Проектирование участка механического цеха для обработки детали «Шток» ЦГ-160.80x560.31. 024 с годовой программой выпуска детали 4500 шт
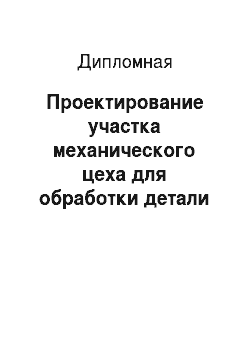
Не оставлять в задней бабке или револьверной головке инструменты, которые не используются при обработке данной заготовки. На сверлильных станках выполнение установки детали осуществляют с соблюдением следующих общих правил безопасности: опорные поверхности выбирают так, чтобы центр тяжести заготовки проходил возможно ближе к середине опорной поверхности, если она одна, и возможно ближе к общему… Читать ещё >
Проектирование участка механического цеха для обработки детали «Шток» ЦГ-160.80x560.31. 024 с годовой программой выпуска детали 4500 шт (реферат, курсовая, диплом, контрольная)
Введение
деталь заготовка технологичность
Машиностроительный комплекс это сложное межотраслевое образование, охватывающее машиностроение и металлообработку. В свою очередь машиностроение включает в себя много специализированных отраслей, сходных по технологии и используемому сырью. Машиностроение наиболее крупная комплексная отрасль, определяющая уровень научно-технического прогресса во всем народном хозяйстве, поскольку обеспечивает все отрасли машинами, оборудованием, приборами, а население предметами потребления. Включает также металлообработку, ремонт машин и оборудования. Для нее особенно характерно углубление специализации производства и расширение ее масштабов. К перечисленным подразделениям машиностроения следует добавить и «малую» металлургию — производство стали и проката, как в литейных цехах машиностроительных предприятий, так и на отдельных специализированных предприятиях по производству литья, поковок, штамповок, и сварных конструкций для машиностроения. В указанной структуре отрасли наиболее сложным является машиностроение, включающее такие важнейшие подотрасли, как машиностроение для межотраслевых производств (электронная и радиопромышленность, приборостроение, станкостроительная и инструментальная, подшипниковая промышленность и др.); производство оборудования для отраслей народного хозяйства (строительно-дорожное машиностроение, транспортное, тракторное и сельскохозяйственное машиностроение и др.); для отраслей промышленности (энергетическое машиностроение, металлургическое, горношахтное и горнорудное машиностроение, химическое машиностроение, производство технологического оборудования для текстильной промышленности и др.); для непроизводственной сферы (коммунальное машиностроение, производство бытовых приборов и машин, военная техника и др.). Кроме отраслевой классификации, машиностроение можно расчленить по стадиям технологического процесса на заготовку; механическую обработку и сборку. По металлоемкости, а также по трудои энергоемкости принято выделять тяжелое, общее и среднее машиностроение. Тяжелое машиностроение отличается большим потреблением металла, относительно малой трудоемкостью и энергоемкостью. Оно включает производство металлоемких и крупногабаритных изделий. Для общего машиностроения характерны средние нормы потребления металла, энергии, невысокая трудоемкость. В основном это производство оборудования для отдельных отраслей промышленности. Общее и среднее машиностроение довольно похожи и четко выраженных закономерностей в географии не имеют. В машиностроении имеется хронологическая классификация. Выделяются новейшие отрасли, возникшие во второй половине XX века. Прежде всего, это отрасли высших этажей машиностроения: электроника, радиотехника, робототехника, ракетно-космическая промышленность и др. Новые отрасли, которые возникли во второй половине XIX и первой половине XX вв.: авиаи автотранспортная техника, паровозои тепловозостроение, производство оборудования для многочисленных отраслей народного хозяйства и промышленности и др. К старым отраслям, возникшим еще в XVIII и первой половине XIX вв. относится производство металлических изделий для первичных отраслей экономики, сельского и лесного хозяйства, добывающей промышленности. Большое значение приобретают в наше время новые формы сотрудничества между странами. Значение машиностроительного комплекса трудно переоценить. Важнейшая его задача, реализация достижений научно-технического прогресса, обеспечение комплексной механизации и автоматизации производства, снабжение народнохозяйственных отраслей новой техникой, удовлетворение населения современными потребительскими товарами.
Темой дипломного проекта является проектирование участка механического цеха для обработки детали «Шток» ЦГ-160.80×560.31.024 с годовой программой выпуска детали 4500 шт. Основой дипломного проекта является разработка технологического процесса в условиях серийного производства.
1. Общий раздел
1.1 Описание конструкции и служебного назначения детали
«Шток» ЦГ-160.80×560.31.024 — представляет собой тело вращения ступенчатой формы с глухим резьбовым отверстием. Общая длина вала 835 мм, наибольший диаметр ступени вала 80 мм, количество ступеней -3.
Деталь «Шток» входит в состав узла: Группа поршневая первой ступени, который состоит из следующих деталей: поршень, шайба, контргайка, гайка, стяжка, шток, кольцо направляющее, кольцо уплотнительное, экспандер, болт М12×40.56, проставка под бурт штока, проставка под гайку штока.
С помощью поршневой группы, а точнее с помощью поршня и уплотнительных колец, которые контактируют со стенками цилиндра создается давление в цилиндре компрессора. Причем так как компрессор двойного действия, то при движении поршня вперед в левой части цилиндра происходит сжатие, а в правой нагнетание; при движении штока назад камеры меняются местами. Давление на выходе первой ступени составляет 0,3МПа.
Деталь «Шток» предназначена для передачи поступательного движения от кривошипно-шатунного механизма к поршню. Так как компрессор двойного действия, то на правой части цилиндра установлены уплотнительные кольца, обеспечивающие герметичность при движении штока назад. Линейная скорость движения штока V=2,5 м/с и для обеспечения высокой износостойкости рабочей поверхности применен соответствующий материал: Сталь 40Х и произведено хромовое покрытие данной поверхности. Для уменьшения нагрева и износа уплотнительных колец, а также для уменьшения усталостных разрушений (так как шток работает при знакопеременных нагрузках) шероховатость рабочей поверхности должна быть незначительной. Для уменьшения концентраторов напряжений и увеличения срока службы штока все переходы между диаметрами выполняются со скруглениями и с небольшой шероховатостью.
В таблице 1 указан химический состав стали 40Х, а в таблице 2 — механические свойства стали.
Таблица 1-Химический состав стали 40Х
марка стали. | C. | Si. | Mn. | Cr не более. | P, S не более. | Cu, Ni не более. | |
сталь 40Х. | 0,36 — 0,44. | 0,17−0,37. | 0,5−0,8. | 0,8−1,1. | до 0,035. | до 0,3. | |
Таблица 2-Механические свойства стали 40Х
марка стали. | ув. | ут. | д. | ш. | ан. | Твердость. | |
Мпа. | Мпа. | %. | %. | Дж/м кв. | HВ (не более). | ||
сталь 40Х. | |||||||
Конструкторская характеристика детали определяется по классификатору ЕСКД.
Класс 71-деталь-тела вращения типа колец, дисков, шкивов и др.
Подкласс 715 000-с L свыше 2D с наружной цилиндрической поверхностью.
Группа 715 300-без уступов, ступенчатые 2-х сторонние с наружной резьбой.
Подгруппа 715 330- с центральным глухим отверстием, без отверстиям вне оси детали.
Вид 715 333- с пазом на наружной поверхности.
715 333 — конструкторский код детали.
Настоящий стандарт распространяется на калиброванную холоднотянутую или холоднокатаную сталь круглого сечения диаметром от 3 до 100 мм.
1.2 Технологический контроль чертежа детали и анализ детали на технологичность
Технологичность конструкции — это совокупность свойств конструкции детали, определяющих ее приспособленность к достижению оптимальных затрат при производстве, эксплуатации и ремонте.
Деталь имеет постоянные базы для механической обработки (внутренние центровые отверстия), позволяющие обеспечить положение осей всех обрабатываемых ступеней вала на одной линии в целях уменьшения радиального биения. Деталь не имеет труднодоступных поверхностей для механической обработки и позволяет ее конструкция производить обработку нескольких поверхностей с одной установки.
Конструкция вала допускает обработку на проход и обеспечивает удобный подход и выход инструмента. Для выхода инструмента предусмотрены канавки.
Все поверхности можно обработать универсальным инструментом. Возможно измерение всех поверхностей универсальными средствами.
Таким образом, деталь очень технологична и можно обработать по типовому технологическому процессу.
Обрабатываемые поверхности
Наружный диаметр 80f9 (), шероховатость Ra=0,1 мкм.
Наружный диаметр 70h9 (), шероховатостьRa=1,6 мкм.
Внутренний диаметрM48×2−6H () метрическая резьба с мелким шагом 2 мм., степень точности — 6, основное отклонение — H, шероховатость Ra=12,5 мкм.
Наружный диаметр M68×3−6g () метрическая резьба с мелким шагом 3 мм, степень точности — 6, основное отклонение — g, шероховатость Ra=12,5 мкм.
Остальные поверхности детали не обрабатываются механически.
Таблица 3 — Анализ технических требований
Условное обозначение технических требований. | Техническое требование. | Методы выполнения требования. | Средства контроля. | |
255…285. | Твердость детали 255…285 HВ. | Поковкаи термообработка. | Прибор Бринеля. | |
H14, h14,±. | Неуказанные предельные отклонения для отверстий Н14, для валов h14. | Черноваяобработка. | ШтангенциркульШЦ-I-125−0,1ГОСТ 166–80. | |
Допуск перпендикулярности поверхности относительно поверхности Г — 0,1. | Черноваяобработка. | Контрольное приспособление. | ||
Допуск радиального биенияотносительно базы Г — ось наружнойцилиндрической поверхности 80f9 — 0,1 мм на длине 500 мм. | Чистоваяобработка. | Контрольное приспособление. | ||
Допуск радиального биенияотносительно базы Г — ось наружной цилиндрической поверхности80f9 — 0,05 мм. | Чистоваяобработка. | Контрольное приспособление. | ||
Допуск радиального биенияотносительно оси наружной цилиндрической поверхности 70h9 — 0,05 мм. | ЧистоваяОбработка. | Контрольное приспособление. | ||
Допуск торцового биенияотносительно поверхности 70h9 — 0,05 мм. | ЧерноваяОбработка. | Контрольное приспособление. | ||
Размерная характеристика
— наибольший наружный диаметр80 мм -9
— длина 835-Н
— диаметр внутренний 48−7
Сталь 40Х — сталь конструкционная углеродистая — 02
Вид детали по технологическому методу изготовления — обрабатывается резанием — 4
Техническая характеристика детали обработанной резанием.
