщин: на тяжелых работах и работах с вредными и (или) опасными условиями труда, а также на подземных работах, за исключением нефизических работ или работ по санитарному и бытовому обслуживанию.
Перечни тяжелых работ и работ с вредными и опасными условиями труда, при выполнении которых запрещается применение труда женщин, утверждены постановлением Правительства Российской Федерации от 25.02.2000 г. № 162.
Постановление Правительства РФ от 06.02.93 № 105 «О новых нормах предельно допустимых нагрузок для женщин при подъеме и перемещении тяжестей вручную» запрещает применение труда женщин на работах, связанных с подъемом и перемещением вручную тяжестей, превышающих предельно допустимые для них нормы. Подъем и перемещение тяжестей при чередовании с другой работой (до 2 раз в час) допускается до 10 кг, постоянно в течение рабочей смены до 7 кг. Величина динамической работы, совершаемой в течение каждого часа рабочей смены, не должна превышать: с рабочей поверхности 1750 кгм, с пола 875 кгм.
Статьей 254 ТК РФ определенно, что беременным женщинам в соответствии с медицинским заключением и по их заявлению снижаются нормы выработки, нормы обслуживания либо эти женщины переводятся на другую работу, исключающую воздействие неблагоприятных производственных факторов, с сохранением среднего заработка по прежней работе.
До предоставления беременной женщине другой работы, исключающей воздействие неблагоприятных производственных факторов, она подлежит освобождению от работы с сохранением среднего заработка за все пропущенные вследствие этого рабочие дни за счет средств работодателя.
При прохождении обязательного диспансерного обследования в медицинских учреждениях за беременными женщинами сохраняется средний заработок по месту работы.
Женщины, имеющие детей в возрасте до полутора лет, в случае невозможности выполнения прежней работы переводятся по их заявлению на другую работу с оплатой труда по выполняемой работе, но не ниже среднего заработка по прежней работе до достижения ребенком возраста полутора лет.
В соответствии со статьей 255 ТК РФ женщинам по их заявлению и на основании выданного в установленном порядке листка нетрудоспособности предоставляются отпуска по беременности и родам продолжительностью 70 (в случае многоплодной беременности — 84) календарных дней до родов и 70 (в случае осложненных родов — 86, при рождении двух или более детей — 110) календарных дней после родов с выплатой пособия по государственному социальному страхованию в установленном федеральными законами размере.
Отпуск по беременности и родам исчисляется суммарно и предоставляется женщине полностью независимо от числа дней, фактически использованных ею до родов. Статьей 256 ТК РФ определенно, что по заявлению женщины ей предоставляется отпуск по уходу за ребенком до достижения им возраста трех лет. Порядок и сроки выплаты пособия по государственному социальному страхованию в период указанного отпуска определяются федеральными законами.
Отпуска по уходу за ребенком могут быть использованы полностью или по частям также отцом ребенка, бабушкой, дедом, другим родственником или опекуном, фактически осуществляющим уход за ребенком.
По заявлению женщины или лиц, указанных в части второй настоящей статьи, во время нахождения в отпусках по уходу за ребенком они могут работать на условиях неполного рабочего времени или на дому с сохранением права на получение пособия по государственному социальному страхованию.
На период отпуска по уходу за ребенком за работником сохраняется место работы (должность).
Отпуска по уходу за ребенком засчитываются в общий и непрерывный трудовой стаж, а также в стаж работы по специальности (за исключением случаев досрочного назначения трудовой пенсии по старости).
Работающим женщинам, имеющим детей в возрасте до полутора лет, в соответствии со статьей 258 ТК РФ, предоставляются помимо перерыва для отдыха и питания дополнительные перерывы для кормления ребенка (детей) не реже чем через каждые три часа продолжительностью не менее 30 минут каждый.
При наличии у работающей женщины двух и более детей в возрасте до полутора лет продолжительность перерыва для кормления устанавливается не менее одного часа. По заявлению женщины перерывы для кормления ребенка (детей) присоединяются к перерыву для отдыха и питания либо в суммированном виде переносятся как на начало, так и на конец рабочего дня (рабочей смены) с соответствующим его (ее) сокращением.