Вид исходной заготовки — штамповка — 22
Точность размеров:
наружная поверхность IT9 — 3
внутренняя поверхность IT14 — 1
Шероховатость (Ra0,1) — 5
Характеристика технологических требований — радиальное биение-В
Вид дополнительной обработки — термообработка -4
Характеристика массы m=30,7 кг — Ж
Технологический код детали 9Н7024.22 315В4Ж
Полный конструкторско-технологический код: ЛМсК715 333.9Н7024.22 315В4Ж
2. Технологический раздел
2.1 Выбор и характеристика принятого типа производства
Выбор типа производства производится по массе изделия M дет и заданной программой выпуска деталей N.
Для детали «Шток» массой Мдет=30,7 кг и N=4500 штук принят тип производства — среднесерийный /2, с. 24/.
Среднесерийное производство характеризуется широкой номенклатурой изделий, изготовляемых периодически повторяющимися партиями и достаточно большим объемом выпуска изделий. В производстве при серийном типе используются универсальные станки полуавтоматы, оснащенные как универсальными, так и специальными приспособлениями, режущими инструментами и средствами измерения, специализированные станки, а так же станки с ЧПУ, как наиболее полно отвечающие требованиям среднесерийного типа производства.
В этом типе производства технологический процесс изготовления деталей преимущественно дифференцирован, то есть, расчленен на отдельные самостоятельные операции, выполняемые на отдельных станках. Производство, в основном, организовано в виде поточных линий, то есть оборудование расположено по ходу технологического процесса. Взаимозаменяемость в условиях серийного типа производства соблюдается, подгонка при сборке не допускается. Квалификация основных рабочих достаточно высокая,.
Себестоимость изделий средняя.
Количество изделий в партии определяется:
n=, шт., (1)
где а-периодичность запуска в днях; а=3,6,12,24; принимается, а=6;
Ф-число рабочих дней, Ф=247 дней.
n==109
2.2 Выбор вида и обоснование способа получения заготовки
Заготовкой называется полуфабрикат по форме и размерам приближенный к готовой детали, имеющий припуски на механическую обработку поверхностей для получения изделий заданного качества. Припуски на обработку должны быть минимальными, но достаточными для изготовления размеров и поверхностей с требуемой и шероховатостью поверхностей.
Использование заготовок с экономичными конструктивными формами и способом получения позволяет производить обработку с наибольшей производительностью и с минимальными затратами. Таким образом, выбор вида и способа получения заготовки является важным фактором, определяющим экономические показатели производства.
Для детали «Шток», изготовленной из стали 40Х ГОСТ 4543–71 в условиях среднесерийного типа производства применяется заготовка-поковка.
В зависимости от типа оборудования различают штамповку на молотах и прессах. Штамповка на молотах имеет недостатки: передача сотрясений при ударах на близко стоящее оборудование; на конструкции зданий кузнечного цеха и окружающих строений, большой шум и невысокая точность получаемых поковок.
В отличие от молота прессы не оказывают ударное воздействие на заготовку. Штамповка на кривошипных горячештамповочных прессах имеет ряд преимуществ по сравнению со штамповкой на молоте. Прежде всего, это улучшение условий труда: меньшая вибрация пола на рабочем месте, меньший шум. Пресс имеет фиксированную величину хода, что дает точность поковок по высоте; верхний и нижний выталкиватели, что дает возможность уменьшить величину штамповочных уклонов и производить штамповку в штампах для выдавливания.
Для получения заготовки выбирается кривошипный горячештамповочный пресс (КГШП)
2.3 Выбор общих припусков и допусков на механическую обработку
Расчет общих припусков и допусков производится по ГОСТ 7505–89.
1. Масса поковки (расчетная)
mp=mq· kp, кг (4)
где kp-расчетный коэффициент; kp=1,6 /прилож. 3/
mp=30,7· 1,6=49,1 кг
2. Класс точности — Т4 /прилож. 1/
3. Группа стали — М2 /табл. 1/
40Х — 0,4%С.
4. Степень сложности — С1 /прилож. 2/
Размеры описывающей поковки фигуры (цилиндр) мм:
диаметр — 80· 1,05 = 84 мм
длина — 835· 1,05 = 877 мм
mоп.ф.=V· с (5)
где V-объем цилиндра, см3
V=рR2· H (6)
V=3,14· 4,22·87,7= 4858 см3
с — плотность стали, mоп.ф.=4858· 0,0078=35,8 кг
5. Конфигурация поверхности разъема штампа — П — плоская /табл. 1/
6. Исходный индекс — 15 /табл. 2/
7. Основные припуски на размеры /табл. 3/:
Наружные диаметры:80Ra0,1; Z=3,2
70Ra1,6; Z=3,2
Длины: 130Ra12,5; Z=3,6
835Ra12,5; Z=5,6
8. Дополнительные припуски.
Смещение по поверхности разъема — 0,4 мм /табл. 4/
9. Размеры поковки:
диаметр d1=80+2· 3.2=86,4 мм принимается 86,5 мм
d2=70+2· 3.2=76,4 мм принимается 76,5 мм
L1=835+2· (0,4+5,6)=847 мм принимается 847 мм
L2=130+0,4+5,6−0,4−3,6=132 мм принимается 132 мм
10. Допускаемые отклонения размеров /табл. 8/
Диаметры Ш86,5Ш76,5
Длины 132 847
11. Принимаем технические требования на изготовление поковки.
12. Неуказанные радиусы закруглений 3 мм
13. Штамповочные уклоны 70 /табл. 18/
14. Допускаемая величина смещения по поверхности разъема -0,7 мм /табл. 9/
15. Допускаемая высота торцового заусенца 6 мм /табл. 11/
Расчет массы заготовки и коэффициента использованияматериала
В общем случае масса заготовки определяется по формуле:
mз.=Vз· с (7)
Рисунок 1 — Эскиз заготовки
V=V1+V2 (8)
V= р? R2•L
V=3,14•4,32•71,5+3,14•3,62•13,2=4153+599=4752 см3
mз.=4752· 0,0078=37 кг
Коэффициент использования материала определяется по формуле:
Ким= (9)
Ким
Данный коэффициент использования материала приемлем для серийного типа производства, метода обработки и конфигурации детали.
2.4 Выбор и обоснование технологических баз
Технологическими базами детали называются поверхности, с помощью которых заготовка ориентируется на станке во время обработки.
Основной технологической базой детали «Шток» являются центровое отверстие и внутренние отверстие, с помощью которых деталь базируется во время обработки, эти же поверхности являются базами при контрольных измерениях.
На первой технологической операции при базировании по черновой необработанной наружной цилиндрической поверхности производится фрезерование торцев и центрование центровых отверстий. На следующих операциях базировании производится по обработанным поверхностям, которое является основной технологической базой.
Основные выполняемые размеры детали заданы от технологических баз, таким образом, производится совмещение технологических и измерительных баз, при этом достигается высокая точность обработки.
2.5 Разработка маршрутного плана обработки детали с выбором оборудования и станочных приспособлений
Для обработки детали «Шток» для условий среднесерийного типа производства предлагается маршрутный план обработки, приведенный в таблице 4.
Таблица 4 — Маршрутный план обработки
№ операциИНаименование операции. | Технологическое оборудование. | Станочное приспособление. | |
005. Фрезерно-Центровальная. | Фрезерно-сверлильный-обточной станок 2Г942Ф2. | Приспособление при станке. | |
010. Токарная с ЧПУ. | Токарный станок с ЧПУмодели 16К20Ф3С32. | Резцедержатель. | |
015. Токарная с ЧПУ. | Токарный станок с ЧПУмодели 16К20Ф3С32. | Резцедержатель. | |
020. Вертикально-фрезерная. | 2202ВМФ4 — вертикально сверлильно-фрезерно-расточный. | Приспособление при станке. | |
025. Слесарная. | Верстак. | Тиски слесарные. | |
030. Контрольная. | Стол контрольный. | ||
035. Термическая. | Термопечь. | ||
040. Круглошлифовальная. | Круглошлифовальный модели 3М151. | Центр и трехкулачковый. | |
045. Круглошлифовальная. | Круглошлифовальный станок модели 3М151. | Центр и трехкулачковый. | |
050. Полировальная. | Токарный станок модели 16К20. | Центр и трехкулачковый. | |
055. Слесарная. | Верстак. | Тиски слесарные. | |
060. Моечная. | Машина моечная. | ||
065. Контрольная. | Стол контрольный. | ||
Принятый маршрутный план обработки детали содержит операции, выполняемые на станках с ЧПУ, что повысит производительность труда, возможность обработать много поверхностей на одном станке.
Характеристика оборудования
2202ВМФ4 — вертикальный сверлильно-фрезерно-расточный станок с крестовым поворотным столом и автоматической сменой инструмента.
Класс точности В
Диаметр поворотной части стола, мм 400
Наибольший ход продольный, поперечный и вертикальный шпиндельной бабки, мм 320
Расстояние от оси шпинделя до рабочей поверхности стола, мм 85 — 405
Расстояние от торца шпинделя до рабочей поверхности стола, мм 110 — 410
Диапазон частоты вращения шпинделя, мин-1 50 — 3150
Диапазон подач, мм/мин 2,5 — 2490
Ускоренное перемещение стола и шпиндельной бабки, мм/мин 7500
Наибольшая скорость вращения стола, мин-1 5
Ёмкость инструментального магазина, шт. 30
Время смены инструмента, не совмещённое с машинным временем, с 4
Тип устройства ЧПУ «Размер 2М-1300»
Мощность главного привода, кВт 5,5
Габарит станка, мм 4150×2340×2660
Масса станка, кг 7160
Станок фрезерно — центровальный мод. 2Г942Ф2 предназначен для двустороннего фрезерования и зацентровки валов. Обеспечивается параллельность и перпендикулярность их к оси детали, что дает возможность в дальнейшем их не обрабатывать.
Диаметр обрабатываемой заготовки, мм 25…125
Длина обрабатываемой заготовки, мм 200…825
Частота вращения шпинделя фрезы, мин-1 125; 179; 249; 358; 497; 712
Рабочая подача фрезы
(бесступенчатое регулирование), мм/мин 20…400
частота вращения сверлильного шпинделя, мин-1 238; 330; 465; 580; 815; 1125
Рабочая подача сверлильной головки
бесступенчатое регулирование), мм/мин 20…300
Продолжительность холостых ходов, мин 0,3
Мощность электродвигателей, кВт 13
Габаритные размеры, мм 3140×1630×1710
16К20ФЗС32 — Токарный патронно-центровой станок
Наибольший диаметр детали над станиной, мм 500
Наибольший диаметр детали, обрабатываемой над суппортом, мм 022
Наибольшая длина детали, устанавливаемая в центрах, мм 1000 Наибольшая длина обработки, мм 870.
Диапазон частот вращения шпинделя, мин-1 22,4−2000
Диапазон подач, мм/об: продольной 0,01−40 поперечной 0,005−20
Наибольшая подача, мм/мин: продольная 5000
поперечная 2500
Ускоренное перемещение, мм/мин: продольное 6000 поперечное 5000
Дискретность задания перемещений, мм: продольное 0,001
поперечное 0,005
Количество позиций резцодержки 6
Тип устройства ЧПУ 2Р22
Мощность главного привода, кВт 11
Габарит станка, мм 3970×1700×2145
Масса станка, кг 4000
3М151-круглошлифовальный автомат для врезного и продольного шлифования.
Наибольший размер устанавливаемой детали, мм. | 200×700. | |
Диапазон размеров шлифования с прибором. | 20−85. | |
активного контроля. | ||
Высота центров над столом, мм. | ||
Наибольшее количество шлифуемых по программе ступеней за одну установку. | ||
Наибольший продольный ход стола, мм. | ||
Ручное перемещение стола за один оборот маховика, мм. | 5,3. | |
Скорость гидравлического перемещения стола, мм/мин. | 50−5000. | |
Наибольший угол поворота стола, град: | ||
По часовой стрелке. | ||
Против часовой стрелке. | ||
Наибольший поперечный ход шлифовальной бабки в Горизонтальной плоскости. | ||
от механизма поворота пиноли, мм. | 0,1. | |
диапазон частоты вращения шпинделя, мин-1 | 50−500. | |
Ускоренное перемещение, мм/мин. | 1700−930. | |
Размер шлифовального круга, мм. | 600×80×305. | |
Скорость поперечной подачи шлифовального круга, мм/мин. | 1,2−0,02. | |
Число программируемых осей координат (включая. | ||
прибор активного контроля). | ||
Число одновременно управляемых координат. | ||
Дискретность задания перемещений, мм: | ||
Шлифовальной бабки. | 0,001. | |
Стола. | 0,1. | |
Суммарная мощность всех электродвигателей, кВт. | 15,2. | |
Габарит. | 5400×2500×2170. | |
Масса, кг. | ||
2.6 Поэлементный техпроцесс обработки детали
Рисунок 2 — Эскиз обрабатываемых поверхностей
Операция 005 — Фрезерно-центровальная
01. Установить и закрепить заготовку.
02. Фрезеровать торцы 1 и 16.
03. Центровать торцы 1 и 16.
04. Снять деталь, контролировать размеры и параметры.
Операция 010-Токарная с ЧПУ
01. Установить и закрепить заготовку.
02. Точить поверхность 5 и 6 начерно.
03. Сверлить отверстие 3.
04. Расточить отверстие 3, снять фаски 4.
05. Расточить канавку 2.
06. Нарезать резьбу 3.
07. Снять деталь, контролировать размеры и параметры.
Операция 015 — Токарная с ЧПУ
01. Установить и закрепить заготовку.
02. Точить фаску 15, поверхность13, 9, фаску 7 начерно.
03. Точить поверхность 9, 13 начисто.
04. Точить канавку 11, 8.
05. Нарезать резьбу на поверхности 13.
06. Снять деталь, контролировать размеры и параметры.
Операция 020 — Вертикально-фрезерная
01. Установить и закрепить заготовку.
02. Фрезеровать паз 14.
03. Снять деталь, контролировать размеры и параметры.
Операция 025 — Слесарная
01. Зачистить острые кромки и заусенцы.
Операция 030 — Контрольная
01. Контролировать размеры.
Операция 035 — Термическая
01. Покрытие поверхности Хтв. 24ГОСТ 9.306−85.
Операция 040 — Шлифовальная
01. Установить и закрепить заготовку.
02. Шлифовать поверхность 6.
03. Снять деталь, контролировать размеры и параметры.
Операция 045 — Шлифовальная
01. Установить и закрепить заготовку.
02. Шлифовать поверхность 9.
03. Шлифовать поверхность 7 и 10.
04. Снять деталь, контролировать размеры и параметры.
Операция 050 — Токарно-винторезная
01. Установить и закрепить заготовку.
02. Полировать поверхность 6.
03. Снять деталь, контролировать размеры и параметры.
Операция 055 — Слесарная
01. Зачистить острые кромки и заусенцы.
Операция 060 — Моечная
01. Промыть деталь.
Операция 065 — Контрольная
01. Контролировать размеры.
2.7 Определение операционных припусков и размеров на одну поверхность Ш70h9 аналитическим методом, на остальные табличным
Наружный диаметр Ш70h9 () должна быть обработана по 9 квалитету и шероховатости Ra1,6.
Порядок обработки:
1) черновое точение
Суммарное значение пространственных отклонений для первой операции определяется по формуле:
с= (8)
где ск — общая кривизна заготовки, мкм
ск=/16, т. 1, стр. 187/
ск — удельное значение кривизны, мкм/мм, ск=0,75 мкм/мм/16, т. 1, стр. 186/
ск= =32 мкм
=0,2518.5 мм
с0==18 500 мкм
с1=с0 · 0,05=18 500?0,05=925 мкм
с2=с1 · 0,04=32·0,04=0,74 мкм
Т.к. значение с1и с2мало, то принимаем равным нулю.
Погрешность установки определяется по формуле:
Еу= (9)
где Еб — погрешность базирования, мкм;
Еб1=0 мкм;
Еб2=0 мкм;
Еу — погрешность установки, мкм;
Еу=0 мкм; /16, т. 1, стр. 42/
Таблица 5 — Аналитический метод определения припусков
Методы обработки поверхности. | Ряд точности, квалитет. | Параметр шероховатости. | Предел. отклонения. | Допуск размера. | Расчетные величины. | ||||
Высота микронеровностейpz, мкм. | Глубина дефект ного слоя, h, мкм. | Сумма простр. отклонений, мкм. | Погрешность установки. | ||||||
Заготовка-штамповКа. | 3 Т. | Rz400. | ; | ||||||
Черновое точение. | h12. | Ra 6,3. | |||||||
Чистовое точение. | h10. | Ra 3,2. | |||||||
Шлифование. | h9. | Ra1,6. | |||||||
Величина расчетного припуска для первой операции определяется по формуле
2Zip=2 (Rzi-1-+hi-1+ +eii-1 (10)
Для последующих операций:
2Zip=2 (Rzi-1-+hi-1+ +ITi-1 (11)
где 2Zip — общий расчетный припуск для данной операции, мкм;
Rzi-1 — высота микронеровностей, оставшихся от предыдущих операций, мкм;
hi-1 — глубина дефектного слоя, оставшегося от предыдущей операции или перехода, мкм;
Eyi — погрешность установки заготовки на данной операции, мкм;
сi-1-суммарное значение пространственных отклонений, оставшихся от предыдущей операции или перехода, мкм;
eii-1 — нижнее предельное отклонение вала после предыдущей операции, мкм;
ITi-1 — допуск размера после предшествующей операции, мкм
I. Припуск на черновое точение
2Z1p=2 (R0-+h0+ +ei0=2 (250+300+447)+1100=3094=3 мм
II. Припуск на чистовое точение
2Z2p=2 (R1+h1+ +IT1 =2 (50+50+22)+300=544=0,5 мм
III. Припуск на шлифовние
2Z3p=2 (R2+h2+ +IT2=2 (25+25)+120=220=0,2 мм
Для удобства определения промежуточных размеров результаты расчетов сведены в таблицу 6.
Таблица 6-Результаты расчетов
Наим. припуска и размера. | Условное обозначение. | Расчетное значение. | Принятые значения. | |
Размер поверхности по чертежу. | d3. | Ш70h9 (). | ||
Исходныйразмер | dисх. | Ш69,926. | ||
Припуск на шлифовании. | 2Z3Р | 0,2. | ||
Размер после чистового точения. | d2. | Ш70,126. | Ш70,2h10 (). | |
Припуск на чистовое точение. | 2Z2Р | 0,5. | ||
Размер после чернового точение. | d1. | Ш70,626. | Ш70,7h12 (). | |
Припуск на черновое точение. | 2Z1Р | |||
Размер заготовки. | Dз. | Ш73,626. | Ш76,5 (). | |
Рисунок 3 — Схема графического расположения припусков и допусков на обработку поверхности Ш70h9 ().
Таблица 7 — Припуски и размеры на обработку
Размер | Метод обработки. | Параметр шерох-ти, Ra, мкм. | Квалитет. | Припуск 2Zmin. | Промежуточный размер | |
80f9 (). | ЗаготовкаТочение чернТочение чистШлифованиеПолирование. | Rz400Ra6,3Ra3,2Ra 0,8Ra 0,1. | 3Тh12h8f9f9. | 30,50,20,1. | Ш86,5 ()Ш83,6h10 ()Ш80,6h9 ()Ш80,1f9 ()Ш80f9 (). | |
М48×2−6H. | Сверлить отвШ24Расточить отв до Ш45,835Нарезать резьбу. | Ra 12,5Ra 6,3. | H14H14. | 5 | Ш24Ш45,835 ()M48×2−6H (). | |
М68×3−6g. | Точение черновоеТочение чистовоеНарезать резьбу. | Ra 12,5Ra 6,3Ra 6,3. | h14h9. | Ш62 ()Ш65 ()M68×3−6g (). | ||
Остальные поверхности обрабатываются однократно.
2.8 Выбор режущего, вспомогательного и измерительного инструмента
Таблица 8 — Режущий, измерительный и вспомогательный инструмент
№ операции. | Режущий инструмент. | Измерительный инструмент. | Вспомогательный инструмент. | |
1. Фреза торцовая левая ф100 ГОСТ 9473–80, ножи Т15К6.2. Фреза торцовая правая ф100 ГОСТ 9473–80, ножи Т15К6.3. Сверло центровочное ф 3 ГОСТ 10 903–77, Р6М5. | ШтангенциркульШЦ-III-300−0,1ГОСТ 166–89. | Оправка фрезерная, патрон сверлильный. | ||
1. Резец проходной, ГОСТ 26 611–85, пластина Т5К10.2. Резец проходной, ГОСТ 26 611–85, пластина Т15К6.3. Сверло ф45 и ф45 Р6М5 ГОСТ 10 903–774. Резец расточной ГОСТ 1882–73 пластина Т5К10.5. Резец канавочный в=4 мм ГОСТ 18 875–73, пластина Т5К10.6. Резьбонарезной резец для метрической резьбы Р6М5 ГОСТ 18 876–73. | ШтангенциркульШЦ-II-800−0,05ГОСТ 166–80. | Резцедержатель для резцов. | ||
1. Резец проходной, ГОСТ 26 611–85, пластина Т5К10.2. Резец канавочный в=6 мм ГОСТ 18 875–73, пластина Т5К10.3. Резец канавочный в=6 мм ГОСТ 18 875–73, пластина Т5К10.4. Резец проходной, ГОСТ 26 611–85, пластина Т15К6.5. Резец резьбонарезной ГОСТ 18 885–73, Т15К6. | ШтангенциркульШЦ-I-150−0,05ГОСТ 166–80Резьбовое кольцо ГОСТ 17 763–72. | Резцедержатель для резцов. | ||
1. Концевая фреза Ш8 Р6М5 ГОСТ 17 025–71. | ШтангенциркульШЦ-I-150−0,05ГОСТ 166–80. | Фрезерный патрон. | ||
Круг шлифовальный 1.100×50×40 24А 40 СТ1. 5К 35 м/с ГОСТ 2424–83. | Калибр-скоба Ш80f9. | Оправка для круга. | ||
Круг шлифовальный 1.100×50×40 24А 40 СТ1. 5К 35 м/с ГОСТ 2424–83. | Калибр-скоба Ш70h9. | Оправка для круга. | ||
Шлифовальная шкурка ЭБ10 ГОСТ 28 743–77. | Калибр-скоба Ш80f9. | Оправка для круга. | ||
2.9 Расчет рациональных режимов резания и определение норм времени на 4 разнохарактерные операции механической обработки
Операция 015 — Токарная с ЧПУ
Переход 02 1. Точить поверхность 63h14 () начерно.