Перерывы для кормления ребенка (детей) включаются в рабочее время и подлежат оплате в размере среднего заработка.
Порядок предоставления ежегодных оплачиваемых отпусков определен статьей 122 ТК РФ. До истечения шести месяцев непрерывной работы оплачиваемый отпуск по заявлению работника должен быть предоставлен:
— женщинам перед отпуском по беременности и родам или непосредственно после него.
Статьей 259 ТК РФ предусмотрены гарантии беременным женщинам и лицам с семейными обязанностями при направлении в служебные командировки, привлечении к сверхурочной работе, работе в ночное время, выходные и нерабочие праздничные дни:
— запрещаются направление в служебные командировки, привлечение к сверхурочной работе, работе в ночное время, выходные и нерабочие праздничные дни беременных женщин;
— направление в служебные командировки, привлечение к сверхурочной работе, работе в ночное время, выходные и нерабочие праздничные дни женщин, имеющих детей в возрасте до трех лет, допускаются только с их письменного согласия и при условии, что это не запрещено им в соответствии с медицинским заключением, выданным в порядке, установленном федеральными законами и иными нормативными правовыми актами Российской Федерации.
При этом женщины, имеющие детей в возрасте до трех лет, должны быть ознакомлены в письменной форме со своим правом отказаться от направления в служебную командировку, привлечения к сверхурочной работе, работе в ночное время, выходные и нерабочие праздничные дни.
Гарантии, предусмотренные частью второй настоящей статьи, предоставляются также матерям и отцам, воспитывающим без супруга (супруги) детей в возрасте до пяти лет, работникам, имеющим детей-инвалидов, и работникам, осуществляющим уход за больными членами их семей в соответствии с медицинским заключением.
Перед отпуском по беременности и родам или непосредственно после него либо по окончании отпуска по уходу за ребенком женщине по ее желанию предоставляется ежегодный оплачиваемый отпуск независимо от стажа работы у данного работодателя (ст. 260 ТК РФ).
Статьей 261 ТК РФ закреплены гарантии беременным женщинам, женщинам, имеющим детей, и лицам, воспитывающим детей без матери, при расторжении трудового договора:
— расторжение трудового договора по инициативе работодателя с беременными женщинами не допускается, за исключением случаев ликвидации организации либо прекращения деятельности индивидуальным предпринимателем;
— в случае истечения срочного трудового договора в период беременности женщины работодатель обязан по ее письменному заявлению и при предоставлении медицинской справки, подтверждающей состояние беременности, продлить срок действия трудового договора до окончания беременности. Женщина, срок действия трудового договора с которой был продлен до окончания беременности, обязана по запросу работодателя, но не чаще чем один раз в три месяца, предоставлять медицинскую справку, подтверждающую состояние беременности. Если при этом женщина фактически продолжает работать после окончания беременности, то работодатель имеет право расторгнуть трудовой договор с ней в связи с истечением срока его действия в течение недели со дня, когда работодатель узнал или должен был узнать о факте окончания беременности;
— допускается увольнение женщины в связи с истечением срока трудового договора в период ее беременности, если трудовой договор был заключен на время исполнения обязанностей отсутствующего работника и невозможно с письменного согласия женщины перевести ее до окончания беременности на другую имеющуюся у работодателя работу (как вакантную должность или работу, соответствующую квалификации женщины, так и вакантную нижестоящую должность или нижеоплачиваемую работу), которую женщина может выполнять с учетом ее состояния здоровья;
— при этом работодатель обязан предлагать ей все отвечающие указанным требованиям вакансии, имеющиеся у него в данной местности. Предлагать вакансии в других местностях работодатель обязан, если это предусмотрено коллективным договором, соглашениями, трудовым договором;
— расторжение трудового договора с женщинами, имеющими детей в возрасте до трех лет, одинокими матерями, воспитывающими ребенка в возрасте до четырнадцати лет (ребенка-инвалида до восемнадцати лет), другими лицами, воспитывающими указанных детей без матери, по инициативе работодателя не допускается (за исключением увольнения по основаниям, предусмотренным пунктами 1, 5 — 8, 10 или 11 части первой статьи 81 или пунктом 2 статьи 336 настоящего Кодекса).