Глубина резания t=2,5 мм
Выбор подачи Sот1=0,4 мм/об /11, т. 2, стр. 15/
Выбранные значения подачи корректируются с учетом поправочных коэффициентов, которые выбираются по карте 4 в зависимости от:
— инструментального материала КSH=1,15
— способа крепления пластин КSР=1
— сечение державки резца КSq=1
— прочности режущей части КSh=1
— механических свойств обрабатываемого материала КSМ=1,05
— схемы установки заготовки КSМ =0,8
— состояния поверхности заготовки КSn=1
— геометрических параметров резца КSб=1
— жесткости станка КSj =1
Значение подач определяется по формуле:
So=Sот· КSH·КSР · КSq·КSh·КSМ·КSМ·КSn·КSб·КSj(20)
So1=0,40· 1,15·1 · 1·1·1,05 · 0,8·1·1·1=0,39 мм/об
Выбор скорости резания
VТ=165 м/мин /11, т. 2, стр. 73/
По карте 23 выбираются поправочные коэффициенты на скорость в зависимости от:
— группа обрабатываемого материала Кvc=1,2
— вида обработки Кvо =1
— жесткости станка КVj=1
— механических свойств обрабатываемого материалаКvМ=1
— геометрических параметров резца Кvб=1
— периода стойкости режущего инструмента Кvт =1
— наличие охлаждения Кvж =1
Скорость резания определяется по формуле:
V= VТ· Кvc·Кvо·КVj·КvМ·Кvб·Кvт·Кvж (21)
V= 165· 1,2·1·1·1·1·1·1=178 м/мин
Частота вращения шпинделя определяется по формуле:
n=(22)
n1=мин-1
Проверка выбранных режимов резания по мощности привода главного движения.
Расчет мощности, необходимый для резания, производится по формуле:
NP=NT· (23)
NT=8,9 кВт /11. т. 2, стр. 73/
NP=8,9· 1,1=9,8 кВт
NПР=11 кВт
NP?NПР (9,8<11) — обработка возможна.
Определение минутной подачи.
Минутную подачу рассчитываем по формуле:
SM=SO· nФ, мм/мин (24)
SM1=0,4· 900=360 мм/мин.
Определение цикла автоматической работы.
ТО= (25)
ТО=мин
Тмв=, (26)
где Lуск — длина ускоренного перемещения (подвод инструмента), мм
Sуск — ускоренная подача, мм/мин
Тмв=мин
Ту.а1=То+Тмв=0,15+0,02=0,17 мин
2. Точить поверхность 70,7h12 () начерно.
Глубина резания t=1,5 мм
Выбор подачи Sо=0,3 мм/об /11, т. 2, стр. 96/
Выбранные значения подачи корректируются с учетом поправочных коэффициентов, которые выбираются по карте 4 в зависимости от:
— инструментального материала КSH=1,15
— способа крепления пластин КSР=1
— сечение державки резца КSq=1
— прочности режущей части КSh=1
— механических свойств обрабатываемого материала КSМ=1,05
— схемы установки заготовки КSМ =0,8
— состояния поверхности заготовки КSn=1
— геометрических параметров резца КSб=1
— жесткости станка КSj =1
Значение подач определяется по формуле 20:
So1=0,3· 1,15 · 1 · 1· 1 · 1,05 · 0,8· 1· 1· 1=0,29 мм/об
Выбор скорости резания
VТ=205 м/мин /11, т. 2, стр. 73/
По карте 23 выбираются поправочные коэффициенты на скорость в зависимости от:
— группа обрабатываемого материала Кvc=1,05
— вида обработки Кvо =1
— жесткости станка КVj=1
— механических свойств обрабатываемого материала КvМ=1
— геометрических параметров резца Кvб=1
— периода стойкости режущего инструмента Кvт =1
— наличие охлаждения Кvж =1
Скорость резания определяется по формуле 21:
V= 205· 1,05· 1· 1· 1· 1· 1· 1=221 м/мин
Частота вращения шпинделя определяется по формуле 22:
n1=мин-1
Проверка выбранных режимов резания по мощности привода главного движения.
Расчет мощности, необходимый для резания, производится по формуле 23:
NT=8,9 кВт /11. т. 2, стр. 73/
NP=8,9· 1,1=9,8 кВт
NПР=11 кВт
NP?NПР (9,8<11) — обработка возможна.
Определение минутной подачи.
Минутную подачу рассчитываем по формуле 24:
SM1=0,3· 996=299 мм/мин.
Определение цикла автоматической работы.
ТО= (25)
ТО=мин
Тмв=, (26)
где Lуск — длина ускоренного перемещения (подвод инструмента), мм
Sуск — ускоренная подача, мм/мин
Тмв=мин
Ту.а2=УТо+Тмв=0,18+0,03=0,21 мин
Переход 03. Точить поверхность 70h9 () начисто.
Глубина резания t=0,25 мм
Выбор подачи Sо=0,2 мм/об /11, т. 2, стр. 96/
Выбранные значения подачи корректируются с учетом поправочных коэффициентов, которые выбираются по карте 4 в зависимости от:
— инструментального материала КSH=1,15
— способа крепления пластин КSР=1
— сечение державки резца КSq=1
— прочности режущей части КSh=1
— механических свойств обрабатываемого материала КSМ=1,05
— схемы установки заготовки КSМ =0,8
— состояния поверхности заготовки КSn=1
— геометрических параметров резца КSб=1
— жесткости станка КSj =1
Значение подач определяется по формуле 20:
So1=0,2· 1,15·1 · 1· 1 · 1,05 · 0,8· 1· 1· 1=0,2 мм/об
Выбор скорости резания
VТ=220 м/мин /11, т. 2, стр. 73/
По карте 23 выбираются поправочные коэффициенты на скорость в зависимости от:
— группа обрабатываемого материала Кvc=1,05
— вида обработки Кvо =1
— жесткости станка КVj=1
— механических свойств обрабатываемого материала КvМ=1
— геометрических параметров резца Кvб=1
— периода стойкости режущего инструмента Кvт =1
— наличие охлаждения Кvж =1
Скорость резания определяется по формуле 21:
V= 220· 1,05· 1· 1· 1· 1· 1· 1=238 м/мин
Частота вращения шпинделя определяется по формуле 22:
n1=мин-1
Проверка выбранных режимов резания по мощности привода главного движения.
Расчет мощности, необходимый для резания, производится по формуле 23:
NT=8,9 кВт /11. т. 2, стр. 73/
NP=8,9· 1,1=9,8 кВт
NПР=11 кВт
NP?NПР (9,8<11) — обработка возможна.
Определение минутной подачи.
Минутную подачу рассчитываем по формуле 24:
SM1=0,2· 1083=217 мм/мин.
Определение цикла автоматической работы.
ТО= (25)
ТО=мин
Тмв=, (26)
где Lуск — длина ускоренного перемещения (подвод инструмента), мм
Sуск — ускоренная подача, мм/мин
Тмв=мин
Ту.а3=УТо+Тмв=0,25+0,03=0,28 мин
Переход 04. Точить канавку в=6 мм на поверхности Ш69h14.
Глубина резания t=0,5 мм
Выбор подачи Sо=0,2 мм/об /11, т. 2, стр. 38/
Выбранные значения подачи корректируются с учетом поправочных коэффициентов, которые выбираются по карте 4 в зависимости от:
— инструментального материала КSH=1,15
— способа крепления пластин КSР=1
— сечение державки резца КSq=1
— прочности режущей части КSh=1
— механических свойств обрабатываемого материалаКSМ=1,05
— схемы установки заготовки КSМ =0,8
— состояния поверхности заготовки КSn=1
— геометрических параметров резца КSб=1
— жесткости станка КSj =1
Значение подач определяется по формуле 20:
So1=0,2· 1,15 · 1 · 1·1 · 1,05 · 0,8·1·1·1=0,2 мм/об
Выбор скорости резания
VТ=68 м/мин /11, т. 2, стр. 73/
По карте 23 выбираются поправочные коэффициенты на скорость в зависимости от:
— группа обрабатываемого материала Кvc=1,05
— вида обработки Кvо =1
— жесткости станка КVj=1
— механических свойств обрабатываемого материалаКvМ=1
— геометрических параметров резца Кvб=1
— периода стойкости режущего инструмента Кvт =1
— наличие охлаждения Кvж =1
Скорость резания определяется по формуле 21:
V= 68· 1,05·1·1·1·1·1·1=73 м/мин
Частота вращения шпинделя определяется по формуле 22:
n1=мин-1
Проверка выбранных режимов резания по мощности привода главного движения.
Расчет мощности, необходимый для резания, производится по формуле 23:
NT=8,9 кВт /11. т. 2, стр. 73/
NP=8,9· 1,1=9,8 кВт
NПР=11 кВт
NP?NПР (9,8<11) — обработка возможна.
Определение минутной подачи.
Минутную подачу рассчитываем по формуле 24:
SM1=0,2· 337=67 мм/мин.
Основное время обработки 25:
ТО=мин
Тмв=мин
Ту.а4.=УТо+Тмв=0,15+0,03=0,18 мин
2. Точить канавку в=6 мм на поверхности Ш63,5h14.
Глубина резания t=2,3 мм
Выбор подачи Sо=0,2 мм/об /11, т. 2, стр. 38/
Выбранные значения подачи корректируются с учетом поправочных коэффициентов, которые выбираются по карте 4 в зависимости от:
— инструментального материала КSH=1,15
— способа крепления пластин КSР=1
— сечение державки резца КSq=1
— прочности режущей части КSh=1
— механических свойств обрабатываемого материалаКSМ=1,05
— схемы установки заготовки КSМ =0,8
— состояния поверхности заготовки КSn=1
— геометрических параметров резца КSб=1
— жесткости станка КSj =1
Значение подач определяется по формуле 20:
So1=0,2· 1,15 · 1 · 1·1 · 1,05 · 0,8·1·1·1=0,2 мм/об
Выбор скорости резания
VТ=68 м/мин /11, т. 2, стр. 73/
По карте 23 выбираются поправочные коэффициенты на скорость в зависимости от:
— группа обрабатываемого материала Кvc=1,05
— вида обработки Кvо =1
— жесткости станка КVj=1
— механических свойств обрабатываемого материалаКvМ=1
— геометрических параметров резца Кvб=1
— периода стойкости режущего инструмента Кvт =1
— наличие охлаждения Кvж =1
Скорость резания определяется по формуле 21:
V= 68· 1,05·1·1·1·1·1·1=73 м/мин
Частота вращения шпинделя определяется по формуле 22:
n1=мин-1
Проверка выбранных режимов резания по мощности привода главного движения.
Расчет мощности, необходимый для резания, производится по формуле 23:
NT=8,9 кВт /11. т. 2, стр. 73/
NP=8,9· 1,1=9,8 кВт
NПР=11 кВт
NP?NПР (9,8<11) — обработка возможна.
Определение минутной подачи.
Минутную подачу рассчитываем по формуле 24:
SM1=0,2· 366=73 мм/мин.
Основное время обработки 25:
ТО=мин
Тмв=мин
Ту.а5.=То+Тмв=0,14+0,02=0,16 мин
Переход 05. Нарезать резьбуМ68×3−6g.
Глубина резания t=2,31 мм
Рабочая высота профиля резьбы h=1,624 мм
Число проходов i=12
Выбор подачи S=0,06 мм/прох /11, т. 2, стр. 96/
Выбор скорости резания выбирается по таблице
V=120 м/мин /11, т. 2, стр. 98/
Частота вращения шпинделя определяется по формуле 22:
n1=мин-1
Проверка выбранных режимов резания по мощности привода главного движения.
Расчет мощности, необходимый для резания, производится по формуле 23:
NT=8,9 кВт /11. т. 2, стр. 73/
NP=8,9· 1,1=9,8 кВт
NПР=11 кВт
NP?NПР (9,8<11) — обработка возможна.
Определение минутной подачи.
Минутную подачу рассчитываем по формуле 24:
Определение цикла автоматической работы по формуле:
= (27)
мин
Тмв=мин
Ту.а6=УТо+Тмв=0,36+0,1=0,46 мин
Ту.а= Ту.а1.+Ту.а2.+Ту.а3.+Ту.а4+Ту.а5+Ту.а6= 0,17+0,21+0,16+0,18+0,28+0,46=1,46
Вспомогательное время определяется по формуле:
Тв=Тв.у.+Тв.он.+Тв.изм, (22)
где Тв.у — время на установку и снятие детали, мин;
Тв.он — вспомогательное время, связанное с операцией, мин;
Тв.изм — вспомогательное время на измерение.
Тв.у=1,3 мин /11, т. 1, стр. 57/
Тв.оп=1,04 мин /11, т. 1, стр. 79/
Тв.изм=0,06+0,14+0,65=0,85 мин /11, т. 1, стр. 89/
Тв=1,3+1,04+0,85=3,19 мин.
Штучное время определяется по формуле:
Тшт=(Ту.а.+Тв· ktb) (1+) (23)
где ktb-поправочный коэффициент на время вспомогательное;
атех, аорг, аотп — время на техническое и организационное обслуживание рабочего места, %.
ktb=0,93 /11, т. 1, стр. 50/
атех+ аорг+аотп=7% /11, т. 1, стр. 90/
Тшт=(1,46+3,19· 0,93) (1+)=4,7 мин.
Штучно-калькуляционное время определяется по формуле:
Тшт.к.=Тшт+ (24)
где Тп.з. — подготовительно-заключительное время.
Тп.з.=24 мин /12, стр. 96/
Тшт.к.=4,7+мин
Операция 005-Фрезерно-центровальная
1. Переход 1. Режущий инструмент: Фреза торцоваяШ100 Т15К6 ГОСТ 9473–80
Sz= 0,2
t=6
2. Расчет длины рабочего хода Lрх
Lрх =Lp+Lп+Lд,
где Lп — длина врезания и перебега
Lд — дополнительная длина хода.
Lp — длина резания
Lрх=15+3,5+10=28,5
3. Частота вращения детали определяется по формуле 22
n=1 000 110/3,1486,5=405 мин-1
4. Выбор скорости резания
VТ=105 м/мин /11, т. 2, стр. 73/
5. По карте 23 выбираются поправочные коэффициенты на скорость в зависимости от:
— группа обрабатываемого материала Кvc=1,05
— вида обработки Кvо =1
— жесткости станка КVj=1
— механических свойств обрабатываемого материала КvМ=1
— геометрических параметров резца Кvб=1
— периода стойкости режущего инструмента Кvт =1
— наличие охлаждения Кvж =1
6. Скорость резания определяется по формуле 21:
V= 105· 1,05· 1· 1· 1· 1· 1· 1=110 м/мин
7. Определение минутной подачи.
Минутную подачу рассчитываем по формуле 24:
SM=0,2· 405=81 мм/мин.
8. Основное время
ТО=, мин
ТО=
Переход 2. Режущий инструмент: Фреза торцоваяШ100 Т15К6 ГОСТ 9473–80
Sz= 0,2
t=6
8. Расчет длины рабочего хода Lрх
Lрх =Lp+Lп+Lд,
где Lп — длина врезания и перебега
Lд — дополнительная длина хода.
Lp — длина резания
Lрх=15+3,5+10=28,5
9. Частотавращениядетали определяется по формуле 22
n=1 000 110/3,1476,5=458 мин-1
10. Выбор скорости резания
VТ=105 м/мин /11, т. 2, стр. 73/
11. По карте 23 выбираются поправочные коэффициенты на скорость в зависимости от:
— группа обрабатываемого материала Кvc=1,05
— вида обработки Кvо =1
— жесткости станка КVj=1
— механических свойств обрабатываемого материала КvМ=1
— геометрических параметров резца Кvб=1
— периода стойкости режущего инструмента Кvт =1
— наличие охлаждения Кvж =1
12. Скорость резания определяется по формуле 21:
V= 105· 1,05· 1· 1· 1· 1· 1· 1=110 м/мин
13. Определение минутной подачи.
Минутную подачу рассчитываем по формуле 24:
SM=0,2· 458=92 мм/мин.
8. Основное время
ТО=, мин
ТО=
переход 3. Режущий инструмент: Ш3,15 Р6М5 ГОСТ 10 903–77
Глубина резания t=1,56 мм
Выбор подачи Sот=0,07 мм/об /11, т. 2, стр. 128/
Выбранные значения подачи корректируются с учетом поправочных коэффициентов, которые выбираются по карте 53 в зависимости от:
— механических свойств обрабатываемого материала КSМ=1,1
Значение подач определяется по формуле 14:
Sо=0,07?1,1=0,08 мм/об
Выбор скорости резания
VТ1=27 м/мин /11, т. 2, стр. 128/
По карте 57 выбираются поправочные коэффициенты на скорость в зависимости от:
— группа обрабатываемого материала Кvм=1,1
— формы заточки инструмента Кvз =1
— наличие охлаждения Кvж =1
— состояние поверхности КVW=1
— материала инструментаКvи=1,0
Скорость резания определяется по формуле:
V=VТ ?Кvм ?Кvз ?Кvж ?КVW?Кvи (23)
V= 27· 1,1·1·1·1·1=29,7 м/мин
Частота вращения шпинделя определяется:
n= мин-1
Расчет мощности, необходимый для резания, производится по формуле:
NP=NT· (24)
NT=0,19 кВт /11. т. 2, стр. 128/
NP=0,19· 1,1=0,2 кВт
NПР=11 кВт
NP?NПР (0,2<11) — обработка возможна.
Минутную подачу рассчитываем по формуле 17:
SM=0,07· 118=8,2 мм/мин
Определение цикла автоматической работы по формулам 19 и 20.
ТО=мин
Тмв=мин
Ту.а=То+Тмв=4,9+0,1=5 мин
Вспомогательное время определяется по формуле 30:
Тв.у=0,8 мин /11, т. 1, стр. 52/
Тв.оп=0,92 мин /11, т. 1, стр. 79/
Тв.изм=0,29 мин /11, т. 1, стр. 87/
Тв=0,8+0,92+0,29=2,01 мин.
Штучное время определяется по формуле 31:
ktb=1 /11, т. 1, стр. 50/
атех+ аорг+аотп=8% /11, т. 1, стр. 90/
Тшт=(5+2,01 · 1) (1+)=8,09 мин.
Штучно-калькуляционное время определяется по формуле 32
Тп.з.=20,5 мин /11, т. 1, стр. 102/
Тшт.к.=8,09 +мин
Операция 020-Вертикально-фрезерная
14. Режущий инструмент: Концевая фреза Ш8Р6М5 ГОСТ 17 025–71
Sz= 0,02
t = 2,5
15. Расчет длины рабочего хода Lрх
Lрх =Lp+Lп+Lд,
где Lп — длина врезания и перебега
Lд — дополнительная длина хода.
Lp — длина резания
Lрх=80+5+10=95
16. Частота вращения детали определяется по формуле 22
n=1 000 105/3,148=1752 мин-1
Уточняем скорость резания
V=105
17. Определение минутной подачи.
Минутную подачу рассчитываем по формуле 24:
SM=0,2· 1752=35 мм/мин.
8. Основное время
ТО=, мин
ТО=
Тмв=мин
Вспомогательное время определяется по формуле 30:
Тв.у=0,8 мин /11, т. 1, стр. 52/
Тв.оп=1,53 мин /11, т. 1, стр. 79/
Тв.изм=0,05 мин /11, т. 1, стр. 87/
Тв=0,8+1,53+0,05=2,38 мин.
Штучное время определяется по формуле 31:
ktb=1 /11, т. 1, стр. 50/
атех+ аорг+аотп=8% /11, т. 1, стр. 90/
Тшт=(0,83+2,38· 1) (1+)=4,29 мин.
Штучно-калькуляционное время определяется по формуле 32
Тп.з.=20,5 мин /11, т. 1, стр. 102/
Тшт.к.=4,29+мин
2.10 Составление управляющей программы обработки заготовки на станке с ЧПУ
Управляющая программа составляется для обработки на станке 16К20Ф3С32 с устройством ЧПУ 2Р22:
N001 S2 900 F0,4 T1*
N002 X75 Z140 EM08*
N003 L08 А0 Р2*
N004 X68,5 Z137Е*
N005 X70 Z127,5*
N006 Z77*
N007 X63,5*
N008 X72 Z74,5*
N009 Z5*
N010 X77*
N011 X80 Z-5*
N012 М17*
N013 S21083 F0,2 T2*
N014 G10*
N015 L10 B4*
N016 X68 Z135 Е*
N017 Z4*
N018 G11*
N019 S2337 F0,2 T2*
N020 X70 Z77*
N021 X63.5*
N022 X70*
N023 X72 Z5*
N024 X69*
N025 X72 Z5*
N026 S2562 F0,06 T2*
N027 L01 F3 W135 X68 A0 P2.31 C0*
N028 Z83*
N029 X70*
N030 M09*
N031 M02*
3. Конструкторский раздел
3.1 Расчет и конструирование режущего инструмента на заданной операции
На токарной операции с ЧПУ операции 010 в качестве режущего инструмента используется сверло диаметром 43 мм. Главное движение — вращение сверла, движение подачи — поступательное перемещение сверла. В качестве материала режущей части используется быстрорежущая сталь Р6М5.