Статьей 262 ТК РФ предоставлены дополнительные выходные дни лицам, осуществляющим уход за детьми инвалидами, работающим в сельской местности. Одному из родителей (опекуну, попечителю) для ухода за детьми — инвалидами по его письменному заявлению предоставляются четыре дополнительных оплачиваемых выходных дня в месяц.
Заключение
Металлизованное сырье все больше востребовано в современном мире Технологический процесс ХИЛ III один из наиболее эффективных процессов по выпуску восстановленных железорудных окатышей, являющихся востребованными в металлургическом производстве В ходе проведённой работы над дипломным проектом был изучены такие вопросы как характеристика продукции процесса ХИЛ III, произведён анализ характеристик скруббера колошникового газа, используемого в процессе ХИЛ III, были изучены технологии производства восстановительного газа и восстановления железа в процессе ХИЛ III.
Так же в ходе выполнения дипломного проекта были произведён расчёт технологических параметров металлизации.
Были рассмотрены вопросы охраны труда при производстве металлизованного продукта В экономической части дипломного проекта был произведен расчет условно-переменных затрат и себестоимость одной тонны брикетов, которая составила 1820,113
Как видно из приведённого в дипломном проекте материала, метод прямого восстановления железа находит всё большее количество приверженцев, что сопряжено, прежде всего, с возрастанием потребностей в чистом металле. Основным сдерживающим фактором его развития в настоящее время являются потребности в наличии природных ресурсов богатой железной руды, природного газа и электроэнергии Их получение в свою очередь предполагает крупные финансовые вложения Тем не менее, в мире наметилась всеобщая тенденция к наращиванию объёмов и мощностей по производству губчатого железа.
Список использованных источников
железо газовый шахтный печь металлизация
Гиммельфарб, А. И. Металлизация и электроплавка железорудного сырья. [Текст]: учебное пособие / А. М. Неменов, Б. Е. Тарасов. М.: Металлургия. 1981. — 152 с.
Девисилов, В. А. Охрана труда [Текст]: учебник/ В. А. Девисилов. — М.: ФОРУМ, 2010. — 512 с.
Жиделева, В. В. Экономика предприятия [Текст]: учебное пособие для вузов/ В. В. Жиделева, Ю. Н. Каптейна. М.: ИНФРА-М, 2008. — 354 с.
Курунов, И.Ф., Состояние и перспективы бездоменной металлургии железа. [Текст] / И. Ф. Курунов, Н. А. Савчук. — М.: Черметинформация, 2002.
Ладыгичев, М. Г. Сырьё для черной металлургии [Текст]: справочник / М. Г. Ладыгичев, В. М. Чижикова. — М.: Теплотехник. 2005. — 443
Линчевский, Б. В. Металлургия черных металлов [Текст]: учебное пособие / Б. В. Линчевский, А. Л. Соболевский, А. А. Кальменев. — М.: Металлургия, 1999. — 336 с.
Нормативно-техническая документация предприятия.
Сергеев, И. В. Экономика предприятия [Текст]: учебное пособие/ И. В. Сергеев. — 3-е издание переработанное и дополненное. — М.: Финансы и статистика, 2006. — 546 с.
Сергеев, И. В. Экономика организаций (предприятий) [Текст]: учебное пособие/ И. В. Сергеев, И. И. Веретенникова. — 3-е издание переработанное и дополненное. — М.: Проспект, 2009. — 560 с.
Трахимович, В. И. Использование железа прямого восстановления при выплавке стали. [Текст]/ В. И. Трахимович, А. Г. Шалимов. — М.: Металлургия. 1982. — 248 с.
Юсфин, Ю. С. Металлургия железа [Текст]/ Ю. С. Юсфин. — М.: Металлургия, 2007. — 336 с.