Сверло состоит из рабочей части и хвостовика соединенных шейкой. Рабочая часть в свою состоит из режущей под углом 118 градусов и калибрующей. Хвостовик конический конус Морзе 5 точности АТ8.
Режимы резания при сверлении.
Подача: S=0,53 мм/об /пункт 2.9/
Скорость резания: V=14,6 м/мин /пункт 2.9/
Частота вращения шпинделя n1=108 мин-1 /пункт 2.9/
Мощность резания: NP=4,1 кВт /пункт 2.9/
Крутящий момент определяется по формуле:
Н? м (34)
Осевая сила резания определяется по формуле:
Ро=10СрDqSyKp(35)
Ср=67; q=1,0; y=0,65. /16, т. 2; с. 281/
Kp=0,75 /16, т. 2, с. 264/
Ро =10•67•431•0,530,65•0,75=14 300 Н
Средний диаметр хвостовика определяется по формуле:
dcp= (36)
гдеугол конуса (для большинства конусов Морзе =1030)
µ - коэффициент трения стали (µ=0,096)
Ди — отклонение угла конуса (Ди=5)
dcp=м=50 мм
Выбирается ближайший больший конус, т. е. конус Морзе № 5 с лапкой. Основные конструктивные размеры: D1=44,7 мм, d2=36,5 мм, b=15,9 мм, h=38 мм, e=29 мм, l3=149,5 мм, R=10 мм.
Определяется длина сверла по ГОСТ 10 903–77 /16, т. 2, с. 146/
— общая длина L=359 мм
— длина рабочей части l=210 мм.
Геометрические параметры сверла: щ=300, 2ц=1160, ш=550, г=120, Ь=150.
Шаг винтовой канавки определяется по формуле:
Н=мм (37)
Толщина сердцевины: dc=0,2D=0,2•43=21,5 мм
Обратная конусность: 0,09 мм.
Ширина ленточки: f0=1,0 мм.
Ширина пера: В=0,58•D=0,58•43=24,94 мм.
3.2 Организация технического контроля на участке. Расчет и конструирование средств измерения для заданной операции
Система контроля качества изделий предназначена для своевременного определения с требуемой точностью параметров качества изделий, изготавливаемых на участке.
Контроль качества изделий на участке производится на контрольных столах контролёрами. Контрольный пункт промежуточного контроля располагается между станками. Это возможно из-за использования простых измерительных средств (калибров, штангенциркулей, штангенрейсмусов и т. п.) и контрольных приспособлений.
Проверка производиться после токарной обработки, после нарезания зубчатых венцов и перед термообработкой, после изготовления детали.
Измерительные средства применяемые для промежуточного контроля заготовки и окончательного контроля детали в серийном производстве могут быть и стандартными, и специальными.
При измерении поверхностей, выполненных по допускам, применяют предельные калибры, т.к. измерение переставными инструментами является сложной и длительной операцией. Средства контроля должны соответствовать требованиям ГОСТ 8.001−71. К применению допускаются средства контроля признанные годными по результатам метрологического надзора в соответствии с требованиями ГОСТ 8 002−71.
Системой контроля качества изделий на участке занимается служба отдела технического контроля, которая находится в подчинении дирекции по качеству.
На 045 операции круглошлифовальной для контроля наружной поверхности 70h9 () применяется калибр-скоба. Калибр относится к нерегулируемым гладким калибрам. Изготавливается цельным из стали 20 с цементацией h 0,8…1,2 до 59…65HRСэ. Проходная сторона должна охватывать поверхность, а не проходная не должна. Расчёт исполнительных размеров гладких калибров производится по формулам ГОСТ 24 853–81.
Предельные отклонения размера наружной поверхности 70h9 ().
ES=0; EI=-74 мкм. /т. 7/.
Предельные размеры поверхности:
Dmax=D+ ES =70+0=70 мм.
Dmin=D+ EI=70−0,074=69,987 мм Допуск поверхности:
TD=ES-EI=0 — (-0,074)=0,074 мм.
Отклонения и допуски на калибр-скобу:
Z1=13 мкм, Y1=0 мкм H1=8 мкм Hp=3 мкм Расчёт размеров проходного калибра ПР:
ПР= Dmax — Z1 ±H1 |2=70−0,013± 0,008/2=69,987±0,004 мм Предельные размеры проходного калибра:
— наибольший: ПРmax=69,987+0,004=69,991 мм.
— наименьший: ПРmin=69,987−0,004=69,983 мм Исполнительный размер проходного калибра ПРисп:
ПРисп=69,983.
Расчёт размеров непроходного калибра НЕ:
НЕ= Dmin±H1 |2=69,926± 0,008/2=69,926±0,004 мм Предельные размеры непроходного калибра:
— наибольший: НЕmax=69,926 +0,004=69,93 мм.
— наименьший: НЕmin=69,926 -0,004=69,922 мм.
Исполнительный размер непроходного калибра НЕисп:
НЕисп=69,922.
Расчет размеров контрольного калибра К-ПР:
К-ПР= Dmax — Z1 ±Hр |2=70−0,013± 0,003/2=69,987±0,0015 мм Предельные размеры контрольного калибра К-ПР:
— наибольший: К-ПРmax=69,987+0,0015=69,9885 мм.
— наименьший: К-ПРmin=69,987−0,0015=69,9855 мм Исполнительный размер проходного калибра К-ПРисп:
К-ПРисп=69,9855.
Расчет размеров контрольного калибра К-НЕ:
К-НЕ= Dmin±Hр |2=69,926± 0,003/2=69,926±0,0015 мм Предельные размеры контрольного калибра К-НЕ:
— наибольший: К-НЕmax=69,926 +0,0015=69,9275 мм.
— наименьший: К-НЕmin=69,926 -0,0015=69,9245 мм.
Исполнительный размер непроходного калибра К-НЕисп:
К-НЕисп=69,9245.
Расчет размеров контрольного калибра К-И:
К-И= Dmax+y1±Hр |2=70+0± 0,003/2=70±0,0015 мм Предельные размеры контрольного калибра К-И:
— наибольший: К-Иmax=70+0,0015=70,0015 мм.
— наименьший: К-Иmin=70−0,0015=69,9985 мм.
Исполнительный размер непроходного калибра К-Иисп:
К-Иисп=69,9985.
Рисунок 5 — Схема расположения полей допусков калибра-скобы контроля размера наружной поверхности 70h9 ().
4. Организационный раздел
4.1 Определение потребного количества технологического оборудования и его загрузки
При серийном производстве широко применяется взаимозаменяемость деталей, технологические процессы выполнены в виде операционных, средняя квалификация рабочих — 5 разряд.
1. Нормативный фонд времени
Fн=(Дк — Дпр — Дв) • а • m
где Дк — число календарных дней (365),
Дпр — число праздничных дней (14),
Дв — число выходных дней (104),
а — продолжительность рабочего дня (8 час),
Кпр — коэффициент, учитывающий плановые простои оборудования в ремонте (0,88),
т — количество смен.
Fн=(365 -104−14) Ў¤ 2 • 8 = 3952 ч.,
где 6 час — сокращенные предпраздничные дни.
К=1−10/100=0,9
а = 10%
Кпр — коэффициент, учитывающий простои оборудования в ремонте (0,9).
2. Действительный фонд времени работы оборудования
Fд= Fн • m • Кпр = 3952 • (1 • 10/100) = 3556,8 ч.
где Кпр — коэффициент, учитывающий плановые простои оборудования в ремонте (0,9).
3. Определяется необходимое количество оборудования исходя из производственной программы проектируемой детали на основе маршрутного техпроцесса.
где tшт — штучное время, мин.
Кв = 1 — 1,2 — коэффициент выполнения норм.
005 Фрезерно-центровальная с ЧПУ (2Г942Ф2)
Ср = 8,09 • 10 000•2/ 3556,8 •1,1 • 60 = 0,69 Принимается Спр = 1 ст.
010 Токарная с ЧПУ (16К20Ф3С32)
Ср = 4,7 • 10 000•2/ 3556,8 •1,1 • 60 = 0,4 Принимается Спр = 1 ст.
015 Токарная с ЧПУ (16К20Ф3С32)
Ср = 4,7 • 10 000•2/ 3556,8 •1,1 • 60 = 0,4 Принимается Спр = 1 ст.
020 Вертикально-фрезерная (5А352ПФ2)
Ср = 4,29 • 10 000•2/ 3556,8 •1,1 • 60 = 0,37 Принимается Спр = 1 ст.
040Круглошлифовальная (3М151)
Ср = 1,2• 10 000•2/ 3556,8 •1,1 • 60 =0,1 Принимается Спр = 1 ст.
045 Круглошлифовальная (3М151)
Ср = 1,2 • 10 000•2/ 3556,8 •1,1 • 60 = 0,1 Принимается Спр = 1 ст.
050Токарно-винторезная (16К20)
Ср = 0,3• 10 000•2/ 3556,8 •1,1 • 60 = 0,03 Принимается Спр = 1 ст.
Общее принятое количество станков Спр = 7 ст.
Определяется уровень загрузки оборудования на механическом участке по обработке детали. Рассчитывается коэффициент загрузки станков по операциям по формуле:
005
010
015
020
040
045
050
На основе произведенных расчётов строится график загрузки оборудования участка, ширина столбиков в соответствующем масштабе пропорциональна количеству станков данной модели. Средний коэффициент загрузки всего станочного парка на проектируемом участке по заданной детали на графике — горизонтальная линия, проходящая через весь график. Данные о количестве, габаритах, мощности электродвигателей и стоимости с учетом транспортировки и монтажа оборудования на участке заносятся в сводную ведомость оборудования.
Для построения графика загрузки оборудования рассчитывается средний коэффициент загрузки металлорежущего оборудования механического участка при заданной производственной программе.
Кз.ср. = 0,32 • 100 = 32%
Таблица 4.1 — Ведомость оборудования
Наименование оборудования. | Ср | Спр | Кз, %. | Мощность электродвигателя кВт. | ||
1 ст. | всех. | |||||
1. Фрезерно-центровальный с ЧПУ 2Г942Ф2. | 0,34. | |||||
2. Токарный с ЧПУ 16К20Ф3С32. | 0,2. | |||||
3. Токарный с ЧПУ 16К20Ф3С32. | 0,2. | |||||
4. Вертикально-фрезерный 5А352ПФ2. | 0,27. | 5,5. | 5,5. | |||
5. Круглошлифовальный 3М151Ф2. | 0,6. | 15,2. | 15,2. | |||
6. Круглошлифовальный 3М151Ф2. | 0,6. | 15,2. | 15,2. | |||
7. Токарный с ЧПУ 16К20Ф3С32. | 0,04. | |||||
8. Верстак. | ; | ; | ; | ; | ||
9. Машина моечная. | ; | ; | 2,5. | ; | ||
10. Стол контрольный. | ; | ; | ; | ; | ||
Итого. | 84,4. | |||||
4.2 Расчет и организация многостаночного обслуживания на участке. Состав и расчет количества участков производства с учетом многостаночного обслуживания
К промышленно-производственному персоналу, обслуживающему оборудование относятся основные и вспомогательные производственные рабочие. Рабочие по техническому обслуживанию оборудования, как правило, включаются в штат цеха.
1. Для расчета численности работающих на участке определяется действительный фонд времени рабочего:
Fдр = (Дк — Дв — Дпр) · s · Дсм·Кпотери, где
Кпотери — коэффициент невыходов на работу
Fдр =(365−14−104) •7 •1 • (1−12/100)= 1522 ч.
Fдр 3 месяца = 380,5 ч.
2. Определение количества рабочих по формуле осуществляется по формуле:
Ri=, чел.
005 Фрезерно-центровальная с ЧПУ (2Г942Ф2)
R = 8,09 • 10 000/ 1522 •1,1 • 60 = 0,8 Принимается R = 1 чел.
010 Токарная с ЧПУ (16К20Ф3С32)
R = 4,7 • 10 000/ 1522 •1,1 • 60 = 0,5 Принимается R = 1 чел.
015 Токарная с ЧПУ (16К20Ф3С32)
R = 4,7 • 10 000/ 1522 •1,1 • 60 = 0,5 Принимается R = 1 чел.
020 Вертикально-фрезерная (5А352ПФ2)
R = 4,29 • 10 000/ 1522 •1,1 • 60 = 0,5 Принимается R = 1 чел.
040Круглошлифовальная (3М151Ф2)
R = 1,2 • 10 000/ 1522 •1,1 • 60 = 0,1 Принимается R = 1 чел.
045Круглошлифовальная (3М151Ф2)
R = 1,2 • 10 000/ 1522 •1,1 • 60 = 0,1 Принимается R = 1 чел.
050Полировальная (16К20Ф3С32)
R = 0,3 • 10 000/ 1522 •1,1 • 60 = 0,03 Принимается R = 1 чел.
3 Общая численность основных производственных рабочих
R пр =7 чел.
Всего вспомогательных рабочих:
R всппр = R контролер + R наладчик + R слесарь
R всп = 3 наладчика +3 контролера + 3 слесаря = 9 чел.
4. Численность наладчиков определяется по формуле:
R нал = (Спр / Нобсл)• S
Нобсл — норма обслуживания, станки
R нал =
Rнал = 2
5 Количество АУП и специалистов определяется методом относительной численности:
Для организации работы на участке принимаем 1 сменного мастера.
Таблица 4.2 — Ведомость работающих на участке
Профессия. | Принятое кол-во. | Разряд. | ||||||
Основные производственные рабочие. | ||||||||
Вспомогательные рабочие. | ||||||||
Сменный мастер | ||||||||
Итого. | ||||||||
4.3 Планировка оборудования и расчет потребных производственных площадей
Площадь участка включает в себя производственную и вспомогательную площадь и бытовые помещения.
Производственная площадь — площадь, занятая оборудованием, рабочими местами. Производственная площадь определяется исходя из габаритов станков и их количества.
Определим площадь, занимаемую каждым станком по формуле:
S = a · b, где
a и b — соответственно длина и ширина станка, м.
Вспомогательная площадь — площадь, занятая под проездами, вспомогательным оборудованием, складами, составляет 10% от всей производственной площади.
Общая площадь = Sпр + Sвсп, м2
К промышленно-производственному персоналу относятся основные, вспомогательные рабочие, младший обслуживающий персонал, административно управленческий персонал, специалисты и служащие.
Таблица 4.3 — Ведомость площади и объема помещения механического участка
Вид помещения. | Удельная площадь на 1 станок, м2 | Количество станков. | Площадь S, м2 | Высота h, м. | Объем V, м3 | |
Производственная площадь. | 20 | 7 | 140 | 12 | 1680 | |
Итого. | ||||||
Вспомогательная площадь. | 20%. | |||||
Общая площадь. | ||||||
4.4 Транспортировка деталей на участке
В процессе производства в цехах предприятия регулярно перемещается большое количество сырья, материала, топлива, полуфабрикатов, инструментов и готовой продукции.
Доставка этих грузов предприятия, перемещения их внутри предприятия является функциями промышленного транспорта, который делится на межцеховой и внутрицеховой. Выбор транспортных средств должен соответствовать объему и характеру грузопотока и учитывать расстояния перевозок, габариты и свойства перевозимых грузов. Доставка заготовок на данный проектируемый участок осуществляется с помощью электрокаров. В качестве тары применяют стандартные прямоугольные банки.
При размещении станков в линии необходимо предусмотреть кратчайшие пути движения каждой детали в процессе обработки.
Зигзагообразное движение деталей в пределах данного пролета из одного ряда станков в другой вполне допустимо, т.к. кран или тележка, двигаясь в одном направлении, имеет возможность доставлять детали к станкам одного и другого ряда без всяких затруднений.
Размеры главных проездов на участке и проходов между рядами станков предназначены для транспортных средств движения людей и определяются в соответствии с габаритами применяемых транспортных средств, санитарно-гигиеническими нормами и нормами техники безопасности. Второстепенные проходы между станками служат для прохода людей к станкам.
Транспортировка детали от начального до конечного этапа изготовления следующая:
1 Заготовка из кузнечного цеха в механический цех транспортируется автопогрузчиком в контейнерах.
2 Заготовки могут складироваться на площадке возле цеха, откуда они, по мере необходимости, поступают на участки механообработки.
3 Транспортировка заготовок на участок производится электропогрузчиком или электрокаром.
4 Передвижение детали на участке от станка к станку осуществляется при помощи пластинчатого конвейера.
5 Из механического цеха в сборочный цех детали передаются партиями на электрокарах или электропогрузчиках.
4.5 Организация ремонта оборудования на участке
Основой организации ремонта оборудования на участке является провидение планово-предупредительного ремонта (ППР). Он включает в себя совокупность различного вида работ по техническому уходу и ремонту оборудования, мероприятия межремонтного обслуживания, как-то: наблюдение за правилами эксплуатации оборудования, своевременное устранение мелких неисправностей и осмотры между плановыми ремонтами выполняют как рабочие, обслуживающие данное оборудование, так и дежурный персонал ремонтной службы цеха (слесари, электрики, смазчики). Межремонтное обслуживание выполняют во время перерывов в работе оборудования: малый, средней и капитальный, а так же изготовление запасных частей — обычно возлагаются на ремонтно-механический цех завода. Капитальный ремонт может выполнятся на специальных ремонтных заводах.
На предприятиях 30% вспомогательных рабочих заняты ремонтом оборудования. В цехе ремонтное хозяйство возглавляем механик цеха, ему подчиняются мастера механика и рабочие механика. Механик цеха несёт ответственность за состояние оборудования, качество его ремонта и проведение профилактических мероприятий, удлиняющих срок службы оборудования и устраняющих преждевременные поломки и аварии.
Механик цеха осуществляет технадзор и руководство ремонтными работами и их своевременную подготовку.
4.6 Обеспечение нормальных условий труда на участке
Для скоординированной и планомерной работы в области безопасности труда на каждом предприятии создается служба охраны труда, подчиняемая главному инженеру.
Главный инженер несет ответственность за безопасность производственных процессов и осуществляет контроль за всеми мероприятиями, направленными на оздоровление условий труда. Всю практическую работу в подразделениях предприятий организуют начальники цехов, участков, смен, а так же мастера. На участке обработки детали стакан подшипника — применяются токарно-револьверные, токарно-винторезные, сверлильные станки.
Отличительной особенностью токарных станков являются: вращающиеся станочные приспособления и заготовки, а так же образующаяся в процессе резания стружка. Для безопасности работы на токарных станках должны применяться защитные устройства для предотвращения опасного соприкосновения рабочего с движущимися элементами станка и режущим инструментом, а так же для локализации опасных зон, куда отлетают частицы обрабатываемого металла.
При работе особое внимание должно быть уделено правильному и надежному закреплению заготовок. При установке инструмента необходимо соблюдать следующие правила:
1) резцы следует закреплять с минимально возможным вылетом из резцедержателя (чтобы он не превышал более чем в 1,5 раза высоту державки) и не менее чем двумя болтами.
2) не оставлять в задней бабке или револьверной головке инструменты, которые не используются при обработке данной заготовки. На сверлильных станках выполнение установки детали осуществляют с соблюдением следующих общих правил безопасности: опорные поверхности выбирают так, чтобы центр тяжести заготовки проходил возможно ближе к середине опорной поверхности, если она одна, и возможно ближе к общему центру поверхностей, если их несколько; точки приложения усилий закрепления размещают так, чтобы направление вектора силы не выходило за пределы поверхностей опор.
Основными опасными и вредными производственными факторами при шлифовальных работах являются: электрический ток, быстроперемещающийся абразивный инструмент, отлетающие от него частицы, а также наличие СОЖ. К числу важнейших мероприятий, обеспечивающих безопасность шлифовальщика, относятся следующее соответствующее исполнение электрооборудования, применение надёжных защитных и предохранительных устройств, а также средства индивидуальной защиты.
Наиболее вероятным моментом получения травм рабочими, обслуживающими фрезерные станки являются: Установка приспособлений и инструментов на станках, наладка станка и удаление стружки.
Не допускается установка неисправной фрезы, особенно с ненадёжно закреплёнными, выкрошенными зубьями. Необходимо обеспечить жесткость закрепления фрезы на шпинделе, прочное и надёжное закрепление заготовки в приспособлении. Подводить фрезу к заготовке следует постепенно, без удара. При возникновении вибраций необходимо остановить станок, проверить исправность гидросистемы станка, крепёжных приспособлений, крепление оправки фрезы. Останавливая станок, сначала надо выключить подачу, затем вращение шпинделя.
Расчет вентиляции и освещения на участке
Вентиляция производственных и вспомогательных помещений предназначена для уменьшения запыленности, задымленности и для очистки воздуха от вредных выделений производства. Она способствует оздоровлению условий труда, повышению производительности и предотвращению профессиональных заболеваний. Вентиляция может быть естественной, механической (вытяжной, приточной, приточно-вытяжной, местной) и смешанной. Естественная вентиляция осуществляется за счет форточек, фрамуг, окон, дефлекторов.
Площадь фрамуг или форточек принимается в размере не менее
2…4% площади пола.
УSфорт = 0,02· Fn, м2
Sn — площадь пола участка; Sn =222 м2
УSфорт = 0,02· 222 =4.4м2
Расчет освещения.
Степень освещенности того или иного производственного помещения зависит от вида работ, выполняемых в данном помещении. В производственном помещении предусматривается естественное и искусственное освещение.
Расчет естественного освещения.
Естественное освещение обеспечивается устройством окон и зенитных фонарей в крыше. Суммарная площадь окон определяется по формуле:
, м2
где Sn — площадь пола участка; Sn = 222 м2
б — удельная площадь окон, приходящаяся на 1 м2 пола; б = 0,1;
ф — коэффициент, учитывающий потери света от загрязнения остекления; ф=0,6.
Расчет числа окон производится по формуле:
, шт.
где Sок — площадь одного окна;
Sок = 12 — (0,8 + 0,3) = 10,9 м
Принимается Sок = 11 м
Sок = 2 11=22 м2
Принимается 2 окна
Расчет искусственного освещения.
Принимается значение освещённости Е=200 Лк.
Суммарная мощность ламп определяется по формуле:
УNл = PуFn, кВт
где Pу — удельная мощность осветительной установки; при высоте подвеса светильника 6 м, площади пола Sуч = 222 м2 и освещенности Е = 200 Лк Ру = 16,6 Вт/м2.
УNл =16,6· 222= 3071 кВт
Выбирается мощность одой лампы: люминесцентная лампа Nл =30…150 Вт.
Принимается Nл=150 Вт
Число ламп рассчитывается по формуле:
, шт.
. Принимается 21 лампа.
Электробезопасность и пожарная безопасность
Залогом безопасности эксплуатации электрооборудования является высокая техническая грамотность и дисциплина труда электротехнического персонала, строгое соблюдение правил и инструкций, организационных и технических мероприятий. Электроинструменты (электродрели, зачистные, шлифовальные, полировальные, притирочные машины) находят широкое применение на производстве. В помещениях с повышенной опасностью и вне помещений должен использоваться электроинструмент классов 2 и 3 напряжением не выше 42 В.
При пользовании электроинструментом запрещается:
— передавать его даже на непродолжительное время другим лицам;
— разбирать и самим ремонтировать;
— держаться за провод инструмента или касаться вращающегося режущего инструмента;
— удалять руками стружки или опилки во время работы инструмента;
— работать с приставных лестниц;
— вносить внутрь металлических резервуаров переносные трансформаторы и — преобразователи частоты;
— оставлять его без надзора и включенным в электросеть.
Для питания переносных светильников в помещениях с повышенной опасностью и особо опасных должно применяться напряжение не выше 42 В, а при наличии особо неблагоприятных условий не выше 12 В. Выбирая средства защиты, надо руководствоваться необходимостью исключения возникновения искровых разрядов с энергией, превышающей на 40% минимальную энергию зажигания окружающей среды.
Пожарная безопасность.
Пожар согласно определению по стандарту — неконтролируемое горение, развивающееся во времени и пространстве. Он наносит большой материальный ущерб и нередко сопровождается несчастными случаями с людьми. Опасными факторами пожара, воздействующими на людей, являются: открытый огонь и искры, повышенная температура воздуха, различных предметов, токсичные продукты горения, дым, пониженная концентрация кислорода; взрыв, обрушение и повреждение зданий, сооружений и установок.
Основными причинами возникновения пожаров является не осторожное обращение с огнем, нарушение правил пожарной безопасности при сварочных и других огневых работах, нарушении правил эксплуатации электрооборудования, не исправность отопительных приборов и термических печей, нарушение правил хранения легковоспламеняющихся и горючих материалов, самовозгорание смазочных и обтирочных материалов.
Пожарная безопасность зданий и помещений существенно зависит от горючести (возгораемости) строительных материалов и огнестойкости строительных конструкций, из которых они построены.
Пожарная профилактика — комплекс организационных и технических мероприятий, направленных на обеспечение безопасности людей, предотвращение пожара, ограничение его распространения, а также создание условий для успешного тушения пожара. К этим мероприятиям относятся меры пожарной безопасности, предусматриваемые при строительстве и проектировании предприятий.
Курение в производственных помещениях допускается только в специально отведенных для этого местах, оборудованных резервуарами с водой и урнами. В производственных и административных зданиях запрещается:
— загромождать проходы к месту расположения первичных средств пожаротушения и к внутренним кранам;
— убирать помещение с применением легковоспламеняющихся и горючих жидкостей;
— оставлять в помещениях после окончания работы топящиеся печи, электроотопительные приборы, включенные в электросеть, не обесточенное технологическое и вспомогательное оборудование, легковоспламеняющиеся и горючие жидкости, неубранные в специально отведенные места;
— производить работы с применением открытого огня в непредусмотренных для этой цели местах.
4.7 Экология производства
Проблема охраны окружающей среды и рационального использования природных ресурсов является одной из наиболее актуальных среди глобальных общечеловеческих проблем, так как от ее решения зависит жизнь на земле, здоровье и благосостояние человечества. Определенную долю загрязнении окружающей среды вносят и машиностроительные предприятия.
Для снижения вредного воздействия машиностроительного завода на окружающую среду при его проектировании, строительстве и эксплуатации должны выполняться природоохранительные мероприятия. Вокруг предприятия должна быть санитарно-защитная зона шириной не менее 50 м. Зеленые насаждения обогащают воздух кислородом, поглощают углекислый газ, шум, очищают воздух от пыли и регулируют микроклимат.
Производство с вредными выделениями (окрасочных, кузнечных, деревообрабатывающий и другие участки) по возможности сосредотачивают в филиалах на окраине города.
С целью поддержания чистоты атмосферного воздуха в пределах норм на предприятии предусматривают предварительную очистку вентиляционных и технологических выбросов с их последующим рассеиванием в атмосферу. Воздух, удаляемый из окрасочного отделения, перед выбросом в атмосферу очищают в гидрофильтрах. Очистка в них происходит за счет улавливания загрязняющих воздух веществ водой.
Очищают воздух от древесной пыли, образующейся в деревообрабатывающих цехах, и от абразивной пыли заточных и шлифовальных станков с помощью циклонов: в них пыль отделяется от запыленного воздуха под воздействием центробежной силы и тканевых фильтров. Благоприятное воздействие на атмосферу в приземном слое оказывает искусственные водоемы, которые поглощают пыль, увлажняют, охлаждают и ионизируют воздух.
Для сокращения расхода воды в последнее время широко внедряют системы оборотного водоснабжения, которые позволяют повторно использовать бывшую в употреблении воду после ее очистки в специальных устройствах. При этом чистая вода расходуется только на восполнения потерь из-за испарения и утечек вместе с осадком грязи.
Хозяйственно-бытовые стоки сливаются в канализацию. Их утилизация осуществляется на специальных предприятиях. Очищают производственные сточные воды и ливневые стоки в очистных сооружениях.
4.8 Удаление отходов производства с участка
Удаление отходов металлической стружки с участка производится механически. Под полом участка расположен шнековый конвейер для уборки стружки.
К главному конвейеру подходят разветвления от каждого металлорежущего станка, где производится механическая обработка данной детали с образованием стружки.
Транспортер подает стружку в бункер, который находится вне цеха. Далее стружка, собранная в бункере, перевозится автомашиной или погрузчиком на скрапбазу, где из стружки под давлением делают брикеты и переплавляют в чугунолитейных цехах.
Рациональное использование материальных ресурсов способствует дальнейшему снижению себестоимости продукции и росту эффективности производства.
Заключение
Обоснование технических решений, принятых в проекте
В дипломном проекте был спроектирован участок механического цеха, работы механического участка обработки детали «Шток» ЦГ-160.80×560.31.024с производственной программой выпуска 10 000 штуки. Деталь изготавливается из стали 40Х ГОСТ 4543–71, масса заготовки составляет 37 кг, а чистый вес изделия -30,7 кг. Уровень использования материала по проектируемой детали средний, так как коэффициент использования металла составил 0,83, а уровень отходов материала составил — 27%.
На механическом участке используется современное металлорежущее оборудование, средний коэффициент загрузки которого составил 32%, что является выше среднего уровня. На участке установлено 4 станков с ЧПУ: токарные (16К20Ф3С32), фрезерно-центровальная с ЧПУ (2Г942Ф2), вертикально-фрезерный (5А352ПФ2) и другое оборудование, кроме этого моечные машины, верстаки, рабочие места контролера ОТК. На участке работают 7 основных рабочих 9 вспомогательных и 1 АУП.
Проектируемый технологический процесс обработки детали является оптимальным для условий серийного производства в заданных объемах производства детали. За счет применения новой усовершенствованной технологии и современного оборудования, например, станков с ЧПУ, повышается качество механообработки и снижается ее трудоемкость, снижаются потери от брака и себестоимость изготовления детали. Кв = 1 — 1,2 — коэффициент выполнения норм.
Список источников
1. Белоусов А. П. Проектирование станочных приспособлений.-М.: Высшая школа, 1980
2. Данилевский В. В. Технология машиностроения-Учебник для техникумов. — М.: Высшая школа, 1984
3. Дерябин А. А., Эстерзон М. А. Технология изготовления деталей на станках с ЧПУ и в ГСП.-М.: Машиностроение, 1989.
4. Добрыднев И. С. Курсовое проектирование по предмету «Технология машиностроения» — М.: Машиностроение, 1985
5. Единая система допусков и посадок СЭВ в машиностроение и приборостроении. в 2-х томах — М.: Издательство стандартов, 1989.
6. Клепиков В. В., Бодров А. Н. Технология машиностроения. — М.: Форум-ИНФРА, 2004
7. Марочник сталей и сплавов. Под редакцией В. Г. Сорокина. -М.: Машиностроение, 1989
8. Мельников Г. Н., Вороненко В. П. Проектирование механосборочного цеха. — М.: Машиностроение, 1990
9. Нефедов Н. А. Дипломное проектирование в машиностроительных техникумах. — М.: Высшая школа, 1986
10. Нефедов Н. А. Сборник задач и примеров по резанию металлов и режущему инструменту. — М.: Машиностроение, 1990.
11. Общемашиносроительные нормативы времени и режимов резания для нормирования работ, выполняемых на универсальных и многоцелевых станках с числовым программным управлением. В 2-х частях. — М.: Экономика, 1990.
12. Общемашиностроительные нормативы времени времени вспомогательного на обслуживание рабочего места и подготовительно-заключительного для технического нормирования для станочных работ (серийное производство).-М.: Машиностроение, 1974.
13. Режимы резания металлов. Справочник по ред. А. Д. Корчемкина. — М.: Машиностроение, 1995
14. Тракторы Т40М, Т40АМ, Т40АИМ. Тарасов Г. Д. — М.: Машиностроение, 1990
15. Справочник инструментальщика под ред. И. А. Ординарцева. — Л.: Машиностроение, 1987
16. Справочник технолога-машиностроения в 2-х томах. Под ред. А. Г. Косиловой и Р. К. Мещерикова. — М.: Машиностроение, 1985.